自动配料系统在炼钢系统上的运用
铁合金电炉自动化配料控制系统的设计与应用
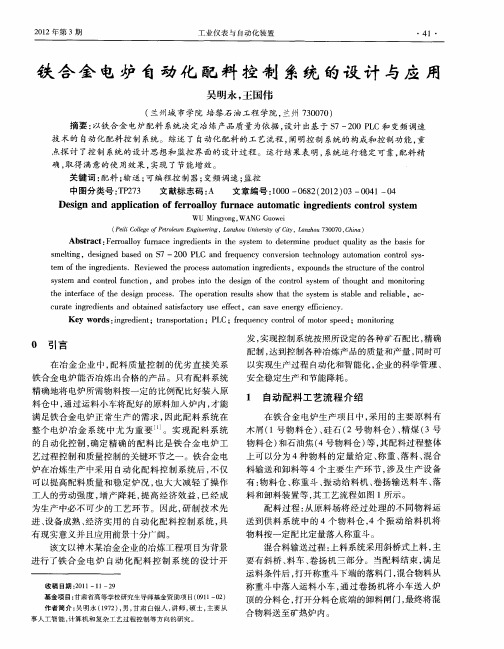
收 稿 日期 :0 l一1 2 21 1— 9
混 合料 输送 过程 : 上料 系统 采用 斜桥 式上料 , 主
要 有 斜桥 、 车 、 扬 机 三部 分 。当配 料 结束 , 足 料 卷 满 运 料条 件后 , 开称重 斗下 端 的落料 门 , 合物 料从 打 混 称 重斗 中落 入运 料 小 车 , 过卷 扬 机 将 小 车送 人 炉 通 顶 的分料 仓 , 打开 分料 仓底 端 的卸料 闸 门 , 终将 混 最 合物 料送 至矿 热炉 内。
点探 讨 了控 制 系统 的设 计 思想和 监控 界 面 的设 计过 程 。运行 结 果表 明 , 系统运行 稳 定可 靠 , 配料 精
确, 取得 满意 的使 用效 果 , 实现 了节 能增 效 。 关 键词 : 配料 ; 送 ; 编程控 制 器 ; 输 可 变频调 速 ; 监控
中图分 类号 :P 7 T 23
A bsr c : ro lo u na e i g e i n s i h y tm o d tr n r d c u l y a h a i o t a t Fe r al y f r c n r d e t n t e s se t e e mi e p o u tq ai s t e b ss f r t
在 铁合 金 电炉 生产 项 目中 , 用 的主要 原 料 有 采 木屑 ( 1号物 料 仓 ) 硅 石 ( 、 2号 物料 仓 ) 精 煤 ( 、 3号 物料 仓 ) 和石 油焦 ( 物料 仓 ) , 配料 过程整 体 4号 等 其 上可 以分 为 4种 物料 的定 量 给定 、 重 、 料 、 称 落 混合
功能 , 保证 了变频 振动 给料 的精 度 和速度 。
矿热炉配料上料自动控制系统的设计与实现

矿热炉配料上料自动控制系统的设计与实现发布时间:2022-11-08T06:35:40.527Z 来源:《福光技术》2022年22期作者:孙川[导读] 矿热炉配料上料控制系统组成部分包括三个部分,分别为配料、上料以及布料。
大连重工机电设备成套有限公司辽宁省大连市 116011摘要:在铁合金生产的过程中,配料是其重要的组成部分。
本文针对目前工厂流行的两种上料方式展开讨论,结合自动化控制系统的应用,能够显著地提高企业的自动化程度。
关键词:矿热炉;自动控制在对铁合金进行冶炼的过程中,为了能够确保产品的高质量以及促进铁合金的正常生产,其关键的技术之一为配料上料系统。
随着近年来我国计算机技术与科学技术的发展,配料与给料系统在矿热炉生产过程中也逐渐朝着信息化、自动化、机械化以及精细化的方向发展。
1 配料上料自动控制系统构成矿热炉配料上料控制系统组成部分包括三个部分,分别为配料、上料以及布料。
在该控制系统中主要是通过建立人机交互界面方式,其中可编程控制器PLC为主机,从机为上位机触摸屏。
自动配上料系统的工艺路线为:炉顶料仓设有料位测量装置,当料仓缺料时,测量装置自动发出求料信号,得到求料信号后,系统自动按照提前设定好的原料配比,将储料仓中的原料由拖拉皮带机加入称量斗,对所需的各种原料进行单独称重,再分别由拖拉皮带机加入混料皮带机,混料时通过变频控制拖拉皮带机的速度来保证混料的均匀,混料后,再由上料皮带机和环形布料机送至炉顶料仓内,料仓内的混合原料再由料管送至炉内。
1.1 配料对于矿热炉系统来说,其配料系统的组成部分主要包括计量秤、PLC、下料小皮带、振打器、触摸屏以及电磁振动给料机等。
根据各个企业在实际生产中的工艺能够使配料系统在触摸屏上对各种不同物料中午的配比情况进行标定,在此过程中,PLC 系统在运作过程中能够读取物料重量的相关信息,同时也能够根据程序起动的电磁振动给料机对物料进行放料与称重等一系列操作。
DCS系统在钢铁行业中的应用案例分享
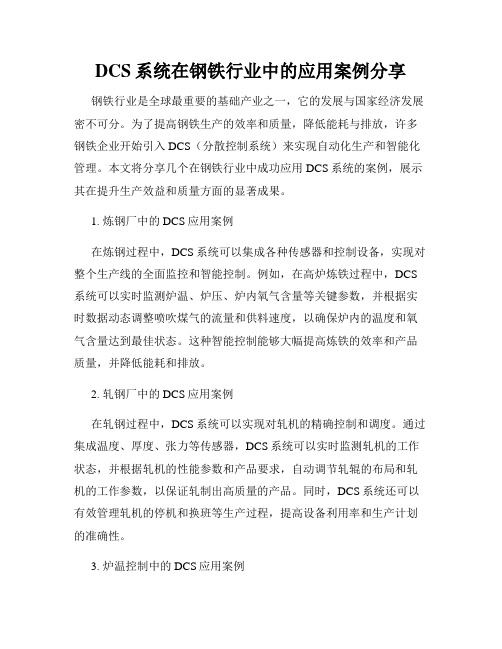
DCS系统在钢铁行业中的应用案例分享钢铁行业是全球最重要的基础产业之一,它的发展与国家经济发展密不可分。
为了提高钢铁生产的效率和质量,降低能耗与排放,许多钢铁企业开始引入DCS(分散控制系统)来实现自动化生产和智能化管理。
本文将分享几个在钢铁行业中成功应用DCS系统的案例,展示其在提升生产效益和质量方面的显著成果。
1. 炼钢厂中的DCS应用案例在炼钢过程中,DCS系统可以集成各种传感器和控制设备,实现对整个生产线的全面监控和智能控制。
例如,在高炉炼铁过程中,DCS 系统可以实时监测炉温、炉压、炉内氧气含量等关键参数,并根据实时数据动态调整喷吹煤气的流量和供料速度,以确保炉内的温度和氧气含量达到最佳状态。
这种智能控制能够大幅提高炼铁的效率和产品质量,并降低能耗和排放。
2. 轧钢厂中的DCS应用案例在轧钢过程中,DCS系统可以实现对轧机的精确控制和调度。
通过集成温度、厚度、张力等传感器,DCS系统可以实时监测轧机的工作状态,并根据轧机的性能参数和产品要求,自动调节轧辊的布局和轧机的工作参数,以保证轧制出高质量的产品。
同时,DCS系统还可以有效管理轧机的停机和换班等生产过程,提高设备利用率和生产计划的准确性。
3. 炉温控制中的DCS应用案例炉温是钢铁生产中非常重要的参数,它直接影响到钢材的质量和生产效益。
DCS系统在炉温控制中的应用可以帮助钢铁企业实现更加精确和稳定的温度控制。
通过采集炉温数据和环境数据,DCS系统可以根据事先设定的温度曲线,自动调节燃烧系统、送风系统等设备的工作参数,以实现最佳的炉温控制效果。
这种智能化控制不仅提高了产品的一致性和质量稳定性,还减少了人工干预和能耗浪费。
总结:DCS系统在钢铁行业中的应用案例丰富多样,从炼钢到轧钢,从生产线的控制到炉温的调节,都能发挥重要作用。
通过引入DCS系统,钢铁企业可以实现生产过程的智能化和自动化,提高生产效率,降低能耗和排放,提升产品质量稳定性和一致性。
工业自动化中的钢铁制造行业实例分析

绿色可持续发展
产业链协同
钢铁制造将更加注重环保和可持续发展, 推动产业绿色化改造,降低能耗和排放, 实现循环经济。
钢铁制造企业将加强与上下游企业的合作 与协同,形成更加紧密的产业链合作关系 ,共同应对市场挑战。
THANKS
感谢观看
炼钢自动化系统的实例分析
总结词:降低成本
详细描述:炼钢自动化系统通过提高生产效率和降低能耗 ,实现了降低成本的目标。该系统能够优化能源和原材料 的使用,减少浪费,同时提高产量和合格率。
轧钢自动化系统的实例分析
总结词
高精度控制
详细描述
轧钢自动化系统通过高精度控制技术 ,实现了高质量的钢材轧制。该系统 能够精确控制轧机的速度、压力等参 数,确保钢材的尺寸、形状和性能符 合要求。
炼铁自动化系统的实例分析
总结词
高自动化程度
详细描述
炼铁自动化系统具备高自动化程度,减少了人工干预,提高了生产效率。该系 统能够自动完成配料、加料、出渣等工序,降低了工人的劳动强度。
炼铁自动化系统的实例分析
总结词:节能减排
详细描述:炼铁自动化系统通过优化能源利用和减少废弃物排放,实现了节能减排。该系统能够根据实际需求调整能源供应 ,降低能耗,同时减少废气、废水和固体废弃物的排放。
成本控制与经济效益
成本控制
钢铁制造企业在引入工业自动化时,需要合 理控制成本。这包括设备采购、维护和更新 成本,以及员工培训和生产效率提升等方面 的成本。通过有效的成本控制,企业可以提 高经济效益。
经济效益
工业自动化有助于提高钢铁制造企业的生产 效率和产品质量,从而增加经济效益。同时 ,自动化技术的应用还可以降低人工成本和 减少生产过程中的浪费,为企业创造更大的
自动化配料系统策划书
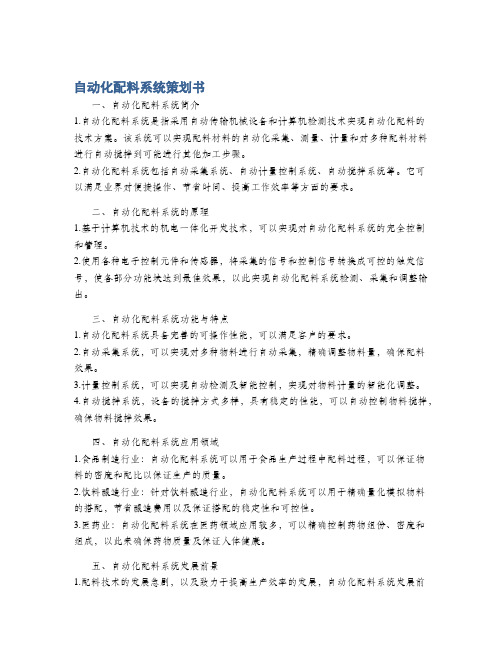
自动化配料系统策划书一、自动化配料系统简介1.自动化配料系统是指采用自动传输机械设备和计算机检测技术实现自动化配料的技术方案。
该系统可以实现配料材料的自动化采集、测量、计量和对多种配料材料进行自动搅拌到可能进行其他加工步骤。
2.自动化配料系统包括自动采集系统、自动计量控制系统、自动搅拌系统等。
它可以满足业界对便捷操作、节省时间、提高工作效率等方面的要求。
二、自动化配料系统的原理1.基于计算机技术的机电一体化开发技术,可以实现对自动化配料系统的完全控制和管理。
2.使用各种电子控制元件和传感器,将采集的信号和控制信号转换成可控的触发信号,使各部分功能块达到最佳效果,以此实现自动化配料系统检测、采集和调整输出。
三、自动化配料系统功能与特点1.自动化配料系统具备完善的可操作性能,可以满足客户的要求。
2.自动采集系统,可以实现对多种物料进行自动采集,精确调整物料量,确保配料效果。
3.计量控制系统,可以实现自动检测及智能控制,实现对物料计量的智能化调整。
4.自动搅拌系统,设备的搅拌方式多样,具有稳定的性能,可以自动控制物料搅拌,确保物料搅拌效果。
四、自动化配料系统应用领域1.食品制造行业:自动化配料系统可以用于食品生产过程中配料过程,可以保证物料的密度和配比以保证生产的质量。
2.饮料酿造行业:针对饮料酿造行业,自动化配料系统可以用于精确量化模拟物料的搭配,节省酿造费用以及保证搭配的稳定性和可控性。
3.医药业:自动化配料系统在医药领域应用较多,可以精确控制药物组份、密度和组成,以此来确保药物质量及保证人体健康。
五、自动化配料系统发展前景1.配料技术的发展急剧,以及致力于提高生产效率的发展,自动化配料系统发展前景广阔。
2.随着生产企业不断完善自动化配料系统,自动化配料系统未来将会得到更多应用,自动化配料系统将会把生产效率提高到前所未有的水平。
3.由于自动化配料系统可以降低人工开销,大大提高了运行效率,未来自动化配料系统将会是市场上重要的产品。
废钢配料工作亮点
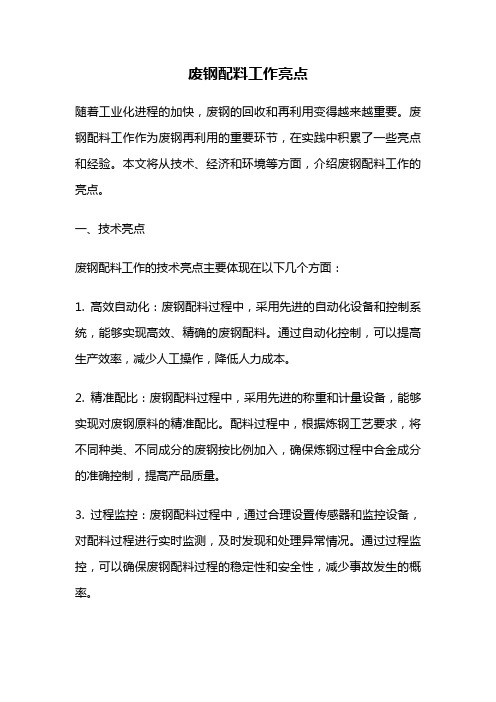
废钢配料工作亮点随着工业化进程的加快,废钢的回收和再利用变得越来越重要。
废钢配料工作作为废钢再利用的重要环节,在实践中积累了一些亮点和经验。
本文将从技术、经济和环境等方面,介绍废钢配料工作的亮点。
一、技术亮点废钢配料工作的技术亮点主要体现在以下几个方面:1. 高效自动化:废钢配料过程中,采用先进的自动化设备和控制系统,能够实现高效、精确的废钢配料。
通过自动化控制,可以提高生产效率,减少人工操作,降低人力成本。
2. 精准配比:废钢配料过程中,采用先进的称重和计量设备,能够实现对废钢原料的精准配比。
配料过程中,根据炼钢工艺要求,将不同种类、不同成分的废钢按比例加入,确保炼钢过程中合金成分的准确控制,提高产品质量。
3. 过程监控:废钢配料过程中,通过合理设置传感器和监控设备,对配料过程进行实时监测,及时发现和处理异常情况。
通过过程监控,可以确保废钢配料过程的稳定性和安全性,减少事故发生的概率。
二、经济亮点废钢配料工作的经济亮点主要表现在以下几个方面:1. 资源利用率高:废钢是一种可再生资源,通过废钢配料工作,可以有效利用废钢资源,减少对原材料的依赖,降低生产成本。
同时,废钢配料还可以减少废钢的堆放和处理成本,节约了企业的资金。
2. 降低能耗:废钢配料过程中,采用先进的能源管理技术,对能源的消耗进行有效控制。
通过优化能源利用,可以降低能源成本,提高企业的经济效益。
3. 增加产品附加值:废钢配料可以根据产品的不同要求,灵活调整废钢的配比比例,以获得不同性能和品质的产品。
通过废钢配料,可以提高产品的附加值,增加企业的竞争优势。
三、环境亮点废钢配料工作的环境亮点主要体现在以下几个方面:1. 降低二氧化碳排放:废钢是再生资源,通过废钢配料工作,可以减少对矿石等原材料的开采和加工,从而减少二氧化碳等温室气体的排放,对环境保护具有积极意义。
2. 减少废弃物产生:废钢配料工作可以有效处理废钢,减少废钢的堆放和处理量,降低对环境的负荷。
电石炉,硅铁炉的自动配料系统
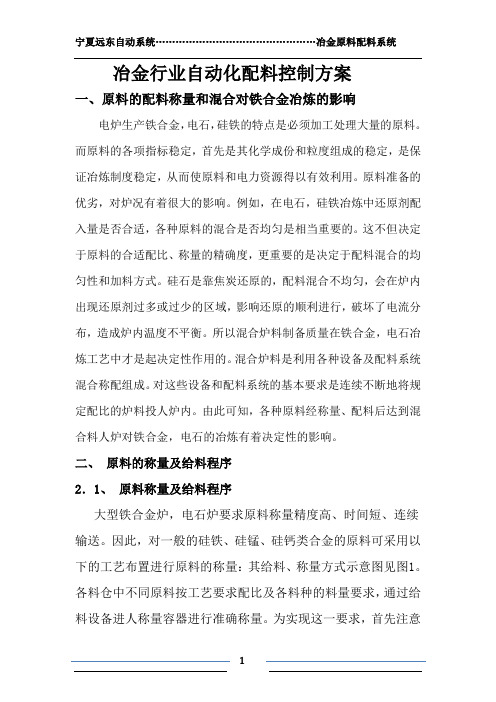
冶金行业自动化配料控制方案一、原料的配料称量和混合对铁合金冶炼的影响电炉生产铁合金,电石,硅铁的特点是必须加工处理大量的原料。
而原料的各项指标稳定,首先是其化学成份和粒度组成的稳定,是保证冶炼制度稳定,从而使原料和电力资源得以有效利用。
原料准备的优劣,对炉况有着很大的影响。
例如,在电石,硅铁冶炼中还原剂配入量是否合适,各种原料的混合是否均匀是相当重要的。
这不但决定于原料的合适配比、称量的精确度,更重要的是决定于配料混合的均匀性和加料方式。
硅石是靠焦炭还原的,配料混合不均匀,会在炉内出现还原剂过多或过少的区域,影响还原的顺利进行,破坏了电流分布,造成炉内温度不平衡。
所以混合炉料制备质量在铁合金,电石冶炼工艺中才是起决定性作用的。
混合炉料是利用各种设备及配料系统混合称配组成。
对这些设备和配料系统的基本要求是连续不断地将规定配比的炉料投人炉内。
由此可知,各种原料经称量、配料后达到混合料人炉对铁合金,电石的冶炼有着决定性的影响。
二、原料的称量及给料程序2.1、原料称量及给料程序大型铁合金炉,电石炉要求原料称量精度高、时间短、连续输送。
因此,对一般的硅铁、硅锰、硅钙类合金的原料可采用以下的工艺布置进行原料的称量:其给料、称量方式示意图见图1。
各料仓中不同原料按工艺要求配比及各料种的料量要求,通过给料设备进人称量容器进行准确称量。
为实现这一要求,首先注意的有以下两点:2.1.1、给料设备的确定目前称配料工艺中主要是给料设备的确定。
由于它是一个间断的给料设备,而间断作业的给料设备仅有一个调节作用——改变原料加人称量容器的速度。
因此,这种给料设备有以下三种方案为基本调节原则。
第一方案:以固定不变的速度送料,直到达到规定的一次称量值,然后关停供料装置;第二方案:一次称量中的大部分原料(90~95%)用最大速度供料,然后将供料装置改换为低速操作制度,直到一次称量规定值为止。
然后关停供料装置;第三方案:以间断开动给料设备,直到规定值为止。
一键炼钢包含的技术项目
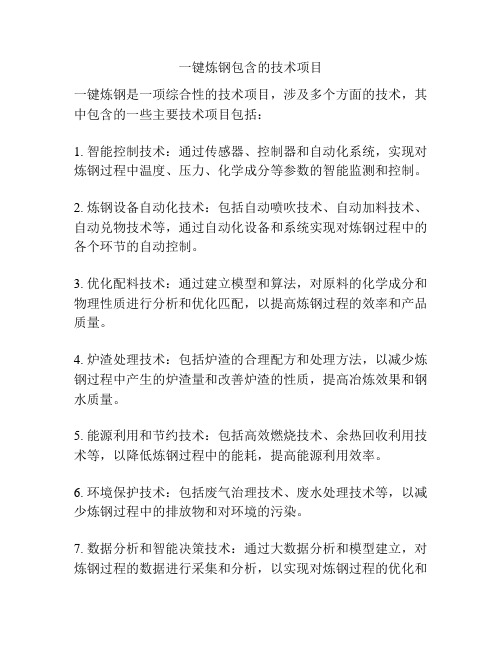
一键炼钢包含的技术项目
一键炼钢是一项综合性的技术项目,涉及多个方面的技术,其中包含的一些主要技术项目包括:
1. 智能控制技术:通过传感器、控制器和自动化系统,实现对炼钢过程中温度、压力、化学成分等参数的智能监测和控制。
2. 炼钢设备自动化技术:包括自动喷吹技术、自动加料技术、自动兑物技术等,通过自动化设备和系统实现对炼钢过程中的各个环节的自动控制。
3. 优化配料技术:通过建立模型和算法,对原料的化学成分和物理性质进行分析和优化匹配,以提高炼钢过程的效率和产品质量。
4. 炉渣处理技术:包括炉渣的合理配方和处理方法,以减少炼钢过程中产生的炉渣量和改善炉渣的性质,提高冶炼效果和钢水质量。
5. 能源利用和节约技术:包括高效燃烧技术、余热回收利用技术等,以降低炼钢过程中的能耗,提高能源利用效率。
6. 环境保护技术:包括废气治理技术、废水处理技术等,以减少炼钢过程中的排放物和对环境的污染。
7. 数据分析和智能决策技术:通过大数据分析和模型建立,对炼钢过程的数据进行采集和分析,以实现对炼钢过程的优化和
智能决策。
以上只是一些主要的技术项目,随着科技的发展和创新,一键炼钢涉及的技术还会不断增加和改进。
钢铁行业如何控制炼钢过程中的温度
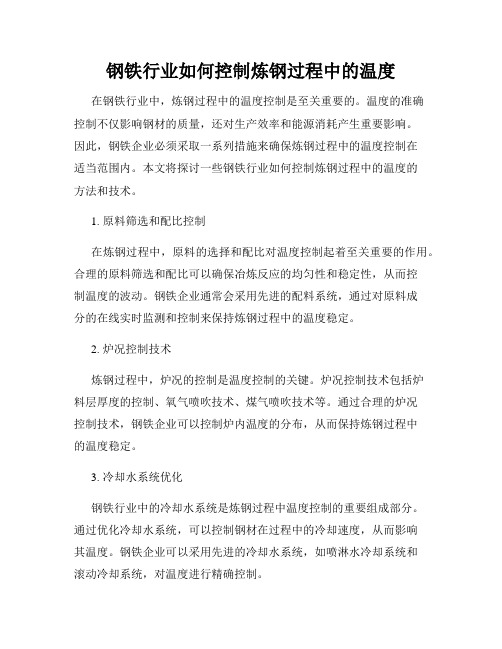
钢铁行业如何控制炼钢过程中的温度在钢铁行业中,炼钢过程中的温度控制是至关重要的。
温度的准确控制不仅影响钢材的质量,还对生产效率和能源消耗产生重要影响。
因此,钢铁企业必须采取一系列措施来确保炼钢过程中的温度控制在适当范围内。
本文将探讨一些钢铁行业如何控制炼钢过程中的温度的方法和技术。
1. 原料筛选和配比控制在炼钢过程中,原料的选择和配比对温度控制起着至关重要的作用。
合理的原料筛选和配比可以确保冶炼反应的均匀性和稳定性,从而控制温度的波动。
钢铁企业通常会采用先进的配料系统,通过对原料成分的在线实时监测和控制来保持炼钢过程中的温度稳定。
2. 炉况控制技术炼钢过程中,炉况的控制是温度控制的关键。
炉况控制技术包括炉料层厚度的控制、氧气喷吹技术、煤气喷吹技术等。
通过合理的炉况控制技术,钢铁企业可以控制炉内温度的分布,从而保持炼钢过程中的温度稳定。
3. 冷却水系统优化钢铁行业中的冷却水系统是炼钢过程中温度控制的重要组成部分。
通过优化冷却水系统,可以控制钢材在过程中的冷却速度,从而影响其温度。
钢铁企业可以采用先进的冷却水系统,如喷淋水冷却系统和滚动冷却系统,对温度进行精确控制。
4. 热能回收利用在钢铁行业中,炼钢过程中产生的大量余热可以通过热能回收系统进行回收利用。
回收利用余热不仅可以降低能源消耗,还可以提供稳定的热源,从而对温度进行控制。
钢铁企业可以通过余热发电、余热锅炉等方式将余热转化为电力或热能,用于炼钢过程中的温度控制。
5. 温度监测和控制系统钢铁行业通常会采用高精度的温度监测和控制系统来实时监测和控制炼钢过程中的温度。
这些系统可以对每个环节的温度进行实时监测,并通过自动控制系统对温度进行调节。
温度监测和控制系统的应用可以大大提高温度控制的准确性和稳定性。
总结起来,钢铁行业在炼钢过程中,通过原料筛选和配比控制、炉况控制技术、冷却水系统优化、热能回收利用以及温度监测和控制系统等措施,可以有效地控制炼钢过程中的温度。
智能化控制在钢铁冶炼中的应用

智能化控制在钢铁冶炼中的应用随着社会的进步和科技的发展,智能化控制越来越多的应用于工业制造中。
钢铁冶炼作为重要的制造产业,也逐渐掌握了智能化控制技术,并取得了良好的效果。
那么智能化控制技术在钢铁冶炼中的应用有哪些呢?一、智能化控制在炼钢中的应用1. 炼钢中的智能化控制技术智能化控制技术在炼钢过程中主要应用于炉料配料系统、炉外预处理系统、炉内自动控制系统、炉外回收系统等方面。
其中,炉料配料系统常采用智能化配料系统,该系统可以根据钢种、生产工艺和炉子的情况进行智能化控制,实现了炼钢生产的自动化和智能化。
2. 智能化控制技术的优势智能化控制技术在炼钢过程中具有控制精确、效率高、稳定性好、自动化程度高等诸多优势。
通过智能化控制技术,可以实现炼钢生产过程的智能化和高效化,大大提高了钢铁冶炼的生产效率和质量水平。
二、智能化控制在炼铁中的应用1. 炼铁中的智能化控制技术智能化控制技术在炼铁过程中主要应用于生铁制备系统、高炉自动控制系统、脱硫脱磷系统等方面。
其中,高炉自动控制系统采用智能化控制技术可以实现高炉自动调控,全面保证了高炉的正常运行和生产效率。
2. 智能化控制技术的优势智能化控制技术在炼铁过程中具有控制精确、效率高、稳定性好、自动化程度高等诸多优势。
通过智能化控制技术,可以实现炼铁生产过程的智能化和高效化,大大提高了钢铁冶炼的生产效率和质量水平。
三、智能化控制技术的未来智能化控制技术的发展前景十分广阔,未来可能应用于更多的制造领域中,包括汽车制造、机械制造、航空制造等。
在钢铁冶炼领域,智能化控制技术也将会在生产工艺、工作环境、设备维护等方面发挥更加重要的作用。
因此,智能化技术的掌握和应用将成为钢铁制造企业提高生产效率和质量水平的关键。
总之,智能化控制技术正在为钢铁冶炼领域带来新的机遇和挑战。
通过持续的技术创新和实践,钢铁制造企业将能够更加高效地进行生产,为现代工业的发展做出更大的贡献。
浅析自控系统在钢铁冶炼中的应用
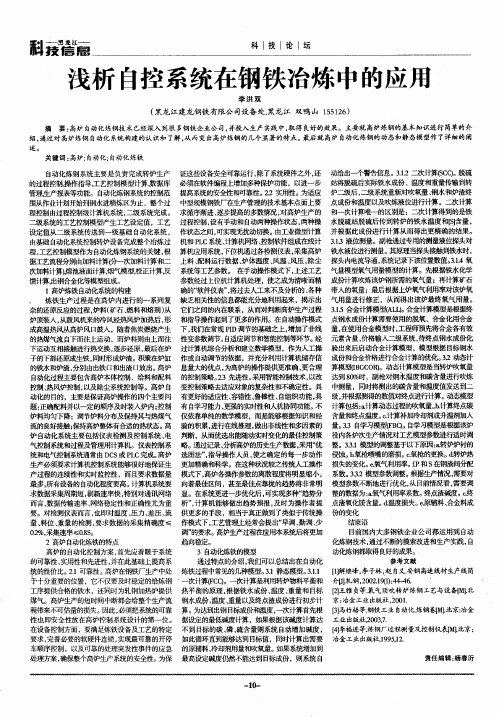
科技 论坛 I {l
浅析 自控系统在钢铁冶炼 中的应用
李 洪 双
ห้องสมุดไป่ตู้
( 黑龙江建龙钢铁 有限公 司设备 处, 黑龙江 双鸭山 15 2 ) 5 16
摘 要: 高炉 自动化炼钢技 术 已经深入到很 多钢铁企业公司, 并投入生产 实践 中, 良好的效果。主要就 高炉炼钢的基本知识进行 简单的介 取得 绍, 通过对高炉炼钢 自动化 系统构建的认识和 了解, 而突出高炉炼钢的几个显著的特点。最后就 高炉 自动化炼钢的动态和静 态模型作 了详 细的阐 从
述。
关键词: 高炉 : 化 : 化 炼 铁 自动 自动
3. 1 2-Of g( c 脱硫 :- s ) t c 。 除了系统硬件之外 , 还 动给出—个警告信息。 . 自 动化炼钢 系统主要是负责完成转炉生产 证这些设备安全可靠运行 , 的过程控制, 操作指导' 工艺控制模型计算, 数据库 必须在软件编程上增加多种保护功能,以进一步 站将脱硫后实际铁水成份、温度和重量传输到转 二级系统重新对吹氧量、 钢水和炉渣终 管理’ 生产报表等功能。自 动化炼钢系统的控制范 提高系统的安全性和可靠性。 2实用性。 2 为适应 炉二级后, :t ¥ 围从作业计划开始到钢水进精炼区为止 , 整个过 中型规模钢铁 厂在生产管理的技术基本 面上要 点成份和温度以及吹炼液位进行计算。-Of * 逐步提高的多数情况, 对高炉生产的 和一次计算唯一的区 别是 : 二次计算得到的是铁 程控制由过程控制级计算机系统, 二级系统完成。 求循序渐进、 二级系 统的工艺控制模型产生工艺设定值 , 工艺 过程控制, 设有手动和自 动两种操作状态 , 两种操 水脱硫站脱硫后传到转炉的铁水温度 和阎含量 , 设定值从二级系统传送到一级基础 自 动化系统 , 作状态之间, 可实现无扰动切换。 由工业微型计算 并根据此成份进行计算从而得 出更精确的结果。 . 1 由基础 自 动化系统控制转炉设备完成整个冶炼过 机和 P C L 系统、 计算机网络、 控制软件组成在线计 3 3液位测量。副枪通过专用的测量液位探头对 下位机通过各检测仪表, 采集高炉 铁水液位进行澳 量 其原理当探头接触到铁水时, 。 程, 工艺控制模型作为自 动化炼钢系 的关键 , 统 根 算机应用系统 , 配料运行数据、 炉体温度 、 风温、 风压 , 除尘 探头内电流导通, 系统记录下该位置数值。. 3. 1 4氧 据工艺 流程分别由加料计算(一次加料计算和二 上料 、 分 次加料计算潞 池液面计算, 烟气模型, 校正计算反 系统等工艺参数。 在手动操作模式下 , 上述工艺 气量模型氧气用量模型的计算。先根据铁水化学 再计算矿石 馈计算, 出钢合金化等模型组成。 参数经过 t 位机计算机处理, 使之成为清晰而精 成份计算吹炼该炉钢所需的氧气量 ; l 高炉炼铁 自 动化系统的构建 确的“ 软件仪表”将过去人工来不及分析的 、 , 各种 带入的氧量;最后根据上炉氧气利用率对该炉氧 从而得出该炉最终氧气用量 。 炼铁生产过程是在高炉内进行的一系列复 缺乏相关性的信息都能充分地利用起来,揭示出 气用量进行修正 , 杂的还原反应的过程 , ( 炉料 矿石 、 燃料和熔剂 ) 从 它们之间的内在联系, 从而对判断高炉生产过程 3 5合金计算模型(L 。 . 1 A U 合金计算模型是根据终 脱氧、合金化用合金 炉顶装入 , 从鼓风机来的冷风经热风炉加热后 , 形 和指导操作起到了 更多的作用。在 自 动操作模式 点钢水成份计算需要使用的 在使用合金模型时, 工程师预先将合金各有效 成高温热风从高炉风 口鼓人 ,随着焦炭燃烧产生 下 , 我们在常规 PD调节的基础之上 , I 增加了非线 量 , 自适应调节和智能控制等环节。 经 元素含量、 价格输 入=级系统, 待终点钢水成份化 的热煤气流自下而往上运动,而炉料则由上而往 性变参数凋节, 模型根据 目 标钢水 下运动互相接触进行热交换, 逐步还原 , 最后在炉 过计算机综合分析和建立数学模型 , 作为人工操 验出来后启动合金计算模型, 优化。 2动态计 3 子的下部还原成生铁 , 同时形成炉渣。积聚在炉缸 作或自动调节的依据, 并充分利用计算机储存信 成份和合金价格进行合金计算的 的铁水和炉渣, 分别由出铁口和出渣 口放出。高炉 息量大的优点, 为高炉的操作提供更准确、 更合理 算模型0 C O 】 BC R 。动态计算模型是当转炉吹氧量 0 自动化过程主要包含高炉本体控制、给料和配料 的控制策略。 3先进性。 X 采用智能控制技术 , 以改 达到 8 %时,副枪对钢水温度和碳含量进行吹炼 具 中测量 ,同时将测出的碳含量和温度值发送到二 控制、 热风炉控制 , 以及除尘系统控制等。高炉 自 容错性、 鲁棒性、 组织功能 , 自 具 级 , 并根据测得的数值对终 点 进行计算。 动态漠型 动化的 目 , 的 主要是保证高炉操作的四个主要问 有更好的适应性、 a b 计算终点碳 题: 正确配料并以一定的顺序及时装入炉内; 控制 有 自 学习能力、 更强的实时性租 人 机协同功能。 不 计算包括:计算动态过程的吹氧量。. a 炉料均匀下降; 调节炉料分布及保持其与热煤气 仅依靠单纯的数学模型, 而是能够根据知识和经 含量和终点温度。 计算补加冷却剂或升温剂加入 3 学习模型0 C。 学习模型是根据该炉 r )自 B 流的 呼接触; 保持高炉整体有合适的热状态。 高 验的积累, 进行在线推理, 做出非线性和多因素的 量 。 3 自 役内 各炉次生产情况对工艺模型参数进行适时调 炉 自动化系统主要包括仪表检测及控制系统 、 电 判断,从而优选出 气控制系统和过程及管理用计算机。仪表控制系 略。 通过记录、 分析高炉的 史生产数据, 采用‘ 整。 3 模型的调整基于以下原因: 炉炉衬的 忱 3. 1 a 转 h c 氧枪的更换。 热 统和电气控制系统通常由 D S P C完成。 C 或 L 高炉 选 图法”指导操作人员, , 使之确定的每一步动作 侵蚀。 氧枪喷嘴的磨损。 . 工操作 损失的变化。 氧气利用率。 P s e £ 和 在钢渣间分配 生产必须要求计算机控制系统能够很好地保证生 更加精确和科学。在这种状况较之传统 人 产过程的连续性和实时监控性,而且要求数据量 模式下, 高炉各操作参数的离散程度将明显缩小 , 系数。 2 3 2模型参数调整。 3 根据生产情况, 需要对 从目前情况看 , 需要调 最多, 所有设备的 自 动化程度要高。 计算机系统要 向着最佳区间 , 甚至最佳点靠拢的趋势将非常明 模型参数不断地进行优化, a 终点渣碱度。 终 c 求数据采集周期短 , 刷新速率快 , 特别对通讯网络 显。在系统更进一步优化后, 可实现多种“ 趋势分 整的数据为 :氧气利用率系数。 而言, 数据传输速率、 网络稳定性和正确性尤为重 析”计算机能够做出趋势预报, , 及时为操作者提 点渣氧化镁含量。 温度损失。 . d e 原辅料、 合金料成 要。 对检测仪表而言 , 也即对温度 、 压力、 、 差压 流 供更多的手段 , 相当于真正做到了类似于传统操 份的变化 量、 、 料位 重量的检测 , 要求数据的采集精确度 ≤ 作模式下 , 工艺管理上经常会提出“ 早调、 勤调、 少 结束语 目 国内大多钢铁企业公司都运用到 自 前 动 0 0, 集速率 ≤n S ./ 采 2o 8。 调” 的要求。 高炉生产过程在应用本系统后将更加 2高炉 自动化炼铁的特点 趋向稳定。 化炼钢技术 , 通过不断的摸索改进和生产实践 , 自 高炉的 自动化控制方案, 首先应着 眼于系统 3自 动化炼铁的 模型 动化炼钢都取得 良好的成果。 参 考文献 的可靠性、 l 实用 生 和先逆J 并在此基础上提高系 } 陛, 通过特点的介绍 , 我们可以总结出在 自 动化 统的性价比。 . 21可靠性。 高炉在钢铁厂生产中处 炼铁过程中常见的几 种模型。 . 静态模型。 .1 『解继峰, 3 1 3. 1 1 1 李子林, 自 安钢高速线材生产线简 赵 义. 手十分重要的位置,它不仅要及时稳定的给炼钢  ̄ 2 0. ( :446 1 ) - ( C。一次计算是利用转炉物料平衡和 介 轧钢,0 2 914 - . F ) C 工序提供合格的 铁水 , 还同时为轧钢加热炉提供 热平衡的原理 , 根据铁水成份、 温度、 重量和 目 标 [】 贞等. 2王雅 氧气顶吹转炉炼钢工艺与设备I . M1 北 煤气。高炉生产的短时间中断都会给整个生产流 钢水成份 、 温度、 重量以及��
自动化炼钢的原理及应用
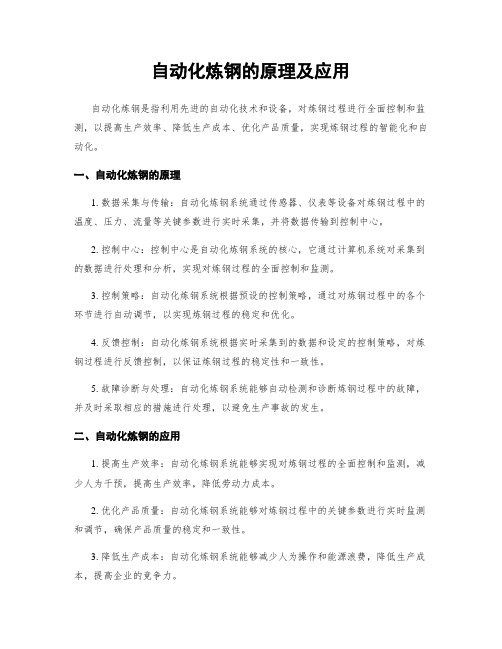
自动化炼钢的原理及应用自动化炼钢是指利用先进的自动化技术和设备,对炼钢过程进行全面控制和监测,以提高生产效率、降低生产成本、优化产品质量,实现炼钢过程的智能化和自动化。
一、自动化炼钢的原理1. 数据采集与传输:自动化炼钢系统通过传感器、仪表等设备对炼钢过程中的温度、压力、流量等关键参数进行实时采集,并将数据传输到控制中心。
2. 控制中心:控制中心是自动化炼钢系统的核心,它通过计算机系统对采集到的数据进行处理和分析,实现对炼钢过程的全面控制和监测。
3. 控制策略:自动化炼钢系统根据预设的控制策略,通过对炼钢过程中的各个环节进行自动调节,以实现炼钢过程的稳定和优化。
4. 反馈控制:自动化炼钢系统根据实时采集到的数据和设定的控制策略,对炼钢过程进行反馈控制,以保证炼钢过程的稳定性和一致性。
5. 故障诊断与处理:自动化炼钢系统能够自动检测和诊断炼钢过程中的故障,并及时采取相应的措施进行处理,以避免生产事故的发生。
二、自动化炼钢的应用1. 提高生产效率:自动化炼钢系统能够实现对炼钢过程的全面控制和监测,减少人为干预,提高生产效率,降低劳动力成本。
2. 优化产品质量:自动化炼钢系统能够对炼钢过程中的关键参数进行实时监测和调节,确保产品质量的稳定和一致性。
3. 降低生产成本:自动化炼钢系统能够减少人为操作和能源浪费,降低生产成本,提高企业的竞争力。
4. 提高安全性:自动化炼钢系统能够自动检测和诊断炼钢过程中的故障,及时采取措施进行处理,提高生产安全性。
5. 环保节能:自动化炼钢系统能够对炼钢过程中的能源消耗进行精确控制,减少能源浪费,降低对环境的影响。
6. 数据分析与优化:自动化炼钢系统能够对炼钢过程中的大量数据进行分析和优化,提供决策支持,匡助企业实现精益生产和持续改进。
总结:自动化炼钢通过先进的自动化技术和设备,实现对炼钢过程的全面控制和监测,提高生产效率、优化产品质量、降低生产成本、提高安全性和环保节能。
自动化炼钢的原理及应用
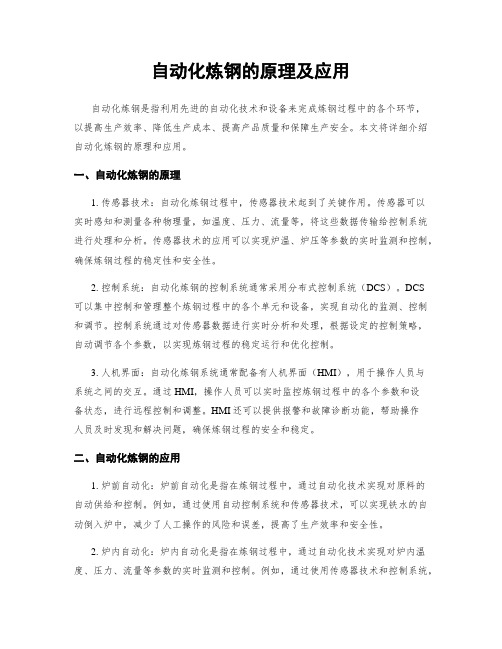
自动化炼钢的原理及应用自动化炼钢是指利用先进的自动化技术和设备来完成炼钢过程中的各个环节,以提高生产效率、降低生产成本、提高产品质量和保障生产安全。
本文将详细介绍自动化炼钢的原理和应用。
一、自动化炼钢的原理1. 传感器技术:自动化炼钢过程中,传感器技术起到了关键作用。
传感器可以实时感知和测量各种物理量,如温度、压力、流量等,将这些数据传输给控制系统进行处理和分析。
传感器技术的应用可以实现炉温、炉压等参数的实时监测和控制,确保炼钢过程的稳定性和安全性。
2. 控制系统:自动化炼钢的控制系统通常采用分布式控制系统(DCS)。
DCS可以集中控制和管理整个炼钢过程中的各个单元和设备,实现自动化的监测、控制和调节。
控制系统通过对传感器数据进行实时分析和处理,根据设定的控制策略,自动调节各个参数,以实现炼钢过程的稳定运行和优化控制。
3. 人机界面:自动化炼钢系统通常配备有人机界面(HMI),用于操作人员与系统之间的交互。
通过HMI,操作人员可以实时监控炼钢过程中的各个参数和设备状态,进行远程控制和调整。
HMI还可以提供报警和故障诊断功能,帮助操作人员及时发现和解决问题,确保炼钢过程的安全和稳定。
二、自动化炼钢的应用1. 炉前自动化:炉前自动化是指在炼钢过程中,通过自动化技术实现对原料的自动供给和控制。
例如,通过使用自动控制系统和传感器技术,可以实现铁水的自动倒入炉中,减少了人工操作的风险和误差,提高了生产效率和安全性。
2. 炉内自动化:炉内自动化是指在炼钢过程中,通过自动化技术实现对炉内温度、压力、流量等参数的实时监测和控制。
例如,通过使用传感器技术和控制系统,可以实现对炉内温度的自动调节,确保炉温在合理范围内,提高炼钢过程的稳定性和产品质量。
3. 炉后自动化:炉后自动化是指在炼钢过程中,通过自动化技术实现对产出产品的自动处理和控制。
例如,通过使用自动化设备和控制系统,可以实现对钢水的自动浇铸和冷却,减少了人工操作的风险和误差,提高了产品质量和生产效率。
炼钢厂转炉系统自动化控制
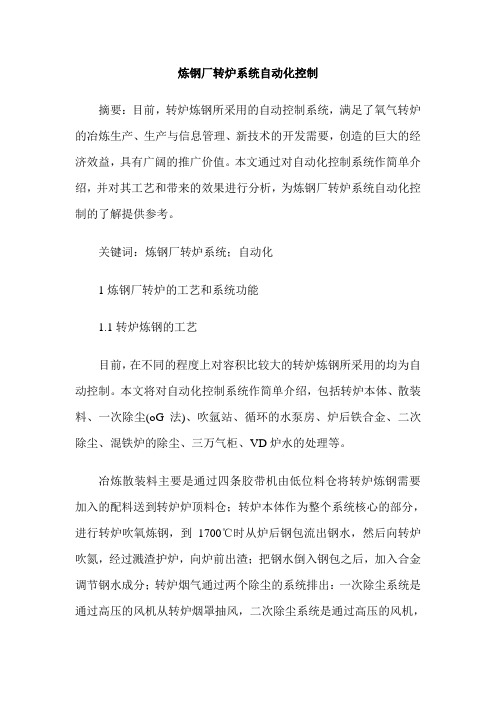
炼钢厂转炉系统自动化控制摘要:目前,转炉炼钢所采用的自动控制系统,满足了氧气转炉的冶炼生产、生产与信息管理、新技术的开发需要,创造的巨大的经济效益,具有广阔的推广价值。
本文通过对自动化控制系统作简单介绍,并对其工艺和带来的效果进行分析,为炼钢厂转炉系统自动化控制的了解提供参考。
关键词:炼钢厂转炉系统;自动化1炼钢厂转炉的工艺和系统功能1.1转炉炼钢的工艺目前,在不同的程度上对容积比较大的转炉炼钢所采用的均为自动控制。
本文将对自动化控制系统作简单介绍,包括转炉本体、散装料、一次除尘(oG 法)、吹氩站、循环的水泵房、炉后铁合金、二次除尘、混铁炉的除尘、三万气柜、VD炉水的处理等。
冶炼散装料主要是通过四条胶带机由低位料仓将转炉炼钢需要加入的配料送到转炉炉顶料仓;转炉本体作为整个系统核心的部分,进行转炉吹氧炼钢,到1700℃时从炉后钢包流出钢水,然后向转炉吹氮,经过溅渣护炉,向炉前出渣;把钢水倒入钢包之后,加入合金调节钢水成分;转炉烟气通过两个除尘的系统排出:一次除尘系统是通过高压的风机从转炉烟罩抽风,二次除尘系统是通过高压的风机,抽出天车从转炉倒入钢水的烟气。
1.2转炉系统功能系统对于生产全过程的情况进行监视,控制和管理的过程,这一点相较于过去的传统生产而言,更加精确的将生产过程中的数据进行了定位,检测,能够让操作人员对于生产过程中的实时参数更加的了解,这样转炉的运用就能够更加的高效和安全。
典型的转炉自动化控制系统的主要组成部分分为过程控制计算机,微型计算机和各种自动检测仪和电子称量装置等各个部分,这些部分共同组成了转炉的自动化系统,而且辅助系统还分为了供氧系统,原料系统和煤气回收系统等,这些都由计算机测控系统来检测。
计算机测控在本次研究中,采用的是PLC系列的产品,选择CPU 是系列中较为高性能的53414CPU型号,现场总线采用的是CRP系列产品,编程软件使用施奈德的产品Concept2.6。
系统自动化的过程主要设置三个级别来进行控制,首先是生产管理级别,然后是过程控制级别,最后是基础自动化级别,这些级别都是利用本次研究中的基础自动化控制级来进行编程的,这些自动化控制系统可以对炼钢厂转炉的数据进行采集,然后对于数据进行顺序的控制,监控的操作和通讯的各种过程控制,这些过程控制构成部分主要是由服务器,交换机和工作站等部分,这个系统自动化控制的试验数据主要是能够存储并且用于研究,所以系统自动化控制的价值还是非常重要的,实现了对于炼钢整个郭晨的参数科学化跟踪,能够对于数据进行分析和管理,整个系统的操作站是西门子的工业型号Win2000+SP3操作系统,性能卓越,能够通过以太网卡、双绞线与工业以太网相接。
钢铁行业智能炼钢技术

钢铁行业智能炼钢技术近年来,随着科技的不断发展和进步,智能化应用已经深入到各个行业中。
钢铁行业作为我国重要的基础产业之一,也不例外。
智能炼钢技术的引入和应用,为钢铁行业带来了新的发展机遇,促进了行业的转型升级。
一、智能炼钢技术的背景与意义钢铁行业是我国经济发展的重要支柱产业,对于国家的发展和国防建设具有重要意义。
但传统的炼钢技术存在一些问题,如资源消耗大、能源利用率低、环境污染等。
智能化技术的引入,可以提高钢铁生产的效率和质量,减少资源的浪费和环境的污染,从而实现可持续发展的目标。
二、智能炼钢技术的应用与案例1. 智能化设备控制系统智能化设备控制系统是实现智能炼钢的基础。
通过先进的传感器和控制技术,可以实时监测和控制炼钢过程中的温度、压力、流量等参数,保证炼钢过程的稳定性和精确性。
2. 智能炉温控制技术利用智能炉温控制技术,可以提高炼钢过程的温度控制精度和稳定性。
通过先进的算法和模型预测,以及对炉温的自动调整和反馈控制,可以有效提高炼钢的质量和生产效率。
3. 智能化质量检测技术智能化质量检测技术可以实时监测和分析炼钢产品的质量参数,包括成分、硫含量、氧含量等。
通过智能化质量检测技术,可以实现自动化检测和数据分析,提高产品质量的稳定性和可靠性。
4. 智能炼钢过程优化技术利用先进的数据分析和智能算法,可以对炼钢过程进行建模和优化。
通过实时监测和分析炼钢过程中的关键参数,调整和优化生产工艺,可以提高钢铁生产的效率和能源利用率,降低生产成本。
三、智能炼钢技术的影响与前景1. 提高生产效率引入智能炼钢技术可以提高生产效率,减少人工操作,提高生产线的稳定性和连续性。
通过数据的自动采集和分析,可以发现生产线中的问题和瓶颈,优化生产过程,提高生产能力和利润。
2. 降低生产成本智能炼钢技术可以实现对炼钢过程的精细化控制,减少资源的浪费和能源的消耗。
通过自动化设备和智能化管理,可以降低生产成本,提高经济效益。
3. 保护环境智能炼钢技术可以实现对废气和废水的处理,减少环境污染。
自动化炼钢的原理及应用
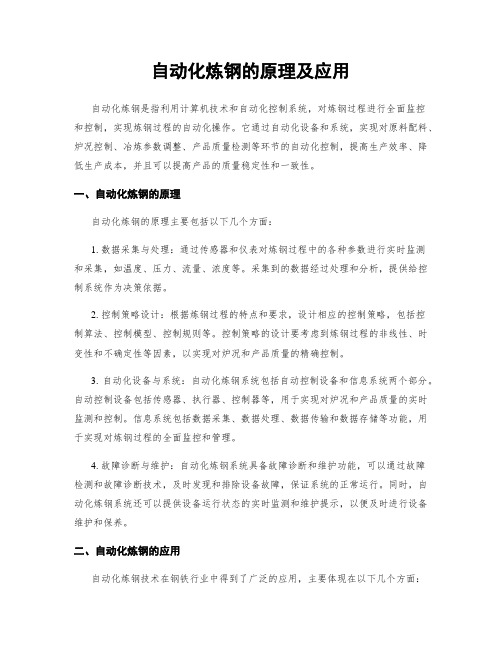
自动化炼钢的原理及应用自动化炼钢是指利用计算机技术和自动化控制系统,对炼钢过程进行全面监控和控制,实现炼钢过程的自动化操作。
它通过自动化设备和系统,实现对原料配料、炉况控制、冶炼参数调整、产品质量检测等环节的自动化控制,提高生产效率、降低生产成本,并且可以提高产品的质量稳定性和一致性。
一、自动化炼钢的原理自动化炼钢的原理主要包括以下几个方面:1. 数据采集与处理:通过传感器和仪表对炼钢过程中的各种参数进行实时监测和采集,如温度、压力、流量、浓度等。
采集到的数据经过处理和分析,提供给控制系统作为决策依据。
2. 控制策略设计:根据炼钢过程的特点和要求,设计相应的控制策略,包括控制算法、控制模型、控制规则等。
控制策略的设计要考虑到炼钢过程的非线性、时变性和不确定性等因素,以实现对炉况和产品质量的精确控制。
3. 自动化设备与系统:自动化炼钢系统包括自动控制设备和信息系统两个部分。
自动控制设备包括传感器、执行器、控制器等,用于实现对炉况和产品质量的实时监测和控制。
信息系统包括数据采集、数据处理、数据传输和数据存储等功能,用于实现对炼钢过程的全面监控和管理。
4. 故障诊断与维护:自动化炼钢系统具备故障诊断和维护功能,可以通过故障检测和故障诊断技术,及时发现和排除设备故障,保证系统的正常运行。
同时,自动化炼钢系统还可以提供设备运行状态的实时监测和维护提示,以便及时进行设备维护和保养。
二、自动化炼钢的应用自动化炼钢技术在钢铁行业中得到了广泛的应用,主要体现在以下几个方面:1. 原料配料:自动化炼钢系统可以根据生产计划和产品要求,自动进行原料的配料和投料。
通过对原料成分和比例的精确控制,可以提高产品质量的稳定性和一致性。
2. 炉况控制:自动化炼钢系统可以实时监测和控制炉况参数,如温度、压力、氧含量等。
通过自动控制设备和控制策略的配合,可以实现炉况的精确控制,提高炼钢过程的稳定性和安全性。
3. 冶炼参数调整:自动化炼钢系统可以根据产品质量要求和工艺要求,自动调整冶炼参数,如温度、时间、速度等。
自动化炼钢的原理及应用
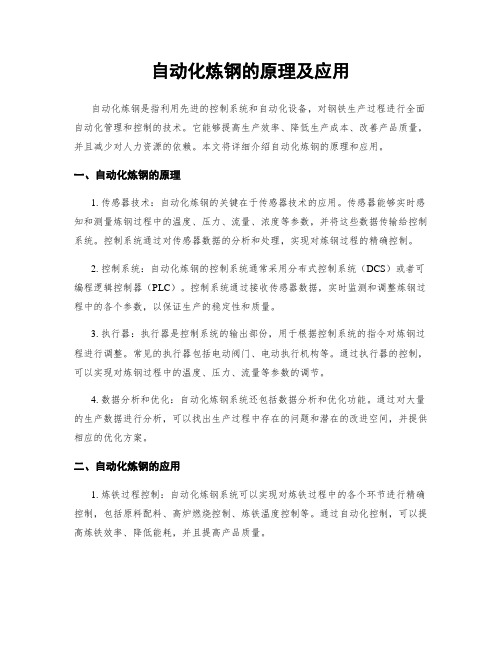
自动化炼钢的原理及应用自动化炼钢是指利用先进的控制系统和自动化设备,对钢铁生产过程进行全面自动化管理和控制的技术。
它能够提高生产效率、降低生产成本、改善产品质量,并且减少对人力资源的依赖。
本文将详细介绍自动化炼钢的原理和应用。
一、自动化炼钢的原理1. 传感器技术:自动化炼钢的关键在于传感器技术的应用。
传感器能够实时感知和测量炼钢过程中的温度、压力、流量、浓度等参数,并将这些数据传输给控制系统。
控制系统通过对传感器数据的分析和处理,实现对炼钢过程的精确控制。
2. 控制系统:自动化炼钢的控制系统通常采用分布式控制系统(DCS)或者可编程逻辑控制器(PLC)。
控制系统通过接收传感器数据,实时监测和调整炼钢过程中的各个参数,以保证生产的稳定性和质量。
3. 执行器:执行器是控制系统的输出部份,用于根据控制系统的指令对炼钢过程进行调整。
常见的执行器包括电动阀门、电动执行机构等。
通过执行器的控制,可以实现对炼钢过程中的温度、压力、流量等参数的调节。
4. 数据分析和优化:自动化炼钢系统还包括数据分析和优化功能。
通过对大量的生产数据进行分析,可以找出生产过程中存在的问题和潜在的改进空间,并提供相应的优化方案。
二、自动化炼钢的应用1. 炼铁过程控制:自动化炼钢系统可以实现对炼铁过程中的各个环节进行精确控制,包括原料配料、高炉燃烧控制、炼铁温度控制等。
通过自动化控制,可以提高炼铁效率、降低能耗,并且提高产品质量。
2. 炼钢过程控制:自动化炼钢系统可以实现对炼钢过程中的各个环节进行精确控制,包括转炉炼钢、电弧炉炼钢等。
通过自动化控制,可以提高炼钢效率、降低能耗,并且提高产品质量。
3. 质量控制:自动化炼钢系统可以实现对产品质量的精确控制。
通过对炼钢过程中的各个参数进行实时监测和调整,可以确保产品的成份、结构和性能符合要求。
4. 安全监测:自动化炼钢系统可以实现对炼钢过程中的安全监测。
通过对炼钢过程中的温度、压力、流量等参数进行实时监测,可以及时发现和处理潜在的安全隐患。
冶金自动化技术及其发展趋势
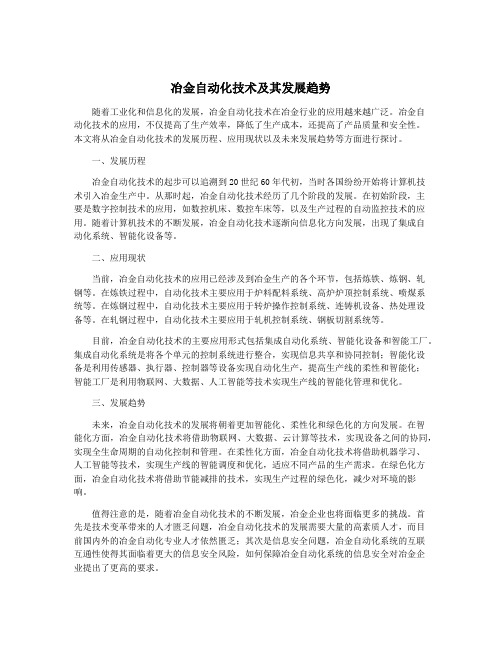
冶金自动化技术及其发展趋势随着工业化和信息化的发展,冶金自动化技术在冶金行业的应用越来越广泛。
冶金自动化技术的应用,不仅提高了生产效率,降低了生产成本,还提高了产品质量和安全性。
本文将从冶金自动化技术的发展历程、应用现状以及未来发展趋势等方面进行探讨。
一、发展历程冶金自动化技术的起步可以追溯到20世纪60年代初,当时各国纷纷开始将计算机技术引入冶金生产中。
从那时起,冶金自动化技术经历了几个阶段的发展。
在初始阶段,主要是数字控制技术的应用,如数控机床、数控车床等,以及生产过程的自动监控技术的应用。
随着计算机技术的不断发展,冶金自动化技术逐渐向信息化方向发展,出现了集成自动化系统、智能化设备等。
二、应用现状当前,冶金自动化技术的应用已经涉及到冶金生产的各个环节,包括炼铁、炼钢、轧钢等。
在炼铁过程中,自动化技术主要应用于炉料配料系统、高炉炉顶控制系统、喷煤系统等。
在炼钢过程中,自动化技术主要应用于转炉操作控制系统、连铸机设备、热处理设备等。
在轧钢过程中,自动化技术主要应用于轧机控制系统、钢板切割系统等。
目前,冶金自动化技术的主要应用形式包括集成自动化系统、智能化设备和智能工厂。
集成自动化系统是将各个单元的控制系统进行整合,实现信息共享和协同控制;智能化设备是利用传感器、执行器、控制器等设备实现自动化生产,提高生产线的柔性和智能化;智能工厂是利用物联网、大数据、人工智能等技术实现生产线的智能化管理和优化。
三、发展趋势未来,冶金自动化技术的发展将朝着更加智能化、柔性化和绿色化的方向发展。
在智能化方面,冶金自动化技术将借助物联网、大数据、云计算等技术,实现设备之间的协同,实现全生命周期的自动化控制和管理。
在柔性化方面,冶金自动化技术将借助机器学习、人工智能等技术,实现生产线的智能调度和优化,适应不同产品的生产需求。
在绿色化方面,冶金自动化技术将借助节能减排的技术,实现生产过程的绿色化,减少对环境的影响。
值得注意的是,随着冶金自动化技术的不断发展,冶金企业也将面临更多的挑战。
钢铁行业智能炼钢技术
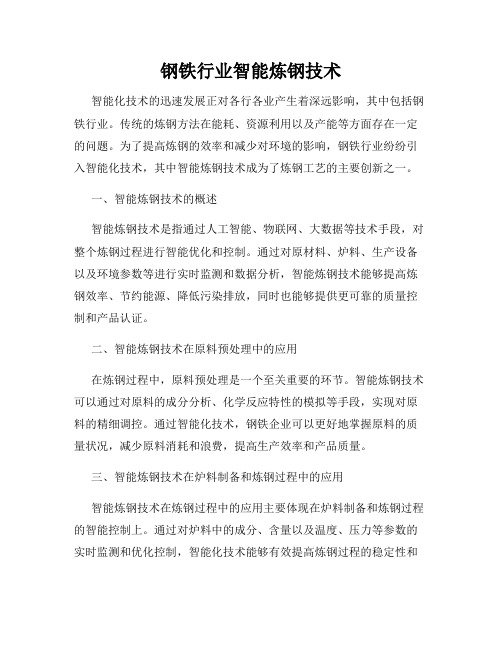
钢铁行业智能炼钢技术智能化技术的迅速发展正对各行各业产生着深远影响,其中包括钢铁行业。
传统的炼钢方法在能耗、资源利用以及产能等方面存在一定的问题。
为了提高炼钢的效率和减少对环境的影响,钢铁行业纷纷引入智能化技术,其中智能炼钢技术成为了炼钢工艺的主要创新之一。
一、智能炼钢技术的概述智能炼钢技术是指通过人工智能、物联网、大数据等技术手段,对整个炼钢过程进行智能优化和控制。
通过对原材料、炉料、生产设备以及环境参数等进行实时监测和数据分析,智能炼钢技术能够提高炼钢效率、节约能源、降低污染排放,同时也能够提供更可靠的质量控制和产品认证。
二、智能炼钢技术在原料预处理中的应用在炼钢过程中,原料预处理是一个至关重要的环节。
智能炼钢技术可以通过对原料的成分分析、化学反应特性的模拟等手段,实现对原料的精细调控。
通过智能化技术,钢铁企业可以更好地掌握原料的质量状况,减少原料消耗和浪费,提高生产效率和产品质量。
三、智能炼钢技术在炉料制备和炼钢过程中的应用智能炼钢技术在炼钢过程中的应用主要体现在炉料制备和炼钢过程的智能控制上。
通过对炉料中的成分、含量以及温度、压力等参数的实时监测和优化控制,智能化技术能够有效提高炼钢过程的稳定性和生产能力。
同时,智能炼钢技术还可以通过预测模型和优化算法,实现炼钢工艺的智能调整,提高炼钢工艺的适应性和灵活性。
四、智能炼钢技术在环境保护和能源利用方面的应用环境保护和节能减排是当前全球炼钢行业必须面对的重要课题。
智能炼钢技术可以通过对排放物的监测和控制,优化炼钢工艺和设备,降低排放物的含量和浓度,保护环境。
同时,智能炼钢技术还可以通过对能源利用的模拟和优化,提高能源利用率,降低能耗,实现可持续发展。
五、智能炼钢技术的挑战与前景智能炼钢技术的应用面临着一些挑战,包括技术成熟度、设备更新成本、数据安全等问题。
但是,智能炼钢技术的前景依然广阔。
随着人工智能、物联网等技术的不断进步和成熟,智能炼钢技术将在提高炼钢效率、保护环境、优化能源利用等方面发挥更大的作用。
- 1、下载文档前请自行甄别文档内容的完整性,平台不提供额外的编辑、内容补充、找答案等附加服务。
- 2、"仅部分预览"的文档,不可在线预览部分如存在完整性等问题,可反馈申请退款(可完整预览的文档不适用该条件!)。
- 3、如文档侵犯您的权益,请联系客服反馈,我们会尽快为您处理(人工客服工作时间:9:00-18:30)。
数据采集自动配料系统在冶炼中的运用杨利峰翟强(江苏沙钢集团有限公司张家港215625)摘要:本文详细介绍了通过OPC方式,实现访问底层功能的西门子PLC合金自动配料系统。
关键字:OPC, DCOM, S7-300, Visual Basic, ORACLE, 合金自动配料系统1. 前言在炼钢厂,合金消耗占整个产品制造成本很大的比重,因此准确反映合金消耗数据,对于测算生产成本显得极为必要。
而目前永新炼钢厂在合金加料控制系统中,采用人工记录的方式,统计数据的及时性、真实性、完整性不能得到很好的保证,这种条件下测算出的成本不能如实反映实际消耗,自然无法对降本降耗的攻关方向产生指导性作用。
近年来,随着PLC和自动控制技术的飞速发展,沙钢集团陆续对许多工厂进行了自动化系统改造,以实现底层数据采集和二级控制系统。
其中,在永新炼钢建设了一个数据采集自动配料监控系统,不仅能如实反映炼钢车间的合金消耗情况,而且能实现按炉进行自动数据采集,自动记录下炉批号、料仓号、合金名称、加料时间、加料重量等信息。
本文将对系统的构成,从以下几个方面进行详述。
2. 系统硬件组成以及功能需求原理图如图1所示:2.1 硬件组成简介本控制系统采用的PLC是西门子S7-300,配有类似于一个小型的DCS系统,包括数字量输出/数字量输入各俩块,模拟量俩块,以太网模块和电源模块和CPU 315模块等。
上位机是一台工控机,可实现监视管理,并能把采集到的数据自动传递给服务器,下层通过PLC完成自动配料计算,并可实现报警控制。
S7-300 PLC功能强大,运行稳定,可以满足大规模控制系统的要求。
系统由一套S7-300 PLC、一台工控机(画面监视)和一台数据采集服务器组成。
其中,工控机(监视机画面)与PLC之间采用以太网进行连结,并通过以太网总线把数据发送到车间的服务器上。
秤的量程范围为0~3000公斤,输出信号为4~20MA,由于现场环境恶劣,所以采用了信号隔离器,以确保输入到PLC信号的稳定。
现场控制电动机的变频器(日本安川),速度设置为二级,一级采用工频50HZ-1400r/min,二级设定25HZ-700r/min。
用PLC控制二级速度。
2.2 功能需求简介1) 按炉进行数据采集,记录炉批号,料斗号,合金名称,加料时间,加料重量等信息。
2) 按倒钢信号进行炉批号的自动累加,及时进行人工确认。
3) 数据库存放到数据库中,可以按炉,按日,按班,按月等要求进行数据统计和汇总工作。
4) 在采集一个炉子当中,记录出钢时间,进料时间等信息并生成报表。
3. 软件功能的实现3.1 PLC编程软件(1)本软件采用西门子自带编程软件(STEP7 V5.2)进行编程,在整个PLC程序中通过组织块OB1、功能块FB1、功能FC10、数据块DB10等来实现合金上料控制和合金数据记录的目的。
FB1:合金上料控制功能块FC10:合金数据记录功能块DB10:合金数据记录数据块图2 S7-300 PLC内部程序块调用示意图(2)为顺利实现数据采集,主要采用的方法有:a.通过控制现场振动仓电机的接触器来判断目前哪个合金仓在加料;b.通过控制现场向大包和电炉加合金的行程开关来判断是向大包加合金还是在向电炉加合金;c.通过合金电子称数据的变化,来计算并记录合金加入数据;d.通过S7-300 PLC内部功能块FC10的加减乘除运算,来准确记录各个料仓每次加入的合金重量;e.通过S7-300 PLC内部功能块FC10的运算,再将运算结果保存在S7-300 PLC内,由DB10数据块的合金数据和人工界面相联接,并将数据传输到VB的画面上;f.为保证每炉钢PLC内数据的刷新,S7-300 PLC程序取电炉倒钢结束快回信号,为清除DB10数据块内上一炉的数据,把这一炉的数据保存到数据库;g.加料时间的记录。
S7-300 PLC在现场料仓电机振动的瞬间,取一数字量信号,通过标准功能块的运用,记录下开始加料的时间。
(3)自动配料部分:假设操作工在人机画面发送500公斤数据到PLC中,其中50公斤为精配料(为经验数据):a. 秤上的数据<0~(500-50)>公斤时,进行快速配料(工频50HZ)。
通过数字量来设置变频器。
b. 秤上的数据<(500-50)~500>公斤时,进行精细配料(工频25HZ)。
通过数字量来设置变频器。
3.2 OPC;DCOM(1)服务器软件采用西门子软件自带的OPC SERVER,通过一系列硬件配置下载到PLC中。
(2)客户端(工控机)通过DCOM来访问OPC SERVER中的点。
(如图3所示)。
图3 OPC Server 和Opc client 之间的访问(3)OPC是用于过程控制的OLE的简称,它是基于DCOM技术的一种开放试系统接口标准。
设备与不同PLC供应商的应用程序之间所进行的数据交换可通过一个接口进行。
它是一个技术规范。
OPC是连接现场总线信号与监控软件的桥梁,有了它做为通用接口,就可以把现场信号与上位监控,人机界面软件方便链结起来,还可以把它们与PC机的某些通用开发平台和应用软件平台链结起来,像Visual Basic ,Delphi,Visual C++等。
3.3 上位机软件上位机软件采用Microsoft VisuaL Basic进行编程,该语言被广泛应用于各种软件的开发,具有以下优点:(1)COM (分布组件对象管理)提供了最完备和高效的Windows基础类库,可提供对Widows系统平台上所需要的全方位的支持;(2)是基于组件设计和可视化的开发环境;(3)语言简单,开发容易;(4)对数据查询提供了极其方便的控件,可通过ODBC访问来实现与Oracle数据库的接口;(5)通过OPC接口的初始化来访问PLC中的点,具体代码如下:Dim OutText As StringOn Error GoTo ErrorHandlerCommand_Start.Enabled = FalseCommand_Read.Enabled = TrueCommand_Write.Enabled = TrueCommand_Exit.Enabled = TruechkGroupActive.Enabled = TrueOutText = "Connecting to OPC-Server"Set ServerObj = New OPCServerServerObj.Connect ("OPC.SimaticNET")//OPC SERVER的名字OutText = "Adding a Group to OPC-Server"Set GroupObj = ServerObj.OPCGroups.Add("MyOPCGroup")//定义GROOPGroupObj.IsSubscribed = TrueChkGroupActive_ClickOutText = "Adding Items to the group"Set ItemObj1 = GroupObj.OPCItems.AddItem("S7:[DEMO]MB1", 1) //定义Item Set ItemObj2 = GroupObj.OPCItems.AddItem("S7:[DEMO]MW3", 2)Serverhandle(1) = ItemObj1.ServerhandleServerhandle(2) = ItemObj2.Serverhandle(6)软件画面如图4所示:图4 合金上料人机界面3.4 数据库和报表数据库是整个管理信息系统的核心。
数据的分析计算都是在数据库中完成的,包括数据存储、数据查询、统计报表等。
因此数据库的安全性和稳定性是十分重要的。
本数据库采用的是甲骨文公司的数据库----Oracle。
数据的记录都是根据上升沿信号来的,信号一到就保存到数据库里。
记录时间,数量等一些信息。
而报表采用Oracle公司自带的报表开发工具Report6i来作的。
如下图所示:图5 合金上料报表界面3.5 注意点1,该程序在运行一段时间后,突然有一天仪器仪表的数据在PLC里突然跳到最大量,以后数据一直不变,经过分析以后仪表没有坏,而输出的信号为最大值,且一直不变,经过商议以后,加了一块信号隔离器以后,故障消失。
2,炉批号的选取,我们选取出钢结束信号为炉批号标志,然后把各个料仓的数据,记录到数据库里面。
但是经过观察,数据库里的料仓记录时间(各个料仓所称重的数据)和出钢结束时间却有点问题,料仓记录时间提前出钢结束时间,这是不对的,因为料仓里的料还没有结束,就已经开始记录到数据库里了,4、用户评语本系统开发完成之后,通过一段时间的应用,发现该系统能满足系统设计的要求,能准确计算出合金的实际消耗,可以及时反映出炼钢成本的变化趋势,便于质量分析和成本分析,进而实现成本有效控制,而且操作简单,为此得到了炼钢车间使用人员的一致好评。
5、结束语OPC技术由于数据交互能力快,已逐步代替Ifix、Intouch等昂贵的组态软件,成为工业软件的主流。
西门子PLC也因价格便宜、软件免费, 处理速度快,接口开放等特点,超出同类PLC。
特别在钢铁企业中西门子PLC更加运用的广泛。
作者简介:杨利峰,男,1979年5月21日生,助理工程师,江苏沙钢集团有限公司自动化研究所从事底层数据采集工作。