镗削的基本加工方法
镗削加工

镗削加工1.什么叫悬伸镗削法?它有哪些特点?使用悬伸的单镗刀杆,对中等孔径和不穿通的同轴孔进行镗削加工,这种加工方法叫悬伸镗削法。
悬伸镗削法的主要特点有:(1)由于悬伸镗削所使用的镗刀杆一般均较短、粗,刚性较好,切削速度的选择可高于支承镗刀杆,故生产效率高。
(2)在悬伸镗刀杆上装夹、调整刀具方便,在加工中又便于观察和测量,能节省辅助时间。
(3)用悬伸镗削法采用主轴送进切削时,由于镗刀杆随主轴送进而不断悬伸,刀杆系统因自重变化产生的挠度也不同,在加工较长内孔时,孔的轴线易产生弯曲。
由于主轴不断伸出,整个刀杆系统刚性不断变差,镗削时在切削力作用下,系统弹性变形逐渐增大,影响孔的镗削精度,使被加工孔产生圆柱度误差。
2、试述采用工作台进给悬伸镗削的特点。
这种镗削方式对被加工孔的精度有何影响?用工作台进给悬伸镗削时;由于主轴悬伸长度在切削前已经调定,故切削过中由刀杆系统自重和受切削力引起的挠曲变形及弹性变形相对较为稳定。
因此被加工孔产生的轴线弯曲和圆柱度误差均比用主轴进给悬伸镗削时小。
这种镗削方式影响孔加工精度的主要原因是床身和工作台导轨的直线度误差,以及它们之间的配合精度。
若床身导轨在水平平面和垂直平面内有直线度误差,会使被加工孔的轴线产生直线度误差和对基准表面产生位置误差;若导轨配合精度差,将会使被加工孔产生圆度误差。
3、什么叫支承镗削法?它有哪些特点?支承镗削法是采用架于镗床尾座套筒内的支承镗杆进行镗削的一种切削加工方式。
支承镗削法的特点是:(1)与悬伸镗削法相比,大大增强了镗杆的刚性。
(2)适合同轴孔系的加工。
可配用多种精度较高的镗刀,加工精度高,能确保加工质量。
(3)装夹和调整镗刀较麻烦、费时,不易观察加工情况,试镗、测量等操作没有悬伸镗削法那样直观、方便。
4、试述采用镗杆进给支承镗削法的特点。
这种镗削方式对被加工孔的精度有何影响?采用镗杆进给支承镗削法镗孔,镗杆伸出长度随主轴进给而不断变化,但镗杆和主轴在两支承点之间的距离不变。
镗床的简介
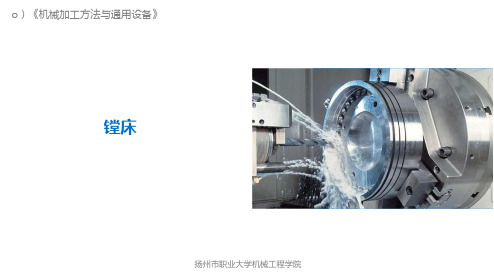
镗床
(1) 结构特点 ___ 0具有坐标位置的精密测量装置; (2) 工艺范围
。加工精密孔(IT5级以上)
和位置精度要求高的孔系(钻模);
。完成样板划线,
孔距及直线尺寸的测量等工作。
1-工作台2-主轴3-主轴箱4-立柱5-渭座6-底座
镗床
双柱坐标镗床
双柱坐标纹底
3 .金刚镇床
卧式金刚镗床
卧式镗床
镗床
2.坐标镗床
因机床上具有坐标位置的精密测量装置而得名。在加工孔时,可按直角坐标来精密
定位,因此坐标镗床是一种高精密机床,主要用于$堂削高精度的孔,尤其适合于相互位 置精度很高的孔系。
其主要零部件的制造和装配 精度都很高,具有良好的刚度和
抗振性,并配备有坐标位置的精 密测量装置,除进行孔系的精密 加工外,还能进行精密刻度、样 板的精密划线、孔间距及直线尺 寸的精密测量等。
o)《机械加工方法与通用设备》
镗床
扬州市职业大学机械工程学院
镗床
知识
1、 镗削加工方法;
亜占
2、 镗床种类。
在镗床上以镗刀的旋转为主运动,工件或镗刀移动作进给运动,对孔进行扩大孔 径及提高质量的方法为镗削加工。
生产中,镗削加工一般用于加工机座、箱体、支架及非回转体等外型复杂的大型 零件上的较大直径孔,尤其是有较高位置精度要求的孔与孔系;对外圆、端面、平面 也可采用镗削进行加工。
镗床
1-支架2-后立柱3-工作台4-径向刀架5-平旋盘6-圍由7-前立柱8-主轴箱 9-后尾筒10-床身11-下滑座12-上滑座13-刀座
镗床
卧式镗床具有以下工作运动: ① 、镗杆和平旋盘的旋转主运动 ② 、镗杆的轴向进给运动; ③ 、主轴箱的垂直进给运动; ④ 、工作台的纵、横向进给运动; ⑤ 、平旋盘径向刀架的进给运动; ⑥ 、辅助运动:主轴箱、工作台在 进 给方向的快速调位运动、后立柱纵 向调 位运动、后支架垂直调位运动、 工作台 的转位运动。这些辅助运动可 以手动, 也可由快速电机传动。
机械制造基础:镗削加工

• 双刃镗刀
•
镗刀块
•
定尺寸
•
可调尺寸
•
组合式
双刃镗刀的镗刀片是浮动的,两个对称的 切削刃产生的切削力,自动平衡其位置。
(1) 加工质量较高 刀片浮动可抵偿偏摆引起不良影响 较宽的修光刃可减少孔壁粗糙度值
(2)生产率较高,两刀刃同时工作,故生产率较 高
• 钻孔、扩孔、铰孔
• 4、工件装夹
• 被加工孔与基准面平行时:用压板,螺栓直接
固定在工作台上。 • 被加工孔与基准面垂直时:用角铁或弯板装夹
。 • 对于有孔系的工件批量生产时:常制作镗模。
• 二、镗削方法
孔径小:用主轴
• 1、单孔镗削:
孔小径大,深度小:用平旋盘
孔
• 2、孔系镗削:
•
孔系:两个以上在空间具有一定相对位置的孔。
(3) 刀具成本较单刃镗刀高 浮动镗刀主要用于批量生产,精加工箱体 零件上直径较大的孔。
镗床的主要加工内容
• (a)镗孔(b)镗较深孔(c)镗同轴孔 • (d)镗大孔(e)镗平行孔(f)镗垂直孔
镗床上加工端面及铣平面和成形面
(a)加工端面
(b)加工内环面
(c)铣平面 •(d)铣成形面
• 镗内螺纹 • • •
镗削加工
认识镗床 镗刀种类 镗削方法
镗削
镗削加工:利用各种镗床对孔进行镗削加工的 加工手段 。镗削是对已有孔进行扩大孔径,并提高表面质量。
镗削运动:镗刀旋转为主运动,工件或镗刀移动为进给 运动。 镗床与钻床比较:镗床可以加工大直径孔,精度较高, 且与孔的轴线的同轴度、垂直度、平行度及孔距精度均 较高。因此镗床特别适合加工箱体、机架等结构复杂, 尺寸较大零件。
镗削加工

图10-4 立 式双柱坐 标镗床 1—工作台 2—横梁 3、 6—立柱 4—顶梁 5—主轴箱
7—主轴 8—床身
(二)立式双柱坐标镗床 立式双柱坐标镗床如图10-4所示,它具有由两侧立柱、顶梁和床身构 成的龙门框架式结构。主轴箱5装在可沿立柱导轨上下调整位置的横 梁2上,工作台1则直接支承在床身8的导轨上。镗孔的坐标位置由主 轴箱沿横梁导轨横向移动和工作台沿床身导轨纵向移动来确定。立式 双柱坐标镗床的主轴箱(装在龙门框架上)其悬伸距离较小,并且工 作台和床身之间层次少,所以,这种坐标镗床刚度较高,承载能力较 强。因此,大、中型坐标镗床常采用这种布局形式。
图10-7 采用镗削加工的箱体
图10-8 机夹式单刃镗刀
a)盲孔镗孔刀 b)通孔镗刀 c)、d)阶梯孔镗刀 二、镗刀的类型及应用 (一) 单刃镗刀 单刃镗刀 它适用于孔的粗、精加工。单刃镗刀的切削效率低,对工人操作技术要 求高。加工小直径孔的镗刀通常作成整体式,加工大直径孔的镗刀可作 成机夹式。图10-8为机夹式单刃镗刀,它的镗杆可长期使用,镗刀头通 常作成正方形或圆形。 镗杆、镗刀头尺寸与镗孔直径的关系见表10-1。
(1)镗杆的旋转主运动; (2)平旋盘的旋转主运动; (3)镗杆的轴向进给运动; (4)主轴箱垂直进给运动; (5)工作台纵向进给运动; (6)工作台横向进给运动; (7)平旋盘径向刀架进给运动; (8)辅助运动:主轴箱、工作台在进给方向上的快速调位 运动、后立柱纵向调位运动、后支架垂直调位运动、工作台 的转位运动。这些辅助运动由快速电机传动。
三 金刚镗床
图10-6是单面卧式金刚镗床 的外形图。机床的主轴箱固 定在床身上,主轴高速旋转 带动镗刀作主运动。工件通 过夹具安装在工作台上,工 作台沿床身导轨作平稳的低 速纵向移动以实现进给运动。 工作台一般为液压驱动,可 实现半自动循环。
镗削加工
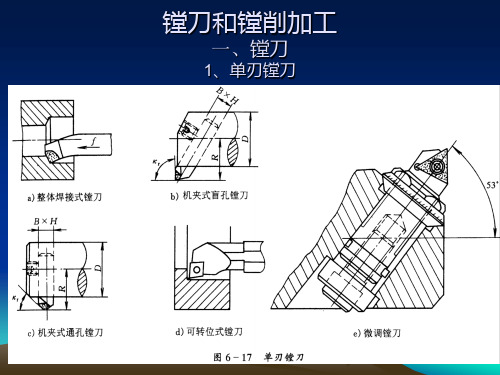
镗刀和镗削加工
一、镗刀
1、单刃镗刀
单刃镗刀 a ) 镗通孔 b)镗盲孔
孔 加 工 刀 具
a
b
单刃镗刀 1 —紧固螺钉 2—精调螺母 3—刀块 4—刀片 5—镗杆 6—导向键
镗 床
单面卧式金刚镗床
镗床夹具
一、镗床夹具的类型 镗床夹具:主要用于加工箱体、支架、支座等 零件上的孔或孔系,保证孔的尺寸精度、几何 形状精度、孔距及位置精度。 组成:夹具体、定位元件、夹紧装置、镗模架 (镗模板)、镗套等组成。
镗套
镗套
导向
导向
支架
镗套的布置方式
1.单支承引导镗夹具
1).特点:
• ②单支承后引导
• 适用于加工D<60的通 孔、盲孔。 • 特点: • 多数情况下,镗杆导向 部分的直径应大于加工 孔直径。
• h=0.5~1D
前后双支承引导镗夹具
• 双支承引导时镗孔的位置精度由镗模保证,不受机床主 轴精度的影响。因此镗杆与机床主轴采用浮动连接。 • 前后双支承镗模一般用于镗削孔径较大、孔的长径比 L/D>1.5的孔或孔系,加工精度较高,但更换刀具不方 便。
前双支承引导镗夹具
镗 床
(2)镗削特点 刀具结构简单,通用性达,可粗加工也可半精加工和精加工,适用批量较 小的加工,镗孔质量取决于机床精度。
(3)运动分析 主运动为镗刀的旋转运动,进给运动为镗刀或工件的移动 。 (4)分类 ①卧式镗床 卧式镗床既要完成粗加工(如粗镗、粗铣、钻孔等),又要进行精加工 (如精镗孔)。因此对镗床的主轴部件的精度、刚度有较高的要求. 卧式镗床的主参数是镗轴直径 。
镗床的加工原理和工艺流程

镗床的加工原理和工艺流程A boring machine, also known as a boring mill, is a machine tool used to increase the size of a hole previously drilled or cast by means of a single-point cutting tool. In Chinese, it is called "镗床", which is widely used in the field of machinery manufacturing.镗床是一种常见的金属加工设备,通常用于扩大已经钻孔或铸造的孔径。
The principle of operation of a boring machine is relatively simple. It involves the use of a rotating cutting tool, known as a boring bar, to enlarge a hole in a workpiece. The workpiece is mounted on a rotating table or clamping device, and the boring bar is fed into the workpiece to remove material and increase the diameter of the hole. From a technical perspective, the boring process relies on the precise coordination of the rotation and feed movement of the boring bar, as well as the selection of appropriate cutting parameters such as speed, feed rate, and depth of cut.镗床的加工原理比较简单,它利用旋转的镗刀对工件中的孔进行扩大。
机械加工镗削工艺
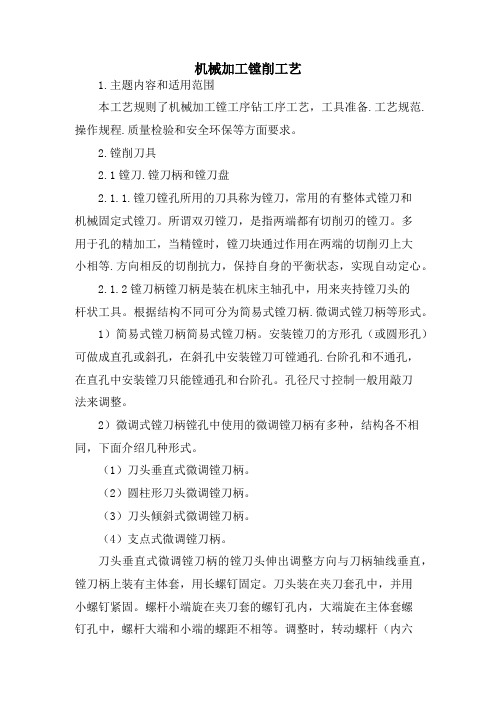
机械加工镗削工艺1.主题内容和适用范围本工艺规则了机械加工镗工序钻工序工艺,工具准备.工艺规范.操作规程.质量检验和安全环保等方面要求。
2.镗削刀具2.1镗刀.镗刀柄和镗刀盘2.1.1.镗刀镗孔所用的刀具称为镗刀,常用的有整体式镗刀和机械固定式镗刀。
所谓双刃镗刀,是指两端都有切削刃的镗刀。
多用于孔的精加工,当精镗时,镗刀块通过作用在两端的切削刃上大小相等.方向相反的切削抗力,保持自身的平衡状态,实现自动定心。
2.1.2镗刀柄镗刀柄是装在机床主轴孔中,用来夹持镗刀头的杆状工具。
根据结构不同可分为简易式镗刀柄.微调式镗刀柄等形式。
1)简易式镗刀柄简易式镗刀柄。
安装镗刀的方形孔(或圆形孔)可做成直孔或斜孔,在斜孔中安装镗刀可镗通孔.台阶孔和不通孔,在直孔中安装镗刀只能镗通孔和台阶孔。
孔径尺寸控制一般用敲刀法来调整。
2)微调式镗刀柄镗孔中使用的微调镗刀柄有多种,结构各不相同,下面介绍几种形式。
(1)刀头垂直式微调镗刀柄。
(2)圆柱形刀头微调镗刀柄。
(3)刀头倾斜式微调镗刀柄。
(4)支点式微调镗刀柄。
刀头垂直式微调镗刀柄的镗刀头伸出调整方向与刀柄轴线垂直,镗刀柄上装有主体套,用长螺钉固定。
刀头装在夹刀套孔中,并用小螺钉紧固。
螺杆小端旋在夹刀套的螺钉孔内,大端旋在主体套螺钉孔中,螺杆大端和小端的螺距不相等。
调整时,转动螺杆(内六角),使夹刀套和镗刀头前后移动,移动最大量等于大端螺距和小端螺距之差。
在螺杆头上刻有刻线,以准确地掌握镗刀头移动尺寸。
调整时,要松开固定刀头的小螺钉圆柱形刀头微调镗刀柄上的镗刀头呈圆柱形,转动微调螺钉,可带动镗刀头沿镗刀柄径向移动。
拧动内六角螺钉传动两个滑块,能夹紧或松开镗刀头。
镗刀柄的斜孔与刀柄轴线成一定角度,它是通过刻度和精密螺纹来进行微调的。
装有可转位镗刀片的镗刀头上有精密螺纹,镗刀头的外圆柱与镗刀柄上的孔相配,并在其后端采用内六角紧固螺钉及垫圈拉紧。
镗刀头的螺纹上旋有带刻度的调整螺母,调整螺母的背部是一个圆锥面,与镗刀柄孔口的内锥面紧贴。
镗削加工基础知识
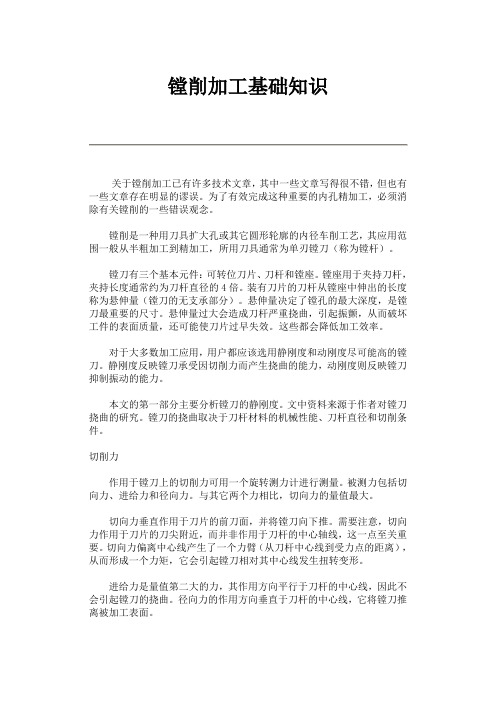
镗削加工基础知识关于镗削加工已有许多技术文章,其中一些文章写得很不错,但也有一些文章存在明显的谬误。
为了有效完成这种重要的内孔精加工,必须消除有关镗削的一些错误观念。
镗削是一种用刀具扩大孔或其它圆形轮廓的内径车削工艺,其应用范围一般从半粗加工到精加工,所用刀具通常为单刃镗刀(称为镗杆)。
镗刀有三个基本元件:可转位刀片、刀杆和镗座。
镗座用于夹持刀杆,夹持长度通常约为刀杆直径的4倍。
装有刀片的刀杆从镗座中伸出的长度称为悬伸量(镗刀的无支承部分)。
悬伸量决定了镗孔的最大深度,是镗刀最重要的尺寸。
悬伸量过大会造成刀杆严重挠曲,引起振颤,从而破坏工件的表面质量,还可能使刀片过早失效。
这些都会降低加工效率。
对于大多数加工应用,用户都应该选用静刚度和动刚度尽可能高的镗刀。
静刚度反映镗刀承受因切削力而产生挠曲的能力,动刚度则反映镗刀抑制振动的能力。
本文的第一部分主要分析镗刀的静刚度。
文中资料来源于作者对镗刀挠曲的研究。
镗刀的挠曲取决于刀杆材料的机械性能、刀杆直径和切削条件。
切削力作用于镗刀上的切削力可用一个旋转测力计进行测量。
被测力包括切向力、进给力和径向力。
与其它两个力相比,切向力的量值最大。
切向力垂直作用于刀片的前刀面,并将镗刀向下推。
需要注意,切向力作用于刀片的刀尖附近,而并非作用于刀杆的中心轴线,这一点至关重要。
切向力偏离中心线产生了一个力臂(从刀杆中心线到受力点的距离),从而形成一个力矩,它会引起镗刀相对其中心线发生扭转变形。
进给力是量值第二大的力,其作用方向平行于刀杆的中心线,因此不会引起镗刀的挠曲。
径向力的作用方向垂直于刀杆的中心线,它将镗刀推离被加工表面。
因此,只有切向力和径向力会使镗刀产生挠曲。
已沿用了几十年的一种经验算法为:进给力和径向力的大小分别约为切向力的25%和50%。
但如今,人们认为这种比例关系并非“最优算法”,因为各切削力之间的关系取决于特定的工件材料及其硬度、切削条件和刀尖圆弧半径。
镗削加工基础知识

镗削加工基础知识关于镗削加工已有许多技术文章,其中一些文章写得很不错,但也有一些文章存在明显的谬误。
为了有效完成这种重要的内孔精加工,必须消除有关镗削的一些错误观念。
镗削是一种用刀具扩大孔或其它圆形轮廓的内径车削工艺,其应用范围一般从半粗加工到精加工,所用刀具通常为单刃镗刀(称为镗杆)。
镗刀有三个基本元件:可转位刀片、刀杆和镗座。
镗座用于夹持刀杆,夹持长度通常约为刀杆直径的4倍。
装有刀片的刀杆从镗座中伸出的长度称为悬伸量(镗刀的无支承部分)。
悬伸量决定了镗孔的最大深度,是镗刀最重要的尺寸。
悬伸量过大会造成刀杆严重挠曲,引起振颤,从而破坏工件的表面质量,还可能使刀片过早失效。
这些都会降低加工效率。
对于大多数加工应用,用户都应该选用静刚度和动刚度尽可能高的镗刀。
静刚度反映镗刀承受因切削力而产生挠曲的能力,动刚度则反映镗刀抑制振动的能力。
本文的第一部分主要分析镗刀的静刚度。
文中资料来源于作者对镗刀挠曲的研究。
镗刀的挠曲取决于刀杆材料的机械性能、刀杆直径和切削条件。
切削力作用于镗刀上的切削力可用一个旋转测力计进行测量。
被测力包括切向力、进给力和径向力。
与其它两个力相比,切向力的量值最大。
切向力垂直作用于刀片的前刀面,并将镗刀向下推。
需要注意,切向力作用于刀片的刀尖附近,而并非作用于刀杆的中心轴线,这一点至关重要。
切向力偏离中心线产生了一个力臂(从刀杆中心线到受力点的距离),从而形成一个力矩,它会引起镗刀相对其中心线发生扭转变形。
进给力是量值第二大的力,其作用方向平行于刀杆的中心线,因此不会引起镗刀的挠曲。
径向力的作用方向垂直于刀杆的中心线,它将镗刀推离被加工表面。
因此,只有切向力和径向力会使镗刀产生挠曲。
已沿用了几十年的一种经验算法为:进给力和径向力的大小分别约为切向力的25%和50%。
但如今,人们认为这种比例关系并非“最优算法”,因为各切削力之间的关系取决于特定的工件材料及其硬度、切削条件和刀尖圆弧半径。
第三章 钻削与镗削工艺与装备
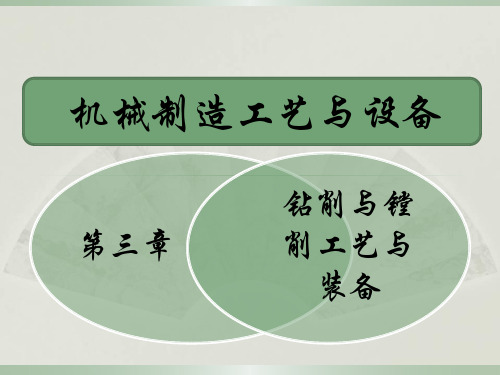
§3- 3 镗削加工工艺装备
2. 卧式铣镗床
镗轴水平布置,并可轴向进给,主轴箱沿前立柱导轨垂 向移动,能进行铣削的镗床称为卧式铣镗床。
1—后支撑架 2—后立柱 3—工作台 4—镗轴 5—平旋盘 6—径向刀具溜板 7—前立柱 8—主轴箱 9—后尾筒 10—床身 11—下滑座 12—上滑座
4. 镗床的加工不仅适用于单件加工、高精度孔的批量加 工,而且还可进行钻孔、扩孔、铰孔,对端面、内螺纹、平 面等进行加工。
机械制造工艺与设备
第三章
钻削与镗 削工艺与
装备
§3-1 钻削加工工艺装备
一、钻削加工方法
钻削加工是在钻床上利用钻孔刀具进行切削的一种方法。 钻削加工时,工件固定不动,刀具随主轴旋转完成主运动,同 时沿轴线移动做进给运动。
§3-1 钻削加工工艺装备
二、钻床
1. 台式钻床
§3-1 钻削加工工艺装备
§3-2 钻削方法
(5)铰尺寸较小的圆锥孔时,可先按小端直径并参照圆柱孔 精铰余量标准留取余量钻出圆柱孔,然后用锥铰刀铰削即可。 对尺寸和深度较大的锥孔,为减小铰削余量,铰孔前可先钻 出阶梯孔,然后再用铰刀铰削。在铰削的最后阶段,要注意 用相配的锥销来试配,以防将孔铰大。试配之前要将铰好的 孔擦洗干净。锥销放进孔内用手按紧时,其头部应高于工件 平面3~5mm,然后用铜锤轻轻敲紧。 (6)对薄壁零件的夹紧力不要过大,以免将孔夹扁,在铰后 产生椭圆形。 (7)铰刀是精加工刀具,要保护好切削刃,避免碰撞,切削 刃上如有毛刺或切屑粘附,可用油石小心地磨去。使用完毕 后要揩擦干净,涂上全损耗系统用油(俗称机油),放置时 要保护好切削刃,以防与硬物碰撞而受损伤。
镗 削 加 工
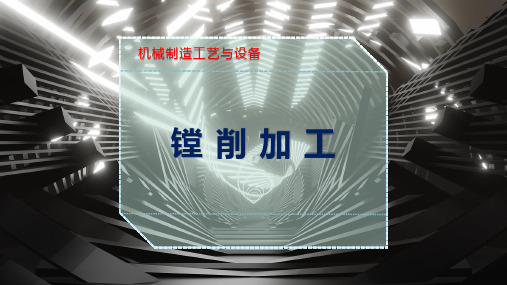
TP619型卧式镗床 1—后立柱; 2—镗杆支承座; 3—床身; 4—下滑座;
5—上滑座; 6—工作台; 7—平旋盘; 8—主轴; 9—主轴箱; 10—主立柱
2.坐标镗床 坐标镗床是指具有精密坐标定位装置的镗床。依靠坐标位
置的精密测量装置能精确地确定工作台、主轴箱等移动部件的 位移量,实现镗刀和工件的精确定位。坐标镗床工艺范围广, 除镗孔、钻孔、扩孔、铰孔及铣削加工外,还能进行精密刻度、 样板的精密划线、孔间距及直线尺寸的精密测量等。其适用于 镗削尺寸、形状、位置精度要求很高的孔系,如精密钻模、镗 模及量具等。
机械制造工艺与设备
镗削加工
镗削加工
镗削加工所用的设备主要是镗床,所用的刀具是镗刀。通常 镗刀的旋转是主运动,镗刀或工件沿孔轴线的移动是进给运动。
镗削加工适合于单件、小批量生产中加工各种大型、复杂工 件上的孔系,这些孔除了要有较高的尺寸精度外,还要有较高的 位置精度,所以生产中常作为大型和箱体零件上孔的半精加工和 精加工工序。
坐标镗床有立式坐标镗床和卧式坐标镗床两大类。立式坐 标镗床主要用于加工轴线与安装基面(底面)垂直的孔系和铣 削顶面,它还有单立柱和双立柱两种形式。卧式坐标镗床主要 用于加工轴线与安装基面平行的孔系和铣削侧面。
1.2 镗刀
1.单刃镗刀 单刃镗刀只有一个切削刃,如图(a)和图(b)所示分别为在
镗床上加工通孔和盲孔用的单刃镗刀。其结构简单,制造方便,粗、 精加工都适用,通用性好,使用范围广,可校正原有孔的轴线歪斜, 但生产率较低,比较适用于单件、小批量生产。单刃镗刀一般均有 尺寸调节装置,可加工直径不同的孔。
单刃镗刀
2.双刃镗刀 双刃镗刀两端都有切
削刃,工作时基本上可消 除径向力对镗杆的影响。 工件的孔径尺寸与精度由 镗刀径向尺寸保证,镗刀 上的两个刀片可径向调整。 调整时,先松开紧固螺钉 5,再旋转调节螺钉3,通 过斜面垫板4将刀齿的径 向尺寸调好后,再拧紧紧 固螺钉5把刀齿固定,如 图所示。
镗床的加工原理和工艺流程

镗床的加工原理和工艺流程下载温馨提示:该文档是我店铺精心编制而成,希望大家下载以后,能够帮助大家解决实际的问题。
文档下载后可定制随意修改,请根据实际需要进行相应的调整和使用,谢谢!并且,本店铺为大家提供各种各样类型的实用资料,如教育随笔、日记赏析、句子摘抄、古诗大全、经典美文、话题作文、工作总结、词语解析、文案摘录、其他资料等等,如想了解不同资料格式和写法,敬请关注!Download tips: This document is carefully compiled by theeditor. I hope that after you download them,they can help yousolve practical problems. The document can be customized andmodified after downloading,please adjust and use it according toactual needs, thank you!In addition, our shop provides you with various types ofpractical materials,such as educational essays, diaryappreciation,sentence excerpts,ancient poems,classicarticles,topic composition,work summary,word parsing,copy excerpts,other materials and so on,want to know different data formats andwriting methods,please pay attention!镗床加工原理镗床是一种用于加工孔径较大的圆柱形、锥形和异形孔的机床。
镗削加工与镗刀_1

6.2.5 镗削加工与镗刀※镗孔:利用镗刀对已有孔(钻孔、铸孔、锻孔)进行再加工的过程。
一、镗床及镗削运动(P124) (一)切削运动 1、主运动⎩⎨⎧)(平旋盘:)(镗 轴:平旋盘镗轴r/min n r/min n2、进给运动(1)镗轴轴向进给:f 镗轴(mm/r ) (2)工作台纵向进给:f 纵向(mm/r ) (3)工作台横向进给:f 横向(mm/r ) (4)主轴箱垂直进给:f 主轴箱(mm/r )(5)平旋盘刀架溜板径向进给:f 径向(mm/r 平旋盘)车端面、车槽、镗削大孔。
镗削大孔(f 径向⇒调节直径d )二、卧式镗床的主要工作(P127) 1、镗孔(a )悬伸式①主运动:镗轴旋转运动:r/min②进给运动:镗轴(镗刀),轴向进给运动,fmm/r※最大挠度:锥孔(椭圆孔)弯曲变形镗杆⇒⇒⇒=3EJFcL Y 3max max ③适宜镗削单侧壁孔,工件转180°,调头,镗另一侧孔。
(b )悬伸式①主运动:镗轴旋转运动 n (r/min ) ②工作台:纵向进给f 纵(mm/r )(c )双刀镗双壁孔①主运动:n (r/min ) ②进给运动:f 纵向(mm/r ) 特点:保证孔与孔的同轴度。
条件:Y max ≤31△x 同轴度(d )平旋盘旋转镗削大孔。
①主运动:n 平旋盘(r/min ) ②进给运动:f 纵向(mm/r )(e)镗床夹具+镗刀(镗杆)+浮动夹头+主轴同轴孔系、平行孔系、垂直孔系(消除主轴干涉)2、镗床的其它工作方式(a)钻孔(b)扩孔(c)铰孔(d)铣平面(e)镗内槽(f)车外圆(g)车端面(h)车内螺纹三、镗削的工艺特点及应用(P128)1、卧式镗床工艺范围加工机座、箱体、支架等大型零件上孔与孔系的加工。
2、加工精度IT8~IT7※表面粗糙度Ra1.6~0.8μm※位置精度(镗模夹具、打表找正)(A )调头镗A 孔与B 孔的同轴度误差(B )垂直孔系A 孔与B 孔的垂直度误差(C )镗模——镗削 平行孔系。
简析平行孔系的镗削方法

简析垂直和平行孔系的镗削方法1.分析镗削与镗削加工镗削是一种用刀具扩大孔或其它圆形轮廓的内径车削工艺,其应用范围一般从半粗加工到精加工,所用刀具通常为单刃镗刀(称为镗杆)。
所谓镗削原则,是指对具体的加工对象(工件的材质、形体、结构)、加工性质(粗镗、半精镗、精镗)等镗削要素提出综合性的判定。
镗削一般在镗床、加工中心和组合机床上进行,主要用于加工箱体、支架和机座等工件上的圆柱孔(见图)、螺纹孔、孔内沟槽和端面;当采用特殊附件时,也可加工内外球面、锥孔等。
对钢铁材料的镗孔精度一般可达IT9~7,表面粗糙度为R a2.5~0.16微米。
镗削时,工件安装在机床工作台或机床夹具上,镗刀装夹在镗杆上(也可与镗杆制成整体),由主轴驱动旋转。
当采用镗模时,镗杆与主轴浮动联接,加工精度取决于镗模的精度;不采用镗模时,镗杆与主轴刚性联接,加工精度取决于机床的精度。
由于镗杆的悬伸距离较大,容易产生振动,选用的切削用量不宜很大。
采用高速钢刀头镗削普通钢材时的切削速度,一般为20~50米/分;采用硬质合金刀头时的切削速度,粗镗可达40~60米/分,精镗可达150米/分以上。
粗镗时,加工余量比较大,此时应先考虑生产效率,后考虑加工精度。
因此,首先应加大切削深度,减少进给次数;其次加大进给量;最后选取与切削深度和进给量相适应的切削速度。
精镗时,主要是为了保证孔的精度和孔的表面粗糙度要求。
为保证表面粗糙度和提高生产效率,应提高切削速度;进给量不宜选取过大。
由于精镗的加工余量往往较小,切削深度受到余量限制,不能任意选取。
镗孔是用镗刀对已有的孔进行扩大加工的方法,是常用的孔加工方法之一。
对于直径较大的孔(D>80mm)、内成形面或孔内环槽等,镗削是唯一适宜的加工方法。
一般镗孔的尺寸公差等级为IT8~IT6,表面粗糙度Ra为1.6μm~0.8 μm;精细镗时,尺寸公差等级可达IT7~IT5,表面粗糙度Ra为0.8μm~0.1 μm。
机械制造技术第8章 镗床和镗削加工

图8.16
同轴孔系的镗削
(2)垂直孔系的镗削
几个轴线互相垂直的孔构成垂直孔系。 垂直孔系的主要技术要求,除各孔自 身的精度要求外,还要保证相关孔的垂直 度。
图8.17
回转法垂直孔系的镗削
(3)相交孔系的镗削
相交孔系的镗削一般采用回转工作 台,由工作台分度来保证所需夹角。 对相交轴线夹角要求较高的工件, 一般需采用镗模来保证。
(3)快速移动
为了提高工效,按动快速电动机按 钮,可将运动传至轴ⅩⅩ,再分配给以 上5个进给运动部件作快速移动。
4.T68型卧式镗床的附件
(1)莫氏锥度接套 (2)不同规格的微调刀杆 (3)平旋盘刀杆及刀杆座 (4)镗大孔用镗削头 (5)可卸式平旋盘
5.镗床的操作与维护保养
(1)镗床的操作
镗工要正确操作镗床,必须对所操作 机床的加工规范,主要机构的功用、性能 及机床的精度有全面的了解。
图8.1 卧式镗床的外形
1.T68型卧式镗床组成
T68型卧式镗床主要由床身、立柱、 主轴箱、平旋盘、进给箱、尾部箱、分配 箱、上下滑座、回转工作台、后立柱等部 件组成。
2.T68型卧式镗床主要技术性能参数
T68型卧式镗床的主要技术性能参数如下。 (1)主轴直径 85mm (2)主轴最大行程 600mm (3)平旋盘径向刀架最大行程 170mm (4)主轴中心线到工作台面距离 30~800mm
5.内沟槽和缺圆零件的镗削
(1)内沟槽的镗削
孔的镗削中,常需要在孔中镗削内沟 槽,常见的几种内沟槽如图8.22所示。 它们主要起安装弹性挡圈等止推零件、 保持垂直相交面的直角过渡以及密封等作 用。
图8.22
内沟槽形式
(2)缺圆零件的镗削
图8.25
第9章_镗削加工

本章要点
概述 镗床 镗削方法
第一节 概述
镗削加工是镗刀的旋转运动为主运动, 与工件随工作台的移动(或镗刀的移 动)为进给运动相配合,切去工件上多 余金属层的一种加工方法
一、镗床的主要加工范围
a) 镗刀镗孔; b)双镗刀镗同轴孔; c)悬伸镗刀 镗大直径孔; d)镗轴装端铣刀铣平面; e)平旋盘 上装车刀车内沟槽; f)平旋盘上装车刀车端面;
T
镗床类
6卧式Biblioteka 1卧式镗床组8
主轴直径25mm
二、镗床的主要部件
工作台 镗轴
平旋盘
主立柱
尾立柱
经向导轨
后支承
主轴箱
上滑座
尾筒
下滑座
床身
第三节 镗削方法
一、工件的安装
1、夹紧力应垂直于主要定位基准面,并尽可能与受 力方向一致。 2、夹紧力应落在支承元件上。 3、夹紧力应落在刚性好的部位。 4、夹紧力应适当可靠,夹紧点应尽可能靠近加工面。
5、夹紧机构应方便、安全、省力。
二、镗刀
1)单刃镗刀
2)镗刀头
3)镗杆
三、镗削方法
a)主轴送进镗孔法 b)工件送进镗孔法 c)用 平旋盘上径向刀架镗平面 d)钻孔 e)工件送进 法镗螺纹 f)用主轴送进镗螺纹
镗削同轴孔系
镗削轴线在同一垂直平面内的平行孔系
镗削垂直孔系
二、镗削加工的特点
1)镗削加工的主运动是镗刀的旋转运动,避免了大型 工件作旋转运动的弊端; 2)适应能力强。镗床的多部件都能进给运动,具有加 工上的多功能性; 3)镗刀杆悬伸较长,切削条件差,易振动。 ——适用于批量生产的零件加工及箱体、机架等结构复 杂、尺寸较大的工件。
第二节 镗床
一、镗床的型号
数控机床镗削加工技巧分享

数控机床镗削加工技巧分享数控机床镗削加工是现代制造业中的一种非常重要的加工方式。
与传统的手动和半自动加工相比,数控机床镗削具有高效性、精度高、可靠性强等优点。
本文将分享一些数控机床镗削加工的技巧,希望对读者在实际应用中有所帮助。
首先,正确选择刀具是数控机床镗削加工的关键。
刀具的选择应根据工件的材质、形状和加工要求来确定。
常用的刀具材料有硬质合金、高速钢和陶瓷等,而刀具的设计要根据具体的加工要求来确定。
在选择刀具时,应注意刀具的强度、刚性和耐磨性等因素,并且要根据工件的尺寸和形状来选择合适的刀具长度。
其次,合理设置加工参数也是数控机床镗削加工的重要一环。
加工参数的设置直接影响到加工效果和加工质量。
在设置切削速度时,应根据工件材料和刀具材料来确定,通常可以通过试切试验来确定最佳的切削速度。
切削进给量的选择要根据切削力的大小和刀具的刃长来确定,切削过大容易导致切削力过大,从而影响加工质量。
此外,还要注意切削液的选择和使用,切削液可以有效降低切削温度、延长刀具寿命和提高加工质量。
另外,精确测量工件尺寸是数控机床镗削加工中不可或缺的一步。
在加工结束后,应通过合适的测量工具来测量工件的尺寸,并与设计尺寸进行对比。
常用的测量工具有千分尺、千分表和高度规等。
同时,在测量过程中要注意保持测量工具的准确度和稳定性,并进行合理的修整和调整。
此外,刀具磨损的检查和更换也是数控机床镗削加工中的重要环节。
刀具的磨损会直接影响加工精度和加工质量,因此应定期检查刀具的磨损情况,并及时更换。
通常可以通过目测和测量刀具的刃口长度等来判断刀具的磨损情况。
一旦发现刀具磨损严重,应立即更换刀具,以保证加工质量。
最后,合理设计夹具和工装也是数控机床镗削加工中的重要一环。
夹具和工装的设计直接影响到工件的稳定性和加工精度。
在设计夹具和工装时,应考虑工件的形状、尺寸和加工要求,并确保夹具和工装能够牢固地夹紧工件,同时又不会对工件造成损坏。
此外,还要注意夹具和工装的刚性和稳定性,避免在加工过程中产生振动和变形。
三爪镗削步骤及注意事项(精)

卡爪调整注意事项
•
• •
二、粗调尺寸到大致位置后,拧紧螺钉;
调整尺寸时,一定要注意卡爪的顺序及安装位置。卡爪及卡盘上都编有顺序号,注意顺序号不要弄
错了,否则安装后的径向跳动肯定会变大。
卡爪夹紧端要正确。每个卡爪都有两头,根据加工工件的不同,两头都会使用。对于特殊卡爪或新 卡爪,我们还比较容易辨认;如果是多次使用的卡爪,特别是夹持直径比较相近时不容易辨认。此 时需要我们特别细心,或在卡爪上做记号识别。如果卡爪装反了,那么径向跳动和轴向跳动都会有 很大的变化。 • 每个卡爪装在卡盘上的位置也要正确。我们一般采用的方法时数齿数。卡爪与卡盘连接时,由于受 到工件直径及卡爪镗削次数的影响,都会存在错齿的情况。我们只需要保证每个卡爪伸出或缩进去 的齿数相等,即可保证卡爪正确安装。如果中间有一个卡爪与其它两个卡爪错开了一个齿,那么径 向的跳动会非常大。
•
•
•
卡爪调整注意事项
•
•
4、去除定位及夹紧部位的毛刺:
卡爪镗削之后,在卡爪边沿会产生毛刺。毛刺必须要清除干净,否则会将工件表面夹伤。
•
•
毛刺去除后,最好用细砂纸将夹紧和定位面Байду номын сангаас磨一遍,可提高夹持面的粗糙度。
卡爪夹持部位的边沿可倒角或修整成R圆弧面,减少对工件夹持部位的伤害。
卡爪调整注意事项
•
• •
3、精镗卡爪定位部分,包括夹紧孔或外圆、定位面等:
如果卡爪的径向和轴向跳动达不到要求时,我们就要镗卡爪。 镗卡爪时,我们必须让卡盘处于一个正确的夹紧位置。例如:卡爪夹持工件外圆时,我们要在卡爪内端夹 持一个垫片;卡爪反撑工件内孔时,我们要卡爪外端加一个圆环。这样可以消除卡爪传动部分的间隙,保 证工件正确夹紧。 镗卡爪时,尺寸要控制到一个比较合理的范围。一般来说,夹持工件外圆时,孔径要小于工件外圆0.10.5mm;反撑内孔时,外径要大于工件内孔0.1-0.5mm。这样可以保证卡爪与工件一直处于六处接触状态 ,接触面积较小,摩擦力相应增大,夹持相当稳定。工件外圆或内孔越小,镗削尺寸与工件夹持部位尺寸 的差异就越小,反之可以相应增大。但差异过大,卡爪与工件完全处于线接触状态,反而会将工件表面夹 伤。如果卡爪镗削尺寸刚好与工件夹持部位尺寸相等,接触面处于一个最大状态,摩擦力减小,大余量加 工时,工件会转动;如果卡爪内孔大于工件外圆或外径小于工件内孔,卡爪和工件只有三处接触,不仅工 件夹持部位会变形,而且摩擦力会减小,大余量加工时会导致工件转动。 卡爪镗削为严重断续加工,因此刀具尽量不选用精加工槽型,采用较耐冲击的半精加工槽型,而且转速不 要过高。轴向尺寸到位后,要对转角清根或口部倒角,使工件能正确定位。如果工件定位和夹持部位有台 阶,应躲开非定位及夹紧处,使工件能正确定位和夹紧。 镗卡爪时,径向和轴向尺寸可用机床显示的相对坐标值控制。例如:控制轴向尺寸时,使刀具轴向尺寸与 卡爪端面处于同一位置位置后,将相对坐标值中的轴向坐标值清零,即可控制镗削时的轴向尺寸。径向尺 寸的控制和轴向尺寸的控制相似。
- 1、下载文档前请自行甄别文档内容的完整性,平台不提供额外的编辑、内容补充、找答案等附加服务。
- 2、"仅部分预览"的文档,不可在线预览部分如存在完整性等问题,可反馈申请退款(可完整预览的文档不适用该条件!)。
- 3、如文档侵犯您的权益,请联系客服反馈,我们会尽快为您处理(人工客服工作时间:9:00-18:30)。
镗削的基本加工方法newmaker1、什么叫悬伸镗削法?它有哪些特点?答:使用悬伸的单镗刀杆,对中等孔径和不穿通的同轴孔进行镗削加工,这种加工方法叫悬伸镗削法。
悬伸镗削法的主要特点有:(1)由于悬伸镗削所使用的镗刀杆一般均较短、粗,刚性较好,切削速度的选择可高于支承镗刀杆,故生产效率高。
(2)在悬伸镗刀杆上装夹、调整刀具方便,在加工中又便于观察和测量,能节省辅助时间。
(3)用悬伸镗削法采用主轴送进切削时,由于镗刀杆随主轴送进而不断悬伸,刀杆系统因自重变化产生的挠度也不同,在加工较长内孔时,孔的轴线易产生弯曲。
由于主轴不断伸出,整个刀杆系统刚性不断变差,镗削时在切削力作用下,系统弹性变形逐渐增大,影响孔的镗削精度,使被加工孔产生圆柱度误差。
2、试述采用工作台进给悬伸镗削的特点。
这种镗削方式对被加工孔的精度有何影响?答:用工作台进给悬伸镗削时;由于主轴悬伸长度在切削前已经调定,故切削过程中由刀杆系统自重和受切削力引起的挠曲变形及弹性变形相对较为稳定。
因此被加工孔产生的轴线弯曲和圆柱度误差均比用主轴进给悬伸镗削时小。
这种镗削方式影响孔加工精度的主要原因是床身和工作台导轨的直线度误差,以及它们之间的配合精度。
若床身导轨在水平平面和垂直平面内有直线度误差,会使被加工孔的轴线产生直线度误差和对基准表面产生位置误差;若导轨配合精度差,将会使被加工孔产生圆度误差。
3、什么叫支承镗削法?它有哪些特点?答:支承镗削法是采用架于镗床尾座套筒内的支承镗杆进行镗削的一种切削加工方式。
支承镗削法的特点是:(1)与悬伸镗削法相比,大大增强了镗杆的刚性。
(2)适合同轴孔系的加工。
可配用多种精度较高的镗刀,加工精度高,能确保加工质量。
(3)装夹和调整镗刀较麻烦、费时,不易观察加工情况,试镗、测量等操作没有悬伸镗削法那样直观、方便。
4、试述采用镗杆进给支承镗削法的特点。
这种镗削方式对被加工孔的精度有何影响?答:采用镗杆进给支承镗削法镗孔,镗杆伸出长度随主轴进给而不断变化,但镗杆和主轴在两支承点之间的距离不变。
而且与工作台进给支承镗孔方式相比,其两支承点之间的距离较短。
因此,由切削力所产生的镗杆挠曲变形比工作台进给支承镗孔方式小,所以抗振性好,可以采用宽刀加工。
但是,由于是镗杆进给,故镗刀在支承间的位置是变化的,因而镗杆自重造成的弯曲就会影响工件孔轴线的直线度误差。
5、试述采用工作台进给支承镗削法的特点。
这种镗削方式对被加工孔的精度有何影响?答:这种镗削方式,由于采用工作台进给,所以镗杆两支承间的距离很长,一般要超过孔长的2倍。
镗杆受力后产生的挠曲变形量相对要大。
用这种方法镗孔,由于刀具调整后,其到镗杆两端支承间的距离不变,因此,孔径尺寸只均匀减小一个定值。
孔的直线度误差主要与机床导轨的直线度及机床导轨和工作台导轨间的配合精度有关。
被镗孔的直线度误差较小。
6、试述用单头镗刀镗孔的主要优缺点。
使用单头镗刀镗孔时,应如何正确选择切削用量?答:用单头镗刀镗孔有如下主要优缺点:(1)加工工艺性广,能加工扩孔钻、铰刀所不能加工的孔,如不通孔、阶梯孔、交叉孔等。
(2)可以纠正由于钻孔、扩孔而留存的各种偏差。
加工精度高,表面粗糙度较细,并能保证孔的形状和位置精度。
(3)使用硬质合金刀片,能够进行高速切削,生产效率高。
(4)主要缺点是调整刀具和对刀时间较多,影响生产效率的提高。
在用单头镗刀镗孔时,切削深度和进给量不宜过小,如果两者过小,容易使刀头磨损,从而使被镗孔的尺寸精度和表面粗糙度达不到要求。
7、用浮动镗刀精镗孔前,被镗孔必须满足哪些基本技术要求?答:用浮动镗刀精镗孔前,被镗孔必须满足以下基本技术要求:(1)孔的直线度要好,表面粗糙度值控制在Rα3.2μm并且要求孔壁上不允许有明显的走刀波纹。
(2)精镗余量不能太大,一般控制在0.06~0.12mm之内。
8、为保证用浮动镗刀精镗孔时的加工精度,应如何正确选择切削用量?答:浮动镗刀精镗孔时的切削深度,一般为0.05~0.10mm;进给量一般为0.3~0.7mm/r;镗削速度v可换算成主轴每分钟转速,一般取8~12r/min。
9、在镗床上加工零件时,常用哪几种定位方法?各有什么特点?答:在镗床上加工零件时,常用下述四种定位方法:(1)划线找正定位其特点是不需专用夹具及镗模;由于增加了划线工序,生产效率低;定位精度低。
(2)利用定位元件定位其特点是简单、可靠;不需成套工艺装备;定位误差较小;成本较低。
(3)利用夹具定位其特点是工件定位迅速,夹紧可靠,加工方便。
但镗床夹具制造周期较长,成本高。
(4)利用其他形式定位如利用千斤顶加特形垫块、利用工件上的工艺搭子定位等。
这些方法,定位精度较低,生产效率不高。
10、加工孔系时,找正镗床主轴起始坐标位置的常用方法有哪几种?各有何特点?答:加工孔系时,找正镗床主轴起始坐标位置常用的方法有:(1)利用百分表测量装置找正定位这种方法,必须先用百分表定心器或定位心轴,将工件上的基准孔坐标定出来,然后根据基准孔坐标,定出主轴的坐标位置。
其特点是精度较高,操作较方便。
(2)利用检验棒找正定位此种方法的特点是找正定位精度低,找正费时。
但这种定位方法可直接找正镗床主轴与起始孔的坐标位置。
(3)利用孔的分界面拢正定位这种方法的特点是可用于分离式箱体孔系的镗削加工。
缺点是辅助时间较长。
(4)利用样板找正定位此种方法的特点是样板结构简单,无需复杂的调整。
但样板易变形,而且当工件需要加工几个不同面上的孔系时,需要几块样板,找正和定位精度也较低。
(end)镗床的铣削加工newmaker1、一般哪些零件在镗床上进行铣削加工?常用方法有哪些?答:以下零件常在镗床上进行铣削加工:(1)孔和其他相关部分的加工精度要求较高,两次装夹易产生装夹误差的零件。
(2)不易装卸的大型笨重零件。
(3)结构形状复杂,加工工序多,且又是单件或小批量生产,有时还受到设备条件的限制,没有更合理的加工设备的零件。
常用的方法有:(1)利用平旋盘进行铣削。
(2)在镗床主轴上装铣刀进行铣削。
(3)借助回转工作台和镗床附件来进行铣削。
2、在镗床上利用平旋盘装刀进行铣削,有哪两种不同的进给方式?试比较其加工特点。
答:一种方式是将平旋盘上的径向刀架固定,单刃弯头镗铣刀装在径向刀架的刀杆上,由工作台或主轴箱作进给。
这种方法适宜于铣削大端面。
铣削过程中,由于切削刃的线速度没有变化,加工面的表面粗糙度比较一致。
但由于刀盘直径较大,刚性较差,又是单刃刀断续切削,易产生较大的振动,使加工面的表面粗糙度变粗。
另一种方式是由平旋盘转动,盘上的径向刀架作径向进给。
这种方法适宜于加工中小尺寸的表面,铣削时振动较小。
但随着刀架的径向运动,刀具的线速度在不断变化,使得在同一个加工面内的表面粗糙度值变化较大。
3、用平旋盘装刀铣削较大平面时,加工后的表面出现中凹或中凸现象的主要原因是什么?答:用平旋盘装刀,径向刀架进给铣削较大的平面时,径向刀架进给运动的方向可以从里向外,也可以从外向里,随着刀架的径向进给运动,刀具的线速度在不断地变化。
如果刀架从外向里铣削,铣削外圈时,刀具线速度大,易磨损,加工出来的平面容易发生中凸现象,反之易产生中凹观象。
(end)钻孔、铰孔和镗孔newmaker1、在铣床上钻出的孔,产生位置不准的主要原因是什么?怎样预防?答:造成孔位置不准的主要原因有:(1)划线不准和样冲眼未打准。
(2)钻头横刃太长使定心不稳或开始钻时工件有移动。
(3)调整孔距时移动尺寸不准。
预防措施是:应提高划线、打样冲眼和钻孔时的对中精度,正确调正机床移距的坐标尺寸,合理修磨钻头横刃。
2、在铣床上钻出的孔,产生偏斜的主要原因是什么?如何预防?答:在铣床上钻出的孔产生偏斜的主要原因有:(1)钻头两主切削刃不对称。
(2)进给量太大而使钻头弯曲。
(3)工件端面与钻头轴线不垂直。
(4)在圆柱面上钻孔时,钻头中心未通过工件轴线。
预防措施是:正确修磨钻头,合理选择切削用量;工件不平整端面应在钻孔前加工平整或在端面预钻一个引导凹坑;在圆柱面上钻孔时,应仔细调整,使钻头中心通过工件轴线,并用中心钻预钻引导凹坑。
3、铰孔能否提高孔的位置精度?铰孔余量太大或太小各有何弊病?答:由于铰削余量较小,而铰刀在装夹后的刚性又差,加之铰刀又用切削刃的导向部分以铰削前的孔加工表面导向定位,均匀地切去余量,因此铰孔不能提高孔的位置精度。
铰孔时余量太小,往往不能把上道工序所留下的加工痕迹全部铰去;余量太大,会使孔的铰削精度降低,表面粗糙度变粗,同时会使铰刀寿命降低。
4、在铣床上镗孔,孔的尺寸公差、表面粗糙度及孔距精度分别可达多少?答:在铣床上镗孔,孔的尺寸公差一般可达IT7~IT8;表面粗糙度值可达Ra0.33~0.8μm;孔距精度一般可控制在0.05mm左右。
5、若铣床主轴轴线与工作台台面不垂直,对镗孔质量有何影响?在立铣上镗好孔后退刀时,为什么要使刀尖指向操作者?答:若铣床主轴轴线与工作台台面不垂直,镗出的孔会产生歪斜或成椭圆。
在立铣上镗好孔后退刀时,应使刀尖指向操作者,即与床身反向。
这样在退刀时,可以利用工作台下降时的外倾,而不致使刀尖在孔壁上拉出刀痕,影响孔的表面质量。
6、在铣床上镗削单孔时,调整镗孔位置的方法有哪几种?试述用碰镗杆法调整的步骤。
答:在铣床上镗削单孔时,调整镗孔位置的方法有以下四种:(1)按划线调整。
(2)用碰镗杆法调整。
(3)用测量法调整。
(4)用试镗和测量相结合调整。
用碰镗杆法调整的步骤是,先在镗杆和被镗孔的设计或定位基准侧面放一量块,然后将镗杆与量块接触,以用手能轻轻推动量块而将手松开后量块又不至下落为宜。
然后计算被测方向应调整的距离。
其值应为基准侧面到孔中心的尺寸加上量块厚度尺寸和镗杆半径。
7、在铣床上镗孔时,造成孔径尺寸不准和表面粗糙度太租的主要原因是什么?答:在铣床上镗孔时,造成孔径尺寸不准的主要原因是:(1)镗刀回转半径调整不当。
(2)测量不准。
(3)在加工一批工件时刀尖磨损过多。
(4)刀尖切削刃用钝后,切削时产生弹性偏让等。
造成表面粗糙度太粗的主要原因有:(1)机床工作台或立铣头调整后未锁紧。
(2)刀杆刚性差,切削时产生振动。
(3)副偏角太大及进给量过大,致使切削后残留面积大。
(4)镗刀变钝,切削时引起振动。
(5)冷却不佳,出屑不畅。
(6)退刀时刀尖背向操作者,使孔壁产生划痕。
8、在铣床上镗孔时,产生孔的形状误差的主要原因。
答:造成孔的形状误差的主要原因有:(1)主轴旋转精度差。
(2)工件或工作台在镗削过程中有晃动。
(3)镗刀杆和镗刀产生弹性变形。
(4)薄壁零件在装夹时产生变形。
(5)立铣头零位不准,并用升降进给。
(6)镗削过程中刀尖磨损和镗刀未紧固等。
(end)在压路机等施工机械中,有一些类型的锥孔类零件(见图1),其锥孔的孔径大且较深,若在卧式镗床上对其进行加工,则零件的加工精度和加工效率都难以得到保证,将严重影响部件的装配质量。