飞剪现场调试资料
飞剪操作说明书

安全操作规程1.为了保证启停式飞剪的安全运行,操作人员必须认真仔细阅读规程,非操作人员严禁启动,操作及其调试飞剪。
2.试车前的准备2.1.首先检查剪刃紧固螺钉,剪刃楔块紧固螺钉是否安全,是否安装牢固。
2.2.检查剪臂停车位置是否正确。
2.3.检查剪刃保险块是否已磨损失效。
2.4.检查刀片是否有缺口。
2.5.检查剪臂工作位置是否正确:2.5.1:旋转方向:按飞剪进料方向,旋转剪臂到刃口垂直位置,切不得逆转。
2.6.空转检查:用手搬动剪臂是否灵活(以用力能搬动为准),检查润滑供给是否正常。
3. 启动飞剪前:操作人员应观察并确认机械现场相关区域无人员后,先开警报器,再关信号灯,最后进行试剪工作(K1若已运行,按住模拟过钢按钮,K1若没有运行,按一下单剪)观察飞剪及其相关设备运行动作是否准确无误。
4. 启动运行过程:将控制柜内的断路器全部合上,合闸,急停恢复,将旋钮旋向启动位,自动位。
5. 停机过程:将操作台旋钮拨向停止位,分闸。
如有必要,断开控制柜内的断路器(除Q1,Q3外)。
6. 生产过程中如遇到下列情况:(1)操作台故障报警灯亮(2)遇有飞钢,堵钢,设备故障及其他异常情况需及时处理时,操作人员应及时将相关飞剪停机,按下急停。
待相应的指示灯亮时,处理故障人员方可进入现场。
飞剪工作原理1.剪前热检检测到红钢后产生信号,此信号作为有钢条件,同时开始计算脉冲,并计时。
2.当计时时间达到首钢夹送辊延时设定时间时压下相应的夹送辊。
3.当脉冲数达到倍尺长度设定时(除首根以剪前热检检测信号为准外,其他以剪切动作为准),启动飞剪。
4.剪切动作后,夹送辊抬起延时时间到达时,夹送辊抬起动作。
5.夹送辊抬起后,另一槽夹送辊压下延时时间到时,另一槽的夹送辊压下动作。
触摸屏操作:末架轧机工作辊径(mm):K1的实际工作辊径。
剪切线速设定(m/s):飞剪的剪切线速,一般要比K1的线速度快一点,但也不要太快了,太快了会出现压头,压尾现象,影响过钢。
高速线材生产线飞剪区域电气系统编程与调试
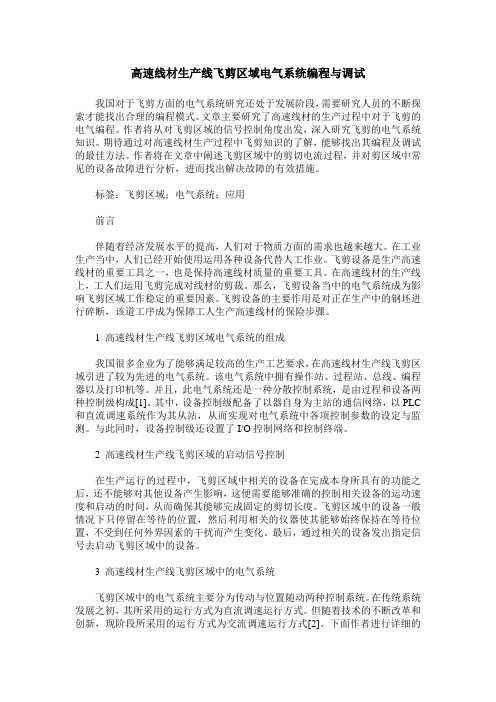
高速线材生产线飞剪区域电气系统编程与调试我国对于飞剪方面的电气系统研究还处于发展阶段,需要研究人员的不断探索才能找出合理的编程模式。
文章主要研究了高速线材的生产过程中对于飞剪的电气编程。
作者将从对飞剪区域的信号控制角度出发,深入研究飞剪的电气系统知识。
期待通过对高速线材生产过程中飞剪知识的了解,能够找出其编程及调试的最佳方法。
作者将在文章中阐述飞剪区域中的剪切电流过程,并对剪区域中常见的设备故障进行分析,进而找出解决故障的有效措施。
标签:飞剪区域;电气系统;应用前言伴随着经济发展水平的提高,人们对于物质方面的需求也越来越大。
在工业生产当中,人们已经开始使用运用各种设备代替人工作业。
飞剪设备是生产高速线材的重要工具之一,也是保持高速线材质量的重要工具。
在高速线材的生产线上,工人们运用飞剪完成对线材的剪裁。
那么,飞剪设备当中的电气系统成为影响飞剪区域工作稳定的重要因素。
飞剪设备的主要作用是对正在生产中的钢坯进行碎断,该道工序成为保障工人生产高速线材的保险步骤。
1 高速线材生产线飞剪区域电气系统的组成我国很多企业为了能够满足较高的生产工艺要求,在高速线材生产线飞剪区域引进了较为先进的电气系统。
该电气系统中拥有操作站、过程站、总线、编程器以及打印机等。
并且,此电气系统还是一种分散控制系统,是由过程和设备两种控制级构成[1]。
其中,设备控制级配备了以器自身为主站的通信网络,以PLC 和直流调速系统作为其从站,从而实现对电气系统中各项控制参数的设定与监测。
与此同时,设备控制级还设置了I/O控制网络和控制终端。
2 高速线材生产线飞剪区域的启动信号控制在生产运行的过程中,飞剪区域中相关的设备在完成本身所具有的功能之后,还不能够对其他设备产生影响,这便需要能够准确的控制相关设备的运动速度和启动的时间,从而确保其能够完成固定的剪切长度。
飞剪区域中的设备一般情况下只停留在等待的位置,然后利用相关的仪器使其能够始终保持在等待位置,不受到任何外界因素的干扰而产生变化。
徐州东亚飞剪说明书

徐州东亚飞剪说明书天津博技机电高科技有限公司天津博技机电高科技有限公司((((((((((((((((((((((((((东亚钢铁有限公司轧钢车间飞剪说明书二零零九年九月天津市博技机电高科技有限公司第1页天津博技机电高科技有限公司天津博技机电高科技有限公司((((((((((((((((((((((((((目录一、飞剪的电气控制及维护二、安全操作规程三、飞剪现行控制方案及相关说明四、飞剪触摸屏相关参数设置说明第2页天津博技机电高科技有限公司天津博技机电高科技有限公司((((((((((((((((((((((((((飞剪的电气控制及维护一:系统概述及控制方案1(概述:本系统主要包括飞剪机械部分(起停式飞剪)、直流电动机和电气控制部分(进线柜、调节柜)。
其工作原理是当PLC采集到剪前热金属检测器有钢信号后,通过高数计数模块进行计数,计算长度达到设定倍尺长度时,飞剪自动启动进行剪切。
倍尺长度可任意设定,剪切速度自动跟踪末架轧机的速度,修改飞剪提速比调节剪切速度。
2(控制方案:如下图所示,该飞剪控制系统主要分三大部分:PLC控制系统,直流驱动系统,电机和飞剪机械部分执行系统。
通过控制柜面板的按钮可以完成对飞剪的控制,并预留飞剪合闸/分闸、运行、飞剪试车、及急停旋钮和飞剪合闸、运行、故障及零位指示灯等信号的接口。
同时通过控制柜上的人机接口(触摸屏)可以对PLC进行剪切方式、剪切长度及剪切速度的设定。
第3页天津博技机电高科技有限公司天津博技机电高科技有限公司((((((((((((((((((((((((((控制方案图系统工作过程如下:当成品棒材经过传感器时,传感器给PLC发出有钢信号,同时PLC启动计数器记录末架轧机码盘上的脉冲数,PLC根据脉冲计算出棒材的长度等于定尺时便给直流驱动系统发出剪切命令,飞剪机械部分做出相应剪切动作,在剪刃对齐时,有接近开关发出信号给PLC系统。
PLC系统即发出制动信号并给出反转速度。
FM350-1调试简单说明(适用于飞剪)
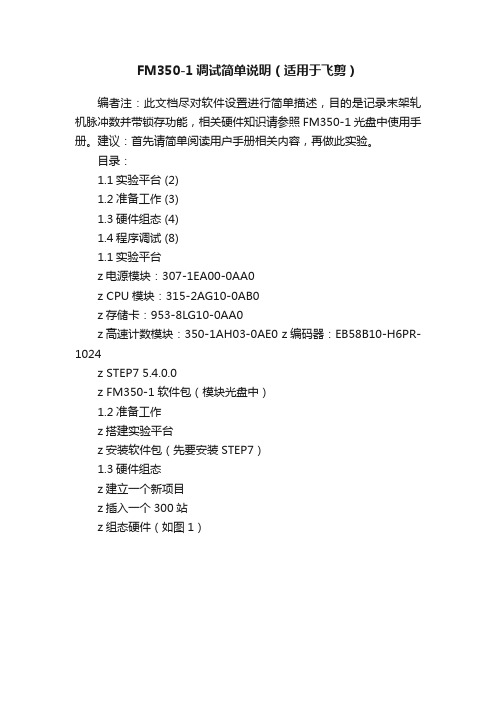
FM350-1调试简单说明(适用于飞剪)编者注:此文档尽对软件设置进行简单描述,目的是记录末架轧机脉冲数并带锁存功能,相关硬件知识请参照FM350-1光盘中使用手册。
建议:首先请简单阅读用户手册相关内容,再做此实验。
目录:1.1实验平台 (2)1.2准备工作 (3)1.3硬件组态 (4)1.4程序调试 (8)1.1实验平台z电源模块:307-1EA00-0AA0z CPU模块:315-2AG10-0AB0z存储卡:953-8LG10-0AA0z高速计数模块:350-1AH03-0AE0 z编码器:EB58B10-H6PR-1024z STEP7 5.4.0.0z FM350-1软件包(模块光盘中)1.2准备工作z搭建实验平台z安装软件包(先要安装STEP7)1.3硬件组态z建立一个新项目z插入一个300站z组态硬件(如图1)图1z双击FM350 COUNTER,出现COUNTER MODULE画面(图2)图2z进入Operating Modes,修改Gate的模式为Latch(图3)图3z进入Encoders,修改Signal Type为24V incremental(图4)图4z进入Input,修改Set Counter(Set DI)为Multiple,同时取消Evaluate zero mark for setting(图5)图5z进入Output,修改DO1为Active on reaching the comparison value for pulse duration(up),把Pulse duration改为500ms(图6)图6z保存设置,编译并下载1.4程序调试z打开Libraries,选择FMx50Lib(图7)图7z复制FC2和UDT1到实验工程中(图8)图8z回到实验项目,插入DB1(图9)图9z编程注意事项必须要赋值的三个参数DB1.DBW6(高数模块地址),DB1.DBD8(高数模块地址首址),DB1.DBB12(高数模块地址长度)(图10)图10必须置位的点,FC2中的SW_GATE(允许计数),DB1.DBX27.0和DB1.DBX27.1(允许硬件I2清零),DB1.DBX28.0和DB1.DBX28.1(允许硬件Q0和Q1输出)FC2说明(主要参数说明)(图11)DB_NO 对应DB块的DB号,本例为1SW_GATE 软件门,为“真”的时候,允许计数L_DIRECT 软件清零L_PIRPER 设置LOAD_V AULT_CMP_V1 设置比较值1(对应DO1)T_CMP_V2 设置比较值2(对应DO2)图11当前值为DB1.DBD30,锁存值为DB1.DBD34(硬件I0出现上升沿,当前值就被锁存到DB1.DBD34中)(图12)图12设置DB1.DBD14(装载值):在给DB1.DBD14赋值的同时,必须给FC2的L_PREPAR为“真”一次设置DB1.DBD18(比较值1)和DB1.DBD22(比较值2):在给DB1.DBD18和DB1.DBD22赋值的同时,必须给FC2的T_CMP_V1和T_CMP_V2为“真”一次。
飞剪设备使用、维护说明书

目录一、技术参数 (1)1. 工艺描述 (1)2. 主要技术参数 (1)二、起吊、运输、安装 (2)三、工作环境 (3)四、润滑 (3)五、运行 (4)1. 运行前检查 (4)2. 启动 (4)3. 运行 (5)六、安全 (11)七、维护保养 (11)八、故障处理 (12)一、技术参数1. 工艺描述小棒飞剪:面对剪刃侧,走钢线为从左至右。
高线飞剪:面对剪刃侧,走钢线为从右至左。
功能:在正常工作时,飞剪用于对轧件进行切头,确保轧件无端部变形、黑头或开裂,有利于轧件进入下游轧机组;在发生事故时对轧件进行碎断以缩短事故处理时间。
形式:小棒粗轧飞剪启停式曲柄飞剪小棒一中轧飞剪启停式曲柄飞剪小棒二中轧飞剪启停式回转剪小棒精轧后飞剪启停式曲柄-回转组合剪小棒碎断剪连续式回转剪高线粗轧飞剪启停式曲柄飞剪高线中轧飞剪启停式回转剪2. 主要技术参数剪切断面(mm)剪切速度(m/s)电机功率(kW)电机转速(r/min)小棒粗轧Φ102~Φ1150.38~1.0425743小棒一中轧Φ53~Φ82 1.1~3.3600745小棒二中轧Φ30~Φ44 3.42~9.0425743小棒精轧后Φ19.6~Φ78 1.35~15.4600745小棒碎断剪Φ19.6~Φ41 5.3~15.4901450高线粗轧Φ72~Φ77.30.45~1.6425743高线中轧Φ32.5~Φ34.6 2.48~8.0425743二、起吊、运输、安装在起吊、运输、安装过程中应遵循如下注意事项:1) 起吊整个机列时,应使用底座上的吊耳。
注意: 钢丝绳钢链条与底座接触部分应垫橡胶皮等物加以保护。
2) 飞剪机列运输、存放时应放在木块上或平滑干燥的基础之上,请勿直接放在水泥地面上。
3) 请勿推、拉飞剪机列,以免损伤接触底面。
4) 飞剪机列到货后如半年之内不安装,要对外露的加工面重涂防锈油,谨防锈蚀。
5) 飞剪机列安放在安装基础上之后,需用水平仪找正,其水平度不得低于0.1/1000。
MCT150B 同步 飞剪控制器 使用说明书

MCT150B同步/飞剪控制器使用说明书■同时集成同步和飞剪控制■方便的参数设置取代复杂的编程工作■简单配置即可开始工作■500KHz计数频率,内部4倍频后可达2MHz■FPGA+高性能处理器架构,快速动态响应(约30us)■位置同步和比例控制■飞剪控制使用S型速度曲线平滑运动■电平、脉冲两种相位修整模式■自带套准功能■虚拟主轴可选■14位高精度D/A输出■编码器采用5V差分信号输入,I/O口全部采用光耦隔离■编码器输出信号源主从轴可选,级联方便■RS232/RS485串口通讯,内嵌MODBUS从机通讯协议■DIN35导轨安装、设置简便,高性价比1.介绍MCT150B是采用FPGA和高性能处理器架构设计的高性能同步和飞剪控制器,用于实现两个独立的电机间的同步控制或飞剪控制,可以配合多种电机使用(直流、变频、伺服等),通过输出-10~+10V的电压进行速度和位置控制。
500KHz(内部4倍频后可到2MHz)的响应频率可以实现高精度和高速的运行,约为30us的响应时间,使用伺服驱动可在动态过程中实现精准的同步和飞剪控制。
完全比例及飞剪控制和其它功能如电平、脉冲两种远程相位修整控制和套准(套色)都作为标准功能集成,使得应用范围更加广泛和方便。
MCT150B既适用于一般情况下的同步控制,还可以适用于飞剪(轮切)系统、局部印刷和旋转轮冲孔或者打标应用的控制。
MCT150B的飞剪功能针对飞剪的特定要求,以最大的精度、最高效率、最小机械冲击为目标而设计。
超短的控制周期和智能的运动曲线在任何条件下都可以提供卓越的性能。
下面所提及裁剪指的是飞剪功能。
所有的设置都是数字式的,不须电位调节;具有RS-232及RS-485通讯功能,采用MODBUS从站通讯协议,非常方便与其它控制器及标准触摸屏联机,进行调试和二次开发。
采用全铝外壳做成,所有的连接端子都在前面板;采用DIN35式工业导轨安装方式,安装调试方便。
MCT150B使用24V直流供电(实际支持18V~30VDC)。
飞剪调试
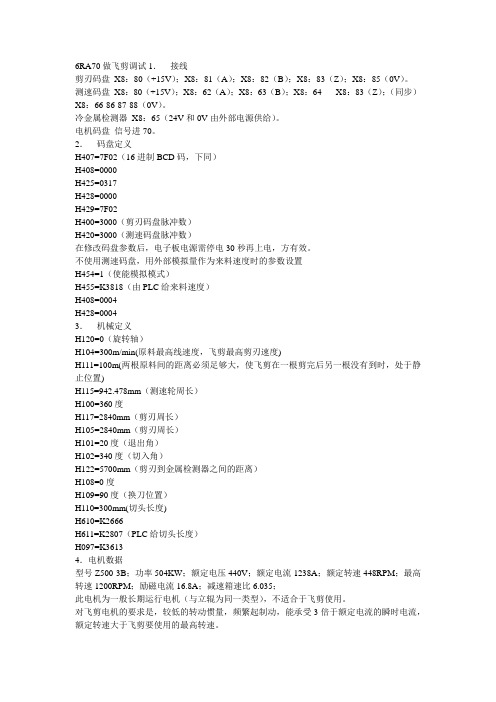
6RA70做飞剪调试1.接线剪刃码盘 X8:80(+15V);X8:81(A);X8:82(B);X8:83(Z);X8:85(0V)。
测速码盘 X8:80(+15V);X8:62(A);X8:63(B);X8:64-----X8:83(Z);(同步)X8:66-86-87-88(0V)。
冷金属检测器 X8:65(24V和0V由外部电源供给)。
电机码盘信号进70。
2.码盘定义H407=7F02(16进制BCD码,下同)H408=0000H425=0317H428=0000H429=7F02H400=3000(剪刃码盘脉冲数)H420=3000(测速码盘脉冲数)在修改码盘参数后,电子板电源需停电30秒再上电,方有效。
不使用测速码盘,用外部模拟量作为来料速度时的参数设置H454=1(使能模拟模式)H455=K3818(由PLC给来料速度)H408=0004H428=00043.机械定义H120=0(旋转轴)H104=300m/min(原料最高线速度,飞剪最高剪刃速度)H111=100m(两根原料间的距离必须足够大,使飞剪在一根剪完后另一根没有到时,处于静止位置)H115=942.478mm(测速轮周长)H100=360度H117=2840mm(剪刃周长)H105=2840mm(剪刃周长)H101=20度(退出角)H102=340度(切入角)H122=5700mm(剪刃到金属检测器之间的距离)H108=0度H109=90度(换刀位置)H110=300mm(切头长度)H610=K2666H611=K2807(PLC给切头长度)H097=K36134.电机数据型号 Z500-3B;功率 504KW;额定电压 440V;额定电流 1238A;额定转速 448RPM;最高转速 1200RPM;励磁电流 16.8A;减速箱速比 6.035;此电机为一般长期运行电机(与立辊为同一类型),不适合于飞剪使用。
对飞剪电机的要求是,较低的转动惯量,频繁起制动,能承受3倍于额定电流的瞬时电流,额定转速大于飞剪要使用的最高转速。
飞剪操作说明(PLC2)
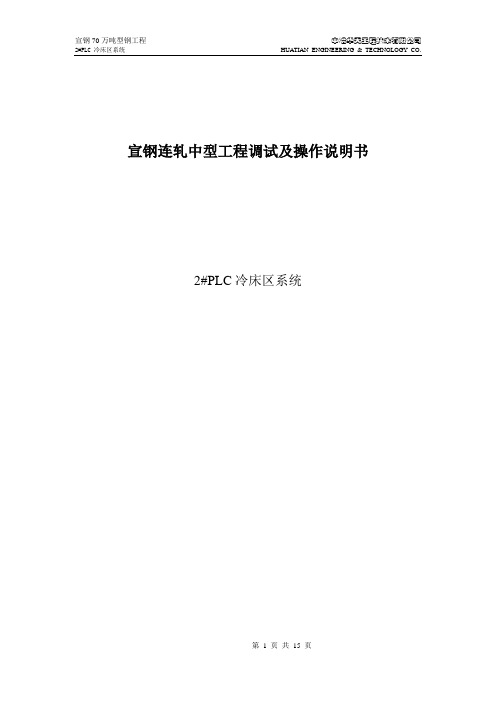
宣钢连轧中型工程调试及操作说明书2#PLC冷床区系统目录附件1 2#PLC的I/O表附件2 2#PLC的OS画面表附件3 2#PLC的报警表冷床输入辊道(M001)控制设备1(9AOC):——操作开关SAE2,冷床输入辊道“前进/后退”控制设备2(4AOS):——操作开关4SAE,冷床输入辊道“前进/后退”控制设备3(4CS):——操作按钮M001,冷床输入辊道“前进/后退”操作说明:正常生产时,冷床输入辊道应置于自动运行方式。
◆手动操作:1.操作箱9AOC上旋钮开关“SAE13”打到“机旁”位,通过操作开关“SAE2”控制冷床输入辊道“前进/后退”。
2.操作箱9AOC上旋钮开关“SAE13”打到“集中”位,操作台4AOS 上旋钮开关“1SAE”打到“手动”位,通过操作开关4SAE,控制冷床输入辊道“前进/后退”。
3.操作箱9AOC上旋钮开关“SAE13”打到“集中”位,操作台4AOS 上旋钮开关“1SAE”打到“自动”位,通过操作按钮M001,控制冷床输入辊道“前进/后退”。
◆自动操作:操作台4AOS上旋钮开关“1SAE”打到“自动”位,当系统收到“全线启动”或“模拟扎制”命令,冷床输入辊道自动按设定的速度运行。
4CS上有此段辊道的速度设定。
在4CS上已设定此段辊道的提速比、摩擦系数输入辊道拨入装置(M002)控制设备1(9AOC):——操作开关SAE1,输入辊道拨入装置“前进/后退”控制设备2(4CS):——操作按钮M002,输入辊道拨入装置“前进/后退”操作说明:正常生产时,输入辊道拨入装置应置于自动运行方式。
◆手动操作:1.操作箱9AOC上旋钮开关“SAE13”打到“机旁”位,通过操作开关“SAE1”控制输入辊道拨入装置“前进/后退”。
操作箱9AOC上旋钮开关“SAE13”打到“集中”位,通过操作按钮M002,控制输入辊道拨入装置“前进/后退”。
◆自动操作:操作台4AOS上旋钮开关“1SAE”打到“自动”位,系统自动控制输入辊道拨入装置运行。
飞剪调试说明
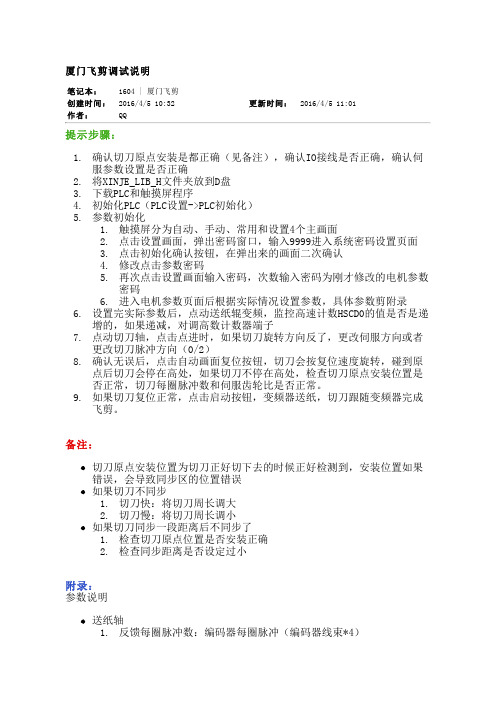
笔记本: 创建时间: 作者: 1604 | 厦门飞剪 2016/4骤: 1. 确认切刀原点安装是都正确(见备注),确认IO接线是否正确,确认伺 服参数设置是否正确 2. 将XINJE_LIB_H文件夹放到D盘 3. 下载PLC和触摸屏程序 4. 初始化PLC(PLC设置->PLC初始化) 5. 参数初始化 1. 触摸屏分为自动、手动、常用和设置4个主画面 2. 点击设置画面,弹出密码窗口,输入9999进入系统密码设置页面 3. 点击初始化确认按钮,在弹出来的画面二次确认 4. 修改点击参数密码 5. 再次点击设置画面输入密码,次数输入密码为刚才修改的电机参数 密码 6. 进入电机参数页面后根据实际情况设置参数,具体参数剪附录 6. 设置完实际参数后,点动送纸辊变频,监控高速计数HSCD0的值是否是递 增的,如果递减,对调高数计数器端子 7. 点动切刀轴,点击点进时,如果切刀旋转方向反了,更改伺服方向或者 更改切刀脉冲方向(0/2) 8. 确认无误后,点击自动画面复位按钮,切刀会按复位速度旋转,碰到原 点后切刀会停在高处,如果切刀不停在高处,检查切刀原点安装位置是 否正常,切刀每圈脉冲数和伺服齿轮比是否正常。 9. 如果切刀复位正常,点击启动按钮,变频器送纸,切刀跟随变频器完成 飞剪。 备注: 切刀原点安装位置为切刀正好切下去的时候正好检测到,安装位置如果 错误,会导致同步区的位置错误 如果切刀不同步 1. 切刀快:将切刀周长调大 2. 切刀慢:将切刀周长调小 如果切刀同步一段距离后不同步了 1. 检查切刀原点位置是否安装正确 2. 检查同步距离是否设定过小 附录: 参数说明 送纸轴 1. 反馈每圈脉冲数:编码器每圈脉冲(编码器线束*4)
2. 反馈齿轮比:送纸压辊转一圈,编码器转多少圈 3. 滚轮周长:压纸辊周长 切刀轴 1. 脉冲方向:0/2切换电机转向 2. 脉冲方向端子:伺服方向接线端子 3. 换向延时时间:伺服换向延时时间 4. 伺服额定转速:电机额定转速 5. 伺服每圈脉冲数:伺服每圈脉冲数 6. 伺服齿轮比:切刀转一圈 7. 复位速度:切刀复位时的速度(单位%,伺服额定转速百分比) 8. 周长:切刀一圈周长 9. 补偿系数:0.2-2(补偿的快慢,一般设为0.5) 10. 切刀个数:切刀的个数 11. 同步距离:同步的长度
如何提高飞剪的剪切精度

如何提高飞剪的剪切精度飞剪是一种常见的剪切设备,广泛应用于纺织、皮革、建筑、汽车等行业。
为了提高飞剪的剪切精度,以下是一些建议:1.优化设备和刀具:确保飞剪设备和刀具的质量,选择具有高精度的剪切刀具,并进行定期维护和保养。
2.调整刀位和切割参数:通过调整刀具的位置和切割参数,如切割速度、刀具压力等,来提高切割的精度。
在切割过程中,应根据材料的特性和要求进行合理的调整。
3.控制材料的张力和平整度:材料张力过大或不均匀会直接影响切割精度,因此需要采取措施来控制材料的张力。
同时,还需确保材料的平整度,避免在切割过程中出现材料浪度或皱纹。
4.使用专业的辅助定位装置:针对不同的切割需求,可以采用专业辅助定位装置,如红外线辅助切割定位装置、激光定位装置等,帮助提高切割的精度和准确性。
5.加强操作人员技能培训:操作人员的技能水平和经验对于飞剪的剪切精度至关重要。
通过加强培训,提高操作人员的技能和操作规范性,从而能够更好地控制切割过程中的各种参数,提高剪切的精度。
6.采用自动化控制系统:现代飞剪设备大多具备自动化控制系统,通过采用先进的传感器技术和控制算法,可以实现对刀具位置、切割速度、压力等参数的精确控制和调整,从而提高剪切的精度。
7.定期检测和质量控制:定期检测机器和刀具的工作状态,以及切割效果。
可以利用专业的测量仪器,如激光测距仪、厚度计等,对切割后的材料进行测量和检验,确保切割精度符合要求。
8.精心设计和优化工艺流程:在飞剪的设计和工艺流程中,应根据具体的切割要求和特性进行精心的设计和优化。
充分考虑材料的特性、切割速度、刀具形状等因素,综合施工制定一套适合的工艺流程。
总之,提高飞剪的剪切精度需要从设备、刀具、材料等多个方面进行综合考虑和优化。
不仅需要关注硬件设备的质量和调整,还需要重视操作人员的技能培训和质量控制措施。
通过以上提出的建议和方法,可以有效提高飞剪的剪切精度,并满足不同行业对切割精度的要求。
飞剪调试注意事项
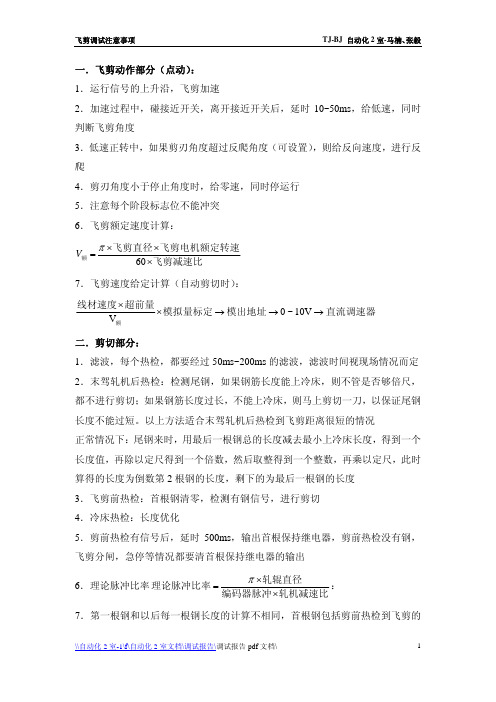
一.飞剪动作部分(点动):1.运行信号的上升沿,飞剪加速2.加速过程中,碰接近开关,离开接近开关后,延时10~50ms ,给低速,同时判断飞剪角度3.低速正转中,如果剪刃角度超过反爬角度(可设置),则给反向速度,进行反爬4.剪刃角度小于停止角度时,给零速,同时停运行5.注意每个阶段标志位不能冲突6.飞剪额定速度计算:60V π××=×额飞剪直径飞剪电机额定转速飞剪减速比7.飞剪速度给定计算(自动剪切时):0~10V V ××→→→额线材速度超前量模拟量标定模出地址直流调速器 二.剪切部分:1.滤波,每个热检,都要经过50ms~200ms 的滤波,滤波时间视现场情况而定2.末驾轧机后热检:检测尾钢,如果钢筋长度能上冷床,则不管是否够倍尺,都不进行剪切;如果钢筋长度过长,不能上冷床,则马上剪切一刀,以保证尾钢长度不能过短。
以上方法适合末驾轧机后热检到飞剪距离很短的情况正常情况下:尾钢来时,用最后一根钢总的长度减去最小上冷床长度,得到一个长度值,再除以定尺得到一个倍数,然后取整得到一个整数,再乘以定尺,此时算得的长度为倒数第2根钢的长度,剩下的为最后一根钢的长度3.飞剪前热检:首根钢清零,检测有钢信号,进行剪切4.冷床热检:长度优化5.剪前热检有信号后,延时500ms ,输出首根保持继电器,剪前热检没有钢,飞剪分闸,急停等情况都要清首根保持继电器的输出6.理论脉冲比率π×=×轧辊直径理论脉冲比率编码器脉冲轧机减速比:7.第一根钢和以后每一根钢长度的计算不相同,首根钢包括剪前热检到飞剪的距离8.首根钢是剪前热检的上升沿给高速计数器清零信号,其他是飞剪接近开关给高速计数器清零信号9.第一根钢长度对应的脉冲数=(剪前热检到飞剪的距离+倍尺长度)/ 实际(理论)比率10.非首根钢长度对应的脉冲数=倍尺长度/ 实际(理论)比率11.计算实际比率:首根钢时,因为是剪前热检给高速计数器清零,所以应用钱前热检到冷床热检的距离除以钢头到达冷床热检时的脉冲数,非首根钢则用剪切位置到冷床热检的距离除以钢头到达冷床热检的脉冲数,此时得到的比率为实际比率。
飞剪控制功能规格书
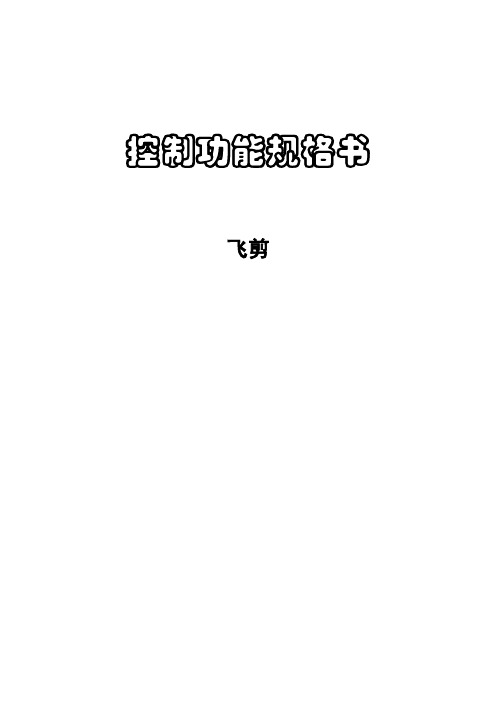
控制功能规格书飞剪一、控制设备飞剪系统控制的设备包括:飞剪前辊道(E2)、飞剪前侧导板(HSG2)、飞剪(CS)、废料收集箱、精轧机除磷箱(DES3)、精轧除磷辊道(E3)。
二、工艺过程描述1.剪前辊道安装在热卷箱与飞剪之间,用于将由热卷箱输送来的中间坯料运输到飞剪之间,中间坯料进入精轧机前,剪前辊道线速度与热卷箱开卷速度保持同步,中间坯料进入精轧机后,剪前辊道线速度与F1速度保持同步。
2.飞剪前侧导板用于对中,运送轧件进入飞剪进行剪切。
3.飞剪安装在热卷箱与精轧机列之间。
用于对运行中的中间坯不规则的头部和尾部进行剪切。
切头时将中间坯切成凸形圆弧形,以减少中间坯咬入精轧机架时的冲击载荷,切尾时将中间坯尾部切成后凸形,以减短常在热连轧机中出现的长长的“燕尾”。
飞剪由两台直流电动机串连驱动。
电动机功率为2×500KW,额定转速为900rpm。
电动机经电机联轴器,主减速机(速比I=21.9),主联轴器与下转鼓相联接,上转鼓与下转鼓之间通过同步齿轮相互传动。
传动侧下同步齿轮设有副齿轮,副齿轮与主齿轮之间用弹簧撑开,用以消除齿轮付之间的传动间隙,而实现无隙啮合,以保证上、下剪刃相互位置的准确和减少齿轮付的冲击。
在主电机和主减速机之间设有制动器,制动器的作用主要是保证在剪刃停止时,保持其位置准确,而每次剪切后的制动主要由电气来完成。
转鼓飞剪主要由上、下剪鼓相向同步运转,而装在剪鼓上的两对剪刃对中间坯实行剪切。
在上、下转鼓上分别安装了切头用剪刃和切尾用剪刃,每个转鼓上的两个剪刃成90度布置,按剪时的转动方向看,切尾剪刃在前,切头剪刃在后。
这种布置方法可以使需要剪切时剪鼓的启动角增大。
剪刃下有承载刀座,剪刃刀座侧面还设有垫板,在剪刃的背面有7个角楔块籍蝶形弹簧组的弹力使剪刃被夹紧在转鼓上。
上、下转鼓啮合运行时,上下剪刃间的间隙完全依赖与安装或装配位置来保证。
在制造时应保证剪刃槽互成90度的相对位置和刃槽与同步齿轮的相对位置的一致性。
UNICO飞剪整理资料

横剪飞剪2400 E40装置技术总结一.触摸屏1、将拨码开关7 拨下来,和5,6一样位置后,触摸屏启动后,直接启动,就没有需要点击“RUN”这个界面了。
2、触摸屏参数:前置PG-----此为刀轴转一圈的周长,固定值,目前为785.39电机PG----此为固定值,跟速比和刀轴运转有关系,目前此值为183.233、飞剪操作台上“锁定指示”为刀轴电机后面销子的限位,即锁死电机的信号4、触摸屏“微调”中的分辨率,是可调的,目前为0.10,最好调到0.05二、硬件1.通道1)进入参数7.Help,找到“3 PIO”,右边黄色的插槽是输入,左边的黑色插槽是输出。
共16位,BIT0---BIT15,蛇形分布如图所示2)输入-----送电后看到BIT5,即通道5亮,通道5代表的意思,可以查,3 PIO----按向下箭头,翻到5 fast stop IN5 即为通道5代表急停,右上方有16位二进制显示的,例如此次为----(省略前8位)--------,X0100XX0 X代表位使用,即没有插东西,可以看到第5位显示为1,说明此时5号插槽灯亮,代表急停有信号。
3)输出------可以看到,当所谓的参考输出有了后,此11BIT11亮的,可以看到3 PIO---翻到11 reference sts ,刚送电时,由于参考输出时没有的,此11灯肯定是灭的,看右上方的二进制位可以看出来是0还是1的。
3)具体通道修改见下。
2、参数组1)参数总表,在7.HELP ,然后按10进入总表,452参数组,代表继电器2,453号组代表继电器3,这2个继电器用于电机启动信号的。
如图,左边是继电器2,右边是继电器3。
2)458号组,fast stop 目前是IN5,也就是通道5,如果通道坏了,可以将通道5上黄色插板插到没用的通道中,例如插到通道2上,此时硬件上除了要将通道5拔出,插到通道2上,参数458也要由目前IN5修改为IN2.同时右边的线也要改对。
高线3号飞剪的安装调试与电机选用
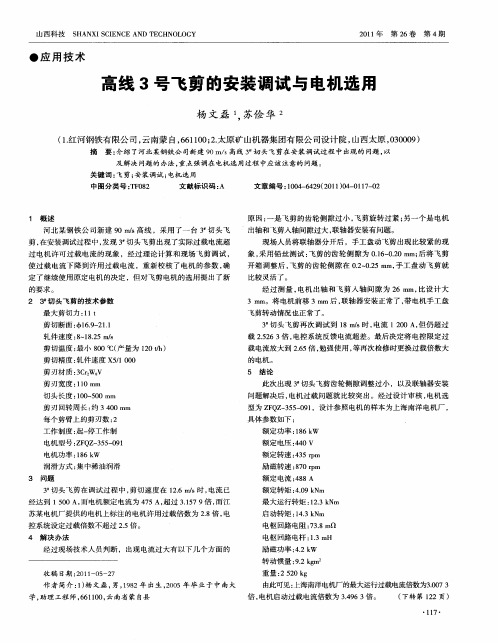
剪切温度 : 最小 8 0℃( 0 产量为 10t ) 2 h / 剪切精度 : 轧件速度 X / 0 0 51 0
剪刃材质 :C2 V 3r W 剪刃宽度 : 1 m 10m
切头长度 :0 — 0 10 5 0mm 剪刃 回转周长 : 34 0mm 约 0 每个剪臂上的剪刃数 : 2 工作制度 : 停工作制 起一
开箱 调整后 , 飞剪 的齿轮侧 隙在 02 02 . . mm, ~ 5 手工 盘动 飞剪 就
比较 灵 活 了 。
定 了继续 使用原定 电机 的决定 ,但对 飞剪电机 的选用 提出 了新
的要求 。 2 3 切 头 飞 剪 的技 术 参 数 * 最 大 剪 切 力 : 1 1 t
河北 某钢铁 公 司新建 9 / 高线 ,采用 了一 台 3 切 头飞 0m s
剪, 在安装调试过程 中 , 发现 3 切头 飞剪 出现了实际过载 电流超 过 电机许可过 载 电流 的现象 ,经过理论计 算和 现场 飞剪 调试 , 使过 载电流下 降到许用 过载 电流 ,重新 校核 了电机 的参 数 , 确
额 定 功 率 :8 W 16k 额 定 电压 :4 4 0V 额 定 转 速 :3 m 4 5r p 励 磁 转 速 :7 m 80r p
电机功率 :8 W 16k 润滑方式 : 集中稀油 润滑
3 问题
额定 电流 :8 4 8A 额定转矩 :.9k m 40 N 最大运行转矩 :23k m 1. N 启动转矩 :43k m 1. N 电枢 回路 电阻 :38m 7 . n 电枢 回路 电杆 :. mH 1 3 励磁功率 :. k 42 W
山西科技
S A X C E C N E HN L G H N I I N E A DT C O O Y S
3_剪参数设置
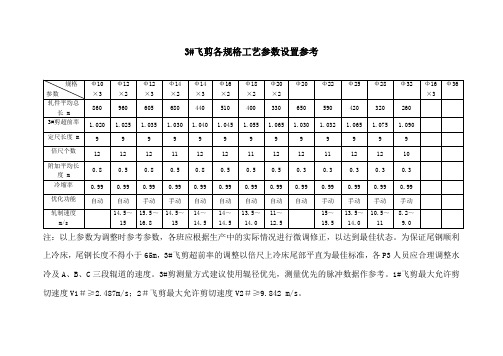
0.99
0.99
0.99
0.99
0.99
0.99
0.99
0.99
0.99
0.99
优化功能
自动
自动
手动
手动
自动
自动
自动
自动
自动
手动
手动
手动
手动
轧制速度
m/s
14.5~15
15.5~16.8
14.5~15
14~14.5
14~14.5
13.5~14.0
11~12.5
15~15.5
13.5~14.0
1.040
1.045
1.055
1.065
1.030
1.032
1.065
1.075
1.090
定尺长度m
9
9
9
9
9
9
9
9
9
9
9
9
9
倍尺个数
12
12
12
11
12
12
11
12
12
11
12
12
10
附加平均长度m
0.8
0.5
0.8
0.5
0.8
0.5
0.5
0.5
0.3
0.3
0.3
0.3
0.3
冷缩率
0.99
0.99
3#飞剪各规格工艺参数设置参考
规格
参数
Ф10
×3
Ф12
×2
Ф12
×3
Ф14
×2
Ф14
×3
Ф16
×2
Ф18
×2
Ф20
飞剪矫直机操作方法
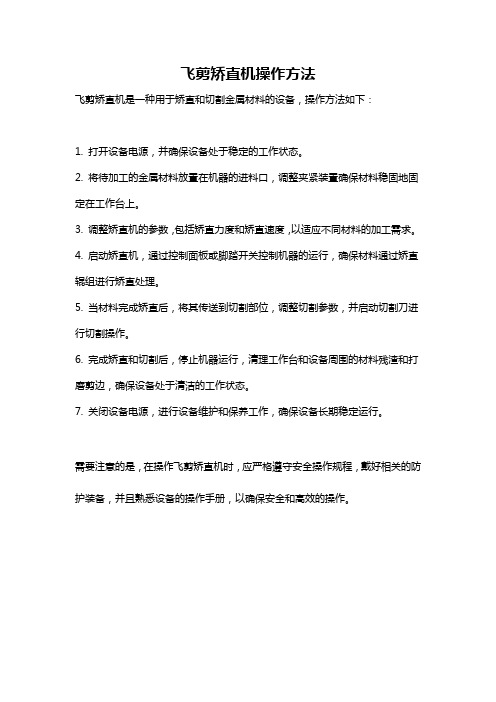
飞剪矫直机操作方法
飞剪矫直机是一种用于矫直和切割金属材料的设备,操作方法如下:
1. 打开设备电源,并确保设备处于稳定的工作状态。
2. 将待加工的金属材料放置在机器的进料口,调整夹紧装置确保材料稳固地固定在工作台上。
3. 调整矫直机的参数,包括矫直力度和矫直速度,以适应不同材料的加工需求。
4. 启动矫直机,通过控制面板或脚踏开关控制机器的运行,确保材料通过矫直辊组进行矫直处理。
5. 当材料完成矫直后,将其传送到切割部位,调整切割参数,并启动切割刀进行切割操作。
6. 完成矫直和切割后,停止机器运行,清理工作台和设备周围的材料残渣和打磨剪边,确保设备处于清洁的工作状态。
7. 关闭设备电源,进行设备维护和保养工作,确保设备长期稳定运行。
需要注意的是,在操作飞剪矫直机时,应严格遵守安全操作规程,戴好相关的防护装备,并且熟悉设备的操作手册,以确保安全和高效的操作。
2#剪调试碎断计划
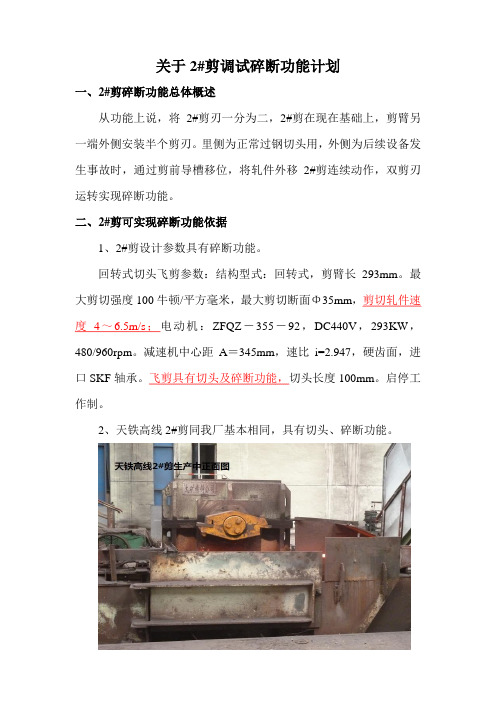
关于2#剪调试碎断功能计划一、2#剪碎断功能总体概述从功能上说,将2#剪刃一分为二,2#剪在现在基础上,剪臂另一端外侧安装半个剪刃。
里侧为正常过钢切头用,外侧为后续设备发生事故时,通过剪前导槽移位,将轧件外移2#剪连续动作,双剪刃运转实现碎断功能。
二、2#剪可实现碎断功能依据1、2#剪设计参数具有碎断功能。
回转式切头飞剪参数:结构型式:回转式,剪臂长293mm。
最大剪切强度100牛顿/平方毫米,最大剪切断面Φ35mm,剪切轧件速度4~6.5m/s;电动机:ZFQZ-355-92,DC440V,293KW,480/960rpm。
减速机中心距A=345mm,速比i=2.947,硬齿面,进口SKF轴承。
飞剪具有切头及碎断功能,切头长度100mm。
启停工作制。
2、天铁高线2#剪同我厂基本相同,具有切头、碎断功能。
3、我厂试生产时,对2#剪碎断功能进行了调试工作,未调成原因,现在分析可能是:剪臂动作一圈为一个启停工作周期,因保证生产正常切头功能,无法安装双剪刃,用单剪刃进行碎断调试,导致碎断轧件过长,引起堆钢和飞溅等因素,但此调试证明2#剪能够碎断。
4、我厂现在2#剪单用于切头功能,经电气郭志刚查看2#剪控制程序和相关参数,经程序改动后2#剪可实现连续运转。
(我厂自动化控制程序有备份,即使调试不成功,恢复时不会有影响)5、参照天铁高线2#剪形式,我厂2#剪在剪刃上可稍作改造,且不需另外购进备件,只将剪刃送机修车削半边即可(现场安装不受影响),可实现双剪刃进行碎断的硬件保证。
6、2#剪前导槽实现移位功能,可参考天铁高线,将剪前导槽按两部分制作,前部为固定式,后部在气缸的推动下,实现位移,气缸动作可和2#剪碎断功能启用实现电气连锁,电气需考虑剪刃动作和气缸动作必须同步进行。
三、试验计划利用4月份检修时间,停机后利用30分钟时间,维修将2#剪臂另一端全剪刃装上,电气将控制程序更改后,启动K11至K16轧机过小料进行碎断试验。
用T400控制飞剪的调试记录
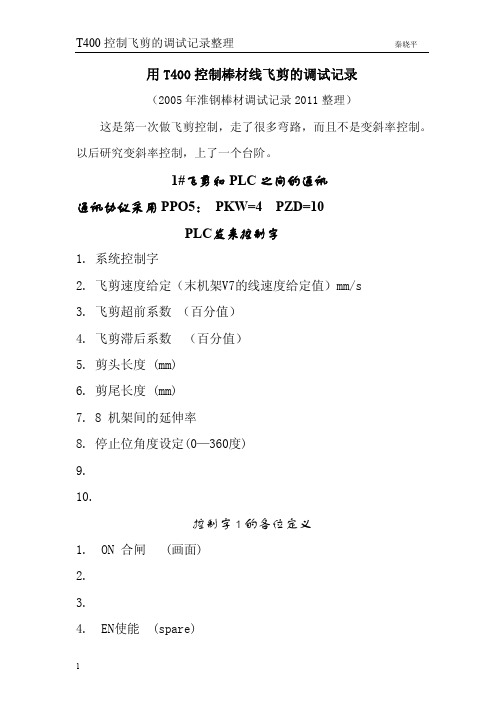
用T400控制棒材线飞剪的调试记录(2005年淮钢棒材调试记录2011整理)这是第一次做飞剪控制,走了很多弯路,而且不是变斜率控制。
以后研究变斜率控制,上了一个台阶。
1#飞剪和PLC之间的通讯通讯协议采用PPO5:PKW=4 PZD=10PLC发来控制字1. 系统控制字2. 飞剪速度给定(末机架V7的线速度给定值)mm/s3. 飞剪超前系数 (百分值)4. 飞剪滞后系数 (百分值)5. 剪头长度 (mm)6. 剪尾长度 (mm)7. 8 机架间的延伸率8. 停止位角度设定(0—360度)9.10.控制字1的各位定义1. ON 合闸 (画面)2.3.4. EN使能 (spare)5.手动剪切 1有效 (按钮) (按一下切一刀)6.剪后轧机有钢信号 (spare)7. 选择剪头(画面)8. 选择剪尾(画面)9. 飞剪故障复位 (画面)10. 剪前轧机有钢信号 (spare)11.12. 飞剪位置复位(手动剪刃定位指令)(按钮)13. 回转/曲柄 1=曲柄 (spare)14. 手动/自动(1=手动)(画面15. 碎断 (按钮)16. 飞剪速度设定选择 1=设定 (spare)传动发给PLC的数据1. 状态字2.速度检测值3.电流反馈值状态字的各位1. 6RA70 合闸准备就绪2. 等待操作 ready to OP.3. 运行 run4. 6RA70 重故障5. 超速6. 剪前热检信号(2m)7. 轻故障8. 飞剪剪切9. 本地=1/远程=010. =1 (通讯)11.剪后热检(SPARE)12. 电流等于零 I=013.速度等于零 N=014.剪后热检 (SPARE)15.飞剪到达停止位信号16.6R70-READYT400 送CUD1的通讯数据W1. TO CUD1 的控制字W2. 速度设定值W3. 上升时间(备用)W4. 下降时间(备用)其中W1各位的分配为:bit 0 I1 合闸bit 3 I4 使能bit 8 I9 剪切位信号(CPS)bit 14 I15 碎断(结束延时1.2秒)CUD1送T400的数据W1.6RA70状态字(重组)W2.电机速度反馈(K167)W3.电机电流实际值(K117)W4. 剪刃位置(K42)状态字的构成1. 6RA70 Ready B02. 6RA70 ready to Op. B13. run B24. fault B35.6.7.8. ALARM B79.10.11.12. 0=Emergency stop B16913. 0=外控/内控=114. ME已ON B12415. 故障复位16. Over speedT400的数字量输入 DIIN4 XC1:35 T56 剪切位信号IN5 T57 剪前热检1#飞剪 常数设定1.H014 切头误差补偿(mm)2.3.4.H015 切尾误差补偿 (mm)5.6.7.H002 D2:M7-M8的距离(mm)8.H001 D1:M7-M8间热检到M8的距离(mm)2#飞剪的参数数字量输入4.剪切位信号 Q4 T565.剪前7米热检 Q5 T576. 剪后40米热检(南) Q6 T587. 剪后40米热检 (北) Q7 T598. M14出口热检 Q8 T602#飞剪PLC发来的数据PZD1. 系统控制字2. 飞剪速度给定(成品机架的线速度mm/s)3. 飞剪超前系数4. 飞剪滞后系数5. 第1根倍尺长度mm6. 切尾长度 mm7. 第2根倍尺长度 (SPARE)8.停止位角度设定(度)9. 成品机架的 辊径/减速比10. 第4根倍尺长度 (FUTURE)控制字各位的分配1. ON 合闸2.3.4. EN 使能(spare)5. 手动剪切 (按钮)6. 剪后轧机有钢信号 (spare)7. 剪头选择 (画面)8. 剪尾选择 (画面)9. 飞剪故障复位 (画面)10. 剪前轧机有钢信号 (spare)11.12. 飞剪位置复位(手动剪刃定位指令) (按钮)13. 回转/曲柄 1=曲柄 (spare)14. 手动/自动(1=手动) (画面)15. 碎断 (按钮)16. 飞剪速度设定选择 1=设定 (spare)2#飞剪发送给PLC的数据1. 状态字2.速度检测 100%=540rpm3.电流反馈4.5 成品钢速(SPARE)状态字的各位分配1. 6RA70 合闸准备就绪2. 等待操作 ready to OP.3. 运行 run4. 6RA70 重故障5. 超速6. 剪前热检信号(6m)7. 轻故障8. 飞剪剪切9. 本地=1/远程=010.=111.剪后热检12. I=013.速度等于零 N=014.剪后热检 (SPARE)15.飞剪到达停止位信号16.(6R70-READY)2#飞剪的常数值在程序段 LONG_TIME (A1) 之中2#飞剪的DI分配4.剪切位 Q4 T565.剪前7米热检 Q5 T576. 剪后40米热检(南) Q6 T587. 剪后40米热检 (北) Q7 T598. M14出口热检 Q8 T60位置闭环用脉冲的计算1.方法把6RA70装置的脉冲编码器的位置计数值K42送到T400,作为剪刃停止位的实际值信号.2.飞剪1(FJ1)的齿轮减速机的变比为6.5, 编码器的脉冲数为1024,采用4倍频的方式计数.在T400中把剪刃旋转一周定为360度->1.03.当剪刃转一周360度时,电动机转过6.5周,计数脉冲数为4096×6.5=266244.把26624送到T400, Y=X×NF/16384, 为使Y值标定为1.0,系数NF应为16384/26624=0.61538 . 内控设定角度值在程序段COM_PLC(A1) 的P_SET_SEL X25.飞剪3 同理:4096×2.186=8953.8616384/8953.86=1.82986.PLC送来角度设定值是16384==360度V-N系数的计算(线速度和转速的换算)飞剪1:电机每分钟540转, 剪刃半径482mm 减速比为6.5 角速度为ω = (540×2π)/(6.5×60)=2.769π线速度为v=ω×r=2.769π×482=4192.95mm/s当线速度为1000mm/s时,相应的百分值角速度为:0.2381000/4192 =0.238所以V-N系数为0.000238飞剪3:电机每分钟540转, 剪刃半径575mm 减速比为2.186角速度为 ω = (540×2π)/(2.186×60)=8.234π线速度为 v=ω×r=8.2349π×575=14874mm/s当线速度为1000mm/s时,相应的百分值角速度为:1000/14874 =0.0672所以V-N系数为0.0000672H参数(切头飞剪)H参数序号内容注释H000H001 剪前热检到8机架距离(mm)剪前热检到飞剪距离H002 7,8机架间距离(mm)飞剪到剪后热检的距离H003H004 剪前热检得电延时(毫秒ms)H005 剪前热检失电延时(毫秒ms)H006 接近开关延时(毫秒ms)H007 剪刃停止位设定(内控时)H008 剪刃位置闭环PI调节器KP设定H009 剪刃位置闭环PI调节器TN设定(ms)H010 位置闭环速度设定值1=100%速度H011 手工剪刃复位速度设定值手工剪刃复位速度设定值POS(A4) H012 碎断速度设定1=100%速度H013 1=100%速度H014 剪头误差补偿(mm)H015 剪尾误差补偿(mm)H016H017H018H019H020H021H022H023H024H025H026H027H028H029D030 自PLC线速度设定值(V7 mm/s) RD031 飞剪实际位置(度) RD032 BD033 BD034 剪切位接进开关状态剪切位接进开关状态 BD035 剪前热检状态剪前热检状态RD036 网上发来超前系数RD037 网上发来滞后系数RD038D039 网上发来切头长度(mm)RD040 网上发来切尾长度(mm)R红色表示3号飞剪FJ3复位按钮的作用当故障发生或切下ME开关时,将位置环,剪切,碎断,手动定位等RS触发器都清零,为下一次起动做准备.DE了一个BUG2005年11月27日: 当碎断停车时,发现有速度设定重叠的现象,开始以为是碎断和位置闭环的两个S端信号有100ms的重叠,经6RA70的示波器拍波形,没有此现象,在向CUDI发送转速给定的P调节器即FR_POS(A5)的NSET_SEL之前加切换开关NSW后,100ms的重叠现象消除.定位准确性达到计算值。
3#飞剪剪切长度及精度的调整方法
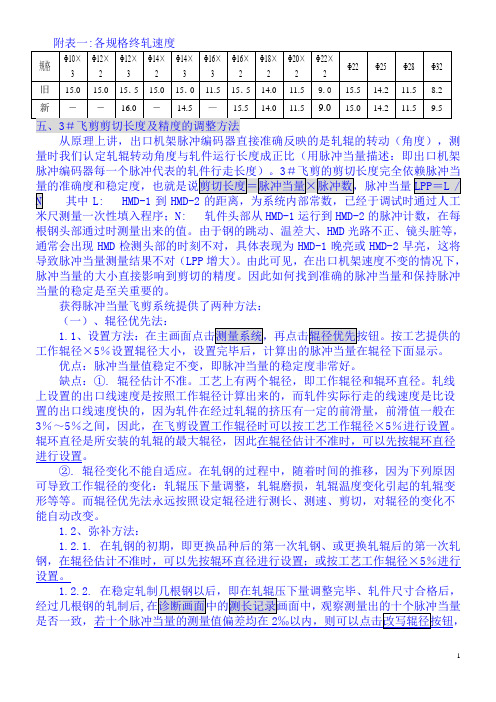
量时我们认定轧辊转动角度与轧件运行长度成正比(用脉冲当量描述:即出口机架其中L: HMD-1到N: 轧件头部从HMD-1运行到HMD-2的脉冲计数,在每根钢头部通过时测量出来的值。
由于钢的跳动、温差大、HMD光路不正、镜头脏等,通常会出现HMD检测头部的时刻不对,具体表现为HMD-1晚亮或HMD-2早亮,这将导致脉冲当量测量结果不对(LPP增大)。
由此可见,在出口机架速度不变的情况下,脉冲当量的大小直接影响到剪切的精度。
因此如何找到准确的脉冲当量和保持脉冲当量的稳定是至关重要的。
获得脉冲当量飞剪系统提供了两种方法:(一)、辊径优先法:1.1工作辊径×5优点:脉冲当量值稳定不变,即脉冲当量的稳定度非常好。
缺点:①. 辊径估计不准。
工艺上有两个辊径,即工作辊径和辊环直径。
轧线上设置的出口线速度是按照工作辊径计算出来的,而轧件实际行走的线速度是比设置的出口线速度快的,因为轧件在经过轧辊的挤压有一定的前滑量,前滑值一般在3%~5%之间,因此,在飞剪设置工作辊径时可以按工艺工作辊径×5%进行设置。
辊环直径是所安装的轧辊的最大辊径,因此在辊径估计不准时,可以先按辊环直径进行设置。
②. 辊径变化不能自适应。
在轧钢的过程中,随着时间的推移,因为下列原因可导致工作辊径的变化:轧辊压下量调整,轧辊磨损,轧辊温度变化引起的轧辊变形等等。
而辊径优先法永远按照设定辊径进行测长、测速、剪切,对辊径的变化不能自动改变。
1.2、弥补方法:1.2.1. 在轧钢的初期,即更换品种后的第一次轧钢、或更换轧辊后的第一次轧钢,在辊径估计不准时,可以先按辊环直径进行设置;或按工艺工作辊径×5%进行设置。
则辊径随即按十个脉冲当量的测量值的平均值反算出的辊径进行修改。
此时的辊径即是准确的工作辊径,由此算出的脉冲当量即是准确的脉冲当量。
1.2.3. 在轧钢过程中,要注意观察测长记录。
随着时间的推移,操作人员会发现测量出的脉冲当量会越来越小,此时剪切出的钢的长度会越来越短。
- 1、下载文档前请自行甄别文档内容的完整性,平台不提供额外的编辑、内容补充、找答案等附加服务。
- 2、"仅部分预览"的文档,不可在线预览部分如存在完整性等问题,可反馈申请退款(可完整预览的文档不适用该条件!)。
- 3、如文档侵犯您的权益,请联系客服反馈,我们会尽快为您处理(人工客服工作时间:9:00-18:30)。
飞剪现场调试资料(6RA70直流装置简要调试步骤) 1.现场安装
1)系统单独接地,不要与其它系统共用地线,比如轧机、辊道变频器等
根据《工业与民用电力装置的接地设计规范(GBJ65‐83)》,要求如下:
人工接地体的材料可采用水平敷设的圆钢、扁钢、垂直敷设的角钢、圆钢等。
接地装置的导体截面,应符合热稳定与均压的要求,且不应小于表1所列规格。
表 1 钢接地体和接地线的最小规格
注:
1.电力线路杆塔的接地体引出线,其截面不应小于50 cm2,并应热镀锌
2.经常流过直流电力电流的接地体和接地线,其地下部分最小规格见附录1
3.作为接地线的钢管,表中地下系指车间地坪内
敷设在腐蚀较强场所的接地装置,应根据腐蚀的性质采取热镀锌、热镀锡等防腐措施,
或适当加大截面。
2)动力电缆与控制电缆必须分开铺设;编码器、接近开关、热检的电缆线铺设时必须穿钢管铺设
3)编码器电缆必须要用屏蔽双绞线
4)检查电机绝缘
5)每个气缸气源必须要有空气过滤器,气动阀安装位置离气缸越近越好,并且要对电磁阀做好保护
2.查线
1)根据原理图查线,控制线必须使用屏蔽电缆,并且要把屏蔽层接到柜体接地处
2)要求每根线都要穿有线号,字迹清楚,并且接线牢固
3)现场检测元件(接近开关,编码器,热检等)必须要确认接线正确
4)检查柜内各大线(铜牌)螺丝没有松动
3.送电
1)确认系统没有短路
2)系统依次上电,确认系统正常
3)检查系统风机,电机风机(电机风机出风口风量大)转向正确
4)依次检查现场检测元件(接近开关,编码器,热检等)信号正确进入PLC 5)依次给各电磁阀上电,检查气缸动作,调节好气缸气源压力
6)检查摆杆摆动方向,默认电磁阀没有信号,指向1#(3#)通道
7)如果直流电机为老电机的情况下,在电机运行之前,先给停机励磁15~30分钟
方法如下:
P102 设置电机额定励磁电流
P082=2 在整流器已经达到运行状态o7或更高时,达到在参数P258中设置的时间以后,在P257中设置的停机励磁自动接入
参数设置好后,通过P257(停机励磁)输出励磁
保持励磁输出(100%)和飞剪风机电机运行
4.6RA70设置
1)P051=21 参数初始化
2)U840 用于模拟工作模式的控制参数(输入11~26,分别测试12路点火脉冲) 3)检查只读参数
R010 开关量输入,0‐6位对应36‐42端子状态
R011 开关量输出状态,0位对应46端子状态,1位对应48端子状态
R015 实际电枢进线电压,应在允许值范围内(主接触器合闸后显示)
R016 实际励磁进线电压,应在允许值范围内(励磁空开合闸后显示)
4)参数设定
P076 整流器额定电流减少(机械车间调试默认即可)(现场调试循寻此公式:P076.001≥P100 * max(P171,P172)÷R072;P076.002≥ P102 ÷ R073)
P078 整流器额定电源电压的衰减(i001:电枢额定输入电压;i002:励磁额定输入电压;实际应用到功率单元的供电系统额定电压值必须在这个参数中设置) (现场调试,P078.001=R015;P078.002=R016)
P082 励磁的运行模式(2为在整流器达到运行状态O7或更高时,停机励磁自动接入;3为励磁持续有效)
P083 速度实际值选择(2为脉冲编码器反馈,3为电压反馈)
P100 电机额定电流(电机铭牌)
P101 电机额定电压(电机铭牌)
P102 电机励磁电流(电机铭牌)(在电机冷态时,适当调整此值。
使柜体励磁电流表值不超过铬牌额定励磁电流;励磁电压表值接近并且不超过铬牌额定电压* 70%)
P140 脉冲编码器类型(常用为 1)
P141 脉冲编码器的脉冲数(常用为1024)
P142 脉冲编码器信号的匹配(0为5v信号,1为15v信号)
P143 电机额定转速(电机铭牌)
P171 转矩方向ⅠⅡ的系统电流限幅(根据实际应用设置)(机械车间调试默认即可)
P172 转矩方向Ⅱ的系统电流限幅(根据实际应用设置)(机械车间调试默认即可)
P303 斜坡上升时间1(飞剪调试可设0.02)(轧机调试为系统默认)
P304 斜坡下降时间1(飞剪调试可设0.02)(轧机调试为系统默认)
P305 初始圆弧1(飞剪调试可设0.02)(轧机调试为系统默认)
P306 最终圆弧1(飞剪调试可设0.02)(轧机调试为系统默认)
P430.3 固定给定值接入的源(常用为16)
P431.3 固定给定值的源(常用为15)
P771 开关量输出1(常用为106“故障”)
P772 开关量输出2(常用为104“运行”)
U580=4 换向监控控制字,4为估算最大电流实际值
1)先把速度反馈设为电压反馈,P83设为3
2)内控,合闸,运行,观察r1,旋转电位计到5%左右,观察飞剪运行状态,包括转向,机械情况等等。
如果转向不对的话,断运行,分闸,把端子上励磁两根线互导即可。
在机械状态正常的情况下,再进行下面步骤。
3)观察r24(编码器速度),是否与飞剪同向(应为正数)并且较稳定
4)把速度反馈设为编码器反馈,P83设为2。
内控,运行,观察飞剪状态 5)优化6RA70,电流优化(P40设为25)和速度优化(P40设为26)
P051 = 25 电枢和励磁的预控制和电流调节器的优化运行
P051 = 26 速度调节器的优化运行
SIMOREG 整流器转换到运行状态o7.4 几秒钟,然后进入状态o7.0 或o7.1 并且等待“合闸”和“运行使能”输入。
输入“合闸”和“运行使能”指令。
PMU (简易操作控制面板)上的运行状态显示的十位闪烁,预示在“合闸”指令后将执行一个优化运行。
如果在30 秒时间内没有“合闸”指令输入,这个等待状态终止并显示故障信息F052。
当整流器达到运行状态<o1.0 (运行)时,执行优化运行。
在PMU 上出现一个活动的显示,包括二个2 位数,由一个上下移动的条分开,这二个数表明(SIEMENS 专用)当前的优化运行状态。
P051 = 25 电枢和励磁的预控制和电流调节器的优化运行(持续大约40s)电流调节器优化运行也可以在电机轴上没有负载时执行,必要时要将电机机械锁住。
以下参数被自动设置: P110,P111,P112,P155,P156,P255,P256,P826。
P051 = 26 速度调节器的优化运行(持续大约6 秒)。
如果负载比较重的情况下,可适当减少P236。
用P236 选择速度调节回路动态响应的程度,在此,小值将产生一个软的调节器设定。
在速度调节器优化之前设定P236 并将影响到P225、P226 和P228 的设定。
对于速度调节器的优化,在电机轴上必须接上最后有效的机械负载,因为所设定的参数同所测量的转动惯量有关。
以下参数被自动设置: P225,P226 和P228。
上述步骤完成后,执行如下步骤:
步骤1:内控运行飞剪,适当调节电位计(R001显示内控速度给定百分比)并观察飞剪机械部分、箱体油路以及电机是否存在问题。
并且监控程序或触摸屏观察飞剪角度变化和接近开关信号是否正确。
步骤2:外控合闸,点动运行飞剪。
使用DriveMonitor联接6RA70监控达速曲线并保存,设置如下:
调试过程中几点注意:
z飞剪首次通电运行之前,必须手动盘一圈,避免机械故障。
z优化过程中,必须观察外部飞剪动作状况,若有紧急情况立刻分闸
z分闸后10秒钟左右,观察柜体励磁电压/电流表是否归零;如未归零,检查6RA70背面励磁功率单元并检查励磁电缆绝缘性
注:
1.轧机调试过程中,需增加冲击补偿参数,详见附录2
2.调试过程中,对相关参数进行记录,记录格式详见“飞剪传动状态反馈单”,
调试完成后带回公司归档保存。
附录1
直流电力网中的接地装置,应符合下列要求:
A.能与地构成闭合回路且经常流过电流的接地线,应沿绝缘垫板敷设,不得与金属管道、建筑物和设备的构造件有金属的连接;
B.经常流过电流的接地线和接地体,除应符合载流量和热稳定的要求外,其地下部分的最小规格不应小于:圆钢直径10cm,扁钢和角钢厚度6cm,钢管管壁厚度4.5cm。
C.接地装置应尽量避免敷设在土壤中含有电解时排出活性作用物质或各种溶液的地方,必要时可采用外引式接地装置,否则应采取改良土壤的措施。
附录2
6RA70冲击补偿参数设置:
U197.001=109 (1st不带滤波限幅值监控信号源;i001:输入信号)
U197.002=9186 (1st不带滤波限幅值监控信号源;i002:开关阀值)
U198=10 (限幅值监控的可调开关阀值,适用于K9186)
U199=5 (1st不带滤波的限同值监控的滞环)
U449.001=9170 (定时器4输入信号和复位信号的源)
U450=0.1 (定时器4的时间)
U451=1 (定时器4的方式)
U242.001=0 (连接器转换开关2输入量源为常数0)
U242.002=409 (连接器转换开关2输入量源为K0409)
U243=9586 (连接器转换开关2控制信号源为B9586)
P645=9211 (附加给定值源为K9211)
P409=2 (设置K0409的值为2)。