细磨石灰石粉替代部分生石灰粉进行烧结生产总结
石灰石代替石灰在转炉炼钢中的应用实践分析

石灰石代替石灰在转炉炼钢中的应用实践分析近年来,在炼钢行业中发现,相比于传统模式中用石灰在转炉炼钢,利用石灰石代替石灰能够取得高效的炼钢质量和效率,降低石灰消耗量,进而降低炼钢成本,为企业获得更高收益。
文章就围绕石灰石代替石灰在转炉炼钢中的应用实践进行分析探究。
标签:石灰石;转炉炼钢;降温材料前言随着可持续发展战略的进一步加深,各行各业都越加重视能源节约问题,在炼钢生产领域,对于炼钢成本的控制也提出了更高的要求。
2013年,西钢炼钢厂率先选用石灰石代替石灰,投入到转炉炼钢生产当中,不但实现了转炉内多余热量的有效利用,而且起到较好的节能减耗效果,进一步提升了企业的经济收益。
1理论支撑1.1 石灰石代替石灰在现代炼钢行业当中,通常是选用石灰作为转炉炼钢的主要造渣材料,而石灰属于石灰石经过高温煅烧后形成的产物。
2013年,西岗炼钢厂通过技术革新,率先在转炉炼钢中直接投入石灰石,用石灰石取代石灰作为转炉炼钢材料工作,也就是将石灰石煅烧过程与转炉炼钢过程有效结合到一起,并取得不错效果。
究其本质原因,由于转炉在正常工作状态下,炉内温度通常会保持在1300℃与1400℃中间范围内,因此,将石灰石投入转炉后会直接受到的1300℃至1400℃的高温煅烧,瞬间升温会导致石灰石外表层的碳化钙会进行化学分解反应,这高温情况下,使得原本应需达到2-5小时的分解过程能够迅速完成。
1.2 利用石灰石降温在传统的炼钢领域中,除了转炉炼钢过程较长问题之外,还存在降温材料资源较少而且材料成本较高的问题,这同样严重阻碍了转炉炼钢工作的正常开展,各炼钢企业都在迫切尋求寻找成本较低、来源丰富且降温作用明显的新型材料,以解决现有的降温材料问题。
从理论角度来讲,石灰石在投入转炉后,会在高温煅烧情况下产生化学反应,生产氧化钙和大量的二氧化碳,在这过程中,会消耗大量的热能。
由此可见,将石灰石应用到转炉炼钢中,不但能够取代石灰满足转炉的碱性需求,另外还能够有效消耗转炉内多余的热能,起到降温材料所应当发挥的效果,进而降低用于降温的金属材料的用量,不但能够为企业大幅压缩用于降温材料的生产成本,还能够有效环节能源短缺问题,具有十分可靠的应用可行性[1]。
电石渣代替部分石灰石配料的生产实践

2~3 < 0.3
- 20~- 50
窑 尾 温 度/℃
1 000~1 100
- 100~- 200
二 次 风 温/℃
900~1 000
300~320
三 次 风 温/℃
900~950
520~530
入 窑 表 观 分 解 率/%
90~95
640~660
掺入后 780~790 840~850 860~870 900~910 90~100
1) 电 石 渣 中 细 颗 粒 较 多 , 10 ~50μm 的 颗 粒 占 80%以上, 80μm 筛筛余< 8%, 同时由于降低了石灰石 入磨粒度, 导致生料磨内钢球级配不合理, 大球多, 小 球少, 冲击能力过强, 研磨能力减弱, 造成磨机产量降 低。
2) 原来石灰石、砂岩、铁粉和粉煤灰 4 种物 料配 料, 入磨 物料综合水 分为 2.8%; 电石 渣含水分较 大, 含量在 30%左右, 电石渣掺入后, 入磨物料综合水分 达到 5.6%。由于物料综合水分含量升高, 造成烘干能
好, 且开关灵活。防止大量冷风漏入后,入磨风量减 少, 入磨废气温度降低, 导致磨机烘干能力下降, 影响 磨机产量。
通过以上措施的实施, 解决了因掺入电石渣后生 料磨产量降低的问题, 生料磨恢复了正常生产。
4 烧成系统出现的问题及解决措施
4.1 出现的问题 采用电石渣代替部分石灰石进行配料后, 预热器
SO3 烧失量 R2O 比表面积 筛余
/%
/%
/% /(m2/kg) /%
凝 结 时 间/min
初凝
终凝
安定性
抗 折 强 度/MPa
3d
28d
2.9
3.5
0.60
转炉炼钢中用石灰石部分代替石灰的生产实践

关键词 : 转炉炼钢 ; 石灰石 ; 石灰 ; 碱度 ; 成 本
中 图分 类 号 : T F 7 1 3 . 3 文 献标 识 码 : A 文章编 号 : 1 0 0 6— 5 0 0 8 ( 2 0 1 7 ) 1 1 — 0 0 5 4— 0 4
成本 , 又创 造 了资 源 。在 当前环 保压 力 下 , 石 灰 的生
( 1 ) 满 足转 炉冶 炼 时间
石灰 石受 高温 分解 方程 式 :
Ca CO3 _ Ca O 十 1 2 0—1 4 4 . 6 T J / mo l
Ke y W or d s:c o nv e Re r s t e e l ma ki ng; l i m es t on e; l i m e;a l ka l i ni t y;c o s t
0
弓 l 言
石灰 石代替部 分石灰及 冷料达到转 炉热平衡 。
1 使 用石 灰石 代 替石灰 的 理论依 据
W a n g Yu g a n g,Fa n S a i ,Ch e n Don g n i n g,Li u Da o me n g,Zh a o Gu a ng x u n
( No . 1 S t e e l Mi l l o f HBI S Gr o u p Ha n s t e e l Co mp a n y,Ha n d a n,He b e i ,0 5 6 0 1 5)
d o i : 1 0 . 1 3 6 3 0 / j . c n k i . 1 3—1 1 7 2 . 2 0 1 7 . 1 1 1 4
PRODUCTI ON PRACTI CE OF PARTI AL LI M ESTONE
工业生产工艺之烧结小结
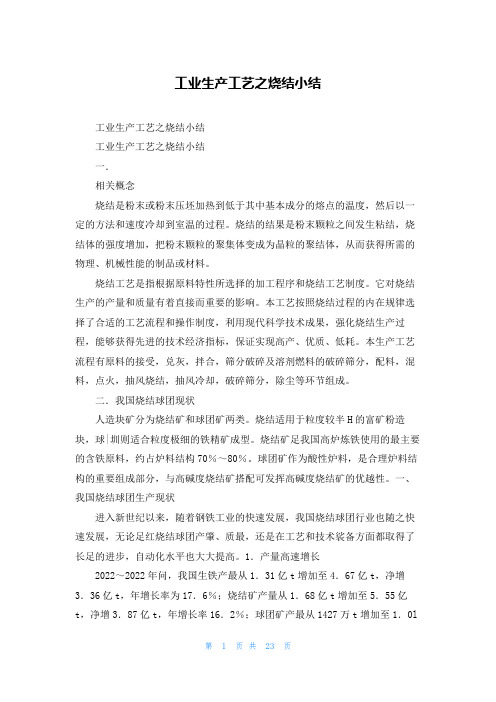
工业生产工艺之烧结小结工业生产工艺之烧结小结工业生产工艺之烧结小结一.相关概念烧结是粉末或粉末压坯加热到低于其中基本成分的熔点的温度,然后以一定的方法和速度冷却到室温的过程。
烧结的结果是粉末颗粒之间发生粘结,烧结体的强度增加,把粉末颗粒的聚集体变成为晶粒的聚结体,从而获得所需的物理、机械性能的制品或材料。
烧结工艺是指根据原料特性所选择的加工程序和烧结工艺制度。
它对烧结生产的产量和质量有着直接而重要的影响。
本工艺按照烧结过程的内在规律选择了合适的工艺流程和操作制度,利用现代科学技术成果,强化烧结生产过程,能够获得先进的技术经济指标,保证实现高产、优质、低耗。
本生产工艺流程有原料的接受,兑灰,拌合,筛分破碎及溶剂燃料的破碎筛分,配料,混料,点火,抽风烧结,抽风冷却,破碎筛分,除尘等环节组成。
二.我国烧结球团现状人造块矿分为烧结矿和球团矿两类。
烧结适用于粒度较半H的富矿粉造块,球|圳则适合粒度极细的铁精矿成型。
烧结矿足我国高炉炼铁使用的最主要的含铁原料,约占炉料结构70%~80%。
球团矿作为酸性炉料,是合理炉料结构的重要组成部分,与高碱度烧结矿搭配可发挥高碱度烧结矿的优越性。
一、我国烧结球团生产现状进入新世纪以来,随着钢铁工业的快速发展,我国烧结球团行业也随之快速发展,无论足红烧结球团产肇、质最,还是在工艺和技术裟备方面都取得了长足的进步,自动化水平也大大提高。
1.产量高速增长2022~2022年问,我国生铁产最从1.31亿t增加至4.67亿t,净增3.36亿t,年增长率为17.6%;烧结矿产量从1.68亿t增加至5.55亿t,净增3.87亿t,年增长率16.2%;球团矿产最从1427万t增加至1.0l亿t,净增8637万t,年增长率28.2%。
近年来全国生铁、烧结矿和球团矿产量见图1。
2.设备大型化我国烧结不仅在数量上增长迅猛,在技术装备水平上也有一个大匕跃。
1985年,宝钢从日本引进的450m2烧结机投产,显示了诸多的优势,烧结矿质量好、能耗低,劳动生产率和自动化水平高,便于生产管理和环境保护,技术经济指标达到了囤际先进水平。
石灰石替换部分石灰造渣的工艺实践

在炉外需要煅烧 3~5 h的石灰石在转炉炉 内由
(3) 石灰 石 在 分解 后 ,铁 一 渣界 面 会有 一
于 内外表面巨大的温度差 ,使石灰石煅烧速度 段 时间保持低温 ,更有利 于铁水在吹炼初期 的
加快 ,煅烧时间降到几分钟 以内 ,这个时 间不 脱磷。
影 响转炉 生产 节奏 。
(4) 在石灰 生成 瞬间 ,其具 有较 大 的活
(3) 辅 料 用 量 大 (约 31.5元 /吨 ),吨 钢 渣量增加 ,不仅使物料成本上升还带走 部分钢 水 ,不利于钢耗指标的完成 。
(4)终点磷质量分数 只有 0.02%,对于冶
作者 :李健畅 ,大学 学历 ,工程师 ,现主要从事 炼终点 磷质量 分数要 求 <0.035%的钢种来 说 ,
关 键词 :转炉 冶炼 ;造 渣 ;石 灰石 ;石 灰 ;物耗 ;终点渣 成分
Process Practice on Partial Lim e Slagging Replaced by
一
●
~
一
一
Lim estone Slagging
LI Jianchang W ANG Zhiguo CHEN Lipeng
2.3 石 灰石 造渣 的优 势
进行 ,即当炉 内温度 >896℃时 ,石灰石分解为
(1)省去石灰石在石灰窑 中的煅烧步骤 ,
CaO和 CO 气体 ,氧枪开 吹时转炉 内铁水温度 大幅度降低石灰煅烧成本和热量损失 ,原料的
一 般在 1 200 oC~1 400℃,转炉熔池火点温度 进货与管理都更加方便简单。
得 到较 大 程 度 的缓 解 。而 当转 炉 冶 炼 中 ,终 点 磷 已经 远 低 于 钢 种 要 求 的范 围时 ,就 会 出现 质 量 过剩 的情 况 ,进 而 导致 指标 退 步 、成 本 上 升 。 本 着 精 细 化 管 理 的原 则 ,就 必 须 对 现 有 的物 料 结构实行优化 ,在保证钢水质量的前提下 ,对 转 炉 造 渣 物 料 进 行 调 整 ,并 在 改进 过 程 中跟 踪 终点成分和渣样的变化 ,建立相关合 理的工艺 模 型 ,选 取综 合 质量 成本 最 优 的方 案 投入 生产 。 本 文总结采用石 灰石替换部分石灰造渣 的工艺 实 践 。
用电石渣代替生石灰与石灰石的研1

用电石渣代替生石灰与石灰石的研究藏疆文张群王梅菊摘要本文从电石渣的理化性能、对烧结矿产质量的影响、烧结矿的矿物组成与显微结构、烧结矿成本等方面研究了用电石渣代替生石灰与石灰石生产烧结矿的可行性,结果表明,可以用电石渣代替部分或全部石灰石与生石灰。
用电石渣代替石灰石时,原料成本变化不大;用电石渣代替生石灰时,每配加1t电石渣,可降低烧结矿生产成本62.40元。
1.引言我国电石主要用于生产乙炔,然后进一步用于生产聚氯乙烯(PVC)、醋酸乙烯、氯丁橡胶、三氯乙烯、四氯乙烯、双氰胺等化工产品,以及用于金属加工业(切割焊接等)。
我国2004年共消费电石540万t,其中:生产聚氯乙烯消耗电石约340万t,生产醋酸乙烯等其它化工产品消耗电石约100万t,金属加工业消耗电石约100万吨.电石渣是由电石加水生成乙炔气过程中产生的废渣,电石渣的主要成分是Ca(OH)2,它的化学反应式为CaC2十H2O=C2H2 + Ca(OH)2根据计算,每使用1t纯电石,大约要生成1.16t电石渣。
仅2004年,我国就产生600多万t电石渣。
目前,对电石渣的利用主要有两个方面,一是用于建筑工业,如制水泥、煤渣砖等;另一方面是用于环境治理,如酸性污水处理、污泥脱水、烟气脱硫等。
通过这些途径仅利用了部分电石渣,仍有大量电石渣未被利用。
电石渣的大量堆放既占用了大量的土地资源,又污染了环境。
因此,如何合理利用电石渣是一个待解决的问题。
在生产烧结矿过程中,需在烧结料中配加碱性熔剂,其目的在于:(1)获得一定碱度烧结矿,使高炉冶炼时不加或少加熔剂,以利于提高高炉冶炼强度,降低焦比;(2)在烧结过程中,熔剂中的碱性物质CaO及MgO可以与矿粉中的酸性脉石Si02及Al2O3组成低熔点物质,从而在燃料消耗较低的情况下,获得足够的液相以改善烧结矿的强度及冶金性能(还原性);(3)烧结配加生石灰,可以改善混合料的成球性。
目前,烧结生产过程中使用的碱性熔剂包括:白云石、石灰石及生石灰等。
用石灰石部分替代石灰造渣炼钢过程行为初探

用石灰石部分替代石灰造渣炼钢过程行为初探李军辉杨利康龙广黄燕飞(杭州钢铁集团公司转炉炼钢厂, 杭州 310022)摘 要 通过分析石灰石热分解过程中的能量消耗、特征性能及分解过程中的渣化反应,用石灰石原矿部分替代石灰的工业实践表明使用石灰石原矿不仅可减少冷却废钢的用量,还可以平衡转炉富余的热量;石灰石部分替代活性石灰,还可以降低石灰石煅烧过程能耗,有利于节能环保的同时满足了转炉冶炼普通钢种的要求。
关键词 转炉炼钢石灰石造渣The Research of Slag Forming Steelmaking Process aboutPartial Substitution of Lime with LimestoneLi Junhui Yang Likang Long Guang Huang Yanfei(The Converter Steelmaking Plant of Hangzhou Iron and Steel Group Company, Hangzhou, 310022)Abstract Through the analysis of limestone slag forming reaction during the thermal decomposition of energy consumption, performance characteristics and decomposition process, show that industrial practice of limestone ore partial substitution of lime, the use of limestone ore is not only reduce the consumption of cooling scrap steel,but also can be balance the rich heat of smelting process;limestone partial instead of active lime, also can reduce energy consumption during the calcination of limeston. The process of steelmaking is conducive to energy conservation and environmental protection and satisfy the requirements of ordinary steelmaking.Key words converter steelmaking, limestone, slag forming北京科技大学提出了一种新的炼钢方法,用石灰石代替石灰加入转炉造渣炼钢,已在国内两个钢铁公司进行工业试验取得了成功,这一方法是对氧气转炉炼钢工艺的大变革。
石灰石代替石灰电炉冶炼工业试验研究柯飞飞1高建军2

石灰石代替石灰电炉冶炼工业试验研究柯飞飞1 高建军2发布时间:2021-08-19T01:39:07.450Z 来源:《基层建设》2021年第15期作者:柯飞飞1 高建军2 [导读] 本文通过工艺设计,在电炉粗炼钢水阶段,分批次加入石灰石以代替石灰进行造渣,验证石灰石造渣的工艺合理性和经济性。
工业试验表明,合理的工艺技术手段,电炉石灰石替代比可达70%以上,且冶炼过程平稳可控,在保证粗炼钢水冶金质量的同时有效降低了电炉造渣成本。
1.2天津重型装备工程研究有限公司天津 300457摘要:本文通过工艺设计,在电炉粗炼钢水阶段,分批次加入石灰石以代替石灰进行造渣,验证石灰石造渣的工艺合理性和经济性。
工业试验表明,合理的工艺技术手段,电炉石灰石替代比可达70%以上,且冶炼过程平稳可控,在保证粗炼钢水冶金质量的同时有效降低了电炉造渣成本。
关键词:石灰石;石灰;电炉一、前言现有的电炉造渣工艺,石灰石作为造渣原料,并不少见。
电炉冶炼过程中,石灰石一般可作为造渣主原料和冷却剂,常见于高比例热兑铁水冶炼方式,如铁水配比大于60%,由于高强度吹氧下粗炼钢水升温迅速,为合理控制钢水升温节奏,提高前期造渣脱磷工艺效果,除石灰外,还需搭配使用一定比例的石灰石、轻烧白云石、改渣剂对熔渣进行改性处理,以满足粗炼钢水冶金质量对熔渣的理化指标要求。
中国一重炼钢厂现有电炉100T、40T各一台,其钢水主要产品以大型铸锻件为主,对[P]、[S]等有害残余元素要求较高,其电炉出钢一般[P]≤0.003%,重点产品则要求[P]≤0.001%。
由于属全废钢冶炼,其冶炼周期较长,吨钢石灰用量在400-600kg之间,较一般冶金电炉单耗高出25%-35%。
其冶金石灰外供,单价较高且原料质量波动较大,导致冶金过程难以把控。
考虑到电炉粗炼钢水对于产品最终冶金质量的影响较小,且吨钢石灰用量最大,提出用部分石灰石代替石灰在电炉造渣,设计了工艺方案,并进行了15个炉次的工业试验,对各项经济技术指标进行了分析对比,同时观察替换后电炉冶金过程的可控性。
转炉中石灰石替代石灰对脱磷、炉气成分及氧枪枪位的影响

125管理及其他M anagement and other转炉中石灰石替代石灰对脱磷、炉气成分及氧枪枪位的影响白志坤,张文祥,张万庆,冯 帅(河钢集团唐钢新区,河北 石家庄 050000)摘 要:在转炉炼钢过程中用石灰石代替石灰进行冶炼,可以降低炼钢成本,减少CO 2排放。
为了改善转炉炼钢过程中,石灰石对脱磷,炉内气体成分和氧枪枪位的影响,对生产实践数据进行了汇总。
通过不断实践摸索和热力学分析结果表明,石灰石替换比为25%时脱磷效果最佳,比原有炼钢工艺模式的终点磷含量降低了47%。
同时在进行工艺改善后,煤气回收时间增加1min ~2min,这就就会大大提升了煤气的回收量,使转炉炼钢过程中的氧枪枪位由1.7m 提升到1.8m。
关键词:转炉炼钢;石灰石替代比;分解;脱磷效率;炉气成分;氧枪枪位中图分类号:TF713 文献标识码:A 文章编号:11-5004(2020)22-0125-2 收稿日期:2020-11作者简介:白志坤,男,生于1988年,河北唐山,本科,中级工程师,研究方向:炼钢工艺技术。
在我国传统的石灰结渣和炼钢工艺中,首先将石灰石在石灰窑中破碎,并以生产出活性石灰,然后将活性石灰装入造渣和炼钢转炉内,这种钻孔过程增加了石灰窑的基础设施。
而且这种石灰石的生产成本较高,同时会使周围的空气受到严重的污染,显然不是最理想的炼钢方式。
随着我国炼钢工艺的不断提升,很多企业开始利用石灰石代替石灰完成造渣炼钢,不管是生产成本还是生态环境保护上,都得到了巨大的收益。
目前关于石灰石在转炉炼钢中的应用有很多的相关研究资料。
很多冶金企业对这一工艺模式进行了大量的生产实践。
在炼钢过程中使用纯氧后,在转炉中会产生大量热量,因此,必须添加石灰石或白云石以在冶炼的后期完成吸热冷却过程。
但在整个工艺研究过程中,很少考虑到节能环保问题,为此有很多的专家学者提出了氧气转炉炼钢过程中,利用石灰石代替石灰造渣的炼钢工艺模式,同时也将其应用到冶金的实践当中,但由于不同的冶金企业所用的转炉不同原辅料和生产模式也具有不同的优势,因此,在这一工艺模式的利用效果中,也不尽相同。
配加石灰石粉前后生产技术指标对比总结(汇总)

配加石灰石粉前后生产技术指标对比总结一、对烧结过程影响根据厂部安排从1月25日起,一烧尝试配加不同配比的石灰石粉代替部分溶剂,先后配加3.0%、3.5%、4.0%不同配比,配加石灰石粉后生产技术指标对比总结如下:未配加石灰石粉前,料流控制在64-65kg,固体燃耗平均57-59kg/t,碱度在1.95-2.0之间,混合料温62-65°,1#机速平均50-52HZ,2#机速平均19-20HZ,1#机料层厚度平均680mm,总管负压13.0kpa左右;2#机料层厚度平均720mm,总管负压13.5-14.0kpa,双机终点温度控制在300°以上。
配比3.0%-3.5%时:料流控制在64-65kg,与没有配加石灰石粉前比较料流没有变化,固体燃耗平均58-60kg/t,与没有配加前上升近1-2kg/t,碱度在2.0-2.05之间,有上升趋势,混合料温58-60°,平均混合料温下降5°左右,1#机速平均50HZ,2#机速平均19HZ,1#机料层厚度平均670-690mm,下降10mm左右,总管负压13.5kpa,与没有配加前上升0.5kpa;2#机料层厚度平均700mm左右,平均下降20mm,总管负压14.0-14.5kpa,平均升高0.5kpa,双机废气温度及终点温度能够保证在正常范围。
配比 4.0%时:料流平均62-63kg,料流下降2kg,固体燃耗60-61.5kg/t,上升2-3kg/t,碱度平均在2.0-2.05之间,变化不大,混合料温52-56°,下降10°左右,1#机速平均48HZ,平均下降1-2HZ,料层平均650mm,下降30mm,总管负压13.8-14.0kpa,上升0.8-1.0kpa;2#机速平均18HZ,料层厚度680mm,下降40mm,总管负压14.5-15.0kpa,上升1.0kpa,双机终点温度在280°左右,下降20°以上。
采用石粉部份替代石灰石进行配料改造的措施

134Burdening技术/配料鹿泉金隅鼎鑫水泥有限公司三分公司拥有一条Ф5×60m 二档短窑熟料生产线,由原天津院设计,设计能力为日产熟料4000吨,实际生产能力达到了6300吨;该生产线生料系统采用了TRM53.4辊式立磨,磨机设计台时440吨/小时,磨机吨电耗为15度。
2009年4月投入运行后,生料磨吨电耗一直偏高,实际生料磨电耗为18度左右。
为充分发挥示范线作用,提高市场竟争力,我公司经调研发现,每年该地区周围有近千万吨被采石厂废弃的下脚料石粉,一是该石粉品位虽偏低、不稳定,但经过工艺调整可以部分替代石灰石原料,节约日趋紧张的矿产资源。
二是采石厂距市区较近,周边石粉堆积成山,严重污染环境,三是石粉价格低廉,可降低成本,提高产品竞争力。
为此我公司计划通过改造生料立磨系统实现石粉替代部分石灰石以达到节能降耗的目的。
立磨系统采用石粉添加部分替代石灰石改造项目,主要问题是需解决石粉的添加改变了原来的入磨原料颗粒级配,对生料磨立磨系统稳定性产生较大影响的问题,同时解决石粉添加过程粉尘治理问题。
我公司通过对立磨系统各个参数的调整,对设备进行局部改造,最终实现了生料立磨系统的高产稳定运行,有效降低生料制备电耗,且保证了窑系统高产运行。
具体措施如下:采用石粉部份替代石灰石进行配料改造的措施韩永鹏李胜保(鹿泉金隅鼎鑫水泥有限公司,河北鹿泉050200)摘要:TR M53.4辊式立磨系统将石灰石粉末部分替代石灰石进行配料改造。
通过调整立磨的挡料环高低,优化参数,对风环形式和结构进行改造,优化通风面积和风速等措施使立磨系统适应原料颗粒级配的变化。
使石粉替代石灰石掺加比例到40%,超出设计台时产量40余吨,并且合理利用废渣,降低生产成本,更好的实现资源综合利用。
关键词:石粉替代石灰石降耗中图分类号:TQ 172.614文献标识码:B文章编号:1007-6344(2013)09-0134-02135 Burde ning配料/技术1挡料环的优化调整由于石粉的掺加,原入磨原料颗粒级配发生了重大变化,为稳定磨机料层,寻找最佳挡料环高度。
转炉石灰石代替石灰造渣炼钢研究现状及展望

转炉石灰石代替石灰造渣炼钢研究现状及展望摘要:钢铁行业作为重要的基础产业,其生产过程中能源消耗大、环境污染严重。
为实现可持续发展,石灰石替代石灰在转炉炼钢中的应用逐渐受到关注。
本文从石灰石替代石灰的基本原理、炼钢过程中的作用、实验研究与技术创新、以及未来发展趋势等方面进行了详细论述。
结论指出,石灰石替代石灰在转炉炼钢中具有显著的优势和广阔的发展前景,是推动钢铁行业可持续发展和环境友好转型的重要技术创新。
关键词:石灰石;石灰;转炉炼钢;替代;可持续发展;环境友好一、引言随着全球工业化进程的加速,钢铁作为基础建设和制造业的关键材料,需求量逐年上升。
转炉炼钢法是目前钢铁生产中最为广泛采用的方法之一,由于其较高的生产效率和较低的成本,深受钢铁企业的青睐。
然而,在传统的转炉炼钢法中,石灰作为造渣剂的使用,不仅会带来能源消耗与成本问题,还会对环境产生一定的负面影响。
因此,研究石灰的替代品成为了业界关注的焦点。
在这一背景下,石灰石作为石灰的一种替代品,逐渐引起了学者和工程师们的关注。
石灰石与石灰在化学成分上有一定的相似性,但石灰石的价格更低、资源更丰富,这使得石灰石在转炉炼钢中的应用具有很大的潜力。
然而,由于石灰石的物理性质与石灰有所差异,如何在保证钢铁生产质量和效率的前提下,实现石灰石在转炉炼钢中的替代,仍是一个亟待解决的问题。
本文旨在分析石灰石在转炉炼钢中替代石灰的研究现状,并探讨其环境、经济和技术方面的前景。
首先,通过对比石灰与石灰石的化学成分、物理性质和反应机理,阐述石灰石替代石灰的可能性与挑战。
其次,对现有的实验研究与技术创新进行分析,总结石灰石替代石灰的关键技术与优化措施。
然后,从环境与可持续性的角度,评估石灰石替代石灰对碳排放、渣的回收与再利用等方面的影响。
最后,对石灰石替代石灰的经济效益进行分析,展望其在钢铁市场中的应用前景与潜力。
二、石灰石替代石灰的优势在深入了解了石灰石与石灰的化学成分、物理性质和反应机理的差异之后。
石灰石代替石灰工艺

石灰石代替石灰工艺采用石灰石代替石灰不仅能够消除现在存在的环境问题,而且能够把传统中要排放的CO2改质成CO,增加二次能源转炉煤气的回收量,因而将产生巨大的环境和经济效益。
一、目前工艺存在问题:1、原工艺存在能源问题:1)石灰出炉温度一般在1000℃以上,必须降温才能向转炉料仓运输,而在转炉内又要升温到炼钢温度1600℃左右,这温度的一降一升显然浪费热能;2)石灰煅烧出炉后会很快吸收空气中的H2O和CO2,生成Ca(OH)2和CaCO3,入转炉后需要二次煅烧分解排出H2O和CO2,这个过程也要浪费能量;3)炼钢是氧化过程,却要把石灰石所具有的氧化性(CO2)消除后再加入转炉,也是一种能源浪费。
2、生产过程存在的问题。
1) 炼钢厂需设石灰煅烧工序,煅烧石灰时排放大量的粉尘和CO2,需设环保装置减排粉尘,长期消耗水和电;2) 煅烧石灰很难控制石灰石的分解过程,不易得到炼钢所需要的高活性石灰,且石灰大量吸收燃料中的硫而遭到污染;3) 石灰结构疏松,转运过程因摩擦碰撞产生大量粉末要筛分掉,原料利用率低:4) 称量后的石灰还有粉末,在投入转炉的瞬间,粉末会被炉气带走,加重转炉除尘系统负荷;5) 石灰比石灰石价格高,因此炼钢成本增高,随着能源价格、人工费用的上涨和碳税、能源税的征收,石灰和石灰石的价差还会增大,这部分成本还要增加;6) 石灰对转炉的冷却能力不够,因此需加的废钢、铁块进行冷却以求热平衡,废钢、铁块的市场价格都比铁水高,增加炼钢成本;7) 若采用矿石增加冷却强度,则必须增加石灰加入量和渣量,增加耗能和成本。
二、用石灰石代替石灰造渣炼钢的好处。
(1) 石灰石进货、上料管理简单;(2) 石灰石加入转炉后分解出的C02具有氧化性,可强化前期炉内供氧;(3) 石灰石分解会使渣、铁界面上维持较长时间的低温,有利于吹炼初期铁水脱磷:(4) 石灰生成的瞬间具有最大的活性,是炼钢最理想的活性石灰原料,这时石灰与炉渣接触,化渣速度肯定加快;(5) 石灰石比重大,块度更小些也不必担心会被转炉炉气带出,入炉后急剧受热还会开裂增大表面积,加快烧成与化渣;(6) 如果铁水成分合适,能实现全铁水操作,可以减少炉前装废钢铁料等候时间3分钟左右,提高作业率;(7) 减少废钢使用可以减少钢中混入有害元素的含量,有利于优质钢冶炼;(8) 对于原来需要自铸铁块供给转炉冷铁料的企业,可以不用再铸铁块,减少相关浪费;(9) 石灰石中碳酸钙能够被完全利用,分解后CaO参与造渣,C02参与炉内氧化反应,生成的CO可供回收;(10) 有利于实现清洁生产。
石灰石及生石灰对烧结的影响

19
实验样 4
80.8
7.82
20.8
53.9 8.6
84.5 83.50 16.50 61.0
2.03
89
实验样 5
80.3
8.00
20.7
54.0 8.9
83.3 84.00 16.00 61.3
2.02
01
实验样 6
79.9
7.95
21.4
54.0 8.7
82.4 84.10 15.90 61.8
1
实验样 2
81.4
7.80
21.4
54.0 8.8
83.0 82.00 18.00 59.0
2.03
27
实验样 3
81.5
7.75
21.3
54.0
82.8 81.80 18.20 58.8
8.9 2.01
0
平均 81.4
7.82
21.2
54.0 8.8
82.7 81.70 18.30 58.3
2.02
2.03
18
平均 80.3
7.92
21.0
54.0 8.7
83.4 83.87 16.13 61.4
2.03
09
实验样 7
77.6
7.85
22.8
54.0 8.8
83.3 82.60 17.40 58.6
2.02
06
4 数据及分析 4.1 通过实验数据结果看,可分为三个部分 4.1.1 生石灰配比>5.5%:烧结过程从烧结时间变化不大,混合料粒度大于3mm 部分增加,烧结矿强度下降0.4%,返矿率增加2.2%。 4.1.2 生石灰配比4.5%~5.5%:此阶段混合料粒度>3mm 部分下降近1%,但 烧结过程中烧结时间反而缩短,强度增加,返矿率下降。 4.1.3 生石灰配比<4.5%:混合料粒度大于3mm 部分明显下降,烧结时间延长, 转鼓降低。 4.1.4 整个实验过程燃料消耗没有变化,亚铁变化不大。 4.2 原因分析 4.2.1 生石灰主要成分是 CaO,其遇水即消化成消石灰 Ca(OH)2后,在烧结料 中起粘结剂的作用,增加了混合料的成球性,并提高了混合料成球后的强度,改 善了烧结料的粒度组成,提高了料层的透气性;其次,由于消石灰粒度极细,比 表面积比消化前增大100倍左右,因此与混合料中其他成分能更好的接触,更快 发生固液相反应,不仅加速烧结过程,防止游离 CaO 存在,而且它还可以均匀 分布在烧结料中,有利于烧结过程化学反应的进行。粒度细微的 Ca(OH)2颗粒 比粒度较粗石灰石颗粒更易生成低熔点化合物,液相流动好,凝结成块,从而降 低燃料用量和燃烧带阻力。生石灰消化:CaO+H2O= Ca(OH)2,同时白灰消化 时放出的热量,可提高混合料料温;但,烧结料会过分疏松,混合料堆密度下降, 不利于烧结过程反应使烧结矿强度降低,返矿率增加;生石灰用量过多生球强度 反而会变坏,在烧结布料和烧结过程中极易破碎,使烧结的透气性变差,产量下
转炉石灰石替代部分石灰冶炼实践研究

第43卷第2期2021年4月甘㊀肃㊀冶㊀金GANSU㊀METALLURGYVol.43No.2Apr.ꎬ2021文章编号:1672 ̄4461(2021)02 ̄0033 ̄03转炉石灰石替代部分石灰冶炼实践研究季德静1ꎬ邢㊀禹2(1.吉林电子信息职业技术学院ꎬ吉林㊀吉林㊀132021ꎻ2.吉林建龙钢铁股份有限公司ꎬ吉林㊀吉林㊀132021)摘㊀要:首先从理论角度切入ꎬ对石灰石替代部分石灰可能性进行分析ꎬ得出可以用石灰石替代部分石灰进行造渣ꎬ然后介绍某厂转炉炼钢用石灰石替代部分石灰造渣现场应用情况ꎬ并对生产试验的数据㊁石灰石在渣中的分解熔化情况及其对生产操作的影响进行深入分析ꎬ最终得出石灰石替代部分石灰进行造渣的结论:可满足脱磷的要求ꎻ可降低氧气消耗量ꎻ可提高吨钢煤气回收量增加ꎻ可缩短冶炼周期ꎮ关键词:炉渣ꎻ石灰石ꎻ分解中图分类号:TF713.3㊀㊀㊀㊀㊀文献标识码:ASteel ̄MakingOperationsbySubstitutingLimestoneforSomeLimesinConverterJIDe ̄jing1ꎬXINGYu2(1.JilinInstituteofElectronicInformationTechnologyꎬJilin132021ꎬChinaꎻ2.JilinJianlongIronandSteelCoꎬLtd.ꎬJilin132021ꎬChina)Abstract:Inthispaperꎬthepossibilityoflimestonereplacingpartoflimeisanalyzedfromthetheoreticalpointofview.Itisconcludedthatlimestonecanbeusedtoreplacepartoflimeinslagmaking.Thenꎬthefieldapplicationoflimestoneinconvertersteelmakingisintroducedꎬandthedataofproductiontestꎬthedecompositionandmeltingoflimestoneinslaganditsinfluenceonproductionoperationareintroducedthroughin ̄depthanalysisꎬitisconcludedthatlimestonecanreplacepartoflimeforslagmaking:itcanmeettherequirementsofdephosphorizationꎻitcanreduceoxygenconsumptionꎻthere ̄coveryofpertonofsteelgasisincreasedꎻthesmeltingcycleisshortened.KeyWords:slagꎻlimestoneꎻdecomposition1㊀引言石灰是转炉炼钢常用的主造渣料ꎬ石灰是用煤或煤气煅烧石灰石生产的ꎮ炼钢最早使用石灰作为造渣原料主要是解决平炉炼钢终点热量不足问题ꎬ当使用高纯度的顶吹氧气炼钢后ꎬ冶金过程的热效率越来越高ꎬ以及炼钢各环节的热损失越来越少ꎬ转炉终点的温度逐步富余ꎬ使得越来越多的生料及冷料投入到转炉生产环节中ꎬ如:矿石㊁白云石㊁废钢等ꎮ石灰作为转炉炼钢主造渣料是否可以用石灰石替代进行造渣是有研究意义的ꎮ石灰石是生产石灰的原材料ꎬ转炉炼钢用石灰石替代石灰进行造渣最主要的问题在于是否可以满足转炉的脱磷需求[1-2]转炉炼钢使用石灰石时的热量平衡情况及石灰石在炉内进行的分解反应对炼钢生产过程是否有利?2㊀理论分析每公斤石灰和石灰石由20ħ加热到1600ħꎬ若以每公斤CaO为基数相比较(按石灰石生成56%的石灰计算)ꎬ每公斤石灰和石灰石消耗的热能相差849kcal/kg[3]ꎮ石灰石在分解炉中的分解率可以达到95%~98%ꎬ热耗为3260~3550kJ/kgꎬ反应式为:CaCO3=CaO+CO2转炉冶炼需要废钢平衡转炉冶炼过程中的富裕热量ꎬ假设废钢在铁水中于1400ħ熔化ꎬ废钢升温和熔化的吸热值与CaCO3的升温分解吸热值相比ꎬ1kg废钢仅相当于0.385kg[3]石灰石的吸热水平ꎬ石灰石在转炉内分解成石灰ꎬCaCO3升温分解成1kgCaO的吸热量ꎬ约是原来转炉冶炼使用1kg石灰升温所吸热量的4.46倍[3]ꎮ转炉内无论前期温度还是过程温度都远远大于煅烧窑内温度ꎬ所以ꎬ转炉内具备石灰石完全转变成石灰的热力学条件ꎬ且在供氧过程中炉内随着氧气的强搅拌与碳氧反应的进行及石灰石受热时产生的CO2作用ꎬ这给石灰石转变成石灰创造了良好的动力学条件ꎬ而且刚形成的CaO气孔率较高ꎬ会快速的和钢中的SiO2㊁MnO㊁FeO㊁MgO等形成复杂化合物ꎬ快速熔化形成炉渣ꎮ同时由于在转炉内煅烧石灰石过程不使用煤气或煤煅烧ꎬ有效降低了炼钢过程的硫负荷ꎬ减少一个生产工序ꎮ石灰石在炉内消耗的热量ꎬ实际上节约了在煅烧窑消耗的热量ꎬ节约了燃料ꎬ且没有炉窑热量损失ꎬ没有运输损失ꎬ总体上来说在转炉内使用石灰石造渣ꎬ会大大降低能源消耗ꎮ同时石灰在运输及存放过程中会存在粉化㊁碎裂现象ꎬ而石灰石则不会出现此类现象ꎬ使用石灰石炼钢时减少了运输储存成本ꎬ减轻了环境污染[4]ꎮ3㊀现场应用3.1㊀试验石灰石和石灰理化指标对比表1㊀石灰石㊁石灰粒度㊁化学成分名称CaO/%S/%SiO2/%粒度/mm活性灰900.0425~50石灰石530.0050.85~40由于石灰石是烧制石灰的原料ꎬ石灰石中有44%原子量的CO2ꎬ所以石灰石中的CaO与SiO2与石灰的比例并无差异ꎬ但石灰中的硫比石灰石中的硫大大增加了ꎬ是由于在煅烧过程中煤或煤气中的硫进入石灰中所致(表1)ꎮ3.2㊀造渣方案以150t转炉为例ꎬ铁水装入量135tꎬ废钢装入量30tꎬ铁水硅含量为0.3%时加入石灰5tꎬ转炉终点碱度3.2左右ꎬ转炉在加入3t石灰时ꎬ需加入3.6t石灰石平衡碱度ꎮ石灰石替代部分石灰造渣在留渣炉次上使用ꎬ石灰石在上一炉次溅渣结束后加入转炉内ꎬ加入量为1600kgꎬ为了平衡转炉热量平衡ꎬ每加入1000kg石灰石废钢量比正常未使用石灰石炉次减少1.5tꎮ石灰石加入转炉内后ꎬ前后来回摇炉ꎬ然后加废钢兑铁ꎮ前后摇炉使石灰石和转炉内终渣均匀铺在炉底ꎬ其目的有两个:一是是降低转炉内终渣温度和流动性ꎬ防止兑铁时发生喷溅ꎻ二是保证尽可能多的石灰石在转炉内加热分解ꎮ点火后加入剩余的石灰石与石灰等其他造渣料ꎮ尽量避免在转炉中期加入超过500kg以上的石灰石ꎬ会造成烟气突然暴增ꎬ造成火焰外溢ꎮ4㊀冶金效果分析试验收集了40炉生产数据ꎬ加入石灰石炉次兑铁时ꎬ从炉口冒出的火与没有加入石灰石炉次相比ꎬ个别炉次炉火稍微有点偏大ꎬ大多数炉次正常ꎬ不会出现兑铁喷溅的现象ꎬ转炉冶炼过程操作前期化渣较快ꎬ但没有出现冶炼过程喷溅现象ꎮ数据如下表2ꎮ表2㊀加入石灰石和没有加石灰石炉次数据对比项目类别铁水Si/%双渣前加入石灰石/kg双渣碱度转炉终点温度/ħ终点脱磷率/%终渣碱度加石灰石炉次0.3216001.51161390.183.5未加炉次0.3401.93163689.93.31㊀㊀从表2数据得知ꎬ用石灰石替代石灰的炉次终点碱度没有发生较大波动ꎬ脱磷率保持正常水平ꎮ加入石灰石的炉次即使废钢量比正常炉次减少3tꎬ但双渣温度和终点温度仍然要比正常炉次分别低8ħ和低13ħꎬ说明石灰石的冷却效果较强ꎬ在冶炼过程中的吸热较大ꎬ因此当转炉终点温度不满足全石灰石冶炼时ꎬ可根据转炉的温度平衡采用部分石灰石替代石灰进行造渣ꎮ为了解石灰石在冶炼过程中熔解的进程ꎬ在部分炉次采取双渣操作ꎬ在转炉双渣时(吹炼4~5min)对炉渣进行取样观察ꎬ发现有部分石灰石没有完全分解熔入炉渣中ꎬ并对未熔解的石灰石进行刨开观察ꎮ在渣中的石灰石由于受热原因已经转变为石灰ꎬ说明石灰石在炉内的煅烧进程要远远大于在窑内煅烧的速度(图1㊁图2)ꎮ当钢水冶炼至终点时对终点进行取渣样ꎬ使用石灰石替代石灰的渣样形貌与使用石灰冶炼的渣样形貌并无太大差异ꎬ从实验室化验结果来看碱度达标ꎬ说明在冶炼终点时石灰石已经完全熔解成渣ꎬ而且使用石灰石造渣的炉次脱磷率与石灰造渣的脱磷率并无差异ꎮ㊀㊀石灰石在渣中的熔解过程是石灰石直接与炉渣43㊀㊀㊀㊀㊀㊀㊀㊀㊀甘㊀肃㊀冶㊀金㊀㊀㊀㊀㊀㊀㊀㊀㊀㊀㊀㊀㊀㊀㊀㊀第43卷图1㊀双渣取出渣样中没有熔化的石灰石图2㊀没有完全熔化的石灰石剖开图片接触ꎬ可以认为在其表面层中分解反应产生的CO2逸出的同时ꎬ就发生了石灰的化渣反应ꎬ增加了界面的扩散速度ꎬ减弱了硅酸二钙保护层的屏障作用ꎬ因此参与反应的石灰都具有较高气孔率和活性ꎮ石灰一层层地生成ꎬ一层层地反应溶入炉渣ꎬ煅烧反应层的移动方向与化渣反应层的移动方向一致ꎮ石灰石上新生成的石灰表面层可以快速地消失ꎬ让内部石灰石的表面裸露出来ꎬ也可以使向石灰石内部的传热加快ꎮ因此从动力学角度看ꎬ石灰石在转炉内的煅烧造渣过程ꎬ实际上是煅烧化渣同时进行的过程ꎮ这个过程对转炉的冶炼过程脱磷过程与正常使用石灰造渣并无差异ꎮ同时对比使用石灰造渣与石灰石替代石灰的炉次发现ꎬ使用石灰石替代石灰造渣的炉次冶炼时间缩短1min左右ꎬ同时使用石灰石替代石灰造渣时转炉烟气的煤气浓度上升较快ꎬ到达30%CO浓度的煤气回收标准的速度要比石灰造渣早40s左右ꎬ使得总体的煤气回收量得以增加ꎮ这是由于石灰石受热分解的CO2也参与了炉内的反应ꎬ即增加了煤气回收量也降低了氧气消耗量[5]ꎮ反应式为:CO2+C=2CO5㊀结语⑴讨论结果表明ꎬ转炉炼钢加入石灰石做造渣原料时在双渣时没有完全成渣ꎬ但已经完全转化成石灰ꎬ说明石灰石在转炉生产过程中是先分解再成渣的过程ꎬ但在后期的吹炼中可以完全熔化到渣中ꎬ这对转炉的整体脱磷率没有较大影响ꎮ⑵使用石灰石造渣时ꎬ避免在碳氧反应剧烈期大量加入ꎬ否则会瞬间产生较大烟气量ꎬ造成火焰外溢ꎮ⑶使用石灰石造渣时ꎬ由于石灰石的分解吸收大量热量ꎬ所以应注意现场的实际造渣料构成ꎬ根据转炉的热量平衡㊁碱度要求情况来选择石灰石替代石灰造渣的比例ꎮ⑷从终点碱度及多炉次脱磷率统计对比ꎬ石灰石替代部分石灰造渣可以完成转炉正常脱磷的要求ꎮ⑸使用石灰石替代部分石灰造渣时ꎬ煤气回收量有所增加ꎬ氧气消耗量有所降低ꎬ对缩短冶炼周期以及提高吨钢煤气回收量有一定好处ꎮ参考文献:[1]㊀王鹏飞ꎬ张怀军.石灰石替代石灰炼钢造渣效果研究[J].包钢科技ꎬ2012ꎬ38(04):30 ̄32.[2]㊀石㊀磊ꎬ钱高伟ꎬ朱志鹏ꎬ等.转炉采用石灰石替代部分石灰的工业试验[J].武钢技术ꎬ2013ꎬ51(04):23 ̄25.[3]㊀王新华.钢铁冶炼一炼钢学[M].北京:高等教育版社ꎬ2007.[4]㊀刘㊀宇ꎬ王文科ꎬ王㊀鹏ꎬ等.转炉采用石灰石部分替代石灰的冶炼实践[J].鞍钢技术ꎬ2011(05):41 ̄44.[5]㊀李㊀宏ꎬ曲㊀英.氧气转炉炼钢用石灰石替代石灰节能减排初探[J].中国冶金ꎬ2010ꎬ20(09):45 ̄48.收稿日期:2020 ̄09 ̄27作者简介:季德静(1983 ̄)ꎬ女ꎬ吉林省吉林市人ꎬ副教授ꎬ本科ꎮ从事冶金技术专业教学ꎮ(上接第32页)[2]㊀项中庸ꎬ王筱留.炼铁工艺设计理论与实践[M].北京:冶金工业出版社ꎬ2009:53 ̄54.[3]㊀周传典.高炉炼铁生产技术手册[M].北京:冶金工业出版社ꎬ2012:1//5.收稿日期:2020 ̄08 ̄31作者简介:史建雄(1986 ̄)ꎬ男ꎬ汉族ꎬ甘肃省定西市陇西县人ꎬ工程师ꎬ本科ꎮ现从事高炉原燃料管理工作ꎮ53第2期㊀㊀㊀㊀㊀㊀㊀㊀㊀㊀季德静ꎬ等:转炉石灰石替代部分石灰冶炼实践研究㊀㊀㊀㊀。
第二原料车间配加石灰石粉降低配矿成本的实践

第二原料车间配加石灰石粉降低配矿成本的实践摘要:从优化烧结熔剂结构入手,通过料场配加石灰石粉替代部分白灰粉的工业生产情况,分析了配加石灰石粉对烧结经济指标的影响。
实践证明,烧结生产过程中合理的石粉配比,对烧结产质量及能耗指标无负面影响,而且可适当提高烧结矿质量,有效降低熔剂成本。
关键词:石灰石粉;配矿成本The second raw material workshop of Handan Iron and Steel Group Handan Branch Logistics CompanyFan Bingtao(Hebei Iron and Steel Group Handan Iron and Steel Branch StorageCenter Handan,Hebei 056015)Abstract:starting from the optimization of sintering flux structure,the influence of limestone powder on sintering economic index is analyzed through the industrial production of replacing part of lime powder with limestone powder in stock yard. The practice shows that the reasonable proportion of stone powder in the sintering process has no negative effect on the sintering production quality and energy consumption index,and can properly improve the quality of sinter and effectively reduce the cost of flux.Key words:limestone powder ore blending cost1前言2008年建成投产的河钢邯钢西区,作为产线布局优良、设备先进可靠、自动化水平高、管理一流,在国内同类型钢铁企业中极具竞争力的两座3200m3高炉,具备年产铁水550万吨以上的水平。
石灰石替代部分生石灰的烧结生产实践

和 干燥带 石灰 石 即可完 全 分 解 释 放 C O , 起 疏 松 料
层作 用 , 对改 善烧 结料 层 热 态 透 气性 也 具 有 较 好 的
效果 。
因此 , 使 用石 灰石部 分替 代生 石灰 , 就解 决现 有 条件 下 全生石 灰熔 剂 结 构 的 弊端 , 具 备 理 论 上 的可
1 ) 配加 3 %及 5 % 石 灰 石 粉 与全 生 石 灰操 作 相 比, 烧 结利用 系 数接 近 , 原 因在 于虽然 添加 了石灰 石 粉 后混 合料 成球 率降低 , 混 合料透 气性 有所 下降 , 但 烧 结蓄 热作用 增 强 , 同时全 生 石 灰 下 混合 料 容 积 密
50
莱钢 科技
2 0 1 6年 1 2月
验 阶段采 用焦 粉 , 试验 分三 个 阶段 , 每个 阶段 为一个
混匀料堆使用周期。使用原料其化学成分见表 1 , 试 验 方案 及试 验结 果见 表 2~ 4 。
表 1 原 料 化 学成 分 .
3 试 验 结 果 及 使 用 效 果 分 析
不 定期 停 机处理 , 而 且 未 完 全 消化 的 生 石 灰在 f f I 混
增 加低 熔点 液相 生成 得 以实 现 , 但 其所 适用 的原 料 条件 主要是 过去 精粉 比例 较高及 高铁 低硅 的原 料条 件下 , 自2 0 1 0年 以来 , 随着 钢铁市 场竞 争 日趋加 剧 , 进 口低 品质 矿粉 的大 比例 使 用 , 使 得 原 料 结 构从 粒 度组成 到化 学成 分 都 有 了较 大 变 化 , 在 此 条 件下 全
作者简介 : 谢 旭( 1 9 7 7一) , 男, I 9 9 8年 7月毕 业 于 上 海 冶 金 高 等 专
细磨石灰石粉替代部分生石灰粉进行烧结生产总结

细磨石灰石粉替代部分生石灰粉进行烧结生产总结一、方案:1、使用方案二铁2月初接到石灰石细磨粉试用通知后,确立两个配加方案。
方案一:对一配14号料仓进行改造(原除尘灰料仓),对料仓顶部进行密封,上小布袋,采用单点除尘,下部使用星阀给料,进行设备安装改造。
方案二:二配有两个白灰仓,分出一仓供细磨石灰石使用,另外一仓单下白灰面(配比4%左右完全能够满足要求)。
缺点就是白灰下料仓出现问题后,烧结就面临全下石灰石的情况,对烧结矿质影响较大。
最后确立一配配加的方案,2月23日改造完成,投入使用。
2、溶剂成分:原料名称SiO2% CaO% MgO% H2O% 单价(元)生石灰 4.57 76.31 6.02 309.98细磨灰石粉 3.21 49.38 3.42 0.26 145.3白云石粉 1.98 30.25 20.65 0.85 60.15 3、细磨石灰石粉粒度组成:>60目>100目>120目>160目>200目<200目28.25% 50.66% 15.74% 2.18% 0.24% 2.94%二、使用情况1、2014年2月18日20时开始配加1.5%的细磨石灰石粉,同时将生石灰配比下调1%。
2月23日将细磨石灰石粉配加1.8%,2月27日上调烧结矿R2,将细磨石灰石粉配加3%。
2、烧结生产参数对比项目使用细磨石粉前配加3% 料层厚度mm 750 750抽风负压kpa 16.0-16.3 16.2-16.5自循环返矿配比% 18 15利用系数t/m2〃h 1.64 1.61 废气温度℃140-145 140-145 垂烧速度mm/min 28.6 27.0混合料水分% 7.6 7.4烧结矿产量t 8490.8 8474.413、烧结矿化学成分对比名称Fe FeO SiO2 CaO MgO R2 实验前53.49 8.91 5.88 11.14 3.10 1.90 配比3% 53.17 8.83 6.17 12.07 2.97 1.96 4、烧结矿粒度组成情况对比名称-5mm 5-10mm 10-25mm 25-40mm >40mm实验前 4.23 24.87 43.03 19.37 8.50配比3% 4.00 21.33 45.07 22.47 7.13 5、烧结矿冶金性能对比名称还原强度RDI+6.3 还原粉化指数RDI+3.15磨损指数RDI-0.5还原度RI(%)还原速率RVI(%min-1)实验前42.20 73.80 4.90 81.60 0.60 配比3% 42.10 73.00 5.20 81.60 0.54三、使用情况对比分析1、配加细磨石灰石粉前后混合料料温无明显变化,经实测料温维持在40-45℃左右。
烧结消石灰替代生石灰和提高生石灰质量试验与实践

烧结消石灰替代生石灰和提高生石灰质量试验与实践谢学荣【摘要】在2台烧结机供应4座高炉(简称“2对4”)的供料模式下,宝钢股份公司烧结开展了消石灰替代生石灰、提高生石灰质量的试验与实践.烧结杯试验结果表明,消石灰替代生石灰较为适宜的比例为60%左右;生产实践消石灰替代比例为0.62%时负压较基准期降低0.52 kPa.生石灰提高质量试验结果表明,提高生石灰灼减和活性度对利用系数、成品率、强度、固体燃料消耗和工序能耗等指标有不同程度改善,如成品率提高1.07%,强度提高1.04%,工序能耗降低1.01 kg/t.【期刊名称】《宝钢技术》【年(卷),期】2018(000)005【总页数】4页(P20-23)【关键词】烧结;消石灰;生石灰【作者】谢学荣【作者单位】宝山钢铁股份有限公司炼铁厂,上海201900【正文语种】中文【中图分类】TF0441 概述烧结是将各种粉状含铁原料按要求配入一定数量的燃料和熔剂,混匀、制粒后放到烧结设备上点火烧结;在燃料燃烧产生高温和一系列物理化学反应后,混合料中部分易熔物质发生软熔,产生一定数量的液相,液相物质润湿其他未熔化的矿石颗粒;随着温度的降低,液相物质将矿粉颗粒黏结成块[1]。
现代烧结法采用抽风烧结,从工艺角度上来说,通过烧结料层的有效抽风量与烧结利用系数成正比例关系,即“风量就是产量”。
影响有效抽风量的最重要因素是烧结过程透气性,包括冷态透气性和热态透气性,一切能改善透气性的措施均能有效提高烧结利用系数。
烧结用料中,熔剂性质对冷态透气性和热态透气性均有重要影响,如生石灰与水反应后能形成Ca(OH)2胶体,比表面积大幅增加,在制粒过程中可强化颗粒间作用力,在烧结料层中增加持水能力改善过湿;但提高配比到一定程度后会影响CaO源和矿石的正常分布,进而对生成液相及液相性质产生负面影响。
过量未消化的生石灰还会在烧结过程中吸水膨胀,破坏制粒小球。
宝钢原料准备工艺没有使用生石灰消化器,生石灰、石灰石等物料经配料后直接进入强混、二混和三混混匀,制粒参与后续烧结。
烧结总结报告

粉末冶金烧结总结报告41331033 叶星平一.概述烧结是:对粉末或压坯在低于主要组分熔点(约0.7~0.8T绝对温度)温度下保温,使颗粒相互联结(粒界变为晶界),减小或除去颗粒间的缝隙和孔洞,提高烧结体密度和强度。
烧结过程中发生的物理化学变化:水分或有机物的蒸发或挥发,吸附气体的排除,应力的消除,粉末颗粒表面氧化物的还原;原子间发生扩散,粘性流动和塑性流动,晶粒间的接触面积增大,再结晶等;还可能有固相的溶解和重结晶。
很复杂。
二.烧结的驱动力:粉末颗粒比一大块的烧结体的比表面积大得多,粉末表面的原子都倾向于变成内部原子来降低能量(能量越低越稳定)这些由粉末变成烧结体减少的表面能就是烧结能够进行的主要驱动力。
还有由于晶格的缺陷所贮存的能量也是驱动力。
烧结中的物质迁移方式:表面迁移和体积迁移。
表面迁移主要:表面扩散,蒸发-凝聚;体积迁移主要:体积扩散,晶界扩散,塑性流动,粘性流动。
三、烧结三个阶段:粘结阶段,烧结颈长大阶段,闭孔隙球化和缩小阶段。
1、开始阶段(粘结和烧结颈长大阶段)粉末颗粒间的点接触能导致烧结颈的长大,这个过程的物质迁移机构有:粘性流动机构:在应力的作用下,原子或空位顺着应力的方向发生流动。
颗粒中心距离不发生变化,表面物质的迁移填充到接触颈部。
体积扩散机构:由于存在空位浓度面使原子发生流动,粉末颗粒中心距离减小。
蒸发-凝聚机构:在颗粒外表面的曲率半径与接触颈部的曲率半径是不相同的,接触点以外的表面的物质更易蒸发,然后在接触点凝聚,使烧结颈长大。
对烧结后期的孔隙球化起作用。
仅发生在高蒸汽压物质的烧结过程中。
表面扩散机构:表面的原子和表面的空位相互交换位置。
粉末表面在原子尺度上来看是凹凸不平的,即使没有畸变,表面也是阶梯状而不是连续的,所以表面原子很容易发生扩散和移动,低温烧结时占主导的是表面扩散。
晶界扩散机构:颗粒内部及表面的原子通过晶界向烧结颈移动,所以颗粒中心距离会缩小。
靠近晶界的孔隙总是优先被迁移过来的原子填充。
- 1、下载文档前请自行甄别文档内容的完整性,平台不提供额外的编辑、内容补充、找答案等附加服务。
- 2、"仅部分预览"的文档,不可在线预览部分如存在完整性等问题,可反馈申请退款(可完整预览的文档不适用该条件!)。
- 3、如文档侵犯您的权益,请联系客服反馈,我们会尽快为您处理(人工客服工作时间:9:00-18:30)。
细磨石灰石粉替代部分生石灰粉进行烧结生产总结
一、方案:
1、使用方案
二铁2月初接到石灰石细磨粉试用通知后,确立两个配加方案。
方案一:对一配14号料仓进行改造(原除尘灰料仓),对料仓顶部进行密封,上小布袋,采用单点除尘,下部使用星阀给料,进行设备安装改造。
方案二:二配有两个白灰仓,分出一仓供细磨石灰石使用,另外一仓单下白灰面(配比4%左右完全能够满足要求)。
缺点就是白灰下料仓出现问题后,烧结就面临全下石灰石的情况,对烧结矿质影响较大。
最后确立一配配加的方案,2月23日改造完成,投入使用。
2、溶剂成分:
原料名称SiO2% CaO% MgO% H2O% 单价(元)生石灰 4.57 76.31 6.02 309.98
细磨灰石粉 3.21 49.38 3.42 0.26 145.3
白云石粉 1.98 30.25 20.65 0.85 60.15 3、细磨石灰石粉粒度组成:
>60目>100目>120目>160目>200目<200目28.25% 50.66% 15.74% 2.18% 0.24% 2.94%
二、使用情况
1、2014年2月18日20时开始配加1.5%的细磨石灰石粉,同时将生石灰配比下调1%。
2月23日将细磨石灰石粉配加1.8%,2月27日上调烧结矿R2,将细磨石灰石粉配加3%。
2、烧结生产参数对比
项目使用细磨石粉前配加3% 料层厚度mm 750 750
抽风负压kpa 16.0-16.3 16.2-16.5
自循环返矿配比% 18 15
利用系数t/m2〃h 1.64 1.61 废气温度℃140-145 140-145 垂烧速度mm/min 28.6 27.0
混合料水分% 7.6 7.4
烧结矿产量t 8490.8 8474.41
3、烧结矿化学成分对比
名称Fe FeO SiO2 CaO MgO R2 实验前53.49 8.91 5.88 11.14 3.10 1.90 配比3% 53.17 8.83 6.17 12.07 2.97 1.96 4、烧结矿粒度组成情况对比
名称-5mm 5-10mm 10-25mm 25-40mm >40mm
实验前 4.23 24.87 43.03 19.37 8.50
配比3% 4.00 21.33 45.07 22.47 7.13 5、烧结矿冶金性能对比
名称还原强
度
RDI+6.3 还原粉化
指数
RDI+3.15
磨损指数
RDI-0.5
还原度
RI(%)
还原速率
RVI(%min-1)
实验前42.20 73.80 4.90 81.60 0.60 配比3% 42.10 73.00 5.20 81.60 0.54
三、使用情况对比分析
1、配加细磨石灰石粉前后混合料料温无明显变化,经实测料温维持在40-45℃左右。
2、烧结混合料水分变化不大,由于配用细磨石灰石粉后混合料湿容性下降,混合料适应水分下降0.1-0.2%。
3、烧结点火温度未有明显变化,始终控制在1100℃左右,点火料面均匀,无生烧及过熔现象出现。
4、烧结总管负压与使用前基本持平,在烧结风门100%及料层厚度750mm不变的情况下,烧结总管负压维持在16.0-16.5kpa之间。
5、配加细磨石灰石粉后,为保证烧结过程中的物理、化学反应充分,机速略有下降,垂烧速度由28.6mm/min下降至27mm/min,烧结矿产量维持在8480t左右,无明显变化。
6、烧结返矿率明显下降,返矿配比随细磨灰石粉配比升高由18%逐渐下降到16%。
7、烧结矿液相反应充分,烧结矿强度有所提升,烧结成品率提升3%。
8、烧结矿粒度组成愈加均匀,小于10mm粒级部分降低3.77%,大于40mm部分降低1.37%,10-40mm中间粒级部分提高5.14%。
9、烧结固体燃料消耗略有上升,实验阶段细磨石灰石粉配加后影响固体燃料消耗升高0.5kg/t矿。
四、生产过程控制措施
适当降低混合料水分、强化制粒、加强生石灰消化、烧结进行压料、降机速等一系列技术调整,强化烧结料制粒效果、稳定混合料料温、保证足够的烧结反应时间,稳定烧结生产。
烧结矿料温控制在40℃,料层厚度控制750mm,点火温度控制1140℃,机速控制1.25m/min,烧结矿液相反应充分,红层厚度控制在1/3—1/2,烧结矿强度明显
增强,成品率提升,返矿量下降。
五、效益分析
1、引用数据
成本费用及溶剂单价
烧结矿成分
烧结吨矿溶剂单耗
白灰的有效CaO=76.31-4.57×2.0=67.17%
石灰石细磨粉有效CaO=49.38-3.21×2.0=42.96%
R2升高影响生石灰消耗:(1.96-1.88)*5.88%/67.17%*1.15=8.05kg SiO2升高影响生石灰消耗:
(6.17%-5.88%)*1.96/67.17*1.15=9.73kg 合计影响生石灰消耗:8.05+9.73=17.78kg
成本对比:
1.使用细磨石灰石粉前烧结溶剂成本:
(59.38+17.78)*309.98/1000+48.84*49.41/1000=26.33元
使用细磨石灰石粉后烧结溶剂成本:
62.68*309.98/1000+50.88*49.41/1000+24.63*145.3/1000=25.52元结合实际生产配加3%石灰石细磨粉,熔剂成本下降26.33-25.52=0.81元
2.烧结矿成品率升高2%,影响烧结矿成本下降:2%×75=1.5元吨;固体燃料消耗上升0.5Kg/t;
影响成本升高: 0.5×910/1000=0.46元/吨矿;
3.综合成本影响下降:26.33-25.52+1.5-0.46=1.85元/吨矿;
细磨石灰石粉替代生石灰对烧结矿品位无影响,故影响铁水成本下降:1.85×1.36=2.52元/吨。
三、结论
1、烧结在大量使用外矿粉时,配加少量细磨石灰石粉替代部分生石灰,可增加烧结混合料堆密度,使烧结料反应更加充分,烧结矿强度增强,成品率提升,内循环返矿量下降,烧结矿粒度组成更加均匀,有利于烧结矿质改善。
2、配加3%的细磨石灰石粉替代部分生石灰,烧结矿成本下降1.85元/吨,铁水成本下降2.52元/吨。
3、配加少量细磨石灰石粉替代部分生石灰,可拓宽烧结溶剂来源,减少原料供应压力。
4、配加3%的细磨石灰石后烧结矿固体燃料消耗升高0.5Kg/t,烧结矿产量无影响。