塑料注塑成型故障排除
注塑机常见故障及维修方法探讨
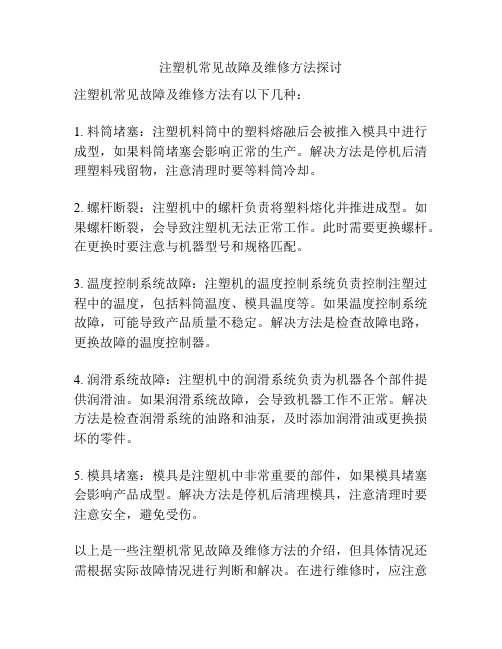
注塑机常见故障及维修方法探讨
注塑机常见故障及维修方法有以下几种:
1. 料筒堵塞:注塑机料筒中的塑料熔融后会被推入模具中进行成型,如果料筒堵塞会影响正常的生产。
解决方法是停机后清理塑料残留物,注意清理时要等料筒冷却。
2. 螺杆断裂:注塑机中的螺杆负责将塑料熔化并推进成型。
如果螺杆断裂,会导致注塑机无法正常工作。
此时需要更换螺杆。
在更换时要注意与机器型号和规格匹配。
3. 温度控制系统故障:注塑机的温度控制系统负责控制注塑过程中的温度,包括料筒温度、模具温度等。
如果温度控制系统故障,可能导致产品质量不稳定。
解决方法是检查故障电路,更换故障的温度控制器。
4. 润滑系统故障:注塑机中的润滑系统负责为机器各个部件提供润滑油。
如果润滑系统故障,会导致机器工作不正常。
解决方法是检查润滑系统的油路和油泵,及时添加润滑油或更换损坏的零件。
5. 模具堵塞:模具是注塑机中非常重要的部件,如果模具堵塞会影响产品成型。
解决方法是停机后清理模具,注意清理时要注意安全,避免受伤。
以上是一些注塑机常见故障及维修方法的介绍,但具体情况还需根据实际故障情况进行判断和解决。
在进行维修时,应注意
安全,并遵循相关操作规程。
建议在遇到严重故障时,及时请专业的维修技术人员进行处理。
PVC发泡塑料注塑成型的14个故障,你都知道吗

本文摘自再生资源回收-变宝网()PVC发泡塑料注塑成型的14个故障,你都知道吗PVC发泡塑料注塑成型的14个故障,你都知道吗?溢料飞边(1)模具密封不严.应维修模具。
(2)冷却速度太慢。
应提高冷却效率,增加冷却速度,最好在底模通冷却水,冷却效果较好。
(3)注射量和供料过多。
应适当减少。
(4)塑化时间和注射压力配合不当。
在测定出压力和发泡时间的关系曲线后,合理调整注射压力和发泡时间。
(5)料模内衬板翘曲变形。
应对内衬板进行修理或更换。
(6)液压系统漏油造成合模力不足。
应维修液压系统。
(7)销模钩子上的弹簧太松。
应调换弹簧,增加钩子的拉力。
(8)定型时间不够,制品表层尚未冷透,第一次开模时中间的热料突破表层外溢。
应适当延长第一开模时间。
起大泡(1)发泡剂的粒径太粗,分散不均匀。
一般发泡剂需经三辊研,在料筒内产生磨机研磨2~4遍,将其研细后使用。
(2)捏合及造粒时加工温度太高,发泡剂过早分解,粒子有发泡现象。
应适当降低捏合及造粒温度,挤出的粒子切开时不能有小泡。
(3)熔料在料筒种滞留时间太长或加工温度太高。
应采用快速预塑,已塑化的熔料应一次注完,并尽量采用一机多模生产。
(4)螺杆背压太小,熔料在料筒中受热膨胀。
应加大背压,使熔料内所含的发泡剂受热分解后无预膨胀的机会。
(5)料筒端部漏料,在端部出口处形成低压区,导致熔料在出口处膨胀形成气泡。
应适当降低出料口温度,最好在出料口部采用节流阀式结构,封住端部出口。
(6)再生料回用比例不当。
应适当减少其用量。
发泡倍率太大(1)发泡剂投料量太多,致使发气量过高。
应测定发气量,准确投料。
(2)增塑剂用量太多。
应适当减少。
(3)起模温度太高。
应降温出模。
(4)保压时间太短。
应保证制品完全定型后出模。
发泡倍率不够(1)发泡剂投料量太少,致使发气量不足。
应测定发气量,准确投料。
(2)增塑剂用量太少。
应适当增加投料量。
(3)制品在第二次加工时,第二次膨胀时间太短。
应适当延长加工时的蒸煮发泡时间,而且第一次和第二次发泡时间间隔不能超过12小时。
塑胶注成型不良缺陷种类及原因分析以及改善对策
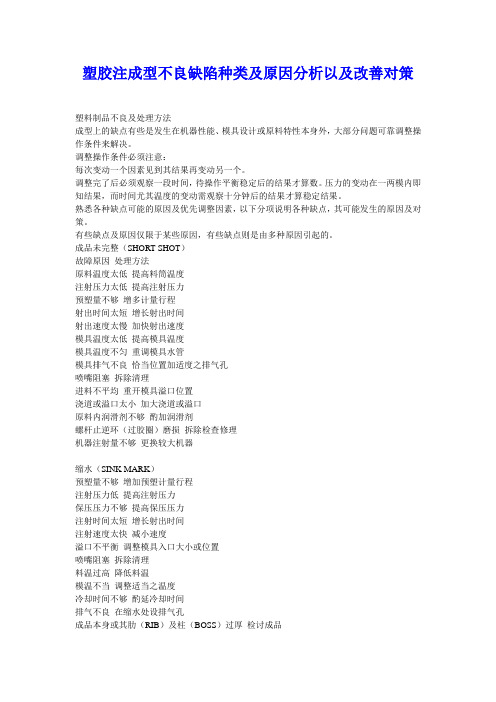
塑胶注成型不良缺陷种类及原因分析以及改善对策塑料制品不良及处理方法成型上的缺点有些是发生在机器性能、模具设计或原料特性本身外,大部分问题可靠调整操作条件来解决。
调整操作条件必须注意:每次变动一个因素见到其结果再变动另一个。
调整完了后必须观察一段时间,待操作平衡稳定后的结果才算数。
压力的变动在一两模内即知结果,而时间尤其温度的变动需观察十分钟后的结果才算稳定结果。
熟悉各种缺点可能的原因及优先调整因素,以下分项说明各种缺点,其可能发生的原因及对策。
有些缺点及原因仅限于某些原因,有些缺点则是由多种原因引起的。
成品未完整(SHORT SHOT)故障原因处理方法原料温度太低提高料筒温度注射压力太低提高注射压力预塑量不够增多计量行程射出时间太短增长射出时间射出速度太慢加快射出速度模具温度太低提高模具温度模具温度不匀重调模具水管模具排气不良恰当位置加适度之排气孔喷嘴阻塞拆除清理进料不平均重开模具溢口位置浇道或溢口太小加大浇道或溢口原料内润滑剂不够酌加润滑剂螺杆止逆环(过胶圈)磨损拆除检查修理机器注射量不够更换较大机器缩水(SINK MARK)预塑量不够增加预塑计量行程注射压力低提高注射压力保压压力不够提高保压压力注射时间太短增长射出时间注射速度太快减小速度溢口不平衡调整模具入口大小或位置喷嘴阻塞拆除清理料温过高降低料温模温不当调整适当之温度冷却时间不够酌延冷却时间排气不良在缩水处设排气孔成品本身或其肋(RIB)及柱(BOSS)过厚检讨成品料筒过大更换较小规格料筒螺杆止逆环(过胶圈)磨损拆除检查修理成品粘模(PRODUCT STICKING)注射压力太高降低射出压力剂量过多使用脱模剂保压时间太久减少保压时间注射速度太快减小速度料温过高降低料温进料不均匀使部分过饱变更溢口大小或位置冷却时间不足增加冷却时间模具温度过高或过低调整模温及两侧相对温度模具内有脱模倒角(UNDERCUT)修模具去除倒角模具表面不光打光模具浇道(水口)粘模(SPROE STICKING)注射压力太高降低射出压力加热温度过高调节温度浇道过大修改模具浇道冷却不够延长冷却时间或降低料筒温度浇道脱模角不够修改模具重新调整其配合增加角度浇道凹弧(SPRUE BUSHING)与射嘴配合不正重新调整其配合浇道内表面不光或有脱模倒角检修模具浇道外孔有损坏检修模具无浇道抓锁(SNA TCHPIN)加设抓锁填料过饱降低射出剂量、时间及速度毛头、披锋(FLASE)加热温度太高降低加热温度、降低模具温度注射压力太高降低射出压力填料过饱降低射出剂量、时间及速度合模线(PARTING LINE)或密封面(MA TING SURFACE)不良检修模具锁模压力不够增加锁模压力制品投影面积过大更换锁模压力较大之机器开模时或顶出时成品破裂(CRACKING)填料过饱降低射出剂量、时间及速度模温太低升高模温部份脱模角不够检修模具有脱模倒角检修模具成品脱模时不能平衡脱离检修模具顶针不够或位置不当检修模具脱模时模具产生真空现象降低开模或顶出慢速、加进气设备结合线(WELD LINES)塑料熔融不佳提高塑料温度;提高背压;加快螺杆转速模具温度过低提高模具温度注射速度太慢增加注射速度注射压力太低提高注射压力塑料不洁或掺有他料检查原料脱模油太多少用脱模油或尽量不用浇道及溢口过大或过小调整模具入口尺寸或改变位置模内空气排除不及增开排气孔或检查原有排气孔是否堵塞流纹(FLOW LINES)塑料熔融不佳提高塑料温度;提高背压;加快螺杆转速模具温度过低提高模具温度注射速度太快或太慢调整适当注射速度注射压力太高或太低调整适当注射压力塑料不洁或掺有他料检查原料溢口过小产生内射纹加大溢口成品断面厚薄相关太多变更成品设计或溢口位置银纹、气疮(SILVER STREAKS)塑料含有水分塑料彻底烘干;提高背压塑料温度过高或模具过热降低原料温度,射嘴及前段温度塑料中其他添加物如润滑剂染料等之分解减少其使用量或更换耐温较高之代替品塑料中其他添加物混合不匀彻底混合均匀注射速度太快减慢注射速度模具温度太低提高模具温度塑料粒粗细不匀使用粒状均匀之原料料筒内夹有空气降低料筒后段温度;提高背压原料在模内流程不当调整溢口大小及位置使模具温度保持平均成品表面不光泽模具温度太低提高模具温度塑料剂量不够增加注射压力、速度、时间及剂量模内有过多脱模油擦拭干净模内表面有水擦拭并检查是否漏水模内表面不光模具打光成品变形(WARPING)成品顶出时尚未冷却降低模具温度;延长冷却时间;降低塑料温度成品形状及厚薄不对称脱模后以定型架固定;变更成型设计进料过多减少射出压力、速度、时间及剂量几个溢口进料不平均更改溢口顶出系统不平衡改善顶出系统模具温度不均匀调理模具温度近溢口部分原料太松或太紧增加或减少注射时间成品内有气孔(AIR BUBBLES)成品断面、肋或柱过厚变更成品设计或溢口位置注射压力太低提高注射压力注射时间不足增加注射时间浇道溢口太小加大浇道及入口注射速度太快调慢注射速度塑料含水分塑料彻底干燥塑料温度过高以致分解降低塑料温度模具温度不平均调整模具温度冷却时间太长减少模内冷却时间,使用水浴冷却水浴冷却过急减短水浴时间或提高水浴温度背压不够提高背压料筒温度不当降低喷嘴及前段温度,提高后段温度黑点(BLACK SPOTS)原料过热部分附着料筒管壁彻底空射;拆除料筒清理;降低塑料温度;减短加热时间塑料混有异物、纸屑等检查塑料;彻底空射射入模内时产生焦斑(BURNING MARK)降低注射压力及速度;降低塑料温度;加强模具排气孔;酌降合模压力;更改入口位置料筒内有使原料过热的死角检查喷嘴与料筒间接触面有无间隙或腐蚀现象必须考虑回收材料的材质硬度必须要和新料相同,最理想的回收是连续性粉碎、干燥、加工不使回收材料贮放太久,粉碎粒子尽量和新粒子接近,树脂经一再的回收,将降低成品的特性,制品有特殊性要求时,最好勿使用回收料。
注塑成型过程中不良及原因分析对策
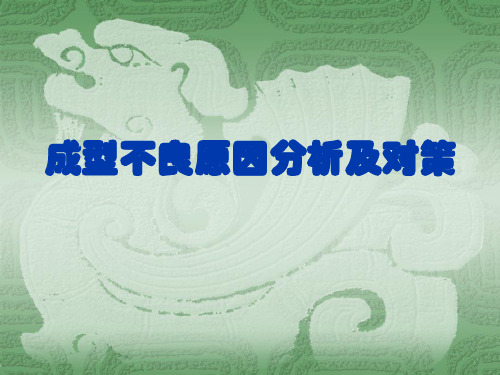
◆ 与成型品外观有关的成型不良
飞边 树脂进入模具分型线(PL)从而使薄膜附着在成型品四周 的现象。树脂粘度较低或保压过高时会出现这种现象。 凹痕 成型品表面出现凹陷的现象。厚壁产品容易出现这种现象。 须状斑纹 浇口周边形成独特的胡须状旋涡斑纹的现象。POM树脂容 易产生这一问题。 表面剥离 成型品的表面层与内部层产生分离的现象。 气泡 成型品表面拱状鼓起的现象。 变色 成型品颜色发生变化的现象。原因估计是滞留或树脂分解 等。
(2)产生熔合纹的原因
(2-1) 树脂温度偏低 两股树脂流相遇时便会出现熔合。此时,两者的温度越低,熔合就越明显。由于熔合处的 两股树脂流并不会相互混合(因为在喷流中一边半固化一边前进),因此如果温度偏低, 表层就会变厚,纹路很明显,而且强度也会降低。这是因为两者的粘合力变弱所致。相 反,如果两股树脂流的温度较高,粘合力便会增强,外观也就变得不很明显。
(2-3) 流动性和射出速度 材料的流动性较差时,充填时间 将延长,成型品表面层在保压工 序之前就已凝固,因此有时无法 向树脂施加保压。结果容易产生 麻点等不良外观。注射速度较慢 时也会由于同样的理由而易于产 生麻点。
(3)“麻点”的对策
(3-1) 尝试提高保压
首先尝试着逐渐提高保压设定值。这样基本上会解决问题。下面有指向本公司推 荐的材料成型条件的链接,请参阅。
◆ 与成型品外观有关的成型不良
空洞 成型品内部产生空洞的现象。厚壁 产品容易产生这种现象。 波纹 浇口附近出现波纹状皱纹的现象。 射速过慢时会产生这种现象。
BS(黑点)
(1)何谓“黑点”(外观)? 黑点是指成型品中出现黑色的点或条纹的现象。 成型品表面上出现的黑色的点便是BS(黑点)。由于某些原因,其成 分估计是焦化树脂或碳化树脂。
亚克力加工注塑成型各种缺陷的现象及解决方法
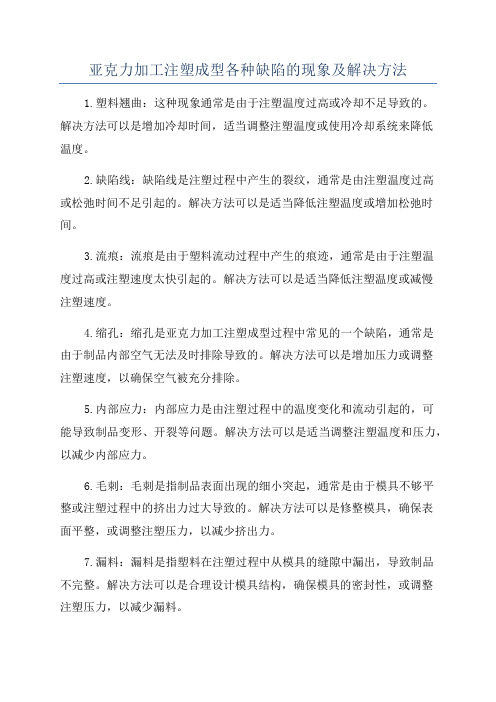
亚克力加工注塑成型各种缺陷的现象及解决方法1.塑料翘曲:这种现象通常是由于注塑温度过高或冷却不足导致的。
解决方法可以是增加冷却时间,适当调整注塑温度或使用冷却系统来降低温度。
2.缺陷线:缺陷线是注塑过程中产生的裂纹,通常是由注塑温度过高或松弛时间不足引起的。
解决方法可以是适当降低注塑温度或增加松弛时间。
3.流痕:流痕是由于塑料流动过程中产生的痕迹,通常是由于注塑温度过高或注塑速度太快引起的。
解决方法可以是适当降低注塑温度或减慢注塑速度。
4.缩孔:缩孔是亚克力加工注塑成型过程中常见的一个缺陷,通常是由于制品内部空气无法及时排除导致的。
解决方法可以是增加压力或调整注塑速度,以确保空气被充分排除。
5.内部应力:内部应力是由注塑过程中的温度变化和流动引起的,可能导致制品变形、开裂等问题。
解决方法可以是适当调整注塑温度和压力,以减少内部应力。
6.毛刺:毛刺是指制品表面出现的细小突起,通常是由于模具不够平整或注塑过程中的挤出力过大导致的。
解决方法可以是修整模具,确保表面平整,或调整注塑压力,以减少挤出力。
7.漏料:漏料是指塑料在注塑过程中从模具的缝隙中漏出,导致制品不完整。
解决方法可以是合理设计模具结构,确保模具的密封性,或调整注塑压力,以减少漏料。
8.颜色差异:颜色差异是指相同批次的亚克力制品颜色变化不一致。
解决方法可以是确保加色剂的质量稳定,避免杂质的混入,或使用稳定性好的加色剂。
9.尺寸不一致:尺寸不一致是指相同批次的亚克力制品尺寸变化过大。
解决方法可以是优化模具结构,确保注塑过程稳定,或使用高精度的注塑机器。
10.缺陷处理:当发现亚克力加工注塑制品出现缺陷时,应及时进行处理。
常见的处理方法包括修补、局部加热、二次注塑等。
总之,亚克力加工注塑成型过程中可能会出现多种缺陷,但通过适当的调整注塑参数、优化模具结构、使用高质量原料等方法,可以有效减少缺陷的出现,并提高亚克力制品的质量。
注塑不正常情况及处理办法
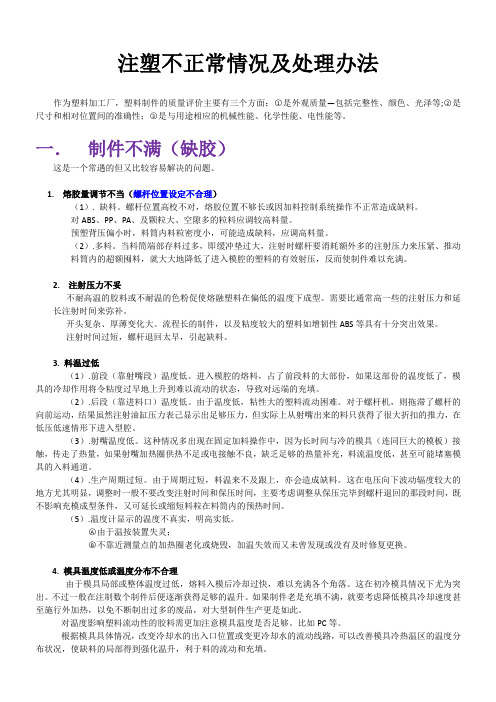
注塑不正常情况及处理办法作为塑料加工厂,塑料制件的质量评价主要有三个方面:○1是外观质量—包括完整性、颜色、光泽等;○2是尺寸和相对位置间的准确性;○3是与用途相应的机械性能、化学性能、电性能等。
一.制件不满(缺胶)这是一个常遇的但又比较容易解决的问题。
1. 熔胶量调节不当(螺杆位置设定不合理)(1). 缺料。
螺杆位置高校不对,熔胶位置不够长或因加料控制系统操作不正常造成缺料。
对ABS、PP、PA、及颗粒大、空隙多的粒料应调较高料量。
预塑背压偏小时,料筒内料粒密度小,可能造成缺料,应调高料量。
(2).多料。
当料筒端部存料过多,即缓冲垫过大,注射时螺杆要消耗额外多的注射压力来压紧、推动料筒内的超额囤料,就大大地降低了进入模腔的塑料的有效射压,反而使制件难以充满。
2. 注射压力不妥不耐高温的胶料或不耐温的色粉促使熔融塑料在偏低的温度下成型。
需要比通常高一些的注射压力和延长注射时间来弥补。
开头复杂、厚薄变化大。
流程长的制件,以及粘度较大的塑料如增韧性ABS等具有十分突出效果。
注射时间过短,螺杆退回太早,引起缺料。
3. 料温过低(1).前段(靠射嘴段)温度低。
进入模腔的熔料,占了前段料的大部份,如果这部份的温度低了,模具的冷却作用将令粘度过早地上升到难以流动的状态,导致对远端的充填。
(2).后段(靠进料口)温度低。
由于温度低,粘性大的塑料流动困难。
对于螺杆机,则拖滞了螺杆的向前运动,结果虽然注射油缸压力表己显示出足够压力,但实际上从射嘴出来的料只获得了很大折扣的推力,在低压低速情形下进入型腔。
(3).射嘴温度低。
这种情况多出现在固定加料操作中,因为长时间与冷的模具(连同巨大的模板)接触,传走了热量,如果射嘴加热圈供热不足或电接触不良,缺乏足够的热量补充,料流温度低,甚至可能堵塞模具的入料通道。
(4).生产周期过短。
由于周期过短,料温来不及跟上,亦会造成缺料。
这在电压向下波动辐度较大的地方尤其明显,调整时一般不要改变注射时间和保压时间,主要考虑调整从保压完毕到螺杆退回的那段时间,既不影响充模成型条件,又可延长或缩短料粒在料筒内的预热时间。
尺寸不稳定注塑缺陷分析及排除方法
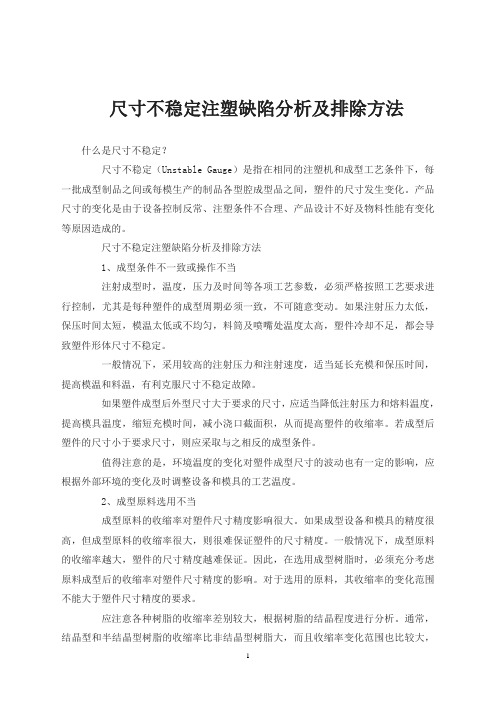
尺寸不稳定注塑缺陷分析及排除方法什么是尺寸不稳定?尺寸不稳定(Unstable Gauge)是指在相同的注塑机和成型工艺条件下,每一批成型制品之间或每模生产的制品各型腔成型品之间,塑件的尺寸发生变化。
产品尺寸的变化是由于设备控制反常、注塑条件不合理、产品设计不好及物料性能有变化等原因造成的。
尺寸不稳定注塑缺陷分析及排除方法1、成型条件不一致或操作不当注射成型时,温度,压力及时间等各项工艺参数,必须严格按照工艺要求进行控制,尤其是每种塑件的成型周期必须一致,不可随意变动。
如果注射压力太低,保压时间太短,模温太低或不均匀,料筒及喷嘴处温度太高,塑件冷却不足,都会导致塑件形体尺寸不稳定。
一般情况下,采用较高的注射压力和注射速度,适当延长充模和保压时间,提高模温和料温,有利克服尺寸不稳定故障。
如果塑件成型后外型尺寸大于要求的尺寸,应适当降低注射压力和熔料温度,提高模具温度,缩短充模时间,减小浇口截面积,从而提高塑件的收缩率。
若成型后塑件的尺寸小于要求尺寸,则应采取与之相反的成型条件。
值得注意的是,环境温度的变化对塑件成型尺寸的波动也有一定的影响,应根据外部环境的变化及时调整设备和模具的工艺温度。
2、成型原料选用不当成型原料的收缩率对塑件尺寸精度影响很大。
如果成型设备和模具的精度很高,但成型原料的收缩率很大,则很难保证塑件的尺寸精度。
一般情况下,成型原料的收缩率越大,塑件的尺寸精度越难保证。
因此,在选用成型树脂时,必须充分考虑原料成型后的收缩率对塑件尺寸精度的影响。
对于选用的原料,其收缩率的变化范围不能大于塑件尺寸精度的要求。
应注意各种树脂的收缩率差别较大,根据树脂的结晶程度进行分析。
通常,结晶型和半结晶型树脂的收缩率比非结晶型树脂大,而且收缩率变化范围也比较大,与之对应的塑件成型后产生的收缩率波动也比较大;对于结晶型树脂,结晶度高,分子体积缩小,塑件的收缩大,树脂球晶的大小对收缩率也有影响,球晶小,分子间的空隙小,塑件的收缩较小,而塑件的冲击强度比较高。
ABS塑料制品注塑成型缺陷问题及解决方案

A B S塑料制品注塑成型缺陷问题及解决方案乐享集团公司,写于2021年6月16日ABS塑料注塑成型缺陷之一:料头附近有暗区料头附近有暗区Dull areas near sprue1、表观在料头周围有可辨别的环形—如使用中心式浇口则为中心圆,如使用侧浇口则为同心圆,这是因为环形尺寸小,看上去像黯晕;这主要是加工高粘性低流动性材料时会发生这种现象,如PC、PMMA和ABS等;物理原因如果注射速度太高,熔料流动速度过快且粘性高,料头附近表层部分材料容易被错位和渗入;这些错位就会在外层显现出黯晕;在料头附近,流动速度特别高,然后逐步降低,随着注射速度变为常数,流动体前端扩展为一个逐渐加宽的圆形;同时在料头附近为获得低的流体前流速度,必须采用多级注射,例如:慢—较快—快;目的是在整个充模循环种获得均一的熔体前流速度;通常以为黯晕是在保压阶段熔料错位而产生的;实际上,前流效应的作用是在保压阶段将熔料移入了制品内部;与加工参数有关的原因与改良措施见下表:1、流速太高采用多级注射:慢-较快-快2、熔料温度太低增加料筒温度,增加螺杆背压3、模壁温度太低增加模壁温度与设计有关的原因与改良措施见下表:1、浇口与制品成锐角在浇口和制品间成弧形2、浇口直径太小增加浇口直径3、浇口位置错误浇口重新定位ABS塑料注塑成型缺陷之二:锐边料流区有黯区锐边料流区有黯区Dull areas downstream of edges1、表观成型后制品表面非常好,直到锐边;锐边以后表面出现黯区并且粗糙;物理原因如果注射速度太快,即流速太高,尤其是对高粘性流动性差的熔体,表面层容易在斜面和锐边后面发生移位和渗入;这些移位的外层冷料就表现为黯区和粗糙的表面;与加工参数有关的原因与改良措施见下表:1、流体前端速度太快采用多级注射:快-慢,在流体前端到达锐边之前降低注射速度与设计有关的原因与改良措施见下表:1、模具内锐角过渡提供光滑过渡ABS塑料注塑成型缺陷之三:表面光泽不均表面光泽不均Gloss Variations on textured surfaces1、表观虽然模具具有均一的表面材质,制品表面还是表现为灰黯和光泽不均匀;物理原因注射成型生产的制品表面多少是模具表面的翻版;表面粗糙取决于热塑性材料本身,它的粘性、速度设置以及成型参数如注射速度、保压和模温;因而,由于仿制的表面粗糙度的原因,制品表面会出现为灰黯、较黯或光滑;理论上说,当被点蚀或侵蚀过的模具表面已精确仿制,投射到制品表面的光线会发生漫反射;因此,表面会出现黯区;对具有较少精确仿制的表面,漫反射现象就会得到控制进而制品表面出现好的光泽效果与加工参数有关的原因与改良措施见下表:1、保压太低提高保压压力2、保压时间太短提高保压时间3、模壁温度太低提高模壁温度4、熔料温度太低提高熔体温度与设计有关的原因与改良措施见下表:1、模壁截面差异太大提供更均一的模壁截面2、材料积留过多或棱边尺寸过大避免材料积留过重或棱边尺寸过大3、料流线处排气不好提高模具在料流线处的排气ABS塑料注塑成型缺陷之四:空隙空隙Void1、表观制品内部的空隙表现为圆形或拉长的气泡形式;仅仅是透明的制品才可以从外面看出里面的空隙;不透明的制品无法从外面测出;空隙往往发生在壁相对较厚的制品内并且是在最厚的地方;物理原因当制品内有泡产生时,经常认为是气泡,是模具内的空气被流入模腔的熔料裹入;另一个解释是料筒内的水气和气泡会想方设法进入到制品的内部;所以说,这样的“泡”的产生有多方面的根源;一开始,生产的制品会形成一层坚硬的外皮,并且视模具冷却的程度往里或快或慢的发展;然而在厚壁区域里,中心部分仍继续保持较长时间的粘性;外皮有足够强度抵抗任何应力收缩;结果,里面的熔料被往外拉长,在制品内仍为塑性的中心部分形成空隙与加工参数有关的原因与改良措施见下表:1、保压太低提高保压压力2、保压时间太短提高保压时间3、模壁温度太低提高模壁温度4、熔料温度太高降低熔体温度与设计有关的原因与改良措施见下表:1、浇口横截面太小增加浇口横截面,缩短浇道2、喷嘴孔太小增大喷嘴孔3、浇口开在薄壁区浇口开在厚壁区ABS塑料注塑成型缺陷之五:气泡气泡Gas bubbles1、表观制品表面和内部有许多气泡—主要在料头附近;流道中途和远离料头的地方—不仅是发生在制品壁厚的地方;气泡有着不同的尺寸和不同的形状;物理原因气泡主要发生在必须在高温下加工的热敏性材料;如果必须的成型温度太高,通过分子分裂而导致材料分解,熔料就有发生热降解的危险,成型过程中气泡就容易产生;如果周期时间长,通常可能是太长的残留时间和行程利用不足的原因;也可能因为料筒内的熔料过热;与加工参数有关的原因与改良措施见下表:1、熔料温度太高降低料筒温度、螺杆背压和螺杆转速2、熔料在料筒内残留时间过长使用较小的料筒直径与设计有关的原因与改良措施见下表:1、不合理的螺杆几何形状使用低压缩螺杆ABS塑料注塑成型缺陷之六:白点白点Granules Unmelted1、表观料头附近有未熔化的颗粒;对薄壁制品来说是不可能获得光滑的表面;物理原因由于薄壁制品生产成型周期短,因此必须以很高的螺杆转速进行塑化从而使熔料在螺杆料筒内残留时间缩短;在碰到薄壁制品生产时,通常包括PE、PP,模具工会试着降低熔料温度以缩短冷却时间,未完全熔化的颗粒会被注射进模具内;与加工参数有关的原因与改良措施见下表:1、熔料温度太低增加料筒温度2、螺杆转速太高降低螺杆转速3、螺杆背压太低增加螺杆背压4、循环时间短,即熔料在料筒内残留时间短延长循环时间与设计有关的原因与改良措施见下表:1、不合理的螺杆几何形状选用适当几何形状的螺杆含计量切变区ABS塑料注塑成型缺陷之七:灰黑斑纹灰黑斑纹Grey or black clouding1、表观灰黑斑纹可能发生在浇口附近,流道的中间和远离浇口的部分;只能在透明的零件中可看出,并且往往用PMMA,PC和PS料制成的产品有此现象;物理原因如果计量过程开始太早,螺杆喂料区里颗粒裹入的空气没有溢出喂料口,空气就会被挤入熔料内;然而,喂料区内的压力太低不能将空气移到后面;料筒内熔料中被挤入的空气就会使制品内产生灰黑斑纹;就像压缩点火式柴油发动机里面所发生的情况一样,被料筒内挤入的空气所造成的焦化现象有时被称为“柴油机效应”;焦化现象可解释熔料和挤入的气泡交接的地方由于压缩作用产生高温,同时空气内的氧气通过氧化作用使熔料产生断裂;工艺调试应该在喂料区的中间开始熔化过程,此处熔料压力已较高,迫使颗粒之间的空气朝后移动并溢出料口;与加工参数有关的原因与改良措施见下表:1、螺杆背压太低增加螺杆背压2、喂料区的料筒温度过高降低喂料区的料筒温度3、螺杆转速过快降低螺杆转速4、循环时间短,即熔料在料筒内残留时间短延长循环时间与设计有关的原因与改良措施见下表:1、不合理的螺杆几何形状选用加料段长的螺杆,且加料段的螺槽较深ABS塑料注塑成型缺陷之八:料头附近有灰黑斑料头附近有灰黑斑Diesel effect away from sprue1、表观制品表面上以浇口或附近一点为中心向外发散出现银色或黑色纹迹;如果使用低粘性高流动性材料和高成型温度,纹路大多是黑色,如果采用高粘性低流动性材料,纹路大多是银白色;物理原因这是由被挤入和压缩的另一种气泡;如果螺杆降压幅度太高螺杆回缩,降压速度过快,螺杆头前面的熔料释放太多,会在熔料内产生负压,在熔料温度太高的情况下,很容易在熔料内形成气泡;这些气泡会在以后的注射阶段再次受到压缩,导致黑色纹路在制品内生成,最终成为“柴油机效应”;如果浇口为中心式浇口,纹路就会从料头向外辐射;在带热流道注射的情况下,纹路只会再某段流道以后出现,因为在热流道里的材料不包含任何气泡,因而材料不会产生烧焦的痕迹;只有再料筒头的熔料才会产生烧焦的痕迹;假如是低粘性的熔料,纹路比高粘性材料更灰黯和更大,因为前者再螺杆降压过程中容易产生真空和空隙;3、与加工参数有关的原因与改良措施见下表:1螺杆降压太高减小螺杆降压幅度2螺杆降压率太高减小螺杆降压率3熔料温度太高降低料筒温度,降低螺杆背压,降低螺杆转速ABS塑料注塑成型缺陷之九:放射纹放射纹Jetting1、表观从浇口喷射出,有灰黯色的一股熔流在稍微接触模壁后马上被随后注入的熔料包住;此缺陷可能部分或完全隐藏在制品内部;物理原因放射纹往往发生在当熔料进入到模腔内,流体前端停止发展的方向;它经常发生在大模腔的模具内,熔流没有直接接触到模壁或没有遇到障碍;通过浇口后,有些热的熔料接触到相对较冷的模腔表面后冷却,在充模过程中不能同随后的熔料紧密结合在一起;除去明显的表面缺陷,放射纹伴随不均匀性,熔料产生冻结拉伸,残余应力和冷应变而产生,这些因素都影响产品质量;在多数情况下不太可能只通过调节成型参数改进,只有改进浇口位置和几何形状尺寸才可以避免;与加工参数有关的原因与改良措施见下表:1、注射速度太快降低注射速度2、注射速度单级采用多级注射速度:慢-快3、熔料温度太低提高料筒温度对热敏性材料只在计量区;增加低螺杆背压与设计有关的原因与改良措施见下表:1、浇口和模壁之间过渡不好提供圆弧过渡2、浇口太小增加浇口3、浇口位于截面厚度的中心浇口重定位,采用障碍注射ABS塑料注塑成型缺陷之十:冷料头冷料头Cold slug1、表观这指的是有一块冷料卡在或粘在料头附近的表面上;冷料头会导致制品表面出现痕迹,严重的还会降低制品的力学性能2、物理原因当熔料可以在机器喷嘴或热流道附近冷却时往往会产生冷料头;由于先注射进的熔料总是聚集在浇口附近,在此区域就会产生缺陷;它的成因是因为机器喷嘴或热流道喷嘴周围的温度控制不合理;3、与加工参数有关的原因与改良措施见下表:•热流道温度太低增加热流道温度•喷嘴温度太低测量喷嘴温度,提高喷嘴温度,减少喷嘴接触区4、与设计有关的原因与改良措施见下表:•喷嘴横截面太小增加喷嘴横截面•浇口几何尺寸不合理改变浇口几何尺寸将冷料头留在通道•热流道几何尺寸不合理改变热流道喷嘴几何尺寸ABS塑料注塑成型缺陷之十一:唱片纹唱片纹Gramophone rippie1、表观在整个料流方向上甚至到流道末端可以看出很深的槽;在采用高粘性流动性差材料和厚壁的制品生产时出现这种现象,这些槽看上去象唱片上的纹路;在PC料做成的产品上非常清晰,但在ABS制品上更大,并且呈灰黯色;2、物理原因如果在注射过程中—特别时在低注射速度的条件下,接触模具表面的熔体凝结速度太快,流动阻力太高,就会在流体前端产生扭曲;凝固的外层材料不会完全接触模腔壁而形成波浪状;这些波浪状的材料会冻结,保压也不再能够将它们弄平整;与加工参数有关的原因与改良措施见下表:•注射速度太低增加注射速度•熔料温度太低提高料筒温度,增加螺杆背压•模具表面温度太低增加模具温度•保压太低增加保压与设计有关的原因与改良措施见下表:1、浇口横截面太小增加浇口横截面,缩短浇道2、喷嘴孔太小增大喷嘴孔ABS塑料注塑成型缺陷之十二:熔接缝熔接缝Weld line表观在充模方式里,熔接缝是指各流体前端相遇时的一条线;特别是模具有高抛光表面的地方,制品上的熔接缝很象一条刮痕或一条槽,尤其是在颜色深或透明的制品上更明显;熔接缝的位置总是在料流方向上;物理原因熔接缝形成的地方为熔料的细流分叉并又连接在一起的地方,最典型的是型芯周围的熔流或使用多浇口的制品;在细流再次相遇的地方,表面会形成熔接缝和料流线;熔料周围的型芯越大或浇口间的流道越长,形成的熔接缝就越明显;细小的熔接缝不会影响制品的强度;然而,流程很长或温度和压力不足的地方,充模不满会造成明显的凹槽;原因主要是流体前端未均匀熔合产生弱光点;聚合物内加入颜料的地方可能会产生斑点,这是因为在取向上有明显的差异;浇口的数量和位置决定了熔接缝的数量和位置;流体前锋相遇时的角度越小,熔接缝越明显;大多数情况下,工艺调试不可能完全避免熔接缝或料流线;所能做到的是降低其亮度,或将它们移到不显眼或完全看不见的地方与加工参数有关的原因与改良措施见下表:1、注射速度太低增加注射速度2、熔料温度太低提高料筒温度3、模具表面温度太低增加模具温度4、保压太低增加保压,尽早进行保压切换与设计有关的原因与改良措施见下表:1、浇口位置不合理重新定位浇口并将其移到不可见的地方2、料流道处无排气孔排气孔尺寸应符合材料的特性ABS塑料注塑成型缺陷之十三:水迹纹水迹纹Moisture streaks表观水迹纹是在制品表面有很长的银丝,水迹纹的开口方向沿着料流方向;在制品未完全充满的地方,流体前端很粗糙;物理原因一些塑料如PA、ABS、PMMA、SAN和PBT等容易吸水;如果塑料储藏条件不好,潮气就会进入颗粒或附在表面;当颗粒熔化时,潮气会转变成蒸汽形成气泡;在注射期间,这些气泡会暴露在流体前锋的表面,爆裂然后产生不规则的纹路与加工参数有关的原因与改良措施见下表:1、颗粒内残留的水分太高检查颗粒的储藏条件,缩短颗粒在料斗内的时间,给材料提供足够的预烘干ABS塑料注塑成型缺陷之十四:颜色不均颜色不均Colour streaks表观颜色不均是制品表面的颜色不一样,可在料头附近和远处,偶尔也会在锐边的料流区出现;物理原因颜色不均是因为颜料分配不均而造成的,尤其是通过色母、色粉或液态色料加色时;在温度低于推荐的加工温度情况下,母料或色料不能完全均匀化;当成型温度过高,或料筒的残留时间太长,也容易造成颜料或塑料的热降解,导致颜色不均;当材料在正确的温度下进行塑化或均化时,如果通过料头横截面时注射太快,可能会产生摩擦热造成颜料的降解和颜色的改变;通常在使用色母料时,应确保颜料及其溶解液需上色的树脂在化学、物理特性方面的相容性;与加工参数有关的原因与改良措施见下表:1、材料未均匀混合降低螺杆速度;增加料筒温度,增加螺杆背压2、熔料温度太低增加料筒温度,增加螺杆背压3、螺杆背压太低增加螺杆背压4、螺杆速度太高减少螺杆速度与设计有关的原因与改良措施见下表:1、螺杆行程过长用直径较大或长径比较大的料筒2、熔料在料筒内停留时间短用直径较大或长径比较大的料筒3、螺杆L:D太低使用长径比较大的料筒4、螺杆压缩比低采用高压缩比螺杆5、没有剪切段和混合段提供剪切段和或混合段注塑成型缺陷之十五:烧焦纹烧焦纹Charred streaks表观制品表面表现出银色和淡棕色的非常暗的条纹;物理原因烧焦暗纹是因为熔料过度热降解而造成的;淡棕色的黯纹是因为熔料发生氧化或分解;银纹的造成一般是因为螺杆、止逆环、喷嘴、料头、制品内窄的横截面或锐边区域产生摩擦;一般来说,在机器停工而料筒仍继续加热的时间内塑料会发生严重降解或分解现象;如果仅在料头附近发现条纹,原因就不止是热流道温度控制优化不足,还同机器的喷嘴有关;熔料的温度哪怕是稍微有点高,熔料在料筒内的残留时间相对较长,也会导致制品的力学性能下降;在因为分子热运动而产生的降解连锁反应的作用下,熔料的流动性会增加,以至让模件不可避免地发生溢模的现象;对复杂模具尤其要小心;与加工参数有关的原因与改良措施见下表:1、熔料温度太高降低料筒温度2、热流道温度太高检查热流道温度,降低热流道温度3、熔料在料筒内残留时间太长采用小直径料筒4、注射速度太高减小注射速度:采用多级注射:快-慢ABS塑料注塑成型缺陷之十六:玻璃纤维银纹玻璃纤维银纹Glass fiber streaks表观加入了玻璃纤维的塑料模制品的表面呈多样缺陷:灰暗、粗糙,部分出现金属亮点等很明显的特征,尤其是凸起部分料流区,流体再次会合的接合线附近;物理原因如果注射温度太低并且模温太低,含有玻纤的材料往往在模具表面凝结过快,此后玻纤再也不会嵌到熔体内;当两股料流前锋相遇时,玻纤的取向是在每条细流的方向上,因而会在交叉的地方导致表面材质不规则,结果就会形成接合缝或料流线;这些现象在料筒内熔料内未完全混合时更加明显,例如螺杆行程太长,导致熔料混合不均的熔料也被注射;与加工参数有关的原因与改良措施见下表:1、注射速度太低增加注射速度:考虑用多级注射:先慢-后快2、模温太低增加模温3、熔料温度太低增加料筒温度,增加螺杆背压4、熔料温度变化高,如熔料不均匀增加螺杆背压;减小螺杆速度;使用较长的料筒以缩短行程ABS塑料注塑成型缺陷之十七:溢边溢边Flash表观在凹处周围,沿分型线的地方或模具密封面出现薄薄的飞边;物理原因在多数情况下,溢边的产生是因为在注射和保压的过程中,机器的合模力不够,无法沿分型线将模具锁紧并密封;如果模腔内有地方压力很高,此处模具变形就有可能造成溢模;在高的成型温度和注射速度条件下,熔料在流道末端仍能充分流动,如果摸具没有锁紧就会产生溢边;如果只在模具上某一点发现溢边,这就说明模具本身有缺陷:此处模具未完全封住;典型的溢边情形:局部产生溢边是由于模具有缺陷,而扩展到整个周围则是因为合模力不够;必须注意为避免溢边在增加合模力时应该慎重,因为合模力过量易损坏模具;建议正确的做法是应仔细确认溢边的真正原因;特别是在使用多型腔的模具之前,准备一些模具的分析资料不失为一个好办法,这样可以给所有的问题提供正确答案;与加工参数有关的原因与改良措施见下表:1、锁模力不够增加锁模力2、注射速度太快减少注射速度:用多级注射:快-慢3、保压切换晚早一点保压切换4、熔料温度太高降低料筒温度5、模壁温度太高降低模壁温度6、保压太高降低保压与设计有关的原因与改良措施见下表:1、模具强度不够增加模具强度2、模具在分型线或凸边处密封不足重新设计模具ABS塑料注塑成型缺陷之十八:收缩收缩Sink marks表观塑件表面材料堆积区域有凹痕;收缩水主要发生在塑件壁厚厚的地方或者是壁厚改变的地方;物理原因当制品冷却时,收缩体积减小,收缩发生,此时外层紧模壁的地方先冻结,在制品中心形成内应力;如果应力太高,就会导致外层的塑料发生塑性变形,换句话说,外层会朝里凹陷下去;如果在收缩发生和外壁变形还未稳定因为还没有冷却时,保压没有补充熔料到模件内,在模壁和已凝固的制品外层之间就会形成沉降;这些沉降通常会被看成为收缩;如果制品有厚截面,在脱模后也有可能产生这样的缩水;这是因为内部仍有热量,它会穿过外层并对外层产生加热作用;制品内产生的拉伸应力会使热的外层向里沉降,在此过程中形成收缩;与加工参数有关的原因与改良措施见下表:1、保压太低增加保压2、保压时间太短延长保压时间3、模壁温度太高降低模壁温度4、熔料温度太高降低熔料温度,降低料筒温度与设计有关的原因与改良措施见下表:1、料头横截面太小增加料头横截面2、料头太长缩短料头3、喷嘴孔太小增加喷嘴孔径4、料头开在薄壁处将料头定位在厚壁处5、材料堆积过量避免材料堆积6、壁/筋的截面不合理提供较合理的壁/筋的截面比例ABS塑料注塑成型缺陷之十九:注射不足注射不足Short shot表观:模腔未完全充满,主要发生在远离料头或薄壁面的地方;物理原因熔料的注射压力和/或注射速度太低,熔料在射向流长最末端过程中冷却;通常在低熔料温度和模温的条件下注射高粘性材料时会碰到这种情况;它也会发生在需要高压注射但保压设置低不成比例的时候;实际上,当需要高注射压力时,保压也应按比例提高:正常时,保压应为注射压力的50%左右,但如果采用高注射压力,保压应为70%~80%;如在料头附近发现注射不满,可以解释为:流体前锋在这些点被阻挡,较厚的地方先被充满;如此,在模腔几乎被充满之后,在薄壁处的熔料已经凝结并且在流体中心部位有少量的流动导致注射不足;与加工参数有关的原因与改良措施见下表:1、注射压力太低增加注射压力2、注射速度太低增加注射速度3、保压太低增加保压4、保压切换太早延迟从注射到保压的切换5、熔料温度太低增加料筒温度,增加螺杆背压6、保压时间太短延长保压时间与设计有关的原因与改良措施见下表:1、流道/料头横截面太小增加流道/料头的横截面2、模具排气不足提高模具排气性3、喷嘴孔太小增加喷嘴孔径4、薄壁处的厚度不够增加截面厚度ABS塑料注塑成型缺陷之二十:翘曲翘曲Warpage表观制品的形状在制品脱模后或稍后一段时间内产生旋转或扭曲现象;典型表现为,制品平坦部分有起伏,直边朝里或朝外弯曲或扭曲;物理原因制品-因其特性-冻结的分子链在应力作用下发生内部移位;在脱模的时候,按不同的制品形状,应力往往会造成不同程度的变形;内应力使制品收缩不均,小颗粒移位,颗粒内冷却不平衡或颗粒内产生过量的压力;特别是用部分结晶材料制成的制品,如PE、PP、POM比非晶体材料如PS、ABS、PMMA和PC更容易产生缩壁,更易于翘曲;。
塑料注塑成型不良现象原因及处理办法

塑料注塑成型不良现象原因及处理办法一、气泡气泡是一种常见的注塑不良现象,造成气泡的原因可以分为产品设计、原料选择和注塑工艺三个方面。
1.产品设计问题:设计中未考虑到壁厚梯度过大、封闭空腔、通孔无曲线等情况,导致气泡无法排除。
处理办法:合理优化产品设计,减小壁厚梯度、增加封闭空腔的通气孔。
2.原料选择问题:原料中含有过多的挥发性成分、水分或杂质,或者原料中添加了过多的促进剂。
处理办法:使用质量可靠的原料,并严格控制原料中的水分和杂质含量。
3.注塑工艺问题:温度、压力、注射速度等工艺参数设置不合理,导致气泡无法排除。
处理办法:合理调整注塑工艺参数,保持合适的温度、压力和注射速度,防止气泡产生。
二、热缩痕热缩痕是注塑过程中产生的一种表面缺陷,常见于产品壁厚不一致、结构复杂的部分。
1.壁厚不一致问题:在产品设计中,壁厚过大或过小的部分易产生热缩痕。
处理办法:调整产品结构,减小壁厚梯度,避免热缩痕的产生。
2.注塑工艺问题:注塑过程中温度、压力不稳定,或者注射速度过快,都会导致热缩痕的产生。
处理办法:优化注塑工艺参数,保持合适的温度、压力和注射速度,避免热缩痕的产生。
三、翘曲变形翘曲变形是注塑成型中常见的一种现象,主要是由于材料流动不均匀或受力不平衡造成的。
1.部件结构问题:产品设计中存在壁厚不均匀、结构不合理等问题,易导致翘曲变形。
处理办法:优化产品结构设计,减小壁厚梯度,增加强度和刚度。
2.注塑工艺问题:注塑过程中温度、压力、注射速度等参数设置不合理,也会导致翘曲变形。
处理办法:调整注塑工艺参数,保持合适的温度、压力和注射速度,控制注塑过程中的变形。
四、色差色差是指注塑成型产品的颜色不均匀或与要求的颜色不符,主要由原料或工艺引起。
1.原料问题:原料中的色母粒质量不好、色母粒加入不均匀等原因,导致产品的色差问题。
处理办法:选用质量可靠的色母粒,并加入均匀进行混合。
2.注塑工艺问题:注塑过程中温度控制不当,熔融状态不稳定,颜色出现偏差。
注塑机常见故障及解决方法

注塑机常见故障及解决方法注塑机是一种广泛应用于塑料制品生产的设备,它的稳定运行对于生产过程的顺利进行至关重要。
然而,由于操作不当、设备老化或其他因素,注塑机在使用过程中可能会出现一些常见故障。
本文将介绍一些常见的注塑机故障,并提供相应的解决方法,希望对注塑机的用户有所帮助。
1. 温度控制系统故障温度控制系统是注塑机中关键的一个部件,它负责控制熔融温度和模具温度,保证产品质量和生产效率。
然而,温度控制系统可能会出现故障,导致温度不稳定,甚至无法达到设定值。
常见的故障原因包括热电偶损坏、控制器故障、温度传感器失效等。
解决方法可以是更换热电偶或传感器,修复或更换控制器。
2. 润滑系统故障注塑机的润滑系统起到保护设备的作用,减少摩擦和磨损。
如果润滑系统出现故障,设备的使用寿命将会大大降低。
故障可能包括润滑油供应不足、润滑管道堵塞或润滑泵失效等。
解决方法可以是检查和清理润滑管道,更换润滑油或修复润滑泵。
3. 压力控制系统故障注塑机的压力控制系统对于产品质量的稳定性有着重要影响。
如果压力控制系统出现故障,可能导致产品尺寸不一致或成型不完整。
常见的故障原因包括压力传感器故障、液压阀门堵塞或液压泵损坏等。
解决方法可以是更换压力传感器、清洁液压阀门或修复液压泵。
4. 料斗堵塞料斗堵塞是注塑机使用过程中常见的问题之一。
料斗堵塞可能导致原料供给不足,影响生产效率。
常见的堵塞原因包括原料结块、料斗内残留物过多或供料机构故障等。
解决方法可以是使用振动器或料斗搅拌器解除堵塞,检查和清理料斗内部。
5. 机械故障注塑机的机械部件在长时间运行后可能会出现磨损或松动,导致设备的稳定性下降。
常见的机械故障包括模具开合不顺畅、注射装置卡死或机械传动部件松动等。
解决方法可以是修复或更换损坏的机械部件,调整机械传动部件的紧固度。
总结起来,注塑机常见故障包括温度控制系统故障、润滑系统故障、压力控制系统故障、料斗堵塞和机械故障等。
对于这些故障,我们可以根据具体情况采取相应的解决方法进行修复。
聚碳酸酯注塑成型故障得成因及对策
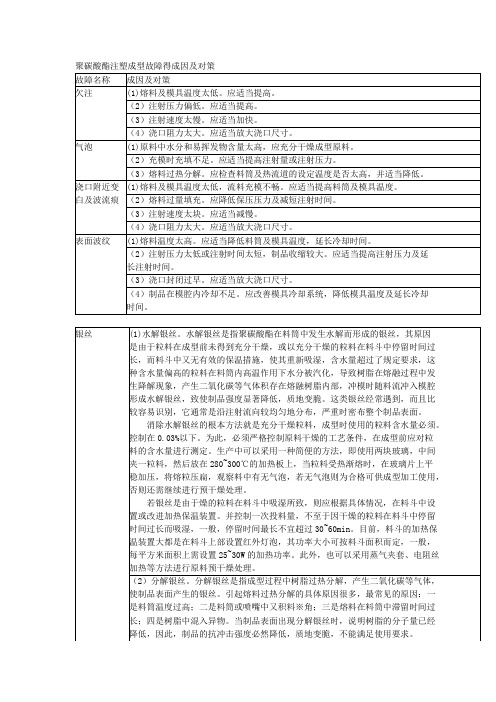
段温度过高而造成的,应将该段料筒温度降低;如果是在料筒或喷嘴中又积料※
角,则应清理滞料部位并修除※角;如果是由于熔料在料筒中滞留时间过长,则
应在保证制品质量的前提下尽量缩短成型周期,若仍不见效,则应考虑换用容量
较小的注射机进行加工。
(3)结构银丝。结构银丝是指由于制品结构设计不合理、壁厚严重不均匀或出
(2)注射机容量不足。应换用较大规格的注射机。
(3)注射压力偏低。应适当提高。
(4)注射速度太慢。应适当加快。
(5)模具温度太低。应适当提高。
(6)供料不足。应检查喷嘴是否堵塞,料斗内有无“架桥”及堵塞现象。
(7)树脂的流动性能太差。应添加少量润滑剂,添加量以0.03%~0.15%质量比
为宜。
(8)浇注系统结构尺寸偏小。应适当放大浇口和流道截面。
和缩瘪等故障,有时甚至在制品内部产生不同程度的气泡。
结构银丝一般可通过改变注射速度的方法来排除。当制品截面变化不大时,
可减慢注射速度,采用慢速注射,使料流平稳地充填模腔,从而使料流经过突变
断面时不致混入空气,避免产生银丝。但是,降低注射速度又可能出现欠注,这
就需要调整模具和喷嘴温度等其他工艺条件协调解决。
聚碳酸酯注塑成型故障得成因及对策
故障名称
成因及对策
欠注
(1)熔料及模具温度太低。应适当提高。
(2)注射压力偏低。应适当提高。
(3)注射速度太慢。应适当加快。
(4)浇口阻力太大。应适当放大浇口尺寸。
气泡
(1)原料中水分和易挥发物含量太高,应充分干燥成型原料。
(2)充模时充填不足。应适当提高注射量或注射压力。
塑料注塑成型时四大问题分析解决方案
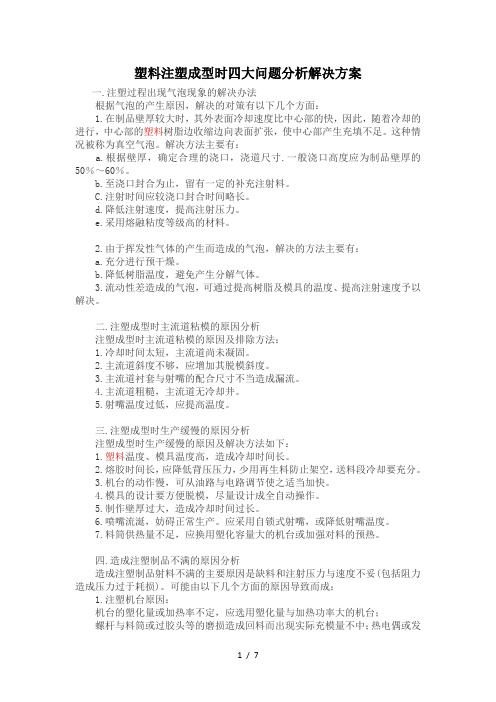
塑料注塑成型时四大问题分析解决方案一.注塑过程出现气泡现象的解决办法根据气泡的产生原因,解决的对策有以下几个方面:1.在制品壁厚较大时,其外表面冷却速度比中心部的快,因此,随着冷却的进行,中心部的塑料树脂边收缩边向表面扩张,使中心部产生充填不足。
这种情况被称为真空气泡。
解决方法主要有:a.根据壁厚,确定合理的浇口,浇道尺寸.一般浇口高度应为制品壁厚的50%~60%。
b.至浇口封合为止,留有一定的补充注射料。
C.注射时间应较浇口封合时间略长。
d.降低注射速度,提高注射压力。
e.采用熔融粘度等级高的材料。
2.由于挥发性气体的产生而造成的气泡,解决的方法主要有:a.充分进行预干燥。
b.降低树脂温度,避免产生分解气体。
3.流动性差造成的气泡,可通过提高树脂及模具的温度、提高注射速度予以解决。
二.注塑成型时主流道粘模的原因分析注塑成型时主流道粘模的原因及排除方法:1.冷却时间太短,主流道尚未凝固。
2.主流道斜度不够,应增加其脱模斜度。
3.主流道衬套与射嘴的配合尺寸不当造成漏流。
4.主流道粗糙,主流道无冷却井。
5.射嘴温度过低,应提高温度。
三.注塑成型时生产缓慢的原因分析注塑成型时生产缓慢的原因及解决方法如下:1.塑料温度、模具温度高,造成冷却时间长。
2.熔胶时间长,应降低背压压力,少用再生料防止架空,送料段冷却要充分。
3.机台的动作慢,可从油路与电路调节使之适当加快。
4.模具的设计要方便脱模,尽量设计成全自动操作。
5.制作壁厚过大,造成冷却时间过长。
6.喷嘴流涎,妨碍正常生产。
应采用自锁式射嘴,或降低射嘴温度。
7.料筒供热量不足,应换用塑化容量大的机台或加强对料的预热。
四.造成注塑制品不满的原因分析造成注塑制品射料不满的主要原因是缺料和注射压力与速度不妥(包括阻力造成压力过于耗损)。
可能由以下几个方面的原因导致而成:1.注塑机台原因:机台的塑化量或加热率不定,应选用塑化量与加热功率大的机台;螺杆与料筒或过胶头等的磨损造成回料而出现实际充模量不中;热电偶或发热圈等加热系统故障造成料筒的实际温度过低;注射油缸的密封元件磨损造成漏油或回流,而不能达到所需的注射压力;射嘴内孔过小或射嘴中心度调节不当造成阻力过大而使压力消耗.2.注塑模具原因:a.模具局部或整体的温度过低造成入料困难,应适当提高模温;b.模具的型腔的分布不平衡,制件壁厚过薄造成压力消耗过磊而且充模不力。
塑料注塑缺陷及解决方法
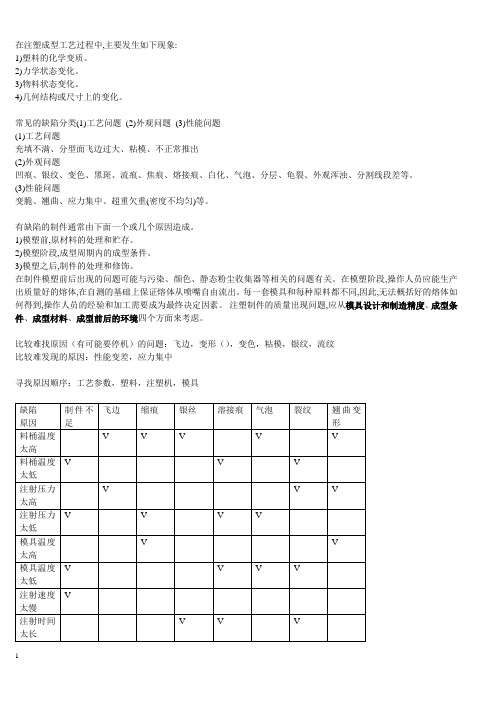
在注塑成型工艺过程中,主要发生如下现象:
1)塑料的化学变质。
2)力学状态变化。
3)物料状态变化。
4)几何结构或尺寸上的变化。
常见的缺陷分类(1)工艺问题(2)外观问题(3)性能问题
(1)工艺问题
充填不满、分型面飞边过大、粘模、不正常推出
(2)外观问题
凹痕、银纹、变色、黑斑、流痕、焦痕、熔接痕、白化、气泡、分层、龟裂、外观浑浊、分割线段差等。
(3)性能问题
变脆、翘曲、应力集中、超重欠重(密度不均匀)等。
有缺陷的制件通常由下面一个或几个原因造成。
1)模塑前,原材料的处理和贮存。
2)模塑阶段,成型周期内的成型条件。
3)模塑之后,制件的处理和修饰。
在制件模塑前后出现的问题可能与污染、颜色、静态粉尘收集器等相关的问题有关。
在模塑阶段,操作人员应能生产出质量好的熔体,在自测的基础上保证熔体从喷嘴自由流出。
每一套模具和每种原料都不同,因此,无法概括好的熔体如何得到,操作人员的经验和加工需要成为最终决定因素。
注塑制件的质量出现问题,应从模具设计和制造精度、成型条件、成型材料、成型前后的环境四个方面来考虑。
比较难找原因(有可能要停机)的问题:飞边,变形(),变色,粘模,银纹,流纹
比较难发现的原因:性能变差,应力集中
寻找原因顺序:工艺参数,塑料,注塑机,模具。
注塑机部分常见问题以及处理
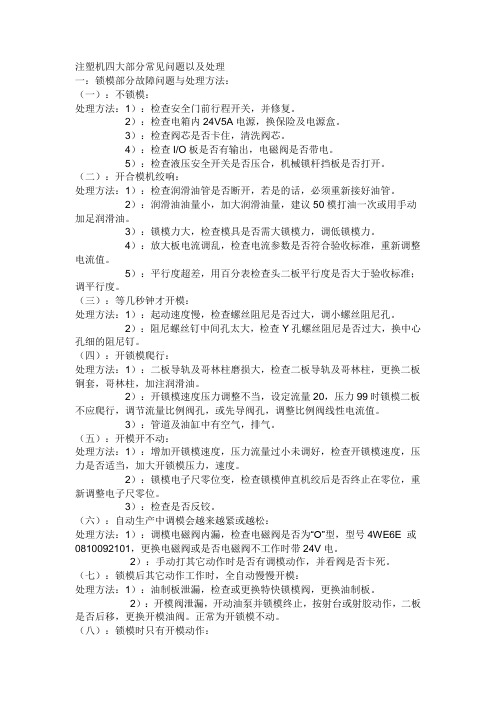
注塑机四大部分常见问题以及处理一:锁模部分故障问题与处理方法:(一):不锁模:处理方法:1):检查安全门前行程开关,并修复。
2):检查电箱内24V5A电源,换保险及电源盒。
3):检查阀芯是否卡住,清洗阀芯。
4):检查I/O板是否有输出,电磁阀是否带电。
5):检查液压安全开关是否压合,机械锁杆挡板是否打开。
(二):开合模机绞响:处理方法:1):检查润滑油管是否断开,若是的话,必须重新接好油管。
2):润滑油油量小,加大润滑油量,建议50模打油一次或用手动加足润滑油。
3):锁模力大,检查模具是否需大锁模力,调低锁模力。
4):放大板电流调乱,检查电流参数是否符合验收标准,重新调整电流值。
5):平行度超差,用百分表检查头二板平行度是否大于验收标准;调平行度。
(三):等几秒钟才开模:处理方法:1):起动速度慢,检查螺丝阻尼是否过大,调小螺丝阻尼孔。
2):阻尼螺丝钉中间孔太大,检查Y孔螺丝阻尼是否过大,换中心孔细的阻尼钉。
(四):开锁模爬行:处理方法:1):二板导轨及哥林柱磨损大,检查二板导轨及哥林柱,更换二板铜套,哥林柱,加注润滑油。
2):开锁模速度压力调整不当,设定流量20,压力99时锁模二板不应爬行,调节流量比例阀孔,或先导阀孔,调整比例阀线性电流值。
3):管道及油缸中有空气,排气。
(五):开模开不动:处理方法:1):增加开锁模速度,压力流量过小未调好,检查开锁模速度,压力是否适当,加大开锁模压力,速度。
2):锁模电子尺零位变,检查锁模伸直机绞后是否终止在零位,重新调整电子尺零位。
3):检查是否反铰。
(六):自动生产中调模会越来越紧或越松:处理方法:1):调模电磁阀内漏,检查电磁阀是否为“O”型,型号4WE6E 或0810092101,更换电磁阀或是否电磁阀不工作时带24V电。
2):手动打其它动作时是否有调模动作,并看阀是否卡死。
(七):锁模后其它动作工作时,全自动慢慢开模:处理方法:1):油制板泄漏,检查或更换特快锁模阀,更换油制板。
注塑制品易出现的缺陷、原因和解决方法 Mold flow

1、欠注欠注(short)也可以称为填充不足或短射,是指聚合物不能完全充满模具型腔的各个角落现象,从(Fill Time)。
产生欠注现象的原因及相关解决方案如下:1、注塑设备选择不合理在选择注射机时,注射机的最大注塑量应该大于产品重量(包括制品、流道、飞边等),要得到较好的效果,注塑总量应保证在最大注塑量的85%以下。
2、聚合物流动性能较差针对这种情况,应该在原料中增加适量的助剂,改善树脂的流动性能,同时,检查原料中的再生料的比例,适当减少用量。
或者考虑改进模具的浇注系统,倒是设置浇道位置、扩大浇口、流道和浇口尺寸以及采用较大的喷嘴等,从而改善模具浇注系统的滞流缺陷。
3、浇注系统实际不合理合理的浇注系统考虑到浇口、流道的平衡,各个型腔内的空腔体积要与浇口大小成正比,从而能够使聚合物同时充满各个型腔,同时浇口位置要选择在厚壁处,也可采用分流道平衡布置的设计方案。
对于浇口或流道小、薄、长的情况,熔料在流动过程中压力损失太大,流动受阻,容易产生欠注现象,针对这种情况应该扩大流道截面和浇口面积,必要时可采取多点进料的方法。
4、料温、模温太低通常情况下,料温与充模长度接近于正比例关系,较低的料温会使熔体的流动性能下降,使得充模长度缩短。
当确认料温较低时,应检查料筒加热器是否完好并设法提高料筒温度。
如果为了防止熔料分解,而不得不采取低温注射时,可适当提高料筒前部区段的温度,或者加快注塑的速度,减少聚合物冷却的时间,但是同时应该注意,注射速度过快可能引起熔体破裂而形成皱纹缺陷。
较低的模温会导致熔融聚合物过早地冷却,从而无法填充整个型腔。
针对这种情况,应该将模具加热到满足工艺要求的温度,并且在注塑初期,应减少冷却介质的流量。
如果模具温度始终较低,应该改变冷却系统的设计方案。
5、注塑喷嘴温度低在注射过程中,喷嘴与模具直接接触,由于模具温度一般低于喷嘴温度,且温差较大,两者频繁接触后使喷嘴温度下降,导致熔料在喷嘴处冷凝(又称干尖)。
注塑产品不良原因分析及解决方案
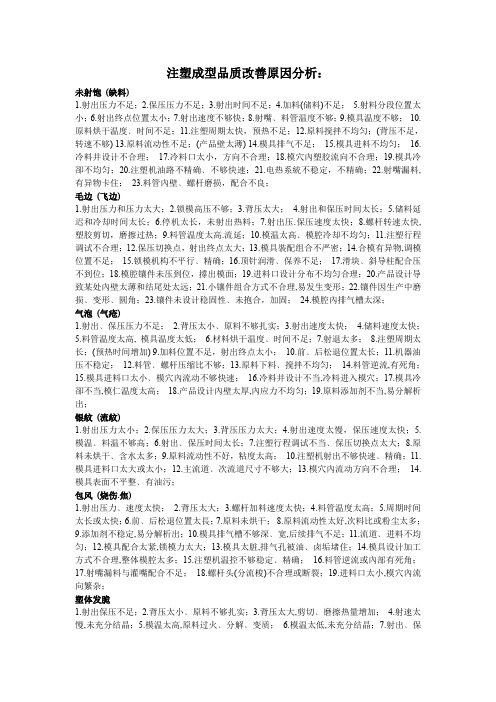
注塑成型品质改善原因分析:未射饱(缺料)1.射出压力不足;2.保压压力不足;3.射出时间不足;4.加料(储料)不足;5.射料分段位置太小;6.射出终点位置太小;7.射出速度不够快;8.射嘴﹑料管温度不够;9.模具温度不够;10.原料烘干温度﹑时间不足;11.注塑周期太快,预热不足;12.原料搅拌不均匀;(背压不足,转速不够) 13.原料流动性不足;(产品壁太薄) 14.模具排气不足;15.模具进料不均匀;16.冷料井设计不合理;17.冷料口太小,方向不合理;18.模穴內塑胶流向不合理;19.模具冷卻不均匀;20.注塑机油路不精确﹑不够快速;21.电热系統不稳定,不精确;22.射嘴漏料,有异物卡住;23.料管內壁﹑螺杆磨损,配合不良;毛边(飞边)1.射出压力和压力太大;2.锁模高压不够;3.背压太大;4.射出和保压时间太长;5.储料延迟和冷却时间太长;6.停机太长,未射出热料;7.射出压.保压速度太快;8.螺杆转速太快,塑胶剪切,磨擦过热;9.料管温度太高.流延;10.模温太高﹑模腔冷却不均匀;11.注塑行程调试不合理;12.保压切换点,射出终点太大;13.模具裝配组合不严密;14.合模有异物,调模位置不足;15.锁模机构不平行﹑精确;16.顶针润滑﹑保养不足;17.滑块﹑斜导柱配合压不到位;18.模腔镶件未压到位,撐出模面;19.进料口设计分布不均匀合理;20.产品设计导致某处內壁太薄和结尾处太远;21.小镶件组合方式不合理,易发生变形;22.镶件因生产中磨损﹑变形﹑圆角;23.镶件未设计稳固性﹑未抱合,加固;24.模腔內排气槽太深;气泡(气疮)1.射出﹑保压压力不足;2.背压太小﹑原料不够扎实;3.射出速度太快;4.储料速度太快;5.料管温度太高, 模具温度太低;6.材料烘干温度﹑时间不足;7.射退太多;8.注塑周期太长;(预热时间增加)9.加料位置不足,射出终点太小;10.前﹑后松退位置太长;11.机器油压不稳定;12.料管﹑螺杆压缩比不够;13.原料下料﹑搅拌不均匀;14.料管逆流,有死角;15.模具进料口太小﹑模穴內流动不够快速;16.冷料井设计不当,冷料进入模穴;17.模具冷卻不当,模仁温度太高;18.产品设计內壁太厚,內应力不均匀;19.原料添加剂不当,易分解析出;银紋(流紋)1.射出压力太小;2.保压压力太大;3.背压压力太大;4.射出速度太慢,保压速度太快;5.模温﹑料温不够高;6.射出﹑保压时间太长;7.注塑行程调试不当﹑保压切换点太大;8.原料未烘干﹑含水太多;9.原料流动性不好,粘度太高;10.注塑机射出不够快速﹑精确;11.模具进料口太大或太小;12.主流道﹑次流道尺寸不够大;13.模穴內流动方向不合理;14.模具表面不平整﹑有油污;包风(烧伤.焦)1.射出压力﹑速度太快;2.背压太大;3.螺杆加料速度太快;4.料管温度太高;5.周期时间太长或太快;6.前﹑后松退位置太長;7.原料未烘干;8.原料流动性太好,次料比或粉尘太多;9.添加剂不稳定,易分解析出;10.模具排气槽不够深﹑宽,后续排气不足;11.流道﹑进料不均匀;12.模具配合太紧,锁模力太大;13.模具太脏,排气孔被油﹑卤垢堵住;14.模具设计加工方式不合理,整体模腔太多;15.注塑机温控不够稳定﹑精确;16.料管逆流或內部有死角;17.射嘴漏料与灌嘴配合不足;18.螺杆头(分流梭)不合理或断裂;19.进料口太小,模穴內流向繁杂;塑体发脆1.射出保压不足;2.背压太小﹑原料不够扎实;3.背压太大,剪切﹑磨擦热量增加;4.射速太慢,未充分结晶;5.模温太高,原料过火﹑分解﹑变质;6.模温太低,未充分结晶;7.射出﹑保压时间不足;8.停机时间和周期时间太长;9.储料时间太长;10.次料添加太多或粉尘太多;11.原料強度﹑韧性不够,粘度不够;12.添加剂不合理,或添加太多;13.原料未充分烘干;14.模穴內结构不均匀,结合处太远;15.模具进料不均匀,冷料井不够;16.产品设计內壁太薄,无辐助加强;17.注塑机温控不稳定﹑精确;18.料管逆流或內部有死角;19.顶出不合理,塑体应力增加,产生破裂;20.塑体后期冷却处理不当,易龟裂;缺料原因:设备方面:(1)注塑机塑化容量小。
注塑工艺 注塑成型缺陷分析及不良解决对策
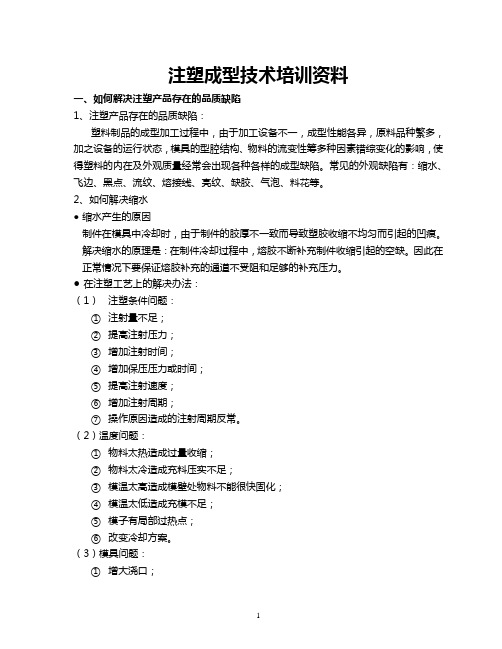
注塑成型技术培训资料一、如何解决注塑产品存在的品质缺陷1、注塑产品存在的品质缺陷:塑料制品的成型加工过程中,由于加工设备不一,成型性能各异,原料品种繁多,加之设备的运行状态,模具的型腔结构、物料的流变性筹多种因素错综变化的影响,使得塑料的内在及外观质量经常会出现各种各样的成型缺陷。
常见的外观缺陷有:缩水、飞边、黑点、流纹、熔接线、亮纹、缺胶、气泡、料花等。
2、如何解决缩水●缩水产生的原因制件在模具中冷却时,由于制件的胶厚不一致而导致塑胶收缩不均匀而引起的凹痕。
解决缩水的原理是:在制件冷却过程中,熔胶不断补充制件收缩引起的空缺。
因此在正常情况下要保证熔胶补充的通道不受阻和足够的补充压力。
●在注塑工艺上的解决办法:(1)注塑条件问题:①注射量不足;②提高注射压力;③增加注射时间;④增加保压压力或时间;⑤提高注射速度;⑥增加注射周期;⑦操作原因造成的注射周期反常。
(2)温度问题:①物料太热造成过量收缩;②物料太冷造成充料压实不足;③模温太高造成模壁处物料不能很快固化;④模温太低造成充模不足;⑤模子有局部过热点;⑥改变冷却方案。
(3)模具问题:①增大浇口;②增大分流道;③增大主流道;④增大喷嘴孔;⑤改进模子排气;⑥平衡充模速率;⑦避免充模料流中断;⑧浇口进料安排在制品厚壁部位;⑨如果有可能,减少制品壁厚差异;⑩模子造成的注射周期反常。
(4)设备问题:①增大注压机的塑化容量;②使注射周期正常;(5)冷却条件问题:①部件在模内冷却过长,避免由外往里收缩,缩短模子冷却时间;②将制件在热水中冷却。
3、如何解决飞边●产生飞边的原因:产品溢边往往由于模子的缺陷造成,其他原因有:注射力大于锁模力、物料温度太高、排气不足、加料过量、模子上沾有异物等。
●如何判断产生飞边的原因:在一般情况下,采用短射的办法。
即在注塑压力速度较低、不用保压的情况下注塑出制件90%的样板,检查样板是否出现飞边,如果出现,则是模具没有配好或注塑机的锁模压力不足,如果没有出现,则是由于注塑条件变化而引起的飞边,比如:保压太大、注射速度太快等。
注塑件常见品质问题及原因分析、解决方法
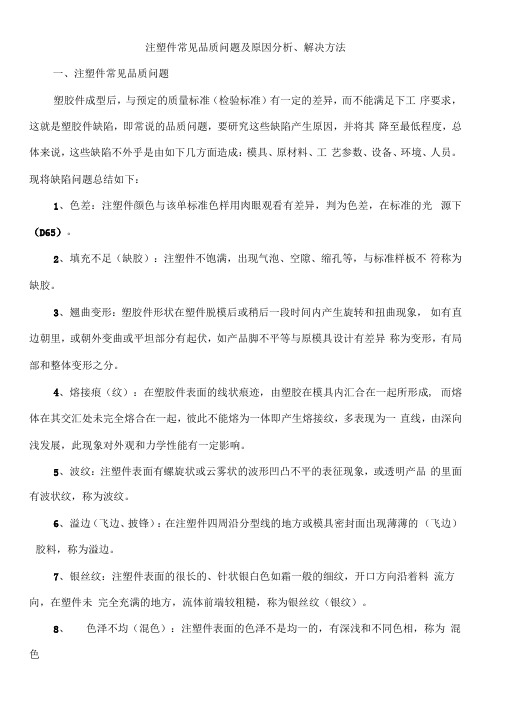
注塑件常见品质问题及原因分析、解决方法一、注塑件常见品质问题塑胶件成型后,与预定的质量标准(检验标准)有一定的差异,而不能满足下工序要求,这就是塑胶件缺陷,即常说的品质问题,要研究这些缺陷产生原因,并将其降至最低程度,总体来说,这些缺陷不外乎是由如下几方面造成:模具、原材料、工艺参数、设备、环境、人员。
现将缺陷问题总结如下:1、色差:注塑件颜色与该单标准色样用肉眼观看有差异,判为色差,在标准的光源下(D65)。
2、填充不足(缺胶):注塑件不饱满,出现气泡、空隙、缩孔等,与标准样板不符称为缺胶。
3、翘曲变形:塑胶件形状在塑件脱模后或稍后一段时间内产生旋转和扭曲现象,如有直边朝里,或朝外变曲或平坦部分有起伏,如产品脚不平等与原模具设计有差异称为变形,有局部和整体变形之分。
4、熔接痕(纹):在塑胶件表面的线状痕迹,由塑胶在模具内汇合在一起所形成, 而熔体在其交汇处未完全熔合在一起,彼此不能熔为一体即产生熔接纹,多表现为一直线,由深向浅发展,此现象对外观和力学性能有一定影响。
5、波纹:注塑件表面有螺旋状或云雾状的波形凹凸不平的表征现象,或透明产品的里面有波状纹,称为波纹。
6、溢边(飞边、披锋):在注塑件四周沿分型线的地方或模具密封面出现薄薄的(飞边)胶料,称为溢边。
7、银丝纹:注塑件表面的很长的、针状银白色如霜一般的细纹,开口方向沿着料流方向,在塑件未完全充满的地方,流体前端较粗糙,称为银丝纹(银纹)。
8、色泽不均(混色):注塑件表面的色泽不是均一的,有深浅和不同色相,称为混色9、光泽不良(暗色):注塑件表面为灰暗无光或光泽不均匀称为暗色或光泽不良。
10、脱模不良(脱模变形):与翘曲变形相似,注塑件成型后不能顺利的从模具中脱出,有变形、拉裂、拉伤等、称为脱模不良。
11、裂纹及破裂:塑胶件表面出现空隙的裂纹和由此形成的破损现象。
12、糊斑(烧焦):在塑件的表面或内部出现许多暗黑色的条纹或黑点,称为糊斑或烧焦。
注塑模具常见故障解决措施
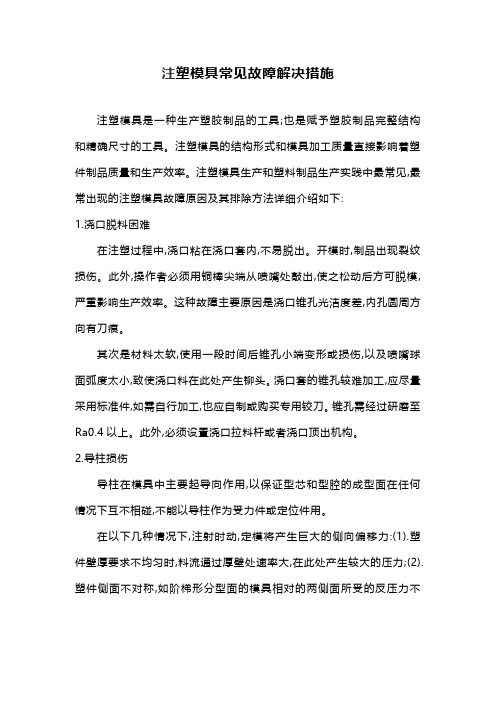
注塑模具常见故障解决措施注塑模具是一种生产塑胶制品的工具;也是赋予塑胶制品完整结构和精确尺寸的工具。
注塑模具的结构形式和模具加工质量直接影响着塑件制品质量和生产效率。
注塑模具生产和塑料制品生产实践中最常见,最常出现的注塑模具故障原因及其排除方法详细介绍如下:1.浇口脱料困难在注塑过程中,浇口粘在浇口套内,不易脱出。
开模时,制品出现裂纹损伤。
此外,操作者必须用铜棒尖端从喷嘴处敲出,使之松动后方可脱模,严重影响生产效率。
这种故障主要原因是浇口锥孔光洁度差,内孔圆周方向有刀痕。
其次是材料太软,使用一段时间后锥孔小端变形或损伤,以及喷嘴球面弧度太小,致使浇口料在此处产生铆头。
浇口套的锥孔较难加工,应尽量采用标准件,如需自行加工,也应自制或购买专用铰刀。
锥孔需经过研磨至Ra0.4以上。
此外,必须设置浇口拉料杆或者浇口顶出机构。
2.导柱损伤导柱在模具中主要起导向作用,以保证型芯和型腔的成型面在任何情况下互不相碰,不能以导柱作为受力件或定位件用。
在以下几种情况下,注射时动,定模将产生巨大的侧向偏移力:(1).塑件壁厚要求不均匀时,料流通过厚壁处速率大,在此处产生较大的压力;(2).塑件侧面不对称,如阶梯形分型面的模具相对的两侧面所受的反压力不相等。
3.大型模具因各向充料速率不同,以及在装模时受模具自重的影响,产生动﹑定模偏移。
在上述几种情况下,注射时侧向偏移力将加在导柱上,开模时导柱表面拉毛,损伤,严重时导柱弯曲或切断,甚至无法开模。
为了解决以上问题在模具分型面上增设高强度的定位键四面各一个,最简便有效的是采用圆柱键。
导柱孔与分模面的垂直度至关重要.在加工时是采用动,定模对准位置夹紧后,在镗床上一次镗完,这样可保证动,定模孔的同心度,并使垂直度误差最小。
此外,导柱及导套的热处理硬度务必达到设计要求。
4.动模板弯曲模具在注射时,模腔内熔融塑料产生巨大的反压力,一般在600~1000公斤/厘米。
模具制造者有时不重视此问题,往往改变原设计尺寸,或者把动模板用低强度钢板代替,在用顶杆顶料的模具中,由于两侧座跨距大,造成注射时模板下弯。
- 1、下载文档前请自行甄别文档内容的完整性,平台不提供额外的编辑、内容补充、找答案等附加服务。
- 2、"仅部分预览"的文档,不可在线预览部分如存在完整性等问题,可反馈申请退款(可完整预览的文档不适用该条件!)。
- 3、如文档侵犯您的权益,请联系客服反馈,我们会尽快为您处理(人工客服工作时间:9:00-18:30)。
塑料知识塑料注塑成型故障排除不良现象的原因及处理办法1.充填不足2.溢料3.气孔4.波纹5.银条纹6.表面晕喑7.融合线8.气泡9.黑条纹及烧痕10.龟裂11.离模溢料12.弯曲13.脱模不良14.直浇口的脱模不良15.材料的叠边不良不良现象及其原因处理办法1、充填不足[1] 成形品的体积过大i)要使用成形能力大的成形机。
ii)使用成形多数个成品的模具时,要关闭内腔。
[2] 流道、浇口过小i)扩展流道或浇口。
ii)放快射出速度。
iii)增强射出压力。
[3] 喷头温度低 i)喷射空气,以排出冷却的材料。
ii)升高材料的温度。
iii)改用大型喷头。
[4] 材料的温度或者射出压力低i)升高材料的温度。
ii)增强射出压力。
iii)添加外部润滑。
[5] 内腔里的流体流动距离过长 i)设置冷余料洼坑。
ii)升高材料的温度。
[6] 模具温度低了 i)升高模具温度。
ii)放快射出速度。
iii)增强射出压力。
[7] 射出速度慢了i)加快射出速度。
ii)升高材料的温度。
[8] 材料的供给量过少 i)如属螺桨式装置,增加增塑量;而采用柱塞方式时,则增加从料斗落下的数量。
ii)减少外部润滑,改进螺桨的加工条件。
[9] 排气不良放慢射出速度。
ii)将填充不良的位置改为镶件结构或在模具上加设排气槽。
iii)改变胶口的位置iiii)改变成形品的厚度。
2、溢料[1]锁模力不足 i)加强锁模力。
ii)降低射出压力。
iii)改用大型成形机。
[2] i)确实调整好连杆。
i)补修导推杆或导钉梢的部位ii)修正模具安装板。
增加支撑柱。
iii)使用轨距联杆的强度足够的成机i)确实做好模具面的贴合。
[3]模具面的杂质i)除去杂物[4]i)使用大型成形机。
[5]i)降低材料的温度。
ii)放慢射出速度。
[6]材料供给量过剩i)调整好供给量。
[7]射出压力高i)降低射出压力。
ii)降低材料的温度3气孔在材料为充分干燥时,是挥发物或空气所致;大多时候发生在产品胶厚的位置,实际是材料的收缩引起的真空气泡[1] i)将流道或浇口扩展。
ii)增强射出压力。
[2] 成形品的壁厚差大i)尽量使壁厚度要均匀。
ii)要使壁厚差不显著。
[3] 材料的温度高i)降低材料的温度。
ii)要改进发生气孔的部位的冷却条件。
[4] 离浇口的流动距离长i)增强射出压力。
ii)加快射出速度。
iii)在成形品上设置棱或厚层部位。
[5] 脱模过早i)延长冷却时间。
[6] 射出压力低i)增强射出压力。
[7] i)延长冷却时间。
ii)降低模具温度。
[8] 保压不充分i)延长保压时间。
ii)增强保压压力。
4 波纹[1]材料流动不畅 i)升高材料的温度。
ii)换用流动性高的材料。
iii)增强射出压力。
iiii)设定冷料井。
加速射出速度。
[2]模具温度低i)采用热油机或热水机提高模温。
[3]进浇口过小i)加大进浇口。
ii)升高材料的温度。
5 银条纹[1] i)使材料充分干燥。
ii)使用料斗式装载机。
[2]材料的温度过高i)降低材料的温度。
ii)放慢射出速度。
[3]模具温度低i)升高模具温度。
[4]排气不良i)在模具耦合面加上排气用的条缝。
ii)放宽模具与推挺钉梢的间隙。
iii)设置真空排气结构间隙[5] i)放大浇口或流道。
ii)消除急剧的壁厚差现象。
iii)将耦合部位加圆,防止乱流现象的产生。
iiii)降低注射速度和注射压力。
[6]模具面上的水分或挥发成分防止模具被过分冷却。
ii)减少润滑剂或脱模剂。
[8]混入夹杂的材料i)严格材料的管理。
[9] i)降低旋转数。
ii)升高增塑中的背压。
6.表面晕暗[1] 润滑或挥发成分过多i)材料要干燥好。
ii)减少润滑剂。
iii)升高材料的温度。
[2]i )升高模具温度。
i)减少使用量。
7 融合线------实际是2股或多股材料汇合时,材料的融合线。
与材料汇合时,材料的粘度有很大的关系。
从理论上讲,材料的汇合肯定会产生融合线,只是明显程度的不同而已。
[1]材料的温度 i)升高材料的温度。
和使用较高的模具温度。
ii)加速射出速度。
iii)增强射出压力。
[2]改用圆形或扇形进胶口。
增加胶口的数量。
ii)扩大浇口iii)更改浇口位置,使融合线的位置改变。
[3]材料里的挥发成分或脱模剂过多 i材料要干燥好ii)减少脱模剂,在材料的汇合处增加排气槽。
iii)改善内腔里的排除条件[4]材料的凝固快 i)升高材料的温度ii)升高模具温度iii)增强射出压力[5]成形品的设计不良 i )加速射出速度 )设置余料洼坑i)在融合部位设棱ii)加厚成形品的壁层8 气泡------在材料为充分干燥时,是挥发物或空气所致;大多时候发生在产品胶厚的位置,实际是材料的收缩引起的真空气泡[1]浇口或流道过小i)扩大浇口或流道ii)将进胶位置改到容易产生收缩或气泡的位置。
iii)提高模具的温度。
[2]射出压力低i)增强射出压力ii)延长保压时间[3] i)充分干燥好材料[4]成形品的设计不良 i)消除壁厚的剧变部位ii)增强保压时的压力[5]排气不良 i)在容易产生捕捉空气的部位设置推挺钉ii)实行真空排气9 黑条纹及烧痕------实际是材料受到高温、高压的作用出现分解烧焦的现象。
[1]材料过热 i)降低材料的温度ii)缩短成形周期iii)使用小型成形机.[2] i )减少螺桨的旋转数 i)消除炮筒内螺杆和炮筒的伤痕ii)消除螺桨的伤痕iii)检查螺杆止流环是否有破损[3]模具的设计不良 .浇口小。
排气不良 i)扩大浇口ii)放慢射出速度iii)扩大推挺钉与模具的间隙iii)在模具耦合面加上排气用的条缝10.龟裂------实际是材料由无规则状态被注塑成型为特定形状时,内部的分子结构产生的内应力所致。
[1]射出压力过强[2]材料的流动不畅[3][4][5]保压的调整不良[6][7]11.离模溢料------[1][2][3]材料的温度低[4]模具温度低12.弯曲------实际是材料的收缩不均匀导致。
[1]冷却不充分[2]直浇口的脱模不良[3]冷却不均匀[4]射出压力不适宜[5]浇口位置不适当[6]模芯偏倚[7]13 脱模不良[1]射向压力高[2][3]模具的设计不良○ 来自模芯的通气不良○14 直浇口的脱模不良[1]模具的安装不良[2]直浇口的形状不良15 材料的叠边不良[1]料斗的落料不佳[2]粉碎的回收材料拌入量过多[3]外部润滑剂过剩i )采用真空排气法i)减弱射出压力i)升高材料的温度ii)使用模具机提高模具温度iii)避免急剧的壁厚变化i )将边角部分加圆i)改变推挺钉的位置ii)将模具分割为三块i)扩大推挺钉与模具的间隙ii)将模具分割为三块iii)采用压缩空气脱模方法i)减少保压压力ii)缩短保压时间iii)使用浇口阀i )喷头上使用单向阀i)进行成形品的退火后处理,对于有金属镶件的塑料成型,需预先加热镶件。
i)不用侵蚀性溶剂擦拭内腔,洗涤嵌衬 i)修正浇口,使之向料薄方向流去ii)扩大浇口的断面积iii)改为翼片浇口i)减慢射出速度i)升高材料的温度i)升高模具温度 i)延长冷却时间ii)降低模具温度i)请参阅"直浇口的脱模不良"一节i)尽量使成形品的壁厚均匀ii)减少型腔与模蕊温差,产品会向温度偏高的模具方向弯曲变形。
iii)缩小棱i )修正冷却水槽沟i)调到弯曲最小的压力,同时注意分段压力对产品变形影响。
i)设置到薄层部位i)修正模蕊ii)改为多点浇口i)改为多点浇口ii)扩大浇口 i)减弱射出压力。
ii)降低材料的温度iii)降低模具温度。
i)升高内腔一侧的模具温度,降低模蕊一侧的温度。
i)扩大推挺钉与模具的间隙。
ii)使用脱模剂。
iii)实行压缩空气脱模。
i)降低射出压力。
ii)改造模具。
i)消除喷孔与直浇口孔的误差。
i)扩大直浇口。
ii)扩大直浇口的锥形角度。
ii直浇口基层部位大时,要使冷却灵敏。
i)i )在喷头与直浇口推杆之间插入热板。
i)为料斗配上震荡器螺桨滤清器。
ii)增多外部润滑剂。
i)同上。
ii)筛选粉状物。
i)减少润滑剂的数量。
ii)采用二轴螺桨式射出成形机。
塑料制品的尺寸精度等级SJ1372-78公称尺寸精度等级1 2 3 4 5 6 7 8公差数值-3 0.04 0.06 0.08 0.12 0.16 0.24 0.320.48>3-6 0.05 0.07 0.08 0.14 0.18 0.28 0.360.56>6-10 0.06 0.08 0.10 0.16 0.20 0.32 0.400.64>10-14 0.07 0.09 0.12 0.18 0.22 0.36 0.440.72>14-18 0.08 0.10 0.12 0.20 0.26 0.40 0.480.80>18-24 0.09 0.11 0.14 0.22 0.28 0.44 0.560.88>24-30 0.10 0.12 0.16 0.24 0.32 0.48 0.640.96>30-40 0.11 0.13 0.18 0.26 0.36 0.52 0.721.0>40-50 0.12 0.14 0.20 0.28 0.40 0.56 0.801.2>50-65 0.13 0.16 0.22 0.32 0.46 0.64 0.921.4>65-85 0.14 0.19 0.26 0.38 0.52 0.76 1.01.6>80-100 0.16 0.22 0.30 0.44 0.60 0.88 1.21.8>100-120 0.18 0.25 0.34 0.50 0.68 1.0 1.42.0>120-140 0.28 0.38 0.56 0.76 1.1 1.52.2>140-160 0.31 0.42 0.62 0.84 1.2 1.72.4>160-180 0.34 0.46 0.68 0.92 1.4 1.82.7>180-200 0.37 0.50 0.74 1.0 1.5 2.03.0>200-225 0.41 0.56 0.82 1.1 1.6 2.23.3>225-250 0.45 0.62 0.90 1.2 1.8 2.43.6>250-280 0.50 0.68 1.0 1.3 2.0 2.64.0>280-315 0.55 0.74 1.1 1.4 2.2 2.84.4>315-355 0.6 0.82 1.2 1.6 2.4 3.2 4. 8>355-400 0.65 0.9 1.3 1.8 2.6 3.6 5. 2>400-450 0.70 1.0 1.4 2.0 2.8 4.0 5. 6>450-500 0.80 1.1 1.6 2.2 3.2 4.4 6. 4注:1、本标准的精度等级分成1-8共8个等级。