双馈电机英文文献
双馈式感应发电机(DFIG)说明

双馈式感应发电机(DFIG)简介大明双馈电机(或称为交流励磁电机),它早在四十年代就已经出现。
随着电力电子技术和数字控制技术的发展,双馈电机在电气性能方面所具有的一系列优点和巨大的潜力,已经引起国外的高度重视。
双馈式感应发电机(Doubly-Fed Induction Generator, DFIG) 使用绕线式转子,由于电力可经由转子侧之电力转换器双向流动,因此发电机馈入电力系统的界面同时包括定子侧(Line side)及转子侧(Rotor side),其电力转换器功率仅为发电机额定功率之20~30%,故成本较低,而且发电机可变速围可达同步转速之±30%,因此性能/价格比值最高,为目前大型风力发电机中最普遍采用之组态。
全球前10大风力发电机制造商的产品中有六成以上的变速风力发电机采用双馈式感应发电机,本文将介绍双馈式感应发电机的基本原理与特性。
一、双馈式感应发电机(DFIG)基本原理双馈式感应发电机(DFIG)是在同步发电机和异步发电机的基础上发展起来的一种新型发电机,其转子具有三相励磁绕组结构。
当通以某一频率(转差频率)的交流电时,就会产生一个相对转子旋转的磁场,转子的实际转速加上交流励磁产生的旋转磁场所对应的转速等于同步转速,则在电机气隙中形成一个同步旋转磁场,在定子侧感应出同步频率的感应电势。
从定子侧看,这与同步发电机直流励磁的转子以同步转速旋转时,在电机气隙中形成一个同步旋转的磁场是等效的。
双馈式感应发电机与一般感应发电机不同之处在于联接其转子侧之PWM脉宽调变电力转换器具有四象限之运转能力,电力转换器提供低频(转差频率)的交流电流(或电压)进行励磁,调节励磁电流(或电压)的幅值、频率、相位,来实现定子恒频恒压输出,其定子输出特性与同步发电机十分类似,所以有一些文献指出,双馈式感应发电机可以视为同步发电机与感应发电机之综合体。
从能量流动的特性来看,与采用直流励磁的同步发电机相比,同步发电机励磁的可调量只有直流励磁电流的幅值一个,所以同步发电机励磁一般只能对无效功率进行调节,而双馈式感应发电机,其励磁的可调量除了励磁电流的幅值外,还有励磁电流的频率和相位。
双馈式感应发电机(DFIG)说明
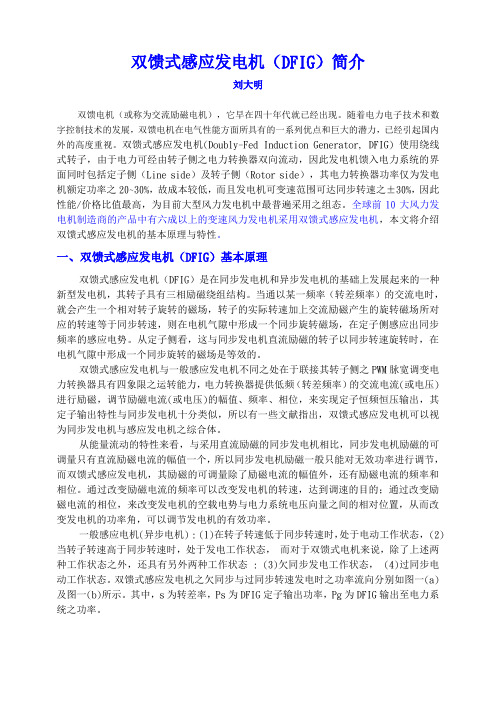
双馈式感应发电机(DFIG)简介刘大明双馈电机(或称为交流励磁电机),它早在四十年代就已经出现。
随着电力电子技术和数字控制技术的发展,双馈电机在电气性能方面所具有的一系列优点和巨大的潜力,已经引起国内外的高度重视。
双馈式感应发电机(Doubly-Fed Induction Generator, DFIG) 使用绕线式转子,由于电力可经由转子侧之电力转换器双向流动,因此发电机馈入电力系统的界面同时包括定子侧(Line side)及转子侧(Rotor side),其电力转换器功率仅为发电机额定功率之20~30%,故成本较低,而且发电机可变速范围可达同步转速之±30%,因此性能/价格比值最高,为目前大型风力发电机中最普遍采用之组态。
全球前10大风力发电机制造商的产品中有六成以上的变速风力发电机采用双馈式感应发电机,本文将介绍双馈式感应发电机的基本原理与特性。
一、双馈式感应发电机(DFIG)基本原理双馈式感应发电机(DFIG)是在同步发电机和异步发电机的基础上发展起来的一种新型发电机,其转子具有三相励磁绕组结构。
当通以某一频率(转差频率)的交流电时,就会产生一个相对转子旋转的磁场,转子的实际转速加上交流励磁产生的旋转磁场所对应的转速等于同步转速,则在电机气隙中形成一个同步旋转磁场,在定子侧感应出同步频率的感应电势。
从定子侧看,这与同步发电机直流励磁的转子以同步转速旋转时,在电机气隙中形成一个同步旋转的磁场是等效的。
双馈式感应发电机与一般感应发电机不同之处在于联接其转子侧之PWM脉宽调变电力转换器具有四象限之运转能力,电力转换器提供低频(转差频率)的交流电流(或电压)进行励磁,调节励磁电流(或电压)的幅值、频率、相位,来实现定子恒频恒压输出,其定子输出特性与同步发电机十分类似,所以有一些文献指出,双馈式感应发电机可以视为同步发电机与感应发电机之综合体。
从能量流动的特性来看,与采用直流励磁的同步发电机相比,同步发电机励磁的可调量只有直流励磁电流的幅值一个,所以同步发电机励磁一般只能对无效功率进行调节,而双馈式感应发电机,其励磁的可调量除了励磁电流的幅值外,还有励磁电流的频率和相位。
(完整版)电机学英文文献翻译

The three-phase induction motor speed control methodThree-phase asynchronous motor speed formula: N = 60f / p (1-s) Can be seen from the above formula, change the power supply frequency f, motor pole number p and the slip s may be too much to change the speed of purpose. From the speed of the essence of view, is simply a different way to change speed synchronous AC motor does not change the sync transfer speed or two.Widespread use in production machines without changing the synchronous speed of motor speed control method Wound Rotor Series Resistance Speed, chopper speed control, cascade control, and application of electromagnetic slip clutch, fluid couplings, clutches and other film speed. Change the synchronous speed of change on the number of stator pole multi-speed motor to change the stator voltage and frequency to frequency conversion with no change to the motor speed and so on.Energy from the speed point of view when, with high speed method and inefficient methods of two kinds of speed: high speed when the slip refers to the same, so no slip losses, such as multi-speed motors, Slip frequency control and loss can speed recovery methods (such as cascade control, etc.). A deteriorating loss of speed control methods are inefficient speed, such as series resistance of the rotor speed method, the energy loss in the rotor circuit on; Electromagnetic Clutch The speed method, the energy loss in the clutch coils; fluid coupling speed, energy loss in the fluid coupling of the oil. General deterioration in loss increased with the expansion speed range, if not speed range, the energy loss is minimal.1, variable speed control method of pole pairsThis speed is then used to change the stator winding way to change the red cage motor stator pole pairs to achieve speed control purposes, the followingfeaturesWith hard mechanical properties, good stability;No slip loss, high efficiency; Wiring simple, easy to control, low price;A level speed, differential large, can not get smooth speed control;With pressure and speed adjustment, with the use of electromagnetic slip clutch,smooth and efficient access to high speed characteristics.This method is suitable for the production does not require variable speed machinery, such as metal cutting machine Bed , Lift , Lifting equipment, Fans Water Pump And so on.2, Frequency Control Method Frequency control is to change the motor stator Power supply Frequency, thus changing the speed of its synchronous speed method. Frequency control system main equipment is to provide variable frequency power supply Inverter , Inverter can be divided into AC - DC - AC inverter and AC - AC converter two categories, most of the current domestic use of AC - DC - AC inverter. Its characteristicsHighefficiency, speed the process without additional loss;Wide range of applications, can be used for cage induction motor;Speed range, features a hard, high accuracy;Technical complexity, high cost, difficult maintenance and overhaul.This method is suitable for the high accuracy, good speed performance occasions.3, cascade control method Cascade control is wound into the rotor circuit in the series of additional potential can be adjusted to change the motor's slip, to achieve speed control purposes. Most of the deterioration in power to be in series with the added potential absorbed, re-use generate additional devices to absorb the deterioration in power to return power to use or conversion of energy. Slip-power absorption under way, cascade control can be divided into Motor Cascade control, mechanical and thyristor cascade control cascade control, and multi-use cascade control thyristor, characterized byCan speed the process of deterioration in loss of feedback to the network or productionmachinery, more efficient;Installed capacity and speed range in direct proportion to investment, applicable speed range 70% -90% rated speed of production machinery;peed device failure can switch to full speed, to avoid the cut-off;Thyristor cascade speed low power factor, harmonics greater impact.This method is suitable for fans, pumps and rolling mills, mine hoist, extrusion machines.4, wound rotor motor speed control method of Series ResistanceWound Rotor Motor additional resistance in series, so that the motor slip up, motor running at low speed. The greater the resistance in series, the motor speed is lower. This method is simple, easy to control, but deteriorate the power consumption in the form of heat in the resistor. Is a class speed, soft mechanical properties.5, the stator pressure and speed adjustment methodStator voltage when changing the motor, you can get a different set of mechanical properties of curves, which were different speeds. Since the motor torque and voltage proportional to the square, the largest decline in a lot of torque, speed range of its small cage motors in general and difficult to apply. In order to expand the speed range, pressure and speed adjustment should be larger rotor resistance value cage motors, such as dedicated voltage regulator with speed torque motor, or series wound motor frequency sensitive resistors. In order to expand the range of stable operation, when the speed of 2:1 or more occasions in the feedback control should be adopted to achieve the purpose of automatic adjustment of speed.Pressure and speed adjustment is a key device to provide power supply voltage, the current way of a tandem common saturation voltage regulator Reactor , Auto Transformer And several other Thyristor Surge. Thyristor Surge is the best way. Adjusting Speed featuresPressure and speed adjustment circuit is simple, easy to realize automatic control;Poor power surge process to heat transfer in the rotor resistance in the form of consumption, low efficiency.Pressure and speed adjustment generally applies to 100KW below production machinery.6.electromagnetic speed regulating motor speed control method of electromagneticspeed regulating electric motor squirrel cage motor, electric slip clutch and DC excitation power supply (Controller) consists of three parts. DC excitation power small, usually consisting of single phase half-wave or full wave rectifiers thyristors composition, change thyristor conduction angle, you can change the magnetizing current size.Electromagnetic slip clutch armature, poles and excitation windings composed of three parts. Armature and the latter has no mechanical contact, are free to rotate. Armature motor coaxial connection active part, driven by motors; docking with the load axis magnetic pole coupling from the moving parts. When the armature poles are at rest, such as excitation windings for DC, along the circumferential surface will form a number of air gap on the n, s, of alternating polarity poles, the magnetic flux through the armature. Dang electric armature with drag motor rotating Shi, due to electric armature and pole between relative movement, and makes electric armature induction produced Eddy, this Eddy and magnetic pass mutual role produced go moments, led has pole of rotor by same direction rotating, but its speed constant below electric armature of speed N1, this is a go difference adjustable speed way, changes go difference clutch device of DC Lai magnetic current, will can change clutch device of output go moments and speed. Characteristics of electromagnetic speed regulating motor speed:appliances, structure and control circuit is simple, reliable operation, easymaintenance; speed and smooth, stepless speed regulationthe power network harmonic effects;lost speed, low efficiency.This method applies to medium and small power, requires low speed when the smooth, short run production machinery.7. the hydraulic coupler speed regulating hydraulic Coupler is a device for hydraulic drive, is made up of the pump and turbine, they collectively work wheels, placed in a sealed case. Shell filled with a certain amount of working fluid, when pump is impulse driven by rotation, in which liquid propelled by blades which rotate, and under the action of centrifugal force along the outer wheels when entering the turbine pump, to thrust to the turbine blades on the same turn, make it drive production machinery running. Power transfer capacity of the hydraulic coupler and shell filled with fluid volume sizes are consistent. In the course of work, changing the filling rate can change the coupler of turbine speed, stepless speed regulation, characterized by:power scope, can meet the needs of from a couple of different power 10-kilowattto shuqianqian;simple structure, reliable performance, easy to operation and maintenance, andlow cost;small size, capacity;easy to adjust, easy to fulfill automatic control.This method applies to the speed of the fan and water pump.三相异步电动机的几种调速方式三相异步电动机转速公式为:n=60f/p(1-s)从上式可见,改变供电频率f、电动机的极对数p及转差率s均可太到改变转速的目的。
双馈风力发电机模型-翻译完毕

Vector Controlled Doubly Fed Induction Generator forWind ApplicationsDr. Ani Gole, Dept. of Electrical and Computer Eng., University of Manitoba.This document discusses the theory of operation behind the doubly fed generator case developed by Ani Gole (Univ. of Manitoba, Canada) and Om Nayak (Nayak Corporation, Princeton, NJ). The controller concept is based on the paper by Pena et al [1].Description of Rotor Current Generation Circuit (Generator PWM Converter and Controls)转子电流产生电路的描述(发电机脉宽调制转换器及其控制)The Doubly fed inductionpower output/input into the stator winding as well as the rotor winding of an induction machine with a wound rotor winding.双馈式感应发电机/电动机通过绕线转子绕组将功率输出/输入感应电INDUCTION GENERATOR13.8 kV, 500 HP机的定子绕组和转子绕组。
Using such a generator it is possible to get a good power factor even when the machine speed is quite different from synchronous speed. 使用这样发电机即使在机器转速完全不同于同步速度时也可以得到一个好的功率因数。
关于电动机的创作文献

关于电动机的创作文献英文回答:Electric Motors: A Comprehensive Overview.Electric motors are electromechanical devices that convert electrical energy into mechanical energy. They are widely used in a variety of applications, ranging from industrial machinery to consumer electronics.Principle of Operation.The basic principle of operation of an electric motor is electromagnetic induction. When an electric current flows through a coil of wire, it creates a magnetic field. If this magnetic field interacts with another magnetic field, it will cause the coil to rotate.Types of Electric Motors.There are many different types of electric motors, each with its own unique characteristics and applications. Some of the most common types include:DC motors: DC motors are powered by direct current (DC). They are relatively simple to operate and can provide a wide range of speeds and torques.AC motors: AC motors are powered by alternating current (AC). They are more efficient than DC motors and can operate at higher speeds.Synchronous motors: Synchronous motors rotate at a constant speed that is synchronized with the frequency of the AC power supply. They are used in applications where precise speed control is required.Induction motors: Induction motors are the most common type of AC motor. They are relatively simple to manufacture and can operate at a variety of speeds.Stepper motors: Stepper motors rotate in discretesteps. They are used in applications where precise positioning is required.Applications of Electric Motors.Electric motors are used in a wide variety of applications, including:Industrial machinery: Electric motors are used to power industrial machinery such as conveyors, pumps, and fans.Consumer electronics: Electric motors are used to power consumer electronics such as refrigerators, washing machines, and air conditioners.Transportation: Electric motors are used to power electric vehicles, such as cars, buses, and trains.Renewable energy: Electric motors are used to generate electricity from renewable energy sources, such as solar and wind power.Advantages of Electric Motors.Electric motors offer a number of advantages over other types of motors, including:High efficiency: Electric motors are very efficient at converting electrical energy into mechanical energy.Low maintenance: Electric motors require very little maintenance.Long lifespan: Electric motors have a long lifespan, especially when properly maintained.Quiet operation: Electric motors are relatively quiet in operation.Compact size: Electric motors are relatively compact in size, making them ideal for use in a variety of applications.Disadvantages of Electric Motors.Electric motors also have some disadvantages, including:High cost: Electric motors can be expensive topurchase and install.Limited torque: Electric motors can have limited torque, especially at low speeds.Heat generation: Electric motors generate heat when they operate, which can be a concern in some applications.Overall, electric motors are versatile and efficient devices that are used in a wide variety of applications. They offer a number of advantages over other types of motors, but they also have some disadvantages. Whenselecting an electric motor for a particular application,it is important to consider the specific requirements ofthe application and the advantages and disadvantages of different types of electric motors.中文回答:电动机,全面概述。
一篇电气专业英语文献与翻译

The Load Estimation and Power Tracking Integrated Control Strategy for Dual-Sides Controlled LCC Compensated WirelessCharging SystemABSTRACT In this paper, the wireless power transfer (WPT) system with dynamic loads such as batteries is studied comprehensively. An integrated control technology of load estimation and power tracking of LCC compensated is proposed, which realizes load estimation, mode judgment and charging control at the transmitter, and standard load setting and decoupling control at the receiver. Based on the inflfluence of reflflection impedance on the output current of the inverter, a method of identifying coupling coeffificient and equivalent load is proposed and a mathematical model is established. Receiver controller provides standard reference load for load estimation. Transmitter controller judges battery status according to the estimation of equivalent load and adopts double closed-loop control to regulate power and current. Receiver decouples control when battery charging voltage reaches the threshold, and providing mode conversion sign for transmitter controller to realize constant current (CC) and constant voltage (CV) charging of battery.The Dual-sides integrated control scheme has no data communication between transmitter and receiver, so it can control independently, which reduces the complexity of the system and is suitable for different charging modes. The proposed controller is more effificient as it maintains a track current, and dynamically alters the pick-up characteristics to suit the load demand. Finally, the simulation and experimental results validate the feasibility of proposed control method, which realizes the estimation of the load and CC/CV charging of the battery. The proposed WPT system achieved the effificiency at 91.16% while delivering 2 kW to the load with a vertical air gap of 150 mm.INDEX TERMS Wireless power transfer, integrated control, load estimation, constant current/voltage charging, LCC compensation, phase shift control.Wireless Power Transmission (WPT) or Contactless Power Transmission (CPT) achieves the power transmission without physical connection, which makes up for the shortcomings of traditional power transmission methods . Wireless charging will promote the development of electric vehicles (EVs), because it provides more convenient, reliable and safer charging options than conductive charging . There are many research fields in WPT for EVs, especially the WPT system is sensitive to coupling coefficient, air gap, resonant frequency, and load change, which makes it hard for There are many research fields in WPT for EVs, especially the WPT system issensitive to coupling coefficient, air gap,resonant frequency, and load change, which makes it hard for robust control, and most scholars focus on the steady state of the WPT systems .When the resonant frequency, position, parameters and load of the wireless charging system change, which result in a higher volt-ampere rating and lower power transfer efficiency. Therefore, resonant compensation is an important part at the transmitter and receiver of the system. Different compensation topologies have been proposed and implemented to tune the two coils working at a resonant frequency in a wide range of applications. there are four basic compensation topologies, namely Series-Series (SS), SeriesParallel (SP), Parallel-Series (PS) and Parallel-Parallel (PP),are widely adopted for EV applications.Many other novel compensation topologies are also used to improve the power transfer efficiency and to simplify the control of WPT systems. Literatures show that LCL topology and series LC topology are the commonly used primary compensation networks for WPT. Compared with series LC, LCL performs better in power conversion efficiency over the full range of coupling and loading imposed, and its constant current source characteristic make its closed-loop control implementation easier. More advantageous compensation topologies are put forward in . The double-sided LCC compensation topology is outstanding since not only is its resonant frequency independent of coupling coefficient and load condition, but also its advantages of facilitating zero voltage switch (ZVS) or zero current switch (ZCS) of the inverter, realize CC charging at zero phase angle (ZPA) condition, increasing lateral misalignment tolerance, and improving WPT efficiency have been demonstrated.The other problem with WPT charger systems is implementing a charge process for EV batteries.Since batteries are considered to be varying loads during charging, the charge converter needs to regulate its output precisely to implement the constant current (CC) charge and constant voltage (CV) mode charge. Thus, meticulous control and tuning of the inverter is necessary since the load varies violently as the receive coil moves with the online EV.This adds to the control complexity and may reduce systematic reliability. In order to improve battery life and charging efficiency, it is necessary for a charger to provide accurate charge current and voltage through stable operations. In recent years, various control strategies have been studied to provide the required output currentorvoltagefortime-varyingloadsatdifferentcharging stages.The traditional control method is to use wireless communication to send the load state information to the transmitter controller to adjust the output power of the inverter to achieve CC/CV charging in . In order to simplify the control of an WPT charger system and avoid the above drawbacks of conventional control methods under wide variations of the load in implementing the CC/CV charge, some researchers have started to utilize the load-independent characteristics of the compensation topologies at their resonant frequencies proposes a design method which makes it possible to implement the CC/CV mode charge with minimum frequency variation during the entire charge process by using the load-independent characteristics of an WPT system under the ZPA condition without any additional switches. But, frequency variation may result in a bifurcation phenomenon,where the control ability and stability of the system are lost.In order to realize ZPA condition in the whole charging process, a switchablehybrid topology is proposed in [19], and [20]. CC and CV charging are realized in different compensation topologies. However, the addition of switches complicates the system, and changes in system parameters can also lead to instability.In[21], a new control technique was proposed, which only employs the controller at transmitting and and load identification approach to adjust charging voltage/current for SS and SP compensated WPT systems. The advantages are that dual-side wireless communication for real-time charging current/voltage adjustment is avoided as well as it is suitable for different charging modes. However, switching between two kinds of topologies is still needed. For the CC/CV charging control at constant frequency, some approaches employ a DC/DC converter to control the output current or voltage while the front-end converter operates at the resonant frequency to achieve the ZPA condition in [22] and [23]. However, this increases the component counts, losses and complexity. In [24], DC/DC converters are used for decoupling control rather than CC or CV charging.In [25]and [26], a single primary-side controller based on phase shift H-bridge inverter are proposed to adjust the charging current or charging voltage against various load, may make it hard for the High frequency inverter to achieve ZVS in full load range, especially with light load condition. Then, the primary-side control method that realizes CC/CV charging for battery is analyzed, which is the main contribution of this paper.The objective of this research is to study and develop a new integrated control strategy for load and power tracking that realizes CC/CV charging for LCC compensation through the double-loop controlled phase shift H-bridge inverter and load identification approach. The system adopts dual-side controller to avoid wireless communication, and the mathematical models of load estimation and mode judgment are derived by using the topological compensation characteristics of double-sided LCC. The working state of the battery is fed back to the transmitter controller by reflecting the impedance of the receiver, and the coupling coefficient of coils and load value are estimated.The transmitter judges the charging mode according to the estimated load, adjusts the output power of the inverter, and maintains CC/CV charging by phase-shifting control. In CC mode, the transmitter can transfer more power and prevents overloading. In CV mode, the output power can be adjusted according to the charging curve. The receiver control circuit adopts Buck-Boost structure. Different from the traditional impedance matching or CC/CV charging control mode, the receiver controller sets the standard reference value of load estimation control by impedance matching. Buck-Boost converter operates in switching mode during charging. When the charging voltage reaches the reference value, the switching action changes the reflection impedance and provides the mode conversion mark for the transmitter. Based on the feedback signal and the amount of transferred power, the controlling module continuously adjusts the transmitting coil current during the charging.The rest of the sections are organized as follows:Section II gives the system structure and basic theoretical analysis. Section III proposes the integrated control method of load estimation and power tracking, and then the double closed-loop PIcontroller of transmitter and receiver is designed. Section IV validates the proposed method with simulations and experiments.Finally,last section summarizes the conclusions drawn from the investigation.II. SYSTEM STRUCTURE AND THEORETICAL ANALYSISIn this section, the system structure and methodology for analyzing the WPT system are discussed. Then, basic output characteristics for LCC compensation are analyzed to propose the Integrated control method on the transmitting side and the receiving side.A.WIRELESS POWER TRANSMISSION SYSTEM TRUCTURE In this paper, the most widely used variable impedance load battery is taken as the research object.Charging characteristic curve of the battery is shown in Figure 1. Charging process includes CC/CV charging. In CC stage, the output power of the power supply increases with the increase of the battery terminal voltage, while the equivalent impedance of the battery increases with little change. In the CV stage, the charge current and power decrease,and the equivalent impedance of the battery increases rapidly.B. LOAD ESTIMATE AND MODEL RECOGNITION The transmitter controller measures Iinv to estimate the load and mutual inductance changes, and judges the working state of the receiver. The inverter operates at ZPA resonant frequency and the controller adjusts fro m 180◦ phase shift, which means that the minimum input voltage is applied to the transmitting coil. According to the requirement of the receiver, the power control unit uses phase shift control to adjust the It and VC to keep the CC and CV working modes at the receiver.The transmitter can control the power output according to the working mode of the receiver and the load demand. In order to achieve this function, the designed controller should be able to estimate mutual inductance and equivalent load, and then judge the charging mode of the receiving end. The control block diagram of load estimation and mode judgment strategy is shown in Figure 5. Where, Rx is the standard reference load of the receiver.CONCLUSION An integrated control method of load estimation and power tracking is proposed in this paper to achieve CC/CV charging.of LCC compensation WPT system. Firstly, through theoretical analysis, the LCC compensation topology can realize the charge of CC mode under ZPA condition, and get the relationship between the equivalent load and the current of the inverters. Then, a standard reference load is set at the receiver so that the transmitter can estimate the equivalent load by calculating the refection impedance and detecting the output current of the inverter. Finally, according to the estimated load value and the conversion mark given by the decoupling control of the receiver, the CC/CV charging for LCC compensation are realized by PI controlled phase shift full-bridge inverter. The simulation and experimental results validate the feasibility of the proposed control method for whole load changes. The proposed WPT system can achieve a high effenciency at 91.16% with a 20-cm air gap when delivering 0.2−2kW to the load in different charging stages.双边控制的LCC补偿型无线充电系统的负载估计与功率跟踪集成控制策略摘要本文对电池等动态负载下的无线电能传输(WPT)系统进行了全面的研究。
双馈风力发电机的控制策略研究英文参考文献

双馈风力发电机的控制策略研究英文参考文献A Review of Control Strategies for Doubly Fed Wind Turbine GeneratorsAbstract:With the escalating global demand for renewable energy sources and the urgent need to mitigate the impact of climate change, wind energy has emerged as a viable and sustainable alternative. Doubly fed wind turbine generators (DFIGs) have gained significant popularity due to their ability to operate at variable speeds and provide reactive power support to the grid. However, the efficient and reliable operation of DFIGs heavily relies on the implementation of effective control strategies. This paper presents a comprehensive review of control strategies for doubly fed wind turbine generators, highlighting the key advancements and challenges in this field.The paper begins with an introduction to doubly fed wind turbine generators, discussing their basic operational principles and the significance of control strategies inensuring optimal performance. It then delves into the various control techniques employed for DFIGs, including vector control, direct torque control, and model predictive control. Each of these techniques is analyzed in detail, discussing their advantages, limitations, and applicability in different scenarios.Furthermore, the paper explores the integration of modern control algorithms, such as artificial intelligence and machine learning techniques, into DFIG control strategies. These algorithms offer promising solutions for enhancing the performance and reliability of wind turbines by enabling adaptive control and predictive maintenance. The paper presents case studies and experimental results demonstrating the effectiveness of these advanced control techniques.Additionally, the review discusses the challenges faced in the control of doubly fed wind turbine generators, including grid integration issues, system stability concerns, and the impact of variable wind conditions. It also examines the potential of hybrid control strategies that combine multiple control techniques to address thesechallenges and enhance the overall performance of wind turbines.Finally, the paper concludes with a summary of the key findings and insights gained from the review. It also provides recommendations for future research directions in the field of doubly fed wind turbine generator control, emphasizing the need for further exploration of advanced control techniques and their integration into practical wind energy systems.By presenting a comprehensive overview of control strategies for doubly fed wind turbine generators, this paper aims to contribute to the ongoing efforts in promoting the efficient and sustainable utilization of wind energy resources. It provides valuable insights for researchers, engineers, and policymakers working in the field of renewable energy and power systems.(Note: This is a summary of a potential article, and the actual article would need to be expanded to meet the requirement of being at least 1000 words in length. The specific content and details would depend on the latestresearch and advancements in the field of doubly fed wind turbine generator control.)。
0引言双馈感应发电机(DFIG)也称为交流励磁发电

0引言双馈感应发电机(DFIG)也称为交流励磁发电机,它在结构上类似于绕线式感应电机,定子三相绕组接工频电网,通过静止变频器给转子绕组提供低频交流励磁,可实现发电机有功、无功和转速的独立调节。
该发电机具有良好的稳定性和较强的进相运行能力;具有原动机转速变化情况下实现定子恒频的特性,即变速恒频发电能力,在风力发电、抽水蓄能,提高电力系统稳定等领域有着广泛的前景,正逐步受到人们的关注和重视。
目前,已有不少文献应用矢量控制技术研究了双馈发电机的有功和无功解耦控制。
文献[1]采用基于气隙磁场定向的矢量控制技术,推导了双馈发电机稳态下的有功、无功解耦励磁控制模型,但由于在推导中忽略了定子漏阻抗和转子漏感的影响,往往带来励磁控制模型精度的下降。
文献[2-3]采用基于定子磁链定向的矢量控制技术,采用电流内环、功率外环的双环控制策略,实现了有功、无功的解耦控制,且控制的动态特性好。
文献[4]在双通道下建立了动态同步轴系的控制方程,实现了稳态解耦控制,文献[5]提出了简化的三阶模型。
文献[6]提出了一种基于电网电压定向的励磁控制策略,该策略仅需要定子侧的电流、电网电压和转子位置角信号,避免了矢量控制策略对定、转子量测量精度,实时性和一致性的严格要求,简化了控制系统。
本文主要结合文献[7-8]中提出的直接功率控制策略对双馈发电机进行了理论和仿真研究,建立了单机与无穷大系统相连的双馈发电机的数学模型,并在此数学模型上运用直接功率控制策略进行了仿真研究。
1双馈发电机数学模型[9-10]发电机与无穷大系统相连的模型如图1所示。
双馈感应发电机的直接功率控制策略张俊峰1,毛承雄1,陆继明1,吴建东2(1.华中科技大学电气与电子工程学院,湖北武汉430074;2.东方电机控制股份有限公司,四川德阳618000)摘要:建立了单机与无穷大系统相连的双馈感应发电机(DFIG)数学模型,并以定子电压综合矢量恒定为控制约束,提出了一种双馈感应发电机的励磁控制策略。
电机学英文文献翻译
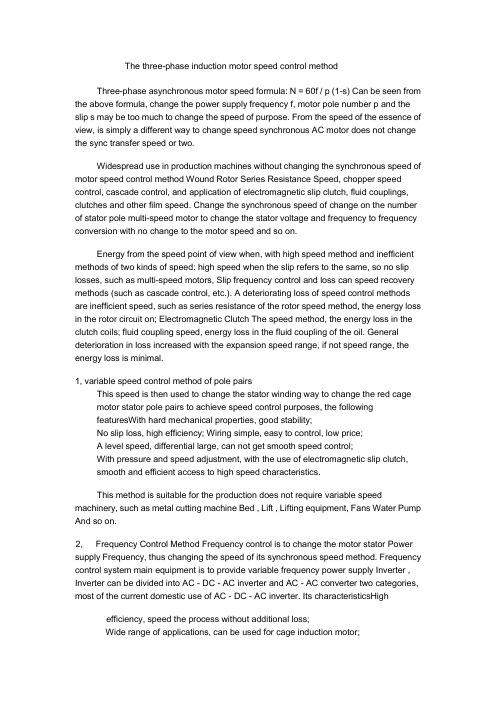
The three-phase induction motor speed control methodThree-phase asynchronous motor speed formula: N = 60f / p (1-s) Can be seen from the above formula, change the power supply frequency f, motor pole number p and the slip s may be too much to change the speed of purpose. From the speed of the essence of view, is simply a different way to change speed synchronous AC motor does not change the sync transfer speed or two.Widespread use in production machines without changing the synchronous speed of motor speed control method Wound Rotor Series Resistance Speed, chopper speed control, cascade control, and application of electromagnetic slip clutch, fluid couplings, clutches and other film speed. Change the synchronous speed of change on the number of stator pole multi-speed motor to change the stator voltage and frequency to frequency conversion with no change to the motor speed and so on.Energy from the speed point of view when, with high speed method and inefficient methods of two kinds of speed: high speed when the slip refers to the same, so no slip losses, such as multi-speed motors, Slip frequency control and loss can speed recovery methods (such as cascade control, etc.). A deteriorating loss of speed control methods are inefficient speed, such as series resistance of the rotor speed method, the energy loss in the rotor circuit on; Electromagnetic Clutch The speed method, the energy loss in the clutch coils; fluid coupling speed, energy loss in the fluid coupling of the oil. General deterioration in loss increased with the expansion speed range, if not speed range, the energy loss is minimal.1, variable speed control method of pole pairsThis speed is then used to change the stator winding way to change the red cage motor stator pole pairs to achieve speed control purposes, the followingfeaturesWith hard mechanical properties, good stability;No slip loss, high efficiency; Wiring simple, easy to control, low price;A level speed, differential large, can not get smooth speed control;With pressure and speed adjustment, with the use of electromagnetic slip clutch,smooth and efficient access to high speed characteristics.This method is suitable for the production does not require variable speed machinery, such as metal cutting machine Bed , Lift , Lifting equipment, Fans Water Pump And so on.2, Frequency Control Method Frequency control is to change the motor stator Power supply Frequency, thus changing the speed of its synchronous speed method. Frequency control system main equipment is to provide variable frequency power supply Inverter , Inverter can be divided into AC - DC - AC inverter and AC - AC converter two categories, most of the current domestic use of AC - DC - AC inverter. Its characteristicsHighefficiency, speed the process without additional loss;Wide range of applications, can be used for cage induction motor;Speed range, features a hard, high accuracy;Technical complexity, high cost, difficult maintenance and overhaul.This method is suitable for the high accuracy, good speed performance occasions.3, cascade control method Cascade control is wound into the rotor circuit in the series of additional potential can be adjusted to change the motor's slip, to achieve speed control purposes. Most of the deterioration in power to be in series with the added potential absorbed, re-use generate additional devices to absorb the deterioration in power to return power to use or conversion of energy. Slip-power absorption under way, cascade control can be divided into Motor Cascade control, mechanical and thyristor cascade control cascade control, and multi-use cascade control thyristor, characterized byCan speed the process of deterioration in loss of feedback to the network or productionmachinery, more efficient;Installed capacity and speed range in direct proportion to investment, applicable speed range 70% -90% rated speed of production machinery;peed device failure can switch to full speed, to avoid the cut-off;Thyristor cascade speed low power factor, harmonics greater impact.This method is suitable for fans, pumps and rolling mills, mine hoist, extrusion machines.4, wound rotor motor speed control method of Series ResistanceWound Rotor Motor additional resistance in series, so that the motor slip up, motor running at low speed. The greater the resistance in series, the motor speed is lower. This method is simple, easy to control, but deteriorate the power consumption in the form of heat in the resistor. Is a class speed, soft mechanical properties.5, the stator pressure and speed adjustment methodStator voltage when changing the motor, you can get a different set of mechanical properties of curves, which were different speeds. Since the motor torque and voltage proportional to the square, the largest decline in a lot of torque, speed range of its small cage motors in general and difficult to apply. In order to expand the speed range, pressure and speed adjustment should be larger rotor resistance value cage motors, such as dedicated voltage regulator with speed torque motor, or series wound motor frequency sensitive resistors. In order to expand the range of stable operation, when the speed of 2:1 or more occasions in the feedback control should be adopted to achieve the purpose of automatic adjustment of speed.Pressure and speed adjustment is a key device to provide power supply voltage, the current way of a tandem common saturation voltage regulator Reactor , Auto Transformer And several other Thyristor Surge. Thyristor Surge is the best way. Adjusting Speed featuresPressure and speed adjustment circuit is simple, easy to realize automatic control;Poor power surge process to heat transfer in the rotor resistance in the form of consumption, low efficiency.Pressure and speed adjustment generally applies to 100KW below production machinery.6.electromagnetic speed regulating motor speed control method of electromagneticspeed regulating electric motor squirrel cage motor, electric slip clutch and DC excitation power supply (Controller) consists of three parts. DC excitation power small, usually consisting of single phase half-wave or full wave rectifiers thyristors composition, change thyristor conduction angle, you can change the magnetizing current size.Electromagnetic slip clutch armature, poles and excitation windings composed of three parts. Armature and the latter has no mechanical contact, are free to rotate. Armature motor coaxial connection active part, driven by motors; docking with the load axis magnetic pole coupling from the moving parts. When the armature poles are at rest, such as excitation windings for DC, along the circumferential surface will form a number of air gap on the n, s, of alternating polarity poles, the magnetic flux through the armature. Dang electric armature with drag motor rotating Shi, due to electric armature and pole between relative movement, and makes electric armature induction produced Eddy, this Eddy and magnetic pass mutual role produced go moments, led has pole of rotor by same direction rotating, but its speed constant below electric armature of speed N1, this is a go difference adjustable speed way, changes go difference clutch device of DC Lai magnetic current, will can change clutch device of output go moments and speed. Characteristics of electromagnetic speed regulating motor speed:appliances, structure and control circuit is simple, reliable operation, easymaintenance; speed and smooth, stepless speed regulationthe power network harmonic effects;lost speed, low efficiency.This method applies to medium and small power, requires low speed when the smooth, short run production machinery.7. the hydraulic coupler speed regulating hydraulic Coupler is a device for hydraulic drive, is made up of the pump and turbine, they collectively work wheels, placed in a sealed case. Shell filled with a certain amount of working fluid, when pump is impulse driven by rotation, in which liquid propelled by blades which rotate, and under the action of centrifugal force along the outer wheels when entering the turbine pump, to thrust to the turbine blades on the same turn, make it drive production machinery running. Power transfer capacity of the hydraulic coupler and shell filled with fluid volume sizes are consistent. In the course of work, changing the filling rate can change the coupler of turbine speed, stepless speed regulation, characterized by:power scope, can meet the needs of from a couple of different power 10-kilowattto shuqianqian;simple structure, reliable performance, easy to operation and maintenance, andlow cost;small size, capacity;easy to adjust, easy to fulfill automatic control.This method applies to the speed of the fan and water pump.三相异步电动机的几种调速方式三相异步电动机转速公式为:n=60f/p(1-s)从上式可见,改变供电频率f、电动机的极对数p及转差率s均可太到改变转速的目的。
永磁和双馈比较-中英文

(Noise Level)
永磁直驱风机噪音更低
(Lower Noise Level for PMDD)
永磁直驱风机省去了齿轮箱,噪音低(The noise level is much lower due to the removal of the gearbox.)
效率
(Efficiency)
永磁直驱风机效率更高,发电效率平均提高5-10% (Higher Efficiency for PMDD with approximate 5-10% than Double Fed turbine)
双馈式风机支持齿轮箱工作,本身也耗电(There are much power loss on the operaiton of the gearbox for the double fed turbine)
运输难度(Transportation)
永磁直驱风机运输难度更大
( Difficulter than Double Fed for Transporation)
永磁直驱风机技术较新,电子化程度高(Adavanced technique and electronization for the PMDD)
相较于双馈式电机,永磁直驱风机更能适应低风速,且能耗较少、后续维护成本低.
So compare with the double fed turbine, PMDD is more suitable with the low speed area,the power loss and subsequent maintenance cost is much lower than double fed turbine.
永磁直驱风机要求更高
无刷双馈电机综述

无刷双馈电机的研究及应用前景*浙江大学电机及其控制研究所 (310027) 张彦锋 潘再平*浙江省自然科学基金资助项目【提要】无刷双馈电机(BDFM )是一种结构简单、坚固可靠、异同步通用的电机,可在无刷情况下实现双馈。
它具有功率因数可调、高效率的特点,可应用于调速系统和变速恒频发电系统中。
本文在系统研究国内外各有关文献的基础上,详细综述了BDFM 的发展历史、运行机理、分析方法、控制方式、研究现状及应用前景,对在我国开展BDFM 的研究有着积极的意义。
关键词 无刷 双馈电机 综述Review and Future Application of Brushless Doubly-Fed MachineZhang Yanfeng Pan Zaiping(Zhejiang University, Hangzhou 310027)Abstract Brushless doubly-fed machine (BDFM) is the electrical machine that incorporates the robustness of the squirrel cage induction machine and the speed and power factor control of the synchronous machine, which shows substantial potential in variable speed drives and variable speed constant frequency generating systems. This paper describes the developments, operation principle, dynamic models, control strategies and future applications of BDFM in detail. It will help a lot to study BDFM in China.Key Words: Brushless, doubly-fed machine, review1、引言无刷双馈电机(简称BDFM)是由串级感应电机发展而来。
双馈异步电动机的工作原理

双馈异步电动机的工作原理英文回答:The working principle of a doubly-fed asynchronous motor, also known as a double-fed induction motor or wound rotor induction motor, is based on the concept of slip.This type of motor has two sets of windings on the stator, namely the main winding and the auxiliary winding. The main winding is connected directly to the power supply, whilethe auxiliary winding is connected to the rotor throughslip rings and brushes.When the motor is started, the main winding is energized, creating a rotating magnetic field in the stator. The rotor windings are short-circuited through the slip rings, allowing current to flow through them. As a result,a magnetic field is induced in the rotor, which interacts with the rotating magnetic field of the stator. This interaction causes the rotor to start rotating in the same direction as the stator magnetic field.The unique feature of a doubly-fed asynchronous motor is that the rotor windings are not directly connected to the power supply. Instead, they are connected through external resistors and slip rings. By adjusting the resistance in the rotor circuit, the speed and torque characteristics of the motor can be controlled.One advantage of this design is that it allows for variable speed operation without the need for complex electronic control systems. By changing the resistance in the rotor circuit, the slip of the rotor can be adjusted, which in turn affects the speed of the motor. This makes doubly-fed asynchronous motors suitable for applications where variable speed control is required, such as in wind turbines and conveyor belts.Another advantage is the ability to provide reactive power to the power grid. In a traditional induction motor, the reactive power is supplied entirely by the power grid. However, in a doubly-fed asynchronous motor, the rotor windings can absorb or generate reactive power, dependingon the operating conditions. This capability isparticularly useful in applications where the power grid is weak or unstable.In summary, the working principle of a doubly-fed asynchronous motor is based on slip and the interaction between the stator and rotor magnetic fields. By adjusting the resistance in the rotor circuit, the speed and torque characteristics of the motor can be controlled. This design allows for variable speed operation and the ability to provide reactive power to the power grid.中文回答:双馈异步电动机,也称为双馈感应电动机或绕线转子感应电动机,其工作原理基于滑差的概念。
电机工程学报英文摘要范文

电机工程学报英文摘要范文Electric motors are the backbone of modern industry, powering a vast array of applications from household appliances to heavy industrial machinery. As the world becomes increasingly reliant on electricity and automated systems, the field of electric motor engineering has grown in both complexity and importance. The design, development, and optimization of electric motors are critical to ensuring the efficiency, reliability, and performance of a wide range of products and systems.At the heart of electric motor engineering is the fundamental understanding of electromagnetic principles and their application to the conversion of electrical energy into mechanical energy. This involves the study of the interaction between magnetic fields, electric currents, and the physical components of the motor, such as the rotor, stator, and windings. Engineers in this field must possess a deep knowledge of topics like electromagnetism, materials science, heat transfer, and mechanical design in order to create motors that are both powerful and efficient.One of the key challenges in electric motor engineering is the need to balance competing design requirements. For example, a motor that is optimized for high torque output may not be as efficient as one designed for maximum power density. Similarly, a motor that is engineered for low cost may sacrifice some performance characteristics. Navigating these trade-offs requires a thorough understanding of the underlying physics and the ability to apply advanced analytical and computational techniques.Another important aspect of electric motor engineering is the development of control systems and power electronics. The precise control of motor speed, torque, and efficiency is essential for many applications, from industrial automation to electric vehicles. This involves the design of control algorithms, power converters, and other electronic components that can precisely regulate the flow of electrical power to the motor.In recent years, the field of electric motor engineering has also been shaped by the growing emphasis on energy efficiency and sustainability. As concerns about climate change and resource scarcity have heightened, there has been a concerted effort to develop motors that are more energy-efficient, use fewer rare-earth materials, and have a lower environmental impact. This has led to advancements in areas such as permanent magnet design, high-efficiency winding configurations, and the use of advanced materialsand manufacturing techniques.The research and development of electric motors is an ongoing process, with engineers constantly pushing the boundaries of what is possible. From the development of high-performance motors for electric vehicles to the optimization of industrial motors for energy efficiency, the field of electric motor engineering plays a crucial role in shaping the technologies that power our modern world.In the pages of this journal, you will find a wealth of cutting-edge research and innovative solutions in the field of electric motor engineering. The papers presented here cover a diverse range of topics, from the fundamental principles of electromagnetism to the latest advancements in motor control and optimization. Whether you are a seasoned professional or a student just starting your journey in this exciting field, this journal is sure to provide valuable insights and inspiration.。
电机及其控制英文作文

电机及其控制英文作文英文:Electric motors are a crucial component in many industries, from manufacturing to transportation. They convert electrical energy into mechanical energy, allowing for the movement of machinery, vehicles, and other equipment. The control of electric motors is also important, as it allows for precise adjustments in speed and direction.There are various types of electric motors, includingAC motors, DC motors, and stepper motors. Each type has its own unique characteristics and applications. For example, AC motors are commonly used in household appliances, while DC motors are often used in electric vehicles. Stepper motors are used in applications that require precise control, such as 3D printers.The control of electric motors can be achieved through various methods, such as using a motor controller or avariable frequency drive. These devices allow for the adjustment of the motor's speed and direction, as well as providing protection against overloading and overheating.In my experience, I have worked with electric motors in the automotive industry. We used DC motors to powerelectric vehicles, and the control of these motors was crucial for the performance of the vehicle. We used a motor controller to adjust the speed and direction of the motor, and to ensure that it did not overheat or overload.Overall, electric motors and their control play a vital role in many industries, and understanding their operation and application is important for anyone working in these fields.中文:电动机是许多行业的关键组件,从制造业到交通运输。
2MW风力双馈异步电动机的研究设计 英中文资料

2MW风力双馈异步电动机的研究设计摘要:一个设计为一个2 MW风力发电机的商业,验证了两种连接方式为标准双馈异步机可延长低速下范围到80%滑动没有增加的额定功率电子变换器。
这远远超出了正常的30%的下限。
较低的速度连接被称作异步发电机模式和机器操作与短路定子绕组和所有的功率流在转子回路。
有两个回路逆变器控制系统方案设计和调整为每一个模式。
本文的目的是当前仿真结果,说明了该控制器的动态性能均为双馈异步发电机的连接方法为2 MW风力涡轮机。
一个简单的分析了双转子电压为连接方法包括作为这个演示的优势的时候,需要考虑设计等先进控制策略。
关键词:双馈电机、异步发电机、风力发电机1、介绍兴趣是持续风力涡轮机,尤其是那些拥有一个额定功率的许多兆瓦这个流行主要由既环保,也可用的化石燃料。
立法鼓励减少碳足迹的所谓的地方,所以目前正在感兴趣的可再生能源。
风力涡轮机仍然被看作是一种建立完善的技术,已形成从定速风力涡轮机,现在流行的调速技术基于双馈异步发电机(DFIGs)。
风力是一DFIG变速与转子变频器控制使转子电压相位和大小调整以保持最佳扭矩和必要的定子功率因数文[1]~[3]。
DFIG技术是目前发达,是常用的风力涡轮机。
定子的DFIG是直接连接到网格与电力电子转子变换器之间,用以转子绕组的网格。
这个变量速度范围是成正比的评级的转子等通过变频器调速范围±30%[4、5、6、7]转子转换器只需要的DFIG总量的30%的力量而使全面控制完整的发电机输出功率。
这可能导致显著的成本节省了转子转换器[4]。
滑动环连接,但必须保持转子绕组,性能安全可靠。
电源发电机速度特性,如图1所示为2 MWwind汽轮机。
对于一个商业发电机速度随风速,然而这种关系是为某一特定地点。
作为风速,并因此机速度快、输出功率下降了的风力发电机减少直至关闭时提取风是比损失的发电机和液力变矩器。
操作模式已经提出,风力机制造商宣称延伸速度范围以便在较低的速度力量提取的风是比损失在系统等系统能保持联系。
风机结构双馈

the rotor up against the wind.
整理课件
19
风向标 返回
整理课件
20
高速轴
返回
Small shaft The small shaft leads the power from the gearbox to the generator. The small shaft runs very quickly, approx. 1500 revolutions per minute.
A tubular steel tower is very str整o理n课g件.
25
基础 返回
整理课件
26
整理课件
11
主轴
返回
Main Shaft The rotor turns the large shaft. The shaft is connected to the gearbox. The rotor uses a large force to turn the shaft. Therefore the shaft has to be very thick.
In some wind turbines (such as this one) the generator is cooled by water.
The radiator cools the water
整理课件
16
控制器
返回
Controller The wind turbine controller is a computer that controls the many parts of wind turbine. The controller yaws the nacelle against the wind and allows the wind turbine rotor to start when the anemometer tells it that there is enough wind.
DIgSILENT_PowerFactory在双馈型风力发电机组控制系统仿真中的应用

DIgSILENT/PowerFactory在双馈型风力发电机组控制系统仿真中的应用发布时间:2021-08-06T15:08:09.953Z 来源:《中国电业》2021年第9期作者:张鹏隋秋楠张磊董吉星吴佳润[导读] 文章介绍了双馈型风力发电机组的典型结构、运行原理及特性、控制系统结构等基础理论。
张鹏隋秋楠张磊董吉星吴佳润蒙东协合新能源有限公司内蒙古自治区通辽市 028011摘要:文章介绍了双馈型风力发电机组的典型结构、运行原理及特性、控制系统结构等基础理论。
在此基础上,讲解了DIgSILENT软件中双馈发电机(DFIG)的控制系统模型。
引言:电力系统是当今社会最重要的能源系统之一。
仿真分析一直是电力系统研究、设计、规划的主要手段。
随着国家“30·60”双碳计划的提出,新能源发电将成为未来电力系统的主体。
为了有效应对和规划大规模新能源发电给电力系统带来的挑战,针对风力发电系统的仿真分析受到了普遍的重视。
目前,能够对风力发电系统进行仿真的软件有很多,例如MATLAB/Simulink、PSCAD、PSS/E、PSASP和DIgSILENT/PowerFactory等,不同种类的仿真软件具备不同的功能特点及优势。
DIgSILEN/PowerFactory的元件库中包含风力发电机组电气部分的主要模型,并且可以通过动态仿真语言DSL(Dynamic Simulation Language)搭建机械、空气动力学及控制系统等模型,具备较高的自由度和灵活性。
[1]本文主要阐述了DIgSILENT/PowerFactory在双馈型发电机(DFIG)控制系统仿真中的应用。
文章首先介绍了双馈型风力发电机组的基本结构、运行特征,然后介绍了双馈型风力发电机组的控制系统结构,最后介绍了DIgSILENT/PoweFactory中双馈型发电机的控制系统模型。
1双馈型风力发电机组主要结构如图1所示,双馈型风力发电机组由风轮系统、齿轮箱及传动系统、双馈感应发电机(DFIG)和背靠背PWM功率变换器组成。