硬质合金刀具涂层
材料表面工程-硬质合金涂层
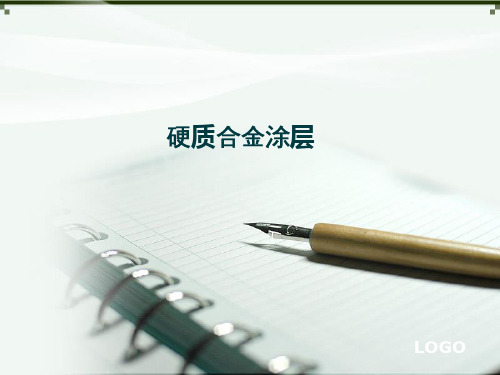
LOGO
目录
定义 涂层工艺 涂层材料 涂层结构 基体 发展
定义及目的
定义:硬质合金涂层是在韧性好的硬质合金 基体上涂覆耐磨性高的硬质涂层。 目的:使刀具能抵抗各种特定的耐磨机理 , 显著提高刀具的功能和刀具的使用寿命 ,并 可大幅度提高刀具的加工效率。
涂层工艺
CVD技术主要用于硬质合 金车削类刀具的表面涂层 ,涂层刀具适用于中到重 型切削的高速粗加工。
涂层工艺
离子镀法
离子镀(IP)法是 采用离子和具有 能量的中性原子 轰击溅射净化后 的基体(沉积前) 并在沉积过程中 控制涂层成核和 生长过程。
涂层工艺
溅射法
溅射法是在高真 空充入适量的氩 气,氩气发生电 离,氩离子被阴 极加速并轰击阴 极靶表面,将靶 材表面原子溅射 出来沉积在基底 表面上形成薄膜 。
涂层材料
涂层结构
单层及多元涂层 多层涂层
梯度涂层
涂层结构
多层涂层金相结构图
TiN-TiCN-TiN-Al2O3-TiN
涂层基体
发展
(1)涂层工艺温度越来越低, 尽量减少了涂层过程中产生的应 力集中。 (2)为满足不同的切削加工需求, 涂层成分更加复杂、更有针 对性。 (3)复合涂层中各单一成分涂层的厚度越来越薄, 并逐步趋于 纳米化。 (4)涂层硬质合金刀具将采用复合表面处理技术, 实现成分、 组织结构的梯度过渡, 获得性能更好的涂层组织以及更高界 面结合强度的产品。
PVD技术适用于硬质合金 精密复杂刀具的涂层处理 。
涂层工艺
工艺过程
汽化
物理气相沉积
相互间反应
涂层材料
原子,分子,离子
迁移
吸附 堆集 形核 长大
涂层刀具的种类
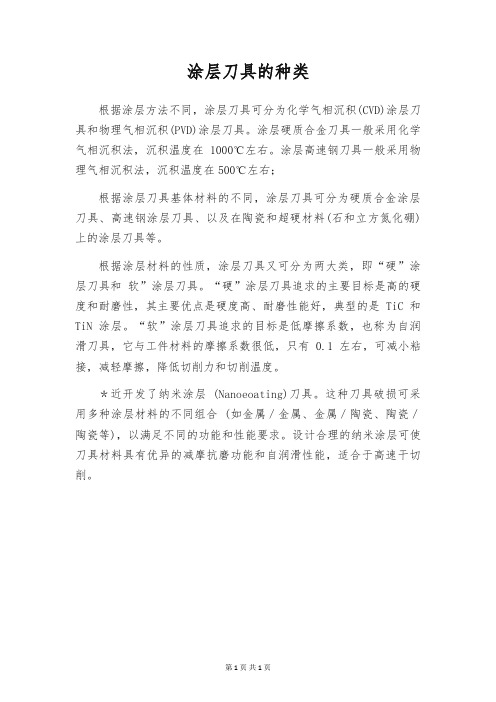
涂层刀具的种类
根据涂层方法不同,涂层刀具可分为化学气相沉积(CVD)涂层刀具和物理气相沉积(PVD)涂层刀具。
涂层硬质合金刀具一般采用化学气相沉积法,沉积温度在1000℃左右。
涂层高速钢刀具一般采用物理气相沉积法,沉积温度在500℃左右;
根据涂层刀具基体材料的不同,涂层刀具可分为硬质合金涂层刀具、高速钢涂层刀具、以及在陶瓷和超硬材料(石和立方氮化硼)上的涂层刀具等。
根据涂层材料的性质,涂层刀具又可分为两大类,即“硬”涂层刀具和软”涂层刀具。
“硬”涂层刀具追求的主要目标是高的硬度和耐磨性,其主要优点是硬度高、耐磨性能好,典型的是TiC和TiN涂层。
“软”涂层刀具追求的目标是低摩擦系数,也称为自润滑刀具,它与工件材料的摩擦系数很低,只有0.1左右,可减小粘接,减轻摩擦,降低切削力和切削温度。
*近开发了纳米涂层 (Nanoeoating)刀具。
这种刀具破损可采用多种涂层材料的不同组合 (如金属/金属、金属/陶瓷、陶瓷/陶瓷等),以满足不同的功能和性能要求。
设计合理的纳米涂层可使刀具材料具有优异的减摩抗磨功能和自润滑性能,适合于高速干切削。
第 1 页共 1 页。
硬质合金切削刀具的材料选择与表面涂层优化
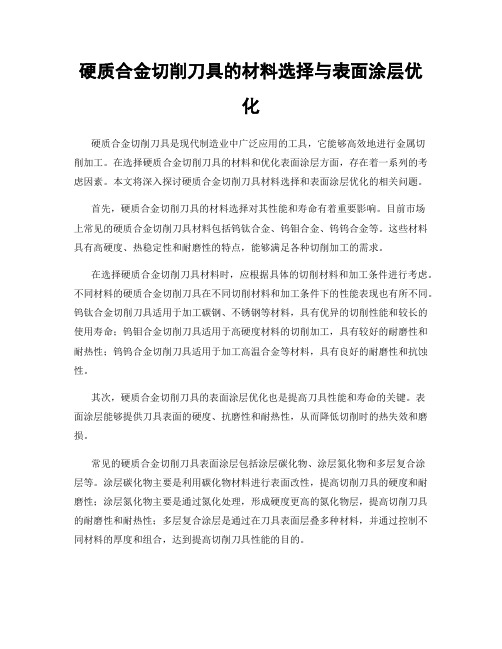
硬质合金切削刀具的材料选择与表面涂层优化硬质合金切削刀具是现代制造业中广泛应用的工具,它能够高效地进行金属切削加工。
在选择硬质合金切削刀具的材料和优化表面涂层方面,存在着一系列的考虑因素。
本文将深入探讨硬质合金切削刀具材料选择和表面涂层优化的相关问题。
首先,硬质合金切削刀具的材料选择对其性能和寿命有着重要影响。
目前市场上常见的硬质合金切削刀具材料包括钨钛合金、钨钼合金、钨钨合金等。
这些材料具有高硬度、热稳定性和耐磨性的特点,能够满足各种切削加工的需求。
在选择硬质合金切削刀具材料时,应根据具体的切削材料和加工条件进行考虑。
不同材料的硬质合金切削刀具在不同切削材料和加工条件下的性能表现也有所不同。
钨钛合金切削刀具适用于加工碳钢、不锈钢等材料,具有优异的切削性能和较长的使用寿命;钨钼合金切削刀具适用于高硬度材料的切削加工,具有较好的耐磨性和耐热性;钨钨合金切削刀具适用于加工高温合金等材料,具有良好的耐磨性和抗蚀性。
其次,硬质合金切削刀具的表面涂层优化也是提高刀具性能和寿命的关键。
表面涂层能够提供刀具表面的硬度、抗磨性和耐热性,从而降低切削时的热失效和磨损。
常见的硬质合金切削刀具表面涂层包括涂层碳化物、涂层氮化物和多层复合涂层等。
涂层碳化物主要是利用碳化物材料进行表面改性,提高切削刀具的硬度和耐磨性;涂层氮化物主要是通过氮化处理,形成硬度更高的氮化物层,提高切削刀具的耐磨性和耐热性;多层复合涂层是通过在刀具表面层叠多种材料,并通过控制不同材料的厚度和组合,达到提高切削刀具性能的目的。
在进行硬质合金切削刀具表面涂层优化时,应根据切削材料、加工条件和切削过程中的磨损机理来选择合适的涂层类型。
以增加刀具的硬度和抗磨性为主要目标,选择碳化物涂层;以提高刀具的耐热性和耐磨性为主要目标,选择氮化物涂层。
同时,在选择涂层材料时,还应考虑成本、制备工艺和刀具几何形状等因素。
此外,刀具表面涂层的结构和性能也需要进行优化。
硬质合金涂层用途

硬质合金涂层用途
硬质合金涂层是一种常见的表面涂层,其主要用途包括以下几个方面:
1. 刀具涂层:硬质合金涂层可用于加工不同材料的刀具表面,如钢、不锈钢、铜、铝等。
其涂层能够提高刀具的耐磨性、耐腐蚀性和热稳定性,使刀具寿命延长,生产效率提高。
2. 模具涂层:硬质合金涂层可以用于模具表面,如注塑模、挤出模、冲压模等。
其涂层可以提高模具的硬度和耐磨性,同时也能够减少模具和产品之间的粘附,避免模具出现卡模现象。
3. 零部件涂层:硬质合金涂层还可以用于零部件表面,如轴承、齿轮、活塞等。
其涂层能够提高零部件的耐磨性和耐腐蚀性,减少零部件的磨损,延长使用寿命。
4. 工程机械涂层:硬质合金涂层可用于工程机械表面,如铲斗、履带、刀片等。
其涂层能够提高工程机械的耐磨性和耐腐蚀性,延长使用寿命,同时也能够提高工程机械的工作效率。
总之,硬质合金涂层广泛应用于各种行业和领域,其优异的性能和可靠性使其成为表面涂层的重要选择之一。
- 1 -。
硬质合金木工刀具涂层制备工艺优化
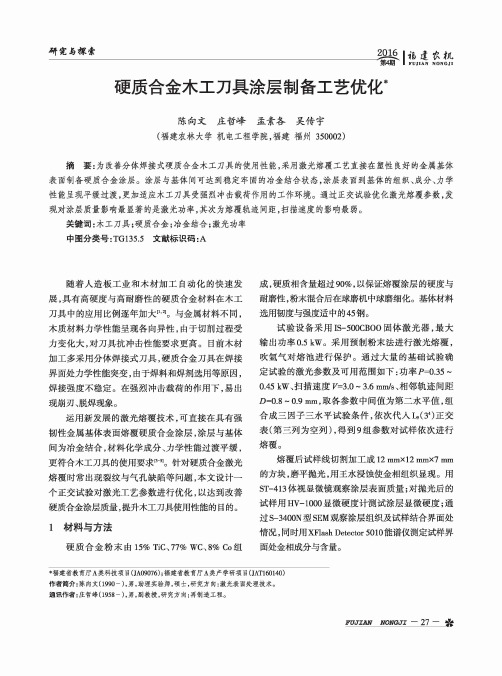
岬究与裸索|#遣■农杈1WAm I FUJIAN NONGJI 硬质合金木工刀具涂层制备工艺优化*陈向文庄哲峰孟素各吴传宇(福建农林大学机电工程学院,福建福州350002)摘要:为改善分体焊接式硬质合金木工刀具的使用性能,采用激光熔覆工艺直接在塑性良好的金属基体 表面制备硬质合金涂层。
涂层与基体间可达到稳定牢固的冶金结合状态,涂层表面到基体的组织、成分、力学 性能呈现平缓过渡,更加适应木工刀具受强烈冲击载荷作用的工作环境。
通过正交试验优化激光熔覆参数,发 现对涂层质量影响最显著的是激光功率,其次为熔覆轨迹间距,扫描速度的影响最弱。
关键词:木工刀具;硬质合金;冶金结合;激光功率中图分类号:TG135.5文献标识码:A随着人造板工业和木材加工自动化的快速发展,具有高硬度与高耐磨性的硬质合金材料在木工 刀具中的应用比例逐年加大[1,2]。
与金属材料不同,木质材料力学性能呈现各向异性,由于切削过程受 力变化大,对刀具抗冲击性能要求更高。
目前木材 加工多采用分体焊接式刀具,硬质合金刀具在焊接 界面处力学性能突变,由于焊料和焊剂选用等原因,焊接强度不稳定。
在强烈冲击载荷的作用下,易出 现崩刃、脱焊现象。
运用新发展的激光熔覆技术,可直接在具有强 軔性金属基体表面熔覆硬质合金涂层,涂层与基体 间为冶金结合,材料化学成分、力学性能过渡平缓,更符合木工刀具的使用要求[3_\针对硬质合金激光熔覆时常出现裂纹与气孔缺陷等问题,本文设计一 个正交试验对激光工艺参数进行优化,以达到改善 硬质合金涂层质量,提升木工刀具使用性能的目的。
1材料与方法硬质合金粉末由15% TiC、77%WC、8%Co组成,硬质相含量超过90%,以保证熔覆涂层的硬度与 耐磨性,粉末混合后在球磨机中球磨细化。
基体材料 选用軔度与强度适中的45钢。
试验设备采用IS-500CBOO固体激光器,最大 输出功率0.5 kW。
采用预制粉末法进行激光熔覆,吹氩气对熔池进行保护。
硬质涂层刀具简介
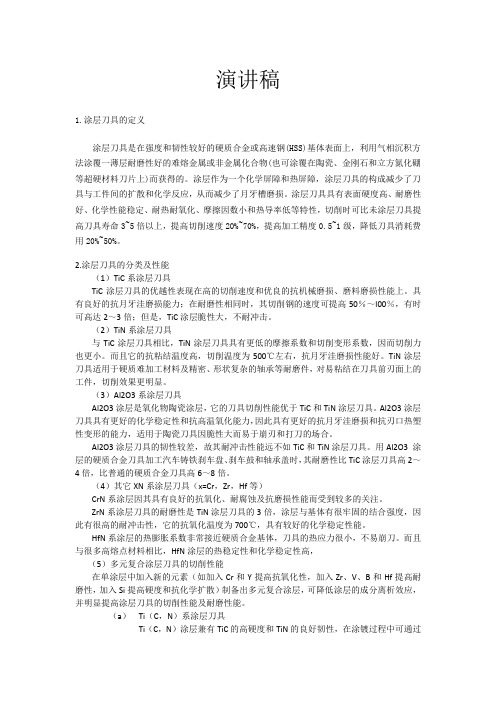
演讲稿1.涂层刀具的定义涂层刀具是在强度和韧性较好的硬质合金或高速钢(HSS)基体表面上,利用气相沉积方法涂覆一薄层耐磨性好的难熔金属或非金属化合物(也可涂覆在陶瓷、金刚石和立方氮化硼等超硬材料刀片上)而获得的。
涂层作为一个化学屏障和热屏障,涂层刀具的构成减少了刀具与工件间的扩散和化学反应,从而减少了月牙槽磨损。
涂层刀具具有表面硬度高、耐磨性好、化学性能稳定、耐热耐氧化、摩擦因数小和热导率低等特性,切削时可比未涂层刀具提高刀具寿命3~5倍以上,提高切削速度20%~70%,提高加工精度0.5~1级,降低刀具消耗费用20%~50%。
2.涂层刀具的分类及性能(1)TiC系涂层刀具TiC涂层刀具的优越性表现在高的切削速度和优良的抗机械磨损、磨料磨损性能上。
具有良好的抗月牙洼磨损能力;在耐磨性相同时,其切削钢的速度可提高50%~l00%,有时可高达2~3倍;但是,TiC涂层脆性大,不耐冲击。
(2)TiN系涂层刀具与TiC涂层刀具相比,TiN涂层刀具具有更低的摩擦系数和切削变形系数,因而切削力也更小。
而且它的抗粘结温度高,切削温度为500℃左右,抗月牙洼磨损性能好。
TiN涂层刀具适用于硬质难加工材料及精密、形状复杂的轴承等耐磨件,对易粘结在刀具前刃面上的工件,切削效果更明显。
(3)Al2O3系涂层刀具Al2O3涂层是氧化物陶瓷涂层,它的刀具切削性能优于TiC和TiN涂层刀具。
Al2O3涂层刀具具有更好的化学稳定性和抗高温氧化能力,因此具有更好的抗月牙洼磨损和抗刃口热塑性变形的能力,适用于陶瓷刀具因脆性大而易于崩刃和打刀的场合。
Al2O3涂层刀具的韧性较差,故其耐冲击性能远不如TiC和TiN涂层刀具。
用Al2O3 涂层的硬质合金刀具加工汽车铸铁刹车盘、刹车鼓和轴承盖时,其耐磨性比TiC涂层刀具高2~4倍,比普通的硬质合金刀具高6~8倍。
(4)其它XN系涂层刀具(x=Cr,Zr,Hf等)CrN系涂层因其具有良好的抗氧化、耐腐蚀及抗磨损性能而受到较多的关注。
硬质合金涂层刀具的发展

硬质合金涂层刀具的进展硬质合金刀具的硬涂层可提高刀具寿命和生产率。
化学气相沉积(CVD)技术已从早期的单涂层进展到现在的由Tic、TiN、TiCN和Al2O3复合多涂层,而且通过选择涂层的次序及涂层的总厚度来充足特种金属切削的要求,尤其是Al2O3涂层可供给包括高的抗扩散性磨损、优良的抗氧化性和高的热硬度等极好的高温性能,所以在铸铁及钢等材料高速加工获得广泛应用。
近年来,刀具制造商已引进中温(MT)CVDTiCN涂层,当使用乙晴作为有机的C/N源,TiCN的沉积大约发生在850℃,而高温CVDTiCN涂层要加热高于1000℃。
MT-TiCN涂层用于车削和铣削时具有很好的耐磨性能,它具有稳定的C/N比,并可削减涂层与硬质合金基体之间界面形成eta相的倾向。
十多年前,物理气相沉积(PVD)已应用于圆柱形硬质合金刀具,包括间断切削和/或一些需要锋利刀刃的金属切削刀片。
最初PVD涂层只限于TiN,而现在工业上已有适用的PVDTiCN和TiAlN涂层,采纳多种不同的PVD技术,如电子束蒸发、溅射、电弧蒸发等。
CVD金刚石涂层采纳了很多金刚石合成技术,最一般的是热丝法、微波等离子法和d、c等离子喷射法。
通过改进涂层方法和涂层的粘结,已生产出金刚石涂层硬质合金刀具,并在加工非铁及非金属材料方面起侧紧要的作用。
近来金刚石涂层刀具已在工业上得到应用。
硬质合金刀具的硬涂层硬涂层的性能切削刀具基体硬涂层的成功是由于涂层的物理和力学性能的复合作用。
从使用的角度来年,涂层应具有稳定的化学稳定性能、热硬度和与基体较强的粘结性能。
优化的涂层厚度、细的显微结构及残余压应力可以进一步提高涂层性能。
化学稳定性涂层材料化学惰性的标准是它的形成标准,自由能的负数很高或在切削温度下它在工件材料的溶解度很低。
至今,CVDAl2O3硬涂层在材材加工中完全可充足这些要求。
无定形PVDAl2O3涂层是软的而且不稳定,因此不如结晶的CVDAl2O3;PVDTiAlN涂层与TiN或TiCN相比,具有较高的稳定性,因此有可能在高速切削加工中获得应用。
硬质合金刀具涂层工艺流程
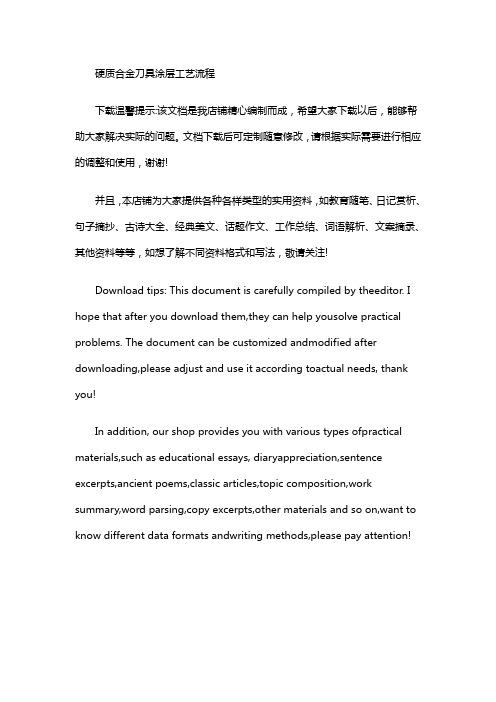
硬质合金刀具涂层工艺流程下载温馨提示:该文档是我店铺精心编制而成,希望大家下载以后,能够帮助大家解决实际的问题。
文档下载后可定制随意修改,请根据实际需要进行相应的调整和使用,谢谢!并且,本店铺为大家提供各种各样类型的实用资料,如教育随笔、日记赏析、句子摘抄、古诗大全、经典美文、话题作文、工作总结、词语解析、文案摘录、其他资料等等,如想了解不同资料格式和写法,敬请关注!Download tips: This document is carefully compiled by theeditor. I hope that after you download them,they can help yousolve practical problems. The document can be customized andmodified after downloading,please adjust and use it according toactual needs, thank you!In addition, our shop provides you with various types ofpractical materials,such as educational essays, diaryappreciation,sentence excerpts,ancient poems,classic articles,topic composition,work summary,word parsing,copy excerpts,other materials and so on,want to know different data formats andwriting methods,please pay attention!硬质合金刀具涂层工艺流程如下:1. 刀具准备在涂层之前,首先要对刀具进行清洁和检查。
涂层刀具的优点及涂层技术的发展
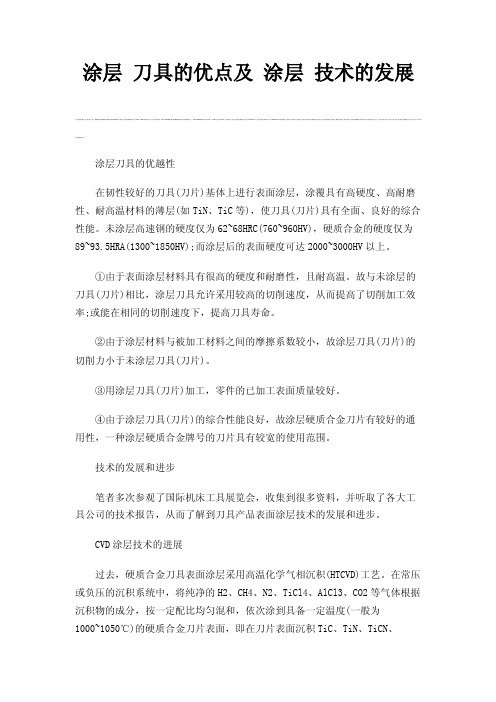
涂层刀具的优点及涂层技术的发展000000000涂层刀具的优越性在韧性较好的刀具(刀片)基体上进行表面涂层,涂覆具有高硬度、高耐磨性、耐高温材料的薄层(如TiN、TiC等),使刀具(刀片)具有全面、良好的综合性能。
未涂层高速钢的硬度仅为62~68HRC(760~960HV),硬质合金的硬度仅为89~93.5HRA(1300~1850HV);而涂层后的表面硬度可达2000~3000HV以上。
①由于表面涂层材料具有很高的硬度和耐磨性,且耐高温。
故与未涂层的刀具(刀片)相比,涂层刀具允许采用较高的切削速度,从而提高了切削加工效率;或能在相同的切削速度下,提高刀具寿命。
②由于涂层材料与被加工材料之间的摩擦系数较小,故涂层刀具(刀片)的切削力小于未涂层刀具(刀片)。
③用涂层刀具(刀片)加工,零件的已加工表面质量较好。
④由于涂层刀具(刀片)的综合性能良好,故涂层硬质合金刀片有较好的通用性,一种涂层硬质合金牌号的刀片具有较宽的使用范围。
技术的发展和进步笔者多次参观了国际机床工具展览会,收集到很多资料,并听取了各大工具公司的技术报告,从而了解到刀具产品表面涂层技术的发展和进步。
CVD涂层技术的进展过去,硬质合金刀具表面涂层采用高温化学气相沉积(HTCVD)工艺。
在常压或负压的沉积系统中,将纯净的H2、CH4、N2、TiCl4、AlCl3、CO2等气体根据沉积物的成分,按一定配比均匀混和,依次涂到具备一定温度(一般为1000~1050℃)的硬质合金刀片表面,即在刀片表面沉积TiC、TiN、TiCN、Al2O3或者它们的复合涂层。
直到现在,HTCVD仍是使用最多的工艺方法,除HTCVD外,还有等离子体化学气相沉积(PCVD)工艺,它是在硬质合金刀具(刀片)表面涂层的另一种方法,因这种涂层工艺温度较低(700~800℃),故刀片的抗弯强度降低。
因为TiC与基体材料的线膨胀系数最接近,通常用TiC薄层先涂在基体表面上,外面再涂TiN、Al2O3,如TiC/TiN、TiC/Al2O3、TiC/TiCN/TiN 等。
硬质合金涂层种类
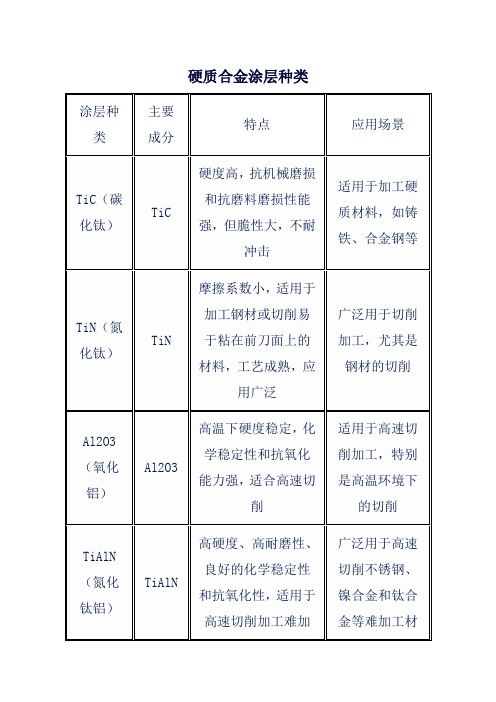
涂层种类
主要成分
特点
应用场景
TiC(碳化钛)
TiC
硬度高,抗机械磨损和抗磨料磨损性能强,但脆性大,不耐冲击
适用于加工硬质材料,如铸铁、合金钢等
TiN(氮化钛)
TiN
摩擦系数小,适用于加工钢材或切削易于粘在前刀面上的材料,工艺成熟,应用广泛
广泛用于切削加工,尤其是钢材的切削
Al2O3(氧化铝)
在某些特定应用场景下,如要求极高耐磨性的场合
CrN(氮化铬)
CrN
高硬度、良好的耐腐蚀性,适用于某些特定切削环境和材料
在需要耐腐蚀性和耐磨性并重的场合
金刚石涂用于极端切削条件,如超硬材料的加工
Al2O3
高温下硬度稳定,化学稳定性和抗氧化能力强,适合高速切削
适用于高速切削加工,特别是高温环境下的切削
TiAlN(氮化钛铝)
TiAlN
高硬度、高耐磨性、良好的化学稳定性和抗氧化性,适用于高速切削加工难加工材料
广泛用于高速切削不锈钢、镍合金和钛合金等难加工材料
WC(碳化钨)
WC
高硬度、高耐磨性,是硬质合金的主要成分之一,也可作为涂层材料使用
PVD涂层硬质合金刀片

刀片材
质
●PVD涂层硬质合金
京瓷公司尚乐特系列的PVD涂层硬质合金是以陶瓷的精细薄
膜技术为基础的,并在铣削加工,车螺纹加工,切槽加工以
及不锈钢的切削中有良好的表现。
通过非常强韧的硬质合金母材和独具的涂层技术实现了优秀
的耐磨损性和涂层薄膜的高速结合性,使刀具寿命更长,加
工稳定。
● 特点
• 从低速加工到高速加工,精加工到重加工都十分适合。
• 高韧性使加工稳定。
• 特殊TiN基础的涂层可做到良好的精加工表面和高精度加
工。
● PVD涂层超硬合金区域图● PR830 涂层● 涂层特性
■ PVD
涂层硬质合金的特性
■ 应用
P
V
D
涂
层
硬
质
合
金
20
21
刀片材质■ 切削数据
P V D 涂层硬质合金。
硬质合金涂层用途

硬质合金涂层用途硬质合金涂层是一种高性能的涂层材料,具有极高的硬度、耐磨性和耐腐蚀性,广泛应用于机械、航空、航天、汽车、电子、医疗等领域。
本文将从涂层的定义、特点、应用领域等方面介绍硬质合金涂层的用途。
涂层是一种在基材表面形成的薄膜,可以改善基材的性能,如增加硬度、耐磨性、耐腐蚀性、导电性等。
硬质合金涂层是一种由钨钴合金和其他金属或非金属元素组成的涂层材料,具有极高的硬度和耐磨性,可以有效地保护基材表面,延长使用寿命。
硬质合金涂层的特点主要有以下几个方面:1. 高硬度:硬质合金涂层的硬度可以达到1500-2500HV,比普通钢材的硬度高出数倍,可以有效地抵抗磨损和划伤。
2. 耐磨性:硬质合金涂层具有极高的耐磨性,可以在高速、高温、高压等恶劣环境下长时间使用。
3. 耐腐蚀性:硬质合金涂层具有良好的耐腐蚀性,可以在酸、碱、盐等腐蚀介质中长时间使用。
4. 导电性:硬质合金涂层具有良好的导电性,可以用于电子、通讯等领域。
硬质合金涂层的应用领域非常广泛,主要包括以下几个方面:1. 机械加工:硬质合金涂层可以用于刀具、钻头、铣刀等机械加工工具的涂层,可以提高切削效率和切削质量。
2. 航空航天:硬质合金涂层可以用于飞机、火箭等航空航天器的表面涂层,可以提高其耐磨性和耐腐蚀性。
3. 汽车工业:硬质合金涂层可以用于汽车发动机、变速器、制动系统等零部件的表面涂层,可以提高其耐磨性和耐腐蚀性。
4. 电子通讯:硬质合金涂层可以用于电子器件、通讯设备等的表面涂层,可以提高其导电性和耐磨性。
5. 医疗器械:硬质合金涂层可以用于医疗器械的表面涂层,可以提高其耐腐蚀性和生物相容性。
硬质合金涂层是一种高性能的涂层材料,具有极高的硬度、耐磨性和耐腐蚀性,广泛应用于机械、航空、航天、汽车、电子、医疗等领域,为各行各业的发展提供了有力的支持。
硬质合金涂层工艺
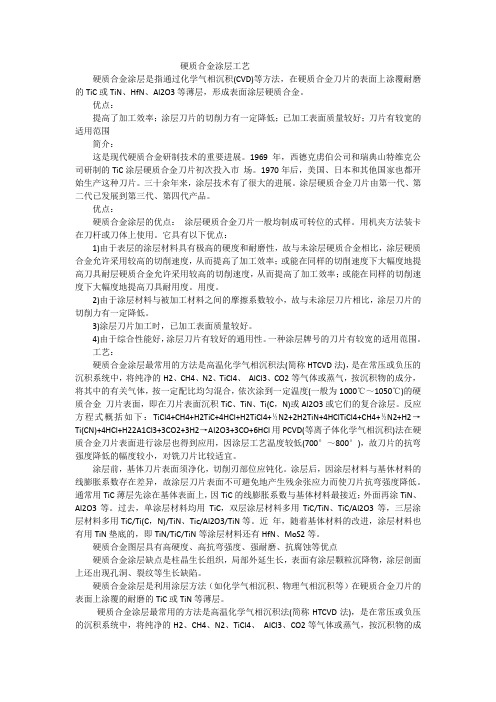
硬质合金涂层工艺硬质合金涂层是指通过化学气相沉积(CVD)等方法,在硬质合金刀片的表面上涂覆耐磨的TiC或TiN、HfN、Al2O3等薄层,形成表面涂层硬质合金。
优点:提高了加工效率;涂层刀片的切削力有一定降低;已加工表面质量较好;刀片有较宽的适用范围简介:这是现代硬质合金研制技术的重要进展。
1969年,西德克虏伯公司和瑞典山特维克公司研制的TiC涂层硬质合金刀片初次投入市场。
1970年后,美国、日本和其他国家也都开始生产这种刀片。
三十余年来,涂层技术有了很大的进展。
涂层硬质合金刀片由第一代、第二代已发展到第三代、第四代产品。
优点:硬质合金涂层的优点:涂层硬质合金刀片一般均制成可转位的式样。
用机夹方法装卡在刀杆或刀体上使用。
它具有以下优点:1)由于表层的涂层材料具有极高的硬度和耐磨性,故与未涂层硬质合金相比,涂层硬质合金允许采用较高的切削速度,从而提高了加工效率;或能在同样的切削速度下大幅度地提高刀具耐层硬质合金允许采用较高的切削速度,从而提高了加工效率;或能在同样的切削速度下大幅度地提高刀具耐用度。
用度。
2)由于涂层材料与被加工材料之间的摩擦系数较小,故与未涂层刀片相比,涂层刀片的切削力有一定降低。
3)涂层刀片加工时,已加工表面质量较好。
4)由于综合性能好,涂层刀片有较好的通用性。
一种涂层牌号的刀片有较宽的适用范围。
工艺:硬质合金涂层最常用的方法是高温化学气相沉积法(简称HTCVD法),是在常压或负压的沉积系统中,将纯净的H2、CH4、N2、TiCl4、AlCl3、CO2等气体或蒸气,按沉积物的成分,将其中的有关气体,按一定配比均匀混合,依次涂到一定温度(一般为1000℃~1050℃)的硬质合金刀片表面,即在刀片表面沉积TiC、TiN、Ti(C,N)或Al2O3或它们的复合涂层。
反应方程式概括如下:TiCl4+CH4+H2TiC+4HCl+H2TiCl4+½N2+2H2TiN+4HClTiCl4+CH4+½N2+H2→Ti(CN)+4HCl+H22A1Cl3+3CO2+3H2→Al2O3+3CO+6HCl用PCVD(等离子体化学气相沉积)法在硬质合金刀片表面进行涂层也得到应用,因涂层工艺温度较低(700°~800°),故刀片的抗弯强度降低的幅度较小,对铣刀片比较适宜。
刀具涂层的特点及用途
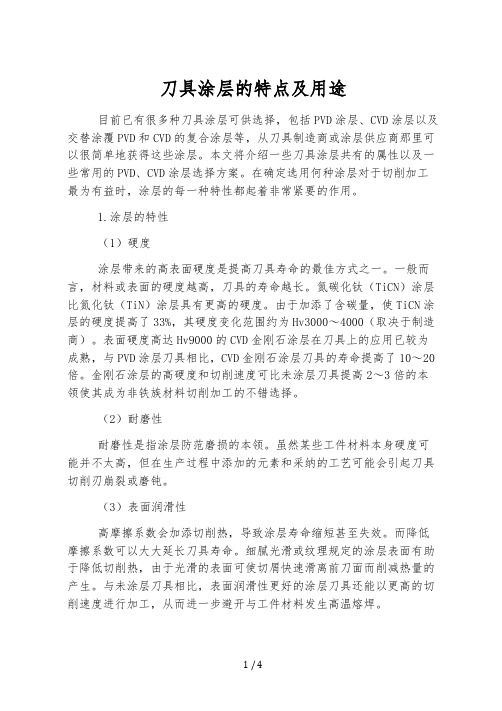
刀具涂层的特点及用途目前已有很多种刀具涂层可供选择,包括PVD涂层、CVD涂层以及交替涂覆PVD和CVD的复合涂层等,从刀具制造商或涂层供应商那里可以很简单地获得这些涂层。
本文将介绍一些刀具涂层共有的属性以及一些常用的PVD、CVD涂层选择方案。
在确定选用何种涂层对于切削加工最为有益时,涂层的每一种特性都起着非常紧要的作用。
1.涂层的特性(1)硬度涂层带来的高表面硬度是提高刀具寿命的最佳方式之一。
一般而言,材料或表面的硬度越高,刀具的寿命越长。
氮碳化钛(TiCN)涂层比氮化钛(TiN)涂层具有更高的硬度。
由于加添了含碳量,使TiCN涂层的硬度提高了33%,其硬度变化范围约为Hv3000~4000(取决于制造商)。
表面硬度高达Hv9000的CVD金刚石涂层在刀具上的应用已较为成熟,与PVD涂层刀具相比,CVD金刚石涂层刀具的寿命提高了10~20倍。
金刚石涂层的高硬度和切削速度可比未涂层刀具提高2~3倍的本领使其成为非铁族材料切削加工的不错选择。
(2)耐磨性耐磨性是指涂层防范磨损的本领。
虽然某些工件材料本身硬度可能并不太高,但在生产过程中添加的元素和采纳的工艺可能会引起刀具切削刃崩裂或磨钝。
(3)表面润滑性高摩擦系数会加添切削热,导致涂层寿命缩短甚至失效。
而降低摩擦系数可以大大延长刀具寿命。
细腻光滑或纹理规定的涂层表面有助于降低切削热,由于光滑的表面可使切屑快速滑离前刀面而削减热量的产生。
与未涂层刀具相比,表面润滑性更好的涂层刀具还能以更高的切削速度进行加工,从而进一步避开与工件材料发生高温熔焊。
(4)氧化温度氧化温度是指涂层开始分解时的温度值。
氧化温度值越高,对在高温条件下的切削加工越有利。
虽然TiAlN涂层的常温硬度或许低于TiCN涂层,但事实证明它在高温加工中要比TiCN有效得多。
TiAlN涂层在高温下仍能保持其硬度的原因在于可在刀具与切屑之间形成一层氧化铝,氧化铝层可将热量从刀具传入工件或切屑。
硬质合金刀具涂层及种类

硬质合金刀具涂层及种类自从20世纪60年代以来,经过近半个世纪的的发展,刀具表面涂层技术已经成为提升刀具性能的主要方法。
刀具表面涂层,主要通过提高刀具表面硬度,热稳定性,降低摩擦系数等方法来提升切削速度,提高进给速度,从而提高切削效率,并大幅提升刀具寿命。
图一 PVD涂层刀具一、涂层工艺刀具涂层技术通常可分为化学气相沉积(CVD)和(PVD)两大类。
1.CVD技术被广泛应用于硬质合金可转位刀具的表面处理。
CVD可实现单成份单层及多成份多层复合涂层的沉积,涂层与基体结合强度较高,薄膜厚度较厚,可达7~9μm,具有很好的耐磨性。
但CVD工艺温度高,易造成刀具材料抗弯强度下降;涂层内部呈拉应力状态,易导致刀具使用时产生微裂纹;同时,CVD工艺排放的废气、废液会造成较大环境污染。
为解决CVD工艺温度高的问题,低温化学气相沉积(PCVD),中温化学气相沉积(MT-CVD)技术相继开发并投入实用。
目前,CVD(包括MT-CVD)技术主要用于硬质合金可转位刀片的表面涂层,涂层刀具适用于中型、重型切削的高速粗加工及半精加工。
2.PVD技术主要应用于整体硬质合金刀具和高速钢刀具的表面处理。
与CVD工艺相比,PVD工艺温度低(最低可低至80℃),在600℃以下时对刀具材料的抗弯强度基本无影响;薄膜内部应力状态为压应力,更适于对硬质合金精密复杂刀具的涂层;PVD工艺对环境无不利影响。
PVD涂层技术已普遍应用于硬质合金钻头、铣刀、铰刀、丝锥、异形刀具、焊接刀具等的涂层处理。
图二 PVD涂层原理物理气相沉积(PVD)在工艺上主要有(1)真空阴极弧物理蒸发(2)真空磁控离子溅射两种方式。
(1)阴极弧物理蒸发(ARC)真空阴极弧物理蒸发过程包括将高电流,低电压的电弧激发于靶材之上,并产生持续的金属离子。
被离化的金属离子以60~100eV平均能量蒸发出来形成高度激发的离子束,在含有惰性气体或反应气体的真空环境下沉积在被镀工件表面。
刀具涂层的种类及作用介绍【汇总】

刀具涂层的种类及作用介绍内容来源网络,由深圳机械展收集整理!更多数控刀具技术展示,就在深圳机械展-刀具展区!刀具涂层的种类1氮化钛涂层(TiN)TiN是一种通用型PVD涂层,是工艺最成熟和应用最广泛的硬质涂层材料,可以提高刀具硬度并具有较高的氧化温度,适用于高速钢切削刀具或成形工具,改善其加工性能。
2氮化铬涂层(CrN)CrN涂层良好的抗粘结性使其在容易产生积屑瘤的加工中成为首选涂层。
涂覆了这种几乎无形的涂层后,高速钢刀具或硬质合金刀具和成形工具的加工性能将会大大改善。
3金刚石涂层(Diamond)CVD金刚石涂层可为非铁金属材料加工刀具提供最佳性能,是加工石墨、金属基复合材料(MMC)、高硅铝合金及许多其它高磨蚀材料的理想涂层。
适用于硬铣、攻丝和钻削加工的涂层各不相同,分别有其特定的使用场合。
此外,还可以采用多层涂层,此类涂层在表层与刀具基体之间还嵌入了其它涂层,可以进一步提高刀具的使用寿命。
4氮碳化钛涂层(TiCN)TiCN涂层中添加的碳元素可提高刀具硬度并获得更好的表面润滑性,是高速钢刀具的理想涂层。
可增加涂层的厚度,阻止裂纹的扩展,减少崩刃。
所以,目前生产的一些刀片,如瑞典Sandvik公司推荐用于加工钢料的GC4000系列刀片、中国株洲硬质合金厂生产的CN系列刀片、日本东芝公司的T715X 和T725X涂层刀片中均有TiCN涂层成份。
TiCN基涂层适于加工普通钢、合金钢、不锈钢和耐磨铸铁等材料,用它加工工件时的材料切除率可提高2~3倍。
株硬--FMA11系列面铣刀5氮铝钛或氮钛铝涂层(TiAlN/AlTiN)TiAlN/AlTiN涂层中形成的氧化铝层可以有效提高刀具的高温加工寿命。
主要用于干式或半干式切削加工的硬质合金刀具可选用该涂层。
根据涂层中所含铝和钛的比例不同,AlTiN涂层可提供比TiAlN涂层更高的表面硬度,因此它是高速加工领域又一个可行的涂层选择。
例如,美国Kennametal公司推出的H7刀片,系TiAlN涂层,是专为高速铣削合金钢、高合金钢和不锈钢等高性能材料而设计的。
- 1、下载文档前请自行甄别文档内容的完整性,平台不提供额外的编辑、内容补充、找答案等附加服务。
- 2、"仅部分预览"的文档,不可在线预览部分如存在完整性等问题,可反馈申请退款(可完整预览的文档不适用该条件!)。
- 3、如文档侵犯您的权益,请联系客服反馈,我们会尽快为您处理(人工客服工作时间:9:00-18:30)。
硬质合金刀具的涂层技术[ 摘要]切削刀具表面涂层技术是近几十年应市场需求发展起来的材料表面改性技术。
采用涂层技术可有效提高切削刀具使用寿命,使刀具获得优良的综合机械性能,从而大幅度提高机械加工效率。
主要介绍涂层硬质合金刀具涂层材料的特点、要求,涂层制备技术,分析化学气相沉积法(CVD)、物理气相沉积法(PVD),单、复合涂层制备方法及优缺点。
[关键字] 硬质合金涂层刀具;化学气相沉积法;物理气相沉积法;现状及发展引言现代化的金属切削加工要求刀具具有高切削速度、高进给速度、高可靠性、长寿命、高精度和良好的切削控制性。
因此, 高水平、稳定的刀具涂层技术越来越受到机械加工企业的青睐。
涂层技术是提高切削效率, 降低加工成本的有效途径。
刀具基体与硬质薄膜表层相结合, 由于基体保持了良好的韧性和较高的强度, 硬质薄膜表层又具有高耐磨性和低摩擦因数, 从而使刀具的性能显著提高, 而且,随着涂层技术设备的日趋集成化、模块化和智能化, 涂层费用已比初期下降1/2~ 2/3, 涂层刀具在刀具总量中所占的比例将会越来越大。
表面涂层硬质合金在基体硬质合金上, 用(CVD)化学气相沉积,或(PVD)物理气相沉积等方法, 涂覆耐磨的TiC、TiN、Al2O3等薄层, 形成表面涂层硬质合金。
涂层硬质合金刀片均为可转位形式, 刚机夹方法装夹在刀杆或刀体上使用。
具有以下优点: 1) 表面涂层材料具有很高的硬度和耐磨性, 故与未涂层刀片相比, 涂层硬质合金可采用较高的切削速度, 或能在同样的切削速度下大幅度地提高刀具耐用度。
2)涂层材料与被加工材料之间的摩擦系数较小, 故切削力有一定减小, 比未涂层刀片约降低 5%左右。
润滑薄膜具有良好的固相润滑性能, 可有效地改善加工质量, 也适合于干式切削加工。
3)用涂层刀片加工, 已加工表面质量较好。
4) 涂层技术作为刀具制造的最终工序, 对刀具精度几乎没有影响, 并可进行重复涂层工艺。
5)由于综合性能好, 涂层刀片有较好的通用性。
一种牌号的刀片经常有较宽的适用范围。
涂层切削刀具所带来的益处: 可大幅度提高切削刀具寿命; 有效地提高切削加工效率; 明显提高被加工工件的表面质量; 有效地减少刀具材料的消耗,降低加工成本; 减少冷却液的使用, 降低成本, 利于环境保护。
1 涂层材料的发展现状与趋势1.1 涂层材料的特点涂层的特点是涂层薄膜与刀具基体相结合, 提高刀具的耐磨性而不降低基体的韧性, 从而降低刀具与工件的摩擦因数, 延长刀具的使用寿命。
此外, 由于涂层自身的热传导系数比刀具基体和加工材料低得多, 可以有效减少摩擦所产生的热量, 形成热屏蔽, 改变热量的散失途经, 从而降低刀具与工件、刀具与切屑之间的热冲击和力冲击, 有效地改善了刀具的使用性能。
刀具涂层所起的作用表现为: 1) 在刀具与被切削材料之间形成隔离层; 2)通过抑制从切削区到刀片的热传导来降低热冲击; 3)有效减少摩擦力及摩擦热。
刀具通过涂层处理, 实现固体润滑, 减少摩擦和粘结, 使刀具吸收热量减少, 从而可承受较高的切削温度。
刀具表面的硬质薄膜要求: 1) 硬度高, 耐磨性能好; 2)化学性能稳定, 不与工件材料发生化学反应; 3)耐热耐氧化, 摩擦因数低, 与基体附着牢固等。
单一涂层材料很难全部达到上述技术要求。
单一涂层向多元复合涂层的发展把不同的涂层材料所具有的优良特性结合起来, 这些特性包括: 由中间层提供高的热稳定性, 由最上层提供高硬度, 或者由软的或固态自润滑层的最上层提供低的摩擦因数。
1.2 国外刀具涂层技术的现状刀具涂层技术通常可分为化学气相沉积(CVD)技术和物理气相沉积(PVD) 技术两大类。
二十世纪六十年代以来,CVD 技术被广泛应用于硬质合金可转位刀具的表面处理。
PVD 技术出现于二十世纪七十年代末,由于其工艺处理温度可控制在500 ℃以下,因此可作为最终处理工艺用于高速钢类刀具的涂层。
工业发达国家自九十年代初就开始致力于硬质合金刀具PVD 涂层技术的研究,至九十年代中期取得了突破性进展,PVD 涂层技术已普遍应用于硬质合金立铣刀、钻头、阶梯钻、油孔钻、铰刀、丝锥、可转位铣刀片、异形刀具、焊接刀具等的涂层处理。
经过几十年的研究和开发,各种刀具涂层工艺已广泛应用于硬质合金和高速钢切削刀具。
涂层工艺的主要发展阶段及应用领域见表1表1 主要涂层工艺发展时段及应用领域当前世界涂层技术的发展具有以下趋势:由于单一涂层材料难以满足提高刀具综合机械性能的要求,因此涂层成分将趋于多元化、复合化;为满足不同的切削加工要求,涂层成分将更为复杂、更具针对性;在复合涂层中,各单一成分涂层的厚度将越来越薄,并逐步趋于纳米化;涂层工艺温度将越来越低,刀具涂层工艺将向更合理的方向发展。
1.3 刀具涂层的分类从PVD 技术的发展和应用角度, PVD涂层可按2 种方法进行分类。
按成分对涂层区分通常可分为两大类, 即硬涂层和软涂层。
硬涂层以TiN、T iCN、TiAlN 等为代表, 包括了单层薄膜和复合薄膜。
软涂层薄膜的硬度相对较低, 通常为1000HV 左右。
软涂层目前种类并不多, 以MoS2、碳基薄膜为主, 在切削加工领域内, 其目的是通过在硬涂层表面覆盖一层这种薄膜, 试图增加涂层表面的润滑性, 改善被加工工件表面质量, 以满足某些应用领域的需要。
涂层的内部结构的变化已越来越多地影响着涂层刀具的应用效果。
相同的涂层成分、不同的结构形式, 可以导致涂层刀具使用效果的截然不同。
就目前PVD 技术的发展状况, 涂层薄膜结构大体可分类如下:( 1) 单一层涂层:涂层由某一种化合物或固溶体薄膜构成, 理论上讲在薄膜的纵向生长方向上涂层成分是恒定的,这种结构的涂层可称之为普通涂层。
( 2) 复合涂层: 由多种不同功能( 特性) 薄膜组成的结构可以称之为复合涂层结构膜, 其典型涂层为目前的硬涂层+ 软涂层, 每层薄膜各具不同的特征, 从而使涂层更具良好的综合性能.( 3) 梯度涂层: 涂层成分沿薄膜纵向生长方向逐步发生变化, 这种变化可以是化合物各元素比例的变化, 如TiAlCN 中Ti、Al 含量的变化, 也可以由一种化合物逐渐过渡到另一种化合物。
( 4) 多层涂层:多层涂层由多种性能各异的薄膜叠加而成, 每层膜化学组分基本恒定。
( 5) 纳米多层涂层:这种结构的涂层与多层涂层类似, 只是各层薄膜的尺寸为纳米数量级, 又可称为超显微结构。
( 6) 纳米复合结构涂层:纳米复合结构涂层。
以( nc-Ti1- x AlxN) / (α-Si3N4) 纳米复合相结构薄膜为例, 在强等离子体作用下, 纳米TiAlN 晶体被镶嵌在非晶态的Si3N4 体内 , 当TiAlN 晶体尺寸小于10nm 时, 位错增殖源难于启动, 而非晶态相又可阻止晶体位错的迁移,即使在较高的应力下, 位错也不能穿越非晶态晶界。
随着涂层技术的进步, 硬质合金刀具涂层种类也在不断地增加, 从单一的化合物涂层朝着多元复杂化合物涂层发展。
通过多次实验, 将单涂层与复合涂层硬质合金的刀具寿命作了比较。
研究结果表明, 复合涂层刀具在提高切削性能方面效果是显著的。
由于复合涂层综合利用各种涂层成分的优点, 使其获得更好的综合性能, 保证了非常好的耐磨性和韧性, 并减少了摩擦力, 因而能减少积屑瘤的形成,并具有抗机械冲击和抗热冲击性能, 刀具寿命可提高2倍以上。
因此, 今后多层涂层刀片使用比例必将不断增加。
2 CVD涂层技术C VD 法是利用气态物质在固体表面发生化学反应, 生成固态沉积物的过程,即在硬质合金工具、模具基体上沉积TiC、TiCN 等涂层,反应进行的方向与各反应物的生成自由能及温度有关。
但该过程中由于基体和涂层之间各元素的扩散和化学反应,容易在基体材料表面形成一层脱碳层(η相层, W3Co3C 或W6Co6C) 。
虽然少量很薄的点状、短线状η相层(小于012μm) 对提高涂层和基体之间的结合强度和耐磨损性能有利,但由于脱碳层硬度高、脆性大,能大幅降低涂层制品的抗弯强度和韧性,从而影响涂层制品的使用性能。
特别是用于精加工的螺纹刀片,由于脱碳层的影响,往往更容易引起刀尖崩刃。
所以在CVD 技术沉积涂层的过程中,应尽量减少脱碳层的产生。
2.1试验方法(1)C VD 涂层工艺设计本试验所选用的硬质合金材料为成都工具研究所生产的CP2 型B8N2 - 3 刀片和标准试验条。
选用以下四种CVD 涂层方案。
GY1 HT(TiC + TiCN + TiC + TiCN) 为高温涂层,每层涂层时间为20min。
TiN 为900 ℃中温涂层,涂层时间为40min ;GY2 第一层中温TiN 涂层时间为20- 40min ,再升温按GY1 涂覆涂层;GY3 第一层MT -TiCN 为中温涂层,时间为30min ,高温涂层HT - (TiC+ TiCN + TiN) 每层涂层时间为40min ;GY4 所有涂层均为低于900 ℃的中温涂层, TiCN 涂层时间为40min ,TiN 涂层时间为50min。
表2 CVD 涂层工艺设定(2)性能检测采用划痕试验机检测涂层的结合强度;用DX-1000 型X射线衍射仪分别对涂层后的试样进行X衍射分析;采用日本奥林巴斯Gx71 光学显微镜观察涂层后的金相组织;每种涂层工艺放5 根试样条进行涂层,然后进行抗弯强度测定。
(3)结果分析与讨论2.2 各CVD 涂层硬质合金刀片划痕实验结果与分析划痕实验是在WS - 2000 涂层附着力自动划痕仪上进行。
该设备主要采用声发射监听记录装置记录涂层破裂时的临界载荷LC ,并以此判断涂层的结合力大小。
本检测采用连续加载方式,加载速度为100N/ m ,终止载荷为100N ,划痕长度为5mm。
不同涂层工艺的临界载荷LC 见表3:表3 不同涂层工艺的平均临界载荷从表3可知,四种工艺涂层的结合强度都很高,都在8kg 左右,远远高于行业推荐的4kg在显微镜下观察划痕形貌都很好。
CVD 涂层后的XRD 结果与分析用DX- 1000 型X射线衍射仪分别对涂层后的试样进行X衍射分析。
X 射线测试采用Cu 靶辐射线进行连续扫描方式,扫描角度2θ范围为28°- 69°,采样时间1s , 波长值1154184A。
,管电压40kV ,管电流25mA。
各涂层工艺试样的η相三强峰峰强比见表4。
由表4 可知,GY1η相峰强比最高,GY2、GY3η相峰强比有所降低,而GY4η相峰强比几乎为0。
由于X射线衍射分析不但能定性的分析物相的存在,各相峰强比也能部分定量的反映物相的多少。
尽管CVD 涂层具有很好的耐磨性,但CVD 工艺亦有其先天缺陷:一是工艺处理温度高,易造成刀具材料抗弯强度下降;二是薄膜内部呈拉应力状态,易导致刀具使用时产生微裂纹;三是CVD 工艺排放的废气、废液会造成较大环境污染,与目前大力提倡的绿色制造观念相抵触,因此自九十年代中期以来,高温CVD 技术的发展和应用受到一定制约。