一体压铸工艺
一体化压铸技术及免热合金:汽车轻量化降本的趋势所在(附股)

⼀体化压铸技术及免热合⾦:汽车轻量化降本的趋势所在(附股)1、2020年9⽉的电池⽇上,特斯拉宣布Model Y将采⽤⼀体式压铸后地板总成,将原来通过零部件冲压、焊接的总成⼀次压铸成型,相⽐原来可减少79个部件,制造成本因此下降40%。
并且特斯拉宣布下⼀步计划将应⽤2-3个⼤型压铸件替换由370个零件组成的整个车体总成,重量将进⼀步降低10%,对应续航⾥程可增加14%。
2021年12⽉18⽇,蔚来发布旗下最便宜车型“电动轿跑eT5”, 32.8 万元起售,长续航⾥程达1000 公⾥,值得注意的是,eT5零到百公⾥加速4.3秒,采⽤蔚来⾃研的四活塞铝合⾦⼀体式铸造卡钳,百公⾥到零制动距离33.9⽶。
其中涉及到了⼀个降本法宝——⼀体压铸,相⽐传统车⾝制造的“冲压+焊接”⼯艺,⼀体压铸具有轻量化、零件数量及⼯序步骤减少、⼈员及⼟地节约等优势,能极⼤地节约造车成本。
⼩鹏汽车在此⽅⾯也有⼀定尝试,据相关消息显⽰,⼩鹏武汉⼯⼚除了规划了常规的冲压、焊接、涂装车间,还加⼊了⼀体化压铸⼯艺车间,武汉⼯⼚将引进⼀套(条)以上超⼤型压铸岛及⾃动化的⽣产线。
2、压铸是⼀种⾦属铸造⼯艺,其原理类似于注射成型。
它向熔融⾦属施加⾼压,并将其注⼊模具的型腔,以铸造出所需的形状。
⼀体化压铸车⾝是轻量化技术的升级,减少车⾝零件数量,使得车⾝结构⼤幅简化;在轻量化的同时,简化供应链环节,具备降低车重减少电池成本、原材料利⽤率⾼、⼯⼚占地⾯积减少等多种优点,实现汽车组装效率⼤幅提升。
传统车⾝的制造⼯艺,按照冲压-焊装-涂装-总装的流程开展,⼀辆车由⼤约500个不同形状、不同材料的零件焊接⽽成。
每⼀个零件都有误差,每⼀个零件的误差波动都会对最终的车⾝精度造成影响,但⼀体式压铸,⼀次成型,没有先冲压后焊接的复杂过程。
除了减轻重量、减少部件、降低成本外,⼀体化的安全性也有所提⾼,在原先的汽车中,零件处有多个焊点,汽车碰撞过程中,焊点可能会承受冲击⼒然后遭遇撕扯,但对于⼀体化零件来说,受⼒⽅向并不是问题,因为整块零件都由完整的⾦属构成。
一体压铸工作原理

一体压铸工作原理
一体压铸工作原理:
一体压铸是一种将金属(通常是铝合金)熔化后注入高压铸模中,通过压力和冷却过程将金属凝固成为成型件的加工方法。
其工作原理如下:
1. 准备工作:首先准备好所需的压铸模具,包括上下模具、销子等。
同时准备好所需的原料,通常会选择铝合金作为材料,并将其熔化。
2. 开模:将熔化的金属倒入注射机中,通过机械或液压系统将金属注入到高压铸模的腔室中。
同时,上下模具合拢,将腔室封闭。
3. 塑形:通过高压注射,金属在腔室中充分填充,填满整个模腔并形成所需的形状。
注射结束后,维持在一定的压力下,以保持金属的形状稳定。
4. 冷却:在注射完成后,模具中的金属开始冷却。
冷却过程可以通过水冷却系统或其他方式进行,通常需要一定的时间以确保金属完全凝固。
5. 分模:当金属完全凝固后,上下模具分开,将成品从模腔中取出。
同时清理模具,以备下一次压铸。
6. 后处理:取出的成品可以进行后续的加工和处理,如去除余
边、研磨、抛光等,以达到最终要求的尺寸和表面光洁度。
通过以上工作步骤,一体压铸可以快速、高效地生产出金属零件。
它具有成本低、生产效率高、制造精度高等优点,广泛应用于汽车、航空航天、家电等行业。
一体化压铸工艺 特点

一体化压铸工艺特点一体化压铸工艺是目前较为先进的金属制造工艺之一,它将铸造和加工两个工序融合在一起,通过一次连续的生产过程,将熔化的金属直接注入模具,经过凝固、冷却和脱模等步骤,最终得到所需的成品。
一体化压铸工艺具有以下几个特点:1. 整体性强:一体化压铸工艺将铸造和加工两个工序融合在一起,实现了从原材料到成品的一次性加工,避免了传统铸造和加工过程中的多次搬运和中间加工环节,提高了生产效率。
2. 精度高:一体化压铸工艺采用模具来控制产品的形状和尺寸,模具具有较高的精度和稳定性,可以生产出形状复杂、尺寸精确的零部件,满足高精度要求的产品制造。
3. 节约材料:一体化压铸工艺可以减少废品和余料的产生,因为它是通过熔化金属直接注入模具进行成型,不需要额外的材料加工和切割操作,有效降低了材料的浪费。
4. 稳定性好:一体化压铸工艺在生产过程中,可以通过调整工艺参数和模具设计来控制产品质量,保证每个产品的一致性和稳定性,降低了因为工艺变化而引起的质量差异。
5. 生产效率高:一体化压铸工艺的生产过程中,可以实现自动化和连续化操作,减少了人工干预和中间环节,大大提高了生产效率,降低了生产成本。
6. 适用范围广:一体化压铸工艺适用于各种金属材料的制造,包括铝合金、镁合金、铜合金等,可以生产出不同材质的零部件,满足不同行业的需求。
7. 环保节能:一体化压铸工艺相对于传统的铸造和加工工艺,减少了能源消耗和废气废水的排放,对环境友好,符合可持续发展的要求。
一体化压铸工艺具有整体性强、精度高、节约材料、稳定性好、生产效率高、适用范围广、环保节能等特点。
随着科技的不断进步和工艺的不断革新,一体化压铸工艺在金属制造领域的应用将会越来越广泛,为各行各业提供高质量、高效率的产品制造解决方案。
模塑科技一体化压铸工艺流程

模塑科技一体化压铸工艺流程一、模具安装模具安装前,压铸工必须全面了解模具结构状况,包括:1、模具有无抽芯;动模抽芯,还是静模抽芯;滑块抽芯,还是液压抽芯。
2、是否需要安装复位杆。
3、浇口套大小,溶杯大小,结合尺寸是否一致。
4、是否中心浇口。
5、顶棒位置、大小、长短是否合适。
二、操作规范1、根据模具情况更换熔杯冲头,必要时调节压射升降机构。
2、检查动静模板,确保表面无异物、无高点。
3、正确安装吊具,在确定安全的情况下起吊,并确保模具进入机床前无摇动,以免撞伤机床。
4、根据模具情况,正确安装模具。
特别注意,带有液压抽芯的模具,必须将机床相对应抽芯状态调到“选择”并且抽芯在动模的,要调到“锁模前”插芯;抽芯在静模的,要调到“锁模后”插芯状态。
5、压紧模具,接好油管及冷却水管完成模具安装。
三、模具调试1、安装完毕后进行模具调试,装有抽芯器的先调试抽芯器,调试时必须注意。
2、严禁在动模未插芯到位及静模未抽芯到位时,合模。
3、严禁在静模插芯时,开模。
4、严禁动模抽芯器芯未抽芯到位时,顶出。
5、装有拉杆的模具,必须先调试顶出行程,拉杆未复到位严禁插芯或合模。
6、调节机床开档选择合适的锁模力。
7、调节压射跟出行程,检查冲头冷却水,确保无泄漏。
四、压铸生产1、压铸生产前,对模具型腔、顶杆、复位杆、导柱、导套、型芯、滑道等全面刷油。
2、在冷模状态下,在工艺无特除规定情况下应将机床二快和增压关闭。
3、根据零件重量,合理选择浇注量进行试压,并相应调节,确保料饼厚度。
4、模具在冷模状态下,多刷油少喷涂,模具热起来按正常喷涂料。
5、模具到了正常温度后,将二快和增压打开,按正常程序生产。
6、生产的首件产品,必须进行全面检查,作好记录,并保留由检验员检验。
7、在正常生产过程中,压铸工要根据压铸工艺要求,正确控制并及时调整如下要素:①喷涂②料温控制③模温控制④料饼厚度控制⑤分型面清理⑥滑动部位润滑。
8、在正常生产过程中,要按要求检查铸件质量,如有异常,及时停止生产做好修理或更换模具工作。
一体式压铸技术

一体式压铸技术
一体式压铸技术是一种高效、精确的金属成形工艺,它将压铸与机械加工相结合,实现了一次成型的目标。
本文将介绍一体式压铸技术的原理、应用领域以及优势。
一体式压铸技术是指将金属熔融后,直接注入模具中进行压铸,无需进行二次加工的一种工艺。
这种技术的关键在于模具的设计和制造,通过精确的模具设计,可以实现高精度、高质量的产品生产。
与传统的铸造和机械加工相比,一体式压铸技术具有以下几个优势。
一体式压铸技术可以实现复杂形状零件的生产。
由于模具的可塑性较高,可以制作出各种形状的模具,从而实现对复杂零件的一次成型。
这种技术在汽车、航空航天等领域的零件生产中得到广泛应用。
一体式压铸技术可以提高生产效率。
传统的铸造和机械加工需要多道工序,而一体式压铸技术可以将这些工序合并为一道,大大缩短了生产周期。
同时,由于模具的高精度和稳定性,可以实现高速生产,提高了生产效率。
一体式压铸技术可以提高产品质量。
由于一体式压铸技术可以实现高精度的成型,可以减少产品的尺寸误差和形状偏差,提高产品的一致性和稳定性。
此外,一体式压铸技术还可以减少材料的浪费,提高材料利用率。
一体式压铸技术还可以降低生产成本。
由于一体式压铸技术可以减少生产工序和材料浪费,可以降低生产成本。
同时,由于一体式压铸技术可以实现高效生产,可以减少人力投入,降低人工成本。
一体式压铸技术是一种高效、精确的金属成形工艺,具有复杂形状零件生产能力、高生产效率、优良产品质量以及低生产成本等优势。
随着科技的不断进步,一体式压铸技术在各个领域的应用将会越来越广泛。
一体式铝合金压铸简介

一体式铝合金压铸简介一体式铝合金压铸是一种高效、精密的金属成型工艺,广泛应用于制造汽车零部件、电子设备外壳、航空航天零件等领域。
本文将对一体式铝合金压铸的工艺流程、特点以及应用领域进行详细介绍。
1. 工艺流程a.模具设计与制造一体式铝合金压铸的第一步是设计和制造压铸模具。
模具设计需要考虑零件的几何形状、壁厚、冷却通道等因素,以确保最终产品的质量和精度。
b.铝合金熔化在压铸过程中,铝合金通常以固态铝或铝合金的形式供应。
通过将铝合金加热至液态,以便在压铸中充分流动并填充模具腔体。
c.注射与充填铝合金熔体被注射到事先设计好的模具腔体中。
注射过程需要确保熔体充分填充模具,并避免气体夹杂或其他缺陷。
d.冷却与固化一旦模具腔体内的铝合金被充填完毕,就需要进行冷却,使其迅速固化。
冷却过程的控制对于最终产品的质量至关重要。
e.脱模与后处理冷却后,成品可以从模具中取出。
一些产品可能需要进行后处理工艺,如去除余料、修磨、喷涂等,以满足最终产品的设计要求。
2. 特点与优势a.高精度与复杂性一体式铝合金压铸可实现高度精密的零件制造,包括复杂的几何形状、细小的结构和细节,从而提高产品的整体质量。
b.高强度与轻量化铝合金具有较高的强度和轻质化的特点,适用于要求强度与重量比的应用领域,如汽车和航空航天。
c.良好的表面质量一体式铝合金压铸可以在模具中实现光滑表面和细腻纹理,减少后续表面处理工序的需求。
d.高生产效率相比传统的铸造方法,压铸具有较快的生产周期,可以在短时间内大规模生产零部件,提高生产效率。
e.成本效益尽管模具制造和设备投资可能较高,但由于高生产效率和较少的后续加工需求,一体式铝合金压铸在大规模生产中通常具有成本效益。
3. 应用领域a.汽车工业一体式铝合金压铸在汽车工业中应用广泛,制造引擎零部件、车身结构、悬挂系统等。
b.电子与通讯电子设备外壳、散热器和其他电子零部件常使用一体式铝合金压铸技术。
c.航空航天由于铝合金的轻量和高强度,一体式铝合金压铸在航空航天领域用于制造飞机结构、发动机零件等。
轻量化材料一体化压铸成型技术方案(二)

轻量化材料一体化压铸成型技术方案一、实施背景随着全球能源短缺和环境污染问题的日益严重,汽车制造业正在寻求更加环保、高效的制造方式。
轻量化材料一体化压铸成型技术应运而生,成为汽车产业转型升级的关键技术之一。
二、工作原理轻量化材料一体化压铸成型技术结合了材料科学、机械工程、模具设计等多个学科领域的知识,采用高压铸造的方式,将多个零部件一次压铸成型,从而减少了生产过程中的繁琐工艺和模具成本。
具体工作原理如下:1.材料选择:选用轻量化材料,如铝合金、镁合金等,具有高强度、低密度的特点,可有效降低车身重量。
2.高压铸造:利用高压铸造机,将熔融状态的金属液体快速压入模具,填充模具的各个部分,形成复杂的零部件结构。
3.冷却定型:通过冷却系统将压铸件冷却定型,保证其尺寸稳定性。
4.取出清理:将压铸件从模具中取出,进行表面清理和修整。
三、实施计划步骤1.材料研发:与材料供应商合作,研发适用于一体化压铸成型的轻量化材料。
2.模具设计:根据产品需求,设计合理的模具结构,确定各部分的尺寸和形状。
3.设备选型:根据生产需求,选择合适的压铸机和辅助设备。
4.工艺调试:进行试制和调试,确定最佳的工艺参数,如压力、温度、时间等。
5.生产实施:按照调试好的工艺参数进行批量生产。
6.质量控制:建立完善的质量控制体系,确保产品质量符合要求。
四、适用范围轻量化材料一体化压铸成型技术适用于汽车制造业中的多个领域,如车身结构件、底盘零部件、发动机零部件等。
同时,也可应用于航空航天、电子设备等领域。
五、创新要点1.材料创新:研发新型轻量化材料,提高材料的综合性能,以满足一体化压铸成型的需求。
2.工艺创新:优化压铸工艺参数,提高生产效率和质量稳定性。
3.技术集成:将多个学科领域的技术进行集成,实现轻量化材料一体化压铸成型技术的整体优化。
4.生产管理创新:引入先进的生产管理理念和技术手段,提高生产效率和成本控制水平。
六、预期效果1.重量减轻:采用轻量化材料和一体化压铸成型技术,可有效降低产品重量,从而提高燃油经济性和减少碳排放。
铝的一体化压铸

铝的一体化压铸全文共四篇示例,供读者参考第一篇示例:铝的一体化压铸是一种先进的工艺技术,它将铸造和成型两个环节整合在一起,使得生产效率大大提高,产品质量也更加稳定。
一体化压铸技术在工业生产中得到了广泛应用,特别是在汽车零部件、电子产品、建筑材料等行业中发展迅猛。
本文将从技术原理、应用领域、发展趋势等方面介绍铝的一体化压铸技术。
一体化压铸技术是将铝及其合金加热熔化后,通过高压注射模具形成产品的工艺。
相比传统的压铸工艺,一体化压铸技术不仅可以将产品生产周期缩短,还可以减少成本、提高产品质量。
这是因为一体化压铸技术可以有效避免铸造过程中的气孔、热裂纹等缺陷,确保产品的一致性和稳定性。
一体化压铸技术还可以实现对产品结构和形状的精确控制,满足不同客户的需求。
铝的一体化压铸技术在汽车零部件、电子产品、建筑材料等行业中得到广泛应用。
在汽车行业中,一体化压铸技术可以制造轻量化、高强度的零部件,提高汽车的燃油效率和安全性。
在电子产品领域,一体化压铸技术可以生产小型、高精度的零部件,满足电子产品对轻量化和高性能的要求。
在建筑材料领域,一体化压铸技术可以制造形状复杂的构件,提高建筑物的整体性和美观性。
随着工业技术的不断进步,铝的一体化压铸技术也在不断创新和发展。
未来,一体化压铸技术将更加智能化、自动化,进一步提高产品的生产效率和质量。
一体化压铸技术还将广泛应用于更多的行业,为工业制造带来更大的变革和提升。
第二篇示例:铝的一体化压铸是一种先进的生产技术,能够将铝合金材料一次性压制成特定形状的工件。
通过一体化压铸技术,不仅可以降低生产成本,提高生产效率,而且可以提高产品质量,满足客户的需求。
本文将重点介绍铝的一体化压铸技术的工艺流程、特点及应用。
一、铝的一体化压铸技术的工艺流程铝的一体化压铸技术是指将铝合金材料加热至一定温度,然后注入模具中,通过高压铸造技术将铝液压制成特定形状的工件。
其工艺流程主要包括以下几个步骤:1. 材料准备:首先需要选用适合的铝合金材料,将其进行加热处理,以确保铝合金材料在一定温度下可流动性良好。
铝合金一体化压铸技术

铝合金一体化压铸技术【摘要】铝合金一体化压铸技术是一种高效的金属加工技术,通过压铸设备将铝合金熔融液注入模具中,经过高压铸造成型,实现一次成型并得到零件产品。
这种技术在汽车、航空航天、电子产品等领域有广泛的应用,其优势主要体现在生产效率高、产品质量好、设计自由度大等方面。
随着科技的不断发展,铝合金一体化压铸技术的工艺流程越来越完善,未来的发展趋势将更加智能化和自动化。
铝合金一体化压铸技术的未来发展具有重要意义,不仅可以提高生产效率,降低生产成本,还可以推动金属加工行业的发展。
铝合金一体化压铸技术的经济效益和重要性不言而喻。
随着技术的不断改进和应用领域的扩大,铝合金一体化压铸技术必将在未来发展出更广阔的市场。
【关键词】铝合金、一体化、压铸技术、原理、应用领域、优势、发展趋势、工艺流程、未来发展、重要性、经济效益1. 引言1.1 铝合金一体化压铸技术概述铝合金一体化压铸技术是一种先进的压铸工艺,将铝合金和其他金属或非金属材料一次性压制成型,实现了多种工艺的一体化,具有高效、省时、省力的特点。
该技术在制造业中被广泛应用,可用于汽车零部件、航空航天设备、通讯设备等领域。
铝合金一体化压铸技术的优势主要包括生产效率高、成本低、产品质量稳定等。
随着科技的不断进步和市场需求的变化,铝合金一体化压铸技术不断发展壮大,未来的发展趋势将更加智能化、自动化。
该技术的工艺流程主要包括模具设计、铸造工艺、静态与动态模具等环节。
铝合金一体化压铸技术在未来的发展中将发挥越来越重要的作用,不仅在经济上带来效益,而且在技术发展上也有着重要意义。
2. 正文2.1 铝合金一体化压铸技术的原理铝合金一体化压铸技术的原理是指将铝合金材料经过精密的合金配比,加热至一定温度后,通过高压注射成型,使铝合金在模具中快速冷却凝固,形成具有一定形状和尺寸的铝合金零件。
这一过程主要包括以下几个步骤:1. 铝合金材料处理:首先需要对铝合金进行合适的合金配比,以确保零件具有良好的力学性能和耐蚀性。
一体化压铸后道工序流程

一体化压铸后道工序流程
小伙伴们!今天咱们来说说一体化压铸后的道工序流程。
这一体化压铸啊,后面的工序可是相当重要的呢!
首先呢,压铸完了之后,得把压铸件从压铸机里取出来。
这一步可不能太粗暴哦,要小心一点。
我觉得呢,在取的时候,可以稍微检查一下外观有没有明显的缺陷,像那种大的裂痕啥的一眼就能看出来。
不过呢,也不用太仔细啦,毕竟后面还有工序会进一步检查的嘛。
接下来就是对压铸件进行初步的清理。
这清理呢,主要就是把表面一些大的杂质啊、残留的材料啊弄掉。
怎么清理呢?这就看具体情况啦,你可以用工具轻轻刮掉,也可以用风枪吹一吹。
根据我的经验呢,风枪吹的时候要注意角度,不然有些杂质可能吹不掉呢!
然后呢,可能就要进行切割或者修整的工序啦。
这时候要根据压铸件的实际需求来操作哦。
有时候可能需要把多余的部分切掉,这个时候就得小心别切多了或者切歪了。
要是不小心切坏了,那前面的功夫可就白费了,是不是?
再往后就是表面处理环节了。
这表面处理可就有很多种方式了。
可以进行打磨,让表面更光滑;也可以进行涂装,让它看起来更美观。
我觉得这一步可以更灵活一些,根据产品最后的用途来决定怎么做。
比如说,如果是内部零件,可能打磨一下就够了;但如果是外观件,那涂装就得好好搞一搞啦。
最后呢,就是包装入库啦。
包装的时候要选择合适的材料,保护好压铸件在运输和储存过程中不被损坏。
这个环节可以根据实际情况自行决定包装的方式哦。
一体化压铸 热处理

一体化压铸热处理
一体化压铸是指在压铸过程中,将热处理步骤整合进去,使得铸件在一次成型后即可完成热处理工艺。
这种工艺能够提高生产效率,缩短生产周期,并且能够保证铸件的性能和质量。
一体化压铸热处理工艺一般包括以下几个步骤:
1. 材料准备:选择合适的压铸材料,并进行预处理,如除油、除氧等。
2. 压铸成型:将预热好的材料注入到压铸模具中,进行压力成型,得到所需形状的铸件。
3. 热处理前处理:对铸件进行去毛刺、修整等处理,以便后续的热处理工艺进行。
4. 热处理:根据铸件的材料和要求,选择适当的热处理方法,如退火、淬火、时效等。
通过控制温度、时间等参数,改变铸件的组织结构和性能。
5. 表面处理:对热处理后的铸件进行酸洗、清洗、喷漆等表面处理,以提高外观质量和耐腐蚀性。
通过一体化压铸热处理工艺,可以大大简化生产流程,减少操作环节,提高生产效率和产品质量。
同时,还能够降低成本,并方便对产品进行质量控制和追溯。
轻量化材料一体化压铸成型技术方案(一)

轻量化材料一体化压铸成型技术方案一、实施背景随着全球能源短缺和环境污染问题的日益严重,汽车制造业正在寻求更加环保、高效的制造方式。
轻量化材料一体化压铸成型技术是一种具有革命性的技术,能够显著降低汽车制造成本和提高制造效率,同时也能有效降低车辆的重量,从而减少能源消耗和排放。
因此,轻量化材料一体化压铸成型技术已经成为汽车制造业的一个重要发展方向。
二、工作原理轻量化材料一体化压铸成型技术是一种先进的制造工艺,它将铝合金等轻量化材料通过高压注入模具中,在极短的时间内完成凝固和成型过程。
该技术主要包括以下几个步骤:1.熔炼:将铝合金等轻量化材料加热至熔融状态。
2.注射:将熔融的铝合金等轻量化材料通过高压注射到模具中。
3.成型:在高压作用下,熔融的铝合金等轻量化材料快速凝固并形成产品。
4.脱模:将产品从模具中取出。
5.修整:对产品进行必要的修整和检测。
三、实施计划步骤1.确定轻量化材料:选择适合一体化压铸成型的轻量化材料,如铝合金等。
2.设计模具:根据产品要求,设计合适的模具。
3.安装设备:安装高压注射设备、熔炼设备、冷却设备等必要的设备。
4.调试工艺:对模具和设备进行调试,确保工艺的可行性。
5.试生产:进行小批量试生产,验证产品的质量和生产的稳定性。
6.优化工艺:根据试生产的结果,对工艺进行优化和改进。
7.正式生产:在确保产品质量和生产稳定性的前提下,进行正式生产。
四、适用范围轻量化材料一体化压铸成型技术适用于各种汽车零部件的制造,特别是那些形状复杂、尺寸较大、数量较多的零部件,如汽车发动机缸体、变速器壳体、车桥壳体等。
该技术的优点是可以大幅度提高生产效率,降低制造成本,同时可以减少生产过程中的废料和能源消耗。
此外,由于采用轻量化材料,还可以有效减轻产品重量,从而降低车辆的能耗和排放。
因此,轻量化材料一体化压铸成型技术在汽车制造业具有广泛的应用前景。
据预测,到2025年,全球轻量化材料一体化压铸成型技术的市场规模将达到300亿美元以上。
一体压铸工艺

一体压铸工艺
一体压铸工艺
一体压铸工艺是一种铸造工艺,可以以一体成型的方式生产铸件,且采用热加工或热处理的工艺。
一体压铸工艺可以将铸造和热处理结合在一起,在热处理过程中,可以改善零件的耐磨性、硬度、材料密度等属性,提高零件的使用性能和使用寿命。
与传统铸造工艺相比,一体压铸工艺有很多优点,其中包括:
1、可提高铸件的性能:采用一体压铸工艺制作的零件可以充分
利用各种热加工或热处理的工艺,改善其耐磨性、硬度及材料密度等性能,从而提高铸造件的使用性能和使用寿命。
2、可减少零件缺陷:采用一体压铸工艺可以有效减少铸件缺陷,减少焊接接头缝隙,增强焊接强度,同时减少焊接接头的杂质,确保零件的质量。
3、可减少加工成本:一体压铸工艺具有较高的加工效率,压铸
机行进速度较快,能够大幅度节省加工成本。
4、可提高设备生产效率:一体压铸工艺不仅可以完成一体成型
的铸件,还可以大幅度提高设备的生产效率,更快速地完成产品制造。
一体压铸工艺在铸造工艺中应用越来越广泛,它的优点使其成为现代铸造行业的首选工艺。
因此,在广泛应用一体压铸工艺时,应加强相关研究,充分利用其优势,以提高设备的加工效率,提高产品质量和使用性能。
- 1 -。
一体化压铸工艺

一体化压铸工艺
一体化压铸本质上属于高压铸造工艺。
2019 年以前压铸机锁模力通常在400-5000吨不等,汽车高压铸造工艺主要应用于发动机系统、变速箱系统、离合器等精密件,以及横梁、纵梁、减震塔等车身结构件。
一体化压铸指的是车身件的一体化,即原本设计中多个单独、分散的小件经过重新设计高度集成,再利用压铸机进行一次成型,省略焊接的过程直接得到一个完整大零件,一体化车身件尺寸大、材料特殊、模具复杂、制造工艺难度较高,需要大吨位压铸机进行生产。
高压压铸工艺包括合模、射料、回锤、冷却、充氮气(惰性气体)、离嘴开模、顶出、顶回等步骤。
当压铸生产时,先将熔融的液态铝合金倒入压铸机的压射机构内,压射机构将铝液快速推入模具内并加压成型,通过模具内的冷却系统将铝合金零件快速冷却至固态,最后模具打开由机器手取出零件、清理喷涂脱模剂再进行下一循环生产,整个生产过程温度极高、烟气多、噪音大,业内通常使用自动化生产。
一体压铸概念

一体压铸概念
一体压铸是一种高效的金属成型工艺,通过在单个工艺过程中完成金属的熔化、注射和固化,以一次成形的方式制造高质量的铝合金、镁合金等金属零件。
它是一种综合了铸造和成型两种传统工艺的新型加工技术。
一体压铸的原理是将金属材料通过高温和高压的作用,使其熔化并注入压铸模具中,然后在模具中固化成型。
与传统的压铸工艺相比,一体压铸具有以下优点:
优良的材料性能:一体压铸工艺可以使金属材料在熔融状态下达到高压状态,从而可以获得优良的材料性能和高密度的组织结构。
减少生产流程:一体压铸可以在单个工艺过程中完成铸造和成型,减少了多次处理的时间和成本,提高了生产效率和产品质量。
可以制造复杂零件:一体压铸可以通过模具的设计和优化,制造出复杂形状、高精度的金属零件,从而满足市场对高质量零件的需求。
环保节能:一体压铸工艺使用的是金属熔化和固化的自然热能,而不需要外部能源的输入,因此可以有效地减少能源消耗和环境污染。
综上所述,一体压铸是一种高效、环保、节能的金属加工技术,具有制造高质量零件、减少生产流程、制造复杂零件和保护环境等多重优点,正越来越受到工业界的广泛关注和应用。
特斯拉一体压铸成型工艺

特斯拉一体压铸成型工艺
特斯拉模具一体化制备技术是一种先进的高科技生产工艺。
该技术采用CAD/CAM技术
和CNC加工设备制备模具。
模具的一体化结构设计在模具结构上可以实现多种功能集成,
为汽车零部件的制造提供了可靠的保证。
该技术在汽车零部件加工制造中应用广泛,在特
斯拉汽车的制造中也得到了广泛的应用。
在特斯拉汽车中,一些汽车部件加工复杂度很高,需要一体成型的加工工艺。
例如,
特斯拉旗下的Model S,Model X和Model Y车型都采用了一种采用铝合金一体成型技术生产的电池盒。
该电池盒采用了特斯拉自己的一体化压铸工艺来生产。
特斯拉一体压铸成型技术在汽车制造中可以用于制造高强度、耐磨、耐腐蚀、抗变形
的汽车组件。
该技术将铝合金压铸成型和CNC机器加工一体化,具有成型速度快、成本低、生产周期短、产品精度高等优点。
特斯拉一体压铸成型工艺的核心是合理设定合金比例,并通过铸造工艺进行一体成型。
这种一体化成型工艺在汽车生产中具有很高的精度和效率。
该工艺的实现需要从材料选择、模具制造、模具使用、铸件设计和加工等方面进行细致的考虑。
在特斯拉汽车的生产中,这种一体化加工工艺已经得到了大规模的应用。
特斯拉汽车中,很多零部件都采用了这种一体化成型技术。
例如,电池组件、动力总成、底盘部件、
车身结构件等都采用了该工艺。
该工艺的使用使得汽车零部件的制造达到了更高的效率、
更高的精度和更高的质量。
总之,特斯拉一体压铸成型工艺是一种领先的汽车制造技术,其在提高汽车零部件制
造效率、提高产品精度和产品质量上具有很大的优势。
一体化压铸深度研究报告

一体化压铸深度研究报告一体化压铸是指将压铸工艺与其他加工工艺相结合,实现对铝合金零件的一体成型加工。
随着科技的不断进步和制造业的发展,一体化压铸在近年来得到了越来越广泛的应用。
本文将从一体化压铸的定义、工艺流程、优势和存在的问题等方面进行深入研究。
一、一体化压铸的定义一体化压铸是指在压铸过程中结合其他加工工艺,实现对铝合金零件的一体成型加工。
传统的压铸工艺只能够对铝合金进行形状的加工,而一体化压铸相对于传统压铸来说,在形状加工的同时还可以实现其他加工工艺,如钻孔、铣削、螺纹加工等。
二、一体化压铸的工艺流程一体化压铸的工艺流程包括模具准备、原料制备、合金熔炼、压铸成型、二次加工等环节。
首先,需准备好压铸模具,包括模具设计、制造和调试等工作。
然后,进行原料的制备,主要是将铝合金材料按照一定配比进行混合,并在合金的熔炼过程中加入适量的添加剂。
接下来,将熔化的铝合金倒入压铸机的加热沙坛中,通过压铸机的压力将铝合金充填到模具腔中,并进行冷却。
最后,进行二次加工,如切割、打磨、孔加工等,以得到最终的产品。
三、一体化压铸的优势1.提高生产效率:一体化压铸相对于传统压铸来说,可以在形状加工的同时实现其他加工工艺,减少了生产环节,提高了生产效率。
2.降低生产成本:通过一体化压铸可以减少设备、人力等资源的使用,降低了生产成本。
3.提高产品质量:一体化压铸可以避免由于多道工序带来的加工误差,提高了产品的一致性和精度。
4.减少废品率:一体化压铸的工艺中能够对铝合金进行一次成型,减少了铝合金的浪费和废品率。
四、一体化压铸存在的问题1.技术难度大:一体化压铸需要将多个加工工艺相结合,对技术人员的要求较高,技术难度相对较大。
2.设备投资较高:一体化压铸需要采购配套的设备和工具,投资成本较传统压铸要高一些。
3.模具设计复杂:一体化压铸需要根据产品的形状、尺寸等要求进行模具设计,设计复杂度较高。
综上所述,一体化压铸是将压铸工艺与其他加工工艺相结合,实现对铝合金零件的一体成型加工。
一体式压铸技术
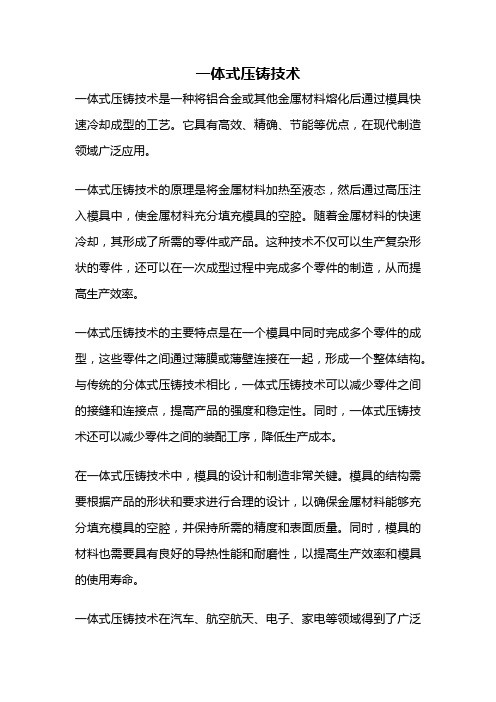
一体式压铸技术一体式压铸技术是一种将铝合金或其他金属材料熔化后通过模具快速冷却成型的工艺。
它具有高效、精确、节能等优点,在现代制造领域广泛应用。
一体式压铸技术的原理是将金属材料加热至液态,然后通过高压注入模具中,使金属材料充分填充模具的空腔。
随着金属材料的快速冷却,其形成了所需的零件或产品。
这种技术不仅可以生产复杂形状的零件,还可以在一次成型过程中完成多个零件的制造,从而提高生产效率。
一体式压铸技术的主要特点是在一个模具中同时完成多个零件的成型,这些零件之间通过薄膜或薄壁连接在一起,形成一个整体结构。
与传统的分体式压铸技术相比,一体式压铸技术可以减少零件之间的接缝和连接点,提高产品的强度和稳定性。
同时,一体式压铸技术还可以减少零件之间的装配工序,降低生产成本。
在一体式压铸技术中,模具的设计和制造非常关键。
模具的结构需要根据产品的形状和要求进行合理的设计,以确保金属材料能够充分填充模具的空腔,并保持所需的精度和表面质量。
同时,模具的材料也需要具有良好的导热性能和耐磨性,以提高生产效率和模具的使用寿命。
一体式压铸技术在汽车、航空航天、电子、家电等领域得到了广泛应用。
例如,在汽车制造中,一体式压铸技术可以用于生产发动机缸盖、底盘零件、车身结构等;在电子行业,一体式压铸技术可以用于生产电脑外壳、手机壳体等。
这些应用不仅满足了产品的外观要求,还提高了产品的性能和质量。
尽管一体式压铸技术具有许多优点,但也存在一些挑战。
首先,模具的制造和维护成本较高,对技术和设备要求较高。
其次,一体式压铸技术在处理大型零件时存在一定的困难,需要解决金属液流动性差和冷却不均匀等问题。
此外,一体式压铸技术还需要解决金属氧化、气孔、缩松等缺陷问题,以提高产品的质量。
一体式压铸技术是一种高效、精确、节能的金属加工技术。
它通过一次成型过程,将金属材料快速冷却成型,生产出复杂形状的零件和产品。
在现代制造领域的广泛应用中,一体式压铸技术不仅提高了生产效率,还提高了产品的质量和性能。
一体压铸连接方案

一体压铸连接方案一体压铸连接方案是一种常见的连接方式,广泛应用于各个行业。
它的主要特点是将两个或多个零部件通过压铸成型的方式,使其形成一个整体。
这种连接方式不仅可以提高产品的整体性能和稳定性,还可以减少零部件之间的接缝和连接处的松动问题,从而提高产品的使用寿命和可靠性。
一体压铸连接方案的实施过程通常包括以下几个步骤:第一步,设计和制造模具。
在进行一体压铸连接之前,需要先设计和制造适合的模具。
模具的设计要考虑到连接部位的形状和尺寸,以及零部件的材料和厚度等因素。
模具制造完成后,需要经过严格的检查和测试,确保其质量和精度达到要求。
第二步,准备原材料。
一体压铸连接通常使用金属材料,如铝合金、铜合金等。
在进行一体压铸之前,需要准备好符合要求的原材料,并进行必要的加工和处理,以确保其质量和性能符合要求。
第三步,进行压铸连接。
在进行一体压铸连接之前,需要将待连接的零部件放置在模具的合适位置,然后施加适当的压力,使其形成一个整体。
在压铸过程中,需要控制好温度、时间和压力等参数,以确保连接质量和效果。
第四步,进行后续处理。
一体压铸连接完成后,需要进行一些后续处理工作,如去除多余的材料、加工表面、清洁和喷涂等。
这些工作旨在进一步提高连接的质量和外观。
一体压铸连接方案的应用范围非常广泛。
在汽车制造业中,一体压铸连接常用于发动机和底盘等关键部位,以提高整车的稳定性和安全性。
在航空航天领域,一体压铸连接可以减少零部件的重量和接缝,提高飞行器的性能和燃油效率。
在电子电气领域,一体压铸连接可以提高产品的散热性能和抗干扰能力,提高产品的可靠性和稳定性。
一体压铸连接方案的优势在于能够减少零部件之间的接缝和连接处的松动问题,提高产品的整体性能和稳定性。
与传统的连接方式相比,一体压铸连接更加紧密和牢固,可以提高产品的使用寿命和可靠性。
此外,一体压铸连接还可以减少产品的重量和体积,提高产品的性能和效率。
因此,一体压铸连接方案在各个行业中得到了广泛的应用和推广。
- 1、下载文档前请自行甄别文档内容的完整性,平台不提供额外的编辑、内容补充、找答案等附加服务。
- 2、"仅部分预览"的文档,不可在线预览部分如存在完整性等问题,可反馈申请退款(可完整预览的文档不适用该条件!)。
- 3、如文档侵犯您的权益,请联系客服反馈,我们会尽快为您处理(人工客服工作时间:9:00-18:30)。
一体压铸工艺
一体压铸工艺是一种将金属或其他材料一次性压铸成形的工艺。
它是在传统压铸技术的基础上发展而来的。
与传统压铸相比,一体压铸具有更高的生产效率和更好的产品质量。
一体压铸工艺的基本流程包括:原料准备、模具设计、熔炼铸造、冷却、去毛刺、加工和表面处理等步骤。
其中,模具设计是关键步骤之一。
模具的质量将影响到产品的精度和表面质量。
一体压铸的模具通常由多个部分组成,包括模座、模芯、浇口、冷却系统等。
这些部分需要精密加工,以确保模具的高精度和长寿命。
在一体压铸工艺中,原材料通常是金属合金或高性能材料,如铝合金、镁合金、锌合金等。
这些材料具有高强度、耐腐蚀性和良好的导热性能,适合于一体压铸工艺的要求。
一体压铸的主要优点是可以一次性完成铸造、冷却、去毛刺和加工等多个步骤,从而节省了生产时间和成本。
此外,一体压铸还可以生产出更加复杂和精密的零件,如汽车发动机缸体、摩托车发动机壳体、电子设备外壳等。
在一体压铸中,熔炼铸造是关键步骤之一。
熔炼铸造需要控制好熔炼温度、熔炼时间和熔炼材料的比例等参数,以确保铸件的质量。
铸件的质量将影响到产品的性能和寿命。
一体压铸中还需要进行冷却和去毛刺等步骤,以消除铸件表面的缺陷和毛刺,提高产品的表面质量。
一体压铸工艺还需要进行后续的加工和表面处理等步骤。
加工包括铣削、钻孔、螺纹加工等,以形成最终的产品形态。
表面处理包括喷漆、喷砂、电泳涂装等,以提高产品的外观和耐腐蚀性能。
一体压铸工艺是一种高效、精密、高质量的制造工艺。
它可以生产出各种复杂和精密的零件,具有广泛的应用前景。
在未来,一体压铸工艺将在各个领域得到广泛的应用,为人们的生产和生活带来更多的便利和创新。