电炉炼钢工艺计算及炉型设计
年产万吨钢坯电炉炼钢车间初步设计
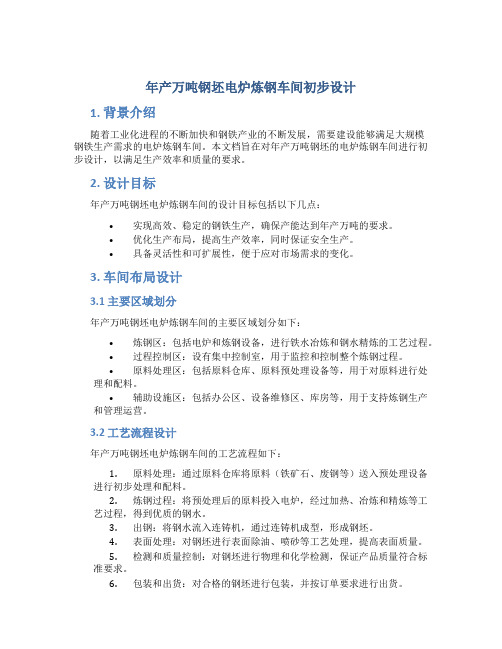
年产万吨钢坯电炉炼钢车间初步设计1. 背景介绍随着工业化进程的不断加快和钢铁产业的不断发展,需要建设能够满足大规模钢铁生产需求的电炉炼钢车间。
本文档旨在对年产万吨钢坯的电炉炼钢车间进行初步设计,以满足生产效率和质量的要求。
2. 设计目标年产万吨钢坯电炉炼钢车间的设计目标包括以下几点:•实现高效、稳定的钢铁生产,确保产能达到年产万吨的要求。
•优化生产布局,提高生产效率,同时保证安全生产。
•具备灵活性和可扩展性,便于应对市场需求的变化。
3. 车间布局设计3.1 主要区域划分年产万吨钢坯电炉炼钢车间的主要区域划分如下:•炼钢区:包括电炉和炼钢设备,进行铁水冶炼和钢水精炼的工艺过程。
•过程控制区:设有集中控制室,用于监控和控制整个炼钢过程。
•原料处理区:包括原料仓库、原料预处理设备等,用于对原料进行处理和配料。
•辅助设施区:包括办公区、设备维修区、库房等,用于支持炼钢生产和管理运营。
3.2 工艺流程设计年产万吨钢坯电炉炼钢车间的工艺流程如下:1.原料处理:通过原料仓库将原料(铁矿石、废钢等)送入预处理设备进行初步处理和配料。
2.炼钢过程:将预处理后的原料投入电炉,经过加热、冶炼和精炼等工艺过程,得到优质的钢水。
3.出钢:将钢水流入连铸机,通过连铸机成型,形成钢坯。
4.表面处理:对钢坯进行表面除油、喷砂等工艺处理,提高表面质量。
5.检测和质量控制:对钢坯进行物理和化学检测,保证产品质量符合标准要求。
6.包装和出货:对合格的钢坯进行包装,并按订单要求进行出货。
4. 设备选型和布置4.1 电炉选型年产万吨钢坯电炉炼钢车间的主要设备之一是电炉。
根据生产需求和技术要求,选用适当容量和高效率的电炉。
4.2 其他设备选型根据车间的实际情况,选用适当的设备,如炉盖起重机、原料处理设备、连铸机等。
选型时需要考虑设备的性能、稳定性、能耗和维护等因素。
4.3 设备布置根据车间布局和工艺流程,合理布置设备,保证生产流程的顺畅和安全。
电炉炼钢流程

电炉炼钢流程电炉炼钢是一种利用电能作为热源,通过电弧加热炉料,将废钢和铁合金等原料炼制成优质钢材的冶炼方法。
电炉炼钢流程通常包括预处理、炉料装入、炉前准备、炉内冶炼和炉后处理等环节。
下面将详细介绍电炉炼钢的流程及各个环节的操作步骤。
1. 预处理。
在进行电炉炼钢之前,首先需要对原料进行预处理。
这包括对废钢进行分类、清理和切割,对铁合金进行筛分和称重等工作。
同时,还需要对电炉进行检查和维护,确保电炉设备处于良好状态。
2. 炉料装入。
在炉料装入环节,操作人员需要按照炉料配比要求,将预处理好的废钢和铁合金装入电炉中。
同时,还需要加入适量的石灰、氧化铁等炼钢助剂,以调整炉料成分和保证冶炼质量。
3. 炉前准备。
在炉前准备阶段,操作人员需要对电炉进行预热,提高炉温至冶炼温度。
同时,还需要对电炉进行真空抽气或气体通风,以确保炉内气氛符合冶炼要求。
4. 炉内冶炼。
炉内冶炼是电炉炼钢的核心环节,操作人员需要根据工艺要求,通过电弧加热炉料,使其迅速熔化。
在冶炼过程中,还需要根据炉料状况进行合理的搅拌和氧化处理,以保证炼钢过程的顺利进行。
5. 炉后处理。
炉后处理是指在炼钢结束后,对冶炼产物进行处理和整理的环节。
这包括对炉渣进行清理和处理,对炼钢温度进行控制,以及对炼钢成品进行取样和检验等工作。
总结。
通过以上流程的介绍,我们可以看到,电炉炼钢是一个复杂的工艺过程,需要操作人员严格按照流程要求进行操作,以确保炼钢质量和生产效率。
同时,还需要对电炉设备进行定期维护和检查,以保证设备的正常运行和安全生产。
希望本文的介绍能够帮助大家更好地了解电炉炼钢的流程和操作要点,为相关行业的生产和管理工作提供参考和指导。
年产100万吨连铸坯的电弧炉 炼钢车间工艺设计

目录1 电弧炉炼钢技术现状及发展 (1)1.1电弧炉炼钢发展概况 (1)1.2国内外电炉炼钢技术的发展趋势 (1)2 电弧炉炼钢车间的设计方案 (3)2.1电炉车间生产能力计算 (3)2.1.1电炉容量和台数的确定 (3)2.1.2 电炉车间生产技术指标 (3)2.2电炉车间设计方案 (4)2.2.1 电炉炼钢车间设计与建设的基础材料 (4)2.2.2 产品大纲 (4)2.2.3 电炉炼钢车间的组成 (4)2.2.4 电炉车间各跨的布置情况 (5)3 电弧炉炉型设计 (6)3.1电弧炉炉型 (6)3.1.1 炉缸 (6)3.1.2 熔化室 (7)3.1.3 电极分布 (8)3.1.4 工作门和出钢口 (8)3.1.5 炉衬厚度 (8)3.2电弧炉变压器容量选择 (9)3.3水冷炉壁与水冷炉盖 (9)3.3.1 水冷炉盖的设计 (9)3.3.2 水冷炉盖的安装 (10)3.4偏心底出钢的设计 (11)3.4.1 EBT电炉的炉壳 (11)3.4.2 EBT电炉的炉底 (12)3.4.3 出钢口 (12)3.4.4 机械装置 (13)3.4.5 偏心底出钢箱的设计 (13)3.5水冷挂渣炉壁的设计 (14)3.5.1 电弧炉炉壁的热流 (14)3.5.2 冷却水流量 (14)3.5.3 水冷炉壁水速的确定 (15)3.5.4 管径的确定 (15)3.5.5 平衡挂渣厚度 (15)3.5.6 综合传热系数 (16)3.5.7 临界热流量与最大热流量 (16)4 电弧炉炼钢过程中的物料平衡与热平衡计算 (17)4.1物料平衡计算 (17)4.1.1熔化期计算 (19)4.1.2 氧化期计算 (23)4.2热平衡的计算 (27)4.2.1 计算热收入Qs 。
(27)4.2.2 计算热支出Qz 。
(29)5 电弧炉炼钢车间工艺设计 (33)5.1.1 废钢 (33)5.1.2 辅助料 (33)5.2电弧炉冶炼工艺 (34)5.3精整工艺 (35)5.4连铸操作工艺 (36)6 电弧炉炼钢车间工艺布置 (38)6.1原料跨 (38)6.1.1 原料跨的宽度 (39)6.1.2 原料跨的烘烤间 (39)6.1.3 原料跨总长度确定 (40)6.2炉子跨整体布置 (40)6.2.1 炉子跨工作平台高度 (40)6.2.3 炉子的变压器室和控制室 (40)6.2.4 电弧炉出渣和炉渣处理 (40)6.2.5 精炼炉的工艺布置 (40)6.2.6 炉子跨的长度、跨度、高度 (40)6.3连铸跨 (41)6.3.1 总体布置 (41)6.3.2 钢包回转台的布置 (41)6.3.3 连铸机操作平台的高度、长度、宽度 (41)6.3.4 连铸机总高和本跨吊车轨面标高 (42)6.3.5 连铸机总长度 (42)6.3.6 其它布置 (43)6.4精整跨 (43)7 车间主要设备的选择和配置 (45)7.1电弧炉主体设备选择 (45)7.1.1 校核年产量 (45)7.1.2 电极 (45)7.2精炼炉设备选择 (45)7.2.1 LF钢包炉的参数确定 (45)7.2.2 LF钢包炉的工艺确定 (46)7.3连铸设备选择 (46)7.3.1 钢包允许的最大浇注时间 (46)7.3.2 铸坯断面 (47)7.3.3 拉坯速度 (47)7.3.4 连铸机的流数 (48)7.3.5 铸坯的液相深度和冶金长度 (48)7.3.6 弧型半径 (49)7.4连铸机的生产能力的确定 (49)7.4.1 连铸浇注周期的计算 (49)7.4.2 连铸机作业率 (50)7.4.3 连铸坯收得率 (50)7.4.4 连铸机生产能力的计算 (51)7.4.5 最高日浇注炉数 (51)7.4.6 最高日产量 (52)7.5中间包及其运载设备 (52)7.5.1 中间包的形状和构造 (52)7.5.2 中间包的主要工艺参数 (52)7.6结晶器及其振动装置 (53)7.6.1 结晶器的性能要求及其结构要求 (53)7.6.2 结晶器主要参数选择 (53)7.6.3 结晶器的振动装置 (55)7.7二次冷却装置 (55)7.7.1 二冷装置的基本结构 (55)7.7.2 二次冷却水冷喷嘴的布置 (55)7.7.3 二次冷却水量的计算 (55)7.8拉矫装置及引锭装置 (56)7.9铸坯切割装置 (56)7.10盛钢桶的选择 (56)7.10.1 型号选择 (56)7.10.2 容纳钢水量 (56)7.10.3 盛钢桶内渣量 (57)7.10.4 盛钢桶容积 (57)7.10.5 盛钢桶壁砖衬厚度 (57)7.10.6 盛钢桶外壳 (57)7.10.7 盛钢桶的质量 (58)7.10.8 钢包需用量 (58)7.11渣罐及渣罐车的选择 (59)7.11.1 车间所需的渣罐数量 (59)7.11.2 车间所需渣罐车数量 (59)7.12起重机和电动平车的选择 (59)7.13其它辅助设备的选择 (60)8.1技术经济指标 (61)8.2车间人员编制 (61)9参考文献 (64)10 专题........................................... 错误!未定义书签。
电炉选型
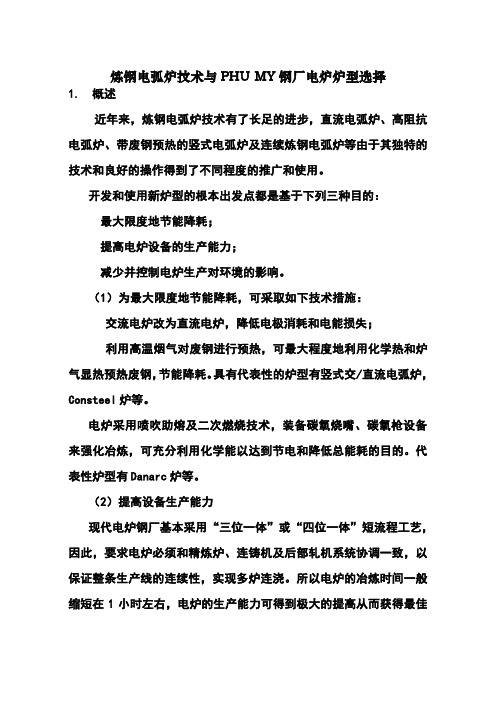
炼钢电弧炉技术与PHU MY钢厂电炉炉型选择1. 概述近年来,炼钢电弧炉技术有了长足的进步,直流电弧炉、高阻抗电弧炉、带废钢预热的竖式电弧炉及连续炼钢电弧炉等由于其独特的技术和良好的操作得到了不同程度的推广和使用。
开发和使用新炉型的根本出发点都是基于下列三种目的:最大限度地节能降耗;提高电炉设备的生产能力;减少并控制电炉生产对环境的影响。
(1)为最大限度地节能降耗,可采取如下技术措施:交流电炉改为直流电炉,降低电极消耗和电能损失;利用高温烟气对废钢进行预热,可最大程度地利用化学热和炉气显热预热废钢,节能降耗。
具有代表性的炉型有竖式交/直流电弧炉,Consteel炉等。
电炉采用喷吹助熔及二次燃烧技术,装备碳氧烧嘴、碳氧枪设备来强化冶炼,可充分利用化学能以达到节电和降低总能耗的目的。
代表性炉型有Danarc炉等。
(2)提高设备生产能力现代电炉钢厂基本采用“三位一体”或“四位一体”短流程工艺,因此,要求电炉必须和精炼炉、连铸机及后部轧机系统协调一致,以保证整条生产线的连续性,实现多炉连浇。
所以电炉的冶炼时间一般缩短在1小时左右,电炉的生产能力可得到极大的提高从而获得最佳的经济规模,取得最大的经济效益。
提高变压器的功率水平,采用废钢预热、喷吹碳-氧进行强化冶炼及双炉壳电炉技术都有利于缩短冶炼时间,提高电炉的生产能力。
(3)减少和控制电炉生产对环境的影响电炉生产对环境的影响主要集中在以下三个方面:烟气及有毒气体对空气的污染;电炉的噪音危害;电炉冶炼对电网冲击造成的闪烁。
Consteel电炉和竖式电炉由于废钢预热的温度比较高,一般在600~700℃,废气中的有害气体基本上可以得到较完全地燃烧而不裂解为有害气体污染周围环境。
直流电弧炉要求的电网容量一般为变压器容量的40倍,小于传统交流电弧炉80倍的要求,因此在同样电炉容量情况下,直流炉的“闪烁”值仅为交流炉的45~50%。
此外,直流炉电弧稳定,噪音也比交流炉低15~20dB.高阻抗电弧炉由于串入电抗器,减少了电流波动,减轻了闪烁和谐波对电网的干扰。
炼钢用电弧炉主要技术参数
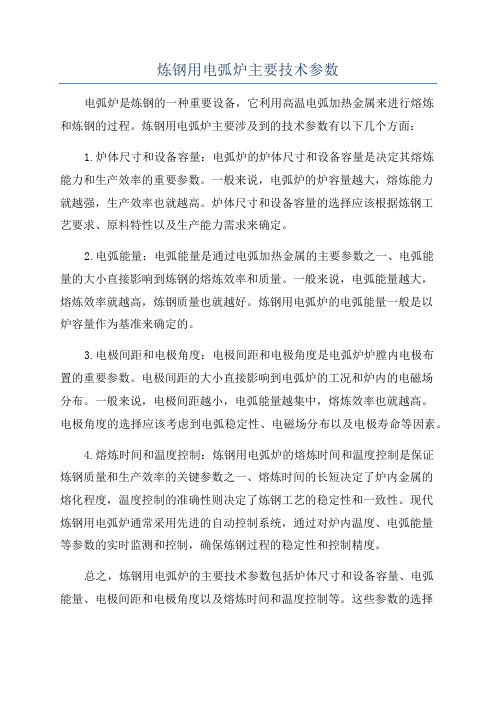
炼钢用电弧炉主要技术参数电弧炉是炼钢的一种重要设备,它利用高温电弧加热金属来进行熔炼和炼钢的过程。
炼钢用电弧炉主要涉及到的技术参数有以下几个方面:1.炉体尺寸和设备容量:电弧炉的炉体尺寸和设备容量是决定其熔炼能力和生产效率的重要参数。
一般来说,电弧炉的炉容量越大,熔炼能力就越强,生产效率也就越高。
炉体尺寸和设备容量的选择应该根据炼钢工艺要求、原料特性以及生产能力需求来确定。
2.电弧能量:电弧能量是通过电弧加热金属的主要参数之一、电弧能量的大小直接影响到炼钢的熔炼效率和质量。
一般来说,电弧能量越大,熔炼效率就越高,炼钢质量也就越好。
炼钢用电弧炉的电弧能量一般是以炉容量作为基准来确定的。
3.电极间距和电极角度:电极间距和电极角度是电弧炉炉膛内电极布置的重要参数。
电极间距的大小直接影响到电弧炉的工况和炉内的电磁场分布。
一般来说,电极间距越小,电弧能量越集中,熔炼效率也就越高。
电极角度的选择应该考虑到电弧稳定性、电磁场分布以及电极寿命等因素。
4.熔炼时间和温度控制:炼钢用电弧炉的熔炼时间和温度控制是保证炼钢质量和生产效率的关键参数之一、熔炼时间的长短决定了炉内金属的熔化程度,温度控制的准确性则决定了炼钢工艺的稳定性和一致性。
现代炼钢用电弧炉通常采用先进的自动控制系统,通过对炉内温度、电弧能量等参数的实时监测和控制,确保炼钢过程的稳定性和控制精度。
总之,炼钢用电弧炉的主要技术参数包括炉体尺寸和设备容量、电弧能量、电极间距和电极角度以及熔炼时间和温度控制等。
这些参数的选择和控制对于炼钢工艺的效果和产能都有重要影响,因此必须经过精心的设计和调整,以满足生产的要求和提高炼钢效率。
现代化电炉炼钢工艺
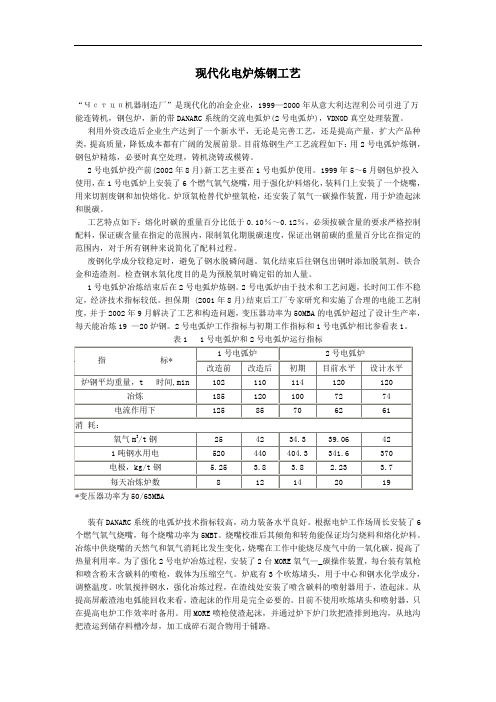
现代化电炉炼钢工艺“Чстцп机器制造厂”是现代化的冶金企业,1999—2000年从意大利达涅利公司引进了万能连铸机,钢包炉,新的带DANARC系统的交流电弧炉(2号电弧炉),VDNOD真空处理装置。
利用外资改造后企业生产达到了一个新水平,无论是完善工艺,还是提高产量,扩大产品种类,提高质量,降低成本都有广阔的发展前景。
目前炼钢生产工艺流程如下:用2号电弧炉炼钢,钢包炉精炼,必要时真空处理,铸机浇铸或模铸。
2号电弧炉投产前(2002年8月)新工艺主要在1号电弧炉使用。
1999年5~6月钢包炉投入使用,在1号电弧炉上安装了6个燃气氧气烧嘴,用于强化炉料熔化,装料门上安装了一个烧嘴,用来切割废钢和加快熔化。
炉顶氧枪替代炉壁氧枪,还安装了氧气一碳操作装置,用于炉渣起沫和脱碳。
工艺特点如下:熔化时碳的重量百分比低于0.10%~0.12%,必须按碳含量的要求严格控制配料,保证碳含量在指定的范围内,限制氧化期脱碳速度,保证出钢前碳的重量百分比在指定的范围内,对于所有钢种来说简化了配料过程。
废钢化学成分较稳定时,避免了钢水脱磷问题。
氧化结束后往钢包出钢时添加脱氧剂、铁合金和造渣剂。
检查钢水氧化度目的是为预脱氧时确定铝的加人量。
1号电弧炉冶炼结束后在2号电弧炉炼钢。
2号电弧炉由于技术和工艺问题,长时间工作不稳定,经济技术指标较低。
担保期 (2001年8月)结束后工厂专家研究和实施了合理的电能工艺制度,并于2002年9月解决了工艺和构造问题,变压器功率为50MBA的电弧炉超过了设计生产率,每天能冶炼19 —20炉钢。
2号电弧炉工作指标与初期工作指标和1号电弧炉相比参看表1。
表1 1号电弧炉和2号电弧炉运行指标*变压器功率为50/63MBA装有DANARC系统的电弧炉技术指标较高,动力装备水平良好。
根据电炉工作场周长安装了6个燃气氧气烧嘴,每个烧嘴功率为5MBT。
烧嘴校准后其倾角和转角能保证均匀烧料和熔化炉料。
冶炼中供烧嘴的天然气和氧气消耗比发生变化,烧嘴在工作中能烧尽废气中的一氧化碳,提高了热量利用率。
电炉炼钢设计(物料平衡+热平衡)
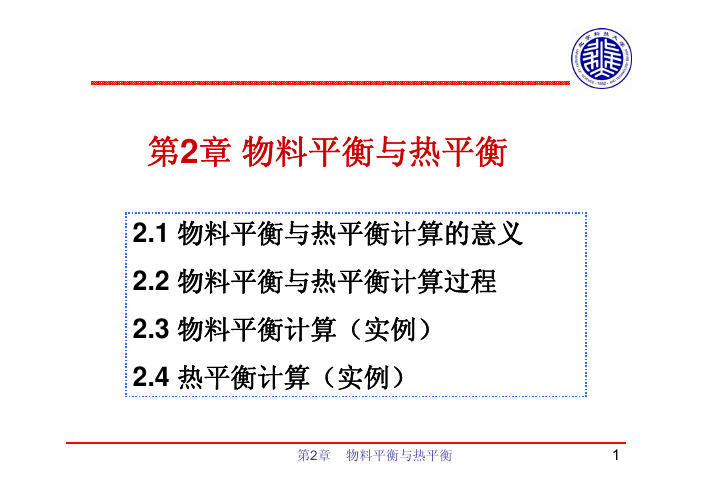
炼钢过程的物料平衡与热平衡计算是建立在物质
生铁
锰铁硅铁
物料平衡计算前,必须确定冶炼设备和方法以及炉
现代电弧炉冶炼工艺与传统三段式有较大的变化
火砖块是浇铸系统的废弃品,它的
配碳比钢种规格中线高0.70%,焦炭的收得率按75%计(7-28)
熔化期脱碳量30%,
CO:CO2=7:3,下同
Fe含量见表7-29
余见注释
焦炭中C含量
烧损率为25%
石灰中的S含
量为0.06%
(3)确定炉渣量:炉渣源于炉料中Si、Mn、P、Fe等元素的氧化产物,炉顶和炉衬的蚀损,焦炭和电极中的灰分,以及加入的各种溶剂。
结果见表7-32.
(4)确定金属量:金属量Qi=金属炉料重+矿石带入的铁量-炉料中C、Si、Mn、P和Fe的烧损量+焦炭配入得碳量
炉顶、炉衬消耗
量见表7-28
烧损的Fe,其中20%进入渣中,其中75%为Fe2O3,25%为FeO
引起氧化期物料波动的因素有:扒除熔化渣,造新渣;金属中
还原期采用白渣操作,引起该期物料变化的因素有:。
电炉炼钢工艺流程图

电炉炼钢工艺流程图电炉炼钢是一种通过电力加热原料来进行钢铁冶炼的工艺,其工艺流程图如下:1. 原料准备阶段。
在电炉炼钢的工艺流程中,首先需要进行原料的准备工作。
通常情况下,原料主要包括废钢、铁合金、脱氧剂等。
这些原料需要经过分类、清洁、切割等处理,以确保其符合炼钢工艺的要求。
2. 上料阶段。
在原料准备完成后,需要将原料通过吊车或其他设备,装入电炉的炉膛中。
在上料的过程中,需要注意原料的均匀分布和合理堆放,以确保炉料的均匀加热和炼钢质量的稳定。
3. 加热熔化阶段。
一旦原料装入炉膛后,电炉开始加热炉料,直至原料完全熔化。
在这个阶段,炉料的温度和化学成分会发生变化,需要通过严格的控制和监测,以确保炉料的熔化过程符合炼钢工艺的要求。
4. 合金加入阶段。
在炉料完全熔化后,需要根据炼钢的要求,加入合金来调整炉料的成分和性能。
通常情况下,合金的加入需要根据炼钢工艺流程图中的配料比例和时间节点进行,以确保炉料的成分达到设计要求。
5. 脱氧合金加入阶段。
除了合金外,还需要在炉料熔化后,加入脱氧剂来去除炉料中的氧化物。
脱氧剂的加入需要根据炼钢工艺流程图中的规定进行,以确保炉料中的氧化物得到有效去除,从而提高钢水的质量。
6. 渣化阶段。
在炉料熔化和合金、脱氧剂加入完成后,需要进行渣化处理。
渣化是指将炉料中的渣和杂质通过化学反应和物理分离,从而得到高质量的钢水。
渣化的过程需要根据炼钢工艺流程图中的温度、时间和操作要求进行,以确保渣化效果的最大化。
7. 出钢阶段。
最后,经过炉料加热、合金加入、脱氧、渣化等一系列工艺处理后,可以通过倒钢机将炉料中的钢水倒出,进入连铸机进行连铸成型。
出钢的过程需要根据炼钢工艺流程图中的操作要求进行,以确保钢水的质量和生产的连续性。
总结:电炉炼钢工艺流程图涵盖了原料准备、上料、加热熔化、合金加入、脱氧合金加入、渣化和出钢等多个阶段。
在实际生产中,需要严格按照工艺流程图的要求进行操作,以确保炼钢工艺的稳定性和钢水质量的可控性。
电弧炉炼钢工艺(一)
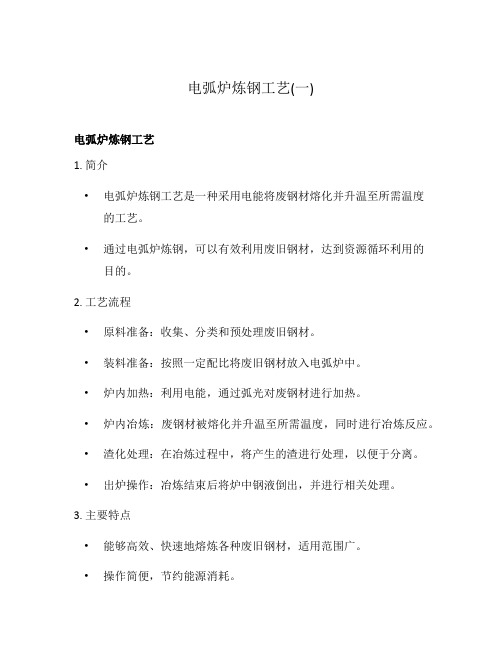
电弧炉炼钢工艺(一)电弧炉炼钢工艺1. 简介•电弧炉炼钢工艺是一种采用电能将废钢材熔化并升温至所需温度的工艺。
•通过电弧炉炼钢,可以有效利用废旧钢材,达到资源循环利用的目的。
2. 工艺流程•原料准备:收集、分类和预处理废旧钢材。
•装料准备:按照一定配比将废旧钢材放入电弧炉中。
•炉内加热:利用电能,通过弧光对废钢材进行加热。
•炉内冶炼:废钢材被熔化并升温至所需温度,同时进行冶炼反应。
•渣化处理:在冶炼过程中,将产生的渣进行处理,以便于分离。
•出炉操作:冶炼结束后将炉中钢液倒出,并进行相关处理。
3. 主要特点•能够高效、快速地熔炼各种废旧钢材,适用范围广。
•操作简便,节约能源消耗。
•可以在较小的空间内进行工艺操作,节约厂房占地面积。
•炉温、炉内状况等参数可实时监测和调节,提高生产效率。
4. 应用领域•电弧炉炼钢广泛应用于废旧钢铁回收、再利用领域,有助于环境保护和资源循环利用。
•适用于生产各种类型的钢材,如不锈钢、合金钢等。
•在建筑、交通、机械制造等行业均有广泛应用。
5. 优势与展望•电弧炉炼钢工艺具有高效、环保、节能等优势,可以有效降低钢铁工业的排放和资源消耗。
•随着技术的不断创新和进步,电弧炉炼钢工艺的效率和质量将进一步提高。
•未来,电弧炉炼钢有望成为钢铁行业的主流工艺,推动钢铁工业的可持续发展。
以上是关于电弧炉炼钢工艺的文章,希望能够为读者提供一些基本了解。
电弧炉炼钢作为一种先进的工艺,将在钢铁行业中发挥重要作用,并为环境保护和资源利用做出贡献。
6. 工艺优化与改进•随着技术的进步和工艺的优化,电弧炉炼钢工艺也不断改进,以提高生产效率和产品质量。
•优化电弧炉设计,增加炉体容积,提高炉内钢液的搅拌效果,减少炉温不均匀性。
•利用先进的电控系统,实现对炉温、电流、电压等参数进行精确调控,减少能源浪费。
•引入氧气供给系统,增加氧气的注入量,提高钢液的燃烧效率,减少废气排放。
•改进废钢材的预处理工艺,提高炉内的装料质量,减少杂质对钢质的影响。
2电弧炉炉型设计

2电弧炉炉型设计2.1电弧炉炉型设计电弧炉是电路炼钢车间的核心设备,电炉设计的好坏直接影响到炼钢生产的顺利与否。
如果设计不合理造成先天性缺陷,一旦投产就很难再做改动,所以对于电炉设计应予以重视。
2.1.1电弧炉炉型电弧炉炉型是指炉子内部空间的形状和尺寸,不同的熔炼炉因工作条件不同,供热热源不同而有不同的内部空间。
电弧炉近于球形体,从减少散热面出发,以球形为最好。
现代电弧炉炉体中部是圆筒形,炉底为弧形,炉顶为拱形。
作为发热体,电极端部的三电弧位于炉内中心部位。
电弧炉设计应保证高的生产率,电能、耐火材料、电极等消耗要低,同时要满足冶金反应顺利进行,故应考虑以下因素:(1)选用大功率变压器;(2)保证高的热效率和电流效率;(3)采用高质量的耐火材料砌筑材料;(4)炉子各部分形状和尺寸设计布局合理;(5)炉子熔炼室容积能一次装入堆比量中等的全部炉料;(6)炉子倾斜10°~20°能保证钢液顺利流出。
2.1.2熔池的形状和尺寸电弧炉的大小以其额定容量来表示,所谓额定容量是指新设计的电炉熔池所能容纳的钢水量。
实际生产过程中,随着熔炼炉数的增多,熔池容积逐渐增大,装入量或者出钢量也就不断增加。
另外生产中还经常用提高炉门槛即造假炉门槛的办法来增加炉产量,这样就出现了超装问题,一般认为吵装20%50%为宜,不宜超装太多,大电弧炉基本上都不超装。
熔池:容纳钢液和熔渣的那部分容积。
熔池的容积应能足够容纳适宜熔炼的钢液和熔渣,并留有余地。
(1)池的形状其形状应有利于冶炼反应的顺利进行,砌筑容易,修补方便。
目前使用的多为锥球型熔池,上部分为倒置的截锥,下部分为球冠。
球冠形电炉炉底使得熔化了的钢液能积蓄在熔池底部,迅速形成金属熔池,加快炉料的熔化并及早造渣去磷。
截锥形电炉炉破便于补炉,炉坡倾角45°,其优点如下○145°角叫自然锥角,砂子等松散材料成堆后的自然锥角正好也是45°(2)熔池尺寸计算○1熔池容积V池。
26 首钢贵阳特殊钢公司电炉炼钢工程工艺设计

首钢贵阳特殊钢公司电炉炼钢工程工艺设计武国平宋宇(北京首钢国际工程技术有限公司, 北京,100043)摘要本文介绍了首钢贵阳特殊钢公司电炉炼钢厂的工艺流程和设备配置,分析了各电炉厂的布置形式,阐述了同跨布置和多跨并列布置各自的优缺点,并简要介绍了首钢贵阳特殊钢公司电炉炼钢工程工艺设计的特点。
立式连铸机、透气砖拆除机构、连铸机整体除尘等设备均为国内首例,粉尘排放指标低于20mg/ Nm3,各项工序能耗指标均低于国家标准。
关键词电炉工艺设计先进设备Process Design of EAF Project of Shougang Guiyang Special SteelCompanyWu Guoping, Song Yu(Beijing shougang international engineering technology co.ltd, beijing, 100043)Abstract An introduce of the process flow and equipments of shougang guiyang special steel company EAF plant is made out in this paper. Besides, the layout forms of several EAF plants are analyzed. The effects and defects of single span layout and appositional multi-span layout are illuminated. The characteristics of the process design of the shougang guiyang special steel company EAF project are given out briefly as also. The equipments, such as vertical CCM and vent brick removal machine, are the domestic first cases. Dust emission index is lower than 20mg/ Nm3. In the meanwhile, power consumption index of working procedures are under the level of national standards.Key Words EAF Process Design Advanced Equipments前言首钢贵阳特殊钢有限责任公司(简称贵钢),地处贵州省会城市贵阳城市中心。
电弧炉炼钢工艺设备(三)

4 电弧炉炼钢工艺设备4.2.2 电弧炉的电气设备4.2.2.1高压供电部分国家规定对地电压大于500V即为高电压,线电压大于250KV为超高压。
目前我国的高电压等级主要有1000V、6000V、10KV、35KV、110KV、220KV、500KV等,炼钢厂高压供电采用国外电压等级标准,即33KV。
高压供电系统是由若干个高压设备组成的,能够完成某种供电功能的系统。
电弧炉的高压供电系统是一种特色特殊的供电系统,它的特点是低电压、高电流,电弧炉的高压供电系统实际上是为电弧炉冶炼提供一套满足冶炼要求的,可以调整和控制的可靠的电源。
高压供电系统原理见图4.19。
图4.19 电弧炉高压系统系统简图电弧炉电弧炉高压供电设备主要有以下设备组成:1)来电显示器来电显示器用于直观显示电弧炉上一级变电站(220KV总降压站)33KV高压电送电、停电情况。
当总降33KV高压送电至炼钢厂后,来电显示器发出红色闪烁信号;停电后红色闪烁信号熄灭。
在进线隔离开关断开后,用于初步判断总降至炼钢厂的高压电是否已送电或停电。
2)高压隔离开关高压隔离开关的作用是与真空断路器配合使用,保证停电工作的可靠性。
在线路上某一点检修工作时,在电源侧必须要有明显的断开点,这就是高压隔离开关的主要作用。
另外,隔离开关常用作电压互感器、避雷器、配电所用变压器及计量柜等低负荷设备的通、断开关使用。
隔离开关的特点是没有灭弧装置,严禁通、断大负荷运行的线路,否则将产生剧烈的电弧光,极易烧毁隔离开关,对人身安全和设备安全将会产生相当大的威胁。
3)高压接地开关当高压电气设备停电检修时,高压接地开关作为保证人员人身安全和设备安全的重要接地装置,代替封挂临时接地线。
在高压配电装置中进行电气作业时,为了工作和检修的安全,必须执行停电、验电、装设临时接地线、悬挂标示牌和装设临时遮拦四项安全技术措施,其中装设临时接地线的操作比较繁琐。
当高压隔离开关配有一体式接地开关时,在隔离开关主闸刀未分断前,接地开关绝不允许合闸;而接地开关未打开前,主闸刀也绝不允许合闸。
电弧炉炼钢

精选ppt
6
3.碱性及酸性电弧炉
第1章 电弧炉炼钢
碱性电弧炉
酸性电弧炉
炉衬材料 MgO、CaCO3
SiO2
造渣材料 以石灰为主
以石英砂为主
特点
可有效去除有害杂质 元素P、S等,可冶炼 高级优质钢
无法去除P、S等有害杂 质,造长渣,不易散热, 保温效果好,钢水流动性 好,夹杂为酸性渣,对钢 性能有优良作用。故一般 铸造厂选酸性渣
5.2.2新车间
150t、100t地磅各一套;30t(22000)、50t(32000) EBT高功率电弧炉各1台;40t(9000)、60t(14000)LF (VD)5工位精炼炉各1台,真空机械泵2套;VC铸锭坑6 座,VC罐车2台,天车24台,最大起重200t,天车轨面高 度24m,厂房面积约4.8wm2。检验设备有美国LECO公司 氧氮氢联合分析仪和ThermoARL3400直读光谱仪 。
这几个阶段组成
① 扒补炉:快补落衬
② 装料:大小中料
③ 熔化期:穿井 大电压,小电流;熔化 大电压,大电流;末期 小电压,大电 流加吹氧。
④ 氧化期:操作加矿或吹氧或矿氧结合 目标:终点C满足要求,P低于规格一 半,温度高于出钢温度20℃,任务去气 体夹杂。
⑤ 还原期:任务调成分,S高于规格一半, 温度满足出钢要求,目标去[O]。
精选ppt
24
第2章 电弧炉设备
精选ppt
25
第2章 电弧炉设备
精选ppt
26
1.电弧炉机械设备
第2章 电弧炉设备
1.2电炉炉体 炉体是电弧炉最主要的装置,它用来熔化和进行各
种冶金反应。电弧炉炉体由金属构件和耐火材料砌筑成的 炉衬两部分组成。炉体的金属构件包括炉壳、炉门、出钢 口、炉盖圈和电极密封圈。炉壳是用钢板焊接成的,其上 部有加固圈。大炉子上部往往做双层的,中间同冷却水。 供门供观察炉内情况及扒渣、取样、加料等操作,炉门口 平时用炉门掩盖。炉门一般通水冷却。小型电炉的炉门盖 需人工启闭,大炉子用压缩空气或油压机等启闭。
电炉炼钢开炉方案
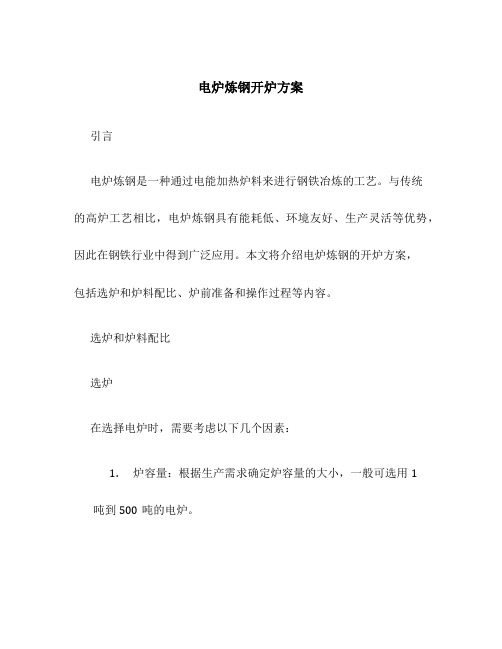
电炉炼钢开炉方案引言电炉炼钢是一种通过电能加热炉料来进行钢铁冶炼的工艺。
与传统的高炉工艺相比,电炉炼钢具有能耗低、环境友好、生产灵活等优势,因此在钢铁行业中得到广泛应用。
本文将介绍电炉炼钢的开炉方案,包括选炉和炉料配比、炉前准备和操作过程等内容。
选炉和炉料配比选炉在选择电炉时,需要考虑以下几个因素:1.炉容量:根据生产需求确定炉容量的大小,一般可选用1吨到500吨的电炉。
2.电炉类型:电炉可以分为直接电弧炉和感应电炉两种。
直接电弧炉适合处理废钢、异型钢材等,而感应电炉适用于生产合金钢、不锈钢等特殊钢种。
3.电炉质量:选择质量可靠、技术成熟的电炉品牌和型号。
炉料配比炉料配比是电炉炼钢过程中的关键步骤,合理的炉料配比可以提高钢水质量、降低生产成本。
常用的炉料包括废钢、生铁、铸块、废钢水、合金等。
在配比过程中,需要考虑以下几个因素:1.主要材料比例:根据所需的钢种和成分要求确定主要材料的比例。
对于低合金钢,一般以废钢为主,添加少量生铁和合金;而对于高合金钢,需要添加较多的生铁和合金。
2.炉料质量:选择质量好、成分稳定的炉料,避免因炉料质量差导致的生产事故和质量问题。
3.炉料粒度:炉料粒度的合适范围有助于提高炉料的利用率。
一般情况下,炉料的粒度应控制在10mm到80mm之间。
炉前准备设备检查在开炉前需要对电炉及相关设备进行检查和维护,确保其正常运行。
主要检查内容包括:1.电炉本体:检查炉体内部和外部的设备是否正常,是否存在结渣或积灰的情况。
2.电源系统:检查电源系统的稳定性和供电情况。
3.水冷系统:检查水冷系统的管路是否畅通,防止因冷却不良而导致设备损坏。
炉衬修复炉衬是电炉内部保护炉体的关键部分,需要定期进行修复。
开炉前需要检查炉衬的状态,如有损坏或磨损情况,需要进行修复或更换。
炉底清理炉底的清理工作是确保炉内工作环境良好的关键步骤。
在开炉前,需要清理炉底的渣铁和杂质,并确保炉底畅通。
操作过程开炉操作开炉操作是电炉炼钢的起始步骤,包括以下几个过程:1.加料:根据炉料配比,按照一定顺序将主要材料、辅助材料和合金料加入电炉中。
转炉炉型设计计算
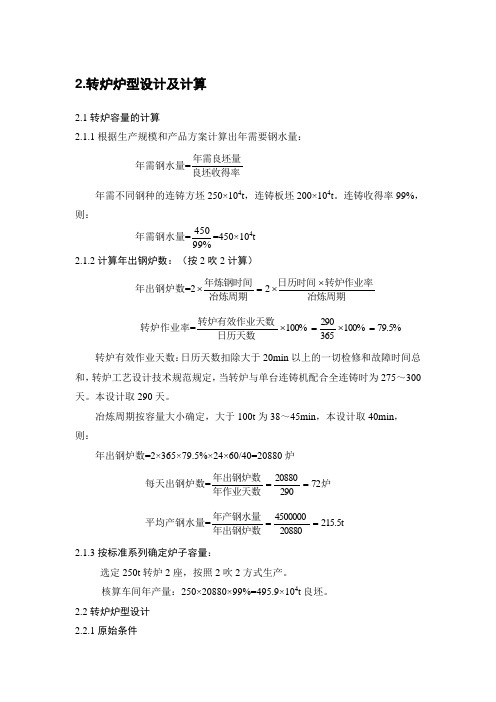
2.转炉炉型设计及计算2.1转炉容量的计算2.1.1根据生产规模和产品方案计算出年需要钢水量:年需钢水量=良坯收得率年需良坯量年需不同钢种的连铸方坯250×104t ,连铸板坯200×104t 。
连铸收得率99%,则:年需钢水量=99%450=450×104t 2.1.2计算年出钢炉数:(按2吹2计算) 年出钢炉数=2冶炼周期转炉作业率日历时间冶炼周期年炼钢时间⨯⨯=⨯2转炉作业率=79.5%100%365290100%=⨯=⨯日历天数转炉有效作业天数转炉有效作业天数:日历天数扣除大于20min 以上的一切检修和故障时间总和,转炉工艺设计技术规范规定,当转炉与单台连铸机配合全连铸时为275~300天。
本设计取290天。
冶炼周期按容量大小确定,大于100t 为38~45min ,本设计取40min , 则:年出钢炉数=2×365×79.5%×24×60/40=20880炉每天出钢炉数=炉年作业天数年出钢炉数7229020880==平均产钢水量=215.5t 208804500000==年出钢炉数年产钢水量2.1.3按标准系列确定炉子容量:选定250t 转炉2座,按照2吹2方式生产。
核算车间年产量:250×20880×99%=495.9×104t 良坯。
2.2转炉炉型设计 2.2.1原始条件炉子平均出钢量为250t ,铁水密度6.8g/cm 3,铁水收得率为92%。
2.2.2炉型选择顶底复吹转炉的炉型基本上与顶吹和底吹转炉相似;它介于顶吹转炉和底吹转炉之间。
为了满足顶底复吹的要求炉型趋于矮胖型,由于在炉底上设置底吹喷嘴,炉底为平底,所以根据原始数据,为了便于设置底部供气构件,选择截锥形炉型。
2.2.3炉容比炉容比指转炉有效容积V t 与公称容量T 之比值V t /T(m 3/t)。
V t 系炉帽、炉身和熔池三个内腔容积之和。
碱性电弧炉炼钢工艺流程

碱性电弧炉炼钢工艺流程碱性电弧炉炼钢工艺流程碱性电弧炉氧化法炼钢工艺过程主要包括原材料准备、补炉、配料及装料、熔化期、氧化期、还原期及出钢等7个阶段。
一、原材料准备废钢是电弧炉炼钢的主要材料,废钢质量的好坏直接影响钢冶的质量、成本和生产率,因此,对废钢质量有如下几点要求。
1)废钢表面应清洁少锈,因废钢中沾有的泥沙等杂物会降低炉料的导电性能,延长熔化时间,还会影响氧化期去鳞效果及侵蚀炉衬。
废钢锈蚀严重或沾有油污时还会降低钢和合金元素的收得率,并增加钢中的含氢量。
2)废钢中不得混有铅、锡、砷、锌和铜等有色金属。
铅的密度大,熔点低,不溶于钢液,易沉积在炉底缝隙中造成漏钢事故;锡、砷和铜易引起钢的热脆。
3)废钢中不得混有密封容器,以及易燃、易爆物和有毒物,以保证安全生产。
4)废钢化学成分应明确,且需按成分分类存放,硫、磷含量不宜过高。
5)废钢外形尺寸不能过大(截面积不宜超过300mm×300mm,最大长度不宜超过350mm)。
二、补炉一般情况下,每炼完一炉钢后,在装料前要进行补炉,其目的是修补炉底和被侵蚀的渣线及被破坏的部位,以维持正常的炉体形状,从而保证冶炼的正常进行和安全生产,补炉的要点如下:1)出钢后立即检查炉衬,需填补炉底时,应先将炉底残渣全部扒出,然后进行填补。
补炉的原则是高温、快补、薄补,维护炉膛原状。
2)补炉料要提前半个小时混合均匀,补炉后放下电极烘烤30min,若补镁砂量较大,应酌情延长烘烤时间。
三、配料及装料配料是电炉炼钢工艺中不可缺少的组成部分,配料是否合理关系到炼钢工能否按照工艺要求正常地进行冶炼操作。
合理的配料能缩短冶炼时间。
配料时应注意以下几点:一是必须正确地进行配料计算和准确地称量炉料装入量;二是炉料的大小要按比例搭配,以达到好装、快速熔化的目的;三是各类炉料应根据钢液的质量要求和冶炼方法搭配使用;四是配料成分必须符合工艺要求。
装料前应先在炉底铺上一层石灰,其重量约为炉料重量的2,,以便提前造好熔化渣,有利于早期去磷,减少钢液吸气和加速升温。
- 1、下载文档前请自行甄别文档内容的完整性,平台不提供额外的编辑、内容补充、找答案等附加服务。
- 2、"仅部分预览"的文档,不可在线预览部分如存在完整性等问题,可反馈申请退款(可完整预览的文档不适用该条件!)。
- 3、如文档侵犯您的权益,请联系客服反馈,我们会尽快为您处理(人工客服工作时间:9:00-18:30)。
电炉炼钢工艺计算及炉型设计
70吨超高功率直流电弧炉
**科技大学
材料与冶金学院
2011级冶金2班
**
*******
目录
一、物料平衡计算
1、计算所需原始数据
2、物料平衡基本项目
3、计算步骤
熔化期计算
氧化期计算
还原期计算
二、热平衡计算
1、计算热收入Qs
2、计算热支出Qz
三、电炉炉型计算
1、电炉基本炉型
2、偏心底出钢电炉
四、参考文献
一、物料平衡计算
1、计算所需原始数据
基本原始数据有:冶炼钢种及其成分;其他数据;原材料成分;合金元素回收率;炉料中元素烧损率。
表一、冶炼钢种及其成分
钢种
成分/%
备注
C
Si
Mn
P
S
Cr
Fe
GCr15
0.95~1.05/1.00
0.15~0.35/0.25
0.25~0.45/0.35
≤0.025
≤0.025
1.40~1.65/1.53
余量
氧化法冶炼
表二、其他数据
名称
参数
配碳量
熔化期脱碳量
电极消耗量
炉顶高铝砖消耗量
炉衬镁砖消耗量
熔化期和氧化期所需要氧量
氧气纯度和利用率
焦炭中碳的回收率
碳氧化产物
烟尘量
比钢种规格中限高0.70%,即达1.70%
30%,即1.70%×30%=0.51kg
4-6kg/t(金属料):熔化期60%;氧化期和还原期各20%
1.5kg/t(金属料):熔化期50%;氧化期35%;还原期15%
4.5kg/t(金属料):熔化期40%;氧化期和还原期30%
50%来自氧气,其余来自空气和矿石
氧气纯度98.5%,氮气1.5%,;利用率90%
焦炭中碳的回收率75%
按70%生成CO,有30%生成CO2
按7-8kg/t(金属料)
表三、原材料成分
名称
C
Si
Mn
P
S
Al
Fe
H2O
灰分
挥发分
碳素废钢炼钢生铁FeMn FeSi SiMn FeCr
Al
焦炭
电极
0.18 3.50 6.60
1.65 4.35
81.95 99.00
0.25 0.40
73.00 20.50 0.40
0.55 0.40 67.80 0.50 63.20
0.030 0.080 0.230 0.050 0.065 0.035
0.030 0.030 0.130 0.030 0.045 0.045
67.30
2.50 98.50
余量余量24.74 23.92 14.54 27.87 1.50
0.58
12.40 1.00
5.52
名称CaO SiO2 MgO Al2O3 CaF2 Fe2O3 FeO
H20
P2O5
S
P
石灰
萤石
铁矿石火砖块高铝砖镁砂
焦炭灰分电极灰分
90.00
1.00 0.55
3.80
4.50 3.70 9.10
2.50 0.80 5.00 60.80 4.00
3.80 49.00 57.40
1.30 0.60 0.50 0.60 0.10 89.70 1.00 0.10
1.30 3.50 1.00 36.80 91.30 0.50 28.10 33.3.
92.31
62.00 1.25
0.80
1.50 18.00
30.50 2.20
0.20 0.10
0.10 0.055
0.535
表四、合金元素回收率
合金材料
加入时间
回收率/%
C
Si
Mn
Cr
Al
FeMn
FeSi
FeCr
Al
Fe-Si粉
Al粉
还原初期
出钢前
还原初期
还原后期
还原初期
还原初期预脱氧还原后期终脱氧还原期扩散脱氧还原期扩散脱氧
100
100
100
100
100
65
95
100
50
96
98
100
100
100
96
60
40
表五、炉料中元素烧损率
成分
C
Si
Mn
P
S
烧损率/% 熔化期
25~40,取30
70~95,取85
60~70,取65
40~50,取45
可以忽略氧化期0.06①
全部烧损
20
0,015②
25~30,取27
1 按末期含量比规格下限低0.03%~0.10%(取0.06%)确定(一般不应低于0.30%的脱碳量);
2 按末期含量0.015%来确定。