缸筒加工的镗削滚压工艺分析
反动式筒形高压内缸加工工艺分析与探究
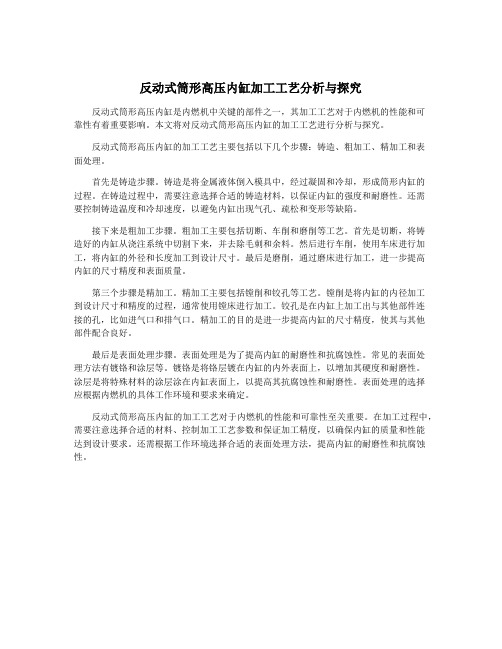
反动式筒形高压内缸加工工艺分析与探究反动式筒形高压内缸是内燃机中关键的部件之一,其加工工艺对于内燃机的性能和可靠性有着重要影响。
本文将对反动式筒形高压内缸的加工工艺进行分析与探究。
反动式筒形高压内缸的加工工艺主要包括以下几个步骤:铸造、粗加工、精加工和表面处理。
首先是铸造步骤。
铸造是将金属液体倒入模具中,经过凝固和冷却,形成筒形内缸的过程。
在铸造过程中,需要注意选择合适的铸造材料,以保证内缸的强度和耐磨性。
还需要控制铸造温度和冷却速度,以避免内缸出现气孔、疏松和变形等缺陷。
接下来是粗加工步骤。
粗加工主要包括切断、车削和磨削等工艺。
首先是切断,将铸造好的内缸从浇注系统中切割下来,并去除毛刺和余料。
然后进行车削,使用车床进行加工,将内缸的外径和长度加工到设计尺寸。
最后是磨削,通过磨床进行加工,进一步提高内缸的尺寸精度和表面质量。
第三个步骤是精加工。
精加工主要包括镗削和铰孔等工艺。
镗削是将内缸的内径加工到设计尺寸和精度的过程,通常使用镗床进行加工。
铰孔是在内缸上加工出与其他部件连接的孔,比如进气口和排气口。
精加工的目的是进一步提高内缸的尺寸精度,使其与其他部件配合良好。
最后是表面处理步骤。
表面处理是为了提高内缸的耐磨性和抗腐蚀性。
常见的表面处理方法有镀铬和涂层等。
镀铬是将铬层镀在内缸的内外表面上,以增加其硬度和耐磨性。
涂层是将特殊材料的涂层涂在内缸表面上,以提高其抗腐蚀性和耐磨性。
表面处理的选择应根据内燃机的具体工作环境和要求来确定。
反动式筒形高压内缸的加工工艺对于内燃机的性能和可靠性至关重要。
在加工过程中,需要注意选择合适的材料、控制加工工艺参数和保证加工精度,以确保内缸的质量和性能达到设计要求。
还需根据工作环境选择合适的表面处理方法,提高内缸的耐磨性和抗腐蚀性。
对深孔镗加工原理和工艺分析及刀具应用

冷加工
C刀 具
utting Tools
斜孔加工的夹具设计
汉川数控机床股份公司 (陕西汉中 723003) 张雎军
平面上的斜孔有两种情况:①在斜面上钻孔。 ②在平面上钻斜孔。它们有一个共同的特点,即孔 的中心与钻孔端面不垂直。这在没有工装保证的情 况下,就成了较困难的问题。
目前国内生产深孔镗床的厂家一般都不生产深 孔镗刀,而且生产深孔镗刀的厂家也往往不生产深 孔镗床。深孔镗刀的具体形式各有不同,但原理
R a>0.4μm,产生这种现象的原因有如下几点:①
深孔镗切削液防锈作用差,或者是加工后切削液 不清理或者清理不干净,导致加工面锈蚀,严重
44
2013年 第6期
43
C刀 具
utting Tools
(1)对深孔镗床的介绍 深孔镗床主要由床 身、床头箱和卡盘、托板(包括镗杆固定架)、进 给箱、中心架、授油器、镗杆支架、马达装置、冷 却系统及液压系统等部分组成,如图2所示。
都是能实现金属切削和滚压作用的组合体(见图 4)。
(a)深孔镗刀滚柱
(b)深孔镗加工示意
深孔镗床是加工圆柱形零件的专用机床,它可 以镗削通孔、阶梯孔,也可以进行光整滚压加工, 镗削方式为推镗,排屑方式采用向前排屑,在生 产中适用于大批量生产,也适用于小批量生产。 以T2235为例,其镗孔最大直径为350mm,根据床 身导轨长度及定制刀杆的长度,加工深度可达2~ 10m,加工表面粗糙度值达到R a≤0.4μm。 (2)深孔镗刀的加工原理 深孔镗的液压缸筒 内孔成形原理是由缸筒毛坯料经粗镗刀头粗镗完内 孔之后,再由深孔镗刀上的滚压体通过和缸筒高速 旋转相对运动光整成形。深孔镗滚压刀头的前部是 镗刀(也就是成形刀),它采用的是硬质合金涂层 机夹刀片,后部是采用和轴承钢类似具有高强高硬 度的多个滚柱。由于滚柱具有高强和高硬度,经过 滚压的缸筒内孔会产生冷作硬化,表面生成光滑如 镜的表面硬化层,经粗糙度仪检测,其表面粗糙度 值可达到R a=0.1~0.08μm。而且缸筒内壁的硬化 层使得缸筒不磨损。深孔镗镗刀如图3所示。
发动机气缸镗磨工艺分析
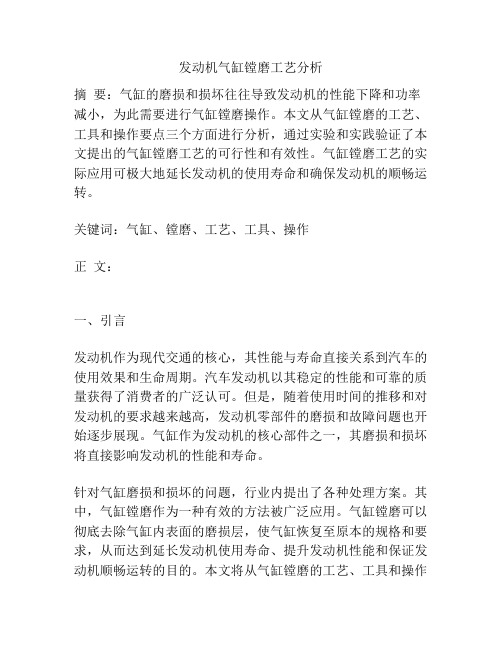
发动机气缸镗磨工艺分析摘要:气缸的磨损和损坏往往导致发动机的性能下降和功率减小,为此需要进行气缸镗磨操作。
本文从气缸镗磨的工艺、工具和操作要点三个方面进行分析,通过实验和实践验证了本文提出的气缸镗磨工艺的可行性和有效性。
气缸镗磨工艺的实际应用可极大地延长发动机的使用寿命和确保发动机的顺畅运转。
关键词:气缸、镗磨、工艺、工具、操作正文:一、引言发动机作为现代交通的核心,其性能与寿命直接关系到汽车的使用效果和生命周期。
汽车发动机以其稳定的性能和可靠的质量获得了消费者的广泛认可。
但是,随着使用时间的推移和对发动机的要求越来越高,发动机零部件的磨损和故障问题也开始逐步展现。
气缸作为发动机的核心部件之一,其磨损和损坏将直接影响发动机的性能和寿命。
针对气缸磨损和损坏的问题,行业内提出了各种处理方案。
其中,气缸镗磨作为一种有效的方法被广泛应用。
气缸镗磨可以彻底去除气缸内表面的磨损层,使气缸恢复至原本的规格和要求,从而达到延长发动机使用寿命、提升发动机性能和保证发动机顺畅运转的目的。
本文将从气缸镗磨的工艺、工具和操作要点三个方面对气缸镗磨的方法和实践进行深入探讨和分析。
二、气缸镗磨的工艺气缸镗磨的工艺是关键的一步,不同的工艺会产生不同的效果。
气缸镗磨可分为手动气缸镗磨和自动气缸镗磨,本文中主要介绍自动气缸镗磨的工艺。
1. 准备工作在进行气缸镗磨之前,需要进行准备工作:a. 拆卸气门机构、缸盖和活塞等零部件。
b. 对气缸进行检测和测量,检测气缸是否存在裂纹、变形等问题;测量气缸径和气缸度(气缸内套直径与气缸轴向高度之间的比率)。
c. 对气缸做好清洁和涂料保护。
2. 镗磨操作a. 将镗刀装入镗刀座,安放于镗机主轴上。
b. 调整切刃高度和切刃位置,使其与气缸内壁接触。
c. 启动镗机,平稳加速,控制镗头与气缸壁接触。
d. 通过旋转气缸和前后移动镗头,对气缸进行全面的加工和镗磨。
e. 实现镗磨精度控制,控制直径和度数误差,避免磨损过量导致的气缸径受损。
发动机气缸孔压板镗珩加工工艺研究

文章编号:1000-0925(2004)03-075-06250061发动机气缸孔压板镗珩加工工艺研究彭 浪1,曹 武2(1.常州东风汽车有限公司,常州213033;2.东风汽车股份有限公司)R esearch on Machining T echnics of Engine Block Bore with Simulate BoardPENG Lang 1,CHAO Wu 2(1.Changzhou Dongfeng Automotive C ompany ,Changzhou 213033,China ;2.Dongfeng Automotive C ompany )Abstract :Using simulate cylinder head in engine block machining to simulate the practical assembling state ,with technical bolts compaction technical board ,fastening a gasget on the cylinder block ,block bore finish machin 2ing (hone )has heen realized.This technics can revise transfiguration of block when a cylinder head is assembled on the block ,assure the round tolerance and prick tolerance of a bore ,and reduce the forepart inhomogeneous wear of a block bore effectively.摘要:作者在发动机气缸加工中采用压板镗珩工艺,模拟实际装配状态,用工艺缸盖螺栓将工艺压板(模拟缸盖)、工艺缸垫与气缸体压紧,然后对气缸孔进行精镗、珩磨等精加工,对气缸在实际装配时所产生的变形进行校正,从而保证发动机在装配缸盖后气缸孔的圆度和锥度,有效减少气缸孔的早期不均匀磨损。
浅析缸孔精镗工艺优化

浅析缸孔精镗工艺优化摘要:发动机缸孔的加工是缸体加工中的关键环节,精镗为其中的中心环节,其加工节拍长、加工内容多、加工质量要求严格。
本文以某发动机缸体生产线缸孔加工中精镗工艺为例,结合实际生产中遇到的问题,就缸孔精镗加工工艺的优化进行浅要的解析。
关键词:缸体,工艺,刀具,气动镗刀引言缸孔精镗,是珩磨前的最后一道加工工序,缸孔各项质量要求如直径、粗糙度、圆度、圆柱度、位置度、缸孔倒角等均有严格的要求。
在实际生产中,精镗刀具加工易发生较多问题,本文分析加工中刀具崩刀导致的缸孔加工质量问题,除从刀具方面优化外,更需要从工艺方面并结合刀具进行问题解决。
1 缸孔精镗加工设备加工中心采用德国EXCEL设备,设备型号XS321(B-AXIS,HSK63,FanucCNC系统)。
设备主轴图见图1.设备主要参数如下,X/Y/Z工作行程=630mm×630mm×710mm,X/Y/Z快速移动速度=66m/min×66 m/min×66 m/min,,X/Y/Z最小加速度=6 m/s*s×6 m/s*s×6 m/s*s,主轴转速=10000rpm,主轴功率>30kW(100%)/45kW(40%),采用Heindenhein的光栅尺,主轴内冷并内冷压力=5Mpa,轴定位精度<=8μm,轴重复定位精度<=4μm,主轴端面跳动跳动和径向跳动均<=2μm。
图1机床结构示意图2 气动镗刀结构分析:生产线使用的精加工镗刀为Ingersoll公司生产的气动镗刀,其主要构成部分为:a.调节刀具直径大小的调节螺母;b.固定半精加工、精加工刀片的刀夹;c.活塞、活塞杆、楔块及刀片组成的气动结构。
动作过程:半精加工刀片固定不动,加工完毕后,压缩空气从主轴进入气缸驱动活塞运动,活塞继而通过活塞杆将轴向方向运动转换为楔块的径向运动,从而使精加工弹性刀夹弹出,进行精镗。
油缸内孔一次镗滚成型工艺

图" %" 螺钉 柱 道
镗滚头的结构 ," 浮动镗刀 1、 %0" 套筒 4" 螺钉 0" 滚 2、 %!" 跑 %," 卡环
&" 粗镗刀 3" 保持器
!" 导向跑道
%-" 心轴
%%" 轴承套
%&" 止推轴承
粗镗刀是两刃高速钢刀片, 主偏角 ! 5 主偏角增大, 主要是为了减少切削力, 但 0!., 是在此内孔加工中, 切屑向前排, 如不继续增 大 ! 角, 铁屑不易排出, 反而受阻, 增加切削 负荷。采用两个刃, 可减少切削厚度, 使切屑 易于变形, 减少切削力。更重要的是, 因两个 切削刃受吃刀抗力相反, 使切削中刀杆受的 径向力相互抵消一部分 (不可能完全抵消, 因 切削刃有误差) 。
00
拖拉机与农用运输车
&""" 年第 4 期
滚压器既起滚压作用, 又起着导向和刚 性支承作用, 减少刀杆的弯曲和震动。 (!) 滚压器是由相同尺寸的两排滚柱在 轴向上排列组成, 它既起导向作用, 又起滚压 作用。紧挨着浮动镗刀的第一排滚柱, 起浮 动镗刀的导向作用, 滚柱与加工工件孔壁之 间隙为 "#"$ %%, 形成高精度的滚压摩擦, 使 导向不易磨损, 始终保持高的定位、 导向精 度, 也起着退刀时作为镗杆的支撑作用, 保证 镗刀不致于在已加工的表面划出刀痕。 (&) 第二排滚柱起滚压作用, 同时也增强 刚性和起到导向作用, 经滚压后, 表面产生一 层冷硬层, 提高油缸的耐磨性。滚压时, 滚柱 的过盈量不易太小, 否则, 就会使精镗过的孔 表面细小刀痕滚压不下ቤተ መጻሕፍቲ ባይዱ, 滚压后的表面粗 糙度达不到要求。过盈量也不宜过大, 过大 将使滚压阻力过大, 易使孔的母线偏移。适 宜的过盈量为 "#&" ’ "#&( %% 左右。滚柱与 跑道接触不宜过小。合适的跑道接触长度应 为滚柱长度的一半左右, 这样也有利于防止 工件母线的偏移。 ($) 第三排滚柱用于第二次滚压, 提高表 面质量。经过二次滚压后, 表面粗糙度值可 达到 !" ! " ) ! ! %。孔径尺寸将比精镗后扩 大 "#"! %%。
液压油缸内孔推镗的滚压工艺及设备

液压油缸内孔推镗的滚压工艺及设备张丽丽胡大龙张重州摘要:对液压油缸缸体内孔加工所采用的复合镗滚工艺、工艺装备设计及设备的选用进行了详尽的介绍,并对加工过程中的工艺经验数据加以推荐,对研究加工工艺与生产实践有一定的参考价值.关键词:缸体;推镗滚压工艺;镗滚压头设备中图分类号:TH 12 文献标识码: BRolling Technique and Equipment of Inner Bore Push Boring ofThe Oil VatZHANG Li-li, HU Da-long, ZHANG Chong-zhou (Zhengzhou Coalmining Machinery Plant,Zhengzhou 450007,China)Abstract:In this paper,the compound bore rolling technique of the inner bore of the oil vat body, design of the technological clamping appartus and selection of the equipment were introduced, and some practical process parameters were given.This paper can provide some reference for the study of manufacturing process.Key words:vat body; technology of the push boring rolling press; boring rolling press head equipment0 引言液压支架关键零件之一的缸体需要量很大,缸体的内孔加工又是该零件的关键工序,其内孔的加工方法有推镗珩磨和推镗滚压两种.近年来,推镗珩磨逐渐被推镗滚压所替代.我厂采用新型高效精密复合镗滚工艺,用Φ63,Φ125,Φ160及Φ230等缸筒镗滚压头代替珩磨工艺,经滚压后的内孔表面硬度、尺寸精度、位置精度,均能达到设计要求,粗糙度可达Ra0.4 mm,镗滚头的设计标准化、系列化已基本形成了模式.1 液压油缸的技术要求以Φ125油缸为例,缸体的技术要求见图1.缸体材料为27SiMn,调质硬度HB=230~270,属厚壁无缝钢管,其孔径与长度之比大于5.图1 Φ125油缸零件设计图2 镗滚头结构设计特点[1,2]滚压加工是通过滚柱对零件表面进行挤压,使零件材料产生塑性变形,从而降低零件表面的粗糙度并提高其强度.滚压加工属于无屑加工,所设计的推镗头和滚压头都与镗削加工复合在一起,因此称之为推镗滚压.镗滚压头将普通推镗头中的硬质合金导向条改为滚柱,将滑动摩擦变为滚动磨擦.这样除具有导向作用外,还有滚压作用.为了增加其滚压效果,可将滚柱设置前、后两排,每排6个滚柱,一次行程兼起两次行程的作用,可使油缸的塑性变形得到改善.滚压头的结构见图2,主要由刀盘1、滚压滚柱4、保持器5、平面上推轴承7、芯轴8、半圆卡环6等组成 .1.刀盘2.紧固螺钉3.机夹刀4.滚压滚柱5.保持器6.半圆环7.平面轴承8.芯轴图2 镗滚头结构示意图滚压时,动力通过床头主轴接盘转动带动零件,滚柱受零件孔壁摩擦力带动,沿其滚道的外圆滚动,迫使保持器等相对于滚道作旋转运动,被加工表面的原始波峰在滚柱的辗压作用下,晶粒沿滚柱运动方向位移,并被拉长使微观波谷填平.滚压结束后,当纵向进给伸进套筒接盘后,令主轴停转,刀盘卸下,然后卸下半圆卡环,滚柱退至过渡套,滚压头工作直径即自行减少,滚压头退出.滚柱的材料为GCr15,热处理淬火硬度HRC 62~66,尺寸Φ13×20,Ra<0.2,滚柱前端磨出R=2 mm的圆弧,尾部有30°×4的锥度.镗刀采用机夹刀具.不重磨涂层刀片,刀片材料选用YB 435,排屑方式采用杠销式,刀片、刀杆的耐用度很高,且刀片具有很高的尺寸精度,能够保证排出C形屑.3 推镗滚压加工机床[3]加工缸体内孔滚压时,缸径>Φ140时是在T 2120或T 2130镗床上进行的,而对于缸径<Φ125的油缸,因机床负荷大,输油器镗杆粗,不适合在镗床上加工,须将C 630车床改装成镗床.改装时,将尾座去掉改为镗杆座,拖板上面的方刀架、横向走刀溜板卸下,改成输油器.输油器具有冷却、导向、夹紧工件的作用.车床主轴卡盘装一套筒和带90°锥面的接盘,镗刀体镗杆孔中心线与车床主轴中心线等高,同轴度误差不大于0.02 mm,滚压头与刀杆中心同轴度误差不小于0.02 mm.加工装夹示意图见图3.缸体外圆的45°倒角作定位夹紧基准,通过床头接盘和输油器上的接盘顶住工件即可定位夹紧.切削冷却液从输油器的侧口输入,在内腔沿刀杆流向刀头,将切削热和切屑带走.加工时工件旋转,刀具作直线运动,这样有利于油缸壁厚均匀,能保证其直线性.1.床头箱2.套筒接盘3.镗滚头4.后接盘5.输油器6.镗杆导向套7.镗杆8.镗杆座图3 缸体加工工艺系统图4 工艺参数的选择(1) 用加长C630车床时,刚性要好,精度要高,主轴径向和轴向跳动误差应小于0.015 mm.(2) 前后排6个滚柱的几何尺寸和形位公差必须选配一致,误差应在0.002 mm以内,每排滚柱连接圆角R也必须一致,否则影响滚压质量.(3) 为使滚压头进入工件前有一个可靠的初始导向,输油器上的滚压导向套过盈导向,其过盈量为0.02 mm.这样在滚柱进入工件前,镗刀不易发生让刀现象,保证了内孔的尺寸精度和直线度.(4) 滚压时工件的过盈量按下式选取Δt=hp+he+Δ,式中:hp为压下量,滚压后孔径实际尺寸与滚压前镗刀对刀尺寸之差;he为弹性恢复量.在挤压力作用下,Δt高度内,一部分金属产生塑性变形hp,一部分产生弹性变形he;Δ为扩张量,与机床工艺系统刚度、切削用量(V,f)大小,工件的外形是否规则,弯曲度大小等有关.Δt为过盈量,滚压前滚子的对刀尺寸与镗刀对刀尺寸之差;过盈量一般选取0.12~0.15mm.(5) 利用对刀规,使对刀精度达到0.01 mm.(6) 滚压开始必须先通入冷却液,以防高温烧伤内孔表面.冷却液采用乳化液、机油或861通用切削液等,必须对切削液采取过滤和防尘措施.(7) 若镗滚前壁厚差大小于1.5 mm需粗镗,而当壁厚差小于1.5 mm 时,可直接镗滚.粗镗的目的是为了保持镗滚时余量较均匀,不致于因余量变化过大导致切削力变化过大而引起振动.文章编号:1007-6492(1999)01-0106-02作者简介:张丽丽(1961-),女,广东省潮阳县人,郑州煤矿机械厂高级工程师,主要从事金属加工工艺等技术工作.作者单位:郑州煤矿机械厂,河南郑州 450007参考文献[1]程通模.滚压和挤压光整加工[M].北京:机械工业出版社,1989.[2]金属机械加工工艺设计手册[M].上海:上海科学技术出版社,1987.[3]王先逵.机械制造工艺学[M].北京:清华大学出版社,1989.收稿日期:1998-06-18; 修订日期:1998-10-30。
液压缸缸筒镗孔工艺分析

作进给运动,切削稳定性很好。所 以它特别适用于加工直线度要求较
油是从镗头周围喷射切削区,不仅 对镗刀支承块导向块进行强制润滑 冷却 ,亦可减轻镗头 与缸筒的摩
擦 ,从而减轻 了切 削过程的振动 。
高、长径比较大以及壁薄的缸体,
但必须是等直径的通孔。由于这种 加工方法在镗削时,切削液带着切 屑沿着镗杆表面和缸筒待加工表面
排 屑孔流入镗杆 内孔 ,向后排出到
装卸亦较麻烦 ,即使一次拉镗完
成 ,其 效 率 还是 较 低 。据 统 计 ,
图 1
( )缸体旋转、刀具 固定而 2 只做进给运动 这种形式是在粗镗 及半精镗时,由于镗头导向套孔轴 线与床头箱主轴轴线存在同轴度误 差。该误差值考虑到授油器经常移 动磨损和主轴温升的补偿需要,在 机床精度检验标准中规定了其允差
维普资讯
胁1 e 7 :
0
■ 一汽 山东汽车 改装厂, 葛树才 张 玲 吕光宙
筒镗孔工艺分析
液压缸缸筒加工工艺可分为两 大类:一类是用热轧无缝钢管进行 粗镗、精镗、滚压或珩磨,称之谓 热轧管镗滚法或镗珩法;另一类是 用冷拔管强力珩磨,称之谓冷拔管
之 间的 环形 空 隙 流 出 ,所 以 镗 杆 表 面 易 被 切 屑划 伤 。 同时 ,为 保
注意切削用量的选择。如为了减少
轴 向进给 力引起镗杆弯 曲,要适 当 降低进给量等 。
这对延长刀具寿命以及降低缸筒内
表面粗糙 度值都非常有利 。据 实验
对比,半精镗时,后者加工表面粗 糙度值能稳定在R = ./ 32t . m,而前 者从整个表面上看是R = .1 32 m, x 但每根缸筒都可发现几处只能达到
类:推镗法和拉镗法。
超小直径缸筒的加工
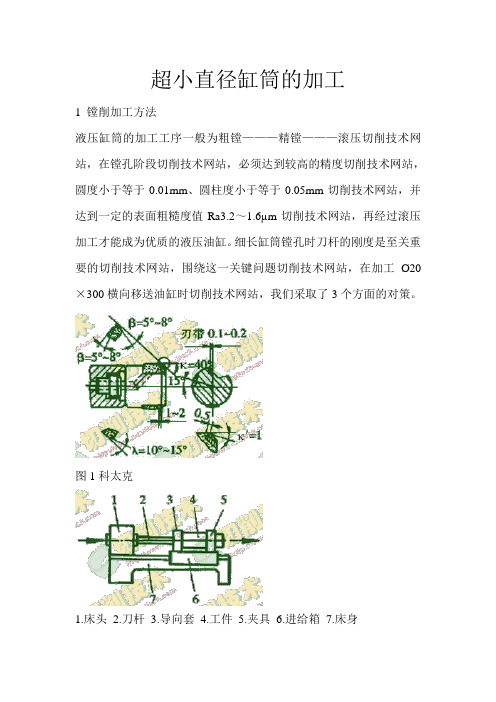
超小直径缸筒的加工1 镗削加工方法液压缸筒的加工工序一般为粗镗———精镗———滚压切削技术网站,在镗孔阶段切削技术网站,必须达到较高的精度切削技术网站,圆度小于等于0.01mm、圆柱度小于等于0.05mm切削技术网站,并达到一定的表面粗糙度值Ra3.2~1.6µm切削技术网站,再经过滚压加工才能成为优质的液压油缸。
细长缸筒镗孔时刀杆的刚度是至关重要的切削技术网站,围绕这一关键问题切削技术网站,在加工Ø20×300横向移送油缸时切削技术网站,我们采取了3个方面的对策。
图1科太克1.床头2.刀杆3.导向套4.工件5.夹具6.进给箱7.床身图2科太克1.前调整螺母2.滚子3.砂架4.推力轴承5.后调整螺母6.锁紧钉7.刀体8.压片9.螺钉图3科太克首先在毛坯上进行控制选取规格为Ø28×5、材料为45钢的热轧无缝钢管切削技术网站,使镗孔的加工余量在1~1.5mm左右。
在加工前对毛坯进行校直处理切削技术网站,使其直线度小于0.3mm切削技术网站,这样就把切削时的刀具负荷降至最低切削技术网站,使较细的刀杆也能有较大的刚度。
刚性镗刀(见图1)这种刀具能将粗镗和精镗两道工序一次完成。
它由刀头和刀杆两部分组成切削技术网站,刀头与刀杆采用可拆式切削技术网站,双圆柱定心切削技术网站,具有较高的重复定位精度。
刀片和两条长40mm的导向块采用硬质合金材料切削技术网站,并焊接在刀头上切削技术网站,刀杆为外径Ø18切削技术网站,内径Ø8的空心杆。
切削液从中空的刀杆里直接喷射至加工区域切削技术网站,冷却和润滑刀具并冲走切屑。
刀具的主要参数如下:前角g=5°~8°切削技术网站,后角b=5°~8°切削技术网站,主偏角k=40°切削技术网站,过渡刃主偏角k’=16°’刃倾角l=10°~15°切削技术网站,修光刃长3~4mm切削技术网站,刀尖应较支承刃超前1~2mm。
镗削工艺特点
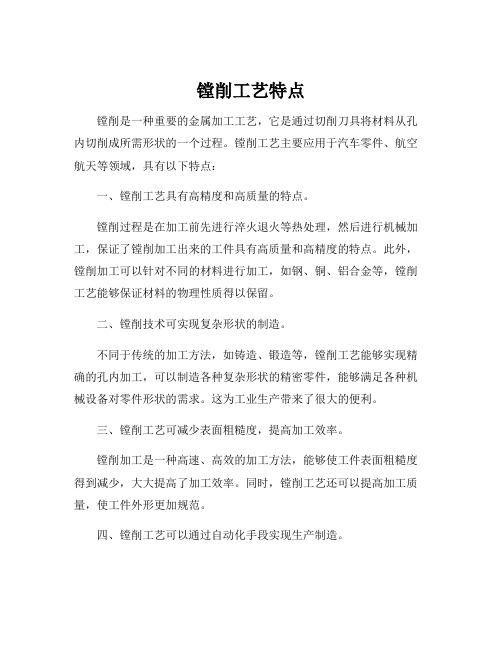
镗削工艺特点
镗削是一种重要的金属加工工艺,它是通过切削刀具将材料从孔内切削成所需形状的一个过程。
镗削工艺主要应用于汽车零件、航空航天等领域,具有以下特点:
一、镗削工艺具有高精度和高质量的特点。
镗削过程是在加工前先进行淬火退火等热处理,然后进行机械加工,保证了镗削加工出来的工件具有高质量和高精度的特点。
此外,镗削加工可以针对不同的材料进行加工,如钢、铜、铝合金等,镗削工艺能够保证材料的物理性质得以保留。
二、镗削技术可实现复杂形状的制造。
不同于传统的加工方法,如铸造、锻造等,镗削工艺能够实现精确的孔内加工,可以制造各种复杂形状的精密零件,能够满足各种机械设备对零件形状的需求。
这为工业生产带来了很大的便利。
三、镗削工艺可减少表面粗糙度,提高加工效率。
镗削加工是一种高速、高效的加工方法,能够使工件表面粗糙度得到减少,大大提高了加工效率。
同时,镗削工艺还可以提高加工质量,使工件外形更加规范。
四、镗削工艺可以通过自动化手段实现生产制造。
镗削机械可以通过数控自动化,实现自动化生产制造,不仅提高了生产效率,也可以避免因人误差带来的生产损失,保证了工件的质量。
其模块化的特点,也方便更换刀具附件等加工零部件,从而加快生产效率。
总之,镗削工艺在加工业中占据着重要的地位,其独特的优势可以适应不同领域的加工需求。
随着机械制造技术的发展,镗削工艺也将进一步发展,不断演化为更加先进和高效的加工方法,为工业自动化生产提供了更多的可能。
油缸内孔的滚压加工
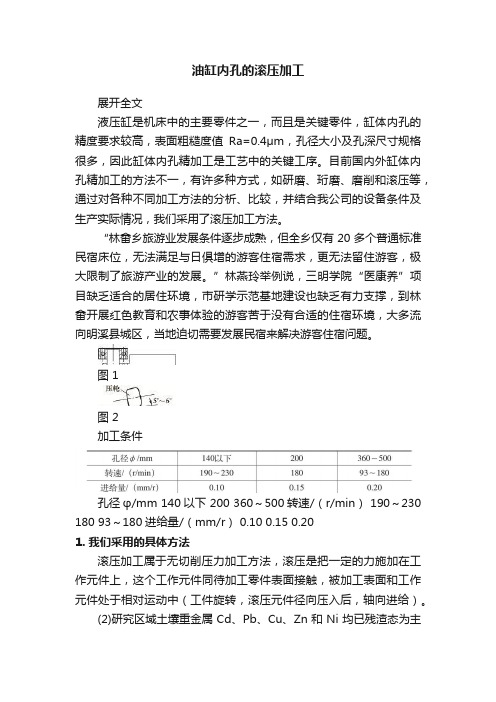
油缸内孔的滚压加工展开全文液压缸是机床中的主要零件之一,而且是关键零件,缸体内孔的精度要求较高,表面粗糙度值Ra=0.4μm,孔径大小及孔深尺寸规格很多,因此缸体内孔精加工是工艺中的关键工序。
目前国内外缸体内孔精加工的方法不一,有许多种方式,如研磨、珩磨、磨削和滚压等,通过对各种不同加工方法的分析、比较,并结合我公司的设备条件及生产实际情况,我们采用了滚压加工方法。
“林畲乡旅游业发展条件逐步成熟,但全乡仅有20多个普通标准民宿床位,无法满足与日俱增的游客住宿需求,更无法留住游客,极大限制了旅游产业的发展。
”林燕玲举例说,三明学院“医康养”项目缺乏适合的居住环境,市研学示范基地建设也缺乏有力支撑,到林畲开展红色教育和农事体验的游客苦于没有合适的住宿环境,大多流向明溪县城区,当地迫切需要发展民宿来解决游客住宿问题。
图 1图 2加工条件孔径φ/mm 140以下 200 360~500转速/(r/min) 190~230 180 93~180进给量/(mm/r) 0.10 0.15 0.201. 我们采用的具体方法滚压加工属于无切削压力加工方法,滚压是把一定的力施加在工作元件上,这个工作元件同待加工零件表面接触,被加工表面和工作元件处于相对运动中(工件旋转,滚压元件径向压入后,轴向进给)。
(2)研究区域土壤重金属Cd、Pb、Cu、Zn和Ni均已残渣态为主要存在形态,除Cu元素外,其余4种元素的3种活性组分之和比例均较高,尤其是Cd元素,其有效态略高于稳定态,生物活性最强,生物有效性大小顺序为Cd>Pb>Ni>Zn>Cu。
工作元件可以是滚压球和硬质合金嵌入物。
这种相对运动与切削加工一样是通过速度值和进给量表征的。
我们采用以202或204单列向心球轴承为主要元件的滚压工具,如图1所示。
在加工较小孔径的缸体时,我们采用了整体滚压工具。
例如,在加工CK61160数控重型卧式车床床头箱内的变速液压缸时(孔径为φ80+0.05 +0.03mm),使用的是深孔弹性滚压工具。
缸筒深孔镗削工艺改进前后工艺特点分析
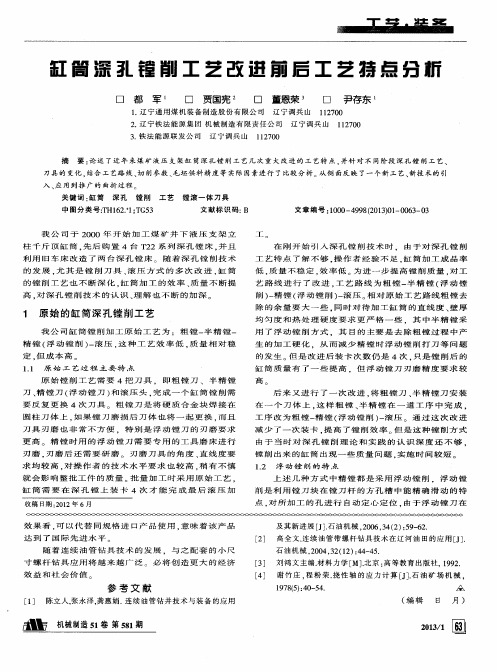
关键 词 : 缸筒
深子 L 镗 削 工 艺
镗 滚 一 体 刀 具
中 图分 类 号: T H1 6 2 . 1 ; T G 5 3
文献标识码: B
文章编号 : 1 0 0 0 — 4 9 9 8 f 2 0 1 3 ) 0 1 — 0 0 6 3 — 0 3
3 . 铁 法 能 源 联 发 公 司 辽 宁 调兵 山 1 1 2 7 0 0
摘
要: 论 述 了近 年 来 煤 矿 液 压 支 架缸 筒 深 孔 镗 削 工 艺 几 次 重 大 改 进 的 工 艺特 点 , 并针 对 不 同阶 段 深孔 镗 削 工 艺 、
刀 具 的 变化 , 结合工艺路线、 切 削参 数 、 毛 坯供 料 精 度 等 实 际 因 素进 行 了 比较 分 析 。 从 侧 面反 映 了一 个 新 工 艺 、 新技术的引
就 会 影 响 整 批 工 件 的 质 量 批 量 加 工 时 采 用 原 始 工 艺 . 缸 筒 需 要 在 深 孔 镗 上 装 卡 4次 才 能 完 成 最 后 滚 压 加
收 稿 日期 : 2 0 1 2年 6月
上 述 几 种 方 式 中 精 镗 都 是 采 用 浮 动 镗 削 .浮 动 镗 削 是 利 用 镗 刀 块 在 镗 刀 杆 的 方 孔 槽 中 能 精 确 滑 动 的特
点 . 对 所 加 工 的 孔 进 行 自动 定 心 定 位 . 由于浮 动镗 刀在
效 果看 . 可 以代 替 同 规 格 进 口产 品 使 用 . 意 味 着 该 产 品
达 到 了 国 际 先 进 水 平 随 着 连 续 油 管 钻 具 技 术 的发 展 .与 之 配 套 的 小 尺
缸筒深孔镗削工艺改进前后特点分析
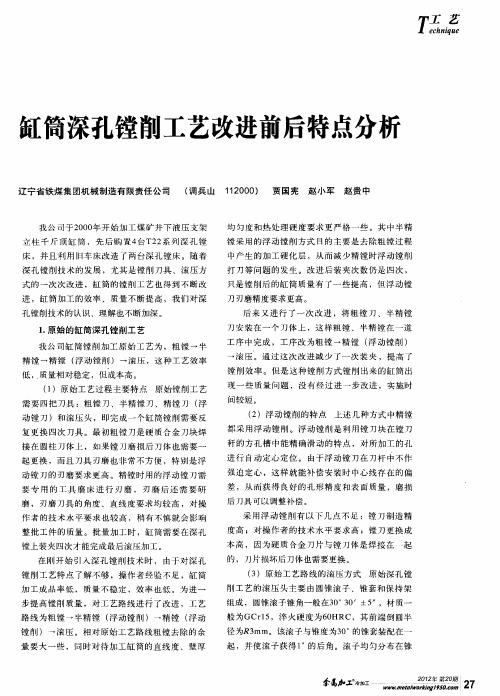
保 证 了 滚 道 同其 他 配 合面 的 同轴 度 ,提 高 了 镗 滚
( )镗滚一体 刀具镗滚特点 镗滚一体 刀具 1
( 图2 见 )就 是 把 半精 镗 、精 镗 、滚 压 三道 工 序 合 并 为 一 道 工 序 ( 有 将 粗 镗 、半 精 镗 、精 镗 、 滚 也
孔镗削技术的认识、理解也不断加深。
1 原始的缸 筒深 孔镗削工艺 .
我 公 司 缸 筒 镗 削加 工 原 始 工 艺 为 ,粗 镗 一半 精 镗 一精 镗 ( 动 镗 削 ) 一 滚 压 ,这 种 工 艺 效 率 浮 低 ,质 量 相对 稳 定 ,但 成 本 高 。 .
工序 中完成 ,工序 改为粗镗 一精镗 ( 浮动镗削 )
一
滚 压 。通 过 这 次 改 进 减 少 了一 次 装 夹 ,提 高 了
镗 削效 率 。 但 是 这 种 镗 削 方 式 镗 削 出来 的缸 筒 出 现 一 些 质 量 问题 , 没 有 经 过 进 一 步 改 进 ,实 施 时
间较 短 。
( )原始 工艺过程主要特 点 原始镗 削工艺 1
圆锥 滚子 锥套
1 . 镗杆
2推力轴承 .
3导向内套 4半环 . . 8 . 滚子
5前压盖 .
6压盖 固定螺钉 .
7 . 铜套保持架
9后压盖 1 . 0刀体
l. 1刀体固定螺钉
1. 2 可转位刀片
胶 木 条 的 支 承 、导 向是 有 间 隙 的 。所 以 滚 柱 的 导
向精度更高 ,这既提高 了产 品质量 ,又达到 了简
Th l < e c
缸筒深孔镗削工艺改进前后特点分析
发动机气缸镗磨工艺分析

销 孔 的裙 部 直 径 增 大 0 0 5~ 0 0 5 .2 .3mm ,垂 直 于 销 孔 方 向 的
பைடு நூலகம்
8 %左右 的气缸 体可采 用下平面 定位镗缸 ( 0 方法 2 ),
2% 左 右 的 气 缸 体 可 以 采 用 修 整 后 的 下 平 面 固 定 镗 缸 ( 法 0 方
00 0~ 0 0 6 .1 .1mm, 宽度为 0 0 4~ 0 0 6 .0 .0 mm,间隔距离应
隙相差 1 mm,则汽 车要少行 l 00 m; O 0 k 镗缸定位基 准选择不 不 经 加热 直 接 安 装 活 塞 销 及 连 杆 ,活 塞 变 形 极 为 严 重 。如 果
当 ,可 能 会 产 生 全 部 活 塞 装配 后都 向 同 一 方 向 偏 斜 等 现 象 ; 将 活 塞 从 10 0 ℃的 水 中取 出 立 即 装 用 活 塞 销 ,则 也 有 不 同 程 而 切 削 角 选 择 不 当 ,就 不 能 在 缸 壁 上 贮 油 ,会 大 大 降 低 气 缸 度 的影 响 。 在 磨 合 阶段 的 耐 磨 性 。本 文 在 总 结 公 司 多 年 维 修 经 验 的 基 础 上 提 出 几个 镗 磨 时应 注 意 的 问题 。
温 后使 用 。
适 用 范 围
( ) 塞 连 杆 组 件 装 入 气 缸 前 应 做 到 3 测量 缸 壁 间隙 。 3活 次 测 量 的 方 法 是 ,把 活 塞 倒 置 气 缸 中 ,用 一 定 厚 度 、 宽度 和长
度的厚薄规塞入活塞 ( 承压方向)与缸壁 问,用弹簧秤拉 出 厚薄规 ,其拉 力应符合技 术条件 的规定 ( 见维修手册 )。
() 1 要根据活塞材料的膨胀系数 选留适 当的缸壁 间隙,
缸筒加工的镗削滚压工艺分析

缸筒加工的镗削滚压工艺分析缸筒作为油缸、矿用单体支柱、液压支架、炮管等产品的主要部件,其加工质量的好坏直接影响整个产品的寿命和可靠性。
缸筒加工要求高,其内表面粗糙度要求为Ra0.4~0.8µm,对同轴度、耐磨性要求严格。
缸筒的基本特征是深孔加工,其加工一直困扰加工人员。
采用滚压加工,由于表面层留有表面残余压应力,有助于表面微小裂纹的封闭,阻碍侵蚀作用的扩展。
从而提高表面抗腐蚀能力,并能延缓疲劳裂纹的产生或扩大,因而提高缸筒疲劳强度。
通过滚压成型,滚压表面形成一层冷作硬化层,减少了磨削副接触表面的弹性和塑性变形,从而提高了缸筒内壁的耐磨性,同时避免了因磨削引起的烧伤。
滚压后,表面粗糙度值的减小,可提高配合性质。
1 滚压刀具的设计以我们设计的Ø160mm组合镗滚刀为例说明刀具设计及工艺。
如结构图所示,保护帽1用于保护芯轴头部对刀仪的基准位置。
支承垫4和支承钉6的作用是保护保持架(ZQSn6-6-3)免受滚柱轴向压力的压裂。
支承套11材料为GCr15,要求与芯轴15过盈配合,组装后配磨。
滚柱材料为GCr15或高速钢W18Cr4V,62~65HRC。
滚柱在镗滚刀中起滚压和导向作用。
采用滚柱滚压的原因是它较圆珠滚压工作接触面积大,能承受较大的滚压力,可选用较大的进给量,从而提高生产率。
对薄壁低刚性的工件,应选用直径较小而较长的滚柱,滚柱直径较小时可得较小的表面粗糙度值,这里我们选Ø13mm滚柱。
滚柱圆角半径r在一定范围内影响表面粗糙度,减小圆角半径,相应地增加了单位应力,能减小表面粗糙度值和提高表面冷硬度。
滚柱数量z 增多可减小滚压粗糙度值,但所需滚压力增大。
一般z取5~10,我们取6。
加大滚柱滚压后角a可减小表面粗糙度值,但a过大易形成过冷硬状态,破坏表面层,一般取a≤1°。
滚柱直径方向上高低不一会造成卡死、振动、拉伤加工表面,故直径方向上差值不大于0.03mm。
镗削工艺与技巧

镗削工艺与技巧镗削是一种精密加工方法,可用于加工各种孔和内表面,广泛应用于机械制造、航空航天、汽车工业和模具制造等领域。
本文将探讨镗削的工艺与技巧,以帮助读者更好地理解和运用这一加工方法。
一、镗削工艺概述镗削是通过旋转刀具来加工孔和内表面的方法,工艺流程一般包括以下几个步骤:工件夹紧、刀具装夹、切削参数设定、进给运动和切削运动等。
在进行镗削之前,需要清洁和检查工件及刀具,确保其表面光洁度和精度达到要求。
镗削通常分为粗抛削和精抛削两个阶段。
粗抛削是为了去除工件内部的余量,使之接近最终尺寸。
精抛削则是为了提高工件的表面质量和尺寸精度。
在粗抛削过程中,一般采用较大的进给量和较低的转速;而在精抛削过程中,进给量较小且转速较高,以获得更好的加工效果。
二、镗削技巧1. 刀具的选择与装夹选用合适的刀具是镗削的基础。
一般情况下,刀具的长度应尽可能短,以提高刚度和稳定性。
同时,刀具的材质和涂层也需要根据加工材料的硬度和耐磨性进行选择。
刀具的装夹要牢固可靠,确保切削过程中不产生松动或振动。
2. 切削参数的设定切削参数的设定直接影响到镗削质量和效率。
一般来说,切削速度越高,切削力越大,但加工效率也会相应提高。
合理的切削速度应根据工件材料和刀具材质进行选择。
进给速度和进给量也需要根据工件情况进行调整,以保证加工精度和表面质量。
3. 切削液的选择与使用切削液在镗削过程中起到冷却、润滑和清洁的作用,可以降低切削温度、减少摩擦和磨损,并防止切屑和切削液滞留在切削区域。
选择合适的切削液要考虑工件和刀具材料、加工条件以及环保要求等因素。
4. 工艺操作的注意事项在进行镗削操作时,需要注意以下几个方面:- 预热工件:对于较大尺寸和较硬的工件,可以适当预热,以减少切削应力和切削工具的磨损。
- 控制进给力度:镗削过程中,要保持平稳的进给力度,避免产生振动和过大的切削力,以确保加工质量和工具寿命。
- 定期检查和更换刀具:刀具磨损会影响加工质量和效率,因此要定期检查刀具的磨损情况,并及时更换。
大直径油缸内孔镗-滚复合加工工艺
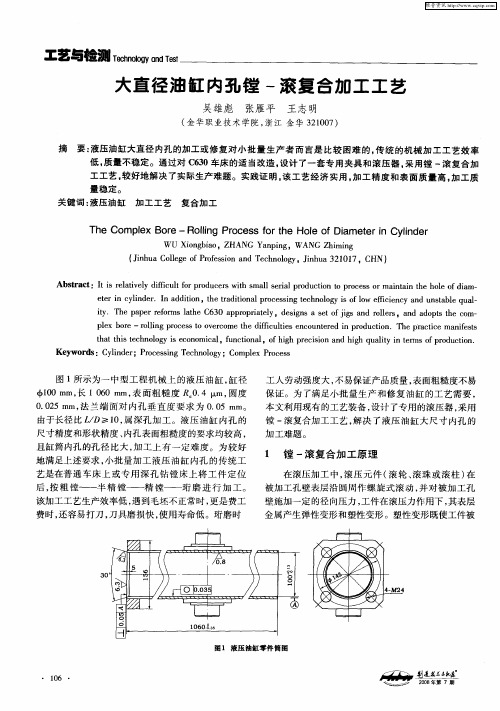
l
l
l
_
曼
\ 『 ( \ u/ J )
l J I
ee n c l de . I d iin,t e ta i o a r c s i e h l g so w fiin y a d u sa l u l tr i y i r n a d to n h r dt n lp o e sngt c noo y i fl efc e c n n tb e q a — i o
后 , 粗 镗—— 半 精 镗— —精 镗— — 珩 磨 进 行 加 工 。 按 该 加工 工艺 生产效 率低 , 到毛坯 不 正常 时 , 是费工 遇 更 费 时 , 容易 打刀 , 还 刀具磨 损快 , 用寿命 低 。珩磨 时 使
I
_
金属 产生 弹性 变形 和塑 性变 形 。塑性 变形 既使工 件被
pe r l x boe—r l n r c s o o e c me t e d f c te nc u tr d i r d to o l g p o e st v r o h i ul se o n e e n p o ucin.Th x cie ma ie t i i i ep '艺 , 决 了液 压 油缸 大 尺 寸 内孔 的 解
加工难 题 。
尺 寸精度 和形状 精 度 、 内孔表 面粗糙 度 的要求 均较 高 ,
滚压工艺参数及滚压注意事项

滚压工艺参数4.1 滚压量的确定滚压缸体时滚柱在缸筒工件表面上作无滑动的滚动,使缸筒表面层金属产生弹一塑性变形,修正表面微观几何形状误差,降低表面粗糙度值。
滚压加工时,在缸筒工件表面上形成3个变形区域:①滚压前工件终加工表面的微观几何形状误差在滚压时的变形为Ah=0.5R =2R ;②滚压时工件表面材料的塑性变形为△R;③滚压后工件表面材料的弹性变形恢复量为A6。
滚压时各参数如图3所示。
滚压前的镗孔尺寸可按下面算式I2 确定:式中:D 为缸孔内孔的图纸要求尺寸;&i为挤压应力;E为弹性模量;HB为材料布氏硬度;R1为滚柱半径;R2为缸孔内孔半径;R 为缸孔预加工表面粗糙度;△R为缸筒径向塑性变形量。
以上计算给出了滚压缸筒所需的关键参数即滚压深度,为工艺工序尺寸的确定以及镗滚头的设计提供了依据,但由于缸筒材料参数以及尺寸在不同部位和不同工件的差异性,所以具体尺寸还需通过工艺实验现场验证。
不同缸径的工件,滚压深度不同,但并非成比例增大。
对中等直径工件(80~200 miD.)而言,一般为0.05~0.15 mm。
由于滚压过程中孔壁产生塑性变形的同时还产生弹性变形,滚压后工件实际孔径要比滚压头直径小,因此完成滚压后,不能直接拉出滚压头,否则会在滚柱相应位置拉伤工件。
4.2 滚压次数缸体表面在第一次滚压中塑性变形最显著、最充分,表面质量得以明显提高,随后效果便不再明显;相反,滚压次数的增加,会使表面产生过大的压应力,破坏第一次滚压得到的表面质量,因而实际生产中一般采用一次滚压。
4.3 进给量进给量对工件表面的微观几何形状和物理机械性能影响很大,在滚压深度一定的条件下,疲劳强度随着进给量的减小而增大。
但当进给量减小到一定值时(0.3 mm/r),疲劳强度几乎保持不变。
进给量太大,滚压不充分;进给量太小,等于重复滚压,效果适得其反。
实际生产中一般为0.1~0.3 mm/r。
4.4 滚压速度滚压速度是指滚压工件旋转的线速度,滚压速度的高低,不仅影响生产率,而且关系到滚压质量的好坏。
- 1、下载文档前请自行甄别文档内容的完整性,平台不提供额外的编辑、内容补充、找答案等附加服务。
- 2、"仅部分预览"的文档,不可在线预览部分如存在完整性等问题,可反馈申请退款(可完整预览的文档不适用该条件!)。
- 3、如文档侵犯您的权益,请联系客服反馈,我们会尽快为您处理(人工客服工作时间:9:00-18:30)。
缸筒加工的镗削滚压工艺分析
缸筒作为油缸、矿用单体支柱、液压支架、炮管等产品的主要部件,其加工质量的好坏直接影响整个产品的寿命和可靠性。
缸筒加工要求高,其内表面粗糙度要求为Ra0.4~0.8µm,对同轴度、耐磨性要求严格。
缸筒的基本特征是深孔加工,其加工一直困扰加工人员。
采用滚压加工,由于表面层留有表面残余压应力,有助于表面微小裂纹的封闭,阻碍侵蚀作用的扩展。
从而提高表面抗腐蚀能力,并能延缓疲劳裂纹的产生或扩大,因而提高缸筒疲劳强度。
通过滚压成型,滚压表面形成一层冷作硬化层,减少了磨削副接触表面的弹性和塑性变形,从而提高了缸筒内壁的耐磨性,同时避免了因磨削引起的烧伤。
滚压后,表面粗糙度值的减小,可提高配合性质。
1 滚压刀具的设计
以我们设计的Ø160mm组合镗滚刀为例说明刀具设计及工艺。
如结构图所示,保护帽1用于保护芯轴头部对刀仪的基准位置。
支承垫4和支承钉6的作用是保护保持架(ZQSn6-6-3)免受滚柱轴向压力的压裂。
支承套11材料为GCr15,要求与芯轴15过盈配合,组装后配磨。
滚柱材料为GCr15或高速钢W18Cr4V,62~65HRC。
滚柱在镗滚刀中起滚压和导向作用。
采用滚柱滚压的原因是它较圆珠滚压工作接触面积大,能承受较大的滚压力,可选用较大的进给量,从而提高生产率。
对薄壁低刚性的工件,应选用直径较小而较长的滚柱,滚柱直径较小时可得较小的表面粗糙度值,这里我们选Ø13mm滚柱。
滚柱圆角半径r在一定范围内影响表面粗糙度,减小圆角半径,相应地增加了单位应力,能减小表面粗糙度值和提高表面冷硬度。
滚柱数量z 增多可减小滚压粗糙度值,但所需滚压力增大。
一般z取5~10,我们取6。
加大滚柱滚压后角a可减小表面粗糙度值,但a过大易形成过冷硬状态,破坏表面层,一般取a≤1°。
滚柱直径方向上高低不一会造成卡死、振动、拉伤加工表面,故直径方向上差值不大于0.03mm。
技术要求:
(1)装配后转动后齿环、保待架和滚柱面能自由滑动(2)退刀时,保证刃口向上,以免拉伤
1.保护帽
2.紧定螺钉
3.保持架
4.支承垫
5.滚柱
6.支承钉 7轴承 8.后齿环 9.前齿环
10.小套 11.支承套 12.螺栓 13.刀体 14.机夹刀块 15.芯轴
组合镗滚刀结构图
滚压完成,退刀时,勾动后齿环8,使前、后齿环成啮合状态,在保持架3与芯轴15之间插人退刀半环(其长度为滚柱长度基本尺寸),从而使得保持架带动滚柱沿支承套1:40的锥度后移,退入支承套槽中,使滚柱与缸筒脱离接触,实现退刀。
镗滚刀中滚柱、支承套、保持架为易损件,每副易损件约可滚压Ø90m×2150m油缸150根(以行程计算)。
2 滚压影响因素分析
1.工件材料滚压适用于50以下碳钢,碳含量愈低,孔扩张量愈小。
材料硬度越低,塑性越高,则滚压的表面质量越好。
滚压后硬度虽可达到400HB,但从280HB开始,滚压后效果显著下降,因此,滚压前工件材料硬度一般不低于140HB。
2.预加工一般采用车削或镗削。
工件的几何形状精度由预加工来保证,一般要求预加工Ra0.25~5µm,锉削滚压加工余量0.5mm左右。
3.滚压次数第一次滚压中塑性变形最显著、最充分,表面质量得到明显提高,随着滚压次数的增加,表面产生过大的压应力,会破坏第一次滚压所得到的表面质量,即破坏滚压冷硬层,造成脱皮现象故组合撞滚刀的滚压次数选一次。
4.切削用量进给量f越大,表面粗糙度值将增大;滚压速度v与表面质量关系不大。
滚压头过盈量一般取0.15mm左右(普通Ø60~200mm孔径油缸),滚压量0.02~0.04m。
以
Ø160mm孔加工为例,我们取v=30~40m/min,f=0.1~0.25mm/r。
5.冷却清洁我们采用HT-40机械油:煤油(GB258-64)=1:1,也可采用硫化油:柴油=1:1配方。
加工时压力油从滚压头后部冲向镗滚刀,经未加工表面从床头侧排到油槽中,这样避免了脱落的切屑刮伤已加工表面。
油箱的设计,主要问题是清洁、沉淀而不是冷却,因为切削油每20min循环一次,根本来不及沉淀,加大容量不是方法。
过滤问题主要通过选择合适的过滤器材和在工艺上来保证。
现场证明,过滤网孔隙太大,毛毡孔隙太小容易堵塞。
缸筒滚压加工常见问题及解决方法:尺寸超差:对刀不准,刀具或滚压头磨损;内表面有振动波纹:材料太硬,转速太高;明显刀纹:进给量大,切削深度过大;拉沟:刀刃断裂,切削液量小,切削液温度太高。
3 应用实例
镗削滚压工艺是一种高效高质量的工艺措施,现以Ø160mm健削滚压头(45钢无缝钢管)为例证明镗滚效果。
滚压后,孔表面粗糙度由幢滚前 Ra3.2~6.3µm减小为Ra0.4~0.8µm,孔的表面硬度提高约30%,缸筒内表面疲劳强度提高25%。
油缸使用寿命若只考虑缸筒影响,提高 2~3倍,镗削滚压工艺较磨削工艺效率提高3倍左右。
以上数据说明,该镗削滚压工艺是高效的,能大大提高缸筒的表面质量。