铸造工艺结构
铸件的结构设计

(a)直角连接 (b)圆角连接 图6-35 转角处的热节
(a)直角连接 (b)圆角连接 图6-36 金属结晶的方向性
2.避免锐角连接
如图6-37(a)所示,锐角连接会由于 内角散热条件差而增大热节,容易产生缩 孔、缩松等铸造缺陷。若两壁间的夹角小 于90°,则应采取过渡形式,如图6-37(b) 所示。
(b)改进后
图6-31 内腔的两种结构
2.便于砂芯固定、排气和铸件清理
如图6-32(a)所示,轴承架铸件的内腔需要采用两个砂芯,其中较 大的砂芯呈悬臂状,需用型芯撑支撑固定;如图6-32(b)所示,将轴承 架铸件的内腔改为整体砂芯,则砂芯的稳定性大大提高,并有利于排气。
(a)改进前
(b)改进后
图6-32 轴承架铸件
铸件中垂直于分型面的不 加工表面最好有结构斜度,以 便于起模或者便于用砂垛代替 砂芯。如图6-34(a)所示的铸 件结构设计不合理,对铸件的 结构斜度进行改进后的合理设 计如图6-34(b)所示。
(a)改进前
(b)改进后
图6-34 结构斜度的设计
二、合金铸造性能对铸件结构的要求
(一)铸件壁厚设计合理
工程材料及成形工艺
铸件的结构设计
一、铸造工艺对铸件结构的要求
铸件的结构设计不应只考虑对其结构性能的影响,还应有利于提高 铸件的工艺水平。所以铸件结构应尽可能使制模、造型、造芯、合箱和 清理过程简单化,防止产生废品,并为实现机械化生产创造条件。铸件 外形力求简单,铸件内腔设计合理是铸造工艺对铸件结构的主要要求。
为保证金属液充满铸型,避免浇不足、冷隔等缺陷的产生,铸件应当有合理 的壁厚。每种铸造合金都有其适宜的壁厚,选择得当,既能保证铸件力学性能, 又能防止铸造缺陷的产生。几种常用铸件在砂型铸造时的最小壁厚如表6-7所示。
第二章-铸造工艺方案的确定
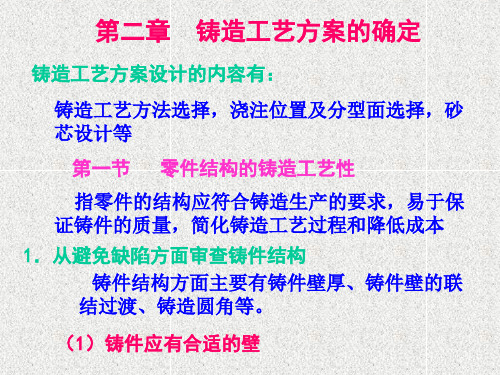
课堂讨论 图3-2-26
1.应使铸件全部或大部分置于同一半型内
图2-15 轮毂分型方案
2.应尽可能减少分型面数目 铸件的分型面少,铸件精度容易保ቤተ መጻሕፍቲ ባይዱ,且砂箱数目 少
图2-16 确定分型面数目的实例
3.平直分型面和曲折分型面的选择 尽可能选择平直分型面以简化工装结构及
其制造、加工工序和造型操作
图2-17 摇臂铸件的分型面
最小壁厚/㎜
高温合金
铝合金
0.6~1.0
1.5~2.0
0.8~1.5
2.0~2.5
1.0~2.0
2.5~3.0
—
3.0~3.5
—
3.5~4.0
铸件尺寸㎜
50×50 100×100 225×225
金属型铸造时铸件的最小壁厚
铝硅合 金
最小壁厚/㎜
铝镁合金、镁合 铜合金 金
灰铸铁
2.2
3
2.5
3
2.5
3
3
(1)改进妨碍起模的凸台、凸缘和肋板结构
改进妨碍起模的铸件结构 a)不合理 b)合理
教材220面,学生看,老师提问
(2)尽量取消铸件外表侧凹
图2-6 外壁内凹的框形件 a)不合理 b)合理
(3)有利于砂芯的固定和排气 (4) 减少或简化分型面(P221)
轴承架铸件
P222
(5)便于铸件的清理 (P222,图3-2-15) (6)简化模具制造 (P222,图3-2-16)
原则:
铸件精度和生产批量 吃砂量要求 吃砂量的确定
吃砂量: 铸件表面所需要的的最小型砂厚度。
根据铸件大小、重量、厚度、种类以 及型砂的特性和砂箱的结构确定。
吃砂量过小 砂型紧实困难,易引起胀砂、包砂、掉砂、
零件上常见的工艺结构
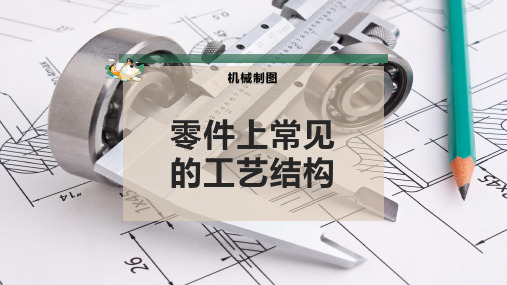
(c)正确
(d)错误
图8-58 钻孔应注意的问题
(e)正确
(a)不合理 (b)合理
图8-59 钻孔的方便性
机械制图
谢谢观看!
(a)
(b)
图8-55 退刀槽和砂轮越程槽
(c)
1.2 机械加工工艺结构 3.凸台和凹坑
为了保证零件表面在装配时接触良好和减少机械加工 的面积,常在零件表面上设计出凸台或凹坑,并尽量使多 个凸台在同一水平面上,以便于加工,如图8-56所示。
图8-56 凸台和凹坑
1.2 机械加工工艺结构
4.钻孔结构
1.2 机械加工工艺结构
2.退刀槽和砂轮越程槽
切削时(主要是车削和磨削),为了便于退出刀具或 砂轮,常在待加工面的轴肩处预先车出退刀槽和砂轮越程 槽。这样既能保证加工表面满足加工技术要求,又便于装 配时相关零件间靠紧。常见退刀槽和砂轮越程槽的简化画 法及尺寸标注如图8-55所示。
1.2 机械加工工艺结构机 Nhomakorabea制图零件上常见 的工艺结构
零件上常见的工艺结构
零件的结构形状主要是由零件在机器中的作用以及 其制造工艺所决定的。因此,零件的结构除满足使用要 求外,还应具有合理的工艺结构。零件上常见的工艺结 构有铸造工艺结构、机械加工工艺结构等。
1.1 铸造工艺结构
铸造是指将熔融的液态金属或合金浇入砂型型腔中, 待其冷却凝固后获得的具有一定形状和性能的铸造零件 的方法。铸造的工艺结构包括铸造圆角、起模斜度和铸 件壁厚等。
1.2 机械加工工艺结构
(a)45°倒角 (b)非45°倒角
图8-54 倒角和圆角
1.2 机械加工工艺结构
为了避免因应力集中而产生裂纹,在轴或孔中直径不 等的交接处,常加工成环面过渡,称为倒圆,如图8-54(c )所示。
铸件结构设计
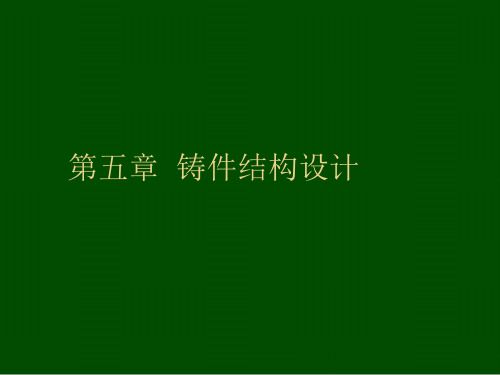
三、铸件内腔的设计 原则:减少型芯数量,利于型芯 的固定、排气和清理。 作用:防止偏芯、气孔等缺陷的 产生;简化造型工艺,降低成本。 1. 尽量节省型芯,避免不必要的 型芯
壁厚不均匀 →冷却速度不同→收缩不一致→产生热应力→厚薄连接处产生裂纹。
第二节 不同成型工艺对铸件结构的要求
原 为则防1止:热合裂理增,设可计加在铸铸件工件壁易厚艺裂处孔增设,防裂可筋。型芯定位稳固,有利于排气和清理。加工后
堵住。 > 500
15 ~ 20 10 ~ 15
12 ~ 20 ----
2)如采用丁字形、工字形、槽形或箱形结构,脆弱处安加强筋。
◆外圆角还可美化铸件外形;
原则:外形设计应便于起模,简化造型工艺。
设计铸件壁的连接或转角时,也应尽力避免金属的积聚和内应力的产生。
◆注意与拔模斜度的区别:
第二节 铸件结构与合金铸造性能的关系
拔模斜度:是在制定铸造工艺时,为了拔模方便而加上去的,一般要切削掉。
表2-13 砂型铸造铸件的最小壁厚 (mm)
原则2:铸件壁后应均匀,避免厚大截面 所谓铸件壁厚的均匀性是使铸件各壁的冷却速度相近,并非 要求所有的壁厚完全相同。 ◆缺陷分析: 壁厚差别过大 → 厚壁处易于产生缩孔、缩松缺陷。 壁厚不均匀 →冷却速度不同→收缩不一致→产生热应力→ 厚薄连接处产生裂纹。
2、铸件壁的连接 设计铸件壁的连接或转角时,也应尽力避免金属的积聚和内 应力的产生。 原则1: (1)铸件的结构圆角 ——铸件结构的基本特征 结构圆角可使铸件壁间的转角处避免热节、减轻应力集中、 改善结晶方向,从而提高转角处的机械性能。 ◆外圆角还可美化铸件外形;内圆角还可防止金属液冲坏型 腔尖角。铸造内圆角的大小应与铸件的壁厚相适应。表2-15。
简述铸造工艺对铸件结构的要求

简述铸造工艺对铸件结构的要求铸造工艺是制造铸件的常用工艺之一,具有成本低、生产效率高、生产周期短等优点。
在铸造工艺中,铸件结构的合理设计对提高工艺性能、提高产品质量和降低成本起着重要作用。
首先,铸造工艺对铸件结构要求有以下几点:1.简洁性:铸件的结构设计应尽量简洁,减少过多的孔洞、内腔和悬臂等复杂形状,以降低铸件的成本和制造难度。
2.精确性:铸件的结构设计要考虑到所需的精度和尺寸变化,在设计过程中要保证铸件的尺寸精度和形状精度。
3.可焊性:在铸造工艺中,铸件需要与其他零件进行焊接,因此铸件的结构设计要符合焊接要求,保证焊接良好。
4.强度和刚度:铸件结构设计要考虑到所需的强度和刚度,保证铸件在使用过程中的稳定性和可靠性。
5.声学性:铸件结构设计要考虑到声学要求,避免铸件在使用过程中产生过多的噪音。
其次,铸造工艺对铸件结构要求的具体内容如下:1.浇注系统:铸造工艺要求铸件具有合理的浇注系统,包括浇注口、导流冒、浇口、深水孔等。
浇注系统的设计合理与否直接影响到熔铁的进入、充实和充实性能,影响到铸件的质量。
2.冷却系统:铸造工艺要求在铸造过程中有效控制铸件的冷却速度,避免产生太多的内部应力和组织不均匀等缺陷。
冷却系统的设计包括冷却通道、冷铁、水冷壁等。
3.支撑系统:在铸造过程中,铸件需要支撑来防止变形和开裂。
支撑系统的设计要考虑到铸件的几何形状、重量和固定方式等因素。
4.清洁性:铸造工艺要求铸件具有良好的清洁性能,避免在铸造过程中产生太多的气泡、夹杂物和夹渣等缺陷。
5.铸型材料:铸造工艺要求铸件的结构设计与所选用的铸型材料相匹配,避免因材料特性不合适而导致的缺陷。
总而言之,铸造工艺对铸件结构的要求主要包括简洁性、精确性、可焊性、强度和刚度、声学性等方面。
合理的铸造工艺设计可以提高铸件的品质和可靠性,降低制造成本,为产品的应用提供可靠的基础。
简述铸造工艺对铸件结构的要求
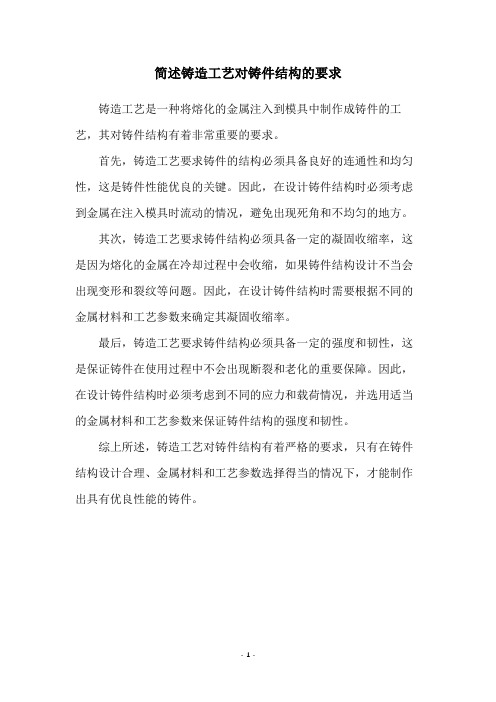
简述铸造工艺对铸件结构的要求
铸造工艺是一种将熔化的金属注入到模具中制作成铸件的工艺,其对铸件结构有着非常重要的要求。
首先,铸造工艺要求铸件的结构必须具备良好的连通性和均匀性,这是铸件性能优良的关键。
因此,在设计铸件结构时必须考虑到金属在注入模具时流动的情况,避免出现死角和不均匀的地方。
其次,铸造工艺要求铸件结构必须具备一定的凝固收缩率,这是因为熔化的金属在冷却过程中会收缩,如果铸件结构设计不当会出现变形和裂纹等问题。
因此,在设计铸件结构时需要根据不同的金属材料和工艺参数来确定其凝固收缩率。
最后,铸造工艺要求铸件结构必须具备一定的强度和韧性,这是保证铸件在使用过程中不会出现断裂和老化的重要保障。
因此,在设计铸件结构时必须考虑到不同的应力和载荷情况,并选用适当的金属材料和工艺参数来保证铸件结构的强度和韧性。
综上所述,铸造工艺对铸件结构有着严格的要求,只有在铸件结构设计合理、金属材料和工艺参数选择得当的情况下,才能制作出具有优良性能的铸件。
- 1 -。
零件上常见的工艺结构

3)在需要增强铸件强度时,可采用加肋的办法,而不是 单纯增加壁厚,如图8.7(c)所示。
4)为了便于清砂,铸件的内腔应当做成开式的,不要做 成封闭的,如图8.7(d)所示。
(c)
图8.7 铸件的壁厚
(d)
1.2机械加工零件的工艺结构
1. 倒角和圆角:为了去除毛刺、锐边,以防伤人及便 于装配,在轴端、孔口及零件的端部常加工出倒角。为 了避免应力集中而引起断裂,在孔、轴的台肩转折处, 常加工成圆角过渡的形式,称为倒圆。倒角宽度和圆角 半径可根据轴径和孔径查表确定。如图8.8所示。
图8.14 过渡线(二)
机械制图
1、铸造圆角 在铸件各表面的相交处应当做成 圆角.如图8.5所示。否则砂型在尖 角处容易落砂,同时由于金属冷却 时要收缩,在尖角处容易产生裂纹 或缩孔。
图8.5 铸造圆角
2、起模斜度
造型时,为了能将木模顺利地从砂型中提取出来,一般
常在铸件的内外壁上沿着起模方向设计出斜度,这个斜度 称为起模斜度,如图8.6所示。起模斜度一般按1:20选取, 也可以角度表示(木模造型约取1°~3°)。该斜度在零 件图上一般不画、不标。如有特殊要求,可在技术要求中 说明。
图8.8 倒角和圆角
2. 凸台和凹坑: 零件与零件相互接 触和配合的表面一般 应切削加工,为了降 低机械加工量及便于 装配,应尽可能缩小 加工面积及接触面积, 如图8.9所示。常见的 办法即在零件表面作 出凸台或凹坑。同一 平面上的凸台应尽量 同高,以便于加工。
图8.9 减少加工面积
3.退刀槽和越、
边受力,产生
偏斜或钻头折
断,因此,在与
孔轴线倾斜的
零件表面处,
第四章 铸件结构与工艺设计

铸件结构设计 砂型铸造工艺设计 铸造工艺设计实例
第一节 铸件结构设计
铸件结构不仅会直接影响到铸件的力学性 能、尺寸精度、重量要求和其它使用性能, 同时,对铸造生产过程也有很大影响。 所谓铸造工艺性良好的铸件结构,应该是 铸件的使用性能容易保证,生产过程及所 使用的工艺装备简单,生产成本低。 铸件结构要素与铸造合金的种类、铸件的 大小、铸造方法及生产条件密切相关。
(压铸)便于取出铸件的设计
熔模铸件平面上的工艺孔和工艺肋
2.铸件的组合设计 2.铸件的组合设计
因工艺的局限而无法整铸的结构,应采用组合设计。
铸钢底座的铸焊
组合床身铸件
a)砂型铸件改为b)组合压铸件 a)砂型铸件改为b)组合压铸件
第二节 砂型铸造工艺设计
1) 2) 3) 4)
砂型铸造工艺具体设计内容包括: 选择铸件的浇注位置和分型面; 确定工艺参数(机械加工余量、起模斜度、铸造圆 角、收缩量等); 确定型芯的数量、芯头形状及尺寸; 确定浇冒口、冷铁等的形状、尺寸及在铸型中的 布置等。 然后将工艺设计的内容(工艺方案)用工艺符号或文 字在零件图上表示出来,即构成了铸造工艺图。
冒口 上 中 上 下
中 下 放收缩率1% 放收缩率1% 余量:上面>侧面> 余量:上面>侧面>下面 单件小批 手工三箱造型 大批量
外 型 芯 块
两箱机器造型
第三节 铸造工艺设计实例
例1:支架零件铸造工艺设计
材料为HT200,单件、小批量生产工作时承受中等 静载荷,试进行铸造工艺设计。
1.零件结构分析: 零件结构分析: 零件结构分析 筒壁过厚,转角处未采用圆角。修改后的结 构如图b)所示。 选择铸造方法及造型方法: 2.选择铸造方法及造型方法: 3.选择浇注位置和分型面
铸件结构设计

铸件结构设计
铸件壁厚 力求均匀, 避免局部 过厚形成
避免铸造缺陷的合理结构
回到主页
热节的结
构 不合理 合理
成形工艺基础-铸件结构 设计
23
回到主页
铸件结构设计
铸件壁厚 力求均匀, 避免局部 过厚形成
避免铸造缺陷的合理结构
热节的结
构
不合理
合理
成形工艺基础-铸件结构 设计
24
铸件结构设计
避免铸造缺陷的合理结构
避免铸件产生 翘曲变形和大
的水平平面结
构
不合理
成形工艺基础-铸件结构 设计
合理
29
回到主页
铸件结构设计
避免铸造缺陷的合理结构
避免铸件产 生翘曲变形
和大的水平
平面结构 不合理 合理
成形工艺基础-铸件结构 设计
30
回到主页
铸件结构设计
避免铸造缺陷的合理结构
避免铸件产生 翘曲变形和大
的水平平面结
构 不合理
成形工艺基础-铸件结构 设计
40
回到主页
铸件结构设计
简化工艺过程的合理结构
不 合 理
铸件结构应有 利于型芯的固 定、排气和清 理
合 理
成形工艺基础-铸件结构 设计
41
铸件结构设计
结合铸造方法的合理结构 熔模铸造成形件的结构
回到主页
设计熔模铸造时应考虑 的问题:
•便于从压型中取出蜡模 和型芯 •孔、槽不宜过小或过深 •壁厚均匀、同时凝固、 避免分散的热节
合 理
成形工艺基础-铸件结构 设计
33
铸件结构设计
简化工艺过程的合理结构
不 合 理碍拔模的 局部凹陷结构
第1章 铸造(第4节)

3)铸件壁与壁的连接要逐步过渡
为减少应力集中,防止铸造过程中产生裂纹, 铸件壁从厚到薄或从薄到厚的连接应逐步过渡, 避免截面突变。
图1-51 壁厚逐步过渡
3、避免铸件收缩受阻的设计
铸件收缩受阻时,易产生内应力,从而产生裂纹,故 应尽量避免受阻收缩。如图1-52的轮辐可采用奇数轮辐数 或采用弯曲轮辐。直线形奇数轮辐,可借助轮辐本身的微 量变形自行减少内应力。
所谓铸件壁厚尽可能均匀,并非指铸件所有 的壁厚完全相同,而是使铸件各壁的冷却速 度相近,如铸件内壁由于散热条件较差,因 此要求内壁厚度应小于外壁,使铸件内、外 壁冷却速度相近,如图2-47所示。
此外,利用加强筋来减少铸件 的壁厚,见图1-48所示。
2、铸件壁间连接的设计
为减少热节、防止缩孔,减少应力,防止裂纹,壁间 应圆角连接并逐步过渡。如图1-52所示。
铸件侧壁上若有凹入部分,会妨碍起模,通常需要增 加砂芯才能形成铸件凹入部分的形状。见图2-38a所示端 盖铸件。由于上面是凸缘法兰,使铸件具有两个分型面, 采用三箱造型或者增加环形外型芯,使造型工艺复杂。改 进设计后,见图2-38b所示,取消了下部法兰凸缘,使铸
件仅有一个分型面,简化了造型工艺。
2)分型面应是平面,铸件外形应去掉不必 要的外圆角。
图1-54 防止变形的铸件结构设计
二、铸造工艺的影响
铸件结构设计,除应满足零件的 使用要求外,还应使铸造工艺过程简 化,以提高生产和质量。
1、铸件外形设计 设计时应尽量避免侧凹、窄槽和不必 要的曲面。图1-56的箱体铸件;图1-57的托 架结构。
图1-56 箱体的结构
图1-57 托架结构
1)避免铸件外表面侧凹
2)铸件的临界壁厚:厚壁铸件,易产生 缩孔、缩松、晶粒粗大等缺陷,力学性能 下降,故存在一个最大壁厚;一般取最小 壁厚的三倍。
2.4砂型铸造

参见表2-12
有色金属:表面光洁,加工余量少。
生产批量 大批量生产,机器造型
单件、小批生产,手工造型
最小铸出孔直径 铸铁件 铸钢件
Ф 15~30
<Ф25 <Ф35
3.工艺参数的选择
2)起模斜度 :便于模样从砂型中取出。
取决于起模高度、造型方法、模样材料、等。
机器造型比手工造型斜度小; 木模比金属模斜度大; 立壁越高,斜度越小; 内斜度比外斜度大。
造型材料应具备以下性能:
可塑性:砂和芯砂在外力作用下要易于成形。 足够的强度:型砂和芯砂在外力作用下要不易破坏。 耐火性:型砂和芯砂在高温下要不易软化、烧结、粘附。 透气性:型砂和芯砂紧实后要易于通气。
退让性:型砂和芯砂在冷却时其体积可以被压缩。
2)造型方法
用造型混合料及模样等工艺装备制造铸型的过程称为造型,是 砂型铸造的最基本工序。
单面模板
是模板底面一面有模样的模板。 上模板→上型
下模板→下型
合型两块模板。用两台造型机。
(a)铸件
(b)上模板(有浇注系统)
(c)下模板
特点:结构简单,应用较多。
双面模板
上半个模样和浇注系统固定在模底板一侧,下半个模样固定在该 模底板另一侧对应位臵,在同一台造型机上造出上、下型。
双面模板
造下型 1-模底板;
2.铸型分型面的选择 4.铸造工艺图的绘制
作用:制模(模样、 芯盒)、造型(芯)、 准备生产设备、铸件 检验的依据。
定义:在零件图上用各 种工艺符号及参数表示 出铸造工艺方案的图形。
1. 浇注位置的选择
① 铸件重要加工面、主要工作面、大平面、基准面应朝下 (或侧面), 以防产生气孔等,使其组织致密、质量好。
压铸件结构设计和压铸工艺

〔一从简化模具结构、延长模具使用寿命考虑
• 避免内侧凹 • 针对要求采取的措施有: • 1>外形不加大,内部形状凸出至底部〔见下图a>. •
2>局部加厚,内形加至底部,外形加至分型面处,从而消除侧 凹〔见下图b> .
3>原凸台形状不改变,在零件底部开出通孔,模型成型镶件 可以从通孔处插入形成台阶〔见下图c>.
8.压铸嵌件 镶铸件的作用有如下几个方面:
1、加强压铸件某些部位的强度、耐磨性、导电性、成绝缘 性等.如:铝中铸人钢件提高强度,铸入蓝宝石提高耐磨 性,铸入绝缘材料降低成本及提高绝缘性,铸入铁心赋予 导磁性等;
2、清除压铸件过于复杂的型腔以及内侧凹形无法压铸的型 腔;
3、消除热节,避免疏松;
4、利用低熔点金属压铸代替贵金属,如用高硅铝代替青铜;
〔四加工余量
压铸件能达到较高的精度,故多数的表面和部件都 不必进行机械加工,便可直接装配使用.同时还有 以下两个原因也不希望对压铸件进行机械加工:
1>压铸件表层坚实耐磨,加工会失去这层好的表皮;
2>压铸件有时有内部气孔存在,分散而细小的气孔 通常是不影响使用的,但机械加工后却成为外露 气孔,反而可能影响使用.
• 压铸件壁厚的极限范围: • 压铸件壁厚的极限范围很难加以限制.通常可按铸件
各个壁厚表面积的总和来选择适宜的壁厚.在零件的工艺 性能好以及压铸生产中又具备良好的工艺条件时,还可以 压铸出更薄的壁. • 这时,锌合金铸件最小壁厚度为0.5mm,铝合金铸件最小 厚度为0.7mm,镁合金铸件最小厚度为0.8mm,铜合金铸件 最小厚度为1mm.
〔±,但其偏差值为CT6级公差的1/2.
3、非配合尺寸,根据铸件结构而定.
铸件结构工艺性分析.

铜合金铸件铸造技术 课程
铸件结构工艺性分析
2.铸件 结构 分析 的要 点
1)最 小壁 厚
2)最 小孔 和槽
3)壁 厚的 均匀 性和 壁的 连接
4)平 面大 小
5)顺 序凝 固的 要求
铸件结构设计要力求避免分散的和孤立的热 节,便于实现顺序凝固,以防止产生缩孔和缩 松。
使用横浇道的浇冒口系统
铜合金铸件铸造技术 课程
最大深度 孔的直径 3~5 通孔 5~10 盲孔 5
>5~10
>10~20 >20~40 >40~60
>10~30
>30~60 >60~120 >120~200
>5~15
>15~25 >25~50 >50~80
>60~100
>100
>200~300
>300~350
>80~100
>100~120
铜合金铸件铸造技术 课程
铸件结构工艺性分析
1)最小壁厚 2) 最小孔和槽 3)壁 厚的均匀性和壁的 连接 4)平面大小
2.铸件结构分析的 要点
5)顺序凝固的要 求
注意事项
需要指出的是,铸件结构主要是零件设计人员根据零件的使用要 求及生产、加工等方面要求设计决定的,对某些工艺结构不很合理的 铸件,铸造技术人员应和设计、加工等方面技术人员协商解决。 同时,铸件结构工艺性并不是一个一成不变的概念。随着生产技术、 新材料、新工艺的创新和应用,铸件结构的工艺性问题也会发生变化, 原来难以铸造的铸件变得简易可行了。 ★★第一节课到此结束
铜合金铸件铸造技术 课程
铸件结构工艺性分析
2.铸件结 构分析的 要点 1)最小壁 厚 2)最 小孔和槽
3)壁厚的 均匀性和 壁的连接
4)平面大 小
铸造工艺结构
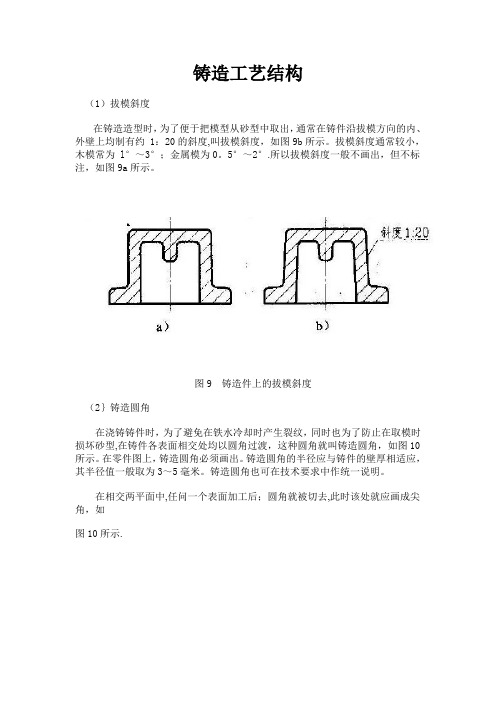
铸造工艺结构(1)拔模斜度在铸造造型时,为了便于把模型从砂型中取出,通常在铸件沿拔模方向的内、外壁上均制有约 1:20的斜度,叫拔模斜度,如图9b所示。
拔模斜度通常较小,木模常为 l°~3°;金属模为0。
5°~2°.所以拔模斜度一般不画出,但不标注,如图9a所示。
图9 铸造件上的拔模斜度(2}铸造圆角在浇铸铸件时,为了避免在铁水冷却时产生裂纹,同时也为了防止在取模时损坏砂型,在铸件各表面相交处均以圆角过渡,这种圆角就叫铸造圆角,如图10所示。
在零件图上,铸造圆角必须画出。
铸造圆角的半径应与铸件的壁厚相适应,其半径值一般取为3~5毫米。
铸造圆角也可在技术要求中作统一说明。
在相交两平面中,任问一个表面加工后;圆角就被切去,此时该处就应画成尖角,如图10所示.(3)铸件壁厚为了保证铸件的制造质量,铸件各部分的壁厚应保持均匀一致,特别要避免突然改变壁厚和局部肥大的现象。
这样可以防止铸件在浇铸时,由于各部分冷却速度不一致,而在壁较厚外形成缩孔,或在较厚壁与较薄壁的交界处产生裂纹,如图11所示。
(4)、过渡线由于铸造工艺上的要求,铸件两表面相交处存在铸造圆角.这时零件表面的交线就不明显;但为了增强图形的直观性,在相交处仍然要画出原有的交线;称为过渡线.过渡线的画法与原有相贯线或截交线的画法相同。
但由于存在有铸造圆角,因此交线的两端不再与零件的轮廓线相接触、如图12所示,为内圆柱相交时,内、外表面上过渡线的画法。
具体画图时,首先应按没有圆角的情况画出相贯钱,然后再在轮廓线处画出小圆角。
图13所示,为零件上常见的圆柱和肋板相交,且相交处有圆角过渡时的画法。
很明显,过渡线的形状与肋板和圆柱是相交还是相切,以及肋板本身的断面形状有关。
《金属工艺学》工程材料及机械制造基础(铸造)
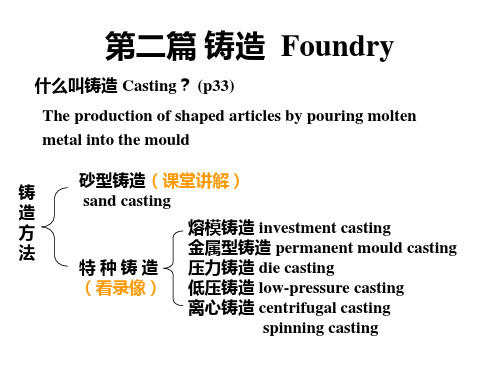
4) 铸件结构: 壁太薄、大水平面,流动困难
§2 铸件的凝固与收缩Freezing and Shrinkage
液态收缩和凝固收缩得不到补偿,将产生缩孔或缩松
1. 铸件的三种凝固方式 the wideness of paste zone
P36 图2-3 (a)逐层凝固 Freezing layer by layer (c)糊状凝固 Paste freezing (b)中间凝固 Middle freezing
2. 铸造合金的收缩 Shrinkage of the Casting Alloys
合金从浇注、凝固、直至冷却到室温,其体积和尺寸缩减 现象(p36)
液态收缩liquid Contraction 体收缩
凝固收缩freezing contraction 体收缩
固态收缩solid contraction 线收缩
Especially for the production of articles with
complicate shape and structure
铸
例如:机箱、阀体、汽缸等
造
各种材料
的
广泛
Suit for almost all kinds of alloy
特
wide-ranging 大小:g~t
白口铸铁→高温退火→石墨呈团絮状 成分:低碳、低硅;2.4~2.8%C,0.4~1.4%Si 适用范围:中压阀门
形状复杂的薄壁小件:大件容易产生麻口 受一定冲击的零件 大批量生产: 单件成本高 牌号KTH300-06
第二篇 铸造 Foundry
什么叫铸造 Casting? (p33) The production of shaped articles by pouring molten metal into the mould
铸造圆角起模斜度是铸造零件的常见工艺结构

铸造圆角起模斜度是铸造零件的常见工艺结
构
1 圆角起模斜度
圆角起模斜度是一种通过斜度和圆角铸造技术生产铸造零部件的常见工艺结构。
使用此种技术生产的零件具有质量高,精度高,表面光洁度高等优势。
圆角起模斜度在铸造工艺中利用模具的斜面起范围,将金属从金属铸件的内部引入到模具的壁缝中,进而获得高精度的圆角特征。
斜度是用于圆角起模斜度的主要参数,可以通过模具设计和压力钳法调节,以达到最佳的生产效果。
此外,圆角起模斜度具有良好的耐磨性能,在生产中可以节省大量的时间和模具材料成本。
相比传统的铸造工艺,其处理速度更快,能够更好地降低生产成本。
最后,圆角起模斜度是一种低成本,高效率的铸造工艺,可以满足各种零部件加工要求,具有良好的环保和加工性能,在行业内非常受欢迎。
2 结论
圆角起模斜度是一种铸造常见的工艺结构,它精度高,表面光洁度好,耐磨性能强,生产效率高,能够满足各种零部件加工要求,适合广泛应用于各类铸件加工。
铸造-铸件结构工艺性1

(3)可制成形状复杂的铸件最 小孔径为1.5mm,最小壁厚可达 0.7mm。
(4)工艺过程复杂。生产周期 长,铸件成本较高,铸件重量不 超过25kg。
应用:在汽车、拖拉机、汽轮机 仪表、刀具和武器等行业中都得 到广泛应用。
二、金属型铸造
1、定义:在重力下将金属液浇入金属铸 型中,以获得铸件的方法。 2、金属型的结构 如图所示(见金属型动画片) 3、金属型铸造的工艺特点
四、离心铸造
1、定义:将金属液浇入旋转的铸型中, 在离心力作用下,成形并凝固的铸造方法。 可用金属型,也可用砂型,适合铸造中空 铸件,又能铸造成形铸件。
2、离心铸造机:分为立式和卧式二大类, 如图所示。立式离心铸机的铸型绕垂直轴 旋转,生产高度小于直径的圆环类铸件 (注意有二个缺点:上薄下厚和内表面气 体及夹杂多);卧式铸机绕水平轴旋转, 主要生产长度大于直径的管、套类铸件。
(1)金属型预热 (2)刷涂料 (3)浇注 (4)开型时间 4、金属型铸造的特点及应用范 围
金属型铸造的优点:
(1)铸型冷却快,组织致密,机械性 能高。
(2)铸件的精度和表面质量较高尺寸 公差为IT11-IT14,表面粗糙度Ra值可达 12.5~6.3μm。
(3)浇冒口尺寸较小节约金属。
(4)不用砂或少用砂,节约造型材料。
4、压力铸造的特点和应用范围
(1)铸件的尺寸精度最高,表面粗糙度 最小,铸件可不经机械加工直接使用。
(2)铸件的强度和表面硬度都较高。因 为表层金属晶粒较细,组织致密。
(3)生产效率高,易于机械化和自动化。
压铸的缺点:
(1)高速液流会包住大量气体铸件表面 形成许多气孔故不能进行较多的切削加 工,以免气孔暴露出来。也不能进行热 处理,高温加热时,气孔内气体膨胀使 铸件表面鼓泡或变形。
- 1、下载文档前请自行甄别文档内容的完整性,平台不提供额外的编辑、内容补充、找答案等附加服务。
- 2、"仅部分预览"的文档,不可在线预览部分如存在完整性等问题,可反馈申请退款(可完整预览的文档不适用该条件!)。
- 3、如文档侵犯您的权益,请联系客服反馈,我们会尽快为您处理(人工客服工作时间:9:00-18:30)。
铸造工艺结构
(1)拔模斜度
在铸造造型时,为了便于把模型从砂型中取出,通常在铸件沿拔模方向的内、 外壁上均制有约1:20的斜度,叫拔模斜度,如图9b 所示。
拔模斜度通常较小, 木模常为I 。
〜3°;金属模为0.5。
〜2°。
所以拔模斜度一般不画出,但不标 注,如图9a 所示。
b)
图9铸造件上的拔模斜度
(2}铸造圆角
在浇铸铸件时,为了避免在铁水冷却时产生裂纹,同时也为了防止在取模时 损坏砂型,在铸件各表面相交处均以圆角过渡,这种圆角就叫铸造圆角,如图 10所示。
在零件图上,铸造圆角必须画出。
铸造圆角的半径应与铸件的壁厚相 适应,其半径值一般取为3〜5毫米。
铸造圆角也可在技术要求中作统一说明。
在相交两平面中,任问一个表面加工后;圆角就被切去,此时该处就应画成 尖角,如
图10所示。
a)
a) b)
图ID铸:造件上的铸造圆角
(3)铸件壁厚
为了保证铸件的制造质量,铸件各部分的壁厚应保持均匀一致,特别要避免突然改变壁厚和局部肥大的现象。
这样可以防止铸件在浇铸时,由于各部分冷却速度不一致,而在壁较厚外形成缩孔,或在较厚壁与较薄壁的交界处产生裂纹,如图11所示。
(4)、过渡线
由于铸造工艺上的要求,铸件两表面相交处存在铸造圆角。
这时零件表面的
交线就不明显;但为了增强图形的直观性,在相交处仍然要画出原有的交线;称为过渡线。
过渡线的画法与原有相贯线或截交线的画法相同。
但由于存在有铸造圆角,因此交线的两端不再与零件的轮廓线相接触、如图12所示,为内圆柱相交时,内、外表面上过渡线的画法。
具体画图时,首先应按没有圆角的情况画出相贯钱,然后再在轮廓线处画出小圆角。
9
腔12 两圆性相交时过渡线的因法
图13所示,为零件上常见的圆柱和肋板相交,且相交处有圆角过渡时的画法。
很明显,过渡线的形状与肋板和圆柱是相交还是相切,以及肋板本身的断面形状 有关。
略13防板与岡林相空时过:瀝线的网漲。