生产线布局(超详细).
生产线布局说明

制动器生产线平面图如下:1-磨床;2-助力臂覆盖区域;3-小车;4-零件放置台;5-工人工作位置;6-液压机;7-工作平台1;8-辊子滑台;9-工作平台2;10-工作平台3;11-油桶;12-成品存放板生产线所完成的工序包括装配制动底板、磨摩擦片外圆、装配凸轮、装配防护罩及后臂总成、收集成品及注油。
以上工序中,工件的搬运、翻转依靠助力臂,工件在辊子滑台上依靠手推移动,装配组件放置在可提升的小车内,小零件放在工作平台上的零件盒内。
一、图示各部分功能介绍:1-磨床,磨摩擦片外圆,工件由助力臂夹持搬运。
2-助力臂覆盖区域,助力臂采用气压夹持,人工操作,能实现工件的圆周移动、上下移动和翻转等动作,覆盖区域保证工序间夹持工件的要求,安装位置方便工人操作。
3-小车,放置装配的组件,采用液压提升装置,便于拿取。
小车的尺寸大小为1000*500*1200(mm)。
4-零件放置台,放置些许制动底板和制动蹄备用。
台的尺寸大小为2500*800*750(mm)。
5-工人工作位置,预留出足够空间,保证操作和移动的方便。
6-液压机,装配制动底板和制动蹄,用液压力代替人力压支撑销。
7-工作平台1,安装螺钉和钢丝锁线,平台上有专门区域放置螺钉和钢丝锁线等零件。
工作平台的尺寸大小为1000*800*750(mm)。
8-辊子滑台,放置各工序完成后的工件,方便移动。
滑台的尺寸大小为1500*800*750(mm),为两工序之间留出2~3个缓冲件,协调工作节拍。
9-工作平台2,安装凸轮和回位弹簧,,平台上有专门区域放置回位弹簧等零件。
10-工作平台3,安装防护罩和后臂总成,平台上专门区域放置螺栓、垫圈等零件。
11-油桶,对装配成品的关键部位注油以润滑、防锈。
12-成品存放板,存放装配好的成品,成品的搬运依靠助力臂。
二、各工序工人任务:1)工人1,主要完成制动底板的装配,包括压支撑销、装螺钉和钢丝锁线。
2)工人2,主要完成磨摩擦片外圆和装凸轮、回位弹簧,包括工件的翻转。
生产线布局方法

生产线布局方法生产线布局方法是一种重要的生产管理方法,它涉及到工厂内部生产线的规划和布局。
合理的生产线布局可以提高生产效率,降低生产成本,优化生产流程,提升产品质量。
本文将详细介绍几种常见的生产线布局方法,并探讨其优缺点。
1. 产品布局方法产品布局方法是按照产品的特点和生产工艺要求来布局生产线。
这种方法适用于产品种类少而相似的生产企业。
在产品布局方法中,相似的产品被放置在相邻的生产线上,这样可以减少生产过程中的切换和调整时间,提高生产效率。
然而,这种布局方法也有一些缺点,比如工艺相对复杂的产品可能会因为生产线之间的物料转移而导致生产过程中的错误。
2. 工艺布局方法工艺布局方法将生产线上的设备和工艺按照一定的顺序进行布局。
这种方法适用于具有复杂工艺流程的生产企业。
在工艺布局方法中,工序相同或者相似的设备被放置在相邻的位置,以便于操作人员进行监控和调整。
这种布局方法可以减少生产过程中的转移和运输时间,提高生产效率。
缺点是由于不同工艺的设备布置紧密,一旦出现故障可能会导致整个生产线停产。
3. 运输布局方法运输布局方法将生产线上的设备和工序按照物料运输路径进行布局。
这种方法适用于物料运输量大的生产企业。
在运输布局方法中,生产线上的设备被按照物料流动的方向进行布置,以减少物料运输的时间和成本。
这种布局方法可以确保物料在生产过程中的流动畅通,减少物料的堆积和阻塞。
然而,过于关注物料运输路径的设计可能会导致空间的浪费和设备利用率的降低。
4. 功能布局方法功能布局方法将生产线上的设备和工序按照功能进行布局。
这种方法适用于具有多种产品和复杂生产流程的企业。
在功能布局方法中,相同功能的设备被放置在相邻的位置,以便于操作人员进行监控和维护。
这种布局方法可以提高生产效率和产品质量,但却可能导致物料运输路径的延长和堆积,增加生产成本。
综上所述,生产线布局方法是一项重要的生产管理技术。
不同的布局方法适用于不同的生产企业,根据产品特点、工艺要求、物料运输量和生产流程等因素来选择合适的布局方法。
生产线布局大全

3. 求出工作站理论值
Nt =T/ Ct
2N0t19—/12/—27 工作站理论值,T——完成作业所需的时间总量
39
节拍时间
一个典型的工作日是包括两个班次的,每一个班会有
9.5个工作小时。那么,这个工作日每一班就有9.5*60=570 分钟,也就是说,每个工作天是1140分钟。
如果按照工作单,每天应该生产160K个产品,那么:
第三步:计算理论工作站数 Nt =T/ Ct=195秒/50.4秒=3.87≈4站
2019/12/27
44
产品原则布局
第四步:选择作业分配工 作 (以后续作业数量多少安排作 业)
2019/12/27
作业 A
B/D C/E F/G/H/I
J K
后续作业数量 6 5 4 2 1 0
45
产品原则布局
第五步对工作站安排作业,工作站周期:50.4秒
1
3
5
7
收发部
铸造
小型玩具 转配线
喷漆
2
4
6
8
塑模与冲 缝纫 大型玩具 机械装配
压 2019/12/27
转配线
线
20
工艺原则布局
次数
车 间 之 间
1 1 2 3
的4
流5
动6
表7
8 2019/12/27
23 175 50
0
45 0 30 100 75 17 88
20
678 200 20 25 90 80 90 125 99 180 5 0 25 0 180 187
节拍时间 =
每天有效时间 每天须生产数
= 1140 分钟 = 0.007 分钟/产品 160K 个产品
生产线布局(超详细)
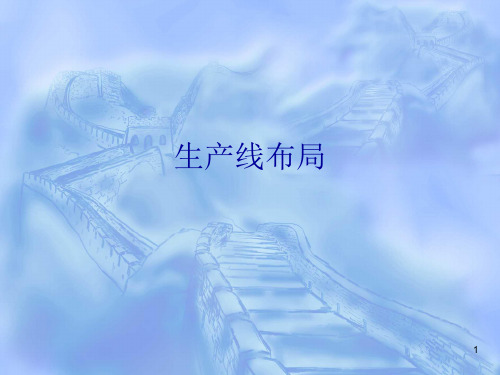
= 0.007 分钟/产品
换句话说,每分钟生产140单位的产品。
1/30/2019 40
产品原则布局
4.进行作业活动分配(作业活动分配到各工作站) 5.向工作站分配作业(作业活动在工作站内分配) 6.评估装配线平衡后的效率 E=T/(Na × Ct)
E——装配线平衡效率 T——完成作业所需的时间总量 Na——实际工作站数 Ct——生产节拍
就生产而言E是怎样的 数值较好?
7.如果不理想,重复第4步骤
1/30/2019 41
产品原则布局
作业 时间(S) 45 11 描述 安装后轮支架,拧紧四个螺 母 插入后轴 作业前提条件 —— A
案例 一玩具厂的玩具 车在流水线上 作业,每天需 生产500辆, 每天生产时间 为420分钟, 生产步骤及时 间如左表:
3 铸造 4 缝纫
5 小型玩具 转配线 6 大型玩具 转配线
7 喷漆 8 机械装配 线
20
工艺原则布局
次数
车 间 之 间 的 流 动 表
1/30/2019
1 1 2 3 4 5 6 7 8
2 3 175 50 0
4 0 100 17
5 30 75 88 20
6 200 90 125 5 0
7 20 80 99 0 180 347
6σ=?
4
6σ标准
PPM等于 多少?
σ
PPM 308,537 66,807 6,210 233 3.4
缺陷减少5倍
2 3 4 5 6
缺陷减少11倍
缺陷减少26倍
缺陷减少68倍
5
鉴别七大浪费
一、生产产生的不良引起的浪费
任何产品的不良都是浪费的一个主要来源。
生产线布局(超详细)【精品课件】.ppt
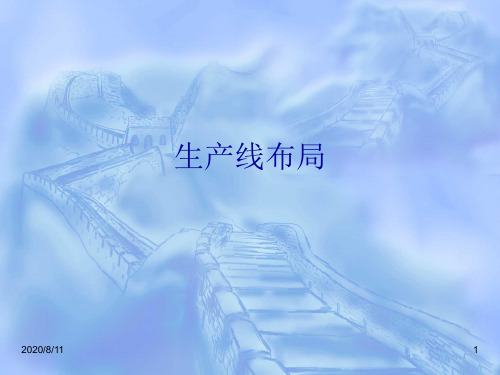
2020/8/11
12
鉴别七大浪费
六、来自工序不当的浪费
工作本身产生的浪费,当机器不正常运作而使操作人员 需要花额外时间,或当操作人员出于习惯或花了过多的 时间使清洁工作超过了规格的要求。
多余的检查也是过程浪费的另一个表现形式。
2020/8/11
13
鉴别七大浪费
七、不需要的动作的浪费
人们在工作设置中经常将工作中的动作搞混乱,实际做的动 作和工作要求的动作往往是不同的。
生产线布局
2020/8/11
1
精益生产五项基本原则
• 价值 (VALUE) : 决定于客户是否愿意为了它而付钱。
• 价值流 (VALUE STREAM) : 从产品设计到客户服务的所有
活动的描述和鉴别,都需要消除非增值活动。
• 流畅 (FLOW) : 消除所有工序的阻滞使价值流“流畅”而没有
中断。
作为一个确定的目的,工作是要作为一组精确的动作来考虑 的,哪些是增值的,那些是不增值的。
一个人在每天的恒定的工作中(例如一个很忙的人)可能实 际上只是很少一部分是增值工作。
工作中的不需要的动作被认为是浪费的,不增值的。
2020/8/11
14
生产布局前的准备工作
▪ 产能评估 ▪ 生产线顺流 ▪ 库存周转评估
1. 采用了看板管理,拉动生产方式 2. 车间布局U型布局; 3. 不同类型的机器摆放在一块; 4. 实现了单件流的生产; 5. 机器小型化 ; 6. 工序中间很少甚至没有库存; 7. 实现了作业标准化; 8. 对工人实行了多技能培训; 9. 具有完善的作业改善活动制度
2020/8/11
3
看谁摘的果子最多!
6
产生更严重的成本连锁反应……
[全]自动化生产线布局介绍
![[全]自动化生产线布局介绍](https://img.taocdn.com/s3/m/0a6e24461611cc7931b765ce05087632311274e6.png)
[全]自动化生产线布局介绍自动化生产线布局是指在生产过程中,以最优的方式布置和安排各个生产设备、工作站、输送系统和物料存储区域等要素,以实现生产效率的最大化、生产流程的最优化和生产成本的最低化。
自动化生产线布局的合理性直接影响着企业的生产能力、生产效率和生产质量。
下面,将从布局原则、布局方法和布局优化等方面进行介绍。
一、布局原则:1.流程合理性:根据生产工艺和产品的特点,合理设置工作站的位置,使得物料顺畅流动,减少不必要的输送和等待时间,从而提高生产效率和质量。
2.空间利用效率:合理利用厂房空间,最大限度地利用各个区域,减少空间浪费,提高生产能力。
3.人机协同:结合工人的工作习惯和人机工程学原理,合理安排工作站的位置和设备的高度,使得工人可以顺利操作和控制设备,提高工作效率和人员安全。
4.安全性:合理布局生产线,设置安全设施和标志,保障工人的人身安全。
二、布局方法:1.直线流程布局:将各个工作站按照产品流程的顺序依次排列,形成一条直线流程,适用于生产过程简单、产品品种少的情况。
2.U形流程布局:将各个工作站按照产品流程的顺序依次排列,形成一个U形,适用于生产过程较复杂、产品品种多的情况。
3.L形流程布局:将各个工作站按照产品流程的顺序依次排列,形成一个L形,适用于生产过程中存在分支流程的情况。
4.网状流程布局:将各个工作站按照产品流程的关联程度进行合理布局,形成一个网状,适用于生产过程中存在多个分支流程和多个子系统的情况。
三、布局优化:1.平衡生产线:通过对不同工作站的生产能力进行平衡,使得每个工作站的产能相对均衡,避免生产线发生拥塞或闲置的情况。
2.减少物料处理:通过优化布局,减少物料的搬运和处理次数,降低物料损耗和处理成本。
3.灵活性和可扩展性:考虑到市场需求的不确定性,布局中应该考虑到生产线的灵活性和可扩展性,方便进行生产线的调整和扩展。
4.考虑环境影响:布局中应该考虑到环境因素,如噪音、振动、粉尘等对工作人员和设备的影响,合理设置防护设施和消声装置。
生产线布局(超详细)全解
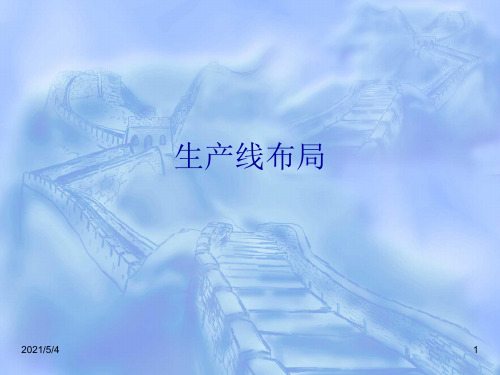
2021/5/4
44
产品原则布局
▪ 第四步:选择作业分配 工作
(以后续作业数量多少安 排作业)
2021/5/4
作业 A
B/D C/E F/G/H/I
J K
后续作业数量 6 5 4 2 1 0
45
产品原则布局
▪ 第五步对工作站安排作业,工作站周期:50.4秒
工作站 作业 时间(S)
工作站1 A
45
二、运输中的浪费
具有代表性的是,有些项目总是无工作性质地移动,时间 花费了在路途中,这是浪费。
2021/5/4
8
鉴别七大浪费
三、来自库存的浪费
库存代表着某些项目正等待某些事情的发生,这里的浪 费表现在:和保存着这些项目来等待有关联的成本,对 这些项目无增值而导致时间的损失。
安全库存是为了保证生产部门的正常运作和弥补不良品 的损失而存在的,但是安全库存不能够超出它们的正常 需要。
▪ 问:
• 金额如何计算出来的? • 组合布局方法或排列有多少种? • 如何排列的才是有效的?
2021/5/4
23
工艺原则布局
▪ 成本矩阵——方案一,总成本合计3474
11 2 3 4 5 6 7 82021/5/4
2
3
175 50
0
4
5
6
7
0
60 400 60
100 150 180 240
17 88 125 198
▪ 使用范围:
• 批量小 • 体积大
▪ 布局特点
• 以产品为中心 • 不考虑物流成本和复杂程度
2021/5/4
18
工艺原则布局
▪ 定义:
• 将相似的设备或功能集中放在一起的布局方式 • 也称车间布局,如车床车间
生产线布局大全

x
x
x
C
x
x
x
D
xx
x
x
x
E
xx
x
F
x
x
x
G
x
x
x
x
H
x
xx
2019/11/23
34
调整的零部件移动路线矩阵
部件 A D F C G B H E
机器
1 2 4 8 10 3 6 9 5 7 11 12
xxxxx
xxxxx
x
xx
xxx
xxx
x
xx
x
xxx
x
x
x
2019/11/23
35
按成组技术布置的方案
第三步:计算理论工作站数 Nt =T/ Ct=195秒/50.4秒=3.87≈4站
2019/11/23
44
产品原则布局
第四步:选择作业分配工 作 (以后续作业数量多少安排作 业)
2019/11/23
作业 A
B/D C/E F/G/H/I
J K
后续作业数量 6 5 4 2 1 0
45
产品原则布局
第五步对工作站安排作业,工作站周期:50.4秒
1. 采用了看板管理,拉动生产方式 2. 车间布局U型布局; 3. 不同类型的机器摆放在一块; 4. 实现了单件流的生产; 5. 机器小型化 ; 6. 工序中间很少甚至没有库存; 7. 实现了作业标准化; 8. 对工人实行了多技能培训; 9. 具有完善的作业改善活动制度
2019/11/23
3
看谁摘的果子最多!
37
产品原则布局
适用范围
大批量、同质性生产 产品需求足够稳定 流水作业
生产线布局(超详细)_图文
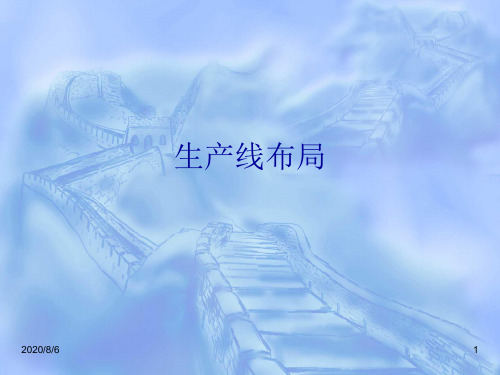
次数
1 1 2 3 4 5 6 7 8
23 175 50
0
45 0 30 100 75 17 88
20
678 200 20 25 90 80 90 125 99 180 5 0 25 0 180 187
347 103 7
21
▪ 玩具厂各车间年物流成本示意图
2020/8/6
22
工艺原则布局
2020/8/6
12
鉴别七大浪费
六、来自工序不当的浪费
工作本身产生的浪费,当机器不正常运作而使操作人员 需要花额外时间,或当操作人员出于习惯或花了过多的 时间使清洁工作超过了规格的要求。
多余的检查也是过程浪费的另一个表现形式。
2020/8/6
13
鉴别七大浪费
七、不需要的动作的浪费
人们在工作设置中经常将工作中的动作搞混乱,实际做的动 作和工作要求的动作往往是不同的。
2020/8/6
15
生产线布局类别
▪ 定位原则布局 ▪ 工艺原则布局 ▪ 产品原则布局 ▪ 成组技术(单元式)布局
2020/8/6
16
定位原则布局
▪ 定义:
• 将原材料和设备按照使用次序和移动的难易程度 在产品的四周进行生产
▪ 起源
• 19世纪初亨利福特的汽车装配线
2020/8/6
17
定位原则布局
2020/8/6
9
不合格品
率高
库
机器故障率高
调整时间太长
存
水
设备能力不平衡
缺勤率高
备件供应不及时
平
采购周期太长 技术服务 工人技能差 后勤服务差
不及时
图 17-1 库存水平高掩盖的管理问题多
合成材料制造的生产线布局

合成材料制造的生产线布局1.合成材料,如塑料、合成纤维和合成橡胶,已经成为现代工业的重要组成部分。
随着科技的进步和市场需求的增长,合成材料的生产效率和质量成为企业竞争力的关键。
生产线布局是影响合成材料制造效率和质量的重要因素之一。
本文将详细分析合成材料制造的生产线布局,以帮助企业优化生产过程,提高生产效率和产品质量。
2. 生产线布局设计原则生产线布局设计需要遵循以下原则:2.1 流程连续性生产线应按照工艺流程的顺序进行布局,以减少物料和人员的流动距离,降低生产过程中的时间和成本。
2.2 灵活性和可扩展性生产线布局应具有一定的灵活性和可扩展性,以适应市场需求的变化和技术进步。
2.3 安全和环保生产线布局应考虑安全和环保要求,合理设置防火、防爆、防泄漏等设施,确保生产过程的安全和环保。
2.4 人性化生产线布局应考虑人性化设计,提高员工的舒适度和满意度,从而提高生产效率和质量。
3. 生产线布局类型根据不同的生产方式和组织形式,生产线布局可以分为以下几种类型:3.1 直线型布局直线型布局是将生产设备按照工艺流程的顺序排列成一条直线,适合于产品种类较少、生产流程简单的合成材料制造。
3.2 U型布局U型布局是将生产设备按照工艺流程的顺序排列成U型,适合于产品种类较多、生产流程复杂的合成材料制造。
3.3 环绕型布局环绕型布局是将生产设备按照工艺流程的顺序排列成一个环形,适合于大型合成材料制造企业,可以有效减少物料和人员的流动距离。
4. 生产线布局优化为了提高合成材料制造的生产效率和质量,企业应根据实际情况对生产线布局进行优化。
4.1 设备选型和配置选择适合企业生产需求的设备,并进行合理的配置,以提高生产效率和质量。
4.2 物料搬运和储存合理设计物料搬运和储存系统,减少物料流动距离和时间,提高生产效率。
4.3 信息和自动化系统引入信息和自动化系统,实现生产过程的实时监控和控制,提高生产效率和质量。
5. 结论合成材料制造的生产线布局对生产效率和质量具有重要影响。
生产线布局(超详细)PPT课件
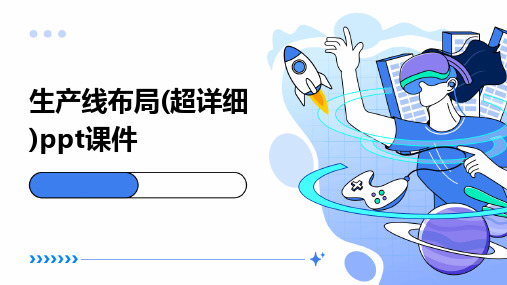
产品特性
产品的工艺要求、生产流程、 物料特性等对生产线布局有直 接影响。
人力资源
员工的技能、经验和工作习惯 对生产线布局的效率和效果有 重要影响。
环境因素
生产环境的要求、法律法规、 环保要求等对生产线布局有制 约作用。
02
生产线布局的类型
直线式布局
总结词
简单明了,便于管理,适合小批量生产
详细描述
布局评估的方法
01
02
03
04
生产流程分析
通过分析生产流程,评估生产 线布局的合理性,找出瓶颈环
节和浪费。
设备利用率评估
计算设备的平均利用率,判断 是否存在设备闲置或使用不足
的情况。
空间利用率评估
评估生产线布局的空间利用率 ,判断是否充分利用了生产空
间。
物流效率评估
分析生产线上的物流效率,判 断是否存在物料搬运距离过长
收集生产线布局相关 的数据,包括设备布 局、设备参数、生产 流程、物流路径等。
分析问题
根据收集的数据,分 析生产线布局存在的 问题和瓶颈环节。
制定方案
根据问题分析结果, 制定相应的布局调整 方案。
实施调整
按照制定的方案,逐 步实施生产线布局的 调整。
效果评估
在布局调整后,对生 产线的运行情况进行 评估,判断调整效果。
详细描述
该电子产品制造企业采用精益的生产线布局,以提高生产效率和降低成本。生产线布局 高效,各工序之间衔接紧密,以减少浪费。同时,大量采用自动
总结词
安全、卫生、人性化
VS
详细描述
该食品加工企业注重生产线的安全性、卫 生和人性化设计。生产线布局合理,保证 清洁度和卫生标准。同时,充分考虑员工 操作的舒适性和安全性,提高生产效率和 工作质量。
生产线布局(超详细).共122页

56、书不仅是生活,而且是现在、过 去和未 来文化 生活的 源泉。 ——库 法耶夫 57、生命不可能有两次,但许多人连一 次也不 善于度 过。— —吕凯 特 58、问渠哪得清如许,为有源头活水来 。—— 朱熹 59、我的努力求学没有得到别的好处, 只不过 是愈来 愈发觉 自己的 无知。 ——笛 卡儿生产线布 Nhomakorabea(超详细).
21、没有人陪你走一辈子,所以你要 适应孤 独,没 有人会 帮你一 辈子, 所以你 要奋斗 一生。 22、当眼泪流尽的时候,留下的应该 是坚强 。 23、要改变命运,首先改变自己。
24、勇气很有理由被当作人类德性之 首,因 为这种 德性保 证了所 有其余 的德性 。--温 斯顿. 丘吉尔 。 25、梯子的梯阶从来不是用来搁脚的 ,它只 是让人 们的脚 放上一 段时间 ,以便 让别一 只脚能 够再往 上登。
拉
60、生活的道路一旦选定,就要勇敢地 走到底 ,决不 回头。 ——左
食品生产车间标准布局图

要求:1、应有1-2名化验人员,应执有初级化验工及以上资格证书上岗。2、按细则要求配相关检验设备和试剂及无菌室。3、按细则有委托检验协议。4、产品应该批批检验,并有真实完整记录。
内包材料存放间
要求:1、设内包材料传递口。2、要求进行封闭杀菌消毒后,从封闭式投递口进入内包装车间。
注:1、应在原料、配料间、生产车间、内包装车间的质量关键工序处,设置关键质量控制点及技术要求。2、凡生产车间、内包装车间人员和化验员要有健康证。3、工艺:原料(辅料)--预处理车间(配料)--生产车间(内包)--外包装车间--成品仓库。
内包装车间(洁净区)
要求:1、需包装杀菌的,应配不低120度的高压锅。2、应设立二次洗手更衣间或独立洗手更衣间。3、空气洁净度达到要求。4、作业指导书上墙。5、设置关键控制点。
辅料(添加剂)仓库
要求:1、应有架空托架,离地10cm离墙20cm有序摆放整齐,原料放在架空托架上。2、应有温度湿度表,并有记录本,记录每次检查数据。3、每堆原料都应标注有原料情况牌,内容包括:进货时间、数量、规格型号、原料生产来源、仓库收货人。5、添加剂通过物流通道进入生产车间。6、有消毒溶剂的要单独隔离存放。
预处理车间(准洁净区)
要求:1、合格原料才能进行预处理。才能进入生产车间或配料间。2、有防蝇、防雀、防鼠设施。
-------------------------
配料间:
要求:1、对原料和辅料进行调配,有相关工作用工具及称量器具。2、每次的配制比都应有车间负责人签字,下达的配料方案都应有具体投料通知单。
成品仓库
要求:1、应有架空托架,离地10cm离墙20cm有序摆放整齐,成品摆放架空托架上。2、应有温度湿度表(有的原料还应有防爆防火要求),并有记录本,记录每次检查数据。3、成品应按分区码放,应设置:合格区、不合格区、待检区等(在产品对应墙体位置标示,也可用活动牌标示)。4、每个产品码堆,都应标注有产品情况表,内容包括:生产时间、数量、规格型号、发货时间,发货数量、仓库发货人、领货人等。5、所有产品放行、返工和进行非食用处理,都应有质量负责人和化验室负责人签字。
- 1、下载文档前请自行甄别文档内容的完整性,平台不提供额外的编辑、内容补充、找答案等附加服务。
- 2、"仅部分预览"的文档,不可在线预览部分如存在完整性等问题,可反馈申请退款(可完整预览的文档不适用该条件!)。
- 3、如文档侵犯您的权益,请联系客服反馈,我们会尽快为您处理(人工客服工作时间:9:00-18:30)。
使用范围
• • • • • 生产设备密集型 设备专业性 自动化程度高 资本密集型 产品重量轻
19玩具厂有8个车间,采用物料集中搬 运方式,每次只能搬运一个周转箱,车间之 间运输成本为1元,每隔一个车间增加1元
1 收发部 2 塑模与冲 压
2018/10/15
3
看谁摘的果子最多!
6σ=?
2018/10/15
4
6σ标准
PPM等于 多少?
σ
PPM 308,537 66,807 6,210 233 3.4
缺陷减少5倍
2 3 4 5 6
缺陷减少11倍
缺陷减少26倍
缺陷减少68倍
2018/10/15
5
鉴别七大浪费
一、生产产生的不良引起的浪费
任何产品的不良都是浪费的一个主要来源。
Í ¼ 17-1 ¿ â´ æË ®Æ ½¸ ßÑ Ú¸ ǵ Ĺ Ü À íÎ ÊÌ â¶ à
2018/10/15 10
鉴别七大浪费
四、来自生产过剩的浪费
公司有时会生产比他们可能卖出去的更多的产品,因为他 们想要建立库存,作为一个安全保证措施来防止可能出错 而造成的后果,或者因为他们想要保证他们的设备和设施 的运转。
3 铸造 4 缝纫
5 小型玩具 转配线 6 大型玩具 转配线
7 喷漆 8 机械装配 线
20
工艺原则布局
次数
车 间 之 间 的 流 动 表
2018/10/15
9
»º ² ϸ ñ· Æ Ê¸ Â ß â ¿ æ ´ ® Ë ½ Æ É¹ ² ºÖ ÜÆ ÚÌ «³ ¤ ¼Ê õ· þÎ ñ »¼ ² °Ê ± ¤È ¹ Ë¼Ä Ü² î óÇ º Ú· þÎ ñ² î è± É ¸Ä ÜÁ ¦² »Æ ½º â ±Ç È Ú ʸ ß ¸¼ ± þ¹ ©Ó ¦² »¼ °Ê ± ú÷ » ƹ ÊÕ Ï ʸ ß ÷Õ µ ûÊ ±¼ äÌ «³ ¤
2018/10/15
工作中的不需要的动作被认为是浪费的,不增值的。
14
生产布局前的准备工作
产能评估 生产线顺流 库存周转评估
2018/10/15
15
生产线布局类别
定位原则布局 工艺原则布局 产品原则布局 成组技术(单元式)布局
2018/10/15
16
定位原则布局
定义:
• 将原材料和设备按照使用次序和移动的难易程度 在产品的四周进行生产
起源
• 19世纪初亨利福特的汽车装配线
2018/10/15
17
定位原则布局
使用范围:
• 批量小 • 体积大
布局特点
• 以产品为中心 • 不考虑物流成本和复杂程度
2018/10/15
18
工艺原则布局
定义:
• 将相似的设备或功能集中放在一起的布局方式 • 也称车间布局,如车床车间
• 尽善尽美(PERFECTION) : 通过持续改善的应用,来提倡“ 第一次就做好”的一种能力。
2018/10/15 2
大规模生产和精益生产方式的区别
大规模生产方式
1. 采用推动生产方式 2. 车间布局是按功能区划分; 3. 相同类型的机器摆放在一块; 4. 大批量的生产; 5. 机器适合于大批量生产 ; 6. 工序中间容易堆积库存 ; 7. 未实现作业标准化; 8. 工人一般只会一种操作; 9. 没有或只有个体的作业改善活动
2018/10/15
6
产生更严重的成本连锁反应……
“一人错误百人忙” 的成本暴增曲线
更多的 防火成本
更多的 救火成本 更多的 返工成本
救火、防火、多余监 督、过度控制、多余 检验、投诉处理、退 货维修、商誉损失、 顾客流失等效应连锁 扩大成本! 重工、返修、报废成本
日常管销/制造成本
7
正常成本
2018/10/15
生产线布局
2018/10/15
1
精益生产五项基本原则
• 价值 (VALUE) : 决定于客户是否愿意为了它而付钱。
• 价值流 (VALUE STREAM) : 从产品设计到客户服务的所有 活动的描述和鉴别,都需要消除非增值活动。 • 流畅 (FLOW) : 中断。 • 拉动 (PULL) : 流动的一种能力。 消除所有工序的阻滞使价值流“流畅”而没有 通过客户的需求来达到产品和工序能够畅通的
鉴别七大浪费
二、运输中的浪费
具有代表性的是,有些项目总是无工作性质地移动,时间 花费了在路途中,这是浪费。
2018/10/15
8
鉴别七大浪费
三、来自库存的浪费
库存代表着某些项目正等待某些事情的发生,这里的浪 费表现在:和保存着这些项目来等待有关联的成本,对 这些项目无增值而导致时间的损失。 安全库存是为了保证生产部门的正常运作和弥补不良品 的损失而存在的,但是安全库存不能够超出它们的正常 需要。
2018/10/15
精益生产方式
1. 采用了看板管理,拉动生产方式 2. 车间布局U型布局; 3. 不同类型的机器摆放在一块; 4. 实现了单件流的生产; 5. 机器小型化 ; 6. 工序中间很少甚至没有库存; 7. 实现了作业标准化; 8. 对工人实行了多技能培训; 9. 具有完善的作业改善活动制度
无论什么原因,没有直接的需求就生产的产品都是浪费。
如果有些项目的需求没有了,那这时,这些项目将不得不被放弃或者 降价处理。 其间,它们储存在仓库里,造成成本的增加和库存的浪费。
2018/10/15 11
鉴别七大浪费
五、来自时间等待的浪费
时间等待的浪费是很容易被鉴别的,它有很多的表现形态, 包括有: • 为定单而等待 • 为批准而等待 • 为零部件而等待 • 为物料而等待 • 为前面过程中叙述的项目而等待 • 为设备的维修而等待
2018/10/15 12
鉴别七大浪费
六、来自工序不当的浪费
工作本身产生的浪费,当机器不正常运作而使操作人员 需要花额外时间,或当操作人员出于习惯或花了过多的 时间使清洁工作超过了规格的要求。 多余的检查也是过程浪费的另一个表现形式。
2018/10/15
13
鉴别七大浪费
七、不需要的动作的浪费
人们在工作设置中经常将工作中的动作搞混乱,实际做的动 作和工作要求的动作往往是不同的。 作为一个确定的目的,工作是要作为一组精确的动作来考虑 的,哪些是增值的,那些是不增值的。 一个人在每天的恒定的工作中(例如一个很忙的人)可能实 际上只是很少一部分是增值工作。