影响纸板粘合的因素有哪些
纸板粘合不牢,出现品质不佳现象的原因

书山有路勤为径;学海无涯苦作舟
纸板粘合不牢,出现品质不佳现象的原因
随着客户对纸箱品质要求的不断提高及用料变化,如果用进口防潮(水)牛卡、高强低克重瓦楞原纸、高车速等因素,生产出口、高档纸箱大都会出现粘合不牢、入库周转脱胶、边缘翘曲等,致使报废增加、影响效益,极大地制约企业的正常运作。
出现上述现象因素甚多
A.高车速使粘合剂在纸张表面停留时间缩短,高强度、低克重纸张的紧密度影响粘合剂的浸润性。
这里就带来二个问题:
1.如果粘合剂粘度太低,浸润性将有所改善,但起粘合作用的淀粉颗粒就少了,并使起糊化作用的载体水转入纸张中,使糊化不彻底,粘合不牢。
2.粘度太高,又会使在高车速下涂胶不匀,过多的糊液吸收热能,使糊液迟缓糊化,出现在出烘道后仍未烘干,大量的水份在堆砌中无法溢出,在冷却时返回纸板,使纸板变软、变形、空鼓脱胶。
A.提高烘缸温度又会使瓦楞与面纸、底纸还未粘合就已糊化、干燥,出现结晶,粘合不牢。
B.增加硼砂及烧碱用量又带来增加成本,纸板在周转及使用中将加大
专注下一代成长,为了孩子。
瓦楞纸板脱胶原因及改善措施(一)
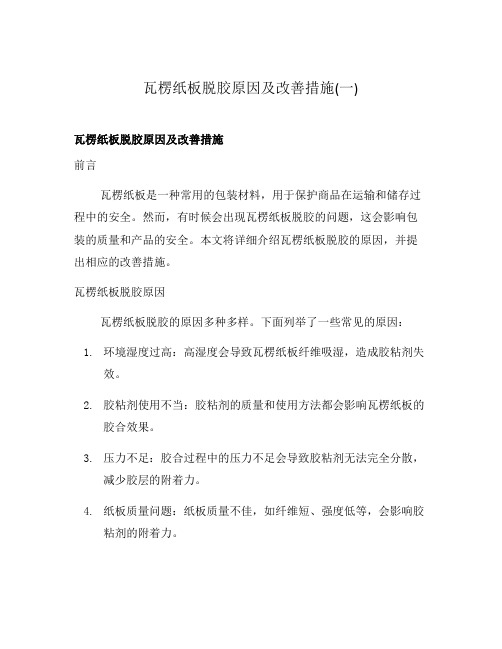
瓦楞纸板脱胶原因及改善措施(一)瓦楞纸板脱胶原因及改善措施前言瓦楞纸板是一种常用的包装材料,用于保护商品在运输和储存过程中的安全。
然而,有时候会出现瓦楞纸板脱胶的问题,这会影响包装的质量和产品的安全。
本文将详细介绍瓦楞纸板脱胶的原因,并提出相应的改善措施。
瓦楞纸板脱胶原因瓦楞纸板脱胶的原因多种多样。
下面列举了一些常见的原因:1.环境湿度过高:高湿度会导致瓦楞纸板纤维吸湿,造成胶粘剂失效。
2.胶粘剂使用不当:胶粘剂的质量和使用方法都会影响瓦楞纸板的胶合效果。
3.压力不足:胶合过程中的压力不足会导致胶粘剂无法完全分散,减少胶层的附着力。
4.纸板质量问题:纸板质量不佳,如纤维短、强度低等,会影响胶粘剂的附着力。
5.操作不当:胶粘剂施加不均匀、操作过程中的温度控制不当等,都会影响瓦楞纸板的胶合效果。
改善措施针对瓦楞纸板脱胶的原因,我们可以采取以下改善措施:1. 控制环境湿度•在生产车间中使用空调设备,保持温度和湿度在适宜范围内。
•安装湿度调节装置,及时调整湿度,确保在正常工作范围内。
2. 优化胶粘剂选择和使用方法•选用质量可靠的胶粘剂,并按照厂家建议的使用方法使用。
•加强对胶粘剂施加过程的监控和管理,确保胶粘剂的合理用量和均匀分布。
3. 提高胶合压力•针对胶粘剂的特性和纸板的厚度,调整瓦楞纸板生产设备中的压力参数,确保胶粘剂能够完全分散。
4. 选用优质纸板•选择纤维长、强度高的纸板材料,提高瓦楞纸板的质量。
•定期检查纸板供应商的资质和质量控制体系,确保所采购的纸板符合要求。
5. 加强操作培训与控制•对操作人员进行胶粘剂使用和设备操作的培训,提高其技能水平。
•建立操作规范和质量控制程序,确保每个环节都符合要求。
•定期检查和维护瓦楞纸板生产设备,确保其正常运行。
总结瓦楞纸板脱胶是一个影响包装质量的重要问题,但通过控制环境湿度,优化胶粘剂的选择和使用方法,提高胶合压力,选用优质纸板,并加强操作培训与控制,我们可以有效地解决这个问题。
浅析:造成瓦楞纸假粘的两大因素

本文摘自再生资源回收-变宝网()浅析:造成瓦楞纸假粘的两大因素纸板粘合强度是瓦楞纸板品质检测的重要一项。
在生产过程有一种情况是,生产出来的纸板从外表看是好的,但是纸板折叠或挤压时,会发出清脆的声音,而面纸与瓦纸粘合处就出现分离状态,行业里基本上把这种情况统称为假粘。
在瓦机生产过程中,经常遇到纸板假粘的情况。
许多人认为是粘合不好,是上胶量少了,没有粘住。
其实不然,这只是一个方面。
上胶量太少当然会粘不好,但绝大多数却不是这方面的原因,还需要从以下两个方面查找原因。
1、温度当纸板出现假粘的时候,我们拨开纸板会发现,瓦楞上和面纸上有胶水的印迹,但就是没有贴合好。
这样的情况多发生在双面机上。
当温度过高时,瓦楞上糊后进入热板,由于纸张温度和热板入口温度过高,引起糊提前糊化,粘合后糊的粘性就不足,从而导致出现假粘现象。
根据纸板楞型及材质不同,可以适当降低热板温度及单瓦进纸温度,让糊在进入热板后开始糊化,这样就能达到更好的粘合效果。
2、高克重材质当用高克重纸生产纸板的时候,如使用低克重的纸张生产工艺,那么纸板粘合就会出现假粘现象。
高克重的面纸其密度高或性能好,在一定的厚度中含有更多的纤维,其传热性能也比一般传统面纸要差,糊很难渗透到纸张纤维中,从而引起纸板假粘。
可以通过增加淀粉固含量及调高热板和进纸温度,提高热能的传递加以解决。
编后语:其实,瓦楞纸板面纸假粘并没有想象中的那么难解决。
纸板粘合好坏,要看糊的工艺与温度的配合如何。
做不同的产品调整不同的配方,只有在变化中进行实时监测和调控,才能保证纸板的品质。
本文摘自变宝网-废金属_废塑料_废纸_废品回收_再生资源B2B交易平台网站;变宝网官网:/?qxb买卖废品废料,再生料就上变宝网,什么废料都有!。
瓦楞纸板搓板状现象及粘合不良的原因
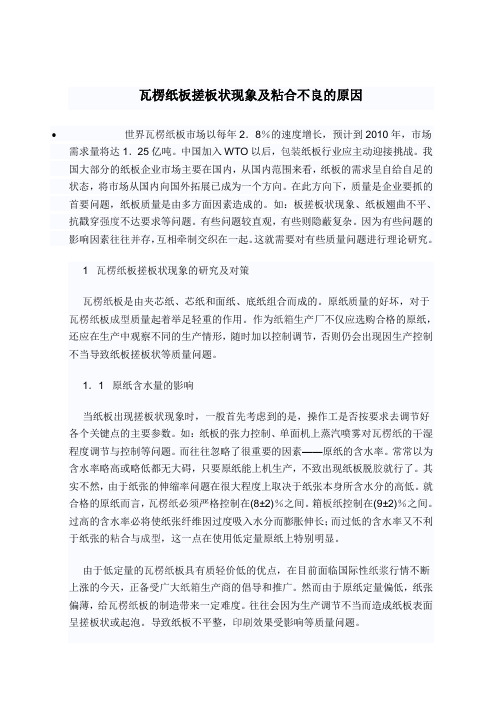
瓦楞纸板搓板状现象及粘合不良的原因世界瓦楞纸板市场以每年2.8%的速度增长,预计到2010年,市场需求量将达1.25亿吨。
中国加入WTO以后,包装纸板行业应主动迎接挑战。
我国大部分的纸板企业市场主要在国内,从国内范围来看,纸板的需求呈自给自足的状态,将市场从国内向国外拓展已成为一个方向。
在此方向下,质量是企业要抓的首要问题,纸板质量是由多方面因素造成的。
如:板搓板状现象、纸板翘曲不平、抗戳穿强度不达要求等问题。
有些问题较直观,有些则隐蔽复杂。
因为有些问题的影响因素往往并存,互相牵制交织在一起。
这就需要对有些质量问题进行理论研究。
1 瓦楞纸板搓板状现象的研究及对策瓦楞纸板是由夹芯纸、芯纸和面纸、底纸组合而成的。
原纸质量的好坏,对于瓦楞纸板成型质量起着举足轻重的作用。
作为纸箱生产厂不仅应选购合格的原纸,还应在生产中观察不同的生产情形,随时加以控制调节,否则仍会出现因生产控制不当导致纸板搓板状等质量问题。
1.1 原纸含水量的影响当纸板出现搓板状现象时,一般首先考虑到的是,操作工是否按要求去调节好各个关键点的主要参数。
如:纸板的张力控制、单面机上蒸汽喷雾对瓦楞纸的干湿程度调节与控制等问题。
而往往忽略了很重要的因素——原纸的含水率。
常常以为含水率略高或略低都无大碍,只要原纸能上机生产,不致出现纸板脱胶就行了。
其实不然,由于纸张的伸缩率问题在很大程度上取决于纸张本身所含水分的高低。
就合格的原纸而言,瓦楞纸必须严格控制在(8±2)%之间。
箱板纸控制在(9±2)%之间。
过高的含水率必将使纸张纤维因过度吸入水分而膨胀伸长;而过低的含水率又不利于纸张的粘合与成型,这一点在使用低定量原纸上特别明显。
由于低定量的瓦楞纸板具有质轻价低的优点,在目前面临国际性纸浆行情不断上涨的今天,正备受广大纸箱生产商的倡导和推广。
然而由于原纸定量偏低,纸张偏薄,给瓦楞纸板的制造带来一定难度。
往往会因为生产调节不当而造成纸板表面呈搓板状或起泡。
影响瓦楞纸箱的黏合度原因有哪些?
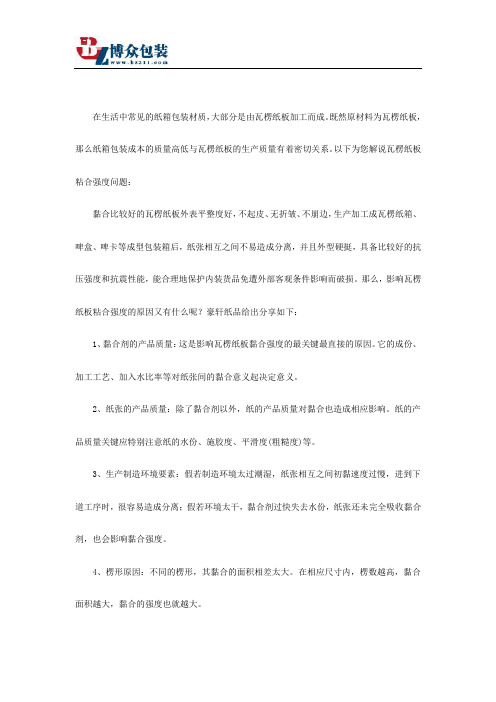
在生活中常见的纸箱包装材质,大部分是由瓦楞纸板加工而成。
既然原材料为瓦楞纸板,那么纸箱包装成本的质量高低与瓦楞纸板的生产质量有着密切关系。
以下为您解说瓦楞纸板粘合强度问题:黏合比较好的瓦楞纸板外表平整度好,不起皮、无折皱、不崩边,生产加工成瓦楞纸箱、啤盒、啤卡等成型包装箱后,纸张相互之间不易造成分离,并且外型硬挺,具备比较好的抗压强度和抗震性能,能合理地保护内装货品免遭外部客观条件影响而破损。
那么,影响瓦楞纸板粘合强度的原因又有什么呢?豪轩纸品给出分享如下:1、黏合剂的产品质量:这是影响瓦楞纸板黏合强度的最关键最直接的原因。
它的成份、加工工艺、加入水比率等对纸张间的黏合意义起决定意义。
2、纸张的产品质量:除了黏合剂以外,纸的产品质量对黏合也造成相应影响。
纸的产品质量关键应特别注意纸的水份、施胶度、平滑度(粗糙度)等。
3、生产制造环境要素:假若制造环境太过潮湿,纸张相互之间初黏速度过慢,进到下道工序时,很容易造成分离;假若环境太干,黏合剂过快失去水份,纸张还未完全吸收黏合剂,也会影响黏合强度。
4、楞形原因:不同的楞形,其黏合的面积相差太大。
在相应尺寸内,楞数越高,黏合面积越大,黏合的强度也就越大。
纸箱厂:5、人为因素:生产制造中粘合剂的摄入量和粘合剂的配制比率还有机器设备的调节等多方面都是依据当场职工常年的的工作经验进行调节的,因此在相同的条件下,不同的操作者所生产制造出的瓦楞纸板的产品质量也会存在差异。
总得来说,在瓦楞纸板的加工过程中,影响瓦楞纸板生产制造产品质量的原因有很多,而在影响瓦楞纸板的粘合强度的很多原因中,粘合剂的配制还有剂量等多方面的管控是处理问题的关键。
因此,各企业能够运用本企业的实际情况熟练掌握,以达到提升企业效益的目的。
文章来源:保定纸箱厂—博众包装来源地址:/content/?181.html。
瓦楞纸板粘合强度的控制

况如 何 无 疑将 直 接 影 响纸 箱产 品 的加 工质 量 。 笔者
认 为 ,粘 合 剂 的 控 制 要 点 , 主 要 是 要 做 好 采 购 控 制 、 检 验 控 制 和 正 确 的 使 用 。 采 购 控 制 就 是 要 选 择 好 的 供 应 商 , 选 择 适 合 生 产 特 点 的 粘 合 剂 品 种 ,这 是 用
果 ; 覆 面 机 辊 隙 调 整 过 大 ,也 容 易 影 响 纸 板 的 粘 合 强 度 : 单 面 机 瓦 辊 不 平 衡 , 也 会 影 响 纸 板 的 粘 合 强
3 6
玉 米 淀 粉 应 该 是 色 泽 洁 白 、 无 异 味 、 无 杂 质 、 含 水 率 ≤ 1 % ,酸 度 ≤2 % ,灰 份 ≤O2 ,细 度 为 ≥9 % 4 0 .% 8
1 影 响 瓦楞 纸 板 粘 合 强 度 的 因素 分 析
在 实 际 生 产 过 程 中 , 影 响 瓦 楞 纸 板 粘 合 强 度 的
2
要 注 重 对 粘 合 剂 的 质 量 控 制
粘 合 剂 是 瓦 楞 纸 板 粘 合 的 重 要 材 料 ,其 质 量 状
因素有很 多 ,粘合 剂 的质量 特 性 、原纸 的质 量特 性 、
强 度 不合 格 时 ,瓦楞 纸板 的边 压 强度 和 纸 箱 的抗 压
度 ; 瓦 楞 辊 、 导 纸 片 出 现 磨 损 ,覆 面 机 辊 出 现 弯 曲 变 形 等 不 良情 况 ,也 会 影 响 纸 板 的 粘 合 强 度 。 因 此 , 提 高 纸 板 的 粘 合 强 度 , 必 须 使 用 好 的 原 辅 材 料 , 要 根 据 生 产 实 际 情 况 ,合 理 调 整 好 粘 合 剂 的 配 比 , 控 制 好 搅拌 时 间 ,并 尽 量 使 用 好 的 水 质 调 配 粘 合 剂 ,
瓦楞纸粘结程度标准

瓦楞纸粘结程度标准一、粘合剂种类瓦楞纸的粘合程度首先取决于所使用的粘合剂的种类。
不同的粘合剂具有不同的特性,如耐水性、耐热性、粘结强度等。
因此,应根据实际应用场景选择合适的粘合剂。
一般来说,对于常规的瓦楞纸粘合,热熔胶和冷胶是常用的选择。
二、粘合剂用量粘合剂用量的多少直接影响到瓦楞纸的粘结程度。
过多的粘合剂可能会降低纸板的强度,而过少的粘合剂则可能导致粘结不牢固。
因此,必须控制好粘合剂的用量,确保足够的粘合剂能够均匀地涂抹在瓦楞纸上。
三、粘合温度粘合温度也是影响瓦楞纸粘结程度的重要因素。
不同的粘合剂有不同的最佳粘合温度。
在粘合过程中,应将粘合温度控制在适当的范围内,以确保粘合剂能够充分发挥作用,达到最佳的粘结效果。
四、粘合时间粘合时间是指瓦楞纸在粘合剂的作用下保持接触的时间。
这个时间的长短取决于粘合剂的类型和固化速度。
只有当粘合剂充分固化后,瓦楞纸才能达到最佳的粘结效果。
因此,在生产过程中,应根据粘合剂的类型和固化速度来确定合适的粘合时间。
五、纸板厚度瓦楞纸的厚度也是影响其粘结程度的一个重要因素。
较厚的瓦楞纸具有更好的抗拉强度和抗压强度,因此在相同的条件下,较厚的瓦楞纸更难实现理想的粘结效果。
在实际生产中,应根据产品要求和实际生产条件来选择合适的纸板厚度。
六、纸板质量瓦楞纸的质量也会对其粘结程度产生影响。
如果瓦楞纸存在质量问题,如纸质疏松、强度不足等,那么即使其他条件都得到了很好的控制,也可能无法实现理想的粘结效果。
因此,必须保证所使用的瓦楞纸质量符合要求。
七、储存条件瓦楞纸的储存条件对其粘结程度也有一定的影响。
如果储存环境过于潮湿或者高温,那么瓦楞纸可能会吸湿或者发生变形,这些都会影响到其粘结程度。
因此,应确保瓦楞纸储存在干燥、通风、避光的地方,以保持其质量稳定。
八、运输条件瓦楞纸在运输过程中也可能会受到一定的影响,如振动、撞击等都可能对其粘结程度产生影响。
因此,在运输过程中应做好防护措施,避免瓦楞纸受到过大的外力作用而影响其粘结程度。
瓦楞纸板脱胶原因及改善措施
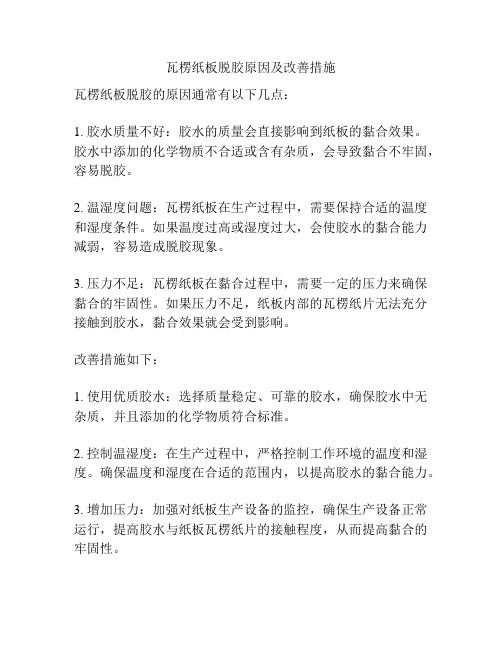
瓦楞纸板脱胶原因及改善措施
瓦楞纸板脱胶的原因通常有以下几点:
1. 胶水质量不好:胶水的质量会直接影响到纸板的黏合效果。
胶水中添加的化学物质不合适或含有杂质,会导致黏合不牢固,容易脱胶。
2. 温湿度问题:瓦楞纸板在生产过程中,需要保持合适的温度和湿度条件。
如果温度过高或湿度过大,会使胶水的黏合能力减弱,容易造成脱胶现象。
3. 压力不足:瓦楞纸板在黏合过程中,需要一定的压力来确保黏合的牢固性。
如果压力不足,纸板内部的瓦楞纸片无法充分接触到胶水,黏合效果就会受到影响。
改善措施如下:
1. 使用优质胶水:选择质量稳定、可靠的胶水,确保胶水中无杂质,并且添加的化学物质符合标准。
2. 控制温湿度:在生产过程中,严格控制工作环境的温度和湿度。
确保温度和湿度在合适的范围内,以提高胶水的黏合能力。
3. 增加压力:加强对纸板生产设备的监控,确保生产设备正常运行,提高胶水与纸板瓦楞纸片的接触程度,从而提高黏合的牢固性。
4. 定期检查和维护设备:对生产设备进行定期维护和检查,确保设备运行正常,避免设备问题导致黏合不牢固。
5. 加强员工培训:提高生产操作人员的技术水平和质量意识,确保生产过程中的操作规范,减少操作失误和质量问题的发生。
纸板粘合工艺技术

纸板粘合工艺技术纸板粘合工艺技术,是指利用胶水等粘合剂将多层纸板黏结在一起的加工工艺技术。
纸板是一种由纤维素纤维构成的板材,具有轻质、强度高、刚性好等特点,在包装、制作盒子等领域有着广泛的应用。
纸板粘合工艺技术在纸板制作过程中起到了至关重要的作用。
粘合工艺技术的好坏直接影响到纸板的质量和性能。
下面将介绍一下纸板粘合工艺技术的主要内容和步骤。
首先是胶水配制。
纸板使用的粘合剂主要有天然胶、合成胶和改性胶等。
胶水的选择要根据纸板用途和要求来确定,同时要考虑到环保和经济性。
胶水的配制要根据胶水的种类和纸板的材料来确定比例,一般需加入适量的催化剂和增稠剂。
其次是纸张的处理。
纸张的表面要干燥、清洁,以便胶水的渗透和粘合效果。
对于有一定保水性的纸张,需要在粘合前进行适量的浸水处理,以增加其粘合性能。
纸板的吸水性也会影响纸板在粘合过程中的吸收能力,所以要根据纸板的材料来调整胶水的稀释度和胶水的渗透时间。
然后是纸板的压合。
在纸板粘合过程中,需要将多层纸张按照要求的顺序和数量粘合起来。
压合的目的是使纸板的各层纸张紧密黏合在一起,提高纸板的强度和整体性,并排除纸张中可能存在的气泡和空隙。
压合的方式有手工压合、机械压合和热压等,其中热压是一种常用的压合方式,通过加热和加压来使纸张和胶水充分交联和黏合。
最后是纸板的干燥和修整。
粘合完毕后的纸板需要干燥一段时间才能达到使用的效果。
在纸板的干燥过程中,要注意避免阳光直射和湿度过高的环境。
干燥的时间根据纸板的厚度和胶水的种类来确定。
干燥完毕后,还需要对纸板进行修整,去除多余的边角和毛刺,使纸板达到平整和美观的要求。
纸板粘合工艺技术的应用非常广泛,不仅在包装行业中有重要的地位,还被广泛应用于建筑材料、家具、印刷等领域。
纸板粘合工艺技术的发展和创新,不仅可以提高纸板的质量和性能,还可以为相关产业的发展提供有效的支撑和保障。
综上所述,纸板粘合工艺技术是一项十分重要的工艺技术,它直接影响到纸板的质量和性能。
柔性版和凹版印刷品粘结的常见原因

柔性版和凹版印刷品粘结的常见原因“粘结”也就是印品墨层之间的不必要黏接,印后的卷筒纸内部、平张纸之间或复合结构承印物中都可能发生这样的问题。
有几种原因可能产生粘结,最常见的有卷筒纸收卷时张力大、溶剂残留量多、油墨中增塑剂含量高以及电晕放电处理过强,并取决于企业的工艺条件。
在包装印刷中,溶剂残留量多是造成粘结的最普遍的原因,印刷中没有挥发的溶剂致使墨层在压力下变软并粘到卷筒纸的背面。
大多数工厂对产品进行抽样并测量单位面积上残留溶剂的毫克数来监测溶剂残留量。
油墨没有干透或“墨层表面结皮”可以引起粘结,墨层表面结皮的现象与墨层发热有关,油墨的表面“干燥”,而墨层里面包含着溶剂。
采用现代的水溶性油墨时,问题会更严重,因为这类油墨的干燥是不可逆过程。
墨层或连接剂中沸点较高的溶剂很难挥发,而且常常导致比较多的残留溶剂。
有些溶剂如甲苯、二甲苯、乙二醇等,不仅可以引起粘连,而且可以产生讨厌的气味。
分析粘结原因的第一步应该利用气相色谱分析(G.C)确定溶剂残留量,如果残留量高,则油墨的抗粘连性降低。
假如印刷品进一步干燥能减少粘结,则溶剂残留很可能就是粘结的祸首。
增塑剂含量过高或连接剂分子量较低的油墨可能在干燥以后变软并发黏,一旦墨层表面变得太软,就会发生粘结。
硝基油墨往往含有大量增塑剂,油墨配方设计师必须对增塑剂与硝化纤维的比例严加控制。
另外,选择改性树脂时必须考虑到油墨配方中的增塑剂含量。
如果选用软树脂,增塑剂的比例应该相应地减小。
就增塑剂引起粘结的情况而言,增塑剂的比例高,溶剂滞留程度也高;印刷墨层变软,并随着时间而变得更软。
粘结试验可以说明墨层变软并随着时间恶化的现象,试样受热或进一步干燥后,粘连性几乎或根本不会改进。
由于电晕放电处理过度所造成的卷筒纸粘结不是太普遍,却同样带来麻烦。
电晕放电处理使墨层表面氧化并增加极性,最终增大表面张力。
这样的表面自然容易彼此粘结。
发生这种粘结后,说明电晕放电处理过度,例如PE薄膜电晕处理接近50甚至60。
印刷附着力不好的原因

印刷附着力不好的原因
印刷附着力不好的原因可能有很多。
举个例子,一种可能的原因是印刷机使用的是低质量的油墨。
这种油墨可能不够粘稠,无法充分附着在纸张上。
另外,印刷过程中的温度和湿度也会对附着力产生影响。
如果温度过高或湿度过大,油墨可能无法干燥,导致附着力不佳。
纸张的质量也是影响印刷附着力的重要因素。
如果纸张的表面光滑度不够,油墨就无法充分渗透进纸张纤维中,从而无法牢固附着。
另外,纸张的吸墨性也会影响附着力。
如果纸张的吸墨性太差,油墨就无法被纸张吸收,也会导致附着力不佳。
印刷机的使用也会对附着力产生影响。
如果印刷机的压力不均匀,或者印刷速度过快,都可能导致油墨无法充分附着在纸张上。
另外,印刷机的清洁程度也对附着力有一定影响。
如果印刷机清洁不彻底,油墨残留会影响附着力。
印刷附着力不好的原因可能是多方面的,包括油墨质量、纸张质量、印刷机使用等。
为了提高印刷附着力,我们可以选择高质量的油墨和纸张,同时确保印刷机的正常清洁和维护。
这样可以提高印刷品的质量,增加附着力,使印刷品更加美观和持久。
如何确保瓦楞纸板的粘合强度
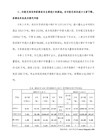
这种现象发生在上胶辊之前,主要是由于导爪挡板与瓦楞辊之间的距离太大、导爪挡板损
在施胶部分出现导爪痕迹或真空痕迹,这样的瓦楞纸板做成的纸箱,在使用时通常会断裂,瓦楞纸板的边压强度和纸箱的抗压强度会大大降低。有导爪的单面机生产出来的瓦楞纸板经常会在施胶部分出现导爪痕迹(一条清晰没有粘合剂的空白),通常主要是由于导爪挡板弯曲、磨损、位置偏或调整压力大;粘合剂就在挡板上积累、凝结成块,这些硬化的淀粉就会擦落上胶辊上的粘合剂,形成导爪空白痕迹。另外,瓦楞原纸含水率高、上胶辊上因磨损造成凹槽或上胶辊上出现较宽的粘合剂被异物擦掉,都会导致此质量问题。无导爪的单面机常会在施胶部分出现真空痕迹,这主要是由于瓦楞辊真空太多造成的,真空会将瓦楞原纸过度粘贴于瓦楞辊上,造成芯纸凹陷,上胶辊无法将粘合剂涂到凹陷的芯纸楞峰上。
当上胶辊和下瓦楞辊之间的间隙太宽时,上胶辊不能接触到下瓦楞辊的地方,瓦楞楞峰上就没有足够的粘合剂。
2、粘合剂横向抛射现象
粘合剂黏度太高;太低或里面硼砂含量太高时,在生产线高速运压和抗压强度者都会降低。
3、导爪痕迹或真空痕迹
如何确保瓦楞纸板的粘合强度
?
施胶不良主要与瓦楞纸板生产线设备状态、粘合剂质量、原纸质量有关,常见的施胶不良导致的质量问题主要表现在以下几个方面:
1、点滴上胶现象
上胶辊上有污垢,如纸屑、淀粉结块及其他异物等,或者辊面网穴处有异物堵塞,导致上胶辊不能顺利上胶,只能传递少量粘合剂,并且容易被擦落,上胶时就会出现在楞峰上胶量不足,出现断断续续的点滴上胶现象。这样的瓦楞纸板表面就会出现面纸与芯纸分层的痕迹,纸箱的抗压强度、边压强度和粘合强度都会降低。
瓦楞纸板黏合强度测量影响因素分析

河南建材2017年第4期胶混凝土可以用在铁路运输方面,以减少火车高速运行的冲击;此外,还可用在建筑的抗震减震方面,以及军用防爆等方面。
4结论及展望橡胶混凝土作为一种新型复合材料,以其独特的抗冲击能力强、抗震性能好、隔音隔热、质量轻、等优点,已在各大领域都得到了较好的应用;同时也解决了废旧橡胶难处理的问题。
然而,作为新生事物,必然还存在许多问题,为更为广泛的推广应用,必须系统的对橡胶混凝土机理进行更为深入的研究,同时开发使用的改性剂,提高强度。
橡胶混凝土作为一种低碳、环保的新型复合材料,符合国家可持续发展战略,必将实现经济和社会效益的统一。
参考文献:[1]魏杨倬,倪明仿,王铮,康露茜.基于资源节约的废旧轮胎回收利用研究[J].再生资源与循环经济,2012(1):34-36.[2]韩阳,白亚强,巴松涛.橡胶集料改性混凝土研究进展与应用[J].混凝土,2013(10):87-90+94.[3]杨春峰,杨敏.废旧橡胶混凝土力学性能研究进展[J].混凝土,2011(12):98-100+109.[4]阮盛华.橡胶混凝土的研究及应用进展[A].天津大学.第十二届全国现代结构工程学术研讨会暨第二届全国索结构技术交流会论文集[C].天津大学,2012:18.[5]王林龙,简宇桥,童代伟,邓文明.橡胶混凝土研究进展[J].公路交通技术,2017(1):17-20.[6]徐自然,危大结.浅谈橡胶混凝土的特点及应用[J].科技信息,2010(17):849.瓦楞纸板黏合强度测量影响因素分析李俊鹏河南省产品质量监督检验院(450000)摘要:通过对瓦楞纸板黏合强度测量影响因素分析、试验比对,得出了影响瓦楞纸板黏合强度的几个因素。
试样制备、针形附件变形、瓦楞被破坏、空气湿度较大和存放时间过长等不同程度影响其黏合强度,为测量瓦楞纸板黏合强度提供了参考,使测量结果更加接近实际值。
关键词:瓦楞纸板;黏合强度;空气湿度瓦楞纸是经过起楞加工后形成有规律且永久性波纹的纸,瓦楞纸板由瓦楞纸和若干层纸黏合在一起组成。
脱胶原因对策
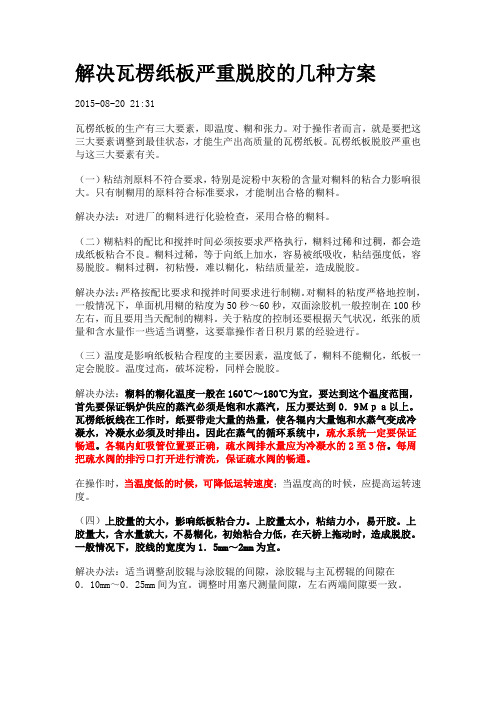
解决瓦楞纸板严重脱胶的几种方案2015-08-20 21:31瓦楞纸板的生产有三大要素,即温度、糊和张力。
对于操作者而言,就是要把这三大要素调整到最佳状态,才能生产出高质量的瓦楞纸板。
瓦楞纸板脱胶严重也与这三大要素有关。
(一)粘结剂原料不符合要求,特别是淀粉中灰粉的含量对糊料的粘合力影响很大。
只有制糊用的原料符合标准要求,才能制出合格的糊料。
解决办法:对进厂的糊料进行化验检查,采用合格的糊料。
(二)糊粘料的配比和搅拌时间必须按要求严格执行,糊料过稀和过稠,都会造成纸板粘合不良。
糊料过稀,等于向纸上加水,容易被纸吸收,粘结强度低,容易脱胶。
糊料过稠,初粘慢,难以糊化,粘结质量差,造成脱胶。
解决办法:严格按配比要求和搅拌时间要求进行制糊。
对糊料的粘度严格地控制,一般情况下,单面机用糊的粘度为50秒~60秒,双面涂胶机一般控制在100秒左右,而且要用当天配制的糊料。
关于粘度的控制还要根据天气状况,纸张的质量和含水量作一些适当调整,这要靠操作者日积月累的经验进行。
(三)温度是影响纸板粘合程度的主要因素,温度低了,糊料不能糊化,纸板一定会脱胶。
温度过高,破坏淀粉,同样会脱胶。
解决办法:糊料的糊化温度一般在160℃~180℃为宜,要达到这个温度范围,首先要保证锅炉供应的蒸汽必须是饱和水蒸汽,压力要达到0.9Mpa以上。
瓦楞纸板线在工作时,纸要带走大量的热量,使各辊内大量饱和水蒸气变成冷凝水,冷凝水必须及时排出。
因此在蒸气的循环系统中,疏水系统一定要保证畅通。
各辊内虹吸管位置要正确,疏水阀排水量应为冷凝水的2至3倍。
每周把疏水阀的排污口打开进行清洗,保证疏水阀的畅通。
在操作时,当温度低的时候,可降低运转速度;当温度高的时候,应提高运转速度。
(四)上胶量的大小,影响纸板粘合力。
上胶量太小,粘结力小,易开胶。
上胶量大,含水量就大,不易糊化,初始粘合力低,在天桥上拖动时,造成脱胶。
一般情况下,胶线的宽度为1.5mm~2mm为宜。
纸原料和粘接剂对瓦楞纸板粘合强的影响

书山有路勤为径;学海无涯苦作舟纸原料和粘接剂对瓦楞纸板粘合强的影响在纸箱物理性能参数中,粘合牢度是一项关键性指标,其数值的高低对纸箱生产和成品纸箱抗压力有极大影响。
许多企业生产瓦楞纸箱,在性能检测时,往往因粘合强度达不到标准值6N/cm平方,造成该批纸箱不合格;有时发往用户,用户无法堆运,造成经济损失。
现就纸原料和粘接剂的质量特性对纸箱粘合牢度的影响谈些认识。
生产纸箱,主要材料为各品种纸。
按克重分为箱板纸与瓦楞原纸,按产地分为进口与国产,按材质又可分为木浆纸、竹浆纸、草浆纸、废纸回造纸等。
所用粘接剂,目前主要为泡花碱和玉米淀粉粘接剂,玉米淀粉粘接剂又分为冷制胶与热制胶,玉米淀粉可以因配方不同,许多不同质量特性的粘接剂。
纸原料和粘接上的质量性能,可影响纸箱的粘合强度。
在正常情况下,粘合性高和渗透性好的胶,制作的纸权粘俣强度高,反之,则差。
热制胶生产的纸板比冷制胶粘合牢度好,在冬天更为明显。
使用玉米淀粉作粘接剂的纸板比使用泡花碱的粘合牢度高,在湿气较大的地区或贮存一段时间后更是如此。
木浆纸生产的纸板则比其它材料生产的纸板粘合牢度好。
纸的质量特性对约板粘合强度的影响主要在纸的含水率和板纸面层与芯层的结构特性。
测试中发现,一些板纸面层与芯层,因工艺造成分层或者纤维拉力小,造成纸板起层,使粘合强度下降。
所和纸的含水率小于14%时,纸吸胶快、渗透好,生产的纸板粘合强度较好,但如果纸过分干燥,会过快地吸收粘合剂中的水分,粘合剂的流动性,抑制粘合剂的渗透,使粘合剂不能渗透到足够的深度,反而降低纸板粘合牢度;反之,原纸过湿,其水分会阻碍纤维吸收粘合剂,导致粘合剂过少,瓦楞纸板胶胶分层,专注下一代成长,为了孩子。
影响纸板粘合的因素有哪些

本文摘自再生资源回收-变宝网()影响纸板粘合的因素有哪些纸板脱胶主要是纸板的粘合能力不好,即粘合不良。
在纸板实际生产过程中,影响纸板粘合的因素有以下几个方面:胶水、设备、温度、速度、原纸克重、胶线宽度等。
一、智能化控制胶水工艺,提升纸板粘合效果首先介绍一下胶水物理指标与纸板粘合之间的关系:1、糊化温度:这是作用在胶水上并使其糊化产生粘性的温度在纸板生产中,保持糊化温度的稳定是关键之一。
即胶水生产循环后糊化温度变化与生产胶水时是否充分搅匀,NaOH和硼砂是否充分中和有关。
①不同速度的瓦楞纸板生产线应配合相应糊化温度的胶水,速度越高,温度作用在原纸上的时间越短,所以相应糊化温度越低。
如:高速线:糊化温度应偏低,200~250米/分,53℃~57℃;低速线:糊化温度应偏高,100~160米/分,58℃~62℃。
②不同设备应配合相应糊化温度的胶水。
单面机:根据单面机里纸和坑纸温度传导及压载的方式,纸与辊直接硬性接触,温度传导性好,糊化温度可偏高。
糊机:根据面纸和见坑纸温度传导及压载方式,因为是单面直接软性接触,压力不能太大,纸板易压扁,所以温度传导一般,糊化温度比单面机上的要偏低一些。
根据上下两层见坑纸的温度传导及压载方式,因为是间接软接触,加压同面纸一样。
温度只能通过热辐射传导,所以温度传导较差,糊化温度比面纸的更低。
建议:高速线糊机上下层胶水要分开,因为糊化温度不同。
注意:糊化温度不是越低越好,过低容易造成胶水提前糊化形成假粘,受环境、设备温度的影响还容易形成胶块。
2、固体含量:即淀粉占胶水的比例,又称水粉比淀粉是胶水之所以有粘性的主体,淀粉固体含量越大,胶水粘性也越强。
①不同克重的原纸配合相应的胶水固体含量,原纸克重越高胶水固体含量越高。
②不同设备配合相应的胶水固体含量,由于压载方式不同,糊机所用胶水之固体含量比单面机所用胶水之固体含量要高,糊机要求的是24%~26%,单面机要求的是20%~22%。
纸板粘合不良的8种原因及解决方法

纸板粘合不良的8种原因及解决方法纸板粘合不良,有许多种表现形式,最常见的就有8种。
当纸板出现粘合不良时,应先观看它的详细表现形式,然后查找原因,对症下药是关键。
本文将共享纸板粘合不良的8种状况及对应解决方法!一、无胶或上胶面明显缺胶原因1:操作失误。
a.胶盘断胶。
b.胶量协作与纸质明显不匹配。
原因2:设备调整问题。
a.糊机压载辊未压或间隙过大。
b.单面机糊辊与瓦辊间隙过大。
解决方法:(1)调整合理的胶水配方,掌握好胶水的温度和粘度,避免胶水堵塞胶管,导致胶盘断胶。
(2)依据自己用材状况形成各种纸质的上胶体系,对操作员工进行培训。
(3)形成校准制度,定期对压载辊间隙和上胶辊与糊辊间隙进行校准,并形成标准。
二、有胶,但胶面白色原因1:操作失误,温度与胶水的糊化温度不匹配。
比如,车速过快、蒸汽压力过低等。
原因2:天气原因,胶水配方未准时调整糊化温度。
原因3:蒸汽管阀异常造成疏水不正常,冷凝水未准时排出。
解决方法:(1)形成自己的胶水配方体系,应对不同气候条件。
(2)建立点检制度,每天检查相应的管阀和蒸汽回收系统。
三、有胶,但显金黄色,并有结晶原因:胶水硼砂过量。
解决方法:调整硼砂用量。
四、有胶,但显淡黄色水印原因:胶水粘度下降,动态固体含量偏低。
解决方法:提高胶水的稳定性,粘度稳定在3秒以内。
五、有胶,但胶位错位原因1:面纸在热板运行时产生大量静电,吸附过大。
原因2:双面机压载力不够或输送带表面磨损造成打滑。
解决方法:(1)采用去除静电的方法,比如,喷防静电液、贴胶带纸板过热板等。
(2)更换输送带。
六、五层纸板中层出现段状的脱胶原因:双面机进纸口压载辊跳动过大,输送带抖动造成纸板二次粘合。
解决方法:检查进纸口压载辊轴承是否有损坏。
七、高耐破面纸三层纸板边口脱胶原因:面纸边口在烘道运行中过分加热,导致边口胶水提前糊化。
解决方法:(1)调整和提前各层单瓦在烘道口的接合点。
(2)调整烘道温度配置,由低到高。
瓦楞纸板的粘合与生产速度、温度的关系
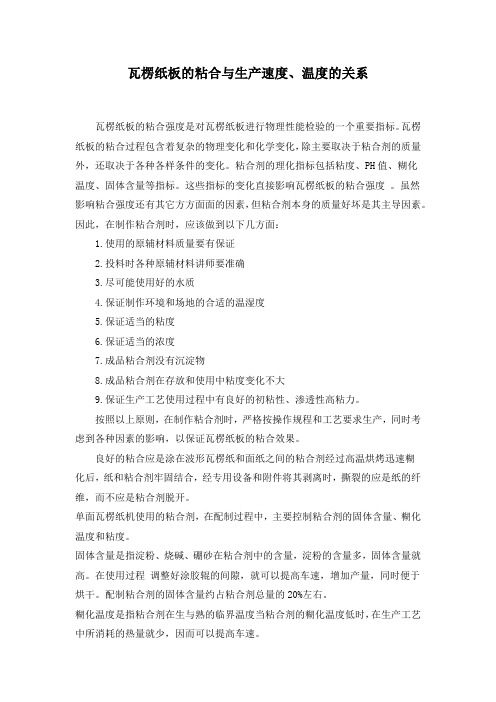
瓦楞纸板的粘合与生产速度、温度的关系瓦楞纸板的粘合强度是对瓦楞纸板进行物理性能检验的一个重要指标。
瓦楞纸板的粘合过程包含着复杂的物理变化和化学变化,除主要取决于粘合剂的质量外,还取决于各种各样条件的变化。
粘合剂的理化指标包括粘度、PH值、糊化温度、固体含量等指标。
这些指标的变化直接影响瓦楞纸板的粘合强度。
虽然影响粘合强度还有其它方方面面的因素,但粘合剂本身的质量好坏是其主导因素。
因此,在制作粘合剂时,应该做到以下几方面:1.使用的原辅材料质量要有保证2.投料时各种原辅材料讲师要准确3.尽可能使用好的水质4.保证制作环境和场地的合适的温湿度5.保证适当的粘度6.保证适当的浓度7.成品粘合剂没有沉淀物8.成品粘合剂在存放和使用中粘度变化不大9.保证生产工艺使用过程中有良好的初粘性、渗透性高粘力。
按照以上原则,在制作粘合剂时,严格按操作规程和工艺要求生产,同时考虑到各种因素的影响,以保证瓦楞纸板的粘合效果。
良好的粘合应是涂在波形瓦楞纸和面纸之间的粘合剂经过高温烘烤迅速糊化后,纸和粘合剂牢固结合,经专用设备和附件将其剥离时,撕裂的应是纸的纤维,而不应是粘合剂脱开。
单面瓦楞纸机使用的粘合剂,在配制过程中,主要控制粘合剂的固体含量、糊化温度和粘度。
固体含量是指淀粉、烧碱、硼砂在粘合剂中的含量,淀粉的含量多,固体含量就高。
在使用过程调整好涂胶辊的间隙,就可以提高车速,增加产量,同时便于烘干。
配制粘合剂的固体含量约占粘合剂总量的20%左右。
糊化温度是指粘合剂在生与熟的临界温度当粘合剂的糊化温度低时,在生产工艺中所消耗的热量就少,因而可以提高车速。
粘度是指在生产工艺使用过程中粘合剂的流动能力。
我们要求粘合剂低粘度,实际就是为了在使用中有良好的流动性。
可以提高初粘力。
据国外的资料介绍,配制熟浆是控制粘合剂粘度的关键。
一要严格控制搅拌时间,当搅拌时间不够时,粘合剂的粘度不稳定;二要掌握好烧碱及其它原料的配比。
只有恰到好处的掌握粘合剂的固体含量、糊化温度和粘度的相对关系,才能制作出质量好的粘合剂,从而保证在生产工艺中良好的粘合。
减少及预防不良纸板的产生

A、进汽与冷凝水回收管(包括进汽及回收金属软管)安装要合理、顺畅。
B、保持所有烘吸管完好、无磨损,所有管路、接口阀门无漏汽。
C、卸水器、单向阀、接口阀门不装反,并保持良好状态。
3、机械调整问题
在一般情况下,可以说绝大部分的不良品都与机器调整有关,因此解决了机械调整方面的问题也就解决了纸板损耗的问题,这对于任何一个公司及其主管来说都是极其重要的。
(1)单面机的调整及控制:
4、原纸预热面积与张力的调整
当纸板由于预热温度不足而造成贴合不良时,应及时加大原纸所经过的所有相关预热器的面积,并相对加大相关原纸架、刹车及自动接纸机的刹车器压力,以使原纸(纸板)能够更紧地贴在预热器上,以增加受热量。
5、原纸预热面积与车速之间的关系
当车速越快时,原纸的预热面积要越大;反之,则越小。当原纸克重≥175g/m2时,车速100米/分以上,其预热面积在70%以上;当原纸克重≤150g/m2时,车速100米/分以上,其在预热缸上包覆面积为30-70%。一般芯纸的包覆面积只为30-50%左右,原纸的张力则是根据纸卷的大小来设定。纸卷越大,张力越大;纸卷越小,张力越小。
A、原纸架、接纸机、预热缸与主机之间必须保持在水平位置,且处于同一条中心线上。
B、压力辊的调整以保持里纸与芯纸贴合良好,里纸有轻微压力线即可(有些机器压力辊压力是以T/cm2为单位,有些是以kg/cm2为单位)。
C、瓦楞辊的偏芯以芯纸成为楞型以后没有偏斜为标准,并使两边压力一致(偏芯在每次更换瓦楞辊时调整,调好以后,任何人不能随意调整)。
解决“粘合不良” 提高瓦楞纸板质量

解决“粘合不良”提高瓦楞纸板质量在瓦楞纸箱的生产实践中,各种纸张间的粘合是非常重要的一个环节,并且在相当程度上决定了产品的质量水平。
各层纸页之间粘合是否紧密牢固,直接影响瓦楞纸板的质量。
粘合良好的瓦楞纸板表面平整,不起泡、无褶皱、不翘曲,加工成瓦楞纸箱后纸页之间不会产生分离,外观硬挺,有较好的抗压和缓冲性能,能有效地保护内装商品免受外界不利因素影响而受损。
但是,在瓦楞纸板生产线上出现瓦楞纸板粘合不良(起泡、脱胶、假粒)的现象时有发生。
据了解,瓦楞纸板生产线产生的废次品中,因粘合问题造成的占了近七成。
所以,要真正达到降本增效的目的,必须将因粘和问题产生的废品率控制在合适范围内。
接下来,我们将找出纸板“粘合不良”产生的原因,为您在实际生产中遇到问题时,提供一系列解决方案。
瓦楞纸板是否粘合良好是对瓦楞纸板进行物理性能检验的一个重要指标。
影响瓦楞纸板粘合强度的原因比较复杂,概括地讲,原纸、黏合剂、瓦楞纸板机械、生产计划安排和员工操作水平等等,均对其施加了影响,并且以上因素之间还相互影响。
原纸在此主要表现在几个方面:1.原纸的含水率:箱板纸或瓦楞原纸过于干燥(低于6%)或水分过大(高于12%),都会造成瓦楞纸板粘合不佳。
太干燥时,黏合剂的膨润和粘合所必需的水分被原纸吸收,结果造成胶未糊化现象。
水分过大时,多余的水分对热量的吸收,导致热量不足,从而粘合不佳。
解决方案是严格控制原纸的水分,太干燥时须喷湿处理,水分过大时,须适当增加原纸的水分,预热面积,如果仍旧不佳,则必须换纸。
2.原纸的吸水性或透水性的好坏:原纸的材质、紧度和施胶度,决定了其吸水性或透水性。
吸水性或透水性太差的原纸,会抑制黏合剂的渗透粘合;吸水性或透水性太强的原纸,一会造成胶未糊化现象,二会产生透胶现象。
前一种的解决方案是黏合剂中使用了添加剂,利用添加剂改善原纸表面的疏水性质,使黏合剂得以渗透。
此外,适当增加黏合剂涂布量也是必要的。
我们知道,瓦楞纸板的粘合首先是楞纸楞峰涂胶,然后与面里纸或夹芯的结合,黏合剂在任一层面间的转移受到阻碍,都将影响粘合效果。
- 1、下载文档前请自行甄别文档内容的完整性,平台不提供额外的编辑、内容补充、找答案等附加服务。
- 2、"仅部分预览"的文档,不可在线预览部分如存在完整性等问题,可反馈申请退款(可完整预览的文档不适用该条件!)。
- 3、如文档侵犯您的权益,请联系客服反馈,我们会尽快为您处理(人工客服工作时间:9:00-18:30)。
本文摘自再生资源回收-变宝网()
影响纸板粘合的因素有哪些
纸板脱胶主要是纸板的粘合能力不好,即粘合不良。
在纸板实际生产过程中,影响纸板粘合的因素有以下几个方面:胶水、设备、温度、速度、原纸克重、胶线宽度等。
一、智能化控制胶水工艺,提升纸板粘合效果
首先介绍一下胶水物理指标与纸板粘合之间的关系:
1、糊化温度:这是作用在胶水上并使其糊化产生粘性的温度
在纸板生产中,保持糊化温度的稳定是关键之一。
即胶水生产循环后糊化温度变化与生产胶水时是否充分搅匀,NaOH和硼砂是否充分中和有关。
①不同速度的瓦楞纸板生产线应配合相应糊化温度的胶水,速度越高,温度作用在原纸上的时间越短,所以相应糊化温度越低。
如:
高速线:糊化温度应偏低,200~250米/分,53℃~57℃;
低速线:糊化温度应偏高,100~160米/分,58℃~62℃。
②不同设备应配合相应糊化温度的胶水。
单面机:根据单面机里纸和坑纸温度传导及压载的方式,纸与辊直接硬性接触,温度传导性好,糊化温度可偏高。
糊机:根据面纸和见坑纸温度传导及压载方式,因为是单面直接软性接触,压力不能太大,纸板易压扁,所以温度传导一般,糊化温度比单面机上的要偏低一些。
根据上下两层见坑纸的温度传导及压载方式,因为是间接软接触,加压同面纸一样。
温度只能通过热辐射传导,所以温度传导较差,糊化温度比面纸的更低。
建议:高速线糊机上下层胶水要分开,因为糊化温度不同。
注意:糊化温度不是越低越好,过低容易造成胶水提前糊化形成假粘,受环境、设备温度的影响还容易形成胶块。
2、固体含量:即淀粉占胶水的比例,又称水粉比
淀粉是胶水之所以有粘性的主体,淀粉固体含量越大,胶水粘性也越强。
①不同克重的原纸配合相应的胶水固体含量,原纸克重越高胶水固体含量越高。
②不同设备配合相应的胶水固体含量,由于压载方式不同,糊机所用胶水之固体含量比单面机所用胶水之固体含量要高,糊机要求的是24%~26%,单面机要求的是20%~22%。
3、粘度:即胶水的单位流量所需时间(胶水稀与浓)
粘度的主要作用是衡量胶水的转移和渗透性能。
粘度小,转移和渗透能力强,粘度过小糊轮不易上浆。
同样,保持粘度的稳定也是生产过程中的关键因素。
胶水生产循环后,粘度的变化将直接影响纸板的粘合品质。
粘度的变化主要是因为管道和浆盘环境温度的影响。
建议:用双层浆筒,用水保温来储存循环胶水。
①不同速度的生产线配合相应的胶水粘度,速度越高,需要胶水的转移和渗透速度越快。
如:
高速线:粘度应偏低,200~250米/分,4号量杯,14~22秒;
低速线:粘度应偏高,100~160米/分,4号量杯,18~30秒。
②不同设备配合相应粘度(高速线)
单面机:由于单面机上胶工序到粘合工序之间的距离短,粘度应偏低,14~18秒;
双面机:由于糊机上胶工序到热板的距离长,粘度应偏高,18~22秒。
4、实施关键点:
①使用全自动制浆机,保证胶水各项指标的稳定。
②定期检测打浆机各传感器是否良好。
③分开不同糊化温度胶水配方(针对高速机)。
④生产线上采用双层浆筒,水要保温以便来储存循环胶水。
智能化控制设备的间隙及平行度,提升纸板粘合效果
要实现生产的纸板粘合质量好,就要保证设备的完好,各辊平行度及糊机各楞型速差都要调整准确,保证楞尖上胶良好。
二、实施关键点:
1、设备的正常保养检查。
要经常检查:
①糊轮与切糊轮之间间隙及平行度。
②糊轮与坑轮之间间隙及平行度。
③糊轮与骑轮之间间隙及平行度。
④糊机各楞型速差:E楞97-98%、B楞95-96%、C楞92-93%、A楞88-90%,要保证各加热器温度的正常。
2、蒸汽系统疏水阀的检查,要保证蒸汽温度的正常。
智能化控制温度,提升纸板粘合效果
温度对纸板粘合的影响表现在:纸板生产过程中温度是在一定的胶水糊化温度下,随着纸质、车速的变化而变化,各工艺点的温度不同。
①纸质克重越高,纸板粘合所需的温度也越高。
②车速越快,纸板粘合所需的温度也越高。
③胶水的糊化温度越高,纸板粘合所需的温度也越高。
④上胶厚度越厚,纸板粘合所需的温度也越高。
建议:使用湿部制程控制之温度控制系统。
三、智能化控制车速,提升纸板粘合效果
车速对纸板粘合的影响,表现在温度作用在纸板上的时间和上胶厚度、间隙。
1、车速越快,温度作用时间越短,对胶水的糊化温度要求越低,要提高各加热器温度值。
2、上胶间隙不变,车速越快,上胶厚度越厚。
本文摘自变宝网-废金属_废塑料_废纸_废品回收_再生资源B2B交易平台网站;
变宝网官网:/?qx
买卖废品废料,再生料就上变宝网,什么废料都有!。