Sheet Metal process mapping 钣金件加工过程
钣金加工工艺流程表

钣金加工工艺流程表
1、材料准备:根据图纸要求准备钣金工件和所需的材料;
2、切割加工:根据图纸尺寸要求,选择合适的切割方法,进行切割加工;
3、冲孔加工:根据图纸中规定的形状和尺寸,进行冲孔加工;
4、焊接加工:根据图纸的要求,进行焊接加工,使焊接部位牢固;
5、机加工:如果图纸中有需要机加工的地方,需要将其加工成所需的形状和尺寸;
6、磨削加工:如果图纸要求,需要进行磨削加工,使表面光滑;
7、安装加工:将加工好的钣金件安装在机器上,检查是否牢固。
钣金生产流程及工艺
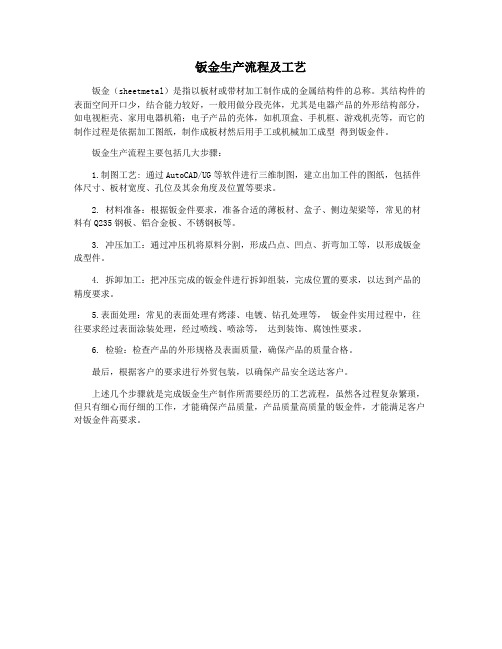
钣金生产流程及工艺
钣金(sheetmetal)是指以板材或带材加工制作成的金属结构件的总称。
其结构件的表面空间开口少,结合能力较好,一般用做分段壳体,尤其是电器产品的外形结构部分,如电视柜壳、家用电器机箱;电子产品的壳体,如机顶盒、手机框、游戏机壳等,而它的制作过程是依据加工图纸,制作成板材然后用手工或机械加工成型得到钣金件。
钣金生产流程主要包括几大步骤:
1.制图工艺: 通过AutoCAD/UG等软件进行三维制图,建立出加工件的图纸,包括件体尺寸、板材宽度、孔位及其余角度及位置等要求。
2. 材料准备:根据钣金件要求,准备合适的薄板材、盒子、侧边架梁等,常见的材料有Q235钢板、铝合金板、不锈钢板等。
3. 冲压加工:通过冲压机将原料分割,形成凸点、凹点、折弯加工等,以形成钣金成型件。
4. 拆卸加工:把冲压完成的钣金件进行拆卸组装,完成位置的要求,以达到产品的精度要求。
5.表面处理:常见的表面处理有烤漆、电镀、钻孔处理等,钣金件实用过程中,往往要求经过表面涂装处理,经过喷线、喷涂等,达到装饰、腐蚀性要求。
6. 检验:检查产品的外形规格及表面质量,确保产品的质量合格。
最后,根据客户的要求进行外贸包装,以确保产品安全送达客户。
上述几个步骤就是完成钣金生产制作所需要经历的工艺流程,虽然各过程复杂繁琐,但只有细心而仔细的工作,才能确保产品质量,产品质量高质量的钣金件,才能满足客户对钣金件高要求。
钣金加工工艺流程与步骤细节,你知道吗?

钣金加工工艺流程与步骤细节,你知道吗?钣金加工:针对金属板材的一种综合冷加工工艺,要分为剪切、冲裁、折弯、铆接、模具成型加工方法等。
常用的板材有热轧板、酸洗板、冷轧板、镀锌板、铜板、铝板、铝型材、不锈钢等。
加工方法:1.通过数冲、数折、激光切割机、剪板机、等设备对板材进行钣金加工,多用于样品及小批量生产,成本较高。
2.通过固定的模具在冲床或压机等设备对板材进行钣金加工,速度快,成本低,但是模具成本很大,且安装、更换时,多用于大批量生产。
钣金件加工工艺流程:1.下料:落料模、激光切割、剪板机、数冲。
2.成型:数冲、数折、成型模具。
3.其他加工:压铆、攻丝。
4.焊接:电弧焊、电阻焊。
5.表面处理:喷粉、电泳、电镀等。
剪板机:用于剪切条料,它主要是为模具落料加工准备,或规则外形的简单零件下料。
速度快、成本低、精度低,只能加工无孔无切角的条料或块料。
可快速换型。
激光切割机:用高能激光照射被切割材料,使材料气化产生空洞,光束移动形成割缝,将零件的结构形状切割出来,需编写激光程式,它可切割各种复杂形状的零件。
成本高,精度高。
可快速换型。
数冲:一种装有数控控制的自动化冲床,通过数控编程指令,操纵冲床动作并加工零件。
通过简单模具组合,可一次完成多种复杂空型和浅拉伸零件,还可通过小模步冲的方式加工大圆孔、方空、腰孔及各种形状的曲线轮廓,也可进行特殊工艺加工,如百叶窗、沉孔、翻边孔、加强筋、压印等。
可以快速换型。
数控折弯机:通过模具对薄板进行折弯设备,操作简单,而且可对带侧壁的工件进行加工。
加工速度快,精度较高,具有自动补偿功能。
可快速换型。
钣金加工工艺设计流程
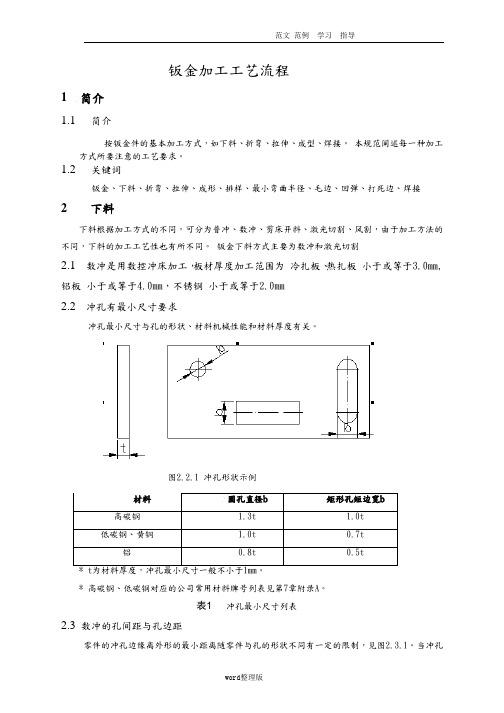
钣金加工工艺流程1简介1.1简介按钣金件的基本加工方式,如下料、折弯、拉伸、成型、焊接。
本规范阐述每一种加工方式所要注意的工艺要求。
1.2关键词钣金、下料、折弯、拉伸、成形、排样、最小弯曲半径、毛边、回弹、打死边、焊接2下料下料根据加工方式的不同,可分为普冲、数冲、剪床开料、激光切割、风割,由于加工方法的不同,下料的加工工艺性也有所不同。
钣金下料方式主要为数冲和激光切割2.1数冲是用数控冲床加工,板材厚度加工范围为冷扎板、热扎板小于或等于3.0mm,铝板小于或等于4.0mm,不锈钢小于或等于2.0mm2.2冲孔有最小尺寸要求冲孔最小尺寸与孔的形状、材料机械性能和材料厚度有关。
图2.2.1 冲孔形状示例* 高碳钢、低碳钢对应的公司常用材料牌号列表见第7章附录A。
表1冲孔最小尺寸列表2.3数冲的孔间距与孔边距零件的冲孔边缘离外形的最小距离随零件与孔的形状不同有一定的限制,见图2.3.1。
当冲孔1.5t。
2.4折弯件或拉深件冲孔时,其孔壁与工件直壁之间应保持一定的距离(图2.4.1)图2.4.1 折弯件、拉伸件孔壁与工件直壁间的距离2.5螺钉、螺栓的过孔和沉头座螺钉、螺栓过孔和沉头座的结构尺寸按下表选取取。
对于沉头螺钉的沉头座,如果板材太薄难以同时保证过孔d2和沉孔D,应优先保证过孔d2。
表2用于螺钉、螺栓的过孔*要求钣材厚度t≥h。
表3用于沉头螺钉的沉头座及过孔*要求钣材厚度t≥h。
表4用于沉头铆钉的沉头座及过孔2.6激光切割是用激光机飞行切割加工,板材厚度加工范围为冷扎板热扎板小于或等于20.0mm, 不锈钢小于10.0mm 。
其优点是加工板材厚度大,切割工件外形速度快,加工灵活.缺点是无法加工成形,网孔件不宜用此方式加工,加工成本高!3折弯3.1折弯件的最小弯曲半径材料弯曲时,其圆角区上,外层收到拉伸,内层则受到压缩。
当材料厚度一定时,内r越小,材料的拉伸和压缩就越严重;当外层圆角的拉伸应力超过材料的极限强度时,就会产生裂缝和折断,因此,弯曲零件的结构设计,应避免过小的弯曲圆角半径。
钣金的工艺流程
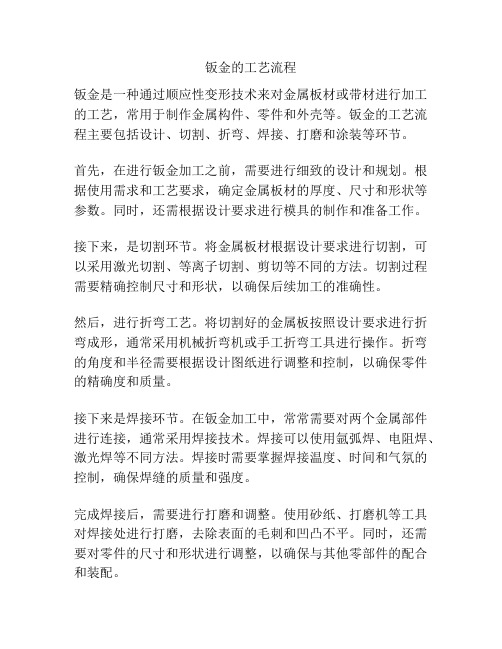
钣金的工艺流程钣金是一种通过顺应性变形技术来对金属板材或带材进行加工的工艺,常用于制作金属构件、零件和外壳等。
钣金的工艺流程主要包括设计、切割、折弯、焊接、打磨和涂装等环节。
首先,在进行钣金加工之前,需要进行细致的设计和规划。
根据使用需求和工艺要求,确定金属板材的厚度、尺寸和形状等参数。
同时,还需根据设计要求进行模具的制作和准备工作。
接下来,是切割环节。
将金属板材根据设计要求进行切割,可以采用激光切割、等离子切割、剪切等不同的方法。
切割过程需要精确控制尺寸和形状,以确保后续加工的准确性。
然后,进行折弯工艺。
将切割好的金属板按照设计要求进行折弯成形,通常采用机械折弯机或手工折弯工具进行操作。
折弯的角度和半径需要根据设计图纸进行调整和控制,以确保零件的精确度和质量。
接下来是焊接环节。
在钣金加工中,常常需要对两个金属部件进行连接,通常采用焊接技术。
焊接可以使用氩弧焊、电阻焊、激光焊等不同方法。
焊接时需要掌握焊接温度、时间和气氛的控制,确保焊缝的质量和强度。
完成焊接后,需要进行打磨和调整。
使用砂纸、打磨机等工具对焊接处进行打磨,去除表面的毛刺和凹凸不平。
同时,还需要对零件的尺寸和形状进行调整,以确保与其他零部件的配合和装配。
最后是涂装环节。
根据设计要求和使用环境,对钣金零件进行喷涂或电泳涂装。
涂装可以提供保护层,增加零件的耐腐蚀性和美观度。
在涂装过程中,需要注意喷涂的厚度、均匀性和涂层的附着力。
总结起来,钣金工艺流程包括设计、切割、折弯、焊接、打磨和涂装等环节。
每个环节都需要严格控制和操作,以确保钣金零件的质量和精度。
钣金工艺在制造业中应用广泛,其成形速度快、成本低廉、零件精度高,被广泛用于汽车制造、电子设备、家电、建筑等领域。
钣金件工艺流程图
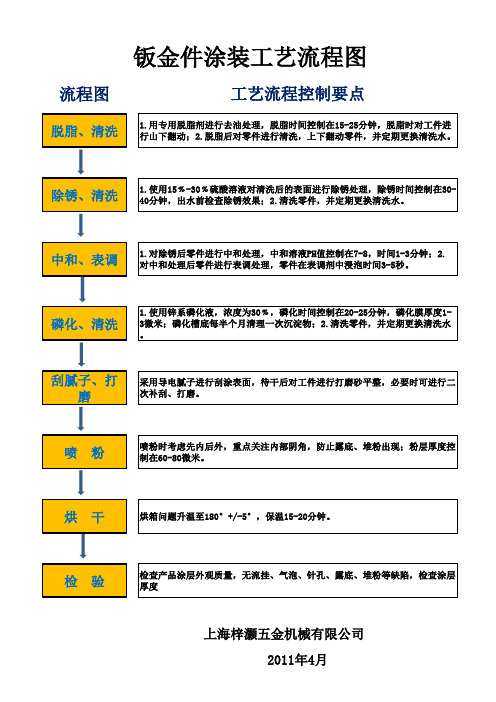
中和、 中和、表调
对除锈后零件进行中和处理,中和溶液PH值控制在7 PH值控制在 时间1 分钟; 1.对除锈后零件进行中和处理,中和溶液PH值控制在7-8,时间1-3分钟;2. 对中和处理后零件进行表调处理,零件在表调剂中浸泡时间3 对中和处理后零件进行表调处理,零件在表调剂中浸泡时间3-5秒。
磷化、清洗 磷化、
刮腻子、打磨 刮腻子、
采用导电腻子进行刮涂表面,待干后对工件进行打磨砂平整, 采用导电腻子进行刮涂表面,待干后对工件进行打磨砂平整,必要时可进行二 次补刮、打磨。 次内后外,重点关注内部阴角,防止露底、堆粉出现;粉层厚度控 喷粉时考虑先内后外, 重点关注内部阴角, 防止露底、 堆粉出现; 制在60 80微米 60- 微米。 制在60-80微米。
1.使用锌系磷化液,浓度为30﹪,磷化时间控制在20-25分钟,磷化膜厚度1使用锌系磷化液,浓度为30﹪,磷化时间控制在20-25分钟,磷化膜厚度1 30﹪,磷化时间控制在20 分钟 微米;磷化槽底每半个月清理一次沉淀物; 清洗零件, 3微米;磷化槽底每半个月清理一次沉淀物;2.清洗零件,并定期更换清洗水 。
钣金件涂装工艺流程图流程图工艺流程控制要点脱脂清洗除锈清洗中和表调磷化清洗刮腻子打磨检查产品涂层外观质量无流挂气泡针孔露底堆粉等缺陷检查涂层厚度上海梓灏五金机械有限公司1
钣金件涂装工艺流程图
流程图
脱脂、 脱脂、清洗
工艺流程控制要点
用专用脱脂剂进行去油处理,脱脂时间控制在15 25分钟 15- 分钟, 1.用专用脱脂剂进行去油处理,脱脂时间控制在15-25分钟,脱脂时对工件进 行山下翻动; 脱脂后对零件进行清洗,上下翻动零件,并定期更换清洗水。 行山下翻动;2.脱脂后对零件进行清洗,上下翻动零件,并定期更换清洗水。
钣金加工工艺流程

For personal use only in study and research; not for commercial use钣金加工工艺流程1简介1.1简介按钣金件的基本加工方式,如下料、折弯、拉伸、成型、焊接。
本规范阐述每一种加工方式所要注意的工艺要求。
1.2关键词钣金、下料、折弯、拉伸、成形、排样、最小弯曲半径、毛边、回弹、打死边、焊接2 下料下料根据加工方式的不同,可分为普冲、数冲、剪床开料、激光切割、风割,由于加工方法的不同,下料的加工工艺性也有所不同。
钣金下料方式主要为数冲和激光切割2.1数冲是用数控冲床加工,板材厚度加工范围为冷扎板、热扎板小于或等于3.0mm,铝板小于或等于4.0mm,不锈钢小于或等于2.0mm2.2冲孔有最小尺寸要求冲孔最小尺寸与孔的形状、材料机械性能和材料厚度有关。
图2.2.1 冲孔形状示例* 高碳钢、低碳钢对应的公司常用材料牌号列表见第7章附录A。
表1冲孔最小尺寸列表2.3数冲的孔间距与孔边距零件的冲孔边缘离外形的最小距离随零件与孔的形状不同有一定的限制,见图,该最小距离应不小于材料厚度t;平行时,应不小于1.5t。
图2.3.1 冲裁件孔边距、孔间距示意图2.4折弯件及拉深件冲孔时,其孔壁与直壁之间应保持一定的距离折弯件或拉深件冲孔时,其孔壁与工件直壁之间应保持一定的距离(图图2.4.1 折弯件、拉伸件孔壁与工件直壁间的距离2.5螺钉、螺栓的过孔和沉头座螺钉、螺栓过孔和沉头座的结构尺寸按下表选取取。
对于沉头螺钉的沉头座,如果板材太薄难以同时保证过孔d2和沉孔D,应优先保证过孔d2。
表2用于螺钉、螺栓的过孔*要求钣材厚度t≥h。
表3用于沉头螺钉的沉头座及过孔*要求钣材厚度t≥h。
表4用于沉头铆钉的沉头座及过孔2.6激光切割是用激光机飞行切割加工,板材厚度加工范围为冷扎板热扎板小于或等于20.0mm, 不锈钢小于10.0mm 。
其优点是加工板材厚度大,切割工件外形速度快,加工灵活.缺点是无法加工成形,网孔件不宜用此方式加工,加工成本高!3 折弯3.1折弯件的最小弯曲半径材料弯曲时,其圆角区上,外层收到拉伸,内层则受到压缩。
钣金生产打磨工艺流程

钣金生产打磨工艺流程【中英文实用版】Title: Sheet Metal Finishing Process - Deburring and PolishingTitle: 钣金生产打磨工艺流程In the sheet metal fabrication process, deburring and polishing are essential steps to ensure the quality and functionality of the final product.This article will discuss the detailed process of deburring and polishing in sheet metal production.在钣金加工过程中,去毛刺和打磨是确保最终产品质量和工作性能的关键步骤。
本文将详细介绍钣金生产中的去毛刺和打磨工艺流程。
Firstly, after cutting, the sheet metal usually has burrs and sharp edges, which need to be removed through deburring.Deburring is the process of removing the burrs and sharp edges generated during the cutting process to ensure the safety and comfort of handling the metal parts.首先,在切割后,钣金通常会有毛刺和锐边,这些需要通过去毛刺来去除。
去毛刺是去除切割过程中产生的毛刺和锐边的过程,以确保金属部件的安全和舒适性。
Secondly, polishing is performed to enhance the appearance and corrosion resistance of the sheet metal.It also helps to improve the sheet metal"s overall performance in terms of durability and aesthetics.There are various polishing methods available, such as hand polishing, machinepolishing, and chemical polishing.其次,打磨是用来提高钣金的外观和耐腐蚀性的。
钣金加工的工艺流程
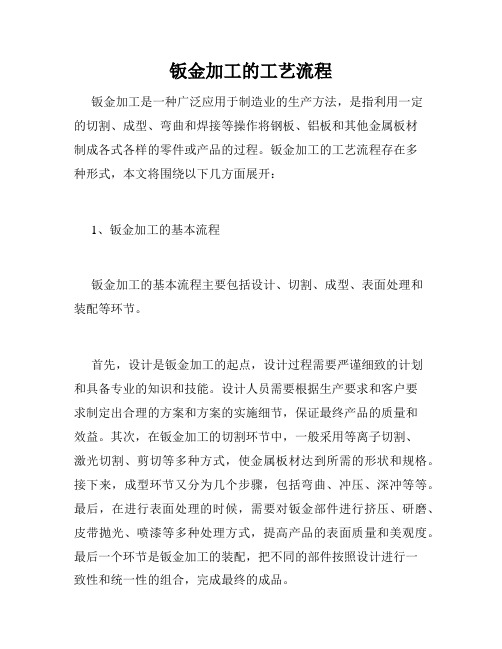
钣金加工的工艺流程钣金加工是一种广泛应用于制造业的生产方法,是指利用一定的切割、成型、弯曲和焊接等操作将钢板、铝板和其他金属板材制成各式各样的零件或产品的过程。
钣金加工的工艺流程存在多种形式,本文将围绕以下几方面展开:1、钣金加工的基本流程钣金加工的基本流程主要包括设计、切割、成型、表面处理和装配等环节。
首先,设计是钣金加工的起点,设计过程需要严谨细致的计划和具备专业的知识和技能。
设计人员需要根据生产要求和客户要求制定出合理的方案和方案的实施细节,保证最终产品的质量和效益。
其次,在钣金加工的切割环节中,一般采用等离子切割、激光切割、剪切等多种方式,使金属板材达到所需的形状和规格。
接下来,成型环节又分为几个步骤,包括弯曲、冲压、深冲等等。
最后,在进行表面处理的时候,需要对钣金部件进行挤压、研磨、皮带抛光、喷漆等多种处理方式,提高产品的表面质量和美观度。
最后一个环节是钣金加工的装配,把不同的部件按照设计进行一致性和统一性的组合,完成最终的成品。
2、钣金加工工艺的具体操作在钣金加工的具体操作过程中,也需要遵循不同的步骤和操作流程。
一般来说,先需要进行材料开料和预处理,即按照设计要求将金属板材进行切割和成型。
这时,还需要对材料进行明确标记和编号,以便于后续的加工操作。
之后,便可以开始进行钣金成型操作。
在钣金加工的成型过程中,通过采用各种加工工艺,使得金属板材达到所需的形状和角度。
在具体操作时,需要选用与工件材料相适配的刀具、模具等加工设备,确保加工质量和效率。
此外,钣金加工过程中,还会产生一定程度的残余压力,需要采取一些去除残余应力的措施,以避免材料变形和开裂等不良后果。
3、钣金成型操作中需要注意的问题在钣金加工中,很多问题都是可以预见的。
一旦出现问题,可能会导致产品的质量不稳定和生产效率下降。
因此,在进行钣金成型操作前,需要做好预处理,把不同部位的问题纳入考虑范围,并采取相应措施。
首先,需要减少金属板材的切割失误。
钣金生产流程表

钣金生产流程表The sheet metal production process involves a series of steps that are essential for creating a wide range of products used in various industries. 钣金生产流程包括一系列步骤,这些步骤对于制造各种工业中使用的产品至关重要。
The first step in the sheet metal production process is the design phase, where engineers and designers work together to create detailed plans and drawings for the product. 钣金生产流程的第一步是设计阶段,工程师和设计师共同合作,为产品制定详细的计划和图纸。
Once the design is finalized, the next step is to procure the raw materials needed for the production. 一旦设计确定,下一步是采购生产所需的原材料。
After the raw materials are obtained, the sheet metal is cut, bent, and formed into the desired shape using specialized equipment and machinery. 在获得原材料之后,使用专门的设备和机械将钣金切割、弯曲和成型成所需的形状。
The formed sheet metal parts are then assembled and welded together to create the final product. 成型的钣金零件然后被组装和焊接在一起,制成最终产品。
板金件设计 Sheet_Metal 钣金

第5頁
3.基本繪圖指令
3-1板金設計工具列
3-1-1 板金參數
操作方法︰
1)
進入板金件模組後,先設定板金參數 包含: • 參數 • 順接曲面端點 • 順接曲面圓角清除 • 順接曲面容差
2)
說明︰
點選OK結束指令
1) 2) 3) 4)
參數內可設定板金件厚度及順接曲面半徑 順接曲面端點內包含沒有清除的最小值、方 形清除、 圓形清除 、 線性、相切、最大等設定值 順接曲面圓角清除包含3種清除圓角模式 順接曲面容差
範例 : Wall1
第8頁
3-1-4 擠伸
操作方法︰
1)
點選
, 選取任一幾何圖形彈出
擠伸定義對話框。 2) 點選OK結束指令。
說明︰ 1) 幾何圖形為圓或弧則對話框中( 形式 ) 欄位呈灰階無法輸入。
2)
3) 4)
曲線不能作擠伸。
對話框中形式欄位包含 ( 尺寸、到平面、到曲面 ) 。 鏡射的長度會依幾何圖形所在平面為中心作對稱擠伸。
範例 : Stamping5
第20頁
3-4-6百葉窗(Louver) 操作方法︰
1)
點選
, 再選取欲做百葉窗的曲線,
百葉窗對話框彈出。 2) 3) 依序輸入各欄位欲做的值。 點選OK結束指令。
說明︰ 1) 2) 欲作百葉窗的曲線必頇是封閉的曲線。 輸入值若不合理則指令無法執行。
範例 : Stamping6
3-4標記工具列
3-4-1點標籤 3-4-2擠伸孔 3-4-3曲線標籤
3-4-4曲面標籤
3-4-5橋 3-4-6百葉窗(Louver)
3-2接件工具列
3-2-1自動順接曲面 3-2-2順接曲面
钣金件加工流程

银金件加工流程任何一个领金件来说,它都有一定的加工过程,也就是所谓的工艺流程.随着银金件结构的差异,工艺流程可能各不相同,但总的不超过以下几点.1 .设计并绘出其镀金件的零件图,又叫三视图.其作用是用图纸方式将其领金件的结构表达出来.2 .绘制展开图.也就是将一结构复杂的零件展开成一个平板件.3 .下料.下料的方式有很多种,主要有以下几种方式:a.剪床下料.是利用剪床剪出展开图的外形长宽尺寸.若有冲孔、切角的,再转冲床结合模具冲孔、切角成形.b.冲床下料.是利用冲床分一步或多步在板材上将零件展开后的平板件结构冲制成形.其优点是耗费工时短,效率高,可减少加工成本,在批量生产时经常用到.c.NC数控下料.NC下料时首先要编写数控加工程序.就是利用编程软件,将绘制的展开图编写成NC数控加工机床可识别的程序.让其跟据这些程序一步一步的在一块铁板上,将其平板件的结构形状冲制出来d.激光下料.是利用激光切割方式,在一块铁板上将其平板件的结构形状切割出来.4 .翻边攻丝.翻边又叫抽孔,就是在一个较小的基孔上抽成一个稍大的孔,再在抽孔上攻丝.这样做可增加其强度,避免滑牙.一般用于板厚比较薄的镀金加工.当板厚较大时,如2.0,2.5等以上的板厚,我们便可直接攻丝,无须翻边.5 .冲床加工.一般冲床加工的有冲孔切角、冲孔落料、冲凸包、冲撕裂、抽孔等加工方式,以达到加工目的.其加工需要有相应的模具来完成操作.冲凸包的有凸包模,冲撕裂的有撕裂成形模等.6 .压挪.压抑就本厂而言,经常用到的有压抑螺柱、压抑螺母、压钾螺钉等,其压钾方式一般通过冲床或液压压钾机来完成操作,将其钾接到领金件上.7 .折弯.折弯就是将2D的平板件,折成3D的零件.其加工需要有折床及相应的折弯模具来完成操作.它也有一定的折弯顺序,其原则是对下一刀不产生干涉的先折,会产生干涉的后折.8 .焊接.焊接就是将多个零件组焊在一起,达到加工的目的或是单个零件边建焊接,以增加其强度.其加工方一般有以下几种:C02气体保护焊、氮弧焊、点焊、机器人焊接等.这些焊接方式的选用是根据实际要求和材质而定.一般来说C02气体保护焊用于铁板类焊接;氢弧焊用于铝板类焊接;机器人焊接主要是在料件较大和焊SS较长时使用.如机柜类焊接,可采用机器人焊接,可节省很多任务时提高工作效率和焊接质量.9 .表面处理.表面处理T殳有磷化皮膜、电镀五彩锌、铭酸盐、烤漆、氧化等.磷化皮膜一般用于冷轧板和电解板类,其作用主要是在料件表上镀上一层保护膜,防止氧化;再来就是可增强其烤漆的附着力.电镀五彩锌一般用冷轧板类表面处理;铭酸盐、氧化一般用于铝板及铝型材类表面处理;其具体表面处理方式的选用,是根据客户的要求而定.10 .组装.所谓组装就是将多个零件或组件按照一定的方式组立在一起,使之成为一个完整的料品。
常见钣金件加工的工艺流程
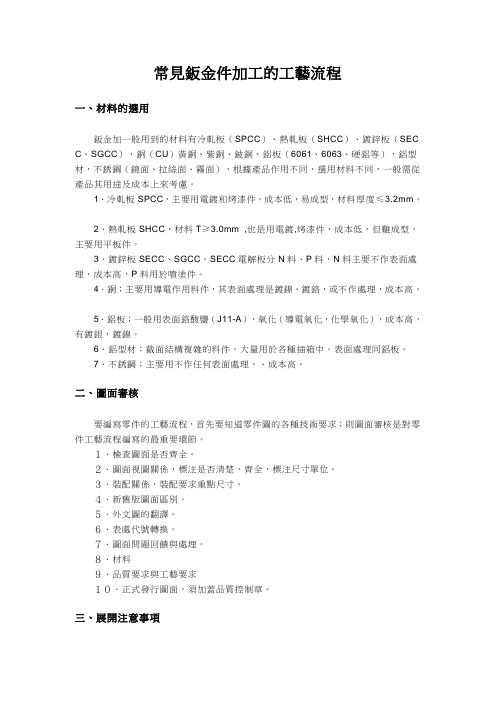
常見鈑金件加工的工藝流程一、材料的選用鈑金加一般用到的材料有冷軋板(SPCC)、熱軋板(SHCC)、鍍鋅板(SEC C、SGCC),銅(CU)黃銅、紫銅、鈹銅,鋁板(6061、6063、硬鋁等),鋁型材,不銹鋼(鏡面、拉絲面、霧面),根據產品作用不同,選用材料不同,一般需從產品其用途及成本上來考慮。
1.冷軋板SPCC,主要用電鍍和烤漆件,成本低,易成型,材料厚度≤3.2mm。
2.熱軋板SHCC,材料T≥3.0mm ,也是用電鍍,烤漆件,成本低,但難成型,主要用平板件。
3.鍍鋅板SECC、SGCC。
SECC電解板分N料、P料,N料主要不作表面處理,成本高,P料用於噴塗件。
4.銅;主要用導電作用料件,其表面處理是鍍鎳、鍍鉻,或不作處理,成本高。
5.鋁板;一般用表面鉻酸鹽(J11-A),氧化(導電氧化,化學氧化),成本高,有鍍銀,鍍鎳。
6.鋁型材;截面結構複雜的料件,大量用於各種插箱中。
表面處理同鋁板。
7.不銹鋼;主要用不作任何表面處理,、成本高。
二、圖面審核要編寫零件的工藝流程,首先要知道零件圖的各種技術要求;則圖面審核是對零件工藝流程編寫的最重要環節。
1.檢查圖面是否齊全。
2.圖面視圖關係,標注是否清楚,齊全,標注尺寸單位。
3.裝配關係,裝配要求重點尺寸。
4.新舊版圖面區別。
5.外文圖的翻譯。
6.表處代號轉換。
7.圖面問題回饋與處埋。
8.材料9.品質要求與工藝要求10.正式發行圖面,須加蓋品質控制章。
三、展開注意事項展開圖是依據零件圖(3D)展開的平面圖(2D)1.展開方式要合,要便利節省材料及加工性2.合理選擇問隙及包邊方式,T=2.0以下問隙0.2,T=2-3問隙0.5,包邊方式採用長邊包短邊(門板類)3.合理考慮公差外形尺寸:負差走到底,正差走一半;孔形尺寸:正差走到底,負差走一半。
4.毛刺方向5.抽牙、壓鉚、撕裂、沖凸點(包),等位置方向,畫出剖視圖6.核對材質,板厚,以板厚公差7.特殊角度,折彎角內半徑(一般R=0.5)要試折而定展開8.有易出錯(相似不對稱)的地方應重點提示9.尺寸較多的地方要加放大圖10.需噴塗保護地方須表示四、板金加工的工藝流程根據鈑金件結構的差異,工藝流程可各不相同,但總的不超過以下幾點。
钣金加工工艺流程图

钣金加工工艺流程1简介1.1简介按钣金件的基本加工方式,如下料、折弯、拉伸、成型、焊接。
本规阐述每一种加工方式所要注意的工艺要求。
1.2关键词钣金、下料、折弯、拉伸、成形、排样、最小弯曲半径、毛边、回弹、打死边、焊接2下料下料根据加工方式的不同,可分为普冲、数冲、剪床开料、激光切割、风割,由于加工方法的不同,下料的加工工艺性也有所不同。
钣金下料方式主要为数冲和激光切割2.1数冲是用数控冲床加工,板材厚度加工围为冷扎板、热扎板小于或等于3.0mm,铝板小于或等于4.0mm,不锈钢小于或等于2.0mm2.2冲孔有最小尺寸要求冲孔最小尺寸与孔的形状、材料机械性能和材料厚度有关。
图2.2.1 冲孔形状示例材料圆孔直径b 矩形孔短边宽b高碳钢 1.3t 1.0t低碳钢、黄铜 1.0t 0.7t铝0.8t 0.5t* 高碳钢、低碳钢对应的公司常用材料牌号列表见第7章附录A。
表1冲孔最小尺寸列表2.3数冲的孔间距与孔边距零件的冲孔边缘离外形的最小距离随零件与孔的形状不同有一定的限制,见图2.3.1。
当冲孔边缘与零件外形边缘不平行时,该最小距离应不小于材料厚度t;平行时,应不小于1.5t。
(图1.4)图2.3.1 冲裁件孔边距、孔间距示意图2.4折弯件与拉深件冲孔时,其孔壁与直壁之间应保持一定的距离折弯件或拉深件冲孔时,其孔壁与工件直壁之间应保持一定的距离(图2.4.1)图2.4.1 折弯件、拉伸件孔壁与工件直壁间的距离2.5螺钉、螺栓的过孔和沉头座螺钉、螺栓过孔和沉头座的结构尺寸按下表选取取。
对于沉头螺钉的沉头座,如果板材太薄难以同时保证过孔d2和沉孔D,应优先保证过孔d2。
表2用于螺钉、螺栓的过孔*要求钣材厚度t≥h。
表3用于沉头螺钉的沉头座与过孔*要求钣材厚度t≥h。
表4用于沉头铆钉的沉头座与过孔2.6激光切割是用激光机飞行切割加工,板材厚度加工围为冷扎板热扎板小于或等于20.0mm, 不锈钢小于10.0mm 。
钣金车间生产流程图
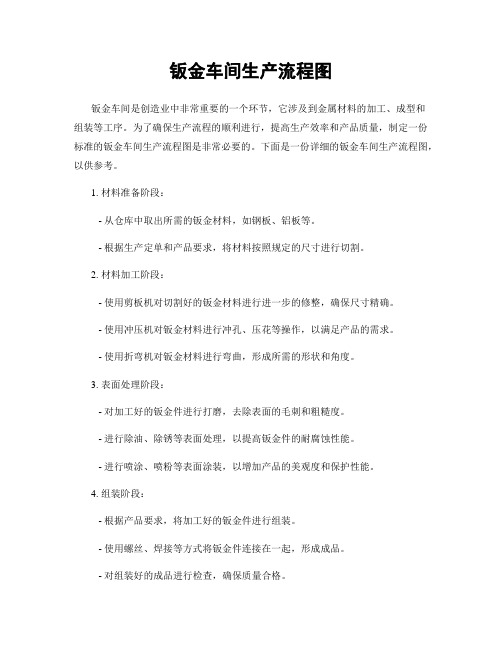
钣金车间生产流程图钣金车间是创造业中非常重要的一个环节,它涉及到金属材料的加工、成型和组装等工序。
为了确保生产流程的顺利进行,提高生产效率和产品质量,制定一份标准的钣金车间生产流程图是非常必要的。
下面是一份详细的钣金车间生产流程图,以供参考。
1. 材料准备阶段:- 从仓库中取出所需的钣金材料,如钢板、铝板等。
- 根据生产定单和产品要求,将材料按照规定的尺寸进行切割。
2. 材料加工阶段:- 使用剪板机对切割好的钣金材料进行进一步的修整,确保尺寸精确。
- 使用冲压机对钣金材料进行冲孔、压花等操作,以满足产品的需求。
- 使用折弯机对钣金材料进行弯曲,形成所需的形状和角度。
3. 表面处理阶段:- 对加工好的钣金件进行打磨,去除表面的毛刺和粗糙度。
- 进行除油、除锈等表面处理,以提高钣金件的耐腐蚀性能。
- 进行喷涂、喷粉等表面涂装,以增加产品的美观度和保护性能。
4. 组装阶段:- 根据产品要求,将加工好的钣金件进行组装。
- 使用螺丝、焊接等方式将钣金件连接在一起,形成成品。
- 对组装好的成品进行检查,确保质量合格。
5. 质检阶段:- 对成品进行全面的质量检测,包括尺寸、外观、功能等方面。
- 对不合格的产品进行修复或者重新制作,确保产品达到标准要求。
6. 包装和出库阶段:- 对合格的成品进行包装,以保护产品在运输和储存过程中的安全。
- 将包装好的成品进行入库,并进行相应的记录和标识。
- 根据定单要求,将成品出库,准备发货。
以上是一份标准的钣金车间生产流程图,其中涵盖了材料准备、材料加工、表面处理、组装、质检以及包装和出库等关键环节。
通过严格按照这个流程进行生产,可以确保产品的质量和交货期的准时性。
固然,具体的生产流程还需要根据实际情况进行调整和优化,以适应不同产品和生产规模的需求。
钣金外壳工艺流程

钣金外壳工艺流程钣金外壳工艺流程是指在钣金部件的生产过程中,通过一系列的工艺步骤,将原材料加工成最终的外壳产品。
以下是一个典型的钣金外壳工艺流程。
第一步:材料准备钣金外壳的材料通常是金属薄板,如不锈钢、铝合金等。
在开始生产之前,首先需要对材料进行准备,包括切割、拉直、折弯等。
第二步:模具制作根据产品的要求和设计图纸,制作相应的模具。
模具可以分为压力模具和冲裁模具,用于将金属薄板加工成所需形状。
第三步:冲压将金属薄板放置在冲床上,利用冲床的冲裁模具进行冲压加工。
冲压过程中,通过对薄板进行切割、拉伸等操作,将其加工成所需的外壳形状。
第四步:折弯将冲压好的外壳进行折弯加工,使其获得所需的弯曲形状。
折弯通常使用折弯机进行,可以根据产品图纸上的要求进行精确的折弯角度。
第五步:焊接将折弯好的外壳进行组装焊接。
焊接可以采用手工焊接、气焊或激光焊接等方式进行,确保外壳的接缝牢固、密封。
第六步:表面处理对焊接好的外壳进行表面处理,以保护其外观和耐腐蚀性能。
常见的表面处理方法包括喷涂、电泳、阳极氧化等。
第七步:成品检验对成品外壳进行严格的质量检验,包括外观检查、尺寸测量、强度测试等。
确保外壳符合设计要求和客户的需求。
第八步:包装与发货将符合检验要求的成品外壳进行包装,通常采用纸箱、木箱等包装材料。
然后安排发货,将成品外壳送至客户指定的地点。
综上所述,钣金外壳加工的工艺流程包括材料准备、模具制作、冲压、折弯、焊接、表面处理、成品检验和包装发货等多个步骤。
通过这些工艺流程,可以生产出高质量的钣金外壳产品,满足不同领域的使用需求。
钣金制作流程分解

钣金制作流程分解下载温馨提示:该文档是我店铺精心编制而成,希望大家下载以后,能够帮助大家解决实际的问题。
文档下载后可定制随意修改,请根据实际需要进行相应的调整和使用,谢谢!并且,本店铺为大家提供各种各样类型的实用资料,如教育随笔、日记赏析、句子摘抄、古诗大全、经典美文、话题作文、工作总结、词语解析、文案摘录、其他资料等等,如想了解不同资料格式和写法,敬请关注!Download tips: This document is carefully compiled by the editor. I hope that after you download them, they can help yousolve practical problems. The document can be customized and modified after downloading, please adjust and use it according to actual needs, thank you!In addition, our shop provides you with various types of practical materials, such as educational essays, diary appreciation, sentence excerpts, ancient poems, classic articles, topic composition, work summary, word parsing, copy excerpts,other materials and so on, want to know different data formats and writing methods, please pay attention!钣金加工是一种常见的金属加工方法,广泛应用于汽车制造、航空航天、电子设备等领域。
钣金加工工艺流程(Sheetmetalprocessingflowchart)

钣金加工工艺流程(Sheet metal processing flow chart)Sheet metal processing flow chartWith the development of society, the sheet metal industry also developed rapidly, now metal related to all walks of life, for any of a sheet metal, it has a certain process, the so-called process, to understand the process of sheet metal processing, we must first know the sheet metal materials.A,The selection of materials, sheet metal with cold rolled plate generally used materials (SPCC), hot-rolled plate, galvanized plate (SHCC) (SECC, SGCC), copper (CU) brass, copper, beryllium copper, aluminum (6061, 6063, etc.), aluminum, stainless steel (wire drawing, mirror, fog) the effect of different products, according to the selection of materials, different from general products and cost up to consider its use.1. cold rolled plate SPCC, mainly used in electroplating and paint, low cost, easy molding, material thickness is less than 3.2mm.2. hot rolled plate material SHCC, T =3.0mm, is also used in electroplating, paint, low cost, but difficult to molding, mainly for flat pieces.3. galvanized sheet SECC, SGCC. SECC electrolytic plate is divided into N material, P material, N material, mainly not for surface treatment, high cost, P material used for spraying parts.4. copper; the main use of conductive materials, the surface treatment is nickel plated, chrome plated, or do not deal with, the cost is high.5. aluminum plate; generally used surface chromate (J11-A), oxidation (conductive oxidation, chemical oxidation), high cost, with silver plated, nickel plated.6. aluminum profiles, complex structures and materials, are widely used in various boxes. Surface treatment with aluminum sheet.7. stainless steel; mainly used without any surface treatment,High cost.Two,In order to prepare the parts' technological process, the first step is to know the technical requirements of the parts drawing. Then, the audit of the drawings is the most important part of the part's technological process.1. check whether the surface is complete.2., the diagram view relations, whether the mark is clear, complete, dimensioning unit.3. assembly relations, assembly requirements, key dimensions.4., the old and new boundaries are different.5. foreign language translation.6. table name conversion.7. feedback and embedding of face problem.8. materials9. quality requirements and process requirements10. the official release shall be stamped with a quality control sheet.Three. Draw attention to the development of the plan, which is based on the 2D (3D)1., the expansion should be combined, it is convenient to save materials and processing2., reasonable choice gap and hemming way, T=2.0 following gap 0.2, T=2-3 ask gap 0.5, wrapping method adopts long side bag short side (door panel type)3., reasonable consideration of tolerance, shape size: negative difference to the end, the difference is half, hole shape size: positive difference in the end, half of the negative difference.4. burr directionFiveDraw the cutaway view of the tooth, press, rivet, tear, punch point (bag), position and so on6. check material, plate thickness, to plate thickness tolerance7., special angle, bend angle inside radius (general R=0.5) must try to fold, and must start8., there is error prone (similar asymmetry) should focus on the tip9., more places to enlarge the big picture10. where spraying is required, the protection shall be indicatedFour process, sheet metal processing, according to the difference of sheet metal, the process may vary, but generally does not exceed the following points.1, blanking: blanking method has a variety of, mainly in the following ways1. Shears: shears shear strip has the advantages of simple materials, it is mainly for the mold blanking forming preparation process, low cost, accuracy is less than 0.2, the strip or block but can only be processed without orifice cuttingangle.2. Punch: the use of punch plate parts are divided one or more steps in the blanking plate on parts forming materials of various shapes, the utility model has the advantages of cost of short working hours, high efficiency, high precision, low cost, suitable for mass production, but to design the mold.The.NC NC material, NC material under the first to write CNC machining program, using the programming software, the expansion plan will be drawn into the preparation of NC number of pull machine can identify the program, so that under these programs step in the flat knife shape plate blanking,But its structure is limited by the tool structure and the precision is 0.15.4. Laser cutting, is the use of laser cutting, cutting out the shape of the large flat, the flat, with the NC material to be prepared the same CD program, flat, it can lower the complex shape of the high cost and precision in 0.1.Sawing machine: the main used aluminum profiles, square tubes, tubes, round bars, etc., low cost, low accuracy.1. fitter: countersunk, tapping, reaming, drillingSink hole angles of 120 DEG C, for rivet, 90 DEG C for countersunk head screws, tapping the bottom inch.2. flange: also called smoke hole, through hole, holes in thebase is a small pump into a larger hole, then tapping, mainly used in thick sheet metal processing relatively thin, increasing its strength and number of threads, to avoid slipping, generally used for plate thickness is thin, the hole of Zhou Zhengchang shallow flanging, thickness did not change, allowing a thickness of 30-40%, high high 40-60% level than normal flanging, squeeze 50% thin, can get maximum flanging height, when the plate thickness is large, such as 2, 2.5 above the plate thickness, can be directly tapping.3.: punch mold forming manufacturing processes, general punch processing punching, blanking, cutting, convex hull (bumps), red tear, smoke hole, forming and other processing methods, processing needs corresponding mold to complete the operation, such as punching, blanking die, die bulge and tear die, die, drawing hole forming mold,The operation mainly pays attention to position and direction.4. pressure riveting: pressure riveting of the company, the main pressure riveting nut, screw loose, etc., it is through the hydraulic pressure riveting machine or punch to complete the operation, the riveted to the sheet metal, and rivet, should pay attention to the direction of.5. bending; bending is the 2D flat parts, folding D parts successfully. The processing needs of folding bed and a corresponding bending mold, it also has some bending sequence, the principle is the a first folding knife does not produce interference, will produce interference after folding.L the number of bending bars is 6 times lower than T=3.0mm, and the width of plate thickness is calculated, such as: T=1.0, V=6,.0, F=1.8, T=1.2, V=8, F=2.2, T=1.5, V=10, F=2.7, T=2.0, V=12,F=4.0L bending mold classification, straight knife, machete (80 C and 30 C)L aluminum plate bending, cracks, can increase the die width increase slot mold R (annealing can avoid cracking)L bending attention: 1. Drawing surface, request thickness of plate, quantity; second, bend directionBending angle: 4. Bending size; appearance of chromium plated parts can not be creased.Bending and riveting process, under normal circumstances, first pressure riveting, bending, but there are parts of the pressure riveting will interfere, it is necessary to first fold, after pressure, and some need to bend - pressure riveting - re bending process.6. welding: welding: welding material is formed integrally define atomic and molecular lattice distance from BeijingClassification: a melting welding: argon arc welding, CO2 welding, gas welding, hand weldingB pressure welding: spot welding, butt welding, butt weldingC brazing: Electric chromium welding, copper wireWelding method: A, CO2 gas shielded weldingB argon arc weldingC point welding, etc.D robot weldingWelding method is selected according to the actual requirements and material, generally CO2 gas shielded welding for welding iron making; TIG welding for stainless steel, aluminum welding, welding robot, can save time, improve work efficiency and welding quality, reduce the work intensity.The welding symbol: Delta angle welding part, I welding, V welding, single V welding (V) welding with edge type V (V), (O), spot welding plug welding slot welding or welding (II), edge (x), with a blunt edge (unilateral V type welding V), type U with the blunt welding, J welding, with a blunt back sealing welding, when weldingArrow and jointWelding defects and preventive measuresSpot welding: not enough strength, can bump bump, impose welding areaCO2 welding: high productivity, low energy consumption, low cost, strong rust resistanceArgon arc welding: it has the advantages of deep dissolving, slow dissolving speed, low efficiency, high production cost and the defects of tungsten inclusion. But it has the advantages of better welding quality. It can weld non-ferrous metals such as aluminum, copper, magnesium and so on.The causes of welding deformation: before welding is insufficient, need to increase the fixtureWelding jig bad improvement processThe welding order is badThe effect of welding deformation method: flame effect methodVibration methodHammerArtificial aging methodPhosphating - drying - Spray - drying, this is a common metal shell process.For sheet metal parts, the general can be used electroplatingor electrolysis, oxidation, such as anodizing can be made of gold, yellow and so on. Plating electrophoresis paint is mainly for conducting, in many occasions for electromagnetic shielding; painting and powder: paint the surface thickness is smaller, generally less than 10 mu m, and sand grain powder fixation should be slightly thicker, but compared with painting, color and texture to a stroke above.In less demanding situations, as long as do internal sheet metal electroplating antirust can, ^_^. If the internal parts of color requirements are considered oxidation, the outside parts should be selected to spray better.。
钣金生产工艺流程
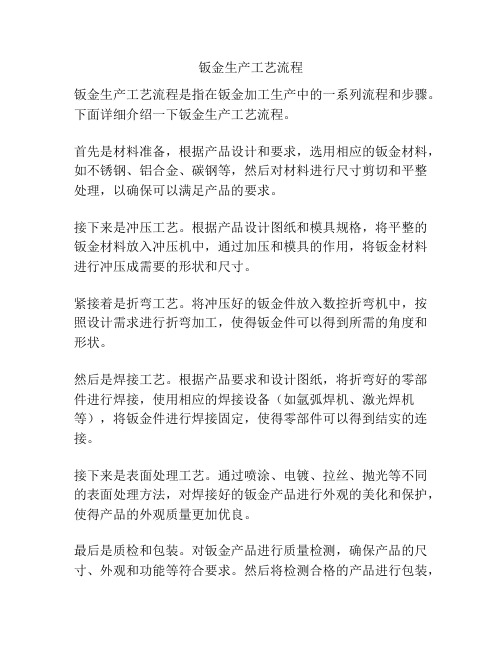
钣金生产工艺流程
钣金生产工艺流程是指在钣金加工生产中的一系列流程和步骤。
下面详细介绍一下钣金生产工艺流程。
首先是材料准备,根据产品设计和要求,选用相应的钣金材料,如不锈钢、铝合金、碳钢等,然后对材料进行尺寸剪切和平整处理,以确保可以满足产品的要求。
接下来是冲压工艺。
根据产品设计图纸和模具规格,将平整的钣金材料放入冲压机中,通过加压和模具的作用,将钣金材料进行冲压成需要的形状和尺寸。
紧接着是折弯工艺。
将冲压好的钣金件放入数控折弯机中,按照设计需求进行折弯加工,使得钣金件可以得到所需的角度和形状。
然后是焊接工艺。
根据产品要求和设计图纸,将折弯好的零部件进行焊接,使用相应的焊接设备(如氩弧焊机、激光焊机等),将钣金件进行焊接固定,使得零部件可以得到结实的连接。
接下来是表面处理工艺。
通过喷涂、电镀、拉丝、抛光等不同的表面处理方法,对焊接好的钣金产品进行外观的美化和保护,使得产品的外观质量更加优良。
最后是质检和包装。
对钣金产品进行质量检测,确保产品的尺寸、外观和功能等符合要求。
然后将检测合格的产品进行包装,
并进行入库标识,以便于存储和出货。
以上就是钣金生产工艺流程的主要环节和步骤。
不同产品和要求可能会有略微差异,但整体的钣金生产过程基本相似。
在整个生产过程中,需要严格按照工艺流程要求进行操作,确保产品的质量和效率。
- 1、下载文档前请自行甄别文档内容的完整性,平台不提供额外的编辑、内容补充、找答案等附加服务。
- 2、"仅部分预览"的文档,不可在线预览部分如存在完整性等问题,可反馈申请退款(可完整预览的文档不适用该条件!)。
- 3、如文档侵犯您的权益,请联系客服反馈,我们会尽快为您处理(人工客服工作时间:9:00-18:30)。
JASIC(佳士)气保焊机(二氧化碳)
Panasonic交直流两用氩弧焊机
2.焊接材料类型:ER70S(低合金钢焊丝)、 ER308(不锈钢焊丝)、ER5356/ER5183(铝镁焊 丝)、ER1100(纯铝焊丝)、ER4043/ER4047(铝 硅焊丝)
PLATEING PROCESS MAPPING
AMADA RG35
AMADA RG50
AMADA RG80
AMADA RG100
AMADA RG120
2.折弯模具以及设置参数的选择
HARDWARE工艺说明
紧固件使用的设备:HAEGER和金诺压铆机
WELD工艺说明
1.焊接使用的设备:MILLER交直流两用氩弧 碳钢、不锈钢 焊机。注:交流 直流 铝合金
Process Mapping
Raw Material Incoming Inspection
Shear
Turret
Deburr
Laser
Brake
Packing
Ship
Hardware
Final Inspection
Weld
Assembly
Silkscreen
Incoming Inspection
三角拉丝机器
手动角磨机
手磨机
BRAKE工艺说明
1.冲床使用的设备: AMADA RG35 机器压力:35TONS 最大行程:380X800MM AMADA RG50 机器压力:50TONS 最大行程: 380X800MM AMADA RG60 机器压力:60TONS 最大行程: 380X800MM AMADA RG80 机器压力:80TONS 最大行程: 380X800MM AMADA RG100 机器压力:100TONS 最大行程: 380X800MM AMADA RG120 机器压力:120TONS 最大行程: 380X800MM
进料检验 上挂具 化学除油 水洗 水洗
水洗
出光
水洗
钝化
酸洗
水洗 冷却/成品检验
发货 包装
水洗
水洗
镀锌
纯水洗
水洗
中和
下挂
烤干
热纯水洗
电解除油
水洗
水洗
活化
水洗
水洗
PAINTING PROCESS MAPPING
进料检验
上挂 脱脂 水洗
下挂
冷却/成品检验
包装
中和
烘烤 发货
水洗
喷粉
表调
上挂
防烤
表面处理
磷化
Out Sourcing Paint#/ Plate#/
原材料放置区域以及标明信息
Shear工艺说明
1.剪板使用的设备:AMADA剪板机
2.剪板操作人员需要根据工作包注明的信息 选择材料
TUR工艺说明
1.冲床使用的设备: AMADA EM2510NT 冲压压力:20TONS 最大行程:98.425X50.00INCH AMADA PEGA345 冲压压力:30TONS 最大行程:50X39.37INCH AMADA VIPROS368冲压压力:30TONS 最大行程:78.74X60INCH 操作系统:FANUC系统
AMADA EM2510NT
AMADA PEGA345
AMADA VIPROS368
2.冲床的关键尺寸控制
LASER工艺说明
1.激光切割使用设备:FINN-POWER LASER
2.激光切割过程图
LASER 使用的气体
ser关键尺寸控制
DEBURR工艺说明
1.DEBURR使用的设备 自动拉丝机器
Silkscreen 工艺说明