300机组500轧机断辊分析及控制措施.docx
轧辊破坏常见原因分析及对策
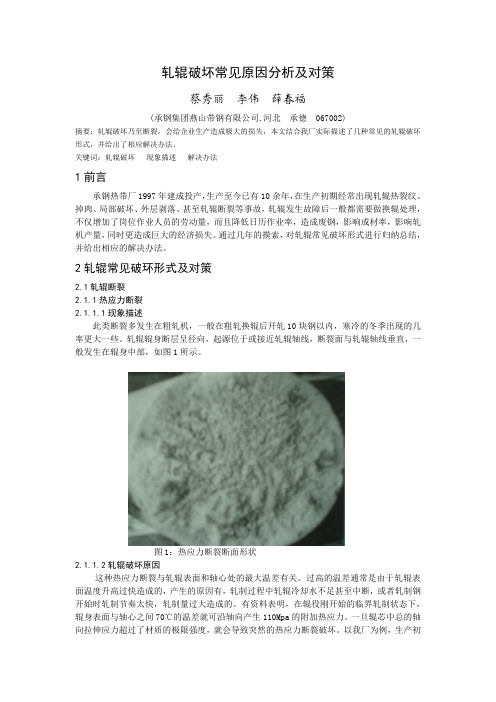
轧辊破坏常见原因分析及对策蔡秀丽李伟薛春福(承钢集团燕山带钢有限公司,河北承德 067002)摘要:轧辊破坏乃至断裂,会给企业生产造成极大的损失,本文结合我厂实际描述了几种常见的轧辊破坏形式,并给出了相应解决办法。
关键词:轧辊破坏现象描述解决办法1前言承钢热带厂1997年建成投产,生产至今已有10余年,在生产初期经常出现轧辊热裂纹、掉肉、局部破坏、外层剥落、甚至轧辊断裂等事故,轧辊发生故障后一般都需要做换辊处理,不仅增加了岗位作业人员的劳动量,而且降低日历作业率,造成废钢,影响成材率,影响轧机产量,同时更造成巨大的经济损失。
通过几年的摸索,对轧辊常见破坏形式进行归纳总结,并给出相应的解决办法。
2轧辊常见破环形式及对策2.1轧辊断裂2.1.1热应力断裂2.1.1.1现象描述此类断裂多发生在粗轧机,一般在粗轧换辊后开轧10块钢以内,寒冷的冬季出现的几率更大一些。
轧辊辊身断层呈径向,起源位于或接近轧辊轴线,断裂面与轧辊轴线垂直,一般发生在辊身中部,如图1所示。
图1:热应力断裂断面形状2.1.1.2轧辊破坏原因这种热应力断裂与轧辊表面和轴心处的最大温差有关。
过高的温差通常是由于轧辊表面温度升高过快造成的,产生的原因有,轧制过程中轧辊冷却水不足甚至中断,或者轧制钢开始时轧制节奏太快,轧制量过大造成的。
有资料表明,在辊役刚开始的临界轧制状态下,辊身表面与轴心之间70℃的温差就可沿轴向产生110Mpa的附加热应力。
一旦辊芯中总的轴向拉伸应力超过了材质的极限强度,就会导致突然的热应力断裂破坏。
以我厂为例,生产初期,有一次正值寒冬腊月,室外温度-20℃,厂房内温度较低,备辊正处在风口上,轧辊上线前没有预热,仅烫辊4块,在烫辊效果不好的前提下,温度较低的冷却水很快浇凉辊面,在轧制中与红钢接触,轧辊处于冷热交替中,内外表面温差大。
断辊后约10分钟,用手摸断辊边缘,触觉为凉辊,带钢轧制部位的轧辊表面微温,轧辊断口内触觉发凉。
热轧轧辊剥落或断裂的原因及预防方法探究

热轧轧辊剥落或断裂的原因及预防方法探究热轧轧辊作为热轧设备中重要的组成部分,其质量直接影响到产品质量和生产效率。
在生产中,往往会出现轧辊剥落或断裂的情况,造成了生产效率低下和安全隐患,因此研究热轧轧辊剥落或断裂的原因及预防方法具有重要的实际意义。
1. 轧辊表面损伤导致轧辊剥落或断裂在轧辊使用过程中,出现轧辊表面损伤容易导致轧辊剥落或断裂。
这种损伤包括表面裂纹、划痕、磨损、腐蚀等,这些损伤会进一步扩大,最终导致轧辊剥落或断裂。
轧辊材质好坏直接影响到轧辊的使用寿命和质量。
如果轧辊的材质不够坚固耐用,那么在热轧过程中会出现轧辊变形、疲劳、裂纹等问题,将极大影响热轧产品质量。
热轧设备的操作不规范也容易导致轧辊剥落或断裂。
例如温度控制不当、轧辊调整不到位等等,都会在热轧过程中产生不同程度的影响,最终导致轧辊剥落或断裂。
热轧工艺参数是热轧过程中必须严格控制的参数,如果热轧工艺参数不合适将会直接影响到轧辊的寿命和使用效果。
例如,轧制过程中的拉伸率、轧制力、速度等参数不合适,都将导致轧辊剥落或断裂。
1. 轧辊材质的优化优化轧辊材质可以提高轧辊的抗拉、抗压、抗疲劳等性能。
特别是在硬度和韧性之间的平衡上,选择合适的轧辊材料可大大提高轧辊的使用寿命。
2. 加强对轧辊的检测热轧轧辊在使用过程中应每隔一些周期对轧辊进行检测,及时发现轧辊损伤和裂纹等问题并进行处理,避免因轧辊的损坏而影响到生产和产品质量。
3. 热轧设备的维护针对热轧设备操作不规范等问题,应加强设备维护,保持轧辊的良好状态。
定期做好轧辊的维护与更新,及时清理轧辊附着的物质,避免附着物进一步侵蚀轧辊表面。
4. 控制热轧工艺参数对于热轧工艺参数不合适问题,应严格控制热轧温度、轧制力、速度等参数。
调整工艺参数能够有效避免轧辊的剥落或断裂。
总之,对于热轧轧辊剥落或断裂问题,合理地选择轧辊材质,加强轧辊的检测和维护,规范热轧设备操作,严格控制热轧工艺参数,是预防轧辊剥落或断裂的有效方法。
热轧轧辊剥落或断裂的原因及预防方法探究
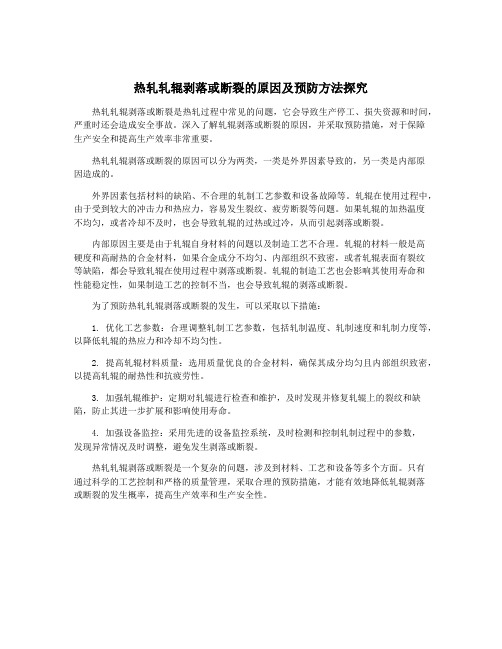
热轧轧辊剥落或断裂的原因及预防方法探究热轧轧辊剥落或断裂是热轧过程中常见的问题,它会导致生产停工、损失资源和时间,严重时还会造成安全事故。
深入了解轧辊剥落或断裂的原因,并采取预防措施,对于保障生产安全和提高生产效率非常重要。
热轧轧辊剥落或断裂的原因可以分为两类,一类是外界因素导致的,另一类是内部原因造成的。
外界因素包括材料的缺陷、不合理的轧制工艺参数和设备故障等。
轧辊在使用过程中,由于受到较大的冲击力和热应力,容易发生裂纹、疲劳断裂等问题。
如果轧辊的加热温度不均匀,或者冷却不及时,也会导致轧辊的过热或过冷,从而引起剥落或断裂。
内部原因主要是由于轧辊自身材料的问题以及制造工艺不合理。
轧辊的材料一般是高硬度和高耐热的合金材料,如果合金成分不均匀、内部组织不致密,或者轧辊表面有裂纹等缺陷,都会导致轧辊在使用过程中剥落或断裂。
轧辊的制造工艺也会影响其使用寿命和性能稳定性,如果制造工艺的控制不当,也会导致轧辊的剥落或断裂。
为了预防热轧轧辊剥落或断裂的发生,可以采取以下措施:1. 优化工艺参数:合理调整轧制工艺参数,包括轧制温度、轧制速度和轧制力度等,以降低轧辊的热应力和冷却不均匀性。
2. 提高轧辊材料质量:选用质量优良的合金材料,确保其成分均匀且内部组织致密,以提高轧辊的耐热性和抗疲劳性。
3. 加强轧辊维护:定期对轧辊进行检查和维护,及时发现并修复轧辊上的裂纹和缺陷,防止其进一步扩展和影响使用寿命。
4. 加强设备监控:采用先进的设备监控系统,及时检测和控制轧制过程中的参数,发现异常情况及时调整,避免发生剥落或断裂。
热轧轧辊剥落或断裂是一个复杂的问题,涉及到材料、工艺和设备等多个方面。
只有通过科学的工艺控制和严格的质量管理,采取合理的预防措施,才能有效地降低轧辊剥落或断裂的发生概率,提高生产效率和生产安全性。
轧制过程中断辊原因
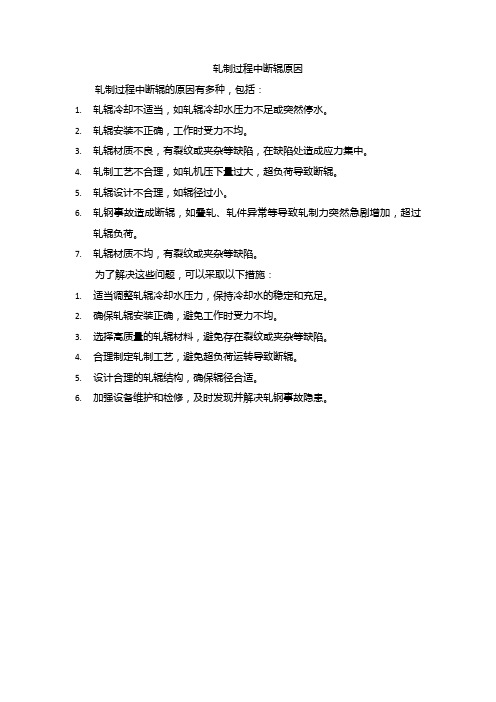
轧制过程中断辊原因
轧制过程中断辊的原因有多种,包括:
1.轧辊冷却不适当,如轧辊冷却水压力不足或突然停水。
2.轧辊安装不正确,工作时受力不均。
3.轧辊材质不良,有裂纹或夹杂等缺陷,在缺陷处造成应力集中。
4.轧制工艺不合理,如轧机压下量过大,超负荷导致断辊。
5.轧辊设计不合理,如辊径过小。
6.轧钢事故造成断辊,如叠轧、轧件异常等导致轧制力突然急剧增加,超过
轧辊负荷。
7.轧辊材质不均,有裂纹或夹杂等缺陷。
为了解决这些问题,可以采取以下措施:
1.适当调整轧辊冷却水压力,保持冷却水的稳定和充足。
2.确保轧辊安装正确,避免工作时受力不均。
3.选择高质量的轧辊材料,避免存在裂纹或夹杂等缺陷。
4.合理制定轧制工艺,避免超负荷运转导致断辊。
5.设计合理的轧辊结构,确保辊径合适。
6.加强设备维护和检修,及时发现并解决轧钢事故隐患。
板带轧机工作辊断裂原因分析

和人 身 的安 全 ,事故处 理 时问 长 ,影 响轧 机 的作业
率 。
板带 工作 辊 的断 裂 可发 生在 辊 身 、辊 颈 、传 动
端轴 头处 。轧辊 断 裂 原 因 通 常有 两 类 :一类 属 于
轧辊材质或制造质量 ,即轧辊本身内在缺陷造成 , 如制造后残余应力过大 、铸造缺陷或热处理不 当
关键 词 轧辊 断裂 残余应力 组织缺 陷
Analysis on Causes of W ork Roll Rupture on Strip M ill
Han Hu ̄un and Lu Rui (H ̄dan Iron and Steel Group Corporation Ltd)
A bstract The article descr ibes the work roll rupture conditions on str ip mil,analyzes the causes of r u pture,dis— cusses the rupture mechanism of various causes,and puts forward the preventive measures avoiding mill roll r upture.
轧制过程中制过程的进行温度逐步上升在此过程中轧辊的热应力与残余应力叠加在一起在中心部位产表面温度高而芯部仍处于低温状态温度沿径向生较大的合成拉应力当合成应力超过材料的抗40宽厚板第14卷拉强度时轧辊芯部就会产生裂纹甚至会发生断辊如果再有缩孔疏松和夹杂缺陷则会加剧断辊的发生
维普资讯
温度沿径向呈抛物线型分布 ,表面温度上升, 体积膨 胀 ,这种 膨胀 受低 温 芯 部 的阻 碍 而产 生应 力 。产 生 的 热 应 力 可 分 解 为 三 部 分 :轴 向应 力 (盯 )、切 向应力 (盯 )及 径 向应 力 (盯 )。三方 向的 热 应力 可根据 弹 性 理 论算 出 ,除 径 向应 力 在 半 径
轧机上断辊的原因分析
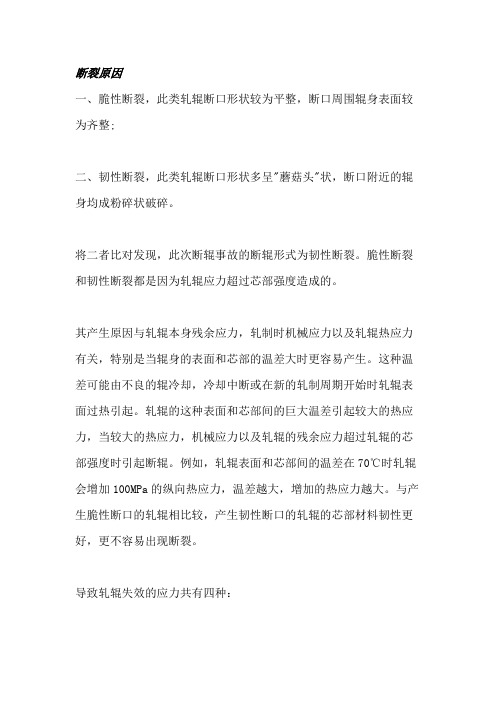
断裂原因一、脆性断裂,此类轧辊断口形状较为平整,断口周围辊身表面较为齐整;二、韧性断裂,此类轧辊断口形状多呈"蘑菇头"状,断口附近的辊身均成粉碎状破碎。
将二者比对发现,此次断辊事故的断辊形式为韧性断裂。
脆性断裂和韧性断裂都是因为轧辊应力超过芯部强度造成的。
其产生原因与轧辊本身残余应力,轧制时机械应力以及轧辊热应力有关,特别是当辊身的表面和芯部的温差大时更容易产生。
这种温差可能由不良的辊冷却,冷却中断或在新的轧制周期开始时轧辊表面过热引起。
轧辊的这种表面和芯部间的巨大温差引起较大的热应力,当较大的热应力,机械应力以及轧辊的残余应力超过轧辊的芯部强度时引起断辊。
例如,轧辊表面和芯部间的温差在70℃时轧辊会增加100MPa的纵向热应力,温差越大,增加的热应力越大。
与产生脆性断口的轧辊相比较,产生韧性断口的轧辊的芯部材料韧性更好,更不容易出现断裂。
导致轧辊失效的应力共有四种:一、制造过程中的残余应力;二、轧制过程中的机械应力;三、轧制过程中轧辊的组织应力;四、轧辊内外温差造成的热应力。
如果是因为制造残余应力过大产生断裂,断辊通常发生在轧辊初始上机使用的前几次,且为开轧的前几块轧材。
此次断裂的轧辊已经上机轧制了四次,工作层消耗了14mm,因此不应是因制造残余应力形成的断裂。
如果是因为机械应力产生的断裂,需要很大的机械应力。
经粗略计算,如此大截面的高铬铸钢轧辊若被机械应力拉断,则需要100MN 以上的拉力,对于该轧辊工作的轧机来说这是不可能的。
轧辊受力最大的部位是传动端辊颈,如果材料的力学性能指标不足,正常轧制情况下首先损坏的是传动端辊颈。
从实际轧制和断辊情况来看,不是由于机械应力造成辊身断裂。
对组织应力影响最大的就是外层组织中残余奥氏体含量。
残余奥氏体在轧制温度,轧制压力和水冷的交变作用下,发生奥氏体向马氏体或贝氏体的转变,由于奥氏体的比容小,而马氏体的比容大,因而在组织转变的过程中伴随着体积的膨胀,会致使轧辊的工作层产生更大的压应力,芯部产生更大的拉应力,芯部应力一旦超过材料的强度,必然造成轧辊断裂。
热轧窄带钢粗轧机轧辊的断裂及预防

热轧窄带钢粗轧机轧辊的断裂及预防摘要:根据我厂热轧窄带钢粗轧机组轧辊的使用情况,分析了轧辊断裂的主要原因,并提出了相应的预防措施。
关键词:热轧窄带钢轧机;断裂;预防措施1.前言莱钢轧钢厂500mm热带是一条全连续热轧窄带钢生产线,具有轧机精度高、检测系统完善等特点。
整条生产线共有十六架轧机,分粗轧机组和精轧粗轧两部分,粗轧部分由八架轧机组成,布置形式为立、平、立、平、平、立、平、平;精轧部分由八架轧机组成,布置形式为立、平、平、平、平、平、平、平。
粗轧机组轧机较多,因此轧辊消耗较大,同时为了提高轧机的生产率,已进行了大量的尝试来改善设备性能和轧制工艺,特别对粗轧机轧辊的断裂做了许多有益的研究,但是轧制条件变得愈加苛刻,并且随着产量的不断增加,轧辊断裂现象还时有发生,不但造成经济上的直接损失,还由于断辊停产,减少了产量,增加了热轧废品,增加了能源消耗,因而增加了总成本。
据不完全统计,仅粗轧辊断裂年损失约40万元,停产时间约17 万元,利润约30万元,综合经济损失年平均约87万元,约占总成本的0.54% 。
因此研究轧辊断裂的原因,并采取有效的预防措施,对降低成本,提高经济效益有非常重要的意义。
本文根据实际综合情况做了具体研究并采取了相应的预防措施。
2.轧辊断裂的原因轧辊是轧机的重要组成部分,热轧时轧辊承受各种载荷及在复杂的条件下工作,如果再加上操作不当往往会造成轧辊断裂。
断辊的原因很多,下面从轧辊断裂的部位来具体分析。
2.1.在轧辊辊身处断裂从断裂现象看断裂部位绝大多数在辊环处,断裂截面为不规则的斜面或垂直截面。
断辊原因有以下几个方面:2.1.1.轧辊质量(1)粗轧平辊机组为二辊轧机,工作辊与高温板坯直接接触,并承受各种载荷,因此要有良好的耐热性,如果轧辊辊身硬度随轧辊温度升高而降低的幅度较大时,说明轧辊的耐热性较差,将严重影响轧辊的整体性能。
(2)从轧制条件看要求轧辊还应具有良好的耐磨性和适当的硬度和强度。
轧辊失效分析

轧辊缺陷引发失效有三个原因:制造商轧机轧辊维护及管理(管理指磨辊)失效后数据收集要了解:1. 事故段的轧制压力,电压,水压等2. 事故发生时的操作情况3. 轧制废品种规格4. 对最后轧制的板卷暂时保存用于对事故产生原因分析失效分析要点1.辊身剥落为CVC形态,基本为表面缺陷较垂直延伸至结合层,四周快速发展2.剥落区一侧垂直,另一侧逐步过渡至表面,基本剥落区为出口3.多处小块掉肉,掉肉面为棘齿形态,是硬块疲劳裂纹造成4.弧形掉肩通常是支撑辊倒角设计不合理5.断口端面由内向外四周散射,是心部缺陷或强度不够造成的断裂6.近辊身端部环形剥落且在环形带为多元发展源,单侧异常超负荷制造厂轧辊质量引发事故分析元宝形大剥落1.结合层严重非金属夹渣引起的轧辊剥落蜂窝状且色发黑为非金属价夹渣:如,钢水渣,耐火砖,测温管等辅助材料的掉入大块的非金属夹渣只要存在于复合辊的结合层2.金属夹杂引发轧辊剥落剥落后表面发亮成块状,颗粒状:金属原料没有充分熔化,或非原料的金属夹入3.异常发展引发断辊(内部金属夹杂)微小的轧辊夹杂早期在辊身暴露会使轧制的板材产生凸块,使钢材表面质量受到影响4.辊身硬度不均匀形成裂纹—裂纹平行,斜纹,不规则如果裂纹未能磨削干净,会使裂纹扩展5.应力造成轧辊开裂,裂纹环带有的可贯穿整个轴向和颈开裂内应力过大引起的断辊和开裂内应力造成轧辊使用中轴向爆裂为两半(中心向四周扩撒)由于过大的残余内应力,径向断裂多从心部成中心附件,显示放射状痕迹,断面垂直于轧辊轴心,断面起源常位于辊身辊身表面和心部的最大温度差有关---产生残余应力危害:运输中爆裂在磨削过程中爆裂在使用过程中发生爆裂(处理时间长)制造商在热处理,调质处理后的严格按工业技术程序执行,出厂前做应力测试,以消除内应力。
可以买回新辊,放仓库先释放应力。
首次使用的轧制周期不要过长6.黑斑:石墨球化不良铸造时浇铸时间,速度不当造成元素分布不均匀引起7.内部缺陷扩展,引发大的剥落,剥落处可看见一处原地向四周发展预防:结合层缺陷,用UT测试8.工作层厚薄不均匀引发剥落,工作层(精轧)余量8MM, 但实际工作辊余量还要大些9.结合层碳化物平行发展引发轧辊轧制事故10.工作层强度降低(原因:石墨比较大)11.辊颈抗拉强度低造成断辊(牛眼状铁素体,保证轧辊强度)12.辊颈铸接不良,辊颈折断13.卡刚,异物掉入引发大剥落(轴向,径向产生裂纹)14.粘钢引起掉肉。
轧机勒辊原因分析及控制措施

厚度 减 薄 ,从而 会 导致, : 刑 第 l f J 【 架 …【 1 发' I -
辊 现 象
在实 际轧制 时 ,原 料给定性 能 ’ j 实际 能 小州 从高强 钢 向强 度较 低强 符 也是一种常 见现象 陔现象分为阿种情况 :1 ) 味料 度 钢 种《 n n l F 钢) 过 渡时 容 易存4 、5 机架 发 牛勒辊 现 给定性 能低于实际性能的情况 例 系统给定的材料 制钠 的. 1 『 1 种发 变化时 , 象 ,= L嵫涉 及C Q 。 HS S 钢种  ̄ i i cq 钢 种之 问的过渡 连 接或 磷高强钢 C Q钢种的过渡连接
轧机 ቤተ መጻሕፍቲ ባይዱ辊 的原 因分析
根据 近 几年 对冷连轧 5 机 架6 辊轧 机组的 跟踪 、
跑偏 造成 的。带钢 粘辊 、勒辊较 轻微时 ,带钢 表 面 分析 ,及埘冷轧 产工 艺的不断探讨 与研究。对 发生 及轧辊 本身都 有勒 印 ,严 重时 会发 断 带事故 。例 勒辊现象时 的带钢 实物 、轧 制理论 及MI C A 线 等多
勒 辊 的发生 工 艺优 化后 ,保证 了各 种规格 等难轧 品种 生产 的稳 定轧制 ,稳定 降低 了生产成 本及
轧 辊 消 耗 ,提 高 了产 品 质 量 .
存 拎 连 轧 牛 产 巾 ,带 钢 在 机 架 I ' n 】 发 生 的勒 辊
现象 频繁 发牛 。勒辊 是 F } i 丁轧辊 的辊缝 弹跳跨 度过 大 ,斥下量过 大致 使带钢 产生重叠 及带 钢在机 架问
过程 中带钢 在机架 内瞬 间失张而 偏离轧 制 中心 线所
致 本文根据本钢某冷轧P L . T C M机组的生产实际 ,
热轧轧辊剥落或断裂的原因及预防方法探究
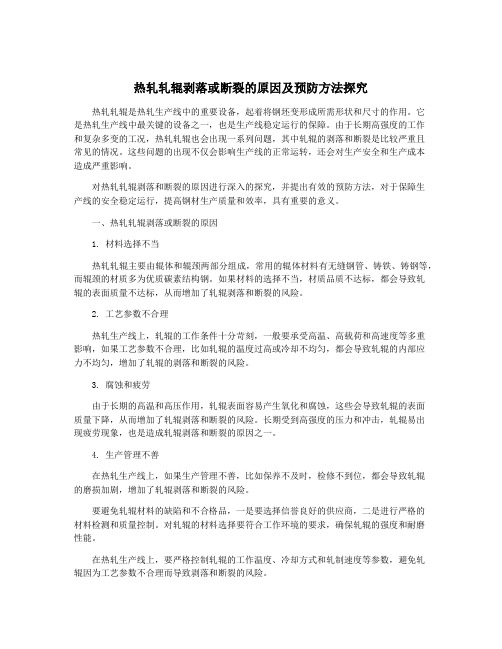
热轧轧辊剥落或断裂的原因及预防方法探究热轧轧辊是热轧生产线中的重要设备,起着将钢坯变形成所需形状和尺寸的作用。
它是热轧生产线中最关键的设备之一,也是生产线稳定运行的保障。
由于长期高强度的工作和复杂多变的工况,热轧轧辊也会出现一系列问题,其中轧辊的剥落和断裂是比较严重且常见的情况。
这些问题的出现不仅会影响生产线的正常运转,还会对生产安全和生产成本造成严重影响。
对热轧轧辊剥落和断裂的原因进行深入的探究,并提出有效的预防方法,对于保障生产线的安全稳定运行,提高钢材生产质量和效率,具有重要的意义。
一、热轧轧辊剥落或断裂的原因1. 材料选择不当热轧轧辊主要由辊体和辊颈两部分组成,常用的辊体材料有无缝钢管、铸铁、铸钢等,而辊颈的材质多为优质碳素结构钢。
如果材料的选择不当,材质品质不达标,都会导致轧辊的表面质量不达标,从而增加了轧辊剥落和断裂的风险。
2. 工艺参数不合理热轧生产线上,轧辊的工作条件十分苛刻,一般要承受高温、高载荷和高速度等多重影响,如果工艺参数不合理,比如轧辊的温度过高或冷却不均匀,都会导致轧辊的内部应力不均匀,增加了轧辊的剥落和断裂的风险。
3. 腐蚀和疲劳由于长期的高温和高压作用,轧辊表面容易产生氧化和腐蚀,这些会导致轧辊的表面质量下降,从而增加了轧辊剥落和断裂的风险。
长期受到高强度的压力和冲击,轧辊易出现疲劳现象,也是造成轧辊剥落和断裂的原因之一。
4. 生产管理不善在热轧生产线上,如果生产管理不善,比如保养不及时,检修不到位,都会导致轧辊的磨损加剧,增加了轧辊剥落和断裂的风险。
要避免轧辊材料的缺陷和不合格品,一是要选择信誉良好的供应商,二是进行严格的材料检测和质量控制。
对轧辊的材料选择要符合工作环境的要求,确保轧辊的强度和耐磨性能。
在热轧生产线上,要严格控制轧辊的工作温度、冷却方式和轧制速度等参数,避免轧辊因为工艺参数不合理而导致剥落和断裂的风险。
要对轧辊的表面进行防腐处理,避免氧化和腐蚀的发生;并对轧辊进行定期的疲劳检测和预防性维护,延长轧辊的使用寿命。
型钢轧辊断辊分析

型钢轧辊断辊原因分析
最近连着断了4付辊,其中3付是断在中间台,一付断在孔型正中央,从轧机过钢电流来看,电流正常,没有超负荷,钢的出炉温度也正常,求助各位高手,帮我看看,是什么原
注:断辊的是两个不同的机架,每个机架断了2根。
观点一:从断口看,有老的裂纹。
可能有以下原因:1)轧辊用到直径下线,轧辊长期处于疲劳状态;2)水冷却不足;3)孔型道次变形不合理;4)轧辊本身问题。
观点二:轧辊的质量有问题、轧机的稳定性不好导致有老伤孔型设计是否也有问题。
观点三:从图4看,轧槽表面有龟裂纹,是缺水。
从图2看,断面边缘有“旧印”,是疲劳损坏。
造成疲劳的原因除了负荷增大(温度、变形量、变形程度、异物咬入等)以外,还有:下辊槽底圆角太小;圆角车削不光、有沟或凸棱(一般车削都是先车好下辊侧壁斜面,后用R刀车圆角,这样圆角与斜面和槽底平面不相切),造成应力集中;在弯腰大斜度孔型系统中,为保证成品孔槽口宽大于成品前孔轧件宽,上辊辊环加粗造成下辊对应位置过细,降低了下辊强度;
解决办法:1)增大圆角改善车削质量;2)将轧制线下移,增大下辊轧槽直径;3)减小上辊辊环直径(减小孔型锁口长度),这样带来的不利是减小了成品槽口宽度,可用增大槽口圆角解决。
如果成品前轧件腿外有棱(对应辊缝处),成品轧件腿外侧碾皮,应减小成品再前孔来料腿厚。
4)适当调整孔型腿的斜度,改善咬入、增大辊径,一般成品孔腿斜度最大15%,成品前孔腿斜度33%左右。
观点四:从轧辊组织上看(看不太清),还可以。
最好是没有这种从中心向外的放射状“图案”,最不好的是用手还能掰下小块,掌面抚过,往下掉渣。
观点五:轧辊制造缺陷,从图1看,心部为裂纹源!!。
热轧轧辊剥落或断裂的原因及预防方法探究
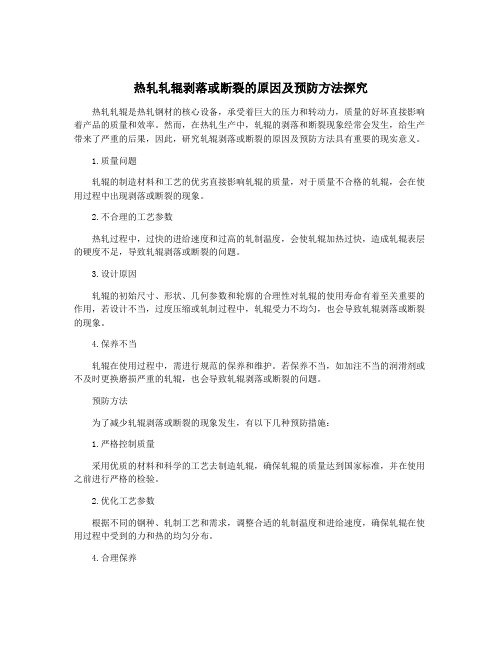
热轧轧辊剥落或断裂的原因及预防方法探究热轧轧辊是热轧钢材的核心设备,承受着巨大的压力和转动力,质量的好坏直接影响着产品的质量和效率。
然而,在热轧生产中,轧辊的剥落和断裂现象经常会发生,给生产带来了严重的后果,因此,研究轧辊剥落或断裂的原因及预防方法具有重要的现实意义。
1.质量问题轧辊的制造材料和工艺的优劣直接影响轧辊的质量,对于质量不合格的轧辊,会在使用过程中出现剥落或断裂的现象。
2.不合理的工艺参数热轧过程中,过快的进给速度和过高的轧制温度,会使轧辊加热过快,造成轧辊表层的硬度不足,导致轧辊剥落或断裂的问题。
3.设计原因轧辊的初始尺寸、形状、几何参数和轮廓的合理性对轧辊的使用寿命有着至关重要的作用,若设计不当,过度压缩或轧制过程中,轧辊受力不均匀,也会导致轧辊剥落或断裂的现象。
4.保养不当轧辊在使用过程中,需进行规范的保养和维护。
若保养不当,如加注不当的润滑剂或不及时更换磨损严重的轧辊,也会导致轧辊剥落或断裂的问题。
预防方法为了减少轧辊剥落或断裂的现象发生,有以下几种预防措施:1.严格控制质量采用优质的材料和科学的工艺去制造轧辊,确保轧辊的质量达到国家标准,并在使用之前进行严格的检验。
2.优化工艺参数根据不同的钢种、轧制工艺和需求,调整合适的轧制温度和进给速度,确保轧辊在使用过程中受到的力和热的均匀分布。
4.合理保养轧辊在使用过程中,应定期进行润滑和维护,并根据实际情况进行轧辊更换和修理,以保证轧辊使用寿命的延长。
总之,热轧轧辊的剥落或断裂问题的解决需要多方面的努力,除了以上预防措施之外,还需要提高工作人员的素质,严格执行操作规程,保证生产环境安全、清洁、整洁,以及进行适当的科技创新和技术改进,以确保轧辊质量及生产效率的提高。
轧机断辊处理预案模板设计

一、预案概述为确保轧机在发生断辊事故时能够迅速、有效地进行处置,最大限度地减少事故损失,特制定本预案。
本预案适用于公司所有轧机设备在运行过程中发生的断辊事故。
二、事故定义断辊事故是指轧机辊环在轧制过程中因各种原因导致断裂,影响正常生产的事故。
三、事故原因分析1. 辊环材质或热处理不当;2. 辊环磨损严重;3. 辊环装配不当;4. 轧制工艺参数设置不合理;5. 设备故障或维护保养不到位。
四、应急预案1. 报警与响应- 发生断辊事故时,操作人员应立即停止设备运行,并报告现场负责人。
- 现场负责人接到报告后,应立即启动应急预案,组织人员进行处置。
2. 现场处置- 确保现场安全,防止次生事故发生。
- 使用专用工具和设备,将断辊从轧机中取出。
- 清理现场,避免影响后续生产。
3. 事故调查- 对断辊原因进行调查分析,查明事故原因。
- 对相关责任人进行责任追究。
4. 恢复正常生产- 根据事故原因,对辊环进行更换或修复。
- 调整轧制工艺参数,确保生产安全。
- 对设备进行全面检查和维护。
五、预防措施1. 加强辊环材质和热处理质量监控;2. 定期检查辊环磨损情况,及时更换磨损严重的辊环;3. 严格执行辊环装配操作规程,确保装配质量;4. 合理设置轧制工艺参数,避免超负荷运行;5. 加强设备维护保养,确保设备正常运行。
六、预案演练1. 定期组织应急预案演练,提高员工应对事故的能力;2. 演练内容包括事故报警、现场处置、恢复正常生产等环节;3. 演练结束后,对演练情况进行总结,完善应急预案。
七、预案更新1. 根据事故调查结果和实际情况,及时更新应急预案;2. 定期对预案进行审查,确保预案的有效性和适用性。
八、附件1. 断辊事故调查报告模板;2. 轧机断辊事故应急预案演练方案。
九、实施与监督1. 本预案由设备管理部门负责实施和监督;2. 全体员工应熟悉并掌握本预案内容,提高应急处置能力。
通过以上预案模板的设计,旨在为轧机断辊事故的处理提供一套科学、规范的流程,确保事故发生时能够迅速、有效地进行处置,保障生产安全。
热轧轧辊剥落或断裂的原因及预防方法探究
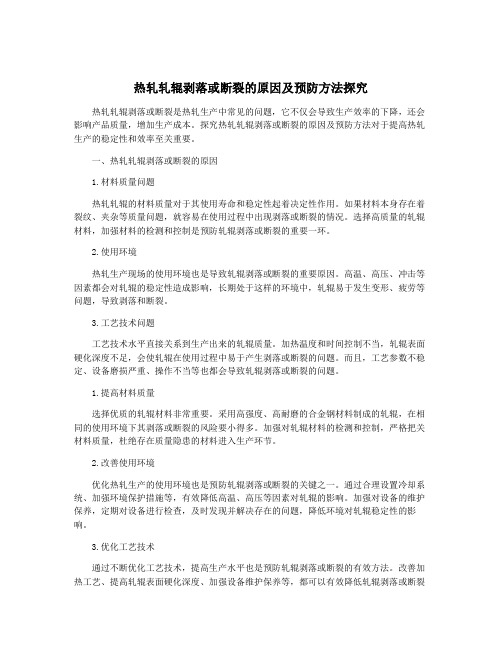
热轧轧辊剥落或断裂的原因及预防方法探究热轧轧辊剥落或断裂是热轧生产中常见的问题,它不仅会导致生产效率的下降,还会影响产品质量,增加生产成本。
探究热轧轧辊剥落或断裂的原因及预防方法对于提高热轧生产的稳定性和效率至关重要。
一、热轧轧辊剥落或断裂的原因1.材料质量问题热轧轧辊的材料质量对于其使用寿命和稳定性起着决定性作用。
如果材料本身存在着裂纹、夹杂等质量问题,就容易在使用过程中出现剥落或断裂的情况。
选择高质量的轧辊材料,加强材料的检测和控制是预防轧辊剥落或断裂的重要一环。
2.使用环境热轧生产现场的使用环境也是导致轧辊剥落或断裂的重要原因。
高温、高压、冲击等因素都会对轧辊的稳定性造成影响,长期处于这样的环境中,轧辊易于发生变形、疲劳等问题,导致剥落和断裂。
3.工艺技术问题工艺技术水平直接关系到生产出来的轧辊质量。
加热温度和时间控制不当,轧辊表面硬化深度不足,会使轧辊在使用过程中易于产生剥落或断裂的问题。
而且,工艺参数不稳定、设备磨损严重、操作不当等也都会导致轧辊剥落或断裂的问题。
1.提高材料质量选择优质的轧辊材料非常重要。
采用高强度、高耐磨的合金钢材料制成的轧辊,在相同的使用环境下其剥落或断裂的风险要小得多。
加强对轧辊材料的检测和控制,严格把关材料质量,杜绝存在质量隐患的材料进入生产环节。
2.改善使用环境优化热轧生产的使用环境也是预防轧辊剥落或断裂的关键之一。
通过合理设置冷却系统、加强环境保护措施等,有效降低高温、高压等因素对轧辊的影响。
加强对设备的维护保养,定期对设备进行检查,及时发现并解决存在的问题,降低环境对轧辊稳定性的影响。
3.优化工艺技术通过不断优化工艺技术,提高生产水平也是预防轧辊剥落或断裂的有效方法。
改善加热工艺、提高轧辊表面硬化深度、加强设备维护保养等,都可以有效降低轧辊剥落或断裂的风险。
培训操作人员,提高其技术水平,增强操作规范性,也是有效预防轧辊剥落或断裂的方法之一。
4.加强监控和管理加强对生产过程的监控和管理,及时发现并处理存在的问题也是预防轧辊剥落或断裂的关键。
轧机断带处置方案及措施

轧机断带处置方案及措施背景轧机是进行金属加工的重要设备,也是铁路、汽车、船舶等行业的核心设备之一。
轧机在正常运行中,可能会发生断带情况,如果不及时处理,不仅会损失大量原材料,还会对生产带来负面影响。
因此,制定合理的轧机断带处置方案及措施是非常必要的。
方案及措施1. 人员巡查人员巡检是轧机断带处置的重要环节,工作人员应定期对轧机进行巡检,并及时发现和解决问题。
巡检时应注意以下几点:•认真检查轧机是否有杂物混入,特别是生锈、腐蚀、磨损等情况•观察轧机传动部分的轴承、齿轮是否正常运行,以及调整和检查轧辊润滑系统•检查轧机内的冷却水管道和气密性是否良好2. 技术措施技术措施是预防和处置轧机断带的重要手段。
可以采取以下技术措施来预防轧机断带:•确保轧机的垂直度和水平度,以最大程度减少轧机不稳定因素的干扰•使用更高质量的轧辊,定期对轧辊进行加工、维护和修复。
•要求轧机工作面和轧辊表面粗糙度符合要求,在轧辊表面和33辊之间设置适当的间隙,以减少轧制压力所产生的摩擦力•对轧机进行计量和检测,及时检查和修复轴承、齿轮、安全阀和离合器等易损件。
3. 处置方案一旦轧机断带,必须及时采取措施。
处理方案应根据具体情况而定。
•先停机。
一旦发现轧机发生断带,应该立即停机以避免二次断带,发现问题之后应及时关闭主控阀门和流量阀门。
•停机后,进行必要清理。
清理过程中,应确保工人的安全。
清理中尽量不要带钢外倾,以减少受损范围•检查和评估伤害范围。
根据不同情况,分析具体损伤范围和程度•根据评估结果,对有损的设备进行维修或更换,以恢复轧机正常运转。
结论轧机断带是生产过程中常见的问题,可以通过科学的方案和措施进行预防和处置。
通过定期巡检、技术保障和及时处理等步骤可以有效降低轧机断带的发生率。
在发生轧机断带时,一定要及时停机、清理、评估和修复,以恢复生产的正常运转,减少损失。
轧机勒辊原因分析及控制措施

轧机勒辊原因分析及控制措施发表时间:2017-10-24T17:30:47.767Z 来源:《电力设备》2017年第16期作者:胥洋张跃张翼斌[导读] 摘要:轧机勒辊是冷连生产过程中频繁发生的现象,主要原因是在生产过程中轧辊的辊缝跳动过大,过大的下压力导致带钢生产时发生重叠和跑偏造成的。
在生产过程中勒辊或粘辊不大时,辊体和带钢便面会产生勒印,严重的时候也会发生断带。
(河钢承钢维护检修中心 067102)摘要:轧机勒辊是冷连生产过程中频繁发生的现象,主要原因是在生产过程中轧辊的辊缝跳动过大,过大的下压力导致带钢生产时发生重叠和跑偏造成的。
在生产过程中勒辊或粘辊不大时,辊体和带钢便面会产生勒印,严重的时候也会发生断带。
勒辊是生产冷轧带钢质量控制的重要因素,其影响了带钢的质量的同时还损伤了机械和电气设备,对轧辊进一步的损伤。
本文通过对轧机生产中勒辊现象进行了深度分析,提出合理的改善方案,有效的提高了带钢生产效率。
关键词:轧机;勒辊原因;分析;控制措施一、轧机勒辊的原因在生产过程中,轧机勒辊的原因主要有轧制钢带的原材料控制,产品的动态规格,轧制下压率不同,钢带偏离中心线和辊缝变化等所产生的。
本文以冷轧PL-TCM机组为实例进行勒辊问题详细解析,发生勒辊的主要技术点是在机组第1机架和第4、第5机架上,造成带钢表面勒印、扎漏以致缎带现象。
就此现象我展开太套和研究其原因和解决方案有以下几点: 1、压制过渡模型在市场竞争激烈的环境中,多品种生产增加了车间生产的难度,降低了生产效率,PL-TCM机组主要提供冷硬卷生产,品种多导致品种强度变化较大,在生产过程中,当冷轧钢生产品种变化时,会发生勒辊等现象,如高强度向低强度过度时在4和5机架会发生勒辊,其原因是钢种过度链接,根据统计数据分析,发生勒辊显现是两种钢种焊缝区内应力变化较大,焊缝经过每个机架是都会产生落差,导致张力变化,引起辊缝变化。
当焊缝经过机架时使得钢带失衡,偏离中心线,导致勒辊、断裂,钢带越薄越容易发生此现象。
- 1、下载文档前请自行甄别文档内容的完整性,平台不提供额外的编辑、内容补充、找答案等附加服务。
- 2、"仅部分预览"的文档,不可在线预览部分如存在完整性等问题,可反馈申请退款(可完整预览的文档不适用该条件!)。
- 3、如文档侵犯您的权益,请联系客服反馈,我们会尽快为您处理(人工客服工作时间:9:00-18:30)。
300机组500轧机断辊分析及控制措施
安钢第一轧钢厂300机组是一个年产量90余万吨的棒材机组,其主要产品有φ22、φ25、φ28、φ30、φ32规格的圆钢、螺纹钢。
由于低成本战略的提出以及节能降耗的实际要求,500轧机断辊事故在各类事故中一直占有突出位置,成为影响该机组产能发挥的主要因素。
如何控制500轧机断辊,成为当前技术人员的重点工作。
1.断辊原因分析
轧辊是实现轧制过程中金属变形的直接工具。
断辊是指在轧制过程中轧件所产生的轧制压力超过了轧辊本身所能承受的强度极限造成的轧辊断裂。
造成断辊的原因主要有以下几种:
1.1.轧辊冷却不适当;
1.2.轧辊安装不正确,造成工作时受力不均;
1.3.由于缠辊、喂错孔、多条轧制变形量过大;或轧制温度过低,使变形抗力增加,轧制力超过了轧辊强度极限;
1.4.轧辊内在质量不好,原始应力未消除或存在铸造缩孔;轧辊在某些地方强度低,造成应力集中;
1.5.轧辊刻槽较深,轧辊的工作直径太小,轧辊强度不够;
1.6.堆焊工艺缺陷。
2.原因分析
根据现场的实际情况,检查轧辊的断裂部位、断口形态及颜色是分析断辊原因的主要方法。
热轧棒材轧辊的断口部位、形态及颜色有:
2.1.当轧制温度偏低或压下量偏大使变形抗力增大时,轧辊可能在孔型的工作辊径上折断,这时的断裂口是剪应力断口。
剪应力断口为灰白色断口。
2.2.当发生误操作,轧件进入较小规格孔型,轧件进入辊环或缠辊,造成扭转力矩大于轧辊本身强度时,轧辊在辊身与辊径接触处被扭断,这时的断裂口是扭应力断口。
扭应力断口为灰白色断口。
2.3.当轧辊磨损不均匀、受不均匀冷却的交变作用,造成局部缺陷并逐渐扩大时,轧辊发生疲劳断裂。
断裂部位不一定在轧制道次的孔型内,也可能在相邻孔型内,这时的断裂口为疲劳断口。
因疲劳断辊的断口为深褐色断口。
2.4.轧机缺水断辊。
当轧机供水不足或缺水造成轧辊局部温度升高,使轧辊局部晶粒粗大,强度降低,造成断辊。
当轧机缺水,局部温度升高,使轧辊局部材质晶粒粗大,立即给水后急剧冷却,材质经淬火后晶粒变细,产生拉应力,这时断裂部位在轧机应力集中处。
因缺水断辊的断口为深兰色断口。
2.5.因轧辊堆焊质量断辊:①轧辊在多次堆焊使用过程中产生疲劳,疲劳层逐渐由轧辊外层向中心延伸,在堆焊前疲劳层剥不净再次堆焊,使用时疲劳层向内外扩展,使轧辊强度降低造成断辊。
②轧辊堆焊热处理工艺过程不合理。
轧辊堆焊前的预热过快,堆焊时表面温度较高,在堆焊后的冷却过程中,表面和中心冷却速度不一样,一般表面冷却快而中心冷却慢,因而中心对表面产生拉应力,当组织应力与拉应力相叠加超过金属的强度极限时,轧辊就产生应力裂纹,这种裂纹往往。