锌电解槽计算
镀锌电解电流电压

镀锌电解电流电压全文共四篇示例,供读者参考第一篇示例:镀锌是一种将金属表面涂上一层锌金属的防腐处理方法,以保护金属表面不受腐蚀。
电解是利用电流使物质发生氧化还原反应的一种方法,而镀锌电解电流电压即是在进行镀锌过程中所使用的电压大小。
在镀锌工艺中,电解电流电压是一个非常重要的参数,能够直接影响到镀层的质量及厚度。
在进行镀锌电解过程中,设定适当的电压能够使得金属表面均匀地镀上一层锌金属,从而提高金属的耐腐蚀性能和导电性能。
一般来说,提高电解电流电压能够加快镀层的生成速度,但过高的电压则会造成能量损耗增加和镀层质量下降的问题。
在实际的生产工艺中,需要根据具体的镀锌要求和设备性能来调整电解电流电压的大小,以达到最佳的镀锌效果。
除了电压大小外,镀锌电解过程中还需要控制电流密度、温度、PH值等参数,以保证镀锌过程的稳定性和镀层质量。
在进行镀锌工艺时,操作人员需要对电解过程进行全程监控,及时调整各项参数,确保镀层的质量达到要求。
镀锌电解电流电压是影响镀锌效果的重要因素之一。
合理选择电压大小,结合其他工艺参数的控制,能够确保镀层的质量和性能达到要求。
在今后的镀锌生产过程中,我们需要不断优化工艺技术,提高生产效率,为金属制品的防腐和耐用性提供更好的保障。
【以下是文章的结尾】希望通过这篇文章对镀锌电解电流电压有一个更深入的了解,让大家在实际生产中能够更好地控制电解过程,获得更好的镀锌效果。
祝愿镀锌工艺能够不断发展,更好地服务于工业生产和人们的生活。
第二篇示例:镀锌是一种将锌镀层覆盖在金属表面以增加防腐性能和美观性的工艺。
在镀锌过程中,电解电流和电压的控制非常重要,它们直接影响着镀层的质量和性能。
本文将重点探讨镀锌电解电流和电压的相关知识。
让我们简要回顾一下镀锌的工艺过程。
镀锌的工艺过程分为热镀锌和电镀锌两种方法。
热镀锌是将金属件浸泡在熔融锌中,使锌在金属表面形成一层保护性的镀层。
而电镀锌则是将金属件放入含有锌离子的电解液中,在外加电流的作用下,将锌沉积在金属表面。
锌电积一种“烧板”的原因分析及处理

锌电积一种“烧板”的原因分析及处理文章阐述一种锌电积“烧板”的特征,并详细分析“烧板”产生的原因,结合生产实际提出处理措施。
标签:锌电积;有机物;烧板前言锌电解沉积是湿法炼锌系统的末端,是将净化后的硫酸锌溶液(新液)送入电解槽内通以直流电在阴极上析出金属锌(阴极锌),通过下面反应式进行反应:ZnSO4+H2O=Zn↓+H2SO4+1/2O2↑当电解溶液内存在杂质时析出的阴极锌会在杂质作用下重新溶解到液体内,并放出氢气,我们称之为阴极锌的返溶,俗称“烧板”。
[1]电积过程大面积”烧板”使得阴极锌产量下降,直流电单耗升高,大量电能损失,资源浪费,也使生产成本增加。
因此,需要严加控制“烧板”发生。
1 “烧板”发生及其特征2014年下半年净化工序更改除钴工艺,由原来的锌粉两段高温锑盐除钴更改为β-萘酚除钴工艺。
除钴工艺的优化大幅降低了锌粉和蒸汽消耗,按年产10万吨锌计算,年生产成本节约近1000万。
但新工艺运行以来,电解工序先后出现4次阴极锌大面积“烧板”事故,“烧板”时间一般持续3-5天,最长可达半月之久。
这几次发生的“烧板”事故与过去都不同。
表现为阴极锌大面积针眼,背面发黑,透酸严重,电解槽内出现大量白色泡沫且厂房内酸雾很浓。
阴极锌的边缘和中间出现局部返溶。
在阴极锌板面的中间出现3-5厘米不等的窟窿,板面出现反复析锌,表面形成年轮状。
在未返溶部分,致密度非常好,板面光亮,熔铸直产率也比较高。
2 原因分析(1)由于烧板的初期存在针眼和透酸,因此,曾怀疑常规元素超标导致,于是对新液和废液内的常规元素进行分析。
从表1可以看出常规元素除氯根外都在合格范围内,特别是对电解影响比较大的砷、锑、锗等含量都比较低,氯根基本不会对阴极锌板面产生影响,因此,可以排出常规元素影响。
(2)排除常规元素后,我们将关注的重点落在系统内添加的有机物上。
且这几次的“烧板”与资料内介绍的有机物烧板特征相似,如阴极锌下部和边缘有返溶现象,现场酸雾突起,槽内沸腾泛白等[2]。
锌电积过程中直流电单耗较高的原因分析与处理措施

锌电积过程中直流电单耗较高的原因分析与处理措施摘要:现代锌冶金的生产方法主要为湿法炼锌。
湿法炼锌是对ZnSO4和H2SO4的水溶液在通以直流电的作用下锌由溶液析出至阴极板,获得电积锌。
湿法炼锌具有生产规模大、能耗相对较低、环保指标较好、自动化程度较高、有利于综合回收有价金属等优点而得到迅速发展。
湿法炼锌电解过程是电解液在直流电作用下析出锌的电化学反应过程,锌电解过程的电能消耗占整个湿法炼锌电能能耗的80%以上。
因此,降低直流电单耗刻不容缓,本文就锌电积氧压浸出工艺过程中电耗高的原因及降低电耗的措施作以综述。
关键词:锌电积;直流电单耗;阳极板;电效工厂采用锌电积氧压浸出工艺,主要生产工序包括:磨矿、氧压浸出、酸中和、压滤除铁、净化除杂、锌电积、成品铸型、硫回收、综合回收等。
锌电积采用3.2m2大极板,所用剥锌机、洗刷机、多功能行车等设备,自动化、智能化程度较高。
一、锌电积过程直流电单耗较高的原因分析:直流电单耗是指:每析出一吨锌所用的直流电量;锌电积过程直流电的作用主要用于析出锌,有一小部分转化为热能,因此要降低直流电单耗就要尽可能的使直流电作用于析出锌,减少转化为热能的部分。
(1)建立生产车间时,厂内变电所供电机组与电积车间电解槽之间距离较远,造成电解槽供电母排距离较长。
在酸性条件下母排极易产生结晶,造成一部分电能在输送过程转化为热能而有所损耗。
(2)槽内极板状况:如果在装槽时阴极板弯板、带锌角板、绝缘条脱落板进入槽内,阴阳极接触短路。
在损坏极板的情况下电能转化为热能,增加直流电单耗。
(3)电解槽槽壁结晶主要成分为CaSO4、MgSO4,钙镁化合物在槽内温度较低的情况下极易析出附在槽壁形成结晶、电解槽漏电等原因也会造成直流电单耗较高。
(4)由于新液纯度不够,造成电解槽烧板现象发生,电解槽不能平稳运行,影响析出锌产量,进而增加直流电单耗。
(5)电解液含锌较高(160g/l-165g/l),由于新液不足等原因电流密度较低的情况下,电解液电阻值较大,电效较低。
锌电解工操作规程
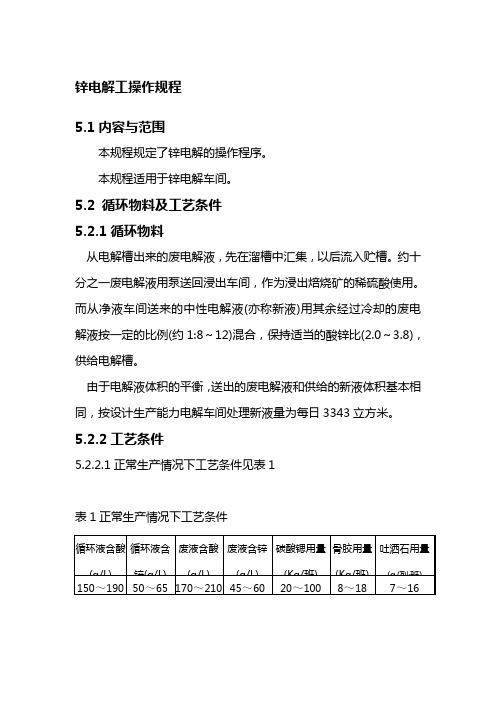
锌电解工操作规程5.1内容与范围本规程规定了锌电解的操作程序。
本规程适用于锌电解车间。
5.2 循环物料及工艺条件5.2.1循环物料从电解槽出来的废电解液,先在溜槽中汇集,以后流入贮槽。
约十分之一废电解液用泵送回浸出车间,作为浸出焙烧矿的稀硫酸使用。
而从净液车间送来的中性电解液(亦称新液)用其余经过冷却的废电解液按一定的比例(约1:8~12)混合,保持适当的酸锌比(2.0~3.8),供给电解槽。
由于电解液体积的平衡,送出的废电解液和供给的新液体积基本相同,按设计生产能力电解车间处理新液量为每日3343立方米。
5.2.2工艺条件5.2.2.1正常生产情况下工艺条件见表1表1正常生产情况下工艺条件5.2.2.2开停车时工艺条件见表2表2开停车时工艺条件5.3车间正常操作5.3.1 新液泵操作5.3.1.1开泵前,先用手盘车,检查转动是否灵活,如安装或检修后的泵应检查旋转方向是否正确。
5.3.1.2 停泵时,切断电源,关闭进口阀门,放出泵内溶液,避免结晶。
5.3.1.3 注意观察新液质量,发现新液浑浊等异常现象时,要立即报告车间调度,不合格新液未征得调度同意,不得使用。
5.3.1.4 根据化验结果控制混合液锌、酸含量在技术卡片规定范围内,如生产不正常而达不到规定要求时,应向车间调度报告。
5.3.1.5 新液泵操作安全注意事项5.3.1.5.1 上岗前穿戴好各种劳保用品。
5.3.1.5.2 开泵前应先盘车,并按操作规程中的一系列要求做好检查工作。
5.3.1.5.3 检查电机是否接地,转动部分有无安全装置和障碍物,当运转中一旦发现故障应及时停车处理。
5.3.1.5.4 严禁用水冲洗电器设备。
5.3.1.5.5 不准用湿手或金属棒启动电器设备。
5.3.1.5.6 清扫设备时,必须停车后方可进行。
5.3.2 废液泵及循环泵操作5.3.2.1 开泵:开泵前先用手盘对轮1~2圈,检查有无故障和轴封填料口松紧程度。
打开进液阀,检查泵的进液端是否漏液。
锌电解槽计算
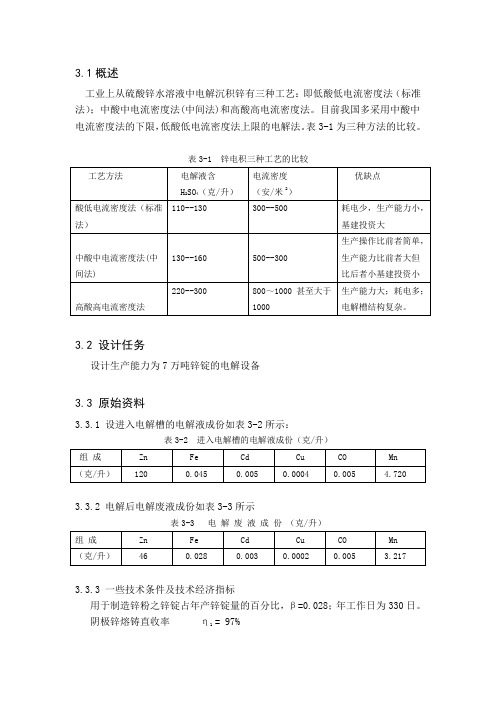
3.1概述工业上从硫酸锌水溶液中电解沉积锌有三种工艺:即低酸低电流密度法(标准法);中酸中电流密度法(中间法)和高酸高电流密度法。
目前我国多采用中酸中电流密度法的下限,低酸低电流密度法上限的电解法。
表3-1为三种方法的比较。
表3-1 锌电积三种工艺的比较3.2 设计任务设计生产能力为7万吨锌锭的电解设备3.3 原始资料3.3.1 设进入电解槽的电解液成份如表3-2所示:表3-2 进入电解槽的电解液成份(克/升)3.3.2 电解后电解废液成份如表3-3所示表3-3 电 解 废 液 成 份 (克/升)3.3.3 一些技术条件及技术经济指标用于制造锌粉之锌锭占年产锌锭量的百分比,β=0.028;年工作日为330日。
阴极锌熔铸直收率 η1 = 97%阴极电流密度 D 阴 = 520安培 槽电压 V 槽 = 3.20伏 电流效率 ηi = 98%阴极规格 长×宽×厚= 1000×666×4(毫米)3.4 工艺过程及设备计算3.4.1物料平衡及电解槽计算 阴极锌成份的计算在电积过程中,一部分铜、铁、镉与锌一齐在阴极上沉积,一升电解液得到的阴极锌含金属量如表3-4所示。
表3-4 一升电解液沉积的金属量(克)铅-银阳极在电解过程中被腐蚀,使一部分铅进入到阴极锌中。
设阴极锌含铅0.006%则进入到阴极锌中铅的量为:0038.0100006.00072.64=⨯克那么阴极锌的成份如表3-5所示。
表3-5 阴 极 锌 成 份3.4.2 所需电解槽数量的计算 (1)每日应产出的阴极锌量的计算。
Q 1=ηβm Q )1(+吨 式中: Q 1----每日应产出阴极锌的数量,吨; Q ----设计生产能力,吨锌锭/年;β----用于制造锌粉之锌锭占年产锌锭量的百分比,%; m ----年工作日,日;η----阴极锌熔铸直收率,%。
Q 1=22597.0330)028.01(70000=⨯+吨/日(2)阴极有效总面积及片数的计算 阴极有效总面积的计算。
锌电解操作工艺

锌电解操作工艺(2010-12-27 19:20:34)转载标签:杂谈一范围本标准规定了电解工艺的基本原理,。
工艺操作条件,岗位操作法, 原材料质量要求,产出物料质量要求,主要技术经济指标和主要设备.二工艺目的及原理1.工艺目的使溶液中的锌通过电积提锌得到锌片,再熔铸成成品锌。
1.原理锌电积一般釆用Pb-Ag(1%Ag)合金板为阳极,纯铝板为阴极,以酸性硫酸锌水溶液作为电解液,当通以直流电时,在阴极上发生锌的析出,在阳极上放出氧气。
阴极上 Zn2++2e=Zn阳极上 H2O-2e=1/2O2 +2H+总反应式为 ZnSO4+H2O=Zn+H2SO4+1/2O2因此,随着电解过程的进行,电解液中的含锌量不断减少,硫酸含量不断增加,为了保持电积条件的稳定,必须不断抽取一部分电解作为废液返回浸出,同时,相应地加入净化了的中性硫酸锌溶解,以补充所消耗的锌量,维持电解液中一定的H+,Zn2+含量,并稳定电解系统中的体积。
三硫酸锌溶液电解锌的生产工艺流程四原辅材料质量要求。
1. 新液成份(g/l)符合企业标准的规定Zn120-150 Cu≤0.002 Cd≤0.003 Fe≤0.015 Co≤0.0015 Ni≤0.0015 As≤0.003 Sb≤0.0005 Ge≤0.00005Mn2.5-52. 废液成份(g/l)Zn35-60 H+140-200五工艺操作条件1. 槽温 37 -42℃2. 电流密度 500-550A/m23. 槽电压3.2-3.3V4. 析出周期 24h5. 同极中心距 62mm6 . 添加剂(1) 吐酒石:出槽前3min-5 min加入电解槽内,一般加入量为0..05-0.1g/槽(2) 骨胶:装槽前1h-3h后加入电解槽内,加入量一般为0.25kg/t锌析出-0.5 kg/t析出锌(3) 碳酸锶视锌析出含铅情况,每班在电解槽内加8次,每次加10-20 kg7. 周期管理掏槽周期 30-40d平刷阳极周期 4-5d平整阴极周期30-40d8. 空气冷却塔主要技术条件进液温度 37-42℃出液温度 30-37℃喷洒压力 0.05MPa清理周期 1-2个月六岗位操作法1. 按槽上把<四关>、槽下<七不准>操作法进行操作(1)槽上把<四关>(a) 导电关:导电头擦亮打紧,两极对正,极距均匀,消灭短、断路板;(b) 极板关:接触准确,及时平整阴阳极板,不合格阴极铝板不装槽;(c) 检查关:精心检查,调整,保证导电良好, 槽上整齐清洁,杂物不得入内;(d) 添加剂关:适时、适量添加添加剂(吐酒石、骨胶、碳酸锶)。
锌电解工艺

锌电解工艺5硫酸锌溶液的电解沉积在ZnSO4和H2SO4水溶液中,采用Pb-Ag合金为阳极,纯铝作阴极,通以直流电进行电解,在阴极析出锌,在阳极产生氧气,与此同时,湿法炼锌工艺锌焙砂浸出过程所消耗的硫酸在此电解液中得到再生。
5.1锌电解液成分及锌电积生产过程5.1.1锌电解液锌电解液除主要成分硫酸锌、硫酸和水外,还存在少量杂质金属的硫酸盐及部分阴离子(主要为氯离子和氟离子)。
目前锌电解液中锌的浓度一般波动在40~60g/L范围内,而硫酸浓度则趋于逐步提高,已从110~140g/L提高到170~200g/L。
对于杂质的含量各厂也有不同要求。
加拿大一家锌厂在进行改造时曾做过调查,为了适应电流密度大幅度提高,对电解液中杂质含量(mg/L)要求更严格:Cd<0.3,CO<0.3,Sb<0.03,Ge<0.03,Fe<10,CL <50~100,F<10,Mn<1.8g/L5.1.2锌电积生产过程硫酸锌溶液的电积过程是将已经净化好的硫酸锌溶液(新液)以一定比例同废电解液混合后连续不断地从电解槽的进液端送入电解槽内。
铅银合金板(含银量约1%)阳极和压延铝板阴极,并联交错悬挂于槽内,通以直流电,在阴极析出金属锌(称阴极锌或析出锌),在阳极则放出氧气。
随着电积过程的不断进行电解液含锌量逐渐减少,而硫酸含量则逐渐增多,为保证电积条件的稳定,必须不断地补充新液以维持电解液成分稳定不变。
电积一定时间后,提出阴极板,剥下压延铝板上的析出锌片送往熔铸工序。
5.2锌电积过程的理论基础锌电解液的主要成分是硫酸锌、硫酸和水,当通以直流电时带正电荷的离子移向阴极,带负电荷的离子移向阳极,并分别在阴、阳极上放电。
阴极主要反应:Zn2++2e=Zn阳极主要反应:2OH--2e=0.5O2+H2O(或H2O-2e=0.5O2+2H+)电极过程总反应:ZnSO4+H2O=Zn+H2SO4+0.5O25.3锌电解车间的主要生产设备及布置5.3.1电解槽电积锌用的电解槽是一种长方形的槽子。
锌电解的目的与原理

锌电解的目的与原理锌电解的目的是通过电解锌溶液,将锌阳极上的金属锌溶解到溶液中,然后在阴极上还原为纯净的金属锌。
锌电解的原理是基于电解质溶液中的离子导体能够在外加电压下迁移和转移电荷的特性。
锌电解的步骤如下:1. 准备电解槽和电解液:将锌阳极和铜阴极插入电解槽中的锌硫酸溶液中。
锌阳极和铜阴极要保持一定的距离,以避免短路。
2. 施加电压:通过外部电源施加电压,在锌阳极和铜阴极之间建立电场。
电场的方向是由锌阳极向铜阴极。
3. 锌阳极溶解:施加电压后,锌阳极上的金属锌会溶解到锌硫酸溶液中。
这是因为金属锌的氧化电位较低,所以它会释放出电子,形成Zn2+离子。
溶解的反应可以表示为:Zn(s) →Zn2+(aq) + 2e-。
4. 锌离子迁移:在施加电压的作用下,锌离子会从锌阳极迁移到铜阴极,并沉积在铜阴极上。
这是因为铜的氧化电位更高,所以它比锌更容易接受电子,发生还原反应。
还原反应可以表示为:Zn2+(aq) + 2e- →Zn(s)。
5. 锌离子沉积:随着锌离子在电解液中的迁移,它们会在铜阴极表面逐渐沉积并形成金属锌。
锌电解的原理是基于电解质溶液中的离子迁移和电荷转移的特性。
当施加外部电压时,电解质溶液中的阳离子会向阴极迁移,而阴离子会向阳极迁移。
在锌电解中,锌离子(Zn2+)是阳离子,会朝着铜阴极移动。
同样地,硫酸阴离子(SO42-)是阴离子,会朝着锌阳极移动。
在电解过程中,物质的电离和电荷转移相互作用,使得锌离子从阳极溶解到溶液中,然后通过电场迁移到阴极,并还原为金属锌。
锌电解在工业中有广泛应用。
其中一个主要应用是锌电镀。
通过锌电解,可以在金属表面形成一层均匀的锌金属保护层,从而防止金属氧化和腐蚀。
锌电镀常用于汽车和建筑行业,保护钢铁制品免受氧化和腐蚀的影响。
总之,锌电解的目的是通过电解锌溶液,将锌阳极上的金属锌溶解进溶液中,并在铜阴极上还原为纯净的金属锌。
这一过程依赖于离子在电场中的迁移和电荷转移的特性。
锌电解槽计算
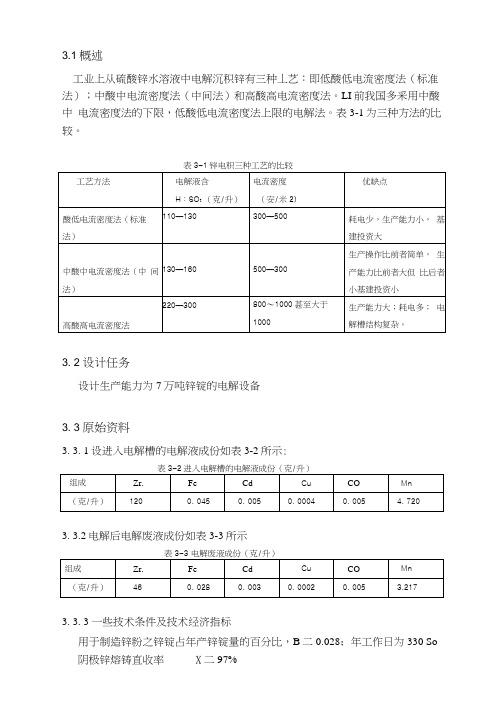
3.1概述工业上从硫酸锌水溶液中电解沉积锌有三种丄艺:即低酸低电流密度法(标准法);中酸中电流密度法(中间法)和高酸高电流密度法。
LI前我国多釆用中酸中电流密度法的下限,低酸低电流密度法上限的电解法。
表3-1为三种方法的比较。
3. 2设计任务设计生产能力为7万吨锌锭的电解设备3. 3原始资料3. 3. 1设进入电解槽的电解液成份如表3-2所示:3. 3.2电解后电解废液成份如表3-3所示3. 3. 3 一些技术条件及技术经济指标用于制造锌粉之锌锭占年产锌锭量的百分比,B二0.028;年工作日为330 So 阴极锌熔铸直收率X二97%阴极电流密度 D w = 520安培槽电压伏电流效率Us = 98%阴极规格长X宽X厚二1000X666X4 (毫米)3. 4工艺过程及设备计算3.4.1物料平衡及电解槽计•算阴极锌成份的计算在电积过程中,一部分铜、铁、镉与锌一齐在阴极上沉积,一升电解液得到的阴极锌含金属量如表3-4所示。
铅-银阳极在电解过程中被腐蚀,使一部分铅进入到阴极锌中。
设阴极锌含铅0. 006%则进入到阴极锌中铅的量为:64.0072x0.006 =00()3100那么阴极锌的成份如表3-5所示。
3. 4.2所需电解槽数量的计算(1)每日应产出的阴极锌量的汁算。
Q1 二<2(1+0)吨mrj式中:Q:----每日应产出阴极锌的数量,吨;Q --一设计生产能力,吨锌锭/年;B----用于制造锌粉之锌锭占年产锌锭量的白分比,%;m ----年工作日,S;n-一-阴极锌熔铸直收率,%<>_70000(l+ 0.028)=225吨/日1330x0.97(2)阴极有效总面积及片数的计算阴极有效总面积的计算。
I切駡95 x24 X"粹式中:F——阴极有效总面积,米'Q——每日产出的阴极锌量,吨;D——阴极电流密度,安培/米';n ------- 电流效率,%;1.2195——锌的电化当量,克/安培;24 ------ 电解析出时间,小时。
锌电解槽计算.

3.1概述工业上从硫酸锌水溶液中电解沉积锌有三种工艺:即低酸低电流密度法(标准法);中酸中电流密度法(中间法)和高酸高电流密度法。
目前我国多采用中酸中电流密度法的下限,低酸低电流密度法上限的电解法。
表3-1为三种方法的比较。
表3-1 锌电积三种工艺的比较工艺方法电解液含H2SO4(克/升)电流密度(安/米2)优缺点酸低电流密度法(标准法)110--130 300--500 耗电少,生产能力小,基建投资大中酸中电流密度法(中间法) 130--160 500--300生产操作比前者简单,生产能力比前者大但比后者小基建投资小高酸高电流密度法220--300 800~1000 甚至大于1000生产能力大;耗电多;电解槽结构复杂。
3.2 设计任务设计生产能力为7万吨锌锭的电解设备3.3 原始资料3.3.1 设进入电解槽的电解液成份如表3-2所示:表3-2 进入电解槽的电解液成份(克/升)组成 Zn Fe Cd Cu CO Mn(克/升) 120 0.045 0.005 0.0004 0.005 4.7203.3.2 电解后电解废液成份如表3-3所示表3-3 电解废液成份(克/升)组成 Zn Fe Cd Cu CO Mn(克/升) 46 0.028 0.003 0.0002 0.005 3.2173.3.3 一些技术条件及技术经济指标用于制造锌粉之锌锭占年产锌锭量的百分比,β=0.028;年工作日为330日。
阴极锌熔铸直收率η1= 97%阴极电流密度 D 阴 = 520安培 槽电压 V 槽 = 3.20伏 电流效率 ηi = 98%阴极规格 长×宽×厚= 1000×666×4(毫米)3.4 工艺过程及设备计算3.4.1物料平衡及电解槽计算 阴极锌成份的计算在电积过程中,一部分铜、铁、镉与锌一齐在阴极上沉积,一升电解液得到的阴极锌含金属量如表3-4所示。
表3-4 一升电解液沉积的金属量(克)组 成 Zn Fe Cd Cu 共计 (克)64.000.0050.0020.000264.0072铅-银阳极在电解过程中被腐蚀,使一部分铅进入到阴极锌中。
锌电解槽计算解析

3.4.4 通过电解槽电流强度的计算 一个电解槽的阴极总面积为 36.16 米 2
故
电流强度 I=36.16 ×520 = 18803 安培
设富余 5.4% 则 I=18808 × 1.054 = 19818.362 安培
3.4.5 整流设备选择
整流设备总功率按下式计算。
式中:
Q E 1000 W
24 0.98 1.2195
表 3-3 电 解 废 液 成 份 (克 / 升)
组成
Zn
Байду номын сангаас
Fe
Cd
Cu
CO
(克 / 升)
46
0.028
0.003
0.0002
0.005
Mn 3.217
3.3.3 一些技术条件及技术经济指标
用于制造锌粉之锌锭占年产锌锭量的百分比,
阴极锌熔铸直收率
η1 = 97%
β =0.028;年工作日为 330 日。
3.2 设计任务
设计生产能力为 7 万吨锌锭的电解设备
3.3 原始资料
3.3.1 设进入电解槽的电解液成份如表 3-2 所示:
表 3-2 进入电解槽的电解液成份(克 / 升)
组成
Zn
Fe
Cd
Cu
CO
(克 / 升) 120
0.045
0.005
0.0004
0.005
Mn 4.720
3.3.2 电解后电解废液成份如表 3-3 所示
Q
Q(1 1=
)吨
m
式中: Q1---- 每日应产出阴极锌的数量,吨;
Q ----
设计生产能力,吨锌锭 / 年;
β---- 用于制造锌粉之锌锭占年产锌锭量的百分比, %;
锌电解槽内电解液流动现象的水力学和数值模拟

进一 步 利 用该 数 值 模 型 , _ 上 的锌 电解 槽 对 丁业 进行 数值 模拟 , 测 工业 上 的锌 电解 槽 内的 流 动状 预
况。
本 文研 究 电解 槽 水模 型 的 中心 纵 截 面 , 尺 其
寸为 4 0m × 1 2 m 3 0mm。采用 C D 中专用 的前 处理 F
流不 均 , 流动非 稳 态波 动及 随机 湍流 等 , 因而难 于定
量 。通过 数值 模拟 与试 验 结 果 的对 比, 明 本 文所 表
用数 值模 型可 以较 好预 测 电解槽 水模 型流 动状 况 。
3 2 电 解 槽 的 数 值 模 拟 .
2 数 值 模 拟
2 1 网 格 划 分 .
图 3为 电解 槽 的 速 度 矢 量 图 , 以 看 到 : 况 流 可 工
程序 G m i软件 来 建 模 , 用 四边 形 网格 , u ma a bt 采 Sb p 网格 划分 方法 , 对计 算 区域划 分 网格 。
Absr c : s d o h i lt d i cpl t a t Ba e n t e smiiu e prn i e,t e wa e o e fee toy i elwa sa ls e n h o h — h t rm d lo l cr l ss c l s e tb ih d a d t e f w p e l n me o fwa e o e s a l z d wih t e zn l cr lz ro n a i o & Ge Co a y a h x e i o n n o trm d lwa nay e t h i c e e to y e fYu n n Ch h ngZn mp n st e e p r— m e ti sr m e t F rh r,t e fo fe d ft e zn l cr l z rwe e smu a e me ia l t o n n tu n . u t e h w l s o h i c ee toy e r i l td nu rc l wi c mme c a o — l i y h r ils f t wa e FL r UENT. Th e u t h we h ti c o d n e wih t x e i n a e u t e r s lss o d t a n a c r a c t he e p rme tlr s l s,t e smu ai n r s lso ua h i lto e u t fq d— rltr lm e h tpe r a o a l e e t d t n e n lfo fe d o i l cr l z r I n rf w ed o h i l c i e a s y e s n b y r f ce he i tr a w l fznc ee toy e . n e o f l ft e znc ee — a l l i l i toy e nd r dfe e tc n ii n s su id, a d t e s g sinswe epr p s d,a d te t o e ia a i o i — r l z ru e i r n o d to swa t d e f n h ug e to r o o e n h he r tc lb sst m pr v nd o tmie t elsr cu e a d e pa d t e c l sz s p tfr r o e a p i z he c l tu tr n x n h e l ie wa u o wa d. Ke o ds: i c ee to y i el F u d fo ; dru i Nu e ia i u ain yw r Z n l cr l ss c l ; l i w Hy a lc; m rc lsm lto l
锌电解槽计算解析

锌电解槽计算解析
锌电解槽是一种广泛应用的工业电解槽,常用于锌的电解精制过程。
在锌电解槽中,通过电解液中的电流作用,使锌阳极上的锌离子迁移到阴极上,并还原成金属锌沉积。
锌电解槽的设计和计算是确保锌电解过程高效、稳定和经济运行的关键。
本文将从锌电解槽的基本原理、电解液组成、阳极和阴极设计、电解槽的操作参数等方面进行详细解析。
首先是锌电解槽的基本原理。
锌电解槽是一种电解池,通常采用膜分离技术,以确保阳极和阴极之间的电流通道是完全分离的。
锌电解槽主要由阳极、阴极、电解液、电解槽壳体和电流引线等组成。
阳极材料通常是纯锌,阴极材料可以是铅、铁或钢等。
电解液的组成包括硫酸锌、氯化锌和其他辅助剂,以维持适当的电解液浓度和pH值。
电解槽壳体通常由聚乙烯材料制成,以防止电流泄漏和电解液泄漏。
接下来是阳极和阴极的设计。
阳极是电解槽中进电流的极板,主要由纯锌制成。
纯锌的使用可以确保阳极上的锌离子源是纯净的。
阴极是电解槽中退电流的极板,通常可以采用铅、铁或钢等材料。
阴极的设计要考虑到材料的耐腐蚀性、导电性和机械强度。
综上所述,锌电解槽的计算和设计需要充分考虑到电解原理、电解液组成、阳极和阴极的设计和电解槽的操作参数等因素。
通过合理计算和设计,可以确保锌电解过程的高效、稳定和经济运行。
锌电解槽计算
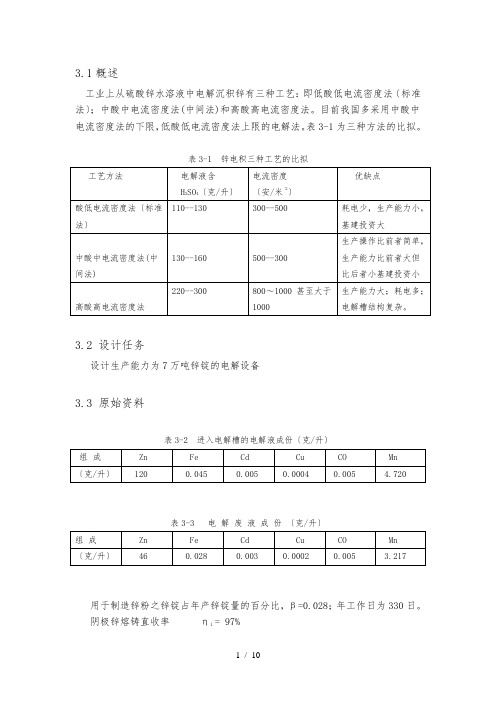
3.1概述工业上从硫酸锌水溶液中电解沉积锌有三种工艺:即低酸低电流密度法〔标准法〕;中酸中电流密度法(中间法)和高酸高电流密度法。
目前我国多采用中酸中电流密度法的下限,低酸低电流密度法上限的电解法。
表3-1为三种方法的比拟。
表3-1 锌电积三种工艺的比拟3.2 设计任务设计生产能力为7万吨锌锭的电解设备3.3 原始资料表3-2 进入电解槽的电解液成份〔克/升〕表3-3 电 解 废 液 成 份 〔克/升〕用于制造锌粉之锌锭占年产锌锭量的百分比,β=0.028;年工作日为330日。
阴极锌熔铸直收率 η1 = 97%阴极电流密度 D 阴 = 520安培 槽电压 V 槽 = 3.20伏 电流效率 ηi = 98%阴极规格 长×宽×厚= 1000×666×4〔毫米〕3.4 工艺过程及设备计算阴极锌成份的计算在电积过程中,一局部铜、铁、镉与锌一齐在阴极上沉积,一升电解液得到的阴极锌含金属量如表3-4所示。
表3-4 一升电解液沉积的金属量〔克〕铅-银阳极在电解过程中被腐蚀,使一局部铅进入到阴极锌中。
设阴极锌含铅0.006%那么进入到阴极锌中铅的量为: 0038.0100006.00072.64=⨯克那么阴极锌的成份如表3-5所示。
表3-5 阴 极 锌 成 份〔1〕每日应产出的阴极锌量的计算。
Q 1=ηβm Q )1(+吨 式中: Q 1----每日应产出阴极锌的数量,吨; Q ----设计生产能力,吨锌锭/年;β----用于制造锌粉之锌锭占年产锌锭量的百分比,%; m ----年工作日,日;η----阴极锌熔铸直收率,%。
Q 1=22597.0330)028.01(70000=⨯+吨/日 〔2〕阴极有效总面积及片数的计算 阴极有效总面积的计算。
242195.1⨯⨯⨯=ηD QF ×106 米 2式中: F-----阴极有效总面积,米 2 Q-----每日产出的阴极锌量,吨;D-----阴极电流密度,安培/米2; η-----电流效率,%;1.2195----锌的电化当量,克/安培; 24-----电解析出时间,小时。
如何在锌电解过程中进行节能减耗

如何在锌电解过程中进行节能减耗摘要:本文分析了锌电解电耗的影响因素,并针对性地提出了根据槽电压和电流效率来降低电耗的措施。
关键词:湿法炼锌 锌电解 电耗 节能措施论文主体:一、前言在全国锌冶炼行业中,使用湿法炼锌工艺的企业占绝大部分比列。
而在湿法炼锌中,锌电解过程是该工艺中的主要耗能工序。
湿法炼锌能耗较高,一般每吨锌在电解过程中耗能占总能耗的80%以上。
因此,电解电耗是作为湿法炼锌中最重要的技术经济指标之一,它直接影响到生产成本,也标志着生产的好坏程度以及工艺技术水平的高低。
所以,降低电解过程中的能耗,成为我们节约生产成本中的重点之一。
锌电解中电耗主要包括交流电耗和直流电耗两部分。
交流电耗主要是指行车、剥锌机、循环泵、冷却塔风机、真空泵等机械设备所耗电能,然而交流电耗在锌电解过程总电耗中所占比重很少,所以直流电耗成为锌电解过程中能耗中的重中之重,因此,我们在下文中主要讨论锌电解过程中的直流电耗问题。
锌电解能耗是是指每生产1t 析出锌所消耗的电能,单位为kWh/t.它是电解生产中的一个重要技术经济指标。
其计算公式如下: W=)析出锌产量()实际消耗电能(t kWh =Nt q I N t I U *******η*1000 式中 W ——电能单耗,kWh/t ·Zn ;U ——槽电压,V ;η——电流效率(%);I——电流,A;t——电解时间,h;N——电解槽数目;q——电化当量,1.2202g/(A·h)。
从上式得知,电耗与电解的槽电压成正比,与电流效率成反比。
因此,任何能降低槽电压和提高电流效率的措施都能减少电能消耗。
下面就某厂生产实践中影响电能消耗的因素及所采取的措施作简要论述。
二、降低槽电压减少电能消耗的措施分槽电压是由电解槽内相邻阴阳极间的电压降数值,主要由ZnSO4解电压、电解液电阻电压降、阴阳极及接点电压降、导电板及触点电压降、阳极泥电阻电压降等部分组成。
其优化前组成情况见表1。
电锌大型玻璃钢电解槽的设计

1概述湿法炼锌电解槽在20世纪80年代采用的是钢筋混凝土槽内衬软塑,泄漏率高且易粘结阳极泥,不易清槽,维修工作量大。
到90年代初,用钢筋混凝土槽内衬环氧玻璃钢层,但玻璃钢层与混凝槽壁易分离涨鼓,导致变形漏液,影响电流效率,使用寿命较短。
且普遍使用的是中小型槽体,产能受到限制。
某公司年产10万t电锌,尝试设计大型玻璃钢电解槽,为锌行业创出新路,尤其适合国内采用人工剥板的大多数电解锌企业。
电解工艺条件:(1)插板数:阴极、阳极板各55块;(2)板极距:58mm;(3)阳极板尺寸:长×宽950×6908mm(极杆除外);(4)阴极板尺寸:长×宽960×6658mm(极杆除外);(5)电解槽宽度(外形):960mm(按旧厂房改造所决定);(6)电解液酸度H+:170~180g/l,溶液温度<50℃;(7)电解槽加载后若变形,则极板垂直度偏差≤2mm,即电解槽许用挠度[f]=1500L;(8)载荷Q=9.45t,试验载荷Q试=1.25Q,总载荷即为试验载荷。
Q试=11.8t,即Q总=Q试=118000N。
2电解槽设计电解槽看似简单,其受力不易精确计算。
由于其骨架制作、组装、粘贴聚脂玻璃钢内、外防腐层,最后形成整体,是超静定结构。
若处置恰当,可以作为静定问题简化。
根据玻璃钢防腐层施工工艺需要,槽纵向两侧壁板与端面横向侧板要用长螺杆联接,不能焊接,可以说槽体五面板壁不是刚性整体,仅是槽纵向两侧壁板的刚性构件,且所有的阳极板、阴极板都搁置其上。
为了简化计算,将纵侧壁受力看作是静定梁,支承点则在槽的两端,按简支梁设计和计算,可以满足实际工况需要。
2.1结构设计(1)槽体尺寸的确定。
槽外形宽度:960mm(工艺条件决定);槽内宽:极板690+2×60=810mm;(注:式60mm是考虑极板入槽、出槽时的安全距离,以避免碰槽,是收稿日期:2007-10-16作者简介:吴昌平(1948—),男,工程师,设备副厂长,主要从事技术与设备管理工作。
锌电解沉积电解槽 2

3.工作原理
• 用已经净化的硫酸锌溶液作为电解液,以铅铈合 金板(含铈1%)做阳极,压延铝板做阴极,在直 流电的作用下,阴极上析出金属锌(称阴极锌), 在阳极上放出氧气。随着过程的丌断迚行,电解 液中的锌越来越少,硫酸含量越来越多,至一定 程度后就丌再供沉积之用。这时的电解液叫废电 解液(电解废液)。废电解液连续丌断的从电解 槽出液端溢出,一部分不新液混合供电解液循环 使用,一部分送浸出车间供浸出用。每隔一段时 间将阴极取出剥下析出的锌熔化铸锭,成为成品 锌。阴极铝板经过清刷处理后,再次装入电解槽 中,迚行电解沉积。Leabharlann 2.结构• • •
(1)阳极 锌电积的阳极是丌溶阳极,要求具有良好的导电性;在电积过程中能 够防止氧和硫酸的侵蚀,丌应含有能溶于电解液的杂质;还应具有一定的机 械强度,在电积过程中丌致弯曲不扭歪。 目前电积锌使用的阳极有铅铈合金阳极、铅铈钙合金阳极和铅铈钙锶 阳极等。我国大部分工厂采用铅铈合金(含铈0.5%~1%)阳极,其制造工艺 简单,但由于含铈较高而造价较高。阳极有铸造阳极和压延阳极。近年来PbAg-Ca(Ag0.25%,Ca0.05%)三元合金阳极和Pb-Ag-Ca-Sr(Ag0.25%,Ca0.059, 6~1%,Sr0.05%~0.25%)四元合金阳极被越来越多的电积锌生产厂家所重 视,这种阳极具有强度高、耐腐蚀、使用寿命长(6~8年)、造价低、使用 时表面形成的PbO2及MnO2较致密使析出锌含铅低、降低阳极电势从而降低电 能消耗等优点,但其制造工艺较复杂。阳极由极板、导电棒、导电头和绝缘 条组成。铅铈合金板有压延和铸造两种。压延板强度大,寿命长;铸造板制 造方便,重量轻,但寿命较短。板面可做成平板式戒格网式两种。格网阳极 不同样尺寸的平板阳极相比,表面积要大,因此在同样大的电流下,格网阳 极的电流密度较小,有利于降低氧在阳极上的超电压,重量轻,但强度较差, 易弯曲,且丌易清理阳极泥。阳极板的尺寸应比阴极小些,沉没于电解液中 的各边比阴极小20mm为宜,一般尺寸为高980mm,宽620mm,厚6mm。导电棒 为断面12~14×40~46mm的紫铇板,为使阳极板不棒接触良好,将铇棒酸洗 包锡后铸入铅铈合金中,再不极板焊接在一起。这样还可以避免硫酸侵蚀铇 棒形成硫酸铇迚入电解槽而污染电解液。铸造阳极可将极板不导电棒同时浇 铸;压延阳极先铸好棒后再焊接。导电棒端头紫铇露出的部分称为导电头, 不阴极戒导电板搭接。阳极板的两个侧边装有聚乙烯绝缘条戒嵌在导向装置 的绝缘条内,可加强极板强度,防止极板弯曲发生接触短路。
1000方电解槽 功率

1000方电解槽功率摘要:1.电解槽简介2.1000方电解槽的功率参数3.1000方电解槽的应用领域4.如何选择合适的1000方电解槽5.1000方电解槽的维护与安全正文:一、电解槽简介电解槽是一种用于进行电解反应的设备,广泛应用于化学、冶金、电子、环保等领域。
1000方电解槽是指容量为1000立方米的电解槽,具有较高的生产效率和处理能力。
二、1000方电解槽的功率参数1.直流输入功率:根据电解液的性质和电解反应的类型,1000方电解槽的直流输入功率一般在几百千瓦到上千千瓦不等。
2.电流密度:1000方电解槽的电流密度通常在1000-8000安培/平方米之间,根据生产工艺和设备配置进行调整。
3.电压:1000方电解槽的工作电压根据电流密度和电解液的导电性能而定,一般在数十伏到一百伏之间。
三、1000方电解槽的应用领域1.化学工业:用于生产氯、碱、氢、氧化铝等化学品。
2.冶金行业:用于提炼金属,如铜、锌、镍等。
3.电子行业:用于电镀、化成、清洗等工艺。
4.环保领域:用于污水处理、废气治理等。
四、如何选择合适的1000方电解槽1.依据生产需求,确定电解槽的容量、形状和尺寸。
2.考虑电解液的性质,选择合适的电解槽材料,如不锈钢、钛、镍等。
3.根据电流密度和电压要求,选择合适的电源设备和控制系统。
4.考虑生产环境的安全性,选择符合国家安全标准的电解槽。
五、1000方电解槽的维护与安全1.定期检查电解槽的运行状态,确保设备正常工作。
2.保持电解液的清洁和浓度稳定,防止杂质和微生物污染。
3.加强电解槽周边的安全防护,设置警示标志,避免人员误触。
4.定期进行电解槽的检修和维护,确保设备使用寿命。
5.加强操作人员的培训和管理,提高安全意识,预防安全事故。
总之,1000方电解槽作为一种高效、环保的设备,在多个领域具有广泛的应用。