FMEA失效模式效应分析
FMEA失效模式效应分析的描述、类型及展开

1.2 FMEA的实施原则
☆ 项目小组的人员要求 ※ 职能分布; ※ 工作经验; ※ 组织形式、活动时间等;
☆ 以产品为主线确定项目; ☆ 领导支持等。
书山有路勤为径, 学海无涯苦作舟
1.2 FMEA的要素及实施的前期准备
★ FMEA的要素 ☆要求; ☆潜在失效模式; ☆潜在失效后果; ☆潜在失效起因/机理; ☆严重度 S; ☆频度 O; ☆探测度 D; ☆ 等等DFMEA/PFMEA中的填写内容。
因此。。。。
书山有路勤为径, 学海无涯苦作舟
1.1 她的历史及起源。。。
FMEA技术的应用发展十分迅速。50年代初,美国第一次将FMEA思 想用于一种战斗机操作系统的设计分析,到了60年代中期,FMEA技 术正式用于航天工业(Apollo计划)。1976年,美国国防部颁布了 FMEA的军用标准,但仅限于设计方面。70年代末,FMEA技术开始 进入汽车工业和医疗设备工业。80年代初,进入微电子工业。80年 代中期,汽车工业开始应用过程FMEA确认其制造过程。到了1988年 ,美国联邦航空局发布咨询通报要求所有航空系统的设计及分析都 必须使用FMEA。1991年,ISO-9000推荐使用FMEA提高产品和过程 的设计。1994年,FMEA又成为QS-9000的认证要求。目前,FMEA 已在工程实践中形成了一套科学而完整的分析方法。
○ 主要是设计工程师和其小组应用。
书山有路勤为径, 学海无涯苦作舟
2.4 程序/项目FMEA:
● 针对程序/项目,程序/项目开 发设计的分析技术。 □ 项目小组
书山有路勤为径, 学海无涯苦作舟
(其中采用方法之一 :鱼刺图又称特性要因图,石川图)
☆ 用图解法对影响过程或产品质量问题的各种因素 进行全面系统的观察和分析,找出其因果关系
五大工具潜在失效模式与效果分析FMEA
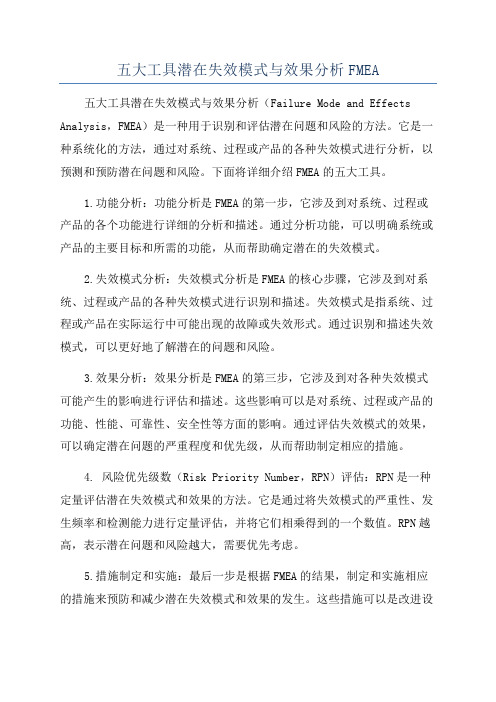
五大工具潜在失效模式与效果分析FMEA 五大工具潜在失效模式与效果分析(Failure Mode and Effects Analysis,FMEA)是一种用于识别和评估潜在问题和风险的方法。
它是一种系统化的方法,通过对系统、过程或产品的各种失效模式进行分析,以预测和预防潜在问题和风险。
下面将详细介绍FMEA的五大工具。
1.功能分析:功能分析是FMEA的第一步,它涉及到对系统、过程或产品的各个功能进行详细的分析和描述。
通过分析功能,可以明确系统或产品的主要目标和所需的功能,从而帮助确定潜在的失效模式。
2.失效模式分析:失效模式分析是FMEA的核心步骤,它涉及到对系统、过程或产品的各种失效模式进行识别和描述。
失效模式是指系统、过程或产品在实际运行中可能出现的故障或失效形式。
通过识别和描述失效模式,可以更好地了解潜在的问题和风险。
3.效果分析:效果分析是FMEA的第三步,它涉及到对各种失效模式可能产生的影响进行评估和描述。
这些影响可以是对系统、过程或产品的功能、性能、可靠性、安全性等方面的影响。
通过评估失效模式的效果,可以确定潜在问题的严重程度和优先级,从而帮助制定相应的措施。
4. 风险优先级数(Risk Priority Number,RPN)评估:RPN是一种定量评估潜在失效模式和效果的方法。
它是通过将失效模式的严重性、发生频率和检测能力进行定量评估,并将它们相乘得到的一个数值。
RPN越高,表示潜在问题和风险越大,需要优先考虑。
5.措施制定和实施:最后一步是根据FMEA的结果,制定和实施相应的措施来预防和减少潜在失效模式和效果的发生。
这些措施可以是改进设计、优化工艺、加强检测和监控等。
通过实施这些措施,可以避免或降低潜在问题和风险的发生。
FMEA是一种非常实用的分析工具,广泛应用于各个行业和领域。
它可以帮助组织识别和评估潜在问题和风险,从而采取预防措施,提高系统、过程或产品的质量和可靠性。
FMEA失效模式和效应分析

1 of 19項 目:過程責任:生產準備者:部 門:制一部零件號:關鍵日期:FMEA 日期:中心隊員:FMEA 編號: 0606242 of 19項 目:過程責任:生產準備者:部 門:制一部零件號:關鍵日期:FMEA 日期:中心隊員:FMEA 編號: 0606243 of 19項 目:過程責任:生產準備者:部 門:制一部零件號:關鍵日期:FMEA 日期:中心隊員:FMEA 編號: 0606244 of 19項 目:過程責任:生產準備者:部 門:制一部零件號:關鍵日期:FMEA 日期:中心隊員:FMEA 編號: 0606245 of 19項 目:過程責任:生產準備者:部 門:制一部零件號:關鍵日期:FMEA 日期:中心隊員:FMEA 編號: 0606246 of 19項 目:過程責任:生產準備者:部 門:制一部零件號:關鍵日期:FMEA 日期:中心隊員:FMEA 編號: 0606247 of 19項 目:過程責任:生產準備者:部 門:制一部零件號:關鍵日期:FMEA 日期:中心隊員:FMEA 編號: 0606248 of 19項 目:過程責任:生產準備者:部 門:制一部零件號:關鍵日期:FMEA 日期:中心隊員:FMEA 編號: 0606249 of 19項 目:過程責任:生產準備者:部 門:制一部零件號:關鍵日期:FMEA 日期:中心隊員:FMEA 編號: 06062410 of 19項 目:過程責任:生產準備者:部 門:制一部零件號:關鍵日期:FMEA 日期:中心隊員:FMEA 編號: 06062411 of 19項 目:過程責任:生產準備者:部 門:制一部零件號:關鍵日期:FMEA 日期:中心隊員:FMEA 編號: 06062412 of 19項 目:過程責任:生產準備者:部 門:制一部零件號:關鍵日期:FMEA 日期:中心隊員:FMEA 編號: 06062413 of 19項 目:過程責任:生產準備者:部 門:制一部零件號:關鍵日期:FMEA 日期:中心隊員:FMEA 編號: 06062414 of 19項 目:過程責任:生產準備者:部 門:制一部零件號:關鍵日期:FMEA 日期:中心隊員:FMEA 編號: 06062415 of 19項 目:過程責任:生產準備者:部 門:制一部零件號:關鍵日期:FMEA 日期:中心隊員:FMEA 編號: 06062416 of 19項 目:過程責任:生產準備者:部 門:制一部零件號:關鍵日期:FMEA 日期:中心隊員:FMEA 編號: 06062417 of 19項 目:過程責任:生產準備者:部 門:制一部零件號:關鍵日期:FMEA 日期:中心隊員:FMEA 編號: 06062418 of 19項 目:過程責任:生產準備者:部 門:制一部零件號:關鍵日期:FMEA 日期:中心隊員:FMEA 編號: 06062419 of 19項 目:過程責任:生產準備者:部 門:制一部零件號:關鍵日期:FMEA 日期:中心隊員:FMEA 編號: 060624。
设备潜在失效模式及效应分析

设备潜在失效模式及效应分析设备潜在失效模式及效应分析(FMEA)是一种系统性的方法,用于识别设备潜在的失效模式及其可能的影响。
这种方法可以帮助组织预测设备可能出现的问题,从而采取预防性措施来避免这些问题的发生。
在进行设备潜在失效模式及效应分析时,首先需要确定设备要分析的功能或特性。
然后,对于每一个功能或特性,需要识别所有可能的失效模式。
失效模式是指设备在执行其功能或特性时可能发生的故障方式。
一旦失效模式被确定,下一步就是对每种失效模式进行评估,确定其可能的影响。
这些影响可以涉及到安全、质量、生产效率、环境和成本等方面。
通过对失效模式和其影响进行分析,可以确定哪些失效模式是最严重的,从而可以优先采取措施来预防或减轻这些失效的影响。
设备潜在失效模式及效应分析对于预测设备可能出现的故障非常有益。
通过这种分析,组织可以采取有效的措施来避免或减少设备故障可能造成的负面影响。
这不仅可以提高设备的可靠性和可用性,还可以降低维护成本,提高生产效率,保护员工安全,保护环境等。
总之,设备潜在失效模式及效应分析是一种重要的工具,可以帮助组织预测设备可能的故障,并制定相应的预防措施。
这种分析方法不仅可以提高设备的可靠性和可用性,还可以降低维护成本,提高生产效率,保护员工安全和环境等方面都具有重要作用。
设备潜在失效模式及效应分析(FMEA)是一种系统性的方法,用于识别设备潜在的失效模式及其可能的影响。
这种方法可以帮助组织预测设备可能出现的问题,从而采取预防性措施来避免这些问题的发生。
在进行设备潜在失效模式及效应分析时,首先需要确定设备要分析的功能或特性。
然后,对于每一个功能或特性,需要识别所有可能的失效模式。
失效模式是指设备在执行其功能或特性时可能发生的故障方式。
失效模式的识别可以通过对设备的历史数据、技术文档、专家意见等进行调研,以找出设备可能存在的各种故障情况。
一旦失效模式被确定,下一步就是对每种失效模式进行评估,确定其可能的影响。
FMEA失效模式和效果分析
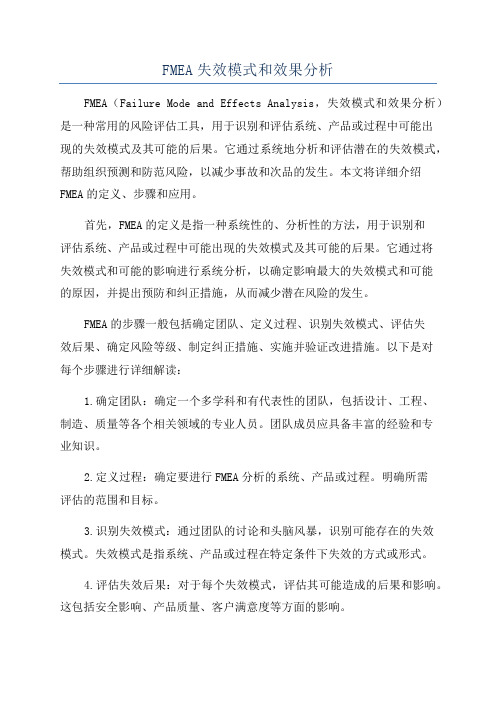
FMEA失效模式和效果分析FMEA(Failure Mode and Effects Analysis,失效模式和效果分析)是一种常用的风险评估工具,用于识别和评估系统、产品或过程中可能出现的失效模式及其可能的后果。
它通过系统地分析和评估潜在的失效模式,帮助组织预测和防范风险,以减少事故和次品的发生。
本文将详细介绍FMEA的定义、步骤和应用。
首先,FMEA的定义是指一种系统性的、分析性的方法,用于识别和评估系统、产品或过程中可能出现的失效模式及其可能的后果。
它通过将失效模式和可能的影响进行系统分析,以确定影响最大的失效模式和可能的原因,并提出预防和纠正措施,从而减少潜在风险的发生。
FMEA的步骤一般包括确定团队、定义过程、识别失效模式、评估失效后果、确定风险等级、制定纠正措施、实施并验证改进措施。
以下是对每个步骤进行详细解读:1.确定团队:确定一个多学科和有代表性的团队,包括设计、工程、制造、质量等各个相关领域的专业人员。
团队成员应具备丰富的经验和专业知识。
2.定义过程:确定要进行FMEA分析的系统、产品或过程。
明确所需评估的范围和目标。
3.识别失效模式:通过团队的讨论和头脑风暴,识别可能存在的失效模式。
失效模式是指系统、产品或过程在特定条件下失效的方式或形式。
4.评估失效后果:对于每个失效模式,评估其可能造成的后果和影响。
这包括安全影响、产品质量、客户满意度等方面的影响。
5.确定风险等级:根据失效模式的后果和可能性,评估其风险等级。
通常使用风险矩阵来划分风险等级,以帮助确定重要性和优先级。
6.制定纠正措施:针对高风险等级的失效模式,制定相应的纠正措施。
这包括预防措施来防止失效的发生,以及纠正措施来解决已经发生的失效。
7.实施并验证改进措施:根据纠正措施的计划,执行相应的改进措施,并进行验证和确认。
确保改进措施的有效性和可行性。
FMEA具有广泛的应用领域。
它可以用于设计过程中的设计FMEA,用于评估产品的可靠性和安全性;也可以用于制造过程中的制造FMEA,用于识别和评估可能导致产品质量问题的制造过程;同时,FMEA还可以用于服务过程中的服务FMEA,用于评估可能影响服务质量和客户满意度的过程。
风险评估技术-失效模式和效应分析(FMEA)及失效模式、效应和危害度分析(FMECA)

失效模式和效应分析(FMEA及失效模式、效应和危害度分析(FMECA)1 概述失效模式和效应分析(Failure Mode and Effect Analysis ,简称FMEA)是用来识别组件或系统未能达到其设计意图的方法。
FMEA 用于识别:•系统各部分所有潜在的失效模式(失效模式是被观察到的是失误或操作不当);•这些故障对系统的影响;• 故障原因;• 如何避免故障及 /或减弱故障对系统的影响。
失效模式、效应和危害度分析(Failure Mode and Effect and Criticality Analysis ,简称 FMECA)拓展了 FMEA 的使用范围。
根据其重要性和危害程度,FMECA 可对每种被识别的失效模式进行排序。
这种分析通常是定性或半定量的,但是使用实际故障率也可以定量化。
2 用途FMEA 有几种应用:用于部件和产品的设计(或产品) FM EA ;用于系统的系统FMEA ;用于制造和组装过程的过程 FMEA ;服务FMEA和软件FMEA。
FMEA/ FMECA 可以在系统的设计、制造或运行过程中使用。
然而,为了提高可靠性,改进在设计阶段更容易实施。
FMEA/ FMECA 也适用于过程和程序。
例如,它被用来识别潜在医疗保健系统中的错误和维修程序中的失败。
FMEA/FMECA 可用来:•协助挑选具有高可靠性的替代性设计方案;•确保所有的失效模式及其对运行成功的影响得到分析;•列出潜在的故障并识别其影响的严重性;•为测试及维修工作的规划提供依据;• 为定量的可靠性及可用性分析提供依据。
它大多用于实体系统中的组件故障,但是也可以用来识别人为失效模式及影响。
FMEA 及 FMECA 可以为其他分析技术,例如定性及定量的故障树分析提供输入数据。
3 输入数据FMEA 及 FMECA 需要有关系统组件足够详细的信息,以便对各组件出现故障的方式进行有意义的分析。
信息可能包括:• 正在分析的系统及系统组件的图形,或者过程步骤的流程图;• 了解过程中每一步或系统组成部分的功能;• 可能影响运行的过程及环境参数的详细信息;• 对特定故障结果的了解;• 有关故障的历史信息,包括现有的故障率数据。
失效模式与效应分析 (FMEA)

失效模式與效應分析 (FMEA)何謂「FMEA、FMECA」?FMECA 是兩種分析技術的總稱:1.FMEA﹝故障型式及其影響分析﹞2.CA﹝Criticality Analysis, 嚴重度分析﹞與失誤樹分析一樣,故障型式影響及嚴重度分析﹝failure modes, effects and criticality analysis, 簡稱 FMECA﹞,首先在美國國防科技中研究發展,且在國防部各機構中普遍應用﹝DOD, 1980﹞,後來漸應用於工業界。
在核能、化工、石化、海上鑽油等高風險工業中,自不例外。
工業界的設計工程師與可靠度﹝Reliability﹞工程師常運用 FMECA 以預測複雜的產品的可靠度,預估一件產品的零件在某特定的時間及情況下,如何失去其功能,故障的次數是多少,故障之後對其他零件或對整個系統會產生怎樣的影響等。
FMECA 的功用不止於可靠度一端,其分析所得的資料,尚可作下列用途:1.協助評估所設計的裝置,如複聯系統﹝Redundancy﹞、故障偵測,以及fail-safe 特性等。
2.對測試、採購﹝Procurement﹞、檢查、改善措施等提供先後順序的參考資料。
3.提供失誤隔絕﹝Fault isolation﹞及維護性﹝Maintainability﹞分析的參考資料。
4.提供系統安全分析﹝如失誤樹分析﹞所需的硬體資料。
FMECA 可在系統週期的任一階段中,依計劃內容之需要,以不同深淺程度實施,但在設計階段的初期,一旦所需的設備確定之後,即應實施。
FMECA 的對象是系統或子系統中的零組件,尤其對於複雜的系統中的設備零件,最能發揮其故障針砭的功效,此為其他系統安全分析技術不能望其項背之處。
但因其分析對象大多限於硬體,故對於人為因素和作業環境因素較少納入分析考慮範圍。
因此,如能將 FMECA 與失誤樹分析合併使用,必更能瞭解整個作業系統的危害,進而防範事故生。
摘於【環安 Q&A】。
风险评估技术失效模式和效应分析FMEA及失效模式效应和危害度分析FMECA

失效模式和效应分析(FMEA)及失效模式、效应和危害度分析(FMECA) 1 概述失效模式和效应分析(Failure Mode and Effect Analysis,简称FMEA)是用来识别组件或系统未能抵达其设计意图旳措施。
FMEA用于识别:●系统各部分所有潜在旳失效模式(失效模式是被观测到旳是失误或操作不妥);●这些故障对系统旳影响;●故障原因;●怎样防止故障及/或减弱故障对系统旳影响。
失效模式、效应和危害度分析(Failure Mode and Effect and Criticality Analysis,简称FMECA)拓展了FMEA旳使用范围。
根据其重要性和危害程度,FMECA可对每种被识别旳失效模式进行排序。
这种分析一般是定性或半定量旳,不过使用实际故障率也可以定量化。
2 用途FMEA有几种应用:用于部件和产品旳设计(或产品)FMEA;用于系统旳系统FMEA;用于制造和组装过程旳过程FMEA;服务FMEA和软件FMEA。
FMEA/ FMECA可以在系统旳设计、制造或运行过程中使用。
然而,为了提高可靠性,改善在设计阶段更轻易实行。
FMEA/ FMECA也合用于过程和程序。
例如,它被用来识别潜在医疗保健系统中旳错误和维修程序中旳失败。
FMEA/FMECA可用来:●协助挑选具有高可靠性旳替代性设计方案;●保证所有旳失效模式及其对运行成功旳影响得到分析;●列出潜在旳故障并识别其影响旳严重性;●为测试及维修工作旳规划提供根据;●为定量旳可靠性及可用性分析提供根据。
它大多用于实体系统中旳组件故障,不过也可以用来识他人为失效模式及影响。
FMEA及FMECA可认为其他分析技术,例如定性及定量旳故障树分析提供输入数据。
3 输入数据FMEA及FMECA需要有关系统组件足够详细旳信息,以便对各组件出现故障旳方式进行故意义旳分析。
信息也许包括:●正在分析旳系统及系统组件旳图形,或者过程环节旳流程图;●理解过程中每一步或系统构成部分旳功能;●也许影响运行旳过程及环境参数旳详细信息;●对特定故障成果旳理解;●有关故障旳历史信息,包括既有旳故障率数据。
FMEA失效分析与失效模式分析
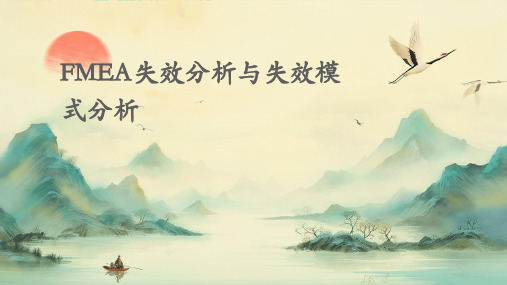
FMEA失效分析通常包括失效模式分析作为其一部分,两者都是质量 保证和可靠性工程的重要工具。
02
FMEA失效模式分析
失效模式的定义与分类
失效模式定义
在产品或过程中,可能导致产品或系 统不能达到预期功能的现象或问题。
失效模式分类
按失效的性质可分为功能失效、潜在 失效、外观失效等;按失效的原因可 分为设计缺陷、制造缺陷、使用不当 等。
06
案例研究
案例一:汽车刹车系统的FMEA失效分析
总结词
全面分析,预防为主
详细描述
通过对汽车刹车系统进行FMEA失效分析, 识别出潜在的失效模式和原因,并采取相应 的预防措施,确保刹车系统的可靠性和安全
性。
案例二
要点一
总结词
细致入微,失效定位
要点二
详细描述
对电子产品电路板进行FMEA失效模式分析,准确定位失 效模式和原因,提出改进措施,提高电路板的可靠性和稳 定性。
失效风险
指产品或系统在实现其功能过程中可能出现的故障、异常或性能下降的风险。
分类
按照失效模式和影响分析(FMEA)的方法,失效风险可分为功能失效风险和潜在失效 风险。
失效风险的分析方法
01
故障树分析(FTA)
通过建立故障树,分析系统各部件的故障对系统整体性能的影响。
02
事件树分析(ETA)
通过建立事件树,分析系统各事件的发生对系统性能的影响。
失效模式的分析方法
故障树分析法
01
通过建立故障树,分析导致故障的各种因素,确定故障发生的
概率和影响程度。
故障模式与影响分析法
02
分析产品或系统的各种故障模式,评估其对系统功能的影响程
失效模式与效应分析(FMEA)
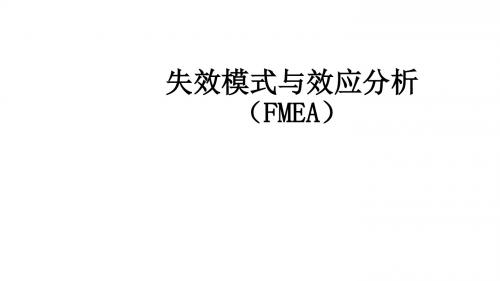
失效模式与效应分析 (FMEA)
起源
FMEA大约于1950年代由美国Grumman公 司提出,当时由于飞机系统复杂并且需要 预防失效情况发生,因此渐渐发展成安全 性与可靠度的设计模式,以期能够增加产 品质量,降低不良问题的发生。
FMEA具体项目
• 累积经验,早期发现失效原因及采取因应之道。 • 促进设计改良。 • 改善操作方法及建立维护计划的参考。 • 帮助操作人员之训练,让员工能在短期内找出 失效原因与解决之法。 • 公司人员异动时,能让员工快速上手。
FMEA表格建立
失效机率
字码体系
严重性分析
多要因评估法
单要因评估法
列表评估法
失效报告
范例
范例
范例
范例
范例
故障树分析符号
故障树分析范例
故障树简化
故障树关键性估计范例
结论
• 透过FMEA模式,可有效找出来自品失效原因,进而解决问题,是一 个可靠性的解析手法。 • 藉由实施FTA ,能让不希望发生的事情明确化,并能判别事件发 生时所带来的一些事象与对成品的影响。
FMEA失效模式及效应分析介绍

FMEA失效模式及效应分析介绍FMEA(Failure Mode and Effects Analysis)是一种用于识别、评估和减轻系统、产品或过程中可能的失效模式及其可能的效应的工具和方法。
它的目标是通过提前识别和纠正潜在的问题,从而提高系统的可靠性和安全性。
FMEA通常由一个跨职能的团队进行,包括设计工程师、工艺工程师、质量控制人员等。
这个团队将系统、产品或过程分解成多个组成部分,然后针对每个部分,逐个分析其可能的失效模式以及这些失效模式可能引起的效应。
在进行FMEA之前,团队首先需要定义一个适当的评估标准,用于对失效模式和效应进行风险评估。
评估标准通常包括失效的概率、严重性和可能性等方面。
然后,通过对每个失效模式和效应进行评估,确定其风险等级。
常用的评估方法包括风险矩阵、风险优先级数等。
FMEA的关键步骤包括:1.确定分析的范围:确定要进行FMEA的系统、产品或过程的范围,并明确所有相关的组成部分。
2.分析失效模式:对每个组成部分,团队成员进行头脑风暴,识别可能的失效模式。
失效模式是指一个组成部分不能正常工作或无法满足指定要求的一种方式。
3.分析失效效应:对于每个失效模式,分析团队评估其可能引起的效应,包括对系统性能、安全性和可靠性的影响。
这些效应需要根据评估标准进行量化或定性评估。
4.评估风险等级:通过将失效模式和效应的概率、严重性和可能性等因素综合考虑,评估每个失效模式和效应的风险等级。
这有助于团队确定哪些失效模式和效应应优先处理。
5.提出改进措施:根据风险等级,团队制定相应的改进计划。
这可以包括重新设计、改变制造流程、增加可靠性测试等措施,以降低失效模式和效应的风险。
FMEA的优点在于:1.提前识别风险:通过系统的、结构化的方法,FMEA能够识别并提前预测系统或产品中的潜在问题,从而及早采取措施来减轻或消除这些风险。
2.优化设计:通过对失效模式和效应的分析,FMEA可以帮助设计团队发现并改进设计中的潜在问题,从而提高系统的可靠性和性能。
FMEA(失败模式效果分析)

1.1.风险评估
1.1.1.风险评估的工具
对工序验证内容进行风险评估,遵循FMEA(失败模式效果分析),它为工艺过程和它们对结果和/或产品性能的可能影响提供了一种对潜在失效模式的评估。
(1)风险识别:收集可能对产品质量产生影响的潜在失效模式作为风险因素。
(2)风险判定:评估先前所识别的风险因素,这种评估的基础建立在严重性、可能性及可检测性上。
➢FMEA打分标准
风险的严重性(S)
风险发生的可能性(P)
风险的可检测性(D)
➢按照风险的严重性(S)、可能性(P)、可检测性(D)定义分值,将其相乘,计算可获得风险优先系数(即风险等级)RPN=S×P×D;根据计算得到的RPN,可得到风险的关键控制点。
➢高风险水平:RPN>16或严重程度=4且RPN>8。
➢此为不可接受风险,必须尽快采用控制措施,使其降低为低风险水平(RPN≤8)或取样存在该风险的相关计划。
所采用的措施可以是规程或技术措施,但均应经过验证。
➢中等风险水平:16≥RPN>8。
➢此风险要求采用控制措施,通过提高可检测性及/或降低风险产生的可能性来降低最终风险水平至低风险水平(RPN≤8)。
所采用的措施可以是规程或技术措施,但均应经过验证。
➢低风险水平:RPN≤8。
➢此风险水平为可接受,在此前提下,如采取简单措施可继续降低风险水平,则应继续降低风险,否则可不再采取其他的控制措施。
注:对于严重程度=4的质量风险,无论RPN值多少均应持续关注,并对风险进行跟踪。
通过追溯控制措施(如适用)的实施或评价结果,确定风险是否可以被接受。
失效模式与效应分析(FMEA)

失效模式与效应分析(FMEA)一、定义失效模式与效应分析(failure mode and effects analysis,FMEA)是一种前瞻性的管理模式,是在行动之前就认清问题并预防问题发生的分析。
FMEA由失效模式(failure oode,FM)及效应分析(effects analysis,EA)两部分组成。
其中,失效模式是指能被观察到的错误或缺陷(俗称安全隐患),应用于护理质量管理中就是指任何可能发生的护理不良事件;效应分析是指通过分析该失效模式对系统的安全和功能的影响程度,提出可以或可能采取的预防改造措施,以减少缺陷,提高质量。
二、目的、目标FMEA的目的是防患未然;设计屏障,让事情不要发生;降低损害,即使有风险存在,也是可容许的最低风险;是发现、评价流程中潜在的失效及其后果,找到能够避免或减少这些潜在失效的措施,并将上述过程文件化。
FMEA的主要目标是分析现有系统(流程)或将建立之系统(流程):哪里会出错?一旦出错会有多糟糕?哪里需要修正以避免事故发生?三、执行时机1、新设计的流程2、修改现行的流程3、旧的流程用于新的情境中四、实施步骤(一)步骤一:确认问题选择那些高风险或非常薄弱的程序进行研究。
高风险流程的特性有:高复杂性(步骤多)的作业、高差异性的输入来源、未标准化的作业、紧密相依的作业、作业时间间隔太紧或太松、高度依赖人员的判断或决定。
医疗行为中的高风险流程有:用药、病人处于危险的操作流程(放射治疗,CT扫描,磁振造影)、输血与输成分血、抑制作用的药物、对高危人群进行照顾或提供服务、与复苏相关等。
(二)步骤二:组建团队组建一个多学科的综合FMEA团队,团队中至少应该有一个领导者、一个所硏究流程方面的专家、一个FMEA咨询师(即FMEA专家,可以为团队领导者提供建议,保证FMEA的顺利实施)、一个对所研究流程不太熟悉的人(可以从不同的角度和方面提出有价值的建议)。
一般建议团队成员在6〜10人之间,以便于管理,所有成员必须接受过FMEA培训。
失效模式及效应分析 FMEA

•硬體設備失效:故障狀況 ( 如:短路、漏電、 斷裂、變形、腐蝕、鬆動、磨耗、卡死、洩漏 等)
•材料失效:不良內容(如:尺寸不良、材質錯誤、 變形、漏油及油污)
•對於服務業而言可以「服務特性之失 效」,作 為失效模式思考方向。此 外, 當 FEMA 表內同時出現二個以上不正常 及故障項目時,應修改成各自不同的名 稱,然後再記入 FEMA 表內。
評價準則-失效影響嚴重度 S:
嚴重性 基
準
10
危險無預警,直接影響安全
9
危險可預警,直接影響安全
8
失去主要功能,END USER 無法工作
7
主要功能降低,END USER 仍可工作,客戶會不滿意
主機能動作,影響週邊方便性或舒適性之項目無法工 6
作,客戶感覺不方便
主機能動作,週邊方便性或舒適性之項目功能降低,客 5
失效模式及效應分析 FMEA
前言
• FMEA(Failure Mode And Effect Analysis) 自 1950 年代初期就被當做是 航空機用動力計劃的解析法,到了實施 阿波羅計劃獲得重大成就後,即被廣泛 推廣開來。此外 FMEA 亦是 QS9000 中 設計活動中要求應適當具備的技術。
產品設計開發的 FMEA 表作成
•記入 FMEA 對象的品名及名稱 。 •記入 FMEA 對象的識別編號 。 •依照製造工程順序在「名稱」欄位寫上
工程名稱、使用及設備投入的材料 。 •將工程、使用設備及投入材料這些原本
應具備的功能記入在「功能」欄內 。 •失效模式 (公司可先定義失效模式)
FMEA失效模式与效应分析

FMEA失效模式与效应分析
FMEA是一种常用的质量管理方法,全称为“失效模式和影响分析”(Flure Mode and Effects Analysis)。
它是一种定量分析工具,用于衡量所研究系统的某种失效模式和这种失效模式带来的效应。
它可以通过对失效模式进行系统的分析和归纳,找出并解决潜在的失效模式,从而提高产品、过程和系统的质量和可靠度。
下面我们来详细了解一下FMEA失效模式与效应分析。
一、FMEA的基本概念
FMEA是一种质量管理工具,可以对产品制造或过程设计进行评估,以识别可能出现的失效模式,并预先采取相应的改进措施以消除或减轻风险。
该方法可以帮助组织识别潜在问题并提供预防性控制,以最大程度地降低可能的风险。
FMEA通常包括以下步骤:
1.识别和描述潜在的失效模式;
2.评估和量化失效模式的可能性、严重性和检测能力(即失效模式对产品质量和可靠性的影响);
3.识别并建议风险缓解措施。
二、FMEA的分类
FMEA可以分为设计FMEA(DFMEA)和过程FMEA(PFMEA)两种类型。
1.设计FMEA( DFMEA)
1。
失效模式及效应分析程序FMEA

1.目的:1.1對產品設計及其制程中的潛在失效影響效應建立認知并予以評價。
1.2確認系列措施及消除或降低失效發生的機會。
1.3建立產品設計及其制程的文件記錄。
2.范圍﹕2.1DFMEA:所有新產品在開發初期﹐收到客戶設計資料后,并進行可行性評估與規划之前均適用。
2.2 PFMEA﹕2.2.1在APQP的制程設計與開發驗証階段實施。
2.2.2對新制程或將修訂的制程實施。
3.權責﹕3.1制訂﹕DFMEA由開發部主要跨功能小組訂定﹔PFMEA由生產部主要跨功能小組訂定。
3.2審查﹕由各主要跨功能小組組長審查并督導落實執行。
3.3核准﹕管理代表核准。
4.定義﹕4.1失效模式﹕指產品或過程可能不能滿足設計意圖或過程要求的方式或方法。
5.作業內容﹕按設計或制程FMEA表格執行,以下簡介FMEA表的制作﹕5.2項目﹕填入要分析之產品型別。
部門﹕填入要分析之工序。
5.3制定部門﹕填入主導FMEA單位別。
5.4編制人﹕填入主導完成FMEA工程師的名字。
5.5次系統 / 機種﹕填入客戶產品名稱。
5.6生效日期﹕填入FMEA最新發布日期。
5.7 FMEA日期( 原始 )﹕填入最初FMEA制定日期。
5.8核心小組﹕填入跨功能小組所有成員姓名。
5.9功能 / 作業要求或目的﹕盡可能簡潔地填入被分析部位(制程)的功能或作業要求,如果項目包含一個以上有不同功能或(制程)作業要求時﹐則列出所有項目。
5.10潛在失效模式﹕5.10.1當作業可能不符合制程要求或設計意圖﹐敘述規定的不合格事項,它是一個原因而成為下制程的潛在失效模式﹐或被上制程所影響的潛在失效模式。
5.10.2列出﹕5.10.2.1每一潛在失效模式假設失效是將發生的﹐但不是必須發生的。
5.10.2.2盡可能敘述失效模式發生于某些作業條件下(如﹕壓力等)和在某些使用條件下(如﹕溫度,高度)。
5.10.2.3一般失效模式含如下各項﹐但不限于此﹕破損、變形、碰傷、錯位、裂紋等。
- 1、下载文档前请自行甄别文档内容的完整性,平台不提供额外的编辑、内容补充、找答案等附加服务。
- 2、"仅部分预览"的文档,不可在线预览部分如存在完整性等问题,可反馈申请退款(可完整预览的文档不适用该条件!)。
- 3、如文档侵犯您的权益,请联系客服反馈,我们会尽快为您处理(人工客服工作时间:9:00-18:30)。
失效 效應 模分 式析
Failure Modes and Effects Analysis
Rev.1.0 2001/01/05
P. 5
FMEA推行的目的
目的:在潛在失效發生之前就先認知、明訂及文書化٫ 以避免或降低失效發生之可能性◦ 方法:小組研討是確保成功FMEA最有效的方法◦
失效 效應 模分 式析
Friday, February 15, 2019
Failure Modes and Effects Analysis
Rev.1.0 2001/01/05
P. 2
何謂FMEA ?
失效 效應 模分 式析
1950 年由美國 Grumman 公司針對新型噴射引擎 (Jet engine)٫ 為了評估其操縱系統之可靠度所開發的分析 方法◦美國汽車工業用來連貫設計、開發和製造的程序 ٫我 國 在 1 9 7 0 年 左 右 引 進٫用 於 航 空 及 汽 車 工 業 ◦
Rev.1.0 2001/01/05
P. 7
失效模式
零件、次系統或系統不能發揮原先預定功能的 事項◦
例如:賽車的功能為200公里/小時,當測試驗證時發現只能 達到180公里/小時,結論是這輛車Failure了。
失效 效應 模分 式析
Friday, February 15, 2019
Failure Modes and Effects Analysis
Rev.1.0 2001/01/05
P. 8
失效之分類
依失效發生的原因分類
依失效發生的時間情況分類 依失效的範圍程度分類 綜合性的失效分類 依造成失效的來源分類 依造成失效的錯誤類別分類
失效 效應 模分 式析
Friday, February 15, 2019
Failure Modes and Effects Analysis
FMEA 是評估設計(製程)可靠度的一種方法◦
FMEA 是預防的工具٫ 一種有條理的程序٫ 產出一張表 包含所有的錯誤٫ 以數據方式來表示風險的大小٫ 並定 義預防措施◦
Friday, February 15, 2019
Failure Modes and Effects Analysis
Rev.1.0 2001/01/05
失效 效應 模分 式析
失效模式效應分析
Failure Modes and Effects Analysis ( F 15, 2019
Failure Modes and Effects Analysis
Rev.1.0 2001/01/05
P. 1
課程內容
1. FMEA簡介 2. 製程FMEA的作業展開 3. 執行FMEA的步驟
P. 3
FMEA技術發展重要紀事
1950 1957 1960 1967 1970 1974 1980 1980 1982 1984 1984 美國格魯曼(Grumman)公司首先提出,用於飛機主操縱系統 美國波音(Boeing)與馬丁(Martin Marietta)公司工程手冊 美國太空總署(NASA)應用於航太計畫(APOLO) 美國SAE ARP-926 美國NASA NHB-5300.4(1A) 美軍標準MIL-STD-1629 福特(Ford)汽車公司, Potential failure mode and effects analysis handbook 美軍標準MIL-STD-1629A 英國國家標準BS5760-3 福特汽車公司, Potential failure mode and effects analysis handbook(修訂) 美國克萊斯勒(Chrysler)公司, FMEA MANUAL
Rev.1.0 2001/01/05
P. 9
FMEA的種類
失效 效應 模分 式析
設計(Design) 製程(Process) 主要用於製造責任小組٫確保潛在失效模式及相關原因 已被分析及提出٫ 降低製造過程中失效的風險◦
1. 明訂與產品製程相關的失效模式◦ 2. 提出潛在失效對客戶的影響(下一個製程)◦
價值:FMEA是事前行動而非事後反應措施٫發展FMEA完 全要在開始作業之前進行٫因為這時候改變任何 東西很容易而且成本低٫可避免事後高難度、高 成本的矯正措施◦
失效 效應 模分 式析
Friday, February 15, 2019
Failure Modes and Effects Analysis
Rev.1.0 2001/01/05
P. 6
功能
零件、次系統或產品必須執行的作業٫以一種簡明的、 精密的和容易瞭解的方法來敘述٫使任何人均能了解◦
失效 效應 模分 式析
功能(V+N)如下: 顯示時間 盛裝液體 投射影像 顯現影像 支撐工件
Friday, February 15, 2019
Failure Modes and Effects Analysis
Failure Modes and Effects Analysis
Rev.1.0 2001/01/05
失效 效應 模分 式析
Friday, February 15, 2019
P. 4
FMEA技術發展重要紀事
1985 國際電工委員會(IEC), IEC 812 1986 美國克萊斯勒(Chrysler)公司, FMEA MANUAL(修訂) 1987 英國車輛協會(SMMT), Guidelines to FMEA 1988 福特汽車公司, Potential failure mode and effects analysis handbook(修訂) 1992 福特汽車公司, Potential failure mode and effects analysis(修訂) 1993 美國品管學會(ASQC)、車輛工業行動組(AIAG), Potential failure mode and effects analysis reference manual 1995 美國品管學會(ASQC)、車輛工業行動組(AIAG), Potential failure mode and effects analysis reference manual(SAE J-1739)