关于储罐施工现场自动焊焊接纵横缝的工艺及焊接角变形共11页文档
大型储罐横缝自动焊打底双面成形焊接技术

从 事 石 油 化 工 工 程 焊 接技 术 管 理 。
6 8
2l O o年第 6期
滑 , 渣容 易脱 落 ( 1 。 焊 图 )
。
.
( ) 壁 厚 l ~ 2m n a 6 3 l
( ) 壁厚 1 b 2mm
图 2 壁 板 横 缝 坡 口形 式 表 1 焊 接 参 数 图 1 背 面 垫 焊 剂 机 构 及 焊 缝 成 形 照 片
2 工 程 应 用
中国石油乌 鲁木 齐石 化 分公 司炼 油 厂原 油储 备 项 目, 拟建 四 台 5 0 的 原油 储 罐 , 司 承担 安 装 其 00 0 m 公 中的 2台储 罐 。 2 1 壁板 规格及 坡 口加工 . 该储 罐共 有 l O带 板 , 中底 部 有 8带 板 , 质 为 其 材 1 Mn 厚 度 为 1 6 R, 2~3 m; 部 有 2带 板 , 质 为 2m 上 材 Q3 2 5一B, 厚度 为 1 m。坡 V用数 控切 割机 一次 加 工 2m I 用 电锤清 理 焊 渣 , 部 成 形 差 的部 位 再 用 砂 轮 打 局
俘 搭 经验交流
大 型 储 罐 横 缝 自 动 焊 打 底 双 面 成 形 焊 接 技 术
中油吉林化 建 工程有 限公 司( 吉林 市 12 2 ) 3 0 1 沈 阳大学焊接 自动 化研 究所 ( 10 4 10 4 ) 为适应 大型 油罐 建设 项 目逐 年 增加 的趋 势 , 高 提 市 场竞争 力 , 司 开发 了横 缝 埋 弧 自动 焊 打 底 双 面 成 公 形焊接技术 , 并应用在工程项 目中 , 取得了显著的效果 。
磨 处理 。
3 结 果
采用 上 述 焊 接 工 艺 , 面 成 形 良好 , 局 部 部 位 背 除
大型储罐倒装法施工立焊自动焊接工艺

摘要:发展大型储罐倒装法施工技术过程中,为了全面实现倒装法施工罐壁立缝的全自动焊接,从焊机结构改善、罐壁组装工序调整、焊接工况改进等方面开展工作,创造出全自动气电立焊焊接的作业条件,并制定相适应的焊接工艺,最终实现了罐壁立缝的气电立焊焊接。
相较于正装法立缝自动焊接工艺,倒装法立缝自动焊接在地面操作实施,操作更加便利、安全,质量更易于控制。
关键词:大型储罐;倒装法;气电立焊中图分类号:TG409文献标识码:B 文章编号:1001-2303(2012)02-0082-02第42卷第2期2012年2月Vol.42No.2Feb.2012Electric Welding Machine李卫国(新疆石油建设有限责任公司,新疆克拉玛依834000)Automatic vertical position welding procedure of large storage tankwith the upside-down construction technologyLI Wei-guo(Xinjiang Petroleum Engineering Construction Co.,Ltd.,Karamay 834000,China)Abstract :As the development of the upsidedown construction technology of large storage ,the automatic welding in vertical position of tank shells turns into reality through adjusting welders'structure ,changing the sequence of tank shells installation ,improving the welding conditions and developing related electrogas welding procedure.The automatic vertical position welding procedure of larger storage tank with the upside-down construction technology makes welding operation easier and safer and quality higher than that with erection tank by scaffold.Key words :storage tank ;jacking method ;electrogas welding 收稿日期:2011-12-31作者简介:李卫国(1981—),男,河北满城人,工程师,主要从事压力容器制造、储罐制安等技术工作。
储罐底板焊接变形控制分析

储罐底板焊接变形控制分析摘要:储罐是石油化工生产常用的容器设备,其焊接方法较多,如手工电弧焊、半自动焊接和自动焊接等方法。
不管采取哪种焊接方法,在焊接过程中存在的主要问题是焊接变形问题,特别是储罐底板焊缝多、板厚小,施工中时常会产生较大的波浪变形等。
关键词:储罐底板;焊接变形控制;大型储罐底板焊接后的变形主要有波浪变形和角变形,通过对储罐成型的研究发现,大型储罐底板的焊接变形可以通过选择合理的组装方法、焊接顺序和焊接方法得到控制。
一、储罐底板焊接变形控制1.储罐焊接变形产生的原因储罐属于薄壁焊接容器,其焊接的主要问题是焊接变形问题,特别是钢制储罐底板厚度小、焊缝多,施焊不当经常产生较大的波浪变形,其主要原因有以下几点。
(1)焊缝的横向收缩对钢板产生的应力与变形;(2)焊缝的径向收缩对钢板产生的应力与变形;(3)底板与壁板角缝、边缘板与中幅板间环焊缝的径向收缩引起边缘板角变形和中幅板的应力与变形;(4)以上三种应力的叠加极易使钢板失稳,产生较大的波浪变形。
2. 焊接变形与焊后残余应力的关系控制大面积焊接工程的焊接变形,不能从某一方面去考虑,而应综合考虑,实践经验告诉我们,焊接过程产生的焊接变形和焊后残余应力并不是两种孤立的现象,两者之间是有机联系的,他们同时存在于同一焊件。
在实践当中,我们通过利用外部条件来约束焊缝变形,即在平焊缝处点焊上门形卡,壁板与底板的角焊缝处点焊上三角板,形成约束应力,并将焊缝全部点固,使其刚性增加。
这样就达到了增加焊接残余应力,以减少焊接变形的目的。
3. 焊接线能量。
在底板焊接前,我们还要考虑到在保证焊接质量的前提下,尽量减少焊接能量的输入,这样就从源头减少底板焊接加工的总能量,能同时减少焊接残余应力及焊接变形,这就需要我们制定合理的,正确的焊接参数,在底板焊接前,我们通过做焊接试验,通过实验焊件确定最合理的焊接电流,电压及焊接速度,选定能保证焊件焊接质量的最合理焊接线能量,并制定焊接作业指导书。
关于储罐施工现场自动焊焊接纵横缝

和罐底的工艺及焊接角变形一.焊接纵环缝角变形说明1.在储罐施工现场引起纵环缝角变形的原因主要有两点。
A .安装组对变形,就是板材安装焊缝组对时,为了试焊前满足焊缝内的间隙,达到工艺要求,强制组对,而产生的角变形。
B .焊接变形,纵环缝焊接时会对焊缝内侧和焊缝两侧进行局部加热,就会因为热涨冷缩的原理,产生应力,而产生角变形。
2.储罐现场罐体环缝焊接所产生的角变形。
由于焊接应力和焊接热收缩影响,在焊接壁板外侧时相反的一侧会出现角变形。
由于焊接焊缝外侧时,壁板已向外倾斜,即焊接焊缝内测时,为了解决角变形和罐体的整体垂直度,达到工艺要求,就要更好的控制焊缝内侧的焊接量。
3.如果焊道向内倾斜的数值小于或大于向外测倾斜的数值,产生的误差值超出允许的数值时,壁板垂直度就达不到标准的工艺要求,影响大型储罐的正常使用,控制角变形的主要措施就是焊接工艺参数和内侧焊道清根量大小的确定和控制二.焊接罐底和罐底三缝角变形说明1.在储罐施工现场引起罐底焊缝角变形的原因主要有叁点。
a.安装组对变形,就是板材安装焊缝组对时,为了试焊前满足焊缝内的间隙,达到工艺要求,强制组对,而产生的角变形。
b.没按施工工艺要求,隔道或者顺序试焊,又没采取有效的措施,产生的角变形。
c.焊接变形,平缝焊接时会对焊缝内侧和焊缝两侧进行局部加热,就会因为热涨冷缩的原理,产生应力,而产生角变形.2.在储罐施工现场引起罐底三缝角变形的原因主要有两点。
A ,焊接变形,角缝焊接时未按工艺要求,分段焊接或者焊接厚度未达到工艺要求。
B ,防焊接变形要提前做支撑,防止角变形过量三.埋弧环缝工艺参数清根控制减少角变形1,环焊缝焊接工艺控制角变形以及工艺要求:通过控制焊接工艺参数,在保证焊接质量的前提下,尽量在焊接线能量以内输入,从而减小角变形。
环缝焊接控制前后使用的工艺参数为(以第一圈环焊缝为例:变厚为32mm/25mm):电流电压外侧参数(电流A:350-500电压U:26-30焊接数度40-65),内侧电流电压参数(电流A380-500电压U:26-30焊接数度42-70)。
储罐工程焊接施工方案(3篇)

第1篇一、工程概况本工程为XX储罐项目,位于XX地区。
储罐总容量为XX立方米,包括XX座储罐,分别有XX立方米、XX立方米、XX立方米等不同规格。
储罐材质为XX,罐壁厚度为XX毫米,罐底厚度为XX毫米。
本次施工方案针对储罐主体结构进行焊接施工。
二、施工工艺1. 焊接方法:采用手工电弧焊(SAW)进行焊接,焊接方法应符合GB/T 985.1-2015《钢制焊接压力容器》的要求。
2. 焊材选择:根据储罐材质和焊接要求,选用相应的焊条,焊材牌号应符合GB/T 5293-2017《碳钢焊条》的要求。
3. 焊接顺序:按照先底板、后壁板、再顶板的顺序进行焊接。
4. 焊接设备:选用适合的焊接设备,如CO2气体保护焊机、电弧焊机等。
5. 焊接参数:根据焊材和焊接要求,确定焊接电流、电压、焊接速度等参数。
三、施工步骤1. 施工准备:对施工人员进行技术培训,确保其掌握焊接技术;准备施工所需材料、设备、工具等。
2. 罐底板焊接:先进行罐底板的焊接,采用先中心后边缘、先低后高的焊接顺序。
焊接过程中,注意控制焊接热输入,避免出现裂纹、气孔等缺陷。
3. 罐壁板焊接:罐底板焊接完成后,进行罐壁板的焊接。
先焊接罐壁板的中心线,然后逐渐向两侧扩展。
焊接过程中,注意控制焊接顺序、焊接速度和焊接热输入。
4. 罐顶板焊接:罐壁板焊接完成后,进行罐顶板的焊接。
采用先中心后边缘、先低后高的焊接顺序。
焊接过程中,注意控制焊接热输入,避免出现裂纹、气孔等缺陷。
5. 焊缝检查:焊接完成后,对焊缝进行检查,包括外观检查、无损检测等。
发现缺陷及时进行修复。
6. 焊接记录:记录焊接过程,包括焊材牌号、焊接参数、焊接顺序等。
四、质量控制1. 焊接质量应符合GB/T 985.1-2015《钢制焊接压力容器》的要求。
2. 焊接过程中,严格控制焊接热输入,避免出现裂纹、气孔等缺陷。
3. 焊接完成后,对焊缝进行检查,确保焊接质量。
4. 加强焊接过程的管理,确保焊接质量。
储罐焊接方法(重要)

T03、T04主要焊接方案根据母材化学成份和力学性能分析和焊缝使用性能要求,结合我单位施工的技术力量和以往施工的经验,罐主体焊接方法选择如下:罐壁板焊缝全部采用自动焊接工艺:纵缝采用CO2药芯双保护自动焊接,焊机为VEGA-VB-AC型气电立焊机;横缝采用美国林肯AGWISINGLE型埋弧自动焊机;罐底中幅板的焊接采用半自动焊打底+碎焊丝+高速埋弧自动焊盖面成型;罐底大角缝采用手工焊内外打底,角缝自动焊填充盖面;浮顶及附件的焊接采用CO2半自动焊和手工电弧焊相结合的焊接方法,其中浮顶底板必须采用手工电弧焊。
6.1罐底的焊接为减少罐底的焊接变形,采用自由收缩法施工,罐底组对焊接顺序为:边缘板组对、点焊→焊接边缘板外侧300mm焊缝→中幅板短焊缝组对焊接→长焊缝组对焊接→组对焊接通长缝→边缘板与壁板大角缝组对焊接→边缘板剩余对接焊缝焊接→边缘板与中幅板收缩缝组对焊接。
6.1.1罐底中幅板的焊接1、罐底中幅板全部为对接加垫板的结构形式。
罐底施焊两遍,初层焊的焊肉为7mm,凸出部分采用砂轮机打磨至6 mm,并进行着色检查,合格后再施焊第二遍。
中幅板的焊接方法为:打底焊采用CO2气体保护半自动焊,盖面采用添加碎焊丝的高速埋2、中幅板的组对点焊要严格按焊接作业指导书规定的程序执行。
3、中幅板组对完后,应用钢丝刷清除干净坡口及两侧25mm内的锈、赃物,方可进行施焊。
4、罐底中幅板焊接时应采用分段退步施焊。
先焊短缝,后焊长缝,最后施焊通长缝。
通长缝焊前应使用大型槽钢及龙门板进行加固,以减少焊接变形。
通长缝的焊接,由中心开始向两侧分段退步施焊,焊至距边缘板300mm处停止施焊。
5、对较多平行排列的焊缝(长缝),应由二台焊机从中心向外对称隔缝施焊,施焊程序如附图2:6.为减少中幅板短缝和长缝在焊接后两端产生的下凹变形,中幅板短缝和长缝的端部应在焊道两侧加短背杠,同时端部焊接预留长度尽量短,以不焊至垫板为原则。
6.1.2边缘板的焊接1、边缘板的焊接采用手工电弧焊,顺序为:先焊外侧500mm,由外向内施焊,注意层间接头相互错开30-50mm,外侧加引弧板防止起弧产生缺陷。
储罐横缝埋弧自动焊打底焊接技术

储罐横缝埋弧自动焊打底焊接技术1 前言随着国家对石油消耗和储备的增长,原油、成品油储罐向大型化发展已成必然趋势。
焊接是储罐建造中的主要工序,对储罐质量和最终成本起着关键作用。
因此,进行储罐焊接新技术开发,是实现社会效益和企业效益最大化的必需,是每个石油华工设备制造和安装企业的职责。
2007年年初,我公司将储罐横缝埋弧焊打底焊接技术作为重点项目进行了开发,并成功应用在新疆独乌鲁木齐石化公司炼油厂2台5万立原油储罐的焊接施工中。
本文在简要介绍国内储罐横缝焊接技术现状的基础上,论述了大型储罐横缝埋弧自动焊打底焊接技术的特点、工艺和应用范围。
2 国内储罐横缝焊接技术现状2.1 拱顶储罐横缝的焊接国内拱顶储罐的容积多为1万立及以下,最大的为3万立。
这类储罐钢板相对较薄,且多采用倒装法组装,所以,在焊接上多直接采用手工焊条电弧焊。
对于较厚钢板(厚度大于10mm)的横缝焊接,亦可以采用埋弧自动焊焊接,但仍需采用手工焊条电弧焊或CO2半自动焊进行打底焊接。
2.2 大型浮顶储罐横缝的焊接近年来,国内一些焊机生产厂家陆续开发了多种型号的储罐环缝埋弧自动焊设备,使大型浮顶储罐横缝的埋弧焊得到了更加广泛的应用。
在焊接顺序上通常是:先焊外侧焊缝、外侧焊完后对背面进行清根处理(通常采用碳弧气刨加砂轮打磨,也可采用其他机械方法)、然后再采用埋弧自动焊完成背面的焊接,或者采用在外侧采用手工焊条电弧焊打底,埋弧自动焊直接进行背面填充、盖面的方法。
2.3 储罐横缝焊接亟待解决的问题一方面,由于打底仍需采用人工,对于大型储罐,存在人工时增加、效率提高不彻底、工人劳动强度大等问题;另一方面,大量的清根处理,浪费材料,污染环境,工序的增加也会带来工期延长,成本增加等直接经济损失。
3 储罐横缝埋弧自动焊打底焊接技术3.1 储罐横缝埋弧自动焊打底焊接,是通过采取一定技术措施和合适的焊接工艺参数,使采用埋弧自动焊进行打底即可获得良好的背面成形或焊透,以实现背面不清根或少量清根为目的的一种焊接技术。
大型储罐焊接工艺及如何控制变形的策略
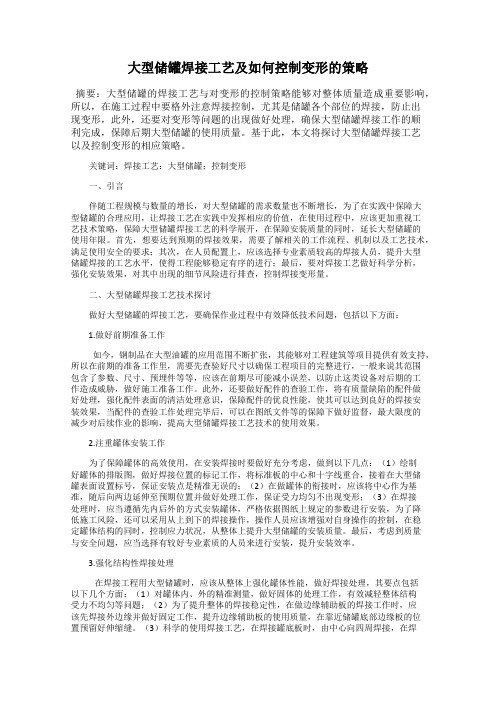
大型储罐焊接工艺及如何控制变形的策略摘要:大型储罐的焊接工艺与对变形的控制策略能够对整体质量造成重要影响,所以,在施工过程中要格外注意焊接控制,尤其是储罐各个部位的焊接,防止出现变形,此外,还要对变形等问题的出现做好处理,确保大型储罐焊接工作的顺利完成,保障后期大型储罐的使用质量。
基于此,本文将探讨大型储罐焊接工艺以及控制变形的相应策略。
关键词:焊接工艺:大型储罐;控制变形一、引言伴随工程规模与数量的增长,对大型储罐的需求数量也不断增长,为了在实践中保障大型储罐的合理应用,让焊接工艺在实践中发挥相应的价值,在使用过程中,应该更加重视工艺技术策略,保障大型储罐焊接工艺的科学展开,在保障安装质量的同时,延长大型储罐的使用年限。
首先,想要达到预期的焊接效果,需要了解相关的工作流程、机制以及工艺技术,满足使用安全的要求;其次,在人员配置上,应该选择专业素质较高的焊接人员,提升大型储罐焊接的工艺水平,使得工程能够稳定有序的进行;最后,要对焊接工艺做好科学分析,强化安装效果,对其中出现的细节风险进行排查,控制焊接变形量。
二、大型储罐焊接工艺技术探讨做好大型储罐的焊接工艺,要确保作业过程中有效降低技术问题,包括以下方面:1.做好前期准备工作如今,钢制品在大型油罐的应用范围不断扩张,其能够对工程建筑等项目提供有效支持,所以在前期的准备工作里,需要先查验好尺寸以确保工程项目的完整进行,一般来说其范围包含了参数、尺寸、预埋件等等,应该在前期尽可能减小误差,以防止这类设备对后期的工作造成威胁,做好施工准备工作。
此外,还要做好配件的查验工作,将有质量缺陷的配件做好处理,强化配件表面的清洁处理意识,保障配件的优良性能,使其可以达到良好的焊接安装效果,当配件的查验工作处理完毕后,可以在图纸文件等的保障下做好监督,最大限度的减少对后续作业的影响,提高大型储罐焊接工艺技术的使用效果。
2.注重罐体安装工作为了保障罐体的高效使用,在安装焊接时要做好充分考虑,做到以下几点:(1)绘制好罐体的排版图,做好焊接位置的标记工作,将标准板的中心和十字线重合,接着在大型储罐表面设置标号,保证安装点是精准无误的;(2)在做罐体的衔接时,应该将中心作为基准,随后向两边延伸至预期位置并做好处理工作,保证受力均匀不出现变形;(3)在焊接处理时,应当遵循先内后外的方式安装罐体,严格依据图纸上规定的参数进行安装,为了降低施工风险,还可以采用从上到下的焊接操作,操作人员应该增强对自身操作的控制,在稳定罐体结构的同时,控制应力状况,从整体上提升大型储罐的安装质量。
贮罐现场组焊防变形安装技术

贮罐现场组焊防变形安装技术摘要:贮罐在现场制作组焊过程中,由于钢板厚度薄,相对刚度小,直径大,焊缝长,在焊接热影响作用下,焊缝纵向收缩量大,在罐体上很容易产生各种变形,而变形控制是难度最大的一项工作。
关键词:贮罐组焊Abstract: made on site storage tank compound process, because the thickness of the steel plate thin, relatively small stiffness, large in diameter, and weld in length, under the action of heat on welding the weld lengthwise shrinkage, in the tank is easy to produce all sorts of deformation, and deformation control is one of the most difficult work.Keywords: storage compound1、贮罐施工变形的主要表现在罐底板上主要表现为鼓包;在罐顶上主要表现为鼓包和塌陷;在罐壁上可造成罐壁椭圆度、垂直度和环缝处局部内凹度超标的现象。
罐底鼓包变形可通过采用先短后长、先中间后两边、先壁板与弓形板后弓形板与底板的焊接程序,配以对称施焊,比较容易控制鼓包的发生。
罐顶变形也可采用先安装骨架后铺板、先短后长、先中间后两端对称施焊的施工程序,也可以控制其变形。
在施工过程中,总结了如下控制罐壁变形的施工措施。
1.1 罐壁产生变形的原因罐壁环缝局部内凹变形的最直接的原因是焊缝纵向收缩和横向收缩。
1)焊缝纵向收缩引起内凹的原因在焊接过程中,焊接热量对钢板造成局部不均匀加热,引起钢板不均匀膨胀和收缩而产生变形。
即在焊接热源周围的钢板受热后要膨胀,但又被相邻温度低的金属约束,当温差较大时,这些膨胀受阻的金属将产生压缩塑性变形,温差越大,产生的变形量也就越大。
钢结构工程储罐埋弧自动横焊施工工法

埋弧自动横焊焊接施工工法1 前言为了在储罐焊接中贯彻执行国家的技术经济政策,做到技术先进,经济合理,安全适用,确保质量,公司进行了科技创新,形成了储罐埋弧自动横焊焊接新颖的施工工法。
通过几个项目的实际应用,焊接速度和焊接质量有了明显的提高,达到了预期的效果,技术先进合理,取得了良好的经济效益。
本工法编写是遵循国家相关法律法规及美国国家标准API620(“大型焊接低压储罐设计和建造”)和ASME(美国机械工程师协会)标准有关要求进行。
2 工法特点2.1 储罐埋弧自动横焊的生产率高,焊接速度快,而且焊接变形小。
2.2 焊剂层对焊缝金属的保护好,使金属充分熔透,焊缝表面缺陷少,成形美观内在质量好。
2.3 由于电弧被焊剂保护着,使电弧的热得到充分利用,从而节省了电能;2.4 除减少劳动量之外,由于自动焊时看不到弧光,焊接过程中发出的气体量少,这对保护焊工眼睛和身体健康是很有益。
2.5用机器代替人工,大大降低生产成本,降低安全风险,经济效益显著。
3 适用范围适用于造船、石油、石化和电力等行业,且板厚在10mm~45mm范围内、直径大于等于6m、每节板幅在1~3.2m范围内的钢制大型储罐环形横向焊缝的焊接施工。
4 工艺原理储罐埋弧自动横焊,由多台埋弧横焊机沿罐壁圆周均匀对称布置,采用同向、同速、先焊外壁后焊内壁的焊接工艺进行施焊。
外壁焊接完成后,内壁先用磨光机打磨清根,充分保证内壁坡口不受破坏,然后再将焊机移到内壁进行焊接。
5 施工工艺流程及操作要点5.1 施工工艺流程见图5.1。
图5.1 施工工艺流程图5.2 操作要点5.2.1 坡口加工形式横向焊缝埋弧自动焊接,应采用双面K形坡口。
由于首层焊缝需要采用手工电弧焊封底,坡口的钝边要留得小一些,一般2-3mm,有利于第一层焊透。
其坡口形式参见图5.2.1。
图5.2.1 坡口示意图坡口的制备最好采用机械法刨削,如现场加工有困难,也可以用火焰切割法加工,但要求采用半自动割机,以保证坡口的形状和尺寸准确,坡口面进行磨光处理。
储罐施工过程中预防焊接应力及焊接变形的技术措施

储罐施工过程中预防焊接应力及焊接变形的技术措施摘要:储罐是石油化工中油品和各种液体化学品的储存设备,是石油化工装置和储运系统设施的重要组成部分。
储罐施工主要要求是在保证质量安全的前提下,缩短施工周期、提高经济效益和安全性。
本文以凯瑞英项目储罐建造项目为实例,结合实际情况,运用理论知识,浅谈防止储罐焊接变形、焊接应力的措施方法。
关键词:储罐;技术总结;焊接变形;焊接应力;措施一、引言本文以山东凯瑞英羟脲磺胺类医药中间体产业链项目消防给水及加压泵站2台6000m³拱顶储罐为例,进行储罐施工过程中预防焊接应力及焊接变形的技术措施的技术总结。
2台6000m³拱顶储罐中单台储罐重量约180吨,直径22000mm,高度为20772mm;底板厚度为10mm;各带壁板厚度6~18mm之间。
储罐一般刚性较差,板薄,施工过控制焊接应力、焊接变形非常重要。
二、储罐焊接应力与焊接变形储罐焊接过程中由于温度场的变化及焊件的约束,在焊缝及附近区域产生应力成为焊接应力。
焊接过程中产生的应力超过材料的弹性极限,以至于冷却后在焊件中留有未能消除的应力称为残余应力。
焊接热输入引起材料局部加热,使焊缝区融化,而熔池毗邻的高温区材料的热膨胀则受到周围材料的限制,受压产生变形。
在冷却过程中,已发生变形的这部分材料又受到周围材料制约,不能自由收缩,在不同程度上又拉伸而产生变形。
与此同时,熔池凝固,金属冷却收缩也产生了相应的收缩拉应力和变形。
这种随焊接热过程而变化的内应力场和构件变形,称为瞬态应力与变形。
在室温条件下,焊后残留于构件中的内应力场和宏观变形称为焊接残余应力与焊接残余变形。
三、储罐焊接应力及变形的危害当外部载荷的应力与结构中某区域的残余应力叠加之和达到屈服点时,这一区域的材料就会产生局部塑形变形,丧失了进一步承受外部载荷的能力,造成结构的有效截面积减小,结构的刚度也随之降低。
如材料处于脆性状态,则拉伸残余应力和外部载荷应力叠加有可能使局部区域的应力首先达到断裂强度,导致结构早期破坏。
储罐焊接技术方案
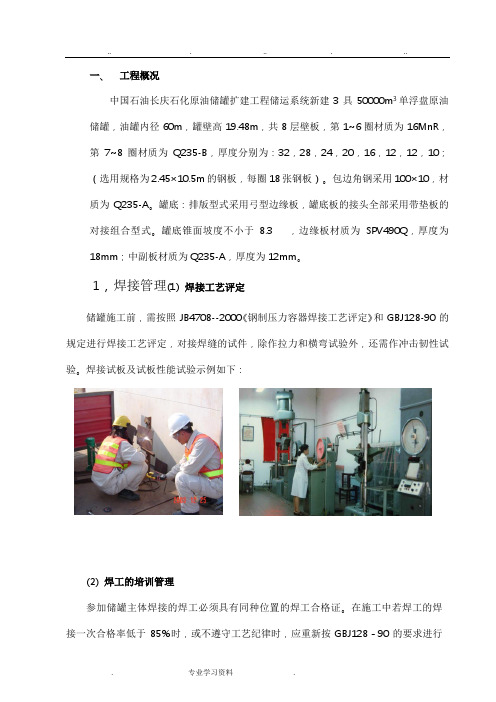
一、 工程概况中国石油长庆石化原油储罐扩建工程储运系统新建3具50000m 3单浮盘原油储罐,油罐内径60m ,罐壁高19.48m ,共8层壁板,第1~6圈材质为16MnR ,第7~8圈材质为Q235-B ,厚度分别为:32,28,24,20,16,12,12,10;(选用规格为2.45×10.5m 的钢板,每圈18张钢板)。
包边角钢采用100×10,材质为Q235-A 。
罐底:排版型式采用弓型边缘板,罐底板的接头全部采用带垫板的对接组合型式。
罐底锥面坡度不小于8.3 ,边缘板材质为SPV490Q ,厚度为18mm ;中副板材质为Q235-A ,厚度为12mm 。
1,焊接管理(1) 焊接工艺评定储罐施工前,需按照JB4708--2000《钢制压力容器焊接工艺评定》和GBJ128-90的规定进行焊接工艺评定,对接焊缝的试件,除作拉力和横弯试验外,还需作冲击韧性试验。
焊接试板及试板性能试验示例如下:(2) 焊工的培训管理参加储罐主体焊接的焊工必须具有同种位置的焊工合格证。
在施工中若焊工的焊接一次合格率低于85%时,或不遵守工艺纪律时,应重新按GBJ128-90的要求进行培训和考试,考试合格后方能重新参与主体焊接。
若再有上述现象发生,则取消该焊工的施焊资格。
(3) 焊接材料管理焊接材料应有质量合格证明。
焊接材料应设专人负责保管,并按规定进行烘干和使用。
焊接材料应按部位领用,焊材管理人员应作好记录。
焊接材料应保管在避风露,通风好,不潮湿的仓库内,湿度不大于60%。
(4) 焊接环境管理在下列任何一种情况下如不采取有效措施不能进行焊接:雪天或雨天。
手工焊时,风速超过8m/s;气电气焊时,风速超过2.2m/s。
大气相对湿度超过90%。
焊接环境气温:普通碳素钢低于-20℃时;低合金钢低于0℃时。
5.2 焊接施工(1) 罐底焊接由于自动焊焊接电流较大,自动焊直接焊接容易产生焊穿等影响质量的缺陷,因此罐底采用手工焊打底、自动焊填充。
2019罐体横缝双面自动化焊接设备及焊接工艺.doc

罐体横缝双面自动化焊接设备及焊接工艺第37卷第12期2OO7年12月重晖拽ElectricWeldingMachineV o1.37No.12Dec.2oo7罐体横缝双面宜动化焊接设备及焊接i艺李景波,王刚,沙玉章,李建军,李群智,李德明,王保青,陈玉杰(1.沈阳大学,辽宁沈阳l10044;2.华北石油工程建设有限公司,河北任丘062552)摘要:通过对大型罐主体建设施工现场的研究,分析了罐体自动化焊接施工的特性,开发研制成功了罐体横环缝双面埋弧自动焊接操作机.焊接效率高,焊接质量好,极大地减轻了工人的劳动强度,降低了综合成本,有广阔的应用前景.关键词:双面埋弧自动焊;横环缝;焊接工艺中图分类号:TG423文献标识码:A文章编号:1001-2303(2007)12--0024—03 Studyondouble?sideautomaticweldingtechnologyandequipmentof girthseamofcontainerbodyLIJing—bo,WANGGang,SHAYu—zhang,LIJian-jun,LIQu—zhi2,LIDe—mind,WANGBao—qing2,CHENYu-jie(1.ShenyangUniversity,Shenyang110044,China;2.HuabeiPetroleumEngineeringConstr uctionCorporation,Renqiu062552,China)Abstract:Thepaperanalyzesthepropertiesofautomatizationweldingbuildingofcontainerb odybystudingonbuildingsiteoflargy—typecontainerbody.Wedevelopedsuccessfullydouble—sideautomatizationsubmergedarcweldingmanipulatoroftransverseand girthseamofcontainerbody.Theweldingtechnologyisadvanced,weldingefficiencyimpro vedlargely,weldingqualityisgood,labourstrengthofworkerlightensgreatly,thecomprehensivecostdecreasesandapplicationprospe ctisextensive.Keywords:double.sideautomaticsubmergedarcwelding;girthseam;weldingtechnique U刖肓近年来随着我国经济的发展,大型钢结构建设突飞猛进,特别是战备储油库,氧化铝种分槽,冶金钢铁高炉等建设的规模已越来越大,罐体的建设也越来越多,如何提高焊接质量,焊接效率和工程进度,是施工建设单位迫切需要解决的问题.我们在前期开发研制自动化焊设备的基础上,根据罐体的施工特点,开发了成套自动化焊接设备,即在罐体横环缝焊接中,采用"横缝单面埋弧自动焊接机GHH_Ⅱ",单面横焊时正面多道焊接完成后,背面必须进行清根,打磨处理,再用"单面横焊机"挂在背面,再进行多道焊接,罐体壁板横缝根部焊接质量难以保障一次焊接成形.为了保证根部的焊接质量,提高焊接效率,研制收稿日期:2007—09-30作者简介:李景波(1956--),男,辽宁沈阳人,教授级高工,主要从事大型钢结构焊接自动化设备的研究工作.了"横缝双面埋弧自动焊接机SGHH—II",如图1所示.实现横环焊缝双面同时焊接,打底焊接双面一次成形,再进行多道焊.提高了焊缝质量.我们已研制了8套这种设备,使用效果良好.图1横缝双面埋弧自动焊接机SGHH—II专题讨论李景波等:罐体横缝双面自动化焊接设备及焊接工艺第l2期1单面横缝埋弧自动焊接设备组成1-1单面横环缝埋弧自动焊接机GHH—II设备构成该设备主要由铝合金板罩面载体操作车,大车行走机械系统及控制系统,焊接送丝系统,焊枪调整装置,焊剂自动循环输送回收器,焊接自动控制系统,焊接电源,配电装置等组成.1.2主要特点单面横环缝埋弧自动焊接机的大车悬挂在罐体的壁上,以罐壁上边缘为导向沿罐壁行走,行走轮采用白位机构,可以随罐壁的曲率自行转弯,能适宜小直径罐体,完成横环缝的多道多层埋弧自动化焊接.埋弧焊剂自动输送回收,循环使用,减少了损耗.焊接操作大车载体外形封闭,铝合金板罩面,抗风性能强,适合野外和高空作业.车体轻便,操作员在其内部作业,操作简单,安全可靠,焊接效率高.适用于正装法施工的圆筒型罐体横环缝焊接,可焊罐体直径一般大于5ITI,适应焊接板幅宽度范围(即简体每节高度)1.4-3.0m,可以焊接板厚8-50mm.2双面横缝埋弧自动焊接设备组成双面横缝埋弧自动焊接操作机的主要参数如双面横缝埋弧自动焊接操作机的组成和特点:(1)将2台单面横缝埋弧自动焊机顶部通过铰链组合在一起,利用其中l台的行走传动系统,组合为双面横缝埋弧自动焊接操作机.图l所示为悬挂在罐体壁板的正,背两面,焊机骑挂在罐体的壁上,以罐壁上边缘为导向,沿罐壁行走平行焊缝,进行焊接.(2)双面横焊机的内部组成各自保持单面横焊机内配套的焊接电源,焊接送丝系统,焊枪,调整装置,焊剂托盘,焊剂循环输送回收器,焊接自动控制箱,焊接电缆,照明装置等器件.(3)由于2台车体工作,质量增加,驱动力增大.为保证焊接工作的平稳性,采用双驱动系统,工作时由一组行走系统双驱动,两套焊接系统同时工作, 即两把焊枪同时焊接.(4)焊接时,一面(正面)为主操作者,另一面(背面)为副操作者.为保证焊接操作者在正,背两面同步,协调工作,安装了同步控制器,保证双方联系. (5)增加了支撑装置和顶靠装置,保证施工过程中焊接操作机的安装与罐壁钢板不干涉,罐壁钢板背面的工艺夹具方便安装拆卸.(6)该机安装拆卸方便,拆卸后可以恢复为l台独立的横缝单面埋弧自动焊接操作机.(7)若背面不焊接,可以做为拖弧系统,实现打表1所示.底单面焊双面成形.表1双面横缝埋弧自动焊接机SGHH—II主要参数3横缝双面埋弧自动焊施工工艺双面横环缝埋弧焊采用多层多道焊接,其焊接坡口,焊缝层次等规范参数,都要按其特定的条件做相应的变动,以适应双面焊接过程的需要.3.1焊接坡口组对(1)坡口形式.常见坡口形式和双面横缝焊接过程如图2所示.双面横环缝埋弧自动焊接,罐壁板筒体上侧的坡口根据板厚情况可以加工成等边或不等边K形坡口,单边V形40.-45.坡口.钝边l~2nqffl,组对间隙2-3mm.(2)坡口制作.为保证坡口加工的一致性,罐壁板筒体上的坡口最好采用机械法刨削.如果现场加工有困难,也可以采用火焰切割法加工,但要求采用半自动割机来进行,以保证坡口的形状和尺寸精确度达到要求.(3)坡口组对后,罐壁钢板背面的工艺夹具必须可靠,背杠可以方便快捷地拆卸.3.2焊接过程(1)焊缝层次.横环缝埋弧自动焊常采用多层多道焊.焊接的板厚不同,层数也不同,板越厚,焊接层数越多.单面焊接时,通常先焊外壁,后焊内壁.步骤是:打底层一填充一盖面.图3为正面焊接过程. 双面横缝埋弧自动焊与单面横缝埋弧自动焊的最大不同就是解决打底层——即第一道焊接为双面同时焊接,一次成形.(2)由于正面焊接与背面焊接是两个焊接系统?25?题l1|^专蠢讨论雹晖俄第37卷Ba坡几形式和焊缝层次b实物图2坡口形式与双面横环缝实物图3正面焊接过程同时_丁作,焊接速度同步,所以要求正面与背面的焊枪应有一相对的位置,错位大约30-50mm.焊接的压道方式如图2所示.(3)开始焊接前,两面操作者调节好焊枪位置,由正面操作者起动行车,罐壁板坡口小的一侧先起弧,坡口大的一侧后起弧.焊接熔池开始形成时,正面铁水流动到背面,被背面的焊剂阻挡,当背面的焊接熔池形成时其正面已经成形,两面的打底层焊道不能被击穿,由于双面焊接熔池形成,产生热效率更高,根部焊接质量?26?幺∞得以提高.从而实现双面焊一次成形.(4)确定焊枪角度.焊前可通过调整装置旋转,一般应为15.-25.的倾斜角度,有利于焊缝成形.(5)填充焊接.焊接下一道焊缝前,应对前一道焊缝进行修整清理,进行填充焊接,保证焊缝的熔合性.焊缝的填充量要根据坡口大小调节焊接速度来控制.(6)焊缝外观焊道即盖面.焊道要排列整齐,宽度比坡口面增宽2~4n'lln,余高0~2mm.余高差小于等于2mm,无明显的凸起或沟槽,如图4所示.图4焊缝表面质量(7)X线检查焊缝达到施l丁要求.3.3焊接工艺参数焊接工艺参数如表2所示.表2焊接工艺参数4结论(1)通过大量的工艺实验,工艺评定合格,达到实际应用阶段,现已有8套这种焊机用于大型10万m石油原油储罐罐体主体工程施工中,其焊接过程稳定可靠.(2)采用双面横环缝埋弧自动焊接工艺,解决了打底焊道最关键的一条焊缝,避免了打底焊道易出现焊穿,夹渣,未熔合等缺陷.(3)内外侧壁同时焊接完毕,避免对罐体内侧坡口用碳弧气刨或角磨砂轮清根,减少罐体的变形. 极大地提高了焊接质量,减轻了T人的劳动强度,降低了综合成本.(4)现场施工中各工序应合理配合,制定合理的焊接工艺.。
钢结构工程储罐埋弧自动横焊施工工法

埋弧自动横焊焊接施工工法1 前言为了在储罐焊接中贯彻执行国家的技术经济政策,做到技术先进,经济合理,安全适用,确保质量,公司进行了科技创新,形成了储罐埋弧自动横焊焊接新颖的施工工法。
通过几个项目的实际应用,焊接速度和焊接质量有了明显的提高,达到了预期的效果,技术先进合理,取得了良好的经济效益。
本工法编写是遵循国家相关法律法规及美国国家标准API620(“大型焊接低压储罐设计和建造”)和ASME(美国机械工程师协会)标准有关要求进行。
2 工法特点2.1 储罐埋弧自动横焊的生产率高,焊接速度快,而且焊接变形小。
2.2 焊剂层对焊缝金属的保护好,使金属充分熔透,焊缝表面缺陷少,成形美观内在质量好。
2.3 由于电弧被焊剂保护着,使电弧的热得到充分利用,从而节省了电能;2.4 除减少劳动量之外,由于自动焊时看不到弧光,焊接过程中发出的气体量少,这对保护焊工眼睛和身体健康是很有益。
2.5用机器代替人工,大大降低生产成本,降低安全风险,经济效益显著。
3 适用范围适用于造船、石油、石化和电力等行业,且板厚在10mm~45mm范围内、直径大于等于6m、每节板幅在1~3.2m范围内的钢制大型储罐环形横向焊缝的焊接施工。
4 工艺原理储罐埋弧自动横焊,由多台埋弧横焊机沿罐壁圆周均匀对称布置,采用同向、同速、先焊外壁后焊内壁的焊接工艺进行施焊。
外壁焊接完成后,内壁先用磨光机打磨清根,充分保证内壁坡口不受破坏,然后再将焊机移到内壁进行焊接。
5 施工工艺流程及操作要点5.1 施工工艺流程见图5.1。
图5.1 施工工艺流程图5.2 操作要点5.2.1 坡口加工形式横向焊缝埋弧自动焊接,应采用双面K形坡口。
由于首层焊缝需要采用手工电弧焊封底,坡口的钝边要留得小一些,一般2-3mm,有利于第一层焊透。
其坡口形式参见图5.2.1。
图5.2.1 坡口示意图坡口的制备最好采用机械法刨削,如现场加工有困难,也可以用火焰切割法加工,但要求采用半自动割机,以保证坡口的形状和尺寸准确,坡口面进行磨光处理。
储罐焊接方法(重要).doc

T03、T04 主要焊接方案根据母材化学成份和力学性能分析和焊缝使用性能要求,结合我单位施工的技术力量和以往施工的经验,罐主体焊接方法选择如下:罐壁板焊缝全部采用自动焊接工艺:纵缝采用 CO2 药芯双保护自动焊接,焊机为VEGA-VB-AC 型气电立焊机;横缝采用美国林肯 AGWISINGLE 型埋弧自动焊机;罐底中幅板的焊接采用半自动焊打底 +碎焊丝 +高速埋弧自动焊盖面成型;罐底大角缝采用手工焊内外打底,角缝自动焊填充盖面;浮顶及附件的焊接采用CO2 半自动焊和手工电弧焊相结合的焊接方法,其中浮顶底板必须采用手工电弧焊。
6.1 罐底的焊接为减少罐底的焊接变形,采用自由收缩法施工,罐底组对焊接顺序为:边缘板组对、点焊→焊接边缘板外侧 300mm 焊缝→中幅板短焊缝组对焊接→长焊缝组对焊接→组对焊接通长缝→边缘板与壁板大角缝组对焊接→边缘板剩余对接焊缝焊接→边缘板与中幅板收缩缝组对焊接。
6.1.1 罐底中幅板的焊接1、罐底中幅板全部为对接加垫板的结构形式。
罐底施焊两遍,初层焊的焊肉为 7mm,凸出部分采用砂轮机打磨至 6 mm,并进行着色检查,合格后再施焊第二遍。
中幅板的焊接方法为:打底焊采用CO2 气体保护半自动焊,盖面采用添加碎焊丝的高速埋弧自动焊。
焊接工艺如下:焊接参数保护材质规格焊接方法焊材规格电流( A)电压( V)速度 cm/minQ235B 11mm GMAW ER50-6 φ1.2 240-320 30-40 18-30 CO2Q235B 11mm SAW H08A φ3.2 480-540 27-30 40-502、中幅板的组对点焊要严格按焊接作业指导书规定的程序执行。
3、中幅板组对完后,应用钢丝刷清除干净坡口及两侧25mm 内的锈、赃物,方可进行施焊。
4、罐底中幅板焊接时应采用分段退步施焊。
先焊短缝,后焊长缝,最后施焊通长缝。
通长缝焊前应使用大型槽钢及龙门板进行加固,以减少焊接变形。
大型储罐施工中的焊接变形控制
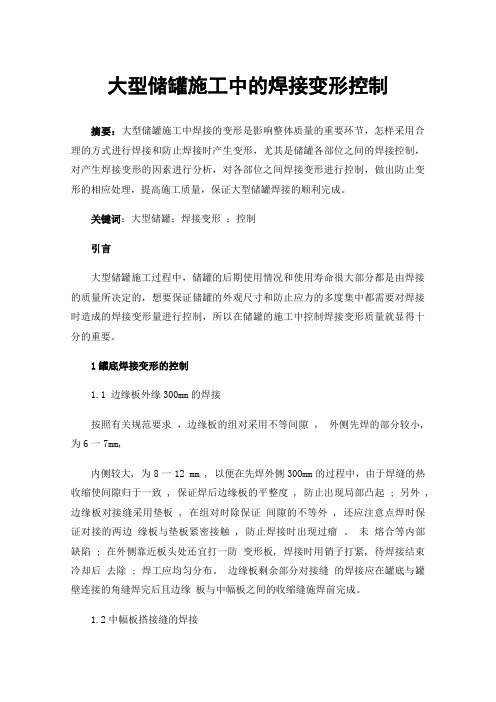
大型储罐施工中的焊接变形控制摘要:大型储罐施工中焊接的变形是影响整体质量的重要环节,怎样采用合理的方式进行焊接和防止焊接时产生变形,尤其是储罐各部位之间的焊接控制,对产生焊接变形的因素进行分析,对各部位之间焊接变形进行控制,做出防止变形的相应处理,提高施工质量,保证大型储罐焊接的顺利完成。
关键词:大型储罐;焊接变形;控制引言大型储罐施工过程中,储罐的后期使用情况和使用寿命很大部分都是由焊接的质量所决定的,想要保证储罐的外观尺寸和防止应力的多度集中都需要对焊接时造成的焊接变形量进行控制,所以在储罐的施工中控制焊接变形质量就显得十分的重要。
1罐底焊接变形的控制1.1 边缘板外缘300mm的焊接按照有关规范要求,边缘板的组对采用不等间隙,外侧先焊的部分较小, 为6一7mm,内侧较大, 为8一12 mm , 以便在先焊外侧30Omm的过程中,由于焊缝的热收缩使间隙归于一致 , 保证焊后边缘板的平整度 , 防止出现局部凸起 ; 另外 , 边缘板对接缝采用垫板 , 在组对时除保证间隙的不等外 , 还应注意点焊时保证对接的两边缘板与垫板紧密接触 , 防止焊接时出现过瘤、未熔合等内部缺陷 ; 在外侧靠近板头处还宜打一防变形板, 焊接时用销子打紧, 待焊接结束冷却后去除 ; 焊工应均匀分布。
边缘板剩余部分对接缝的焊接应在罐底与罐壁连接的角缝焊完后且边缘板与中幅板之间的收缩缝施焊前完成。
1.2中幅板搭接缝的焊接焊接顺序的原则是将罐底板由单块焊接成一组两块,再由一组两块焊接成一组四块,依此类推。
焊前预留的收缩缝应分开,使每组罐底独立,自由收缩,以减少或防止因温度变化和焊接收缩不均匀引起的罐底中心偏移。
类似的相邻焊缝不应同时焊接,应逐个焊接。
较长的接头应分段退焊,每段1.5~2m。
走廊板的长缝应从中心向两端分段退焊。
每层焊道的接头应错开50~100mm。
其他焊缝完成后,应进行点焊和焊接。
值得注意的是,在实际施工中,我们在与边缘板连接的每个接缝处预留500~800mm,不需焊接,待中间板与边缘板的收缩缝最终焊接好后再焊接在一起。
《罐体焊接工艺》word版

2〕以海底阀法兰内孔配做割制:圆孔∮190。
手动等离子割机
2.底部放油孔开孔:图14
割孔边缘光滑,圆孔位置尺寸公差±5mm,
1〕以罐体后封头短轴为基准,在罐体筒体底部纵向中心线
810mm处处划线,画出底部放油口中心线。
5米盒尺、石笔
2〕以底部放油口中心线,割制底部放油口圆孔∮120。
3.弧度滚压成型。
卷板机、5米盒尺
保证尺寸150
40
转序
整形、修边;检验转序。
同上
防波板旋制
10
准备
检查防波板领料尺寸、数量:2080*1450*5 3件。并确认无误。
CO2焊机
30
旋制
防波板尺寸要求:长轴=2000mm;短轴=1370mm
旋边机、5米盒尺
公差要求:长轴0-3mm,短轴0-2mm,
1.划线:周边向内35mm
漏焊、咬边等焊接缺陷。
50
转序
清理、修整焊缝,检验转序。
同上
电流<A>
220~240
电压<V>
21~23
标记
处数
更改文件号
签字〔日期〕
标记
处数
更改文件号
签字〔日期〕
编制〔日期〕
审核〔日期〕
批准〔日期〕
工步号
工序名称
工序内容
使用设备及工装
质量要求及注意事项
20
防波板焊接
图9所示以前封头向后1430mm划线,点焊三角定位板于筒身
10
自检
检查板料的板厚、几何尺寸、板料表面质量,并确认无误。
5米盒尺
筒身材料尺寸:5680X1440X4 3件
大型储罐自动焊接横立焊存在的缺陷及修正探析

大型储罐自动焊接横立焊存在的缺陷及修正探析摘要:本文主要探讨了大型储罐自动横立焊接存在的缺陷及其修正方法。
从大型储罐横立焊接技术的应用现状及存在的问题出发,详细介绍了横立焊接中可能存在的缺陷,包括焊接质量、焊缝性能、安全性等方面,并针对缺陷提出当前主流的大型储罐横立焊接修正方法,包括加强焊接质量控制,提高焊接技术水平等方法,以期为大型储罐横立焊接的质量和安全提供参考依据。
关键词:大型储罐;自动横立焊接;存在缺陷;修正方法当前工业化的日益发展,大型储罐的需求日益增加,而自动焊接技术的出现为大型储罐的制造提供了便利。
焊接工作是储罐建造的重要工序,焊接质量对于储罐的质量具有决定性的意义。
但是,自动焊接也存在着一些缺陷,影响着大型储罐的质量和安全。
因此,针对这些缺陷需要制定控制策略,能够真正意义上保障大型储罐施工过程中的焊接质量和安全。
1.大型储罐横立焊接技术的应用现状及存在的问题大型储罐横立焊接技术是一种自动化焊接技术,广泛应用于石化、化工、医药等行业中。
与传统的手工焊接相比,自动焊接具有高效、高精度、高质量等优点。
但是,在实际应用中,大型储罐横立焊接也存在一些问题。
首先,由于大型储罐体积较大,所以横立焊接的质量问题成为制约其使用的主要因素之一。
大型储罐横立焊接质量差会导致焊接强度不足,从而影响储罐的使用寿命。
其次,焊缝性能问题也是大型储罐横立焊接中存在的问题之一。
由于横立焊接的焊接面积较大,所以焊缝性能的差异也会对整个储罐的使用产生影响。
例如,焊缝的裂纹、缺陷等问题可能会导致储罐漏油或发生安全事故。
最后,大型储罐横立焊接的安全性问题也不容忽视。
横立焊接需要高度自动化设备进行操作,如果设备的安全保障措施不够完善,就可能导致焊接事故的发生,严重危及人员的生命安全和财产安全。
2.大型储罐横立焊接中可能存在的缺陷2.1焊接质量问题大型储罐横立焊接质量问题是制约其使用的主要因素之一。
在实际操作中,焊接质量问题主要表现在以下几个方面:(1)焊缝的尺寸不稳定。
- 1、下载文档前请自行甄别文档内容的完整性,平台不提供额外的编辑、内容补充、找答案等附加服务。
- 2、"仅部分预览"的文档,不可在线预览部分如存在完整性等问题,可反馈申请退款(可完整预览的文档不适用该条件!)。
- 3、如文档侵犯您的权益,请联系客服反馈,我们会尽快为您处理(人工客服工作时间:9:00-18:30)。
关于储罐施工现场自动焊焊接纵横缝和罐底的工艺及焊接角变形一.焊接纵环缝角变形说明1.在储罐施工现场引起纵环缝角变形的原因主要有两点。
A .安装组对变形,就是板材安装焊缝组对时,为了试焊前满足焊缝内的间隙,达到工艺要求,强制组对,而产生的角变形。
B .焊接变形,纵环缝焊接时会对焊缝内侧和焊缝两侧进行局部加热,就会因为热涨冷缩的原理,产生应力,而产生角变形。
2.储罐现场罐体环缝焊接所产生的角变形。
由于焊接应力和焊接热收缩影响,在焊接壁板外侧时相反的一侧会出现角变形。
由于焊接焊缝外侧时,壁板已向外倾斜,即焊接焊缝内测时,为了解决角变形和罐体的整体垂直度,达到工艺要求,就要更好的控制焊缝内侧的焊接量。
3.如果焊道向内倾斜的数值小于或大于向外测倾斜的数值,产生的误差值超出允许的数值时,壁板垂直度就达不到标准的工艺要求,影响大型储罐的正常使用,控制角变形的主要措施就是焊接工艺参数和内侧焊道清根量大小的确定和控制二.焊接罐底和罐底三缝角变形说明1.在储罐施工现场引起罐底焊缝角变形的原因主要有叁点。
a.安装组对变形,就是板材安装焊缝组对时,为了试焊前满足焊缝内的间隙,达到工艺要求,强制组对,而产生的角变形。
b.没按施工工艺要求,隔道或者顺序试焊,又没采取有效的措施,产生的角变形。
c.焊接变形,平缝焊接时会对焊缝内侧和焊缝两侧进行局部加热,就会因为热涨冷缩的原理,产生应力,而产生角变形.2.在储罐施工现场引起罐底三缝角变形的原因主要有两点。
A , 焊接变形,角缝焊接时未按工艺要求,分段焊接或者焊接厚度未达到工艺要求。
B , 防焊接变形要提前做支撑,防止角变形过量三.埋弧环缝工艺参数清根控制减少角变形1 ,环焊缝焊接工艺控制角变形以及工艺要求:通过控制焊接工艺参数,在保证焊接质量的前提下,尽量在焊接线能量以内输入,从而减小角变形。
环缝焊接控制前后使用的工艺参数为(以第一圈环焊缝为例:变厚为32mm/25mm):电流电压外侧参数(电流A:350-500电压U:26-30焊接数度40-65),内侧电流电压参数(电流A380-500电压U:26-30焊接数度42-70)。
2 ,环焊缝内部清根量控制角变形焊道内侧清根量大小的确定,和控制通过焊道内侧清根深度和宽度来满足焊接技术要求。
由于自动焊在外侧焊接时,因为焊接工艺参数及装备质量的误差影响,焊接第一圈环焊缝的角变形量也大不相同,所以在内侧清根前,由质检员负责使用1米长的直线样板检查变形量的大小,来确定内侧的清根量的大小,参考值为较薄板厚度60%左右,变形量大的地方清根量要比变形量小的地方深,这样对角变形较为有利。
以第一圈环焊缝为例板厚在32MM-25MM之间环焊缝角变形量大约在10-26mm之间,清根控制在8-15之间。
通过调整清根量,将向外产生的超差变形矫正过来,以确保壁板的垂直度,内侧使用砂轮机清根时把钝边全部清除。
四,纵焊缝焊接角变形说明以及控制壁板纵焊缝焊接变形有;壁板焊接时内倾角变形,壁板向内倾直接影响管壁板的垂直度。
另外,由于每圈壁板的焊接角变形不同,在下圈壁板焊接完成后,进行组对上圈板时,必须要进行强力组对或使用背杠,才能使上下两圈壁板达到设计图纸要求的内表面平齐标准,这样,就对壁板的垂直度产生了很大影响,使壁板垂直度超差,必须采取以下控制措施:1 ,采用壁板安装组对反变形措施由于纵缝下口拘束度大,上口拘束下,,使得上口收缩大而下口收缩小,纵缝焊接后壁板普遍向内倾,向内倾斜程度因板厚度以及板宽度而有所不同,因此在壁板纵缝组对时采用预倾斜法控制其垂直度,以板厚25MM。
板规格为12000×2400壁板材质:SPV490Q的第二圈为例来说明问题,经过对以往储罐焊接数据的分析,纵缝焊接后垂直度偏差14MM左右,而焊接前9MM以内为合格(标准要求每圈的垂直度允许偏差为该圈壁板高度的3%),纵缝焊焊接后垂直度超差为5mm左右。
为解决纵缝焊接后壁板向内倾斜的问题,在壁板纵缝组队时壁板采用比标准值往外倾斜5MM左右来控制其垂直度。
2 ,采用控制焊接工艺参数和工件辅助来控制角变形对于板厚25mm以上采用双面成型的油罐壁板,如果不采用适当措施,非常容易产生棱角变形,因为在焊接纵缝外侧时,内侧用龙门板(用来固定背侧铜背杠,这是立焊机工艺所决定)对向内的角变形产生拘束,,从而阻止了外侧时产生向内侧的角变形,而在焊接内侧时需将龙门板去掉,而又未采取其他有效控制措施时,导致产生的角变形超差,焊接角变形值(以第三圈板为例:板厚20MM、板规格为:12000×2400、壁板材质:spv490q)在12-17mm之间(允许偏差10MM)。
3 ,通过改变焊接破口的尺寸来控制纵缝角变形为控制壁板组装、焊接变形,25mm、32mm后壁板破口采用双Y 型:在厚度反方向上,纵缝破口内外侧比例为4:6图纸要求(5:5)纵缝焊接完成后,内侧用砂轮机进行清根,在保证将钝边,焊接缺陷清理掉后,必须保证请跟后,纵缝内外破口比例为6:4.这样能能保证焊接时产生向内的角变形大一些,来矫正向外产生的角变形。
五,储罐施工现场手用工具及机卡具1.大龙门板2.小龙门板3.铁销子4.圆销子5.撬杠6.手锤7.边缘板蝴蝶卡子8.底圈壁板定位块9.地圈壁板斜支撑10.立缝卡具11.丝杠12.立缝组对加固弧形板13.豆腐块14.吊装吊耳15.7字板16.涨圈固定恰17.液压升降吊耳18.挡板19.轨道20.长槽钢储罐现场施工及焊接一.罐底板的焊接1.焊接前的处理及采用的焊接方法①在施工现场安装有两台小型空气压缩机,当罐底板铺设、组对、定位焊到一定程度后,采用压缩空气对坡口内的杂物进行吹扫,待杂物清理干净后采用电动钢刷对坡口两侧的铁锈和油污进行清理后进行焊接。
②打底焊:罐底板焊接采用CO2气体保护焊进行打底,从中心向外依次进行焊接。
③盖面焊:盖面焊采用自动焊,依次从中间向外焊接长缝。
2.垫板接缝处下面的小垫板处理①小垫板应根据大板排列情况依次进行焊接;为了及时调整收缩量,不宜多焊。
②中幅板的焊接各组块焊缝均采用从中心向两端跳焊法,跳焊长度大约450mm—500mm。
先进行首层打底焊,焊高5mm,其中两端部位,全部手工焊,中间部位自动焊填平。
组块之间的长焊缝焊接,该焊缝焊接必须保证其间隙在范围之内,然后在短缝焊完后,点焊组块之间长缝,打掉连结板进行焊接,焊接时从罐中心向外进行跳焊,施焊时加上实际变形卡具进行手工焊打底,然后进行自动焊。
组对是应考虑到焊接的收缩量。
3. 走廊板的组焊①在中幅板长度方向的焊缝组焊完毕后,再进行走廊板的焊接。
②将走廊板与垫板压缝点焊,先焊短缝后焊长缝,长缝从中心向外部焊接。
③焊缝丁字接头打底焊焊接完毕后,应进行渗透检测,合格后进行盖面焊接。
4. 罐底板异形端部的焊接①底板小板端部应预留500 mm焊道不进行焊接。
②目的:便于组对龟甲缝过程中由于小板端部较长需要切割,不焊部分在组对完龟甲缝、焊接龟甲缝前焊接完毕。
5. 龟甲缝,大角缝组焊1)龟甲缝①龟甲缝垫板应在铺设边缘板前铺设完毕,铺设边缘板时点焊在边缘板上。
②排列罐底板外缘异形板时应预留60--100mm 长的余量,搭在边缘板上,然后用对口工具压紧固定。
2)底板和大角缝焊接结束后,按照图纸设计要求的对口间隙切割掉小板预留量,再使用对口卡具。
3)底圈壁板与边缘板(即大角焊缝)③防止角度变形如。
④大角缝焊接顺序:根据现有焊接经验先焊里面初层,然后焊外侧的初层。
一般规律是内侧焊接四层,外侧焊接三层,要求外侧根部焊接前应进行预热将角缝内的水分烤干,大角缝施工一般在第三圈壁板施工完毕后进行。
(3) 大角焊缝点缝方法:•点焊应与正式焊接工艺一致.•焊前要预热。
•无论手工焊、自动焊,均需对称进行施焊。
•大角缝焊接时应留出排水缝.不进行焊接时用楔子垫起以便壁板和底板间隙6—8mm做排水用,该排水缝在充水前用手工焊焊完。
二.边缘板工卡具安装及组焊1.对口工具种类:A:龙门块,圆锥销;B:补强板(单面焊100mm以上)2. 由于边缘板第一层焊接长度是边缘板端部外侧500mm,所以在打底焊接前,应在边缘板两端安装2个龙门块。
3. 三个垫板相交处的小垫板应点焊在边缘板缝的垫板上,以便进行边缘板焊接时随着边缘板一起收缩。
4.边缘板组对焊接边缘板组对时,垫板要长出边缘板外端40mm;并放上防变形卡具并使反变形量在3—5mm,然后再进行焊接。
三.壁板组装1. 壁板组装前注意事项(1) 应对预制的壁板成型尺寸进行检查,合格后方可组装.需要重新校正时,应防止出现锤痕。
(2) 壁板组装前应安装工卡具,根据壁板宽度为2400mm确定立缝工卡具安装位置,立缝安装3组对称的定位块,定位块之间安装大龙门板来固定壁板。
(3) 由于壁板长度为12600mm,环缝安装12组小龙门板,龙门板距离壁板上侧距离为525mm,之间间距为1050mm,环缝采用10#工字钢作为反变形工具。
(4) 组装前应检查壁板组立位置外的边缘板焊缝是否焊好,砂轮是否修磨平整,而且要求射线探伤无问题2. 第一节壁板组装(1) 在壁板位置线内外交错点焊定位角钢或定位板,其间距为1m,并在立缝位置左右300mm处进行加密定位,距壁板画线距离为20—30mm。
(2) 在壁板上点焊所需安装的工卡具或临时用的各种配件。
(3) 壁板立缝间隙,由立缝卡具控制,且需要在板上边沿横缝点焊12块龙门板,以做横缝对口用(即背杠)。
(4) 第一节壁板组装应严格控制上口水平度,当壁板和边缘间隙过大时,应用契子垫起边缘板,以保证壁板上口水平度。
3.第二节板及以上各节组立(1) 第二节以上各节板组立时其立缝应和一节板立缝错开1/3位置,依次组立。
(2) 环缝临时采用龙门板加背杠方法固定,放置距离1.2m左右,立缝组对和第一节板相同。
4. 壁板组装时应符合相应规定(1) 底圈壁板要求相邻壁板上口水平的允许偏差,不应大于2mm,在整个圆周上任意两点水平的允许偏差,不应大于6mm。
(2) 底圈壁板的垂直度允许偏差不应大于3mm,其他各圈壁板垂直度不应大于该圈壁板高度的0.3%。
(3) 壁板组装时,应保证内表面齐平,错边量应符合下列要求:纵向焊缝错边量:手工焊时,不应大于板厚的0.1倍,且不应大于1.5mm,自动焊时不应大于1mm。
环向焊缝错边量:手工焊时,错边量不应大于板厚的0.2倍,自动焊时不应大于1.5mm。
5. 焊缝焊接(1) 立缝焊接要求焊接采用对称焊接两台立缝焊机焊接完成一道焊缝时延同一方向行走,始终保持对称.对于立缝采用双面焊时,背面采用碳弧气刨清根后,应进行渗透检测,合格后进行焊接,不同厚度的壁板,每焊完一层,需要进行无损检测的部位,检测时间必须在焊接完成36h后方可进行.无损检测合格后方可进行下一步焊接。