φ355.6 8.7-9711.1工艺卡
(完整版)机械加工工艺过程卡片及工序卡片模板
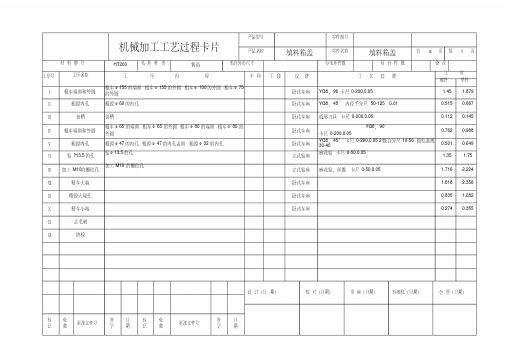
设备名称
卧式车床
夹具编号
设备型号
设备编号
夹具名称
三爪卡盘
工位器具编号
工位器具名称
同时加工件数 切削液
工序工时 (分)
准终
单件
工步号 工
Ⅰ Ⅱ Ⅲ Ⅳ
步
内
粗车Φ 155 的端面
粗车Φ 155 的外圆
粗车Φ 100 的外圆
粗车Φ 75 的外圆
主轴转速 切削速度 进给量 切削深度 进给
工步工时
容
工艺装备
进给 次数
工步工时
基本
0.287
辅助
设 计(日 期) 校 对(日期) 审 核(日期) 标准化(日期) 会 签(日期)
标记 处数 更改文件号 签字 日期 标记 更改文件号 签字 日期
标记 处数 更改文件号 签字 日期 标记 更改文件号 签字 日期
会 签(日期)
机械加工工序卡片
产品型号 产品名称
填料箱盖
车间
毛坯种类
零件图号
零件名称 工序号
填料箱盖
共8
工序名称
Ⅱ
粗镗Φ 60 的内孔
毛坯外形尺寸 每毛坯可制件数
页第 2 页 材 料 牌号
每 台 件数
设备名称
卧式车床
夹具编号
设备型号
设备编号
麻花钻 卡尺 0-50,0.05
0.762 0.501 1.35
0.145 0.988 0.649 1.75
立式钻床 麻花钻,丝锥 卡尺 0-50,0.05
1.716 2.224
Ⅷ
精车大端
卧式车床
1.818 2.356
Ⅸ
精镗大端孔
卧式车床
0.835 1.082
工艺卡、工序卡(拨叉)2023
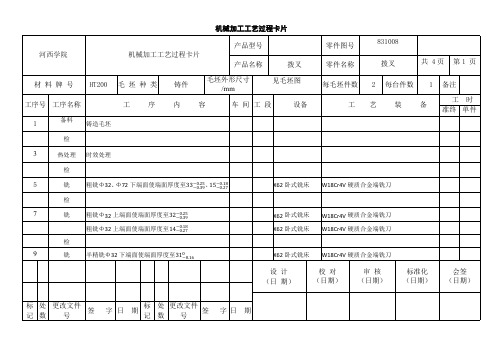
半精镗Φ480+0.16孔至Φ49.70+0.10
精镗Φ49.70+0.10孔至Φ500+0.039
Z550 立式钻床 高速钢麻花钻 Z550 立式钻床 硬质合金扩孔钻 Z550 立式钻床 硬质合金铰刀 Z550 立式钻床 硬质合金铰刀
T68 卧式镗床 T68 卧式镗床 T68 卧式镗床
硬质合金镗刀 硬质合金镗刀 硬质合金镗刀
设计 (日 期)
校对 (日期)
审核 (日期)
标准化
会签
(日期) (日期)
标 处 更改文件
标 处 更改文件
签 字日 期
签 字日 期
记数 号
记数 号
河西学院
机械加工工艺过程卡片(续)
机械加工工艺过程卡片
产品型号 产品名称
拨叉
零件图号 零件名称
831008 拨叉
共 4页 第 3 页
材 料 牌 号 HT200 毛 坯 种 类
mm
机动 辅助
1.7 0.85
1 4.8s 1 5.2s
0.15
1 2s
设计 (日 期)
校对 (日期)
审核 (日期)
标准化 (日期)
会签 (日期)
标 处 更改文件
标 处 更改文件
签 字 日期
签 字日 期
记数 号
记数 号
SB408
高速钢机动丝锥 W18Cr4V
设计 (日 期)
校对 (日期)
审核 (日期)
标准化
会签
(日期) (日期)
标 处 更改文件
标 处 更改文件
签 字日 期
签 字日 期
记数 号
记数 号
河西学院
机械加工工艺过程卡片(续)
机械加工工艺卡

160140工设备段C620-1 YG6640.013外圆面保证尺寸0650.013046.060+倒角武汉纺织大学机械加工工序卡产品名称填料箱盖产品型号零件名称填料箱盖零件图号车间工序号工序名称材料牌号车床车间I 车削端面HT200 毛坯种类毛坯外型尺寸每台件数每件毛坯可制件数铸造件 1 1 设备名称设备型号设备编号同时加工件数卧式车床C620-1 1 夹具编号夹具名称切削液三抓卡盘工位器具编号工位器具名称工序工时准终单件工步号工步内容工艺装备主轴转速切削速度进给量切削深度工时定额机动辅助1 粗车两端面,保证尺寸为137±0.04 YG6外圆车刀150r/min 75.4m/min 0.5mm/r 3mm2 粗车Φ155外圆YG6外圆车刀150r/min 314m/min 0.5mm/r 5mm编制张龙班级机设071 学号0702051008 审核共10 页第1 页武汉纺织大学机械加工工序卡产品名称填料箱盖产品型号零件名称填料箱盖零件图号车间工序号工序名称材料牌号车床车间II 粗车外圆HT200武汉纺织大学机械加工工序卡产品名称填料箱盖产品型号零件名称填料箱盖零件图号车间工序号工序名称材料牌号车床车间III 钻孔HT200 毛坯种类毛坯外型尺寸每台件数每件毛坯可制件数铸造件 1 1 设备名称设备型号设备编号同时加工件数转塔车床365L夹具编号夹具名称切削液专用夹具1 粗车Φ65、Φ80、Φ100/外圆及各倒角YG6外圆车刀230r/min 75.1m/min 0.5mm 17mm2 车槽切槽刀305r/min 152.5m/min 0.25mm/r 4mm编制张龙班级机设071 学号0702051008 审核共10页第2页武汉纺织大学机械加工工序卡产品名称填料箱盖产品型号零件名称填料箱盖零件图号车间工序号工序名称材料牌号钻床车间IV 钻12孔HT200 毛坯种类毛坯外型尺寸每台件数每件毛坯可制件数铸造件 1 1 设备名称设备型号设备编号同时加工件数摇臂钻床Z3025 1 夹具编号夹具名称切削液专用夹具武汉纺织大学机械加工工序卡产品名称填料箱盖产品型号零件名称填料箱盖零件图号车间工序号工序名称材料牌号车床车间V 精车HT200 毛坯种类毛坯外型尺寸每台件数每件毛坯可制件数铸造件 1 1 设备名称设备型号设备编号同时加工件数卧式车床C616 1 夹具编号夹具名称切削液三抓卡盘工位器具编号工位器具名称工序工时准终单件工步号工步内容工艺装备主轴转速切削速度进给量切削深度工时定额机动辅助1 精车外圆Φ65金刚石车刀、卡尺1200r/min 245m/min 0.1mm/r 0.4mm2 精车外圆Φ100金刚石车刀、卡尺1200r/min 376.8m/min 0.35mm/r 0.4mm3 精车外圆Φ80端面金刚石车刀、卡尺1200r/min 301m/min 0.1mm/r 0.4mm编制张龙班级机设071 学号0702051008 审核共10 页第5 页武汉纺织大学机械加工工序卡产品名称填料箱盖产品型号零件名称填料箱盖零件图号车间工序号工序名称材料牌号镗床车间VI 镗孔Φ65 HT200。
(完整版)工艺过程卡和工序卡卡片
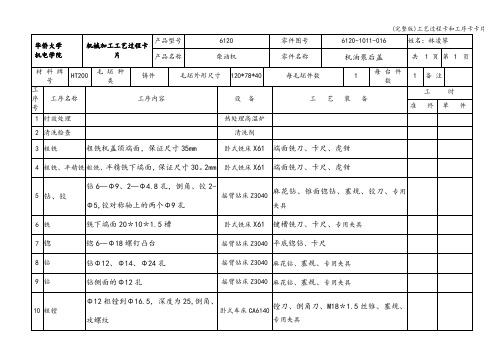
华侨大学机电学院机械加工工序卡片产品型号6120零件图号6120-1011—016姓名:林凌攀产品名称柴油机零件名称机油泵后盖共13页第1页车间工序号工序名称材料牌号粗铣HT200毛坯种类毛坯外形尺寸每毛坯可制件数每台件数铸件120*78*4011设备名称设备型号设备编号同时加工件数卧式铣床X611夹具编号夹具名称切削液虎钳工位器具编号工位器具名称工序工时 (分)准终单件工步号工步内容工艺装备主轴转速切削速度进给量切削深度进给次数工步工时r/min m/s mm/r mm机动辅助1粗铣机盖顶端面,保证尺寸35mm硬质合金端面铣刀、卡尺16011。
65132。
82华侨大学机电学院机械加工工序卡片产品型号6120零件图号6120—1011—016姓名:林凌攀产品名称柴油机零件名称机油泵后盖共13页第2页车间工序号工序名称材料牌号粗铣、半精铣HT200毛坯种类毛坯外形尺寸每毛坯可制件数每台件数铸件120*78*351设备名称设备型号设备编号同时加工件数卧式铣床X611夹具编号夹具名称切削液虎钳工位器具编号工位器具名称工序工时(分)准终单件工步号工步内容工艺装备主轴转速切削速度进给量切削深度进给次数工步工时r/min m/s mm/r mm机动辅助1粗铣下端面,保证尺寸31mm硬质合金端面铣刀、卡尺1601 1.64132。
82华侨大学机电学院机械加工工序卡片产品型号6120零件图号6120-1011-016姓名:林凌攀产品名称柴油机零件名称机油泵后盖共13页第3页车间工序号工序名称材料牌号HT200毛坯种类毛坯外形尺寸每毛坯可制件数每台件数铸件120*78*30。
21设备名称设备型号设备编号同时加工件数摇臂钻床Z30401夹具编号夹具名称切削液专用夹具工位器具编号工位器具名称工序工时 (分)准终单件工步号工步内容工艺装备主轴转速切削速度进给量切削深度进给次数工步工时r/min m/s mm/r mm机动辅助1钻6-Φ9mm孔Φ9高速钢麻花钻、塞规6300.290。
工艺卡、工序卡、检验卡

Word 资料Word 资料机械加工工序卡片机械加工工序卡片产品型号零(部)件图号产品名称输油泵壳体零(部)件名称输油泵壳体共 4 页第 1 页车间工序号工序名称材料牌号35 钻HT200毛坯种类毛坯外形尺寸每毛坯可制件数每台件数精密锻件 1 1设备名称型号同时加工件数钻床Z518 1夹具编号夹具名称切削液000-1 专用夹具工位器具编号工位器具名称工序工时准终单件2.088 2.093工步号工步内容工艺装备主轴转速r/min切削速度m/min进给量mm/r切削深度mm进给次数工步工时(min)机动辅助1 钻φ8孔Z518 1100 26.1 0.3 4 1 0.101 1.87 23Word 资料机械加工工序卡片机械加工工序卡片产品型号零(部)件图号产品名称输油泵壳体零(部)件名称输油泵壳体共 4 页第 2 页车间工序号工序名称材料牌号35 钻HT200毛坯种类毛坯外形尺寸每毛坯可制件数每台件数精密锻件 1 1设备名称型号同时加工件数钻床Z518 1夹具编号夹具名称切削液000-2 专用夹具工位器具编号工位器具名称工序工时准终单件2.088 2.093工步号工步内容工艺装备主轴转速r/min切削速度m/min进给量mm/r切削深度mm进给次数工步工时(min)机动辅助1 钻φ8孔Z518 1100 26.1 0.3 4 1 0.101 1.87Word 资料23机械加工工序卡片机械加工工序卡片产品型号零(部)件图号产品名称输油泵壳体零(部)件名称输油泵壳体共 4 页第 3 页车间工序号工序名称材料牌号35 钻HT200毛坯种类毛坯外形尺寸每毛坯可制件数每台件数精密锻件 1 1设备名称型号同时加工件数钻床Z518 1夹具编号夹具名称切削液000-3 专用夹具工位器具编号工位器具名称工序工时准终单件Word 资料2.088 2.093工步号工步内容工艺装备主轴转速r/min切削速度m/min进给量mm/r切削深度mm进给次数工步工时(min)机动辅助1 钻φ8孔Z518 1100 26.1 0.3 4 1 0.101 1.87 23机械加工工序卡片机械加工工序卡片产品型号零(部)件图号产品名称输油泵壳体零(部)件名称输油泵壳体共 3 页第 1 页车间工序号工序名称材料牌号35 钻HT200毛坯种类毛坯外形尺寸每毛坯可制件数每台件数精密锻件 1 1设备名称型号同时加工件数钻床Z518 1夹具编号夹具名称切削液000-1 专用夹具Word 资料检验工序卡Word 资料Word 资料。
无损检测工艺卡
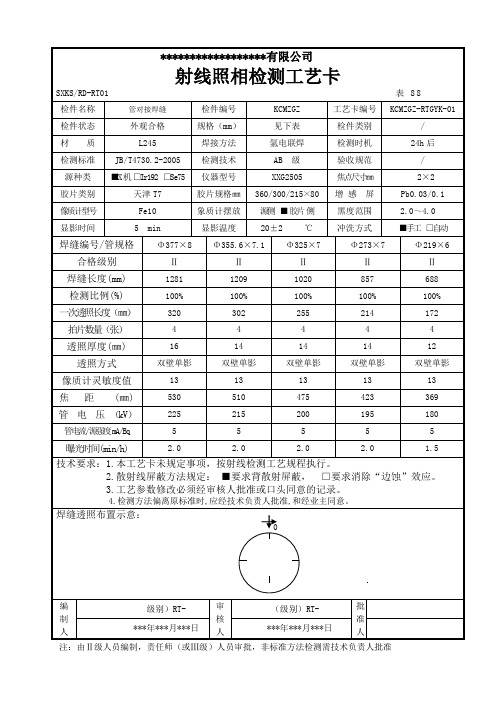
去除
先用不脱毛的布或纸擦拭大部分多余渗透剂去除后,再用喷去除剂的布或纸擦拭,擦拭时应按一个方向进行,不得往复擦拭。
6
干燥
自然干燥5-10min
7
显像
喷涂法施加,喷咀距被检面300~400mm,喷涂方向与被检面夹角约为30~40º,使用前应将喷罐摇动使显像剂均匀。显像时间应>7min。
8
观察
显像剂施加后7~60min内进行观察,受检面的可见光照度应≥1000Lx必要时可用5~10倍放大镜观察。
******************有限公司
射线照相检测工艺卡
SXKS/RD-RT01表88
检件名称
管对接焊缝
检件编号
KCMZGZ
工艺卡编号
KCMZGZ-RTGYK-01
检件状态
外观合格
规格(mm)
见下表
检件类别
/
材 质
L245
焊接方法
氩电联焊
检测时机
24h后
检测标准
JB/T4730.2-2005
检测技术
设备
/
检测标准
SY/T4109-2005
标准试块
镀铬试块
检验标准
/
检测比例
100%
合格级别
渗透检测质量评级要求:
1、不允许存在任何裂纹。
2、不允许任何线性缺陷磁痕。
3、圆形缺陷(评定框尺寸为35㎜×100㎜)d≤1.5,且在评定框内不大于1个。
示意草图:
************有限公司
渗 透 检 测 工 艺 卡(续)
2、安全防护:
a、检测现场应设灭火器,用于防火。
b、罐内检测应有良好的通风。
c、进罐内检测电器,照明用电应Байду номын сангаас用安全电压。
工艺评定编号表

方案编号 HP-01-92-001
记录(报告)编号 HP-01-92-06-001
工艺卡编号 GYK-01-92-001
HP-01-92-002 HP-01-92-06-002 GYK-01-92-002
HP-01-92-003 HP-01-92-06-003 GYK-01-92-003
HP-01-92-004 HP-01-92-06-004 GYK-01-92-004
HP-02-95-001 HP-02-95-002 HP-02-95-003 HP-02-95-004 HP-02-95-005 HP-03-93-001、2 HP-03-93-003、4 HP-03-93-005、6 HP-03-93-007、8 HP-03-93-009、10 HP-03-93-011、12 HP-03-93-013、14 HP-04-93-001 HP-04-93-002 HP-04-93-003 HP-05-92-001 HP-05-92-002 HP-05-92-003 HP-05-92-004 HP-05-92-005 HP-06-92-001、2 HP-06-92-003、4 HP-06-92-005、6
PD-01-001 HP-03-92-001
任务书编号 材质顺序编号 表示评定代号
工序卡新

器械有限公司
机械加工工序卡
产品型号
JQ105-11
零件图号
共页
产品名称
Kim钳
零件名称
第页
车间
工序号
工序名称
材料牌号
线切割车间
01
线切割AB面
毛坯种类
毛坯外形尺寸
每毛坯件数
每台件数
铸件
1
4
设备名称
设备型号
设备编号
同时加工件数
线切割机
夹具编号
夹具名称
切削液
工位器具编号
工位器具名称
工序工时
准终
单件
工步号
工步内容
工艺装备
主轴
转速
(r/min)
切雪
速度
(m/min)
进给
量
(mm/r)
切雪
深度
(mm)
进给次数
Байду номын сангаас工步工时
机动
辅助
1
A面外形加工
2
B面外形加工
设计(日期)
审核(日期)
标准化(日期)
会签(日期)
校对(日期)
标记
处数
更改文件号
签字
日期
标记
更改文件号
签字
日期
P11管道焊接工艺卡

温度测量方式:热电偶
层间温度:≤350℃
后热温度:℃
保温时间:min
热处理温度:670-700℃
保温时间:60min
焊接工艺参数
焊接
层道
焊接方法
焊材牌号
规格(mm)
电流极性
电流
(A)
电压(V)
焊接速度(mm/min)
其他
1
GTAW
CHG55B2
Φ2.5
正接
90~142
10~12
40~50
GTAW
CHH307
Φ2.5
正接
90~142
10~12
40~50
2
SMAW
CHH307
Φ3.2
反接
75~136
21~23
50~70
3及以上
SMAW
CHH307
Φ4。0
反接
84~161
21~23
50~70
表面
SMAW
CHH307
Φ3.2
反接
86~149
21~23
50~70
工艺说明
焊前准备、清理和检查:
焊接工艺评定编号:
焊接方法:GTAW+SMAW
焊接位置:全位置
接头型式:对接
衬垫材料:无
接头型式、坡口和组装尺寸示意图:单位:mm
焊接层道示意图:单位:mm
母材
A侧
B侧
母材材质牌号:
SA-106GrB
A335-P11
母材类别:
AⅠ
BⅠ
母材直径范围(mm):≥109。5
母材厚度范围(mm):9~24
填充材料
Φ3.2
加工工序卡片02精车

机械加工工序卡片15°15°3.26.3QQ3.2A底图号 装订号 描校 描图蚌埠学院机械加工工艺卡片 产品型号 零部件图号产品名称零部件名称轴 共6页第5页车间工序号 工序名 材料牌号 金工车间 1 切屑加工 45 毛坯种类毛坯外 形尺寸 每毛坯可制件数每台件数锻件386⨯92 1 1 设备名称 设备型号 设备编号同时加工件数普通车床C614011 夹具编号夹具名称 切削液 1 通用夹具工位器具编号工位器具名称工序工时准终单件工步号 工步内容工艺装备主轴速度 r/min 切削速度m/min 进给量mm/r 背吃刀量mm 进给次数 工步工时机动 辅助 1 精车外圆面Φ05.004.54+710 222.9 0.15 0.1 1 0.83 2 精车外圆面Φ024.0011.060++ 710 222.9 0.15 0.1 1 0.83 3精车外圆面Φ021.0002.080++ 710 222.9 0.15 0.1 1 0.83 4 精车外圆面Φ024.0011.060++ 710 222.9 0.15 0.1 10.83设 计 (日期) 审核 (日期) 标准化(日期) 会签(日期)标记 处数 更改文 件号 签字 日期 标记 处数 更改文 件号签字 日期机械加工工序卡片底图号 装订号 描校 描图蚌埠学院机械加工工艺卡片产品型号 零部件图号 产品名称零部件名称拨叉 共8页第2页车间工序号 工序名 材料牌号 精加工车间 2 拉键槽 HT200毛坯种类毛坯外 形尺寸 每毛坯可制件数每台件数铸件1 1 设备名称 设备型号设备编号同时加工件数拉床21 夹具编号夹具名称 切削液 2专用夹具工位器具编号工位器具名称工序工时准终单件工步号 工步内容 工艺装备主轴速度 r/min 切削速度m/min 进给量mm/r 背吃刀量mm 进给次数 工步工时 机动 辅助 1 拉六齿方型花键0.06 0.06 1 1 0.13设 计 (日期) 审核 (日期) 标准化(日期) 会签(日期)标记 处数 更改文 件号签字 日期 标记 处数 更改文 件号 签字 日期QQQQQ机械加工工序卡片底图号 装订号 描校 描图蚌埠学院机械加工工艺卡片产品型号 零部件图号 产品名称零部件名称拨叉 共6页第3页车间 工序号 工序名 材料牌号 精加工车间 3 铣面 HT200毛坯种类毛坯外 形尺寸 每毛坯可制件数每台件数铸件 1 1 设备名称 设备型号 设备编号同时加工件数铣床 X62W31 夹具编号夹具名称 切削液 3 专用夹具工位器具编号工位器具名称工序工时准终单件工步号 工步内容 工艺装备主轴速度 r/min 切削速度m/min 进给量mm/r 背吃刀量mm 进给次数 工步工时 机动 辅助 1 粗铣B 面 160 23.7 0.6 3 1 0.525 2 精铣B 面210 33.1 0.512 0.2 1 0.336设 计(日期) 审核 (日期)标准化(日期) 会签(日期)3.2QQB记 数 件号 字 期 记 数 件号 字 期机械加工工序卡片底图号 装订号 描校 描图蚌埠学院机械加工工艺卡片产品型号 零部件图号 产品名称零部件名称拨叉 共6页第4页车间 工序号 工序名 材料牌号 精加工车间4 铣槽 HT200毛坯种类毛坯外 形尺寸 每毛坯可制件数每台件数铸件 1 1 设备名称 设备型号 设备编号同时加工件数铣床 X62w31 夹具编号夹具名称 切削液 4专用夹具工位器具编号工位器具名称工序工时准终单件工步号 工步内容 工艺装备主轴速度 r/min 切削速度m/min 进给量mm/r 背吃刀量mm 进给次数 工步工时 机动 辅助 1 铣800。
T管加工检验工艺卡(范例)

套管加工工艺标准卡
规格
代号1
钢级
扣型
执行标准
配带接箍参数
外径
钢级
接箍长度
Ø139.7×7.72
5-1/2〞17LB/FT
J55
LC
API5CT(9th)、
API 5B(15th)
Ø153.67mm
J55
203.2mm(+0.6mm~+1.6mm)
序号
工序名称
工艺参数
1
管端探伤
项目
探伤类型
探伤级别
探伤位置
探伤方向
参数
手提超声
L2
管端450mm内,内外表面
纵向
2
螺纹检查公差
项目
紧密距
螺距
L4长度
牙型角
参数
±2.5mm
0.125"±0.002"
88.9±3.175mm
60°(±11/2°)
项目
齿高
锥度
最小Lc长度
倒角
参数
0.07125
(-0.002"~+0.004")
0.061~0.066in/in
5
通径
项目
通径位置
通径规直径
通径规长度
参数
接箍拧紧后全长通径
≥121.08mm
≥152mm
6
保护环
项目
保护环品牌及类型
螺纹脂
参数
津英达外钢内塑可吊装保护帽
1、型号:
2、戴保护环前需均匀涂抹,并覆盖裸露丝扣
7
喷标
打印
项目
喷标内容
打印内容
色环
参数
长度MM重量KG TPCOAPI 5CT日期(年季)139.7mm×7.72mmJ S P33.5 LC D炉号批号支号班次号DH
(工艺技术)工艺卡片样本

工艺规范产品名称工序名称设备名称编号共 16 页 AH/TLC70-01 框扇下料工装名称编号第 1 页工序简图技术标准1、下料长度L充差≤2000mm±1mm2、下料角度90°±0.5°3、切割后型材断面应平整光洁,外表面清洁无划伤。
操作要求1、切割前检查设备运转是否正常。
2、装夹注意夹紧力适当,牢固,定位正确,切割过程中防止型材变形。
3、型材搬取,存放过程中防止型材划伤,磕碰,表面质量。
4、首件产品严格检查合格后方可生产。
检验方法1、用钢卷尺检查下料长检测工具1.钢卷尺。
2.角度尺。
不合格品处置度。
2、用角度尺检查下料角度。
3、目测外观质量。
更改记录编制批准日期批准审核日期工艺规范产品名称工序名称设备名称编号共 16 页 AH/TLC70-01 铣排水孔工装名称编号第 2 页工序简图技术标准1、排水孔为Φ5×30槽孔,每根料数量2个。
2、纵向位置允差别±3mm,排列均匀。
3、排水孔表面光洁,无毛刺、铣刀不得损坏型材腹板4、排水孔设在外轨道左侧。
操作要求1、铣料前检查设备运转是否正常。
2、注意排水孔的位置均匀和数量。
3、铣孔时避免划伤型材表面质量。
4、首件产品严格检查,合格后方可生产。
检验方法1、用卡尺测量排水孔尺检测工具1、卡尺。
2、卷尺。
不合格品处置寸。
2、用卷尺测量排水孔位置。
更改记录编制批准日期批准审核日期工艺规范产品名称工序名称设备名称编号共 16 页 AH/TLC70-01 铣边框料工装名称编号第 3 页工序简图技术标准1、边框上方仿型铣深度距离为40mm。
2、边框下方仿型铣深度距离为50mm。
3、仿型铣后,光滑无毛刺,深度距离偏差L±1mm。
4、边框左右铣切距离为68mm,距离偏差L±0.5mm。
操作要求1、工作前检查仿型铣床运转是否正常。
2、检查铣刀型号是否正确。
3、工作时型材轻取轻放,避免划伤型材表面质量。
机械制造工艺学工艺卡

新余学院机械加工工艺过程卡片产品型号零件图号产品名称输出轴零件名称输出轴共页第页材料牌号毛坯种类铸件毛坯外形尺寸250 每毛坯件数每台件数备注工序号工步号工序内容车间工段设备工艺装备工时准终单件05 备料、模锻10 用三爪卡盘定位φ55回转体表面,粗车φ176外圆和粗铣φ176端面X53T立式铣床CA6140卧式车床YT15硬质合金刀,游标卡尺,三爪自定心卡盘15 用三爪卡盘定位φ176回转体表面,粗铣φ55端面和粗车φ55、φ60、φ65、φ75的回转体表面。
X53T立式铣床高速钢镶齿套式端铣刀20 用三爪卡盘定位φ55回转体表面,半精车φ55、φ60、φ65、φ75、φ176的外圆CA6140卧式车床YT15硬质合金刀,游标卡尺,外径千分尺25 用三爪卡盘定位φ55回转体表面,粗磨φ65、φ75的外圆表面磨床棕刚玉平形砂轮外径千分尺30 用三爪卡盘定位φ55回转体表面,粗车、半精车过度锥面CA6140卧式车床YT15硬质合金刀,游标卡尺,外径千分尺35 以轴的回转轴线为基准,粗镗内孔φ50、φ80、φ104 CA6140卧式车床钻头,游标卡尺,塞规40 以轴的回转轴线为基准,半精镗内孔φ50、φ80、φ104CA6140卧式车床钻头,游标卡尺,塞规45 以φ80孔的中心线为基准,钻、扩、铰孔10×φ20CA6140卧式车床钻头,游标卡尺,塞规描图50 钻斜孔2×φ8Z3025摇臂钻床钻头,游标卡尺,塞规55 以轴的回转轴线为基准,粗铣键槽X53T立式铣床高速钢镶齿套式端铣刀描校60 热处理:调质处理硬度为200-230HBW X53T立式铣床高速钢镶齿套式端铣刀65 精车φ65、φ75的外圆及锥面CA6140卧式车床90º刀,三爪卡盘底图号70 用三爪卡盘定位φ55回转体表面,精磨φ65、φ75的外圆表面磨床棕刚玉平形砂轮外径千分尺75 以轴的回转轴线为基准,精铣键槽,用三爪卡盘定位φ55回转体表面,精铣φ176端面;用三爪卡盘定位φ176回转体表面, 精铣φ55端面。
压力容器制造工艺卡

3 气 切割下料 4 刨 刨削破口。破口形式见右图A、B。 5 铆 卷制成型。 注:对口错边量≤3.0㎜ 6 焊 焊接筒节。SAW 7 铆 筒节校圆。注:棱角度≤3.4㎜,椭圆度≤22㎜
8
探
按JB/T4730.2-2005RT-AB进行20%射线探伤,Ⅲ 级合格。
组对筒节间的环焊缝,注:对口错变量≤3.5㎜ 9铆
姓名 日期
产品名称
产品图号
材料
20
检验者签字
姓名
日期
工令号 主要材料 下料尺寸
第页 共页 Ф 273*8
简图说明
******公司
法兰工艺卡Ⅰ
件号 h 标准号 HG/T20592-2009 名称 人孔法兰
件号 工种
工作内容及技术要求
1 铆 领料20Ⅱ,确认材质证明书及材料标记
2
车
1)、夹持外圆,车削内孔及端面。 2)、夹持端部,车削外圆面。
设备制造工艺卡目录
工艺卡名称
产品名称 DN1600*1500压缩空气储气罐 工令号
产品图号 KD2011-Y63-01 主要材料
Q345R
页数
简图说明
第页 共页
签名栏
编制 审核
日期 日期
******公司
封头工艺卡Ⅰ
件号 4 标准号 GB/T25198-2010 名称 椭圆封头
件号 工种
工作内容及技术要求
10 铆 划端面切割线。
1)、封头深度公差为-4.4㎜/+13.2㎜
2)、圆度公差≤11.0㎜
11 检 3)、直边高度允差-2.0㎜/+4㎜
4)、间隙外凸≤27.5㎜,内凹≤13.7㎜
6)、最小壁厚≥12㎜
产品名称 DN1600*1500压缩空气储气罐 工令号
工艺卡片(范例)

磨平面
平面磨床
磨上下平面,留磨削余量0.3~0.4mm,磨相邻两侧面保证垂直
5
钳工划线
高度游标卡尺
划出对称中心线,固定孔及销孔线
6
孔加工
钻床
加工固定孔及销孔
7
热处理
淬火,回火,按热处理工艺保证58~62HRC
8
磨平面
平面磨床
磨上下平面级基准面达要求
9
型孔精加工
坐标磨床
在坐标磨床上磨型孔,留研磨余量0.01mm
10
研磨型孔
平面磨床
钳工研磨型孔达技术要求
11
检验
7
热处理
淬火、回火28~32HRC
8
平磨
磨床
磨上下平面及基准ቤተ መጻሕፍቲ ባይዱ达要求
9
线切割
电火花线切割机
找正,切割各型孔留研磨量0.01~0.02mm
10
研磨
平面磨床
磨上下两端面,保证孔壁与上下端面的垂直度达要求尺寸
11
检验
附三:卸料板加工工艺卡片
工序号
工序名称
设备
工序内容
1
备料
空气锤
将毛坯锻成平行六面体,尺寸为:100mm×100mm×14mm
工序内容
1
下料
空气锤
锻至140mm×100mm×6mm
2
热处理
退火
3
铣平面
立式铣床
铣各平面,厚度留磨削余量0.6mm,侧面留磨削余量0.4mm
4
磨平面
平面磨床
磨上下平面,留磨削余量0.3~0.4mm,磨相邻两侧面保证垂直
5
钳工
老虎钳
倒角去毛刺,划出对称中心线,固定孔及销孔线
工序卡片

机械加工工序卡片机械加工工序卡片产品型号零(部件)图号产品名称活塞零(部件)名称活塞共 12页第 1 页车间工序号工序名材料牌号1 粗车止口铝合金毛坯种类毛坯外形尺寸每毛坯可制件数每台件数模锻件Φ105mmx110mm 1 1设备名称设备型号设备编号同时加工车床C618 1夹具编号夹具名称切削液三爪定心卡盘工位器具编号工位器具名称工序工时/s准终单件105工步号工步内容工艺设备主轴转速/r﹒s-1 切削速度/m﹒s-1进给量/mm﹒r-1走刀长度/mm进给次数工步工时/s机动辅助1 粗车止口,保持尺寸直径φ94.7054.0mm深度10,Ra6.3 长三爪卡盘,YG8车刀,毛止口量规2.0 0.74 0.2 1.7 1 582 倒角0.5x45° 6.33 手动设计(日期)审核(日期)标准化(日期)会签(日期)标记处数更改文件号签字日期标记处数更改文件号签字日期机械加工工序卡片机械加工工序卡片产品型号零(部件)图号产品名称活塞零(部件)名称活塞共 12页第 2 页车间工序号工序名材料牌号2 粗镗销孔铝合金毛坯种类毛坯外形尺寸每毛坯可制件数每台件数模锻件Φ105mmx110mm 1 1设备名称设备型号设备编号同时加工车床 1夹具编号夹具名称切削液三爪定心卡盘工位器具编号工位器具名称工序工时/s准终单件168工步号工步内容工艺设备主轴转速/r﹒s-1 切削速度/m﹒s-1进给量/mm﹒r-1走刀长度/mm进给次数工步工时/s机动辅助1 镗孔φ27005.0mmYG8专用镗刀,毛销孔量规,压紧工具,止口座12.7 2.67 0.1 1 1 32设计(日期)审核(日期)标准化(日期)会签(日期)标记处数更改文件号签字日期标记处数更改文件号签字日期机械加工工序卡片机械加工工序卡片产品型号零(部件)图号产品名称活塞零(部件)名称活塞共 12页第 3 页车间工序号工序名材料牌号3 粗车外圆顶面、环槽铝合金毛坯种类毛坯外形尺寸每毛坯可制件数每台件数模锻件Φ105mmx110mm 1 1设备名称设备型号设备编号同时加工多刀半自动车床C720 1夹具编号夹具名称切削液三爪定心卡盘工位器具编号工位器具名称工序工时/s准终单件86工步号工步内容工艺设备主轴转速/r﹒s-1 切削速度/m﹒s-1进给量/mm﹒r-1走刀长度/mm进给次数工步工时/s机动辅助1 车外圆φ102.4±0.05mm,保持尺寸107±0.05YG毛环槽切刀,环槽到止口端面距离卡规,环槽刀夹2.0 0.69 0.52 1.7 1 252 车外圆φ101.68±0.05mm,保持尺寸29.63±0.05 2.0 0.69 0.52 1.7 1 163 车沟槽在77.37±0.05处,保证宽度4.0±0.03,下刀深度保持直径φ91.8±0.0250.5 0.17 手动 14 分别车三槽,保证三槽宽2.2±0.03,三环岸宽3.8±0.03,下刀深度保持直径φ92.8±0.0250.5 0.17 手动 3设计(日期)审核(日期)标准化(日期)会签(日期)标记处数更改文件号签字日期标记处数更改文件号签字日期机械加工工序卡片机械加工工序卡片产品型号零(部件)图号产品名称活塞零(部件)名称活塞共12页第 4页车间工序号工序名材料牌号4 铣直横槽铝合金毛坯种类毛坯外形尺寸每毛坯可制件数每台件数模锻件Φ105mmx110mm 1 1设备名称设备型号设备编号同时加工铣槽机 1夹具编号夹具名称切削液铣槽专用夹具工位器具编号工位器具名称工序工时/s准终单件105工步号工步内容工艺设备主轴转速/r﹒s-1 切削速度/m﹒s-1进给量/mm﹒r-1走刀长度/mm进给次数工步工时/s机动辅助1 在于裙部轴心线倾斜1°30´±30´下端至止口端面距离为4.2mm-8.2mm处铣直槽,保证槽宽1.5±0.12mm止口座,拉紧工具,片铣刀φ60x1.5mm,片铣刀φ120-φ135x3mm2.5 0.98 0.032 0.5 4 1382 在外圆φ91.8沟槽处铣横槽,保证宽3±0.12mm,弦长74.6±0.4mm2.5 0.98 0.032 0.5 4 138设计(日期)审核(日期)标准化(日期)会签(日期)标记处数更改文件号签字日期标记处数更改文件号签字日期机械加工工序卡片机械加工工序卡片产品型号零(部件)图号产品名称活塞零(部件)名称活塞共12页第 5页车间工序号工序名材料牌号5 钻油孔铝合金毛坯种类毛坯外形尺寸每毛坯可制件数每台件数模锻件Φ105mmx110mm 1 1设备名称设备型号设备编号同时加工台钻Z12 1夹具编号夹具名称切削液钻油孔夹具工位器具编号工位器具名称工序工时/s准终单件178工步号工步内容工艺设备主轴转速/r﹒s-1 切削速度/m﹒s-1进给量/mm﹒r-1走刀长度/mm进给次数工步工时/s机动辅助1 在8个工位上钻孔φ3.5mm,孔中心必须在环槽中间钻油孔夹具,φ3.5mm钻头18 0.28 手动 2.5 8设计(日期)审核(日期)标准化(日期)会签(日期)标记处数更改文件号签字日期标记处数更改文件号签字日期机械加工工序卡片机械加工工序卡片产品型号零(部件)图号产品名称活塞零(部件)名称活塞共 12页第 6页车间工序号工序名材料牌号6 精车止口,打中心孔铝合金毛坯种类毛坯外形尺寸每毛坯可制件数每台件数模锻件Φ105mmx110mm 1 1设备名称设备型号设备编号同时加工镗孔机床 1夹具编号夹具名称切削液三爪定心卡盘工位器具编号工位器具名称工序工时/s准终单件138工步号工步内容工艺设备主轴转速/r﹒s-1 切削速度/m﹒s-1进给量/mm﹒r-1走刀长度/mm进给次数工步工时/s机动辅助1 精车止口,保持尺寸直径φ95015.0mm,深10,Ra3.2um 车刀,中心钻,光止口塞规,三爪卡盘3.0 0.50 0.05 0.05 1 1052 倒角倒角2x45°,Ra,1.60um 6.33 手动3 钻中心孔φ2.5mm-φ3mm,深度不大于4.8mm 18 0.28 手动 2.5 1设计(日期)审核(日期)标准化(日期)会签(日期)标记处数更改文件号签字日期标记处数更改文件号签字日期机械加工工序卡片机械加工工序卡片产品型号零(部件)图号 产品名称活塞零(部件)名称活塞 共 12页第 7 页车间 工序号 工序名 材料牌号 7 精车环槽 铝合金 毛坯种类 毛坯外形尺寸 每毛坯可制件数每台件数模锻件 Φ105mmx110mm 1 1 设备名称 设备型号 设备编号同时加工车床 C6201 夹具编号夹具名称 切削液三爪定心卡盘工位器具编号工位器具名称工序工时/s 准终 单件168工步号 工步内容工艺设备主轴转速/r ﹒s -1切削速度/m ﹒s -1进给量/mm ﹒r -1走刀长度 /mm进给次数工步工时/s 机动 辅助 1 精车沟槽,保持尺寸4.755060.0035.0++,直径φ910250-。
数控车床加工工序卡
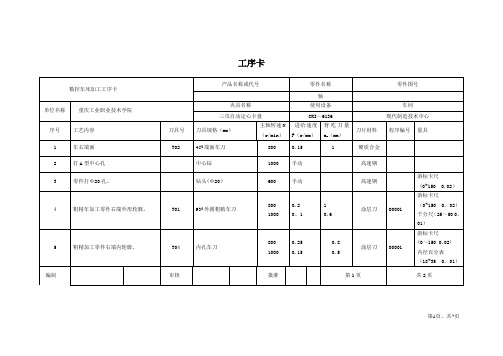
数控车床加工工序卡
产品名称或代号
零件名称
零件图号
轴
单位名称
重庆工业职业技术学院
夹具名称
使用设备
车间
三爪自动定心卡盘
CKI—6136
现代制造技术中心
序号
工艺内容
刀具号
刀具规格(mm)
主轴转速N(r/min)
进给速度F(r/mm)
背吃刀量ap(mm)
刀片材料
程序编号
量具
1
车右端面
T02
450端面车刀
5
粗精加工零件右端内轮廓。
T04
内孔车刀
800
1000
0.25
0.15
0.8
0.5
涂层刀
O0001
游标卡尺
(0~150 0.02)
内径百分表
(18~35 0。01)
编制
审核
批准
第1页
零件名称
零件图号
轴
单位名称
重庆工业职业技术学院
夹具名称
使用设备
车间
三爪自动定心卡盘
千分尺(25~50, 0.01)
8
粗、精车零件左端内轮廓.
T04
内孔车刀
800
1000
0。25
0。15
0.8
0。5
涂层刀
O0004
游标卡尺
(0~150 0。02)
内径百分表
(18~35 0。01)
9
切6xΦ38的内槽
T03
内孔槽刀
600
0.08
0。8
涂层刀
10
去毛刺
11
检验
编制
审核
批准
ASME工艺卡
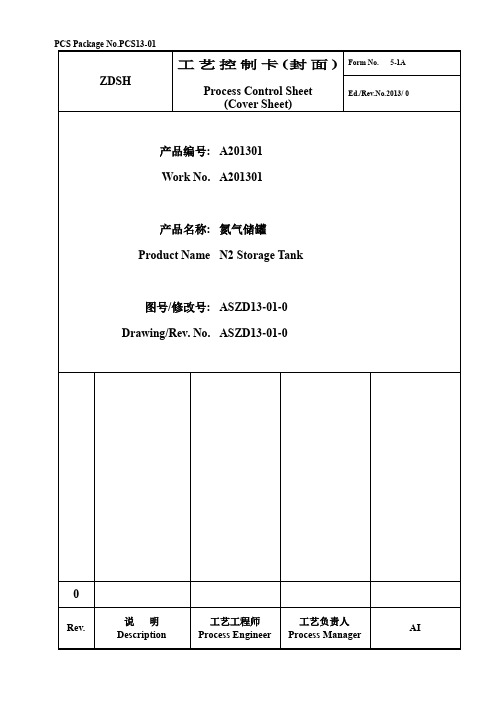
ZDSH/A-CW-4.2
Rev.0
4-4
Examination
检查:尺寸及标记
ZDSH/A-CW-4.5
Rev.0
E
4-5
组对、点焊(C1)
fitting up tack welding
(C1)
按焊接工艺要求组对、点焊N1法兰(件1-1与件2-1)
WPS13-02
签字
Sign
日期
Date
检查点
Examination
Point
签字
Sign
日期
Date
检验点
InspectionPoint
签字
Sign
日期
Date
3-1
入厂检验
Examination
1.MATERIAL INSPECTION
材料审查:材料质量证明书、材料标识
2.VISION INSPECTION
外观检查:法兰外表面不得有划痕、裂纹等影响机械性能的缺陷
控制卡号PCSNo.PCS13-01
ZDSH
工艺控制卡
Process Control Sheet
FormNo. 5-1C
Ed./Rev.No.2013/ 0
页数Page
Page 3 of 38
图号/修改号
Drawing/Rev.No.
ASME B16.5-2009
件号
Part No.
1-2
部件名称
Part Name
零部件名称
Description of Fabrication
1
PCS13-01-1
Rev.0
2
法兰FLANGE
- 1、下载文档前请自行甄别文档内容的完整性,平台不提供额外的编辑、内容补充、找答案等附加服务。
- 2、"仅部分预览"的文档,不可在线预览部分如存在完整性等问题,可反馈申请退款(可完整预览的文档不适用该条件!)。
- 3、如文档侵犯您的权益,请联系客服反馈,我们会尽快为您处理(人工客服工作时间:9:00-18:30)。
X 射线实时成像 同钢级、同规格 6000mm 长管样 焊缝:Ф 3.2 直通孔 无 无 同焊速 焊缝和焊缝两侧母材 30mm 范围 内全长 100%自动探伤 能够检测出 0.4mm 气孔、夹渣等 灵敏度 缺陷。 缺陷尺寸小于 GB/T 9711.1 标准 验收标准 缺欠信号大于合格极限信号均视为缺陷 要求 备注:1)做好相应的记录;2)质量责任人为该岗位的操作者;3)每班次管端位置拍片 1 张,标注日期、规格、班组、管号。
称重、测长
重量:单位为 KG,数据保留小数点后 2 位 长度:单位 mm,数据取整数
按自动称重、测长设备要求 操作。
自动称重、 侧长 1) 定时检测设备精 仪 度。
喷标
在钢管内壁距管端不小于 150mm 处开始, 按下列形 按自动喷标设备要求操 式喷标: 作,严格控制距管端距 凌钢钢管 GB/T 9711.1-1997 355.6mm*8.7mm 离不小于 150mm, 标识要 *12000 Q235B ******(管号) 求清晰,工整。
核对钢带宽度、厚度,检查钢 吊车 带是否有划伤,分层等缺陷。 开卷机 剪切对 焊机
接板
按标准焊接, 焊缝应均匀光滑不得有电弧烧伤且余 高应不大于 1.5mm(不铣坡口),焊缝表面不得有 自动埋弧焊或人工焊 气孔、裂纹、烧穿、断弧、咬边等缺陷。
钢带
钢带宽度为 685mm。 钢带偏差为-1mm~1mm; 钢 按同一炉号顺序剪料, 合格后 带边缘应无毛刺等缺欠(不铣坡口)。钢带表面 圆盘剪 准备投入生产。 不得有明显划伤、压痕、分层等缺欠。
自动喷标仪
1) 由成品检验岗位 人员逐支检查。
备注:1)做好相应的记录 2)质量责任人为该岗位的操作者。
批准
日期
2012-08-08
审核
日期
2012-08-08
编制
刘德重
日期
2012-08-08
注:本工艺卡首页签字后生效。
原料验收工艺卡
编号:LGBPGG-BW-3-2012-8-355.6 规格 355.6*8.7*12000 执行标准 GB/T 9711.1-1997 内容 化学成分最大重量百分比含量要求: C 0.12-0.20 Si max 0.3 Mn 0.30-0.70 P max S max 0.045 V Max Nb max CEV%max 岗位:质检科 材质 Q235B
开卷剪切对焊工艺卡
编号:LGBPGG-BW-3-2012-8-355.6 规格 355.6*8.7*12000 执行标准 内容 工序名称 投料 工艺参数与要点 按同一规格、同一炉号顺序投料 操作要求 设备 控制措施 用校验后的测量尺复验 钢带尺寸;目测检查。 检验每个接头,目测检 验。 GB/T 9711.1-1997 岗位:上料岗位 材质 Q235B
垂直,切割后的钢管两端不应有棱角, 锯切时给平头倒棱留有 10mm 平头倒 棱余量, 不允许存在超过大于 1.59mm
岗位:扩径岗位 材质 Q235B
设备
控制措施
锯 切
等离子切割 锯
用校验后的测量器具检 测。
切斜与错口。
备注:1)做好相应的记录;2)质量责任人为该岗位的操作者。
批准
日期
2012-08-08
钢管应逐根进行静水压试 验,试验压力为 6.9MPa; 静水压试验的稳压时间至少 静水压试验机的鉴定:静水压试验开始前,静水压试验压 力表应用静载试验机校准。以后至少每周校准一次,每次 爆管后也应校准一次; 试验时,钢管表面不能带水操作, 钢管管端喷水不能超过 300mm,否则钢管重新试验; 爆管应视为不合格管; 全焊道进行巡回认真检查,有无缺陷遗漏和渗漏水现象。 检查时每两米用棒敲击一下。 静水压试验机 静水压试验记录应能追 踪到管号和熔炼炉批号, 且有自动记录装置。
备注:1)做好相应的记录 2)质量责任人为该岗位的操作者。
批准
日期
2012-08-08
审核
日期
2012-08-08
编制
刘德重
日期
2012-08-08
注:本工艺卡首页签字后生效。
无损检测工艺卡
编号:LGBPGG-BW-3-2012-8-355.6 规格 工序名称 设备型号 设备校验频 次 探头类型 对比标样 人工缺陷 藕合剂 检测时机 扫查速度 探伤方式及 部位 355.6*8.7*12000 焊缝自动超声波探伤 TBCT(DSP)A 每工作班(4 小时)校验 1 次。 双晶直探头,单晶斜探头 同钢级、同规格 6000mm 长管样 焊缝:Ф 3.2 直通孔 水 水压试验后 同焊速 焊缝和焊缝两侧母材 30mm 范围内全长 100%自动探伤 焊缝 Ф 3.2 直通孔波幅 80%作为探伤灵敏 度;检测灵敏度加 2~3db。 执行标准 GB/T 9711.1-1997 内容 X 射线检测 CMH 每工作班(4 小时)校验 1 次 材质 岗位: 无损检测 Q235B
批准
日期
2012-08-08
审核
日期
2012-08-08
编制
刘德重
日期
2012-08-08
注:本工艺卡首页签字后生效。
成品检验工艺卡
编号:LGBPGG-BW-3-2012-8-355.6 规格 355.6*8.7*12000 GB/T 9711.1-1997 材质 内容 项目 规定要求 管体外径/mm 距管端大于 101.6mm 最小值φ 354.81,中径φ 356.4,最大值φ 357.98 管端外径/mm 距管端 101.6mm 内最最小值φ 354.81,中径φ 356.4,最大值φ 357.98 壁厚/mm 7.62-10.00 11990-12010(为避开带钢接头,可在 11500-12500 之间,但长度必须在 单根长度/mm 管端注明,单独摆放) 坡口角/° 30°- 35° 钝边/mm 0.79-2.39 直度/mm/m max 2 切斜/mm max 1.59 内焊缝/mm 0~3.2 外焊缝/mm 0~3.2 错边/mm max 1.6 钢管上不允许有扩展到管端面或坡口上面且横向尺寸超过 3.0mm 分层和 分层 夹杂 缺欠和缺陷 其它 所有表面深度大于壁厚负偏差 12.5%(1mm)的缺欠均视为缺陷。 表面质量 内外表面应清洁、光滑、无缺陷。 备注:1)做好相应的记录 2)质量责任人为该岗位的操作者。 执行标准 岗位:成品检验岗位 Q235B 检测频次
成 型 机
用校验后的测量器具检测。
批准
日期
2012-08-08
审核
日期
2012-08-08
编制
刘德重
日期
2012-08-08
注:本工艺卡首页签字后生效。
焊接工艺卡
编号 规格 工序名称 内焊 LGBPGG-BW-3-2012-8-355.6 355.6*8.7*12000 执行标准 内容 工艺参数 使用焊丝型号外焊为 ER50-6*4.5mm,内焊为 ER50-6*4.0mm,内焊与外焊均采用 SJ301 焊剂。 焊缝应均匀光滑且余高不大于 3.0mm。焊缝过度角 ≥135°。外焊缝宽度为 12-14mm,内焊缝宽度为 10-12mm。焊缝最大焊偏量为 2.4mm。 车速为 1.7 米/分时,内焊电流 600A-650A,电压 为 28V-30V。外焊缝电流为 700A-730A,电压 30V-34V。车速如有变化可根据车速调整电流与电 压。 焊丝型号外焊为 ER50-6*4.5mm,内焊为 ER50-6*4.0mm,内焊与外焊均采用 SJ301 焊剂,焊 剂循环使用 3 次必须烘干 1 次。 操作要求 设备 控制措施 GB/T 9711.1-1997 材质 岗位:焊接岗位 Q235B
逐根
批准
日期
2012-08-08
审核
日期
2012-08-08
编制
刘德重
日期
2012-08-08
注:本工艺卡首页签字后生效。
称重、测长、喷标工艺卡
编号 规格 工序名称 LGBPGG-BW-3-2012-8-355.6 355.6*8.7*12000 工艺参数 执行标准 内容 操作要求 设备 控制措施 GB/T 9711.1-1997 材质 岗位:焊接岗位 Q235B
审核
日期
2012-08-08
编制
刘德重
日期
2012-08-08
注:本工艺卡首页签字后生效。
平头倒棱工艺卡
编号:LGBPGG-BW-3-2012-8-355.6 规格 工 序 名 称 钢管管端加工坡口,坡口角 30°- 35° ,管端余留的厚度为 1.59mm±0.8mm,见图。 平 头 倒 棱 钢管切断后,钢管两端面应与 平头倒棱机 其轴线垂直,切斜不得大于 1.59mm。 用经校验的宽座直角尺、塞 尺以钢管轴线为基准测量管 端的几何尺寸。 355.6*8.7*12000 工艺参数与要点 执行标准 GB/T 9711.1-1997 内容 操作要求 设备 控制措施 材质 岗位:平头 Q235B
备注:1)做好相应的记录;2)质量责任人为该岗位的操作者。
批准
日期
2012-08-08
审核
日期
2012-08-08
编制
刘德重
日期
2012-08-08
注:本工艺卡首页签字后生效。
静水压试验工艺卡
编号:LGBPGG-BW-3-2012-8-355.6 规格 355.6*8.7*12000 执行标准 GB/T 9711.1-1997 内容 工 序 工艺参数与要点 名称
批准
日期
2012-08-08
审核
日期
2012-08-08
编制刘德重日期2012-08-08注:本工艺卡首页签字后生效。
锯切工艺卡
编号: 规格 LGBPGG-BW-3-2012-8-355.6 355.6*8.7*12000 执行标准 GB/T 9711.1-1997 内容 工序名称 工艺参数与要点 长度范围:11990mm-12010mm 焊管存在带钢对接处长度可在: 11500mm-12500mm 范围内,尽可能 在 11990mm-12010mm 范围内。 操作要求 锯切必须保证带钢对焊处距离管 端不小于 400mm, 油性粉笔标记管 号切管后的钢管断面尽量与钢管轴线