Epitaxial Y-stabilized ZrO2 on silicon Dynamic growth process and interface structure
一种磷酸肽固相萃取小柱及制备和应用
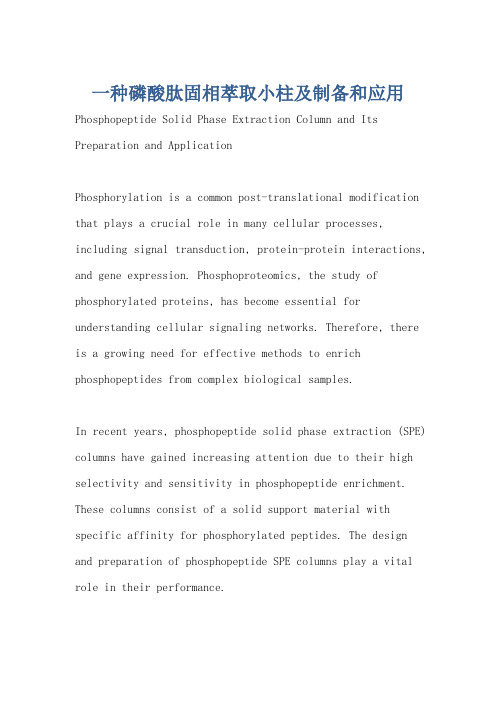
一种磷酸肽固相萃取小柱及制备和应用Phosphopeptide Solid Phase Extraction Column and Its Preparation and ApplicationPhosphorylation is a common post-translational modification that plays a crucial role in many cellular processes, including signal transduction, protein-protein interactions, and gene expression. Phosphoproteomics, the study of phosphorylated proteins, has become essential for understanding cellular signaling networks. Therefore, there is a growing need for effective methods to enrich phosphopeptides from complex biological samples.In recent years, phosphopeptide solid phase extraction (SPE) columns have gained increasing attention due to their high selectivity and sensitivity in phosphopeptide enrichment. These columns consist of a solid support material with specific affinity for phosphorylated peptides. The design and preparation of phosphopeptide SPE columns play a vital role in their performance.To prepare the phosphopeptide SPE column, several key factors need to be considered. Firstly, the selection of the solid support material is critical. It should have high surface area and good chemical stability to ensureefficient adsorption and desorption of phosphopeptides. Silica-based materials, such as titanium dioxide (TiO2) or zirconium dioxide (ZrO2), are commonly used due to their excellent binding capacity for phosphopeptides.Secondly, the surface modification of the solid support material is necessary to enhance its selectivity towards phosphopeptides. This can be achieved by introducing metal ions or metal oxides onto the support surface through various chemical reactions. For example, immobilizingferric ions onto TiO2 can greatly improve its affinity for phosphopeptides.Thirdly, optimizing the binding conditions is crucial for achieving high recovery rates and minimizing non-specific interactions. Factors such as pH, salt concentration, and organic solvent content should be carefully adjusted to facilitate selective enrichment of phosphopeptides.After preparing the phosphopeptide SPE column, it can be applied in various proteomic studies. One commonapplication is the enrichment of phosphopeptides from complex protein digests prior to mass spectrometry analysis. This allows for the identification and quantification of phosphorylated peptides, which play important roles in cellular signaling pathways.Moreover, phosphopeptide SPE columns can also be used for phosphoproteome profiling, where the complete set of phosphorylated proteins in a biological sample is analyzed. By selectively enriching phosphopeptides, the complexity of the sample can be reduced, improving the detection and identification of low-abundance phosphoproteins.In conclusion, the development and application of phosphopeptide SPE columns have significantly contributedto the field of phosphoproteomics. These columns provide a powerful tool for enriching and analyzing phosphorylated peptides in complex biological samples. The optimization of column preparation parameters and binding conditions iscrucial for achieving high recovery rates and improved selectivity. Therefore, further research in this area is necessary to enhance and expand their applications in proteomic studies.磷酸肽固相萃取小柱及其制备和应用磷酸化是一种常见的蛋白质翻译后修饰,在细胞信号传导、蛋白质相互作用和基因表达等许多细胞过程中起着至关重要的作用。
三氧化二钇稳定二氧化锆
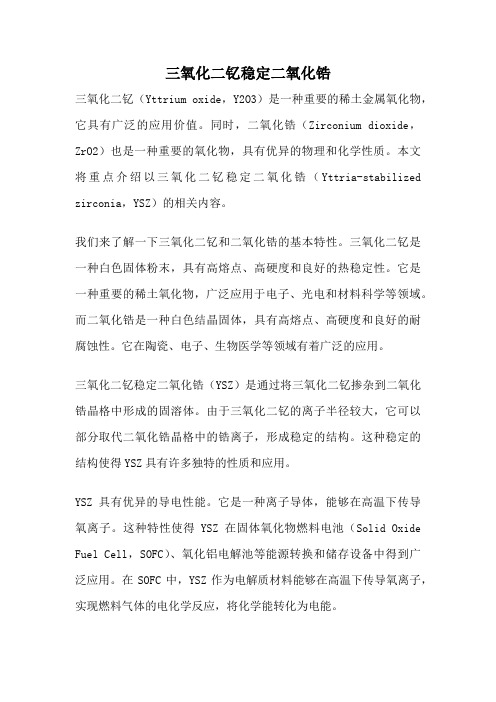
三氧化二钇稳定二氧化锆三氧化二钇(Yttrium oxide,Y2O3)是一种重要的稀土金属氧化物,它具有广泛的应用价值。
同时,二氧化锆(Zirconium dioxide,ZrO2)也是一种重要的氧化物,具有优异的物理和化学性质。
本文将重点介绍以三氧化二钇稳定二氧化锆(Yttria-stabilized zirconia,YSZ)的相关内容。
我们来了解一下三氧化二钇和二氧化锆的基本特性。
三氧化二钇是一种白色固体粉末,具有高熔点、高硬度和良好的热稳定性。
它是一种重要的稀土氧化物,广泛应用于电子、光电和材料科学等领域。
而二氧化锆是一种白色结晶固体,具有高熔点、高硬度和良好的耐腐蚀性。
它在陶瓷、电子、生物医学等领域有着广泛的应用。
三氧化二钇稳定二氧化锆(YSZ)是通过将三氧化二钇掺杂到二氧化锆晶格中形成的固溶体。
由于三氧化二钇的离子半径较大,它可以部分取代二氧化锆晶格中的锆离子,形成稳定的结构。
这种稳定的结构使得YSZ具有许多独特的性质和应用。
YSZ具有优异的导电性能。
它是一种离子导体,能够在高温下传导氧离子。
这种特性使得YSZ在固体氧化物燃料电池(Solid Oxide Fuel Cell,SOFC)、氧化铝电解池等能源转换和储存设备中得到广泛应用。
在SOFC中,YSZ作为电解质材料能够在高温下传导氧离子,实现燃料气体的电化学反应,将化学能转化为电能。
YSZ具有优异的热稳定性和化学稳定性。
它能够在高温下保持结构的稳定性,并且能够抵抗化学腐蚀。
这使得YSZ在高温熔体电解池、高温炉和电子器件等领域有着广泛的应用。
在高温熔体电解池中,YSZ作为电解质材料能够在高温下传导氧离子,实现熔融盐的电解和分解,从而实现金属的提取和精炼。
YSZ还具有优异的机械性能和热膨胀性能。
它具有高硬度和优异的抗磨损性能,能够耐受高温和高压环境的考验。
这些特性使得YSZ 在陶瓷制品、热障涂层和高温结构材料等领域得到广泛应用。
在陶瓷制品中,YSZ作为添加剂能够提高陶瓷的强度和耐磨性,使其具有更好的性能和寿命。
一种锂离子电池用聚酰亚胺粘结剂及其制备方法

一种锂离子电池用聚酰亚胺粘结剂及其制备方法1. 引言1.1 背景介绍传统的聚酰亚胺材料具有优异的热稳定性、机械性能和化学稳定性,但在电池中的应用受到限制。
通过将聚酰亚胺与导电剂等材料结合,制备出聚酰亚胺粘结剂,可以有效提高电池的循环寿命、安全性和性能稳定性。
聚酰亚胺粘结剂在锂离子电池中的应用不仅能够提高电池的电化学性能,还能够减少电极材料的脱落和固液界面的电荷传递阻抗,从而提高电池的能量密度和循环寿命。
在本文中,将介绍一种新型的聚酰亚胺粘结剂的制备方法,探讨其在锂离子电池中的应用及其性能与优势,并通过实验结果与讨论分析影响因素,最终总结展望未来研究方向。
【背景介绍】1.2 研究意义研究聚酰亚胺粘结剂在锂离子电池中的应用具有重要的意义。
聚酰亚胺粘结剂可以有效提高锂离子电池的循环稳定性和安全性能,延长电池的使用寿命。
聚酰亚胺粘结剂的优异性能可以提高锂离子电池的能量密度和功率密度,改善电池的性能指标。
研究聚酰亚胺粘结剂在锂离子电池中的应用,有助于减少电池的成本,推动锂离子电池技术的发展和进步,促进可再生能源的普及和应用。
深入研究聚酰亚胺粘结剂在锂离子电池中的应用具有重要的科学意义和工程应用价值。
2. 正文2.1 聚酰亚胺粘结剂的制备方法聚酰亚胺粘结剂是一种在锂离子电池中广泛应用的重要材料,其制备方法直接影响着其性能和应用效果。
通常,聚酰亚胺粘结剂的制备方法包括以下几个步骤:1. 原料准备:首先需要准备聚酰亚胺基体材料、溶剂和交联剂等原料。
这些原料的选择和质量直接影响着后续制备过程和成品质量。
2. 溶解:将聚酰亚胺基体材料和溶剂按一定配比混合后,在一定温度下进行搅拌和加热溶解,直至形成均匀的溶液。
3. 添加交联剂:在溶液中适量加入交联剂,并继续搅拌混合,使交联剂均匀分散在溶液中。
4. 涂覆或浸渍:将制备好的聚酰亚胺粘结剂溶液涂覆在锂离子电池的正负极材料上,或者直接浸渍在材料中,使其充分渗透并固定在材料表面。
硅外延及其应用
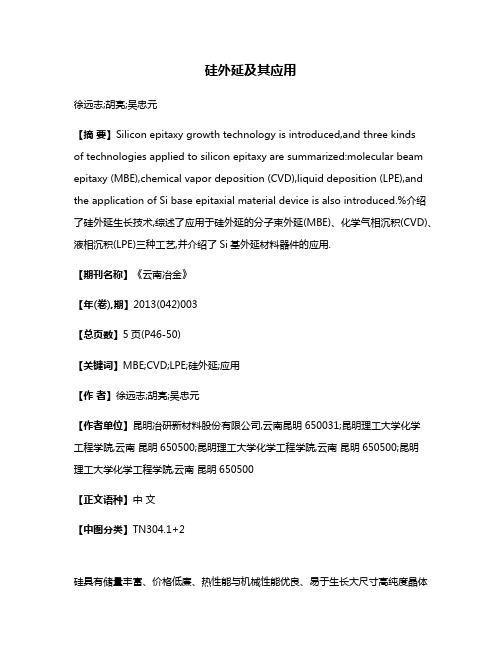
硅外延及其应用徐远志;胡亮;吴忠元【摘要】Silicon epitaxy growth technology is introduced,and three kindsof technologies applied to silicon epitaxy are summarized:molecular beam epitaxy (MBE),chemical vapor deposition (CVD),liquid deposition (LPE),and the application of Si base epitaxial material device is also introduced.%介绍了硅外延生长技术,综述了应用于硅外延的分子束外延(MBE)、化学气相沉积(CVD)、液相沉积(LPE)三种工艺,并介绍了Si基外延材料器件的应用.【期刊名称】《云南冶金》【年(卷),期】2013(042)003【总页数】5页(P46-50)【关键词】MBE;CVD;LPE;硅外延;应用【作者】徐远志;胡亮;吴忠元【作者单位】昆明冶研新材料股份有限公司,云南昆明650031;昆明理工大学化学工程学院,云南昆明650500;昆明理工大学化学工程学院,云南昆明650500;昆明理工大学化学工程学院,云南昆明650500【正文语种】中文【中图分类】TN304.1+2硅具有储量丰富、价格低廉、热性能与机械性能优良、易于生长大尺寸高纯度晶体等优点。
目前,硅半导体材料仍是电子信息产业最主要的基础材料,95%以上的半导体器件和99%以上的集成电路(IC)是用硅材料制作的。
在21 世纪,它的主导和核心地位仍不会动摇。
半导体制造商生产IC 芯片用硅片分别采用硅抛光片(PW)和硅外延片以及非抛光片三种类型,用量最多的为前二类硅片。
半导体硅材料自从60 年代被广泛应用于各类电子元器件以来,其用量保持高速增长。
SEMI(国际半导体设备与材料协会)报告预测了晶圆的需求前景,2013 年预计99.95 亿in2 (不包括非抛光硅片)。
liquid–liquid phase separation
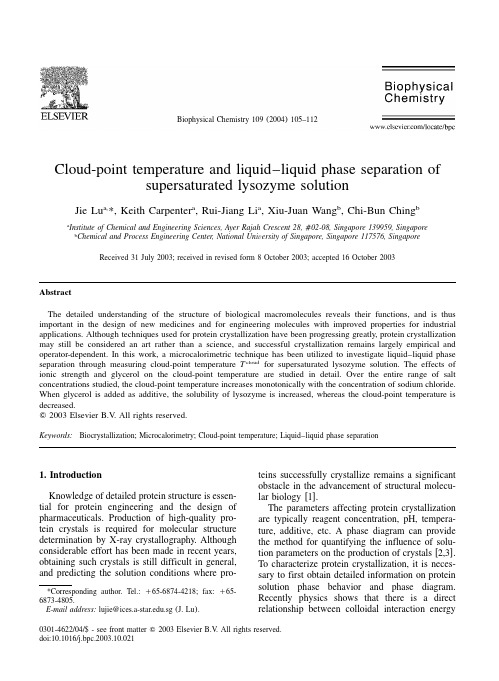
Biophysical Chemistry 109(2004)105–1120301-4622/04/$-see front matter ᮊ2003Elsevier B.V .All rights reserved.doi:10.1016/j.bpc.2003.10.021Cloud-point temperature and liquid–liquid phase separation ofsupersaturated lysozyme solutionJie Lu *,Keith Carpenter ,Rui-Jiang Li ,Xiu-Juan Wang ,Chi-Bun Ching a ,a a b bInstitute of Chemical and Engineering Sciences,Ayer Rajah Crescent 28,࠻02-08,Singapore 139959,Singapore aChemical and Process Engineering Center,National University of Singapore,Singapore 117576,SingaporebReceived 31July 2003;received in revised form 8October 2003;accepted 16October 2003AbstractThe detailed understanding of the structure of biological macromolecules reveals their functions,and is thus important in the design of new medicines and for engineering molecules with improved properties for industrial applications.Although techniques used for protein crystallization have been progressing greatly,protein crystallization may still be considered an art rather than a science,and successful crystallization remains largely empirical and operator-dependent.In this work,a microcalorimetric technique has been utilized to investigate liquid–liquid phase separation through measuring cloud-point temperature T for supersaturated lysozyme solution.The effects of cloud ionic strength and glycerol on the cloud-point temperature are studied in detail.Over the entire range of salt concentrations studied,the cloud-point temperature increases monotonically with the concentration of sodium chloride.When glycerol is added as additive,the solubility of lysozyme is increased,whereas the cloud-point temperature is decreased.ᮊ2003Elsevier B.V .All rights reserved.Keywords:Biocrystallization;Microcalorimetry;Cloud-point temperature;Liquid–liquid phase separation1.IntroductionKnowledge of detailed protein structure is essen-tial for protein engineering and the design of pharmaceuticals.Production of high-quality pro-tein crystals is required for molecular structure determination by X-ray crystallography.Although considerable effort has been made in recent years,obtaining such crystals is still difficult in general,and predicting the solution conditions where pro-*Corresponding author.Tel.:q 65-6874-4218;fax:q 65-6873-4805.E-mail address:lujie@.sg (J.Lu ).teins successfully crystallize remains a significant obstacle in the advancement of structural molecu-lar biology w 1x .The parameters affecting protein crystallization are typically reagent concentration,pH,tempera-ture,additive,etc.A phase diagram can provide the method for quantifying the influence of solu-tion parameters on the production of crystals w 2,3x .To characterize protein crystallization,it is neces-sary to first obtain detailed information on protein solution phase behavior and phase diagram.Recently physics shows that there is a direct relationship between colloidal interaction energy106J.Lu et al./Biophysical Chemistry109(2004)105–112and phase diagram.Gast and Lekkerkerker w4,5x have indicated that the range of attraction between colloid particles has a significant effect on the qualitative features of phase diagram.A similar relationship should hold for biomacromolecules, i.e.the corresponding interaction potentials govern the macromolecular distribution in solution,the shape of the phase diagram and the crystallization process w6x.Many macromolecular crystallizations appear to be driven by the strength of the attractive interactions,and occur in,or close to,attractive regimes w7,8x.Recent intensive investigation has revealed that protein or colloidal solution possesses a peculiar phase diagram,i.e.liquid–liquid phase separation and sol–gel transition exists in general in addition to crystallization w9,10x.The potential responsible for the liquid–liquid phase separation is a rather short range,possibly van der Waals,attractive potential w11,12x.The measurement of cloud-point temperature T can provide useful informationcloudon the net attractive interaction between protein molecules,namely,the higher the cloud-point tem-perature,the greater the net attractive interaction. Herein Taratuta et al.w13x studied the effects of salts and pH on the cloud-point temperature of lysozyme.Broide et al.w14x subsequently meas-ured the cloud-point temperature and crystalliza-tion temperature for lysozyme as a function of salt type and concentration.From these works the cloud-point temperature was found to be typically 15–458C below the crystallization temperature. Furthermore,Muschol and Rosenberger w15x deter-mined the metastable coexistence curves for lyso-zyme through cloud-point measurements,and suggested a systematic approach to promote pro-tein crystallization.In general,an effective way to determine the strength of protein interactions is to study temperature-induced phase transitions that occur in concentrated protein solutions.Liquid–liquid phase separation can be divided into two stages w11x:(1)the local separation stage at which the separation proceeds in small regions and local equilibrium is achieved rapidly;and(2) the coarsening stage at which condensation of these small domains proceeds slowly to reduce the loss of interface free energy w16x.The coexisting liquid phases both remain supersaturated but differ widely in protein concentration.The effect of a metastable liquid–liquid phase separation on crystallization remains ambiguous w17x.Molecular dynamics simulations and analyt-ical theory predict that the phase separation will affect the kinetics and the mechanisms of protein crystal nucleation w18x.tenWolde and Frenkel w19x have demonstrated that the free energy barrier for crystal nucleation is remarkably reduced at the critical point of liquid–liquid phase separation, thus in general,after liquid–liquid phase separa-tion,crystallization occurs much more rapidly than in the initial solution,which is typically too rapid for the growth of single crystal with low defect densities w15x.The determination of the location of liquid–liquid phase separation curve is thus crucial for efficiently identifying the optimum solution conditions for growing protein crystals. Microcalorimetry has the potential to be a useful tool for determining:(1)the metastable-labile zone boundary;(2)the temperature-dependence of pro-tein solubility in a given solvent;and(3)the crystal-growth rates as a function of supersatura-tion w20x.Microcalorimeters can detect a power signal as low as a few microwatts whereas standard calorimeters detect signals in the milliwatt range. Because of this greater sensitivity,samples with small heat effects can be analyzed.In addition, microcalorimetry has the advantage of being fast, non-destructive to the protein and requiring a relatively small amount of material.The present work is concerned with the analysis of the transient heat signal from microcalorimeter to yield liquid–liquid phase separation information for lysozyme solutions at pH4.8.To further examine the role of salt and additive on interprotein interactions, cloud-point temperature T has been determinedcloudexperimentally as a function of the concentrations of salt,protein and glycerol.2.Materials and methods2.1.MaterialsSix times crystallized lysozyme was purchased from Seikagaku Kogyo,and used without further107J.Lu et al./Biophysical Chemistry 109(2004)105–112purification.All other chemicals used were of reagent grade,from Sigma Chemical Co.2.2.Preparation of solutionsSodium acetate buffer (0.1M )at pH 4.8was prepared with ultrafiltered,deionized water.Sodi-um azide,at a concentration of 0.05%(w y v ),was added to the buffer solution as an antimicrobial agent.Protein stock solution was prepared by dissolving protein powder into buffer.To remove undissolved particles,the solution was centrifuged in a Sigma centrifuge at 12000rev.y min for 5–10min,then filtered through 0.22-m m filters (Mil-lex-VV )into a clean sample vial and stored at 48C for further experiments.The concentration of protein solution was determined by measuring the absorbance at 280nm of UV spectroscopy (Shi-madzu UV-2550),with an extinction coefficient of 2.64ml y (mg cm )w 21x .Precipitant stock solution was prepared by dissolving the required amount of sodium chloride together with additive glycerol into buffer.The pH of solutions was measured by a digital pH meter (Mettler Toledo 320)and adjusted by the addition of small volumes of NaOH or HAc solution.2.3.Measurement of solubilitySolubility of lysozyme at various temperatures and precipitant y additive concentrations was meas-ured at pH 4.8in 0.1M acetate buffer.Solid–liquid equilibrium was approached through both crystallization and dissolution.Dissolving lasted 3days,while the period of crystallization was over 2weeks.The supernatant in equilibrium with a macroscopically observable solid was then filtered through 0.1-m m filters (Millex-VV ).The concen-tration of diluted supernatant was determined spec-troscopically and verified by refractive meter(Kruss)until refractive index remained unchanged ¨at equilibrium state.Solubility of each sample was measured in duplicate.2.4.Differential scanning microcalorimetry Calorimetric experiments were performed with a micro-differential scanning calorimeter with anultra sensitivity,micro-DSC III,from Setaram SA,France.The micro-DSC recorded heat flow in microwatts vs.temperature,thus can detect the heat associated with phase transition during a temperature scan.The sample made up of equal volumes of protein solution and precipitant solu-tion was filtered through 0.1-m m filters to remove dust particles further.To remove the dissolved air,the sample was placed under vacuum for 3min while stirring at 500rev.y min by a magnetic stirrer.The degassed sample was placed into the sample cell of 1.0ml,and a same concentration NaCl solution was placed into the reference cell.The solutions in the micro-DSC were then cooled at the rate of 0.28C y min.After every run,the cells were cleaned by sonicating for 10–15min in several solutions in the following order:deionized water,methanol,ethanol,acetone,1M KOH and finally copious amounts of deionized water.This protocol ensured that lysozyme was completely removed from the cells.The cells were then placed in a drying oven for several hours.The rubber gaskets were cleaned in a similar manner except acetone and 1M KOH were omitted and they were allowed to dry at low temperature.3.Results and discussionA typical micro-DSC scanning experiment is shown in Fig.1.The onset of the clouding phe-nomenon is very dramatic and easily detected.The sharp increase in the heat flow is indicative of a liquid–liquid phase separation process producing a latent heat.This is much consistent with many recent investigations of the liquid–liquid phase separation of lysozyme from solution w 22,23x .In fact,such a liquid–liquid phase separation is a phase transition with an associated latent heat of demixing.In this work,the cloud-point tempera-tures at a variety of lysozyme,NaCl and glycerol concentrations are determined by the micro-DSC at the scan rate of 128C y h.3.1.Effect of protein concentrationIn semilogarithmic Fig.2we plot the solid–liquid and liquid–liquid phase boundaries for lyso-108J.Lu et al./Biophysical Chemistry 109(2004)105–112Fig.1.Heat flow of a typical micro-DSC scan of lysozyme solution,50mg y ml,0.1M acetate buffer,pH 4.8,3%NaCl.The scan rate 128C y h is chosen referenced to the experimental results of Darcy and Wiencek w 23x .Note the large deflection in the curve at approximately 4.38C indicating a latent heat resulting from demixing (i.e.liquid–liquid phase separation )process.Fig.2.Cloud-point temperature and solubility determination for lysozyme in 0.1M acetate buffer,pH 4.8:solubility (5%NaCl )(s );T (5%NaCl,this work )(d );T (5%cloud cloud NaCl,the work of Darcy and Wiencek w 23x )(*);solubility (3%NaCl )(h );T (3%NaCl )(j ).cloud Fig.3.Cloud-point temperature determination for lysozyme as a function of the concentration of sodium chloride,50mg y ml,0.1M acetate buffer,pH 4.8.zyme in 0.1M acetate buffer,pH 4.8,for a range of protein concentrations.It is worth noting that,at 5%NaCl,our experimental data of T from cloud micro-DSC are quite consistent with those from laser light scattering and DSC by Darcy and Wiencek w 23x ,with difference averaging at approx-imately 0.88C.This figure demonstrates that liquid–liquid phase boundary is far below solid–liquid phase boundary,which implies that the liquid–liquid phase separation normally takes place in a highly metastable solution.In addition,cloud-point temperature T increases with the cloud concentration of protein.3.2.Effect of salt concentrationFig.3shows how cloud-point temperature changes as the concentration of NaCl is varied from 2.5to 7%(w y v ).The buffer is 0.1M acetate (pH 4.8);the protein concentration is fixed at 50mg y ml.Over the entire range of salt concentrations studied,the cloud-point temperature strongly depends on the ionic strength and increases monotonically with the concentration of NaCl.Crystallization is driven by the difference in chemical potential of the solute in solution and in the crystal.The driving force can be simplified as w 24xf sy Dm s kT ln C y C (1)Ž.eq109J.Lu et al./Biophysical Chemistry 109(2004)105–112Fig.4.The driving force required by liquid–liquid phase sep-aration as a function of the concentration of sodium chloride,50mg y ml lysozyme solution,0.1M acetate buffer,pH 4.8.In the same way,we plot the driving force,f ,required by liquid–liquid phase separation as a function of the concentration of sodium chloride in Fig.4.At the moderate concentration of sodium chloride,the driving force required by liquid–liquid phase separation is higher than that at low or high salt concentration.As shown in Fig.3,with NaCl concentration increasing,the cloud-point temperature increases,which is in accord with the results of Broide et al.w 14x and Grigsby et al.w 25x .It is known that protein interaction is the sum of different potentials like electrostatic,van der Waals,hydrophobic,hydration,etc.The liquid–liquid phase separation is driven by a net attraction between protein molecules,and the stronger the attraction,the higher the cloud-point temperature.Ionic strength is found to have an effect on the intermolecular forces:attractions increase with ionic strength,solubility decreases with ionic strength,resulting in the cloud-point temperature increases with ionic strength.It is worth noting that,the effect of ionic strength on cloud-point temperature depends strongly on the specific nature of the ions w 13x .Kosmotropic ions bind adjacent water molecules more strongly than water binds itself.When akosmotropic ion is introduced into water,the entro-py of the system decreases due to increased water structuring around the ion.In contrast,chaotropes bind adjacent water molecules less strongly than water binds itself.When a chaotrope is introduced into water,the entropy of the system increases because the water structuring around the ion is less than that in salt-free water.This classification is related to the size and charge of the ion.At high salt concentration ()0.3M ),the specific nature of the ions is much more important w 25x .The charges on a protein are due to discrete positively and negatively charged surface groups.In lysozyme,the average distance between thesecharges is approximately 10Aw 26x .As to the salt ˚NaCl used as precipitant,Na is weakly kosmo-q tropic and Cl is weakly chaotropic w 27x .At low y NaCl concentrations,as the concentration of NaCl increases,the repulsive electrostatic charge–charge interactions between protein molecules decrease because of screening,resulting in the increase of cloud-point temperature.While at high NaCl con-centrations,protein molecules experience an attrac-tion,in which differences can be attributed to repulsive hydration forces w 14,25x .That is,as the ionic strength increases,repulsive electrostatic or hydration forces decrease,protein molecules appear more and more attractive,leading to higher cloud-point temperature.At various salt concentra-tions,the predominant potentials reflecting the driving force for liquid–liquid phase separation are different.Fig.4shows that the driving force,f ,is parabolic with ionic strength,while Grigsby et al.w 25x have reported that f y kT is linear with ionic strength for monovalent salts.The possible reasons for that difference include,their model is based on a fixed protein concentration of 87mg y ml,which is higher than that used in our study,yet f y kT is probably dependent on protein concentration,besides the solutions at high protein and salt concentrations are far from ideal solutions.3.3.Effect of glycerolFig.5compares cloud-point temperature data for 50mg y ml lysozyme solutions in absence of glycerol and in presence of 5%glycerol,respec-110J.Lu et al./Biophysical Chemistry109(2004)105–112parison of cloud-point temperatures for lysozyme at different glycerol concentrations as a function of the con-centration of sodium chloride,50mg y ml,0.1M acetate buffer, pH4.8:0%glycerol(s);5%glycerol(j).Fig.6.Cloud-point temperatures for lysozyme at different glycerol concentrations,50mg y ml lysozyme,5%NaCl,0.1M acetate buffer,pH4.8.Fig.7.Cloud-point temperature and solubility determination for lysozyme at different concentrations of glycerol in0.1M acetate buffer,5%NaCl,pH4.8:solubility(0%glycerol)(s); T(0%glycerol)(d);solubility(5%glycerol)(h);cloudT(5%glycerol)(j).cloudtively.Fig.6shows the cloud-point temperature as a function of the concentration of glycerol.The cloud-point temperature is decreased as the addi-tion of glycerol.In semilogarithmic Fig.7we plot the solid–liquid and liquid–liquid phase boundaries at dif-ferent glycerol concentrations for lysozyme in0.1 M acetate buffer,5%NaCl,pH4.8,for a range of protein concentration.This figure demonstrates that liquid–liquid and solid–liquid phase bounda-ries in the presence of glycerol are below those in absence of glycerol,and the region for growing crystals is narrowed when glycerol is added. Glycerol has the property of stabilizing protein structure.As a result,if crystallization occurs over a long period of time,glycerol is a useful candidate to be part of the crystallization solvent and is often included for this purpose w28x.In addition,glycerol is found to have an effect on the intermolecular forces:repulsions increase with glycerol concentra-tion w29x.Our experiment results of solubility and cloud-point temperature can also confirm the finding.The increased repulsions induced by glycerol can be explained by a number of possible mecha-nisms,all of which require small changes in the protein or the solvent in its immediate vicinity.The addition of glycerol decreases the volume of protein core w30x,increases hydration and the size of hydration layer at the particle surface w31,32x. In this work,we confirm that glycerol shifts the solid–liquid and liquid–liquid phase boundaries. The effect of glycerol on the phase diagram strong-111 J.Lu et al./Biophysical Chemistry109(2004)105–112ly depends on its concentration and this canprovide opportunities for further tuning of nuclea-tion rates.4.ConclusionsGrowing evidence suggests protein crystalliza-tion can be understood in terms of an order ydisorder phase transition between weakly attractiveparticles.Control of these attractions is thus keyto growing crystals.The study of phase transitionsin concentrated protein solutions provides one witha simple means of assessing the effect of solutionconditions on the strength of protein interactions.The cloud-point temperature and solubility datapresented in this paper demonstrate that salt andglycerol have remarkable effects on phase transi-tions.The solid–liquid and liquid–liquid bounda-ries can be shifted to higher or lower temperaturesby varying ionic strength or adding additives.Ourinvestigation provides further information upon therole of glycerol used in protein crystallization.Glycerol can increase the solubility,and decreasethe cloud-point temperature,which is of benefit totuning nucleation and crystal growth.In continuingstudies,we will explore the effects of other kindsof additives like nonionic polymers on phasetransitions and nucleation rates.Much more theo-retical work will be done to fully interpret ourexperimental results.AcknowledgmentsThis work is supported by the grant from theNational Natural Science Foundation of China(No.20106010).The authors also thank Professor J.M.Wiencek(The University of Iowa)for kinddiscussion with us about the thermal phenomenaof liquid–liquid phase separation.Referencesw1x A.McPherson,Current approaches to macromolecular crystallization,Eur.J.Biochem.189(1990)1–23.w2x A.M.Kulkarni, C.F.Zukoski,Nanoparticle crystal nucleation:influence of solution conditions,Langmuir18(2002)3090–3099.w3x E.E.G.Saridakis,P.D.S.Stewart,L.F.Lloyd,et al., Phase diagram and dilution experiments in the crystal-lization of carboxypeptidase G2,Acta Cryst.D50(1994)293–297.w4x A.P.Gast, C.K.Hall,W.B.Russel,Polymer-induced phase separations in non-aqueous colloidal suspensions,J.Colloid Interf.Sci.96(1983)251–267.w5x H.N.W.Lekkerkerker,W.C.K.Poon,P.N.Pusey,et al., Phase-behavior of colloid plus polymer mixtures,Euro-phys.Lett.20(1992)559–564.w6x A.Tardieu,S.Finet,F.Bonnete,Structure of the´macromolecular solutions that generate crystals,J.Cryst.Growth232(2001)1–9.w7x D.Rosenbaum,C.F.Zukoski,Protein interactions and crystallization,J.Cryst.Growth169(1996)752–758.w8x A.George,W.W.Wilson,Predicting protein crystalli-zation from a dilute solution property,Acta Cryst.D50(1994)361–365.w9x D.Rosenbaum,P.C.Zamora, C.F.Zukoski,Phase-behavior of small attractive colloidal particles,Phys.Rev.Lett.76(1996)150–153.w10x V.J.Anderson,H.N.W.Lekkerkerker,Insights into phase transition kinetics from colloid science,Nature416(2002)811–815.w11x S.Tanaka,K.Ito,R.Hayakawa,Size and number density of precrystalline aggregates in lysozyme crys-tallization process,J.Chem.Phys.111(1999)10330–10337.w12x D.W.Liu,A.Lomakin,G.M.Thurston,et al.,Phase-separation in multicomponent aqueous-protein solutions,J.Phys.Chem.99(1995)454–461.w13x V.G.Taratuta,A.Holschbach,G.M.Thurston,et al., Liquid–liquid phase separation of aqueous lysozymesolutions:effects of pH and salt identity,J.Phys.Chem.94(1990)2140–2144.w14x M.L.Broide,T.M.Tominc,M.D.Saxowsky,Using phase transitions to investigate the effect of salts onprotein interactions,Phys.Rev.E53(1996)6325–6335. w15x M.Muschol,F.Rosenberger,Liquid–liquid phase sep-aration in supersaturated lysozyme solutions and asso-ciated precipitate formation y crystallization,J.Chem.Phys.107(1997)1953–1962.w16x C.Domb,J.H.Lebowitz,Phase Separation and Critical Phenomena,Academic,London,1983.w17x D.F.Rosenbaum,A.Kulkarni,S.Ramakrishnan,C.F.Zukoski,Protein interactions and phase behavior:sen-sitivity to the form of the pair potential,J.Chem.Phys.111(1999)9882–9890.w18x O.Galkin,P.G.Vekilov,Nucleation of protein crystals: critical nuclei,phase behavior and control pathways,J.Cryst.Growth232(2001)63–76.w19x P.R.tenWolde, D.Frenkel,Enhancement of protein crystal nucleation by critical density fluctuations,Sci-ence277(1997)1975–1978.w20x P.A.Darcy,J.M.Wiencek,Estimating lysozyme crystal-lization growth rates and solubility from isothermalmicrocalorimetry,Acta Cryst.D54(1998)1387–1394.112J.Lu et al./Biophysical Chemistry109(2004)105–112w21x A.J.Sophianopoulos,C.K.Rhodes,D.N.Holcomb,K.E.vanHolde,Physical studies of lysozyme.I.Characteri-zation,J.Biol.Chem.237(1962)1107–1112.w22x Y.Georgalis,P.Umbach, A.Zielenkiewicz,et al., Microcalorimetric and small-angle light scattering stud-ies on nucleating lysozyme solutions,J.Am.Chem.Soc.119(1997)11959–11965.w23x P.A.Darcy,J.M.Wiencek,Identifying nucleation tem-peratures for lysozyme via differential scanning calorim-etry,J.Cryst.Growth196(1999)243–249.w24x M.L.Grant,Effects of thermodynamics nonideality in protein crystal growth,J.Cryst.Growth209(2000)130–137.w25x J.J.Grigsby,H.W.Blanch,J.M.Prausnitz,Cloud-point temperatures for lysozyme in electrolyte solutions:effectof salt type,salt concentration and pH,Biophys.Chem.91(2001)231–243.w26x D.Voet,J.Voet,Biochemistry,Wiley,New Y ork,1990. w27x K.D.Collins,Charge density-dependent strength of hydration and biological structure,Biophys.J.72(1997)65–76.w28x R.Sousa,Use of glycerol and other protein structure stabilizing agents in protein crystallization,Acta Cryst.D51(1995)271–277.w29x M.Farnum, C.F.Zukoski,Effect of glycerol on the interactions and solubility of bovine pancreatic trypsininhibitor,Biophys.J.76(1999)2716–2726.w30x A.Priev,A.Almagor,S.Yedgar,B.Gavish,Glycerol decreases the volume and compressibility of proteininterior,Biochemistry35(1996)2061–2066.w31x S.N.Timasheff,T.Arakawa,Mechanism of protein precipitation and stabilization by co-solvents,J.Cryst.Growth90(1988)39–46.w32x C.S.Miner,N.N.Dalton,Glycerol,Reinhold Publishing, New Y ork,1953.。
【word】非苯乙烯骨架极性吸附树脂的合成及结构表征
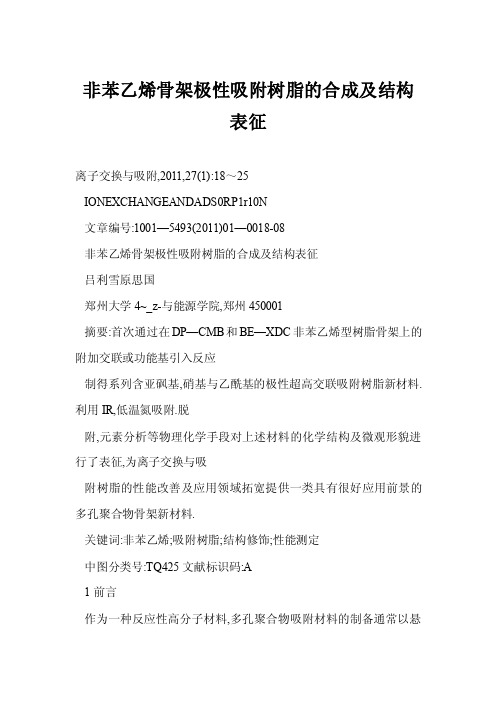
非苯乙烯骨架极性吸附树脂的合成及结构表征离子交换与吸附,2011,27(1):18~25IONEXCHANGEANDADS0RP1r10N文章编号:1001—5493(2011)01—0018-08非苯乙烯骨架极性吸附树脂的合成及结构表征吕利雪原思国郑州大学4~_z-与能源学院,郑州450001摘要:首次通过在DP—CMB和BE—XDC非苯乙烯型树脂骨架上的附加交联或功能基引入反应制得系列含亚砜基,硝基与乙酰基的极性超高交联吸附树脂新材料.利用IR,低温氮吸附.脱附,元素分析等物理化学手段对上述材料的化学结构及微观形貌进行了表征,为离子交换与吸附树脂的性能改善及应用领域拓宽提供一类具有很好应用前景的多孔聚合物骨架新材料.关键词:非苯乙烯;吸附树脂;结构修饰;性能测定中图分类号:TQ425文献标识码:A1前言作为一种反应性高分子材料,多孔聚合物吸附材料的制备通常以悬浮聚合或后交联法完成[】】.近年来,无论是这类材料的骨架结构设计与化学修饰,还是它们在众多领域的应用都得到飞速发展.但由上述方法制得的大孔(macropore)或超高交联(hypercrosslinking)树脂,其骨架结构虽存在AA.DVB(丙烯酸或丙烯酰胺与二乙烯基苯)等形式,但目前仍以苯乙烯.二乙烯基苯(ST-DVB)居多.与此同时,他们的制备工艺及材料的性价比还有一定的改进空间.近年来,我们利用双氯甲基芳烃自身或与苯,联苯,萘,甲苯等简单有机分子的连续Friede1.Crafts烷基化聚合反应合成了l0余种未见报道的新型非苯乙烯型超高交联吸附树脂[34】,这类新型非极性吸附树脂制备方法简单,且具有比表面积高(可达1780m2/g),孔径分布窄(多集中于微孔和低端介TL),孔体积大(>1.5m3儋)的突出优点.此外,它们在苯,甲苯类有毒有害气体高效滤除以及突发泄露事件的紧急处置等领域也展示出广阔的应用前景.非极性吸附树脂具有吸附量大,脱附再生容易等优点,但由于其分子内不含极性化学功能基团,它们的亲水与吸附专一等性能较差.基于上述原因,近年来国内外在吸附树脂的结构设计与化学修饰方面进行了大量工作『5.引,并在使用性能改善与应用领域拓宽等方面取得了很好进展.收稿日期:2010年2月25日项目基金:国家自然科学基金面上项目(No.20574063)作者简介:NNN(1983-),女,河南省人,在读研究生.}}通讯联系人:************************.cn第27卷第1期离子交换与吸附?l9?本文在实验室前期工作基础上,通过在非苯乙烯型多孔聚合物载体上的附加交联与结构修饰反应(图1),制得3种分别含亚砜基,乙酰基和硝基的中强极性吸附树脂新材料,并对它们的化学与孔结构,微观形貌以及亲水性能进行了初步表征,试图为工业有机废水资源化处理,天然产物活性组分选择性吸附分离等领域的实际应用提供一类具有良好前景的反应与功能性高分子新材料.HNO~a2SO4SOCb/A℃bic一b@10C“c”sFig.1TheRouteofStructuralModification2实验部分2.1化学试剂苯(BE),联苯(DP),氯化亚砜,浓硝酸,浓硫酸,浓盐酸,二氯乙烷,硝基苯,无水三氯化铝,无水三氯化铁,N,N一二甲基甲酰胺(DMF)均为分析纯;二水合氯化亚锡为化学纯;乙酰氯(化学纯,使用前重蒸精制);4,4’一二氯甲基联苯(CMB),1,4-二氯甲基苯(X.DC),PBr3为工业品:BE.XDC和DP.CMB树脂分别为本实验室通过1,4一二氯甲基苯(XDC)与苯(BE)或4,4’一二氯甲基联苯(CMB)与联苯(DP)的连续化Friedel—Crafts烷基化聚合反应制备【4】,基本结构参数见表1.Table1CharacteristicsoftheResinBE—XDCandDp-CMB IonExchangeandAdsorption2011年2月2.2树脂的合成2.2.1SO—DPCMB树脂的合成将0.1721g(含2.13mmol苯环)DP—CMB树脂于15mL硝基苯中过夜溶胀,次日加0.1mL氯化亚砜(1.38mmo1),然后加入催化剂.无水三氯化铝,40℃下反应lh,60℃下反应3h,8O℃下反应3h.冷却后过滤出溶剂,用lmol/L的稀盐酸反复冲洗浸泡树脂,用蒸馏水洗至滤液为中性后用丙酮抽提,过滤后自然晾干,60~C下真空干燥得到砖红色颗粒,树脂增重8.89%.元素分析结果为C:81.44%,H:4.64%,S:5.59%.红外图谱中在1066cm处出现了.S=O的伸缩振动吸收峰.2.2.2NO,一BE—XDC树脂的合成将0.8048g(含8.05mmol苯环)BE—XDC树脂于50mL的二氯乙烷中过夜溶胀,将反应瓶置冰水中,向其中缓慢滴加33mL混酸(硝酸:硫酸=l:2,体积比),然后60~C下反应2h,自然冷却后过滤出溶剂,依次用60%,30%的硫酸溶液冲洗树脂,然后用水,丙酮洗至中性,自然晾干后60~C下真空干燥得到淡黄色颗粒,树脂增重51.6%.元素分析结果为C:56.51%,H:3.12%,N:9.51%,推算O:21.74%.红外图谱中在1530.43cm一,1348.46cm处出现了一NO2中N一0键的不对称伸缩振动和对称伸缩振动吸收峰.2.2.3CHCO—BE.XDC树脂的合成将0.2768g(含2.77mmol苯环)BE—XDC树脂于20mL的硝基苯中溶胀2h,加0.4582g(3.43mmo1)无水三氯化铝和0.25mL(3.53mmo1)乙酰氯,25℃下反应4h,40~C下反应6h,反应后过滤,用1mol/L的稀盐酸反复冲洗浸泡树脂,然后用蒸馏水洗至中性,最后用丙酮抽提,60~C下真空干燥得到暗黄色颗粒,增重17.59%.元素分析结果为C:87.89%,H:6.22%,推算O:5.89%.红外图谱中在1685.27cm.处出现了C=O的伸缩振动吸收峰.2.3吸附树脂性能测定2.3.1比表面积及孔径分布表征树脂充分干燥后由NOV A2000e比表面及孔径测定仪测定.2.3.2红外光谱分析将干燥树脂研磨至粉末再与溴化钾混合均匀压片后,在FT-IR200红外光谱仪上进行.2.3.3功能基含量测定亚砜基,硝基,乙酰基树脂功能基含量经FLASHEA1112Series元素分析测试,并结合产物增重率等计算得出.2.3.4树脂吸水率测定吸水率:(广m2)/(m2-m0)取0.2g树脂在溶剂里浸泡24h,取出后放入离心管中,用AnkeTDL80—2B离心机以3000r/min速度除去过量的溶剂,将树脂迅速转移到称量瓶中盖上盖(瓶重mo)后称重m1,第27卷第1期离子交换与吸附然后将装有树脂的称量瓶放于真空干燥箱中,50~C下抽真空干燥(真空度为0.08MPa)至恒重,称重m:.3结果与讨论3.1极性吸附树脂的合成3.1.1树脂骨架结构的选择DP—CMB和BE—XDC树脂是交联剂CMB或XDC通过与苯或联苯的连续Friedel.Crafts烷基化聚合反应制备的.与交联剂CMB或XDC自身的连续烷基化聚合产物相比,DP.CMB和BEXDC树脂的交联网络相对稀疏,因此其比表面积较小(Ssa:553m/g和836m/g)而平均孔径则相对较大(R:3.85nm,2.80nm),从而有可能为树脂高分子骨架上发生的附加交联或化学结构修饰提供更适宜的空间.3.1.2SO—DP—CMB树脂亚砜基吸附树脂的制备是通过SOCI2在DP—CMB骨架上的附加交联反应得到的.在我们的实验条件下,树脂的亚砜基含量和比表面积分别可达1.75mmol/g和906m/g.对该树脂进行的孔结构(BEF方法)分析(结果见图2)可以看出,DP-CMB树脂经”亚砜桥”(一SO-)后交联反应后,其平均孔(半)径基本不变(3.85nm到3.89nm),但树脂的比表面积从553m2/g增加到906m2/g,孔体积也从1.06mL/g增至1.77mLIg;文献u曾利用苯乙烯一二乙烯基苯(ST-DVB)型大孔树脂制得亚砜基螯合功能树脂,其亚砜基(一SO一)含量和比表面积分别为1.5mmol/g和136m2/g(起始骨架比表面积为54rnZ/g).文献Ij报道含亚砜功能基的螯合树脂在各种金属离子共存体系中对Au2十,Pd和Cu离子有很好的吸附选择性能.显然,我们制备的这种高比表面积(906m2/g)与亚砜基含量(1.75mmol/g)的螫合树脂将有利于配位吸附过程中吸附容量与速率的进一步提高.亚砜基树脂的元素分析表明,当交联剂SOC12以接近理论量参与DP-CMB树脂的附加交联反应(SOCI2:苯环=0.65,摩尔比)时,亚砜基树脂中c,H,s元素总量为91.67%(S含量为5.59%),其比表面积可达906m2/g.这说明交联剂SOC12基本以交联桥形式参与了SO.DP.CMB交联网络的构建.为进一步提高树脂中亚砜功能基含量,我们将SOC12与树脂中苯环的摩尔比增加至1:1,此时虽然产物树脂中的S含量升高至8.35%,但亚砜树脂的比表面积并未提高,其C,H,S总量反而降至87.7%.我们推测,可能是由于交联剂SOC12的过量使用,使大量一SOC1基团以侧基方式悬垂于DP—CMB骨架上,不利于最终产物中亚砜基交联网络的生成.3.1.3NO2一BE—XDC树脂本文采用混酸硝化方法制得超高交联硝基树脂.由于硝化反应是放热反应,因此过高反应温度将导致硝酸的氧化作用加剧,且树脂强度也会受损.在我们的实验条件下,BE.XDC树脂在60~C下反应1~2h可以得到硝基含量7.14mmol/g,比表面积为144m2/g,22IonExchangeandAdsorption2011年2月且机械强度较好的硝基树脂,其孔径分布图见图2.硝基树脂的元素分析结果为C:56.51%,H:3.12%,N:9.51%.由N含量推算硝基中的氧含量应为21.74%,因此,最终硝基树脂中c,H,N,0元素总量仅为90.88%.考虑到BE—XDC树脂结构单元中存在大量亚甲基,我们认为,在进行上述树脂的硝化反应时,由于硝酸的氧化性,骨架中部分亚甲基可能被氧化为.C=O,产物红外图谱中1647.4cm.处的中强吸收峰进一步证实了羰基的存在.文献【l6l报道了硝基修饰的超高交联树脂对酚类化合物具有良好的吸附性能,本实验所制备的硝基树脂在对酚类化合物吸附应用方面的工作正在进行中.3.1.4CH3CO—BE.XDC树脂我们通过乙酰氯在BE—XDC树脂骨架上的Friedel—Crafts酰基化反应制得一种具有中等极性的吸附树脂新材料.乙酰化后的BE.XDC树脂在1685.27cm处出现强C=O伸缩振动吸收峰;由于含氧功能基(CH3CO.)的引入,树脂增重率约17.59%,其c,H元素总量则从原来的98.81%降至94.11%.假设树脂增重完全由乙酰基(CH3CO 一)所贡献,则树脂中的氧含量应为5.70%.这个氧含量推测值与从树脂C,H元素分析值(C,H总量=94.11%)中推测的氧含量十分接近,这进一步证实:1)含氧功能基(一CH3CO)确实被引入树脂高分子骨架中;2)在我们的实验条件下,基本上没有乙酰化反应之外的副产物生成.文献【.】有以AmberliteXAD.4(:880.2m2/g)为骨架制各乙酰基吸附树脂的报道,并对比了AmberliteXAD一4骨架和相应乙酰基吸附树脂对酚类化合物的吸附性能.研究发现乙酰基吸附树脂对酚类化合物的吸附容量相对于AmberliteXAD一4骨架提高20%.本文中制各的乙酰基吸附树脂,其乙酰基含量和比表面积分别为3.78mmol/g和675m2/g,具有良好的亲水性能和较高的比表面积,这将有利于该树脂对水溶液中酚类物质的吸附.目前关于这方面的工作正在进行中.3.2结构修饰对树脂孑L结构与亲水性能的影响3.2.1树脂反应前后的孔结构变化树脂骨架在引入功能基后,其孔结构会产生复杂的变化.通常情况下,强极性功能基团的引入使大分子链间的作用力增强,从而引起多孔聚合物比表面积,孔体积和平均孔径的大幅度降低;而中,弱极性功能基团的引入所带来的电荷效应对分子链间的作用力相对较弱,故其比表面积降低幅度不大.在我们的极性吸附树脂合成中:1)SO.DP—CMB树脂的比表面积从原来的553ma/g升至906m2/g,我们认为,虽然极性亚砜基的引入有可能使DP—CMB 树脂原有的链间作用力增强,并导致其孔结构塌陷,比表面积降低;但附加交联反应所生产的”-SO-”桥则使得其微孔结构更加丰富.而两种作用力平衡的结果使得最终产物亚砜基树脂内部的微孔结构更加丰富,使得树脂的比表面积有所增大.2)与前述的亚砜基以桥联形式参与树脂交联网络的形成不同,BE—XDC树脂中乙酰基和硝基的引入均不形成新的交联键,而这些功能第27卷第1期离子交换与吸附?23?基所带来的电荷或氢键效应反而使得孔结构塌陷,比表面积降低.其中,由于硝基极性大于乙酰基,所以两种树脂的比表面积也分别由起始BE—XDC树脂的836m2/g降为675m2/g和144m2/g.3)从树脂的孔径分布可以看出,反应前后,树脂孔径未发生明显变化,3种极性树脂的孔径分布仍主要集中于微孔和低端介孔区间.显然,这有利于它们对有机小分子的选择性吸附与回收.0l020304050PoreRadius(nm)O204060PoreRadius(nm)O2040PoreRadius(nm)Fig.2PoreSizeDistributionsofthePolarResinsContainingSulfoxide,Nitroa ndAcetylGroupTable2CharacteristicsoftheResinsContainingSulfoxide,NitroandAcetyl Groupa.meansthattheconcentrationoffunctionalgroupisobtainedbyelementalan alysis3.2.2吸附树脂的亲水性能我们按照文献”测试了各种树脂在水溶液中的溶胀性能.从表2可以看出,DP.CMB或BE.XDC树脂经亚砜桥交联或硝基,乙酰基化学修饰后,其吸水性能由原来的1-3%分别提高至2050%.通常情况下吸附树脂的亲水性能与功能基含量,极性强弱,比表面积及孔体积等因素密切相关.在我们的研究中,含乙酰基,硝基和亚砜基3种极性树脂的吸24IonExchangeandAdsorption水率均明显高于他们的前体(DP—CMB,BE—XDC)非极性树脂.其中,乙酰基树脂可能由于它的功能基含量,比表面积及孔体积等综合优势而具有更佳的亲水性能.可以预期,在有机酚,胺类工业废水资源化处理及天然产物活性组分选择性分离等过程中,树脂材料的极性功能基修饰以及亲水性能的提高将会发挥十分有益的作用.4结论本文以非苯乙烯型多孔聚合物为骨架首次合成了含亚砜基,硝基和乙酰基的极性吸附树脂,其功能基含量分别为1.75mmol/g,7.14mmol/g和3.78mmol/g,比表面积分别为906mE/g,144m,g和675mE/g.用物理化学手段对上述材料的化学结构及微观形貌进行了表征,结果表明,这3种极性吸附树脂相对于其非极性骨架有很好的亲水性(吸水率在20~50%之间),且其孔径分布仍主要集中于微孔和低端介孔区间,这类材料预期在有机酚,胺类工业废水资源化处理及天然产物活性组分选择性吸附分离等过程中发挥十分有益的作用.参考文献【1】TsyurupaMDavankovV A.ReactFunctPolym[J]_2006,66(7):768—779. 【2]SherringtonDC.ChemCommun[J]_1998,2275—2286.【3】原思国,王秀莉,周永豪,等.高比表面吸附树脂的合成方法及其用途[P].CN200810140986.7.[4】原思国,金秋,张晓燕,等.芳烃小分子化合物制备高比表面积吸附树脂的方法【P】.CN20091066288.[5]许辉,胡喜章.功能高分子学[J].1.998,l1(4):513—520.[6]LiAimin,ZhangQuanxing,ChenJinlong,eta1.Reactive&Function alPolymers[J].2001,49(3):225—233.【7】卞国建,魏荣卿,刘晓宁,等.过程工程[J].2005,5(1):44—48. 【8]孟冠华,李爱民,杨鑫,吴林,张全兴.环境污染与防治【J].2007,29(5):347—351.[9]王津南,李爱民,费正皓,张波,张全兴.离子交换与吸附[J].2007,23(3):199—207.f10]费正皓,刘福强,李爱民,陈金龙,张全兴.离子交换与吸附【J】.2006,22(2):146—151.[11】孙越,陈金龙,李爱民,张全兴.高分子[J].2005,28(6):801—806. [12]SunY ue,LiAimin,ZhangQuanxing,eta1.SeparationScienceandTechn ologyfJ].2008,43(2):389—402.[13】GermainJonathan,FrechetJeanMJ,SvecFrantisek.JournalofMaterialsChem istry[J】.2007,17(47):4989—4997.[14]阎虎生,张全兴,何炳林.离子交换与吸附[J].1988,3(4):167—171. 第27卷第1期离子交换与吸附?25?[15]QuRongjun,SunChangmei,ChunhuaWang,eta1.ReactFunctPolym 【J].2005,41(7):1525.[16]王津南,李爱民,周友冬,张全兴.环境污染与防治[J】.2008,30(5):4-9.【17】何炳林,黄文强.离子交换与吸附树脂[M】.上海:上海科技教育出版社,1995,p101—102.SYNTHESISANDSTRUCTURALCHARACTERIZA TIoNoFNoN-PoL YSTYRENEMA TRIXPoLARADSoR】}’TIVERESINL VLixueYUANSiguo SchoolofChemicalEngineeringandEnergy,ZhengzhouUniversity,Zhengz hou450001,ChinaAbstract:Aseriesofhypercrosslinkedpolaradsorptiveresinscontainingsulf oxide,nitroand acetylgroupwerefirstlypreparedviathepostcrosslinkingortheintroducingo ffunctionalgroup onnon—polystyrenetypeporouspolymermatrixDP—CMBandBE-XDC. Thechemicalstructure andmicromorphologyofthesenovelporousmaterialswerecharacterizedby 瓜,low-temperatureni~ogenadsorption—desorption,elementalanalysis.The ywillprovideakindof newporouspolymermaterialshavinggoodapplicationprospectfortheapplic ationperformance improvementoftheionexchangeandadsorptionresins.Keyword:Non?-polystyrene;Adsorptiveresins;Structuralmodification;Pe rformancemeasurement.。
表柔比星超顺磁性氧化铁纳米粒(EPI-SPION)经皮递药抗肿瘤作用研究
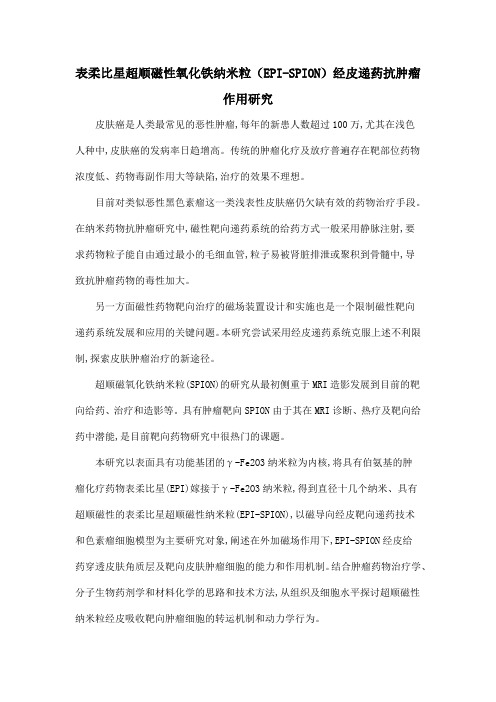
表柔比星超顺磁性氧化铁纳米粒(EPI-SPION)经皮递药抗肿瘤作用研究皮肤癌是人类最常见的恶性肿瘤,每年的新患人数超过100万,尤其在浅色人种中,皮肤癌的发病率日趋增高。
传统的肿瘤化疗及放疗普遍存在靶部位药物浓度低、药物毒副作用大等缺陷,治疗的效果不理想。
目前对类似恶性黑色素瘤这一类浅表性皮肤癌仍欠缺有效的药物治疗手段。
在纳米药物抗肿瘤研究中,磁性靶向递药系统的给药方式一般采用静脉注射,要求药物粒子能自由通过最小的毛细血管,粒子易被肾脏排泄或聚积到骨髓中,导致抗肿瘤药物的毒性加大。
另一方面磁性药物靶向治疗的磁场装置设计和实施也是一个限制磁性靶向递药系统发展和应用的关键问题。
本研究尝试采用经皮递药系统克服上述不利限制,探索皮肤肿瘤治疗的新途径。
超顺磁氧化铁纳米粒(SPION)的研究从最初侧重于MRI造影发展到目前的靶向给药、治疗和造影等。
具有肿瘤靶向SPION由于其在MRI诊断、热疗及靶向给药中潜能,是目前靶向药物研究中很热门的课题。
本研究以表面具有功能基团的γ-Fe2O3纳米粒为内核,将具有伯氨基的肿瘤化疗药物表柔比星(EPI)嫁接于γ-Fe2O3纳米粒,得到直径十几个纳米、具有超顺磁性的表柔比星超顺磁性纳米粒(EPI-SPION),以磁导向经皮靶向递药技术和色素瘤细胞模型为主要研究对象,阐述在外加磁场作用下,EPI-SPION经皮给药穿透皮肤角质层及靶向皮肤肿瘤细胞的能力和作用机制。
结合肿瘤药物治疗学、分子生物药剂学和材料化学的思路和技术方法,从组织及细胞水平探讨超顺磁性纳米粒经皮吸收靶向肿瘤细胞的转运机制和动力学行为。
首先通过共沉淀-交联耦合法制备功能化γ-Fe2O3纳米粒,经仿生化表面修饰后将药物嫁接至纳米粒表面,得到性质稳定的EPI-SPION递药系统,并试图通过调控外磁场作用方式和强度,高效递送抗肿瘤药物至肿瘤局灶区。
我们前期得到的载药SPION水合粒径大小为16±2nm,主要理化性质研究表明,该纳米粒具有类球形单畴晶格形貌,保持良好磁性效能,饱和磁化强度大于70 emu/g,矫顽力几乎为零,具有良好的超顺磁性能。
赤藓糖醇相变储热材料研究进展
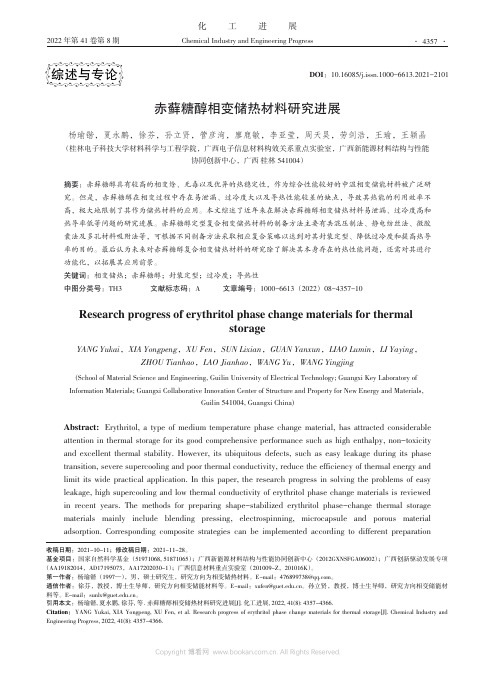
化工进展Chemical Industry and Engineering Progress2022年第41卷第8期赤藓糖醇相变储热材料研究进展杨瑜锴,夏永鹏,徐芬,孙立贤,管彦洵,廖鹿敏,李亚莹,周天昊,劳剑浩,王瑜,王颖晶(桂林电子科技大学材料科学与工程学院,广西电子信息材料构效关系重点实验室,广西新能源材料结构与性能协同创新中心,广西桂林541004)摘要:赤藓糖醇具有较高的相变焓、无毒以及优异的热稳定性,作为综合性能较好的中温相变储能材料被广泛研究。
但是,赤藓糖醇在相变过程中存在易泄漏、过冷度大以及导热性能较差的缺点,导致其热能的利用效率不高,极大地限制了其作为储热材料的应用。
本文综述了近年来在解决赤藓糖醇相变储热材料易泄漏、过冷度高和热导率低等问题的研究进展。
赤藓糖醇定型复合相变储热材料的制备方法主要有共混压制法、静电纺丝法、微胶囊法及多孔材料吸附法等,可根据不同制备方法采取相应复合策略以达到对其封装定型、降低过冷度和提高热导率的目的。
最后认为未来对赤藓糖醇复合相变储热材料的研究除了解决其本身存在的热性能问题,还需对其进行功能化,以拓展其应用前景。
关键词:相变储热;赤藓糖醇;封装定型;过冷度;导热性中图分类号:TH3文献标志码:A文章编号:1000-6613(2022)08-4357-10Research progress of erythritol phase change materials for thermalstorageYANG Yukai ,XIA Yongpeng ,XU Fen ,SUN Lixian ,GUAN Yanxun ,LIAO Lumin ,LI Yaying ,ZHOU Tianhao ,LAO Jianhao ,WANG Yu ,WANG Yingjing(School of Material Science and Engineering,Guilin University of Electrical Technology;Guangxi Key Laboratory ofInformation Materials;Guangxi Collaborative Innovation Center of Structure and Property for New Energy and Materials,Guilin 541004,Guangxi China)Abstract:Erythritol,a type of medium temperature phase change material,has attracted considerable attention in thermal storage for its good comprehensive performance such as high enthalpy,non-toxicity and excellent thermal stability.However,its ubiquitous defects,such as easy leakage during its phase transition,severe supercooling and poor thermal conductivity,reduce the efficiency of thermal energy and limit its wide practical application.In this paper,the research progress in solving the problems of easy leakage,high supercooling and low thermal conductivity of erythritol phase change materials is reviewed in recent years.The methods for preparing shape-stabilized erythritol phase-change thermal storage materials mainly include blending pressing,electrospinning,microcapsule and porous material adsorption.Corresponding composite strategies can be implemented according to different preparation综述与专论DOI :10.16085/j.issn.1000-6613.2021-2101收稿日期:2021-10-11;修改稿日期:2021-11-28。
Comparison of properties of solid phase epitaxial SOS films recrystallized by annealing
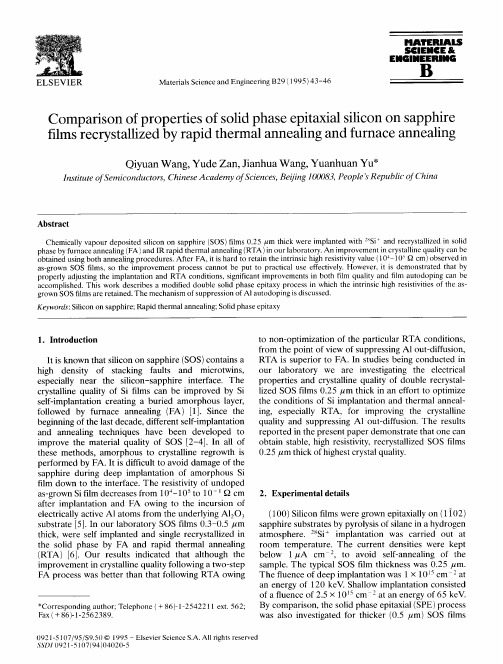
44
Q. WarN et al.
/
Materials Science and Engineerimd B29 (1995) 43-4C~
which underwent double implantation to increase the width of the amorphous region followed by a single SPE process. The implantation schedule was as follows: E , = 2 8 5 keV, D ~ = 2 x l 0 t ~ ; E ~ = 1 2 0 keV, D ~ = 2 x 1015 for 0.5 ktm SOS. EA was carried out at 1000 °C in flowing N~ for 30-45 rain. IR annealing was performed by heating a graphite block in flowing N 2, the sample heating up owing to the high concentration of free carriers absorbing IR light (wavelength at peak energy 2/~m). This technique provides rapid and uniform heating over a large area [7]. Depth profiles of the crystallinity were recorded using 2 M e V ~He + Rutherford backscattering (RBS) and channelling. The defect microstructure was characterized by vertical cross-section transmission electron microscopy (TEM). The electrical properties of SOS films were analysed by Hall measurements. Auger electron spectroscopy (AES) in combination with Ar + sputtering was used to determine the interface width of SOS films as a measure of AI out-diffusion [8].
单分子甲醛吸附研究取得新进展
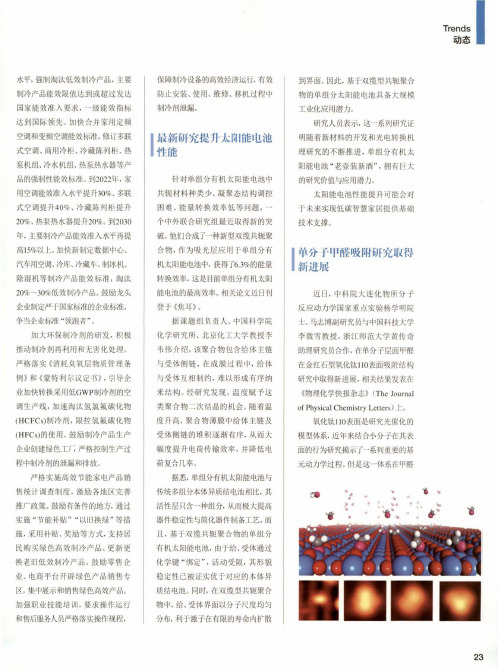
Trends动态水平,强制淘汰低效制冷产品,主要制冷产品能效限值达到或超过发达国家能效准入要求,一级能效指标达到国际领先。
加快合并家用定频空调和变频空调能效标准,修订多联式空调、商用冷柜、冷藏陈列柜、热泵机组、冷水机组、热泵热水器等产品的强制性能效标准。
到2022年,家用空调能效准入水平提升30%、多联式空调提升40%、冷藏陈列柜提升20%、热泵热水器提升20%。
到2030年,主要制冷产品能效准入水平再提高15%以上。
加快新制定数据中心、汽车用空调、冷库、冷藏车、制冰机、除湿机等制冷产品能效标准,淘汰20%〜30%低效制冷产品。
鼓励龙头企业制定严于国家标准的企业标准,争当企业标准“领跑者”。
加大环保制冷剂的研发,积极推动制冷剂再利用和无害化处理。
严格落实《消耗臭氧层物质管理条例》和《蒙特利尔议定书》,引导企业加快转换采用低GWP制冷剂的空调生产线,加速淘汰氢氯氟碳化物(HCFCs)制冷剂,限控氢氟碳化物(HFCs)的使用。
鼓励制冷产品生产企业创建绿色工厂严格控制生产过程中制冷剂的泄漏和排放。
严格实施高效节能家电产品销售统计调查制度,激励各地区完善推广政策。
鼓励有条件的地方,通过实施“节能补贴”“以旧换绿”等措施,釆用补贴、奖励等方式,支持居民购买绿色高效制冷产品、更新更换老旧低效制冷产品。
鼓励零售企业、电商平台开辟绿色产品销售专区,集中展示和销售绿色高效产品。
加强职业技能培训,要求操作运行和售后服务人员严格落实操作规程,保障制冷设备的高效经济运行,有效防止安装、使用、维修、移机过程中制冷剂泄漏。
最新研究提升太阳能电池性能针对单组分有机太阳能电池中共辘材料种类少、凝聚态结构调控困难、能量转换效率低等问题,一个中外联合研究组最近取得新的突破。
他们合成了一种新型双缆共轨聚合物,作为吸光层应用于单组分有机太阳能电池中,获得了6.3%的能量转换效率,这是目前单组分有机太阳能电池的最高效率。
相关论文近日刊登于《焦耳》。
异氰酸酯改性环氧树脂的研究

当代化工研究Modern Chemical Research34基础研究2020・23异氟酸酉旨改片生环氧树片旨的研究*王哲彭程瑶张宇鹏田雨(西北民族大学化工学院甘肃730124)摘耍:为了获得较高餉环氧树脂韧性,本文合成了嵌段异氨酸酯的预聚物和具有特殊结构的环氧树脂强韧固化剂.首先,通过甲苯二异氤酸酯(TDI)和扩链剂时扩链反应制备异氟酸酯末端预聚物,然后与咪哇(MI)进一步合成封端的异氟酸酯预聚物,该咪哇通常用作封端剂.用低聚物作为增韧剂对环氧树脂进行改性,然后在指定温度下固化.在实验中,研究了不同剂量的不同封闭剂,反应温度,时间和不同的进料方式对封闭率的影响,以及不同介质对封闭温度的影响.结果表明,合成封闭的多异氤酸酯的最佳条件为:MI/-NC0餉摩尔比为1.1-1.2,封闭反应温度为601C,封闭反应时间为3h;固化时间温度为1OOV,时间为3h°关键词:异鼠酸酯;封闭剂;扩链剂;环氧树脂中图分类号:TQ文献标识码:ADegradation on Isocyanate Modified Epoxy ResinWang Zhepeng,Cheng Yao,Zhang Yiipeng,Tian Yii(School of Chemical Engineering,Northwest Minzu University,Gansu,730124) Abstracts In order to obtain high toughness ofepoxy resin,in this p aper,prepolymer ofblocked isocyanate and tough curing agaent with special structure f or epoxy resin is synthesized.First,isocyanate terminal p repolymer are prepared through chain extension reaction of t oluene diisocyanate (TDI)and chain extender,and then blocked isocyanate prepolymer is f arther synthesized with imidazole(MI)which is often used as the blocking agaent.The epoxy resin is modified using the oligomer as a toughening agent,then cure at the specified temperature.In the experiment,the effects of different dosages of d ifferent blocking agents,reaction temperatures,time and differentfeeding methods on the blocking rate are studied,also the effects of d ifferent media on the deblocking temperature.The results show that the optimum conditions f or the synthesis ofblocked p oly-isocyanates are f ound as f ollows:the molar ratio ofMI/-NCO is f rom1.1to1.2,the blocking reaction temperature is60°C,and the blocking reaction time is3h;curing time temperature is100°C,time is3h.Key wordsi isocyanates blocking agaenh chain extender^epoxy resin研究封闭异氤酸酯增韧环氧树脂对于环氧树脂的广泛应用具有重要意义。
中科大马骋教授新型固态电解质—氧氯化锆锂文章
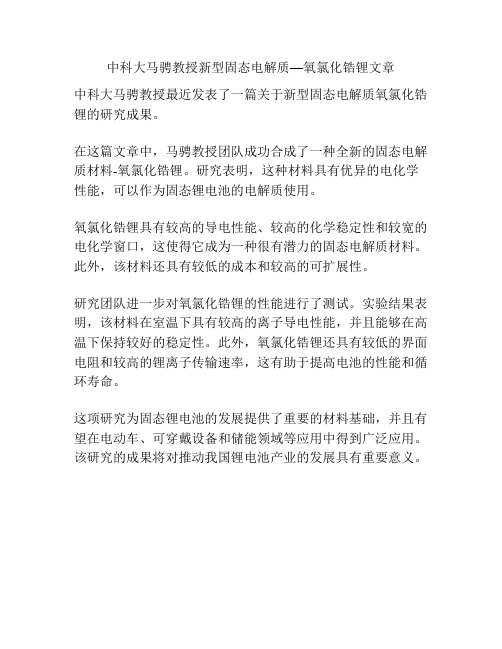
中科大马骋教授新型固态电解质—氧氯化锆锂文章
中科大马骋教授最近发表了一篇关于新型固态电解质氧氯化锆锂的研究成果。
在这篇文章中,马骋教授团队成功合成了一种全新的固态电解质材料-氧氯化锆锂。
研究表明,这种材料具有优异的电化学性能,可以作为固态锂电池的电解质使用。
氧氯化锆锂具有较高的导电性能、较高的化学稳定性和较宽的电化学窗口,这使得它成为一种很有潜力的固态电解质材料。
此外,该材料还具有较低的成本和较高的可扩展性。
研究团队进一步对氧氯化锆锂的性能进行了测试。
实验结果表明,该材料在室温下具有较高的离子导电性能,并且能够在高温下保持较好的稳定性。
此外,氧氯化锆锂还具有较低的界面电阻和较高的锂离子传输速率,这有助于提高电池的性能和循环寿命。
这项研究为固态锂电池的发展提供了重要的材料基础,并且有望在电动车、可穿戴设备和储能领域等应用中得到广泛应用。
该研究的成果将对推动我国锂电池产业的发展具有重要意义。
2. Silicon Epitaxy by Chemical Vapor Deposition

2Silicon Epitaxy by Chemical Vapor DepositionMartin L. Hammond1.0INTRODUCTIONThe word epitaxy is derived from the Greek “epi”—upon, and “taxis”—to arrange. Thus, epitaxial silicon deposition requires the ability to add and arrange silicon atoms upon a single crystal surface. Epitaxy is the regularly oriented growth of one crystalline substance upon another. Specific applications require controlling the crystalline perfection and the dopant concentration in the added layer.Two different kinds of epitaxy are recognized:Homoepitaxy growth in which the epitaxial layer is of thesame material as the substrate.Heteroepitaxy growth in which the epitaxial layer is a differentmaterial from the substrate.Virtually all commercial silicon epitaxy is homoepitaxy, with the exception of silicon-on-sapphire.Epitaxial silicon layers can be created by a wide range of tech-niques, including evaporation, sputtering, molecular beams, and various4546Thin-Film Deposition Processes and Technologiesregrowth concepts. This chapter discusses epitaxial deposition by chemi-cal vapor deposition (CVD) in which the silicon and dopant atoms are brought to the single crystal surface by gaseous transport.[1][2] Chemical vapor deposition is the formation of stable solids by decomposition of gaseous chemicals using heat, plasma, ultraviolet, or other energy sources, or a combination of sources. CVD is a relatively old technology. It was used to refine refractory metals in the 1800s, to produce filaments for Edison’s incandescent carbon filament lamps in the early 1900s, for hard metal coatings in the 1950s, and for semiconductor material preparation beginning in the 1960s.[2a]Commercial silicon epitaxy production, at present, is accomplished primarily by CVD using heat as the energy source for decomposing the gaseous chemicals.With the silicon epitaxy process, radical changes in materials’ prop-erties can be created over small distances within the same crystal. This capability permits the growth of lightly doped single crystal silicon on top of heavily doped single crystal silicon. At present, no other process technique permits this configuration of doped regions within a single crystal substrate.Many different configurations are made possible by the CVD epi-taxial deposition process. Some of the possibilities in use today include:•n-type silicon over p-type silicon•p-type silicon over n-type silicon•Lightly doped over heavily doped of either type•Lightly doped over heavily doped buried layer patterns•Conducting silicon layers over insulating surfaces•Silicon layers with controlled dopant profiles•Silicon selectively deposited through oxide1.1Applications of Silicon EpitaxySilicon epitaxy is required for isolation and for device perfor-mance in bipolar integrated circuits. It is also important far discrete device performance, and is becoming important for MOS integrated circuits (ICs).Chapter 2: Silicon Epitaxy by Chemical Vapor Deposition47 For bipolar devices, epitaxy provides a wide range of device perfor-mance benefits too numerous to describe here. Among these benefits are:[1]•Higher switching speeds•Improved high voltage, linearity characteristics•Simplified isolation•Lower base resistance•Independently controlled dopant profiles•Buried layer patternsMOS ICs have not required an epitaxy layer to create device isolation; however, as MOS ICs have become more complex, epitaxial layers can provide many device benefits.[3] MOS ICs are usually created in lightly doped substrates. When a lightly doped epitaxial layer is used over a heavily doped substrate, the benefits to MOS ICs include:•Lower diffused-line capacitance•Better diffused-line charge retention•Better control of spurious charge (such as alpha particlesand static charge)•Improved dynamic random access memory performanceFor complementary MOS (CMOS) ICs, the benefit is a very significant improvement in latch-up protection.Because of its wide-ranging applications to semiconductor technol-ogy, approximately 50% of all silicon processed requires an epitaxy layer, and this percentage is expected to increase to 60–70% when epitaxy is used more extensively in MOS IC production.[4]Silicon epitaxy is used in a wide range of thicknesses and resistivi-ties. In commercial silicon epitaxy, layer thickness is usually expressed in micrometers (µm), commonly abbreviated microns (µ) or 10-4 cm. Resistiv-ity is expressed as ohm-cm, and resistivity is related to the electrical carrier concentration by Irwin’s curves.[5]Table 1 lists typical specifications for the common silicon device structures now in production. With the trend to ever smaller feature sizes and ever higher circuit densities, there is a long range tendency toward thinner epitaxial layers; however, the values noted in Table 1 will probably be valid until well into the 1990s.48Thin-Film Deposition Processes and TechnologiesTable 1. Typical Epitaxy SpecificationsDevice Type Thickness Resistivity(microns)(ohm-cm) Bipolar discrete devicesHigh Frequency0.5–30.15–1.5Power5–100+0.5–100+ Bipolar integrated circuitsDigital memory0.5–50.3–1.5 Microprocessor0.5–50.3–1.5Linear3–152–20MOS-on-epitaxy integrated circuitsP/P+4–2010–40 (Back-sealed substrates)N/N+0.5–71–10BiMOS*0.5–30.5–3* BiMOS = Bipolar and MOS devices together in the same device.Evaluation of silicon epitaxy is a major technology and detailed information for standardized techniques is available in Refs. 5 and 6. This chapter on silicon epitaxy will address:•Theory of silicon epitaxy by CVD•Silicon epitaxy process chemistry•Process adjustments•Equipment considerations for silicon epitaxy•Other equipment considerations•Defects in epitaxy layers•Safety•Key technical issuesChapter 2: Silicon Epitaxy by Chemical Vapor Deposition49 2.0THEORY OF SILICON EPITAXY BY CVDSuccessful silicon epitaxy depends upon having:•High surface mobility for the arriving atoms.•Numerous, equivalent growth sites.•Commercially significant growth rates.Production silicon epitaxy since the early 1960s has been manufactured by chemical vapor deposition in H2 from the chlorosilanes: SiCl4, SiHCl3, SiH2Cl2, and SiH4 in open tube, vapor transport systems. Alternate chem-istries using iodides and bromides have been investigated but no over-whelming advantages have been noted. Fluorine chemistry has not been explored significantly because the Si-F bond is thermodynamically very strong and very high temperatures would be required to crack most Si-F compounds.As illustrated in Fig. 1, CVD is a heterogeneous reaction involving at least the following steps:[1d][2b][7]Arrival1.Bulk transport of reactants into the process volume2.Gaseous diffusion of reactants to the surface3.Absorption of reactants onto the surfaceSurface reaction4.Surface reaction (reaction can also take place in thegas volume immediately above the surface)5.Surface diffusion6.Crystal lattice incorporationRemoval of reactant by-products7.Reaction by-product desorption8.Gaseous transport of by-products9.Bulk transport of by-products out of process volumeThe rate of chemical vapor deposition is primarily controlled by one of the following major groups of process steps:•The rate of arrival of reactants•The surface reaction rate•The rate of removal of by-products50Thin-Film Deposition Processes and TechnologiesFor typical epitaxy process, the reaction conditions are established so that the rate of arrival of the reactants controls the growth rate. This procedure gives the best crystal quality, a feature necessary in good device performance.The crystal quality of the epitaxial layer is controlled primarily by:•The nature of the surface prior to epitaxial growth•The arrival rate relative to the surface diffusion rate•The nature of the lattice incorporationIf the surface prior to deposition has contamination, such as oxides, which are not removed during heat-up and etch, or if the crystal upon which the epitaxial layer is to be grown is defective, then the epitaxial layer will have crystal defects. If the rate of arrival of reactants greatly exceeds the surface diffusion rate, then the diffusing atoms cannot move to positions of lowest energy, and again, crystal defects occur.The rate of lattice incorporation is a function of crystal orientation because the density of atomic sites is a function of which crystallographic faces are exposed. Figure 2 shows the effect of substrate orientation on growth rate for (111), (110), and (100) faces. For silicon, the (110) plane has the highest growth rate, followed by the (100) and (111) planes.[8]Chapter 2: Silicon Epitaxy by Chemical Vapor Deposition51 For epitaxial growth on crystal faces directly on orientation, the low growth rate for the (111) planes encourages a defect called faceting or orange peel. Growth perpendicular to the (111) surface is slow, while growth on a facet not parallel to the surface is faster. The result is a shingle-like faceted surface. To prevent faceting, (111) surfaces for epitaxial growth are cut a few degrees off the (111) to cause the growth to proceed in waves across the surface. Epitaxial growth on the (100) plane does not have this problem; therefore, (100) surfaces are usually cut directly on orientation.Surface preparation is an important factor in producing good epi-taxial crystal quality. The surface requires a high quality, defect-free chemical/mechanical polish that leaves the surface polished without me-chanical damage to the crystal structure. Foreign matter such as organic compounds must be removed because it will react with the crystal surface during heat-up to form undesirable silicon compounds, leading to defects.Figure 2. Effect of substrate orientation on epitaxial silicon growth rate.[1c]52Thin-Film Deposition Processes and Technologies3.0SILICON EPITAXY PROCESS CHEMISTRYThe conditions for acceptable commercial silicon epitaxy are out-lined in Table 2. Generally, the lower the temperature, the lower the growth rate for acceptable epitaxy quality, and the lower the tolerance for oxidiz-ers in the process space. If silicon oxides, including SiO, are allowed to form during deposition, they interfere with surface diffusion and lattice incorporation, leading to various defects in the epitaxy layer.Table 2. Silicon Epitaxy Growth ConditionsGrowth Rate Temperature Range Allowed Oxidizer Chemistry(microns/minute)(°C)(ppm)SiCl40.4–1.51150–12505–10 SiHCl30.4–3.01100–12005–10SiH2Cl20.3–2.01050–1150<5SiH40.1–0.3950–1050<2 Epitaxy quality is especially sensitive to the presence of oxidizers during heat-up. Water vapor absorbed on cold wafer carriers can be a significant source of oxidizer in the process chamber; therefore, there is a substantial difference in surface quality between beginning the epitaxy cycle with a cold or warm wafer carrier. In a leak-free system, water vapor from a cold wafer carrier can easily be the largest source of oxidizer in the reactor.[9a]At low concentration, water vapor etches Si surfaces by formation of volatile SiO in H2. However, at about 1 part per million (ppm) H2O at 900°C, water vapor begins to form SiO2 on the Si surface, and this SiO2 can lead to surface and crystal defects.[9b] The presence of excess H2 will reverse this reaction somewhat; however, only a few ppm of water vapor during heat-up will seriously degrade the epitaxy quality. (See Table 2 and Ref. 9a).Epitaxial silicon can be grown from less than 1 micron thickness to more than 100 microns. Thicknesses below about 2 microns are consid-ered very thin and careful consideration must be given to the dopant transition from a heavily doped substrate to a more lightly doped epitaxy layer. Thicknesses above about 30 microns are considered very thick and care must be taken to reduce defects that can develop during long deposition times.Chapter 2: Silicon Epitaxy by Chemical Vapor Deposition53 Epitaxial silicon is normally doped with PH3, AsH3, and B2H6. Resistivity levels below about 0.1 ohm-cm are considered heavily doped and require proportionately much higher dopant concentrations in the gas stream to achieve the desired resistivity levels. As the dopant solid solubil-ity is approached (nominally 0.001 ohm-cm), very high concentrations of dopant are required in the gas stream and the epitaxial layer can become a two-phase polycrystalline deposit if the solid solubility is exceeded. When very high concentrations of dopant are added to the reactor, dopant can be absorbed onto the reactor walls and be liberated into the room upon exposure to room air and water vapor. Rigorous safety procedures and adequate ventilation are required when using dopant hydrides, especially when using concentrations in the supply cylinder greater than about 100 ppm.Resistivity levels above about 10 ohm-cm are considered very lightly doped because the intended dopant level is low enough to be influenced by the typical background dopant levels in the reactor. The undoped or intrinsic dopant level in a commercial epitaxy reactor is a function of the purity of the deposition chemicals, the integrity of the SIC coating on the graphite wafer carrier, the level of other unwanted contami-nation, and the dopant history of the heated parts within the system. A clean reactor with a fresh wafer carrier and commercially available deposit chemicals should be able to demonstrate an intrinsic resistivity level of greater than 100 ohm-cm n-type on 0.005–0.010 ohm-cm Sb (n+) and on >10 ohm-cm p-type substrate. In most reactor designs, autodoping from more heavily doped As-, P-, or B-doped substrates will affect the intrinsic resistivity. The larger the area of heavily doped silicon in the reactor, the more effect.Gaseous HCl is used to etch the silicon surface and remove surface damage prior to epitaxial deposition. The etch rate slowly increases with increasing temperature and, at about 1150°C, a 0.1% HCl/H2 mixture will remove silicon at 0.1–0.3 micron/minute. If the HCl etch rate is too high for a given temperature, the surface will be pitted instead of being polished. For temperatures above about 1150°C, silicon can be etched at up to 1.5 microns/minute without pitting. In the 1050–1100°C range, an etch rate of 0.1–0.5 micron/minute will polish the surface. Below 1050°C HCl is more likely to pit rather than polish the water surface.[10a,d] SF6 has been consid-ered as a Si etchant because it provides a smooth surface at etch tempera-tures below 1100°C.[10e] Unfortunately, SF6 reacts with the H2 to form H2S, and the resulting odor makes SF6 unusable in a commercial environment.54Thin-Film Deposition Processes and TechnologiesBecause of the quality of chemical/mechanical polishing available today,[10f] there is generally little requirement to remove silicon from the surface to achieve good epitaxy quality. An H2 bake at 1150°C for 10 minutes will remove native oxide and provide good surfaces.[l0g,h] None-theless, commercial epitaxy processes often call for a light HCl etch to remove a micron or less Si just to ensure a low defect density.When depositing with chlorosilanes, HCl is created by surface and gas phase reactions. This HCl enhances film quality by etching the high energy surface atoms during deposition. When HCl is added to SiH4, this simulta-neous etch/deposit process also occurs and the etch reaction can be treated as if it were separated from the SiH4 deposition process.For conditions used in commercial production, the epitaxial silicon growth rate is proportional to the concentration of silicon source gas in the process stream.[1][11a,b] Dopant incorporation, for a given temperature, is approximately proportional to the dopant concentration; however, tem-perature is a primary factor. As and P exist as metallic vapor at deposition temperature;[11b] therefore, higher temperatures increase the escaping tendency of these dopants and, thereby, increase the resistivity for fixed dopant concentration in the gas stream. As is more sensitive to tempera-ture than P. B forms complex hydrides at deposit temperatures; therefore, higher temperatures promote higher reaction rates near the wafer surface and produce lower resistivities. B doping is more sensitive to the presence of oxidizers than As or P.[11d] Oxidizers generally inhibit the incorporation of dopant.4.0COMMERCIAL REACTOR GEOMETRIESThe reactor chamber geometry affects the gas flow characteristics which, in turn, affect the properties of the deposited layers.Chemical reactors can be described by one of two flow types:•Displacement or plug flow in which the entering gas displacesthe gas already present with a minimum of mixing.•Mixed flow in which the entering gas thoroughly mixes withthe gas already present before exiting the reactor.When making a gas composition change in a displacement or plug flow reactor, one volume change can produce an approximately 100% change in gas composition by displacing the volume of gas already present. Whenmaking a gas composition change in an ideal mixed flow reactor, the gas composition changes exponentially with the number of volume changes.Because the epitaxy process involves complex intermediate chemi-cal reactions with trace quantities of dopant making significant changes in material properties, the nature of gas flow in the reactor can have a major effect on reactor performance. In general, mixed flow reactors have very uniform wafer-to-wafer resistivity control, even if there is significant autodoping from the substrate. Displacement flow reactors can have sharper dopant transition widths, with autodoping effects increasing from wafer to wafer along the length of the process gas stream. High total flow rate, reduced pressure operation, and other reactor design elements will strongly influence these generalizations.Figure 3 illustrates the three principal reactor geometries used in commercial epitaxy production.4.1Horizontal ReactorThe horizontal reactor is a displacement flow system in which the depletion of reactants downstream is accommodated by tilting the susceptor up to increase the local velocity, and thereby, increase the local growth rate. Overall gas velocities are in the 30–70 cm/sec range.[12]Figure 3. Principle CVD reactor geometries for silicon epitaxy.4.2Cylinder ReactorThe commercial cylinder reactor is a combination flow system with a substantial degree of gas mixing and a complex flow path in which the entering gas eventually displaces the depleted gas out the exhaust port.[13] Depletion is accommodated by having the wafer carrier tilt out at the bottom to increase the local velocity and by having two gas jets which give a strong downward velocity to the gas as it enters the reaction space. This downward velocity is locally 40–70 cm/sec and averages 10–20 cm/sec over the surface of the cylindrical wafer carrier. Rotation of the carrier through the high velocity/high concentration and low velocity/low concen-tration portions of the mainstream improves uniformity. Tangential veloci-ties for the cylinder reactor are nominally 2–3 cm/sec.4.3Vertical ReactorThe vertical reactor is a mixed flow system in which fresh process gas enters the process space through a central port and mixes with the depleted gas as it flows radially inward over the wafer carrier surface. The fresh process gas stimulates a convection current which rises from the center of the carrier plate, cools at the bell jar surface, and flows back toward the carrier plate along the bell jar wall. Radial gas velocities near the carrier plate are estimated to be 5–10 cm/sec, compared with the tangen-tial velocities of 2–4 cm/sec where wafers are placed on the wafer carrier.[14] 4.4New Reactor GeometryA new commercial epitaxy reactor geometry was introduced in May 1986[15] in which a circular cluster of wafer carriers create tapered cavities, with each cavity having two wafers facing each other, as illus-trated in Fig. 4. Process gas enters at the outer diameter defined by the tapered cavities and flows by displacement flow toward the center of the circular cluster of cavities. Process gas depletion is accommodated by the acceleration of the gas in the tapered cavities in a manner similar to that for the horizontal reactor geometry. Because of displacement flow, each cavity is isolated from the others so that very little interaction occurs. With this design, very high intrinsic resistivities can be achieved, even with up to fifty 150-mm diameter heavily doped substrates in the reactor. Radial gas velocities of 15–30 cm/sec are typical compared with 2–3 cm/sec tangential velocities.Figure 4. Tapered cavity epitaxy reactor.[15]5.0THEORY OF CHEMICAL VAPOR DEPOSITIONAn understanding of the theory of CVD is useful in developing techniques for making process adjustments in commercial production. The theory of CVD is based on chemical kinetics, fluid mechanics, chemical engineering principles, and an understanding of growth mecha-nisms.[1][2][12][14]Heterogeneous CVD reactions follow the general reaction path outlined in Fig. 1. For simplicity, one reaction step is considered to be rate controlling. When CVD reaction rates for a particular chemistry and reactor geometry are plotted over reciprocal temperature (Fig. 5), the deposition or growth rate varies exponentially with temperature,[1] and two regimes are recognized.[16]•The kinetic or surface reaction rate controlled regime whichoccurs at lower temperatures.•The diffusion or rate of arrival controlled regime whichoccurs at higher temperatures.The diffusion controlled regime is also termed the mass transport con-trolled regime.Below some temperature, the surface reaction rate normally con-trols because, for a given reactor geometry, the rate of arrival is greater than the surface reaction rate. As the temperature is increased, the overall surface reaction rate usually increases more rapidly than the overall mass transport rate, and the rate of arrival or mass transport rate becomes the limiting factor.Growth rates vs. reciprocal temperature for the chemicals com-monly used in silicon epitaxy are plotted in Fig. 6.[16] The individual curves in Fig. 6 can be moved vertically on the scale by changing the reactant concentration and reactor geometry; however, the shape of the curves is relatively stable. Each growth rate curve can be described by a kinetic and a diffusion controlled regime, as done in Fig. 5. Note that, for a given temperature and concentration, the growth rate is lower for the more thermodynamically stable compounds.Figure 5. Typical overall reaction rate for CVD reactors vs. reciprocal temperature.[16]Figure 6. Temperature dependence of silicon growth rate.[16]Epitaxial silicon is normally grown in the diffusion or mass trans-port limited regime, at a temperature near the high temperature side of the knees of the curves in Fig. 6. This temperature region is selected to be high enough to thermally decompose the selected chemical at a rate commensu-rate with the surface diffusion rate.Bloem’s data[16b] in Fig. 7 demonstrate how growth rate controls the morphology of the deposited layer. In all cases, increasing the rate of arrival causes a decrease in the degree of crystalline order for the polycrystalline-to-amorphous transition in the 550–650°C range and the single crystal-to-polycrystalline transition in the 1000–1400°CThe concept that morphology is controlled by the rate of arrival relative to the surface diffusion rate applies on the finer scale of epitaxial crystal perfection. In general, the lower the temperature of deposition, the lower the growth rate must be to accommodate a given level of crystal perfection. It is this concept that controls the growth rate/temperature conditions used in commercial silicon epitaxy.Figure 7. Relationship of growth rate, morphology, and growth temperature for silicon epitaxy.[16b]6.0PROCESS ADJUSTMENTSThe important CVD reactor control parameters can be divided into two categories: reactor design variables and operator variables. Each has a direct influence on the uniformity, productivity, and quality of the epitaxial layer.The reactor design variables are:•Tilt angle or equivalent•Gas inlet geometry•Wafer/carrier configuration•Wafer/reactor wall configuration•Exhaust configurationOperator variables include:•Gas flow rate•Gas composition•Temperature profile•Temperature value•ChemistryUniformity of an epitaxy layer refers to uniformity of both thickness and resistivity. Thickness is primarily controlled by the mass transport and surface reaction rates. Resistivity is controlled by dopant incorporation which, in turn, depends primarily on local concentration of dopant and local temperature.The most effective process adjustment strategy is:1.Establish a flat temperature profile with the desiredchemistry, temperature, pressure, and growth rate.2.Mechanically adjust for thickness uniformity.3.Fine tune resistivity with local temperature adjustments. Selections of chemistry, temperature, pressure, and growth rate are deter-mined by the desired materials and device properties. The usual operating conditions for commercial silicon epitaxy are presented in Table 1.The key to thickness control in a mass-transport-limited epitaxial CVD process is compensation for depletion.6.1Horizontal ReactorThe horizontal reactor depicted in Fig. 3 offers a simple model for describing how to compensate for depletion and the lessons learned here are applicable to other reactor geometries.It can be useful to break the thickness profile in the direction of gas flow along the wafer carrier or susceptor into the front and back half, as illustrated in Fig. 8. Each half can then be described as thick or thin in front, or thick or thin in back. The advantage is that the mechanical adjustments for thickness uniformity are also divided into those that affect the front half and those that affect the back half of the profile.[17]The overall concave-down profile in Fig. 9 can be described as thin in front and thin in back, rather than thick in the middle. The S-shaped profile in Fig. 9 can be described as thin in front and thick in back.Figures 10 and 11 illustrate the action necessary to correct a thickness profile that is thick or thin in the front or back. The underlying principle is that local growth rate is a direct consequence of local reaction rate. Therefore, local growth rate can be increased by increasing local velocity, temperature, and concentration, and vice-versa.Figure 8. Thickness variation possibilities along the direction of process gas flow for horizontal reactor.[17a]horizontal reactor.[17a]horizontal reactor.[17a]6.2Cylinder ReactorCorrective action for the cylinder reactor is presented in Fig. 12. In this reactor configuration, thickness is increased in the front (top of carrier) by increasing the temperature and/or concentration of reactant.Thickness is increased in the back (bottom of carrier) by increasing the total flow rate, directing the gas jets in a more downward direction, and bringing the back pressure toward a more positive value. Thickness within a wafer from left to right is improved by balancing the two jet flows, by lowering the temperature to make the overall reaction become more surface reaction rate controlled and less dependent upon rate of arrival,and by increasing the distance between the flat wafer surface and the curved bell jar. Reducing the process pressure can cause the process gas to heat more slowly, and thereby, decrease the thickness in front and increase the thickness at the back. Thickness variation at any distance along the carrier is averaged by rotation.[l7b]Figure 11. Process adjustments for correcting thickness variations in the back half of the horizontal reactor.[17a]。
纳米二氧化锆催化剂上一氧化碳加氢合成异丁烯

收稿日期:2001-12-07. 第一作者:李映伟,男,1976年生,博士研究生.联系人:贺德华.T el:(010)62772592;E -mail:hedeh@mail.tsi .基金项目:清华大学基础研究基金和清华大学分析基金资助课题.文章编号:0253-9837(2002)02-0185-06纳米二氧化锆催化剂上一氧化碳加氢合成异丁烯李映伟, 贺德华, 袁余斌, 程振兴, 朱起明(清华大学化学系一碳化学与化工国家重点实验室,北京100084)摘要:考察了纳米Zr O 2的制备方法及Al 2O 3和KOH 助剂的添加对Zr O 2催化CO 加氢合成异丁烯反应的影响.纳米Zr O 2的制备方法对ZrO 2的物理性质和催化性能有较大的影响.用超临界流体干燥法干燥并在流动N 2气氛中焙烧制得的ZrO 2催化剂对异丁烯具有较高的选择性.Al 2O 3和K OH 助剂表现出非常优良的助剂效应,在大幅度提高催化剂对i -C 4烃选择性的同时保持了和ZrO 2同样高的催化活性.催化剂的酸碱性表征结果表明,酸碱性对催化剂的催化性能影响很大,催化剂上适宜的酸碱数量和酸碱比例是影响其催化CO 加氢合成异丁烯性能的非常重要的因素.关键词:纳米催化剂,二氧化锆,一氧化碳,加氢,异构合成,异丁烯,酸碱性,助剂中图分类号:O643 文献标识码:ASynthesis of Isobutene from CO Hydrogenation over Nanosized Zirconium Dioxide -Based CatalystsLI Yingwei,HE Dehua *,YUAN Yubin,CHENG Zhenxing,ZHU Qiming(State Key L abor ator y of C1Chemistr y and T echnology ,Dep ar tment of Chemistry ,T singhua Univer sity ,Beij ing 100084,China)Abstract:T he influence of the preparation m ethods of the nanosized ZrO 2-based catalysts and the addition of Al 2O 3and KOH promoters to ZrO 2on their catalytic properties for the direct synthesis of isobutene from CO hy -drogenation w as investigated.The results indicate that the physical properties and the catalytic performance of the nanosized ZrO 2are strongly influenced by the preparation methods.The ZrO 2catalyst that is dried by the su -percritical fluid drying method then calcined in a flow of N 2is the most selective to isobutene.Al 2O 3and KOH show ex cellent promoting effects on ZrO 2and can remarkably enhance the i -C 4selectivity (6512%)in the total hydrocarbons,while surely m aintaining the CO conversion at 2019%,w hich is more than that over the pure ZrO 2(1819%).The acidic and basic properties of the Al 2O 3and KOH promoted ZrO 2-based catalysts w ere char -acterized by NH 3-TPD and CO 2-T PD.The results indicate that the catalyst performance depends strongly on the acid -base properties of the catalysts.Increasing the amounts of acid sites on ZrO 2can enhance the activity and promote the form ation of linear C 4hydrocarbons.How ever,the amounts of base sites are very important for the formation of i -C 4hydrocarbons.With the increasing of the ratio of base sites to acid sites on the catalysts,the percentage of i -C 4in the total C 4hydrocarbons increases.A certain amount of Al 2O 3and KOH added to ZrO 2en -hances both the amount of acid and base sites on ZrO 2,w hile maintaining an appropriate ratio of base sites to acid sites.Key words:nanosized catalyst,zirconium diox ide,carbon monoxide,hydrogenation,isosynthesis,isobutene,acid -base property,promoter 异构合成(isosynthesis)是指由CO 加氢生成异丁烯(和异丁烷)的反应.异丁烯是一种非常重要的化工原料,例如,它能和甲醇在大孔强酸性阳离子交换树脂催化剂的作用下合成甲基叔丁基醚(M TBE,一种清洁高效的汽油添加剂).目前,异丁烯主要来源于石油催化裂解过程中的碳四馏分,数量有限[1].因此,从煤经水煤气变换所得合成气直接合成异丁烯将可以大大缓解异丁烯供不应求的压力.异构合成反应最先由Pichler 等[2]报道,他们发现,ThO 2能在非常苛刻的反应条件(10~100M Pa)第23卷第2期 Vol.23N o.2催 化 学 报Chinese Journal of Catalysis2002年3月 M arch 2002下将合成气转化为支链C4~C8烃.但是,由于T hO2具有放射性,而且反应条件苛刻,其进一步的研究受到限制.后来,M aehashi和M aruya等[3,4]发现ZrO2也是性能优良的异构合成催化剂,能够选择性地催化合成异丁烯.近年来,人们对ZrO2体系进行了广泛的研究[5~10],但是结果表明,在该体系上的异构合成反应不能同时获得高的CO转化率和高的i-C4烃选择性.本文考察了纳米ZrO2的制备方法及Al2O3和KOH助剂的添加对ZrO2催化CO加氢合成异丁烯反应的影响,并结合催化剂酸碱性的表征结果,探讨了催化剂的酸碱性质与催化活性和选择性的关系.1实验部分1.1纳米ZrO2催化剂的制备在剧烈搅拌的条件下,将0115mol/L的ZrOCl2#8H2O(AR,北京刘李店化工厂产品)溶液滴加到沉淀剂氨水(215%,北京益利精细化学品有限公司产品)中,并保持溶液的pH值在10左右.滴加完毕后,陈化3h,制得Zr(OH)4水凝胶.将Zr(OH)4水凝胶用如下不同的方法干燥和焙烧后制得具有不同性能的纳米ZrO2催化剂.方法A:Zr(OH)4水凝胶用去离子水充分洗涤至水凝胶的离子电导率小于15L8-1,过滤,滤饼在383K空气气氛中干燥10h,然后在823K空气中焙烧3h.所制得的催化剂记作ZrO2-A.方法B:Zr(OH)4水凝胶用去离子水充分洗涤,过滤,所得滤饼在383K流动的N2气氛中干燥,然后在823K流动的N2气氛中焙烧3h.所制得的催化剂记作ZrO2-B[11,12].方法C:Zr(OH)4水凝胶用去离子水充分洗涤,过滤,所得滤饼用无水乙醇(AR)置换其中的水分,得到Zr(OH)4醇凝胶.将醇凝胶装入高压釜中,进行超临界流体干燥(乙醇为超临界溶剂,操作压力为510MPa).干燥后于823K空气中焙烧3h.所制得的催化剂记作ZrO2-C.方法D:用方法C制得的Zr(OH)4醇凝胶经超临界流体干燥后,于823K流动的N2气氛中焙烧3 h.所制得的催化剂记作ZrO2-D.方法E:将Zr(OH)4水凝胶加入到NaOH溶液中,使pH值保持在11左右,于373K下加热蒸煮回流24h.再用去离子水充分洗涤至离子电导率小于15L8-1,于383K空气中干燥10h,于823K空气中焙烧3h.所制得的催化剂记作ZrO2-E[13,14].1.2助剂的添加Zr(OH)4水凝胶用去离子水充分洗涤至水凝胶的离子电导率小于15L8-1,过滤,滤饼在383K空气气氛中干燥10h,然后在823 K空气中焙烧115h,加入一定量的C-Al2O3(北京化学试剂工厂产品)和KOH(北京益利精细化学品有限公司产品)助剂,充分混合后再在同样条件下焙烧115h.1.3催化剂表征用Br&u ker公司的D8型X射线衍射仪(Cu K A射线)测定催化剂的晶相结构.比表面积的测定在CH EM BET-3000型(Quanta Chrome 公司)自动吸附仪上进行.用XRD宽线法测定催化剂的晶粒大小.晶相组成由下述公式[15]进行计算: m(-111)/[116m(-111)+t(111)]式中,m(-111)和t(111)分别指单斜晶相和四方晶相在各自晶面上的衍射峰强度.酸碱性表征在自行搭建的NH3-TPD和CO2-T PD装置上进行,催化剂用量为100mg,脱附升温速率为20K/min,用Balzers 公司的M SC200型质谱仪检测.1.4催化剂活性评价催化剂活性评价在固定床反应器(内径为<8mm的不锈钢反应管)中进行,催化剂用量110ml.反应前催化剂在673K的N2气氛中预处理3h,再切换为合成气(CO B H2摩尔比为1B1)进行反应.用两台气相色谱仪在线分析反应物及产物.一台采用GDX-101色谱柱,热导池检测器,主要用来分析CO,CO2,CH3OH和CH3OCH3等.另一台采用<0153mm@30m的Al2O3毛细管色谱柱,氢焰检测器,用来分析烃类产物.2结果与讨论2.1制备方法对纳米ZrO2催化性能的影响催化剂的制备方法影响催化剂的结构,并最终影响催化剂的催化性能.本文以ZrOCl2#8H2O为锆盐原料,采用几种方法制备了一批不同比表面积、晶相结构和晶粒大小的催化剂,以系统考察这些物性的变化对催化剂催化性能的影响.2.1.1催化剂的表征结果不同方法制备的ZrO2催化剂的表征结果见表1.可以看出,在N2气氛中焙烧的催化剂(ZrO2-B和ZrO2-D)具有较大的比表面积和较小的粒径.原因可能是,在常规的热处理过程中,随着水分的蒸发,气液界面产生毛细管张力,毛细孔的孔径逐渐变小,一部分水被封锁在较186催化学报第23卷表1 用不同方法制备的纳米ZrO 2催化剂的物性表征结果T able 1 Physical properties of the nanosized ZrO 2catalystsprepared by different m ethods Catalyst a Surface area (m 2/g)Crystal phase (%)M onoclinicT etragonalParticlesize (nm)ZrO 2-A 51100027ZrO 2-B 143307014ZrO 2-C 79475318ZrO 2-D 136425816ZrO 2-E2291007a.After precipitation,Zr (OH)4hydrogel w as calcined in air (ZrO 2-A),or calcined in flow ing N 2(ZrO 2-B ),or treated w ith supercritical ethanol and calcined in air (ZrO 2-C ),or treated w ith supercritical ethanol and calcined in flow ing N 2(ZrO 2-D),or refluxed in NaOH solution (ZrO 2-E).表2 制备方法对ZrO 2催化剂催化异构合成反应性能的影响T able 2 Influence of the preparation methods on the performance of the ZrO 2catalysts for the isosynthesisCatalyst CO conversion(%)S electivi ty for products (%)aCO 2CH 3OH+CH 3OCH 3HydrocarbonsDistri bution of hydrocarbons (%)aC 1~C 3C 4C +5i -C 4ZrO 2-A 18.951.37.341.423.351.625.141.4ZrO 2-B 21.734.68.656.818.462.219.347.7ZrO 2-C 24.538.3 5.556.219.756.623.842.3ZrO 2-D 23.039.7 6.553.713.470.915.753.0ZrO 2-E6.445.654.462.537.15.511.3Reaction conditions:673K,510M Pa,GHSV=650h -1,CO/H 2molar rati o=1.a.T he fraction is on carbon molar basis.表3 Al 2O 3和K OH 改性的ZrO 2催化剂的表征结果Table 3 Characterization results of the Al 2O 3and KOH promoted ZrO 2catalys tsNo Content of Al 2O 3a (%)Content of KOH a (%)Particle si z e b (nm )Surface area (m 2/g)Amount of acid sites (L mol/g)Amount of base si tes (L mol/g)100155440.686.62 5.60145852.480.5316.90166463.067.5435.10167181.660.75100c0515683.140.9600.5165521.9160.577.40.5166237.7141.9815.30.5147545.7139.3923.70.5157547.1128.81040.80.5148050.3112.6a.M easured by X -ray fluorescence diffraction.b.Calculated from the X -ray li ne broadening analysis.c.Pure Al 2O 3catal yst (commercial).小的孔中,产生较大的蒸气内压而导致结构塌陷,从而引起催化剂比表面积的减小和粒子聚集加剧[16];用溶剂置换凝胶中的水,或在流动气氛中及时带走表面水分,就可以减小气液界面张力,防止塌陷,从而制得有较大比表面积和较小粒径的催化剂.ZrO 2-E 的比表面积最大,可能是因为加热蒸煮回流有利于防止粒子的聚集.XRD 表征结果表明,用不同方法制得的ZrO 2具有不同的晶相结构.其中方法A 制备的ZrO 2主要为单斜晶相,方法E 制得的ZrO 2主要为四方晶相,而其它方法制得的ZrO 2则为单斜和四方混合的晶相结构.2.1.2 催化剂的活性评价结果 催化剂的活性评价结果如表2所示.一般来说,具有较高比表面积的催化剂,由于暴露的活性中心较多,其催化活性应较高.而表2表明,催化剂对异构合成反应的催化活性与其比表面积没有明显的顺变关系.用蒸煮法制备的催化剂(ZrO 2-E )虽然具有最大的比表面积,但其CO 的转化率(6%左右)却很低,说明催化剂的比表面积并不是影响催化剂活性的关键因素.在N 2气氛中焙烧的催化剂上(ZrO 2-B 和ZrO 2-D)i -C 4烃选择性较高,其中方法D 制备的ZrO 2上i -C 4选择性(53%左右)最高,而且具有较高的C 4选择性(71%左右).这可能是因为在流动的N 2气氛下,催化剂孔道中的溶剂容易蒸发出来,降低了气液表面的张力,可以得到较大孔径的催化剂,而这些大孔又有利于碳链的增长而形成C +4烃.ZrO 2-E 催化剂不仅活性较低,而且烃类产物中绝大部分为CH 4和C 2H 6,i -C 4的选择性(11%左右)很低.2.2 Al 2O 3和KOH 助剂对ZrO 2催化性能的影响187第2期李映伟等:纳米二氧化锆催化剂上一氧化碳加氢合成异丁烯2.2.1 改性催化剂的表征结果 Al 2O 3和KOH 助剂改性的ZrO 2基催化剂的表征结果如表3所示.可以看出,随着Al 2O 3含量的增加,催化剂的比表面积增大.这可能是Al 2O 3的比表面积(156m 2/g)比纯ZrO 2(54m 2/g)大得多的缘故.但是催化剂晶粒和晶相组成随Al 2O 3的加入变化不大.单斜相是Al 2O 3和KOH 改性的锆基催化剂的主要晶相.NH 3-TPD 和CO 2-TPD 表征结果表明,催化剂表面的酸碱量随着助剂Al 2O 3和KOH 的加入变化较大.从表3可以看出,纯Al 2O 3表面具有比纯ZrO 2更多的酸位和更少的碱位数量.所以,随着Al 2O 3的加入,ZrO 2催化剂的酸位数量增多,而碱位数量减少.当Al 2O 3含量增加到35%时(No 4),其酸位数量接近纯Al 2O 3的酸位数量.另一方面,KOH 的加入增加了ZrO 2表面的碱位数量而减少了酸位数量(No 6).Al 2O 3-KOH 改性的ZrO 2催化剂的表面酸、碱位数量也随着Al 2O 3的加入而呈现和Al 2O 3-ZrO 2催化剂相同的变化趋势,但其变化幅度要比后者缓和得多.表4 Al 2O 3和KO H 改性的Z rO 2基催化剂的活性评价结果T able 4 Catalytic performan ce of the Al 2O 3and KOH promoted ZrO 2catal ysts for the is osynthesisNo Content of Al 2O 3(%)Content of KOH (%)CO conversion(%)Di stribution of hydrocarbons (%)C 1C 2C 3C 4C 5C +6i -C 4(i -C =4)10018.97.810.4 4.451.618.47.442.3(41.1)2 5.6020.78.09.3 5.160.111.6 5.945.5(42.4)316.9025.97.37.9 5.467.88.8 2.844.8(41.2)435.1020.19.37.97.256.814.2 4.633.8(28.7)51000 5.246.020.510.010.313.20.0 2.2(1.3)3.a16.9036.611.420.18.655.2 3.90.839.5(32.2)600.515.816.69.08.641.219.1 5.536.2(31.1)77.40.518.112.1 6.7 3.564.610.6 2.555.2(50.4)815.30.520.9 2.7 4.0 2.577.59.5 3.865.2(62.3)923.70.522.3 3.8 4.8 2.977.87.3 3.464.0(60.8)1040.80.523.314.78.15.261.88.31.945.2(38.5)Reaction conditions:673K,5.0M Pa,GHSV=650h -1,CO/H 2molar rati o=1.a.Reaction at 723K.2.2.2 改性催化剂的活性评价结果 Al 2O 3-ZrO 2和Al 2O 3-KOH -ZrO 2催化剂的活性评价结果如表4所示.空白实验表明,在本实验条件下,不锈钢管的反应活性(<1%)很低,且产物中大部分为甲烷和乙烷等低碳烷烃,没有C +4烃产物生成.从表4可以看出,采用普通沉淀法制备且未添加助剂的ZrO 2即具有一定的异构合成催化活性(No 1),在673K 时,其CO 转化率为1819%,烃类产物中i -C 4选择性为4213%.据研究报道,较高的反应压力有利于重碳烃类物质的生成[6,8].但是在本研究中,在纯ZrO 2催化剂上,烃类产物中C +5烃类的生成量(25%)比文献报道的同条件下的(\50%)少得多.升高反应温度提高了CO 转化率,但同时也导致大量的低碳烃类物质(C 1~C 3)的生成.在1619%Al 2O 3-ZrO 2催化剂上,当反应温度升至723K 时(No 3.),CO 转化率能提高到3616%,但同时C 1~C 3烃类产物的选择性增加至40%左右,而烃类产物中异丁烯的选择性降低到3212%.从表4可以看出,Al 2O 3改性的ZrO 2催化剂的催化活性随着Al 2O 3加入量的增加而提高.1619%Al 2O 3-ZrO 2催化剂上的CO 转化率最高,为26%左右,与纯ZrO 2催化剂(CO 转化率为1819%)相比,活性得到了很大的提高.同时,烃类产物中C 4烃的选择性增大,而C +5烃的选择性大幅度降低.然而,Al 2O 3的加入对i -C 4烃的生成没有明显影响,而且当Al 2O 3的加入量增加到35%时,催化剂的活性和i -C 4烃选择性都下降(No 4).作为对比,也对纯Al 2O 3进行了活性评价.可以看出,纯Al 2O 3(No 5)对异构合成反应的催化活性仅为纯ZrO 2催化剂的1/4左右,而且主要产物为甲烷,i -C 4的选择性(212%)很低.纯Al 2O 3虽然具有比ZrO 2大得多的比表面积和较小的粒径,但是它并不能催化异构合成反应.据研究报道[17],在F -T 合成催化剂(如Fe)中加入少量的碱金属组分(如K 2O,K 2CO 3等)能显著增加催化剂的活性和产物中高分子烃类的选择性.考虑到异构合成反应与F -T 合成反应的相似性(从合成气出发合成烃类),我们将KOH 加入到ZrO 2中,以期能起到与传统F -T 合成催化剂中碱金属组188催 化 学 报第23卷分相似的助剂作用.Al 2O 3-KOH 改性的锆基催化剂的反应评价结果见表4.从表4可以看出,与F -T 合成中不同,少量KOH 的加入对ZrO 2的催化性能有负效果,导致反应活性和烃类产物中i -C 4烃选择性大大降低.但是,当Al 2O 3和KOH 同时加入到ZrO 2中时,反应活性和选择性能都得到很大的提高(No 7~9).与Al 2O 3-ZrO 2催化剂相似,Al 2O 3-KOH -ZrO 2催化剂的催化活性也随着催化剂中Al 2O 3含量的增加而增大(KOH 的量恒为015%).但当Al 2O 3含量增加到2317%时,CO 的转化率达到2213%.可以发现,随着Al 2O 3的加入,催化剂上的C 4和i -C 4的选择性大大提高.C 4选择性最高为7718%(No 9),比纯ZrO 2催化剂(5116%)大得多.与Al 2O 3-ZrO 2催化剂不同的是,Al 2O 3-KOH -ZrO 2上烃类产物中i -C 4的选择性也得到很大的提高.对于1513%Al 2O 3-015%KOH -ZrO 2催化剂(No 8),i -C 4的选择性为6512%,是纯ZrO 2的115倍左右.但是,当Al 2O 3的添加量增加到40%以上时,C 4和i -C 4烃的选择性又大大降低.过量Al 2O 3的加入对异构合成反应具有负面影响,可能是因为Al 2O 3本身基本上不具有催化异构合成反应的性能(No 5).图1 Al 2O 3和KO H 改性的ZrO 2催化剂表面酸位数量与催化活性的关系Fig 1 Relationship betw een CO conversion and amount of acidsites on th e ZrO 2catalysts promoted by Al 2O 3and KOH(#)3511%Al 2O 3-ZrO 22.2.3 酸碱性对改性催化剂性能的影响 将催化剂的酸碱性表征结果(表3)与催化剂的活性评价结果(表4)进行关联,发现改性催化剂的催化性能与其表面酸碱性存在着很大的相关性.图1示出了Al 2O 3-ZrO 2和Al 2O 3-KOH -ZrO 2催化剂的催化活性和表面酸位数量的关系.从图中可以看出,除3511%Al 2O 3-ZrO 2催化剂外,催化剂的活性随着表面酸量的增加而增大.这说明CO 分子更易在催化剂的酸位上进行吸附和活化[10].单独加入KOH 导致活性大大下降可能是因为KOH 的加入大大降低了催化剂表面的酸位数量(2119L mol/g,而纯ZrO 2为4016L mol/g).3511%Al 2O 3-ZrO 2催化剂活性较低的原因可能是过量Al 2O 3的加入使ZrO 2催化剂的性质发生了变化,因为前已证实纯Al 2O 3并不具有催化异构合成反应的性能.同时,增加催化剂表面酸位数量提高了烃类产物中直链C 4烃的选择性,如图2所示.然而,太多的酸位数量并不利于i -C 4烃的生成.从图2中可以看出,适宜数量的酸位有利于i -C 4烃的生成.图2 Al 2O 3和K OH 改性的ZrO 2催化剂表面酸位数量与烃类产物中n -C 4和i -C 4烃选择性的关系Fig 2 Relationship between n -C 4and i -C 4selectivity in totalhydrocarbons and amount of acid sites on the ZrO 2cat -alysts promoted by Al 2O 3andKOH图3 Al 2O 3和K OH 改性的ZrO 2催化剂表面碱位数量与烃类产物中n -C 4和i -C 4烃选择性的关系Fig 3 Relationship between n -C 4and i -C 4selectivity in totalhydrocarbons and amount of base si tes on the ZrO 2cat -alysts promoted by Al 2O 3and KOH(#)015%KOH -ZrO 2图3示出了催化剂表面碱位数量与烃类产物中直链C 4烃和支链C 4烃选择性的关系.可以看出,189第2期李映伟等:纳米二氧化锆催化剂上一氧化碳加氢合成异丁烯除015%KOH -ZrO 2催化剂外,烃类产物中i -C 4选择性随着锆基催化剂表面碱位数量的增加而增大.M aruya 等[4]报道了类似的结果.015%KOH -ZrO 2催化剂上的异构合成反应活性较差可能是因为KOH 在一定程度上降低了ZrO 2表面的酸量,导致碳链增长比较困难,从而大大降低了烃类产物中C +4烃的选择性(表4,No 6).这说明催化剂表面酸性和碱性对异构合成中的碳链增长步骤都非常重要[5,9].从图3还可以看出,催化剂表面碱量和烃类产物中n -C 4的选择性没有明显的顺变关系.因此,催化剂表面碱性对i -C 4烃的生成非常重要.如果异构合成中异丁烯的生成遵循醇醛缩合机理[9],催化剂的表面碱位将是C 3氧化物中活性氢脱除的必不可少的活性位.比较催化剂表面的酸碱比例可以看出,凡是具有较大碱/酸比的催化剂,其C 4烃类产物中i -C 4的含量较高,如图4所示.由此推测n -C 4和i -C 4是在催化剂不同的活性位上生成的,虽然目前还不清楚活性位的具体结构和性质,但是可以肯定这些活性位和催化剂表面酸碱性有着一定的联系.图4 ZrO 2催化剂表面碱酸比和产物中i -C 4和n -C 4烃比的关系Fig 4 Relationship betw een the i -C 4/n -C 4ratio and thebase sites/aci d sites ratio of the ZrO 2catalysts从以上结果可以看出,Al 2O 3和KOH 表现出非常优良的助剂效应,在大幅度提高i -C 4烃选择性的同时保持了和纯ZrO 2同样高的催化活性.催化剂的表面酸性和碱性对异构合成反应都非常重要.增加催化剂表面的酸位数量能提高催化反应活性和烃类产物中n -C 4烃的选择性.而增加碱位数量却能提高烃类产物中i -C 4烃的选择性.催化剂表面碱位与酸位的比例将决定C 4烃类产物中i -C 4的比例.一定量Al 2O 3和KOH 的加入能同时提高ZrO 2表面的酸碱量并保持适宜的表面碱酸比例.参考文献1 蔡启瑞,彭少逸.碳一化学中的催化作用.北京:化学工业出版社(Cai Q R,P eng Sh Y.Catalysis in C1Chem -istry.Beijing:Chem Ind Press),1995.3492 Pichler H,Ziesecke K H.Brennst Chem ,1949,30(1):13 M aehashi T ,M aruya K,Domen K,Aika K,Onishi T.Chem Lett ,1984,(5):7474 M aruya K ,M aehashi T ,Haraoka T ,N arui S,Asakaw a Y ,Domen K ,Onishi T.Bull Chem Soc Jp n ,1988,61(3):6675 Jackson N B,Ekerdt J G.J Catal ,1990,126(1):316 Postula W S,Feng Z,Philip C V,A kg er man A,A nthony R G.J Catal ,1994,145(1):1267 Jackson N B,Ekerdt J G.J Catal ,1990,126(1):468 M aruya K ,T akasawa A,Har aoka T ,Domen K ,O nishi T .J Mol Catal A :Chem ,1996,112(1):1439 M aruya K,Komiy a T ,Hayakawa T ,L u L ,Yashima M.J M ol Catal A :Chem ,2000,159(1):9710 Su C,L i J,He D,Cheng Z,Zhu Q.A pp l Catal A ,2000,202(1):8111 Xu B -Q ,Wei J -M ,W ang H -Y ,Sun K -Q,Zhu Q -M.Cataly T oday ,2001,68(1-3):21712 徐柏庆,魏俊梅,程振兴,李晋鲁,朱起明(Xu B Q,Wei J M ,Cheng Zh X,L i J L,Zhu Q M ).CN 1280882A.200113 尹双凤,徐柏庆,朱起明.催化学报(Yin Sh F,Xu B Q ,Zhu Q M.Chin J Catal)),2001,22(5):49414 徐柏庆,尹双凤,张昕,魏俊梅,朱起明(Xu B Q ,Y inSh F,Zhang X,W ei J M ,Zhu Q M ).CN 1267568A.200015 T rens P,Hudson M J,Denoyel R.J M ater Chem ,1998,8(9):214716 Gesser H D,Goswami P C.Chem Rev ,1989,89(4):76517 Dry M E,Shingles T ,Boshoff L J.J Catal ,1972,25(1):99(Ed LYX)190催 化 学 报第23卷。
《Silicon Liquid Phase Epitaxy(EPILIFT液相外延硅太阳能电池)》原创译文
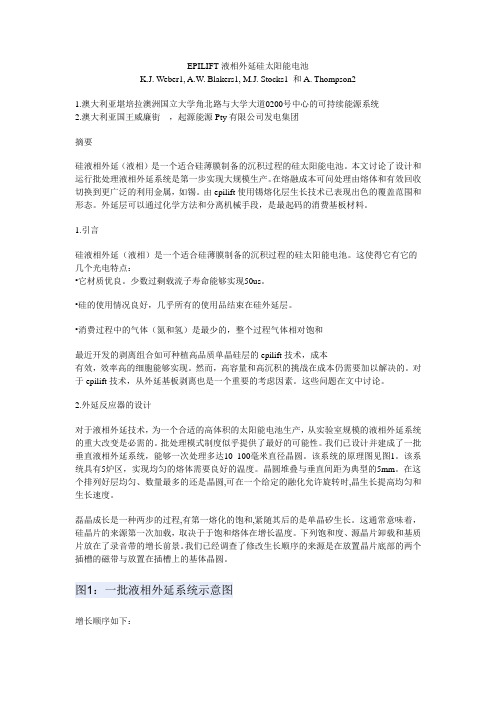
EPILIFT液相外延硅太阳能电池K.J. Weber1, A.W. Blakers1, M.J. Stocks1 和A. Thompson21.澳大利亚堪培拉澳洲国立大学角北路与大学大道0200号中心的可持续能源系统2.澳大利亚国王威廉街,起源能源Pty有限公司发电集团摘要硅液相外延(液相)是一个适合硅薄膜制备的沉积过程的硅太阳能电池。
本文讨论了设计和运行批处理液相外延系统是第一步实现大规模生产。
在熔融成本可问处理由熔体和有效回收切换到更广泛的利用金属,如锡。
由epilift使用锡熔化层生长技术已表现出色的覆盖范围和形态。
外延层可以通过化学方法和分离机械手段,是最起码的消费基板材料。
1.引言硅液相外延(液相)是一个适合硅薄膜制备的沉积过程的硅太阳能电池。
这使得它有它的几个光电特点:•它材质优良。
少数过剩载流子寿命能够实现50us。
•硅的使用情况良好,几乎所有的使用品结束在硅外延层。
•消费过程中的气体(氮和氢)是最少的,整个过程气体相对饱和最近开发的剥离组合如可种植高品质单晶硅层的epilift技术,成本有效,效率高的细胞能够实现。
然而,高容量和高沉积的挑战在成本仍需要加以解决的。
对于epilift技术,从外延基板剥离也是一个重要的考虑因素。
这些问题在文中讨论。
2.外延反应器的设计对于液相外延技术,为一个合适的高体积的太阳能电池生产,从实验室规模的液相外延系统的重大改变是必需的。
批处理模式制度似乎提供了最好的可能性。
我们已设计并建成了一批垂直液相外延系统,能够一次处理多达10 100毫米直径晶圆。
该系统的原理图见图1。
该系统具有5炉区,实现均匀的熔体需要良好的温度。
晶圆堆叠与垂直间距为典型的5mm。
在这个排列好层均匀、数量最多的还是晶圆,可在一个给定的融化允许旋转时,晶生长提高均匀和生长速度。
磊晶成长是一种两步的过程,有第一熔化的饱和,紧随其后的是单晶矽生长。
这通常意味着,硅晶片的来源第一次加载,取决于于饱和熔体在增长温度。
差速贴壁技术对大鼠脑皮质星形胶质细胞纯化率的影响
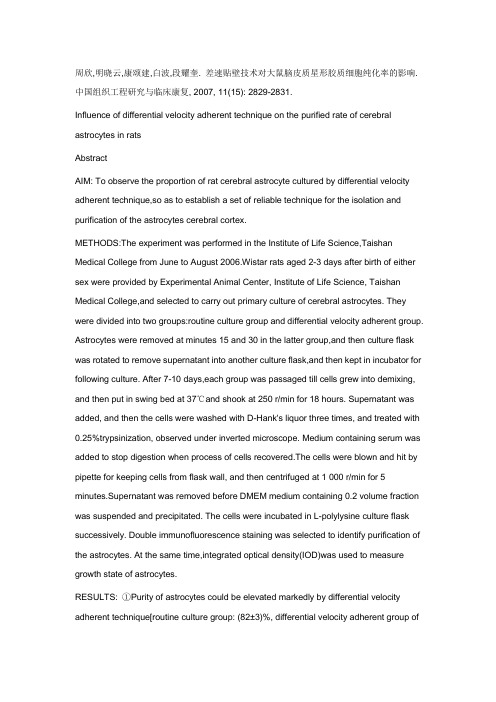
周欣,明晓云,康颂建,白波,段耀奎. 差速贴壁技术对大鼠脑皮质星形胶质细胞纯化率的影响. 中国组织工程研究与临床康复, 2007, 11(15): 2829-2831.Influence of differential velocity adherent technique on the purified rate of cerebral astrocytes in ratsAbstractAIM: To observe the proportion of rat cerebral astrocyte cultured by differential velocity adherent technique,so as to establish a set of reliable technique for the isolation and purification of the astrocytes cerebral cortex.METHODS:The experiment was performed in the Institute of Life Science,Taishan Medical College from June to August 2006.Wistar rats aged 2-3 days after birth of either sex were provided by Experimental Animal Center, Institute of Life Science, Taishan Medical College,and selected to carry out primary culture of cerebral astrocytes. They were divided into two groups:routine culture group and differential velocity adherent group. Astrocytes were removed at minutes 15 and 30 in the latter group,and then culture flask was rotated to remove supernatant into another culture flask,and then kept in incubator for following culture. After 7-10 days,each group was passaged till cells grew into demixing, and then put in swing bed at 37℃and shook at 250 r/min for 18 hours. Supernatant was added, and then the cells were washed with D-Hank's liquor three times, and treated with 0.25%trypsinization, observed under inverted microscope. Medium containing serum was added to stop digestion when process of cells recovered.The cells were blown and hit by pipette for keeping cells from flask wall, and then centrifuged at 1 000 r/min for 5 minutes.Supernatant was removed before DMEM medium containing 0.2 volume fraction was suspended and precipitated. The cells were incubated in L-polylysine culture flask successively. Double immunofluorescence staining was selected to identify purification of the astrocytes. At the same time,integrated optical density(IOD)was used to measure growth state of astrocytes.RESULTS: ①Purity of astrocytes could be elevated markedly by differential velocity adherent technique[routine culture group: (82±3)%, differential velocity adherent group of15 minutes: (94±2)%, differential velocity adherent group of 30 minutes: (95±2)%, P<0.01. Differential velocity adherent technique needed enough time. There was no significant difference in elevating cell purity in the 15 minutes group and 30 minutes group. ②IOD of astrocytes in the differential velocity adherent group was higher than that in the routine culture group(routine culture group: 528±25, differential velocity adherent group of 15 minutes: 972±17, differential velocity adherent group of 30 minutes: 996±35, P<0.05. CONCLUSION:①The differential velocity adherent technique can remarkably elevate the purity of astrocytes, and the growth is distinctly better than that by routine culture method.②The best differential velocity adherent time is 15 minutes, and there is no significant effect of longer adherent time on elevating purity.Zhou X, Ming XY, Kang SJ, Bai B ,Duan YK. Influence of differential velocity adherent technique on the purified rate of cerebral astrocytes in rats. Zhongguo Zuzhi Gongcheng Yanjiu yu Linchuang Kangfu 2007; 11(15): 2829-2831(China)摘要目的: 观察差速贴壁技术对星形胶质细胞纯化率的影响,旨在建立一套可靠的大鼠脑皮质星形胶质细胞的取材分离、纯化培养技术。
锂离子电池负极材料钛酸锂的研究评述
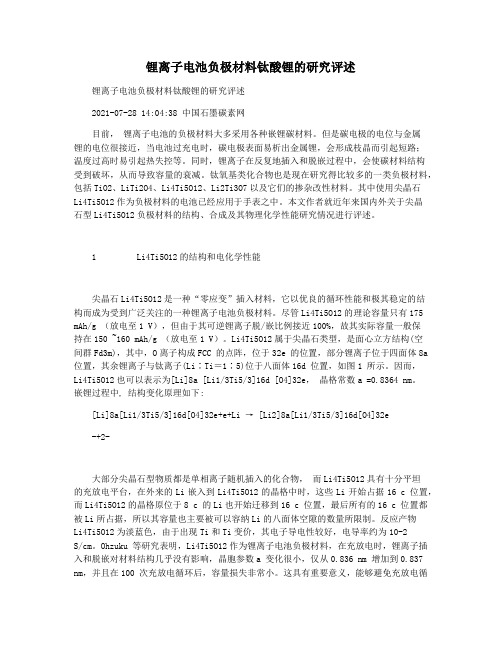
锂离子电池负极材料钛酸锂的研究评述锂离子电池负极材料钛酸锂的研究评述2021-07-28 14:04:38 中国石墨碳素网目前,锂离子电池的负极材料大多采用各种嵌锂碳材料。
但是碳电极的电位与金属锂的电位很接近,当电池过充电时,碳电极表面易析出金属锂,会形成枝晶而引起短路;温度过高时易引起热失控等。
同时,锂离子在反复地插入和脱嵌过程中,会使碳材料结构受到破坏,从而导致容量的衰减。
钛氧基类化合物也是现在研究得比较多的一类负极材料,包括TiO2、LiTi2O4、Li4Ti5O12、Li2Ti3O7以及它们的掺杂改性材料。
其中使用尖晶石Li4Ti5O12作为负极材料的电池已经应用于手表之中。
本文作者就近年来国内外关于尖晶石型Li4Ti5O12负极材料的结构、合成及其物理化学性能研究情况进行评述。
1 Li4Ti5O12的结构和电化学性能尖晶石Li4Ti5O12是一种“零应变”插入材料,它以优良的循环性能和极其稳定的结构而成为受到广泛关注的一种锂离子电池负极材料。
尽管Li4Ti5O12的理论容量只有175 mAh/g (放电至1 V),但由于其可逆锂离子脱/嵌比例接近100%,故其实际容量一般保持在150 ~160 mAh/g (放电至1 V)。
Li4Ti5O12属于尖晶石类型,是面心立方结构(空间群Fd3m),其中,O离子构成FCC 的点阵,位于32e 的位置,部分锂离子位于四面体8a 位置,其余锂离子与钛离子(Li∶Ti=1∶5)位于八面体16d 位置,如图1 所示。
因而,Li4Ti5O12也可以表示为[Li]8a [Li1/3Ti5/3]16d [O4]32e,晶格常数a =0.8364 nm。
嵌锂过程中, 结构变化原理如下:[Li]8a[Li1/3Ti5/3]16d[O4]32e+e+Li → [Li2]8a[Li1/3Ti5/3]16d[O4]32e-+2-大部分尖晶石型物质都是单相离子随机插入的化合物,而Li4Ti5O12具有十分平坦的充放电平台,在外来的Li嵌入到Li4Ti5O12的晶格中时,这些Li开始占据16 c 位置,而Li4Ti5O12的晶格原位于8 c 的Li也开始迁移到16 c 位置,最后所有的16 c 位置都被Li所占据,所以其容量也主要被可以容纳Li的八面体空隙的数量所限制。
- 1、下载文档前请自行甄别文档内容的完整性,平台不提供额外的编辑、内容补充、找答案等附加服务。
- 2、"仅部分预览"的文档,不可在线预览部分如存在完整性等问题,可反馈申请退款(可完整预览的文档不适用该条件!)。
- 3、如文档侵犯您的权益,请联系客服反馈,我们会尽快为您处理(人工客服工作时间:9:00-18:30)。
Epitaxial Y-stabilized ZrO2films on silicon:Dynamic growth process and interface structureS.J.Wang and C.K.Ong a)Center for Superconducting and Magnetic Materials(CSMM),and Department of Physics,National University of Singapore,Singapore119260͑Received11December2001;accepted for publication5February2002͒We have studied the initial stage of the growth of yttria-stabilized zirconia͑YSZ͒films on nativelyoxidized͑100͒Si wafer by pulsed-laser deposition.X-ray photoelectron spectroscopy andhigh-resolution electron microscopy show that,for thefirst few monolayers of crystalline YSZdeposited on͑100͒Si,the dynamic processes appear to be the decomposition of SiO2to SiO,theformation of ZrO2,and the desorption of SiO.The native amorphous SiO2layer is removedcompletely with the continued deposition of YSZ.The atomically sharp and commensurate YSZ/Siinterface is suggested to have a sequence of Si–Si–O–Zr–O–.©2002American Institute ofPhysics.͓DOI:10.1063/1.1467970͔Developments in the semiconductor industry over thepast20years have dramatically reduced the feature size ofmetal-oxide-semiconductor transistors,and the gate oxideSiO2thickness has been scaled down to around2nm.1,2Tofurther the ambition of minimizing feature sizes,alternativegate dielectrics with much higher dielectric constant͑⑀͒are needed to replace the conventional SiO2(⑀silicaϳ4)3,4dielec-trics.Crystalline oxides on silicon as alternative gatedielectrics,5–9maintaining one-to-one atomic correspon-dence at the oxide/silicon interface without the formation ofan underlying SiO2layer,are expected to have excellentphysical properties and chemical stability.However,the is-sue concerning the dynamic growth process of crystallineoxide on silicon is a very crucial step and should be solvedfirst for the implementation of this structure.In this letter wepresent experimental results that reveal the dynamic growthmechanism of crystalline oxide on natively oxidized siliconwafer.Yttria-stabilized zirconia͑YSZ͒is chosen as the targetmaterial,as it has a sufficiently large electron barrier10andexcellent thermodynamic stability in contact with Si at tem-perature up to900°C.10–16The pulsed laser deposition sys-tem with a base vacuum of5ϫ10Ϫ7mbar is used to growYSZfilms on͑100͒Si.9,17All the Si substrates were cut fromone piece of as-purchased Si wafer used in chip manufactur-ing.This is to ensure that each substrate has an identicalnative oxide layer,surface morphology and crystalline orien-tation.As determined by high-resolution transmission elec-tron microscopy͑HRTEM͒analysis,the thickness of the na-tive SiO2is around 1.0–1.5nm.The Si substrates areultrasonically cleaned in dilute nitric acid and then thor-oughly rinsed.In this treatment the amorphous SiO2layerremains on the substrates.The deposition is done at a sub-strate temperature of730°C in an ambient oxygen pressureof6–8ϫ10Ϫ6mbar.This pressure is just above the transi-tion line from passive oxidation to active oxidation in theP–T phase diagram of silicon oxidation,and at the same timethe desorption of SiO can be expected to take place in this condition.18–20Laserfluence͑wavelength248nm͒of1.5J/cm2and laser repetition frequency of3Hz are set for allthe samples.YSZfilms are deposited for only5,10,20,and30s,respectively.For the30sfilm,the thickness is about1.5nm.As the deposition of YSZ is performed at a temperatureover700°C,one concern would be whether the thickness ofnative SiO2on substrate remains the same or increases.Fig-ures1͑a͒and1͑b͒show the x-ray photoelectron spectroscopy ͑XPS͒spectra obtained from an as-cleaned substrate and a substrate which has been heated in the deposition chamber at730°C for5min in the deposition pressure but without thedeposition of YSZ,paring Fig.1͑b͒withFig.1͑a͒,the intensity of the Si2p peak at103.6eV,corre-sponding to the binding energy of SiO2,does not increasea͒Electronic mail:phyongck@.sgFIG.1.Si2p core-level XPS spectra of samples without YSZ deposition͑a͒as deposited,͑b͒heated,and with YSZ deposition for5͑c͒,10͑d͒,20͑e͒,and30͑f͒s,respectively.APPLIED PHYSICS LETTERS VOLUME80,NUMBER148APRIL200225410003-6951/2002/80(14)/2541/3/$19.00©2002American Institute of Physics Downloaded 23 Nov 2002 to 137.132.3.12. Redistribution subject to AIP license or copyright, see /aplo/aplcr.jspsignificantly;this implies that the heating treatment does not result in considerable further oxidation of the Si surface.In the series of samples where YSZ thin films are deposited on the substrates for 5,10,20,and 30s,an evolution of the Si 2p peaks in both intensity and position in their XPS spectra ͓Figs.1͑c ͒–1͑f ͔͒can be paring the Si 2p peaks in Figs.1͑b ͒and 1͑f ͒,we find that the intensity from Si is dramatically reduced in the latter.This reduction is due to the substrate being covered by a layer of ZrO 2film that attenuates the photoelectron signals.Although the thickness of ZrO 2layer is different for dif-ferent samples and it is hard to extract the variation of SiO 2thickness from the intensity variation by simulation,the bond information can be obtained from the shift of the peak loca-tions.The Si 2p peak corresponding to SiO 2shifts towards lower binding energy,from 103.6eV ͓Fig.1͑b ͔͒to 102.8eV ͓Fig.1͑f ͔͒.This can be attributed to two causes:one is the oxygen loss for SiO 2layer;another one is the formation of silicate.21–23In order to check this kinetic process,we turn to O 1s and Zr 3d core-level spectra to examine the nature of oxide formed on the silicon,shown in Figs.2and 3,respectively.Before the deposition of YSZ,both native substrate and heated substrate present only a peak near 533eV ,corre-sponding to the O 1s binding energy for SiO 2.The slight shift of the O 1s peak 0.3eV towards higher binding energy,together with the enhancement of the Si 2p peak intensity shown in Fig.1͑b ͒,are attributed to the incorporation of a small amount of oxygen atoms into the substrate surface dur-ing the heating process.However,after YSZ is deposited for 5s,the peak at 533eV disappears and a peak at 530.5eV emerges.With increasing YSZ thickness,this peak keeps on shifting towards lower energy and fixes its position at 529.4eV after deposition of 2–3ML of YSZ ͑20–30s of deposi-tion ͒.The binding energy of O 1s in ZrO 2is 529.4eV .The O 1s binding energy for silicate is in the range 531.1–532.0eV .21–23The jump of peak to 530.3eV for the 5s sample in Fig.2could be considered as the combination of a dominat-ing O 1s peak from ZrO 2,and a weak O 1s peak from oxygen deficient SiO x (x Ͻ2)and the silicate.With contin-ued YSZ deposition,the peak shape becomes sharper and the peak shifts to lower binding energy at 529.4eV ,correspond-ing to that of ZrO 2.In addition,as seen from the HRTEM image in Fig.4͑a ͒,the YSZ films are found to grow epitaxi-ally on ͑100͒Si substrate.From the film surface to the inter-face,the films show uniform atomic pattern,cubic YSZ structure,which had been confirmed by the electron diffrac-tion pattern and the x-ray diffraction pattern.24The epitaxial relationship between YSZ and silicon is YSZ ͑001͒ʈSi ͑001͒and YSZ ͓100͔ʈSi ͓100͔.Figure 4͑a ͒shows a magnified HRTEM interface image of crystalline YSZ film on ͑100͒Si wafer.It can be clearly seen that there is no amorphous in-terfacial oxide at the interface.The simulated HRTEM image of crystalline YSZ on silicon ͓in Fig.4͑b ͔͒is well in agree-ment with experimental HRTEM image,indicating that the film on silicon is cubic YSZ film.Based on the HRTEM cross-section images of the YSZ/Si interface in Fig.4͑a ͒and the priority sequence for forming different stable phases,25the atomic structure of the YSZ/Si interface is proposed to be –Si–O–Zr–O–as shown in Fig.4͑c ͒.Therefore,we think,when the deposited film is very thin ͑such as 5and 10s samples ͒and the native SiO 2layer has not been completely removed,the deposited YSZ reacts with part of SiO 2to form Zr–silicate;the Si–O–Zr and Si–O bonds in the silicate and SiO 2contribute greatly to the XPS O 1s peaks.But in the oxygen deficient environment,the Zr ions will absorb the oxygen atoms in the silicate layer,and the silicate will de-compose with the continued deposition of YSZ to form stable ZrO 2.11Recent experiment indicates there is no sili-cate forming during subsequent rapid thermal annealing of ZrO 2in high oxygen pressure.15Thus the formation of ZrO 2is an irreversible process,and the original amorphous SiO 2is removed with the progress of film deposition.As we noted before,all the films are fabricated onna-FIG.2.O 1s core-level XPS spectra of substrates and the samples with YSZdeposition.FIG.3.Zr 3d core-level XPS spectra of the samples with YSZdeposition.FIG.4.͑a ͒An original HRTEM cross-section image of crystalline YSZ on ͑100͒Si;͑b ͒simulated HRTEM image of crystalline ZrO 2on silicon ͑viewed from the direction of Si ͓110͔͒;͑c ͒schematic atomic structure of the interface ZrO 2/Si.͑The white lines represent the position of the YSZ/Si interface.͒Downloaded 23 Nov 2002 to 137.132.3.12. Redistribution subject to AIP license or copyright, see /aplo/aplcr.jsptively oxidized silicon wafers.The thickness of native oxideis about1.5nm.However,no amorphous SiO2layer can beobserved at the YSZ/Si interface.Therefore,we think thisphenomenon is due to the following chemical reaction at theinitial stage of YSZ deposition on natively oxidized Si wa-fers:ZrϩSiO2→Zr–silicate→ZrO2ϩSiO or ZrϩSiO2→ZrO2ϩSiO,followed by the desorption process of SiO because of low ambient oxygen pressure and hightemperature.20This view is further supported by Zr3d spec-tra and HRTEM analysis.In contrast to the change in the Si2p and O1s bindingenergies,the XPS spectra of Zr3d5/2͑183.2eV͒and Zr3d3/2͑185.6eV͒peaks only show enhanced intensity but without energy shift͑Fig.3͒with the variation offilm thickness.The distance between two peaks does not change for different films.These two peaks correspond to the binding energy of Zr–O in ZrO2structure.There is no sign of Zr–Si bonds ͑e.g.,from ZrSi2͒appearing in the XPS spectra.13As to the variation of peak shapes for different samples,it can be at-tributed to the contribution of Si–O–Zr bonds when the de-positedfilm is very thin,which has been discussed above.From experimental and simulation studies on the laser-generated plume,26it is known that at an ambient gas pres-sure of10Ϫ6mbar,the species in the plume could reach akinetic energy as high as103eV.When Zr ions with kineticenergy of102–103eV impinge on the Si substrate surface,Zr ions may easily travel through a few monolayers of SiO2and cause collision-induced bond breaking or vibration,which consequently induce the chemical reactions describedabove.The ambient oxygen pressure and substrate tempera-ture in our experiment are controlled in critical regions suchthat the formation of zirconium silicide(ZrSi2)is suppressedbut allows the SiO,an intermediate product of the reaction,to be easily evaporated from substrate surface.Thus theamorphous oxide layer on the substrate is removed immedi-ately when Zr ions impinge on the substrate and a commen-surate interface between ZrO2and Si is formed.The experi-mental results discussed above are the direct evidence thatthe dynamic processes are de-oxidization processes fromSiO2to SiO x(xϽ2),the desorption of SiO,and the forma-tion of crystalline ZrO2.In summary,we present clear evidence on the growthmechanism of commensurately crystalline YSZ on nativelyoxidized Si wafer.The dynamic processes at the initial stageappear to be the decomposition of SiO2to SiO,the formationof ZrO2,and the desorption of SiO.The native SiO2is re-moved immediately when Zr atoms impinge upon the sub-strate surface,while the SiO2layer can be an oxygen sourceto form initial monolayers of ZrO2.As a result of the excel-lent structural properties,the crystalline YSZ on Si show much low leakage current.9The description of the dynamic growth mechanism of crystalline YSZ can be applied to fab-ricate other dielectricfilms on silicon or SiGe substrate by other techniques,such as sputtering.The project is supported by the National University of Singapore.The authors would like to thank S.Y.Xu,J.Y. Lin,and C.H.Sow for valuable discussions.The authors also would like to acknowledge W.C.Tjiu and J.W.Chai for HRTEM and XPS analysis in IMRE.1D.A.Buchanan,IBM J.Res.Dev.43,245͑1999͒.2D.A.Muller,T.Sorsch,S.Moccio,F.H.Baumann,K.Evans-Lutterodt, and G.Timp,Nature͑London͒399,758͑1999͒.3G.D.Wilk,R.M.Wallace,and J.M.Anthony,J.Appl.Phys.89,5243͑2001͒.4A.I.Kingon,J.P.Maria,and S.K.Streiffer,Nature͑London͒406,1032͑2000͒.5R.A.McKee,F.J.Walker,and M.F.Chisholm,Science293,468͑2001͒. 6R.A.McKee,F.J.Walker,and M.F.Chisholm,Phys.Rev.Lett.81,3014͑1998͒.7K.Eisenbeiser,J.M.Finder,Z.Yu,J.Ramdani,J.A.Curless,J.A.Hall-mark,R.Droopad,W.J.Ooms,L.Salem,S.Bradshaw,and C.D.Over-gaard,Appl.Phys.Lett.76,1324͑2000͒.8S.A.Chambers,Y.Liang,Z.Yu,R.Droopad,J.Ramdani,and K.Eisen-beiser,Appl.Phys.Lett.77,1662͑2000͒.9S.J.Wang,C.K.Ong,S.Y.Xu,P.Chen,W.C.Tjiu,J.W.Chai,A.C.H. Huan,W.J.Yoo,J.S.Lim,W.Feng,and W.K.Choi,Appl.Phys.Lett.78, 1604͑2001͒.10J.Robertson,J.Vac.Sci.Technol.B18,1785͑2000͒.11K.J.Hubbard and D.G.Schlom,J.Mater.Res.11,2757͑1996͒.12G.D.Wilk,R.M.Wallace,and J.M.Anthony,J.Appl.Phys.87,484͑2000͒.13T.S.Jeon,J.M.White,and D.L.Kwong,Appl.Phys.Lett.78,368͑2001͒.14M.Copel,M.Gribelyuk,and F.Gusev,Appl.Phys.Lett.76,436͑2000͒. 15J.-P.Maria,D.Wicaksana,A.I.Kingon,B.Busch,H.Schulte,E.Gar-funkel,and T.Gustafsson,J.Appl.Phys.90,3476͑2001͒.16W.J.Qi,R.Nieh,B.H.Lee,L.Kang,Y.Jeon,K.Onishi,T.Ngai,S. Banerjee,and J.C.Lee,Tech.Dig.-Int.Electron Devices Meet.,145͑1999͒.17P.Chen,S.Y.Xu,W.Z.Zhou,C.K.Ong,and D.F.Cui,J.Appl.Phys.85, 3000͑1999͒.18J.Seiple and J.P.Pelz,Phys.Rev.Lett.73,999͑1994͒.19F.M.Ross,J.M.Gibson,and R.D.Twesten,Surf.Sci.310,243͑1994͒. 20R.Tromp,G.W.Rubloff,P.Balk,and R.K.LeGoues,Phys.Rev.Lett.55, 2332͑1985͒.21J.J.Chambers and G.N.Parsons,Appl.Phys.Lett.77,2385͑2000͒.22G.Lucovsky,G.B.Rayner,Jr.,D.Kang,G.Appel,R.S.Johnson,Y. Zhang,D.E.Sayers,H.Ade,and J.L.Whitten,Appl.Phys.Lett.79,1775͑2001͒.23M.J.Guittet,J.P.Crocombette,and M.Gautier-Soyer,Phys.Rev.B63, 125117͑2001͒.24S.J.Wang,C.K.Ong,L.P.You,and S.Y.Xu,Semicond.Sci.Technol. 15,836͑2000͒.25Thermochemical Properties of Inorganic Substances,2nd ed.,edited by O. K.Nacke,O.Kubaschewski,and K.Hesselmann͑Springer,Berlin,1991͒. 26Pulsed Laser Deposition of Thin Films,edited by D.B.Chrisey and G.K. Hubler͑Wiley,New York,1994͒.Downloaded 23 Nov 2002 to 137.132.3.12. Redistribution subject to AIP license or copyright, see /aplo/aplcr.jsp。