超级克劳斯工艺的前景与改进
克劳斯法硫磺回收工艺技术现状及发展趋势
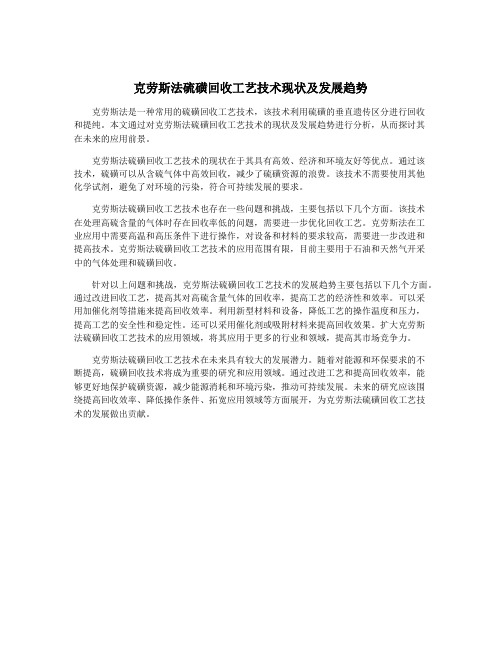
克劳斯法硫磺回收工艺技术现状及发展趋势克劳斯法是一种常用的硫磺回收工艺技术,该技术利用硫磺的垂直遗传区分进行回收和提纯。
本文通过对克劳斯法硫磺回收工艺技术的现状及发展趋势进行分析,从而探讨其在未来的应用前景。
克劳斯法硫磺回收工艺技术的现状在于其具有高效、经济和环境友好等优点。
通过该技术,硫磺可以从含硫气体中高效回收,减少了硫磺资源的浪费。
该技术不需要使用其他化学试剂,避免了对环境的污染,符合可持续发展的要求。
克劳斯法硫磺回收工艺技术也存在一些问题和挑战,主要包括以下几个方面。
该技术在处理高硫含量的气体时存在回收率低的问题,需要进一步优化回收工艺。
克劳斯法在工业应用中需要高温和高压条件下进行操作,对设备和材料的要求较高,需要进一步改进和提高技术。
克劳斯法硫磺回收工艺技术的应用范围有限,目前主要用于石油和天然气开采中的气体处理和硫磺回收。
针对以上问题和挑战,克劳斯法硫磺回收工艺技术的发展趋势主要包括以下几个方面。
通过改进回收工艺,提高其对高硫含量气体的回收率,提高工艺的经济性和效率。
可以采用加催化剂等措施来提高回收效率。
利用新型材料和设备,降低工艺的操作温度和压力,提高工艺的安全性和稳定性。
还可以采用催化剂或吸附材料来提高回收效果。
扩大克劳斯法硫磺回收工艺技术的应用领域,将其应用于更多的行业和领域,提高其市场竞争力。
克劳斯法硫磺回收工艺技术在未来具有较大的发展潜力。
随着对能源和环保要求的不断提高,硫磺回收技术将成为重要的研究和应用领域。
通过改进工艺和提高回收效率,能够更好地保护硫磺资源,减少能源消耗和环境污染,推动可持续发展。
未来的研究应该围绕提高回收效率、降低操作条件、拓宽应用领域等方面展开,为克劳斯法硫磺回收工艺技术的发展做出贡献。
克劳斯法硫磺回收工艺技术现状及发展趋势
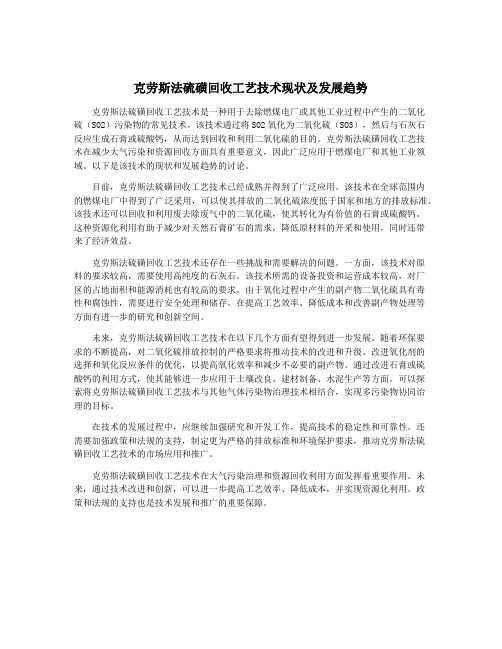
克劳斯法硫磺回收工艺技术现状及发展趋势克劳斯法硫磺回收工艺技术是一种用于去除燃煤电厂或其他工业过程中产生的二氧化硫(SO2)污染物的常见技术。
该技术通过将SO2氧化为二氧化硫(SO3),然后与石灰石反应生成石膏或硫酸钙,从而达到回收和利用二氧化硫的目的。
克劳斯法硫磺回收工艺技术在减少大气污染和资源回收方面具有重要意义,因此广泛应用于燃煤电厂和其他工业领域。
以下是该技术的现状和发展趋势的讨论。
目前,克劳斯法硫磺回收工艺技术已经成熟并得到了广泛应用。
该技术在全球范围内的燃煤电厂中得到了广泛采用,可以使其排放的二氧化硫浓度低于国家和地方的排放标准。
该技术还可以回收和利用废去除废气中的二氧化硫,使其转化为有价值的石膏或硫酸钙。
这种资源化利用有助于减少对天然石膏矿石的需求,降低原材料的开采和使用,同时还带来了经济效益。
克劳斯法硫磺回收工艺技术还存在一些挑战和需要解决的问题。
一方面,该技术对原料的要求较高,需要使用高纯度的石灰石。
该技术所需的设备投资和运营成本较高,对厂区的占地面积和能源消耗也有较高的要求。
由于氧化过程中产生的副产物二氧化硫具有毒性和腐蚀性,需要进行安全处理和储存。
在提高工艺效率、降低成本和改善副产物处理等方面有进一步的研究和创新空间。
未来,克劳斯法硫磺回收工艺技术在以下几个方面有望得到进一步发展。
随着环保要求的不断提高,对二氧化硫排放控制的严格要求将推动技术的改进和升级。
改进氧化剂的选择和氧化反应条件的优化,以提高氧化效率和减少不必要的副产物。
通过改进石膏或硫酸钙的利用方式,使其能够进一步应用于土壤改良、建材制备、水泥生产等方面。
可以探索将克劳斯法硫磺回收工艺技术与其他气体污染物治理技术相结合,实现多污染物协同治理的目标。
在技术的发展过程中,应继续加强研究和开发工作,提高技术的稳定性和可靠性。
还需要加强政策和法规的支持,制定更为严格的排放标准和环境保护要求,推动克劳斯法硫磺回收工艺技术的市场应用和推广。
克劳斯工艺的进展(DOC)

克劳斯工艺技术进展及应用化工09-6苏美慧09031618摘要:现如今,各国对控制工业尾气技术可开发和改进日益注重。
硫磺回收的克劳斯工艺发展前景尤其广阔。
本文将着力介绍克劳斯工艺的基本流程、制约因素、改进技术及其在我国国内的应用。
关键词:克劳斯工艺;局限性;改进;国内应用。
前言:克劳斯工艺发明伊始就成为硫磺回收工业的标准工艺流程。
但是,由于酸性气的组成变化比较复杂,限制了克劳斯工艺的效能,因此有必要根据酸性气组成的不同开发不同的处理工艺,并针对某些特定的工艺条件来开发最优化的系统。
目前已有不少先进的改进技术,而且在我国国内也存在着一定的应用前景。
正文:近年来,随着各国对环境污染的控制日益严格。
世界上许多大公司和科研机构加强了对硫回收技术的开发,出现了许多新工艺、新技术。
超级克劳斯工艺就是一项先进、成熟的硫磺回收技术,具有流程简单、操作灵活、安全可靠、运行费用低、应用规模不限、使用范围广、硫回收率高等优点,成为近20年来发展最快的硫磺回收工艺技术之一。
在新建硫磺回收装置建设及原有老装置改造方面,超级克劳斯硫磺回收工艺都有广阔的应用前景。
现如今,国内外各大企业都在对传统克劳斯工艺进行不断改造,这些技术改造均以提高硫磺回收率为基本目的,在传统工艺的基础上予以创新,目前已取得了较大的技术突破。
下面对克劳斯工艺流程进行简述:(以上内容引用见参考文献[4],流程为自我提炼组织而成)长期以来,为提高克劳斯反应的硫回收率,研究者进行了大量研究工作,但并未取得重大突破,常规克劳斯装置的硫回收率通常只能达到94%~97%,影响硫磺回收率的原因如下:(1)由于克劳斯反应受到热力学的限制,硫的转化反应不可能完全,过程气中仍存有少量的H2S,SO2,限制了硫的转化率。
(2)克劳斯反应要产生一定量的水气,随着水气含量的增加,相应降低H20,S02的浓度,影响了克劳斯反应的平衡,阻碍了硫的生成,限制了硫的转化率。
(3)由于酸气中CO2和烃类的存在,则过程气中会形成COS和CS2,必须使之发生水解反应,为此,第一反应器的温度必须控制在300~340℃,高温虽然有利于水解反应,但是不利于克劳斯反应的进行,则限制了硫的转化率。
超级克劳斯硫璜回收装置在设计、运行中存在的问题及优化方案

超级克劳斯硫璜回收装置在设计、运行中存在的问题及优化方案超级克劳斯硫璜回收装置在设计、运行中存在的问题及优化方案摘要:超优克劳斯工艺基础是富氧燃烧,通过控制富氧空气与酸性气的比例来控制进入超级克劳斯反应器中硫化氢的浓度。
过量的氧进入下游反应器,也会造成反应器床层温度剧烈波动,严重时会发生燃烧反应,损坏设备。
关键词:废锅液流捕集器过程气工艺管线催化剂床层化学当量燃烧过氧国电赤峰化工有限公司硫回收装置采用的是荷兰荷丰超优/超级克劳斯专利技术,由赛鼎工程有限公司详细设计,日产硫磺25.4吨。
2012年12月17日开车投产,2013年3月20日-3月27日超级克劳斯硫酸盐化结束,超级克斯反应器投用,并成功引入氧气,采用富氧操作模式,至今运行比较稳定,排放达标。
针对超优克劳斯反应特点,就开车中存在的重大安全隐患问题做简单介绍并给出解决方案,以供同行借鉴和参考。
一、硫回收装置在设计中存在的问题我公司硫磺回收装置采用的超优/超级克劳斯工艺,其基础是以比值控制富氧空气流量实现硫化氢部分燃烧。
紧急停车后再开车的燃烧过程中,会造成废锅出口过程气过氧,引起克劳斯反应器催化剂床层温度剧烈波动,从而使催化剂活性降低、烧结、粉碎,减少催化剂使用寿命。
另外过程气工艺管线管道壁会残存硫化亚铁,当过程气中氧含量高时,会引发硫化亚铁与氧气燃烧反应,从而损坏管道、设备。
基于上述安全隐患,必须对原有工艺管线进行改造。
原工艺流程简图如下:改造后的工艺简图:燃料气二、改造方案综合考虑,本着投资少、见效快、大大降低安全隐患的原则,在主体设备不动的情况下,对设备管线进行了如下改造。
1.从废锅出口过程气工艺管线PG61501-400上引一条副线PG61519-300到液流捕集器出口阀后与尾气管线相连接;2.废锅出口过程气工艺管线PG61501-400上增加总阀DN400,并且为夹套蝶阀,使用0.5MPa低压蒸汽伴热;3.废锅出口过程气副线PG61519上两端各增加DN300夹套蝶阀做为隔离使用,并使用使用0.5MPa低压蒸汽伴热;4.废锅出口过程气副线PG61519一定要有倾斜度,保证液体自流;管线使用三根0.5MPa低压蒸汽伴热,防止由于阀门内漏造成硫磺堵塞。
克劳斯法硫磺回收工艺技术现状及发展趋势

克劳斯法硫磺回收工艺技术现状及发展趋势随着工业化进程的不断深入,硫磺资源的开发和利用已经成为全球性的热点话题。
硫磺是一种非常重要的化工原料,在化肥、农药、橡胶、化工等多个领域都有着广泛的应用。
大量的工业生产过程中会产生硫磺废气,如果不进行合理的处理和回收,不仅会对环境造成严重的污染,还会浪费大量的资源。
硫磺的回收和再利用技术的研究和开发成为了当今工业界的重要课题之一。
在硫磺回收技术中,克劳斯法硫磺回收工艺技术是一种非常有效的方法。
克劳斯法是一种使用空气中氧气将二氧化硫氧化为三氧化硫,再进一步还原为硫磺的工艺方法。
这种方法在硫磺的回收过程中具有诸多优势,如能够高效回收硫磺、减少排放污染物等。
克劳斯法硫磺回收工艺技术已经在工业生产中得到了广泛的应用。
目前,克劳斯法硫磺回收工艺技术在全球范围内得到了越来越多的关注和应用,其技术现状和发展趋势备受瞩目。
现在,本文将从技术现状和未来发展趋势两个方面入手,对克劳斯法硫磺回收工艺技术进行深入的分析和探讨。
1. 技术原理及流程克劳斯法硫磺回收工艺技术的原理是利用雷电产生的电场和静电作用来促进空气中的氧气与二氧化硫发生氧化反应,生成三氧化硫。
然后,利用氢气将三氧化硫还原为硫磺。
具体的流程包括以下几个步骤:(1)将二氧化硫气体通入反应器中,利用雷电产生的静电场促进二氧化硫与空气中的氧气发生反应生成三氧化硫。
(2)将生成的三氧化硫与氢气在高温条件下发生还原反应,生成硫磺和水蒸气。
(3)通过冷却和凝结,将硫磺和水蒸气分离成为液态硫磺和液态水。
2. 技术优势克劳斯法硫磺回收工艺技术具有以下几个方面的优势:(1)高效回收:该工艺技术能够高效、快速地将二氧化硫转化为硫磺,回收率较高。
(2)减少污染:该工艺技术的产物中不含有硫化物和氮氧化物等污染物,对环境污染小。
(3)资源综合利用:回收的硫磺可以再次应用于化肥、农药等领域,实现资源的综合利用。
3. 应用现状克劳斯法硫磺回收工艺技术已经在一些工业生产中得到了广泛的应用。
克劳斯法硫磺回收工艺技术现状及发展趋势
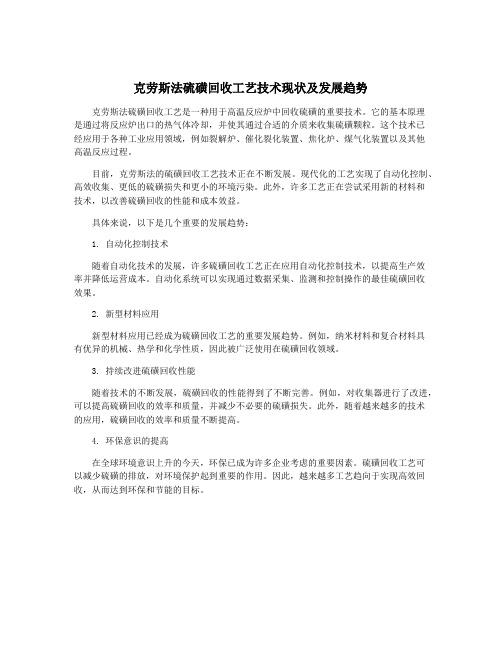
克劳斯法硫磺回收工艺技术现状及发展趋势
克劳斯法硫磺回收工艺是一种用于高温反应炉中回收硫磺的重要技术。
它的基本原理
是通过将反应炉出口的热气体冷却,并使其通过合适的介质来收集硫磺颗粒。
这个技术已
经应用于各种工业应用领域,例如裂解炉、催化裂化装置、焦化炉、煤气化装置以及其他
高温反应过程。
目前,克劳斯法的硫磺回收工艺技术正在不断发展。
现代化的工艺实现了自动化控制、高效收集、更低的硫磺损失和更小的环境污染。
此外,许多工艺正在尝试采用新的材料和
技术,以改善硫磺回收的性能和成本效益。
具体来说,以下是几个重要的发展趋势:
1. 自动化控制技术
随着自动化技术的发展,许多硫磺回收工艺正在应用自动化控制技术,以提高生产效
率并降低运营成本。
自动化系统可以实现通过数据采集、监测和控制操作的最佳硫磺回收
效果。
2. 新型材料应用
新型材料应用已经成为硫磺回收工艺的重要发展趋势。
例如,纳米材料和复合材料具
有优异的机械、热学和化学性质,因此被广泛使用在硫磺回收领域。
3. 持续改进硫磺回收性能
随着技术的不断发展,硫磺回收的性能得到了不断完善。
例如,对收集器进行了改进,可以提高硫磺回收的效率和质量,并减少不必要的硫磺损失。
此外,随着越来越多的技术
的应用,硫磺回收的效率和质量不断提高。
4. 环保意识的提高
在全球环境意识上升的今天,环保已成为许多企业考虑的重要因素。
硫磺回收工艺可
以减少硫磺的排放,对环境保护起到重要的作用。
因此,越来越多工艺趋向于实现高效回收,从而达到环保和节能的目标。
超级克劳斯硫磺工艺发展研究
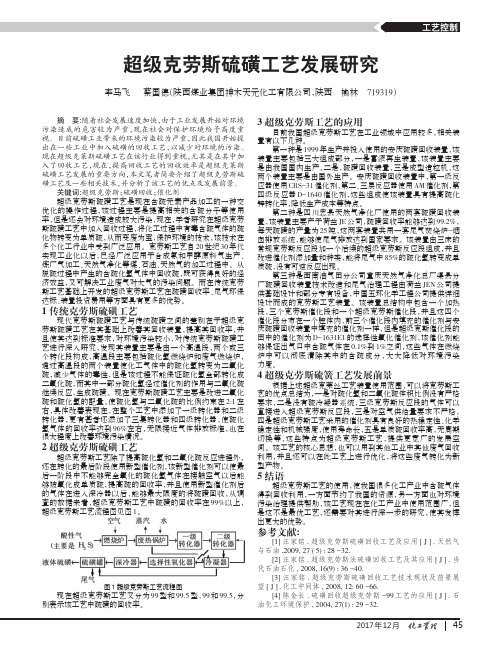
2017年12月超级克劳斯硫磺工艺发展研究李马飞蔡国德(陕西煤业集团神木天元化工有限公司,陕西榆林719319)摘要:随着社会发展速度加快,由于工业发展开始对环境污染造成的危害较为严重,现在社会对保护环境给予高度重视。
目前硫磺工业带来的环境污染较为严重,因此我国开始提出在一些工业中加入硫磺的回收工艺,以减少对环境的污染。
现在超级克莱斯硫磺工艺在该行业得到重视,尤其是在其中加入了回收工艺,现在,提高回收工艺的回收效率是超级克莱斯硫磺工艺发展的重要方向,本文笔者简要介绍了超级克劳斯硫磺工艺及一些相关技术,并分析了该工艺的优点及发展前景。
关键词:超级克劳斯;硫磺回收;催化剂超级克劳斯硫磺工艺是现在含硫元素产品加工的一种交优化的操作过程,该过程主要是提高相关的含硫分子等使用率,但是还会对环境造成较大污染,现在,学者研究在超级克劳斯硫磺工艺中加入回收过程,将化工过程中有毒含硫气体的硫化物转变为单质硫,从而变废为宝,保护环境的技术,该技术在多个化工行业中受到广泛应用。
克劳斯工艺自20世纪30年代实现工业化以后,已经广泛应用于合成氨和甲醇原料气生产、炼厂气加工、天然气净化等煤、石油、天然气的加工过程中。
从脱硫过程中产生的含硫化氢气体中回收硫,既可获得良好的经济效益,又可解决工业废气对大气的污染问题。
而在传统克劳斯工艺基础上开发的超级克劳斯工艺在硫磺回收率、尾气环保达标、装置投资费用等方面具有更多的优势。
1传统克劳斯硫磺工艺现代克劳斯硫磺工艺与传统硫磺之间的差别在于超级克劳斯硫磺工艺在其基础上改善其回收装置,提高其回收率,并且使其达到标准要求,对环境污染较小,对传统克劳斯硫磺工艺进行深入研究,发现其装置主要是由一个高温段,两个或三个转化段构成,高温段主要包括硫化氢燃烧炉和废气燃烧炉,通过高温段的两个装置使化工气体中的硫化氢转变为二氧化硫,减少气体的毒性,但是该过程不能保证硫化氢全部转化成二氧化硫,而其中一部分硫化氢经过催化剂的作用与二氧化硫继续反应,生成硫磺。
超级克劳斯硫回收工艺优化运行及改造分析

超级克劳斯硫回收工艺优化运行及改造分析摘要:在合成氨工艺中,硫回收是该工艺的重要环节,这是因为硫回收关系到水煤气的净化能否维持正常运转,基于此,贵州开阳化工有限公司在合成氨硫回收工艺中,采取采用荷兰荷丰超级克劳斯硫回收技术,年副产硫磺2.1万吨,有效保障环保指标达标排放。
随着公司在提高产能,节能降耗方面的需求,优化改造硫回收工艺势在必行。
关键词:合成氨;硫回收;工艺运行;改造引言:将变换来含氨汽提气和甲醇洗来的H2S体积不大于40%酸性气经过焚烧、催化反应,转化为纯度为99.9%的硫磺,经造粒、包装后外销,尾气达标后(SO2≤960mg/Nm3)通过烟囱排放。
1.超级克劳斯硫回收工艺流程在来自低温甲醇洗工序酸性气经过水洗,脱除大部分甲醇,经过分离器脱除水分,经预热器加热后进入主烧嘴(M6003)内与空分来的氧气按一定比例混合燃烧,大部分酸性气体燃烧后进入酸性气废锅(E6001)与脱盐水换热,同时副产253℃、4.1MPa饱和蒸汽。
酸性气进入第一冷凝器(E6002)冷凝到195℃,出第一冷凝器的液硫经A#液硫封(X6001A)直接流入液硫槽。
未反应完的酸性气再进入第一再热器(E6009)加热到240℃,进入一级克劳斯反应器(R6001),在催化剂作用下进行反应后进入第二冷凝器(E6003),出第二冷凝器的液硫经B#液硫封(X6001B)直接流入液硫槽,出第二冷凝器的克劳斯气体温度约为195℃,在第二再热器(E6010)中再次加热到215 ℃,进入二级克劳斯反应器(R6002),同样在催化剂作用下进行反应后,进入第三冷凝器(E6004),产生液态硫经C#液硫封(X6001C)流入液硫槽。
克劳斯气体进入第三再热器(E6011)再次加热到200 ℃,进入三级克劳斯反应器(R6003)进行反应,出来的克劳斯气体进入第四冷凝器(E6005)被冷却,硫被分离出去,产生液态硫经D#液硫封(X6001D)流入液硫槽。
克劳斯法硫磺回收工艺技术发展与应用

克劳斯法硫磺回收工艺技术发展与应用摘要:我国于1996年4月颁布了GB16297-1996《大气污染物综合排放标准》,对于尾气处理的要求进一步提高。
克劳斯(Claus)法是一种较为成熟的酸性气体硫回收工艺,在石油、化工企业得到了非常广泛的应用。
本文对克劳斯法硫磺回收工艺的技术发展与生产应用进行了介绍。
关键词:克劳斯法硫磺回收工艺发展与应用近年来,随着工业的快速发展,环境污染也成为了一个不容人们忽视的重要问题。
近年来,我国于1996年4月颁布了GB16297-1996《大气污染物综合排放标准》,对于尾气处理的要求进一步提高。
克劳斯(Claus)法是一种较为成熟的酸性气体硫回收工艺,具有流程简单、操作灵活、硫的回收率高、投资较低、环保效益好等优点,自上世纪30年代工业化以来,经过近80年的发展,在化肥厂、炼油厂、天然气净化厂、发电厂等得到了非常广泛的应用。
我国的克劳斯法硫磺回收技术的起步较晚,基础也很差,装置的操作水平比较低,这就导致硫元素的回收效果不太好,通过引入先进技术,提高硫回收率,对于环境保护具有非常重大的意义。
本文介绍了近年来克劳斯法硫磺回收工艺的发展与实际情况,对于企业的生产与技术改进具有一定的指导意义。
1.传统的克劳斯法工艺传统克劳斯法是硫磺回收中最基本的方法之一,其装置由一个高温段和两个或三个转化段构成。
其工艺原理为含H2S的酸性气体发生燃烧反应,约1/3体积的H2S在1200℃左右转化成SO2,放出大量热,此阶段称为热反应阶段;生成的SO2再与剩余2/3体积的H2S在催化剂的作用下反应生成硫单质,此阶段称为催化反应阶段。
这两个阶段的反应方程式如下:3H2S+3/2O2 SO2+2H2S+H2O+518.9KJ/mol3H2S+3/2O2 2H2O+3/xSx+96.1KJ/mol其中,回收的硫还可以用作生产硫酸的的原料。
克劳斯反应是一个可逆反应,存在化学平衡,受温度、压强等反应条件的影响,而且硫的转化率主要取决于n(H2S):n(SO2)(即两者物质的量的比),因此为使装置能达到硫回收的最佳效果,必须保证n(H2S):n(SO2)接近2:1。
克劳斯法硫磺回收工艺技术现状及发展趋势
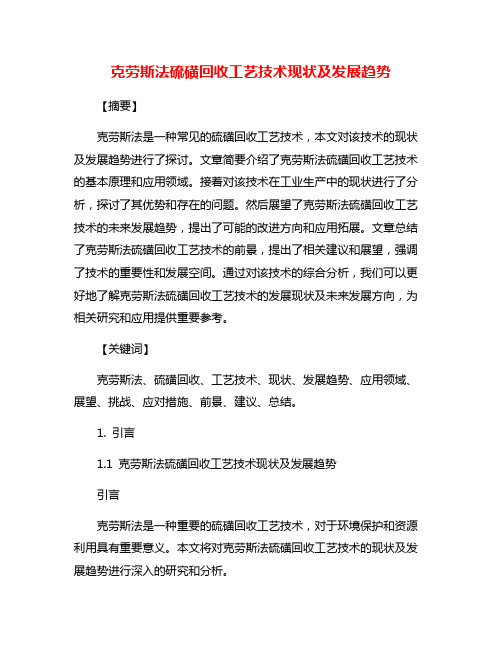
克劳斯法硫磺回收工艺技术现状及发展趋势【摘要】克劳斯法是一种常见的硫磺回收工艺技术,本文对该技术的现状及发展趋势进行了探讨。
文章简要介绍了克劳斯法硫磺回收工艺技术的基本原理和应用领域。
接着对该技术在工业生产中的现状进行了分析,探讨了其优势和存在的问题。
然后展望了克劳斯法硫磺回收工艺技术的未来发展趋势,提出了可能的改进方向和应用拓展。
文章总结了克劳斯法硫磺回收工艺技术的前景,提出了相关建议和展望,强调了技术的重要性和发展空间。
通过对该技术的综合分析,我们可以更好地了解克劳斯法硫磺回收工艺技术的发展现状及未来发展方向,为相关研究和应用提供重要参考。
【关键词】克劳斯法、硫磺回收、工艺技术、现状、发展趋势、应用领域、展望、挑战、应对措施、前景、建议、总结。
1. 引言1.1 克劳斯法硫磺回收工艺技术现状及发展趋势引言克劳斯法是一种重要的硫磺回收工艺技术,对于环境保护和资源利用具有重要意义。
本文将对克劳斯法硫磺回收工艺技术的现状及发展趋势进行深入的研究和分析。
在当前全球环境问题日益严重的背景下,克劳斯法硫磺回收工艺技术逐渐受到人们的关注和重视。
通过将硫磺氧化反应与铜的还原反应结合起来,可以实现硫磺的高效回收,降低污染物排放,减少资源浪费。
克劳斯法硫磺回收工艺技术的研究具有重要的理论和实际意义。
在本文中,将首先对克劳斯法硫磺回收工艺技术进行概述,介绍其基本原理和工作流程。
接着,将分析克劳斯法硫磺回收工艺技术在不同应用领域的情况,探讨其在工业生产中的重要作用。
然后,将对克劳斯法硫磺回收工艺技术的现状进行深入剖析,总结其存在的问题和挑战。
接下来,将展望克劳斯法硫磺回收工艺技术的发展趋势,指出未来的研究方向和发展重点。
将探讨克劳斯法硫磺回收工艺技术面临的挑战,并提出相应的应对措施。
通过这些探讨与分析,我们可以更好地认识和了解克劳斯法硫磺回收工艺技术,并为其未来的发展提供参考和指导。
2. 正文2.1 克劳斯法硫磺回收工艺技术概述克劳斯法硫磺回收工艺技术是一种用于回收硫磺的高效工艺技术,通常应用于化工厂、炼油厂和其他工业生产中。
克劳斯工艺的进展
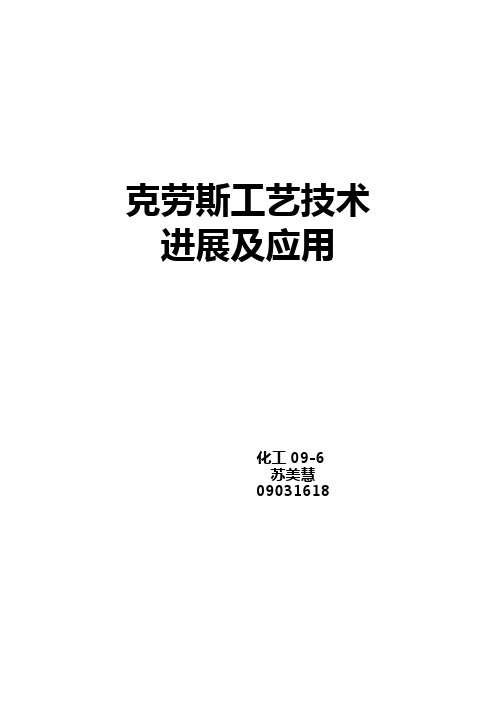
克劳斯工艺技术进展及应用化工09-6苏美慧09031618摘要:现如今,各国对控制工业尾气技术可开发和改进日益注重。
硫磺回收的克劳斯工艺发展前景尤其广阔。
本文将着力介绍克劳斯工艺的基本流程、制约因素、改进技术及其在我国国内的应用。
关键词:克劳斯工艺;局限性;改进;国内应用。
前言:克劳斯工艺发明伊始就成为硫磺回收工业的标准工艺流程。
但是,由于酸性气的组成变化比较复杂,限制了克劳斯工艺的效能,因此有必要根据酸性气组成的不同开发不同的处理工艺,并针对某些特定的工艺条件来开发最优化的系统。
目前已有不少先进的改进技术,而且在我国国内也存在着一定的应用前景。
正文:近年来,随着各国对环境污染的控制日益严格。
世界上许多大公司和科研机构加强了对硫回收技术的开发,出现了许多新工艺、新技术。
超级克劳斯工艺就是一项先进、成熟的硫磺回收技术,具有流程简单、操作灵活、安全可靠、运行费用低、应用规模不限、使用范围广、硫回收率高等优点,成为近20年来发展最快的硫磺回收工艺技术之一。
在新建硫磺回收装臵建设及原有老装臵改造方面,超级克劳斯硫磺回收工艺都有广阔的应用前景。
现如今,国内外各大企业都在对传统克劳斯工艺进行不断改造,这些技术改造均以提高硫磺回收率为基本目的,在传统工艺的基础上予以创新,目前已取得了较大的技术突破。
下面对克劳斯工艺流程进行简述:(以上内容引用见参考文献[4],流程为自我提炼组织而成)长期以来,为提高克劳斯反应的硫回收率,研究者进行了大量研究工作,但并未取得重大突破,常规克劳斯装臵的硫回收率通常只能达到94%~97%,影响硫磺回收率的原因如下:(1)由于克劳斯反应受到热力学的限制,硫的转化反应不可能完全,过程气中仍存有少量的H2S,SO2,限制了硫的转化率。
(2)克劳斯反应要产生一定量的水气,随着水气含量的增加,相应降低H20,S02的浓度,影响了克劳斯反应的平衡,阻碍了硫的生成,限制了硫的转化率。
(3)由于酸气中CO2和烃类的存在,则过程气中会形成COS和CS2,必须使之发生水解反应,为此,第一反应器的温度必须控制在300~340℃,高温虽然有利于水解反应,但是不利于克劳斯反应的进行,则限制了硫的转化率。
对克劳斯法生产硫磺工艺现状分析及对应措施

对克劳斯法生产硫磺工艺现状分析及对应措施化工09—卓2 汪槐斌09031919摘要:随着各国对环境污染的控制日益严格,世界上许多大公司和科研机构加强了对硫回收技术的开发,出现了许多新工艺、新技术。
超级克劳斯工艺就是一项先进、成熟的硫磺回收技术,具有流程简单、操作灵活、安全可靠、运行费用低、应用规模不限、使用范围广、硫回收率高等优点,成为近20年来发展最快的硫磺回收工艺技术之一。
在新建硫磺回收装置建设及原有老装置改造方面,超级克劳斯硫磺回收工艺都有广阔的应用前景。
本文介绍了超级克劳斯及相关的传统克劳斯、超优克劳斯硫磺回收工艺原理,叙述了超级克劳斯工艺的发展及应用概况和技术特点,并对该工艺在国内相关领域的应用前景作出了展望。
关键词:硫磺回收;克劳斯;技术特点;前景展望克劳斯(C1aus)法是一种比较成熟的多单元处理技术,是目前应用最为广泛的硫回收工艺。
自从20世纪30年代实现工业化以后,已经广泛用于合成氨和甲醇原料气生产、炼厂气加T 、天然气净化等煤、石油、天然气的加T过程中在脱硫过程中产生的含H2S气体中回收硫。
克劳斯工艺特点是流程简单、操作灵活、回收硫磺纯度高、投资费用低、环境及规模效益显著。
克劳斯工艺回收硫磺的纯度可达到99.8%,可作为生产硫酸的一种硫资源,也可作其他部门的化工原料,在炼油厂、天然气净化厂、焦化厂、化肥厂、发电厂、煤气化厂得到了广泛的应用而在传统克劳斯工艺基础上开发的新型克劳斯工艺在硫磺回收率、尾气环保达标、装置投资费用等方面具有更多的优势。
一、发展概况利用克劳斯装置净化尾气中的硫化物回收硫磺工艺现已得到了迅速发展,其具体工艺流程有20多种,主要有传统克劳斯工艺,低温克劳斯工艺、超级克劳斯(SuperClaus)工艺,带有SCOT 尾气处理的克劳斯工艺等。
其中超级克劳斯工艺是在两级普通克劳斯转化之后,第三级改用选择性氧化催化剂,将H2S直接氧化成元素硫,传统克劳斯工艺要求H2S/SO2 摩尔比值为2的条件下进行,而此种工艺却维持选择性氧化催化段在富H2S条件下举行,一改以往单纯增加级数来提高H2S的回收率的方法。
克劳斯法硫磺回收工艺技术现状及发展趋势

克劳斯法硫磺回收工艺技术现状及发展趋势1. 引言1.1 背景介绍随着全球经济的快速发展,工业生产的规模和数量不断增加,硫磺作为重要的化工原料在很多领域都有着广泛的应用。
硫磺的生产过程中会产生大量的副产物硫化氢,这不仅对环境造成污染,还会浪费资源。
实现硫磺的有效回收变得尤为重要。
克劳斯法硫磺回收工艺技术作为目前比较成熟的硫磺回收技术之一,已经在工业生产中得到广泛应用。
该技术能够将含硫废气中的硫磺氧化为二氧化硫,再进行吸收和氧化反应,最终得到高纯度的硫磺产品。
克劳斯法技术不仅可以有效减少硫磺的浪费,同时还可以减少对环境的污染,具有较高的经济效益和社会效益。
为了全面了解克劳斯法硫磺回收工艺技术的现状和发展趋势,本文将对该技术进行详细分析,并展望未来的发展方向,以期为相关研究和实践提供参考和指导。
1.2 研究目的研究目的主要是探讨克劳斯法硫磺回收工艺技术的现状及发展趋势,分析其在环保领域中的重要意义和应用前景。
通过深入研究相关技术及行业现状,可以为进一步优化硫磺回收工艺提供参考和指导。
可以针对目前存在的问题和挑战,提出可行的解决方案和发展路径,以推动克劳斯法硫磺回收技术的不断创新和提升。
通过对未来发展趋势进行预测和分析,可以为企业和决策者提供科学的依据和决策支持,促进我国克劳斯法硫磺回收工艺技术的快速发展,实现资源的高效利用和环境的可持续发展。
2. 正文2.1 克劳斯法硫磺回收工艺技术简介克劳斯法硫磺回收工艺技术是一种通过燃烧硫化氢气体来生成二氧化硫的工艺。
这一技术主要应用于炼油、化工、冶金等行业,在生产过程中产生的硫化氢废气可以通过克劳斯法硫磺回收工艺进行处理,将废气中的硫化氢转化为二氧化硫,再进一步转化为硫磺。
克劳斯法硫磺回收工艺主要包括硫化氢气体的燃烧和催化氧化两个步骤。
首先硫化氢气体被燃烧生成二氧化硫,然后通过催化剂的作用,二氧化硫进一步转化为硫磺。
整个工艺具有高效、环保的特点,可以有效减少二氧化硫和硫磺的排放,提高资源利用率。
超级克劳斯SuperClaus工艺的工程实践及初步剖析

第23卷第3期2005年8月天 然 气 与 石 油Natural Gas And OilVol.23,No.3Aug.2005收稿日期:2004 11 09;修回日期:2005 02 16作者简介:肖秋涛(1972 ),女,四川成都人,工程师,学士,主要从事天然气净化及硫磺回收的研究与设计工作。
电话:(028)86014538。
超级克劳斯(SuperClaus)工艺的工程实践及初步剖析肖秋涛1,陈 明2,刘家洪2(1.中国石油工程设计有限公司西南分公司,四川成都610017;2.中国石油西南油气田公司重庆天然气净化总厂,重庆401259)摘 要:四川忠县天然气净化厂硫磺回收装置设计采用荷兰JE 公司许可的四级转化超级克劳斯(SuperClaus)工艺。
通过对引进技术的整理,经过充分消化吸收引进装置的通用先进技术及重点专利技术,结合国内硫磺回收装置的设计经验,对引进工艺的技术进行初步剖析,揭示常规克劳斯工艺的局限性和超级克劳斯工艺的改良性以及超级克劳斯工艺在工业实践中突显的优点。
说明实现超级克劳斯工艺国产化的可能性。
关键词:常规克劳斯工艺;局限性;超级克劳斯工艺;改良性;工业实践优点;国产化文章编号:1006 5539(2005)03 0055 04文献标识码:C0 前言四川忠县天然气净化厂设有2套规模相同的硫磺回收装置,分别与2套规模为300 104m 3/d 的脱硫装置匹配。
装置设计采用荷兰JE 公司许可的四级转化超级克劳斯(SuperClaus)工艺,设计硫回收率为99 2%,单套装置硫磺产量约25t/d 。
2套装置共用1套尾气焚烧炉-烟囱排放系统,SO 2总排放量在35kg/h 以下,符合国家对环保的要求。
该厂采用的超级克劳斯工艺是过去50年中对常规克劳斯技术重大突破的工艺之一,它由三床的常规克劳斯反应段加一个后续的超级克劳斯反应段组成,其关键在于通过改进传统的克劳斯控制系统和采用新开发的超级克劳斯选择性氧化催化剂,显示出增进总硫收率的强大潜在能力。
超级克劳斯硫回收工艺简介
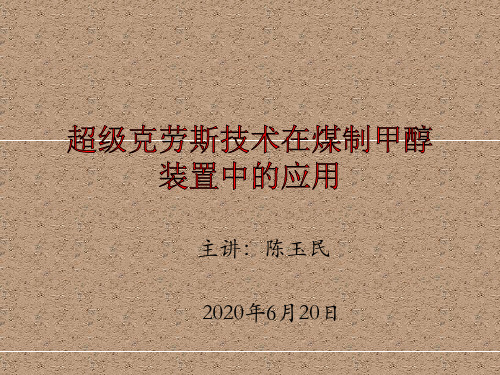
2H2S+SO2 = 2H2O+3S+Q
2.2克劳斯反应器中反应原理 COS+H2O = H2S+CO2+Q
CS2+2H2O = 2H2S+CO2+Q 2H2S+SO2 = 2H2O+3S+Q
2.3超级克劳斯反应器中反应原理 2H2S+O2 = 2H2O+2S+Q 2.4尾气焚烧炉中反应
来自低温甲醇洗工序的酸性气先进入甲醇洗
涤塔利用来自管网的脱盐水进行洗涤,除 去酸性气中夹带的甲醇,产生的酸水由酸 性水泵送往污水处理;塔顶酸性气去酸性 气缓冲罐进行气液分离,分离下来的酸水 回到甲醇洗涤塔底部,酸性气去酸性气预 热器用4.0MPa的中压蒸汽进行预热。
来自变换工序的汽提气进入汽提气缓冲罐 进行气液分离,酸性水回到甲醇洗涤塔底 部,汽提气与预热后一部分酸性气混合进 入主烧嘴,另一部分酸性气绕过烧嘴直接备甲醇装置的气体净 化过程大多采用低温甲醇洗或NHD技术。 其溶剂再生后的酸性气具有H2S 浓度低 (通 常在25-30%),气量不大的特点。而我国原 有或某些新建的甲醇厂通常采用单一的常规 克劳斯工艺,即在克劳斯装置的上游没有气 体吸收段,这就是说酸性气无法提浓;同样, 在克劳斯装置下游也没有尾气处理装置 (SCOT),这样不可能满足国家现有的气体排 放指标。其主要原因是:酸性气浓度低使得
情况下,总硫转化率即可达到99% 或99.5% 以上水平,并达到环保排放要求,具有硫磺 回收和尾气处理的双重作用。
3.3 装置适应性强
超级克劳斯工艺适用的酸性气体浓度范围广, H2S浓度在23% ~93%之间,既可用于新建 装置,也适用于现有的克劳斯装置技术改造, 还能和富氧氧化硫回收工艺结合使用。装置 运行中过程气连续气相催化, 中间不需要进 行冷凝脱水,无“三废” 处理问题。
克劳斯硫回收系统常见问题及优化改进措施

克劳斯硫回收系统常见问题及优化改进措施摘要:近年来,随着环保形势日益严峻,煤化工与石油化工企业多采用克劳斯工艺进行对硫化氢酸性气进行处理。
克劳斯硫回收不仅回收了硫单质,创造了经济效益,而且降低了烟气脱硫成本。
但在其运行过程中存在不稳定因素,影响到生产效率的提高,现就常见问题进行原因分析,并提出了优化改进措施。
关键词:克劳斯硫回收;环保设施;经济效益晋煤集团天溪煤制油分公司年产30万t甲醇装置,变换气经低温甲醇洗脱除H2S后,经过再生浓缩生成25%~35%的H2S高浓度酸性气,送往年产0。
8万t克劳斯硫回收装置。
本装置采用分流法三级克劳斯工艺,硫回收率达到98%左右,运行相对稳定。
1克劳斯硫回收工艺介绍按照酸性气中H2S含量的区别,克劳斯法硫回收工艺分三种:直接氧化法、部分燃烧法以及分流法。
通常酸性气里面的H2S体积浓度小于15%时采取直接氧化法;H2S体积浓度超过50%时采取部分燃烧法;H2S浓度位于两者之间采取分流法。
我公司采用分流法:将三分之一的酸性气体通入燃烧炉,加入空气使其燃烧生成SO2,而其余三分之二酸性气走旁路,绕过燃烧室,与燃烧后的气体汇合进入催化剂床层进行反应。
克劳斯硫回收装置工艺流程主要有传统克劳斯工艺、超级克劳斯工艺和带有SCOT尾气处理的克劳斯工艺等。
其中传统克劳斯工艺三级转换,要求H2S、SO2摩尔比值为2的条件下进行;超级克劳斯工艺是在两级普通克劳斯转化之后,第三级改用选择性氧化催化剂,将H2S直接氧化成元素硫,硫回收率可以从98%提升至99。
5%;而带有SCOT尾气处理的克劳斯工艺,通过第三级加氢还原将过程气中的SO2和单质硫转化为H2S,同时将COS和CS2水解为H2S,采用MDEA吸收尾气中的H2S,胺溶液经加热再生循环使用,再生塔顶的酸性气送制硫燃烧炉,吸收塔顶尾气送尾气焚烧炉燃烧后达标排放。
我公司采用传统三级克劳斯工艺,尾气送至锅炉进行焚烧,炉内进行干法脱硫后,通过镁法脱硫,实现环保排放合格。
超级克劳斯硫磺回收工艺及应用

超级克劳斯硫磺回收工艺及应用摘要:克劳斯硫磺回收工艺自20世纪30年代实现工业化后,已经广泛用于合成氨和甲醇原料气生产、炼厂气加工、天然气净化等煤、石油、天然气的加工过程中。
克劳斯工艺具有流程简单、操作灵活、回收硫磺纯度高(质量分数可达99.8%)、投资费用低、环境及规模效益显著等特点,产品硫磺可作为生产硫酸的一种硫资源,也可作其它部门的化工原料。
本文对超级克劳斯硫磺回收工艺及应用进行了分析探讨,仅供参考。
关键词:硫磺回收;超级克劳斯;工艺一、超级克劳斯硫磺回收工艺从石油,石化、冶金、化肥等行业含H2S等硫化物的酸性气中回收利用硫,根据工艺流程选择和当地产品销路情况,产品可以制成硫磺或硫酸。
对含(一)、S酸性气体的处理,用H2S制取硫磺,工业生产中多采用固定床催化氧化,典型的方法有克劳斯工艺。
利用克劳斯装置净化尾气中的硫化物回收硫磺工艺已得到了迅速发展,其具体工艺流程有20多种,主要有传统克劳斯工艺,低温克劳斯工艺、超级克劳斯(SuperClaus)工艺,带有SCOT尾气处理的克劳斯工艺等。
其中超级克劳斯工艺是在两级普通克劳斯转化之后,第三级改用选择性氧化催化剂,将H2S直接氧化成元素硫,传统克劳斯工艺要求H2S/SO2摩尔比值为2的条件下进行,而此种工艺却维持选择性氧化催化段在富H2S条件下举行,一改以往单纯增加级数来提高H2S的回收率的方法。
超级克劳斯工艺改变了以往单纯提高H2S和SO2反应进程的方法,在传统克劳斯转化的最后一级转化段使用新型选择性氧化催化剂,由此来改进克劳斯工艺的硫回收技术。
在通入过量空气的情况下,超级克劳斯工艺可将来自克劳斯段最后一级过程气中剩余的H2S选择性地氧化为单质硫。
超级克劳斯反应器出口的过程气(含有非常少量的H2S)进入深冷器中,将过程气中的硫磺最大限度地捕集下来,从而将硫磺回收率提高到99%以上。
超级克劳斯工艺流程图见下图。
二、技术特点1、操作灵活方便由于超级克劳斯工艺采用过量空气操作,从而产生较少的SO2,因此对空气的控制要求不是很严格,不要求精确控制H2S和SO2的比例,而是将最后一级克劳斯转化器出口过程气中H2S体积分数控制在0.6%~1.5%,因此可以采用简单的流量控制回路,使操作灵活方便、弹性范围大,操作下限可以达到15%;超级克劳斯催化剂具有良好的热稳定性、化学稳定性和机械强度,有害物质排放少,催化剂使用寿命长达8~10年;过程气中高浓度水含量不会影响H2S的转化率,装置运行平稳可靠,维修方便,非计划性停车时间少于1%。
超优克劳斯硫回收工艺技术及应用前景

超优克劳斯硫回收工艺技术及应用前景
超优克劳斯硫回收工艺技术及应用前景
超优克劳斯工艺是一项先进、成熟的硫回收技术,具有流程简单、操作灵活、安全可靠、运行费用低、应用规模不限、使用范围广、硫回收率高等优点,对新建硫回收装置及原有老装置改造都有一定的推广应用价值.介绍了超优克劳斯硫回收工艺原理、技术特点及国内装置建设概况,并时该工艺在国内相关领域的应用前景作出了展望.
作者:汪家铭 WANG Jia-ming 作者单位:川化集团有限责任公司,四川,成都,610301 刊名:硫磷设计与粉体工程英文刊名:SULPHUR PHOSPHORUS & BULK MATERIALS HANDLING RELATED ENGINEERING 年,卷(期):2009 ""(4) 分类号:X701.3 关键词:硫回收超优克劳斯工艺技术特点应用前景展望。
- 1、下载文档前请自行甄别文档内容的完整性,平台不提供额外的编辑、内容补充、找答案等附加服务。
- 2、"仅部分预览"的文档,不可在线预览部分如存在完整性等问题,可反馈申请退款(可完整预览的文档不适用该条件!)。
- 3、如文档侵犯您的权益,请联系客服反馈,我们会尽快为您处理(人工客服工作时间:9:00-18:30)。
超级克劳斯工艺的前景与改进
一、工艺原理
传统克劳斯法是一种比较成熟的多单元处理技术,克劳斯工艺发明伊始就成为硫回收工业的标准工艺流程,也是目前应用最为广泛的硫回收工艺之一。
根据过程气中H2S体积百分比的高低,分别采用直流克劳斯法、分流克劳斯法、直接氧化克劳斯法。
其工艺过程为含有H2S的酸性气体在克劳斯炉内燃烧,使部分H2S氧化为SO2,然后SO2再与剩余的未反应的H2S在催化剂作用下反应生成硫黄[3] 。
超优克劳斯是克劳斯延伸型工艺,在克劳斯硫回收基础上突破传统观念的基础上,巧妙地组合了近年开发的新技术,对传统的克劳斯工艺进行改进,从改善热力学平衡和强化硫回收的角度出发,这包括发展新型催化剂、富氧燃烧技术、深冷器技术等,对克劳斯工艺作了较大的改造,在传统克劳斯转化之后,最后一级转化段使用新型选择性氧化催化剂,增加一个选择性催化氧化反应器(超级克劳斯反应器),成为超级克劳斯(SuperClaus)工艺,与此同时在最后一级克劳斯催化反应器床层中的克劳斯催化剂下面装填了一层加氢还原催化剂,构成加氢催化还原反应器(超优克劳斯反应器),将SO2还原成硫和H2S 后再选用选择性氧化催化剂,使总硫回收率得以大大提高。
根据酸性气体进料量和催化反应器数量,回收率可以达到99.4%以上或更高
二、国内概况
超优克劳斯工艺是荷兰Jacobs公司的专利技术,具有超级克劳斯工艺的所有优点,不仅适用于现有的克劳斯装置改造,也适用于新建装置,在石化、石油、天然气行业国内也有数套超优克劳斯装置投入运行。
从2007年起,国内新建的数套煤化工装置都采用了超优克劳斯硫回收技术(见表2),目前大多在建。
陕西榆林天然气化工有限公司年产140万吨煤制甲醇资源综合利用项目中的五大关键生产技术之一硫回收技术采用超优克劳斯技术,计划于2011年8月1日投料试车。
此外,内蒙古天河化工有限责任公司年产100万t煤制甲醇的一期工程年产60万t甲醇项目也采用了超优克劳斯技术。
陕西咸阳化学工业有限公司在陕西省咸阳市东郊化工工业园区内建设一套年产60万t甲醇项目。
由于该项目厂址位于西安市和咸阳市之间,人口密度较大,对于环保的要求非常严格。
超优克劳斯工艺能完全满足项目的排放要求。
含H2S的酸性气体进入硫黄回收装置界区,经过处理后酸性尾气达标排放到装置界区外,同时生产液态硫黄产品。
该项目预计在2009年10月投料试车。
华亭中煦煤化工有限公司,年产60万t甲醇项目的硫黄回收技术引进超优克劳斯技术。
该项目的硫黄回收进料酸性气来自甲醇洗单元,酸性气中的COS和H2S 通过超优克劳斯技术加以脱除和回收,尾气中SO2 浓度能够完全满足小于550mg/m3 的排放指标的要求。
陕西延长石油集团年产20万t醋酸及配套项目是以煤炭为原料,选用美国德士古煤气化技术,采用甲醇低压羰基合成法醋酸工艺。
其中合成气的净化采用低温甲醇洗工艺,甲醇洗装置的含H2S酸性气体进入超优克劳斯硫回收装置处理,最终使得尾气中SO2浓度低于国家排放要求。
该项目建设期3年,预计2009
年6月开车。
安徽淮化集团是安徽省最大的煤化工生产基地。
在年产30万t合成氨项目中合成气的净化采用低温甲醇洗工艺,从低温甲醇洗装置出来的含H2S酸性气体成分为:H2S19.98%、CO275.926%、COS1.997%、N21.993%、CH2OH0.104%。
通过减少甲醇循环量、较低再生压力、提高再生温度等措施使酸性气体中的H2S 含量提高到23%以上,满足超优克劳斯工艺对进料气中H2S含量的要求,再进入超优克劳斯硫回收装置处理,装置的操作弹性20%~145%[6] ,处理后的尾气达标排放。
项目预计在2008年年底建成,2009年年中投产运行。
三、应用前景
1996年我国颁布的新环境保护法规《大气污染物综合排放标准》(GB16279-1996)规定酸性气处理装置排放烟气中的SO2最高允许排放浓度≤960mg/m3(即≤0.0336%),虽然目前二级克劳斯和三级克劳斯技术已可立足国内,但不能满足环保要求。
国内三级克劳斯总硫回收率一般在94%~96%,最高在98%。
按回收率98%计算,SO2排放浓度将达到0.29%,远超过环保指标0.0336%。
由于超优克劳斯硫回收工艺可以在原有克劳斯装、运行费用较低,尾气符合排放标准的目的。
煤化工酸性气成分复杂,除了含有炼厂和天然气处理厂常见的烃类、氨和有机硫以外,还含有COS、HCN、NH3、CHOH、CH3OH等杂质。
此外,与炼厂和天然气净化厂酸性气来自MDEA等醇胺吸收不同,煤化工装置酸性气往往直接来自低温甲醇洗等合成气净化,因此H2S浓度较低,一般只有20%~30%。
针对煤化工的特点,应选择适应低酸性气浓度,高弹性范围,可以处理复杂气体的硫回收工艺,同时要求装置投资和操作费用尽量低[7]。
随着国内以煤为原料制合成氨和甲醇生产装置不断增加,可以预计在今后几年内煤制合成氨和甲醇装置还会不断增加且规模趋于大型化,过去适应于小规模装置的传统克劳斯工艺或其他落后的处理工艺已无法满足环保的要求,同时日趋严格的环保法规也对我国煤制合成氨和甲醇装置提出了新的要求。
由于煤化工领域的特殊性,且通常在克劳斯装置下游没有SCOT 尾气处理装置。
针对这样的情况,若采用传统克劳斯+SCOT 工艺,虽能达到环保要求,但该工艺相对流程复杂,操作工艺条件苛刻,装置投资较大。
因此,对于没有溶剂吸收装置的煤化工领域来说,也不是一个很好的选择。
近年来,国内新建的合成氨和甲醇装置中的气体净化大都采用德国鲁奇公司的低温甲醇洗和国内自主开发的NHD法气体净化技术.无论采用哪种技术,溶剂再生后的酸性气体中H2S浓度一般在25%~30%,且气量也不大。
由于酸性气浓度低和气量小,使得燃烧段的温度较低,这样造成其他杂质燃烧不完全。
其次,由于传统克劳斯工艺本身的限制,对于较高酸性气浓度理论上的回收率通常为96%~98%,实际回收率一般只能达到94%~97%。
所以,目前大多数采用单一的传统克劳斯工艺处理的合成氨和甲醇企业都存在着克劳斯尾气排放超标问题[8]。
国内原有或某些新建的甲醇厂和合成氨厂通常采用单一的传统克劳斯工艺,即在克劳斯装置的上游没有气体吸收段,这意味着酸性气无法提浓。
同样,在克劳斯装置下游也没有SCOT尾气处理装置,这样根本不可能满足国家GB1679-1996《大气污染物综合排放标准》中规定的已建装置S02排放浓度必须小于0.042%和新建装置S02排放浓度必须小于0.0336%的排放指标。
面对这样的情况,现有的
克劳斯硫回收装置已不再适合低H2S浓度酸性气净化要求,而超优克劳斯工艺采用的富氧燃烧技术和选择性氧化反应,保证过程气的充分燃烧和完全反应,以及采用深冷器可以将过程气冷却到硫黄的凝固点温度,即114.5℃附近,由此把硫蒸气的损失降到最低水平,通常可以减少近0.06% 的硫损失,降低尾气排放中的SO2含量,可以在没有尾气处理的情况下,满足日益严格的环保要求,是新建煤制合成氨和甲醇酸性气硫回收装置和现有克劳斯装置改造的最佳选择。
总之,选择硫回收工艺主要应考虑经济性,技术性和保证国家现有的和未来的环保指标。
所以,在以煤为原料制取合成氨和甲醇酸性气处理装置采用超优克劳斯硫回收工艺,将是一种最佳的选择。
与带有SCOT工艺的克劳斯装置相比,虽然没有尾气处理装置,但是超优克劳斯装置依然可以达到较高的99.0%以上的硫回收率,且投资费用较低[9]。
与传统克劳斯硫回收装置相比,其主要优势是投资相当,但硫回收率有明显的提高,且尾气符合环保排放要求。
我国目前现有克劳斯硫回收装置77套,以及对于为数不少的小型炼油厂、焦化厂、化肥厂等,H2S 含量低,建大型硫回收装置不合适也不现实,还有一些由于装置规模小,没有设尾气处理单元或尾气处理不达标的硫回收装置,预计超优克劳斯工艺今后在对国内现有克劳斯装置的技术改造和新建装置硫回收方面将具有一定的推广应用价值。
四、硫磺回收工艺存在的问题讨论
1、排放指标与工艺所能达到的收率之间的空间情况应该足够。
现行的大气污染物排放指标是1997年制定并执行的。
至此已经12年了。
德国再一次提高二氧化硫排放约束力,代表了新一轮环保风暴的到来。
作为企业的领导人,关注的不仅仅是工艺,而是工艺路线的发展前景。
2、工艺路线的控制手段应该越简单越好。
中国的国情决定了,工艺路线应该成熟、简单,从广大的成熟并大规模推广的路线上可以得到这个颠簸不破的真理。
不容易控制的工艺,其生命不会长远。
各个企业操作人员一少在少,工艺控制愈复杂,出事故的几率愈大。
3、工艺应该具有一定的抗波动能力。
用中国话说,得抗造,不能动不动放空,动不动停工。
4、工艺开停工应该具有较小的风险性。
装置开停工是一种异常状态,也是容易出现问题的时候,主要是设备问题、人身问题,愈简单的工艺,开停工愈不容易出问题。
5、工艺的故障保护连锁应该贴合实际,确保装置能够充分利用。
很多国外的连锁过于繁琐,造成全部摘除的后果。