产品详细制造过程 (4)
产品生产工艺(3篇)

第1篇一、引言随着科技的不断发展,智能手表作为一种新兴的智能穿戴设备,越来越受到消费者的喜爱。
本文以智能手表为例,详细阐述其生产工艺,从原材料采购、加工制造到组装测试,全面解析智能手表的生产过程。
二、原材料采购1. 金属材料:主要包括不锈钢、钛合金、铝合金等,用于表壳、表带等部件的制作。
2. 塑料材料:如ABS、PC、TPU等,用于表壳、表带、表盘等部件的制作。
3. 液晶材料:OLED、AMOLED等,用于显示屏幕的制作。
4. 电子元件:如传感器、蓝牙芯片、加速度计等,用于智能手表的核心功能实现。
5. 线材:如铜线、锡线等,用于连接各个电子元件。
6. 粘合剂:如胶水、硅胶等,用于固定和密封各个部件。
三、加工制造1. 表壳加工:采用CNC加工、激光切割、冲压等工艺,将金属材料加工成所需形状。
2. 表带加工:根据需求选择合适材料,通过注塑、热压、编织等工艺制作表带。
3. 表盘加工:采用CNC加工、激光切割等工艺,将塑料材料加工成表盘。
4. 显示屏幕制作:将液晶材料与玻璃基板贴合,并通过封装工艺形成OLED、AMOLED等显示屏幕。
5. 电子元件加工:对传感器、蓝牙芯片、加速度计等电子元件进行封装,形成完整的电子模块。
6. 线材加工:对铜线、锡线等线材进行加工,形成所需的连接线。
四、组装测试1. 组装:将加工好的表壳、表带、表盘、显示屏幕、电子模块、线材等部件进行组装,形成完整的智能手表。
2. 功能测试:对智能手表的各项功能进行测试,如时间显示、运动监测、心率监测等。
3. 电池测试:对智能手表的电池进行充放电测试,确保电池性能稳定。
4. 环境测试:对智能手表进行防水、防尘、抗摔等环境测试,确保其在各种环境下都能正常使用。
5. 性能测试:对智能手表的运行速度、功耗、续航能力等进行测试,确保其性能符合要求。
五、包装与运输1. 包装:将组装好的智能手表进行精美包装,包括产品说明书、保修卡等。
2. 运输:将包装好的产品运输至各个销售渠道,如线上电商平台、线下专卖店等。
电子装配策划书范本3篇

电子装配策划书范本3篇篇一电子装配策划书范本一、引言随着电子技术的不断发展,电子装配行业也在不断壮大。
为了满足市场需求,提高生产效率和质量,我们制定了本电子装配策划书。
本策划书旨在提供一个全面的电子装配方案,包括生产流程、设备选型、人员配置、质量控制等方面的内容。
二、生产流程1. SMT 贴片:将电子元件贴装在 PCB 板上。
2. 插件:将插件元件插入 PCB 板上。
3. 焊接:将电子元件焊接在 PCB 板上。
4. 测试:对 PCB 板进行测试,确保其功能正常。
5. 组装:将 PCB 板组装成电子产品。
6. 包装:对电子产品进行包装,准备出货。
三、设备选型1. SMT 贴片机:选择高精度、高效率的 SMT 贴片机,以满足生产需求。
2. 插件机:选择自动化程度高、插件速度快的插件机,以提高生产效率。
4. 测试设备:选择功能齐全、测试精度高的测试设备,以确保产品质量。
5. 组装设备:选择自动化程度高、组装效率高的组装设备,以提高生产效率。
四、人员配置1. 生产管理人员:负责生产计划的制定、生产进度的跟踪和生产质量的控制。
2. 技术人员:负责设备的维护和调试、生产工艺的改进和新产品的开发。
3. 操作人员:负责设备的操作和产品的装配。
4. 质量检验人员:负责产品的质量检验和质量问题的处理。
五、质量控制1. 原材料检验:对原材料进行检验,确保其质量符合要求。
2. 生产过程检验:对生产过程进行检验,确保生产工艺符合要求,产品质量符合标准。
3. 成品检验:对成品进行检验,确保产品质量符合要求。
4. 质量问题处理:对质量问题进行及时处理,采取有效的纠正措施,防止问题再次发生。
六、生产计划1. 生产计划的制定:根据市场需求和订单情况,制定生产计划。
2. 生产进度的跟踪:对生产进度进行跟踪,及时发现问题并解决。
3. 生产计划的调整:根据实际情况,对生产计划进行调整,以确保按时完成生产任务。
七、成本控制1. 原材料成本控制:通过优化采购渠道、降低采购成本等方式,控制原材料成本。
产品生产工艺流程

产品生产工艺流程1. 原料准备阶段在产品生产的第一阶段,必须准备好原料。
原料的质量和数量对产品的最终质量至关重要。
这个阶段通常包括以下步骤:•资源采集:采集所需的原材料,可能包括天然资源、化学原料等。
•原料检验:检验原料的质量和适用性,确保符合生产要求。
•原料储存:将检验合格的原料储存在适合的环境下,以确保在生产过程中不受污染或损坏。
2. 生产工艺设计阶段在这个阶段,制定产品的生产工艺流程。
这包括确定生产工艺的主要步骤、工艺参数和生产设备的选择。
以下是该阶段的主要任务:•工艺流程设计:确定生产步骤和顺序,以确保产品能够按要求制造。
•工艺参数设定:确定各项工艺参数(如温度、压力、时间等)的设定值,以确保产品符合质量标准。
•设备选择:选择适合生产工艺的设备和机器,确保生产过程顺利进行。
3. 生产加工阶段在这个阶段,根据生产工艺流程进行产品的加工生产。
这个阶段通常包括以下步骤:•原料处理:根据工艺流程对原材料进行加工,如混合、搅拌、研磨等。
•生产操作:按照工艺流程,使用相应的设备对原料进行加工制造产品。
•质量控制:在生产过程中进行质量检验,确保产品符合质量要求。
4. 产品组装和包装阶段在产品加工完成后,需要进行产品的组装和包装。
这个阶段通常包括以下步骤:•产品组装:将生产好的各个零部件组装成最终产品。
•包装设计:设计合适的包装形式和材料,以确保产品在运输和使用过程中不受损坏。
•包装作业:将组装好的产品放入包装中,并封装包装材料。
5. 成品质量检验阶段在产品生产完成后,需要进行成品的质量检验。
这个阶段的主要任务是确保产品符合质量标准,可以正常投放市场。
主要的质量检测包括:•外观检验:检查产品外观,确保无瑕疵。
•尺寸测量:测量产品的尺寸,确保符合要求。
•功能测试:对产品进行功能测试,确保正常使用。
6. 包装和出货阶段在成品质量检验通过后,产品将进行最后的包装和出货阶段。
这个阶段包括以下步骤:•包装完成:将通过质检的产品进行最终包装。
详细说明过程设备制造的工艺流程
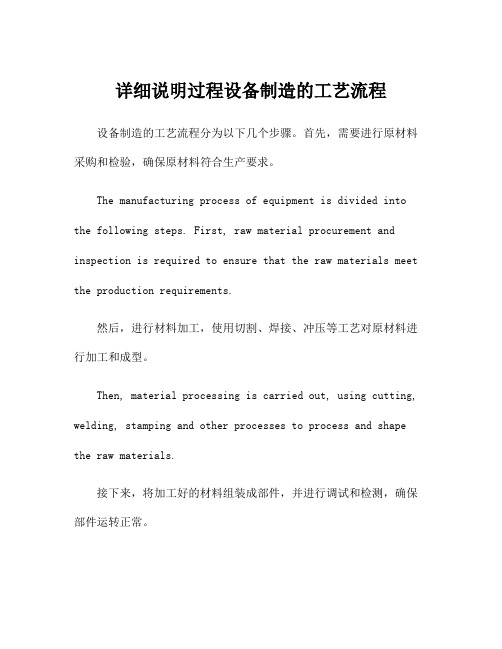
详细说明过程设备制造的工艺流程设备制造的工艺流程分为以下几个步骤。
首先,需要进行原材料采购和检验,确保原材料符合生产要求。
The manufacturing process of equipment is divided into the following steps. First, raw material procurement and inspection is required to ensure that the raw materials meet the production requirements.然后,进行材料加工,使用切割、焊接、冲压等工艺对原材料进行加工和成型。
Then, material processing is carried out, using cutting, welding, stamping and other processes to process and shape the raw materials.接下来,将加工好的材料组装成部件,并进行调试和检测,确保部件运转正常。
Next, the processed materials are assembled into components, and then tested to ensure that the components operate normally.随后,进行总装,将各个部件组装成整机,并进行全面检测和调试。
Subsequently, final assembly is carried out, assembling the various components into a complete machine, followed by comprehensive testing and debugging.最后,需要进行包装和运输,确保设备在运输过程中不受损坏。
Finally, packaging and transportation are carried out to ensure that the equipment is not damaged during transport.在整个制造工艺中,严格执行相关的质量管理标准和流程,保证设备的质量和性能达到要求。
电子信息产品制造流程作业指导书

电子信息产品制造流程作业指导书第1章原材料准备 (4)1.1 原材料的选择与采购 (4)1.1.1 选择原则 (4)1.1.2 采购流程 (4)1.2 原材料的检验与储存 (5)1.2.1 检验标准 (5)1.2.2 检验流程 (5)1.2.3 储存要求 (5)1.3 原材料的管理与配送 (5)1.3.1 管理制度 (5)1.3.2 配送流程 (5)1.3.3 库存控制 (6)第2章设计与研发 (6)2.1 产品设计规范 (6)2.1.1 设计原则 (6)2.1.2 设计要求 (6)2.2 硬件设计流程 (6)2.2.1 需求分析 (6)2.2.2 电路设计 (6)2.2.3 元器件选型 (6)2.2.4 硬件调试 (6)2.3 软件开发与调试 (6)2.3.1 软件架构设计 (6)2.3.2 编码与实现 (7)2.3.3 软件调试 (7)2.3.4 驱动程序开发 (7)2.4 产品样品试制 (7)2.4.1 样品试制计划 (7)2.4.2 样品制作 (7)2.4.3 样品测试 (7)2.4.4 问题反馈与改进 (7)第3章工艺流程规划 (7)3.1 工艺流程设计原则 (7)3.2 关键工序确定 (8)3.3 工艺参数优化 (8)3.4 生产设备选型 (8)第4章 SMT贴片工艺 (8)4.1 SMT生产线布局 (8)4.1.1 设备选型与布局 (9)4.1.2 生产线流程设计 (9)4.1.3 生产环境要求 (9)4.2.1 元器件选用 (9)4.2.2 元器件包装及存储 (9)4.2.3 元器件贴装 (9)4.3 SMT贴片程序编写 (9)4.3.1 程序设计 (9)4.3.2 程序调试 (10)4.4 SMT焊接质量检测 (10)4.4.1 检测方法 (10)4.4.2 检测标准 (10)4.4.3 检测结果处理 (10)第5章焊接工艺 (10)5.1 焊接方法选择 (10)5.1.1 手工焊接:适用于小型电子元器件的焊接,具有操作灵活、成本较低的优点。
家具厂生产工艺流程

家具厂生产工艺流程
《家具厂生产工艺流程》
家具厂生产工艺流程是指家具制造过程中的一系列步骤和工艺流程。
在家具生产中,工艺流程的设计和执行对于产品质量和生产效率都具有重要意义,以下是家具厂生产工艺流程的一般步骤:
1. 设计和规划:家具生产的第一步是设计和规划。
这包括产品设计、材料选择、尺寸确定等工作。
设计阶段的目标是确定产品的外观和功能,确保产品能够满足市场需求。
2. 材料准备:一旦设计完成,接下来就要准备生产所需的原材料。
这包括木材、金属、塑料等各种原材料的采购和加工。
家具制造通常需要大量的原材料,因此材料准备是整个生产过程中非常关键的一环。
3. 制造和加工:一旦原材料准备完成,就可以进行家具的制造和加工。
这包括木工、金属工、油漆工等多个环节。
在这一阶段,通过切割、打磨、组装等工艺,原材料逐渐被转化为成品家具。
4. 装配和包装:当家具制造完成后,就需要进行装配和包装。
这一阶段包括家具的组装、安装附件和配件、以及包装。
良好的装配和包装工艺可以保证产品在运输和销售过程中不受损坏。
5. 质检和品控:最后,家具生产过程中的最后一步是质检和品
控。
这包括对成品家具的质量进行检查和测试,确保产品符合质量标准和规定。
通过上述步骤,家具厂可以完成从原材料到成品的整个生产过程。
通过科学的工艺流程设计和执行,可以提高生产效率,保证产品质量,满足市场需求。
机械制造加工工艺(3篇)

第1篇摘要:机械制造加工工艺是机械制造行业中的重要组成部分,它直接关系到产品的质量和性能。
本文从机械制造加工工艺的基本概念、加工方法、加工设备、加工精度等方面进行了详细阐述,旨在为机械制造行业提供有益的参考。
一、引言机械制造加工工艺是指将原材料通过各种加工方法,加工成具有预定形状、尺寸和性能的零件或产品的过程。
在机械制造行业中,加工工艺的合理选择和优化对于提高产品质量、降低生产成本、提高生产效率具有重要意义。
本文将详细探讨机械制造加工工艺的相关内容。
二、机械制造加工工艺的基本概念1. 加工方法:机械制造加工工艺主要包括切削加工、磨削加工、锻造加工、铸造加工、焊接加工、热处理加工等方法。
2. 加工设备:加工设备是完成加工工艺的必要条件,如车床、铣床、磨床、数控机床等。
3. 加工精度:加工精度是指零件尺寸、形状、位置等几何参数的精确程度,是衡量加工工艺质量的重要指标。
4. 加工表面质量:加工表面质量是指零件加工表面粗糙度、波纹度、裂纹等缺陷的程度,影响零件的使用性能。
三、机械制造加工方法1. 切削加工:切削加工是机械制造中最常用的加工方法,主要包括车削、铣削、刨削、磨削等。
(1)车削:车削是利用车刀在工件上切除多余材料,使工件达到预定尺寸和形状的过程。
车削适用于内外圆柱面、圆锥面、螺纹等加工。
(2)铣削:铣削是利用铣刀在工件上切除多余材料,使工件达到预定尺寸和形状的过程。
铣削适用于平面、斜面、曲面、键槽等加工。
(3)刨削:刨削是利用刨刀在工件上切除多余材料,使工件达到预定尺寸和形状的过程。
刨削适用于平面、斜面、曲面等加工。
(4)磨削:磨削是利用磨具对工件表面进行研磨,使工件达到预定尺寸和形状的过程。
磨削适用于内外圆柱面、圆锥面、平面、曲面等加工。
2. 磨削加工:磨削加工是利用磨具对工件表面进行研磨,提高工件表面质量和精度的一种加工方法。
3. 锻造加工:锻造加工是将金属加热至一定温度,使其具有一定的塑性,然后在模具中施加压力,使金属产生塑性变形,从而获得预定形状和尺寸的零件。
贴面厂的生产流程
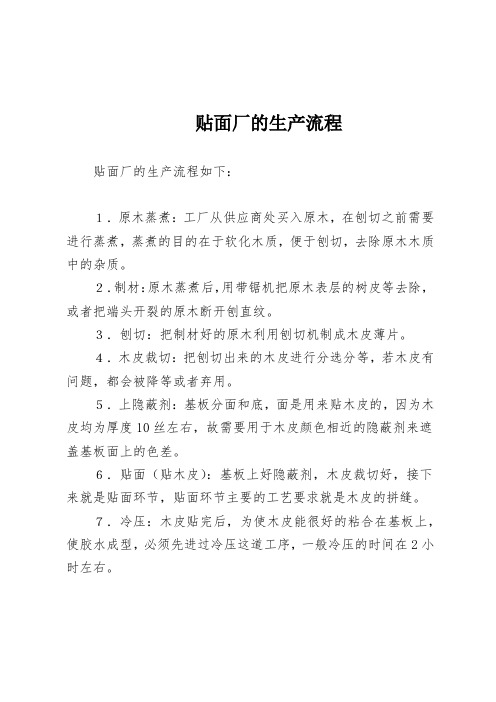
贴面厂的生产流程
贴面厂的生产流程如下:
1.原木蒸煮:工厂从供应商处买入原木,在刨切之前需要进行蒸煮,蒸煮的目的在于软化木质,便于刨切,去除原木木质中的杂质。
2.制材:原木蒸煮后,用带锯机把原木表层的树皮等去除,或者把端头开裂的原木断开刨直纹。
3.刨切:把制材好的原木利用刨切机制成木皮薄片。
4.木皮裁切:把刨切出来的木皮进行分选分等,若木皮有问题,都会被降等或者弃用。
5.上隐蔽剂:基板分面和底,面是用来贴木皮的,因为木皮均为厚度10丝左右,故需要用于木皮颜色相近的隐蔽剂来遮盖基板面上的色差。
6.贴面(贴木皮):基板上好隐蔽剂,木皮裁切好,接下来就是贴面环节,贴面环节主要的工艺要求就是木皮的拼缝。
7.冷压:木皮贴完后,为使木皮能很好的粘合在基板上,使胶水成型,必须先进过冷压这道工序,一般冷压的时间在2小时左右。
产品制造工艺方法及质量保证措施

产品制造工艺方法及质量保证措施(一)金属柜体及内部机架的加工与控制1. 数冲工序我公司所有钣金内产品全部采用高精度数控冲床(日本天田AMADA )加工,先编制电脑程序,通过数据传输给机床,然后操作人员会按照程序指令进行加工,能够较高精度的保证客户要求的开孔尺寸和安装尺寸,孔径、孔距公差一般在±0.1以内,零件外形尺寸公差一般在±0.15以内。
检验:检验人员按图纸要求、公差进行严格检验,批量产品先进行首件检验,确保首件产品完全合格后再批量生产,批量生产期间按20%进行局部抽检,10%进行全面抽检,确保产品合格。
2. 折弯工序所有产品全部采用高精度数控折弯机(日本天田AMADA ),操作工根据图纸要求合理分配尺寸公差值,角度和折弯修正参数后将确定的数值按机床操作先后要求输入机床程序。
加工时,先用与零件相同的材质和料厚的条料或废料在机床试折,然后测量试折件的基本尺寸,两端平行度、角度及折弯弯曲半径。
基本尺寸应符合图纸尺寸公差要求和机床板金件技术条件公差值的要求两端平行度数值参数注:测量点为不少于3个点。
试折件角度误差参数注:测量点不少于3个点L≥1500测量点不少于5个点(平均间隔每300mm 作为一个点)。
试折件常规折弯弯曲处半径R 参数试折件注:弯曲处半径R面上不允许有断裂、开裂等现象折弯尺寸的准确到位,能够最直接的给后续焊接加工作出保证,所以折弯尺寸、角度、平行度要尽可能做到准确无误。
检验:检验员按图纸和操作规程严格检验零件的外形尺寸、角度、平行度、半径大小、公差等,批量产品先进行首件检验,确保首件产品完全合格后再批量生产,批量生产期间按20%进行局部抽检,10%进行全面抽检,确保产品合格。
3. 烧焊成型目前我司主要采用的烧焊主要有两种:氩弧焊(自动焊和手工焊)和二氧化碳气体保护焊,氩弧焊变形较小,二氧化碳气体保护焊变形比较大。
钣金机箱的板材厚度较薄(≤2.0mm),通常采用氩弧焊焊接,批量较小时采用手动氩弧焊焊接,批量较大时,经人工拼接后用氩弧焊自动焊焊接,又称焊接机器人。
产品管理:四步法新产品开发流程
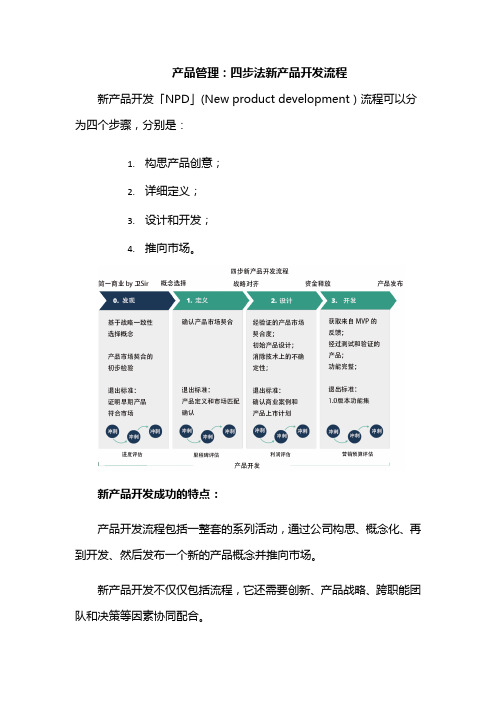
产品管理:四步法新产品开发流程新产品开发「NPD」(New product development)流程可以分为四个步骤,分别是:1.构思产品创意;2.详细定义;3.设计和开发;4.推向市场。
新产品开发成功的特点:产品开发流程包括一整套的系列活动,通过公司构思、概念化、再到开发、然后发布一个新的产品概念并推向市场。
新产品开发不仅仅包括流程,它还需要创新、产品战略、跨职能团队和决策等因素协同配合。
一个创新的产品概念或想法的产生可能来自客户、实验室或工作空间。
新产品开发是一种能力,使公司能够实现这些新生的产品概念,并将它们可靠地、可预测地呈现给客户,同时确保满足客户的需求。
除了产品开发流程之外,NPD 还包括产品开发战略和产品组合管理等元素,通常由跨职能团队执行,这些团队聚集在一起开发新产品。
有效的新产品流程需要确保:•有效的管理来选择新的产品概念;•足够的资金让这些想法得以发展;•对它们进行审查和优先级排序。
一、NPD 的四个步骤1. 发现——创意识别和创意筛选NPD 流程中发现步骤可确保不仅产生新产品创意,而且还需要进行彻底探索和筛选。
使用有效的产品发现技术有助于确保产品市场适合新产品创意,这是创意产生的第一步。
尽管通过发现流程进入市场的时间似乎更长,但如果你的步骤正确,即使它增加了开发时间,你也会看到很大的改进。
这个阶段的想法来源不仅仅包括头脑风暴,也包括基层研发、前端市场销售等环节。
2. 定义——业务分析和概念开发定义阶段需要确保在模糊前端充分探索提出的新产品创意:•概念在新产品开发活动的早期进行测试,想法在早期筛选;•团队敏捷,可以自由创新和迭代以将创意生成细化;•测试技术,识别主要风险;•在新产品开发过程的早期阶段为项目配备合适的资源;•项目不受任何阻碍快速迭代开发的影响;•具有重要的商业潜力。
在客户需求流程的这一步结束时,团队应该有一个明确的具有创业能力的领导者。
团队应向管理层证明,通过对潜在客户的早期市场测试,证明实现收入的时间是可预见的,潜在的市场份额很大,并且收入潜力足以对公司产生影响。
产品生产过程范文
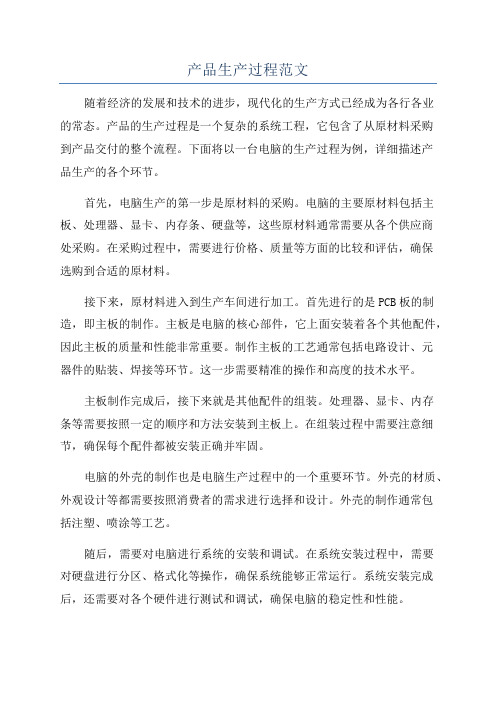
产品生产过程范文随着经济的发展和技术的进步,现代化的生产方式已经成为各行各业的常态。
产品的生产过程是一个复杂的系统工程,它包含了从原材料采购到产品交付的整个流程。
下面将以一台电脑的生产过程为例,详细描述产品生产的各个环节。
首先,电脑生产的第一步是原材料的采购。
电脑的主要原材料包括主板、处理器、显卡、内存条、硬盘等,这些原材料通常需要从各个供应商处采购。
在采购过程中,需要进行价格、质量等方面的比较和评估,确保选购到合适的原材料。
接下来,原材料进入到生产车间进行加工。
首先进行的是PCB板的制造,即主板的制作。
主板是电脑的核心部件,它上面安装着各个其他配件,因此主板的质量和性能非常重要。
制作主板的工艺通常包括电路设计、元器件的贴装、焊接等环节。
这一步需要精准的操作和高度的技术水平。
主板制作完成后,接下来就是其他配件的组装。
处理器、显卡、内存条等需要按照一定的顺序和方法安装到主板上。
在组装过程中需要注意细节,确保每个配件都被安装正确并牢固。
电脑的外壳的制作也是电脑生产过程中的一个重要环节。
外壳的材质、外观设计等都需要按照消费者的需求进行选择和设计。
外壳的制作通常包括注塑、喷涂等工艺。
随后,需要对电脑进行系统的安装和调试。
在系统安装过程中,需要对硬盘进行分区、格式化等操作,确保系统能够正常运行。
系统安装完成后,还需要对各个硬件进行测试和调试,确保电脑的稳定性和性能。
最后,电脑的包装和交付是整个生产过程的最后一步。
电脑通常需要进行外包装的包装,以防止在运输过程中受到损坏。
包装完成后,电脑将被送到物流中心进行储存和分发,最终交付给消费者。
总结起来,产品的生产过程是一个复杂而又严谨的过程,它需要各个环节的精细管理和协调配合。
在生产过程中,需要从原材料采购,到加工制造,再到产品的调试和交付,每个环节都需要精密的操作和高度的技术水平。
只有如此,才能生产出符合消费者需求的优质产品。
制造业生产流程作业指导书

制造业生产流程作业指导书第1章生产流程概述 (4)1.1 生产流程的基本概念 (5)1.2 生产流程的关键环节 (5)1.3 生产流程的组织与管理 (5)第2章生产计划与调度 (6)2.1 生产计划的编制 (6)2.1.1 计划目标与原则 (6)2.1.2 计划编制方法 (6)2.1.3 计划编制步骤 (6)2.2 调度策略与方法 (6)2.2.1 调度目标 (6)2.2.2 调度策略 (7)2.2.3 调度方法 (7)2.3 生产计划的执行与调整 (7)2.3.1 生产计划的执行 (7)2.3.2 生产计划的调整 (7)第3章物料采购与管理 (7)3.1 物料需求分析 (7)3.1.1 物料需求计划的制定 (7)3.1.2 物料需求预测 (8)3.1.3 物料需求分析与优化 (8)3.2 供应商选择与评估 (8)3.2.1 供应商筛选标准 (8)3.2.2 供应商评估与认证 (8)3.2.3 供应商绩效评价 (8)3.3 物料采购流程 (8)3.3.1 采购申请与审批 (8)3.3.2 采购订单管理 (8)3.3.3 物料验收与质量控制 (8)3.3.4 采购付款与结算 (8)3.4 物料库存管理 (8)3.4.1 库存分类与编码 (9)3.4.2 库存控制策略 (9)3.4.3 库存盘点与调整 (9)3.4.4 库存信息管理 (9)第4章生产设备与工艺 (9)4.1 生产设备选型与布局 (9)4.1.1 设备选型原则 (9)4.1.2 设备布局 (9)4.2 设备维护与保养 (9)4.2.1 设备维护 (9)4.3 工艺流程设计 (9)4.3.1 工艺流程设计原则 (10)4.3.2 工艺流程制定 (10)4.4 工艺参数优化 (10)4.4.1 工艺参数调整原则 (10)4.4.2 工艺参数优化方法 (10)4.4.3 工艺参数监控 (10)第5章质量控制与管理 (10)5.1 质量管理体系 (10)5.1.1 质量管理体系概述 (10)5.1.2 质量管理体系文件的编制与实施 (10)5.1.3 内部审核与认证 (10)5.2 质量控制工具与方法 (11)5.2.1 质量控制基本工具 (11)5.2.2 统计过程控制 (11)5.2.3 质量改进方法 (11)5.3 质量检验与不合格品处理 (11)5.3.1 质量检验概述 (11)5.3.2 检验计划的制定与实施 (11)5.3.3 不合格品的控制与处理 (11)5.4 持续改进与质量提升 (11)5.4.1 持续改进的基本原则与方法 (11)5.4.2 质量改进项目的策划与实施 (11)5.4.3 质量文化建设 (11)第6章人力资源管理 (12)6.1 员工招聘与培训 (12)6.1.1 招聘流程 (12)6.1.2 招聘标准 (12)6.1.3 培训与发展 (12)6.2 岗位职责与绩效评估 (12)6.2.1 岗位职责设定 (12)6.2.2 绩效考核体系 (12)6.2.3 绩效反馈与改进 (12)6.3 生产团队建设与管理 (12)6.3.1 团队组织结构 (12)6.3.2 团队沟通与协作 (12)6.3.3 团队激励与关怀 (13)6.4 劳动保护与安全生产 (13)6.4.1 安全生产制度 (13)6.4.2 劳动保护措施 (13)6.4.3 安全培训与演练 (13)6.4.4 安全检查与整改 (13)第7章环境与能源管理 (13)7.1.1 建立环境方针 (13)7.1.2 环境目标与计划 (13)7.1.3 环境因素识别与评价 (13)7.1.4 环境管理体系文件 (13)7.2 能源消耗分析与优化 (13)7.2.1 能源消耗数据收集 (13)7.2.2 能源消耗分析 (14)7.2.3 能源优化措施 (14)7.2.4 能源管理培训与宣传 (14)7.3 废弃物处理与环保法规遵守 (14)7.3.1 废弃物分类与储存 (14)7.3.2 废弃物处理 (14)7.3.3 环保法规遵守 (14)7.3.4 环保设施运行与维护 (14)7.4 绿色生产与可持续发展 (14)7.4.1 绿色生产理念 (14)7.4.2 生态设计 (14)7.4.3 持续改进 (14)7.4.4 环保绩效评价 (14)第8章生产成本控制 (15)8.1 成本构成与成本核算 (15)8.1.1 成本构成 (15)8.1.2 成本核算 (15)8.2 成本控制策略与方法 (15)8.2.1 成本控制策略 (15)8.2.2 成本控制方法 (15)8.3 价值工程与成本优化 (15)8.3.1 价值工程 (15)8.3.2 成本优化 (16)8.4 生产效益分析与提升 (16)8.4.1 生产效益分析 (16)8.4.2 生产效益提升 (16)第9章生产信息化管理 (16)9.1 生产数据采集与处理 (16)9.1.1 数据采集 (16)9.1.2 数据处理 (16)9.2 生产过程监控与调度 (16)9.2.1 生产过程监控 (16)9.2.2 生产调度 (16)9.3 企业资源计划(ERP)系统 (17)9.3.1 系统概述 (17)9.3.2 系统功能 (17)9.3.3 系统实施与优化 (17)9.4 生产线自动化与智能化 (17)9.4.1 自动化生产线 (17)9.4.2 智能化生产线 (17)9.4.3 生产线优化与升级 (17)第10章生产流程持续改进 (17)10.1 改进方法的选取与应用 (17)10.1.1 确定改进目标:根据生产流程现状,明确改进方向和目标,保证改进措施具有针对性和实效性。
工厂车间的生产过程详解
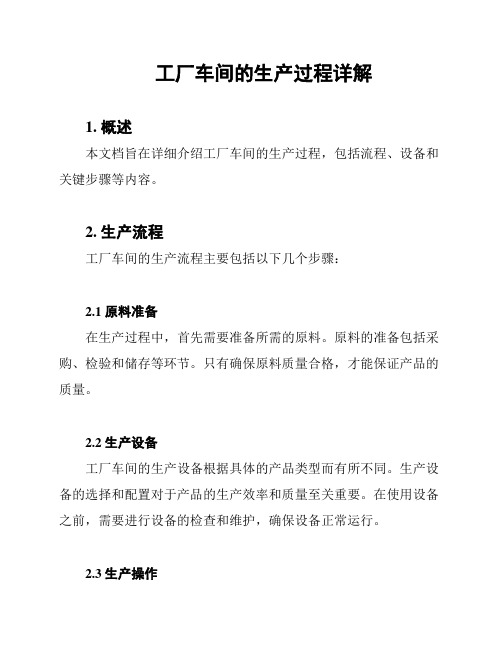
工厂车间的生产过程详解1. 概述本文档旨在详细介绍工厂车间的生产过程,包括流程、设备和关键步骤等内容。
2. 生产流程工厂车间的生产流程主要包括以下几个步骤:2.1 原料准备在生产过程中,首先需要准备所需的原料。
原料的准备包括采购、检验和储存等环节。
只有确保原料质量合格,才能保证产品的质量。
2.2 生产设备工厂车间的生产设备根据具体的产品类型而有所不同。
生产设备的选择和配置对于产品的生产效率和质量至关重要。
在使用设备之前,需要进行设备的检查和维护,确保设备正常运行。
2.3 生产操作生产操作是指根据产品的生产工艺要求,对原料进行加工、组装或装配等操作。
生产操作需要严格按照操作规程进行,确保生产过程的稳定性和高效性。
2.4 质量控制质量控制是工厂车间生产过程中的重要环节。
通过对生产过程中各个环节的监控和检验,确保产品质量符合标准要求。
质量控制包括原料检验、工艺控制和成品检验等环节。
2.5 成品包装生产过程完成后,需要对成品进行包装。
包装的目的是保护产品,方便储存和运输。
包装需要按照相关标准进行,确保产品的完整性和安全性。
3. 关键步骤工厂车间的生产过程中存在一些关键步骤,对产品质量和生产效率影响较大。
这些关键步骤包括原料检验、设备检查和维护、生产操作的严格执行、质量控制和成品包装等。
4. 注意事项在工厂车间的生产过程中,需要注意以下几个方面:- 严格按照操作规程进行生产操作,确保操作的准确性和稳定性。
- 加强设备的检查和维护,确保设备的正常运行。
- 加强质量控制,确保产品质量符合标准要求。
- 注意原料的储存和保管,避免污染和损坏。
5. 总结工厂车间的生产过程是一个复杂而重要的环节。
只有通过严格的流程控制、设备维护和质量控制,才能保证产品质量和生产效率的提高。
以上为工厂车间的生产过程的详细介绍,希望对您有所帮助。
产品加工工艺流程

产品加工工艺流程
《产品加工工艺流程》
产品加工工艺流程是指将原材料经过一系列加工工艺流程,最终制成具有一定形状、尺寸和功能的成品的过程。
在现代工业生产中,产品加工工艺流程扮演着至关重要的角色,它直接影响着产品的质量、成本和生产效率。
下面将以汽车发动机零部件的加工工艺流程为例,来说明产品加工的全过程。
首先,原材料准备。
将原材料按照设计要求进行采购,然后进行原材料的检验和筛选,确保其符合加工要求。
其次,加工工艺规划。
根据产品设计图纸和要求,制定相应的加工工艺流程,包括加工工序顺序、加工精度要求、工装夹具设计等。
然后,进行粗加工。
采用铣削、车削、钻孔等机械加工工艺,将原材料进行初步的成形。
接下来是精加工。
通过磨削、铣削、切割等高精度加工工艺,将零部件进行精细加工,保证其尺寸精度和表面光洁度。
之后,是热处理。
采用火焰淬火、渗碳、回火等热处理工艺,提高零部件的硬度、耐磨性和强度。
最后,进行表面处理。
包括喷涂、镀层、抛光等工艺,提高零部件的外观质量和防腐蚀能力。
通过以上工艺流程,原材料逐步转化为成品零部件,最终用于汽车发动机的装配。
产品加工工艺流程不仅需要精湛的技术和经验,还需要不断创新,以提高生产效率和产品质量,从而满足市场需求。
曝气器生产制作流程

曝气器生产制作流程 1. 原材料准备。
聚丙烯(PP)。
聚乙烯(PE)。
橡胶。
2. 注塑成型。
使用聚丙烯或聚乙烯制成曝气器主体。
注塑成型机将熔化的塑料注入模具中成型。
模具中形成的曝气器外形。
3. 橡胶组件制造。
使用橡胶制造曝气器膜片、密封件和垫圈。
橡胶被压入模具中成型。
成型的橡胶组件与曝气器主体组装。
4. 组装。
将曝气器主体、橡胶组件、螺钉和垫圈组装在一起。
组装过程严格按照设计图纸进行。
组装后的曝气器进行泄漏测试和性能测试。
5. 包装和运输。
包装曝气器以保护它们在运输过程中免受损坏。
使用适当的包装材料,例如气泡膜、泡沫和纸箱。
运输曝气器时采取预防措施以避免损坏。
### 曝气器质量控制。
1. 材料检验。
对聚丙烯、聚乙烯和橡胶进行严格的质量检验。
确保材料符合规定的规格和标准。
2. 生产过程控制。
监控注塑成型和橡胶组件制造过程。
使用测量仪器和控制系统确保尺寸精度和产品质量。
3. 最终产品测试。
对组装后的曝气器进行泄漏测试和性能测试。
测试结果与设计规格进行比较。
4. 定期审核。
定期审核生产流程和质量控制措施。
识别改进领域和解决潜在问题。
5. 客户反馈。
收集客户反馈信息以评估曝气器的质量和性能。
使用反馈信息改进产品和服务。
## 中文回答:### 曝气器生产制作流程。
1. 原材料准备。
曝气器的主要原材料为聚丙烯(PP)、聚乙烯(PE)和橡胶。
2. 注塑成型。
通过注塑成型机将熔化的聚丙烯或聚乙烯注入模具中成型,形成曝气器主体。
3. 橡胶组件制造。
使用橡胶压入模具中成型出曝气器膜片、密封件和垫圈等橡胶组件。
4. 组装。
将曝气器主体、橡胶组件、螺钉和垫圈按照设计图纸组装在一起,并进行泄漏测试和性能测试。
5. 包装和运输。
将曝气器用气泡膜、泡沫和纸箱等包装材料包装好,并采取预防措施运输以避免损坏。
### 曝气器质量控制。
1. 材料检验。
对原材料进行严格的质量检验,确保符合规定规格和标准。
2. 生产过程控制。
监控注塑成型和橡胶组件制造过程,使用测量仪器和控制系统确保尺寸精度和产品质量。
型材成型流程范文

型材成型流程范文第一步:材料准备在进行型材成型之前,首先需要准备所需的材料。
根据具体的需要,可以选择不同种类的金属或其他材料,并根据型材的使用环境和要求选择材料的物理和化学性能。
第二步:原材料切割通常情况下,原材料会准备成一定长度的棒状或板状。
在型材成型之前,需要根据所需尺寸将原材料进行切割。
切割可以使用机械切割工具,如剪切机,也可以使用激光切割机等高精度切割设备。
第三步:热处理有些金属材料在成型之前需要进行热处理,以改变材料的晶体结构和性能。
比如,热处理可以加强材料的硬度、强度和韧性,或者消除材料内部的应力和缺陷。
常见的热处理方法包括退火、淬火和回火。
第四步:型材成型型材成型是整个流程的核心步骤。
型材成型可以通过多种方式进行,常见的方式包括挤压、拉伸、滚轧、锻造和压铸等。
-挤压:将金属材料放入挤压机中,在一定的压力和温度条件下,通过挤出口挤出成型。
挤压可用于制造各种横截面形状的型材。
-拉伸:将金属材料加热至一定温度后,通过外力使其在塑性状态下,逐渐拉长成型。
拉伸可用于制造细长型材,如线材和钢丝。
-滚轧:将金属材料放入滚轧机中,通过多个辊轧制成型。
滚轧广泛用于制造板材、带材和型钢等。
-锻造:将金属材料放入锻造机中,在一定的压力和温度条件下,通过锻打和成型工具对金属进行加工。
锻造可用于制造各种形状的型材,对材料的内部结构有较大的影响。
-压铸:将金属材料加热至液态后,通过高压注入模具中进行成型。
压铸通常用于制造复杂形状的小型型材。
第五步:表面处理在型材成型完成后,通常需要对其表面进行一些处理,以提高外观和性能。
常见的表面处理方式包括抛光、喷涂和电镀等。
第六步:检验和质量控制在成型完成后,需要对型材进行检验和质量控制,以确保其符合要求。
检验可以通过目视检查、专用仪器或无损检测等方法进行,质量控制可以通过制定和遵守相关标准和规范来完成。
最后,经过以上几个步骤,型材成型的流程就基本完成了。
具体的型材成型流程会根据不同的材料和型材形状的要求而有所差异,但以上步骤是成型过程的主要内容。
健身器材工艺流程

健身器材工艺流程
《健身器材工艺流程》
健身器材是现代人们日常锻炼身体的必备设备,它不仅能有效改善体质,还能提升生活质量。
在制造健身器材的过程中,工艺流程显得尤为重要。
首先,在健身器材的设计阶段,需要考虑产品的功能性、稳定性以及舒适度。
设计师需要深入了解人体工程学和运动规律,根据不同的器材类型进行寻找最合适的结构和材料。
接下来是原材料的选取。
健身器材通常由金属、塑料、橡胶等材料制成,这些材料需要符合相关的强度、耐磨、防腐蚀等要求。
选择合适的原材料是保证器材质量的基础。
然后是生产工艺。
在生产过程中,需要采用一系列的工艺加工,包括剪切、焊接、冲压、喷涂等。
在这一过程中,每一道工序都需要严格控制,确保器材的外观和性能不受影响。
最后是装配与调试。
在完成生产加工后,需要将每个部件进行装配,并进行调试。
只有将每个部件严格按照要求组装在一起,才能确保健身器材的正常运行和稳定性。
因此,健身器材工艺流程是一个复杂而严谨的过程,需要设计师、工程师和生产人员共同努力,以确保生产出高质量的健身器材,为人们的健康生活提供保障。
apqp4wind 7个阶段
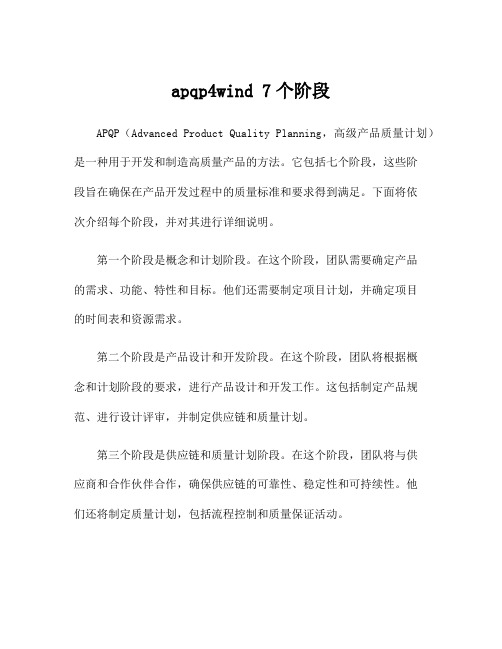
apqp4wind 7个阶段APQP(Advanced Product Quality Planning,高级产品质量计划)是一种用于开发和制造高质量产品的方法。
它包括七个阶段,这些阶段旨在确保在产品开发过程中的质量标准和要求得到满足。
下面将依次介绍每个阶段,并对其进行详细说明。
第一个阶段是概念和计划阶段。
在这个阶段,团队需要确定产品的需求、功能、特性和目标。
他们还需要制定项目计划,并确定项目的时间表和资源需求。
第二个阶段是产品设计和开发阶段。
在这个阶段,团队将根据概念和计划阶段的要求,进行产品设计和开发工作。
这包括制定产品规范、进行设计评审,并制定供应链和质量计划。
第三个阶段是供应链和质量计划阶段。
在这个阶段,团队将与供应商和合作伙伴合作,确保供应链的可靠性、稳定性和可持续性。
他们还将制定质量计划,包括流程控制和质量保证活动。
第四个阶段是过程验证阶段。
在这个阶段,团队将执行产品和过程验证,以确认产品设计和制造过程的一致性和可靠性。
这包括进行样品测试、模拟生产和生产试运行。
第五个阶段是产品和过程评估阶段。
在这个阶段,团队将对产品和过程进行评估,以确认是否满足质量标准和要求。
这包括进行一系列测试和检查,以验证产品的性能和可靠性。
第六个阶段是生产准备阶段。
在这个阶段,团队将准备生产设备、培训生产人员,并制定生产控制计划。
他们还将执行生产试验,确保生产过程的稳定性和可靠性。
最后一个阶段是产品发布和评估阶段。
在这个阶段,团队将跟踪产品的使用情况,并通过收集用户反馈和数据,对产品进行评估和改进。
APQP的每个阶段都有其特定的目标和任务,通过按照这些阶段进行系统化的产品开发和制造过程,可以提高产品的质量和可靠性。
同时,APQP也有助于减少产品开发过程中的风险和不确定性。
总体而言,APQP的7个阶段是:概念和计划阶段、产品设计和开发阶段、供应链和质量计划阶段、过程验证阶段、产品和过程评估阶段、生产准备阶段和产品发布和评估阶段。