HDI制作工艺设计
HDI板工艺流程介绍

HDI板工艺流程介绍HDI板(High Density Interconnect board)是一种采用先进工艺制造的高密度互连电路板,具有更高的线路密度和更小的尺寸,可实现更复杂的电路设计和更高性能的电子产品。
HDI板工艺流程是指制造HDI板所需的一系列工艺步骤,下面将详细介绍HDI板工艺流程。
一、图纸设计与合规性审核HDI板制造的第一步是进行电路板的设计和图纸的制作。
设计师根据电路需求绘制电路图,然后将电路图转换为电路板的布局图,确定线路位置、尺寸和层级等。
设计师还需要对设计的电路板进行合规性审核,确保电路板满足相关的标准和规范要求。
二、材料准备与剥离在HDI板制造过程中,需要准备一系列的基板材料、介质材料和覆铜膜等。
首先,需要将基板材料剥离到所需的厚度,以便后续的加工和处理。
三、内层制作内层制作是HDI板工艺流程中的关键步骤之一、首先,需要在基板上涂覆一层铜薄膜,然后使用光刻技术将需要连接的电路图案绘制在铜薄膜上。
接下来,使用化学腐蚀技术将不需要的铜薄膜腐蚀掉,留下所需的电路线路。
四、填铜与压制填铜是为了加强电路板的机械强度和导电性能。
在填铜工艺中,首先在内层制作后的电路板表面涂覆薄膜覆铜剂,然后通过化学镀铜或电镀技术将铜层填充到所需的厚度。
填铜后,将多张内层电路板堆叠在一起,并使用高温和高压进行压制,以形成电路板的整体结构。
五、表面处理与图案化在HDI板制造的过程中,还需要对电路板进行表面处理和图案化。
表面处理主要是为了改善电路板的防腐蚀性能和易焊性。
常见的表面处理方法包括镀金、镀锡、化学镍金等。
图案化则是将电路板上的电路连接图案和器件安装图案绘制在电路板的外层。
通过光刻技术和蚀刻技术,将所需的线路和器件图案形成。
六、板间铜化与形成多层结构板间铜化是将多层电路板连接起来的关键步骤。
在板间铜化过程中,需要在电路板表面涂覆薄膜覆铜剂,然后通过电镀技术将铜层填充到所需的厚度。
多层电路板经过板间铜化后,形成一个整体的多层结构。
HDI板的一阶,二阶与制造工艺

HDI板的⼀阶,⼆阶与制造⼯艺HDI板的⼀阶,⼆阶与制造⼯艺⼀,什么是HDI?HDI:high Density interconnection的简称,⾼密度互连,⾮机械钻孔,微盲孔孔环在6mil以下,内外层层间布线线宽/线隙在4mil以下,焊盘直径不⼤于0.35mm的多层板制作⽅式称之为HDI板。
盲孔:Blind via的简称,实现内层与外层之间的连接导通埋孔:Buried via的简称,实现内层与内层之间的连接导通盲孔⼤都是直径为0.05mm~0.15mm的⼩孔,埋盲孔成孔⽅式有激光成孔,等离⼦蚀孔和光致成孔,通常采⽤激光成孔,⽽激光成孔⼜分为CO2和YAG紫外激光机(UV)。
⼆.HDI板板料1.HDI板板料有RCC,LDPE,FR4RCC:Resin coated copper的简称,涂树脂铜箔。
RCC是由表⾯经粗化、耐热、防氧化等处理的铜箔和树脂组成的,其结构如下图所⽰:(厚度>4mil时使⽤)RCC的树脂层,具备与FR⼀4粘结⽚(Prepreg)相同的⼯艺性。
此外还要满⾜积层法多层板的有关性能要求,如:(1)⾼绝缘可靠性和微导通孔可靠性;(2)⾼玻璃化转变温度(Tg);(3)低介电常数和低吸⽔率;(4)对铜箔有较⾼的粘和强度;(5)固化后绝缘层厚度均匀同时,因为RCC是⼀种⽆玻璃纤维的新型产品,有利于激光、等离⼦体的蚀孔处理,有利于多层板的轻量化和薄型化。
另外,涂树脂铜箔具有12pm,18pm等薄铜箔,容易加⼯。
三,什么是⼀阶,⼆阶PCB?这个⼀阶,⼆阶就是指打激光孔的次数,PCB芯板压合⼏次,打⼏次激光孔!就是⼏阶。
如下所⽰1,.压合⼀次后钻孔==》外⾯再压⼀次铜箔==》再镭射钻孔这是⼀阶,如下图所⽰2,压合⼀次后钻孔==》外⾯再压⼀次铜箔==》再镭射,钻孔==》外层再压⼀次铜箔==》再镭射钻孔这是⼆阶。
主要就是看你镭射的次数是⼏次,就是⼏阶了。
⼆阶就分叠孔与分叉孔两种。
如下图是⼋层⼆阶叠孔,是3-6层先压合好,外⾯2,7两层压上去,打⼀次镭射孔。
hdi工艺技术
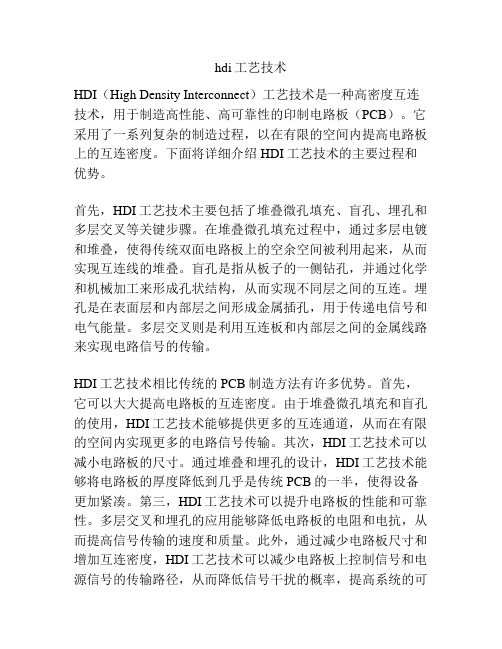
hdi工艺技术HDI(High Density Interconnect)工艺技术是一种高密度互连技术,用于制造高性能、高可靠性的印制电路板(PCB)。
它采用了一系列复杂的制造过程,以在有限的空间内提高电路板上的互连密度。
下面将详细介绍HDI工艺技术的主要过程和优势。
首先,HDI工艺技术主要包括了堆叠微孔填充、盲孔、埋孔和多层交叉等关键步骤。
在堆叠微孔填充过程中,通过多层电镀和堆叠,使得传统双面电路板上的空余空间被利用起来,从而实现互连线的堆叠。
盲孔是指从板子的一侧钻孔,并通过化学和机械加工来形成孔状结构,从而实现不同层之间的互连。
埋孔是在表面层和内部层之间形成金属插孔,用于传递电信号和电气能量。
多层交叉则是利用互连板和内部层之间的金属线路来实现电路信号的传输。
HDI工艺技术相比传统的PCB制造方法有许多优势。
首先,它可以大大提高电路板的互连密度。
由于堆叠微孔填充和盲孔的使用,HDI工艺技术能够提供更多的互连通道,从而在有限的空间内实现更多的电路信号传输。
其次,HDI工艺技术可以减小电路板的尺寸。
通过堆叠和埋孔的设计,HDI工艺技术能够将电路板的厚度降低到几乎是传统PCB的一半,使得设备更加紧凑。
第三,HDI工艺技术可以提升电路板的性能和可靠性。
多层交叉和埋孔的应用能够降低电路板的电阻和电抗,从而提高信号传输的速度和质量。
此外,通过减少电路板尺寸和增加互连密度,HDI工艺技术可以减少电路板上控制信号和电源信号的传输路径,从而降低信号干扰的概率,提高系统的可靠性。
总的来说,HDI工艺技术是一种先进的PCB制造技术,能够实现更高的互连密度、更小尺寸的电路板以及更高性能和可靠性的电路设计。
随着电子产品的发展和需求的不断增加,HDI 工艺技术也将得到广泛的应用。
在未来,我们可以预见,HDI 工艺技术将继续发展,为电子设备带来更多的创新和突破。
盲埋孔(HDI)板制作能力及设计规范
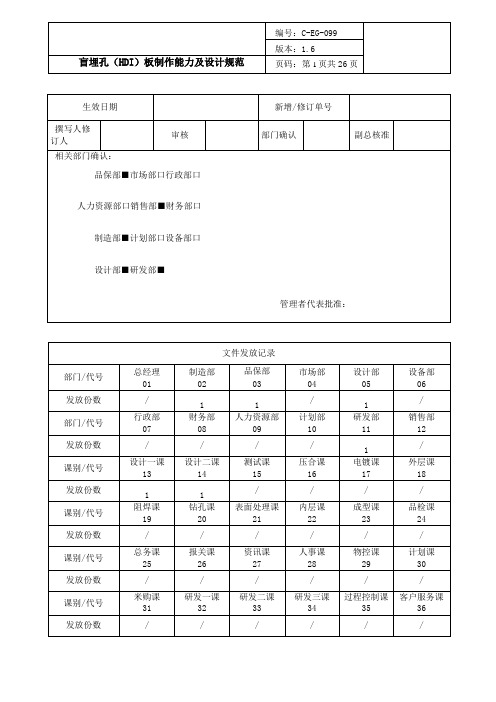
目录制订我司盲埋孔(HDI)板的流程及设计规范。
2.0范围:适用于我司“3+N+3”以内的盲埋孔(HDI)板的制作。
3.0职责:研发部:更新制作能力,制定并不断完善设计规范,解决该规范执行过程中出现的问题。
设计部:按照工艺要求设计并制作相关工具,及时反馈执行过程中出现的问题;负责对工程设计及内层菲林进行监控,及时提出相关意见或建议。
品保部:发行并保存最新版文件。
市场部:根据此文件的能力水平接订单,及向客户展示本公司的制作能力;收集客户的需求,及时向研发部反馈市场需求信息。
4.0指引内容:4.1盲埋孔“阶数”的定义:表示其激光盲孔的堆迭次数(通常用“1+N+1”、“2+N+2”、“3+N+3”等表示)、或某一层次的最多压合次数、或前工序(含:内层一压合一钻孔)循环次数,数值最大的项目则为其阶数。
4.2盲埋孔“次数”的定义:表示一款盲埋孔(HDI)板的压合结构图中所包含的机械钻盲埋孔次数和激光钻盲埋孔次数的总和(如同一次压合后的两面均需激光钻孔,则按盲埋两次计。
但计算钻孔价钱时只按一次激光钻孔的总孔数或一次钻孔的最低消费计)。
4.3盲埋孔“阶数”和盲埋孔“次数”的示例:4.3.1纯激光钻孔的双向增层式叠孔盲埋孔(HDI)板结构图示例盲埋孔阶数1盲埋孔阶数2盲埋孔阶数3阶数表示法1+2+1阶数表示法2+2+2阶数表示法3+2+3盲埋孔次数2盲埋孔次数4盲埋孔次数6编号:C-EG-099版本:1.6盲埋孔(HDI )板制作能力及设计规范页码:第5页共26页4.3.3 简单混合型的双向增层式盲埋孔(HDI )板结构图示例(激光盲孔为错位孔)盲埋孔阶数 1 盲埋孔阶数 2 盲埋孔阶数3 阶数表示法1+2+1 阶数表示法 2+2+2 阶数表示法3+2+3 盲埋孔次数 3 盲埋孔次数 5 盲埋孔次数 7盲埋孔阶数1盲埋孔阶数2盲埋孔阶数 3盲埋孔阶数1 阶数表示法1+2+1盲埋孔次数3盲埋孔阶数2 阶数表示法2+2+2 盲埋孔次数5盲埋孔阶数3 阶数表示法3+2+3 盲埋孔次数74.3.2简单混合型的双向增层式盲埋孔(HDI )板结构图示例(激光盲孔为叠孔)4.3.4复杂混合型的双向增层式盲埋孔(HDI )板结构图示例(激光盲孔同时有叠孔和错位孔)阶数表示法1+2+1阶数表示法2+2+2阶数表示法3+2+3盲埋孔次数3盲埋孔次数5盲埋孔次数7盲埋孔阶数1 盲埋孔次数2 盲埋孔阶数2 盲埋孔次数4编号:C-EG-099 版本:1.6盲埋孔(HDI )板制作能力及设计规范页码:第6页共26页4.3.6 纯机械钻孔的双核双向增层式盲埋孔阶数结构图示例(含假层设计)4.3.7 纯机械钻孔的双核单向增层式盲埋孔阶数结构图示例盲埋孔阶数3 盲埋孔次数5盲埋孔次数1 盲埋孔次数2 盲埋孔次数3 rWFTTTTI盲埋孔阶数2 盲埋孔阶数2 盲埋孔次数3盲埋孔次数5盲埋孔次数6盲埋孔阶数14.3.5纯机械钻孔的盲埋孔次数结构图示例盲埋孔阶数1 盲埋孔阶数1 盲埋孔阶数3盲埋孔阶数1盲埋孔次数3 盲埋孔阶数2 盲埋孔次数6编号:C-EG-099 版本:1.6盲埋孔(HDI )板制作能力及设计规范页码:第7页共26页4.3.8 纯机械钻孔的双核单向增层式盲埋孔阶数结构图示例独立芯板和多次压合盲孔层混合压合时, 该独立芯板的涨缩值与盲孔层的涨缩值相 差较大,独立芯板越薄,差值越大盲埋孔次数64.3.9 复杂混合型的双向增层式盲埋孔板结构图示例14.3.10 复杂混合型的双向增层式盲埋孔板结构图示例2盲埋孔阶数3 盲埋孔次数9PPPP盲埋孔阶数 1 盲埋孔阶数2阶数表示法 1+2+1 阶数表示法 2+2+2 盲埋孔次数 3 盲埋孔次数 6盲埋孔阶数3 阶数表示法3+2+3 盲埋孔次数9盲埋孔阶数34.4备注:1)上表中的难度系数为基于相同层次相同材料无任何盲埋孔时的普通板的难度提升值2)盲埋孔板的制作难度系数=盲孔阶数难度系数+盲孔次数难度系数3)如同时存在激光钻盲孔和机械钻盲孔,其制作难度系数=激光钻盲孔+机械钻盲孔4)如树脂塞孔的通孔需做成“Via-in-PAD”设计,需单独再增加15%的难度系数5)如存在小于0.10mm的薄芯板电镀,每张芯板分别需单独再增加5%的难度系数2)表格中打“*”的,表示是可选择的步骤,或者当前面的副流程执行该步骤时、则后面相关某步骤可不执行。
HDI板制造工艺概述

HDI板制造工艺概述HDI(High-Density Interconnect)板,即高密度互连板,是一种在一张薄板上通过微细线路、孔和盖层连接多个半导体芯片及其他组件的印刷电路板(PCB)。
HDI板制造工艺是一项高级技术,旨在提高电路板的集成度和性能。
本文将对HDI板制造工艺进行概述。
1.设计:HDI板的设计是在硬件设计工程师的指导下完成的。
设计工程师需要根据电路设计要求和性能目标来确定电路板的层数、线宽线距、孔径和钻孔布局等参数。
2.材料准备:制造HDI板需要一系列特定的材料,包括基板材料、导电层、电镀材料和盖层等。
这些材料需要经过精细的加工和处理,以保证其质量和性能。
3.线路制作:线路制作是HDI板制造工艺中的核心步骤之一、它通常包括以下几个主要的步骤:-在基板上涂覆光刻胶,并通过光刻技术将设计好的线路图案转移到光刻胶上。
-使用酸浸蚀或电化学蚀刻的方法将未被光刻胶保护的金属层部分去除,形成线路。
-使用电镀技术将线路上镀上一层金属,以增加导电性能和保护线路。
4.钻孔:钻孔是制造HDI板的另一个重要步骤。
钻孔技术主要包括机械钻孔和激光钻孔两种。
钻孔的主要目的是提供电气连接和通孔间的互连。
5.电镀:电镀是为了保护线路和提高连接性能。
经过钻孔之后,将表面裸露出来的金属线路进行镀铜处理,以增加导电性能。
6.盖层制作:盖层是HDI板的另一个重要组成部分,用于加强电路板的机械强度和稳定性。
盖层通常由聚酰亚胺材料制成,通过热压或化学结合等工艺与板内进行层间粘结。
7.组装和测试:通过焊接和连接等工艺,将芯片、连接器和其他元器件安装到HDI板上。
安装完成后,还需要进行电气和功能测试,以确保产品的质量和性能。
综上所述,HDI板制造工艺是一项复杂而精细的技术,在高密度互连领域具有广泛的应用。
通过精确的设计、材料选择和工艺控制,可以实现电路板的高集成度、高性能和高可靠性。
随着电子产品对小型化、高端化和多功能化的要求不断增加,HDI板制造工艺将会发展出更多的创新和应用。
PCB工艺流程之常见HDI线路板工艺流程
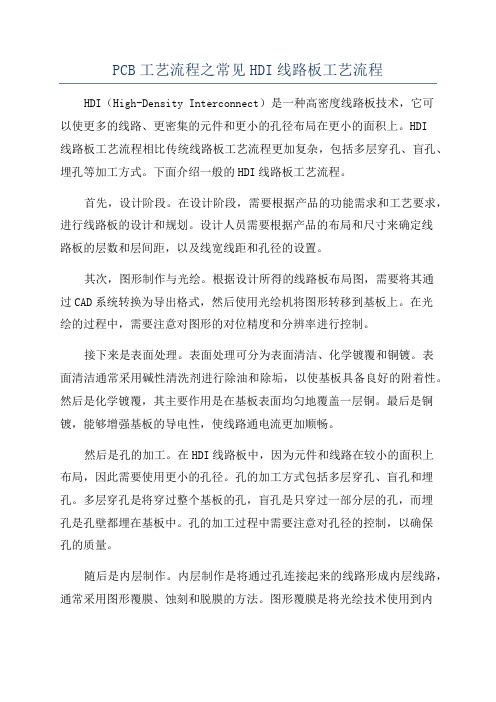
PCB工艺流程之常见HDI线路板工艺流程HDI(High-Density Interconnect)是一种高密度线路板技术,它可以使更多的线路、更密集的元件和更小的孔径布局在更小的面积上。
HDI线路板工艺流程相比传统线路板工艺流程更加复杂,包括多层穿孔、盲孔、埋孔等加工方式。
下面介绍一般的HDI线路板工艺流程。
首先,设计阶段。
在设计阶段,需要根据产品的功能需求和工艺要求,进行线路板的设计和规划。
设计人员需要根据产品的布局和尺寸来确定线路板的层数和层间距,以及线宽线距和孔径的设置。
其次,图形制作与光绘。
根据设计所得的线路板布局图,需要将其通过CAD系统转换为导出格式,然后使用光绘机将图形转移到基板上。
在光绘的过程中,需要注意对图形的对位精度和分辨率进行控制。
接下来是表面处理。
表面处理可分为表面清洁、化学镀覆和铜镀。
表面清洁通常采用碱性清洗剂进行除油和除垢,以使基板具备良好的附着性。
然后是化学镀覆,其主要作用是在基板表面均匀地覆盖一层铜。
最后是铜镀,能够增强基板的导电性,使线路通电流更加顺畅。
然后是孔的加工。
在HDI线路板中,因为元件和线路在较小的面积上布局,因此需要使用更小的孔径。
孔的加工方式包括多层穿孔、盲孔和埋孔。
多层穿孔是将穿过整个基板的孔,盲孔是只穿过一部分层的孔,而埋孔是孔壁都埋在基板中。
孔的加工过程中需要注意对孔径的控制,以确保孔的质量。
随后是内层制作。
内层制作是将通过孔连接起来的线路形成内层线路,通常采用图形覆膜、蚀刻和脱膜的方法。
图形覆膜是将光绘技术使用到内层制作中,蚀刻是通过化学腐蚀将不需要的铜层去除,而脱膜则是将覆盖在铜层上的光敏胶去除。
接下来是外层制作。
外层制作是将内层线路与外层线路连接起来,通常采用图形绘制、蚀刻和阻焊等步骤。
图形绘制将外层图形通过光刻技术转移到基板上,蚀刻将不需要的铜层去除,而阻焊则是在线路板上涂覆一层保护层,以保护线路并增强其对焊接的粘附性。
最后是封装和测试。
2024版HDIPCB板制造工艺详解挑战与解决方案
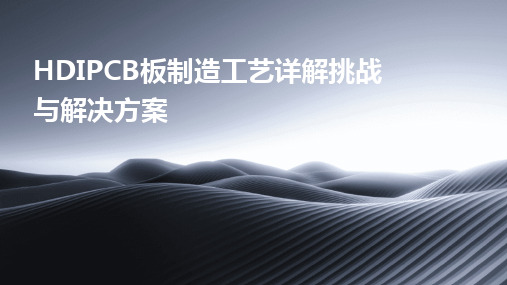
•引言•HDIPCB板制造工艺概述•制造过程中的挑战•解决方案与技术进步目录•设备与工艺协同优化•质量控制与检测手段完善•总结与展望01引言目的和背景汇报范围0102030402HDIPCB板制造工艺概述图形转移原材料准备蚀刻丝印与表面处理阻焊层制作传统PCB 制造工艺HDIPCB制造工艺特点采用微细线路和微小孔径设计,实现更高布线密度。
通过优化材料和工艺,提高产品可靠性和稳定性。
采用自动化生产线和先进设备,提高生产效率和降低成本。
采用环保材料和工艺,减少对环境的影响。
高密度高可靠性高效率环保性内层制作层压钻孔030201孔金属化外层制作阻焊层制作工艺流程及关键步骤丝印与表面处理测试与检验03制造过程中的挑战1 2 3基材选择铜箔要求粘结片材料选择及性能要求精细线路制作难度线宽/线距控制导通孔制作导通孔的尺寸和位置精度对信号传输质量和多层板可靠性至关重要,制作过程中需严格控制钻孔参数和镀铜工艺。
高密度互连技术挑战盲孔与埋孔技术多层板压合技术可靠性问题热稳定性耐湿性抗机械应力04解决方案与技术进步新型材料应用及性能提升高性能基材新型导体材料高性能覆铜板精细线路制作技术优化高精度光刻技术01激光直接成像技术02微电子加工技术03高密度互连技术创新盲埋孔技术微通孔技术高频高速传输技术可靠性增强措施表面处理技术01热设计优化02环境适应性提升0305设备与工艺协同优化设备升级改造方向高精度、高效率提升设备加工精度和生产效率,满足HDIPCB板高精度、高效率的制造需求。
智能化、自动化引入先进的控制系统和自动化技术,提高设备智能化水平,降低人工干预程度。
环保、节能采用环保材料和节能技术,降低设备能耗和废弃物排放,提高生产过程的环保性。
工艺流程优化策略精简工艺流程优化工艺参数引入新工艺技术设备与工艺协同作用设备升级推动工艺进步工艺优化提升设备效能设备与工艺相互促进06质量控制与检测手段完善质量控制关键环节识别原材料质量控制加工过程控制成品检验自动化检测设备应用引入先进的自动化检测设备,如AOI(自动光学检测)、AXI(自动X射线检测)等,提高检测效率和准确性。
hdi生产工艺
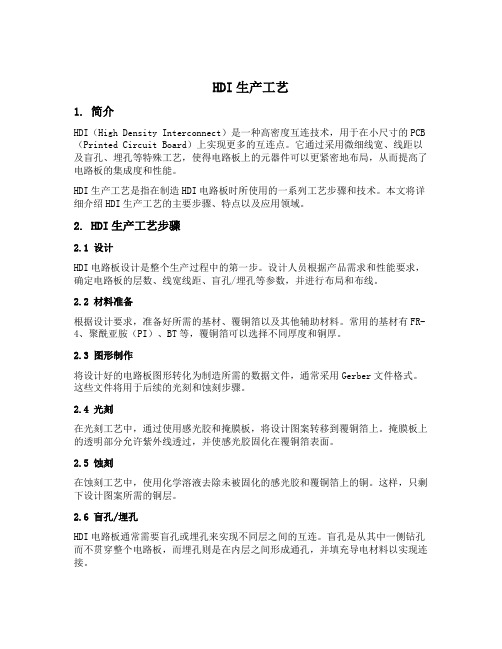
HDI生产工艺1. 简介HDI(High Density Interconnect)是一种高密度互连技术,用于在小尺寸的PCB (Printed Circuit Board)上实现更多的互连点。
它通过采用微细线宽、线距以及盲孔、埋孔等特殊工艺,使得电路板上的元器件可以更紧密地布局,从而提高了电路板的集成度和性能。
HDI生产工艺是指在制造HDI电路板时所使用的一系列工艺步骤和技术。
本文将详细介绍HDI生产工艺的主要步骤、特点以及应用领域。
2. HDI生产工艺步骤2.1 设计HDI电路板设计是整个生产过程中的第一步。
设计人员根据产品需求和性能要求,确定电路板的层数、线宽线距、盲孔/埋孔等参数,并进行布局和布线。
2.2 材料准备根据设计要求,准备好所需的基材、覆铜箔以及其他辅助材料。
常用的基材有FR-4、聚酰亚胺(PI)、BT等,覆铜箔可以选择不同厚度和铜厚。
2.3 图形制作将设计好的电路板图形转化为制造所需的数据文件,通常采用Gerber文件格式。
这些文件将用于后续的光刻和蚀刻步骤。
2.4 光刻在光刻工艺中,通过使用感光胶和掩膜板,将设计图案转移到覆铜箔上。
掩膜板上的透明部分允许紫外线透过,并使感光胶固化在覆铜箔表面。
2.5 蚀刻在蚀刻工艺中,使用化学溶液去除未被固化的感光胶和覆铜箔上的铜。
这样,只剩下设计图案所需的铜层。
2.6 盲孔/埋孔HDI电路板通常需要盲孔或埋孔来实现不同层之间的互连。
盲孔是从其中一侧钻孔而不贯穿整个电路板,而埋孔则是在内层之间形成通孔,并填充导电材料以实现连接。
2.7 堆叠与压合通过堆叠多个经过处理的内外层,使得整个HDI电路板具有更高的集成度和互连能力。
堆叠后的电路板需要经过压合工艺,以确保各层之间的粘合度。
2.8 表面处理为了提高电路板的焊接性能和耐腐蚀性,常常需要对表面进行处理。
常见的表面处理方法有镀金、喷锡、喷镍等。
2.9 最终检测与包装在完成上述工艺步骤后,对HDI电路板进行最终检测,确保其符合设计要求和性能指标。
HDI印刷线路板流程介绍
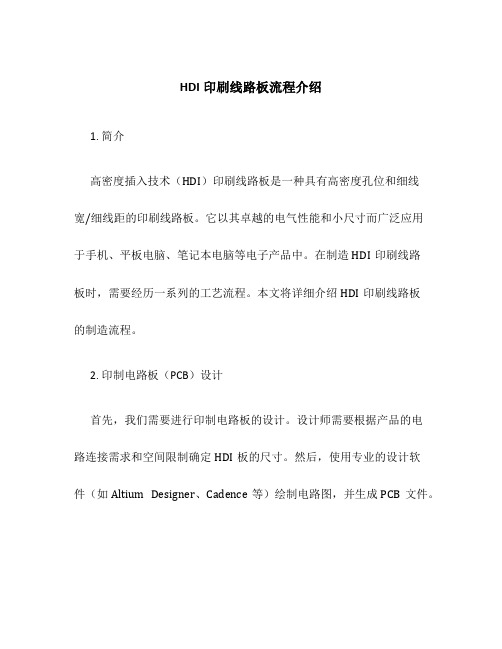
HDI印刷线路板流程介绍1. 简介高密度插入技术(HDI)印刷线路板是一种具有高密度孔位和细线宽/细线距的印刷线路板。
它以其卓越的电气性能和小尺寸而广泛应用于手机、平板电脑、笔记本电脑等电子产品中。
在制造HDI印刷线路板时,需要经历一系列的工艺流程。
本文将详细介绍HDI印刷线路板的制造流程。
2. 印制电路板(PCB)设计首先,我们需要进行印制电路板的设计。
设计师需要根据产品的电路连接需求和空间限制确定HDI板的尺寸。
然后,使用专业的设计软件(如Altium Designer、Cadence等)绘制电路图,并生成PCB文件。
3. 板材选择选择合适的基板材料对于制造HDI印刷线路板至关重要。
常用的基板材料包括FR-4、Rogers和PTEE等。
在选择时,需要考虑板材的介电常数、热膨胀系数、耐高温性能等因素。
4. 镀铜在HDI印刷线路板制造过程中,电路板通常会先进行表面镀铜。
表面镀铜的目的是增加线路板的导电性,方便后续的线路连接。
镀铜过程包括清洗板材、化学镀铜和电解镀铜等步骤。
5. 图形图像化在完成表面镀铜后,需要对线路板进行图形图像化处理。
该过程采用光刻技术,通过光阻层的引入,将PCB文件中的图形转移到线路板上。
6. 钻孔接下来,需要对HDI印刷线路板进行钻孔。
这些钻孔将用作电路的连接点和固定螺纹。
钻孔过程分为机械钻孔和激光钻孔两种方法,激光钻孔一般用于小孔位的处理。
7. 高压喷嘴高压喷嘴是为了清除镀铜过程中产生的废液和杂质。
通过高压水流的冲刷,可以有效地清洗线路板表面,使其光滑而干净。
8. 厚铜板在HDI印刷线路板制造过程中,有几个关键位置需要使用厚铜板来增加导电性和强度。
厚铜板一般通过电解沉积的方法添加到线路板的特定区域。
9. 确定化学镀铜在某些情况下,为了进一步提高线路板的导电性能,还需要进行化学镀铜处理。
化学镀铜可以填充和加强线路板中的细微孔隙。
10. 硬化为了增强线路板的耐用性和稳定性,需要对其进行硬化处理。
hdi合成工艺
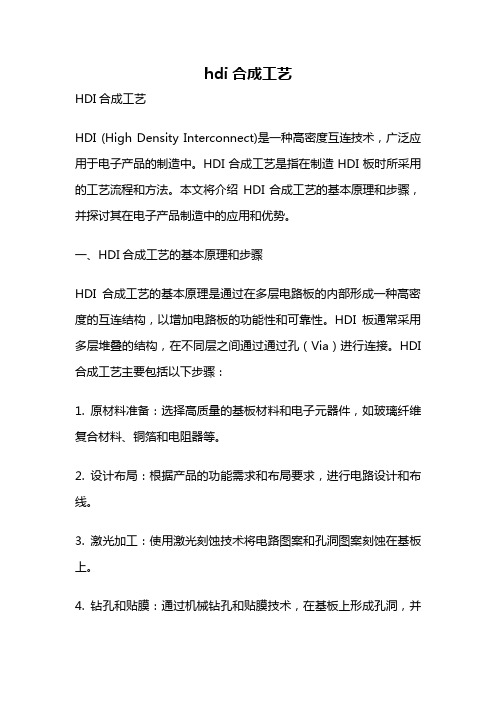
hdi合成工艺HDI合成工艺HDI (High Density Interconnect)是一种高密度互连技术,广泛应用于电子产品的制造中。
HDI合成工艺是指在制造HDI板时所采用的工艺流程和方法。
本文将介绍HDI合成工艺的基本原理和步骤,并探讨其在电子产品制造中的应用和优势。
一、HDI合成工艺的基本原理和步骤HDI合成工艺的基本原理是通过在多层电路板的内部形成一种高密度的互连结构,以增加电路板的功能性和可靠性。
HDI板通常采用多层堆叠的结构,在不同层之间通过通过孔(Via)进行连接。
HDI 合成工艺主要包括以下步骤:1. 原材料准备:选择高质量的基板材料和电子元器件,如玻璃纤维复合材料、铜箔和电阻器等。
2. 设计布局:根据产品的功能需求和布局要求,进行电路设计和布线。
3. 激光加工:使用激光刻蚀技术将电路图案和孔洞图案刻蚀在基板上。
4. 钻孔和贴膜:通过机械钻孔和贴膜技术,在基板上形成孔洞,并在孔洞内部镀上一层导电膜。
5. 堆叠层压:将多个经过处理的基板层叠在一起,并使用压力和热量将其压合。
6. 内部连接:在堆叠的基板层之间形成互连通道,通过导电膜和孔洞进行电路连接。
7. 外层制造:在堆叠结构的外部形成表面电路图案,并进行金属化处理。
8. 最终加工:进行最终的修整和测试,确保HDI板的功能和可靠性。
二、HDI合成工艺在电子产品制造中的应用和优势HDI合成工艺在电子产品制造中具有广泛的应用和重要的优势。
1. 提高了电路板的功能性:HDI合成工艺可以大大增加电路板的功能性和集成度。
通过在多层电路板内部形成高密度的互连结构,可以实现更复杂的电路设计和布线,满足各种功能需求。
2. 提高了电路板的可靠性:HDI合成工艺可以提高电路板的可靠性和稳定性。
通过采用高质量的材料和精密的制造工艺,可以减少电路板的故障率和失效率,提高产品的寿命和性能。
3. 减小了电路板的尺寸和重量:HDI合成工艺可以显著减小电路板的尺寸和重量。
hdi工艺流程
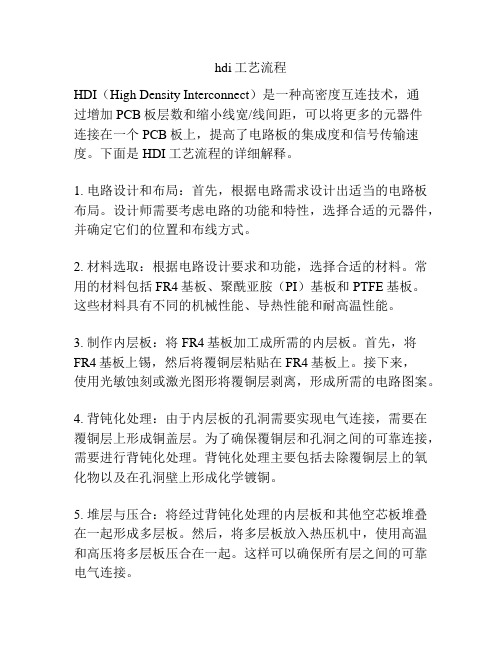
hdi工艺流程HDI(High Density Interconnect)是一种高密度互连技术,通过增加PCB板层数和缩小线宽/线间距,可以将更多的元器件连接在一个PCB板上,提高了电路板的集成度和信号传输速度。
下面是HDI工艺流程的详细解释。
1. 电路设计和布局:首先,根据电路需求设计出适当的电路板布局。
设计师需要考虑电路的功能和特性,选择合适的元器件,并确定它们的位置和布线方式。
2. 材料选取:根据电路设计要求和功能,选择合适的材料。
常用的材料包括FR4基板、聚酰亚胺(PI)基板和PTFE基板。
这些材料具有不同的机械性能、导热性能和耐高温性能。
3. 制作内层板:将FR4基板加工成所需的内层板。
首先,将FR4基板上锡,然后将覆铜层粘贴在FR4基板上。
接下来,使用光敏蚀刻或激光图形将覆铜层剥离,形成所需的电路图案。
4. 背钝化处理:由于内层板的孔洞需要实现电气连接,需要在覆铜层上形成铜盖层。
为了确保覆铜层和孔洞之间的可靠连接,需要进行背钝化处理。
背钝化处理主要包括去除覆铜层上的氧化物以及在孔洞壁上形成化学镀铜。
5. 堆层与压合:将经过背钝化处理的内层板和其他空芯板堆叠在一起形成多层板。
然后,将多层板放入热压机中,使用高温和高压将多层板压合在一起。
这样可以确保所有层之间的可靠电气连接。
6. 机械钻孔和内层成型:使用机械钻孔设备在多层板上钻孔。
钻孔用于形成电气连接和组件安装孔。
然后,使用钻孔尺寸逐层镗孔,使其成为具有特定形状的方孔。
7. 通过盲孔和埋孔:在多层板上形成盲孔和埋孔是HDI技术的关键步骤。
盲孔是从外部图层到内层图层的孔洞,而埋孔是在内部图层之间形成的孔洞。
8. 镀铜和电镀:通过镀铜和电镀等表面处理,形成电路板的导电层。
例如,可以使用电化学方法在覆铜层上镀上一层铜。
然后,再使用金属化学反应将铜沉积在所需的微型线路上。
9. 外层图案制作:使用光敏蚀刻或激光图形在外层板上形成所需的电路图案。
然后,使用外层镀铜和电镀来加固和保护外层图案。
hdi生产工艺

hdi生产工艺HDI生产工艺简介•HDI(High Density Interconnect)即高密度互连技术,是一种新型的电路板制造工艺。
•HDI生产工艺在实现高密度互连的同时,提升了电路板的性能和可靠性。
工艺流程1.设计阶段–使用CAD软件进行电路板设计。
–确定板层结构和层次划分。
2.材料准备–选择高质量的基板材料,如FR-4、高Tg材料等。
–准备合适尺寸的耐热胶片、中间层和薄钼箔。
3.印制内层板–在基板上涂覆铜箔。
–利用光刻技术制作互连图形。
–酸蚀去除多余铜箔。
4.人工堆叠–根据设计要求,将印制好的内层板和其他材料按照设计顺序堆叠在一起。
5.压合–将堆叠好的板材进行高温高压的压合,使其紧密结合。
6.钻孔–利用激光钻孔机对板材进行钻孔,形成互连通孔。
7.化学镀铜–通过电化学反应,在互连通孔内形成导电铜层。
8.镭射光刻–利用镭射光刻机器绘制外层图形。
9.酸蚀与艾纳普电镀–酸蚀去除未被光刻保护的铜箔。
–进行电镀,增加铜箔导电性。
10.表面处理–在电路板的表面形成焊接和防腐蚀层。
–可选择镍/金、锡/铅等材料进行处理。
11.最终测试–对生产好的HDI电路板进行全面的功能和可靠性测试。
特点与应用•特点:–高密度互连:通过减小通孔间距和孔径,实现更高密度的互连。
–降低电磁干扰:采用层与层之间引线及盲通孔结构,减少信号互相干扰的可能性。
–小型化和轻量化:可在有限空间内实现更多功能,适用于小尺寸的电子设备。
–提升性能和可靠性:稳定的制造工艺和高品质材料,提高电路板的性能和可靠性。
•应用:–移动通信设备:如智能手机、平板电脑等。
–汽车电子系统:如车载导航、车载娱乐系统等。
–医疗器械:如医疗监测设备、移植仪器等。
HDI生产工艺的发展为电子产品的革新提供了关键支持,带来了更高的性能、更小的体积和更好的可靠性,将继续在电子制造行业发挥重要作用。
未来发展趋势随着科技的不断进步和需求的增长,HDI生产工艺也在不断发展和创新。
pcb行业hdi生产工艺

pcb行业hdi生产工艺HDI(High Density Interconnect)是PCB行业中一种生产工艺,其主要特点是相对于传统的PCB,具有更高的线路密度和更小的尺寸。
本文将介绍HDI生产工艺的主要步骤和特点。
HDI生产工艺主要包括以下几个步骤:设计,材料准备,制造和测试。
在设计阶段,设计师将根据产品要求绘制PCB线路图,并确定使用HDI工艺进行制造。
设计师还需要考虑电路板上各个组件的布局,以最大程度地提高线路密度,并减少电路板的尺寸。
此外,还需要考虑信号完整性和电磁兼容性等方面的需求。
在材料准备阶段,制造商将根据设计要求选择相应的材料。
HDI生产工艺通常使用厚膜、薄膜和微细孔填充材料。
这些材料具有良好的导电性能和粘附性能,能够满足高密度线路的需求。
此外,还需要准备其他必要的物料,如镀铜液、镀锡液等。
在制造阶段,制造商将使用一系列工艺步骤来制造HDI电路板。
首先,将预先铺好的基材放入数控铣床中进行切割,得到板材的形状和尺寸。
然后,通过激光钻孔或机械钻孔的方式在板材上进行孔的加工。
接下来,在表面上涂覆层厚膜材料,以增加线路的导电性能。
然后,在细孔中填充微细孔填充材料,以便后续的线路连接。
最后,在电路板表面涂覆薄膜材料作为保护层,并使用镀铜和镀锡工艺对电路板进行加工。
整个制造过程需要高度精密的机器和设备来确保产品的质量。
最后,通过测试阶段对制造好的HDI电路板进行测试。
测试人员将使用专用的测试设备来测试电路板的性能和功能。
测试过程包括电气测试、可靠性测试和外观检查等。
如果电路板通过测试,将继续进行下一步的组装工艺,如焊接电子元件等。
如果电路板未通过测试,则需要进行修复或重新制造。
HDI生产工艺具有以下几个特点:1. 高线路密度:HDI电路板的线路密度远高于传统的PCB。
这使得HDI电路板可以在更小的尺寸上容纳更多的电子组件,从而满足了如今电子产品对小型化和轻量化的需求。
2. 优异的电性能:HDI生产工艺中使用的材料具有良好的导电性能和粘附性能,可以有效地减少信号损失和干扰,提高信号完整性和电磁兼容性。
hdi的工艺技术
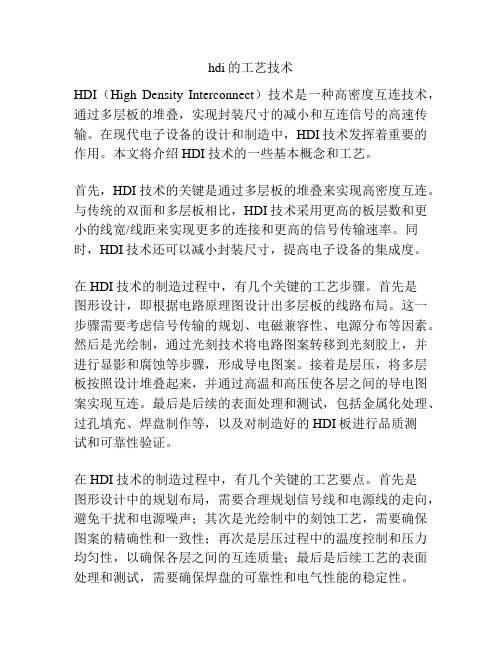
hdi的工艺技术HDI(High Density Interconnect)技术是一种高密度互连技术,通过多层板的堆叠,实现封装尺寸的减小和互连信号的高速传输。
在现代电子设备的设计和制造中,HDI技术发挥着重要的作用。
本文将介绍HDI技术的一些基本概念和工艺。
首先,HDI技术的关键是通过多层板的堆叠来实现高密度互连。
与传统的双面和多层板相比,HDI技术采用更高的板层数和更小的线宽/线距来实现更多的连接和更高的信号传输速率。
同时,HDI技术还可以减小封装尺寸,提高电子设备的集成度。
在HDI技术的制造过程中,有几个关键的工艺步骤。
首先是图形设计,即根据电路原理图设计出多层板的线路布局。
这一步骤需要考虑信号传输的规划、电磁兼容性、电源分布等因素。
然后是光绘制,通过光刻技术将电路图案转移到光刻胶上,并进行显影和腐蚀等步骤,形成导电图案。
接着是层压,将多层板按照设计堆叠起来,并通过高温和高压使各层之间的导电图案实现互连。
最后是后续的表面处理和测试,包括金属化处理、过孔填充、焊盘制作等,以及对制造好的HDI板进行品质测试和可靠性验证。
在HDI技术的制造过程中,有几个关键的工艺要点。
首先是图形设计中的规划布局,需要合理规划信号线和电源线的走向,避免干扰和电源噪声;其次是光绘制中的刻蚀工艺,需要确保图案的精确性和一致性;再次是层压过程中的温度控制和压力均匀性,以确保各层之间的互连质量;最后是后续工艺的表面处理和测试,需要确保焊盘的可靠性和电气性能的稳定性。
HDI技术的应用非常广泛,例如在智能手机、平板电脑和笔记本电脑等电子产品中。
HDI技术可以实现更小的封装尺寸,提高设备的集成度和可靠性。
同时,HDI技术还可以实现更高的信号传输速率,满足高速数据传输和通信需求。
在未来,随着电子设备的不断进步和智能化的发展,HDI技术将继续发挥着重要的作用。
综上所述,HDI技术是一种高密度互连技术,通过多层板的堆叠来实现高密度互连和信号传输。
hdi流程工艺技术

hdi流程工艺技术HDI(High Density Interconnect)是一种高密度互连技术,用于制造多层印制电路板(PCB)。
HDI流程工艺技术是为了满足现代电子产品对更小、更轻、更高性能的要求而发展起来的。
HDI流程工艺技术一般分为以下几个步骤:首先是基板制备。
基板通常由玻璃纤维与环氧树脂复合材料构成,制备基板的过程包括材料选择、切割、清洗、钻孔等工序。
在HDI技术中,通常需要进行微孔钻孔和盲孔钻孔,以满足高密度布线的要求。
然后是图形化处理。
通过光刻技术,将电路设计转移到基板上。
这个过程涉及到照相、曝光、显影等步骤,最终形成图案化的电路线路。
接下来是电镀和制作多层。
在电镀工艺过程中,将电路板浸入电解液中,利用电流使其表面镀上一层金属,以提高导电性。
制作多层是为了增加电路板的布线密度,通过将多个薄板层叠在一起并使用层间电镀技术,以实现电路的互连。
然后是图形化处理第二次。
在HDI流程工艺技术中,通常需要进行多次图形化处理,以满足高密度布线的要求。
这包括用光刻技术制作更细小的线路,并且需要更高的精度和分辨率。
最后是外层处理。
外层处理是为了保护电路线路,提供更好的焊接性能和电阻特性。
这包括覆盖清漆、锡镀等工艺,以提高电路板的可靠性和耐久性。
HDI流程工艺技术的优点在于它可以实现更高的布线密度、更低的信号损耗和更好的电热性能。
这使得HDI技术在现代电子产品中得到了广泛应用,如智能手机、平板电脑、笔记本电脑等。
然而,HDI流程工艺技术也存在一些挑战。
首先是生产成本较高,特别是在多层制作和精度要求较高的情况下。
其次,HDI 技术需要更为复杂的制造设备和技术,对制造商的要求较高。
总的来说,HDI流程工艺技术是一种提高电路板布线密度和性能的重要技术。
随着电子产品对更小、更轻、更高性能的需求不断增加,HDI技术将继续得到广泛应用和进一步发展。
hdi生产流程
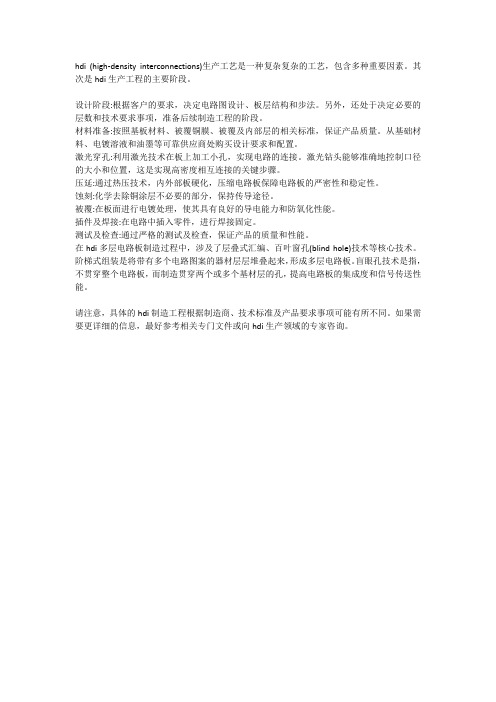
hdi (high-density interconnections)生产工艺是一种复杂复杂的工艺,包含多种重要因素。
其次是hdi生产工程的主要阶段。
设计阶段:根据客户的要求,决定电路图设计、板层结构和步法。
另外,还处于决定必要的层数和技术要求事项,准备后续制造工程的阶段。
材料准备:按照基板材料、被覆铜膜、被覆及内部层的相关标准,保证产品质量。
从基础材料、电镀溶液和油墨等可靠供应商处购买设计要求和配置。
激光穿孔:利用激光技术在板上加工小孔,实现电路的连接。
激光钻头能够准确地控制口径的大小和位置,这是实现高密度相互连接的关键步骤。
压延:通过热压技术,内外部板硬化,压缩电路板保障电路板的严密性和稳定性。
蚀刻:化学去除铜涂层不必要的部分,保持传导途径。
被覆:在板面进行电镀处理,使其具有良好的导电能力和防氧化性能。
插件及焊接:在电路中插入零件,进行焊接固定。
测试及检查:通过严格的测试及检查,保证产品的质量和性能。
在hdi多层电路板制造过程中,涉及了层叠式汇编、百叶窗孔(blind hole)技术等核心技术。
阶梯式组装是将带有多个电路图案的器材层层堆叠起来,形成多层电路板。
盲眼孔技术是指,不贯穿整个电路板,而制造贯穿两个或多个基材层的孔,提高电路板的集成度和信号传送性能。
请注意,具体的hdi制造工程根据制造商、技术标准及产品要求事项可能有所不同。
如果需要更详细的信息,最好参考相关专门文件或向hdi生产领域的专家咨询。
HDI板制造工艺概述

一、 CO2 激光钻孔
1. CO2激光成孔原理 CO2气体在增加功率及维持放电时间下,产生波长
在9400nm~10600nm之间的可实用的脉冲式红外激光, 众所周知,红外线的基本特性是能够穿透绝大多数的 有机物材料表面到内部的特性。同时,绝大多数有机 物材料具有强烈吸收红外线波长的特点。有机物材料 分子吸收红外线波长而提高能量,这就体现了红外线 的“热效应”特性。CO2激光钻机就是应用红外线的 这种光热效应对有机物进行烧灼,形成连通性盲孔。
Dongguan Yili Circuit Plate Co, Ltd. 15
3. CO2激光成孔的钻孔方法
CO2激光成孔的钻孔方法主要有直接成孔法和 敷形掩膜成孔法两种。所谓直接成孔工艺方法就是 把激光光束经设备主控系统将光束的直径调制到与 被加工印制电路板上的孔直径相同,在没有铜箔的 绝缘介质表面上直接进行成孔加工。敷形掩膜工艺 方法就是在印制板的表面涂覆一层专用的掩膜,采 用常规的工艺方法经曝光/显影/蚀刻工艺去掉孔 表面的铜箔面形成的敷形窗口。然后采用大于孔径 的激光束照射这些孔,切除暴露的介质层树脂。现 分别介绍如下:
Dongguan Yili Circuit Plate Co, Ltd. 3
2.什么是HDI (High Density Interconnection)
●凡非機械鑽孔,孔徑在0.15mm(6mil)以下 (大部份為盲孔),孔環(Annular Ring or Pad or Land)之環徑在0.25mm(10mil)以下者, 特稱為Microvia微導孔或微孔。
Dongguan Yili Circuit Plate Co, Ltd. 9
HDI板加工流程图

成型
成型后
電性測試
最終檢驗
OSP
包裝前
包裝后
L1/L6層線路及圖樣之制作 板面塗上綠漆作為保護線路及絕緣 將加工板的尺寸切割成客戶要的尺寸 以目視,目鏡及驗孔機等確認板面孔徑及外觀品質. 將加工板的尺寸切割成客戶要的尺寸 在基板上鑽孔,以方便后續加工(對位及檢修) 表面鍍銅,使L1-L6&L1-L2&L5-L6層能導通 使用補強材料以使上,下增層成為四層板 在基板上鑽孔,以方便后續加工(對位及檢修) I(1+4+1)疊構之制作流程圖 以目視,目鏡及驗孔機等確認板面孔徑及外觀品質. 作為L1/L6層與層導通之通道 板面塗上綠漆作為保護線路及絕緣 板面進行護銅膜之處理,以確保銅面之品質 表面鍍銅,使L1-L6&L1-L2&L5-L6層能導通 表面鍍銅,使L1-L6&L1-L2&L5-L6層能導通 表面鍍銅,使L2/L5層能導通 L3/L4內層線及圖樣之制作 L3/L4內層線及圖樣之制作
電鍍烤箱
MASK后板子
鐳射鑽孔機
PLASMA去膠渣
去黑膜
BLASER AOI
Laser去黑膜后板
防焊前處理
防焊噴塗
防焊曝光機
作為L2/L5層與層導通之通道 用laser能量打出碗狀孔形,作為盲孔層導通之通道(L1-L2&L6-L5) 表面鍍銅,使L1-L6&L1-L2&L5-L6層能導通 L1/L6層線路及圖樣之制作 使用補強材料以使上,下增層成為四層板 I(1+4+1)疊構之制作流程圖 L1/L6層線路及圖樣之制作 作為L1/L6層與層導通之通道 以目視,目鏡及驗孔機等確認板面孔徑及外觀品質. 合格品依客戶需求進行包裝及入庫 將加工板的尺寸切割成客戶要的尺寸 板面塗上綠漆作為保護線路及絕緣 用laser能量打出碗狀孔形,作為盲孔層導通之通道(L1-L2&L6-L5) 將加工板的尺寸切割成客戶要的尺寸 在銅面上開出孔型,以利Laser打孔加工!. 表面鍍銅,使L1-L6&L1-L2&L5-L6層能導通 將加工板的尺寸切割成客戶要的尺寸 L3/L4內層線及圖樣之制作 板面局部進行化金處理,作為接觸或標示用
- 1、下载文档前请自行甄别文档内容的完整性,平台不提供额外的编辑、内容补充、找答案等附加服务。
- 2、"仅部分预览"的文档,不可在线预览部分如存在完整性等问题,可反馈申请退款(可完整预览的文档不适用该条件!)。
- 3、如文档侵犯您的权益,请联系客服反馈,我们会尽快为您处理(人工客服工作时间:9:00-18:30)。
HDI制作工艺
导读:二阶盲孔制板在我司从实验至今,已一年有余,作为一种新工艺,从HDI的发展趋势来看,将会继续向高密度互连发展。
而且二阶盲孔制板过程繁杂,多次往返内、外层。
随着该类板市场前景越来越好,我部在样品制作及设备引入方面都做了一些准备工作,我们将从样板制作方面归纳一些经验,希望在此与大家互相交流,以做进一步提高,希望在批量推广过程中能起到借鉴作用。
二阶盲孔比例分析统计该类定单的产品结构(如附图),可看出Staggered via的二阶盲孔即将成为主流产品。
二阶盲孔的分类二阶盲孔常用材料
镭射的开窗形式
制作流程设计
Staggered via 单次盲孔制作流程同一阶盲孔采用X-ray + 板边孔+ Conformal Mask+CO2(UV)的钻孔工艺优点:工艺成熟、通孔与盲孔配套好缺点:孔易鼓形
采用X-ray + Large window+CO2(UV)的钻孔工艺优点:对位好,孔形好,简化流程。
降低电镀难度缺点:增加X-ray的产能,镭射要求高、不适合Pad size小的板采用
X-ray+Conformal mask工艺优点:对位好,提高与Capture Pad的对位缺点:孔型控制难采用UV开窗
+CO2的钻孔工艺优点:实现微小孔化,避免漏开窗、孔径均一缺点:产能低采用UV 直接钻孔优点:微小孔化,避免漏开窗,刮内层靶标,与Target Pad 对位极好、孔径均一缺点:产能极低,易伤底铜
Staggered via按照工艺的优缺点选择方法孔径D:当D≤
2mil时只能选择UV直接钻孔当2 <> 当D>4mil时采用Conformal Mask或Large window工艺锡圈:如果锡圈小于
4mil时最好用X-ray+Conformal mask工艺
Stack via (Telescopicvia)
采用UV+CO2的钻孔工艺适用于RCC材料采用Conformal Mask+CO2+UV+CO2的钻孔工艺适用于FR4材料及外层表铜为镀铜的板
Skip via(可以融合到Staggered via或Stack via的设计中)制作流程1(以含IVH八层板,负片流程为例)
适用二阶盲孔范围:交错盲孔和叠加盲孔中的plating filling 的制板生产控制重点:镭射钻孔:正常的开窗+CO2的钻孔电镀:采用正常的直流电镀或填平电镀线制作
制作流程2(以含IVH八层板,负片流程为例)
适用二阶盲孔范围:常规的Stacked via的制板生产控制重点:镭射钻孔:1、镭射钻孔的流程指定2、不同孔径的钻孔参数及FA电镀:采用三合一(沉铜两次)+脉冲电
镀
特别提示(样板制作中的教训)同一制板中孔的种类以最少为原则Staggered via和Stack via(Telescopic via)尽量不能设计于同一个板中,若非允许时则一定采用Plating filling工艺介电材料的选择(LUHB020)4mil Core的钻孔电镀改为HDI 板(4+4)
对位设计对位设计原则:以盲孔为主,先盲孔再通孔ˉX-Ray 靶标的设计:盲孔Target Pad所在层必须设计靶标,以八层板三次压板为例
盲孔孔径大小及对应Pad的设计
二阶盲孔的制作难点
对位不正可能原因:1、干菲林曝光对位偏解决方法:1、坚控菲林的涨缩在+/-1mil范围内,首板曝光后和显影后分别检查对位情况,保证至少1mil的锡圈;2、完善不同板厚经过前处理磨板后的菲林预补偿情况;3、二阶盲孔板采用自动曝光机制作各层图形及Conformal Mask开窗线路对位不正可能原因:1、Conformal Mask曝光对位偏解决方法:1、坚控菲林的涨缩在+/-1mil范围内,及设置自动曝光机的涨缩控制范围在50um Conformal Mask开窗偏孔对位问题特别控制方面物料的选择-----建议不选用尺寸稳定性较差的物料锔板周期条件:105℃x4Hrs
热应力周期条件:150 ℃2Hrs
干菲林Conformal Mask:控制蚀刻后的盲孔孔径线路的制作:埋孔线路及次外层图形一定用自动机曝光
CO2 镭射钻孔可能原因:1、镭射钻孔参数能量大
2、被重复钻孔
3、板边孔钻偏解决方法:1、FA参数的选择2、调整镭射钻孔参数3、钻孔后用30倍和200倍放大镜结合检查,出货前全检可能原因:1、镭射钻孔参数能量小
2、UV开窗后的板漏钻
3、镭射机本身能量低解决方法:1、FA参数的选择
2、调整镭射钻孔参数
3、UV开窗后和修孔后的板做不同标记
4、每四小时监控一次钻机能量
5、钻孔后用30倍和200倍放大镜结合检查,出货前全检
可能原因:1、Large Window钻孔参数设置不合理,能量集中,伤底铜2、镭射机波形的影响
解决方法:1、FA参数的选择2、调整镭射参数,选择合适的Aperture来避免
3、需要供应商调整设备
UV镭射钻孔可能原因:1、UV参数能量大
2、底铜薄解决方法:1、UV镭射参数的调整及选择
2、采用UV+CO2的工艺
3、底铜厚度小于1/2oz时不可以采用UV直接钻孔
4、每四小时监控一次钻机能
量5、钻孔后用30倍和200倍放大镜结合检查可能原因:1、UV参数设置不合理,能量偏大
2、锡圈小,Pad松动
3、铜厚度及均匀性的影响解决方法:1、UV镭射参数的调整及选择,采用两步以上钻孔时需设置不同的能量2、对于次外层铜需要UV镭射钻孔时,要求最小锡圈为4mil
3、经过镀铜的板不能选择UV钻孔
镭射钻孔设备的优点利用设备的利用尤其发挥UV Laser钻机的优点,可以钻大于或等于1mil的盲孔,可以利用UV开窗而且不会漏孔,孔越小速度越快等特点;设备的搭配,根据不同孔类型选择不同的设备,例如Sumitomo可以钻10mil 以上的大孔,速度相对较快
盲孔电镀
可能原因:1、沉铜不良2、镭射伤底铜,影响药水交换解决方法:1、由于盲孔纵横比大,药水在孔内交换困难,采用沉铜两次+脉冲电镀或者三合一+脉冲电镀的方法2、定期分析药水,按时添加和保养3、调整镭射钻孔参数或流程,保证钻孔不能伤底铜,保证孔型良好,孔壁有一定的斜度,一般要求孔底直径为空口直径的70%可能原因:1、三合一微蚀缸停留时间长造成微蚀过度
2、镭射钻孔及通孔后过SUEP解决方法:1、加强设备的检
修、培训员工的操作和上、下板的方法
2、缩短工序之间的停留时间,减小环境的影响
3、Conformal Mask、Laser、通孔后绝对不允许再做SUEP
可能原因:1、磨板造成孔内杂物2、药水缸内杂物解决方法:1、试验X-Ray →钻板边孔→Conformal Mask →机械钻孔→磨板→镭射钻孔→三合一的
工艺流程,减小磨板的影响2、缩短工序之间的停留时间,减小环境的影响,而且三合一后的不能进行磨板等处理3、加强电镀线的保养
线路的制作----开、短路及蚀刻不清Q原因:板凹,铜粗,进入干菲林的板磨板质量不佳,贴膜不紧菲林松,曝光垃圾,走光等等改进:定期检查压板钢板质量改善板凹,压板拆板后的板及运输过程中都需要隔胶片,防止擦伤,电镀前磨板及加强电镀缸的过滤和保养改善铜粗,非Conformal Mask板进入干菲林前用氧化铝磨板,贴膜时预热和后压,尤其埋孔未塞树脂的板减缓贴膜速度及贴膜后放置一小时以上,优先使用自动机进行曝光防止走光。
实验杜邦湿法贴膜工艺,减少板面问题带来的开、短路
绿油问题可能原因:
1、绿油手动对位
2、菲林涨缩影响解决方法:1、欲购置绿油自动曝光机提高对位,当前采用十
倍镜对位2、少量认证板可采用UV镭射修理,保证完美交货3、控制菲林的涨缩在+/-1mil范围内及严格控制绿油洁净房的温湿度绿油对歪上Pad
可能原因:1、曝光不良解决方法:1、需要调整蓝油的曝光参数,降低曝光能量2、做板前先做曝光尺加以检验可能原因:1、丝印的局限
2、孔上绿油薄解决方法:1、若采用Curtain coating或者Spray coating的方法,结果绿油颜色均匀2、按照现在的丝印方法则只能通过返印绿油加以改善盲孔不过油、发红正常图片可能原因:1、丝印的局限解决方法:1、采用Curtain coating 或者Spray coating的方法,结果绿油颜色均匀绿油高于Pad 正常图片。