叠式热流道模具研究
笔记本内壳叠层热流道注射模具设计

t h e
c l a m p i n gd i r e c t i o n , d u e t o t h e s t r u c t u r a l d e s i g n , f u n c t i o n a l r e q u i r e m e n t s a n d a s s e m b l y , p r o d u c t s h o l e s o l - e l n o T e u n e v e n , nd a
Ab s t r a c t : N o t e b o o k i n n e r s h e l l l a mi n a t e d i n j e c t i o n m o l d t e c h n o l o g y o v e r l a p p i n g a r r a n g e m e n t o f m u l t i p l e C t 2 1 3 i t y
un r n e r s y s t e m, d o u b l e - m o l d s t r u c t u r e , t o e n s u r e t h e q u a l i t y o f t h e p l st a i c p a r t s , a n d t o i m p r o v e p r o d u c t i o n e f ic f i e n c y .
na a l o g il f l , lo f w ,c o o l , p a c k nd a w a r p a g e na a l y s s,S i O t o ch a i e v e t h e t e c h n i c a l p e  ̄ o r m a  ̄e r e q u i r e me n t s . I t l l  ̄ e s h o t
热流道模具技术发展特点与趋势

分析:热流道模具技术发展特点与趋势文/李欢欢热流道模具在当今世界各工业发达国家和地区均得到极为广泛的应用。
这主要因为热流道模具拥有如下显著特点:1、缩短制件成型周期因没有浇道系统冷却时间的限制,制件成型固化后便可及时顶出。
许多用热流道模具生产的薄壁零件成型周期可在5秒钟以下。
2、节省塑料原料在纯热流道模具中因没有冷浇道,所以无生产费料。
这对于塑料价格贵的应用项目意义尤其重大。
事实上,国际上主要的热流道生产厂商均在世界上石油及塑料原料价格昂贵的年代得到了迅猛的发展。
因为热流道技术是减少费料降低材料费的有效途径。
3、减少费品,提高产品质量1.塑料材料种类热流道模具已被成功地用于加工各种塑料材料。
如PP,PE,PS,ABS,PBT,PA,PSU,PC,POM,LCP,PVC,PET,PMMA,PEI,ABS/PC等。
任何可以用冷流道模具加工的塑料材料都可以用热流道模具加工。
2.零件尺寸与重量用热流道模具制造的零件最小的在0.1克以下。
最大的在30公斤以上。
应用极为广泛灵活。
3.工业领域热流道模具在电子,汽车,医疗,日用品,玩具,包装,建筑,办公设备等各工业部门都得到广泛应用。
国际上热流道模具生产情况在世界上工业较为发达的国家和地区热流道模具生产极为活跃。
热流道模具比例不断提高。
许多10人以下的小模具厂都进行热流道模具的生产。
从总体上讲北美,欧洲使用热流道技术时间较久,经验较多水平较高。
在亚洲,除日本外,新加坡,南韩,台湾,香港处于领先地位。
北美,欧洲虽然模具制造水平较高,但价格较高交货期较长。
相比之下,亚洲的热流道模具制造商在价格与交货期上更具竞争性。
而中国的热流道模具尚处于起步阶段,但是正在快速增长,比例不断提高。
热流道技术在我国渐行渐热的同时,其元件呈现出几个主要发展趋势。
1、是元件小型化。
元件小型化,可以实现小型制品一模多腔和大型制品多浇口充模。
通过缩小喷嘴空间,可在模具上配置更多型腔,提高制品产量和注射机利用率,这对于`时间即是金钱`的现代塑料加工业来说非常重要。
热流道塑料模具技术的研究与发展前景

热流道塑料模具技术的研究与发展前景发表时间:2020-09-10T10:33:34.563Z 来源:《建筑实践》2020年4月第10期作者:邓旭文[导读] 塑料制品与人们的生活息息相关,与此同时人们也对塑料制品的质量和性能开始更多关注摘要:塑料制品与人们的生活息息相关,与此同时人们也对塑料制品的质量和性能开始更多关注。
当前我国塑料制造业正在迅速发展,在塑料制造的过程中,塑料模具技术十分关键,直接对塑料成型产生影响,需要对注塑模具进行不断的优化与改善。
不过注塑模具在我国的起步较晚,当前我国注塑行业中很多设备和技术都需要从国外引进,因此需要加强技术研究。
本文从热流道技术的相关概念入手,讨论热流道塑料模具技术的现状,最后对热流道塑料模具技术的发展趋势进行分析,希望对相关研究具有借鉴意义。
关键词:热流道塑料模具技术;研究;发展前景热流道技术是注塑制造业发展的重大革命,该技术相较于普通的下流道技术来说具有提升生产效率、提升产品质量、提升模具使用年限以及节约资源的作用,同时在诸多工业发达国家中。
热流道技术也在得到广泛推广,经济效益明显,当前我国对热流道技术的利用高度重视,不过在关键性技术方面还存在问题相关元件生产未能达到标准化要求相信通过技术攻关一定会实现热流道塑料模具的元件微型化标准化。
一、热流道技术的相关概念(一)热流道技术热流道塑料模具技术在注塑制造领域中十分关键,主要是用于塑料注塑膜流道绕柱系统的先进技术。
热流道成型期间就是利用注射机喷嘴,在送往浇口塑料过程中始终保持熔融以状态。
在热流道技术的支持下,每次开模不需要再次将废料取出,在浇筑系统的相关容量能下,可以在下次注射期间注入型腔。
(二)热流道系统的组成流道系统包括喷嘴、热源件热分流板温控器,不同热流道公司所选用的热流道形式也存在差异,主要的形式包括一字形H字形Y字形。
根据喷嘴形式,热流道模具相关结构包括以下两类:一种是外加热流道板,另一种是内加热流道板。
塑胶模具的前沿技术叠成模具

塑胶模具的前沿技术叠成模具叠层模具技术是区别于普通注塑模具技术的一种模具前沿技术,即在一副模具中将多个型腔在合模方向重叠布置。
这种模具通常有多个分型面,每个分型面上可以布置一个或多个型腔。
简单地说,叠层模具就相当于将多副单层模具叠放在一起,安装在一台注塑机上进行注塑生产。
叠层模具结构上由叠层模具热流道系统、专用模架系统、承载导向系统、双向顶出系统、开合模联动系统等多个系统组成,整个叠层模具的完美设计与应用除了科学的结构设计之外,还需要从最基本的模具钢材和热传材料的选择以及质量把控上进一步提高。
叠层模具生产效率超过普通的单层模具一倍或多倍,大幅度降低注塑生产成本。
从结构特点来看,叠层模具将多副型腔组合在一副模具中,充分利用普通注塑设备便可满足生产。
模具的充模、保压和冷却时间与单层模具相同,这就决定了叠层模具的生产效率将超过普通单层模具一倍甚至多倍,大大提高制品单位时间的产量。
叠层模具可安装在与单层模具相同的注塑机上,无须投资购买额外的机器和设备,从而节约了机器、设备、厂房和新增劳动力的成本。
叠层模具制造要求基本上与普通模具相同。
据统计,1副双层叠层模具的制造周期比两副单层模具的制造周期短5%~10%。
经生产验证,叠层式注射模具结构设计合理、可靠,制品尺寸一致性好,模具费用降低30%,成型效率提高一倍或多倍。
叠层模具适合于大批量生产形状扁平的大型制品,小型多腔壁薄制品,批量越大,制品生产成本越低。
叠层模具技术特点:通常,注塑机与常规模具配合使用时,其本身的注射量和开模行程只使用了额定的20%~40%,没有充分发挥注塑机的性能。
与常规模具相比,叠层式注射模具的锁模力只提高了5%~10%,但产量可以增加90%~95%,极大地提高了设备利用率和生产率,并降低了成本。
叠层注射模具作为一种新型的模具技术得到了不断的发展,特别是与热流道技术的结合,使它成为当今塑料模具发展的一项前沿技术。
传统的常规模具设计理论已经不适用于叠层式注射模具设计,因此急需发展一套全新的模具设计理论以指导叠层式注射模具设计。
注塑模具的热流道技术

注塑模具的热流道技术发布日期:2007-3-24 热流道模具与普通流道模具相比,具有注塑效率高、成型塑件质量好和节约原料等优点,随着塑料工业的发展,热流道技术正不断地发展完善,其应用范围也越来越广泛。
热流道是通过加热的办法来保证流道和浇口的塑料保持熔融状态。
由于在流道附近或中心设有加热棒和加热圈,从注塑机喷嘴出口到浇口的整个流道都处于高温状态,使流道中的塑料保持熔融,停机后一般不需要打开流道取出凝料,再开机时只需加热流道到所需温度即可。
热流道注射成型法于20世纪50年代问世,经历了一段较长时间的推广以后,其应用普及率逐年上升。
80年代中期,美国的热流道模具占注射模具总数的15%~17%,欧洲为12%~15%,日本约为10%。
但到了90年代,美国生产的塑料注射模具中热流道模具已占40%以上,在大型制品的注射模具中则占90%以上。
热流道系统的优势节约原料、降低制品成本是热流道模具最显著的特点。
普通浇注系统中要产生大量的料柄,在生产小制品时,浇注系统凝料的重量可能超过制品的重量。
由于塑料在热流道模具内一直处于熔融状态,制品不需修剪浇口,基本上是无废料加工,因此可节约大量原材料。
由于不需废料的回收、挑选、粉碎、染色等工序,故省工、省时、节能降耗。
注射料中因不再掺入经过回收加工的浇口料,故产品质量可以得到显著地提高,同时由于浇注系统塑料保持熔融,流动时压力损失小,因而容易实现多浇口、多型腔模具及大型制品的低压注塑。
热浇口利于压力传递,在一定程度上能克服塑件由于补料不足而形成的凹陷、缩孔、变形等缺陷。
适用树脂范围广、成型条件设定方便。
由于热流道温控系统技术的完善及发展,现在热流道不仅可以用于熔融温度较宽的聚乙烯、聚丙烯,也能用于加工温度范围较窄的热敏型塑料,如聚氯乙烯、聚甲醛等。
对易产生流涎的聚酰胺(PA),通过选用阀式热喷嘴也能实现热流道成型。
另外,操作简化、缩短成型周期也是热流道模具的一个重要特点。
与普通流道相比,缩短了开合模行程,不仅制件的脱模和成型周期缩短,而且有利于实现自动化生产。
热流道发展——精选推荐
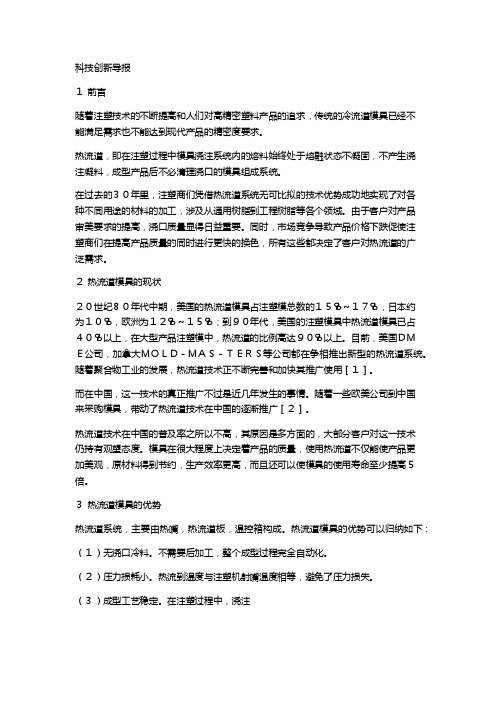
科技创新导报1前言随着注塑技术的不断提高和人们对高精密塑料产品的追求,传统的冷流道模具已经不能满足需求也不能达到现代产品的精密度要求。
热流道,即在注塑过程中模具浇注系统内的熔料始终处于熔融状态不凝固,不产生浇注凝料,成型产品后不必清理浇口的模具组成系统。
在过去的30年里,注塑商们凭借热流道系统无可比拟的技术优势成功地实现了对各种不同用途的材料的加工,涉及从通用树脂到工程树脂等各个领域。
由于客户对产品审美要求的提高,浇口质量显得日益重要。
同时,市场竞争导致产品价格下跌促使注塑商们在提高产品质量的同时进行更快的换色,所有这些都决定了客户对热流道的广泛需求。
2热流道模具的现状20世纪80年代中期,美国的热流道模具占注塑模总数的15%~17%,日本约为10%,欧洲为12%~15%;到90年代,美国的注塑模具中热流道模具已占40%以上,在大型产品注塑模中,热流道的比例高达90%以上。
目前,美国DME公司,加拿大MOLD-MAS-TERS等公司都在争相推出新型的热流道系统。
随着聚合物工业的发展,热流道技术正不断完善和加快其推广使用[1]。
而在中国,这一技术的真正推广不过是近几年发生的事情。
随着一些欧美公司到中国来采购模具,带动了热流道技术在中国的逐渐推广[2]。
热流道技术在中国的普及率之所以不高,其原因是多方面的,大部分客户对这一技术仍持有观望态度。
模具在很大程度上决定着产品的质量,使用热流道不仅能使产品更加美观,原材料得到节约,生产效率更高,而且还可以使模具的使用寿命至少提高5倍。
3热流道模具的优势热流道系统,主要由热嘴,热流道板,温控箱构成。
热流道模具的优势可以归纳如下:(1)无浇口冷料。
不需要后加工,整个成型过程完全自动化。
(2)压力损耗小。
热流到温度与注塑机射嘴温度相等,避免了压力损失。
(3)成型工艺稳定。
在注塑过程中,浇注系统内的塑料始终处于熔融状态,注塑压力损失小,可实现多点浇口多腔模具及大型塑件的低压注塑。
热流道叠模
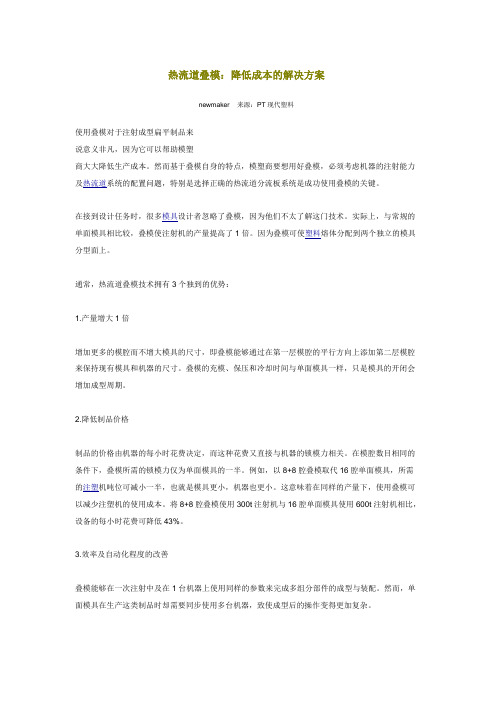
热流道叠模:降低成本的解决方案newmaker 来源:PT现代塑料使用叠模对于注射成型扁平制品来说意义非凡,因为它可以帮助模塑商大大降低生产成本。
然而基于叠模自身的特点,模塑商要想用好叠模,必须考虑机器的注射能力及热流道系统的配置问题,特别是选择正确的热流道分流板系统是成功使用叠模的关键。
在接到设计任务时,很多模具设计者忽略了叠模,因为他们不太了解这门技术。
实际上,与常规的单面模具相比较,叠模使注射机的产量提高了1倍。
因为叠模可使塑料熔体分配到两个独立的模具分型面上。
通常,热流道叠模技术拥有3个独到的优势:1.产量增大1倍增加更多的模腔而不增大模具的尺寸,即叠模能够通过在第一层模腔的平行方向上添加第二层模腔来保持现有模具和机器的尺寸。
叠模的充模、保压和冷却时间与单面模具一样,只是模具的开闭会增加成型周期。
2.降低制品价格制品的价格由机器的每小时花费决定,而这种花费又直接与机器的锁模力相关。
在模腔数目相同的条件下,叠模所需的锁模力仅为单面模具的一半。
例如,以8+8腔叠模取代16腔单面模具,所需的注塑机吨位可减小一半,也就是模具更小,机器也更小。
这意味着在同样的产量下,使用叠模可以减少注塑机的使用成本。
将8+8腔叠模使用300t注射机与16腔单面模具使用600t注射机相比,设备的每小时花费可降低43%。
3.效率及自动化程度的改善叠模能够在一次注射中及在1台机器上使用同样的参数来完成多组分部件的成型与装配。
然而,单面模具在生产这类制品时却需要同步使用多台机器,致使成型后的操作变得更加复杂。
叠模的基本特征叠模的特点是有两个分型面或者分型线。
叠模比单面模具要求的锁模力低,是因为两侧模腔的凸模表面抵消了相互之间的作用力。
估算锁模力有一个经验性方法,即制品成型面积与熔体压力的乘积,再乘以系数1.1所得的数值即为所需的锁模力。
使用此锁模力,就可在不增加设备模板尺寸的前提下,以双倍的模腔进行生产。
大多数叠模两个分型面的模腔数目相等。
热流道模具研究报告
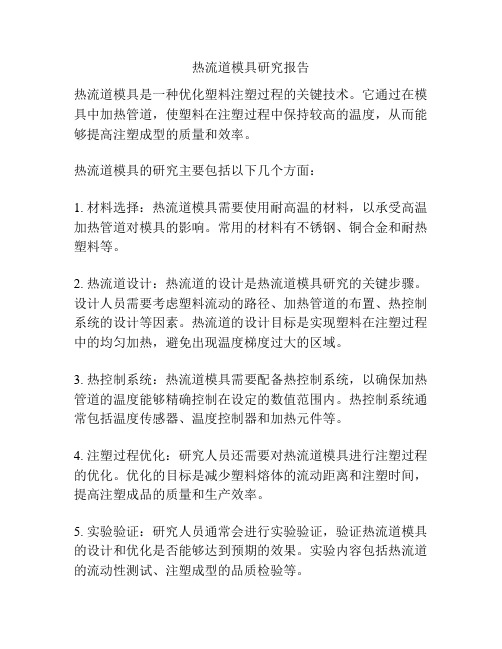
热流道模具研究报告
热流道模具是一种优化塑料注塑过程的关键技术。
它通过在模具中加热管道,使塑料在注塑过程中保持较高的温度,从而能够提高注塑成型的质量和效率。
热流道模具的研究主要包括以下几个方面:
1. 材料选择:热流道模具需要使用耐高温的材料,以承受高温加热管道对模具的影响。
常用的材料有不锈钢、铜合金和耐热塑料等。
2. 热流道设计:热流道的设计是热流道模具研究的关键步骤。
设计人员需要考虑塑料流动的路径、加热管道的布置、热控制系统的设计等因素。
热流道的设计目标是实现塑料在注塑过程中的均匀加热,避免出现温度梯度过大的区域。
3. 热控制系统:热流道模具需要配备热控制系统,以确保加热管道的温度能够精确控制在设定的数值范围内。
热控制系统通常包括温度传感器、温度控制器和加热元件等。
4. 注塑过程优化:研究人员还需要对热流道模具进行注塑过程的优化。
优化的目标是减少塑料熔体的流动距离和注塑时间,提高注塑成品的质量和生产效率。
5. 实验验证:研究人员通常会进行实验验证,验证热流道模具的设计和优化是否能够达到预期的效果。
实验内容包括热流道的流动性测试、注塑成型的品质检验等。
研究热流道模具有助于提高塑料注塑成型的质量和效率,推动塑料行业的发展。
未来的研究方向包括热流道模具的多层多通道设计、自适应温度控制技术等。
中山透镜模具热流道分享叠式模具热流道设计过程中应注意的五大问题
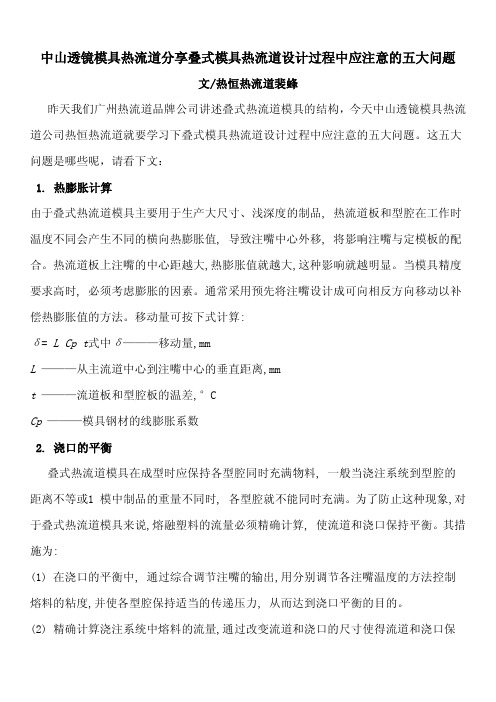
中山透镜模具热流道分享叠式模具热流道设计过程中应注意的五大问题文/热恒热流道裴蜂昨天我们广州热流道品牌公司讲述叠式热流道模具的结构,今天中山透镜模具热流道公司热恒热流道就要学习下叠式模具热流道设计过程中应注意的五大问题。
这五大问题是哪些呢,请看下文:1. 热膨胀计算由于叠式热流道模具主要用于生产大尺寸、浅深度的制品, 热流道板和型腔在工作时温度不同会产生不同的横向热膨胀值, 导致注嘴中心外移, 将影响注嘴与定模板的配合。
热流道板上注嘴的中心距越大,热膨胀值就越大,这种影响就越明显。
当模具精度要求高时, 必须考虑膨胀的因素。
通常采用预先将注嘴设计成可向相反方向移动以补偿热膨胀值的方法。
移动量可按下式计算:δ= L Cp t式中δ———移动量,mmL ———从主流道中心到注嘴中心的垂直距离,mmt ———流道板和型腔板的温差,°CCp ———模具钢材的线膨胀系数2. 浇口的平衡叠式热流道模具在成型时应保持各型腔同时充满物料, 一般当浇注系统到型腔的距离不等或1 模中制品的重量不同时, 各型腔就不能同时充满。
为了防止这种现象,对于叠式热流道模具来说,熔融塑料的流量必须精确计算, 使流道和浇口保持平衡。
其措施为:(1) 在浇口的平衡中, 通过综合调节注嘴的输出,用分别调节各注嘴温度的方法控制熔料的粘度,并使各型腔保持适当的传递压力, 从而达到浇口平衡的目的。
(2) 精确计算浇注系统中熔料的流量,通过改变流道和浇口的尺寸使得流道和浇口保持平衡。
开始时,可将浇注系统的尺寸设计得小一些,在试模过程中对它进行修正。
经过上述2 种方法修正得到的浇注系统, 即使当材料或注塑机的工艺参数改变时, 模具上所有的型腔同样可处于平衡状态, 从而使熔融塑料能同时充满模具型腔。
3 .型腔型芯尺寸模具成型部分的尺寸要根据制品的收缩率来确定, 以前一般在模具设计时就定下来而不考虑模具使用的具体工艺条件。
近来的研究显示, 制件在厚度不同、冷却循环时间不同等情况下所表现出的收缩率不同,故模具设计时必须考虑这方面的问题,才能生产出满足使用要求尤其是需要进行装配的高精度制件。
高效注塑模具- 叠层模具的开发探讨

什么是叠层模具?
叠层模具是当今塑料模具发展的一项前沿技术; 型腔是分布在2个或多个层面上的,呈重叠式排列,相当于是将多 副模具叠放组合在一起
叠层模具产生的需求背景
通常注塑机在使用单层塑料注射模具的时候,其本身 的 注 射 量 和 开 模 行 程 只 使 用 了 额 定 的20%~40%,没有充分发挥注 射机的性能,而叠层式注塑模具能够在不增加锁模力的基础上, 在 1 台注射机 1 个操作人员的条件下能使产量根据层数成倍增加, 可以极大地提高生产效率和设备利用率,并能节约生产成本和人 力资源。叠层式注塑模具最适于成型大型扁平制件、浅腔壳体类 制件、小型多腔薄壁制件和需大批量生产的制件。
普通双层叠模的应用实例
产品模具基本信息
模号: 模腔数: B09999 8+8 客户: Zobele US 胶料: PP 产品类型: 香水盒 产品名称: Inner housing 胶料牌号: PP copolymer 缩水率: 1.017
制作部门: 精密一部 T1时间:
2009-08-18 产品尺寸: 38X64X90mm
第八步:安装同步开合模机构
第九步:接通水路、电子线路
注塑工艺
炮筒温度:230/245/240/235/220 摄氏度 射胶压力:85/95 kgf/cm2 保压:35% 注射时间:2.68s,保压时间:6S,冷却时间:9s 周期时间:29s 锁模力:350T 前模温度:35º C 后模温度: 35º C
叠层模具的优点是什么?
与常规模具相比,叠层式模具锁模力只提高了10%~15%,但产量可 以增加90%~95%; 模具制造要求基本上与常规模具相同,且将多副型腔组合在一副模 具中,所以模具制造周期也大大缩短; 使用高效叠层注塑模可以得到双倍或者四倍于普通单层模的产出而 无须投资购买额外的机器和设备。这就节约了安装机器、设备和扩 建厂房、新增劳动力的费用; 叠层模具可以装在单层模具要求相近的注塑机上,单位时间的产出 效率却是成倍的增长 节约原料,易于自动化,提高产品性能,缩短生产周期
叠层式热流道注塑模具技术的应用进展
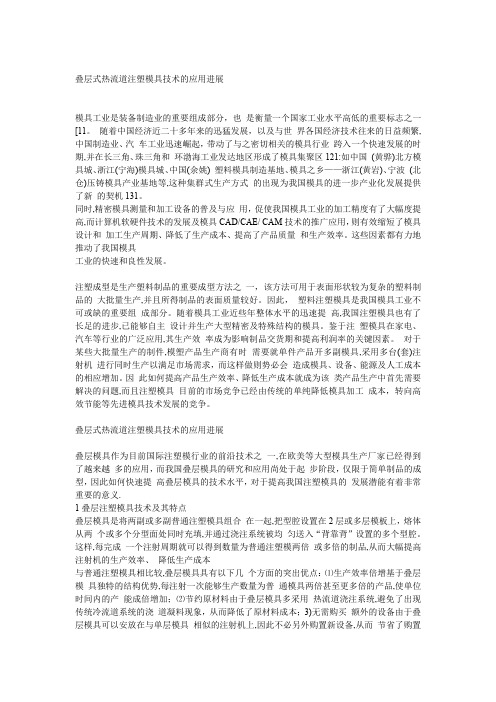
叠层式热流道注塑模具技术的应用进展模具工业是装备制造业的重要组成部分,也是衡量一个国家工业水平高低的重要标志之一[11。
随着中国经济近二十多年来的迅猛发展,以及与世界各国经济技术往来的日益频繁,中国制造业、汽车工业迅速崛起,带动了与之密切相关的模具行业跨入一个快速发展的时期,并在长三角、珠三角和环渤海工业发达地区形成了模具集聚区121:如中国(黄骅)北方模具城、浙江(宁海)模具城、中国(余姚) 塑料模具制造基地、模具之乡——浙江(黄岩)、宁波(北仓)压铸模具产业基地等,这种集群式生产方式的出现为我国模具的进一步产业化发展提供了新的契机131。
同时,精密模具测量和加工设备的普及与应用,促使我国模具工业的加工精度有了大幅度提高,而计算机软硬件技术的发展及模具CAD/CAE/ CAM技术的推广应用,则有效缩短了模具设计和加工生产周期、降低了生产成本、提高了产品质量和生产效率。
这些因素都有力地推动了我国模具工业的快速和良性发展。
注塑成型是生产塑料制品的重要成型方法之一,该方法可用于表面形状较为复杂的塑料制品的大批量生产,并且所得制品的表面质量较好。
因此,塑料注塑模具是我国模具工业不可或缺的重要组成部分。
随着模具工业近些年整体水平的迅速提高,我国注塑模具也有了长足的进步,已能够自主设计并生产大型精密及特殊结构的模具。
鉴于注塑模具在家电、汽车等行业的广泛应用,其生产效率成为影响制品交货期和提高利润率的关键因素。
对于某些大批量生产的制件,模塑产品生产商有时需要就单件产品开多副模具,采用多台(套)注射机进行同时生产以满足市场需求,而这样做则势必会造成模具、设备、能源及人工成本的相应增加。
因此如何提高产品生产效率、降低生产成本就成为该类产品生产中首先需要解决的问题,而且注塑模具目前的市场竞争已经由传统的单纯降低模具加工成本,转向高效节能等先进模具技术发展的竞争。
叠层式热流道注塑模具技术的应用进展叠层模具作为目前国际注塑模行业的前沿技术之一,在欧美等大型模具生产厂家已经得到了越来越多的应用,而我国叠层模具的研究和应用尚处于起步阶段,仅限于简单制品的成型,因此如何快速提高叠层模具的技术水平,对于提高我国注塑模具的发展潜能有着非常重要的意义.1叠层注塑模具技术及其特点叠层模具是将两副或多副普通注塑模具组合在一起,把型腔设置在2层或多层模板上,熔体从两个或多个分型面处同时充填,并通过浇注系统被均匀送入“背靠背”设置的多个型腔。
基于CAE技术的餐盒盖叠层热流道注射模具设计

基于CAE技术的餐盒盖叠层热流道注射模具设计朱海旭;王金莲【摘要】PP塑料餐盒盖,薄壁扁平,大批量生产,可采用叠层热流道模具提高效率,降低成本.介绍了餐盒盖叠层热流道模具的结构和工作原理,借助Mold flow软件确定了进浇位置,完成排气和冷却系统设计,确保塑件质量.【期刊名称】《装备制造技术》【年(卷),期】2016(000)008【总页数】4页(P241-243,246)【关键词】热流道;叠层模具;模流分析;注射成型【作者】朱海旭;王金莲【作者单位】杭州科技职业技术学院机电工程学院,浙江杭州311402;杭州科技职业技术学院机电工程学院,浙江杭州311402【正文语种】中文【中图分类】TQ320.52随着人们生活水平的提高和电子商务的发展,外出点餐和外卖业务井喷式增长,一次性餐盒的市场需求也随之增长。
聚丙烯PP塑料由于安全无毒以及良好的机械性能和热性能成为餐盒主要材料。
传统的塑料餐盒盖生产采用冷流道点浇口进浇,废料耗材甚至超过产品。
另外鉴于餐盒盖扁平薄壁浅腔型的特点,当大批量生产时,要求高锁模力和注射压力,因此需选用中大型注射机,而模具的开模行程和模具厚度又很小,注塑量往往不到注射机额定值的1/4~1/3,机器的生产能力未能充分施展,生产效率不高,造成浪费[1]。
为改变生产现状,可采用叠层热流道模塑技术。
叠层式热流道模具是当今注塑模具工业发展的一项前沿技术。
采用热流道系统,原材料100%产品化,节省原料,提高产品品质。
叠层模具在一副模具中将多个型腔在合模方向重叠布置,生产效率高。
需要的注塑机与单层模具要求相同,无须投资购买额外的机器和设备,大幅降低了注塑生产成本,适用于大批量生产的制品[2]。
本文针对餐盒盖产品特点,利用Moldflow软件进行模流分析,完成餐盒盖叠层热流道2×2腔注塑模具设计。
如图1为一次性餐盒盖的产品图。
产品材料为聚丙烯PP塑料,结构简单,透明,塑件直径达60 mm,高度4 mm,壁厚0.5 mm,脱模斜度2°,属于薄壁扁平类产品。
叠层式热流道模具
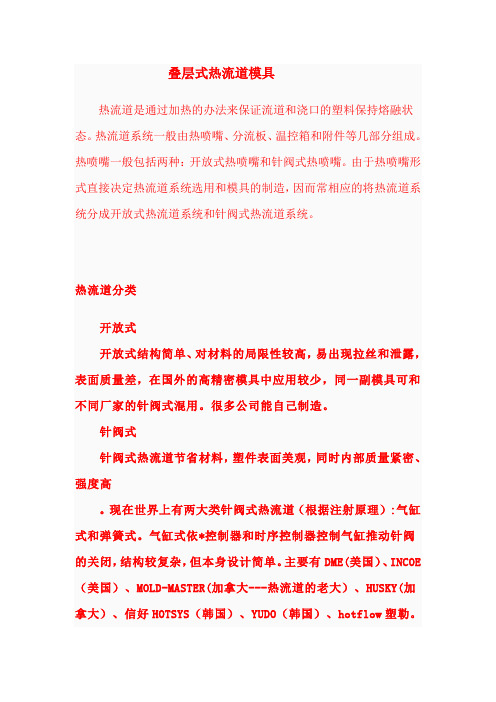
叠层式热流道模具热流道是通过加热的办法来保证流道和浇口的塑料保持熔融状态。
热流道系统一般由热喷嘴、分流板、温控箱和附件等几部分组成。
热喷嘴一般包括两种:开放式热喷嘴和针阀式热喷嘴。
由于热喷嘴形式直接决定热流道系统选用和模具的制造,因而常相应的将热流道系统分成开放式热流道系统和针阀式热流道系统。
热流道分类开放式开放式结构简单、对材料的局限性较高,易出现拉丝和泄露,表面质量差,在国外的高精密模具中应用较少,同一副模具可和不同厂家的针阀式混用。
很多公司能自己制造。
针阀式针阀式热流道节省材料,塑件表面美观,同时内部质量紧密、强度高。
现在世界上有两大类针阀式热流道(根据注射原理):气缸式和弹簧式。
气缸式依*控制器和时序控制器控制气缸推动针阀的关闭,结构较复杂,但本身设计简单。
主要有DME(美国)、INCOE (美国)、MOLD-MASTER(加拿大---热流道的老大)、HUSKY(加拿大)、信好HOTSYS(韩国)、YUDO(韩国)、hotflow塑勒。
气缸式因为其结构的特点决定模具精度要高,同时调试和维护都比较杂,其中MOLD-MASTER堪称热流道中的劳斯莱斯----加热部分在喷嘴上。
他们中的很大成本在调试和维护上,客户基本不能自己维护。
弹簧式就一家--FISA(日本),最大特点,依靠弹簧和注射压力的平衡控制针阀开关,装配调试和维护简单,模具精度不高,日本国内客户基本自己有维护能力,广泛应用在家电、汽车饰件、精密多腔模具中。
弹簧式与气缸的差别在于不能时序控制,不能很好解决熔接痕的问题。
塑美热流道研发了小直径耐磨喷嘴;弹簧针阀及内加热喷嘴价位上基本上这样(中国市场价),MOLD-MASTER、INCOE、DME、HUSKY、SM现在国外流行的叠模非热流道莫属,其实热流道模具减少了设计上的很多要求,对设计人员开发更多的模具结构提供了很大的方便。
近年来随着我国模具工业的迅猛发展,模具零件的标准化、专业化和商品化工作,已具有较高的水平,取得了长足的进步。
叠层式热流道模具的好处
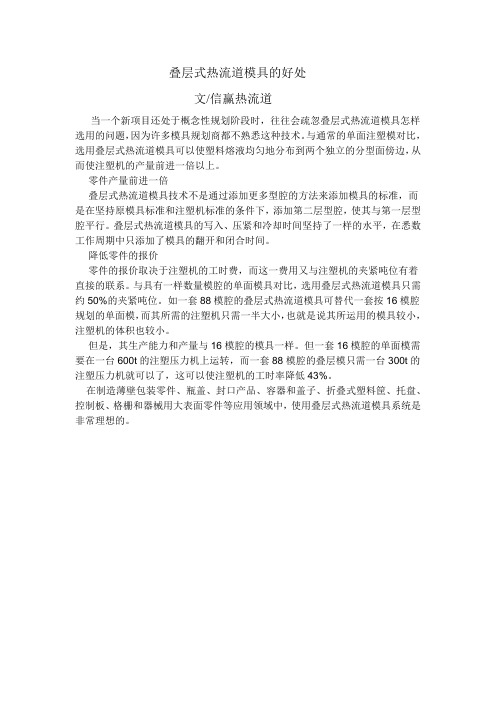
叠层式热流道模具的好处
文/信赢热流道
当一个新项目还处于概念性规划阶段时,往往会疏忽叠层式热流道模具怎样选用的问题,因为许多模具规划商都不熟悉这种技术。
与通常的单面注塑模对比,选用叠层式热流道模具可以使塑料熔液均匀地分布到两个独立的分型面傍边,从而使注塑机的产量前进一倍以上。
零件产量前进一倍
叠层式热流道模具技术不是通过添加更多型腔的方法来添加模具的标准,而是在坚持原模具标准和注塑机标准的条件下,添加第二层型腔,使其与第一层型腔平行。
叠层式热流道模具的写入、压紧和冷却时间坚持了一样的水平,在悉数工作周期中只添加了模具的翻开和闭合时间。
降低零件的报价
零件的报价取决于注塑机的工时费,而这一费用又与注塑机的夹紧吨位有着直接的联系。
与具有一样数量模腔的单面模具对比,选用叠层式热流道模具只需约50%的夹紧吨位。
如一套88模腔的叠层式热流道模具可替代一套按16模腔规划的单面模,而其所需的注塑机只需一半大小,也就是说其所运用的模具较小,注塑机的体积也较小。
但是,其生产能力和产量与16模腔的模具一样。
但一套16模腔的单面模需要在一台600t的注塑压力机上运转,而一套88模腔的叠层模只需一台300t的注塑压力机就可以了,这可以使注塑机的工时率降低43%。
在制造薄壁包装零件、瓶盖、封口产品、容器和盖子、折叠式塑料筐、托盘、控制板、格栅和器械用大表面零件等应用领域中,使用叠层式热流道模具系统是非常理想的。
- 1、下载文档前请自行甄别文档内容的完整性,平台不提供额外的编辑、内容补充、找答案等附加服务。
- 2、"仅部分预览"的文档,不可在线预览部分如存在完整性等问题,可反馈申请退款(可完整预览的文档不适用该条件!)。
- 3、如文档侵犯您的权益,请联系客服反馈,我们会尽快为您处理(人工客服工作时间:9:00-18:30)。
叠式热流道模具研究
1 引言
当前热流道技术的发展趋势有新型阀式喷嘴的研制、叠式热流道模具技术、新型智能化温控、小型化与标准化,以及热流道专家系统等。
叠式模具相当于将多副模具叠放组合在一起,这种模具往往需要有一个较长的主流道来输送熔体到模具中部。
叠式模具最适于成型大型扁平制件、小型多腔薄壁制件和需大批量生产的制件。
最初的叠式模具因使用普通流道, 每次注射都要去除浇道, 不能实现自动化生产, 因而应用较少, 当叠式模具应用了热流道技术后, 其应用才得到了较大的提高。
叠式热流道模具热流道系统的主流道设置在模具的中心部分,由于叠式模具型腔有多个分型面,这意味着需要有一个机构使这些分型面能同时分型。
与常规模具相比, 这种模具锁模力只提高了5 %~10 % , 但产量增加90 %~95 % , 可以极大地提高设备利用率和生产效率,(广州英辉热流道技术有限公司欢迎您,网址)节约成本。
此外,由于模具制造要求基本上与常规模具相同, 主要是将2 副或多副型腔组合在 1 副模具中, 所以模具制造周期可缩短5 %~10 % , 因此尽管这种模具的加工技术要求较高, 同时对注塑机的开模行程要求也较大, 但在工业上的应用前景较好。
2 叠式热流道模具的结构
叠式模具是将2 副或多副常规注射模组合在一起, 并加上热流道系统, 该模具有3 个主要组成部分,即中间部分、动模部分及定模部分(见图1) 。
中间部分由内装有热流道和向两侧供料的进料口的2块模板构成,在动模和定模部分都设置有顶出装置,用机械、液压或气压等动力实现制品脱模。
热流道系统通过模具的定模板部分进行延伸,当模具闭合时与注塑机喷嘴相连接, 这一因素在安排型腔的排列时应考虑进去, 顶出零件决不能穿过热流道伸展区域。
模具部分安装在动模板上, 在脱模过程中, 中间板沿注塑机轴向运动, 将延伸部分同喷嘴脱开。
流道的延伸部分必须足够长, 这样在开模过程中可避免因熔料泄漏粘于导柱、导套而影响模具的运转。
2. 1 热流道系统
叠式模具的热流道系统主要由喷嘴、歧管、热流道板(集流板) 、加热装置等组成。
喷嘴的形式有多种, 常用的喷嘴有开式喷嘴、鱼雷梭式喷嘴和针阀式喷嘴。
在使用开式喷嘴时往往会引起流涎, 除了在塑件表面造成疵点外, 成型塑件的性能也会因此而降低, 形成的冷料甚至可能堵塞浇口, 但通常新式机器都具有熔体减压(在模具打开之前注塑机螺杆后退) 功能,(广州英辉热流道技术有限公司欢迎您,网址)或在热流道歧管的浇口衬套里设有 1 个膨胀腔来解决这个问题。
然而必须注意的是,减压总是要保持在最低限度,
以免在主流道、流道系统或浇口附近吸入空气, 因此叠式热流道系统一般多采用阀式热喷嘴。
2. 2 温控系统
叠式热流道模具中的温控系统包括加热系统和冷却系统, 加热系统的作用是保持流道中的塑料呈熔融状态, 冷却系统的作用则是完成塑料和模具之间的热量交换。
加热系统中温度不能过低或过高,温度过低,塑料会在流道中形成较厚的固化层, 影响实现连续注射; 温度过高, 可能导致塑料分解变色, 在塑件上形成缺陷乃至报废, 因此应严格控温。
特别是新型高分子材料的不断出现,温控要求的敏感度越来越高,国外的温控系统已实现了微电脑控制, 其精度可达±0. 5 ℃。
设计冷却回路时,应考虑塑件的形状及冷却介质种类、温度、流速及冷却管道的布置等因素。
2. 3 开模机构
叠式模具在开模时,不仅动模部分移动,中间部分也同时移动,即应同时打开 2 个分型面,并由两侧的顶出机构使塑件脱模。
目前叠式模具的开模方式一般是由铰接杠杆或齿条驱动来同步开模, 也可使用液压系统(见图2) 。
采用杠杆传动装置的模具运动平稳, 中间板和顶出机构的运动能在较长时间内加速, 受力较小且磨损少。
齿条开模机构在模具的两边各有1 根齿条, 2 根齿条与安装在中间部分的齿轮相啮合, 通过导轨及齿条控制系统使模具在2个分型面同时开启。
与液压驱动和铰接杠杆驱动相比, 齿轮齿条驱动机构性能较好, 也较经济, 但用铰接杠杆移动模具的灵活性则更大。
采用液压辅助开模更易控制开模时间,但结构较大。
叠式模具在开合模过程中需要平稳而有效的支撑, 有效的支撑方式有导柱支撑、上吊式横梁支撑、下导轨架支撑等3 种, 支撑的种类应按模具结构来确定。
用导柱及上横梁支撑有一定的作用, 但是模具中央部分重量可能将导柱或横梁压弯, 从而使分型面不能充分对齐, 因此这种支撑常会产生相当的定量偏斜, 使模具不能充分对齐以及分型面不完全准确闭合。
用下支撑方式可以提供良好的支撑, 但这需要横梁有很好的地基支撑。
3 叠式模具设计过程中应注意的问题
3. 1 热膨胀计算
由于叠式热流道模具主要用于生产大尺寸、浅深度的制品, 热流道板和型腔在工作时温度不同会产生不同的横向热膨胀值, 导致注嘴中心外移, 将影响注嘴与定模板的配合。
热流道板上注嘴的中心距越大,热膨胀值就越大,这种影响就越明显。
当模具精度要求高时, 必须考虑膨胀的因素。
通常采用预先将注嘴设计成可向相反方向移动以补偿热膨胀值的方法。
移动量可按下式计算:
δ= L Cp t
式中δ———移动量,mm
L ———从主流道中心到注嘴中心的垂直距
离,mm
t ———流道板和型腔板的温差,°C
Cp ———模具钢材的线膨胀系数
3. 2 浇口的平衡
叠式热流道模具在成型时应保持各型腔同时充满物料, 一般当浇注系统到型腔的距离不等或1 模中制品的重量不同时, 各型腔就不能同时充满。
为了防止这种现象,对于叠式热流道模具来说,熔融塑料的流量必须精确计算, 使流道和浇口保持平衡。
(广州英辉热流道技术有限公司欢迎您,网址)其措施为:
(1) 在浇口的平衡中, 通过综合调节注嘴的输出,用分别调节各注嘴温度的方法控制熔料的粘度,并使各型腔保持适当的传递压力, 从而达到浇口平衡的目的。
(2) 精确计算浇注系统中熔料的流量,通过改变流道和浇口的尺寸使得流道和浇口保持平衡。
开始时,可将浇注系统的尺寸设计得小一些,在试模过程中对它进行修正。
经过上述 2 种方法修正得到的浇注系统, 即使当材料或注塑机的工艺参数改变时, 模具上所有的型腔同样可处于平衡状态, 从而使熔融塑料能同时充满模具型腔。
3. 3 型腔型芯尺寸
模具成型部分的尺寸要根据制品的收缩率来确定, 以前一般在模具设计时就定下来而不考虑模具使用的具体工艺条件。
近来的研究显示, 制件在厚度不同、冷却循环时间不同等情况下所表现出的收缩率不同,故模具设计时必须考虑这方面的问题,才能生产出满足使用要求尤其是需要进行装配的高精度制件。
3. 4 冷却系统的平衡
制件的冷却也需要进行平衡, 如果冷却系统在模具型腔和型芯上产生温差, 制件将在充填和收缩上产生很大不同。
不同模板间的冷却, 有可能使模板的对齐发生变化, (广州英辉热流道技术有限公司欢迎您,网址)从而影响模板的动作和造成磨损, 所以在叠式热流道模具的设计中要注意模具冷却系统的平衡问题。
3. 5 需要注意的其它问题
叠式热流道模具结构复杂,而在常规情况下,机械结构越简单,越不容易发生故障,因此在设计叠式热流道模具时必须考虑如何便于维修的问题。
使用叠式热流道模具应力求满足以下条件:
(1) 实现自动化生产。
(2)模具结构尽量简单,组装、拆卸应比较容易。
(3) 加热器本身应体积小、功率大,且不发生断电现象,破损后更换容易。
(4) 能够较简单地检测到故障位置, 以缩短维修时间。
(5) 浇注系统无漏料、流涎、拉丝等现象。