汽车传动轴设计资料
汽车传动轴设计范文

汽车传动轴设计范文汽车传动轴是汽车动力传输系统中的关键组成部分,承担着将发动机产生的动力传递到车轮的任务。
传动轴设计的目标是实现高效率、低噪音和可靠性。
在设计传动轴时,需要考虑多个因素,包括传动轴的材料选择、传动轴的结构设计和传动轴的加工工艺等。
传动轴的材料选择是影响传动轴性能的重要因素之一、传动轴通常采用高强度合金钢或碳纤维复合材料制作。
高强度合金钢具有优异的强度和韧性,能够承受高强度的扭转和弯曲力。
而碳纤维复合材料具有高强度、低密度和优异的疲劳寿命,能够降低传动轴的重量并提高耐久性。
传动轴的结构设计是实现高效率传输的关键。
一般来说,传动轴的截面形状决定了其刚度和重量。
传动轴通常采用圆柱形的实心杆或中空杆设计。
实心杆传动轴具有较高的刚度,能够抵御大扭矩和弯曲力,但重量较大。
而中空杆传动轴由于空心结构的设计,能够降低传动轴的重量,并提高传动效率。
但对于承受较大扭矩和弯曲力的应用来说,中空杆传动轴的刚度较低,需要在设计中进行综合考虑。
除了结构设计,传动轴的加工工艺也对传动轴性能产生重要影响。
精确的加工工艺能够提高传动轴的平衡性、可靠性和传动效率。
在加工过程中,需要进行精确的尺寸控制、表面处理和动平衡处理。
尺寸控制是确保传动轴高度精度的关键。
表面处理能够提高传动轴的耐腐蚀性和抗磨性。
动平衡处理能够减少传动轴的振动和噪音,并提高传动效率。
除了上述因素,传动轴设计还需要考虑其他一些因素,如传动轴的长度、传动轴的安装方式和传动轴的支撑方式等。
传动轴长度的选择需要权衡传动效率和车辆布局的要求。
传动轴的安装方式一般分为固定式和可伸缩式两种,根据车型和传动需求进行选择。
传动轴的支撑方式包括悬挂式和支架式,需要根据车辆底盘结构和传动需求进行选择。
在传动轴设计中,还需要进行性能计算和结构优化。
性能计算可以通过计算机辅助工程软件进行,包括传动效率、传动轴的疲劳寿命和传动轴的振动等。
结构优化可以通过有限元分析方法进行,通过调整传动轴的结构参数,优化传动轴的性能和重量。
汽车传动轴设计范文

汽车传动轴设计范文首先,汽车传动轴的主要功能是传递动力。
在设计传动轴时,需要考虑到车辆的功率输出和转速范围。
一般而言,高功率车辆需要更加强固的传动轴来承受更大的转矩和压力。
此外,传动轴的设计还需要考虑到车辆的运行速度范围,以确保传动轴在高速情况下能够承受住转动力。
其次,汽车传动轴的设计对于车辆的平顺性和舒适性也有很大影响。
传动轴的设计需要考虑到轴的重量和平衡性,以减少振动和噪音。
一种常见的设计方法是在传动轴上使用平衡块来平衡轴的重量和减少振动。
此外,传动轴的设计还需要考虑到轴的刚度和弯曲性,以确保传动轴在运转过程中不会发生变形或弯曲,从而影响车辆的平顺性和舒适性。
另外,对于四驱车辆而言,传动轴的设计也需要考虑到车轮之间的差速问题。
差速器通常安装在传动轴上,它能够根据车轮速度的差异来实现差速作用,并帮助车辆更好地应对转弯情况。
因此,传动轴的设计需要考虑到差速器的安装位置和传动轴与差速器之间的连结方式。
此外,与传动轴密切相关的还有轴承和万向节的设计。
轴承的选材和设计对于减少传动轴的摩擦和磨损至关重要。
对于高速和高功率的车辆而言,可能需要采用更耐磨和耐高温的轴承材料来提高传动轴的使用寿命。
万向节的设计则用于传递动力和允许轴的角度变化,以适应车轮的悬挂和转向。
综上所述,汽车传动轴的设计对于汽车性能、安全和舒适性都起着至关重要的作用。
在设计传动轴时,需要兼顾动力传递、平顺性、舒适性和差速等因素,以确保传动轴能够满足车辆的需求。
此外,轴承和万向节的设计也是传动轴设计的重要考虑因素,它们对于传动轴的耐磨性、耐高温性和角度变化能力都有着重要影响。
因此,对于汽车制造商和工程师而言,对于传动轴设计的细节和原理的深入了解是非常必要的。
传动轴设计指南范文
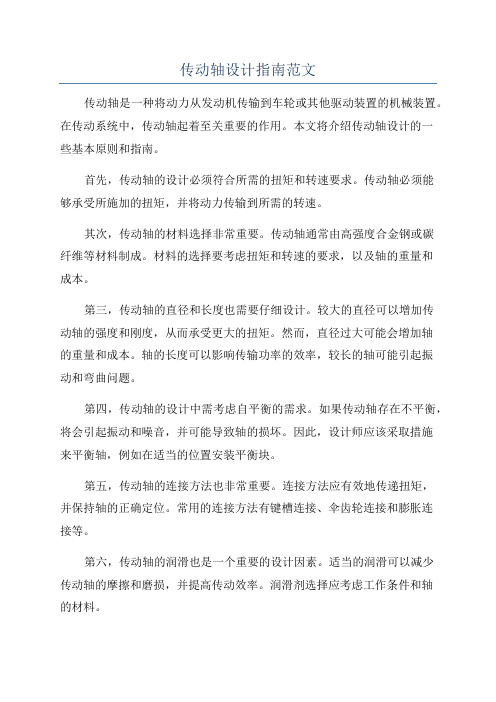
传动轴设计指南范文传动轴是一种将动力从发动机传输到车轮或其他驱动装置的机械装置。
在传动系统中,传动轴起着至关重要的作用。
本文将介绍传动轴设计的一些基本原则和指南。
首先,传动轴的设计必须符合所需的扭矩和转速要求。
传动轴必须能够承受所施加的扭矩,并将动力传输到所需的转速。
其次,传动轴的材料选择非常重要。
传动轴通常由高强度合金钢或碳纤维等材料制成。
材料的选择要考虑扭矩和转速的要求,以及轴的重量和成本。
第三,传动轴的直径和长度也需要仔细设计。
较大的直径可以增加传动轴的强度和刚度,从而承受更大的扭矩。
然而,直径过大可能会增加轴的重量和成本。
轴的长度可以影响传输功率的效率,较长的轴可能引起振动和弯曲问题。
第四,传动轴的设计中需考虑自平衡的需求。
如果传动轴存在不平衡,将会引起振动和噪音,并可能导致轴的损坏。
因此,设计师应该采取措施来平衡轴,例如在适当的位置安装平衡块。
第五,传动轴的连接方法也非常重要。
连接方法应有效地传递扭矩,并保持轴的正确定位。
常用的连接方法有键槽连接、伞齿轮连接和膨胀连接等。
第六,传动轴的润滑也是一个重要的设计因素。
适当的润滑可以减少传动轴的摩擦和磨损,并提高传动效率。
润滑剂选择应考虑工作条件和轴的材料。
第七,传动轴的安装和维护也需要注意。
传动轴的正确安装可以确保轴和其他部件的正常运行。
定期检查和维护传动轴可以延长其寿命并避免故障。
最后,传动轴设计时应考虑实际应用环境的影响。
例如,在恶劣的工作条件下,如高温、高湿度或腐蚀性环境中,轴的材料和设计必须能够适应这些条件。
综上所述,传动轴的设计是传动系统中不可或缺的一部分。
合理的设计可以保证传动系统的正常运行和高效性能。
设计人员应该充分考虑扭矩和转速要求、材料选择、直径和长度、自平衡、连接方法、润滑、安装和维护等因素,以确保传动轴的正常运行和长寿命。
传动轴和万向节设计
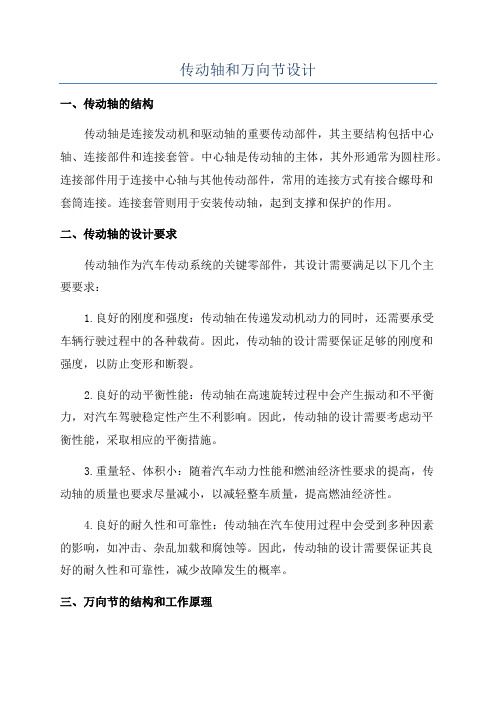
传动轴和万向节设计一、传动轴的结构传动轴是连接发动机和驱动轴的重要传动部件,其主要结构包括中心轴、连接部件和连接套管。
中心轴是传动轴的主体,其外形通常为圆柱形。
连接部件用于连接中心轴与其他传动部件,常用的连接方式有接合螺母和套筒连接。
连接套管则用于安装传动轴,起到支撑和保护的作用。
二、传动轴的设计要求传动轴作为汽车传动系统的关键零部件,其设计需要满足以下几个主要要求:1.良好的刚度和强度:传动轴在传递发动机动力的同时,还需要承受车辆行驶过程中的各种载荷。
因此,传动轴的设计需要保证足够的刚度和强度,以防止变形和断裂。
2.良好的动平衡性能:传动轴在高速旋转过程中会产生振动和不平衡力,对汽车驾驶稳定性产生不利影响。
因此,传动轴的设计需要考虑动平衡性能,采取相应的平衡措施。
3.重量轻、体积小:随着汽车动力性能和燃油经济性要求的提高,传动轴的质量也要求尽量减小,以减轻整车质量,提高燃油经济性。
4.良好的耐久性和可靠性:传动轴在汽车使用过程中会受到多种因素的影响,如冲击、杂乱加载和腐蚀等。
因此,传动轴的设计需要保证其良好的耐久性和可靠性,减少故障发生的概率。
三、万向节的结构和工作原理万向节用于连接传动轴和车轮之间,是一种能够在不同角度下实现传动的装置。
常见的万向节结构有三个球式和常角度式两种。
其中,三个球式万向节是一种可以实现任意角度传动的结构,由两个内圈、两个外圈和三个转动球组成。
常角度式万向节则适用于需要固定角度传动的场合,常用于前驱汽车。
万向节的工作原理是通过球和轴之间的球座和滚道实现传递动力。
当传动轴转动时,球会在轴上转动,通过球面与内圈、外圈的滚道接触传递动力。
相对于三个球式万向节,常角度式万向节的结构相对简单,其工作原理类似。
四、常见问题及解决方法1.传动轴产生振动:造成传动轴振动的原因有很多,可能是由于不平衡、轴材质问题或连接部件松动等原因。
解决方法可以是进行动平衡修正或更换质量较好的传动轴。
传动轴设计[整理版]
![传动轴设计[整理版]](https://img.taocdn.com/s3/m/65cff7c627fff705cc1755270722192e44365855.png)
传动轴设计1概述在汽车传动轴系或其它系统中,为了实现一些轴线相交或相对置经常变化的转轴之间的动力传递,必须采用万向传动装置。
万向传动装置一般由万向节和传动轴组成,当距离较远时,还需要中间支承。
在汽车行业中把连接发动机与前、后轴的万向传动装置简称传动轴。
传动轴设计应能满足所要传递的扭矩与转速。
现轻型载货汽车多采用不等速万向节传动轴。
2传动轴设计2.1传动轴万向节、花键、轴管型式的选择根据整车提供发动机的最高转速、最大扭矩及变速箱提供的一档速比,及由后轴负荷车轮附着力,计算得扭矩,由两者比较得出的最小扭矩来确定传动轴的万向节、花键、轴管型式。
a按最大附着力计算传动轴的额定负荷公式:Mψmax=G·r k·ψ/i oG满载时驱动轴上的负荷r k车轮的滚动半径ψ车轮与地面的附着系数i o主减速器速比b按发动机最大扭矩计算传动轴的额定负荷公式:Mψmax =M·i k1·i p/nM 发动机最大扭矩i k1变速器一档速比i p 分动器低档速比n 使用分动器时的驱动轴数按《汽车传动轴总成台架试验方法》中贯定选取以上二者较小值为额定负荷。
考虑到出现最大附着力时的工况是紧急制动工况此时的载荷转移系数为μ因此实际可利用最大附着力矩:M ψmaxo = M max ·μ传动轴的试验扭矩:由汽车设计丛书《传动轴和万向节》中得知:一般总成的检查扭矩为设计扭矩的1.5-2.0倍。
传动轴设计中轴管与万向节的设计扭矩也应选取1.5-2.0倍的计算扭矩,以满足整车使用中的冲击载荷。
轴管扭转应力公式:τ=16000DM π(D 4-d 4)<[τ] =120N/ mm2D 轴管直径; d 轴管内径;M 变速箱输出最大扭矩;花键轴的扭转应力:τ=16000M πD 23<[τ] =350N/ mm 2D 2花键轴花键底径;D 2=27.667mm 。
Z 花键齿数 m 花键模数M变速箱输出最大扭矩;传动轴花键齿侧的挤压应力:δ=2×TΨ×Z×m×L×Z×m在25-50N.mm2推荐范围内Ψ各齿载荷不均系数;Z花键齿数;L花键齿的最短工作长度长度;m花键模数;2.2传动轴的临界转速计算传动轴的临界转速。
传动轴和万向节设计
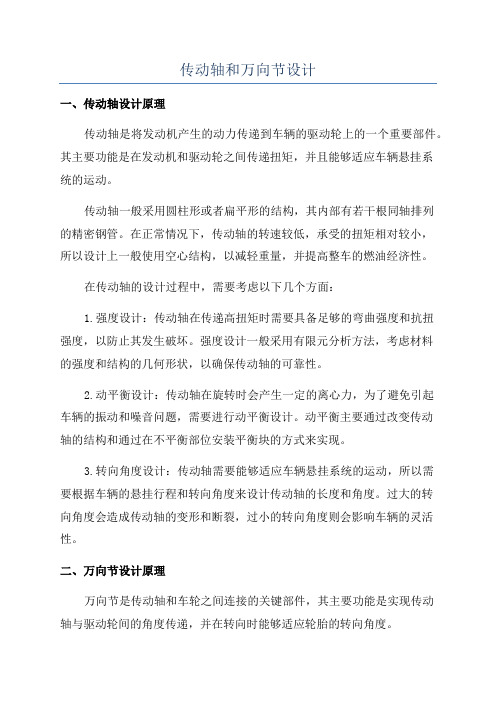
传动轴和万向节设计一、传动轴设计原理传动轴是将发动机产生的动力传递到车辆的驱动轮上的一个重要部件。
其主要功能是在发动机和驱动轮之间传递扭矩,并且能够适应车辆悬挂系统的运动。
传动轴一般采用圆柱形或者扁平形的结构,其内部有若干根同轴排列的精密钢管。
在正常情况下,传动轴的转速较低,承受的扭矩相对较小,所以设计上一般使用空心结构,以减轻重量,并提高整车的燃油经济性。
在传动轴的设计过程中,需要考虑以下几个方面:1.强度设计:传动轴在传递高扭矩时需要具备足够的弯曲强度和抗扭强度,以防止其发生破坏。
强度设计一般采用有限元分析方法,考虑材料的强度和结构的几何形状,以确保传动轴的可靠性。
2.动平衡设计:传动轴在旋转时会产生一定的离心力,为了避免引起车辆的振动和噪音问题,需要进行动平衡设计。
动平衡主要通过改变传动轴的结构和通过在不平衡部位安装平衡块的方式来实现。
3.转向角度设计:传动轴需要能够适应车辆悬挂系统的运动,所以需要根据车辆的悬挂行程和转向角度来设计传动轴的长度和角度。
过大的转向角度会造成传动轴的变形和断裂,过小的转向角度则会影响车辆的灵活性。
二、万向节设计原理万向节是传动轴和车轮之间连接的关键部件,其主要功能是实现传动轴与驱动轮间的角度传递,并在转向时能够适应轮胎的转向角度。
万向节一般由内球和外球组成,内球有两个半球形的凹槽,外球有两个凸槽,内外球通过一个钢球来连接。
当传动轴发生转动时,内外球可以相对转动,以适应车轮的角度变化。
在万向节的设计中,需要考虑以下几个因素:1.角度传递:万向节需要能够在不同角度下传递扭矩,并且保持稳定的工作状态。
在设计中需要注意内外球的形状和尺寸,以确保扭矩的传递效果和稳定性。
2.脱落力设计:万向节在工作过程中会产生较高的脱落力,为了保证其可靠性,需要进行脱落力分析和设计。
一般采用优化设计或者增加连接脱落力的结构,以确保万向节在承受高负荷时不发生脱落。
3.寿命设计:万向节在工作过程中会产生较大的摩擦和磨损,所以需要进行寿命设计。
传动轴毕业设计

传动轴毕业设计引言传动轴是一种重要的机械元件,常用于传递转矩和旋转运动。
它在车辆、工业设备等领域中广泛应用,扮演着重要的角色。
本文将探讨传动轴的设计原理、制造工艺以及性能优化等相关内容。
设计原理1. 传动轴的功能传动轴主要用于将发动机的转速和转矩传递到车辆的传动系统或工业设备中。
它的主要功能包括: - 传递转矩:承受发动机的输出转矩,并将其传递到车轮或设备中。
- 转速变换:根据需要,通过不同的传动比例将发动机的高速旋转转化为车轮或设备所需的合适转速。
2. 传动轴的设计要点传动轴的设计要考虑以下几个要点: - 强度和刚度:传动轴在工作时需要承受较大的转矩和振动载荷,因此需要具备足够的强度和刚度,以保证其不会发生断裂或过大的形变。
- 动平衡:由于传动轴在高速旋转时会产生离心力,因此需要进行动平衡处理,以减少振动和噪音。
- 转速匹配:传动轴的转速应与驱动和被驱动部件相匹配,以确保传动效率和安全性。
- 安装和连接方式:传动轴需要与其他部件连接,因此其安装和连接方式也需要考虑,以保证连接的可靠性和便于维修。
制造工艺传动轴的制造工艺通常包括以下几个步骤: ### 1. 材料选择传动轴通常采用高强度合金钢或碳纤维复合材料制造。
材料的选择需要考虑强度、刚度、耐磨性以及成本等因素。
2. 加工工艺传动轴的加工工艺包括以下几个步骤: - 车削:将原材料进行车削加工,使其具备所需的外形尺寸和表面粗糙度。
- 淬火和调质:通过淬火和调质处理,提高传动轴的硬度和强度。
- 高精度磨削:使用高精度磨床对传动轴进行磨削,以提高其表面精度和减小误差。
- 平衡处理:对传动轴进行动平衡处理,以减少振动和噪音。
3. 表面处理传动轴的表面通常需要进行镀铬、喷涂等处理,以提高其耐腐蚀性和装饰性。
性能优化为了提高传动轴的性能并满足各种工况的需求,可以考虑以下几个方面进行优化:### 1. 材料优化选用高强度、高刚度的材料,如碳纤维复合材料,以提高传动轴的强度和刚度,减小质量。
轿车传动轴的设计与校核

轿车传动轴的设计与校核汽车传动轴(Drive shaft)是汽车发动机与后轴之间的连接杆件,它的设计与校核对于汽车的性能和安全至关重要。
下面将详细介绍轿车传动轴的设计和校核,并阐述其重要性。
一、轿车传动轴的设计1.传动轴材料选择:传动轴需要承受发动机输出的扭矩和转速,因此需要选择具有高强度和耐疲劳性能的材料。
常用的材料包括碳素钢和合金钢。
2.传动轴的长度和直径:传动轴的长度和直径直接影响其刚度和承载能力。
根据发动机和后桥的布置,需要根据一定的分析和计算确定传动轴的合适长度和直径。
3.传动轴连接形式:传动轴通常是由两个或多个连接件组成的。
连接件通常采用螺纹连接、键式连接或插销连接等形式。
设计时需要考虑连接的强度和可靠性。
4.传动轴的平衡:传动轴在高速运转时会产生振动和失衡力。
为了提高行驶的平稳性和减少振动,传动轴需要进行动平衡。
二、轿车传动轴的校核1.扭矩校核:传动轴需要承受发动机输出的扭矩,并将其传递到后轴。
校核时需要考虑发动机的最大输出扭矩,计算传动轴受力情况并选择合适的材料和尺寸。
2.转速校核:传动轴的转速会影响其受力情况和疲劳寿命。
校核时需要根据发动机的最大转速和后桥的传动比,计算传动轴的转速,并选择合适的材料和尺寸。
3.弯曲校核:传动轴在运行过程中会受到弯曲力的作用。
校核时需要根据传动轴的长度、支撑方式和承载情况,计算传动轴的弯曲应力,并选择合适的材料和尺寸。
4.疲劳寿命校核:传动轴在长时间的运行过程中需要承受来自发动机的扭矩和转速的交替作用,容易产生疲劳破坏。
校核时需要根据传动轴的应力、材料的疲劳强度和工作寿命要求,进行疲劳强度校核。
三、轿车传动轴设计与校核的重要性1.提高传动效率:良好的传动轴设计可以减少能量的损耗,提高传动效率,使汽车在行驶过程中更加经济高效。
2.保证安全性:传动轴承载着发动机输出的扭矩和转速,如果传动轴设计不合理或存在缺陷,可能导致传动轴断裂或失效,严重影响行车安全。
传动轴设计及应用演示文稿
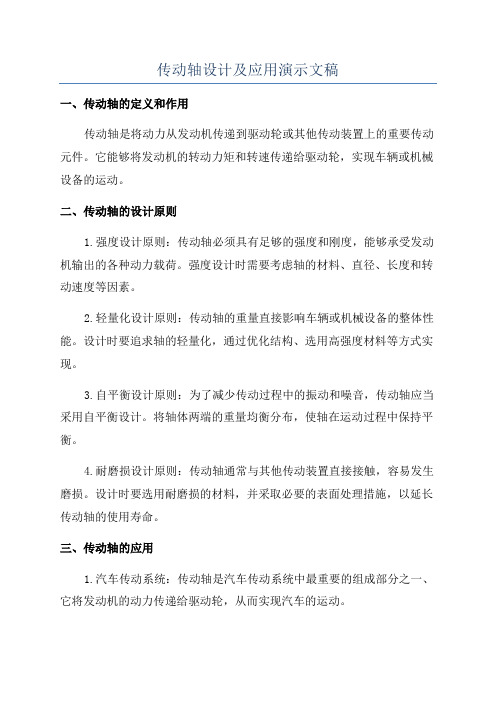
传动轴设计及应用演示文稿一、传动轴的定义和作用传动轴是将动力从发动机传递到驱动轮或其他传动装置上的重要传动元件。
它能够将发动机的转动力矩和转速传递给驱动轮,实现车辆或机械设备的运动。
二、传动轴的设计原则1.强度设计原则:传动轴必须具有足够的强度和刚度,能够承受发动机输出的各种动力载荷。
强度设计时需要考虑轴的材料、直径、长度和转动速度等因素。
2.轻量化设计原则:传动轴的重量直接影响车辆或机械设备的整体性能。
设计时要追求轴的轻量化,通过优化结构、选用高强度材料等方式实现。
3.自平衡设计原则:为了减少传动过程中的振动和噪音,传动轴应当采用自平衡设计。
将轴体两端的重量均衡分布,使轴在运动过程中保持平衡。
4.耐磨损设计原则:传动轴通常与其他传动装置直接接触,容易发生磨损。
设计时要选用耐磨损的材料,并采取必要的表面处理措施,以延长传动轴的使用寿命。
三、传动轴的应用1.汽车传动系统:传动轴是汽车传动系统中最重要的组成部分之一、它将发动机的动力传递给驱动轮,从而实现汽车的运动。
2.工业机械传动:传动轴广泛应用于各种类型的工业机械中,如数控机床、风力发电机组、钢铁设备等,实现动力的传递和转动。
3.农业机械传动:传动轴用于农业机械中,如拖拉机、收割机等。
它将发动机的动力传递给农机各个部位,实现农业机械的工作。
4.船舶传动系统:传动轴是船舶传动系统中的重要组成部分。
它将主机的动力传递给螺旋桨,使船舶前进或后退。
5.轨道交通传动:传动轴广泛应用于轨道交通系统中,如火车、地铁等。
它将电动机的动力传递给车轮,实现车辆的运动。
四、传动轴的设计案例以汽车传动轴为例,对其设计进行详细介绍。
汽车传动轴的设计要求:1.强度要求高:传动轴需要承受高强度的扭矩和冲击载荷。
2.轻量化设计:传动轴的重量直接影响汽车的燃油消耗和操控性能。
3.自平衡设计:传动轴需要在高速运动中保持平衡,减少振动和噪音。
4.耐磨损设计:传动轴需要与齿轮、万向节等传动装置直接接触,容易发生磨损。
汽车传动轴设计资料

五十铃货车传动轴设计第一章五十铃货车原始数据及设计要求发动机的输出扭矩:最大扭矩318.5N·m/2000r/min;轴距:3360mm;变速器传动比: 五挡0.787 ,一挡6.378,轮距:前轮1760毫米,后轮1610毫米,载重量5000千克设计要求:只设计直轴部分,进行受力分析,弯、扭,强度校核,画图第二章万向传动轴的结构特点及基本要求万向传动轴一般是由万向节、传动轴和中间支承组成。
主要用于在工作过程中相对位置不节组成。
伸缩套能自动调节变速器与驱动桥之间距离的变化。
万向节是保证变速器输出轴与驱动桥输入轴两轴线夹角的变化,并实现两轴的等角速传动。
一般万向节由十字轴、十字轴承和凸缘叉等组成。
传动轴是一个高转速、少支承的旋转体,因断改变的两根轴间传递转矩和旋转运动。
重型载货汽车根据驱动形式的不同选择不同型式的传动轴。
一般来讲4×2驱动形式的汽车仅有一根主传动轴。
6×4驱动形式的汽车有中间传动轴、主传动轴和中、后桥传动轴。
6×6驱动形式的汽车不仅有中间传动轴、主传动轴和中、后桥传动轴,而且还有前桥驱动传动轴。
在长轴距车辆的中间传动轴一般设有传动轴中间支承.它是由支承架、轴承和橡胶支承组成。
传动轴是由轴管、伸缩套和万向此它的动平衡是至关重要的。
一般传动轴在出厂前都要进行动平衡试验,并在平衡机上进行了调整。
因此,一组传动轴是配套出厂的,在使用中就应特别注意。
图 2-1? 万向传动装置的工作原理及功用图 2-2? 变速器与驱动桥之间的万向传动装置基本要求:1.保证所连接的两根轴相对位置在预计范围内变动时,能可靠地传递动力。
2.保证所连接两轴尽可能等速运转。
3.由于万向节夹角而产生的附加载荷、振动和噪声应在允许范围内。
4.传动效率高,使用寿命长,结构简单,制造方便,维修容易等第三章五十铃万向传动轴结构分析及选型由于五十铃货车轴距不算太长,且载重量5吨属中型货车,所以不选中间支承,只选用一根主传动轴,货车发动机一般为前置后驱,由于悬架不断变形,变速器或分动器输出轴轴线之间的相对位置经常变化,根据货车的总体布置要求,将离合器与变速器、变速器与分动器之间拉开一段距离,考虑到它们之间很难保证轴与轴同心及车架的变形,所以采用十字轴万向传动轴,为了避免运动干涉,在传动轴中设有由滑动叉和花键轴组成的伸缩节,以实现传动轴长度的变化。
汽车设计五(万向传动轴设计)
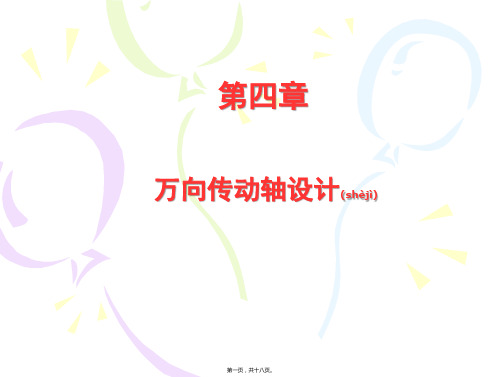
速度有关系式
,这样有
T2
1 sin 2 cos2 1 cos
T1
(4-3)
显然,当
最小时,从动轴上的转矩为最大
;当
最大时,从动轴上的转矩为最小
值与最小值之间每一转变化两次。
。T1与
第十页,共十八页。
一定时,T2在其最大
附加(fùjiā)弯曲力偶矩的分析
具有夹角 的十字轴万向节,仅在主动轴驱
动(qū dònɡ)转矩和从动轴反转矩的作用下是不能 平衡的。从万向节叉与十字轴之间的约束关系分析
第三页,共十八页。
第二节 万向节结构方案(fāng àn)分析
万向节分为刚性万向节和挠性万向节。
刚性万向节可分为不等速万向节(如十字轴式)、准等速万向节(如双联式、凸块 式、三销轴式等)和等速万向节(如球叉式、球笼式等)。
不等速万向节是指万向节连接的两轴夹角大于零时,输出(shūchū)轴和 输入轴之间以变化的瞬时角速度比传递运动的万向节。
第九页,共十八页。
第三节 万向传动的运动(yùndòng)和受力分析
一、单十字轴万向节传动
当十字轴万向节的主动轴与从动轴存在一定夹角α时, 主动轴的角速度 与从动轴的角速度 之间存在如下的关系
2 cos 由于cos 是周期为2 的周期1函数sin,2 所c以os2 1
(4-1) 也为同周期的周期函数。当
第四章
万向传动轴设计(shèjì)
第一页,共十八页。
第四章 万向传动轴设计(shèjì)
• 第一节 概述
•
第二节 万向节结构方案(fāng àn)分析
• 第三节 万向传动的运动和受力分析
• 第四节 传动轴结构分析与设计
第二页,共十八页。
汽车传动轴毕业设计
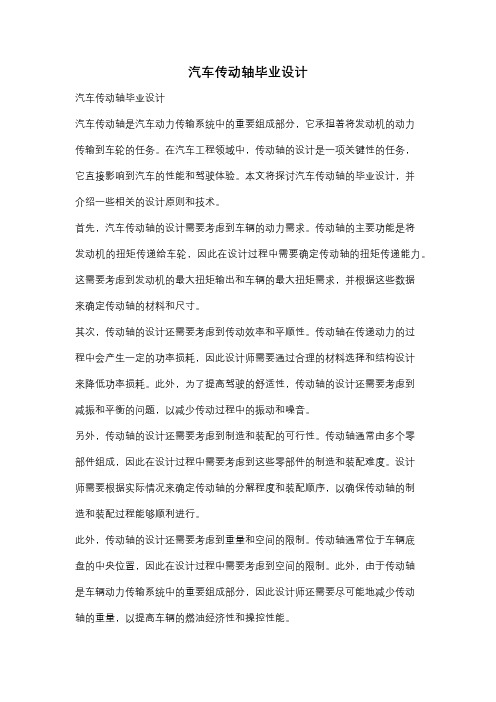
汽车传动轴毕业设计汽车传动轴毕业设计汽车传动轴是汽车动力传输系统中的重要组成部分,它承担着将发动机的动力传输到车轮的任务。
在汽车工程领域中,传动轴的设计是一项关键性的任务,它直接影响到汽车的性能和驾驶体验。
本文将探讨汽车传动轴的毕业设计,并介绍一些相关的设计原则和技术。
首先,汽车传动轴的设计需要考虑到车辆的动力需求。
传动轴的主要功能是将发动机的扭矩传递给车轮,因此在设计过程中需要确定传动轴的扭矩传递能力。
这需要考虑到发动机的最大扭矩输出和车辆的最大扭矩需求,并根据这些数据来确定传动轴的材料和尺寸。
其次,传动轴的设计还需要考虑到传动效率和平顺性。
传动轴在传递动力的过程中会产生一定的功率损耗,因此设计师需要通过合理的材料选择和结构设计来降低功率损耗。
此外,为了提高驾驶的舒适性,传动轴的设计还需要考虑到减振和平衡的问题,以减少传动过程中的振动和噪音。
另外,传动轴的设计还需要考虑到制造和装配的可行性。
传动轴通常由多个零部件组成,因此在设计过程中需要考虑到这些零部件的制造和装配难度。
设计师需要根据实际情况来确定传动轴的分解程度和装配顺序,以确保传动轴的制造和装配过程能够顺利进行。
此外,传动轴的设计还需要考虑到重量和空间的限制。
传动轴通常位于车辆底盘的中央位置,因此在设计过程中需要考虑到空间的限制。
此外,由于传动轴是车辆动力传输系统中的重要组成部分,因此设计师还需要尽可能地减少传动轴的重量,以提高车辆的燃油经济性和操控性能。
最后,传动轴的设计还需要考虑到可靠性和耐久性。
传动轴在汽车运行过程中承受着较大的负荷和振动,因此设计师需要选择合适的材料和加工工艺来确保传动轴的可靠性和耐久性。
此外,设计师还需要考虑到传动轴的维修和更换的问题,以便在需要时能够方便地进行维修和更换。
综上所述,汽车传动轴的毕业设计是一项复杂而重要的任务。
设计师需要考虑到车辆的动力需求、传动效率、平顺性、制造和装配的可行性、重量和空间的限制,以及可靠性和耐久性等方面的问题。
传动轴设计

传动轴设计1.设计参数1.所设计的汽车的载重量为32吨,驱动形式为发动机前置、6轮驱动,汽车的最高时速为max 85Km/h a V =。
斯达—斯太尔1491.280/038/66? ,其发动机的型号为WD 615.67。
2 .WD 615.67发动机的参数如表2—1:max P e ?最大功率,KW ;r η?传动系效率,取0.95r η=; g ?重力加速度,210m/s g =;r f ?滚动阻力系数,货车取0.02f =; D C ?空气阻力系数,0.9D C =;A ?汽车正面投影面积,2m1A B H =,1B ?前轮距,对于重型汽车:12m B ≈;H ?汽车总高,3m H ≈。
所以:21236m A B H ==?=max a V ?最高车速,max 85Km/h a V =;a m ?汽车总质量,Κg a m =32000。
emax T ?发动机的最大输出转矩,emax T N m =1070静态滚动半径 Rstat=0.376m 动态滚动半径 Rdyn=0.401m(N m/r/min)1070/14002.传动轴驱动形式的汽车的传动轴有主传动轴,中、后桥传动轴和前桥驱动轴。
662.1 传动轴概述传动轴是由轴管、伸缩套和万向节组成。
伸缩套能自动调节变速器与驱动桥之间的距离的变化。
万向节是保证变速器输出轴与驱动桥输入轴两轴线夹角的变化,并实现两轴的等角速传动。
一般万向节由十字轴、十字轴承和凸缘叉等组成,重型汽车中,为了达到传递较大转矩的目的,十字轴承采用滚柱十字轴轴承,并配合以短而粗的十字轴。
在轴承端面设蝶形弹簧,以压紧滚柱。
十字轴的端面增加具有螺旋槽的强化尼龙垫片以防止大角或大转矩传递动力时烧结。
传统结构的传动轴伸缩套是将花键套与凸缘叉焊接在一起,将花键轴焊接在传动轴管上。
我们决定采用的是GWB公司所生产的传动轴,它是将花键轴与传动轴关焊接成一体,将花键轴与凸缘叉制成一体以便于挤压成型。
传动轴设计指南范文
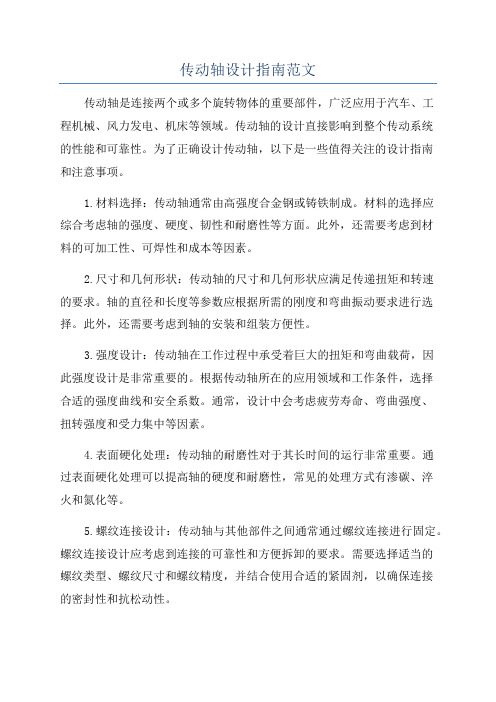
传动轴设计指南范文传动轴是连接两个或多个旋转物体的重要部件,广泛应用于汽车、工程机械、风力发电、机床等领域。
传动轴的设计直接影响到整个传动系统的性能和可靠性。
为了正确设计传动轴,以下是一些值得关注的设计指南和注意事项。
1.材料选择:传动轴通常由高强度合金钢或铸铁制成。
材料的选择应综合考虑轴的强度、硬度、韧性和耐磨性等方面。
此外,还需要考虑到材料的可加工性、可焊性和成本等因素。
2.尺寸和几何形状:传动轴的尺寸和几何形状应满足传递扭矩和转速的要求。
轴的直径和长度等参数应根据所需的刚度和弯曲振动要求进行选择。
此外,还需要考虑到轴的安装和组装方便性。
3.强度设计:传动轴在工作过程中承受着巨大的扭矩和弯曲载荷,因此强度设计是非常重要的。
根据传动轴所在的应用领域和工作条件,选择合适的强度曲线和安全系数。
通常,设计中会考虑疲劳寿命、弯曲强度、扭转强度和受力集中等因素。
4.表面硬化处理:传动轴的耐磨性对于其长时间的运行非常重要。
通过表面硬化处理可以提高轴的硬度和耐磨性,常见的处理方式有渗碳、淬火和氮化等。
5.螺纹连接设计:传动轴与其他部件之间通常通过螺纹连接进行固定。
螺纹连接设计应考虑到连接的可靠性和方便拆卸的要求。
需要选择适当的螺纹类型、螺纹尺寸和螺纹精度,并结合使用合适的紧固剂,以确保连接的密封性和抗松动性。
6.平衡设计:传动轴的平衡性对于减小振动和噪音非常重要。
在设计中,应对轴进行静平衡和动平衡的考虑,以确保轴的旋转平衡性。
7.温度影响:传动轴在工作过程中可能会受到高温影响,尤其是在摩擦剧烈的情况下。
因此,在设计中需要考虑轴的热膨胀系数和热导率等参数,以确保传动轴的稳定性和可靠性。
8.加工和装配:传动轴的加工和装配应满足精度要求,保证轴的圆度、直径和轴承孔的配合度。
此外,装配时需要避免轴与其他部件之间的磨擦和干涉。
总之,传动轴的设计需要综合考虑材料选择、尺寸和几何形状、强度设计、表面硬化处理、螺纹连接设计、平衡设计、温度影响、加工和装配等方面的要求。
传动轴设计说明书
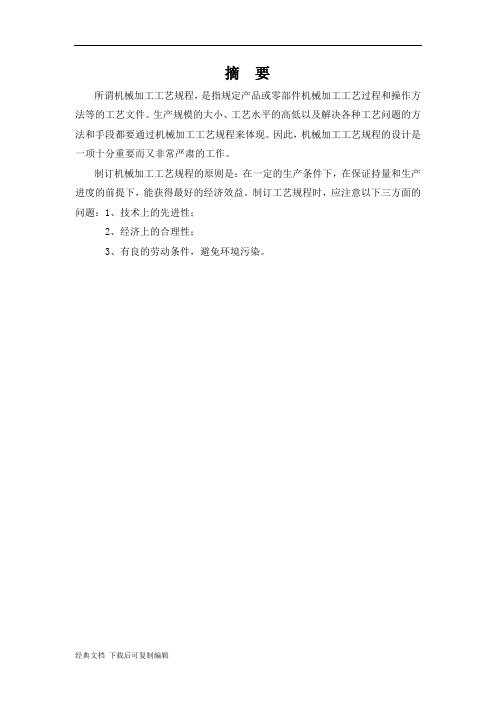
所谓机械加工工艺规程,是指规定产品或零部件机械加工工艺过程和操作方法等的工艺文件。
生产规模的大小、工艺水平的高低以及解决各种工艺问题的方法和手段都要通过机械加工工艺规程来体现。
因此,机械加工工艺规程的设计是一项十分重要而又非常严肃的工作。
制订机械加工工艺规程的原则是:在一定的生产条件下,在保证持量和生产进度的前提下,能获得最好的经济效益。
制订工艺规程时,应注意以下三方面的问题:1、技术上的先进性;2、经济上的合理性;3、有良的劳动条件,避免环境污染。
第一节传动轴(批量为200件)机械加工工艺规程设计一、传动轴的用途二、传动轴的技术要求三、审查传动轴的工艺性四、确定传动轴的生产类型第二节确定毛坯、绘制毛坯简图一、选择毛坯二、确定毛坯的尺寸公差和机械加工余量三、绘制传动轴锻造毛坯简图第三节拟定传动轴工艺路线一、定位基准的选择二、表面加工方法的确定三、加工阶段的划分四、工序的集中与分散五、工序顺序的安排六、确定工艺路线第四节机床设备及工艺装备的选用一、机床设备的选用二、工艺装备的选用第五节加工余量、工序尺寸和公差的确定一、G轴外圆面φ40的确定二、E轴外圆面φ30的确定三、M轴外圆面φ35的确定四、F轴右边部分外圆面φ30的确定五、F轴左边部分外圆面φ30的确定六、N轴外圆面φ25的确定七、M20x1.5螺纹的加工第六节切削用量、时间定额的计算一、切削用量的计算二、时间定额的计算第七节心得体会第八节参考文献第九节附录第一节传动轴(批量为200件)机械加工工艺规程设计一、传动轴的用途传动轴在各种机械或传动系统中广泛使用,用来传递动力。
在传力过程中主要承受交变扭转负荷或有冲击,因此该零件应具有足够的强度、刚度和韧性,以适应其工作条件。
该零件的主要工作表面为E、M、F、N四个阶梯轴的外圆表面,它们的精度和表面粗糙度要求很高,在设计工艺规程时应重点予以保证。
二、传动轴的技术要求无该传动轴零件形状为较简单的阶梯轴,结构简单。
汽车传动轴设计
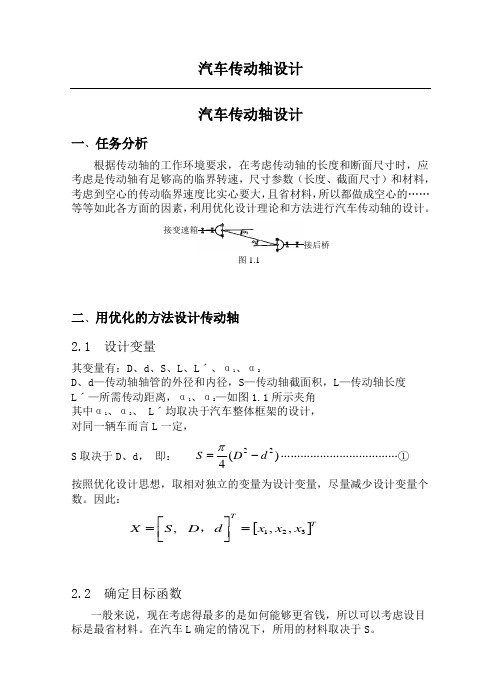
汽车传动轴设计一、任务分析根据传动轴的工作环境要求,在考虑传动轴的长度和断面尺寸时,应考虑是传动轴有足够高的临界转速,尺寸参数(长度、截面尺寸)和材料,考虑到空心的传动临界速度比实心要大,且省材料,所以都做成空心的…… 等等如此各方面的因素,利用优化设计理论和方法进行汽车传动轴的设计。
二、用优化的方法设计传动轴 2.1 设计变量其变量有:D 、d 、S 、L 、L ˊ、α1、α2D 、d —传动轴轴管的外径和内径,S —传动轴截面积,L —传动轴长度 L ˊ—所需传动距离,α1、α2—如图1.1所示夹角 其中α1、α2、 L ˊ均取决于汽车整体框架的设计, 对同一辆车而言L 一定, S 取决于D 、d , 即: )(422d D S -=π………………………………①按照优化设计思想,取相对独立的变量为设计变量,尽量减少设计变量个数。
因此:[]TTx x x d D S X 321,,,=⎥⎦⎤⎢⎣⎡=,2.2 确定目标函数一般来说,现在考虑得最多的是如何能够更省钱,所以可以考虑设目标是最省材料。
在汽车L 确定的情况下,所用的材料取决于S 。
接变速箱接后桥图1.1使S 的值在满足强度要求的情况下最小便成为了这次设计的目的。
即:)(4)(22d D x f -=π2.3 建立约束条件2.3.1传动轴应有足够高的临界转速临界转速:当传动轴的工作转速接近于其弯曲固有频率,即出现共振现象,所以通常将其弯曲固有频率对应的轴的速度称为临界转速。
若固有频率为f (Hz ) 则:k n =2πf rad/s=60 f r/minJ -抗弯惯性矩m kf π21=ρπLd D m ⋅-=)422(代入f 式,代入k n =60 f 整理后得2228102.1Ld D n k +⨯=设计传动轴时通常取0.2~2.1max=n n kn max -传动轴最高转速 m a x 222228353.152102.1n d D L d D n k ⋅≤+=+⨯=δ …………②δ—临界安全系数)(min x f 35384L EJ k =)(6444d D DJ -=π2.3.2传动轴应有足够的扭转强度设传动轴传递的最大转矩为Ts ,则截面上最大剪切应力[]τπτ≤-=⋅=)(16244max d D T D DI T s P s …………………………③ I p -极惯矩 32)(44d D I P -=π[]τ——许用应力,;2.3.3 传动轴应满足空心轴扭转失稳条件要求按最大扭转应力验算:2/3max )(292.0D d D E -≤τ……………………………………④E —传动轴材料的弹性模量,25/101.2mm N E ⨯=2.3.4 传动轴应满足制造工艺条件要求2.3≥-d D …………………………………………⑤ 2.3.5 传动轴外径尺寸不能过大可设 100≤D …………………………………………⑥ 根据以上的各条约束条件以及①式,可建立以下数学优化模型: []TTx x x d D S X 321,,,=⎥⎦⎤⎢⎣⎡=,)4)(min 22d D x f S -==(πmax 222228353.152102.1n d D L d D n k ⋅≤+=+⨯=δ[]τπτ≤-=⋅=)(16244max d D T D DI T s P s2/3max )(292.0Dd D E -≤τ 2.3≥-d D 100≤D三、优化算法的实现3.1优化设计理论优化设计方法是应用数学最优化远离解决实际问题的设计方法。
传动轴毕业设计

传动轴毕业设计一、选题背景及意义传动轴是汽车、机械等工业领域中不可或缺的重要部件,其作用是将发动机产生的动力传递到车轮或机器的运转部分,使其能够正常运转。
因此,传动轴的设计和制造对于整个机械系统的性能和稳定性具有至关重要的影响。
本文旨在探讨传动轴的设计和制造过程以及相关技术。
二、研究内容1. 传动轴基础知识介绍传动轴的定义、分类、结构组成等基础知识,为后续研究提供必要的背景知识。
2. 传动轴设计原理探讨传动轴设计所需考虑的因素,如扭矩、转速、弯曲应力等,并介绍常用计算公式和方法。
3. 传动轴材料选择分析不同材料在传动轴中的应用情况及优缺点,并根据实际需求进行合理选择。
4. 传动轴制造工艺介绍常见的制造工艺,如锻造、铸造、冷拔等,并比较各种工艺在成本、质量和效率等方面的优劣。
5. 传动轴性能测试介绍传动轴的性能测试方法,如扭矩试验、弯曲试验、拉伸试验等,以及测试结果的分析和评估。
三、研究方法本文采用文献资料法和实验法相结合的方式进行研究。
通过查阅相关文献,了解传动轴的基础知识和设计原理,并结合实际情况进行实验验证。
四、预期成果1. 掌握传动轴的基础知识和设计原理;2. 熟悉不同材料在传动轴中的应用情况及优缺点;3. 了解传动轴制造工艺,并比较各种工艺在成本、质量和效率等方面的优劣;4. 掌握传动轴性能测试方法,并能够进行测试结果分析和评估。
五、进度安排1. 第一周:查阅相关文献,了解传动轴基础知识;2. 第二周:探讨传动轴设计原理;3. 第三周:分析不同材料在传动轴中的应用情况及优缺点;4. 第四周:介绍常见的制造工艺,并比较各种工艺在成本、质量和效率等方面的优劣;5. 第五周:介绍传动轴性能测试方法,以及测试结果的分析和评估;6. 第六周:撰写毕业设计论文。
六、结论本文系统地介绍了传动轴的基础知识、设计原理、材料选择、制造工艺和性能测试等方面的内容,为相关领域的研究者提供了一定的参考和指导。
同时,通过实验验证,也为传动轴的设计和制造提供了可靠的依据。
传动轴设计计算

编号:传动轴设计计算书编制:日期:校对:日期:审核:日期:批准:日期:一.计算目的我们初步选定了传动轴,轴径选取Φ27(详见《传动轴设计方案书》),动力端选用球面滚轮万向节,车轮端选用球笼万向节。
左、右前轮分别由1根等速万向节传动轴驱动。
通过计算,校核选型是否合适。
二.计算方法本车传动轴设计不是传统载货车上从变速器到后驱动桥之间长轴传动设计,而是半轴传动设计。
而且传动轴材料采用高级优质合金钢,且热处理工艺性好,使传动轴的静强度和疲劳强度大为提高,因此计算中许用应力按照半轴设计采用含铬合金钢,如40Cr、42CrMo、40MnB,其扭转屈服极限可达到784 N/mm2左右,轴端花键挤压应力可达到196 N/mm2。
传动轴校核计算流程:1.1 轴管直径的校核校核:两端自由支撑、壁厚均匀的等截面传动轴的临界转速22281.2x10n e ld D += (r/min) 式中L 传动轴长,取两万向节之中心距:mm D 为传动轴轴管外直径:mm d 为传动轴轴管内直径:mm各参数取值如下:D =φ27mm ,d =0mm取安全系数K=n e /n max ,其中n max 为最高车速时的传动轴转速, 取安全系数K =n e /n max =1.2~2.0。
实际上传动轴的最大转速n max =n c /(i g ×i 0),r/min其中:n c -发动机的额定最大转速,r/min ;i g -变速器传动比; i 0-主减速器传动比。
1.2 轴管的扭转应力的校核校核扭转应力:τ=][1644τ≤)-(d D DT J(N/mm 2) ][τ……许用应力,取][τ=539N/mm 2[高合金钢(40Cr 、40MnB 等)、中频淬火抗拉应力≥980 N/mm 2,工程应用中扭转应力为抗拉应力的0.5~0.6,取该系数为0.55,由此可取扭转应力为539 N/mm 2,参考GB 3077-88]式中:T j ……传动系计算转矩,N ·mm ,2/k i i T T d g0g1x ema j η= N ·mT emax -发动机最大转矩N ·mm ; i g1-变速器一档传动比或倒档传动比; i g0-主减速器传动比k d -动载系数 η-传动效率1.3 传动轴花键齿侧挤压应力的校核 传动轴花键齿侧挤压应力的校核][)2)(4(2121j j ZLD D D D T σσ≤-+= (N/mm 2)式中:T j -计算转矩,N ·mm ; D 1,D 2-花键的外径和内径,mm ;Z ………花键齿数L ………花键有效长度][j σ……许用挤压应力,花键取][j σ=192 N/mm 2。
- 1、下载文档前请自行甄别文档内容的完整性,平台不提供额外的编辑、内容补充、找答案等附加服务。
- 2、"仅部分预览"的文档,不可在线预览部分如存在完整性等问题,可反馈申请退款(可完整预览的文档不适用该条件!)。
- 3、如文档侵犯您的权益,请联系客服反馈,我们会尽快为您处理(人工客服工作时间:9:00-18:30)。
五十铃货车传动轴设计
第一章五十铃货车原始数据及设计要求
发动机的输出扭矩:最大扭矩318.5N·m/2000r/min;轴距:3360mm;变速器传动比: 五挡0.787 ,一挡6.378,轮距:前轮1760毫米,后轮1610毫米,载
重量5000千克
设计要求:
只设计直轴部分,进行受力分析,弯、扭,强度校核,画图
第二章万向传动轴的结构特点及基本要求
万向传动轴一般是由万向节、传动轴和中间支承组成。
主要用于在工作过程中相对位置不节组成。
伸缩套能自动调节变速器与驱动桥之间距离的变化。
万向节是保证变速器输出轴与驱动桥输入轴两轴线夹角的变化,并实现两轴的等角速传动。
一般万向节由十字轴、十字轴承和凸缘叉等组成。
传动轴是一个高转速、少支承的旋转体,因断改变的两根轴间传递转矩和旋转运动。
重型载货汽车根据驱动形式的不同选择不同型式的传动轴。
一般来讲4×2
驱动形式的汽车仅有一根主传动轴。
6×4驱动形式的汽车有中间传动轴、主传
动轴和中、后桥传动轴。
6×6驱动形式的汽车不仅有中间传动轴、主传动轴和中、后桥传动轴,而且还有前桥驱动传动轴。
在长轴距车辆的中间传动轴一般设有传动轴中间支承.它是由支承架、轴承和橡胶支承组成。
传动轴是由轴管、伸缩套和万向此它的动平衡是至关重要的。
一般传动轴在出厂前都要进行动平衡试验,并在平衡机上进行了调整。
因此,一组传动轴是配套出
厂的,在使用中就应特别注意。
图 2-1? 万向传动装置的工作原理及功用
图 2-2? 变速器与驱动桥之间的万向传动装置
基本要求:
1.保证所连接的两根轴相对位置在预计范围内变动时,能可靠地传递动力。
2.保证所连接两轴尽可能等速运转。
3.由于万向节夹角而产生的附加载荷、振动和噪声应在允许范围内。
4.传动效率高,使用寿命长,结构简单,制造方便,维修容易等
第三章五十铃万向传动轴结构分析及选型
由于五十铃货车轴距不算太长,且载重量5吨属中型货车,所以不选中间支承,只选用一根主传动轴,货车发动机一般为前置后驱,由于悬架不断变形,变速器或分动器输出轴轴线之间的相对位置经常变化,根据货车的总体布置要求,将离合器与变速器、变速器与分动器之间拉开一段距离,考虑到它们之间很难保证轴与轴同心及车架的变形,所以采用十字轴万向传动轴,为了避免运动干涉,在传动轴中设有由滑动叉和花键轴组成的伸缩节,以实现传动轴长度的变化。
空心传动轴具有较小的质量,能传递较大的转矩,比实心传动轴具有更高的临界转速,
所以此传动轴管采用空心传动轴。
传动轴的长度和夹角及它们的变化范围,由汽车总布置设计决定。
设计时应保证在传动轴长度处在最大值时,花键套与花键轴有足够的配合长度;而在长度处于最小时,两者不顶死。
传动轴夹角大小会影响万向节十字轴和滚针轴承的寿命、万向传动效率和十字轴的不均匀性。
变化范围为3。
传动轴经常处于高速旋转状态下,所以轴的材料查机械零件手册选取40CrNi,适用于很重要的轴,具有较高的扭转强度。
3.1传动轴管选择
传动轴管由低碳钢板制壁厚均匀、壁薄(1.5~3.0mm)、管径较大、易质量平衡、扭转强度高、弯曲刚度高、适用高速旋转的电焊钢管制成。
3.2 伸缩花键选择
选择矩形花键,用于补偿由于汽车行驶时传动轴两端万向节之间的长度变化。
为减小阻力及磨损,对花键齿磷化处理或喷涂尼龙,外层设有防尘罩,间隙小一些,以免引起传动轴的震动。
花键齿与键槽按对应标记装配,以保持传动轴总成的动平衡。
动平衡的不平衡度由电焊在轴管外的平衡片补偿。
装车时传动轴的伸缩花
键一端应靠近变速器,减小其轴向阻力和磨损。
其结构图如下:
图 3-1 万向传动轴—花键轴结构简图
1-盖子;2-盖板;3-盖垫;4-万向节叉;5-加油嘴;6-伸缩套;
7-滑动花键槽;8-油封;9-油封盖;10-传动轴管
第四章万向传动轴计算及强度校核
4.1传动轴的临界转速
长度一定时,传动轴断面尺寸的选择应保证传动轴有足够的强度和足够高的临界转速。
所谓临界转速,就是当传动轴的工作转速接近于其弯曲固有振动频率时,即出现共振现象,以致振幅急剧增加而引起传动轴折断时的转速。
传动轴的临界转速nk(r/min)为,安全系数K取2.0,适用于一般精度的伸缩花键
则有
(为发动机转速)
,
4.2传动轴计算转矩
4.3传动轴长度选择
根据轴距3360mm,初选传动轴支承长度为 mm,花键轴长度应小于支承长度,满足万向节与传动轴的间隙要求,取花键轴长度为
4.4传动轴管内外径确定
得
又
初取? ,? 则
——Lc为传动轴长度(mm),即两万向节中心之间的距离;dc和Dc分别为传动
轴轴管的内、外径(mm)
4.5传动轴扭转强度校核
由于传动轴只承受扭转应力而不承受弯曲应力,所以只需校核扭转强度,根据公
式有
?(为
轴管许用扭转应力)
上式说明设计参数满足扭转强度要求
4.6花键内外径确定
取安全系数2.27,则
——为许用扭转应力
——为花键转矩分布不均匀系数,取1.3
——花键外径
——花键内径
——为花键有效工作长度
B——为键齿宽
——为花键齿数
由于花键齿侧许用挤压应力较小,所以选用Lh较大尺寸的花键,查
GB/T1144-2001,取,,
,。
4.7花键挤压强度校核
当花键齿面硬度为35HRC时,许用挤压应力为
则,满足花键挤压强度。
4.8传动轴形位公差确定
通过查手册中轴的公差及基本偏差表,确定轴选用配合e7,此配合适用于有明显间隙、易于转动的支承配合,花键根据手册查得dh为f7,Dh为a11,B为d10,由此可确定轴的外径和内径分别为mm mm,花键外径跟内径分别为,,,,。
传动轴总成的不平衡是传动系弯曲振动的一个激励源,当高速旋转时,将产生明显的振动和噪声。
万向节中十字轴的轴向窜动、传动轴滑动花键中的间隙、传动轴总成两端连接处的定心精度、高速回转时传动轴的弹性变形、传动轴上点焊平衡片时的热影响等因素,都能改变传动轴总成的不平衡度。
提高滑动花键的耐磨性和万向节花键的配合精度、缩短传动轴长度并增加其弯曲刚度,都能降低传动轴的不平衡度。
为了消除点焊平衡片的热影响,应在冷却后再进行动平衡检验。
传动轴的不平衡度,对于五十铃货车,在1000~4000r/min时不大于50~100g.cm。
传动轴总成的径向全跳动不大于0.8mm。
轴管两端的摆差在其两端不大于0.5mm。
用3038N·m的扭矩试验焊接强度,焊接钢丝采用H08Mn2Si。