车间生产线布局31页PPT
合集下载
制造车间布局详解课件

设备设施布局
设备设施布局
系统布置设计(Systematic Layout Planning )
P产品构成分析:
例:叉车产品分析
设备设施布局
系统布置设计(Systematic Layout Planning )
例:P—Q分析
设备设施布局
系统布置设计(Systematic Layout Planning )
在工业安全用色中,橙色表示危险,是警戒色。橙色非常明亮刺眼,如火车头,登山服装,背包,救生衣等。车间现场,橙色可用于安全警示标识,如安全帽、危险作业场所的工作服。
在工业安全用色中,黄色表示提醒注意。如交通号志上的黄灯,工程用的大型机器,学生用雨衣,雨鞋等,危险、保安设施。车间现场,黄色常被用作安全色,因为这极易被人发现,如室外作业的工作服,常用于警示标识,用于通道线、定置线。
图1 产品原则布置示意图
设备设施布局
(2)工艺布置原则(机群式)把同类型的设备和人员集中布置在一个地方。
图4 工艺原则布置示意图
设备设施布局
(3)固定式布置原则(项目布置)主要是工程项目和大型产品生产采用的一种布置形式。 它的加工对象位置,生产工人和设备都随加工产品所在的某一位置而转移。如工程建设、飞机厂、造船厂、重型机器厂等。
车间整体颜色选择
色彩的前后感
处在同一平面上的颜色,有的颜色使人感觉突出,有的颜色给人以退向后方的感觉。前者称前进色,后者称为后退色。由各种不同波长的色彩在人眼视网膜上的成像有前后,红、橙等光波长的色在内侧成像,感觉比较迫近;蓝、紫等光波短的色则在外侧成像,在同样距离内感觉就比较后退。实际上这是视错觉的一种现象,一般暖色、纯色、高明度色、强烈对比色、大面积色、集中色等有前进感觉,相反,冷色、浊色、低明度色、弱对比色、小面积色、分散色等有后退感觉。
设备设施布局
系统布置设计(Systematic Layout Planning )
P产品构成分析:
例:叉车产品分析
设备设施布局
系统布置设计(Systematic Layout Planning )
例:P—Q分析
设备设施布局
系统布置设计(Systematic Layout Planning )
在工业安全用色中,橙色表示危险,是警戒色。橙色非常明亮刺眼,如火车头,登山服装,背包,救生衣等。车间现场,橙色可用于安全警示标识,如安全帽、危险作业场所的工作服。
在工业安全用色中,黄色表示提醒注意。如交通号志上的黄灯,工程用的大型机器,学生用雨衣,雨鞋等,危险、保安设施。车间现场,黄色常被用作安全色,因为这极易被人发现,如室外作业的工作服,常用于警示标识,用于通道线、定置线。
图1 产品原则布置示意图
设备设施布局
(2)工艺布置原则(机群式)把同类型的设备和人员集中布置在一个地方。
图4 工艺原则布置示意图
设备设施布局
(3)固定式布置原则(项目布置)主要是工程项目和大型产品生产采用的一种布置形式。 它的加工对象位置,生产工人和设备都随加工产品所在的某一位置而转移。如工程建设、飞机厂、造船厂、重型机器厂等。
车间整体颜色选择
色彩的前后感
处在同一平面上的颜色,有的颜色使人感觉突出,有的颜色给人以退向后方的感觉。前者称前进色,后者称为后退色。由各种不同波长的色彩在人眼视网膜上的成像有前后,红、橙等光波长的色在内侧成像,感觉比较迫近;蓝、紫等光波短的色则在外侧成像,在同样距离内感觉就比较后退。实际上这是视错觉的一种现象,一般暖色、纯色、高明度色、强烈对比色、大面积色、集中色等有前进感觉,相反,冷色、浊色、低明度色、弱对比色、小面积色、分散色等有后退感觉。
生产线布局(超详细)
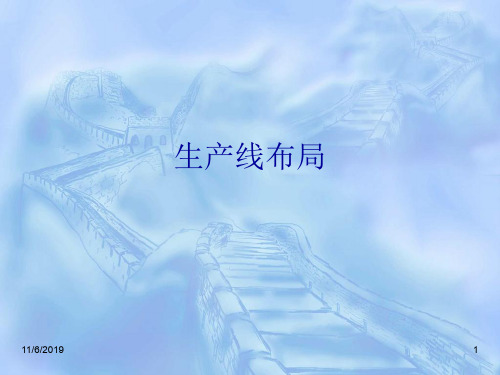
安装前轴车把手,拧紧螺丝
9
上紧全部螺丝
195
作业前提条件 ——
A B —— D C
C
E
E F,G,H,L
42
产品原则布局
解题 第一步:画出流程图
A
B
C
G
D
E
F
I
J
K
H
11/6/2019
43
产品原则布局
第二步:计算工作站周期(节拍) Ct=每天的工作时间/每天的产量 =60秒×420分钟/500辆
1. 采用了看板管理,拉动生产方式 2. 车间布局U型布局; 3. 不同类型的机器摆放在一块; 4. 实现了单件流的生产; 5. 机器小型化 ; 6. 工序中间很少甚至没有库存; 7. 实现了作业标准化; 8. 对工人实行了多技能培训; 9. 具有完善的作业改善活动制度
11/6/2019
3
看谁摘的果子最多!
• 大批量、同质性生产 • 产品需求足够稳定 • 流水作业
11/6/2019
38
产品原则布局
生产平衡规划
• 作业工序和生产线节拍趋于一致,使流动速度最快
步骤:
1. 用流程表明确作业先后关系
就生产而言Ct越大越
2. 工作站(工序)周期——生产节拍 好?还是越小越好?
Ct=每天的工作时间/每天的产量
1 1 2 3
的4
流5
动6
表7
8 11/6/2019
23 175 50
0
45 0 30 100 75 17 88
20
678 200 20 25 90 80 90 125 99 180 5 0 25 0 180 187
347 103 7
车间布局设计演示幻灯片

第2章 项目一:企业厂区与车间平面布局
第二章 项目一:企业厂区与车间平面设计
1
第2章 项目一:企业厂区与车间平面布局
项目一:企业厂区与车间平面设计
项目描述
工厂布局即是将工厂内的所有设备、工具、原料、工作台、附属设施(如工具室 、更衣室、厕所、升降机等)和各种作业(如仓储、品检、搬运等),依生产流程, 作一番适当的安排与布置,使工厂的生产活动能顺利而流畅。
5
第2章 项目一:企业厂区与车间平面布局
? 任务一:工商企业厂区平面布局设计及改善
相关知识 ? 工厂布局的目的 ? 工厂布局的原则 ? 工厂布局的类型
6
第2章 项目一:企业厂区与车间平面布局
利用最适当的配置方 法,以降低产品成本, 提高品质,并增强市 场竞销能力
促使工作环境更佳,安全卫生优良,员工满意而士气高昂; 使材料、半成品及成品的搬运距离最短,使产品制造成本因而降低; 使作业流程圆滑,合乎经济原则,使停顿现象减为最少; 有效利用工厂空间,除了考虑地面的利用外,亦应向空间发展; 提高开工率,使人机等待时间最少; 具有弹性,能适应各种生产条件的变化; 运用什么样的信息技术来实现物流动作的最大效率? 便于工厂管理活动的进行。
?产品的加工特性往往在很大程度上决定设施布置的 基本类型,生产运作管理人员一般只在基本类型选择 的基础上进行设施布置。
?考虑组织结构、各个部门的配置方式 。
30
第2章 项目一:企业厂区与车间平面布局
? 任务三:非工商企业单位部门与机构平面布局及改善
? 场景一
办公室布置 :
注意 事项:
力求使办公室有一个安静的工作环境 办公室应有良好的采光、照明条件
? 场景一
办公室布置 :
第二章 项目一:企业厂区与车间平面设计
1
第2章 项目一:企业厂区与车间平面布局
项目一:企业厂区与车间平面设计
项目描述
工厂布局即是将工厂内的所有设备、工具、原料、工作台、附属设施(如工具室 、更衣室、厕所、升降机等)和各种作业(如仓储、品检、搬运等),依生产流程, 作一番适当的安排与布置,使工厂的生产活动能顺利而流畅。
5
第2章 项目一:企业厂区与车间平面布局
? 任务一:工商企业厂区平面布局设计及改善
相关知识 ? 工厂布局的目的 ? 工厂布局的原则 ? 工厂布局的类型
6
第2章 项目一:企业厂区与车间平面布局
利用最适当的配置方 法,以降低产品成本, 提高品质,并增强市 场竞销能力
促使工作环境更佳,安全卫生优良,员工满意而士气高昂; 使材料、半成品及成品的搬运距离最短,使产品制造成本因而降低; 使作业流程圆滑,合乎经济原则,使停顿现象减为最少; 有效利用工厂空间,除了考虑地面的利用外,亦应向空间发展; 提高开工率,使人机等待时间最少; 具有弹性,能适应各种生产条件的变化; 运用什么样的信息技术来实现物流动作的最大效率? 便于工厂管理活动的进行。
?产品的加工特性往往在很大程度上决定设施布置的 基本类型,生产运作管理人员一般只在基本类型选择 的基础上进行设施布置。
?考虑组织结构、各个部门的配置方式 。
30
第2章 项目一:企业厂区与车间平面布局
? 任务三:非工商企业单位部门与机构平面布局及改善
? 场景一
办公室布置 :
注意 事项:
力求使办公室有一个安静的工作环境 办公室应有良好的采光、照明条件
? 场景一
办公室布置 :
生产线布局(超详细)【精品课件】.ppt
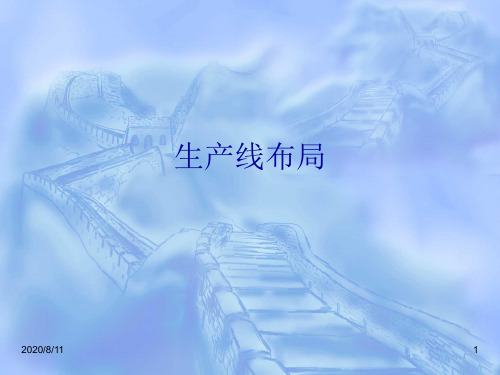
2020/8/11
12
鉴别七大浪费
六、来自工序不当的浪费
工作本身产生的浪费,当机器不正常运作而使操作人员 需要花额外时间,或当操作人员出于习惯或花了过多的 时间使清洁工作超过了规格的要求。
多余的检查也是过程浪费的另一个表现形式。
2020/8/11
13
鉴别七大浪费
七、不需要的动作的浪费
人们在工作设置中经常将工作中的动作搞混乱,实际做的动 作和工作要求的动作往往是不同的。
生产线布局
2020/8/11
1
精益生产五项基本原则
• 价值 (VALUE) : 决定于客户是否愿意为了它而付钱。
• 价值流 (VALUE STREAM) : 从产品设计到客户服务的所有
活动的描述和鉴别,都需要消除非增值活动。
• 流畅 (FLOW) : 消除所有工序的阻滞使价值流“流畅”而没有
中断。
作为一个确定的目的,工作是要作为一组精确的动作来考虑 的,哪些是增值的,那些是不增值的。
一个人在每天的恒定的工作中(例如一个很忙的人)可能实 际上只是很少一部分是增值工作。
工作中的不需要的动作被认为是浪费的,不增值的。
2020/8/11
14
生产布局前的准备工作
▪ 产能评估 ▪ 生产线顺流 ▪ 库存周转评估
1. 采用了看板管理,拉动生产方式 2. 车间布局U型布局; 3. 不同类型的机器摆放在一块; 4. 实现了单件流的生产; 5. 机器小型化 ; 6. 工序中间很少甚至没有库存; 7. 实现了作业标准化; 8. 对工人实行了多技能培训; 9. 具有完善的作业改善活动制度
2020/8/11
3
看谁摘的果子最多!
6
产生更严重的成本连锁反应……
车间生产线布局(不错)参考课件
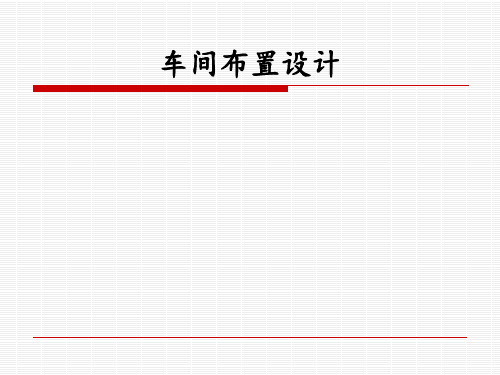
第五部分
车间布置设计 有关技术与参数
第五部分 车间布置设计的有关技术与参数
一、厂房的整体设计的有关参数
1、厂房的整体布置
集中式或分离式
第五部分 车间布置设计的有关技术与参数
设备露天化
优点
(1)节约建筑面积,节约建筑投资 ; (2)节约土建施工工程量; (3)将有毒物质的设备、具有火灾、爆炸危险的设备露 天或半露天化,可以节约厂房通风设备及动力,降低厂房 防火,防爆等级,降低生产费用和厂房造价; (4)对厂房的改建、扩建,增加灵活性。
第二部分 车间布置设计的原则
二、原则
5、车间布置应符合节约建设投资要求的原则 (1)可露天或半露天的设备,尽量采用半露天或露天设计; (2)厂房采用非高层化设计; (3)工艺管道集中布置,减少管线投资和节约能耗; (4)尽量采用一般的土建结构; (5)设备的操作面尽可能与通道安排在同一侧。
第二部分 车间布置设计的原则
二、车间布置设计的依据
5、土建资料和劳动安全、防火、防爆资料 6、车间组织及定员资料 7、厂区总平面布置,包括本车间与其它生产车间、辅助车 间、生活设施的相互联系,厂内人流物流的情况与数量。 8、有关布置方面的一些规范资料
三、工厂车间组成
1、工厂组成:生产车间、辅助车间、动力车间、仓库和堆 场部分、三废治理部分、厂前区行政福利部分 2、工厂生产车间的内部组成: 生产、辅助、生活等三部分 生产部分:原料工段、生产工段、成品工段、回收工段等 辅助部分:通风空调室、变电配电室、车间化验室、控制 室等 生活行政部分:其中包括车间办公室、会议室、更衣室、 休息室、浴室以及厕所等
第五部分 车间布置设计的有关技术与参数
设备露天化
可考虑使用露天布置设备
车间生产线布局ppt课件
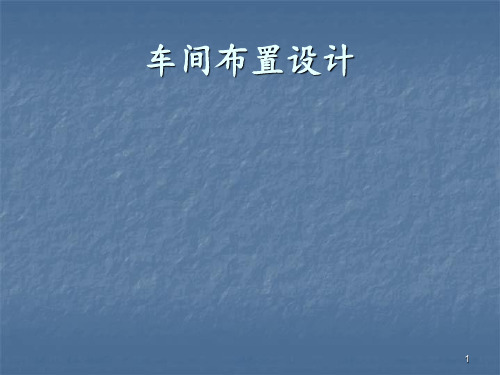
3
二、车间布置设计的依据
1、生产工艺流程图 2、物料衡算数据及物料性质、包括原料、半成品、成品、 副产品的数量及性质;三废的数量及处理方法 3、设备资料,包括设备外形尺寸、重量。支撑形式、保 温情况极其操作条件,设备一览表等 4、公用系统用量,供排水、供电、供热、冷冻、压缩空 气、外管资料等
4
二、车间布置设计的依据
第二部分 车间布置设计的原则
二、原则
6、车间布置应符合安全、卫生和防腐蚀的要求 (1)工厂车间卫生是正常生产的首要环节; (2)要为工人操作创造良好的安全卫生条件; (3)易燃易爆车间要考虑方便工人疏散和防火灭火措施; (4)凡产生腐蚀性介质的设备,其基础、设备周围地面、 墙、柱都要采取防护措施。
5、土建资料和劳动安全、防火、防爆资料 6、车间组织及定员资料 7、厂区总平面布置,包括本车间与其它生产车间、辅助车 间、生活设施的相互联系,厂内人流物流的情况与数量。 8、有关布置方面的一些规范资料
5
三、工厂车间组成
1、工厂组成:生产车间、辅助车间、动力车间、仓库和堆 场部分、三废治理部分、厂前区行政福利部分 2、工厂生产车间的内部组成: 生产、辅助、生活等三部分 生产部分:原料工段、生产工段、成品工段、回收工段等 辅助部分:通风空调室、变电配电室、车间化验室、控制 室等 生活行政部分:其中包括车间办公室、会议室、更衣室、 休息室、浴室以及厕所等
26
第五部分 车间布置设计的有关技术与参数
设备露天化
可考虑使用露天布置设备
(1)生产中不需要经常看管的设备,辅助设备,对气候 影响较小的设备。 (2)需要大气来调节温度、湿度的设备。 (3)不需要人工操作,高度自动化的设备 (4)气候温暖,无酷暑或严寒的地区。
27
二、车间布置设计的依据
1、生产工艺流程图 2、物料衡算数据及物料性质、包括原料、半成品、成品、 副产品的数量及性质;三废的数量及处理方法 3、设备资料,包括设备外形尺寸、重量。支撑形式、保 温情况极其操作条件,设备一览表等 4、公用系统用量,供排水、供电、供热、冷冻、压缩空 气、外管资料等
4
二、车间布置设计的依据
第二部分 车间布置设计的原则
二、原则
6、车间布置应符合安全、卫生和防腐蚀的要求 (1)工厂车间卫生是正常生产的首要环节; (2)要为工人操作创造良好的安全卫生条件; (3)易燃易爆车间要考虑方便工人疏散和防火灭火措施; (4)凡产生腐蚀性介质的设备,其基础、设备周围地面、 墙、柱都要采取防护措施。
5、土建资料和劳动安全、防火、防爆资料 6、车间组织及定员资料 7、厂区总平面布置,包括本车间与其它生产车间、辅助车 间、生活设施的相互联系,厂内人流物流的情况与数量。 8、有关布置方面的一些规范资料
5
三、工厂车间组成
1、工厂组成:生产车间、辅助车间、动力车间、仓库和堆 场部分、三废治理部分、厂前区行政福利部分 2、工厂生产车间的内部组成: 生产、辅助、生活等三部分 生产部分:原料工段、生产工段、成品工段、回收工段等 辅助部分:通风空调室、变电配电室、车间化验室、控制 室等 生活行政部分:其中包括车间办公室、会议室、更衣室、 休息室、浴室以及厕所等
26
第五部分 车间布置设计的有关技术与参数
设备露天化
可考虑使用露天布置设备
(1)生产中不需要经常看管的设备,辅助设备,对气候 影响较小的设备。 (2)需要大气来调节温度、湿度的设备。 (3)不需要人工操作,高度自动化的设备 (4)气候温暖,无酷暑或严寒的地区。
27
金桥冲压车间概况(PPT 31页)

拉深开裂:拉深力过大,超过材料拉深极限 拉深起皱:压边力不足,材料流动失稳 拉深凹陷:材料流动过快,板料塑性变形不足 凸点:下模型面上有细小垃圾 拉深划伤:上下模成型圆角粗糙,划伤板料 拉深印:上下模合模过程中,模具与板料相对运动痕迹
整车质量改进过程中对拉深模的更改:
对于外板零件,一般不对OP10拉深模进行改动。因为外板零件表面质量 要求很高,拉深模有极高的设计和制造要求,其型面经精密数控铣床加 工而成。而冲压车间现场修模主要是手工操作,拉深模维修后的表面质 量极难达到。
翻边、整形模 OP30
压料板
翻边、整形模的功能: 下模翻边镶块 将切好边的零件外边缘向内翻边并整形
上模翻边镶块
翻边、整形模的特点:
翻边也是冲压生产工艺中很重要的一序。翻边工艺主要决定零件的配合间隙, 因此,改进整车配合间隙需要冲压车间修模时,冲压会对翻边模进行更改。翻 边模主要由上下模翻边镶块、压料板组成。
整车质量改进过程中对切边模的更改: 通常,客户要求对零件翻边长度进行更改时,冲压需要对切边模进行更 改。 更改工艺:对上下模刀块进行焊接,打磨,研配和线上试模,另外需要 对上模压料板进行必要的打磨,消除上模刀口与压料板的干涉。
22
冲压生产工艺 Press Production Process
11
冲压生产工艺 Press Production Process
冲压生产主要是利用冲压设备和模具实现对金属材料(板材)的加工过程。 所以冲压加工具有如下特点:
(1) 生产率高、操作简单、容易实现机械化和自动化,特别适合于成批大量生产; (2) 冲压零件表面光洁,尺寸精度稳定,互换性好,成本低廉; (3) 在材料消耗不多的情况下,可以获得强度高、刚度大、而重量小的零件; (4) 可得到其他加工方法难以加工或无法加工的复杂形状零件。 SGM金桥冲压车间作为公司两大冲压生产基地之一,主要生产Buick和Cadillac系列 车型的冲压覆盖件。
整车质量改进过程中对拉深模的更改:
对于外板零件,一般不对OP10拉深模进行改动。因为外板零件表面质量 要求很高,拉深模有极高的设计和制造要求,其型面经精密数控铣床加 工而成。而冲压车间现场修模主要是手工操作,拉深模维修后的表面质 量极难达到。
翻边、整形模 OP30
压料板
翻边、整形模的功能: 下模翻边镶块 将切好边的零件外边缘向内翻边并整形
上模翻边镶块
翻边、整形模的特点:
翻边也是冲压生产工艺中很重要的一序。翻边工艺主要决定零件的配合间隙, 因此,改进整车配合间隙需要冲压车间修模时,冲压会对翻边模进行更改。翻 边模主要由上下模翻边镶块、压料板组成。
整车质量改进过程中对切边模的更改: 通常,客户要求对零件翻边长度进行更改时,冲压需要对切边模进行更 改。 更改工艺:对上下模刀块进行焊接,打磨,研配和线上试模,另外需要 对上模压料板进行必要的打磨,消除上模刀口与压料板的干涉。
22
冲压生产工艺 Press Production Process
11
冲压生产工艺 Press Production Process
冲压生产主要是利用冲压设备和模具实现对金属材料(板材)的加工过程。 所以冲压加工具有如下特点:
(1) 生产率高、操作简单、容易实现机械化和自动化,特别适合于成批大量生产; (2) 冲压零件表面光洁,尺寸精度稳定,互换性好,成本低廉; (3) 在材料消耗不多的情况下,可以获得强度高、刚度大、而重量小的零件; (4) 可得到其他加工方法难以加工或无法加工的复杂形状零件。 SGM金桥冲压车间作为公司两大冲压生产基地之一,主要生产Buick和Cadillac系列 车型的冲压覆盖件。
线平衡和生产线布局概述(PPT 31页)

PRESENTATION TITLE FOOTER 3/24/2020
17
平衡改善法则及注意事项
3. 生产线平衡步骤:
计算节拍时间(Takt time) 测量周期时间(CT=Cycle Time) 确定理论工位数
PRESENTATION TITLE FOOTER 3/24/2020
18
平衡改善法则及注意事项
时
業
间
改
作 业 时 间
善
工序 1 2 3 4 5 工序
23
PRESENTATION TITLE FOOTER 3/24/2020
14
平衡改善法则及注意事项
并行作业,增加人员
1人
作业 作
业
作
时
业
间
时
2人
间
作业
拆解去除
工序 1 2 3 4 5
工序 1 2 3 4 5
PRESENTATION TITLE FOOTER 3/24/2020
④ 空间浪费
缓冲库存的存放设施、存放空间浪费。
PRESENTATION TITLE FOOTER 3/24/2020
25
“传统”输送带和“成长型”输送带
成长型输送带作业
①②
③
④ ⑤
①边送边做 在输送带上完 成装配工作, 消除搬运浪费
②划分节距线 一般为80~ 90cm,用来 确认进度。
③依产距时间 设定速度 产距时间缩短 时,增加工作 站、工作人员 和提高输送带 速度。
问题: 理论上的最少工位数是多少?
Answer:
理论最少工位数, Nt 产品周期时间
Nt = 节拍时间
Nt=55.秒 4 9 .5秒 /个=[9.人 2]取整 10 人
生产线布局(超详细)_图文
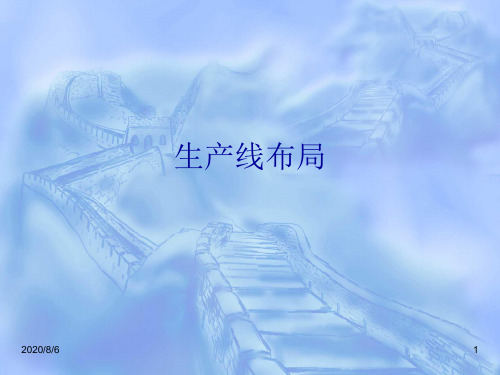
2020/8/6
次数
1 1 2 3 4 5 6 7 8
23 175 50
0
45 0 30 100 75 17 88
20
678 200 20 25 90 80 90 125 99 180 5 0 25 0 180 187
347 103 7
21
▪ 玩具厂各车间年物流成本示意图
2020/8/6
22
工艺原则布局
2020/8/6
12
鉴别七大浪费
六、来自工序不当的浪费
工作本身产生的浪费,当机器不正常运作而使操作人员 需要花额外时间,或当操作人员出于习惯或花了过多的 时间使清洁工作超过了规格的要求。
多余的检查也是过程浪费的另一个表现形式。
2020/8/6
13
鉴别七大浪费
七、不需要的动作的浪费
人们在工作设置中经常将工作中的动作搞混乱,实际做的动 作和工作要求的动作往往是不同的。
2020/8/6
15
生产线布局类别
▪ 定位原则布局 ▪ 工艺原则布局 ▪ 产品原则布局 ▪ 成组技术(单元式)布局
2020/8/6
16
定位原则布局
▪ 定义:
• 将原材料和设备按照使用次序和移动的难易程度 在产品的四周进行生产
▪ 起源
• 19世纪初亨利福特的汽车装配线
2020/8/6
17
定位原则布局
2020/8/6
9
不合格品
率高
库
机器故障率高
调整时间太长
存
水
设备能力不平衡
缺勤率高
备件供应不及时
平
采购周期太长 技术服务 工人技能差 后勤服务差
不及时
图 17-1 库存水平高掩盖的管理问题多
次数
1 1 2 3 4 5 6 7 8
23 175 50
0
45 0 30 100 75 17 88
20
678 200 20 25 90 80 90 125 99 180 5 0 25 0 180 187
347 103 7
21
▪ 玩具厂各车间年物流成本示意图
2020/8/6
22
工艺原则布局
2020/8/6
12
鉴别七大浪费
六、来自工序不当的浪费
工作本身产生的浪费,当机器不正常运作而使操作人员 需要花额外时间,或当操作人员出于习惯或花了过多的 时间使清洁工作超过了规格的要求。
多余的检查也是过程浪费的另一个表现形式。
2020/8/6
13
鉴别七大浪费
七、不需要的动作的浪费
人们在工作设置中经常将工作中的动作搞混乱,实际做的动 作和工作要求的动作往往是不同的。
2020/8/6
15
生产线布局类别
▪ 定位原则布局 ▪ 工艺原则布局 ▪ 产品原则布局 ▪ 成组技术(单元式)布局
2020/8/6
16
定位原则布局
▪ 定义:
• 将原材料和设备按照使用次序和移动的难易程度 在产品的四周进行生产
▪ 起源
• 19世纪初亨利福特的汽车装配线
2020/8/6
17
定位原则布局
2020/8/6
9
不合格品
率高
库
机器故障率高
调整时间太长
存
水
设备能力不平衡
缺勤率高
备件供应不及时
平
采购周期太长 技术服务 工人技能差 后勤服务差
不及时
图 17-1 库存水平高掩盖的管理问题多
生产线布局(超详细)PPT课件
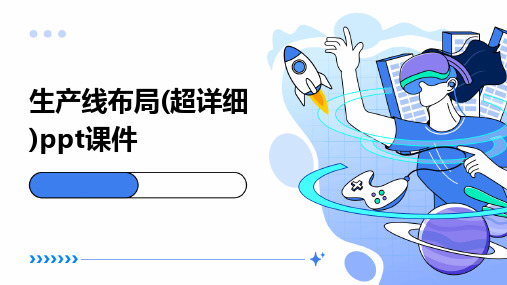
产品特性
产品的工艺要求、生产流程、 物料特性等对生产线布局有直 接影响。
人力资源
员工的技能、经验和工作习惯 对生产线布局的效率和效果有 重要影响。
环境因素
生产环境的要求、法律法规、 环保要求等对生产线布局有制 约作用。
02
生产线布局的类型
直线式布局
总结词
简单明了,便于管理,适合小批量生产
详细描述
布局评估的方法
01
02
03
04
生产流程分析
通过分析生产流程,评估生产 线布局的合理性,找出瓶颈环
节和浪费。
设备利用率评估
计算设备的平均利用率,判断 是否存在设备闲置或使用不足
的情况。
空间利用率评估
评估生产线布局的空间利用率 ,判断是否充分利用了生产空
间。
物流效率评估
分析生产线上的物流效率,判 断是否存在物料搬运距离过长
收集生产线布局相关 的数据,包括设备布 局、设备参数、生产 流程、物流路径等。
分析问题
根据收集的数据,分 析生产线布局存在的 问题和瓶颈环节。
制定方案
根据问题分析结果, 制定相应的布局调整 方案。
实施调整
按照制定的方案,逐 步实施生产线布局的 调整。
效果评估
在布局调整后,对生 产线的运行情况进行 评估,判断调整效果。
详细描述
该电子产品制造企业采用精益的生产线布局,以提高生产效率和降低成本。生产线布局 高效,各工序之间衔接紧密,以减少浪费。同时,大量采用自动
总结词
安全、卫生、人性化
VS
详细描述
该食品加工企业注重生产线的安全性、卫 生和人性化设计。生产线布局合理,保证 清洁度和卫生标准。同时,充分考虑员工 操作的舒适性和安全性,提高生产效率和 工作质量。
产线流水线排线技巧PPT课件
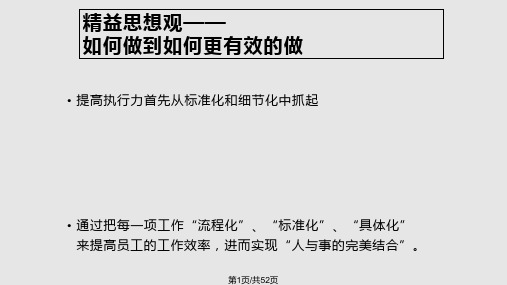
第10页/共52页
• 通过以上案例可知:科学合理的方法才是生 产
效率值稳定的有效保证。因而,产品生产前, 我
们需要分析和设计好方法及生产排列,才能真 正
第11页/共52页
标准化的最直接的体现即在于生产作业方式,即生产 作业技巧、生产作业流程和产能。而这一切,最直接的 方式就是将其应用到实际中去,通过生产排线,将产品 导入到生产线上,进而生产执行,从而实现标准化作业。
增加,以便提高生产效率。
第34页/共52页
讨论 1、新机型,且从未生产的产品如何去评估生产产能? 2、首次大货生产的机型,在生产时我们该怎么做? 3、如何更高效的评估生产所需工时?
第35页/共52页
第36页/共52页
流水线在线改善-动作浪费
第37页/共52页
流水线在线改善-设备浪费
设备故障浪费 转换调试准备浪费 点点停的浪费 制造不良与维修的浪费 速度低下浪费 启动浪费 夹具模具浪费 品质故障浪费 物流慢浪费
• 1、了解此产品之产品结构,熟悉其生产流程; • 2、各工序之操作方法了解及操作; • 3、生产流程的合理性; • 4、所需工装夹具及使用状况; • 5、产线人员之技术装备状况; • 6、排拉所需要的资料之第装25备页状/共5况2页;
如下为某一产品生产状况
第26页/共52页
• 产品周期时间 • 周期时间(C)计算公式
第35动作浪费第37流水线在线改善设备浪费第38动作范围基准手在横向位置的最适范围适合作业区域指臂画半圆的范围应该用更加靠近最适作业区域下的标准作业来设定作业布局图第41下限位置手往下伸时手掌落到臀部时手所处的高度为下限不弯腰作业状态第42上限位置手抬高时与手臂与肩膀同高的位置为上限位置第43物料工具放置点产品组装点操作者手的位置形成的三角形的边长越小越好
• 通过以上案例可知:科学合理的方法才是生 产
效率值稳定的有效保证。因而,产品生产前, 我
们需要分析和设计好方法及生产排列,才能真 正
第11页/共52页
标准化的最直接的体现即在于生产作业方式,即生产 作业技巧、生产作业流程和产能。而这一切,最直接的 方式就是将其应用到实际中去,通过生产排线,将产品 导入到生产线上,进而生产执行,从而实现标准化作业。
增加,以便提高生产效率。
第34页/共52页
讨论 1、新机型,且从未生产的产品如何去评估生产产能? 2、首次大货生产的机型,在生产时我们该怎么做? 3、如何更高效的评估生产所需工时?
第35页/共52页
第36页/共52页
流水线在线改善-动作浪费
第37页/共52页
流水线在线改善-设备浪费
设备故障浪费 转换调试准备浪费 点点停的浪费 制造不良与维修的浪费 速度低下浪费 启动浪费 夹具模具浪费 品质故障浪费 物流慢浪费
• 1、了解此产品之产品结构,熟悉其生产流程; • 2、各工序之操作方法了解及操作; • 3、生产流程的合理性; • 4、所需工装夹具及使用状况; • 5、产线人员之技术装备状况; • 6、排拉所需要的资料之第装25备页状/共5况2页;
如下为某一产品生产状况
第26页/共52页
• 产品周期时间 • 周期时间(C)计算公式
第35动作浪费第37流水线在线改善设备浪费第38动作范围基准手在横向位置的最适范围适合作业区域指臂画半圆的范围应该用更加靠近最适作业区域下的标准作业来设定作业布局图第41下限位置手往下伸时手掌落到臀部时手所处的高度为下限不弯腰作业状态第42上限位置手抬高时与手臂与肩膀同高的位置为上限位置第43物料工具放置点产品组装点操作者手的位置形成的三角形的边长越小越好
生产车间布局图培训资料
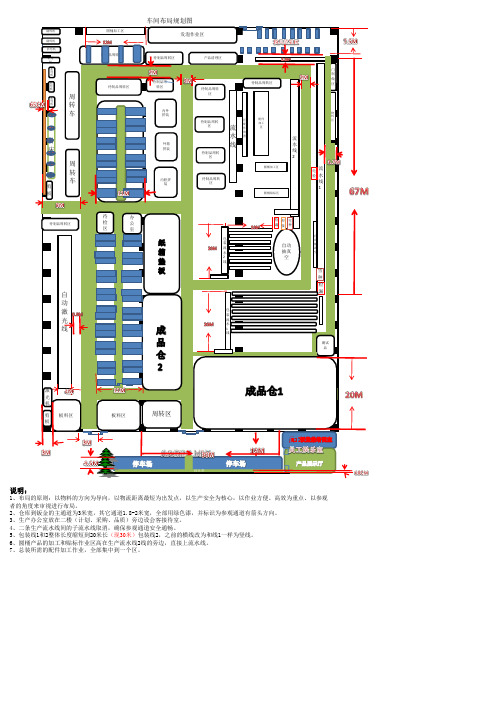
碰焊机
碰焊机
折弯机
折弯 机
折 弯 机
折 弯 机
折
周
弯 机
转
车
冲 床
周 转 车
剪 板
待制品周转区
自 动 激 光 线
圆桶加工区
车间布局规划图
发泡作业区
待制品周转区
待制品周转区
待制品周转区
待制品周 转区
内外 拼装
外箱加工 区
外箱 拼装
内胆拼 装
产品清理区
门
制
做
待制品周转区
区
待制品周转 区
物
料
待制品周转 区
区
流配 件
配件 加工 区
放
水置
流
线
水
待制品周转
线
区
2
圆桶加工区
待制品周转 区
圆桶贴标区
物 料 区
电流 检水
线 1
待
办
检
公
区
室
检焊 雪 漏接 种
包
自 动
装 流
自动
抽
真
水
抽真
空
2
空
线
雪 种
检 漏
包 装 流 水
1 线
成品
测试 品
激 光 机
剪 板料区 板
板料区
周转区
绿化带
说明:
1、布局的原则:以物料的方向为导向,以物流距离最短为出发点,以生产安全为核心,以作业方便、高效为重点、以参观 者的角度来审视进行布局。 2、仓库到钣金的主通道为3米宽,其它通道1.8-2米宽,全部用绿色漆,并标识为参观通道有箭头方向。 3、生产办公室放在二楼(计划、采购、品质)旁边设会客接待室。 4、二条生产流水线间的子流水线取消,确保参观通道安全通畅。 5、包装线1和2整体长度缩短到20米长(现30米)包装线2,之前的横线改为和线1一样为竖线。 6、圆桶产品的加工和贴标作业区高在生产流水线2线的旁边,直接上流水线。 7、总装所需的配件加工作业,全部集中到一个区。
碰焊机
折弯机
折弯 机
折 弯 机
折 弯 机
折
周
弯 机
转
车
冲 床
周 转 车
剪 板
待制品周转区
自 动 激 光 线
圆桶加工区
车间布局规划图
发泡作业区
待制品周转区
待制品周转区
待制品周转区
待制品周 转区
内外 拼装
外箱加工 区
外箱 拼装
内胆拼 装
产品清理区
门
制
做
待制品周转区
区
待制品周转 区
物
料
待制品周转 区
区
流配 件
配件 加工 区
放
水置
流
线
水
待制品周转
线
区
2
圆桶加工区
待制品周转 区
圆桶贴标区
物 料 区
电流 检水
线 1
待
办
检
公
区
室
检焊 雪 漏接 种
包
自 动
装 流
自动
抽
真
水
抽真
空
2
空
线
雪 种
检 漏
包 装 流 水
1 线
成品
测试 品
激 光 机
剪 板料区 板
板料区
周转区
绿化带
说明:
1、布局的原则:以物料的方向为导向,以物流距离最短为出发点,以生产安全为核心,以作业方便、高效为重点、以参观 者的角度来审视进行布局。 2、仓库到钣金的主通道为3米宽,其它通道1.8-2米宽,全部用绿色漆,并标识为参观通道有箭头方向。 3、生产办公室放在二楼(计划、采购、品质)旁边设会客接待室。 4、二条生产流水线间的子流水线取消,确保参观通道安全通畅。 5、包装线1和2整体长度缩短到20米长(现30米)包装线2,之前的横线改为和线1一样为竖线。 6、圆桶产品的加工和贴标作业区高在生产流水线2线的旁边,直接上流水线。 7、总装所需的配件加工作业,全部集中到一个区。
车间平面布置PPT课件
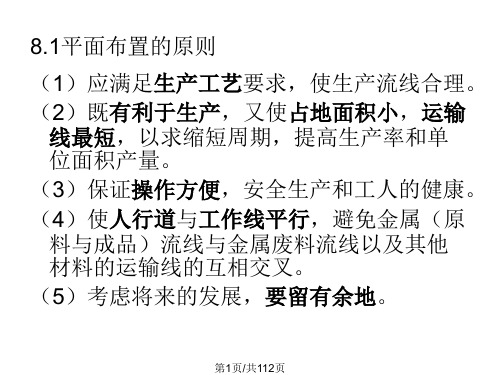
第28页/共112页
8.4 仓库面积计算
为了保证生产的连续性,车间内原料与 成品的存放,中间料的正常周转,在设计 时应留有一定的面积作为原料库、成品库 以及中间再制料的堆放场地,还有其他物 品的存放处。 1)确定仓库面积的原则 (a)必须保证正常生产,不至于由于某个 设备短期停车而造成其他设备的停工待料 现象。一般规定出各种不同用途仓库的存 放天数。
第1页/共112页
8.2 金属流程线的确定 金属流线指生产各类产品由原料到成品
的工艺流程线,把所选定的设备与设施布 置在相应工序的工艺流程线上,同时要考 虑中间的堆料场地以及运输等。
常用的金属流程线如图8-1所示。
第2页/共112页
第3页/共112页
1)直线式 从生产的连续性及运输等方面看是最合
对于顺列式轧机各机座间距离同样可按机列 间距离原则确定。而连轧机各机架间距离主要决 定于设备是否放得下,安装、换辊和检修方便, 以及特殊工艺要求。如图8-3所示。
第19页/共112页
第20页/共112页
轧机机列本身各设备间布置主要应考虑 两方面: (a)从人字齿轮到轧机机座之间距离主要 决定于连接轴的倾角,安装托架与升降台 应放得下。 (b)齿轮机座到减速机和减速机到主电机 距离应尽量近一些。但距离大小主要决定 于检修和安装方便。表8-2所列为中小型轧 机机架间的横向距离。可作参考。
2)原料仓库面积计算 通常原料仓库面积可用下式计算:
式中
F 24AnKt K1QH
A 设备(轧机和挤压机等)产量,吨/ 小时。 n 存放天数,天; Kt 金属投料量系数; Q 每立方米空间所能存放的原料重量,吨/ 米3; H 每堆原料的堆放高度,米; K1 仓库利用系数。
第31页/共112页
8.4 仓库面积计算
为了保证生产的连续性,车间内原料与 成品的存放,中间料的正常周转,在设计 时应留有一定的面积作为原料库、成品库 以及中间再制料的堆放场地,还有其他物 品的存放处。 1)确定仓库面积的原则 (a)必须保证正常生产,不至于由于某个 设备短期停车而造成其他设备的停工待料 现象。一般规定出各种不同用途仓库的存 放天数。
第1页/共112页
8.2 金属流程线的确定 金属流线指生产各类产品由原料到成品
的工艺流程线,把所选定的设备与设施布 置在相应工序的工艺流程线上,同时要考 虑中间的堆料场地以及运输等。
常用的金属流程线如图8-1所示。
第2页/共112页
第3页/共112页
1)直线式 从生产的连续性及运输等方面看是最合
对于顺列式轧机各机座间距离同样可按机列 间距离原则确定。而连轧机各机架间距离主要决 定于设备是否放得下,安装、换辊和检修方便, 以及特殊工艺要求。如图8-3所示。
第19页/共112页
第20页/共112页
轧机机列本身各设备间布置主要应考虑 两方面: (a)从人字齿轮到轧机机座之间距离主要 决定于连接轴的倾角,安装托架与升降台 应放得下。 (b)齿轮机座到减速机和减速机到主电机 距离应尽量近一些。但距离大小主要决定 于检修和安装方便。表8-2所列为中小型轧 机机架间的横向距离。可作参考。
2)原料仓库面积计算 通常原料仓库面积可用下式计算:
式中
F 24AnKt K1QH
A 设备(轧机和挤压机等)产量,吨/ 小时。 n 存放天数,天; Kt 金属投料量系数; Q 每立方米空间所能存放的原料重量,吨/ 米3; H 每堆原料的堆放高度,米; K1 仓库利用系数。
第31页/共112页