(完整版)陶瓷压铸工艺
压铸的工艺过程,特点,优点

压铸模锻工艺简介压铸模锻工艺是一种在专用的压铸模锻机上完成的工艺。
它的基本工艺过程是:金属液先低速或高速铸造充型进模具的型腔内,模具有活动的型腔面,它随着金属液的冷却过程加压锻造,既消除毛坯的缩孔缩松缺陷,也使毛坯的内部组织达到锻态的破碎晶粒。
毛坯的综合机械性能得到显著的提高。
另外,该工艺生产出来的毛坯,外表面光洁度达到7级(Ra1.6),如冷挤压工艺或机加工出来的表面一样,有金属光泽。
所以,我们将压铸模锻工艺称为“极限成形工艺”,比“无切削、少余量成形工艺”更进了一步。
压铸模锻工艺还有一个优势特点是,除了能生产传统的铸造材料外,它还能用变形合金、锻压合金,生产出结构很复杂的零件。
这些合金牌号包括:硬铝超硬铝合金、锻铝合金,如LY11、LY12、6061、6063、LYC、LD等)。
这些材料的抗拉强度,比普通铸造合金高近一倍,对于铝合金汽车轮毂、车架等希望用更高强度耐冲击材料生产的部件,有更积极的意义。
一、压铸简介压力铸造简称压铸,是一种将熔融合金液倒入压室内,以高速充填钢制模具的型腔,并使合金液在压力下凝固而形成铸件的铸造方法。
压铸区别于其它铸造方法的主要特点是高压和高速。
①金属液是在压力下填充型腔的,并在更高的压力下结晶凝固,常见的压力为15—100MPa。
②金属液以高速充填型腔,通常在10—50米/秒,有的还可超过80米/秒,(通过内浇口导入型腔的线速度—内浇口速度),因此金属液的充型时间极短,约0.01—0.2秒(须视铸件的大小而不同)内即可填满型腔。
压铸机、压铸合金与压铸模具是压铸生产的三大要素,缺一不可。
所谓压铸工艺就是将这三大要素有机地加以综合运用,使能稳定地有节奏地和高效地生产出外观、内在质量好的、尺寸符合图样或协议规定要求的合格铸件,甚至优质铸件。
1、压铸机(1)压铸机的分类压铸机按压室的受热条件可分为热压室与冷压室两大类。
而按压室和模具安放位置的不同,冷室压铸机又可分为立式、卧式和全立式三种形式的压铸机。
压铸工艺流程

压铸工艺流程
《压铸工艺流程》
压铸是一种将熔化的金属注入高压模具中,形成所需形状的工艺。
这种工艺经常用于生产汽车零件、家用电器零件、工业零件等,因为它能够生产出具有高精度和表面质量的零件。
压铸工艺流程一般包括以下几个步骤:
1. 型腔设计:首先根据待生产零件的形状和尺寸设计出模具,模具的设计需要考虑到金属在高压下的流动情况和冷却情况,以确保最终产品的质量。
2. 材料准备:在进行压铸之前,需要将待生产的金属材料熔化成液态,通常使用锌合金、铝合金等金属进行压铸。
3. 模具装配:将设计好的模具组装好,保证模具能够承受高压的作用,并且能够在压铸过程中顺利分离,以确保产品的成型。
4. 注射:将熔化的金属材料注入模具中,在一定的压力下使金属充满模具的所有空间,以保证最终产品的尺寸和形状精度。
5. 固化冷却:在金属填充模具空间后,保持一定时间使金属冷却凝固,待产品完全凝固后,打开模具,取出成品。
6. 修边处理:取出成品后,还需要对产品进行去除余料、去除毛刺等修边处理,使产品表面光滑、无毛刺。
以上就是压铸工艺的基本流程,压铸工艺具有生产效率高、产品精度高、表面质量好等优点,因此被广泛应用于各个领域的零件生产中。
铸造工艺(附图)
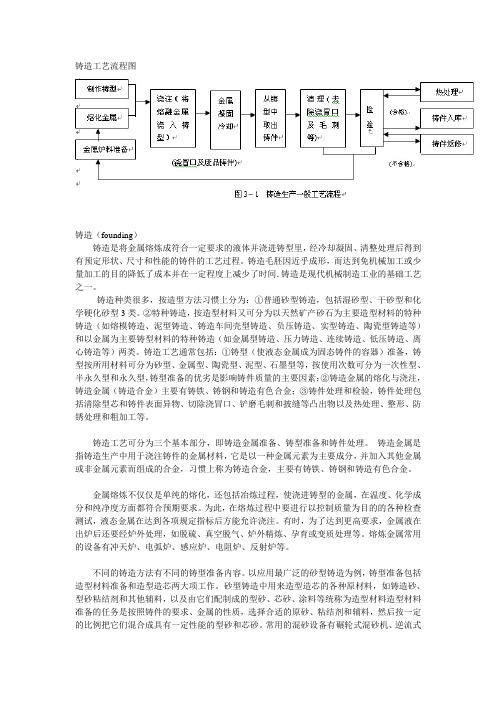
铸造工艺流程图铸造(founding)铸造是将金属熔炼成符合一定要求的液体并浇进铸型里,经冷却凝固、清整处理后得到有预定形状、尺寸和性能的铸件的工艺过程。
铸造毛胚因近乎成形,而达到免机械加工或少量加工的目的降低了成本并在一定程度上减少了时间.铸造是现代机械制造工业的基础工艺之一。
铸造种类很多,按造型方法习惯上分为:①普通砂型铸造,包括湿砂型、干砂型和化学硬化砂型3类。
②特种铸造,按造型材料又可分为以天然矿产砂石为主要造型材料的特种铸造(如熔模铸造、泥型铸造、铸造车间壳型铸造、负压铸造、实型铸造、陶瓷型铸造等)和以金属为主要铸型材料的特种铸造(如金属型铸造、压力铸造、连续铸造、低压铸造、离心铸造等)两类。
铸造工艺通常包括:①铸型(使液态金属成为固态铸件的容器)准备,铸型按所用材料可分为砂型、金属型、陶瓷型、泥型、石墨型等,按使用次数可分为一次性型、半永久型和永久型,铸型准备的优劣是影响铸件质量的主要因素;②铸造金属的熔化与浇注,铸造金属(铸造合金)主要有铸铁、铸钢和铸造有色合金;③铸件处理和检验,铸件处理包括清除型芯和铸件表面异物、切除浇冒口、铲磨毛刺和披缝等凸出物以及热处理、整形、防锈处理和粗加工等。
铸造工艺可分为三个基本部分,即铸造金属准备、铸型准备和铸件处理。
铸造金属是指铸造生产中用于浇注铸件的金属材料,它是以一种金属元素为主要成分,并加入其他金属或非金属元素而组成的合金,习惯上称为铸造合金,主要有铸铁、铸钢和铸造有色合金。
金属熔炼不仅仅是单纯的熔化,还包括冶炼过程,使浇进铸型的金属,在温度、化学成分和纯净度方面都符合预期要求。
为此,在熔炼过程中要进行以控制质量为目的的各种检查测试,液态金属在达到各项规定指标后方能允许浇注。
有时,为了达到更高要求,金属液在出炉后还要经炉外处理,如脱硫、真空脱气、炉外精炼、孕育或变质处理等。
熔炼金属常用的设备有冲天炉、电弧炉、感应炉、电阻炉、反射炉等。
不同的铸造方法有不同的铸型准备内容。
压铸工艺 ppt课件
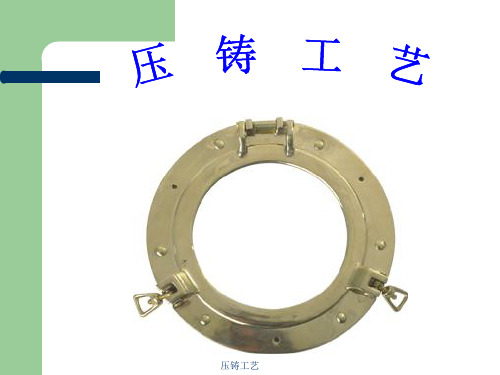
比压的影响
比压对铸件机械性能的影响 :比压增大,结晶 细,细晶层增厚,由于填充特性改善,表面质量 提高,气孔影响减轻,从而抗拉强度提高。
对填充条件的影响:合金熔液在高比压下填充型 腔,合金温度升高,流动性改善,有利于铸件质 量的提高。
压力增大,金属液温度升高
压铸工艺
影响压力的因素
▪ 压铸合金特性,如流动性等,流动性好,有效 比压越大
压铸工艺
浇注温度的作用和影响
合金温度对铸件机械性能的影响。随着合金温度的提高。 机械性能有所改善,但超过一定限度后,性能恶化,主 要原因是:
气体在合金中的溶解度,随温度的升高而 增大,虽然溶解在合金中的气体,但在压铸过程中难
以析出,影响机械性能
含铁量随合金温度升高而增加,使流动性降低, 结晶粗大,性能恶化
• 根据铸件的壁厚要求
• 在一般的情况下,压铸薄壁铸件时,型腔中的流动阻力 较大,内浇口也采用较薄的厚度,因此具有大的阻力, 故要有较大的填充比压,才能保证达到需要的内浇口速 度
• 对于厚壁铸件,一方面选定的内浇口速度较低,并且金 属的凝固时间较长,可以采用较小的填充比压;另一方 面,为了使铸件具有一定的致密度,还需要有足够的增 压比压才能满足要求。
铝合金、镁合金随温度升高氧化加剧,氧化夹杂 物,使合金性能恶化。
压铸工艺
影响浇注温度的重要因素
合金的性质:熔点、热容量、凝固范围等,对镁合金热 容量小,浇注温度可偏高一点,以有利于填充成形;凝 固范围宽的合金,可采用低温低速高压和较厚的内浇口, 对厚壁铸件质量可取得良好的效果。
零件结构的复杂程度。 模具温度较高时,可适当降低浇注温度。 比压和压射速度,均对合金温度有直接影响,动能转化
与压力共同对铸件内部质量,表面要求和轮廓清 晰程度起着重要的作用。压力是速度的基础
(完整)压铸工艺介绍精品PPT资料精品PPT资料
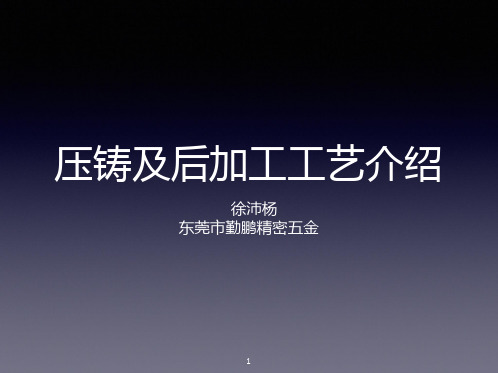
压铸工艺优势
1).压铸件尺寸精度高,表面粗糙度低; 2).铸件强度和表面硬度高; 3).应用范围广,灯具散热器,汽车配件,家具卫浴五金,电
子电器配件,饰品配件,建筑材料,餐具,玩具,运动器材 ,礼品,机械五金配件等等; 4).生产率高,可实现自动化生产; 5).金属利用率高
压铸工艺的劣势
1).压铸时由于液态金属充填型腔速度高,流态不稳定,故采 用一般压铸法,铸件易产生气孔,不容易进行热处理;
• 压铸锌合金
• 锌合金的熔融状态流动性非常好,熔点低只有365 度。可进行各种后加工处理,比如电镀等。所以 用途广泛,之前在 行业也使用很多,但因为比得 大,耐蚀性差渐被铝合金淘汰。目前使用最多的 当属卫浴行业。
• 常用的有2, 3 , 4, 5, 7号合金,目前最广泛的是3号 合金。
压铸金属材料
压铸机
压铸机的分类:
热室压铸机:锌合金,镁合金等
冷室压铸机:锌合金,镁合金,铝 合金,铜合金等
立式压铸机:锌,铝,铜,铅,锡
热室和冷室的区别在于:压铸机的 射料系统是否浸泡在金属溶液里。 压铸机也可分为卧式与立式。
压铸金属材料
• 主要压铸用合金材料有锡、铅、锌、铝、镁、铜 等。以锌、铝合金应用最广,镁、铜合金次之。 当前在电子行业用的以锌,铝,镁合金为主。
压铸模具
• 压铸模具必须用热作模具钢制 作,常用的钢材有:H13, 2344, 8407, 8418, SKD61, DAC, FDAC等 。
• 模具的结构:(后模,前模) 模架,模仁,导柱,导套顶针 ,司筒,分流子,浇口套,滑 块,斜导柱,油压抽芯。
• 3,模具的加工设备:铣床, CNC加工中心,线切割(慢走丝 ),(镜面)火花机,磨床, 车床,焊补设备 。
压铸工艺实操全过程
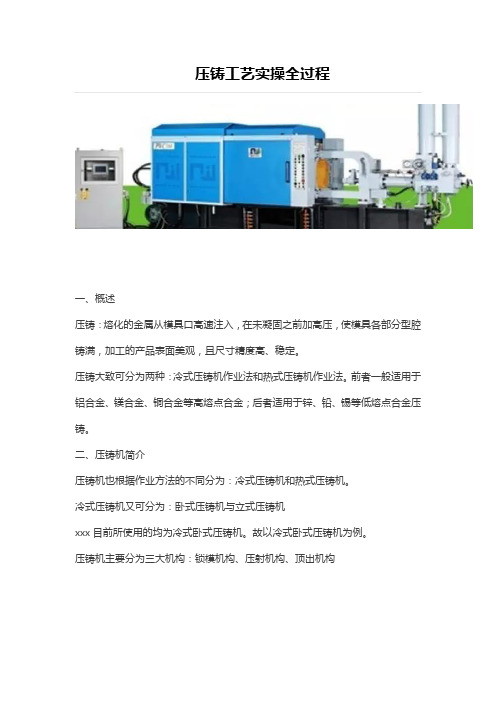
压铸工艺实操全过程一、概述压铸:熔化的金属从模具口高速注入,在未凝固之前加高压,使模具各部分型腔铸满,加工的产品表面美观,且尺寸精度高、稳定。
压铸大致可分为两种:冷式压铸机作业法和热式压铸机作业法。
前者一般适用于铝合金、镁合金、铜合金等高熔点合金;后者适用于锌、铅、锡等低熔点合金压铸。
二、压铸机简介压铸机也根据作业方法的不同分为:冷式压铸机和热式压铸机。
冷式压铸机又可分为:卧式压铸机与立式压铸机xxx目前所使用的均为冷式卧式压铸机。
故以冷式卧式压铸机为例。
压铸机主要分为三大机构:锁模机构、压射机构、顶出机构冷式压铸机本机各部名称:下面是冷式压铸机各装置的典型布局主要有压铸机本机、给汤机、喷涂机、取出机等组成。
三、压铸安全操作注意事项1、开机作业前,必须确认“安全门”、“非常停止按钮”、“操作电源开关”、的功能是否正常。
2、必须确认开合模、与取出机、喷雾机之间的安全互锁关系是否正常。
3、严禁两人或更多的人同时操作按钮。
当有帮手时(换模),必须在相互确认,高声呼喊,方可下一步动作。
4、压铸作业时,模具分型面前方严禁站人。
下面是铸造作业时发生灾害事故的分析:(数据来源日本)a 模具分型面最容易飞散铝液引起烫伤事故。
43%b 开模时候的料饼裂碎会引起烫伤事故。
7%c 被顶出板夹住引起事故。
6%d 被曲柄夹住引起事故。
2%e 其他的灾害事故42%5、取出机活动范围内严禁站人。
6、清理或修理模具时,必须关闭“操作电源开关”或按下“非常停止”按钮。
7、给汤机勺子作业前要预热、涂钛白粉、烘干,以免造成爆炸。
熔解炉中严禁注水。
8、压铸机、模具修理时,如有身体一部分要进入动作结构时,必须切断电源开关,以免机械误动造成人身伤害。
四、发生事故时的应急措施1、铝液爆炸时,操作工应尽快躲避,并高声通知。
2、发现火情,应立即关闭电源,随后用灭火器或砂子扑灭。
3、生产中,发现异常动作时,都应立即停止,报告领导,寻找原因。
4、如有人员受伤必须以最快速度送医院抢救。
陶瓷模铸造
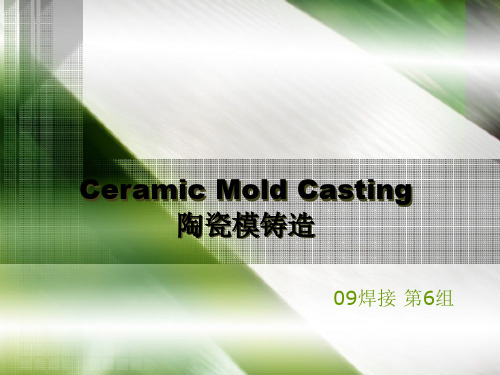
Step 8 Remove Boards
• After 20 minutes, take casting boards apart, scrape off(刮掉) top of plaster and bevel the edges slightly. Grasp opposite sides of the plaster/clay mold and gently twist to loosen clay from the work board as shown. Turn mold over and proceed to lift off clay from model and plaster half of the mold.
Step 14 The Pour Hole
• With both halves now clean of any particles, we now determine where to carve in your Pour Hole. It can be in one half or in both halves as shown. Bevel the outer edge of the parting line on both halves and bevel all outside edges of the mold. This keeps that edge from chipping.
Step 4 Parting Agent
• Apply Parting Agent with a soft brush covering the entire surface. Dry your brush and pick up all excess Parting Agent, leaving a very slick(光 滑的) surface on the object and parting line clay.
压铸的工艺流程及特点

压铸的工艺流程及特点《说说压铸那些事儿》嘿,朋友们!今天咱们来聊聊压铸,这可是个相当有意思的玩意儿,也是个很重要的工业制程呢!先来说说压铸的工艺流程吧。
就好像做菜一样,得先准备好食材,压铸也是,要先有金属材料。
这些材料就像是做菜的原料,得精挑细选。
然后呢,把这些金属加热融化,这就像把菜炒熟一样。
不过这可不是在锅里炒,而是在专门的设备里变成液体。
接下来,就是最精彩的部分啦,把这些液态金属“噗”地一下射到模具里,就好像把菜盛到盘子里一样。
等它冷却凝固了,嘿,一个压铸出来的零件就出炉啦!这过程听起来是不是挺好玩儿的?说到压铸的特点,那可有得唠啦!首先呢,压铸出来的东西那可真是够结实的,质量杠杠的。
就像那种特别强壮的大力士,能扛得住各种压力和折腾。
这可多亏了压铸工艺,能让金属紧密地结合在一起,不容易坏。
其次啊,压铸特别适合做那种形状复杂的东西,就跟变魔术似的,能把金属变成各种奇奇怪怪的形状,什么奇形怪状的零件都不在话下。
还有啊,压铸速度快啊!就好像短跑运动员一样,“嗖”地一下就完成了。
这样就能节省好多时间,快快地生产出好多零件来。
但是呢,压铸也不是完美无缺的。
它就像人一样,也有自己的小缺点。
比如说,模具的成本可不低啊,就跟买个贵贵的包包似的。
而且模具要是坏了,那可就麻烦了,还得花时间和精力去修。
不过总的来说,压铸还是个相当厉害的工艺。
它让我们的生活变得更加方便,那些小汽车啊、电器啊,里面可都少不了压铸的零件呢!它就像一个默默奉献的小英雄,虽然我们可能不太注意到它,但它却在背后发挥着重要作用。
我自己就特别喜欢压铸的过程,看着那些金属在机器里翻滚、变形,最后变成一个个精致的零件,感觉特别神奇。
就好像看着一个小生命在慢慢成长一样。
而且每次看到那些压铸出来的高质量产品,心里就会有一种满满的成就感。
总之呢,压铸的工艺流程和特点都挺有意思的。
它既有自己的优点,又有一些需要注意的地方。
但不管怎么说,它都是工业生产中不可或缺。
陶瓷型铸造
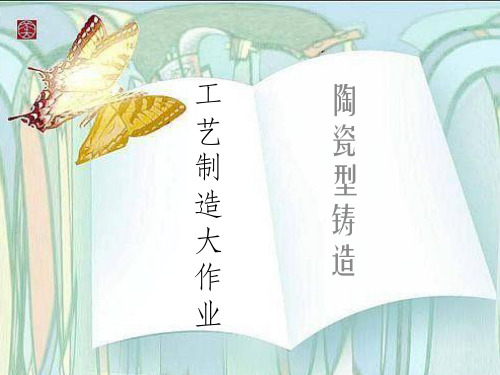
• • • • •
4.脱膜剂,常用的脱模剂有上光腊,变压 器油,机油、有机硅油及凡士林等。 5.透气剂,在陶瓷浆料中加入透气剂以改 善陶瓷型的透气性。常用的透气剂是双氧水, 其加入量为耐火粉料重量的0.2~0.3%。 (二)陶瓷浆料的配制及灌浆 1.耐火材料的选择 在铸造尺寸和光洁度要求高的合金钢锻模、 压铸型、玻璃器皿模具时,应采用耐高温的、 热稳定性好的刚玉粉、钻砂粉或碳化硅作为陶 瓷型浆料的耐火材料。对于铸铁件或铝铸件可 采用价格较便宜的铝矾土或石英粉作为耐火材 料,并正确选择耐火材料的粒度组成。
概述
• 陶瓷型的制造方法可分为两大类:一类是全部采用 陶瓷浆料制造铸型法;另一类就是采用底套(相当 于砂型的背砂层)表面再灌陶瓷浆料以制陶瓷型的 方法。底套又分砂套和金属底套两种; • 小型陶瓷型铸件,常采用全部以陶瓷浆料制造 的陶瓷型,其造型过程如下所示。 1、首先将模型固定于模板上 2、再套上砂箱 3、然后将预先调好的陶瓷浆料倒入砂箱 4、将上表面刮平,等待结胶硬化 5、待浆料一旦出现弹性即可进行起模
• (五)焙烧 • 焙烧的目的是使陶瓷型内残存的乙醇、 水分和少量的有机物烧去,并使陶瓷层的 强度增加。 全部由陶瓷浆料灌制的陶瓷型,焙烧 温度可高达800℃,焙烧时间2~3h,出炉温 度应在250℃以下,以防止产生裂纹。 带有水玻璃套的陶瓷型,焙烧温度 (烘干)在350~550℃。
•
•
• 六)浇注与清理 • 陶瓷型浇注时一定要注意挡渣。浇注 温度与浇注速度可比同类型的砂型铸件稍 高。陶瓷型铸件最好待冷却至室温时再打 箱,这样可防止铸件裂纹与变形。
工艺过程图
制造工艺过程视频
超连接视频 超连接视频
陶瓷铸造的应用
• 陶瓷铸造已成为铸造大型厚壁、精 密铸件的主要方法。如铸造冲模、 锻模、玻璃器皿模、压锻模和板模 等,可以大大节约加工工时,也可 用于生产中型精密铸钢件。
压铸的工艺流程
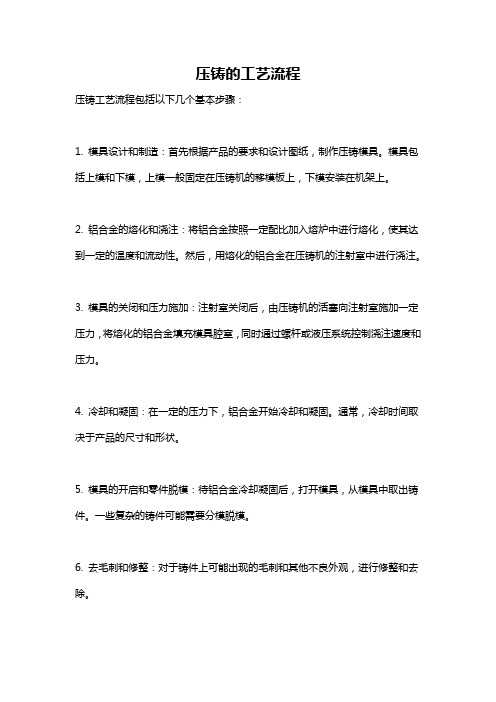
压铸的工艺流程
压铸工艺流程包括以下几个基本步骤:
1. 模具设计和制造:首先根据产品的要求和设计图纸,制作压铸模具。
模具包括上模和下模,上模一般固定在压铸机的移模板上,下模安装在机架上。
2. 铝合金的熔化和浇注:将铝合金按照一定配比加入熔炉中进行熔化,使其达到一定的温度和流动性。
然后,用熔化的铝合金在压铸机的注射室中进行浇注。
3. 模具的关闭和压力施加:注射室关闭后,由压铸机的活塞向注射室施加一定压力,将熔化的铝合金填充模具腔室,同时通过螺杆或液压系统控制浇注速度和压力。
4. 冷却和凝固:在一定的压力下,铝合金开始冷却和凝固。
通常,冷却时间取决于产品的尺寸和形状。
5. 模具的开启和零件脱模:待铝合金冷却凝固后,打开模具,从模具中取出铸件。
一些复杂的铸件可能需要分模脱模。
6. 去毛刺和修整:对于铸件上可能出现的毛刺和其他不良外观,进行修整和去除。
7. 表面处理和后处理:对于一些需要特殊表面处理的铸件,如电镀、喷涂等,进行相应的后处理工序。
8. 检查和质量控制:对铸件进行检查和测量,进行质量控制,确保产品的质量符合要求。
经过以上步骤,压铸工艺流程完成。
最终的铸件可用于各种应用,如汽车零部件、通信设备、家电等。
陶瓷型铸造工艺和原理

陶瓷型铸造所用浆料
陶瓷型铸造与熔模铸造的异同点
制壳材料 制壳方法 硬化方法 起模方法 应用范围
硅酸乙酯 熔模铸造 水解液、
刚玉等
硅酸乙酯
陶瓷型铸 水解液、
• 3.3.1 陶瓷型所用的造型材料
•
陶瓷型所用的造型材料包括耐火材料、粘结剂、
催化剂、脱模剂、透气剂等。
•
1.耐火材料,陶瓷型所用的耐火材料要求杂质少,
熔点高和高温热膨胀系数小。可作陶瓷型的耐火材料
有刚玉粉、铝矾土、碳化硅及锆砂粉等。
•
2.粘结剂,陶瓷型常用的粘结剂是硅酸乙酯水解
液。
• 3.催化剂,陶瓷浆料所用的催化剂有氢氧化钙、 氧化镁、氢氧化钠以及氧化钙等。
硅酸乙酯
水解
硅酸乙酯水解液
+
耐火材料
配置浆料
准备模型及砂套 灌浆
+
催化剂
结胶硬化起模
Байду номын сангаас
铸件 清理 打箱 浇注 合箱 熏烟 焙烧 喷烧
合金熔炼
陶瓷型铸造的工艺流程
陶瓷型铸造(Ceramic Mold Casting)是在砂型铸 造和熔模铸造基础上发展起来的一种铸造方法,又 称Shaw Process肖氏法,它是用高质量陶瓷浆料形 成铸型型腔的方法。
• 4.脱膜剂,常用的脱模剂有上光蜡,变 压器油,机油、有机硅油及凡士林等。
• 5.透气剂,在陶瓷浆料中加入透气剂以 改善陶瓷型的透气性。常用的透气剂是双氧水, 其加入量为耐火粉料重量的0.2~0.3%。
陶瓷型铸造模具制造技术及工艺
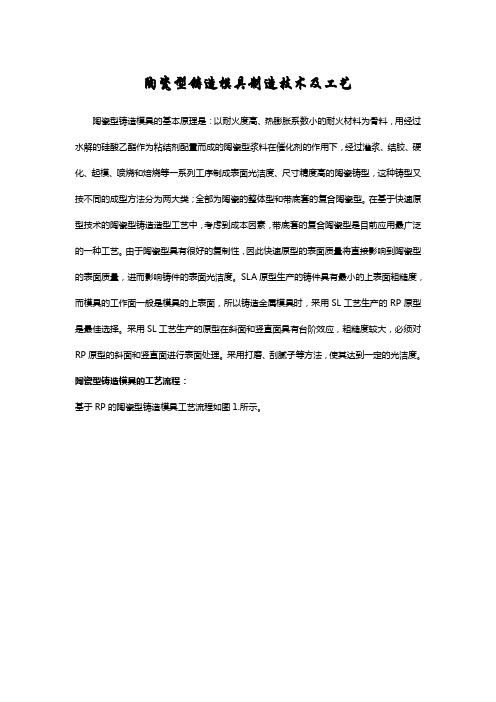
陶瓷型铸造模具制造技术及工艺陶瓷型铸造模具的基本原理是:以耐火度高、热膨胀系数小的耐火材料为骨料,用经过水解的硅酸乙酯作为粘结剂配置而成的陶瓷型浆料在催化剂的作用下,经过灌浆、结胶、硬化、起模、喷烧和焙烧等一系列工序制成表面光洁度、尺寸精度高的陶瓷铸型,这种铸型又按不同的成型方法分为两大类;全部为陶瓷的整体型和带底套的复合陶瓷型。
在基于快速原型技术的陶瓷型铸造造型工艺中,考虑到成本因素,带底套的复合陶瓷型是目前应用最广泛的一种工艺。
由于陶瓷型具有很好的复制性,因此快速原型的表面质量将直接影响到陶瓷型的表面质量,进而影响铸件的表面光洁度。
SLA原型生产的铸件具有最小的上表面粗糙度,而模具的工作面一般是模具的上表面,所以铸造金属模具时,采用SL工艺生产的RP原型是最佳选择。
采用SL工艺生产的原型在斜面和竖直面具有台阶效应,粗糙度较大,必须对RP 原型的斜面和竖直面进行表面处理。
采用打磨、刮腻子等方法,使其达到一定的光洁度。
陶瓷型铸造模具的工艺流程:基于RP的陶瓷型铸造模具工艺流程如图1.所示。
具体过程如下:(1)设计制作模具原型使用三维CAD软件进行模具零件的三维实体造型和面向RT的RP原型工艺设计,在LPS600激光快速成型机上制作模具原型。
(2)原型表面处理由于原型的表面质量将直接影响到陶瓷型的表面质量,进而影响铸件的表面光洁度,因此必须对原型进行表面处理。
采用打磨、刮腻子等方法,使其达到一定的光洁度。
(3)砂箱及水玻璃砂底套的准备根据原型的大小选择合适的砂箱,对于小件,原型距砂箱内壁应为80~100mm。
选用CO2硬化的水玻璃砂底套具有强度高、透气性好、制作简便等特点,其制作工序见图1.2所示。
先用木材做一个外廓尺寸比模具原型大8~10mm的木模(如图2.a)所示,木模的尺寸精度和表面光洁度不做要求。
将木模和砂箱放在平板上,调整好木模与砂箱内壁之间的间隙,在木模上放一个圆锥形木棒(参看图2.b)以便在底套上做出灌浆用的直孔,然后填水玻璃砂、捣实、起模,经吹CO2硬化后便得到水玻璃砂套。
压铸工艺及操作规程(3篇)

第1篇一、压铸工艺概述压铸是一种将金属熔体在高压下注入到铸模中,冷却凝固后得到所需的铸件的金属成型方法。
压铸工艺具有生产效率高、尺寸精度好、表面光洁度高等优点,广泛应用于汽车、家电、电子等行业。
二、压铸工艺流程1. 铝合金熔炼:将铝锭或铝合金锭放入熔炼炉中,通过加热熔化成铝液。
2. 模具准备:根据产品图纸制作或选用合适的模具,并对模具进行预热。
3. 铝液准备:将熔化的铝液过滤、除气、去除杂质,使其达到压铸要求。
4. 压射成型:将铝液注入到预热的模具中,在高压下使铝液充满模具型腔。
5. 冷却凝固:铝液在模具中冷却凝固,形成铸件。
6. 取件:将铸件从模具中取出。
7. 清理:对铸件进行去毛刺、抛光等表面处理。
8. 检验:对铸件进行尺寸、表面质量、机械性能等检验。
三、压铸操作规程1. 安全操作:操作者必须穿戴好劳保用品,如工作服、手套、眼镜等,确保人身安全。
2. 设备检查:开机前,检查设备是否正常运行,如油压、冷却系统、控制系统等。
3. 模具准备:根据产品图纸制作或选用合适的模具,并对模具进行预热。
4. 铝液准备:将熔化的铝液过滤、除气、去除杂质,使其达到压铸要求。
5. 压射成型:将铝液注入到预热的模具中,在高压下使铝液充满模具型腔。
6. 冷却凝固:铝液在模具中冷却凝固,形成铸件。
7. 取件:将铸件从模具中取出。
8. 清理:对铸件进行去毛刺、抛光等表面处理。
9. 检验:对铸件进行尺寸、表面质量、机械性能等检验。
10. 设备维护:定期对设备进行保养、检修,确保设备正常运行。
四、注意事项1. 铝液温度:铝液温度应控制在合适的范围内,过高或过低都会影响铸件质量。
2. 压射压力:压射压力应根据产品材质、厚度等因素进行调整,确保铸件成型质量。
3. 模具预热:模具预热温度应控制在合适的范围内,过高或过低都会影响铸件质量。
4. 铝液过滤:铝液过滤可有效去除杂质,提高铸件质量。
5. 模具维护:定期对模具进行检查、清洗、维护,确保模具使用寿命。
爱尔陶瓷创热压铸工艺流程

爱尔陶瓷创热压铸工艺流程英文回答:Introduction:The hot pressing casting process is a widely used method in the manufacturing of ceramic products. This process involves heating the ceramic material to a high temperature and applying pressure to mold it into the desired shape. In this article, we will discuss the process of hot pressing casting used by Aier Ceramic.Step 1: Preparation of Raw Materials.The first step in the hot pressing casting process is the preparation of raw materials. Aier Ceramic carefully selects and mixes the ceramic powders and other additives to achieve the desired composition and properties of the final product. The raw materials are then ground to a fine powder to ensure uniformity.准备工作:热压铸工艺的第一步是原材料的准备。
爱尔陶瓷会精选和混合陶瓷粉末和其他添加剂,以达到最终产品所需的组成和性能。
然后将原材料研磨成细粉,以确保均匀性。
Step 2: Molding.Once the raw materials are prepared, the next step is molding. Aier Ceramic uses a mold made of high-quality steel or graphite. The mold is carefully designed to achieve the desired shape and dimensions of the final product. The prepared ceramic powder is then poured into the mold.成型:原材料准备好后,下一步是成型。
陶瓷热压铸成型技术的创新发展

陶瓷热压铸成型技术的创新发展陶瓷热压铸成型技术的创新发展引言:陶瓷热压铸成型技术作为一种先进的制造方法,已经在各种工业领域中得到广泛应用。
本文将探讨陶瓷热压铸成型技术的创新发展,包括其原理、材料选择和应用领域,并提出个人观点和理解。
第一部分:陶瓷热压铸成型技术的原理陶瓷热压铸成型技术是将陶瓷粉末与适当的添加剂混合,经过高温高压处理,使其形成致密的陶瓷坯体。
其原理主要包括四个方面:原料准备、铸型制备、热压过程和热处理。
原料准备阶段涉及陶瓷粉末的选择和添加剂的配比。
不同种类的陶瓷材料需要根据其特性来选择合适的陶瓷粉末,以获得所需的力学性能和导热性能。
添加剂的配比对于改善陶瓷的可塑性、流动性和烧结性能也至关重要。
铸型制备阶段主要是根据所需产品的形状和尺寸来设计和制造模具。
模具的设计需要考虑到陶瓷的热膨胀系数和收缩率等因素,以确保成型过程中的尺寸精度和表面质量。
热压过程是陶瓷热压铸成型的核心步骤,通常在高温高压下进行。
过程中,陶瓷粉末在模具中经过压实和烧结,形成致密的坯体。
温度和压力的控制对于成型的质量和性能至关重要,过高或过低的参数都会对最终产品的性能产生负面影响。
热处理阶段是为了进一步提高陶瓷的力学性能和烧结密度。
通过控制热处理的时间和温度,可以使陶瓷的晶粒生长和致密化,从而提高其强度和硬度。
第二部分:陶瓷热压铸成型技术的材料选择陶瓷热压铸成型技术可以用于各种陶瓷材料的制备,包括氧化物陶瓷、非氧化物陶瓷和复合陶瓷。
不同类型的陶瓷材料具有不同的性能和应用领域。
氧化物陶瓷是最常见的陶瓷材料之一,具有优良的绝缘性能和耐热性能。
常见的氧化物陶瓷包括氧化铝、氧化锆和氧化锌等。
这些陶瓷材料在电子、化工和航天等领域中得到广泛应用。
非氧化物陶瓷具有更高的硬度和强度,常用的非氧化物陶瓷包括碳化硅、氮化硅和氮化硼等。
这些陶瓷材料在高温、高压和摩擦磨损等极端条件下具有出色的性能,因此在航空、汽车和切削工具等领域中得到广泛应用。
压铸工艺各个过程、压铸模具各位置作用、设备维护保、各种常见压铸缺陷养及工艺过程知识全解

三、压铸参数调整
28
三、压铸参数调整
29
三、压铸参数调整
30
三、压铸参数调整
速度过慢尾部困气
速度过快气体卷入浪花
合理压射速度
31
三、压铸参数调整
32
三、压铸参数调整
三速压射起点过早 液流混乱包气严重
33
三、压铸参数调整
三速压射起点过迟 液流阻力变大
34
三、压铸参数调整
三速压射起点恰到好处
19
二、压铸的三要素——压铸模
成型系统:
压铸模的结构
就是由优质钢材围成的可以形成零件的空腔。
浇注系统:
就是将合金液引入成型系统,
并排除气体和杂质的通道。
模架系统:
由结构钢组成的用以支撑、定位、导向的结构。
抽芯系统:
解决铸件垂直于开模方向的凹槽和孔洞
成型后出模的 机构。
顶出系统:
就是方便将成型后的铸件从模具内拿下来,并使
• 13、出厂前机器各油阀都已调校完毕,若有需要可对 “射 料工作压力”、及各换向阀的流量进行调整,其余涉及系 统压力、双泵压力、流量比例控制及安全压力等不允许随 便调校。
47
四、压铸机维护与保养
液压系统维护与保养
• 14、应使用优质液压油,其换油程序如下: • 1)一般按规定程序换油的压铸机,水渍及胶质不多,油箱底部没有类
52
四、压铸机维护与保养 电器部分维护与保养
• 四)外部信号装置的保养 • 1、每个月检修一次各行程开关的检测头和接线端子是否
松动,动作是否灵敏,行程开关的安装螺丝是否松动,安 装位置是否符合要求等,如检查安全门吉掣,机械手各限 位吉制,调模限位吉掣,锁模确认吉掣等。 • 2、每2个月检查一次各感应吉掣,擦除其表面的灰尘、油 迹,磁性物质等。 • 3、每半年检修一次操纵面板,观察各按钮的安装是否松 动,接线端子是否有松脱现象,用万用表检测各按钮的相 关点的通断是否安全可靠。
第2讲 压铸工艺
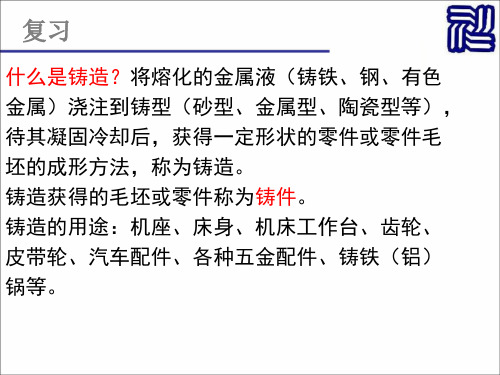
二.压铸生产的工艺特点
但是压铸生产也存在一些缺点: 1.压铸件易出现气孔和缩松; 2.不适合小批量生产; 3.模具的寿命低; 4.受压铸件结构和合金种类所 限。
第二节 压铸件的工艺性
一.压铸件的精度
影响压铸件精度的主要因素有:模具精度及工作情况、压铸机的精 度及刚度、合金成分及性能、压铸件的结构、尺寸、压铸工艺参数等。
2.压铸件的自由角度和锥度公差
3.压铸件的形状和位置公差
压铸件的表面形状和尺寸精度主要取决于压铸模成型表 面的形状和位置精度,同时,压铸件的变形也是不可忽略的 影响因素。
相关公差的选用,见教材:
表1-5 压铸件平行度和垂直度公差;
表1-6 压铸件同轴度和对称度公差。
二.压铸件的表面质量
压铸件的表面粗糙度值,一般比模具成型表面的粗 糙度值低两级。新模具可获得Ra值为0.8μm的压铸件。 模具在正常使用寿命内: 锌合金铸件Ra=1.6~3.2μm 铝、镁合金铸件Ra=3.2μm 铜合金铸件受模具龟裂的影响表面质量最差。 压铸件表面粗糙度的数值,随着模具使用次数的增 加而增大。
1.压铸件的尺寸精度
压铸件尺寸的经济精度可达IT11~IT13级,高时可达IT9~IT10级, 未注公差可参照IT14级选取。 确定压铸件的尺寸公差时,考虑如下因素: (1)以空间对角线表示压铸件轮廓尺寸大小
L空 a2 b2 c2
(2)分型面、活动成型部分对尺寸的影响 与分型面无关的为A类尺寸,与分型面有关的为B类尺寸。
压铸件缺陷:
2.压铸件的孔和槽隙 压铸件可以直接铸出比较小深的小孔和比较窄的槽隙。合 金收缩时会对型心产生很大的抱紧力,使型心抽出时容易弯 曲、折断或破坏铸件。因此,对压铸件的孔径、孔深以及孔 间距应加以限制。
- 1、下载文档前请自行甄别文档内容的完整性,平台不提供额外的编辑、内容补充、找答案等附加服务。
- 2、"仅部分预览"的文档,不可在线预览部分如存在完整性等问题,可反馈申请退款(可完整预览的文档不适用该条件!)。
- 3、如文档侵犯您的权益,请联系客服反馈,我们会尽快为您处理(人工客服工作时间:9:00-18:30)。
(完整版)陶瓷压铸工艺
陶瓷压铸工艺
简介
陶瓷压铸工艺是一种将陶瓷材料通过压铸的方式制作成各种形
状的工艺。
该工艺具有精密、高强度和耐磨损等优点,被广泛应用
于陶瓷制品的生产领域。
工艺步骤
以下是陶瓷压铸工艺的基本步骤:
1. 材料准备:选择适合的陶瓷材料,并进行粉末状或颗粒状的
处理。
2. 模具设计:根据产品的需求和形状设计模具,确保模具可以
满足压铸工艺的要求。
3. 模具制造:根据设计的模具图纸,制造出可用于压铸的模具。
4. 材料注入:将准备好的陶瓷粉末或颗粒注入模具内。
5. 压铸过程:通过机械设备将陶瓷材料进行压铸,使其充分填充模具内的空间。
6. 成型处理:对压铸后的陶瓷制品进行成型处理,如去除多余材料、修整边缘等。
7. 烧结与热处理:将成型后的陶瓷制品进行烧结或热处理,提高其强度和耐久性。
8. 检验与品质控制:对烧结后的陶瓷制品进行检验,确保其质量符合要求。
应用领域
陶瓷压铸工艺广泛应用于以下领域:
- 高温工业领域:用于制造耐高温、耐磨损的陶瓷零部件,如炉具、炉格等。
- 电子领域:用于制造电子元器件的外壳和结构件,具有绝缘性能和耐腐蚀性。
- 医疗领域:用于制造医疗器械、人工关节等产品,具有生物相容性和耐磨性。
- 航空航天领域:用于制造航空航天器的结构件,具有轻量化和抗氧化性能。
总结
陶瓷压铸工艺是一种精密而高效的制造工艺,可以用于生产各种陶瓷制品。
通过适当的材料选择和工艺控制,可以获得高品质的陶瓷制品,满足不同领域的需求。