Biomass Resources for Producing Renewable Power and Fuels 用于生产可再生电力与燃料的生物质资源
关于新能源的作文英语
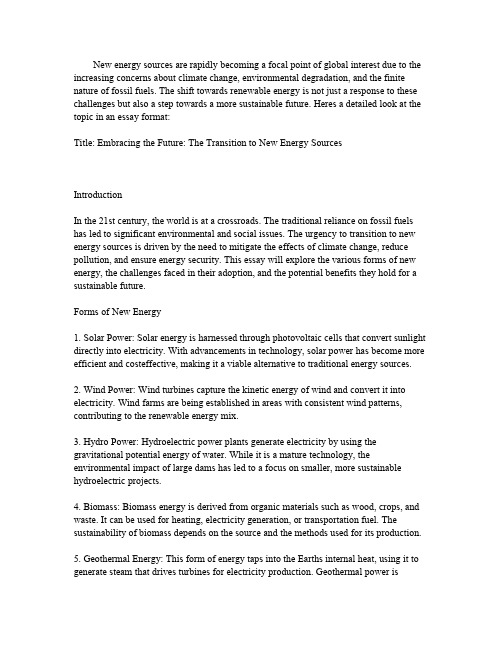
New energy sources are rapidly becoming a focal point of global interest due to the increasing concerns about climate change,environmental degradation,and the finite nature of fossil fuels.The shift towards renewable energy is not just a response to these challenges but also a step towards a more sustainable future.Heres a detailed look at the topic in an essay format:Title:Embracing the Future:The Transition to New Energy SourcesIntroductionIn the21st century,the world is at a crossroads.The traditional reliance on fossil fuels has led to significant environmental and social issues.The urgency to transition to new energy sources is driven by the need to mitigate the effects of climate change,reduce pollution,and ensure energy security.This essay will explore the various forms of new energy,the challenges faced in their adoption,and the potential benefits they hold for a sustainable future.Forms of New Energy1.Solar Power:Solar energy is harnessed through photovoltaic cells that convert sunlight directly into electricity.With advancements in technology,solar power has become more efficient and costeffective,making it a viable alternative to traditional energy sources.2.Wind Power:Wind turbines capture the kinetic energy of wind and convert it into electricity.Wind farms are being established in areas with consistent wind patterns, contributing to the renewable energy mix.3.Hydro Power:Hydroelectric power plants generate electricity by using the gravitational potential energy of water.While it is a mature technology,the environmental impact of large dams has led to a focus on smaller,more sustainable hydroelectric projects.4.Biomass:Biomass energy is derived from organic materials such as wood,crops,and waste.It can be used for heating,electricity generation,or transportation fuel.The sustainability of biomass depends on the source and the methods used for its production.5.Geothermal Energy:This form of energy taps into the Earths internal heat,using it to generate steam that drives turbines for electricity production.Geothermal power isreliable and has a low environmental impact,although its feasibility is dependent on geological conditions.Challenges in AdoptionCost:Despite the falling costs,the initial investment for new energy technologies can still be prohibitive,particularly for developing countries.Infrastructure:The existing energy infrastructure is largely designed for fossil fuels, requiring significant changes to accommodate new energy sources. Intermittency:Renewable energy sources like solar and wind are subject to variability, which poses challenges for grid stability and energy storage.Public Perception:There is a need for increased public awareness and acceptance of new energy technologies to facilitate their widespread adoption.Benefits of New EnergyEnvironmental Impact:New energy sources produce little to no greenhouse gas emissions,contributing to the fight against climate change.Energy Security:Diversifying energy sources can reduce dependence on foreign oil and enhance a countrys energy security.Economic Opportunities:The new energy sector is creating jobs and stimulating economic growth,particularly in the manufacturing and installation of renewable energy systems.Health Benefits:Reducing reliance on fossil fuels can lead to improved air quality and public health,particularly in urban areas.ConclusionThe transition to new energy sources is not just an environmental imperative but also an economic and social one.As the world moves towards a more sustainable future,the role of new energy sources will only grow in importance.With continued innovation, investment,and policy support,the challenges can be overcome,and the benefits realized, paving the way for a cleaner,more secure,and prosperous future.This essay provides a comprehensive overview of the topic,highlighting the importance of new energy sources in the context of global sustainability efforts.。
生物制氢 发酵工艺流程
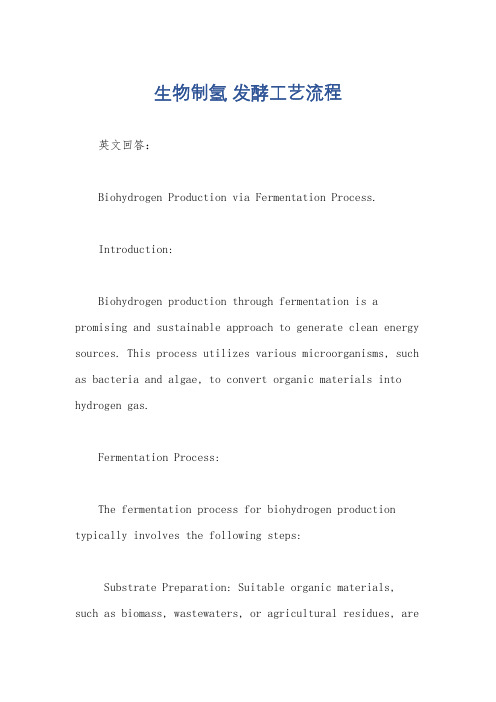
生物制氢发酵工艺流程英文回答:Biohydrogen Production via Fermentation Process.Introduction:Biohydrogen production through fermentation is a promising and sustainable approach to generate clean energy sources. This process utilizes various microorganisms, such as bacteria and algae, to convert organic materials into hydrogen gas.Fermentation Process:The fermentation process for biohydrogen production typically involves the following steps:Substrate Preparation: Suitable organic materials, such as biomass, wastewaters, or agricultural residues, arepre-processed to optimize their biodegradability.Fermentation: The substrate is fermented in an anaerobic environment, typically using a mixed culture of microorganisms or specific bacterial strains. During this stage, the organic matter is converted into intermediate compounds, including volatile fatty acids (VFAs).Hydrogen Production: Specialized microorganisms, such as hydrogen-producing bacteria, utilize the VFAs as substrates to produce hydrogen gas through anaerobic fermentation.Gas Separation: The produced hydrogen gas is separated from other fermentation gases, such as methane and carbon dioxide, using techniques like membrane filtration or pressure swing adsorption (PSA).Advantages of Fermentation Process:Renewable and Sustainable: Uses organic waste materials as substrates, reducing greenhouse gas emissionsand promoting waste management.High Hydrogen Yield: Can achieve relatively high hydrogen yields compared to other bio-production methods.Cost-Effective: Fermentation processes can be more economical than other hydrogen production technologies, especially when utilizing inexpensive biomass resources.Environmentally Friendly: Produces hydrogen gas as a clean energy source, reducing air pollution and promoting carbon neutrality.Challenges and Considerations:Substrate Availability: Securing a reliable and sustainable supply of organic substrates can be challenging.Process Efficiency: Optimizing fermentation conditions, such as pH, temperature, and inoculum composition, iscrucial for maximizing hydrogen production efficiency.Hydrogen Purification: Removing impurities and separating hydrogen from other fermentation gases can be energy-intensive and require advanced separation technologies.Long-Term Stability: Maintaining stable microbial communities and fermentation conditions over prolonged periods can be challenging.Future Research Directions:Ongoing research efforts focus on improving the fermentation process for biohydrogen production. Key areas include:Substrate Optimization: Identifying and pretreating suitable biomass feedstocks to enhance hydrogen yields.Microbial Engineering: Developing genetically modified microorganisms with enhanced hydrogen production capabilities.Process Integration: Exploring innovative approaches to combine fermentation with other technologies, such as dark fermentation and photofermentation.Scale-Up and Commercialization: Demonstrating the feasibility and economic viability of large-scale biohydrogen production systems.中文回答:生物制氢发酵工艺流程。
biomass
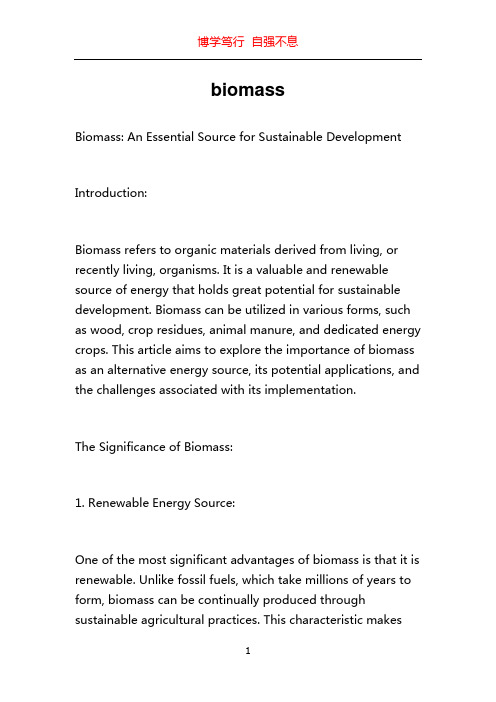
biomassBiomass: An Essential Source for Sustainable DevelopmentIntroduction:Biomass refers to organic materials derived from living, or recently living, organisms. It is a valuable and renewable source of energy that holds great potential for sustainable development. Biomass can be utilized in various forms, such as wood, crop residues, animal manure, and dedicated energy crops. This article aims to explore the importance of biomass as an alternative energy source, its potential applications, and the challenges associated with its implementation.The Significance of Biomass:1. Renewable Energy Source:One of the most significant advantages of biomass is that it is renewable. Unlike fossil fuels, which take millions of years to form, biomass can be continually produced through sustainable agricultural practices. This characteristic makesbiomass a key component in the quest for reducing carbon emissions and combating climate change.2. Energy Diversification:Biomass offers diversification in energy sources, reducing dependence on fossil fuels. By using biomass for electricity generation, heating, and transportation fuels, countries can improve energy security and reduce their reliance on imported energy. This diversification also helps mitigate the price volatility often associated with fossil fuels.3. Waste Management:Biomass utilization plays a crucial role in waste management. By converting organic waste into energy, biomass systems can reduce the burden on landfills and prevent the release of harmful greenhouse gases during decomposition. This not only minimizes environmental pollution but also provides a sustainable solution for waste disposal.Applications of Biomass:1. Heat and Power Generation:Biomass can be used to produce heat and electricity through various technologies, such as combustion, gasification, and anaerobic digestion. Biomass power plants generate electricity by burning biomass to produce steam, which drives a turbine connected to a generator. Heat generated during this process can be utilized for district heating systems or industrial processes, making biomass a versatile energy source.2. Biofuels:Biomass can be converted into liquid biofuels, such as ethanol and biodiesel, which are used as alternatives to fossil fuels. Ethanol, produced by fermenting sugars present in biomass, is commonly blended with gasoline to reduce carbon emissions. Biodiesel, derived from vegetable oils or animal fats, can be directly used in diesel engines or blended with petroleum diesel. Biofuels offer a cleaner and more sustainable option for transportation, reducing greenhouse gas emissions and enhancing energy security.3. Biorefineries:Biomass can be processed in biorefineries to obtain a range of value-added products, such as chemicals, materials, and bio-based products. Biorefineries integrate various conversion technologies to extract maximum value from different biomass feedstocks. This approach utilizes a holistic approach to biomass utilization, creating a sustainable and efficient industry.Challenges and Opportunities:1. Resource Availability:The sustainable utilization of biomass requires careful consideration of resource availability. It is crucial to ensure that biomass is sourced responsibly, without causing deforestation or compromising food security. Sustainable biomass management practices, such as planting dedicated energy crops and utilizing agricultural residues, can help overcome these challenges.2. Technological Advancements:To maximize the potential of biomass, ongoing research and development are essential. Technological advancements are needed to improve biomass conversion processes, enhance efficiency, and reduce costs. Innovation in areas such as pretreatment, fermentation, and thermochemical conversion can significantly improve the viability of biomass as an energy source.3. Policy Support:Governments play a vital role in promoting the adoption of biomass as an energy source. Policy support, such as feed-in tariffs, tax incentives, and research funding, can encourage investment in biomass projects and create a favorable market environment. Clear and supportive policies also help overcome barriers and promote the widespread use of biomass.Conclusion:Biomass is a valuable and renewable resource with immense potential for sustainable development. Its utilization offers numerous advantages, including being a renewable energy source, waste management solution, and diversifying the energy mix. Biomass can be applied in various forms, rangingfrom heat and power generation to biofuels and biorefineries. While challenges related to resource availability and technological advancements exist, with supportive policies and continued research, biomass can contribute significantly to a cleaner and more sustainable future.。
外文翻译--稻草到能源--它可能是个有价值的尝试
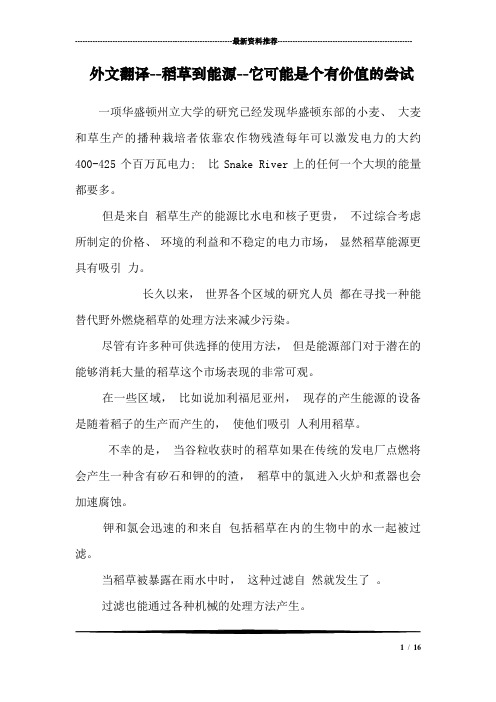
---------------------------------------------------------------最新资料推荐------------------------------------------------------ 外文翻译--稻草到能源--它可能是个有价值的尝试一项华盛顿州立大学的研究已经发现华盛顿东部的小麦、大麦和草生产的播种栽培者依靠农作物残渣每年可以激发电力的大约400-425个百万瓦电力; 比Snake River上的任何一个大坝的能量都要多。
但是来自稻草生产的能源比水电和核子更贵,不过综合考虑所制定的价格、环境的利益和不稳定的电力市场,显然稻草能源更具有吸引力。
长久以来,世界各个区域的研究人员都在寻找一种能替代野外燃烧稻草的处理方法来减少污染。
尽管有许多种可供选择的使用方法,但是能源部门对于潜在的能够消耗大量的稻草这个市场表现的非常可观。
在一些区域,比如说加利福尼亚州,现存的产生能源的设备是随着稻子的生产而产生的,使他们吸引人利用稻草。
不幸的是,当谷粒收获时的稻草如果在传统的发电厂点燃将会产生一种含有矽石和钾的的渣,稻草中的氯进入火炉和煮器也会加速腐蚀。
钾和氯会迅速的和来自包括稻草在内的生物中的水一起被过滤。
当稻草被暴露在雨水中时,这种过滤自然就发生了。
过滤也能通过各种机械的处理方法产生。
1 / 16无论如何,对于能够得出在燃烧中能导致的较高的灰熔性温度和较低的碱和卤素的挥发,这一结果本身就是一个显著的进步。
通过过滤燃烧稻草这种进步已经成功的在实验室里得到证明。
华盛顿东部的栽培者生产小麦、大麦和草种子等丰富农作物。
依照这样下来,他们生产了数以百万计的大量的稻草。
多余的农作物残渣能导致农作物产量减少,繁殖更多对农作物有害之物, 而且为种植下一轮农作物形成一个障碍。
多余的农作物残渣的处理, 尤其在田地最多的乡村中,确实是一个问题。
秸秆焚烧, 过去大多数的解决方法, 不再被社会所接受。
生物柴油 biodiesel=
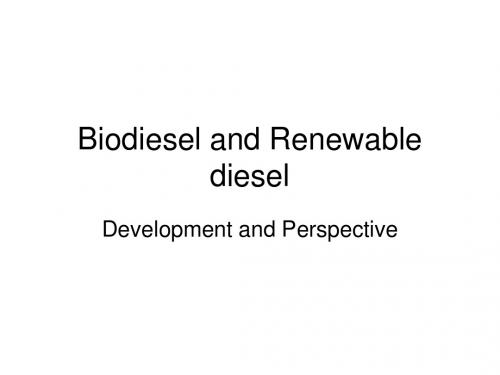
Incentives for Biofuel
• Potential impact of biofuels
– Energy supply – Refining industry
• Biofuels issues
– – – – Sustainability Financial Environmental Social
Perspective
Increases Availability, Reduces Feedstock Cost Technology Breakthroughs Required
Perspectives for future energy
MBPD-Million Barrels Per Day 万桶(一桶为159升 )
• With fast pyrolysis biomass waste is rapidly hporized, and then condensed into liquid fuel. Its heating value is 40% of diesel by weight and 55% by volume.
Coal to liquid (CTL) Biomass-to-liquid (BTL) Gas-to-liquid (GTL)
Jennifer Holmgren, Biofuels:Unlocking The Potential, ERTC 12th Annual Meeting Barcelona, Spain 19-21 November, 2007
What’s Biomass
•
•
•
Biomass is regenerative再生的organic material used for energy production. Sources for biomass fuel include terrestrial 陆生 and aquatic 水生vegetation, agricultural and forestry residues, and municipal and animal wastes. Biomass can be converted into solid, liquid or gaseous energy sources, which allows a wide range of applications. It can be: – burned directly to produce heat and/or electricity, – converted biochemically to produce liquid fuel; – digested or gasified to produce gaseous fuel; and finally, – pyrolized to produce oils and high value chemicals. Some examples of bioproducts in Canada are: – bio-diesel; – ethanol; – industrial plant-based oil products (such as fertilizers, plastics); – plant-made industrial products (such as composites); – modified proteins; – adhesives and resins; – solvents and lubricants.(溶剂、润滑剂)
英语作文 绿色生活
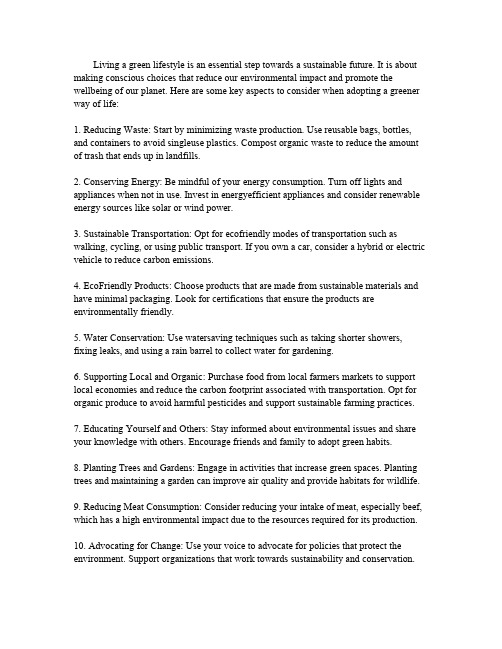
Living a green lifestyle is an essential step towards a sustainable future.It is about making conscious choices that reduce our environmental impact and promote the wellbeing of our planet.Here are some key aspects to consider when adopting a greener way of life:1.Reducing Waste:Start by minimizing waste e reusable bags,bottles, and containers to avoid singleuse post organic waste to reduce the amount of trash that ends up in landfills.2.Conserving Energy:Be mindful of your energy consumption.Turn off lights and appliances when not in use.Invest in energyefficient appliances and consider renewable energy sources like solar or wind power.3.Sustainable Transportation:Opt for ecofriendly modes of transportation such as walking,cycling,or using public transport.If you own a car,consider a hybrid or electric vehicle to reduce carbon emissions.4.EcoFriendly Products:Choose products that are made from sustainable materials and have minimal packaging.Look for certifications that ensure the products are environmentally friendly.5.Water Conservation:Use watersaving techniques such as taking shorter showers, fixing leaks,and using a rain barrel to collect water for gardening.6.Supporting Local and Organic:Purchase food from local farmers markets to support local economies and reduce the carbon footprint associated with transportation.Opt for organic produce to avoid harmful pesticides and support sustainable farming practices.cating Yourself and Others:Stay informed about environmental issues and share your knowledge with others.Encourage friends and family to adopt green habits.8.Planting Trees and Gardens:Engage in activities that increase green spaces.Planting trees and maintaining a garden can improve air quality and provide habitats for wildlife.9.Reducing Meat Consumption:Consider reducing your intake of meat,especially beef, which has a high environmental impact due to the resources required for its production.10.Advocating for Change:Use your voice to advocate for policies that protect the environment.Support organizations that work towards sustainability and conservation.By integrating these practices into your daily life,you contribute to a healthier planet and inspire others to do the same.Remember,every small action counts in the pursuit of a greener world.。
生物质燃料开发
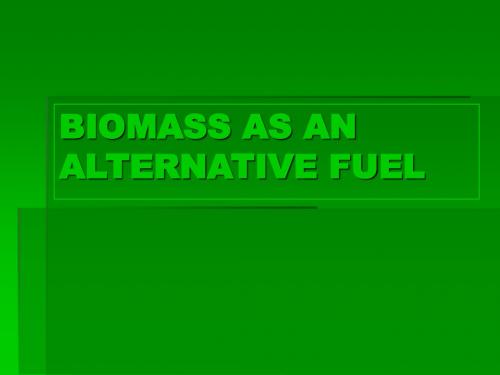
Environmental Benefits
(cont.)
Use of waste that would normally go to landfills. An estimated 350 million tons of waste that goes to landfills could be used for energy production Encourages the preservation of agricultural land that would otherwise be sold for development. Encourages sustainable agricultural techniques for bioenergy crops.
New Ethanol Technologies
Currently, research is being conducted for making ethanol from the cellulose (fiber) component in biomass, like municipal solid wastes and agricultural residues. This type of ethanol is called bioethanol. The use of bioethanol reduces the emission of carbon monoxide and hydrocarbons.
What is Bioenergy?
The energy stored in biomass is called bioenergy. Bioenergy is very versatile: It can be used to provide heat, make fuels, and generate electricity. Many bioenergy sources are replenished through the cultivation of fast growing grasses, trees, and agricultural residues like vegetable oils, wheat straw, or corn.
Biomass Energy Conversion
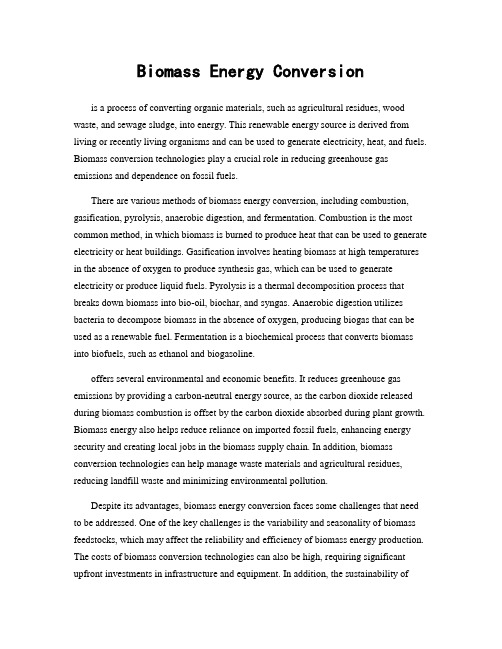
Biomass Energy Conversionis a process of converting organic materials, such as agricultural residues, wood waste, and sewage sludge, into energy. This renewable energy source is derived from living or recently living organisms and can be used to generate electricity, heat, and fuels. Biomass conversion technologies play a crucial role in reducing greenhouse gas emissions and dependence on fossil fuels.There are various methods of biomass energy conversion, including combustion, gasification, pyrolysis, anaerobic digestion, and fermentation. Combustion is the most common method, in which biomass is burned to produce heat that can be used to generate electricity or heat buildings. Gasification involves heating biomass at high temperatures in the absence of oxygen to produce synthesis gas, which can be used to generate electricity or produce liquid fuels. Pyrolysis is a thermal decomposition process that breaks down biomass into bio-oil, biochar, and syngas. Anaerobic digestion utilizes bacteria to decompose biomass in the absence of oxygen, producing biogas that can be used as a renewable fuel. Fermentation is a biochemical process that converts biomass into biofuels, such as ethanol and biogasoline.offers several environmental and economic benefits. It reduces greenhouse gas emissions by providing a carbon-neutral energy source, as the carbon dioxide released during biomass combustion is offset by the carbon dioxide absorbed during plant growth. Biomass energy also helps reduce reliance on imported fossil fuels, enhancing energy security and creating local jobs in the biomass supply chain. In addition, biomass conversion technologies can help manage waste materials and agricultural residues, reducing landfill waste and minimizing environmental pollution.Despite its advantages, biomass energy conversion faces some challenges that need to be addressed. One of the key challenges is the variability and seasonality of biomass feedstocks, which may affect the reliability and efficiency of biomass energy production. The costs of biomass conversion technologies can also be high, requiring significant upfront investments in infrastructure and equipment. In addition, the sustainability ofbiomass feedstocks is important to ensure that land use practices do not cause deforestation or competition with food production.To overcome these challenges, research and development efforts are underway to improve the efficiency and cost-effectiveness of biomass energy conversion technologies. Innovation in biomass pretreatment, conversion processes, and integrated biorefinery systems can help optimize the use of biomass feedstocks and increase energy output. Incentives and policies that support the development of biomass energy projects, such as feed-in tariffs and renewable energy mandates, can also help accelerate the transition to a more sustainable energy future.In conclusion, biomass energy conversion is a promising renewable energy solution that can help reduce greenhouse gas emissions, enhance energy security, and promote economic development. By leveraging the diverse range of biomass conversion technologies and addressing key challenges, we can unlock the full potential of biomass energy and contribute to a more sustainable and resilient energy system.。
Biomass as a Source of Renewable Carbon for Iron and Steelmaking -澳大利亚
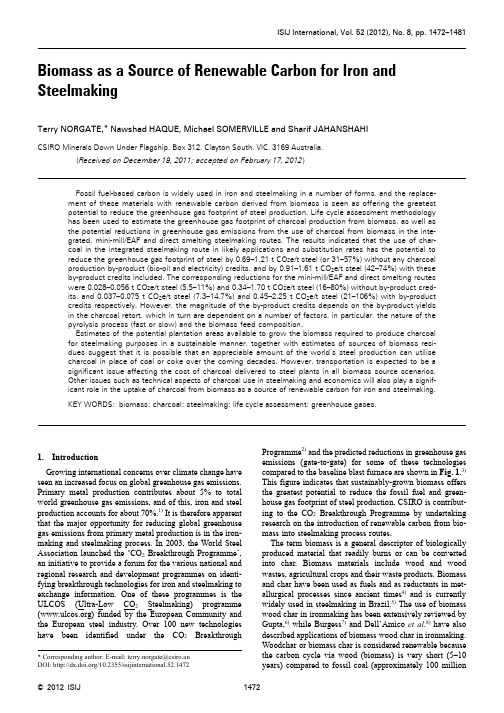
ISIJ International, Vol. 52 (2012), No. 8, pp. 1472–1481 Biomass as a Source of Renewable Carbon for Iron and SteelmakingTerry NORGATE,* Nawshad HAQUE, Michael SOMERVILLE and Sharif JAHANSHAHICSIRO Minerals Down Under Flagship, Box 312, Clayton South, VIC, 3169 Australia.(Received on December 19, 2011; accepted on February 17, 2012)Fossil fuel-based carbon is widely used in iron and steelmaking in a number of forms, and the replace-ment of these materials with renewable carbon derived from biomass is seen as offering the greatestpotential to reduce the greenhouse gas footprint of steel production. Life cycle assessment methodologyhas been used to estimate the greenhouse gas footprint of charcoal production from biomass, as well asthe potential reductions in greenhouse gas emissions from the use of charcoal from biomass in the inte-grated, mini-mill/EAF and direct smelting steelmaking routes. The results indicated that the use of char-coal in the integrated steelmaking route in likely applications and substitution rates has the potential toreduce the greenhouse gas footprint of steel by 0.69–1.21 t CO2e/t steel (or 31–57%) without any charcoalproduction by-product (bio-oil and electricity) credits, and by 0.91–1.61 t CO2e/t steel (42–74%) with theseby-product credits included. The corresponding reductions for the mini-mill/EAF and direct smelting routeswere 0.028–0.056 t CO2e/t steel (5.5–11%) and 0.34–1.70 t CO2e/t steel (16–80%) without by-product cred-its, and 0.037–0.075 t CO2e/t steel (7.3–14.7%) and 0.45–2.25 t CO2e/t steel (21–106%) with by-productcredits respectively. However, the magnitude of the by-product credits depends on the by-product yieldsin the charcoal retort, which in turn are dependent on a number of factors, in particular, the nature of thepyrolysis process (fast or slow) and the biomass feed composition.Estimates of the potential plantation areas available to grow the biomass required to produce charcoalfor steelmaking purposes in a sustainable manner, together with estimates of sources of biomass resi-dues suggest that it is possible that an appreciable amount of the world’s steel production can utilisecharcoal in place of coal or coke over the coming decades. However, transportation is expected to be asignificant issue affecting the cost of charcoal delivered to steel plants in all biomass source scenarios.Other issues such as technical aspects of charcoal use in steelmaking and economics will also play a signif-icant role in the uptake of charcoal from biomass as a source of renewable carbon for iron and steelmaking.KEY WORDS:biomass; charcoal; steelmaking; life cycle assessment; greenhouse gases.1.IntroductionGrowing international concerns over climate change have seen an increased focus on global greenhouse gas emissions. Primary metal production contributes about 5% to total world greenhouse gas emissions, and of this, iron and steel production accounts for about 70%.1) It is therefore apparent that the major opportunity for reducing global greenhouse gas emissions from primary metal production is in the iron-making and steelmaking process. In 2003, the World Steel Association launched the ‘CO2 Breakthrough Programme’, an initiative to provide a forum for the various national and regional research and development programmes on identi-fying breakthrough technologies for iron and steelmaking to exchange information. One of these programmes is the ULCOS (Ultra-Low CO2Steelmaking) programme () funded by the European Community and the European steel industry. Over 100 new technologies have been identified under the CO2 Breakthrough Programme2) and the predicted reductions in greenhouse gas emissions (gate-to-gate) for some of these technologies compared to the baseline blast furnace are shown in Fig. 1.3) This figure indicates that sustainably-grown biomass offers the greatest potential to reduce the fossil fuel and green-house gas footprint of steel production. CSIRO is contribut-ing to the CO2 Breakthrough Programme by undertaking research on the introduction of renewable carbon from bio-mass into steelmaking process routes.The term biomass is a general descriptor of biologically produced material that readily burns or can be converted into char. Biomass materials include wood and wood wastes, agricultural crops and their waste products. Biomass and char have been used as fuels and as reductants in met-allurgical processes since ancient times4) and is currently widely used in steelmaking in Brazil.5) The use of biomass wood char in ironmaking has been extensively reviewed by Gupta,6) while Burgess7) and Dell’Amico et al.8) have also described applications of biomass wood char in ironmaking. Woodchar or biomass char is considered renewable because the carbon cycle via wood (biomass) is very short (5–10 years) compared to fossil coal (approximately 100 million*Corresponding author: E-mail: terry.norgate@csiro.au DOI: /10.2355/isijinternational.52.1472years). However, the challenge is to be able to develop and manage the biomass source on a sustainable basis and to develop charcoal production technology that produces char-coal at a significantly lower cost9) and with lower environ-mental impacts than current production methods.The two main steelmaking routes are the integrated (blast furnace) process and the mini-mill (electric arc furnace) pro-cess, with about 70% of world’s steel production of 1410 million tonnes in 2010 being produced by the integrated route and about 29% by the mini-mill route.10) However, blast furnaces, in general, suffer from a number of disadvan-tages (e.g. agglomerated or lump feed, coke not coal, coke ovens). A range of “direct smelting” processes using bath smelting technology have been developed in recent years to address these issues, one of these processes being the HIsmelt ironmaking process.11) Ironmaking by direct smelt-ing is then followed by the conventional basic oxygen fur-nace (BOF) steelmaking process. While the potential use of biomass charcoal in various stages of steel production have been investigated both conceptually12) and experimentally, e.g. sintering,8,13) iron ore reduction,14) very little has been published on the environmental aspects of charcoal use in steelmaking. An early study in this regard was carried out by SERDF15) and more recently by the authors.9,16) The latter study has since been extended to include a more detailed evaluation of the potential greenhouse gas reductions asso-ciated with the various opportunities for charcoal use in steelmaking, and the impact of a new slow pyrolysis process being developed by CSIRO. The results of this latest study are presented in this paper and provide information that will assist in direction setting for future research in the use of biomass charcoal in ironmaking and steelmaking.2.Charcoal ProductionThere are several commercial processes currently avail-able to pyrolise biomass to charcoal. Historically, batch kilns have been used, but they are labour intensive and require a high degree of control to produce good quality, and high yields, of charcoal. Continuous retorts (e.g. Lambiotte and Lurgi) are used in Australia17) and elsewhere to over-come quality and operational issues of kilns, and where large production capacity is required. Pyrolysis processes may be either conventional (also referred to as slow pyrol-ysis) or fast pyrolysis, although the terms “slow” and “fast”are somewhat arbitrary with no precise definition of the times or heating rates involved in each.18) Biomass decom-poses during pyrolysis to generate vapours, aerosols and charcoal. After cooling and condensation of the vapours and aerosols, a liquid consisting of two phases is formed along with non-condensable gases. One of the liquid phases is organic-based and is referred to as bio-oil, the other is aque-ous-based and is called pyroligneous acid of which water is the main component.5) The proportions of charcoal, bio-oil and gas produced depends on the pyrolysis process, while other determining factors are wood species, moisture con-tent and size. In slow pyrolysis, biomass is heated to approx-imately 500°C. Vapours do not escape as rapidly as they do in fast pyrolysis and the slow heating rate enhances charcoal formation through secondary char making reactions. Typical yields18–20) are charcoal 35%, liquid 25% and gas 40%, all on a dry weight basis, with the liquid containing approxi-mately 8% bio-oil, i.e. 2% overall.19) The latter bio-oil yield is based on experimental slow pyrolysis testwork that was focused on charcoal production and not optimised for bio-oil collection, and as such this bio-oil yield is likely to be conservative. Ongoing developmental testwork on the pro-cess is expected to provide more definitive bio-oil yields. The gas generated during charcoal production can be utilised to generate electricity21,22) and/or heat,23) while the bio-oil can be used as a substitute for diesel fuel.18) Thus charcoal production technologies range from batch processes with no by-product recovery at one end, up to continuous processes with by-product bio-oil, electricity and/or heat at the other.A good example of the latter process is the integrated wood processing (IWP) plant developed by Enecon21,22) based on fast pyrolysis, with approximately 10% of the electricity gen-erated used internally and the remainder exported. Roberts et al.20) reported an energy balance for slow pyrolysis of corn stover1 that showed that despite the lower gas yield with slow pyrolysis and the use of some of the gas for pyrolysis process heat, there was still an excess of gas available that could beFig. parison of estimated greenhouse gas emissions (gate-to-gate) for various steelmaking technologies (after Birat, 2007).1 Corn stover is the residue (stalks and leaves) left behind after corn grain harvest.used for external purposes such as electricity generation.Existing plantations, forests and agricultural residues are all sources of biomass. New plantations can also be a source of biomass, and there is considerable interest in the potential for new tree crops such as Mallee eucalypts to be planted in agricultural regions across Australia to reduce the impact of dryland salinity. Wu et al .24) examined Mallee biomass pro-duction, while Stucley 21) reported details of the full-scale plant built in Western Australia for integrated processing of Mallee eucalypts (wood, bark, twigs and leaves) to produce charcoal or activated carbon, electrical power and bio-oil referred to above. This latter scenario (charcoal production by fast pyrolysis with electricity and bio-oil co-products from Mallee eucalypts) was used as the basis for a life cycle assessment (LCA) of charcoal production previously report-ed by the authors,9,16) including energy and greenhouse gas credits for the gas/electricity and bio-oil by-products. How-ever, CSIRO is currently developing a new slow pyrolysis process aimed at maximising the production of charcoal par-ticularly suited for steelmaking applications, and the LCA of charcoal production described in this paper is based on this new slow pyrolysis process. A schematic diagram of char-coal production from biomass is shown in Fig. 2.2.1.By-product Greenhouse Gas CreditsFirst estimates of bio-oil and gas/electricity greenhouse gas credits for this new slow pyrolysis process were obtained by extrapolating the Enecon fast pyrolysis results 21,22) using the respective by-product yields for the two processes. Although the composition of the by-product gas may change as well as the amount in going from fast to slow pyrolysis, which may also change the amount of elec-tricity that can be generated from the gas, it was assumed for the purpose of this study that any change in gas composi-tion does not significantly influence the amount of electricity produced. The amount of electricity produced was estimated to be 0.36 MWh e /t dry biomass, which compares with a valueof 0.44 MWh e /t dry biomass calculated from the results of Roberts et al .20) for corn stover assuming 35% electricity gen-eration efficiency. The former value (0.36 MWh e /t dry bio-mass) corresponds to avoided greenhouse gas emissions of 357 kg CO 2e/t dry biomass based on black coal derived electricity (with a greenhouse gas emission factor of 987 kg CO 2e/MWh) being replaced. According to Mohan et al .,18)bio-oil from fast pyrolysis has a heating value that is about half that of conventional fuel oil. Assuming here as a first estimate that bio-oil from slow pyrolysis has similar prop-erties to that from fast pyrolysis, this means that bio-oil can only replace about half of its mass of fuel oil (and diesel).Based on a bio-oil yield of 2% as above, the bio-oil green-house gas credit therefore amounts to 32 kg CO 2e/t dry biomass 2, giving a combined by-product greenhouse gas credit of 389 kg CO 2e/t dry biomass or 1111 kg CO 2e/t char-coal.3. Life Cycle Assessment of Charcoal Production The various LCA inventory inputs derived from the data provided by Wu et al .24) for the plantation establishment and management, harvesting and transportation of Mallee euca-lypt biomass to the charcoal plant are given in Table 1. Oth-er assumptions 6,7,9,13,19) made in relation to the charcoal plant were:•green biomass contains 45% moisture;•retort biomass feed properties: 20% moisture (after nat-ural drying), 44.4% carbon (dry basis);•charcoal yield in retort is 35% (dry basis);•charcoal properties: 4.5% moisture, 88.3% carbon (dry basis), ash 2.3%, sulphur 0.2%, calorific valueFig. 2.Schematic flowsheet of charcoal production.2Greenhouse gas emission factor for diesel is 3198 kg CO 2e/t diesel, hence 0.02 t bio-oil/t dry biomass × 3198/2 = 32 kg CO 2e/t dry biomass.Table 1.Inventory data for biomass production.Plantation establishmentEnergy inputs0.17 kg diesel/t green biomass a 0.5 kWh/t green biomass aPlantation managementEnergy inputs0.63 kg diesel/t green biomass a 1.8 kWh/t green biomass aHarvestingEnergy inputs1.57 kg diesel/t green biomass a 4.5 kWh/t green biomass a Yield & composition 19.2 t/ha.y40% wood (45% H 2O, wet basis (wb))25% bark and twigs (45% H 2O, wb)35% leaves (45% H 2O, wb)Transportation to charcoal plantEnergy inputs2.2 kg diesel/t green biomass a,ba.Assumes 58% of energy consumption is diesel (cal value 41 MJ/kg), bal-ance is electricity.b.Transport distance 70 km.31.1MJ/kg (dry basis).An LCA model of charcoal production as shown in Fig.1 was set up based on the above assumptions and incorpo-rating the inventory data given in Table 1. The main envi-ronmental impact category considered was greenhouse gas emissions on an aggregated gas basis (i.e. Global Warming Potential, GWP), with the IPCC (Intergovernmental Panel on Climate Change) characterisation model being used to calculate this impact category. It was assumed that any elec-tricity consumed was generated from black coal, at a gener-ation efficiency of 35%. The study used the international standards framework for conducting life cycle assessments contained in the ISO 14040 series with a functional unit of one tonne of charcoal . The methodology used in carrying out the LCAs in this study (charcoal and steel production lat-er) was similar to that used previously by the authors 25–27) in carrying out cradle-to-gate LCAs of various metal produc-tion processes. While the main source of biomass consid-ered in the study was Mallee eucalypts, forestry or logging residues were also assessed as an alternative source of bio-mass for charcoal production.The results of the LCA of charcoal production are given in Table 2 broken down into both renewable (from biomass)and non-renewable (from fossil fuels) components. It is the non-renewable components that must be reduced if signifi-cant reductions in greenhouse gas emissions from fossil fuels are to be achieved. The renewable component of the gross GWP impact was equal to 1.56 t CO 2e/t charcoal 3.However, these emissions are offset by an equivalent renew-able GWP credit due to the CO 2 sequestered during the growth of the biomass. Thus the net renewable GWP com-ponent of the gross impact shown in Table 2 is equal to zero.From Table 2, the non-renewable GWP impact for charcoal production is 105 kg CO 2e/t charcoal, which reflects the fos-sil fuel used in its production (i.e. plantation management,harvesting and transport). SERDF 15) reported a similar non-renewable GWP impact of 120 kg CO 2e/t charcoal for char-coal production.The contributions of the various stages to the greenhouse gas footprint of charcoal production are shown in Fig. 3.The by-product credits referred to above (i.e. generation of electricity from the gas which is used to replace electricity generated from black coal, and bio-oil which is used toreplace diesel) significantly reduce the non-renewable GWP impacts of charcoal production, resulting in the negative values shown in Table 2, indicating an overall net credit.However, it should be appreciated that the magnitude of the by-product credits depends on the by-product yields in the charcoal retort, which in turn are dependent on a number of factors, in particular, the nature of the pyrolysis process (fast or slow) and the biomass feed composition. Slow pyrolysis tends to maximise the charcoal yield, with less gas and bio-oil by-products produced, thus by-product credits are less with slow pyrolysis.It is of interest to compare the greenhouse gas footprint for the production of biomass feed material delivered to the charcoal plant from the two alternative sources of biomass considered in the study. The non-renewable greenhouse gas footprint of the Mallee eucalypt biomass in Table 2 (without any by-product credits) is 0.105 t CO 2e/t charcoal or 37 kg CO 2e/t dry biomass 4. The non-renewable greenhouse gas footprint for the forestry residues, covering the same stages of biomass production in Table 1, was estimated to be 40 kg CO 2e/t dry biomass from a separate LCA model. However,this latter material requires additional stages of chipping,screening, washing and drying. Including these stages in the LCA model increased the greenhouse gas footprint of bio-mass from forestry residues to 81 kg CO 2e/t dry biomass.But plantations are established and operated for the produc-tion of sawlogs and other main products, and hence harvest-ing must be carried out whether residues are extracted or not. Very little utilisation is normally made of these resi-dues, so in most instances they are not considered to be valuable co-products. Without the need to allocate the ener-gy and greenhouse gas impacts of plantation and harvesting to these residues, the greenhouse gas footprint drops to 49kg CO 2e/t dry biomass. This value is only slightly higher than that for Mallee eucalypt biomass, and reflects the addi-tional processing required for this material. As noted earlier,the following assessment of the use of charcoal in steelmak-ing is based on charcoal produced from Mallee eucalypts.4.Opportunities for Charcoal Use in Steelmaking 4.1.Integrated RouteThe integrated steelmaking route begins with iron ore3From listed assumptions = [((mass of C in dry biomass feed) – (mass of C in charcoal))/mass of charcoal] × 44.01/12.01 = [((1.0 × 0.444) – (0.350 × 0.955 ×0.883))/0.350] × 44.01/12.01 = 1.56 t CO 2e/t charcoal.40.105 t CO 2e/t charcoal and a charcoal yield of 0.35 t/t dry biomass = 0.105 × 0.35 × 1000 = 37 kg CO 2e/t dry biomass.Table 2.LCA results for charcoal production from Mallee euca-lypts.Gross impact(no credits)Electricity& bio-oilcreditsNet impact (with credits)Greenhouse gases (GWP)Renewable (t CO 2e/t charcoal)0.0010.000.00Non-renewable (t CO 2e/t charcoal)0.105 1.111–1.006TOTAL (t CO 2e/t charcoal)0.1051.111–1.0061.Renewable greenhouse gas emissions from charcoal production are 1.56 t CO 2e/t charcoal, but these are offset by an equivalent amount sequestered in the biomass – hence net emissions are zero.Fig. 3.Stage contributions to greenhouse gas footprint of charcoal production (no credits).mining. After crushing and screening, the iron ore fines are either sintered or pelletised and then fed into the blast fur-nace along with lump iron ore. Coke, produced from coal in coke ovens, is used as a fuel and reductant in the blast fur-nace together with fluxes to produce hot metal and slag. Pul-verised coal injection (PCI) into the tuyeres is also used as a supplementary fuel in the blast furnace. The hot metal is transferred to the basic oxygen furnace (BOF) along with steel scrap, where oxygen is used to refine the hot metal into steel by reducing the carbon content and other impurities.The liquid steel is further refined in the ladle metallurgy fur-nace (or ladle refining station), including recarburisation,and is then poured into a casting machine.The main opportunities for the use of biomass in the inte-grated route for steelmaking 28) are shown in Fig. 4 (for the sintering case) and are as follows:•partial or full replacement of solid fuel (coke or anthra-cite) in sintering or pelletising 5;•partial replacement of coke as a reductant and fuel in the blast furnace;•full replacement of pulverised coal injected as a fuel in the blast furnace;•partial or full replacement of nut coke that is mixed within the ferrous burden layers;•carbon/ore composite pellets 29) pre-reduced as blast furnace feed – although the extent of this application is currently uncertain;28)•full replacement of coal-based char used for recarburis-ing the liquid steel.It has been suggested that it is likely to be impossible to operate large blast furnaces with 100% substitution of char-coal for lump coke due to the much lower crushing strength of charcoal compared to coke, with substitution rates up to 20% being considered practical.15) While supporting this view for large blast furnaces, Gupta 6) claims that this mechanical property of charcoal becomes redundant whencharcoal is used as lump in small blast furnaces or as pow-der for tuyere injection in bigger blast furnaces. As the focus here was on medium to large blast furnaces, the use of char-coal to replace only between 2–10% of coke in the blast fur-nace was considered in this study.28) Typical carbon material addition rates are shown in Table 3 along with the charcoal substitution rates used in the study. For the integrated route,the sum of the carbon substituted with charcoal in the appli-cations shown in Table 3 range from 38% (minimum) to 55% (maximum) based on the typical addition rates shown.The mean substitution rate (47%) corresponds to about 287kg charcoal/t steel.4.2.EAF Mini-mill RouteThe mini-mill steelmaking route produces steel by melt-ing steel scrap, or some form of scrap substitute, in an elec-tric arc furnace (EAF) followed by similar steel refining steps to the integrated route. Where steel scrap is in short supply, scrap substitutes such as hot metal or direct reduced iron (DRI) are often used. Carbonaceous material is added to the EAF as charge carbon, the primary purpose of which is to provide a reducing atmosphere during melting which minimises the oxidation of alloys and metallics, and as injectant carbon, also known as slag foaming carbon, where the technique of foaming slag in the EAF is used to increase productivity, lower operating costs and increase the quality of the steel produced. The issue of charcoal crushing strength is less of a concern in EAFs due to short furnaces and absence of any impinging hot blast.6) The main oppor-tunities for the use of biomass in the EAF mini-mill route for steelmaking are also shown in Fig. 4 and are as follows:•partial or full replacement of charge carbon in the EAF;•partial or full replacement of slag foaming carbon;•partial or full replacement of recarburiser carbon.Typical carbon addition rates for the EAF are also shown in Table 3 along with the charcoal substitution rates used in5Solid fuel may not be required to be added to the pelletising step with magnetite ore due to the exothermic smelting reactions in the blast furnace.Fig. 4.Opportunities for charcoal use in steelmaking (sintering).the study.4.3.Direct Smelting RouteIn direct smelting processes, reduction takes place in a single reactor where ore and coal are both charged into the same melt or bath (hence the name “bath smelting”). The processes utilise post combustion of the process offgases, the heat released being transferred back to the bath to com-pensate for the endothermic smelting reactions. The HIsmelt process11) produces molten iron from fine iron ores (and oth-er iron-bearing fines) and non-coking coals. The iron oxides are rapidly reduced by the bath whilst carbon from the coal dissolves in the bath. The primary product from the HIsmelt process is hot metal (iron). This iron is tapped continuously through an open forehearth and is slag-free. It can be used as direct feed to steelmaking processes or cast into pig iron.The lower crushing strength of charcoal is not likely to be a significant issue in the direct bath smelting process for ironmaking, with charcoal substitution rates for coal as a reductant and fuel up to 100% being envisaged. Typical car-bon addition rates for direct smelting are also shown in Table 3 along with the charcoal substitution rates used in the study.5.Life Cycle Assessment of Steelmaking Processes LCA models of each of the three steelmaking routes were set up, and “cradle-to-gate” LCAs of each of these routes were carried out using inventory data reported previously for the three routes.9,16) The functional unit in this case was one tonne of steel, and as for the charcoal LCA, any elec-tricity consumed was assumed to be black coal-based at 35% efficiency. It should be noted that for the integrated route, coke production was assumed to be internalised within the steelworks, and the GWP contributions from the products of this process (coke and coke oven gas) were accounted for by converting the coke inventory inputs to coal equivalents (as coal is the external input to the steelworks, not coke). Other minor inputs into steelmaking such as ferroalloys, refractories and argon gas were not included as their contri-butions to the overall result are much less significant than the major inputs considered and in any case are similar for either coal or charcoal addition. The results of these LCAs are given in Table 4. The GWP values for the integrated route of 2.17 t CO2e/t steel (sintering) and 2.40 t CO2e/t steel (pelletising) are similar to the values reported in other studies, e.g. Mathieson28) 2.20 t CO2e/t steel, Orth et al.30) 2.20 t CO2e/t steel, Scaife et al.31) 2.16 t CO2e/t steel and Birat32) 2.0 t CO2e/t steel. Likewise, the GWP value of 0.51t CO2e/t steel given in Table 4 for the mini-mill/EAF routeTable 3.Typical carbon material addition rates in steelmaking and charcoal substitution rates used in study.Application Typical addition rate1Charcoal substitutionrate (%)1Charcoal substitutionrate used in study2Integrated routeSintering solid fuel45–60 kg/t sinter350–10022.5/60 kg/t sinterCokemaking blend component300–350 kg/t HM2–106/35 kg/t HMBF tuyere fuel injectant150–200 kg/t HM100150/200 kg/t HMBF nut coke replacement45 kg/t HM50–10022.5/45 kg/t HMPre-reduced carbon/ore composites4––18/36 kg/t HMRecarburiser carbon0.25 kg/t steel1000.25 kg/t steelEAF mini-mill routeCharge carbon12 kg/t steel50–1006/12 kg/t steelSlag foaming carbon 5 kg/t steel50–100 2.5/5 kg/t steelRecarburiser carbon 1.4 kg/t steel50–1000.7/1.4 kg/t steelDirect smelting routeBath coal injectant610 kg/t HM20–100122/610 kg/t HMRecarburiser carbon0.25 kg/t steel1000.25 kg/t steel1.Mathieson et al. (2011) for integrated route and EAF mini-mill route.2.Based on upper and lower limits of carbon addition rates and charcoal substitution rates.3.With 1.7 t sinter/t hot metal (HM).4.Not currently practised – 5–10% of iron in blast furnace feed as pre-reduced composites (Mathieson et al.,2011).Table 4.LCA results for various steelmaking routes (without char-coal substitution).Integrated routeDirectsmelting/BOFMini-mill/EAF100% scrapGreenhouse gases (GWP)SinteringRenewable (t CO2e/t steel)0.000.000.00 Non-renewable (t CO2e/t steel) 2.17 2.120.51 Total (t CO2e /t steel) 2.17 2.120.51PelletisingRenewable (t CO2e/t steel)0.00Non-renewable (t CO2e/t steel) 2.40Total (t CO2e /t steel) 2.40。
生物质气化和化学重整的英文
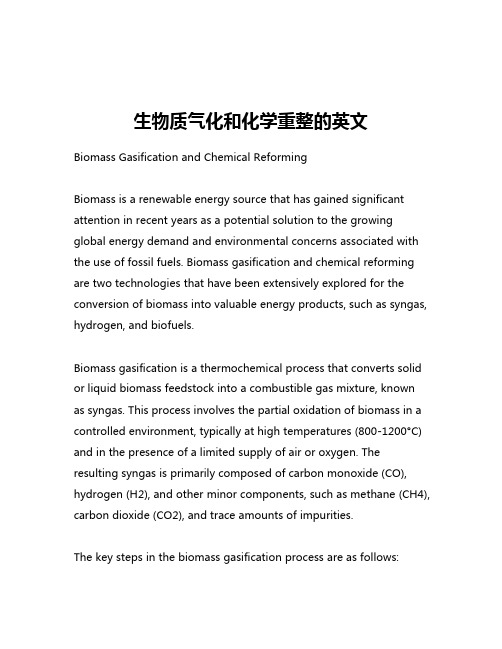
生物质气化和化学重整的英文Biomass Gasification and Chemical ReformingBiomass is a renewable energy source that has gained significant attention in recent years as a potential solution to the growing global energy demand and environmental concerns associated with the use of fossil fuels. Biomass gasification and chemical reforming are two technologies that have been extensively explored for the conversion of biomass into valuable energy products, such as syngas, hydrogen, and biofuels.Biomass gasification is a thermochemical process that converts solid or liquid biomass feedstock into a combustible gas mixture, known as syngas. This process involves the partial oxidation of biomass in a controlled environment, typically at high temperatures (800-1200°C) and in the presence of a limited supply of air or oxygen. The resulting syngas is primarily composed of carbon monoxide (CO), hydrogen (H2), and other minor components, such as methane (CH4), carbon dioxide (CO2), and trace amounts of impurities.The key steps in the biomass gasification process are as follows:1. Drying: The biomass feedstock is first dried to remove any moisture content, which can affect the efficiency of the subsequent conversion processes.2. Pyrolysis: The dried biomass is heated in the absence of oxygen, leading to the thermal decomposition of the organic compounds and the release of volatile components, such as hydrogen, carbon monoxide, and methane.3. Oxidation: The remaining solid char from the pyrolysis step is then partially oxidized, typically with air or oxygen, to generate heat and further convert the carbon-rich material into a combustible gas mixture.4. Reduction: The partially oxidized gas mixture undergoes a reduction process, where the carbon dioxide and water vapor are converted into carbon monoxide and hydrogen through reactions with the remaining solid char.The resulting syngas can be utilized in various applications, such as electricity generation, heat production, or further processing to obtain other valuable products, such as hydrogen or biofuels.Chemical reforming, on the other hand, is a process that aims to convert the syngas produced from biomass gasification into a morehydrogen-rich gas stream. This is typically achieved through a series of chemical reactions, including steam reforming, water-gas shift, and methanation.1. Steam reforming: The syngas, which contains carbon monoxide and hydrogen, is reacted with steam (H2O) at high temperatures (800-900°C) to produce a hydrogen-rich gas mixture. This reaction is endothermic and is typically carried out in the presence of a catalyst to enhance the conversion efficiency.2. Water-gas shift: The carbon monoxide in the gas mixture is further reacted with steam to produce additional hydrogen and carbon dioxide. This reaction is exothermic and is often performed at lower temperatures (300-500°C) to maximize the hydrogen yield.3. Methanation: The remaining carbon monoxide and carbon dioxide in the gas mixture can be converted into methane (CH4) through a series of catalytic reactions, known as the Sabatier process. This step is important for the removal of impurities and the production of a cleaner fuel gas.The hydrogen-rich gas produced through the chemical reforming process can be used for various applications, such as fuel cells, transportation, or further processing into other energy carriers, such as synthetic fuels or chemicals.The integration of biomass gasification and chemical reforming technologies offers several advantages. Firstly, it allows for the efficient conversion of biomass, a renewable and carbon-neutral energy source, into high-value energy products, such as hydrogen and syngas. This can contribute to reducing the reliance on fossil fuels and mitigating the environmental impact associated with their use.Secondly, the synergies between these two technologies can lead to improved overall system efficiency and flexibility. The biomass gasification process provides the necessary feedstock (syngas) for the chemical reforming step, while the reforming process can enhance the overall hydrogen yield from the biomass conversion.Furthermore, the integration of biomass gasification and chemical reforming can open up opportunities for the development of biorefineries, where the biomass-derived products can be utilized in a wide range of applications, including energy generation, transportation fuels, and the production of chemicals and materials.However, the widespread adoption of these technologies is not without challenges. The development and optimization of efficient and cost-effective biomass gasification and chemical reforming systems require ongoing research and technological advancements.Additionally, the integration of these processes into existing energy systems and infrastructure can pose logistical and economic barriers that need to be addressed.In conclusion, the combination of biomass gasification and chemical reforming technologies holds great potential for the sustainable conversion of biomass into valuable energy products. As the global demand for clean and renewable energy continues to grow, the further development and deployment of these technologies can contribute to a more sustainable energy future.。
生物质水蒸气气化制取富氢合成气及其应用的研究进展
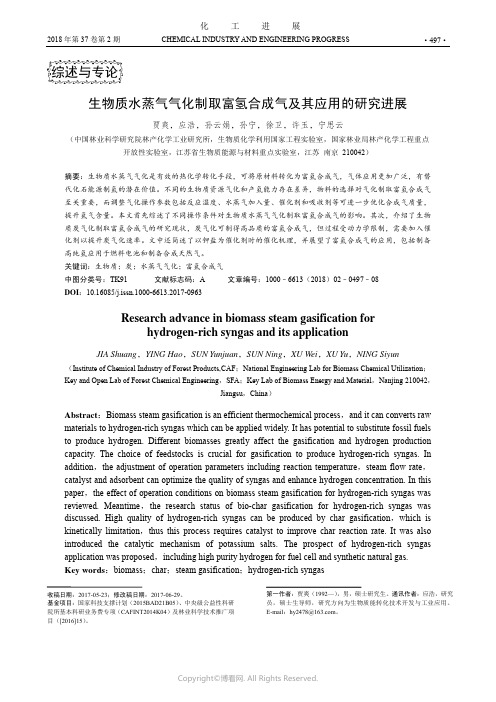
2018年第37卷第2期 CHEMICAL INDUSTRY AND ENGINEERING PROGRESS·497·化 工 进展生物质水蒸气气化制取富氢合成气及其应用的研究进展贾爽,应浩,孙云娟,孙宁,徐卫,许玉,宁思云(中国林业科学研究院林产化学工业研究所,生物质化学利用国家工程实验室,国家林业局林产化学工程重点开放性实验室,江苏省生物质能源与材料重点实验室,江苏 南京 210042)摘要:生物质水蒸气气化是有效的热化学转化手段,可将原材料转化为富氢合成气,气体应用更加广泛,有替代化石能源制氢的潜在价值。
不同的生物质资源气化和产氢能力存在差异,物料的选择对气化制取富氢合成气至关重要,而调整气化操作参数包括反应温度、水蒸气加入量、催化剂和吸收剂等可进一步优化合成气质量,提升氢气含量。
本文首先综述了不同操作条件对生物质水蒸气气化制取富氢合成气的影响。
其次,介绍了生物质炭气化制取富氢合成气的研究现状,炭气化可制得高品质的富氢合成气,但过程受动力学限制,需要加入催化剂以提升炭气化速率。
文中还简述了以钾盐为催化剂时的催化机理,并展望了富氢合成气的应用,包括制备高纯氢应用于燃料电池和制备合成天然气。
关键词:生物质;炭;水蒸气气化;富氢合成气中图分类号:TK91 文献标志码:A 文章编号:1000–6613(2018)02–0497–08 DOI :10.16085/j.issn.1000-6613.2017-0963Research advance in biomass steam gasification forhydrogen-rich syngas and its applicationJIA Shuang ,YING Hao ,SUN Yunjuan ,SUN Ning ,XU Wei ,XU Yu ,NING Siyun(Institute of Chemical Industry of Forest Products,CAF ;National Engineering Lab for Biomass Chemical Utilization ;Key and Open Lab of Forest Chemical Engineering ,SFA ;Key Lab of Biomass Energy and Material ,Nanjing 210042,Jiangsu ,China )Abstract :Biomass steam gasification is an efficient thermochemical process ,and it can converts raw materials to hydrogen-rich syngas which can be applied widely. It has potential to substitute fossil fuels to produce hydrogen. Different biomasses greatly affect the gasification and hydrogen production capacity. The choice of feedstocks is crucial for gasification to produce hydrogen-rich syngas. In addition ,the adjustment of operation parameters including reaction temperature ,steam flow rate ,catalyst and adsorbent can optimize the quality of syngas and enhance hydrogen concentration. In this paper ,the effect of operation conditions on biomass steam gasification for hydrogen-rich syngas was reviewed. Meantime ,the research status of bio-char gasification for hydrogen-rich syngas was discussed. High quality of hydrogen-rich syngas can be produced by char gasification ,which is kinetically limitation ,thus this process requires catalyst to improve char reaction rate. It was also introduced the catalytic mechanism of potassium salts. The prospect of hydrogen-rich syngas application was proposed ,including high purity hydrogen for fuel cell and synthetic natural gas. Key words :biomass ;char ;steam gasification ;hydrogen-rich syngas第一作者:贾爽(1992—),男,硕士研究生。
生物催化的英语
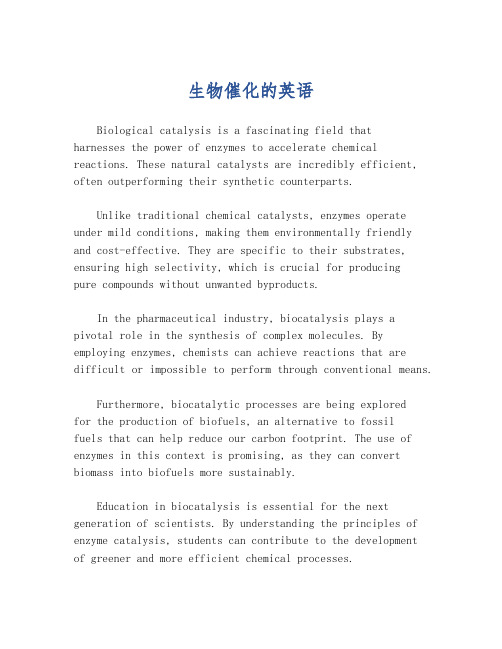
生物催化的英语Biological catalysis is a fascinating field thatharnesses the power of enzymes to accelerate chemical reactions. These natural catalysts are incredibly efficient, often outperforming their synthetic counterparts.Unlike traditional chemical catalysts, enzymes operate under mild conditions, making them environmentally friendly and cost-effective. They are specific to their substrates, ensuring high selectivity, which is crucial for producingpure compounds without unwanted byproducts.In the pharmaceutical industry, biocatalysis plays apivotal role in the synthesis of complex molecules. By employing enzymes, chemists can achieve reactions that are difficult or impossible to perform through conventional means.Furthermore, biocatalytic processes are being exploredfor the production of biofuels, an alternative to fossilfuels that can help reduce our carbon footprint. The use of enzymes in this context is promising, as they can convert biomass into biofuels more sustainably.Education in biocatalysis is essential for the next generation of scientists. By understanding the principles of enzyme catalysis, students can contribute to the developmentof greener and more efficient chemical processes.In conclusion, the study and application of biological catalysis are vital for advancing sustainable chemistry. As our understanding of enzymes deepens, so too does our ability to utilize them in innovative ways to benefit society and the environment.。
METHOD FOR TREATING BIOMASS FOR PRODUCING CELL LY
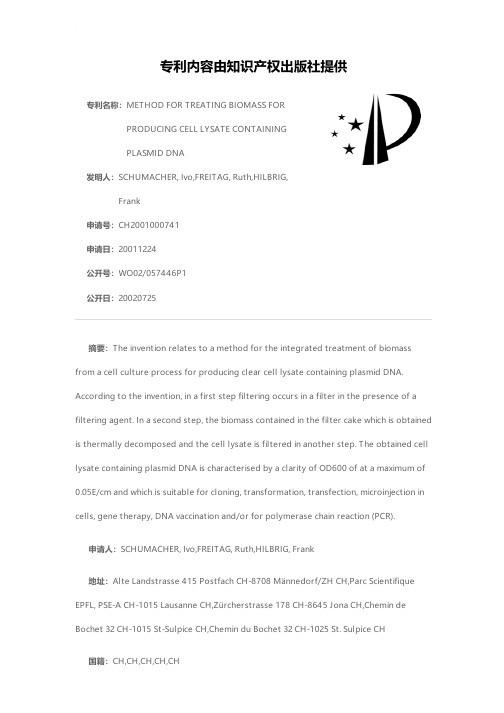
专利名称:METHOD FOR TREATING BIOMASS FOR PRODUCING CELL LYSATE CONTAININGPLASMID DNA发明人:SCHUMACHER, Ivo,FREITAG, Ruth,HILBRIG, Frank申请号:CH2001000741申请日:20011224公开号:WO02/057446P1公开日:20020725专利内容由知识产权出版社提供摘要:The invention relates to a method for the integrated treatment of biomass from a cell culture process for producing clear cell lysate containing plasmid DNA. According to the invention, in a first step filtering occurs in a filter in the presence of a filtering agent. In a second step, the biomass contained in the filter cake which is obtained is thermally decomposed and the cell lysate is filtered in another step. The obtained cell lysate containing plasmid DNA is characterised by a clarity of OD600 of at a maximum of 0.05E/cm and which is suitable for cloning, transformation, transfection, microinjection in cells, gene therapy, DNA vaccination and/or for polymerase chain reaction (PCR).申请人:SCHUMACHER, Ivo,FREITAG, Ruth,HILBRIG, Frank地址:Alte Landstrasse 415 Postfach CH-8708 Männedorf/ZH CH,Parc Scientifique EPFL, PSE-A CH-1015 Lausanne CH,Zürcherstrasse 178 CH-8645 Jona CH,Chemin de Bochet 32 CH-1015 St-Sulpice CH,Chemin du Bochet 32 CH-1025 St. Sulpice CH 国籍:CH,CH,CH,CH,CH代理机构:HERRMANN, Peter 更多信息请下载全文后查看。
bioresource technology简短的快讯类文章 -回复
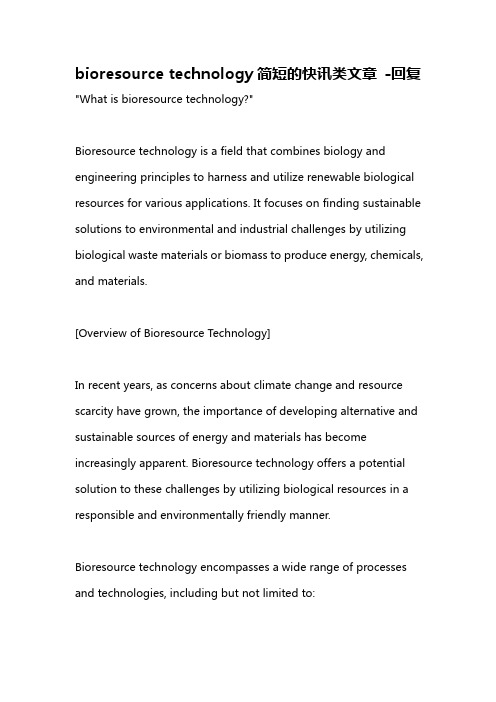
bioresource technology简短的快讯类文章-回复"What is bioresource technology?"Bioresource technology is a field that combines biology and engineering principles to harness and utilize renewable biological resources for various applications. It focuses on finding sustainable solutions to environmental and industrial challenges by utilizing biological waste materials or biomass to produce energy, chemicals, and materials.[Overview of Bioresource Technology]In recent years, as concerns about climate change and resource scarcity have grown, the importance of developing alternative and sustainable sources of energy and materials has become increasingly apparent. Bioresource technology offers a potential solution to these challenges by utilizing biological resources in a responsible and environmentally friendly manner.Bioresource technology encompasses a wide range of processes and technologies, including but not limited to:1. Biomass conversion: Biomass, which refers to organic matter derived from plants, animals, and microorganisms, can be converted into energy-rich substances such as biofuels. Bioethanol, biodiesel, and biogas are examples of biofuels produced from the fermentation or processing of biomass.2. Bioremediation: Bioresource technology can be used to clean up polluted environments through the use of microorganisms or plants to degrade or remove contaminants from soil, water, or air.3. Bioplastics and biomaterials: Bioresource technology explores the development of biodegradable and sustainable alternatives to traditional plastic and materials derived from fossil fuels. By using biomass-based feedstocks, bioplastics and biomaterials can reduce the environmental impact associated with their production and disposal.4. Waste management: Bioresource technology enables the conversion of various types of organic waste, including agricultural waste, food waste, and sewage sludge, into valuable products. These products can include biogas, compost, and nutrients for fertilizer production.5. Bio-based chemicals: Bioresource technology plays a crucial role in the production of bio-based chemicals, which are derived from renewable biological resources. These chemicals can be used as ingredients in various industries, such as pharmaceuticals, cosmetics, and agriculture.[Advantages of Bioresource Technology]Bioresource technology offers several advantages over conventional methods of resource utilization:1. Renewable and sustainable: Unlike fossil fuels, which are finite resources, bioresource technology relies on renewable biological resources. By utilizing biomass, the production of energy, chemicals, and materials can be sustained over the long term without depleting natural resources.2. Reduced greenhouse gas emissions: Bioresource technology helps reduce greenhouse gas emissions since the carbon dioxide released during the production and use of biofuels or biomaterials is offset by carbon dioxide absorbed during biomass growth. Thisconcept is known as carbon neutrality.3. Waste reduction and circular economy: By utilizing organic waste materials to produce valuable products, bioresource technology contributes to waste reduction and promotes the concept of a circular economy. It minimizes the need for landfilling and incineration, reducing pollution and environmental impact.4. Economic opportunities: The development and implementation of bioresource technology create new economic opportunities in various sectors, including agriculture, biotechnology, and energy. It can stimulate job creation and foster sustainable economic growth.[Current and Future Applications]Bioresource technology is actively being researched and implemented globally. Some current and potential future applications include:1. Biofuel production: The production of bioethanol and biodiesel from biomass is extensively researched and commercially implemented in many countries as a renewable fuel source fortransportation.2. Anaerobic digestion: The process of anaerobic digestion, which breaks down organic matter in the absence of oxygen, is widely used to produce biogas from agricultural, municipal, and industrial waste.3. Biorefineries: Integrated biorefineries are being developed to produce multiple products from biomass, including biofuels, chemicals, materials, and even food additives.4. Bioremediation technologies: Bioresource technology is being harnessed to develop innovative bioremediation methods for cleaning up contaminated soils, water bodies, and industrial sites.5. Algal biofuels: Research is ongoing to explore the potential of using algae as a source of biofuel due to its rapid growth, high oil content, and minimal land requirements.ConclusionBioresource technology offers a sustainable and environmentallyfriendly approach to address various challenges related to energy, waste management, and resource utilization. By leveraging renewable biological resources, bioresource technology has the potential to revolutionize several industries and contribute to a more sustainable and greener future.。
FUEL SUBSTITUTION POVERTY IMPACTS ON BIOMASS 贫困的影响对生物质燃料替代
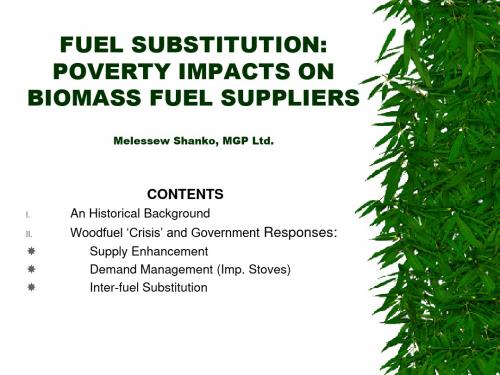
Implications
Comparison of Biomass Weight Inflow to Addis by Carrier Type (1988 and 1992)
We ight (Tons)
160 140 120 100 80 60 40 20
0 Donkeys Women Children Men Lorry
Supply Enhancement
Demand Management (Imp. Stoves)
Inter-fuel Substitution
I.Historical Background
Biomass and Estab. Of Addis as a Capital (1880s)
Biomass major source of energy (95%) Household sector major consumer (90%) of energy HHE heavily reliant on biomass (98%) Energy consumption per capita one of the least in the world
Electric Injera Mitad Ownership and Use in
Addis Ababa
80
72
70
65
60
50
42
40
30
20 10
7
13
0
1981 1985 Y1e9a9r1s 1995 200
LIVELIHOOD AND POVERTY IMPLICATIONS OF PREVIOUS
No. of Customers
生物质资源与生物能源 biomass and bioenergy resources
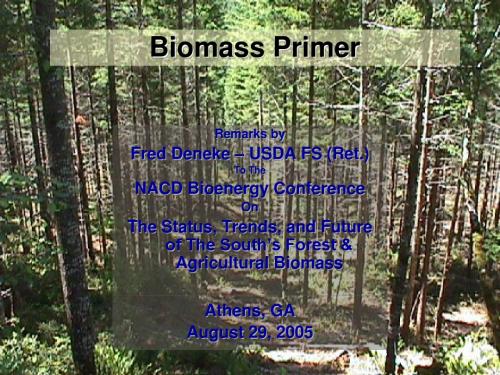
Dedicated agriculture crops such as corn, sorghum, switchgrass, etc.
Rapid fiber forest crops such as silage alder, hybrid poplar, sycamore, and willow
Total = 70.5 Quadrillion Btu
Petroleum 17%
Total = 6.2 Quadrillion Btu
− 2% Wind
Natural Gas 31%
− 45% Hydroelectric
Renewable Energy 9%
− 5% Geothermal
Nuclear Electric 11% Coal 32%
(Heat & Pressure)
Heat
Fuel Gases (CO + H2)
Liquids
Ethanol
CH4
Liquids
H2
Biobased Products from Biomass
USES
Fuels: Ethanol Renewable Diesel Electricity Heat Chemicals – Plastics – Solvents – Pharmaceuticals – Chemical Intermediates – Phenolics – Adhesives – Furfural – Fatty acids – Acetic Acid – Carbon black – Paints – Dyes, Pigments, and Ink – Detergents – Etc. Food and Feed
The promise of renewable energy Biomass energy
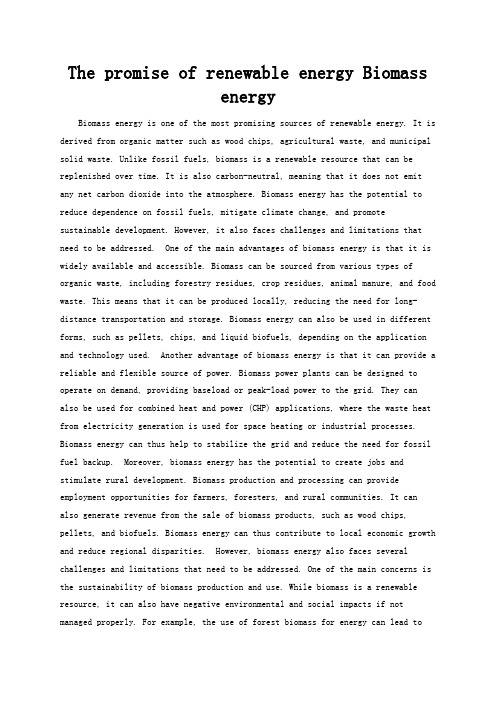
The promise of renewable energy BiomassenergyBiomass energy is one of the most promising sources of renewable energy. It is derived from organic matter such as wood chips, agricultural waste, and municipal solid waste. Unlike fossil fuels, biomass is a renewable resource that can be replenished over time. It is also carbon-neutral, meaning that it does not emit any net carbon dioxide into the atmosphere. Biomass energy has the potential to reduce dependence on fossil fuels, mitigate climate change, and promote sustainable development. However, it also faces challenges and limitations that need to be addressed. One of the main advantages of biomass energy is that it is widely available and accessible. Biomass can be sourced from various types of organic waste, including forestry residues, crop residues, animal manure, and food waste. This means that it can be produced locally, reducing the need for long-distance transportation and storage. Biomass energy can also be used in different forms, such as pellets, chips, and liquid biofuels, depending on the application and technology used. Another advantage of biomass energy is that it can provide a reliable and flexible source of power. Biomass power plants can be designed to operate on demand, providing baseload or peak-load power to the grid. They can also be used for combined heat and power (CHP) applications, where the waste heat from electricity generation is used for space heating or industrial processes. Biomass energy can thus help to stabilize the grid and reduce the need for fossil fuel backup. Moreover, biomass energy has the potential to create jobs and stimulate rural development. Biomass production and processing can provide employment opportunities for farmers, foresters, and rural communities. It can also generate revenue from the sale of biomass products, such as wood chips, pellets, and biofuels. Biomass energy can thus contribute to local economic growth and reduce regional disparities. However, biomass energy also faces several challenges and limitations that need to be addressed. One of the main concerns is the sustainability of biomass production and use. While biomass is a renewable resource, it can also have negative environmental and social impacts if not managed properly. For example, the use of forest biomass for energy can lead todeforestation, biodiversity loss, and soil degradation. The use of agricultural residues can also compete with food production and affect soil fertility. Therefore, it is essential to ensure that biomass production and use are sustainable and do not cause harm to the environment or society. Anotherchallenge for biomass energy is the cost competitiveness compared to fossil fuels and other renewable sources. While the cost of biomass energy has been decliningin recent years, it still faces competition from cheap natural gas and coal. Moreover, the cost of biomass energy can vary depending on the type and quality of biomass, the transportation and storage costs, and the technology used. Biomass energy also competes with other renewable sources such as wind and solar, which have seen significant cost reductions in recent years. Furthermore, biomassenergy faces regulatory and policy challenges that can affect its deployment and growth. Biomass energy is subject to various regulations and standards, such as sustainability criteria, emission limits, and land use restrictions. These regulations can vary depending on the country or region, creating barriers totrade and investment. Biomass energy also depends on policy support and incentives, such as feed-in tariffs, tax credits, and renewable energy targets. Theavailability and stability of these policies can affect the attractiveness and viability of biomass energy investments. In conclusion, biomass energy has the promise to provide a reliable, flexible, and sustainable source of renewable energy. It can reduce dependence on fossil fuels, mitigate climate change, and promote rural development. However, it also faces challenges and limitations that need to be addressed, such as sustainability, cost competitiveness, and regulatory barriers. To unlock the potential of biomass energy, it is essential to adopt a holistic and integrated approach that balances economic, social, and environmental considerations. This approach should involve stakeholders from different sectors and regions, and promote innovation, collaboration, and knowledge sharing. Bydoing so, biomass energy can become a vital component of the global energy mix, contributing to a more sustainable and resilient future.。
- 1、下载文档前请自行甄别文档内容的完整性,平台不提供额外的编辑、内容补充、找答案等附加服务。
- 2、"仅部分预览"的文档,不可在线预览部分如存在完整性等问题,可反馈申请退款(可完整预览的文档不适用该条件!)。
- 3、如文档侵犯您的权益,请联系客服反馈,我们会尽快为您处理(人工客服工作时间:9:00-18:30)。
1) Contribute to the state’s renewable energy and clean fuels goals
2) Serve as showcases of effective technologies and business models for producing power and fuels from biomass, and
Key Challenge
Renewable biomass-to-energy industry in N.J. is limited to electric power generation at landfills
• Little on-the-ground experience with sustainable biomassbased pathways toward the State’s renewable energy and clean fuels goals – that is, pathways with the lowest possible energy costs and no adverse environmental or society consequences.
2. RFP process to be carried out by the State
3. DECISIONS BASED ON: Selection criteria including number of facilities, host sites, eligible technologies, geographic distribution, energy products to be developed, and end-user markets. Weighted “outcome” criteria related to various economic, energy, job, and environmental objectives. The feasibility of providing project-specific State resources and the acceptability of a proposed project at the community level.
BIOMASS RESOURCES FOR PRODUCING RENEWABLE POWER AND FUELS IN THE STATE OF NEW JERSEY
AND INCENTIVES TO PROMOTE THEIR DEVELOPMENT
Report & Recommendations of the Biomass Work Group
Central question: What can the State do to incentivize the development of biomass resources for energy production?
“Energy” in the 2019 Draft Energy Master Plan: Includes vehicle fuel for the first time. Among other measures to encourage the use of clean transportation fuels, promotes a shift to natural gas fuel for truck and bus fleets.
public-private partnerships to build and operate biomass-to-power & fuels plants in two to three years.
OTHER RECOMMENDATIONS • Facilitate and incentivize pilot and small-scale biomass-to-energy
Electric Power and Heat
• Direct combustion
Ethanol Fuel
• Cellulosic ethanol • Dilute acid hydrolysis
Biodiesel Fuel
• Transesterification
Source: Assessment of Biomass Energy Potential in New Jersey, 2019
The Task
State goal: 22.5% of electric power from renewable sources by 2021.
Lagging biomass sector: Current state-level incentives for producing renewable electricity are ineffective in stimulating investment in biomass-to-energy facilities.
Biomass Work Group
Graham Barker, Air & Gas Technologies Jeffrey Beach, N.J. Department of Agriculture Phil Cerria, South Jersey Energy Solutions Edward A. Clerico, Natural Systems Utilities Carol Coren, Rutgers Food Innovation Center Rocco D’Antonio, Organic Diversion LLC Chuck Feinberg, Chairman, Clean Cities N.J Kenneth Frank, N.J. Department of Environmental Protection Serpil Güran, Ph.D., Rutgers EcoComplex Priscilla Hayes, Esq., Materials Management Consultant Zane Helsel, Ph.D., N.J. Ag Experiment Station Richard C. Kunze, The Ocean County Utilities Authority Bryan Luftglass, Linde, Inc. Dennis W. Palmer, P.E., Landis Sewerage Authority Jerome K. Prevete, Pennoni Associates Inc. Gail Richardson, Ph.D., Energy Vision; BWG Co-Chair Gail Rosati, Organic Diversion LLC Robert W. Simkins, Burlington County Resource Recovery Gary Sondermeyer, Bayshore Recycling David Specca, Rutgers EcoComplex; BWG Co-Chair William E. Toffey, Effluential Synergies LLC Joanna D. Underwood, Energy Vision William E. Wells, New Jersey Natural Gas
• No adequate basis, yet, for designing incentives for biomass-based energy facilities.
Recommendations
MAJOR RECOMMENDATION • Biomass to Power & Fuels Initiative: Target State resources to facilitate
Co-Chairs Gail Richardson, Energy Vision David Specca, Rutgers EcoComplex
N.J. Board of Public Utilities – Public Hearing Rutgers EcoComplex • November 10, 2019
N.J. Biomass Resources
Potential Source of Up to 9% Electricity OR 5% of Highway Fuel Consumption
Source: Assessment of Biomass Energy Potential in New Jersey, 2019
RNG WORK GROUP ANALYSIS
• Renewable natural gas is a sustainable biomass-based fuel with an unmatched combination of economic & environmental benefits.
RNG Work Group Perspectives
1. RNG along with conventional natural gas is the only alternative fuel pathway today that can simultaneously a) break the oil dependence of trucks and buses; b) slash health-endangering urban air pollution; c) lower greenhouse gas emissions; and d) reduce fuel costs and price volatility.