TPM 1STEP 手册教材
合集下载
TPM 1STEP 手册教材解析
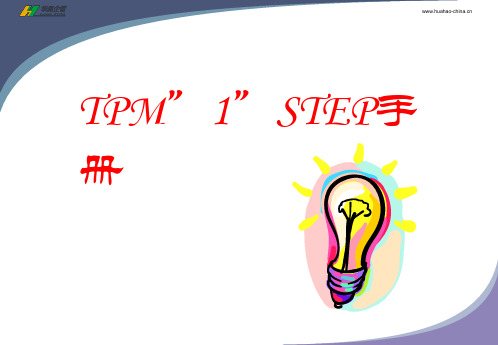
一.什么是TPM活动?
1)定义: 1.在制造企业里以制造部门为主进行的灾害、浪费、不良 、故障为“0”的活动。
2.以主人的身份对我的设备、我的工程进行保护、维持和 管理,来实现生产的最佳状态。 2)目的: 1.自己的设备自己来维护。 2.追求设备的最佳状态。 3.成为熟练的设备运转人员。 4.形成能够发现异常的现场。
遵守基本条件
早期发现异常防止故障的发生 以记录保全DATA来防止再发生
第2阶段(测定劣化的活动):4~5STEP
日常检查(运转的五官检查,巡视) 定期检查,定期更换
第3阶段(劣化复原活动):6~7STEP
实施小维护(异常时的应急处理,更换简单的部件) 故障异常发生时迅速正确的联络 修理突发性故障时,可以进行支援 设定良品条件及管理条件
活动的变化 积极参与改善 彻底维持管理
1. 理解现场革新的基本为什 么是 5S ? 2. 思考设备为什么发生强制 劣化? 3.为什么要做自主保全? 4. 推进 1 阶段以上时理解安 全行动的重要性3
1.改善问题点 2.清扫就是点检 3.点检就是发现问题( 包括疑问点、缺陷、发 生源、困难源) 4.问题点复原改善 5.提高:问题点发现能 力;改善方向设定能力
“清扫是检查”
3)TPM 展开的思维模式:
0STEP (事前准备) TPM活动 阶段开展 思考方式 赋 予 动 机 1STEP 2STEP 3STEP 改 变 设 备 效果: 不良减少 故障减少 4STEP 5STEP 人 变 化 思考的变化 故障、不良是 现场的羞耻 效果 达成故障 不 良 的 “0”化 6STEP 7STEP 现场发生 变化
活动实施
以清扫的手段摸 一摸设备的每个 角落 发现劣化不合理 体会清扫困难源 察觉灰尘污染发生源 正常?异常? 劣化不合理LIST 困难源LIST 发生源LIST 疑问点LIST 潜 在 缺 陷 的 暴 露
TPM-1(全员保全)教材
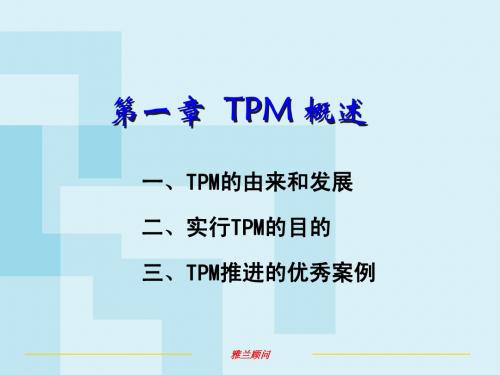
雅兰顾问
1.2 TPM 的内涵
TPM
TOTAL PRODUCTIVE MAINTENANCE
TPM 全员生产维修(保全)
TPM大行动, 时间空间全系统,
M – MAINTENANCE 维修(保全)
设备维护体系的健全
企业经营系统的健全
设备管理靠全员,
效率提高才成功。
-- 实现设备状态最佳管理体系完善
1.1 TPM的历史
全员生产保全TPM
生产保全
自主保全
重点改善 教育培训
MP 维修预防
(美式-设备部门)
雅兰顾问
(日式-全员参与)
1.2 TPM 的内涵
TPM
TOTAL PRODUCTIVE MAINTENANCE
TPM 全员生产维修(保全)
T - TOTAL 综合性
• 追求企业综合效率提高
TPM管理
(设备综合效率 ) ( 自主保全 ( )
计划检修
项目修理
预防维修 ) )
( 团队改善
定人定机
监督检查
(
一人多能 ) )
( 教育培训
部门管理
前期管理
雅兰顾问
( 高层推动
)
( 初期管理 )
TPM的新发展
随时间推移40年来TPM活动规模扩大
营业
降低 3.4倍
• 劳动生产率提高 50%!
1993年 1990年
1082次
1990年
1993年
雅兰顾问
三、TPM活动的优秀案例
上海宝山钢铁集团、 青岛海信集团 上海光明乳业、
天津汽车发动机有限公司、
辽宁鞍钢集团、
青岛海尔集团、
1.2 TPM 的内涵
TPM
TOTAL PRODUCTIVE MAINTENANCE
TPM 全员生产维修(保全)
TPM大行动, 时间空间全系统,
M – MAINTENANCE 维修(保全)
设备维护体系的健全
企业经营系统的健全
设备管理靠全员,
效率提高才成功。
-- 实现设备状态最佳管理体系完善
1.1 TPM的历史
全员生产保全TPM
生产保全
自主保全
重点改善 教育培训
MP 维修预防
(美式-设备部门)
雅兰顾问
(日式-全员参与)
1.2 TPM 的内涵
TPM
TOTAL PRODUCTIVE MAINTENANCE
TPM 全员生产维修(保全)
T - TOTAL 综合性
• 追求企业综合效率提高
TPM管理
(设备综合效率 ) ( 自主保全 ( )
计划检修
项目修理
预防维修 ) )
( 团队改善
定人定机
监督检查
(
一人多能 ) )
( 教育培训
部门管理
前期管理
雅兰顾问
( 高层推动
)
( 初期管理 )
TPM的新发展
随时间推移40年来TPM活动规模扩大
营业
降低 3.4倍
• 劳动生产率提高 50%!
1993年 1990年
1082次
1990年
1993年
雅兰顾问
三、TPM活动的优秀案例
上海宝山钢铁集团、 青岛海信集团 上海光明乳业、
天津汽车发动机有限公司、
辽宁鞍钢集团、
青岛海尔集团、
2024年TPM(一级)教材课件
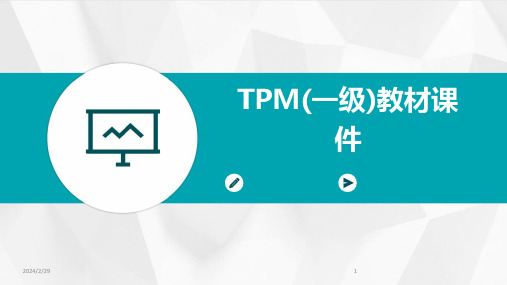
2024/2/29
25
能源计量、监测和报告制度建立
01
能源计量体系建设
完善能源计量器具的配备和管理 ,确保能源计量数据的准确性和 可靠性。
02
能源监测平台建设
03
定期报告制度
建立能源监测平台,实现对企业 能源消耗情况的实时监测和数据 分析。
建立定期报告制度,及时向上级 主管部门报送能源消耗和节能工 作进展情况。
02
分析现有工艺流程,找出瓶颈环节和浪费现象,通过工艺改进
、设备升级等手段提高生产效率。
生产线设计
03
根据产品特性和市场需求,设计高效的生产线,实现生产过程
的连续化、自动化和智能化。
14
工作环境改善与员工素质提升
工作环境改善
优化生产现场的照明、通风、温 度等环境因素,提供舒适的工作 环境,减少员工疲劳和不良品率 。
低污染物排放对环境的影响。
2024/2/29
27
06
信息化技术在TPM中的应用
2024/2/29
28
信息化技术在设备管理中的应用
2024/2/29
设备状态监测与故障诊断
利用传感器和数据分析技术,实时监测设备状态,预测并诊断故障 ,提高设备运行稳定性和可靠性。
设备维修管理
通过信息化手段,建立设备维修档案,实现维修计划、维修过程、 维修结果的全程管理,提高维修效率和质量。
2024/2/29
11
设备预防性维护与保养措施
01 预防性维护
制定设备预防性维护计划,定期对设备进行检查 、清洁、润滑、调整等维护工作,延长设备使用 寿命,减少故障发生。
02 保养措施
根据设备的特点和使用情况,制定相应的保养措 施,如定期更换易损件、清洗油路、校准传感器 等,确保设备的正常运行。
TPM教材 (1)

B C D E
13.测定、调整损失
第一投入工时的良品数 《能源》
经过时间相对的良品数 《材料》
5.短暂停机、空转损失
6.速度降低损失 暧机损失
超负荷损失
投入能源 14.暧机 损失 有效能源
投入材料(个数、重量) 良品个数 良品重量
7.不良、人工修整损失
不良损失 暧机损失
头 改尾 料 损失
放热损失
15.模具、治工具损失
重量的损失
宽裕太多的损失
16 成 品 率 损 失
原材料的效率化…阻碍原材料效率化的3大损失
26
综合设备效率计算(OEE)
1
综合设备效率=设备利用率 人工效率 合格品率 OEE=Availability Performance efficiency Quality rate
27
使用率计算
12
事后维ห้องสมุดไป่ตู้(B.M.)
事后维护(Breakdown Maintenance-B.M.) 适应于 故障后再行修理较为经济的情况,通常适用于不 影响生产的设备。
13
纠正维护(C.M.)
纠 正 维 护 (Corrective Maintenance-C.M.) 即 设 备本质的改善,以提高设备的可靠性和可维护性; 换句话说,延长设备寿命,采用无故障、无维护 麻烦的材料及备品等改良维护保养。
22
我们的任务是预防停机
接 受 新 的 思 维 方 法 (Adopt a new way of thinking) 做到每日的常规点检使设备总是处于最好的运行 状 态 (Develop a daily routine for keeping equipment in top operating condition) 监 视 轻 微 的 异 常 现 象 (Watch for slight abnormalities)
TPM1STEP手册教材
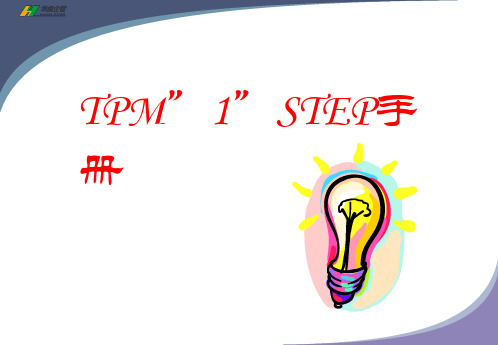
第2阶段(测定劣化的活动):4~5STEP
✓日常检查(运转的五官检查,巡视) ✓定期检查,定期更换
第3阶段(劣化复原活动):6~7STEP
✓实施小维护(异常时的应急处理,更换简单的部件) ✓故障异常发生时迅速正确的联络 ✓修理突发性故障时,可以进行支援 ✓设定良品条件及管理条件
5)TPM 7 STEP:
“清扫是检查”
3)TPM 展开的思维模式:
0STEP (事前准备)
1STEP 2STEP 3STEP
TPM活动
赋
改
阶段开展
予
变
思考方式
动
设
机
备
效果: 不良减少 故障减少
4STEP 5STEP
人 变 化
思考的变化 故障、不良是 现场的羞耻
效果 达成故障 不良的 “0”化
活动的变化 积极参与改善 彻底维持管理
一.什么是TPM活动?
1)定义: ➢1.在制造企业里以制造部门为主进行的灾害、浪费、不良 、故障为“0”的活动。 ➢2.以主人的身份对我的设备、我的工程进行保护、维持和 管理,来实现生产的最佳状态。
2)目的: ➢1.自己的设备自己来维护。 ➢2.追求设备的最佳状态。 ➢3.成为熟练的设备运转人员。 ➢4.形成能够发现异常的现场。
目标 彻底去除影响或阻碍设备或产品机能的一切潜在微缺陷,即微缺陷0化。 彻底清扫设备的每一个角落,并考虑怎样才能舒适、简便、快捷的清扫。
活动准备
1)2)TPM 1 STEP活动流程:
✓理解怎样开展1STEP活动 ✓树立1STEP活动计划 ✓决定设备的责任人 ✓理解设备的结构与性能 ✓理解各部位的检查要点 ✓进行安全教育,制定安全检查单(运转中及停止 中)
TPM自主保全与1STEP实战讲义
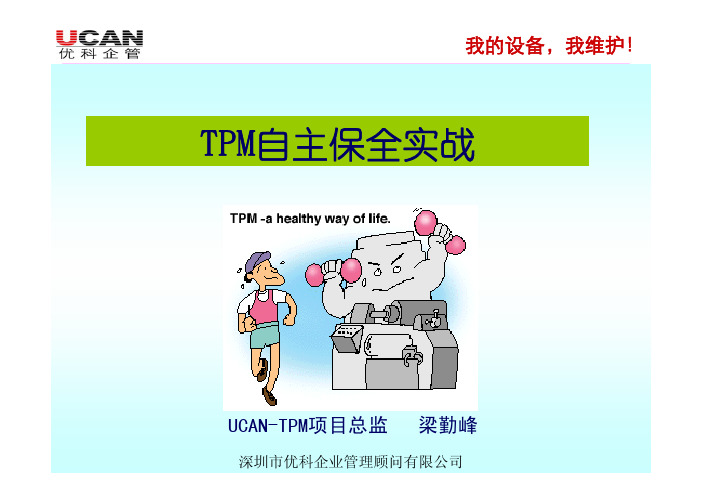
进入下一阶段
我的设备,我维护!
自 主 保全 活 动 的 手段及目的
手段
正确的操作 日常点检 劣化的复原 基本条件满足 维护技能教育 小组活动
目的
防止劣化的活动 实现设备的最佳状态
自主管理
我的设备,我维护!
自主保全推行的基本思路
①清扫就是点检---观念变了! (不是单纯的清扫,是以要发现不合理 情况的心态进行清扫) ②点检就是发现不合理状态---行为变了!
“要点培训”
是指把一个项目在一张纸上进行整理后,以小组成员为对象进行5~10分钟的教育,解除 疑问点的教育方法。主要以疑问点为中心进行教育。
① 基础知识 : 设备、机器的结构和名称、点检分解方法、处理方法等的基础知识内容
② 改善事例 : 扩散适用其他工程的改善事例、自己工程的改善事例
③ 事故事例 : 为了传播其他工程的品质事故事例、故障事例、灾害事例等使用。
婴儿(设备) 母亲(操作工)= 自主保全 医生(维修工)= 专业保全
我们的目 标是婴儿 健康成长
维修人员 (计划保全)
设备
我们的目标 是设备高效
运行
操作员 (自主保全)
AM的益处1
我的设备,我维护!
Î增加设备的可靠性和效率
延长设备寿命
提高设备效率
AM的益处2
Î更好的工作环境
更好的工作环境
我的设备,我维护! 大自然会对你说谢谢
之后张贴在看板上; •第二天,抽人问一问,问前几次中的一个,每天早间会;
我的设备,我维护!
基础知识 OPL (事例)
工作表分类 基础知识(设备技术)
课题
离心泵的清扫点检POINT
小组名 (图解)
进行步骤 说明
我的设备,我维护!
自 主 保全 活 动 的 手段及目的
手段
正确的操作 日常点检 劣化的复原 基本条件满足 维护技能教育 小组活动
目的
防止劣化的活动 实现设备的最佳状态
自主管理
我的设备,我维护!
自主保全推行的基本思路
①清扫就是点检---观念变了! (不是单纯的清扫,是以要发现不合理 情况的心态进行清扫) ②点检就是发现不合理状态---行为变了!
“要点培训”
是指把一个项目在一张纸上进行整理后,以小组成员为对象进行5~10分钟的教育,解除 疑问点的教育方法。主要以疑问点为中心进行教育。
① 基础知识 : 设备、机器的结构和名称、点检分解方法、处理方法等的基础知识内容
② 改善事例 : 扩散适用其他工程的改善事例、自己工程的改善事例
③ 事故事例 : 为了传播其他工程的品质事故事例、故障事例、灾害事例等使用。
婴儿(设备) 母亲(操作工)= 自主保全 医生(维修工)= 专业保全
我们的目 标是婴儿 健康成长
维修人员 (计划保全)
设备
我们的目标 是设备高效
运行
操作员 (自主保全)
AM的益处1
我的设备,我维护!
Î增加设备的可靠性和效率
延长设备寿命
提高设备效率
AM的益处2
Î更好的工作环境
更好的工作环境
我的设备,我维护! 大自然会对你说谢谢
之后张贴在看板上; •第二天,抽人问一问,问前几次中的一个,每天早间会;
我的设备,我维护!
基础知识 OPL (事例)
工作表分类 基础知识(设备技术)
课题
离心泵的清扫点检POINT
小组名 (图解)
进行步骤 说明
TPM Manual
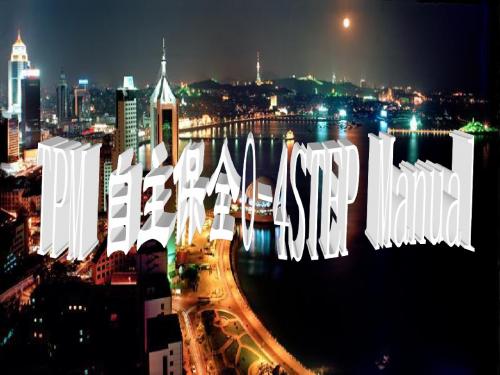
21/61
不合理分类
区 分 不 安 全 部 位 定义 对人产生危害 或有潜在危害 的部位 重点 内容 disc (圆盘) 裁断 照明 旋转物 起重机 移载机 不 合 理 详 细 事 项 凹凸、石柱、损伤、破损、磨损 急倾斜、扭曲、防滑条的脱落、腐蚀、手把 亮度不够、位置不良、罩子污染、保护设施等 破损、防暴不适合 保护罩脱落、露出、并联安全装置、紧急刹车 吊车、起重机类的钢绳、挂构、刹车等 特殊物品、溶剂、有毒气体、隔热材料、危险 标示、保护工具 备注
8/61
1.整理(Seiri) :不必要品与必要品分开,不必要品处理 ※ 彻底去除不必要品,消除空间和管理浪费
整理要领:
1次/月以上 1次/3月以上 1次/年以上 1次/年都不使用 放在作业区 工程或部门仓库 部门仓库 退还.返还
超过保管期
无法使用
废弃
废弃.返还
9/61
2.整顿(Seiton) :必要品容易取拿且使用方便 (防止必要品过剩与不足,便于存取)
18/61
6.不合理查找方法
◇五感:视觉.听觉.触觉.嗅觉.味+感觉 眼、 耳、 手、 鼻、 口 ◇专业知识(理论加实践)
不合理分类
区 分 定义 重点 内容
确定 基准 物品 分类
定品 定位 定量 可视化
不合理 详细事项
无法判断物品的种类及数量 过期品、过量品、废品,缩小、剪短、不必要 动作行为、多余的程序 没有明确标示品名 没有指定明确的原位置 没有标示出最大、最小量、订货点、在库量 人、机、物状态不能一目了然
② 情报共享.
③ 自我展示 物:活动的对象. 三现:现场.现物.现象 人:活动主体
5/61
七.TPM八大支柱
T P M 灾害.故障.不良.浪费“0”化
不合理分类
区 分 不 安 全 部 位 定义 对人产生危害 或有潜在危害 的部位 重点 内容 disc (圆盘) 裁断 照明 旋转物 起重机 移载机 不 合 理 详 细 事 项 凹凸、石柱、损伤、破损、磨损 急倾斜、扭曲、防滑条的脱落、腐蚀、手把 亮度不够、位置不良、罩子污染、保护设施等 破损、防暴不适合 保护罩脱落、露出、并联安全装置、紧急刹车 吊车、起重机类的钢绳、挂构、刹车等 特殊物品、溶剂、有毒气体、隔热材料、危险 标示、保护工具 备注
8/61
1.整理(Seiri) :不必要品与必要品分开,不必要品处理 ※ 彻底去除不必要品,消除空间和管理浪费
整理要领:
1次/月以上 1次/3月以上 1次/年以上 1次/年都不使用 放在作业区 工程或部门仓库 部门仓库 退还.返还
超过保管期
无法使用
废弃
废弃.返还
9/61
2.整顿(Seiton) :必要品容易取拿且使用方便 (防止必要品过剩与不足,便于存取)
18/61
6.不合理查找方法
◇五感:视觉.听觉.触觉.嗅觉.味+感觉 眼、 耳、 手、 鼻、 口 ◇专业知识(理论加实践)
不合理分类
区 分 定义 重点 内容
确定 基准 物品 分类
定品 定位 定量 可视化
不合理 详细事项
无法判断物品的种类及数量 过期品、过量品、废品,缩小、剪短、不必要 动作行为、多余的程序 没有明确标示品名 没有指定明确的原位置 没有标示出最大、最小量、订货点、在库量 人、机、物状态不能一目了然
② 情报共享.
③ 自我展示 物:活动的对象. 三现:现场.现物.现象 人:活动主体
5/61
七.TPM八大支柱
T P M 灾害.故障.不良.浪费“0”化
TPM 阶段手册简化

20/43
5 发生源
故障、不良、灾 害、污染发生的 部位
6 困难部 位
妨碍人的行动的 部位
7 不安全 部位
对人产生危害或 有潜在危害的部 位
8 其它
产品 原料/油
气体 液体
泄漏、流淌、溢流、飞散 润滑油、传动油、燃料油的漏油、流淌、溢流 空气、气体、蒸汽等泄漏 自来水、冷却水、废水漏水 包装材料、半成品、不良品等混放
2/43
Ⅲ. “0”STEP活动实施 3- 1 整理对象 3-2 整理基准 3-3 物品存放要点 3-4 场地规划图(例) 3-5 存放场地改善要点 3-6 循环分析法 3-7 循环分析表 3-8 可视化管理 3-9 可视化实施顺序 3-10 TPM一般划线基准 3-11 废弃物处理基准 3-12 清扫要领 3-13定点摄影 3-14 改善前后对照表 3-15-1 “0”STEP不合理检查要点(1) 3-15-2 “0”STEP不合理检查要点(2) 3-15-3 “0”STEP不合理检查要点(3) 3-15-4 “0”STEP不合理检查要点(4) 3-16 不合理发现LIST 3-17 疑问点作成要领 3-18 疑问点LIST Ⅳ. “0”STEP活动诊断 4-1 “0”STEP基准 4-2 诊断申请书 4-3 TPM诊断现况板 4-4 诊断表
业务复杂、麻烦、程序复杂、顾客不满、顾客不便
21/43
3-1 整理对象 22/43
3-2 整理基准
区分
判断基准
必要品A 一周内使用一次以上
处理方法
标签
备注
在作业区内保管
-
划放置区域
必要品B 一周至六个月内使用一次
办公室或工程内保管
-
搬到合适的场所
必要品C 六个月至一年内使用一次
5 发生源
故障、不良、灾 害、污染发生的 部位
6 困难部 位
妨碍人的行动的 部位
7 不安全 部位
对人产生危害或 有潜在危害的部 位
8 其它
产品 原料/油
气体 液体
泄漏、流淌、溢流、飞散 润滑油、传动油、燃料油的漏油、流淌、溢流 空气、气体、蒸汽等泄漏 自来水、冷却水、废水漏水 包装材料、半成品、不良品等混放
2/43
Ⅲ. “0”STEP活动实施 3- 1 整理对象 3-2 整理基准 3-3 物品存放要点 3-4 场地规划图(例) 3-5 存放场地改善要点 3-6 循环分析法 3-7 循环分析表 3-8 可视化管理 3-9 可视化实施顺序 3-10 TPM一般划线基准 3-11 废弃物处理基准 3-12 清扫要领 3-13定点摄影 3-14 改善前后对照表 3-15-1 “0”STEP不合理检查要点(1) 3-15-2 “0”STEP不合理检查要点(2) 3-15-3 “0”STEP不合理检查要点(3) 3-15-4 “0”STEP不合理检查要点(4) 3-16 不合理发现LIST 3-17 疑问点作成要领 3-18 疑问点LIST Ⅳ. “0”STEP活动诊断 4-1 “0”STEP基准 4-2 诊断申请书 4-3 TPM诊断现况板 4-4 诊断表
业务复杂、麻烦、程序复杂、顾客不满、顾客不便
21/43
3-1 整理对象 22/43
3-2 整理基准
区分
判断基准
必要品A 一周内使用一次以上
处理方法
标签
备注
在作业区内保管
-
划放置区域
必要品B 一周至六个月内使用一次
办公室或工程内保管
-
搬到合适的场所
必要品C 六个月至一年内使用一次
TPM培训教材1
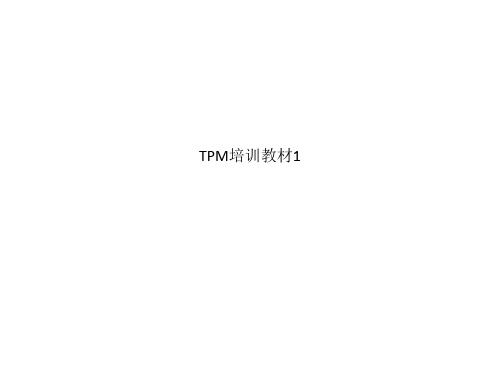
×100
⑧废 弃
生产综合效率 = 时间运转率×性能运转率×良品率 13
基本条件的整备
‘维护的基本——防止劣化的活动’是运转部门的维护活动。但是防止 劣化的活动需要基本条件的整备作为最重要的项目来设定好。 设备故障的大部分情况都是因设备部位的劣化而发生。
⊙劣化包括: 特别是人为的恶劣环境(锈、污垢、漏油、灰尘等)的强制劣化加速设 备的劣化,从而形成设备的故障,大大减短了设备的使用寿命。 因此,如何杜绝这人为的恶劣环境的方法,就是减少故障的要领。为了 延长设备寿命,排除强制劣化是当务之急。 确切的执行清扫、注油、紧固,点检,并维持与管理叫做基本条件整备。
实施短期点检 复原所有部位的不合理
- 活动AREA MAP
- 提出不合理LIST
- 不合理对策书 (PM分析…)
- 标准制,修订项目LIST -SUB-Theme登录 -OPL - 各种标准书 - 要素作业Manual - 点检Manual
生 产 综 合 效 率的 计 算
①计 划 维 护 ②生 产 调 整
时间运转பைடு நூலகம்=
日.历 时间-①②③④ 日.历 时间
×100
③故
障
④ 准备、交换、调整
⑤速 度 低 下
性能运转率=
标准 Index ? 加工数量 运转时间
×100
⑥ 空 转、 暂 停 ⑦ 修 理·再 加 工
加工数量 - ⑦⑧
良品率 =
数量
部位对策
3ST 制订准基准书
4ST 总点检教育
5ST 自主点检
6ST 工程品质保证
12
设备的8大浪费 降低了 生产综合效率!
设备
日历时间 (年 月 日) (A )
TPM1STEP手册
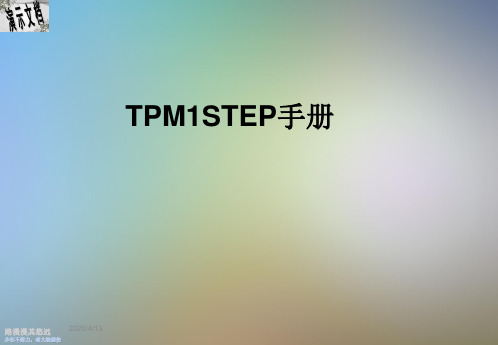
路漫漫其悠远
第2阶段(测定劣化的活动):4~5STEP
✓日常检查(运转的五官检查,巡视) ✓定期检查,定期更换
第3阶段(劣化复原活动):6~7STEP
✓实施小维护(异常时的应急处理,更换简单的部件) ✓故障异常发生时迅速正确的联络 ✓修理突发性故障时,可以进行支援 ✓设定良品条件及管理条件
路漫漫其悠远
6STEP 7STEP
现场发生 变化
1.理解现场革新的基本为什 么是 5S ? 2.思考设备为什么发生强制 劣化? 3.为什么要做自主保全? 4.推进1阶段以上时理解安 全行动的重要性3
路漫漫其悠远
1.改善问题点 2.清扫就是点检 3.点检就是发现问题( 包括疑问点、缺陷、发 生源、困难源) 4.问题点复原改善 5.提高:问题点发现能 力;改善方向设定能力
“清扫是检查”
路漫漫其悠远
3)TPM 展开的思维模式:
0STEP (事前准备)
1STEP 2STEP 3STEP
TPM活动
赋
改
阶段开展
予
变
思考方式
动
设
机
备
效果: 不良减少 故障减少
4STEP 5STEP
人 变 化
思考的变化 故障、不良是 现场的羞耻
效果 达成故障 不良的“0” 化
活动的变化 积极参与改善 彻底维持管理
路漫漫其悠远
活动实施
潜在缺陷的暴露 彻底清扫
以清扫的手段摸 一摸设备的每个
角落
彻底去除灰尘污 染
整理1STEP过程记录指标: 在活动中随时进行
开展主题活动
发现劣化不合理 体会清扫困难源 察觉灰尘污染发生源 正常?异常?
制作清扫一览表
劣化不合理LIST
第2阶段(测定劣化的活动):4~5STEP
✓日常检查(运转的五官检查,巡视) ✓定期检查,定期更换
第3阶段(劣化复原活动):6~7STEP
✓实施小维护(异常时的应急处理,更换简单的部件) ✓故障异常发生时迅速正确的联络 ✓修理突发性故障时,可以进行支援 ✓设定良品条件及管理条件
路漫漫其悠远
6STEP 7STEP
现场发生 变化
1.理解现场革新的基本为什 么是 5S ? 2.思考设备为什么发生强制 劣化? 3.为什么要做自主保全? 4.推进1阶段以上时理解安 全行动的重要性3
路漫漫其悠远
1.改善问题点 2.清扫就是点检 3.点检就是发现问题( 包括疑问点、缺陷、发 生源、困难源) 4.问题点复原改善 5.提高:问题点发现能 力;改善方向设定能力
“清扫是检查”
路漫漫其悠远
3)TPM 展开的思维模式:
0STEP (事前准备)
1STEP 2STEP 3STEP
TPM活动
赋
改
阶段开展
予
变
思考方式
动
设
机
备
效果: 不良减少 故障减少
4STEP 5STEP
人 变 化
思考的变化 故障、不良是 现场的羞耻
效果 达成故障 不良的“0” 化
活动的变化 积极参与改善 彻底维持管理
路漫漫其悠远
活动实施
潜在缺陷的暴露 彻底清扫
以清扫的手段摸 一摸设备的每个
角落
彻底去除灰尘污 染
整理1STEP过程记录指标: 在活动中随时进行
开展主题活动
发现劣化不合理 体会清扫困难源 察觉灰尘污染发生源 正常?异常?
制作清扫一览表
劣化不合理LIST
TPM自主保全Step1-4阶段活动介绍

对策实施 – 现场实物进行改善
评价 – 未达到预期效果时追加改善
Step - 3
清扫,注油基准书制定
3.3 Step 清扫,注油基准书制定
1.定义
-. 制定一个 <能在最短时间内完成>注油,清扫的基准书,总结设备基本条件.
2.行动基准
-.操作人员可切实执行的基准书. -.注油管理基准书与注油点检表一致. -.创造可执行条件(时间,方法,技能培训等) -.以操作人员的角度来制定
3.3 Step 清扫,注油基准书制定
3.阶段性基准书
?
3.3 Step 清扫,注油基准书制定
4.目的
3.3 Step 清扫,注油基准书制定
5.PDCA推进
3.3 Step 清扫,注油基准书制定
6.生产/保全班组负责范围
1
生产
1
保全
1.日常注油,点检 -.油脂,空压机油量点检及补充/减速箱,轴承箱油量点检及补充 等
Step 总点检活动
3.推行
-.必须进行点检程序的培训,培训教材已整理编制好的总点检手册。 -.随后,依照点检手册实施点检技能教育,提升员工的技术水准。 -.总点检的过程一般要持续很长的时间,这也是操作工人检查异常能力的训练过程.
-.通过标准化的日常管理,建立一个防范于未然的机制。 -.员工参与管理的意愿和现场改善能力的提升
4.期待目标
正常与否,一眼便可知晓
时机 信息获取
准确性 准确判断,防止遗漏
共享 信息共享与透明
时效 行动/反映速度
肉眼可见
1.1 Step 初期清扫(5S)
可视化管理 - 2
可视化管理 原则
1.1 Step 初期清扫(5S)
设备自主保全TPM-STEP1(精选)PPT文档30页
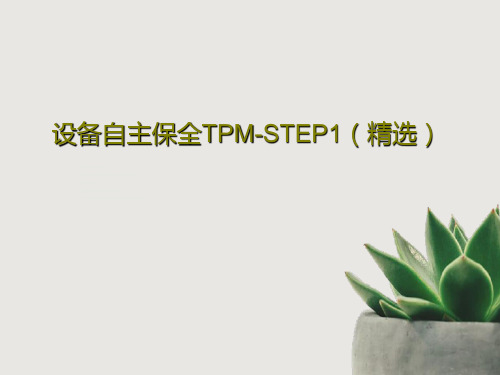
END
16、业余生活要有意义,不要越轨。——华盛顿 17、一个人即使已登上顶峰,也仍要自强不息。——罗素·贝克 18、最大的挑战和突破在于用人,而用人最大的突破在于信任人。——马云 19、自己活着,就是为了使别人过得更美好。——雷锋 20、要掌握书,莫被书掌握;要为生而读,莫为读而生。——布尔沃
设备自主保全TPM-STEP1(精选)
11、获得的成功越大,就越令人高兴 。野心 是使人 勤奋的 原因, 节制使 人枯萎 。 12、不问收获,只问耕耘。如同种树 ,先有 根茎, 再有枝 叶,尔 后花实 ,好好 劳动, 不要想 太多, 那样只 会使人 胆孝懒 惰,因 为不实 践,甚 至不接 触社会 ,难道 你是野 人。(名 言网) 13、不怕,不悔(虽然只有四个字,但 常看常 新。 14、我在心里默默地为每一个人祝福 。我爱 自己, 我用清 洁与节 制来珍 惜我的 身体, 我用智 慧和知 识充实 我的头 脑。 15、这世上的一切都借希望而完成。 农夫不 会播下 一粒玉 米,如 果他不 曾希望 它长成 种籽; 单身汉 不会娶 妻,如 果他不 曾希望 有小孩 ;商人 或手艺 人不会 工作, 如果他 不曾希 望因此 而有收 益。-- 马钉路 德。
TPM1STEP教材(NEW)

7)活动阶段:………………………………… 二.TPM 1 STEP活动内容 ……………… …
1)1 STEP(初期清扫): ……………… … 2)TPM 1 STEP活动流程图: …………… … 3)初期清扫内容: ………………………… 4) 理解设备的结构与性能:……………… … 5) 理解设备各组成部位的检查要点:……… 6)TPM 1 STEP活动的安全………………… 三、小组TPM“1”STEP活动方法:………… … 1) 活动目的、方法:………………… … 2) 小组成功3要素:……………………… 3) 主题活动:…………………………… 四、TPM小组活动板的制作:………………
10 / 48
TPM推进室
TPM推进室
三、 1 STEP 小组 活动方法
1)活动目的、方法
①活动目的
a. 全员参与,全员协力,形成小组凝聚力。 b. 通过活动,培养员工的领导能力和管理能力。 c. 通过活动,可以相互启发。 d. 提高问题意识,改善意识,品质意识,减少成本,积极改善现场的问题点。 e. 自学的遵守标准,履行确保品质标准。
2 / 48
TPM推进室
TPM推进室
一.TPM 活 动 概 述
Total Productive Maintenance (全员生产保全)
3 / 48
1)定义:
* 追求设备综合效率最佳化为目标 * 以设备的寿命周期为对象,把预防体制构筑在生产部门 * 借力于管理设备的计划部门、使用部门、维护部门等 * 从最高经营者到一线的操作工为止的全员参与 * 依靠重复小组活动,即依据小组自主推进TPM
9 / 48
活动准备
3)TPM 1 STEP活动流程:
✓理解怎样开展1STEP活动 ✓树立1STEP活动计划 ✓决定设备的责任人 ( 4 MY ) ✓理解设备的结构与性能(技能提高) ✓理解各部位的检查要点 (设备点检流程) ✓进行安全教育,制定安全检查单
1)1 STEP(初期清扫): ……………… … 2)TPM 1 STEP活动流程图: …………… … 3)初期清扫内容: ………………………… 4) 理解设备的结构与性能:……………… … 5) 理解设备各组成部位的检查要点:……… 6)TPM 1 STEP活动的安全………………… 三、小组TPM“1”STEP活动方法:………… … 1) 活动目的、方法:………………… … 2) 小组成功3要素:……………………… 3) 主题活动:…………………………… 四、TPM小组活动板的制作:………………
10 / 48
TPM推进室
TPM推进室
三、 1 STEP 小组 活动方法
1)活动目的、方法
①活动目的
a. 全员参与,全员协力,形成小组凝聚力。 b. 通过活动,培养员工的领导能力和管理能力。 c. 通过活动,可以相互启发。 d. 提高问题意识,改善意识,品质意识,减少成本,积极改善现场的问题点。 e. 自学的遵守标准,履行确保品质标准。
2 / 48
TPM推进室
TPM推进室
一.TPM 活 动 概 述
Total Productive Maintenance (全员生产保全)
3 / 48
1)定义:
* 追求设备综合效率最佳化为目标 * 以设备的寿命周期为对象,把预防体制构筑在生产部门 * 借力于管理设备的计划部门、使用部门、维护部门等 * 从最高经营者到一线的操作工为止的全员参与 * 依靠重复小组活动,即依据小组自主推进TPM
9 / 48
活动准备
3)TPM 1 STEP活动流程:
✓理解怎样开展1STEP活动 ✓树立1STEP活动计划 ✓决定设备的责任人 ( 4 MY ) ✓理解设备的结构与性能(技能提高) ✓理解各部位的检查要点 (设备点检流程) ✓进行安全教育,制定安全检查单
TPM1STEP设备清扫知识课件

• 下面这些情况全部需要指定为安全隐患。
·垃圾,脏污 ·滴漏,飞散 ·松动,非正常噪音 ·损伤,缺失
·弯曲,磨损 ·生锈,伤痕 ·离心,倾斜 ·异常运转
·振动,摇晃 ·奇异声响,发热 ·怪味,变色
清扫的要点
• 操作员要亲自动手清扫 • 把长年累积的污垢清除掉 • 打开至今为止从来都没有看过的外壳以及盖子,将
• 二: 自主保全
• 1 .什么是自主保全?
•自己的设备是自己守护
•自主:有关自己的事是通过自己解 决 •保全:保护而使之完善(设备)
•处理,恢复能力
•发现异常的能力
•成为优秀的设备操作人
•维持管理能力员
•条件设定能力
•习惯化
•具备设备基本条件的活动:清洁,拧紧,供油
•遵守设备使用条件:
日常保全
•保全员能力向上 •化保全作业标准
•MTTR 1 •MTTR
•改善point
•时间
清扫的定义
• 清扫既是检查 • 检查既是发现安全隐患 • 安全隐患既是需要复原或者改善
什么是隐患
• 将设备的各个角落都仔细检查一遍,然后一定要去发现的 安全隐患到底都是些什么呢?
• 乍一看,根本想象不到这些会和发生故障以及不合格产品 有关系的,一点点的脏污,伤痕以及奇怪的响声,倾斜等 等,不仅是静态的安全隐患,还要动一动机器听听振动和 声音,此外还要看看“运转”情况如何。
更换O垫圈
8 为什么会漏?
O垫圈断裂
修复伤痕
9 为什么会断裂?
杆上有伤痕
防止切割粉尘飞散的对策
10 为什么会有伤痕?
切割粉尘飞散起来沾在杆上 到第3-STEP进行
11 运转,漏油,油温如何 沾上油里的垃圾
·垃圾,脏污 ·滴漏,飞散 ·松动,非正常噪音 ·损伤,缺失
·弯曲,磨损 ·生锈,伤痕 ·离心,倾斜 ·异常运转
·振动,摇晃 ·奇异声响,发热 ·怪味,变色
清扫的要点
• 操作员要亲自动手清扫 • 把长年累积的污垢清除掉 • 打开至今为止从来都没有看过的外壳以及盖子,将
• 二: 自主保全
• 1 .什么是自主保全?
•自己的设备是自己守护
•自主:有关自己的事是通过自己解 决 •保全:保护而使之完善(设备)
•处理,恢复能力
•发现异常的能力
•成为优秀的设备操作人
•维持管理能力员
•条件设定能力
•习惯化
•具备设备基本条件的活动:清洁,拧紧,供油
•遵守设备使用条件:
日常保全
•保全员能力向上 •化保全作业标准
•MTTR 1 •MTTR
•改善point
•时间
清扫的定义
• 清扫既是检查 • 检查既是发现安全隐患 • 安全隐患既是需要复原或者改善
什么是隐患
• 将设备的各个角落都仔细检查一遍,然后一定要去发现的 安全隐患到底都是些什么呢?
• 乍一看,根本想象不到这些会和发生故障以及不合格产品 有关系的,一点点的脏污,伤痕以及奇怪的响声,倾斜等 等,不仅是静态的安全隐患,还要动一动机器听听振动和 声音,此外还要看看“运转”情况如何。
更换O垫圈
8 为什么会漏?
O垫圈断裂
修复伤痕
9 为什么会断裂?
杆上有伤痕
防止切割粉尘飞散的对策
10 为什么会有伤痕?
切割粉尘飞散起来沾在杆上 到第3-STEP进行
11 运转,漏油,油温如何 沾上油里的垃圾
- 1、下载文档前请自行甄别文档内容的完整性,平台不提供额外的编辑、内容补充、找答案等附加服务。
- 2、"仅部分预览"的文档,不可在线预览部分如存在完整性等问题,可反馈申请退款(可完整预览的文档不适用该条件!)。
- 3、如文档侵犯您的权益,请联系客服反馈,我们会尽快为您处理(人工客服工作时间:9:00-18:30)。
初期清扫 发生源 困难源对策 制定准基准书 总点检 自主点检 品质保证深化 自主管理
2
3
4
5
6
7
二.TPM 1 STEP活动内容
1)1 STEP(初期清扫):
目的 直接接触设备来彻底去除污垢,使潜在缺陷显形并彻底消除。 能够用眼睛发现,判断不合理(能够进行检查,并判断异常与否)。 设备方面 除去灰尘污染,以使潜在缺陷明显化。
( × ) ( × ) ( ○ )
KEY
螺丝,螺母的 使用方法
螺 母 在 下 面 松 了 也 看 不 见
螺 母 在 下 面 掉 了 也 看 不 见
“清扫是检查”
3)TPM 展开的思维模式:
0STEP (事前准备) TPM活动 阶段开展 思考方式 赋 予 动 机 1STEP 2STEP 3STEP 改 变 设 备 效果: 不良减少 故障减少 4STEP 5STEP 人 变 化 思考的变化 故障、不良是 现场的羞耻 效果 达成故障 不 良 的 “0”化 6STEP 7STEP 现场发生 变化
本人成功或失败的经验提出来让大家参考。
3. OPL制作方法
选定主题(题目)。
在10─20分内能够写出,大且易读的字体。 尽可能多使用图表,漫画,相片(能够在10分钟内结束 育)。 教
必须由当事人记录,不熟练则由组长进行帮助, 1 张 / 周为最低目标。
以先后顺序装订并保管,放在任何人都能够看得到的 地方。(原则为现况板)
彻 底 清 扫
彻底去除灰尘污 染
重要不合理LIST
整理1STEP过程记录指标: 在活动中随时进行 开展主题活动
制作清扫一览表
制作清扫准基准书及 检查单 重点管理推移曲线 图
STEP诊断
自我诊断→专家诊断→部门经理诊断
总经理诊断 授予合格证 转向2阶段
3)初期清扫内容:
1.原理—清扫就是点检展开图
a. 无尘:不发生—清扫过程中扬尘(用扫把、抹布等)
,把静的污染变成动的污染,形成新的污染。 b. c. 防尘:不扩散—清扫过程中防止灰尘扩散。 消尘:发生后—灰尘存在后,一定要彻底去除。
5、初期清扫必须达到的目的:
a. b. 彻底去除污染(开发有效率的清扫工具) 不合理复原及改善(整理、整顿、微缺陷去除)
1 STEP
设备
以机能 为中心 无论怎么去除大缺陷,缺陷还是在扩大。 (微小缺陷→中缺陷→大缺陷) ⊙潜在缺陷(微小缺陷)
3现主义 -现场 -现物 -现象
§关于缺陷内容的说明:
a.定义:引起故障、不良的原因 b.种类:缺陷分为大、中、小缺陷, 一般来说重点在于大、中缺陷,但微 缺陷具有预防的作用
大缺陷:引起运转停止(故障停机)的缺陷
所以,重视问题的根本原因“微缺陷”,形成一个思考方式,不仅得到 减少慢性故障、不良的结果,最终达到预防不良、故障的效果。
4.初期清扫进行步骤:
a.污染去除的清扫:把设备分解开,擦拭到每个零件,开发清扫工具、
改善清扫方法,减少清扫时间,要学习、了解设备的性能、基能
清扫发现设备存在的ቤተ መጻሕፍቲ ባይዱ陷。
,通过
b.点检、观察的清扫:通过污染去除的清扫,把设备里面的异物拿出来
TPM “1”STEP 手册
目 录
一.什么是TPM活动……………………………………………………1 1)定义……………………………………………1 2)目的……………………………………………1 3)TPM展开的思维模式……………………1 4)活动阶段………………………………………2 5)TPM 7 STEP………………………………3 二.TPM 1 STEP活动内容 ………………………4 1)1 STEP(初期清扫)…………………………4 2)TPM 1 STEP活动流程图 …………………5 3)初期清扫内容…………………………………6 4)理解设备的结构与性能…………………………11 5)理解设备各组成部位的检查要点………………12 6)TPM 1 STEP活动的安全……………………20 三、小组TPM“1”STEP活动方法…………………27 1) 活动目的、方法………………………………27 2) 小组成功3要素………………………………28 3) 主题活动………………………………………28 四、TPM小组活动板的制作:………………………………31
清扫
去除污染、灰尘
预防故障、不良的发生
实施清扫
接触设备的各部分
发现各部位的不合理(缺陷、发生源、困难源、疑问点 ) 不良、故障发生之前采取的措施 通过“三现”,理解设备、工程的技能和原理
接触
2.清扫方法介绍
上面→下面(如先从下面清扫会浪费时间)
清扫方法:
里面→外面 复杂→简单(从复杂的地方开始,到简单的地方)
日常清扫:指日常的扫地,拿着抹布,进行表面的清扫。(“0”STEP中的清扫) 机能清扫:指设备方面的清扫,以加工点为中心进行清扫。(“1”STEP中的清扫)
3.0 STEP与1 STEP活动比较(进一步理解1阶段活动):
区分 对象 重点 不合理 ⊙明显的缺陷(大,中缺陷) 0 STEP 物品 以环境 为中心 -用眼睛看得到的大的 原则 3现主义 -现场 -现物 -现时
后,又发现有新的污染产生,我们要找出这种污染的发生源,并
,如果发生源一直存在,就会存在重复的清扫,在清扫过 到的地方,称为“困难源”。
解决它
程中,检查不
c.改善的清扫:发出发生源和困难源后,就进行改善清扫。
d.维持管理的清扫:形成“我的区域”如何进行清扫的维持清扫基准书。
※ 如何进行“去除污染的清扫”
第2阶段(测定劣化的活动):4~5STEP
日常检查(运转的五官检查,巡视) 定期检查,定期更换
第3阶段(劣化复原活动):6~7STEP
实施小维护(异常时的应急处理,更换简单的部件) 故障异常发生时迅速正确的联络 修理突发性故障时,可以进行支援 设定良品条件及管理条件
5)TPM 7 STEP:
中缺陷:两个或几个问题点相互作用,引起LOSS的原因。 微缺陷:现在对设备故障、品质不良等没有影响,但将来能够发展成为大缺 陷、中缺陷,引起的LOSS的原因。 ◑ 把重点放在大、中缺陷,对突发故障、异常的减少有效。 ◑ 把重点放在微缺陷,对慢性LOSS减少有效。
C.重视微缺陷的目的:
杜绝因微缺陷累计产生的上升作用。 通过慢性LOSS原因的集约化,发现解决方案。
去除微缺陷,可预先防止大、中缺陷引起的故障、不良。
d.发现微缺陷时的注意点:
Ø 根据原理、原则的重复研究。
简单地把设备的固有状态作为目标,原则性判断问题,防止微缺陷的遗漏 。
Ø 不期望于补充率。
补充率成为问题是在初期阶段(不良率高,故障频度高),在这进选择对 降低不良发生及故障发生补充的环节,集中对策很具有效果。
7、清扫时不合理的发现要领
活用五感:视、触、听、嗅、味+感觉 ◑用手: ①摇一摇 ②敲一敲 ③拧一拧 ④按一按、摁一摁 ⑤刮一刮 ⑥紧一紧、 松一松 ⑦掰一掰 ⑧拽一拽 ⑨擦一擦 ⑩理一理
◑用眼睛
①确认是否动作; ②确认是否变动、变更; ③确认是否变色; ④确认正 常、异常; ⑤确认是否不均衡 ⑥确 认是否有疑点
来制作资料。 F自己做老师,拿出来与大家一起进行学习为基本思路。
1.OPL的目的2.OPL的种类
基础知识应用 在进行生产或TPM活动时,以“不知道就不行”的观点来要求自己, 通过制作和教育来补充新知识。 故障及不良事例 以实际发生的故障、不良事例来反省知识及技能上的不足,防止再 发生。 改善事例 通过横向相联系的改善事例学习新的改善思维方法,以提高自主保 全活动中改善的质量。 经验感受
STEP
1
活动内容
以设备为中心彻底去除灰尘污染,彻底发现并解决微缺陷。 制定5种LIST(不合理发现LIST、发生源LIST、困难源LIST、重要不合理LIST、疑问点 LIST)。 树立发生源对策。 采取防止飞散的对策。 改善清扫困难源来缩短时间。 进行润滑机能教育。 进行润滑总检查。 制定在指定时间内能够完成清扫注油的基准。 制定润滑管理体系。 按总检查科目进行技能教育。 总检查。 改善设备检查方法。 制定在检查时,确实能进行检查的基准。 制定自主管理基准周期表。 遵守以设备为对象的活动基准,并踏实地做好日常保全。 以故障“0”为目标。 开展不良“0”活动。 开展不制作不良的活动。 以工序,设备来保证品质,并以不良“0”化为目标。 现在的TPM水平上维持、改善、继承。
5)理解设备各组成部位的检查要点:
1、螺丝,螺母
微小缺陷 螺杆长度 ◆有没有松动,有没有脱落 ◆螺杆是否留有2-3个螺母程度的余长 长孔是否使用着活用KEY 有振动的情况,是否使用弹簧KEY 同场所是否用着几种KEY 是否从下面穿进螺丝,把螺母放到可看到的地方 LIMITER开关是否用2个以上的螺母固定 DOUBLE NUT是否使用了内径小,外径大的 旋转体,振动体是否使用了垫片
对劣化、不合理进行复原。
使设备容易得到检查。 人的方面 通过做清扫来熟悉小组活动。
班长组长学习领导艺术。
通过五官和接触来提高对设备的好奇心。 体会“清扫是检查”。
目标
彻底去除影响或阻碍设备或产品机能的一切潜在微缺陷,即微缺陷0化。 彻底清扫设备的每一个角落,并考虑怎样才能舒适、简便、快捷的清扫。
一.什么是TPM活动?
1)定义: 1.在制造企业里以制造部门为主进行的灾害、浪费、不良 、故障为“0”的活动。
2.以主人的身份对我的设备、我的工程进行保护、维持和 管理,来实现生产的最佳状态。 2)目的: 1.自己的设备自己来维护。 2.追求设备的最佳状态。 3.成为熟练的设备运转人员。 4.形成能够发现异常的现场。
明亮、洁净的现场
提高对外信用度
4)理解设备的结构与性能: