铝合金管材的单道次空拉拔变形机理
拉拔加工的原理与机制

拉拔加工的原理与机制在机械制造领域,拉拔加工是一种常用的金属变形加工方法,也是制造各种金属制品的重要工艺之一。
拉拔加工的本质是通过材料的轴向拉伸,不断减小截面积,从而使金属材料得到一定的纵向延伸,并且在过程中改变其微观结构,获得更好的力学性能。
本文将从原理和机制两方面探讨拉拔加工的工艺特点和应用价值。
一、拉拔加工的原理1. 材料性质拉拔加工是一种利用金属材料在强大拉应力作用下进行塑性变形的工艺,并将金属材料的截面积逐渐缩小。
所以,拉拔过程中材料的塑性应变应该足够大,才能使材料中的晶粒受到彻底的塑性变形,这是保证加工质量和产品牢固性的重要因素。
2. 模具设计通过调整拉拔模具的大小和形状,可以控制金属材料在加工过程中的整体变形。
在设计模具时,必须保证金属材料能够贴合模具表面,并在加工过程中不与模具表面发生滑动,这是避免合金板断裂的关键所在。
此外,适当调整模具表面的表面形状和磨损程度,可以明显改变加工过程中金属材料的形变轨迹和应力分布规律,影响拉伸强度和延展性能。
3. 材料的温度金属材料的塑性和延展性在不同温度下表现出不同的特点。
在触发加工前,需要通过加温或冷却技术将材料置入必要的温度区间,并保持温度的稳定性和一致性,以保证拉拔加工过程不受温度变化的干扰,避免材料裂纹和形变。
二、拉拔加工的机制1. 晶体结构变化材料在拉伸过程中会进行金属晶体的边界移动和实际变化的骨干晶体的扭曲和移动。
在这种情况下,晶界上会产生约束,从而防止晶体继续扭曲和移动。
一定的拉伸应力可以抵消约束,使晶体继续扭曲和移动,因此,晶界实际上充当了内部约束的角色,并有助于材料整体变形。
2. 物理力学影响拉拔过程中的材料变形主要受拉伸力的引导,使截面积不断缩小。
除此之外,加工过程中受到拉力的作用,还会使材料表面和内部发生强烈的拉应力,并影响材料的力学性能和形变机制。
基于这种影响,拉拔加工通常被用来制造需要高拉伸强度和很小延展性的金属制品,例如铜线和钢丝等材料。
铝合金的变形工艺及强化机理
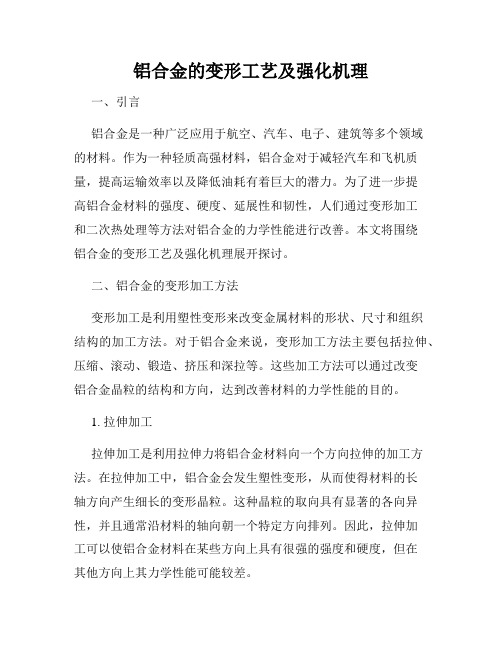
铝合金的变形工艺及强化机理一、引言铝合金是一种广泛应用于航空、汽车、电子、建筑等多个领域的材料。
作为一种轻质高强材料,铝合金对于减轻汽车和飞机质量,提高运输效率以及降低油耗有着巨大的潜力。
为了进一步提高铝合金材料的强度、硬度、延展性和韧性,人们通过变形加工和二次热处理等方法对铝合金的力学性能进行改善。
本文将围绕铝合金的变形工艺及强化机理展开探讨。
二、铝合金的变形加工方法变形加工是利用塑性变形来改变金属材料的形状、尺寸和组织结构的加工方法。
对于铝合金来说,变形加工方法主要包括拉伸、压缩、滚动、锻造、挤压和深拉等。
这些加工方法可以通过改变铝合金晶粒的结构和方向,达到改善材料的力学性能的目的。
1. 拉伸加工拉伸加工是利用拉伸力将铝合金材料向一个方向拉伸的加工方法。
在拉伸加工中,铝合金会发生塑性变形,从而使得材料的长轴方向产生细长的变形晶粒。
这种晶粒的取向具有显著的各向异性,并且通常沿材料的轴向朝一个特定方向排列。
因此,拉伸加工可以使铝合金材料在某些方向上具有很强的强度和硬度,但在其他方向上其力学性能可能较差。
2. 压缩加工压缩加工是将铝合金材料向一个方向施加压缩力的加工方法。
与拉伸加工不同的是,压缩加工会使铝合金晶粒在横截面处变形,从而产生大量的位错和晶间剪切带。
这些位错和晶间剪切带可以增加材料的强度和硬度,并且使材料更加均匀。
3. 滚动加工滚动加工是通过使铝合金材料在滚筒轧压下产生纵向和横向的压缩变形来改善材料的性能。
由于滚压过程中铝合金晶粒发生了强烈的位错和晶界移动,因此形成了一种扭曲的组织结构。
这种扭曲的结构可以增加材料的强度和硬度,提高其耐疲劳性能和韧性。
4. 锻造加工锻造加工是通过让铝合金材料在热态或冷态下受到重复的变形加载来改善材料的性能。
粗晶的铝合金材料可以在经过高温高压的锻造加工后,得到细晶体的组织结构,从而具有更好的机械性能。
在锻造过程中,铝合金材料的晶粒也会沿着加载方向得到排列,形成一种各向同性的组织结构。
拉拔铝管基础
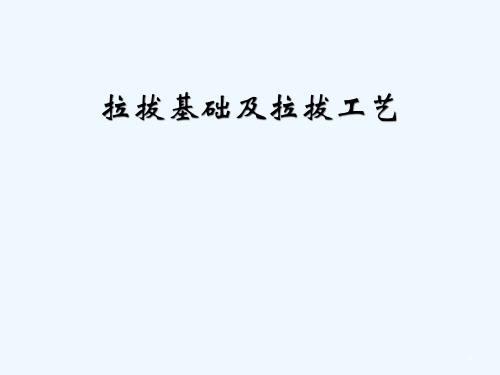
大家有疑问的,可以询问和交流
可以互相讨论下,但要小声点
3 拉拔历史与发展趋向(了解)
• 3.1 拉拔历史 • 拉拔具有悠久的历史,在公元前20~30世纪,就
出现了把金块锤锻后,通过小孔,用手工拉制成 细金丝,在同一时期发现了类似拉线模的东西。 公元前15~17世纪,在亚述、巴比伦、腓尼基等 进行了各种贵金属的拉线,并把这些贵金属线用 于装饰品。公元8~9世纪,能制成各种金属线。 公元12世纪,有锻线工与拉线工之分,前者是通 过锤锻,后者是通过拉拔制线材,人们认为就是 从这个时候起确立了拉拔加工。
• (4)游动芯头拉拔
• 在拉拔过程中,芯头不固定在芯杆上,而 是靠本身的外形建立起来的力平衡被稳定 在模孔中。游动芯头拉拔时管材拉拔较为 先进的一种方法,非常适用于长管和盘管 生产,对于提高拉拔生产率、成品率和管 材内表面质量极为有利。但是与固定芯头 拉拔相比,游动芯头拉拔的难度较大,工 艺条件和技术要求较高,配模有一定限制, 故不可能完全取代固定芯头拉拔。
• (3)工作带
• 工作带的作用是使制品获得稳定而精确的形 状与尺寸。工作带的合理形状是圆柱形。
• (4)出口带
• 出口带的作用是防止金属出模孔时被划伤和 模子定径带出口端因受力而引起的剥落。
1.1.2 拉模的材料
• (1)金刚石 • (2)硬质合金(常用) • (3)钢 • (4)铸铁 • (5)刚玉陶瓷模
2 芯头
• 2.1 芯头的结构与尺寸 • 2.1.1 固定短芯头 • 固定短芯头的形状一般是圆柱形的。在拉
铝合金薄壁零件高速铣削发生变形的机理分析

铝合金薄壁零件高速铣削发生变形的机理分析摘要:铝合金薄壁部件存在质轻、强度高的结构现象,因此在肮空、汽车以及模具规模化管理领域中存在技术开发优势,但这类部件形态又广泛吸收多曲线、深加工技术特征,因此在高速加工与结构延展流程中易引发振动、变形危机。
按照上述隐患状况观察,本文主要联合铝合金材质作为补充样本,全面落实薄壁框体变形机理研究工作,将特定工序下的操作技术修葺完全,进而稳固后期产业科学布局的潜力水准。
前言:铣削加工技术属于某种复杂形态的工程类别,其间动态化的振动状况研究、改良工作,具体围绕切削力学、材料学原理进行综合审视。
在现代化技术规范体制下,大多数工程规范技术问题通常依靠两类途径进行充分应对,包括假设简化与有限单元分析法。
目前计算机管理媒介已经成为机械部件改良应用流程不可获缺的调试工具,为了积极稳固数值模拟操纵实力,技术人员就必须广泛收集高速铣削振动下的大量验证数据。
整体流程在有限元分析流程的融入作用下,有效规避了时间漫长与规模成本数量沉重的危机状况。
1 有限元操纵模式论述这类调试途径主要运用数值科学计算手段进行工程项目转接,并且将弹性理论与计算机模拟软件进行有机搭配,充分稳固数据计算的精准效用和可利用价值。
现在工程项目内部常用数值规划手段包括有限、边界、离散单元模式,其中尤以有限单元调试方案实用地位深厚。
其基本布置原理就是将问题进行单元拆解,不同个体之间依靠稳固节点搭接,其实就是运用无限自由度连续体力学原理实施节点参数计算流程。
因为不同单元结构形态较为简易,涉及平衡关系与节点关联方程便自然轻松提取,之后配合科学搭配与方程组规整手段进行边界条件解析。
这类技术基本将试验周期漫长与整体成本费用高昂的瓶颈限制壁垒冲破,保证大量模拟实验的同步运行速率,技术人员只需在监督过程中加以适量修正改良,就可以稳固树立相关数学搭配与制备模型标准。
结合薄壁框体结构进行侧壁、腹板铣削加工流程的演练,实际成形厚度基本稳定在1.5毫米范围内部,比较符合薄壳结构规范要求,完全可以依照ANSYS 中的壳单元SHELL进行模拟操作。
2A50铝合金单道次等通道转角挤压工艺研究_谭险峰[1]
![2A50铝合金单道次等通道转角挤压工艺研究_谭险峰[1]](https://img.taocdn.com/s3/m/7fee9221453610661ed9f4d9.png)
第33卷第6期V ol .33 N o .6FORGIN G &STAM PIN G TE CH NOLOGY2008年12月Dec .20082A 50铝合金单道次等通道转角挤压工艺研究谭险峰,陈 伟,熊洪淼,李金华(南昌航空大学材料科学与工程学院,江西南昌330063)摘要:等通道转角挤压技术是一种有效细化材料的微观组织的新工艺。
本文选择通道转角、挤压速度、润滑条件、变形温度等4个工艺参数为变量,根据选定的正交试验表对9组不同参数组合方案进行单道次挤压试验,通过极差分析,获得了4个参数中影响2A50铝合金晶粒细化程度的先后顺序,同时找出了影响晶粒细化的主要因素,提出了一个较优化的水平组合方案,为后续的多道次工艺试验提供了科学的依据。
关键词:等通道转角挤压工艺;工艺参数;晶粒细化;铝合金中图分类号:TG376.2 文献标识码:A 文章编号:1000-3940(2008)06-0063-03Study of 2A50aluminum alloys in single -path equal channel angular extrusion processTAN Xian -feng ,CHEN Wei ,X IONG Hong -miao ,LI Jin -hua(Scho ol of M aterials Science a nd Enginee ring ,N anchang Hangko ng U niver sity ,N anchang 330063,China )Abstract :Equal channel angular ext rusion is an advanced technology tha t can refine the micro st ruc ture of materials .N ine se ts of e xperiments w ere carried out for 2A50aluminum alloy s accor ding to selec ted o r thog onal ex periment scheme during the sing le -path equal channel a ng ular ex trusion .F our main pr ocess parameter s we re g iv en in the ex pe ri -ments ,including channel angle ,ex trusion speed ,lubrication co ndition a nd forming tempe rature .T he influence se -quence of the abov e four pa rameters on the g rain -refining were o btained and the optimum scheme w as put forw ar d by a ra ng e analysis to gr ain size ,w hich o ffered the scientific reference fo r multi -pa th ex pe riments .Keywords :equal channel ang ular ex tr usio n ;process par ameter ;g r ain refinement ;aluminum alloy收稿日期:2008-04-21;修订日期:2008-07-21基金项目:江西省教育厅科学技术研究项目资助(DB200701053)作者简介:谭险峰(1968-),男,博士,副教授电子信箱:tan xf niat @1 引言2A50铝合金是一种有着广泛工业应用前景的金属结构材料,属难变形合金[1]。
3.4 拉拔

思考题
什么是拉拔加工?有何特点?有哪些基本加工方法? 1. 什么是拉拔加工?有何特点?有哪些基本加工方法? 简述拉拔工艺过程。 2. 简述拉拔工艺过程。 有人说挤压、 3. 有人说挤压、拉拔仅表现在对金属坯料施加外力的方 向不同,你说对吗?请说明之。 向不同,你说对吗?请说明之。
1. 拉拔配模 (1) (1)管、棒、线材拉拔配模 这类材料拉拔前后均为园形,拉拔配模的主要任务: 这类材料拉拔前后均为园形,拉拔配模的主要任务: 确定拉拔次数n 确定拉拔次数n 道次变形量 道次变形量 变形
为简单起见, 为简单起见,常用均等道次变形率法计算 设:总断面压缩率 rt % 道次断面压缩率 r % 拉拔道次 n
拉拔方法????????????????????????????????加工或塑性差的材料??长芯杆拉拔空拉线材型材棒材实心材拉拔mow?????????????????????空心异型材扩径拉拔顶管较先进方法适于长管游动芯头拉拔径长尺寸广泛应用不适于小直固定芯头拉拔管材空心材拉拔3
3.4 拉拔 . 3.4.1 拉拔原理与方法 1. 拉拔原理 ① 什么是拉拔? 什么是拉拔? 在外加拉力作用下, 在外加拉力作用下,使 金属通过摸孔产生塑性 变形,获得与摸孔形状、 变形,获得与摸孔形状、 尺寸相同的制品的加工 方法,称之为拉拔。 方法,称之为拉拔。
3.4.3 拉拔工艺 拉拔加工一般需要多道次加工才能完成。涉及的过程包括: 拉拔加工一般需要多道次加工才能完成。涉及的过程包括: 确定拉力大小。即实现拉拔的必要条件。 1) 确定拉力大小。即实现拉拔的必要条件。施加在拉件断 金属出模口处σ 否则出现细颈, 面上拉力 σl<金属出模口处σS,否则出现细颈,拉 断。一般采用
拉拔成形原理演示
拉拔加工的特点: ② 拉拔加工的特点: 1) 拉拔制品的尺寸精度高,表面粗糙度低 拉拔制品的尺寸精度高, 工具与设备简单,维护方便, 2) 工具与设备简单,维护方便,一机多用 适用于连续高速生产断面尺寸小的长尺产品(Al、Cu拉 3) 适用于连续高速生产断面尺寸小的长尺产品(Al、Cu拉 拔纤维直径可小至10um; SS可小至O.5um) 可小至O.5um 拔纤维直径可小至10um; SS可小至O.5um) 10um 变形道次多,工艺过程长。 4) 变形道次多,工艺过程长。 拉拔时变形区内的应力状态为:两向压缩一向拉伸。 5) 拉拔时变形区内的应力状态为:两向压缩一向拉伸。
铝合金材料的变形行为研究
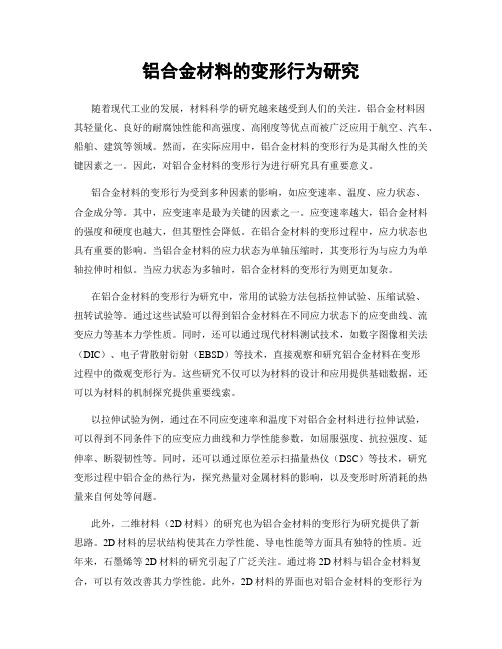
铝合金材料的变形行为研究随着现代工业的发展,材料科学的研究越来越受到人们的关注。
铝合金材料因其轻量化、良好的耐腐蚀性能和高强度、高刚度等优点而被广泛应用于航空、汽车、船舶、建筑等领域。
然而,在实际应用中,铝合金材料的变形行为是其耐久性的关键因素之一。
因此,对铝合金材料的变形行为进行研究具有重要意义。
铝合金材料的变形行为受到多种因素的影响,如应变速率、温度、应力状态、合金成分等。
其中,应变速率是最为关键的因素之一。
应变速率越大,铝合金材料的强度和硬度也越大,但其塑性会降低。
在铝合金材料的变形过程中,应力状态也具有重要的影响。
当铝合金材料的应力状态为单轴压缩时,其变形行为与应力为单轴拉伸时相似。
当应力状态为多轴时,铝合金材料的变形行为则更加复杂。
在铝合金材料的变形行为研究中,常用的试验方法包括拉伸试验、压缩试验、扭转试验等。
通过这些试验可以得到铝合金材料在不同应力状态下的应变曲线、流变应力等基本力学性质。
同时,还可以通过现代材料测试技术,如数字图像相关法(DIC)、电子背散射衍射(EBSD)等技术,直接观察和研究铝合金材料在变形过程中的微观变形行为。
这些研究不仅可以为材料的设计和应用提供基础数据,还可以为材料的机制探究提供重要线索。
以拉伸试验为例,通过在不同应变速率和温度下对铝合金材料进行拉伸试验,可以得到不同条件下的应变应力曲线和力学性能参数,如屈服强度、抗拉强度、延伸率、断裂韧性等。
同时,还可以通过原位差示扫描量热仪(DSC)等技术,研究变形过程中铝合金的热行为,探究热量对金属材料的影响,以及变形时所消耗的热量来自何处等问题。
此外,二维材料(2D材料)的研究也为铝合金材料的变形行为研究提供了新思路。
2D材料的层状结构使其在力学性能、导电性能等方面具有独特的性质。
近年来,石墨烯等2D材料的研究引起了广泛关注。
通过将2D材料与铝合金材料复合,可以有效改善其力学性能。
此外,2D材料的界面也对铝合金材料的变形行为产生重要的影响。
铝合金材料加工中的变形机理与控制

铝合金材料加工中的变形机理与控制在当今的工业生产中,铝合金材料的加工已成为不可或缺的一部分。
由于铝合金材料具有轻质、高强度、耐腐蚀等优点,并且价格相对便宜,因此在汽车、飞机、电子、建筑等领域都有着广泛的应用。
然而,在铝合金材料加工过程中常常会出现变形的问题,这不仅影响了产品的质量,还会增加生产成本。
因此,研究铝合金材料加工中的变形机理与控制是提高生产效率和降低生产成本的重要手段。
一、铝合金材料的变形机理铝合金材料在加工过程中经历了许多形变。
其主要的形变方式有拉伸、压缩、弯曲、剪切等。
不同的形变方式会产生不同的变形机理。
下面主要介绍拉伸和压缩这两种最常见的形变方式。
1. 拉伸变形在铝合金材料的拉伸过程中,材料受到的拉伸力会使材料逐渐拉长,并且横截面积逐渐缩小。
这时候,材料会产生应变,即形变量与原长的比值。
应变又可分为线性应变和非线性应变两种。
线性应变是指拉伸应变与应力成比例,而非线性应变则是指应变随应力呈现出曲线关系。
材料的弹性模量是材料的线性应变和应力的比值,它是用来描述材料抵抗外力变形的能力。
2. 压缩变形与拉伸变形相比,材料在压缩变形过程中受到相反的作用力。
当材料受到压缩力时,横向的体积会缩小,而材料的长度会变短,从而产生应变。
与拉伸变形不同的是,材料在压缩过程中易发生屈曲和剪切,因此压缩变形所产生的应力比拉伸变形更加复杂。
二、铝合金材料变形的控制方法由于变形会对铝合金材料的结构和性质产生影响,因此必须采取一些控制措施来减少或避免变形。
下面介绍一些常见的控制方法。
1. 降低加工温度铝合金的塑性随着温度的升高而增加,因此在加工过程中降低材料的温度可以减少变形。
降低温度的方法有两种:一是通过在加工前对材料进行冷处理,使其温度降至室温以下,然后再进行加工,这种方法适用于小尺寸零件的生产;二是采用低温加工方法,在加工过程中持续降温,控制加工温度在一定范围内,从而减少变形。
2. 选择适当的加工方式在铝合金材料加工过程中,不同的加工方式对材料的变形具有不同的影响。
金属塑性加工方法——拉拔(一)

金属塑性加工方法拉拔(一)——拉拔的基本概念1、拉拔的概念在外加拉力作用下,迫使金属坯料通过模孔,已获得相应形状与尺寸制品的塑性加工方法称之为拉拔,如下图所示,拉拔是管材、棒材、型材以及线材的主要生产方法之一。
图1 拉拔示意图1-坯料;2-模具;3-制品2、拉拔分类按制品截面形状分为:实心材拉拔与空心材拉拔。
(1)实心材拉拔实心材拉拔主要包括棒材、型材及线材的拉拔。
(2)空心材拉拔空心材拉拔主要包括管材及空心异型材的拉拔。
对于空心材拉拔有如下图2所示的几种基本方法。
1)空拉拉拔时管坯内部不放芯头,通过模孔后外径减小,管壁一般会略有变化,如图2-a所示。
经多次空拉的管材,内表面粗糙,严重者产生裂纹。
空拉适用于小直径管材、异型管材、盘管拉拔以及减径量很小的减径与整形拉拔。
2)长芯杆拉拔将管坯自由地套在表面抛光的芯杆上,使芯杆与管坯一起拉过模孔,以实现减径和减量的加工方法称之为长芯杆拉拔,如图2-b所示。
芯杆的长度应略大于管子的长度,在拉拔一道次之后,多需要用脱管法或滚轧使之扩径的方法取出芯杆。
长芯杆拉拔的特点是道次加工率较大,但由于需要准备很多不同直径的长芯秆并且増加脱管工序,因此在通常生产中很少采用。
长芯杆拉拔适用于薄壁管材以及塑性较差的钨、钼管材的生产。
3)固定短芯头拉拔拉拔时将带有芯头的芯杆固定,管坯通过模孔实现减径和减壁,如图2-c所示。
固定短芯头拉拔的管材内表面质量比空拉的好,此法在管材生产中应用的最为广泛,但拉拔细管尤较困难,而且不能生产长管。
4)游动芯头拉拔在拉拔过程中,芯头靠本身所特有的外形建立起来的力平衡被稳定在模孔中,如图2-d所示。
此法是管材拉拔较为先进的一种方法,非常适用于长管和盘管主产,它对提高拉拔生产率、成品率和管材内表面质量极为有利。
但是与固定短芯头拉拔相比、游动芯头拉拔难度较大,工艺条件和技术要求较高,配模有一定限制,故不可能完全取代固定短芯头拉拔5)顶管法此法又称之为艾尔哈特法,将芯杆套人带底的管坯中,操作时管坯连同芯杆一同由模孔中顶出,从而对管坯进行加工,如图2-e 所示。
铝合金管材空拉减径时受力情况和壁厚变化分析
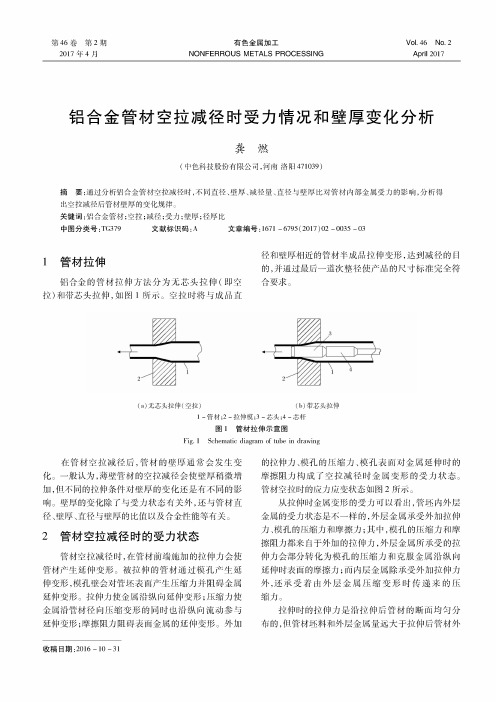
第46卷第2期2017年4月有色金属加工NONFERROUS METALS PROCESSINGVol. 46 No. 2April 2017铝合金管材空拉减径时受力情况和壁厚变化分析龚燃(中色科技股份有限公司,河南洛阳4?1039)摘要:通过分析铝合金管材空拉减径时,不同直径、壁厚、减径量、直径与壁厚比对管材内部金属受力的影响,分析得 出空拉减径后管材壁厚的变化规律。
关键词:铝合金管材;空拉;减径;受力;壁厚;径厚比中图分类号:TG379文献标识码:A文章编号:1671 -6795(2017)02 -0035 -031管材拉伸铝合金的管材拉伸方法分为无芯头拉伸(即空拉)和带芯头拉伸,如图1所示。
空拉时将与成品直径和壁厚相近的管材半成品拉伸变形,达到减径的目 的,并通过最后一道次整径使产品的尺寸标准完全符 合要求。
U )无芯头拉伸(空拉) (>)带芯头拉伸1 -管材;2-拉伸模;3-芯头;4-芯杆图1管材拉伸示意图Fig. 1Schematic diagram of tube in drawing在管材空拉减径后,管材的壁厚通常会发生变 化。
一般认为,薄壁管材的空拉减径会使壁厚稍微増加,但不同的拉伸条件对壁厚的变化还是有不同的影 响。
壁厚的变化除了与受力状态有关外,还与管材直 径、壁厚、直径与壁厚的比值以及合金性能等有关。
2管材空拉减径时的受力状态管材空拉减径时,在管材前端施加的拉伸力会使管材产生延伸变形。
被拉伸的管材通过模孔产生延 伸变形,模孔壁会对管坯表面产生压缩力并阻碍金属 延伸变形。
拉伸力使金属沿纵向延伸变形;压缩力使 金属沿管材径向压缩变形的同时也沿纵向流动参与 延伸变形;摩擦阻力阻碍表面金属的延伸变形。
外加的拉伸力、模孔的压缩力、模孔表面对金属延伸时的 摩擦阻力构成了空拉减径时金属变形的受力状态。
管材空拉时的应力应变状态如图2所示。
从拉伸时金属变形的受力可以看出,管坯内外层 金属的受力状态是不一样的,外层金属承受外加拉伸 力、模孔的压缩力和摩擦力;其中,模孔的压缩力和摩 擦阻力都来自于外加的拉伸力,外层金属所承受的拉 伸力会部分转化为模孔的压缩力和克服金属沿纵向 延伸时表面的摩擦力;而内层金属除承受外加拉伸力 外,还承受着由外层金属压缩变形时传递来的压 缩力。
工业纯铝杆拉拔过程中组织和性能变化规律研究
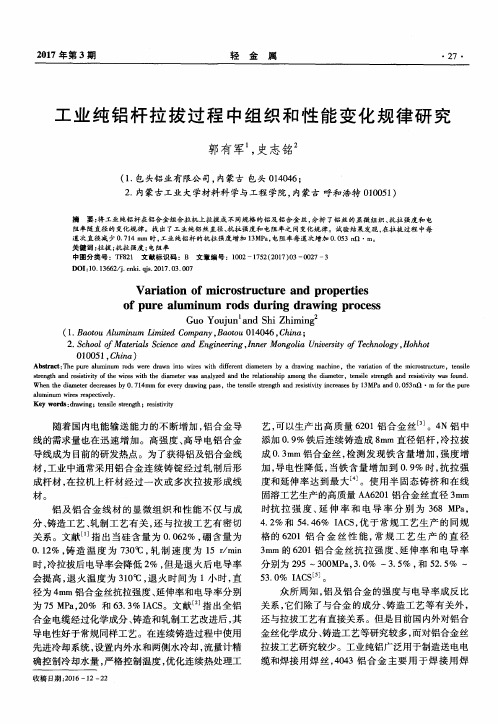
Ke y wo r d s: d r a in w g;t e n s i l e s t r e n th;r g e s i s t i v i t y
随着 国 内电能 输 送 能 力 的不 断增 加 , 铝合 金 导 线的需求量也在迅速增加。高强度 、 高导电铝合金
Ab s t r a c t : T h e p u r e a l u mi n u m r o d s w e r e d r a wn i n t o wi r e s wi t h d i f f e r e n t d i a me t e r s b y a d r a wi n g ma c h i n e,t h e v a r i a t i o n o f t h e mi c r o s t r u c t u r e,t e n s i l e
艺, 可 以生产 出 高 质 量 6 2 0 1铝 合 金 丝 。4 N铝 中 添加 0 . 9 %铁后 连 续铸 造 成 8 mm直 径 铝 杆 , 冷 拉 拔
导线成为 目前的研发热点 。为了获得铝及铝合金线 材, 工业 中通 常采 用 铝 合 金 连 续铸 锭 经过 轧 制 后 形 成杆 材 , 在拉 机上 杆 材 经 过 一 次 或 多 次拉 拔 形 成 线
摘 要: 将. Y - - _ , l k 纯铝杆在铝合金组合拉机上拉拔威不 同规格的铝及 铝舍金丝 , 分析 了铝丝的显微组 织、 抗拉 强度和 电 阻率随直径的 变化规律 。找 出了工业纯铝丝直径、 抗拉强度和 电阻率之间变化规律 。试验 结果发现 , 在拉拔过程 中每 道 次直径减 少0 . 7 1 4 mm时, 工业纯铝杆 的抗拉 强度增加 1 3 MP a , 电阻率每道次增加 0 . 0 5 3 n i l・ m。 关键词 : 拉拔 ; 抗拉强度 ; 电 阻率 中图分类号 :T F 8 2 1 文献标识码 :B 文章编号 :1 0 0 2—1 7 5 2 ( 2 0 1 7 ) 0 3 —0 0 2 7—3
铝合金薄板拉伸变形机理研究
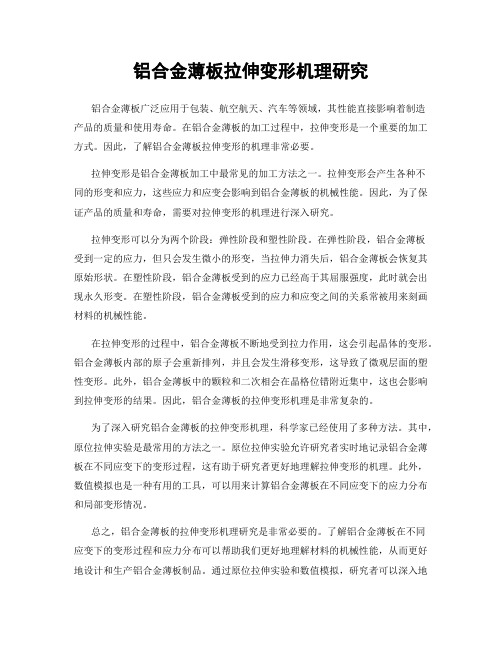
铝合金薄板拉伸变形机理研究铝合金薄板广泛应用于包装、航空航天、汽车等领域,其性能直接影响着制造产品的质量和使用寿命。
在铝合金薄板的加工过程中,拉伸变形是一个重要的加工方式。
因此,了解铝合金薄板拉伸变形的机理非常必要。
拉伸变形是铝合金薄板加工中最常见的加工方法之一。
拉伸变形会产生各种不同的形变和应力,这些应力和应变会影响到铝合金薄板的机械性能。
因此,为了保证产品的质量和寿命,需要对拉伸变形的机理进行深入研究。
拉伸变形可以分为两个阶段:弹性阶段和塑性阶段。
在弹性阶段,铝合金薄板受到一定的应力,但只会发生微小的形变,当拉伸力消失后,铝合金薄板会恢复其原始形状。
在塑性阶段,铝合金薄板受到的应力已经高于其屈服强度,此时就会出现永久形变。
在塑性阶段,铝合金薄板受到的应力和应变之间的关系常被用来刻画材料的机械性能。
在拉伸变形的过程中,铝合金薄板不断地受到拉力作用,这会引起晶体的变形。
铝合金薄板内部的原子会重新排列,并且会发生滑移变形,这导致了微观层面的塑性变形。
此外,铝合金薄板中的颗粒和二次相会在晶格位错附近集中,这也会影响到拉伸变形的结果。
因此,铝合金薄板的拉伸变形机理是非常复杂的。
为了深入研究铝合金薄板的拉伸变形机理,科学家已经使用了多种方法。
其中,原位拉伸实验是最常用的方法之一。
原位拉伸实验允许研究者实时地记录铝合金薄板在不同应变下的变形过程,这有助于研究者更好地理解拉伸变形的机理。
此外,数值模拟也是一种有用的工具,可以用来计算铝合金薄板在不同应变下的应力分布和局部变形情况。
总之,铝合金薄板的拉伸变形机理研究是非常必要的。
了解铝合金薄板在不同应变下的变形过程和应力分布可以帮助我们更好地理解材料的机械性能,从而更好地设计和生产铝合金薄板制品。
通过原位拉伸实验和数值模拟,研究者可以深入地探究铝合金薄板以及其它材料的变形机理,为实现高质量、高效率、低能耗的生产过程提供了重要的科学依据。
金属管材拉拔加工

金属管材拉拔加工是金属加工领域中常见的一种加工方式。
拉拔是将一根金属材料通过金属模具进行拉伸和外形锻造,从而得到一根更长、更细的管材。
这种加工方式在制作高精度、高质量的管道、导线和零件时被广泛使用。
一、的基本原理金属管材拉拔的基本原理是将一根金属坯料通过加压和拉伸的方式,使其通过模具,最终成为更长、更细的金属管材。
这个过程需要不断地加工和伸长,直到达到所需的长度和直径,这种加工方式在金属加工过程中具有非常重要的地位。
二、的步骤的步骤大致包括原料准备、坯料坯化、坯料高压加工、坯料拉伸等几个阶段。
具体来说,包括以下几个步骤:(1)原料准备拉拔加工需要使用高质量的钢材。
在准备原材料之前,需要经过筛选、清洗等多个步骤。
将符合要求的钢坯材料经过多轮清洗、表面处理及钢质预处理后,放入坯料坯化。
(2)坯料坯化时需要将钢坯变成金属坯料,而钢坯通常配置为立方体或圆柱体。
其目的是为坯料高压加工和拉伸制造一组适当的初始条件。
(3)坯料高压加工钢坯材料通过高压加工,经过模具冲压,使得经过冲压加工的坯料外形尺寸和质量指标逐步得到提高。
(4)坯料拉伸坯料经过加压,可以将坯料拉伸成一个圆柱体,也可以拉成带有方形和椭圆形冷模型的金属管材。
通过这一过程,可以使得金属管的外径及壁厚精度逐步增加。
三、的特点中,钢坯经过多次加工和拉伸,可以制造出具有以下特点的金属管材:(1)表面光洁度高:金属管的表面经过多次加工和拉伸,光洁度逐渐增加,表面光洁度比较高。
(2)内、外径大小精度高:金属管拉拔加工时治具模的翻新状况,以及伸拉时磨头的磨损、坯料的高度一致性都影响了每个管子的精度上送,是精密金属管材加工的不可或缺的工艺之一。
(3)壁厚精度高:金属管的壁厚精度对管材质量、强度等性能影响极大,而经过多次加工和拉伸,壁厚大小逐渐趋于稳定。
(4)材质的内应力清除高:因为钢材经过高压加工和拉伸,所以可以清除掉一些内部应力和缺陷,从而大大提高了金属管的抗拉强度和抗压强度。
拉拔加工中的拉拔变形和回弹控制
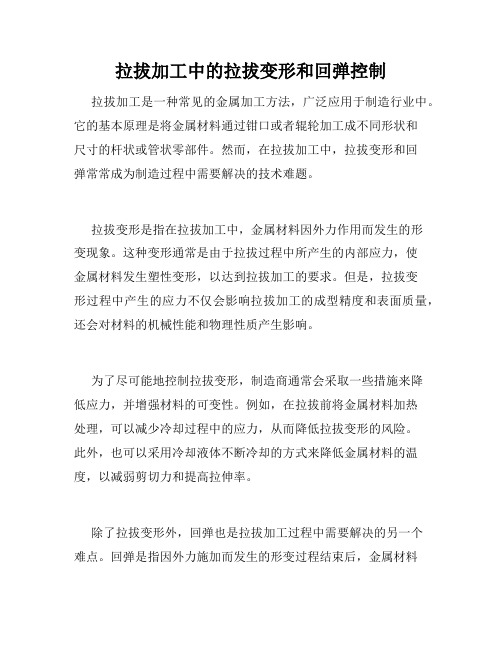
拉拔加工中的拉拔变形和回弹控制拉拔加工是一种常见的金属加工方法,广泛应用于制造行业中。
它的基本原理是将金属材料通过钳口或者辊轮加工成不同形状和尺寸的杆状或管状零部件。
然而,在拉拔加工中,拉拔变形和回弹常常成为制造过程中需要解决的技术难题。
拉拔变形是指在拉拔加工中,金属材料因外力作用而发生的形变现象。
这种变形通常是由于拉拔过程中所产生的内部应力,使金属材料发生塑性变形,以达到拉拔加工的要求。
但是,拉拔变形过程中产生的应力不仅会影响拉拔加工的成型精度和表面质量,还会对材料的机械性能和物理性质产生影响。
为了尽可能地控制拉拔变形,制造商通常会采取一些措施来降低应力,并增强材料的可变性。
例如,在拉拔前将金属材料加热处理,可以减少冷却过程中的应力,从而降低拉拔变形的风险。
此外,也可以采用冷却液体不断冷却的方式来降低金属材料的温度,以减弱剪切力和提高拉伸率。
除了拉拔变形外,回弹也是拉拔加工过程中需要解决的另一个难点。
回弹是指因外力施加而发生的形变过程结束后,金属材料回弹至原状或略微变形的现象。
这种情况也经常在拉拔加工过程中出现,对成品的准确度和精度产生明显影响。
回弹现象与拉拔变形有关。
根据材料的机械性质,金属材料在受到拉拔变形后,会发生弹性回复。
同时,由于拉伸过程会引起主流程的不均匀变化,拉拔次数、工序顺序、钳口尺寸和摩擦力等因素也都影响到拉拔杆的回弹程度。
为了降低拉拔杆的回弹,需要采用合适的制造工艺和加工方法。
可行的解决方案包括在拉拔工序中添加扭转或旋转力,以主动增加金属材料的变形程度,从而减小材料的回弹度。
此外,也可将多次拉拔步骤中的重叠量降低到最小,以减少不均匀的主流程变化,从而降低回弹程度。
在拉拔加工中,拉拔变形和回弹的控制是解决制造过程中技术难题的关键。
控制这些因素需要深刻的理解金属材料的力学性质和变形过程,并采用适宜的技术以降低应力、增加变形量、减小变形不均匀性或减少回弹程度。
保持稳定的生产工艺和制造方法,将是实现高品质金属零部件的关键,实现成本控制和客户满意度的平衡。
《拉拔铝管基础》课件

应用案例三:航空航天领域
总结词
高强度、轻量化
详细描述
在航空航天领域,由于对材料性能的高要求,拉拔铝管成为 重要的结构材料。其高强度和轻量化的特点有助于减轻飞行 器的重量,提高性能和燃油经济性。
的环保性能。
定制化服务
03
根据客户需求定制不同规格和性能的拉拔铝管,满足不同领域
的需求。
未来市场预测
市场规模
随着工业和建筑领域的发展,拉拔铝管市场规模将继续扩大。
竞争格局
具备技术优势和品牌影响力的企业将逐渐占据市场主导地位。
质量要求
对拉拔铝管的质量要求将越来越高,产品质量将成为竞争的核心 要素。
06
;最后,进行成品检验,确保产品质量符合要求。
02
拉拔铝管的性能特点
力学性能
01
02
03
高强度
拉拔铝管具有较高的抗拉 强度和屈服强度,能够承 受较大的压力和拉伸力。
良好的塑性和韧性
拉拔铝管在受到外力作用 时能够发生较大的塑性变 形而不断裂,同时展现出 良好的韧性。
抗疲劳性能
由于其良好的塑性和韧性 ,拉拔铝管在交变应力作 用下不易发生疲劳断裂。
模具通常由硬质合金或高强度钢材制 成,具有高硬度和耐磨性。
模具的维护和保养对于保持其精度和 使用寿命非常重要,需要定期进行检 查和维修。
其他辅助工具
其他辅助工具包括切割机、磨 床、钻床、搬运工具等,用于 铝管的加工、搬运和存储。
这些辅助工具在拉拔铝管生产 中起到重要的辅助作用,可以 提高生产效率和产品质量。
拉拔铝管的生产工艺流程
总结词
拉拔铝管的生产工艺流程包括原材料准备、加热、多道次拉拔、退火处理和成品检验等 环节。
铝合金部件焊接变形的产生及控制

铝合金部件焊接变形的产生及控制随着科学技术的不断发展,铝合金材料已经在众多领域中得到了广泛的应用,因为它的重量轻、强度高、抗腐蚀性好等优秀的性能特点。
因此,在许多工程中,铝合金部件也逐渐成为了主要的材料之一。
但是,在铝合金部件制造过程中,由于热应力和残余应力的存在,铝合金部件在进行焊接加工时很容易产生变形,这也成为制造过程中的一个重要问题。
因此,控制铝合金部件焊接变形是非常重要和必要的。
1. 铝合金部件焊接变形的产生机理铝合金部件在进行焊接过程中,往往会产生一定的热影响区。
这是因为在焊接的加热过程中,焊点处的温度会急剧升高,会使周边的金属材料产生热膨胀,从而引起板材弯曲和变形。
此外,受到焊枪重量和锁定力的作用,板材弯曲和变形的程度也会增加。
2. 铝合金部件焊接变形的控制方法2.1调整焊接参数在铝合金部件的实际焊接过程中,调整焊接参数可以有效地控制焊接变形的产生。
焊接参数主要包括焊接电流、电压、热输入和焊接速度等。
通过合理地调整这些参数,可以使焊接区域受到的热影响更加均匀,从而减少变形的产生。
2.2采用专业的焊接技术和设备铝合金部件的焊接变形受到很多因素的影响,因此要控制焊接变形,我们必须采用专业的焊接技术和设备。
例如,在进行铝合金部件焊接时,可以采用TIG焊接技术,这种技术可以在焊接的过程中使用阻性焊助剂,来提高焊接接头的稳定性。
同时,使用先进的焊接设备也有助于控制焊接变形。
2.3采用机械定位和焊接支撑装置在铝合金部件的制造过程中,通常采用机械定位和焊接支撑装置来控制焊接变形。
机械定位利用夹具和模具等设备,使被焊接的部件相对位置固定,保持尺寸准确、位置恒定,从而减少变形的产生。
而焊接支撑装置则可以用来支撑和稳定焊接部件的位置,避免其扭曲变形,从而提高焊接效果。
3. 铝合金部件焊接变形控制的应用实例对于汽车工业、电子行业、航空航天等多种应用领域,完美的铝合金部件的制造和焊接过程中,尤其要控制好焊接变形。
铝管拉拔工艺流程
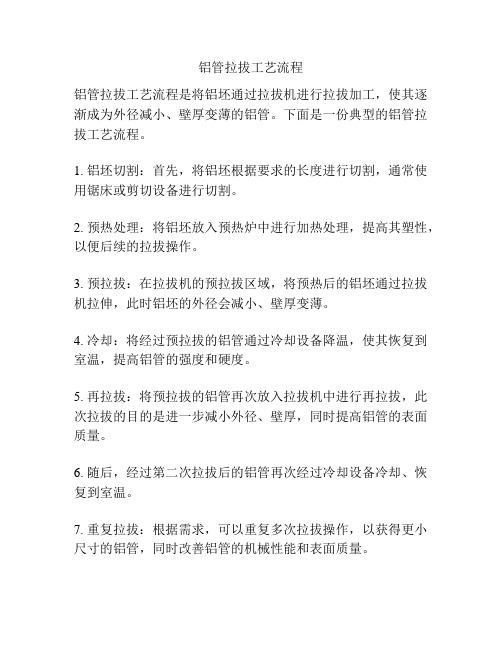
铝管拉拔工艺流程铝管拉拔工艺流程是将铝坯通过拉拔机进行拉拔加工,使其逐渐成为外径减小、壁厚变薄的铝管。
下面是一份典型的铝管拉拔工艺流程。
1. 铝坯切割:首先,将铝坯根据要求的长度进行切割,通常使用锯床或剪切设备进行切割。
2. 预热处理:将铝坯放入预热炉中进行加热处理,提高其塑性,以便后续的拉拔操作。
3. 预拉拔:在拉拔机的预拉拔区域,将预热后的铝坯通过拉拔机拉伸,此时铝坯的外径会减小、壁厚变薄。
4. 冷却:将经过预拉拔的铝管通过冷却设备降温,使其恢复到室温,提高铝管的强度和硬度。
5. 再拉拔:将预拉拔的铝管再次放入拉拔机中进行再拉拔,此次拉拔的目的是进一步减小外径、壁厚,同时提高铝管的表面质量。
6. 随后,经过第二次拉拔后的铝管再次经过冷却设备冷却、恢复到室温。
7. 重复拉拔:根据需求,可以重复多次拉拔操作,以获得更小尺寸的铝管,同时改善铝管的机械性能和表面质量。
8. 毛管分条:将拉拔后的铝管分条,根据要求的长度进行切割。
通常使用锯床或剪切设备。
9. 退火处理:铝管拉拔后,由于塑性变形,内部会产生应力,为了提高铝管的强度和抗压性能,需要进行退火处理。
通常将铝管放入退火炉中加热,并进行适当的保温、冷却过程。
10. 清洗:经过退火处理后的铝管,需要进行清洗,去除表面的油污、杂质等。
通常使用化学清洗方法。
11. 铝管检验:经过清洗后的铝管需要进行检验,主要包括外观检验、尺寸检验、力学性能检验等。
确保铝管的质量符合标准要求。
12. 包装和出厂:合格的铝管经过检验后,进行包装,通常使用塑料保护套或纸箱包装,并进行出厂。
以上就是典型的铝管拉拔工艺流程,通过拉拔加工,铝坯逐渐成为外径减小、壁厚变薄的铝管,从而满足不同领域对铝管的需求。
这一系列工艺流程保证了铝管的质量和性能,使其在工业、建筑、交通运输等领域得到广泛应用。
挤压拉拔主要工艺流程
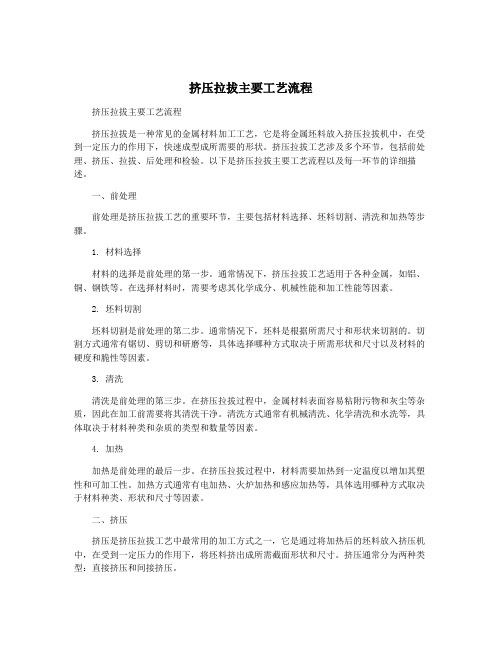
挤压拉拔主要工艺流程挤压拉拔主要工艺流程挤压拉拔是一种常见的金属材料加工工艺,它是将金属坯料放入挤压拉拔机中,在受到一定压力的作用下,快速成型成所需要的形状。
挤压拉拔工艺涉及多个环节,包括前处理、挤压、拉拔、后处理和检验。
以下是挤压拉拔主要工艺流程以及每一环节的详细描述。
一、前处理前处理是挤压拉拔工艺的重要环节,主要包括材料选择、坯料切割、清洗和加热等步骤。
1. 材料选择材料的选择是前处理的第一步。
通常情况下,挤压拉拔工艺适用于各种金属,如铝、铜、钢铁等。
在选择材料时,需要考虑其化学成分、机械性能和加工性能等因素。
2. 坯料切割坯料切割是前处理的第二步。
通常情况下,坯料是根据所需尺寸和形状来切割的。
切割方式通常有锯切、剪切和研磨等,具体选择哪种方式取决于所需形状和尺寸以及材料的硬度和脆性等因素。
3. 清洗清洗是前处理的第三步。
在挤压拉拔过程中,金属材料表面容易粘附污物和灰尘等杂质,因此在加工前需要将其清洗干净。
清洗方式通常有机械清洗、化学清洗和水洗等,具体取决于材料种类和杂质的类型和数量等因素。
4. 加热加热是前处理的最后一步。
在挤压拉拔过程中,材料需要加热到一定温度以增加其塑性和可加工性。
加热方式通常有电加热、火炉加热和感应加热等,具体选用哪种方式取决于材料种类、形状和尺寸等因素。
二、挤压挤压是挤压拉拔工艺中最常用的加工方式之一,它是通过将加热后的坯料放入挤压机中,在受到一定压力的作用下,将坯料挤出成所需截面形状和尺寸。
挤压通常分为两种类型:直接挤压和间接挤压。
1. 直接挤压直接挤压是最简单和常见的挤压方式,它用于制备截面尺寸相对简单的轴类零件,如铝合金钢管等。
直接挤压的主要优点是生产效率高且成本较低。
2. 间接挤压间接挤压通常用于制备截面复杂、形状非轴对称的零件,如汽车零部件等。
在间接挤压中,坯料被置于模具中,并通过一定的力量将其挤出,形状和尺寸是由模具的形状决定的。
间接挤压生产效率较低,但是可以制备较为复杂的形状。
- 1、下载文档前请自行甄别文档内容的完整性,平台不提供额外的编辑、内容补充、找答案等附加服务。
- 2、"仅部分预览"的文档,不可在线预览部分如存在完整性等问题,可反馈申请退款(可完整预览的文档不适用该条件!)。
- 3、如文档侵犯您的权益,请联系客服反馈,我们会尽快为您处理(人工客服工作时间:9:00-18:30)。
图5空拉拔管坯与模具的1/4模型
图3拉拔模具半角定义
为得到精确的半角值,对拉拔载荷F的影响规 律值得研究。较大的拉拔载荷意味着管坯将受到非 常严重的压缩,这可能造成3个后果:管坯的失稳,大 的摩擦剪应力,润滑油被挤压出去。因而要力求较小 的拉拔载荷,在进行了一系列模拟分析的基础上最终 得到了半角口2对拉拔载荷F的影响规律曲线(如图4 所示),从中发现了一个合适的角度范围10~12。。而 口l必须匹配口z,这将确保模孔的角部能够被完全充 满。根据实践经验可知口2≥a。,根据模拟不断试错最 终得到了∞的合适范围8~9。。
QUAN Guo.zheng 1,ZHOU Jie 1,AI Bai—sheng 1,TONG Yin92 (1.College of Mechanical Engineering,Chongqing University,Chongqing 400030,P.R.China;
2.Department of Mechatronics Engineering,Chongqing College of Electronic Engineering, Chongqing 401331,P.R.China)
第31卷第6期 2008年6月
重庆大学学报 Journal of Chongqing University
文章编号:1000—582X(2008)06—0593—05
V01.31 No.6 Jun.2008
矩形截面铝合金管材的单道次空拉拔变形机理
权国政1,周 杰1,艾百胜1,佟 莹2
(1.重庆大学机械工程学院,重庆400030;2.重庆电子工程职业学院机电工程系,重庆401331)
分的变形量发生了,包括径向收缩变形、z向的延展变 形。这道拉拔完全不能使用芯头,因为截面形状的变 化太过剧烈,因而这道拉拔称为无芯头过渡拉拔。
万方数据
第6期
权国政,等:矩形截面铝合金管材的单道次空拉拔变形机理
595
变形前的管坯横截面 变形后的管坯横截面
图2规划的截面变化图
2.2模具半角定义 在图3中,口。为长方形模孔短边的半角;口:为长
基于CAD/CAE软件建立的空拉拔简化运动模
型如图1所示。对所研究对象的形状和位置做了如 下假设:管坯与模具都是平面对称的;对象安装时保 证了完全同轴;采用锥形结构代替实际中的管坯 夹头。
图1简化的运动模型
不带芯头空拉拔的运动方式简化为:模具运动,
而管坯不动。而带芯头拉拔的运动方式简化为:首先 芯头穿入拉拔模具并在模具定径带部位停止,其次模 具和芯头同时运动,而管坯保持不动。
厂一导7枨c [arLctg(糊\/^,J
㈣
式中:m为摩擦因子(此处为0.1);K为剪切屈服应力
极限;u为管坯和模具间的相对滑移速度;A为正常
数(10叫~10_5)。
2拉拔工艺设计
-2.1管材截面变化 研究的目标是经过一次空拉拔得到矩形截面的
铝合金管材,规划的管坯截面变化如图2所示。 对于空拉拔,当圆管变形成近似矩形管时,大部
重庆大学学报
第31卷
究,Prakash和ColleaguesE卜21建立了上限法来研究规 则多边形截面的拉拔工艺;Basily和Sansome[弘钉采用 上限法和下限法研究规则多边形截面棒材的拉拔工 艺,并得到了优化的模具形状;Bour和Webster-[}61采 用稳态有限元法分析了拉拔工艺,并与上限法做了对 比分析;Brucker等口]开发了圆截面和矩形截面棒材 多工步拉拔工艺CAD设计系统;Yoshida等[81采用商 用非线性有限元MARC软件分析了六边形截面的棒 材拉拔过程中圆角充填的问题,并将理论分析的结果 和实验结果做了对比。Kim等口3采用3D N-塑性有 限元法分析了由圆截面拉拔到方形截面棒材的过程 中,圆角充填情况及道次极限变形情况。
空拉拔工艺广泛应用于金属管材的生产,该工艺 可以获得具有良好外表面质量的等截面矩形、椭圆、 异形铝合金管材。对于该工艺,确保产品的尺寸精度 及内表面质量是研究的重点和难点,因为拉拔过程中
失稳现象很容易产生。只有对变形的机理进行深入 的研究后,才能够有效消除失稳并完全控制产品 质量。
目前拉拔领域的一些文献涉及了理论及实验研
摘 要:采用弹塑性有限元法模拟研究铝合金管材由圆截面拉拔变成矩形截面的变形机理,建
立了空拉拔工艺简化的三维运动模型及弹塑性有限元模拟模型,实现了空拉拔模拟。通过一系列
仿真得出了模孔半角对拉拔载荷的影响规律,进而得到了半角的合适取值;得出了失稳状态下切向
应力沿着管坯周向分布的规律,并将模孔定径带优化设计为中拱角度178。,有效消除了失稳现象;
收稿日期:2008—02-20 基金项目:国家科技部技术创新项目(07C26215110824) 作者简介:权国政(1980一),男,重庆大学博士后,主要从事材料变形行为及仿生复合材料的研究,(Tel)023—65103065}
(E-mail)quangz2000@sina.corn。
万方数据
594
拉拔工艺的变形具有典型的接触非线性、几何非 线性、边界非线性,它是一个多重非线性耦合的问题。 建立的有限元模型采用Cauchy应力的Truesdell率型 本构关系[12]进行表示。表达式(2)特别适合于构建金 属薄壳体的弹塑性模型。
如=G,{,d口,
(1)
G削2 f毛l&以+r兰妒∞,r一
仃一,7
实际生产情况如下:首先应用小型压机砸夹头, 将管坯反复翻转,将其一端砸扁、砸实;其次,将砸实 的夹头穿过并露出模具的模孔,此时长管坯的主体部 分由辊轮平稳支撑;最后,拉拔机的夹钳夹持住管坯 砸实的夹头,以一定的速度平稳拉拔。实现该过程的 模拟需通过以下方式:对管坯的锥形夹头加载z、Y、z 三向速度约束,并设定模具Y向运动速度口。所建立 的三维动力模型实现了坯料与模具的相对运动,而没 有改变坯料实际的受力情况,具有研究的可行性。 1.3本构方程
!1:!1!1:些些
]
“号f2(1+2H害)l, @’
式中:G棚为材料的模张量;E为弹性模量;v为泊松 比;H为加工硬化速率;口7为塑性态为1、弹性态为0 的常数;如、岛为Kronecker数组;‘、五分别为剪切应
力矗、砌的偏量。 1.4摩擦模型
为了应对在拉拔过程中速度矢量不断变化的问
题,Chen和Kobayashi[13。14]提出一种与相对速率有关 的反正切摩擦模型。
1∞
O
—l∞ 芒 善—2∞
b
一3∞
—加日
一5∞
图8空拉拔截面Ⅱ处切向应力分布
图11拉拔模孔修正后的定径带
图12优化方案成形后的管材
进入模具的变形锥区域时,管坯与模具的接触边界 (图13中的黑粗线)看起来像个字母“V”。
应用弹塑性有限元法研究了圆截面铝管经过一 次空拉拔成为矩形截面铝管的工艺,在完成了一系列 的模拟之后,分析得到了拉拔过程中管坯接触应力 场、接触边界的分布规律,不同拉拔模半角对拉拔载 荷的影响规律,失稳状态下切向应力场沿矩形周向的 分布规律。基于此,管坯的成形机理逐渐阐述清晰, 这对两道次拉拔成形工艺规划及模具设计有非常重 要的意义。
边的半角。口:对矩形轮廓的充填效果影响很大,角度 值可通过表达式(4)[151近似地计算出来,约为9。。
(4)
式中:口为摩擦因子(此处为0.1);Ro为初始圆管截面
鸯 外径;Rf为变形后管坯的平均外径。
图4不同半角对拉拔载荷的影响规律
充填模孑L 4个角部。在拉拔模孔的定径带区域,受到 压缩后的管坯一方面被最后定形,另一方面水平流动 以充填角部,而在此时失稳现象就发生了。
严
。
芒
暮 i
/10 / ../I
50~_ 20
30
40
图6空拉拔截面I处切向应力分布
截面Ⅱ处管坯切向应力0rt分布曲线如图8所示, 从图中看出切向应力沿着矩形的4个边缘剧烈波动,
Байду номын сангаас
万方数据
596
重庆大学学报
第31卷
图10管坯失稳使内外表面粗糙
图7截面I处成形后的形状
最大切向压应力达400 MPa,而最大切向拉应力达 70 MPa。在截面Ⅱ处成形后的管坯截面如图9所示,从 图中看出管坯的4个侧面由于失稳而发生内凹。
Abstract:An elasto-plastic finite element method(FEM)was used to study the deforming mechanisms of an aluminum tube&awn without a mandrel from a circular to a rectangular cross-section.The simplified dynamics model and FE model of the non-mandrel drawing process were established based on the FEM software deform-3D and simulations subsequently performed.Based on the simulation results,the influence of different semi—die angles on the drawing load was summarized,and the proper values were found.As for the blank instability during the drawing process.the tangential stress distribution rule along the rectangle sides was acquired.The drawing die sizing section then was modified with a camber angle of 1 78。to eliminate instability.The touch boundary and touch—stress distribution during drawing process also were analyzed.The aluminum tube produced by the optimized drawing die possesses eligible dimensions and smooth inner surfaces. Key wolds:non-mandrel drawing;semi-die angle;rectangle;instability;surface roughness;touch-stress