设备综合效率改善ppt课件
合集下载
oee设备综合效率 ppt课件
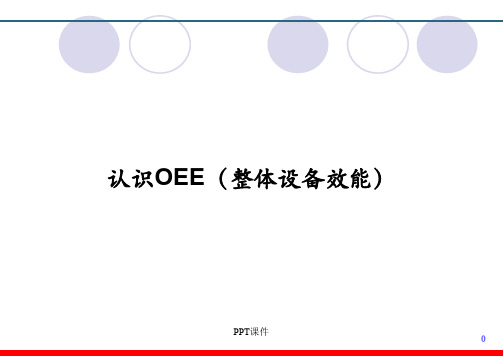
认识OEE(整体设备效能)
PPT课件 0
OEE是什么?
• OEE代表整体设备效能(Overall Equipment Effectiveness) • 这是一种严格的机器总体性能的衡量手段,揭示时间浪费存在于哪里 • 统计各种时间浪费目的在于实现改进
OEE所涵盖的其 他时间损失
传统效率衡量方式 只计算了部分时间
12
6. 质量缺陷
• 定义:在线末或生产流程结束后出现的有缺陷部件
• 由人工记录拒收情况来测量(注:假设每个部件的损坏造成生产该 部件全部时间的损失,从而将损坏部件数量转化为时间损失;假设 返工不在线内进行)
损失
总时间损失
PPT课件 1
OEE用在何时?
OEE用于以明确目的有针对性地支持业务目标的实施 – 限制满足客户需求的价值创造流程能力实现的瓶颈机器设 备 – 利用率必须提高的昂贵设备(如注模设备、压铸设备和冲 压设备)
PPT课件 2
为什么在衡量OEE?
河水与暗礁的比喻
精益生产的目的是要降低库存(河水水位),指出产生生产停顿的潜在 原因(暗礁),清除之使企业能以更强的竞争力即更低水位运作
操作时间
161 - 91.8 = 69.2
机器运转时间
69.2 - 40.3 = 28.9
增值时间
28.9 - 9.7 = 19.2
航天企业举例
计划内停工 = 1 小 时/天
机器故障 = 11.3 小时
换线= 80.5 小时
计划外停工 = 27.4 小时 速度降低 = 12.9 小时
损坏 = 0.3 小时
责任 TP IK, TP TP TP TP IK KB KB IK
• 在本例中,OEE测量同时通过直接PLC记录和手工记录两种方法进行测量,这可以测算出未记录的停工时间并设法
PPT课件 0
OEE是什么?
• OEE代表整体设备效能(Overall Equipment Effectiveness) • 这是一种严格的机器总体性能的衡量手段,揭示时间浪费存在于哪里 • 统计各种时间浪费目的在于实现改进
OEE所涵盖的其 他时间损失
传统效率衡量方式 只计算了部分时间
12
6. 质量缺陷
• 定义:在线末或生产流程结束后出现的有缺陷部件
• 由人工记录拒收情况来测量(注:假设每个部件的损坏造成生产该 部件全部时间的损失,从而将损坏部件数量转化为时间损失;假设 返工不在线内进行)
损失
总时间损失
PPT课件 1
OEE用在何时?
OEE用于以明确目的有针对性地支持业务目标的实施 – 限制满足客户需求的价值创造流程能力实现的瓶颈机器设 备 – 利用率必须提高的昂贵设备(如注模设备、压铸设备和冲 压设备)
PPT课件 2
为什么在衡量OEE?
河水与暗礁的比喻
精益生产的目的是要降低库存(河水水位),指出产生生产停顿的潜在 原因(暗礁),清除之使企业能以更强的竞争力即更低水位运作
操作时间
161 - 91.8 = 69.2
机器运转时间
69.2 - 40.3 = 28.9
增值时间
28.9 - 9.7 = 19.2
航天企业举例
计划内停工 = 1 小 时/天
机器故障 = 11.3 小时
换线= 80.5 小时
计划外停工 = 27.4 小时 速度降低 = 12.9 小时
损坏 = 0.3 小时
责任 TP IK, TP TP TP TP IK KB KB IK
• 在本例中,OEE测量同时通过直接PLC记录和手工记录两种方法进行测量,这可以测算出未记录的停工时间并设法
成型设备改善成果报告ppt课件

●
2000
●
●
2000
3000
3000
●
3000
●
●
3000
核准:
采用PP管及配件:根据给水设计图配 置好PP管及配 件,用 管件在 管材垂 直角切 断管材 ,边剪 边旋转 ,以保 证切口 面的圆 度,保 持熔接 部位干 净无污 物
1.压力管及液压阀密封件老化更换
保养项目
保养前
压力管老 化定期更 换
二:成型5台设备改善展示图
改造日期:2015 服役26年
升级改造: 1.功能修复 2.电气系统+液压系统
服役25年
改造日期:2017
改造日期: 2018
服役26年
问题点: 1.电气系统、功能丧失 2.泵浦老化磨损
问题点: 1.泵浦老化磨损 2.电气系统、动能丧失
问题点: 1.泵浦老化磨损 2.电气系统、动能丧失
保养后
压力管老 化定期更 换,密封 件老化
油箱表面 清洁,毛 刺处理
备注 压力管标 识更换 “日期” 字样
液压阀密 封件更换
定期观察 液压阀渗 油状况
采用PP管及配件:根据给水设计图配 置好PP管及配 件,用 管件在 管材垂 直角切 断管材 ,边剪 边旋转 ,以保 证切口 面的圆 度,保 持熔接 部位干 净无污 物
机台别 改善前
修缮费用 改善后
D2 8240 3850
A2 6220 2830
B3 5860 2200
C4 5510 2500
单位:元
B2 合计 6280 32110 2100 13480
9000
8000
7000
6000
5000 4000Biblioteka 改善前 改善后3000
2024版tpm教材ppt课件

应急处理预案
为关键设备制定应急处理预案,确保在设备突发故障时能够迅速响应, 减少生产中断时间。
06
教育训练与技能提升
TPM教育训练体系构建
制定TPM教育训练计划
根据企业需求和员工实际情况,制定 全面、系统的TPM教育训练计划。
完善教育训练设施
提供完备的教育训练设施,包括教室、 实训场地、教学设备等。
价值体现
TPM能够降低设备维修成本,提高设备利用率和生产效率,进而提高企业竞争力和 经济效益。同时,TPM还有助于培养员工自主管理和团队协作的精神,提升企业整 体管理水平。
02
设备管理与维护策略
设备分类与编码规范
设备分类
根据设备的功能、性质、使用频率等 因素,将设备进行科学合理的分类, 便于后续的管理和维护。
异常处理机制建立
针对可能出现的异常情况,制定 相应的处理措施和流程,确保生
产顺利进行。
04
自主保全活动推进
自主保全概念及意义
自主保全定义
指员工主动参与设备维护、保养和管 理,确保设备正常运行,提高生产效 率的活动。
自主保全的意义
降低设备故障率,提高生产效率,增 强员工责任感和归属感。
自主保全活动步骤与内容
步骤一
步骤二
初期清扫与点检。对设备进行彻底清扫,同 时进行点检,发现潜在问题。
制定自主保全基准。根据设备特性和清扫点 检结果,制定设备维护、保养和管理基准。
步骤三
步骤四
持续开展自主保全活动。按照自主保全基准, 持续开展设备维护、保养和管理活动,确保 设备正常运行。
自主保全成果评价与改善。定期对自主保全 活动成果进行评价,针对存在问题进行改善, 不断提高自主保全水平。
影像管理
为关键设备制定应急处理预案,确保在设备突发故障时能够迅速响应, 减少生产中断时间。
06
教育训练与技能提升
TPM教育训练体系构建
制定TPM教育训练计划
根据企业需求和员工实际情况,制定 全面、系统的TPM教育训练计划。
完善教育训练设施
提供完备的教育训练设施,包括教室、 实训场地、教学设备等。
价值体现
TPM能够降低设备维修成本,提高设备利用率和生产效率,进而提高企业竞争力和 经济效益。同时,TPM还有助于培养员工自主管理和团队协作的精神,提升企业整 体管理水平。
02
设备管理与维护策略
设备分类与编码规范
设备分类
根据设备的功能、性质、使用频率等 因素,将设备进行科学合理的分类, 便于后续的管理和维护。
异常处理机制建立
针对可能出现的异常情况,制定 相应的处理措施和流程,确保生
产顺利进行。
04
自主保全活动推进
自主保全概念及意义
自主保全定义
指员工主动参与设备维护、保养和管 理,确保设备正常运行,提高生产效 率的活动。
自主保全的意义
降低设备故障率,提高生产效率,增 强员工责任感和归属感。
自主保全活动步骤与内容
步骤一
步骤二
初期清扫与点检。对设备进行彻底清扫,同 时进行点检,发现潜在问题。
制定自主保全基准。根据设备特性和清扫点 检结果,制定设备维护、保养和管理基准。
步骤三
步骤四
持续开展自主保全活动。按照自主保全基准, 持续开展设备维护、保养和管理活动,确保 设备正常运行。
自主保全成果评价与改善。定期对自主保全 活动成果进行评价,针对存在问题进行改善, 不断提高自主保全水平。
影像管理
OEE(设备综合效率)分析与管理ppt课件

运行缓慢
库存水平
最新课件
OEE衡量的是礁 石的大小,说明 应该先从哪块暗 礁着手处理。
24
8.OEE可带来的管理效益
1.企业规划: A、可以为企业规划提供客观科學的決策依据。 B、可以为企业提供很多的增值意見和建议。
2.生产管理: A、现场实时数据的收集,建立监控管理系统。 B、对OEE数据分析,规避潜在风险,降低设备六大损失,挖
掘设备最大潜能。 C、为企业精益生产管理提供可视化的生产報告。
最新课件
25
三、OEE的计算方法
2012-8-22
最新课件
26
1.一般企业的时间分类
最新课件
27
1.一般企业的时间分类
最新课件
28
1.一般企业的时间分类
最新课件
29
2.OEE时间分析
最新课件
30
3.设备的六大损失和OEE的关系
最新课件
9
设备运转过快容易造成故障
最新课件
10
您是不是正在制造一个不合格产品
最新课件
11
早晨机器的启动需要花去一定的时间
最新课件
12
二、OEE的定义及开展目的
最新课件
13
1.OEE是什么?
• OEE代表整体设备效能; • 这是一种严格的机器总体性能的衡量手段,揭示时间浪费存
在于哪里,统计各种时间浪费,目的在于实现改进。
最新课件
48
故障是冰山的一角
“如果我们问一问为什么会发生这样的情况——为什么、为什 么、—— 我们通常能找出问题,以及解决问题的方法。
最新课件
49
故障是冰山的一角
故故障障
•灰•灰尘尘、、污污垢垢、、原原料料粘粘附附 •磨•磨损损、、偏偏斜斜、、松松动动、、泄泄露露 •腐•腐蚀蚀、、变变形形、、伤伤痕痕、、裂裂纹纹 •温•温度度、、震震动动、、声声音音等等异异常常
生产效率改善方法-设备综合效率(OEE)改善
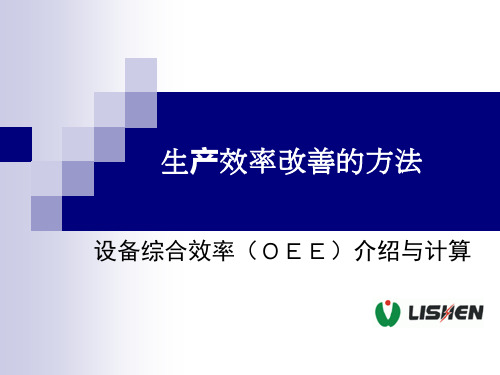
轴向导轨看上去发干!
1. 润滑不当产生的问题?
马达负荷增加、速度减慢、磨损造成精度 不良、异常停机..
对OEE的影响?
2. 脏物污染产生的问题?
(生活中的例子)
1) 空调滤网 2) 冰箱异味 3) 电脑死机
4) 抽油烟机=油物染
5) 电视=灰尘=短路
2. 量化管理的作用
量化后的设备管理现状
质量 缺陷
故障
设置和 调整
停机
7大浪费
物资浪费(Material)
没有的浪费 库存的浪费 搬运的浪费 拿、放的浪费 等待的浪费 困难工序的浪费
人力浪费(Man)
步行浪费 寻找浪费 工序动作浪费 看不见的浪费 设备浪费(Machine)
大型机械的浪费 法定机械的浪费 传送带的浪费 空气加工的浪费 故障的浪费 机械等待的浪费
突发故障时间 换线、调整、测试 物料更换..等
小 时
负 荷 时 间 T L 运 转 时 间 O L
速 度 损 失
速度降低损失时间
空转时间 待料、人员调动
OEE=?
24
有 效 生 产 时 间 Q L
无效价值的时间 (返工、报废品)
生产良品的时间 有价值的设备使用
设备损失结构分析图
正
设备损失结构 休息时间 停 管理对象外 止 时间 计划停止之 时 时间
量化A、B、C
TL可运行时间24 hrs AL计划运行时间21 hrs OL实际运行时间17 hrs QL有效产出时间15hrs
间 负 荷 无负荷时间 停机时间
常
参考定义 影响设备运转之时间---人的休息时间 生产计划规定的休息时间 朝会(每日10分)、发表会、参加讲习会、教育训练、消防演习、健康检查、预 防注射、盘点、试作、原动力设施之停止引起设备之停止时间 计划的预防保全、改良保养时间 1700活动、TPM活动日,每日下班之清扫10分钟 外注品或其他工程部品延迟纳入引起之待料
设备综合效率OEE演示幻灯片ppt课件

6
认识到了贫困户贫困的根本原因,才 能开始 对症下 药,然 后药到 病除。 近年来 国家对 扶贫工 作高度 重视, 已经展 开了“ 精准扶 贫”项 目
六大损失定义
• 停机:未预料到的大于10分钟的设备停机,丧失原有功 能或需要更换零部件的时间。
• 设置和调整:从上一个生产品种生产结束到下一个生产 品种生产出来
17
认识到了贫困户贫困的根本原因,才 能开始 对症下 药,然 后药到 病除。 近年来 国家对 扶贫工 作高度 重视, 已经展 开了“ 精准扶 贫”项 目
案例:单台设备综 合 设 备 效 率 (OEE)计算
例题:
❖ 假设有一工厂某设备某班某天工作时间为8小时,其 中用餐、休息时间为1小时,在上线和收工之前的开 会、点检、清扫需费时30分钟,因突发故障而停机时 间为20分钟,而且每天必须换线2次,每次15分钟, 每天必须更换刀具1次,费时10分钟;生产线生产周 期为0.4分钟,当天生产数量为750个产品,其中不 合格品为50个。请计算其总设备效率。
开动时间 负荷时间
实际生产量 理论生产量
合格品数量 加工量
14
认识到了贫困户贫困的根本原因,才 能开始 对症下 药,然 后药到 病除。 近年来 国家对 扶贫工 作高度 重视, 已经展 开了“ 精准扶 贫”项 目
【OEE】要注意的问题
❖ 我们做OEE不是为了在数字和报表中体现我们的 OEE达到了多么要的水平,如果OEE超过了100%, 那就说明我们的理论循环时间设置偏大(亦即单位 时间里的理论产量设置偏低),要么就是我们在负 荷运行(透支设备的未来水平)。而这两种情况当 然是要不得的。
❖性能开动率: 按瓶颈工序理论C/T 基准 ❖合格品率: 检查工序或者最终工序为基准,合格 品数量上再排除返工的数量
认识到了贫困户贫困的根本原因,才 能开始 对症下 药,然 后药到 病除。 近年来 国家对 扶贫工 作高度 重视, 已经展 开了“ 精准扶 贫”项 目
六大损失定义
• 停机:未预料到的大于10分钟的设备停机,丧失原有功 能或需要更换零部件的时间。
• 设置和调整:从上一个生产品种生产结束到下一个生产 品种生产出来
17
认识到了贫困户贫困的根本原因,才 能开始 对症下 药,然 后药到 病除。 近年来 国家对 扶贫工 作高度 重视, 已经展 开了“ 精准扶 贫”项 目
案例:单台设备综 合 设 备 效 率 (OEE)计算
例题:
❖ 假设有一工厂某设备某班某天工作时间为8小时,其 中用餐、休息时间为1小时,在上线和收工之前的开 会、点检、清扫需费时30分钟,因突发故障而停机时 间为20分钟,而且每天必须换线2次,每次15分钟, 每天必须更换刀具1次,费时10分钟;生产线生产周 期为0.4分钟,当天生产数量为750个产品,其中不 合格品为50个。请计算其总设备效率。
开动时间 负荷时间
实际生产量 理论生产量
合格品数量 加工量
14
认识到了贫困户贫困的根本原因,才 能开始 对症下 药,然 后药到 病除。 近年来 国家对 扶贫工 作高度 重视, 已经展 开了“ 精准扶 贫”项 目
【OEE】要注意的问题
❖ 我们做OEE不是为了在数字和报表中体现我们的 OEE达到了多么要的水平,如果OEE超过了100%, 那就说明我们的理论循环时间设置偏大(亦即单位 时间里的理论产量设置偏低),要么就是我们在负 荷运行(透支设备的未来水平)。而这两种情况当 然是要不得的。
❖性能开动率: 按瓶颈工序理论C/T 基准 ❖合格品率: 检查工序或者最终工序为基准,合格 品数量上再排除返工的数量
OEE(设备综合效率)分析与管理 PPT

传统效率衡量方 式只计算了部分
时间损失
总时间损 失
1.OEE是什么?
* O verall * E quipment * E fficiency
综合 设备 效率
2.OEE和TEEP的总体水平
3.时间开动率
时
计划内停机时间
1.开
3.一级保养时间
动
4.换模试模时间 5.计划维修时间
设备运转过快容易造成故障
您是不是正在制造一个不合格产品
早晨机器的启动需要花去一定的时间
二、OEE的定义及开展目的
1.OEE是什么?
• OEE代表整体设备效能; • 这是一种严格的机器总体性能的衡量手段,揭示时间浪费存
在于哪里,统计各种时间浪费,目的在于实现改进。
OEE所涵盖的 其他时间损失
OEE分析与管理
目录
01 设备的六大损失与管理 02 OEE的定义及开展目的 03 OEE的计算方法 04 OEE的数据收集与分析
一、设备的六大损失与管理
LEAN-识别八种浪费
因人造 成的浪 费
因设备 造成的 浪费
• Correction 返工 • Conveyance 搬运 • Motion 多余动作 • Waiting 等待 • Processing 过程不当 • management 管理 • Inventory 库存 • Overproduction 过量生产
思考:
设备OEE>100%是否成立?为什么?
7.OEE衡量的目的?
河水与暗礁的比喻
精益生产的目的是要降低库存(河水水位),指出产生生产停顿的潜在原因(暗 礁),清除之使企业能以更强的竞争力即更低水位运作。
通过使企业的库存强制减 少到某个既定目标,企业 可以降低水位,主动使暗 礁浮出水面,从而可以清 除礁石或降低暗礁高度
设备综合效率OEE实战(管理篇) ppt课件

2、设备综合效率OEE的原理
设备
6大LOSS
计算设备综合效率
负荷时间
停
运转时间
止 损
失
实际
速 度
运转时间 损
失
不
创造价值 良 运转时间 损
失
(1)故障 (2)作业准备、调整
时间运转率
=
负荷时间-停止时间 负荷时间
×100%
(3)空转、瞬间停止 (4)速度低下
一、认识设备综合效率OEE
2、设备的效率损失在哪里?
1)故障停止损失
故障可分为功能停止型故障和功能下 降型故障两大类。
故障损失是阻碍效率的最大原因。
2)作业准备、调整损失
设备加工部品前的准备、调整阶段停 机就是准备、调整损失。
其中“ 调整时间”有时很长。
停止 LOSS 停机
准备和调整
一、认识设备综合效率OEE
提升设备综合效率实战 管理篇
课程目录
➢ 认识设备综合效率OEE ➢ 如何计算设备的综合效率OEE ➢ 设备综合效率的现场应用
一、认识设备综合效率OEE
1、设备运行效率为什么这么低 2、设备的效率损失在哪里? 3、 OEE的由来与应用! 4、 为什么要使用OEE管理?
一、认识设备综合效率OEE
1. 设备运行效率为什么这么低
设备六大损失
负荷时间
停
运转时间
止 损
失
性
纯运转 能 时间 损
失
不
创造价值 良 运转时间 损
失
(1)故障 (2)作业准备、调整
(3)空转、瞬间停止 (4)速度低下
(5)工程不良 (6)初期修整
设备六 大LOSS
完全有效生产率 TEEP
【全面版】设备综合效率 介绍PPT文档

•表现指数 (性能工作效率) (可用率*表现指数*质量指数 )
OEE Instruction
表有现助指 于数发通现常最用大许的10改0多%进表公空示间,司并这获有样得能一资保产证系上避最列免大如关程果度一于的个回生节报拍产时间节太拍短而的造成计计算算混:乱。
表现指数 (理想节拍时间 产品生产数) 操作时间 = * / 提高设备的OEE则要借助于其它如TDC(True Downtime Cost),RCA(Root Cause Analysis),FTA(Fault Tree Analysis)等工具。
当你正致力于将设备的生产力向世界级发展时,简单的TEEP公式 将是一个优秀的基本工具 TEEP=实际生产件数/全部时间内理论生产件数 全部时间:一天按24小时计
一周按168小时计... 一般来说统计周期的时间越长显示的TEEP可能越低。
如:HGAI每小时理论产出220PCS HSA,一周(6.5天)生产
How to use OEE?
全不部要时 在间如❖:何帮一最天好助按地企利24用小业时OE计关E的注问题改上有进任何现的有犹豫设备的表现 (O可E用E I率n❖s*tr表u有c现tio指n助数*于质量发指现数 )最大的改进空间并获得资产上最大程度的回报
可作为设备可靠性及利用率的分析或基准计算的工具。
OEE Instruction
How to use OEE?
OEE的应用形式多种多样。可作为设备可靠性及利用率的分析或 基准计算的工具。 不要在如何最好地利用OEE的问题上有任何的犹豫 可从小处着手,选择瓶颈设备来收集OEE的有关数据 一旦获得的第一手资料显出OEE是有价值的工具,就可以逐渐地 用OEE测量其它的设备 OEE只用于测量或监控设备的综合性能,不能真正带来成本上的 收益
OEE Instruction
表有现助指 于数发通现常最用大许的10改0多%进表公空示间,司并这获有样得能一资保产证系上避最列免大如关程果度一于的个回生节报拍产时间节太拍短而的造成计计算算混:乱。
表现指数 (理想节拍时间 产品生产数) 操作时间 = * / 提高设备的OEE则要借助于其它如TDC(True Downtime Cost),RCA(Root Cause Analysis),FTA(Fault Tree Analysis)等工具。
当你正致力于将设备的生产力向世界级发展时,简单的TEEP公式 将是一个优秀的基本工具 TEEP=实际生产件数/全部时间内理论生产件数 全部时间:一天按24小时计
一周按168小时计... 一般来说统计周期的时间越长显示的TEEP可能越低。
如:HGAI每小时理论产出220PCS HSA,一周(6.5天)生产
How to use OEE?
全不部要时 在间如❖:何帮一最天好助按地企利24用小业时OE计关E的注问题改上有进任何现的有犹豫设备的表现 (O可E用E I率n❖s*tr表u有c现tio指n助数*于质量发指现数 )最大的改进空间并获得资产上最大程度的回报
可作为设备可靠性及利用率的分析或基准计算的工具。
OEE Instruction
How to use OEE?
OEE的应用形式多种多样。可作为设备可靠性及利用率的分析或 基准计算的工具。 不要在如何最好地利用OEE的问题上有任何的犹豫 可从小处着手,选择瓶颈设备来收集OEE的有关数据 一旦获得的第一手资料显出OEE是有价值的工具,就可以逐渐地 用OEE测量其它的设备 OEE只用于测量或监控设备的综合性能,不能真正带来成本上的 收益
- 1、下载文档前请自行甄别文档内容的完整性,平台不提供额外的编辑、内容补充、找答案等附加服务。
- 2、"仅部分预览"的文档,不可在线预览部分如存在完整性等问题,可反馈申请退款(可完整预览的文档不适用该条件!)。
- 3、如文档侵犯您的权益,请联系客服反馈,我们会尽快为您处理(人工客服工作时间:9:00-18:30)。
9
TPM定义
通过设备为导向的管理,将现有设备的表现 最优化;就是使设备在其寿命周期内保持生 产能力最大化的系统方法和过程
提升设备的有效稼动率及生产能力的过程 维持设备的稳定性,以消除设备变动对产品
质量、产量的干扰的过程 培养对设备关心、爱惜的作业人员与环境
10
定义说明
TPM的目的在于设备保养、消除计划外停机 TPM是改进生产与维护人员协作关系的常规方法
质量 缺陷
故障
设置和 调整
时间
停机
23
7大浪费
物资浪费(Material) 没有的浪费 库存的浪费 搬运的浪费 拿、放的浪费 等待的浪费 困难工序的浪费
作业方法浪费(Method) Lot的浪费 库存的浪费 搬运的浪费 拿、放的浪费 困难工序的浪费
人力浪费(Man) 步行浪费 寻找浪费 工序动作浪费 看不见的浪费
生产效率改善的方法
设备综合效率(OEE)介绍与计算
1
课程目的
1. 了解TPM对企业的重要与TPM的组成部分 2. OEE的定义 3. OEE的目的及作用 4. OEE的理论及计算和如何改善OEE 5. 理解5S与改善OEE 的关系 6. 如何建立和维护设备的历史记录,评价目前
的OEE水平 7. 定义支持OEE的组织和角色
如果我们不关注TPM, 那些情况很可能发生, 或是常看到
1-4
27
一般情况
故障常常发生 临时性的维修频繁 生产中断常常发生 生产过程速度降低 产生成本的浪费 设备状态不稳定(使用时不良、保养时OK) 有人抱怨、没人改善 没有人量化过这种损失
主动思维
通过分析指标构成来寻找生产过程改善空间和 方法;
超前思维
实现设备导向型管理模式。
18
1. 问题引入
19
当前公司的主要关注点
客户
生产力
为中心 WTO 全球性竞争
员工参与
20
生产活动中的16大损失
与设备有关的8大损失
- 计划性的停机和试车/故障/更换品种/设定和调节 /启动和停机/小停机和空转/速度损失/质量缺陷返工 (安装调整、空转短暂停机、试生产)
管理浪费(Management) 资料的浪费 会议的浪费 管理的浪费 通讯的浪费 收据的浪费
遵守安全( Safety ) 防止灾害,事故 灾害事故是浪费以前的浪费 所有解除浪费是安全第一
设备浪费(Machine) 大型机械的浪费 法定机械的浪费 传送带的浪费 空气加工的浪费 故障的浪费 机械等待的浪费
的活 动中,并与企业得到共同的发展
- 通过各项有效工具的开展,挑战零事故,零损失,零缺陷和零 浪费,追求生产和经营效率的极限
8
TPM Objective TPM目标
* Zero accident 零事故
* Zero breakdown and loss 零故障损失
* Zero defect and complaint 零过失及抱怨
4
什么是OEE? Leabharlann 文翻译:设备综合效率 英文名称:
Overall Equipment Effectiveness
作用:生产过程中设备使用效率的一种评 价方法
5
0. 关于TPM
7
Total Productive Maintenance
TPM是“全员共同参与的生产力维护和管理”的简称,是一套综 合性的企业管理体系,以帮助我们建立并维护适合本企业经营和 发展的各类管理系统
与人有关的5大损失
- 生产线布局损失/后勤和运输/管理损失/测量和调 节损 失/操作运动损失
其它方面的3大损失
- 工夹具损失/能源损失/原材料损失
21
设备的6大损失
设备故障 安装与调整 空转短暂停机 速度降低 加工废品 试生产
22
6大损失的形象化
100
%
速度损失
生产能力
启动
小停车 和空转
1-3
12
TPM如何帮助我们?
增进操作人员与 维修人员的团队工作
帮助减少浪费
改善人因 工学
故障后的维护 成本昂贵 (10X)
阐明一个完整的 维护计划
13
TPM活动概要
1970 日本爱知县“日本电装株式会社”为了彻底实施“丰田 生产方式”首度采用“TPM”
TPM效果 生产力 + 400% 故障率 1% 生产不良率 0.3% 1971年获 JIPM协会 “第一类PM优秀奖”
其他日本企业跟进
14
TPM活动的目的
改变对设备的看法、与管理
TPM
设备
生产
15
TPM活动的目的
改变对设备的看法、与管理
设备
TPM
生产
16
问题:
如何评价TPM的效果? 如何利用TPM活动提升高生产效率?
17
引申(回顾)
被动思维
反映了生产管理(含技术、质量)和设备管理 的效果;
包括检查、日常保养、维修、预防/预测性维护等 各种手段 TPM准时化生产的必要条件 TPM过程旨在培养一种环境,以鼓励员工致力于 安全、质量和效率方面的团队努力和创造力
11
TPM 就是使设备在整个寿命期内生产能力
最大化的过程
TPM 旨在培养一种环境
•鼓励全员参与的 •致力于安全、质量、成本、贡献和 创造力方面的努力
质量浪费(Quality) 做出不良品的浪费 维修不良品的浪费 犯错误的浪费 检查的浪费 质量管理的浪费
25
目前的生产环境
(设备与生产的紧密关系)
设备性能决定 产品质量水平 设备能力决定 产品产出能力 设备的费用 是生产成本的第二大项,决定了是
盈利水平
26
我们力神的设备会有哪些情况?
(项目负责人、主管、维护人员、操作员)
8. 掌握实施OEE改善的方法 9. OEE系统
2
课程对我的帮助
加深理解TPM的内容与对企业的重要 认识OEE与OEE计算方法 理解OEE改善项目中的角色 能够计划和实施OEE改善活动 认识OEE系统
3
解决疑惑
OEE就是一项普通的考核指标; OEE是设备人员的事; OEE考核管理给操作人员带来麻烦; 。。。。。。
在TPM系统中包含有大量有效的工具,我们可以运用它们以提高 企业安全健康环保,质量,服务和成本等各方面的管理水平
我们在企业内开展TPM是为了: - 在企业内建立起团队合作和主人翁精神的企业文化 - 使企业中的所有部门都参与到TPM的管理系统中 - 企业中的所有人(从最高层领导到一线的员工)都参与到TPM
TPM定义
通过设备为导向的管理,将现有设备的表现 最优化;就是使设备在其寿命周期内保持生 产能力最大化的系统方法和过程
提升设备的有效稼动率及生产能力的过程 维持设备的稳定性,以消除设备变动对产品
质量、产量的干扰的过程 培养对设备关心、爱惜的作业人员与环境
10
定义说明
TPM的目的在于设备保养、消除计划外停机 TPM是改进生产与维护人员协作关系的常规方法
质量 缺陷
故障
设置和 调整
时间
停机
23
7大浪费
物资浪费(Material) 没有的浪费 库存的浪费 搬运的浪费 拿、放的浪费 等待的浪费 困难工序的浪费
作业方法浪费(Method) Lot的浪费 库存的浪费 搬运的浪费 拿、放的浪费 困难工序的浪费
人力浪费(Man) 步行浪费 寻找浪费 工序动作浪费 看不见的浪费
生产效率改善的方法
设备综合效率(OEE)介绍与计算
1
课程目的
1. 了解TPM对企业的重要与TPM的组成部分 2. OEE的定义 3. OEE的目的及作用 4. OEE的理论及计算和如何改善OEE 5. 理解5S与改善OEE 的关系 6. 如何建立和维护设备的历史记录,评价目前
的OEE水平 7. 定义支持OEE的组织和角色
如果我们不关注TPM, 那些情况很可能发生, 或是常看到
1-4
27
一般情况
故障常常发生 临时性的维修频繁 生产中断常常发生 生产过程速度降低 产生成本的浪费 设备状态不稳定(使用时不良、保养时OK) 有人抱怨、没人改善 没有人量化过这种损失
主动思维
通过分析指标构成来寻找生产过程改善空间和 方法;
超前思维
实现设备导向型管理模式。
18
1. 问题引入
19
当前公司的主要关注点
客户
生产力
为中心 WTO 全球性竞争
员工参与
20
生产活动中的16大损失
与设备有关的8大损失
- 计划性的停机和试车/故障/更换品种/设定和调节 /启动和停机/小停机和空转/速度损失/质量缺陷返工 (安装调整、空转短暂停机、试生产)
管理浪费(Management) 资料的浪费 会议的浪费 管理的浪费 通讯的浪费 收据的浪费
遵守安全( Safety ) 防止灾害,事故 灾害事故是浪费以前的浪费 所有解除浪费是安全第一
设备浪费(Machine) 大型机械的浪费 法定机械的浪费 传送带的浪费 空气加工的浪费 故障的浪费 机械等待的浪费
的活 动中,并与企业得到共同的发展
- 通过各项有效工具的开展,挑战零事故,零损失,零缺陷和零 浪费,追求生产和经营效率的极限
8
TPM Objective TPM目标
* Zero accident 零事故
* Zero breakdown and loss 零故障损失
* Zero defect and complaint 零过失及抱怨
4
什么是OEE? Leabharlann 文翻译:设备综合效率 英文名称:
Overall Equipment Effectiveness
作用:生产过程中设备使用效率的一种评 价方法
5
0. 关于TPM
7
Total Productive Maintenance
TPM是“全员共同参与的生产力维护和管理”的简称,是一套综 合性的企业管理体系,以帮助我们建立并维护适合本企业经营和 发展的各类管理系统
与人有关的5大损失
- 生产线布局损失/后勤和运输/管理损失/测量和调 节损 失/操作运动损失
其它方面的3大损失
- 工夹具损失/能源损失/原材料损失
21
设备的6大损失
设备故障 安装与调整 空转短暂停机 速度降低 加工废品 试生产
22
6大损失的形象化
100
%
速度损失
生产能力
启动
小停车 和空转
1-3
12
TPM如何帮助我们?
增进操作人员与 维修人员的团队工作
帮助减少浪费
改善人因 工学
故障后的维护 成本昂贵 (10X)
阐明一个完整的 维护计划
13
TPM活动概要
1970 日本爱知县“日本电装株式会社”为了彻底实施“丰田 生产方式”首度采用“TPM”
TPM效果 生产力 + 400% 故障率 1% 生产不良率 0.3% 1971年获 JIPM协会 “第一类PM优秀奖”
其他日本企业跟进
14
TPM活动的目的
改变对设备的看法、与管理
TPM
设备
生产
15
TPM活动的目的
改变对设备的看法、与管理
设备
TPM
生产
16
问题:
如何评价TPM的效果? 如何利用TPM活动提升高生产效率?
17
引申(回顾)
被动思维
反映了生产管理(含技术、质量)和设备管理 的效果;
包括检查、日常保养、维修、预防/预测性维护等 各种手段 TPM准时化生产的必要条件 TPM过程旨在培养一种环境,以鼓励员工致力于 安全、质量和效率方面的团队努力和创造力
11
TPM 就是使设备在整个寿命期内生产能力
最大化的过程
TPM 旨在培养一种环境
•鼓励全员参与的 •致力于安全、质量、成本、贡献和 创造力方面的努力
质量浪费(Quality) 做出不良品的浪费 维修不良品的浪费 犯错误的浪费 检查的浪费 质量管理的浪费
25
目前的生产环境
(设备与生产的紧密关系)
设备性能决定 产品质量水平 设备能力决定 产品产出能力 设备的费用 是生产成本的第二大项,决定了是
盈利水平
26
我们力神的设备会有哪些情况?
(项目负责人、主管、维护人员、操作员)
8. 掌握实施OEE改善的方法 9. OEE系统
2
课程对我的帮助
加深理解TPM的内容与对企业的重要 认识OEE与OEE计算方法 理解OEE改善项目中的角色 能够计划和实施OEE改善活动 认识OEE系统
3
解决疑惑
OEE就是一项普通的考核指标; OEE是设备人员的事; OEE考核管理给操作人员带来麻烦; 。。。。。。
在TPM系统中包含有大量有效的工具,我们可以运用它们以提高 企业安全健康环保,质量,服务和成本等各方面的管理水平
我们在企业内开展TPM是为了: - 在企业内建立起团队合作和主人翁精神的企业文化 - 使企业中的所有部门都参与到TPM的管理系统中 - 企业中的所有人(从最高层领导到一线的员工)都参与到TPM