射出成型不良原因分析报告
射出成型常见不良现象级处理措施

射出成型中常见不良现象产生原因分析及对策以下所列举的成型中产生的不良原因及对策是指在一般情况下可能出现的﹐也仅以本人在工作中的一些心得﹐体验为例﹐如有不妥或不周之处﹐还请各位行家指正﹗(一)短射(不饱模)(1)短射(不饱模)﹔即是溶融塑料未能完全填充填满成型空间(模穴)各个角落的现象(2)原因及改善对策(见下表)(二)毛边(1)毛边﹔即是在分模面﹑流道周围及模仁镶块间隙内出现的膜状或毛刺状的多余胶料(2)原因及改善对策(见下表)*注﹔成型时间过长﹐模温过低而采用高压﹐高速射出也是产生毛边的常见原因(三)银线(1)银条(银线)即是在成型产品表面或表面附近﹐沿塑料流动方向﹐呈放射状的银白色条纹。
(2)原因及改善对策(见下表)(四)成品光泽度低(1)成品光泽度低是指成品表面光泽达不到质量要求﹐表面无折光度。
(2)原因及改善对策(见下表)(五)变形(1)变形可分为对角线的扭曲及平行边沿的曲翘两种﹐是成品成型中发生的不规则弯曲现象(2)原因及发善对策(见下表)(六)顶白(1)顶白(也叫白化)是指成品在脱模之际﹐在顶针或其它脱模部位出现白色痕迹(2)原因及改善对策(见下表)(七)结合线(1)结合线是指在成型中﹐二道或多道熔融材料融合时出现的细线状(2)原因及改善对策(见下表)(八)冲料痕(1)冲料痕是指熔融材料在进料点附近﹐以浇口为中心而呈现的条纹状(2)原因及改善对策(九)异色(黑纹)(1)异色(黑纹)是指在成型过程中﹐在成品表面出现的黑色或其它深色条纹(2)原因及改善对策(见下表)(十)气泡(1)气泡是熔融塑料中的水份﹐挥发气体于成型过成中被封入内部而残留的空动现象(2)原因及改善对策(见下表)射出换料要诀在射出成型作业中﹑换料﹑换色的问题﹐值得吾入深入探讨﹒如何以最快速的方法完成换料﹑换色﹐除可节省时间外﹐并可降低一笔相当可观的生产成本﹒一﹑同一材料之换色1﹒1同一材料的换色时﹐原则上从淡色材料换为深浓色材料﹐较从不透明材料换为透明材料容易﹒一般换色作业程序如下﹔(1)关斗漏料斗下部的进料挡门(2)空射数次﹐将加热料管内的材料全部射出(3)新材料加入漏斗(4)打开进料挡门﹐螺杆前进后退十数次直到换色完成﹒从不透明材料换为透明材料时﹐尤需拆除喷嘴头部份﹐清除残留的材料﹐必要时杆亦需抽出撤底清理﹐不可有残余料积存死角处﹒二﹑不同材料之换色2.1 不同材料的更换作业﹐是利用前后各材料的熔融黏度差﹐与加热管的温度控制来施行换料手续。
模具射出成型不良及其原因
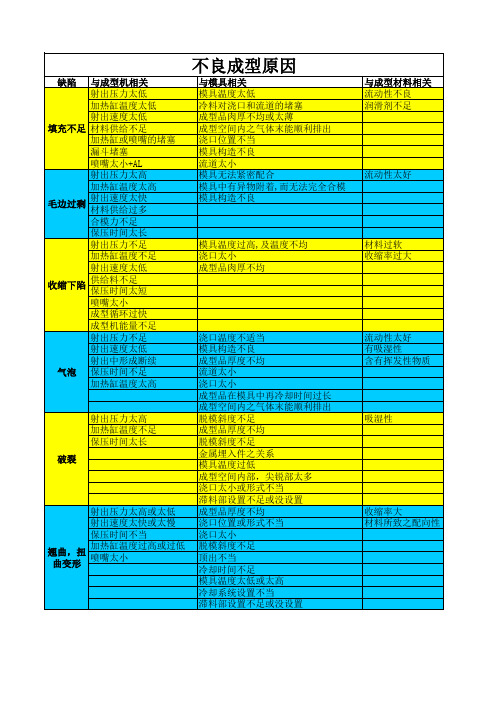
流动性太好
模具温度过高,及温度不均 浇口太小 成型品肉厚不均
材料过软 收缩率过大
射出压力太高 加热缸温度不足 保压时间太长 破裂
射出压力太高或太低 射出速度太快或太慢 保压时间不当 加热缸温度过高或过低 翘曲,扭 喷嘴太小 曲变形
浇口温度不适当 模具构造不良 成型品厚度不均 流道太小 浇口太小 成型品在模具中再冷却时间过长 成型空间内之气体末能顺利排出 脱模斜度不足 成型品厚度不均 脱模斜度不足 金属埋入件之关系 模具温度过低 成型空间内部,尖锐部太多 浇口太小或形式不当 滞料部设置不足或没设置 成型品厚度不均 浇口位置或形式不当 浇口太小 脱模斜度不足 顶出不当 冷却时间不足 模具温度太低或太高 冷却系统设置不当 滞料部设置不足或没设置
银条
烧焦
浇口或流道太小 浇口位置不当 模具温度过低 模具构造不良 模具温度过低 浇口太小 成型空间表面有水分 成型空间内之气体末能顺利排出 浇口太小 成型空间受油质或杂物质污染 顶出机构中之油脂渗入成形空间
材料固化过快 有吸湿性 润滑剂不足 流动性不良 有吸湿性 有挥发物 材料易分解
润滑剂不足 材料易分解
不良成型原因
与成型机相关 射出压力太低 加热缸温度太低 射出速度太低 填充不足 材料供给不足 加热缸或喷嘴的堵塞 漏斗堵塞 喷嘴太小+AL 射出压力太高 加热缸温度太高 射出速度太快 毛边过剩 材料供给过多 合模力不足 保压时间太长 射出压力不足 加热缸温度不足 射出速度太低 供给料不足 收缩下陷 保压时间太短 喷嘴太小 成型循环过快 成型机能量不足 射出压力不足 射出速度太低 射出中形成断续 气泡 保压时间不足 加热缸温度太高 缺陷 与模具相关 模具温度太低 冷料对浇口和流道的堵塞 成型品肉厚不均或太薄 成型空间内之气体末能顺利排出 浇口位置不当 模具构造不良 流道太小 模具无法紧密配合 模具中有异物附着,而无法完全合模 模具构造不良 与成型材料相关 流动性不良 润滑剂不足
成型不良分析

射出成形品的不良现象及原因射出成型作业因成形机的性质,作业者的成形技术及模具设计的缺陷,产生各种不良成形品,通常是交错影响。
不易把握真正的原因。
成形作业须究明不良原因,改善品质,降低不良率。
不良现象和发生之原因,通常有如下几项:缺料(SHORT-SHOT):塑料没有占满、动、静、镆闭合后的空间,形成缺料的现象,其原因:1. 计量设定不够,给料太少。
2. 射出速度太慢。
3. 射出压力太低。
4. 镆具温度太低。
5. 背压太低或无背压。
6. 离型前喷太多。
7. 加热筒温度设定太低。
毛头(FLASH):与第一项相反,塑料跑出,动,静镆闭合后的空间,形成芒刺状的现象,其原因:1. 计量设定太多,给料超过。
2. 射出历力过大。
3. 开镆压力不足。
4. 加热筒温度设定太高。
5. 动、静、镆接合不良。
6. 镆具温度过高。
黑点、异物(BLACK SPECKS)成品表面或内层夹有杂物,导致外观不良的现象。
这些杂物包括清洁剂、铁屑、胶带、纸片或以前成形而残留在加热筒内被烧焦的塑料粒等,其发生原因。
1. 换料时,料筒,加热筒或喷嘴未清除干凈。
2. 填料时胶带或纸袋屑渗入塑料粒内不查或纸袋表面污损、填料前未擦拭干凈。
3. 粉碎或押出处理不当。
4. 镆具表面不凈,成形前处理不良。
黑条、烧焦(BURN MARKS)成品表面出现黑色条纹,或死角处有烧焦痕迹,其发生原因。
1. 塑料在加热筒内停留太久,或温度太高。
2. 射出压力太高。
3. 射出速度太快。
4. 镆具排气不良。
5. 进料口、流道、料门太小或不光滑。
6. 空气渗入射出加热筒内,受高压生热而烧焦。
7. 螺杆回转速度过快。
8. 树脂润滑剂过多,热安全性差。
9. 镆具温度过高。
黄条、色变(DISCOLORATION)成品表面产生近黄色之纹路的现象,其原因。
1. 颜料分散性或热安定不足。
2. 参考第四项不良原因。
六 银条(SILVER STREAK)成品表面有水痕或水泡的现象,其原因。
常见射出成型不良原因及注意事项
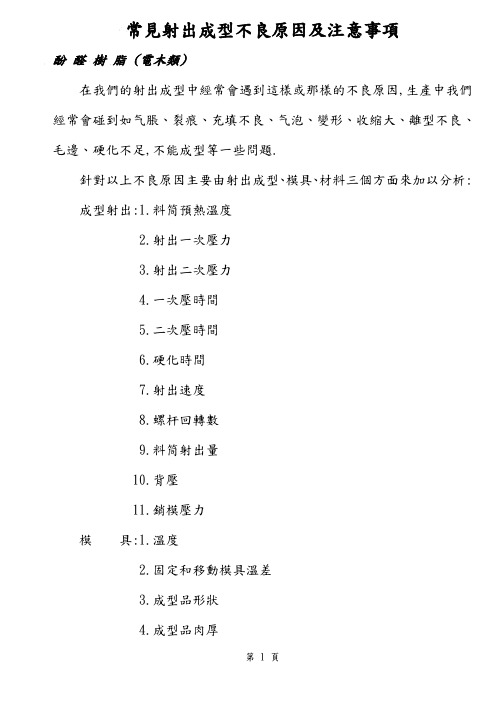
常見射出成型不良原因及注意事項
酚醛樹脂(電木類)
在我們的射出成型中經常會遇到這樣或那樣的不良原因,生產中我們經常會碰到如气脹、裂痕、充填不良、气泡、變形、收縮大、離型不良、毛邊、硬化不足,不能成型等一些問題.
針對以上不良原因主要由射出成型、模具、材料三個方面來加以分析: 成型射出:1.料筒預熱溫度
2.射出一次壓力
3.射出二次壓力
4.一次壓時間
5.二次壓時間
6.硬化時間
7.射出速度
8.螺杆回轉數
9.料筒射出量
10.背壓
11.銷模壓力
模具:1.溫度
2.固定和移動模具溫差
3.成型品形狀
4.成型品肉厚
5.澆口
6.注道
7.透气孔
8.設計構造
9.頂針
10.通气分配
11.表面
12.強度
13.材料漏出
材料:1.軟度
2.硬度
3.吸濕
4.材質
在成型中遇到上述異常時,可以用品管手法魚骨圖來分析
以上列魚骨圖的分布中我們可以看出在生產中出現不良原因,我們可以有針對性的對不良問題加以改善,當然還有許多原因待我們去檢討及分
析.。
射出成型不良原因简介
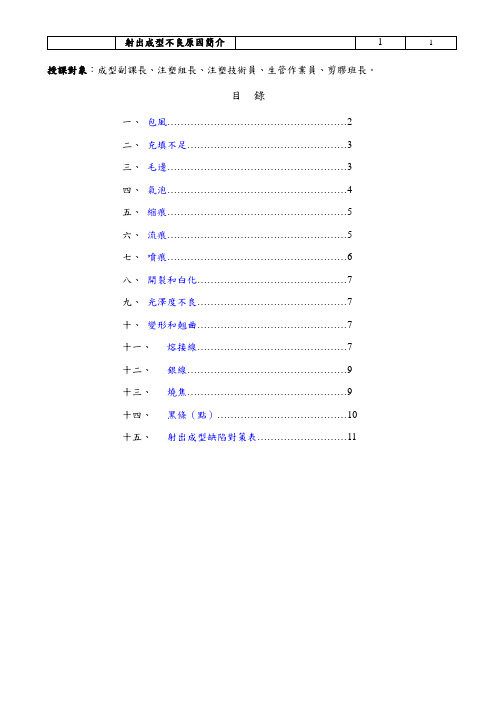
模具
1.模溫控制系統漏水。
2.模面形成凝結水。
射出成型機
1.熔膠溫度太高。2.射速太快。3.射壓太高。
4.螺桿轉速太快,塑化時剪切速率太大。
5.停留時間過長。
(3)解決方法
1.樹脂乾燥不足。
2.肉厚變動大的成品,型腔內的空氣難以排出,放慢射出速度。
3.提高背壓,放慢轉速。
十三、燒焦:
3.射壓或射速過低
射壓或射速過低,熔膠波前形成熔接線時,溫度已經降得太低,接合不良,線條明顯。
(3)解決方法
1.提高模具和料溫。
2.加快射出速度或增加射壓。
3.型腔內的空氣和揮發成分若妨礙樹脂的合流,要減慢射出速度。
十二、銀線:
(1)現象:成型品表面延著流向形成的噴濺狀線條。
(2)可能原因:
塑料
1.乾燥不足。
1.
(3)解決方法:
1.降低射速。
2.檢討製品設計。
3.檢討模具設計。(澆口、流澆道、排氣……)
二、充填不足:
(1)現象:樹脂沒有完全充填到模具型腔角落。
(2)可能原因:
1.樹脂的流動性不足,內壓不足。
2.可塑性不足。
3.氣體、空氣造成注射不足(逃氣)。
(3)解決方法:
1.提高最大射出壓力和射出速度,提高模具溫度和樹脂溫度。
3.循環時間(Cycle Time)不當
當循環時間太短時,塑料在料管內加溫不及,熔膠溫度低,即使勉強將型腔填滿,保壓時還是無法將塑膠壓實,留下熔膠在垂直流動方向的縮痕,狀如年輪。循環時間須延長到塑膠充分融化,熔膠溫度高到足以使得流動方向的縮痕無由產生為宜。
4.料管/噴嘴溫度太低。
(3)(3)解決方法
2.延長保壓時間或增加保壓壓力。
成形不良原因及对策

黑纹
黑色条纹 (black streak)
2:料管和螺杆真圆度偏差引起摩擦烧焦熔胶 3:射嘴过热,烧焦胶料 4:射嘴温度变化范围大
料头及进料点周围有黑色
过胶头组设计不良
序号
问题点
原因分析 1:塑料中之水份或挥发性物质因受压缩而呈现液态状, 当挤出射嘴进入模具后,压力突然下降,而使液态状被蒸发 而成气态,使得塑胶在与模具表面接触时,固化后因表面
成 形 不 良 原 因 及 对 策
造成塑胶产品不良因素主要起因於材料,模具,射出机,成品设计以及成型技术,当中成型技术更是决定成品好坏的重要关键,所以唯有充分了解不良品发生的原理,否则要花很多时间找 出其原因,走一大段冤枉路费力且耗时,以下就常见不良品发生的原因及其故障排除之解决对策,并将不良形态分为五大类 一.表面缺陷 序号
二、变形与尺寸不良 序号 问题点
2:塑料太冷.
2.1:增加料管温度. 2.2:提高模具温度. 2.3:增加螺杆背压.
B1
翘曲、变形
3:制品厚薄不均匀
3.1:调节螺杆后松退位置,减少入料. 3.2:降低射出压力. 3.3:控制或更改塑胶在浇口的流动.
4:脱模设计不良或安装不好. 5:模具温度不均匀. 6:过多废料在浇口周围. 7:保压过度. 1:模塑情况不稳定. 2:变更成形条件. B2 胶品尺寸改变 3:检查塑件时,周围的空气温度. 4:不固定.
A9
序号
问题点 1:模温过低. 2:塑胶粒含水量过高.
原因分析 1:提高模温. 2:烘干塑胶粒经降低含水量. 3:提高射出压力或保压. 4:增加浇口尺寸. 5:加强模具研磨.
改善对策
备
注
3:射出压力太低或保压不足. 表面不光泽 (粗糙) A10 4:浇口尺寸过小. 5:模具研磨太粗糙. 6:模壁有水份. 7:脱模剂过多. 8:射出速度太慢. 1:料温或模温过冷. 表面浮织白痕 表面浮织流痕 2:塑料除湿不完全或次料比例过高. 3:保压不足及射速不足. 4:排气孔不足或排气孔堵塞. 5:塑料过热. A11 颜色混炼不均 螺杆压缩比太小. 螺杆设计配套不适当. 原因分析 1:塑胶制品於太热时脱模.
射出成型不良原因——技术分析鱼骨图剖析
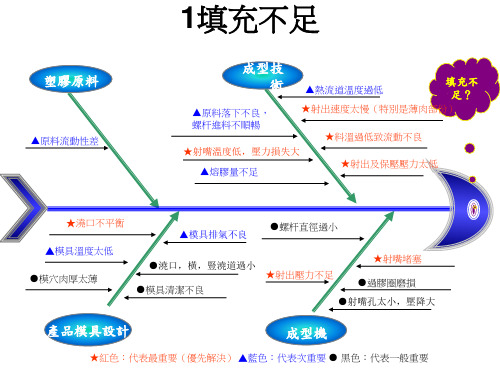
毛邊?
★保壓壓力太高
★料管溫度太高
●模具剛性不良 ▲模具合模有異物 ▲進澆點設計不良 ★模具密著性差 產生斷差 ●模具合模不良 ▲鎖模力不足
●模缸泄漏
產品模具設計
成型機
★紅色:代表最重要(優先解決) ▲藍色:代表次重要 ● 黑色:代表一般重要
8燒焦
●澆口位置及數量設計部當 ●澆口至熔接線部之 流動距離太長 ●模具排氣不良
★射嘴堵塞
★射速不足
產品模具設計
成型機
★紅色:代表最重要(優先解決) ▲藍色:代表次重要 ● 黑色:代表一般重要
3縮水,凹陷
塑膠原料 成型技 術
●冷卻溫度不夠
▲原料流動性差 ★射出壓力太低 ★保壓時間太短 ▲射出速度太快 ★保壓壓力不足 ★熔膠量不足 ★料溫過高(厚件) ▲模溫不當
●射速太快
★模具強度不足 ▲模溫太低
產品模具設計
成型機
★紅色:代表最重要(優先解決) ▲藍色:代表次重要 ● 黑色:代表一般重要
25白化
塑膠原料
▲原料中含有揮發性氣體 ▲原料流動性太好 ●射壓太大
成型技 術
●射速太低
白化?
★模具排氣不良
●鎖模力設定太高
產品模具設計
成型機
★紅色:代表最重要(優先解決) ▲藍色:代表次重要 ● 黑色:代表一般重要
5銀線,銀條
塑膠原料
★原料中含有水 分等揮發性氣體 ★料溫太高,過熱分解 ▲異材混料 ▲染料分解 ●射速太快排氣不良 ●射出壓力太高
成型技 術
★原料停留時間太長, 部分發生過熱現象
銀線, 銀條?
●澆口孔及澆道太小 ●模具排氣不良 ●模具表面有水分 或潤滑劑 ▲螺杆磨損 ▲過膠圈磨損
080射出成型不良现象及原因
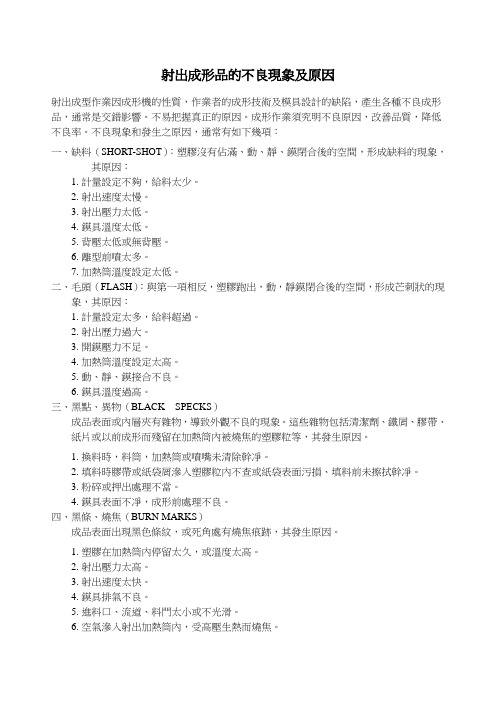
射出成形品的不良現象及原因射出成型作業因成形機的性質,作業者的成形技術及模具設計的缺陷,產生各種不良成形品,通常是交錯影響。
不易把握真正的原因。
成形作業須究明不良原因,改善品質,降低不良率。
不良現象和發生之原因,通常有如下幾項:一、缺料(SHORT-SHOT):塑膠沒有佔滿、動、靜、鏌閉合後的空間,形成缺料的現象,其原因:1.計量設定不夠,給料太少。
2.射出速度太慢。
3.射出壓力太低。
4.鏌具溫度太低。
5.背壓太低或無背壓。
6.離型前噴太多。
7.加熱筒溫度設定太低。
二、毛頭(FLASH):與第一項相反,塑膠跑出,動,靜鏌閉合後的空間,形成芒刺狀的現象,其原因:1.計量設定太多,給料超過。
2.射出歷力過大。
3.開鏌壓力不足。
4.加熱筒溫度設定太高。
5.動、靜、鏌接合不良。
6.鏌具溫度過高。
三、黑點、異物(BLACK SPECKS)成品表面或內層夾有雜物,導致外觀不良的現象。
這些雜物包括清潔劑、鐵屑、膠帶、紙片或以前成形而殘留在加熱筒內被燒焦的塑膠粒等,其發生原因。
1.換料時,料筒,加熱筒或噴嘴未清除幹凈。
2.填料時膠帶或紙袋屑滲入塑膠粒內不查或紙袋表面污損、填料前未擦拭幹凈。
3.粉碎或押出處理不當。
4.鏌具表面不凈,成形前處理不良。
四、黑條、燒焦(BURN MARKS)成品表面出現黑色條紋,或死角處有燒焦痕跡,其發生原因。
1.塑膠在加熱筒內停留太久,或溫度太高。
2.射出壓力太高。
3.射出速度太快。
4.鏌具排氣不良。
5.進料口、流道、料門太小或不光滑。
6.空氣滲入射出加熱筒內,受高壓生熱而燒焦。
7.螺桿回轉速度過快。
8.樹脂潤滑劑過多,熱安全性差。
9.鏌具溫度過高。
五、黃條、色變(DISCOLORATION)成品表面產生近黃色之紋路的現象,其原因。
1.顏料分散性或熱安定不足。
2.參考第四項不良原因。
六、銀條(SILVER STREAK)成品表面有水痕或水泡的現象,其原因。
1.塑膠粒或顏料幹燥不足。
2.背壓不足,空氣卷入。
射出成型之缺陷异常+原因分析与对策

射出成型之缺陷异常原因分析与对策【射出成型之缺陷異常原因分析与对策】概述成型品原则上都是依据规格/标准和客户的要求制造的,但在实际注塑秤过程中它的变化仍是相当广泛而复杂的;有时当生产进行得很顺利时,会突然产生缩水、变形、裂痕、银纹或其它不良缺陷等。
在注塑时我们需从胶件所产生的缺陷,来准确分析/判断问题点所在,找出解决问题的方法,这是一种专业性的技术及经验的累积。
有时只要变更注塑工艺条件、对模具/机器方面稍做调整与改善或更换所使用的原料,就可以解决问题。
注塑成型中对成型品物性的主要影响因素可从以下四个方面来考虑:A、原料B、注塑机C、注塑模具D、成型条件注塑过程中出现的异常问题很多,主要是“产品质量缺陷”和“注塑生产中特有的异常现象”两大类。
注塑产品常见的质量缺陷有:缺胶、缩水、银纹(料花)、披锋(飞边)、烧焦、气泡(缩孔)、水波纹、喷射纹(蛇纹)、流纹(流痕)、夹水纹、裂纹(龟裂)、顶白、表面无光泽、翘曲变形、黑条、混色、拖花、透明度不足、尺寸偏差、剥离(起皮)、冷料斑、黑点、气纹、色差、盲孔、断柱等……注塑生产中特有的异常现象有:喷嘴流涎(流涕)、漏胶、胶件粘模、水口拉丝、嵌件不良、多胶、断针、堵嘴、顶针位穿孔、模印、压模、塑化噪音、下料不畅、螺杆打滑、开模困难等等。
下面分析各种注塑缺陷及异常现象产生的原因并探讨其解决问题的方法。
A、注塑常见缺陷原因分析及改善方法目錄1、走胶不齐的原因分析及改善对策且 (2)2、缩水(缩痕)的原因分析及改善对策 (3)3、银纹(料花、水花)的原因分析对改善对策 (5)4、披锋(飞边)/烧焦(困气)原因分析及改善对策 (8)5、缩孔(真空泡)的原因分析及改善对策 (9)6、水波纹的原因分析及改善对策 (10)7、喷射纹(蛇纹)/流纹(流痕)的原因分析及改善对策 (11)8、夹水纹(熔接线)的原因分析及改善对策 (12)9、裂纹(龟裂)的原因分析及改善对策 (13)10、顶白或顶爆的原因分析及改善对策 (14)11、成品表面无光泽/胶件翘曲变形的原因分析及改善对策 (15)12、黑条(黑纹)的原因分析及改善对策 (17)13、混色的原因分析及改善对策 (18)14、拖花(拉伤)/透明度不足的原因分析及改善对策 (19)15、尺寸偏差/剥离(起皮)的原因分析及改善对策 (20)16、冷料斑/黑点的原因分析及改善对策 (21)17、气纹(阴影)的原因分析及改善对策 (22)18、色差的原因分析及改善对策 (23)19、强度不足的原因分析及改善对策 (24)20、气泡/金属嵌件不良的原因分析及改善对策 (25)21、盲孔的原因分析及改善对策 (26)22、内应力产生的原因及改善对策 (27)23、表面浮纤产生的原因对改善对策 (28)24、白点产生的原因及改善对策 (29)25、注塑生产特有的异常现象(11种现象) (30)26、其它注塑异常现象(10种情况) (36)一、走胶不齐(缺胶未射滿)provides venture platform, makes many youth round has venture dream, for national solution has important of employment problem. Relevant departments units carefully to discover, cultivate talent. From the perspective of Dongping, contradiction of rapid economic development and personnel shortages. Currently facing the industry transformation and upgrading, and transform and upgrade traditional industries, is the development of new industries such as tourism, logistics, e-commerce, we still lack a large number of capital operation and management of talents, the lack of technological innovation, technology transfer, product research and development, tourism services and other high-level professional and technical personnel. Especially with theIndustry further develops, the demand is growing. We must stand in the global and strategic height, with a high degree of political responsibility and historical mission, counties implement talent strategies as a major and pressing task to seize good, practical human resource development as industrial counties of the country. Departments at all levels must firmly establish the "talent is wealth, talent is competitive, talent is creativity" concept, fully aware of the extreme importance of talent, the real talent working on the agenda, the primary task of the primary resources to support the development of talent. 2 the construction of enterprisers ' as the starting point, and promote the transformation and充填不足是溶融的塑料未完全注满模具成型空间的各个角落之现象。
塑胶射出成型不良原因分析及解决对策
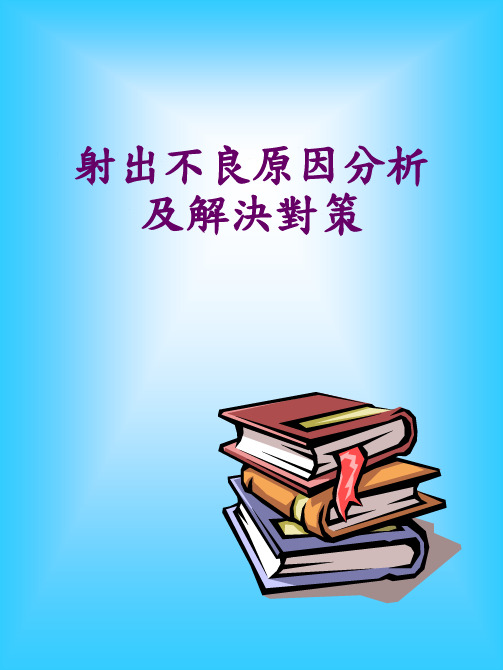
射出機
塑料
1.合模不良
2.分模面上有異物 3.溢口自單邊進膠,撐模力不均 4.透氣孔過大 5.回位梢在長型模具兩端,造成 頂出板回位時,頂出梢與頂出 梢孔干涉磨擦 6.頂出梢太細長,造成頂出梢孔 磨損 7.模具公母模的定位塊不準或缺 乏 1.模具公母模溫度差異 熱交換器 2.模塊及活動模芯熱脹干涉
模具
塑料
3.流動長度對厚度比值太高 熱交換器 1.模溫太低
2.適量增大,減低壓力降,採用 鴨嘴型溢口,穩定的偏慢速, 使流動波前的剪切流動及切 線流動值變小,模溫提高在 90~130℃間,最佳方式是採用 射出壓縮成形法改變流動模 式(消除光彈紋、波浪紋) 3.增加溢口數量 1.適量提高(蛇腹紋、光彈紋、 唱片紋)
短射的故障排除
起源 成設 塑料 發生原因 1.補強肋及局部壁厚太薄 1.流動指數太低 2.料斗進料口下料不順 1.計量不足 2.熔膠溫度太低 3.料斗進料口下料不順 4.充填壓力不足 射出機 解決對策 1.改變設計或均勻化壁厚 1.更換高流動指數塑料 2.再生料顆粒不平均,需篩選挑 除大顆粒塑料 1.提高計量,續壓壓力墊保留至 少3mm以上 2.提高背壓,螺桿轉速及加熱銅 體溫度 3.確保料斗進料口溫度在 50℃~70℃ 4.提高充填壓力,更換使用A級 螺桿,增加充填時間 5.提高射速或使用有蓄能器成 型機 6.追加噴嘴電熱器,射出完畢將 噴嘴退後,防止溫度背模具帶 走 7.更換油封並鎖緊,防止漏油 8.更換逆止閥及補焊螺紋 1.加大相關尺寸 2.提高熱流道溫度,絕緣豎流道 與模板之接融 3.更換電熱器 4.包封處增設排氣孔或改變溢 口位置 5.改善流道的充填平衡 1.提高模溫,使用模溫控制器 2.改善模具散熱系統
成設
1.充填速度不均衡 射出機 2.熔膠溫度太低 3.噴嘴段無加熱器,形成冷膠 4.噴嘴孔徑太小,孔道太長 1.邊溢口太扁,針點溢口太細
射出成型常见不良现象级处理措施

射出成型中常见不良现象产生原因分析及对策以下所列举的成型中产生的不良原因及对策是指在一般情况下可能出现的﹐也仅以本人在工作中的一些心得﹐体验为例﹐如有不妥或不周之处﹐还请各位行家指正﹗(一)短射(不饱模)(1)短射(不饱模)﹔即是溶融塑料未能完全填充填满成型空间(模穴)各个角落的现象(2)原因及改善对策(见下表)(二)毛边(1)毛边﹔即是在分模面﹑流道周围及模仁镶块间隙内出现的膜状或毛刺状的多余胶料(2)原因及改善对策(见下表)*注﹔成型时间过长﹐模温过低而采用高压﹐高速射出也是产生毛边的常见原因(三)银线(1)银条(银线)即是在成型产品表面或表面附近﹐沿塑料流动方向﹐呈放射状的银白色条纹。
(2)原因及改善对策(见下表)(四)成品光泽度低(1)成品光泽度低是指成品表面光泽达不到质量要求﹐表面无折光度。
(2)原因及改善对策(见下表)(五)变形(1)变形可分为对角线的扭曲及平行边沿的曲翘两种﹐是成品成型中发生的不规则弯曲现象(2)原因及发善对策(见下表)(六)顶白(1)顶白(也叫白化)是指成品在脱模之际﹐在顶针或其它脱模部位出现白色痕迹(2)原因及改善对策(见下表)(七)结合线(1)结合线是指在成型中﹐二道或多道熔融材料融合时出现的细线状(2)原因及改善对策(见下表)(八)冲料痕(1)冲料痕是指熔融材料在进料点附近﹐以浇口为中心而呈现的条纹状(2)原因及改善对策(九)异色(黑纹)(1)异色(黑纹)是指在成型过程中﹐在成品表面出现的黑色或其它深色条纹(2)原因及改善对策(见下表)(十)气泡(1)气泡是熔融塑料中的水份﹐挥发气体于成型过成中被封入内部而残留的空动现象(2)原因及改善对策(见下表)射出换料要诀在射出成型作业中﹑换料﹑换色的问题﹐值得吾入深入探讨﹒如何以最快速的方法完成换料﹑换色﹐除可节省时间外﹐并可降低一笔相当可观的生产成本﹒一﹑同一材料之换色1﹒1同一材料的换色时﹐原则上从淡色材料换为深浓色材料﹐较从不透明材料换为透明材料容易﹒一般换色作业程序如下﹔(1)关斗漏料斗下部的进料挡门(2)空射数次﹐将加热料管内的材料全部射出(3)新材料加入漏斗(4)打开进料挡门﹐螺杆前进后退十数次直到换色完成﹒从不透明材料换为透明材料时﹐尤需拆除喷嘴头部份﹐清除残留的材料﹐必要时杆亦需抽出撤底清理﹐不可有残余料积存死角处﹒二﹑不同材料之换色2.1 不同材料的更换作业﹐是利用前后各材料的熔融黏度差﹐与加热管的温度控制来施行换料手续。
射出成形不良要因与对策

提高射速
增加肉厚
改善塑料流动性
3.锁模力不足
(1)无过饱和现象
提高锁模力
4.吻合面间隙太大
(1)特定位置
修护模具
5.模板变形
提早切换到保压
降低保持压力
提高模板强度及刚性
射出成形不良要因与对策
三、凹陷,缩水(sink marks) /真空泡(voids)
基本原因
判断方法
对策
1.充填量不足
(1)全面性的凹陷
降低料温
减少浇口断面积
3.表面固化太慢
(1)厚的部位出现凹陷或光泽
降低模温
降低料温
表面层没有形成坚固的固化层,当中心部收缩时会将表面向内拉成凹陷,甚至由内向外扩散的热量会将表面层再度熔解,而出现光泽。
相反的,在厚的部位如果表面层足够坚固,则中心部的收缩会形成真空泡
塑流通过厚肉区时减速使固化层较厚
调整肉厚(如肋部减薄,厚薄缓变)
提高模温
提高料温
提高射出速度或移动速度的切换位置
提高保持压力
移动浇口位置
检查排气效果
使用较小及较圆的色剂
六、波纹
基本原因
判断方法
对策
当塑流进入较冷的模腔,由于较快的冷却速率(如在较低模温及低射出速度之情形下),使得流动波前靠近模壁部位也形成固化,这个固化层妨碍了后续流动波前贴近模壁,但固化层也会受流动压力拉伸展延,流动波前克服渐弱的妨碍力后会再度挤贴模壁,这样的状况如果在流动速度继续维持较慢时会一再重演,成品的外观上就会留下一圈圈如唱盘状的痕迹。
尺寸安定性不足
升高射出压力
升高保压压力
延长冷却时间
调整适当模具温度
改用流动性较低的材料
常见射出成型不良原因与对策
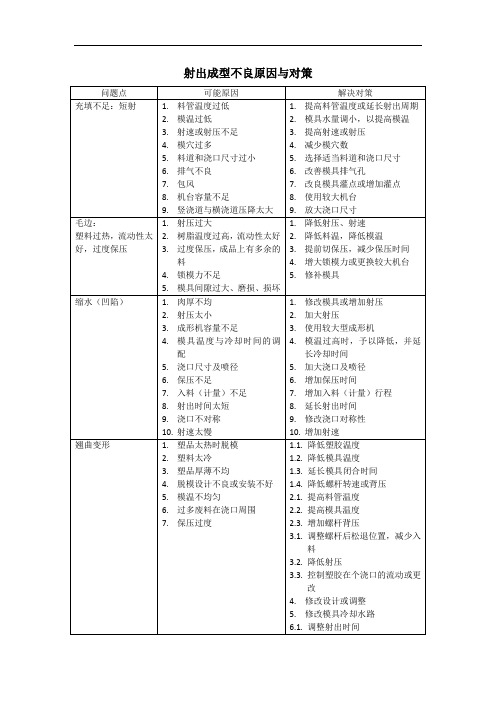
1.1.增加入口处之肉厚
1.2.增加透气孔或增加溢料袋
2.改变进料位置或增加进胶口
顶出困难
1.模具冷却不足
2.模具斜度不够
3.塑件缩水而粘住公模
4.射压过大
5.单边顶出
6.过度保压
1.加大水量或延长冷却时间
2.增加退模位的锥度
3.升高模温或缩短冷却时间
7.螺杆中卷入空气产生压缩而发热
8.螺杆不适当
1.1.降低料管及射嘴温度
1.2.降低背压、转数
1.3.充分干燥塑料
2.检视料管、螺杆是否刮伤
3.1.降低射压及射速
3.2.浇口加大,加设排气孔
4.消除死角以防止材料滞留
5.避免螺纹部的损伤改善密著性
6.检视温控系统,减少塑料滞留时间
7.减少漏斗内的材料,并增高背压
2.加大间隙
3.增加排气效果
银条:
成品沿塑料流动表面,呈现银白色条纹
1.塑料含有水份或挥发性物质,因受压缩而呈现液态状,当挤出射嘴进入模具后压力突然下降而使液态状被蒸发而成气态,使得塑胶在与模具表面接触时,固化后因表面细泡而形成银白色条纹
2.粉粒熔融时其间空气亦随着一起射出
3.塑料过冷,模温过低,造成慢速充填,因而射嘴温度过高使得有冷料问题
3.入料不足
4.射出时间太短
1.塑料充分干燥,增加入料量,螺杆设计提高内压
2.1.增加塑料温度,提高模温
2.2.清洁模具表面
2.3.加大浇道及浇口尺寸,并降低射速
2.4.加大射压,增加保压时间
3.增加进料速度,调整射出速度的变化位置
4.延长射出时间
成品烧焦(变黄)、塑料变色:射出压力太大所引起之压缩烧焦斑点
液态硅胶射出不良现象与原因分析
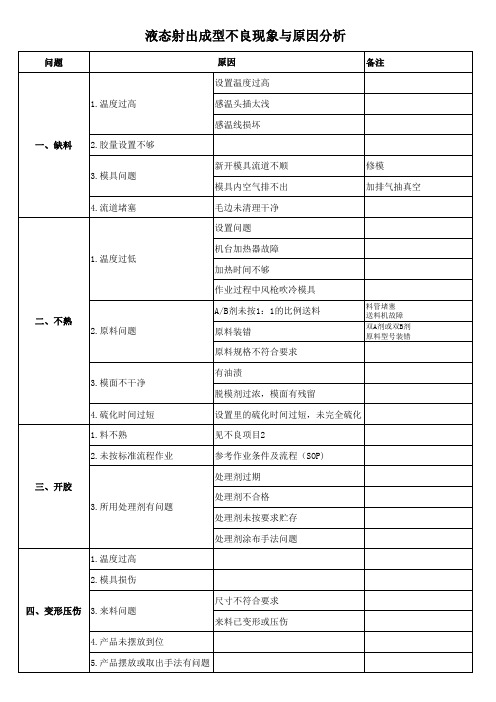
问题 原因 设置温度过高 1.温度过高 感温头插太浅 感温线损坏 一、缺料 2.胶量设置不够 新开模具流道不顺 3.模具问题 模具内空气排不出 4.流道堵塞 毛边未清理干净 设置问题 机台加热器故障 1.温度过低 加热时间不够 作业过程中风枪吹冷模具 A/B剂未按1:1的比例送料 二、不熟 2.原料问题 原料装错 原料规格不符合要求 有油渍 3.模面不干净 脱模剂过浓,模面有残留 4.硫化时间过短 1.料不熟 2.未按标准流程作业 三、开胶 处理剂不合格 3.所用处理剂有问题 处理剂未按要求贮存 处理剂涂布手法问题 1.温度过高 2.模具损伤 尺寸不符合要求 四、变形压伤 3.来料问题 来料已变形或压伤 4.产品未摆放到位 5.产品摆放或取出手法有问题 设置里的硫化时间过短,未完全硫化 见不良项目2 参考作业条件及流程(SOP) 处理剂过期
原因
备得当
4.模具设计不合理,导致产品难 脱模
1.作业环境脏、乱、差 七、脏污、杂质 2.作业手法不标准 3.模具有脏污
料管堵塞 送料机故障 双A剂或双B剂 原料型号装错
备注
修模 加排气抽真空
液态射出成型不良现象与原因分析
问题 1.模具封胶不好 射压和射速过大 2.射出参数设定不合理 胶量设定过多 五、溢胶严重 3.温度过高,胶量流不动 4.原料不符合要求,流动性太 差 5.来料塑料壳尺寸有问题
1.温度过高,硫化时间过长,产 品变脆被拉破
成形不良的原因及对策
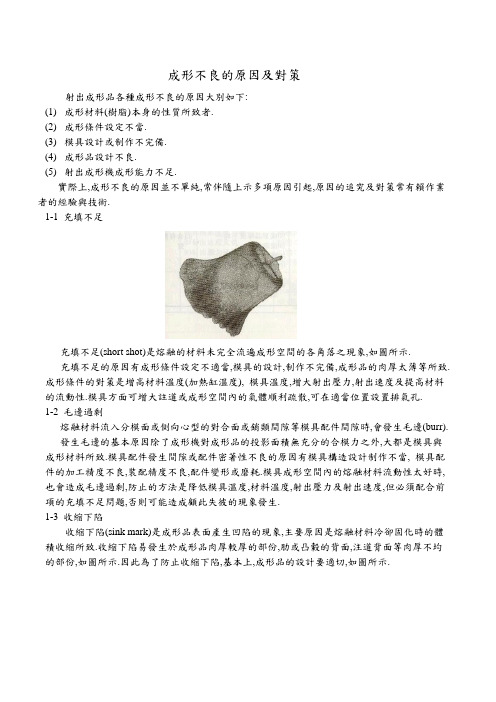
成形不良的原因及對策射出成形品各種成形不良的原因大別如下:(1)成形材料(樹脂)本身的性質所致者.(2)成形條件設定不當.(3)模具設計或制作不完備.(4)成形品設計不良.(5)射出成形機成形能力不足.實際上,成形不良的原因並不單純,常伴隨上示多項原因引起,原因的追究及對策常有賴作業者的經驗與技術.1-1 充填不足充填不足(short shot)是熔融的材料未完全流遍成形空間的各角落之現象,如圖所示.充填不足的原因有成形條件設定不適當,模具的設計,制作不完備,成形品的肉厚太薄等所致.成形條件的對策是增高材料溫度(加熱缸溫度), 模具溫度,增大射出壓力,射出速度及提高材料的流動性.模具方面可增大註道或成形空間內的氣體順利疏散,可在適當位置設置排氣孔.1-2 毛邊過剩熔融材料流入分模面或側向心型的對合面或銷類間隙等模具配件間隙時,會發生毛邊(burr).發生毛邊的基本原因除了成形機對成形品的投影面積無充分的合模力之外,大都是模具與成形材料所致.模具配件發生間隙或配件密著性不良的原因有模具構造設計制作不當, 模具配件的加工精度不良,裝配精度不良,配件變形或磨耗.模具成形空間內的熔融材料流動性太好時,也會造成毛邊過剩,防止的方法是降低模具溫度,材料溫度,射出壓力及射出速度,但必須配合前項的充填不足問題,否則可能造成顧此失彼的現象發生.1-3 收縮下陷收縮下陷(sink mark)是成形品表面產生凹陷的現象,主要原因是熔融材料冷卻固化時的體積收縮所致.收縮下陷易發生於成形品肉厚較厚的部份,肋或凸轂的背面,注道背面等肉厚不均的部份,如圖所示.因此為了防止收縮下陷,基本上,成形品的設計要適切,如圖所示.防止收縮下陷可適度調整成形條件,如降低模具溫度,材料溫度,增高射出壓力,延長射出壓力保持時間(保壓時間),或依成形品的形狀或肉厚而在容易發生收縮下陷的部位追加設置澆口.收縮下陷是成形品收縮所致,易見於PE,PP,PA等成形收縮率大的結晶性塑膠料.所之,以玻璃織維強化的塑膠或充填無機質的塑膠材料之成形收縮率甚小於基質的塑膠材料,其收縮下陷可減至最小.1-4 氣泡氣泡(bubble)是在成形品內部形成的空隙,一般所謂的氣泡有成形品冷卻時,由於體積收縮差在肉厚較厚部形成的空洞與熔融材料中的水分,揮發物形成的氣體而封入成形品內部者.成形品肉厚過大或肉厚嚴重不均勻時,常會發生氣泡,如圖所示.此時,延長保壓時間或增高模具溫度,即可減輕氣泡發生的程度.再者,將成形材料充分幹燥,降低材料溫度,防止熱分解,亦可阻止氣泡之發生.1-5 破裂破裂(cracking)是成形品表面產生毛發狀之裂紋,成形品有尖銳棱角時,此部份常發生不易看出的細裂紋.裂紋是成形品的致命不良現象,主要原因如下所示.(1)脫模不易所致.(2)過度充填所致.(3)模具溫度過低而致.(4)成形品構造上的缺陷所致.若欲避免脫模不良所致的裂紋時,模具成形空間須設有充分的脫模斜度,檢討頂出銷的大小,位置,形式等,頂出時,成形品各部份的脫模阻力要均勻.過度充填是射出成形時,施加過大的射出壓力或材料計量過多,成形品內部應力過大,脫模時造成裂紋,在此種狀態下,模具配件的變形量也增大,更難脫模,助長破裂之發生,此時,宜降低射出壓力,防止過度充填.澆口部常易殘留過大的內部應力,澆口附近易脆化,特別是直接澆口的部份,易因內部應力而破裂,例如杯狀或碗狀成形品,易以澆口為中心而發生放射狀裂紋,如圖所示.1-6 白化成形品脫模之際,常遭受頂出銷的頂出力或有undercut部位時不適當的頂出而變形受力時,該部變白稱為白化(blushing).白化並非裂紋, 但卻是裂紋之預兆, 常見於ABS、HIPS、硬質PVC 等.白化是成形品內部顯著的殘留應力所致, 可套用脫模不良的對策.1-7 翹曲、扭曲翹曲、扭曲都是從模具取出的成形品產生之變形(strain),平行邊變形者稱翹曲(warping),如圖11.27所示.對角線方向的變形稱為扭曲(torsion),如圖所示.這些變形為成形時的各種內部應力所致,原因大致如下:(1)脫模時的內部應力所致.(2)模具溫度控制不充分或不均勻所致.(3)材料或填充料的流動配向所致.(4)成形條件不適當所致.(5)成形品形狀、肉厚等所致.成形品脫模時的內部應力所致的變形,是成形品未充分冷卻固化前,從模具頂出所致.模具內的成形品,若不均勻冷卻,則造成熱收縮不均勻,容易變形.結晶性塑膠的成形收縮大,因此,收縮差所致的變形也大,防止方法是注意模具的溫度控制.成形時的材料或填充料所致的配向性,也是成形品變形的主要原因,配向性所致的變形與模具構造有關系,如澆口的位置、形狀、大小、數目等,影響成形品的變形有重大的關連.防止成形品的變形,只調整成形條件是很難造成的,但為了減少內部的應力所致的變形,可減低射出壓力、縮短保壓時間、減低射出速度.成形品的變形主要取決於成形品設計的良否,使用之成形材料的適池與否,因此,成形品設計時須加以注意.一般為防止成形品變形,可在剛成形后,以冷工模等對成形品施加外力,矯正變形或防止進一步的變形,但成形品在使用中若再次遇到高溫時又會復原,對此點須特別加以注意.1-8 熔合線熔合線(weld line)是熔融材料二道或二道以上合流的部份所形成的細線.熔合線發生的原因如下所示:(1)成形品形狀(模具構造)所致材料的流動方式.(2)熔融材料的流動性不良.(3)熔融材料合流處捲入空氣、揮發物或離形劑等異物.熔合線是流動的材料前端部合流時,此部份的材料溫度特別低所致,即合流部未能充分熔合所致.成形品的窗、孔部周邊難免會造成材料合流,而產生熔合線.但材料的流動性特別良好時, 可使熔合線幾乎看不見, 同時, 升高材料溫度、增高模具溫度, 亦可使熔合線之程度減至最少.改變澆口的位置、數目,將發生溶合線的位置移位他處,或在熔合部設置排氣孔,迅速疏散此部份的空氣及揮發物,或如圖11.29所示,在熔合部附近設材料溢流池,將熔合線移至溢流池,事后再將其切除等皆是有效的處置對策.熔合線不僅有礙成形品之外觀,同時也不利於成形品強度,不含玻璃織維等填充料的非強化塑膠之熔合線部強度與其他部位相差無幾.但玻璃織維強化塑膠(FRTP)的玻璃織維在熔合部不融著,此部份的強度常低很多,圖11.30所示為其實驗例,在試片成形用模具的流道部份設變換閥,能以一點側狀澆及二點側狀澆口(成形后有熔合線)兩方式成形,試驗結果如表11.8所示,玻璃織維(30%)強化塑膠的熔合部強度約為非強化者的60%.1-9 流痕流痕(flow mark)是熔融材料流動的痕跡,以澆口為中心而呈現的條紡模樣.流痕是最初流入成形空間內的材料冷卻過快,而與其后流入的材料間形成界線所致.為了防止流痕,可增高材料溫度,改善材料流動性,調整射出速度,圖11.31所示為射出速度與各種流動模樣的關系.殘留於射出成形機噴嘴前端的冷材料,若直接進入成形空間內,則會造成流痕,因此在注道與流道的會合處或流道與分流道的交接處設充分的滯料部,可有效的防止流痕的發生.同時,亦可增大澆口的尺寸來防止.1-10 噴流痕噴流痕(jetting mark)是從澆口往成形空間內射出的熔融材料成紐帶狀固化,在成形品表面形成蛇行狀態,亦可視為流痕的一種,如圖所示.使用側狀澆口的成形品,在材料的流路中的無滯料部或不充足時,容易產生噴流痕,原固是急速通過澆口的冷材料直接進入成形空間,然后接觸成形空間表面而固化,接著被隨后進入的熱材料推流,而殘留蛇行痕跡.防止噴流痕的方法是在流道系統設置足夠的滯料部,或增大澆口面積、增高模具溫度、防止材料快速固化,或改變澆口形狀,采用重疊澆口或凸片澆口,如圖所示,或使從澆口進入成形空間的材料,一度碰撞成形空間內的銷類或壁面,再者,可減慢材料的射出速度.1-11 銀條銀條(silver streak)是在成形品表面或表面附近,沿材料流動方向,呈現的銀白色條紋.銀條的發生大都是成形材料中的水分或揮分物或附著模具表面的水分等汽化所致,射出成形的螺杆捲入空氣時也會發生銀條.防止銀條的對策是首先充分幹燥成形材料,再者,增高模具溫度、降低材料溫度、減慢射出速度、降低射出壓力及升高螺杆背壓等.1-12 燒焦一般所謂的燒焦(burn mark),包括成形品表面因材料過熱所致的變色及成形品的銳角部份或轂部、肋的前端等材料焦黑的現象.燒焦是滯留成形空間內的空氣,在熔融材料進入時未能迅速排出,被壓縮而顯著升溫,再將材料燒焦所致.1-13 黑條黑條(break streak)是成形品有黑色條紋的現象,如圖11.34所示,其發生的主要原因是成形材料的熱分解所致,常見於熱安定性不良的材料.有效防止黑條發生的對策是防止加熱缸內的材料溫度提高,減慢射出速度.加熱缸內壁或螺杆,若有傷痕或缺口,則附著於此部份的材料會過熱,引起熱分解.逆流防止閥亦會因材料滯留而引起熱分解,所以黏度高的材料或容易分解的材料要特別注意防止黑條的發生.1-14 表面光澤不良成形品表面失去材料本來的光澤,形成乳白色層膜,成為模糊狀態等皆可稱為表面光澤不良(haze).成形品表面光澤不良,大都是由於模具表面狀態所致,模具表面的研磨不良時,成形品表面當然得不到良好的光澤.但模具表面狀態良好時,增高材料溫度、模具溫度,可改良表面光澤.使用過多的離形劑或油脂性離形劑亦是表面光澤不良的原因.同時,材料吸濕或含有揮發物及異質物混入污染亦是造成成形品表面光澤不良的原因之一.1-15 表面剝離成形品表面成云母狀薄層裂痕的現象,稱為表面剝離.表面剝離(pelling)的原因在不同的材料混入或成形條件不當.例如一般用PS與ABS、PE與PP混用時,因彼此間無相容性,故造成表面剝離.平常的剝離發生是在於換料不完全,混用粉碎的再生料時,弄錯材料種類等.同時,材料溫度太低時,流動材料的內部發生交界面,亦會造成剝離現象.。
080射出成型不良现象及原因
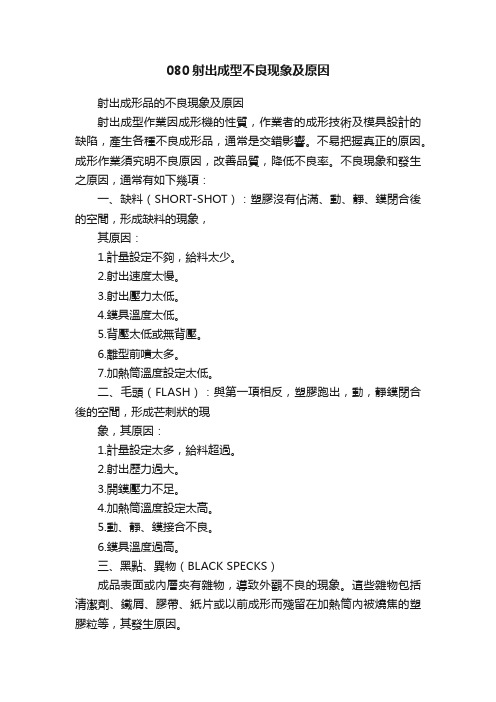
080射出成型不良现象及原因射出成形品的不良現象及原因射出成型作業因成形機的性質,作業者的成形技術及模具設計的缺陷,產生各種不良成形品,通常是交錯影響。
不易把握真正的原因。
成形作業須究明不良原因,改善品質,降低不良率。
不良現象和發生之原因,通常有如下幾項:一、缺料(SHORT-SHOT):塑膠沒有佔滿、動、靜、鏌閉合後的空間,形成缺料的現象,其原因:1.計量設定不夠,給料太少。
2.射出速度太慢。
3.射出壓力太低。
4.鏌具溫度太低。
5.背壓太低或無背壓。
6.離型前噴太多。
7.加熱筒溫度設定太低。
二、毛頭(FLASH):與第一項相反,塑膠跑出,動,靜鏌閉合後的空間,形成芒刺狀的現象,其原因:1.計量設定太多,給料超過。
2.射出歷力過大。
3.開鏌壓力不足。
4.加熱筒溫度設定太高。
5.動、靜、鏌接合不良。
6.鏌具溫度過高。
三、黑點、異物(BLACK SPECKS)成品表面或內層夾有雜物,導致外觀不良的現象。
這些雜物包括清潔劑、鐵屑、膠帶、紙片或以前成形而殘留在加熱筒內被燒焦的塑膠粒等,其發生原因。
1.換料時,料筒,加熱筒或噴嘴未清除幹凈。
2.填料時膠帶或紙袋屑滲入塑膠粒內不查或紙袋表面污損、填料前未擦拭幹凈。
3.粉碎或押出處理不當。
4.鏌具表面不凈,成形前處理不良。
四、黑條、燒焦(BURN MARKS)成品表面出現黑色條紋,或死角處有燒焦痕跡,其發生原因。
1.塑膠在加熱筒內停留太久,或溫度太高。
2.射出壓力太高。
3.射出速度太快。
4.鏌具排氣不良。
5.進料口、流道、料門太小或不光滑。
6.空氣滲入射出加熱筒內,受高壓生熱而燒焦。
7.螺桿回轉速度過快。
8.樹脂潤滑劑過多,熱安全性差。
9.鏌具溫度過高。
五、黃條、色變(DISCOLORATION)成品表面產生近黃色之紋路的現象,其原因。
1.顏料分散性或熱安定不足。
2.參考第四項不良原因。
六、銀條(SILVER STREAK)成品表面有水痕或水泡的現象,其原因。
成形不良的原因与对策
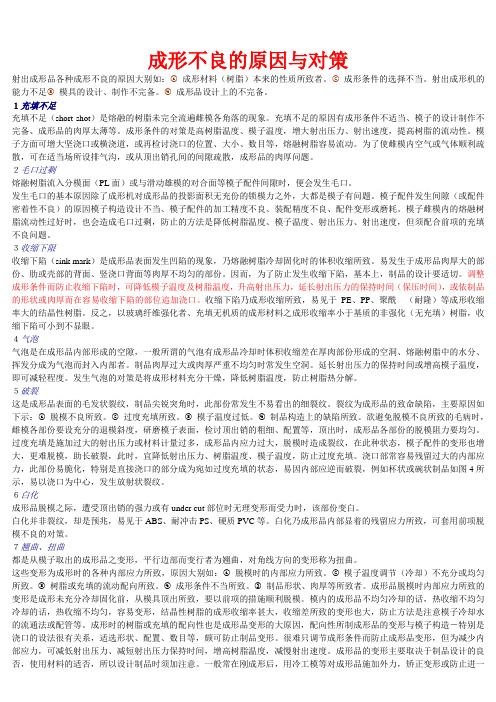
成形不良的原因与对策射出成形品各种成形不良的原因大别如: 成形材料(树脂)本来的性质所致者。
成形条件的选择不当。
射出成形机的能力不足●模具的设计、制作不完备。
❍成形品设计上的不完备。
1充填不足充填不足(short shot)是熔融的树脂未完全流遍雌模各角落的现象。
充填不足的原因有成形条件不适当、模子的设计制作不完备、成形品的肉厚太薄等。
成形条件的对策是高树脂温度、模子温度,增大射出压力、射出速度,提高树脂的流动性。
模子方面可增大坚浇口或横浇道,或再检讨浇口的位置、大小、数目等,熔融树脂容易流动。
为了使雌模内空气或气体顺利疏散,可在适当场所设排气沟,或从顶出销孔间的间隙疏散,成形品的肉厚问题。
2毛口过剩熔融树脂流入分模面(PL面)或与滑动雄模的对合面等模子配件间隙时,便会发生毛口。
发生毛口的基本原因除了成形机对成形品的投影面积无充份的锁模力之外,大都是模子有问题。
模子配件发生间隙(或配件密着性不良)的原因模子构造设计不当、模子配件的加工精度不良、装配精度不良、配件变形或磨耗。
模子雌模内的熔融树脂流动性过好时,也会造成毛口过剩,防止的方法是降低树脂温度、模子温度、射出压力、射出速度,但须配合前项的充填不良问题。
3收缩下限收缩下陷(sink mark)是成形品表面发生凹陷的现象,乃熔融树脂冷却固化时的体积收缩所致。
易发生于成形品肉厚大的部份、肋或壳部的背面、竖浇口背面等肉厚不均匀的部份。
因而,为了防止发生收缩下陷,基本上,制品的设计要适切。
调整成形条件而防止收缩下陷时,可降低模子温度及树脂温度,升高射出压力,延长射出压力的保持时间(保压时间),或依制品的形状或肉厚而在容易收缩下陷的部位追加浇口。
收缩下陷乃成形收缩所致,易见于PE、PP、聚酰(耐隆)等成形收缩率大的结晶性树脂。
反之,以玻璃纤维强化者、充填无机质的成形材料之成形收缩率小于基质的非强化(无充填)树脂,收缩下陷可小到不显眼。
4气泡气泡是在成形品内部形成的空隙,一般所谓的气泡有成形品冷却时体积收缩差在厚肉部份形成的空洞、熔融树脂中的水分、挥发分成为气泡而封入内部者。
成形不良的原因与对策
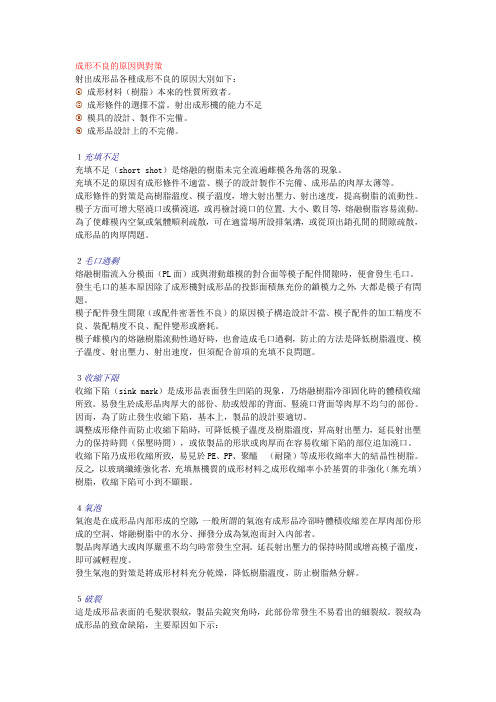
成形不良的原因與對策射出成形品各種成形不良的原因大別如下:成形材料(樹脂)本來的性質所致者。
成形條件的選擇不當。
射出成形機的能力不足●模具的設計、製作不完備。
❍成形品設計上的不完備。
1充填不足充填不足(short shot)是熔融的樹脂未完全流遍雌模各角落的現象。
充填不足的原因有成形條件不適當、模子的設計製作不完備、成形品的肉厚太薄等。
成形條件的對策是高樹脂溫度、模子溫度,增大射出壓力、射出速度,提高樹脂的流動性。
模子方面可增大堅澆口或橫澆道,或再檢討澆口的位置、大小、數目等,熔融樹脂容易流動。
為了使雌模內空氣或氣體順利疏散,可在適當場所設排氣溝,或從頂出銷孔間的間隙疏散,成形品的肉厚問題。
2毛口過剩熔融樹脂流入分模面(PL面)或與滑動雄模的對合面等模子配件間隙時,便會發生毛口。
發生毛口的基本原因除了成形機對成形品的投影面積無充份的鎖模力之外,大都是模子有問題。
模子配件發生間隙(或配件密著性不良)的原因模子構造設計不當、模子配件的加工精度不良、裝配精度不良、配件變形或磨耗。
模子雌模內的熔融樹脂流動性過好時,也會造成毛口過剩,防止的方法是降低樹脂溫度、模子溫度、射出壓力、射出速度,但須配合前項的充填不良問題。
3收縮下限收縮下陷(sink mark)是成形品表面發生凹陷的現象,乃熔融樹脂冷卻固化時的體積收縮所致。
易發生於成形品肉厚大的部份、肋或殼部的背面、豎澆口背面等肉厚不均勻的部份。
因而,為了防止發生收縮下陷,基本上,製品的設計要適切。
調整成形條件而防止收縮下陷時,可降低模子溫度及樹脂溫度,昇高射出壓力,延長射出壓力的保持時間(保壓時間),或依製品的形狀或肉厚而在容易收縮下陷的部位追加澆口。
收縮下陷乃成形收縮所致,易見於PE、PP、聚醯(耐隆)等成形收縮率大的結晶性樹脂。
反之,以玻璃纖維強化者、充填無機質的成形材料之成形收縮率小於基質的非強化(無充填)樹脂,收縮下陷可小到不顯眼。
4氣泡氣泡是在成形品內部形成的空隙,一般所謂的氣泡有成形品冷卻時體積收縮差在厚肉部份形成的空洞、熔融樹脂中的水分、揮發分成為氣泡而封入內部者。
- 1、下载文档前请自行甄别文档内容的完整性,平台不提供额外的编辑、内容补充、找答案等附加服务。
- 2、"仅部分预览"的文档,不可在线预览部分如存在完整性等问题,可反馈申请退款(可完整预览的文档不适用该条件!)。
- 3、如文档侵犯您的权益,请联系客服反馈,我们会尽快为您处理(人工客服工作时间:9:00-18:30)。
注:如果必要的,清潔并拋光
2.減少使用或不使用潤滑劑,不管是內部(在塑
是0.02mm,而高流動性的材料為0.01mm
(壓力及速度) 注:如果必要,使用較多/或較大的頂針
擇的塑料和成型條件(溫度)之間的相容性,
使射出時不會混合不均
F. 模面上有潤滑劑 1.減少使用潤滑劑,不管是混合在塑料中或
是噴在模面上的離型劑
G. 塑料未完全塑化 1.檢查螺桿的長度/直徑比
注:必要的話,更換射出單元或使用混料裝
5.使用空氣頂出針使頂出容易
注:必要時,使用較多且較大的頂針
6.檢查模具
1)調整拔模角度
2)調整倒角
3)調整圓弧
G. 機臺運轉不穩定 1.檢查模具:
1>檢查液壓油壓力
2>檢查液壓油溫度
3>檢查液壓油油量
4>檢查液壓油泄漏情況
5>檢查濾網是否清潔
2.檢查馬達及頂針控制系統
塑
料或外部潤滑(離型劑)
C. 排氣不良 1.在融點線位置增加排氣孔
2.檢查澆口尺寸
注:如有必要,加大或重新安排澆口(平衡)
D. 熔膠內含有熔合特性不良的色母 1.以不含色母的塑料射出來的檢驗色母和
所使用的塑料在此加工條件下的相容性
3.增加熱澆道溫度設定
注:以空射料檢頭實際溫度和之間的差異
2冷料痕
產品內有未熔的塑膠粒,特別是在澆口附近
原因解決方法/檢查要點
A. 熔膠未完全熔融 1.增加料管溫度
2.增加噴嘴溫度
3.增加背壓
4.增加螺杆轉速
5.如果冷卻時間比塑化時間長,降低螺杆轉速
6.如果塑化時間(當塑化時間比冷卻時間長
時,周期時間會加長)
7.檢查螺杆的長度/直徑比
注:如有必要,更換射出單元或使用混料裝置B. 原料被污染 1.檢查原料是否摻有不同流動特性的異物
原料內潤滑劑不夠
9-4縮水
原因對策
模內進膠不足
射出壓力太低
保壓不夠
射出時間太短
射出速度太慢
射料嘴阻塞
冷卻間時間不夠
機器或料管過大
螺杆或逆止環磨損
溢口不平衡
模溫不當
料溫過高
成品本身或其肋(RIB)及柱(BOSS)過厚增加劑量
提高射出壓力
提高或增長保壓
增長射出時間
加快射出速度
拆除檢查修理
延長冷卻時間
更換機器或料管
拆除檢查修理
調整模具溢口大小或位置
調整適當之溫度及具部相對溫度降低料溫
檢討成品
降低射出壓力
減少劑量
減少射出時間
降低射出速度
變更溢口大小或位置
修模具除去倒角
打光模具
開模或頂出減慢或模具加進氣設備檢修模具
降低料溫
對策
降低射出壓力
降低射出劑量時間及速度
重新調整其配合
修改模具
延長冷卻時間或降低冷卻溫度
修改模角具增加角度
修改模具
加設抓銷
降低原料溫度
對策
降低射出壓力
降低射出時間/速度及劑量
增加開模壓力
檢查清理
檢查清理
檢修模具
降低原料溫度﹐降低模具溫度
對策
降低射出壓力/時間/速度及劑量升高模溫
檢修模具
檢修模具
檢修模具檢修模具
開模或頂出慢速加進氣設備檢修模具
對策
增快射出速度
提高射出壓力
提高模具溫度
少用脫模劑油盡量不用調整模具
增開排氣孔或檢查原有排氣孔是否堵塞
變更溢口位置
提高原料溫度
提高背壓
加快螺杆轉速
檢查原料
對策
調整適當射出速度
調整適當射出壓力
提高模具溫度
加大溢口
變更成品設計或溢口位置
提高原料溫度
提高背壓
加快螺杆轉速
檢查原料
成品頂出時尚未冷卻降低模具溫度
延長冷卻時間
降低原料溫度
原料溫度太低提高原料溫度
提高模具溫度
9-11 成品內有氣孔
原因對策
射出壓力太低提高射出壓力
射出時間及劑量不足增加射出時間及劑量
射出速度太快調慢射出速度
被壓不夠提高被壓
料管溫度不當降低射嘴及前段溫度﹐提高后段溫度成品斷面肋或柱過厚變更成品設計或溢口位置
澆道溢口太小加大澆道及溢口
模具溫度不平均調整模具溫度
冷卻時間太長減少模內冷卻時間使用水浴冷卻
水浴冷卻過急減短水浴時間或提高水浴溫度
原料含有水分原料徹底烘干
原料溫度過高致分解降低原料溫度
近澆口部分之原料太松或太緊減少或增大溢口大小
成品頂出時尚未冷卻降低模具溫度
延長冷卻時間
降低原料溫度
原料溫度太低提高原料溫度
提高模具溫度
9-11 成品內有氣孔
原因對策
射出壓力太低提高射出壓力
射出時間及劑量不足增加射出時間及劑量
射出速度太快調慢射出速度
被壓不夠提高被壓
料管溫度不當降低射嘴及前段溫度﹐提高后段溫度成品斷面肋或柱過厚變更成品設計或溢口位置
澆道溢口太小加大澆道及溢口
模具溫度不平均調整模具溫度
冷卻時間太長減少模內冷卻時間使用水浴冷卻
水浴冷卻過急減短水浴時間或提高水浴溫度
原料含有水分原料徹底烘干
原料溫度過高致分解降低原料溫度
馬上做射出成行加工.
2. 塑料預先干燥,尤其已拆封的塑料
B.模面上有結露現象 1. 提高模具溫度
注:提高模具開起關閉的速度可以避免
模面結露現象
凹陷
成品的表面在肋及/或厚度改變的地方不平.
原因解決方法/檢查要點
A. 射膠量不足 1. 增加射膠量且經常秤成品的重量 (檢查重量)
B. 射出速度/壓力不對 1. 調整射出速度
2.射出速度曲線
3.調整射出壓力
4.射出壓力曲線
C. 保壓壓力太低 1. 提高保壓壓力
2.增加保壓時間
3.檢查澆口是否阻塞(污染)
注:如果必要的話,加大或重新安排嘵口
位置(平衡)
D. 由于塑料溫度太高,
造成溫度收縮 1. 降低料管溫度
E. 成品的壁厚差距太大 1. 使用泡劑
(收縮不平均)
F. 模溫太高 1. 降低模具溫度
A. 塑料射入毫阻力的模穴內 1.降低射出速度(檢查重量) 2.調整射出速度曲線 注:尤其是剛開始射出的階段 3.降低射出壓力 4.調整射壓力曲線
注:尤其是剛開始射出的階段 5.調整料管溫度曲線 6.檢查澆口的尺寸
注:必要的話,加大或澆口尺寸
7.檢查澆口是否阻塞(污染)且如果必 要的話,調整澆口的位置
注:重新安排澆口的位置,使熔膠的流動提早分開
8.在模穴內安置阻擋物 注:阻擋物可以使塑料通過澆口時,
在模穴內形成阻力
光 澤
表面不夠光澤
原因 解決方法/檢查要點
A. 模具溫度太低或者不規劃 1.提高模具溫度(檢查重量)
2.檢查模具冷卻均勻性及有無阻塞 B. 模具表面加工不正確 1.檢查模具表面是否受污染 注:必要的話,清潔拋光 C. 塑料溫度太低 1.調整料管溫度 2.提高噴嘴溫度
3.提高熱澆道溫度設定 D. 射出速度不正確 1.調整射出速度
A. 塑料受污染 1.檢查塑料有無受污染
注:避免運送途中及混料系統中受污染 B. 不正確的色母
1.用本色料射出,以便檢查在此加工條件時 母料與色母的相容性 C. 在料管內受污染
1.檢查及清潔料管
注:用料短清潔劑清洗料管,必要的話將
料
管分解
2.用本色射出來檢查料管是否清潔 D. 流道及澆口系統受污染 1.檢查并清潔流道及澆口系統 2.檢查熱澆道系統的死角
E. 在混料系統中受污染
1.檢查混料系統中可能受污染的地方
表面燒焦
成品表面在塑料流道的未端燒焦
原因 解決方法/檢查要點 A. 空氣在模具中無法排出
1.降低射出速度
2.調整射出速度曲線
3.降低射出壓力
4.調整射出壓力曲線
注:尤其在射出的終了降壓及速度
5.檢查成品未填飽的地方,是否排氣不良 注:必要的話,加入排氣口或排氣梢
6.檢查模具排氣口是否污染
7.檢查澆口是否阻塞(污染)
8.檢查澆口尺寸
注:必要的話,加大或重新安排澆口(平
衡)
成品彎曲或扭曲
原因解決方法/檢查要點
A. 模具冷卻系統操作不正常1.檢查模具冷卻的均勻度及冷卻道有無阻塞
2.分別調整公模及母模的冷卻
B.由于塑膠定向造成縱向與橫向 1.提高料管溫度
的收縮率不同 2.調整射出速度
3.調整射出壓力
4.檢查澆口位置
注:必要的話,增加或重新安排流道位置 C. 由于色母造成成品扭曲 1.以下不含色母的色料射出來檢查色母與
塑料和成型條件溫度之間的相容性,使
射出時不會有下料不均的情況
D. 不正確的成型后收縮 1.調整冷卻時間
注:如果無法排除這個問題的話,則使用冷
卻定型劑
料頭脫模不良Array
料頭脫模不良
原因解決方法/檢查要點
A. 由于收縮不良使料頭無法脫離 1.降低保壓壓力
2.降低背壓(如果沒以使用對閉式噴嘴的話)
B. 料頭拔模不良 1.檢查料頭的拔模角度及受損情況
2.檢查料頭與噴嘴銜接處的尺寸與R角.
3.檢查是否料頭的拉拔倒勾不足
注:必要的話,加大料拉拔倒勾
C.因為料頭尚未完全凝固而折斷 1.降低料管溫度
2.調整噴嘴溫度
3.使用較小的料頭。