首件检验管理规定
首件检验管理规定
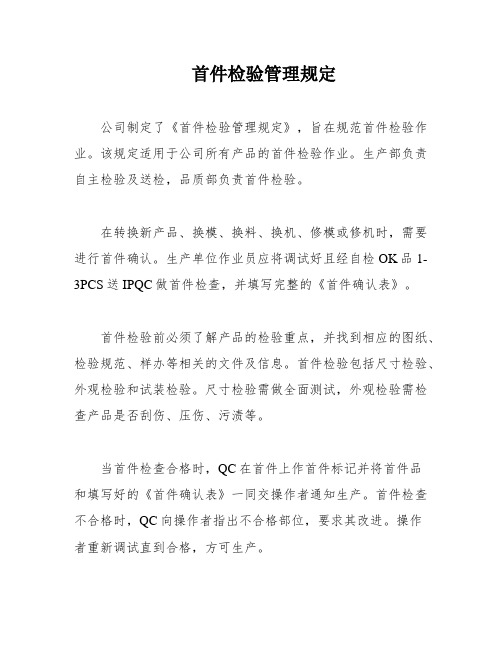
首件检验管理规定
公司制定了《首件检验管理规定》,旨在规范首件检验作业。
该规定适用于公司所有产品的首件检验作业。
生产部负责自主检验及送检,品质部负责首件检验。
在转换新产品、换模、换料、换机、修模或修机时,需要进行首件确认。
生产单位作业员应将调试好且经自检OK品1-
3PCS送IPQC做首件检查,并填写完整的《首件确认表》。
首件检验前必须了解产品的检验重点,并找到相应的图纸、检验规范、样办等相关的文件及信息。
首件检验包括尺寸检验、外观检验和试装检验。
尺寸检验需做全面测试,外观检验需检查产品是否刮伤、压伤、污渍等。
当首件检查合格时,QC在首件上作首件标记并将首件品
和填写好的《首件确认表》一同交操作者通知生产。
首件检查不合格时,QC向操作者指出不合格部位,要求其改进。
操作
者重新调试直到合格,方可生产。
经XXX填写好的《首件确认表》及首件样品应挂于机台旁。
当IPQC接到首件品时应立即确认,原则上首件确认不可超过半个小时,以免影响生产进度。
XXX根据检验结果填写《品质检测报告》交主管审核后存档。
最后,公司没有参考文件,但制定了《首件确认表》作为表单记录。
首件检验管理规定
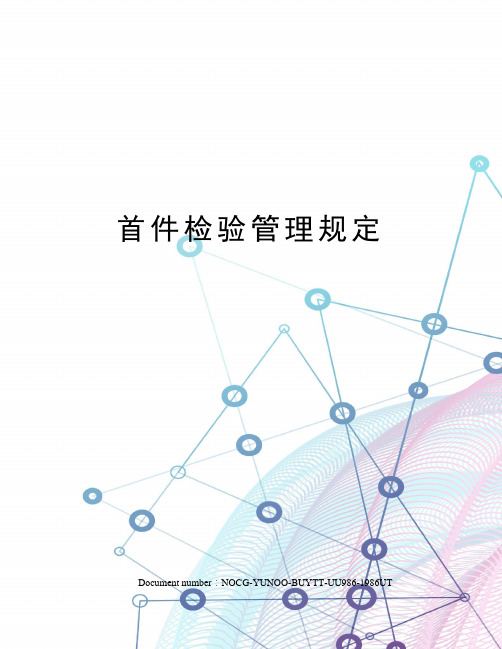
品管部人员在巡检过程中有权监督车间组长、主管对首件检验的落实情况,发现异
常时应及时予以沟通,对不听劝告者,可报备生产副总予以纠正要求,同时记录在【首
检/巡检异常记录表】中,要求车间主管签字确认。
稽核人员、生产副总、品管部经理不定时对首件检验管理规定执行状况进行查核,
状况。确认完成后,在【首件合格标签】上签字确认,并将首件检查确认的数据填写
在【首件检验记录表】上(含检查的项目数据和检查时间)。
生产车间组长、主管及品管部门相应人员应定时(2H/次)对所管辖区域内的生产进行
巡回检查,及时发现制程的生产质量负最终责任,每日应保持2次查核首件检验的执行
当首件检验不合格时,作业员应立即停止生产,同时报告组长/主管请求协助,并将
不合格样品置于不良品存放区,同时在【首件检验记录表】上注明检验结果,待异常
排除后重新进行首件检查,并记录检查结果。
每日开始生产一小时内,组长/主管应坚守岗位,不得托辞不在现场指挥生产,并且
应在1小时内对所负责之区域完成各生产工序的首件质量确认,确保首件检查的合格
每日下班前各车间组长、主管应依据生管之生产排程进行生产派工,将当日的生产完
成数量和次日的派工计划填写在【生产计划进度管理看板】上。每日上班前,准备好
当日生产的技术资料和生产所需物料。
组长、主管在每天班前早会上要说明、强调当日的生产重点及品质控制重点。
开机后,作业人员依据生产计划进度管理看板上的派工次序及数量展开作业,在进行
开机生产3件后,依照首件检验项目展开首件检验,并将检验结果记录在【首件检验
记录表】上。
依项目核对检验完成合格后,作业员须在首件产品上贴上【首件合格标签】,并填写
首件检验管理规定

1 职责项目部负责组织实施首件鉴定。
2 首件鉴定首件鉴定是按照设计图样和工艺规程的要求,对试制和批量试生产的第一件零部(组)件进行全面的工序和成品的检查,以确定生产工艺和设备(生产条件)能否保证生产出符合设计要求的产品。
以验证和鉴定过程的生产能力,为产品的生产(工艺)定型作准备。
3 首件鉴定范围3.1生产(工艺)定型前试制的零部件(组)的首件;3.2在批量生产过程中:a)设计图样的重大更改(如涉及性能、可靠性、维修性、安全性或其他重要特性的更改)后制造的首件;b)工艺规程的重大更改(如设计工艺方法、检测方法、工艺装置、设备等更改)后,对产品的符合性产生影响的首件;c)产品转厂生产的首件;d)非连续批次生产制造的收件。
3.3合同要求制定的项目4 首件鉴定的要求4.1项目部应选定对质量进度或成本有重要影响的零部(组)件,至少应包括关键件、重要件和含有关键工序的零部件。
4.2图样、工艺规程等技术文件应正确、完整、协调和现行有效。
4.3首件鉴定件应有“首件”标识(签)。
4.4首件选用的原材料、器材应符合技术标准或文件规定的要求。
4.5选用的加工、试验设备、检测设备、工艺装备和监视测量应符合规定的要求,处于正常工作状态,并处于合格有效期内。
4.6首件原始记录应完整、准确、清晰。
4.7首件操作者和检验人员必须有相应的资格。
4.8首件生产过程应按《生产过程控制程序》进行控制。
4.9首件鉴定应依据现行有效的合同、设计图样、工艺规程和检验规程等。
4.10首件鉴定合格后,方可进行后续批试制或生产。
4.11首件鉴定不合格时,在鉴定记录完整的前提下,允许用后续产品递补,重新进行首件鉴定。
5 首件鉴定的程序5.1组织首件鉴定组项目部组织进行首件鉴定,首件鉴定成员由设计、工艺、生产、检验等有关人员参加,必要时,请顾客代表参加。
5.2首件鉴定成员应确定首件鉴定检验项目。
5.3生产部按要求生产(加工)首件产品,并对首件进行标示。
首件检验管理规定

首件检验管理规定1.目的:为加强质量控制,规范检验管理,减少批量性返工、用错料,规范作业产品统一性。
2.适用范围:适用制造过程当中所有首件检验。
3.职责:3.1 生产部负责提供首件,并对生产物料、工艺、生产过程的确认并完成首件自检,作好状态标识,照实填写完整《首件确认表》并将首件样、制造工单一起交由品质部。
3.2 品管单位负责制程中的首件检验工作。
3.3 工程技术部:负责提供产品检验所需的产品图样及设计文件、技术标准等技术资料。
3.4 未经新品首件、批首件检验或首件检验不合格,而擅自生产产品,由此引起的质量事故,由直接责任者负责。
3.5 检验员、生产线负责人对首件检验的正确性负责。
3.6 对首件确认工作未完成,检验人员开始出具质量凭证,造成的质量事故,责任由检验人员承担。
4.内容:4.1 首件检验时,操作人员、检验人员必须首先做到“三对照”,即工艺路线卡、工艺规程、原材料(或半成品)要三者相符。
4.2 首件提供:制造单位依据生产进度按生管开立的《生产单》至仓库领料,并作好首件并自检,要根据工艺规程要求进行检验,须经检验合格后再提交品质人员专检。
提交时应包含《制造工单》、《首件确认表》,单个产品需包装完全(包含贴好标识标签;附件如合格证、说明书;所有配件及包装套料)。
4.3 首件检验时,应按工艺规程要求,检验人员在《首件确认表》上签字确认,且在首件产品上做出标识。
4.4 首件经检验人员确认合格后方可继续加工。
未进行首件检验的产品,检验人员有权拒绝验收。
4.5 检验人员依工程样品/检验规范/BOM/等检验依据,将判定的结果记录于《首件确认表》。
A.当确认 OK 时,由主管核准;B.当确认 NG 时,则经理核准;4.6 在首件检验中发现的不合格产品,应立即退回,重做首件,并做好记录,按“不合格品控制程序”的规定处理。
4.7 外观要求按照以下标准检验(见下页)。
类别分类归纳检验项目检验标准检验工具缺陷判定内容备注: 1.在外观类中,A 面为光源直面照射方向所在的面;B 面为A 面的2个侧面;C 面为A 面的反面.2.在包装类中,A 面为包装完成正常放置时朝上的面,B 面为A 面的2个侧面;C 面为A 面的反面.3.抽样水准按GB/T2828.1-2003一般Ⅱ次检验进行.其中CRI=0;MAJ=0.65;MIN=1.5. CRI MAJ MIN外观点污点/杂质 A 面(正面)≦0.4m ㎡或≧0.4m ㎡但不超出2点B 面(侧面)≦1.0m ㎡或≧1.0m ㎡但不超出3点C 面(底部)≦2.0m ㎡或≧2.0m ㎡但不超出4点 直尺/目视 ▲ 砂眼 A 面不可有B 和C 面≤0.5m ㎡卡尺/目视 ▲ 线 划痕 A 面 10mm*0.5mm ≦1条 B 面 15mm*0.75mm ≦2条且间隔≦5cmC 面 20mm*1.0mm ≦3条且间隔≦5cm 目视 ▲毛边 尺寸≤0.3mm卡尺/目视 ▲间隙 间隙≤0.8mm (含除包材外的任意材料间因组装产生的间隙) 卡尺/目视 ▲面 色差/色斑 颜色需与客户要求相同,色差,色斑不允许距灯表面 30cm 仰角30度观察可见卡尺/目视 ▲包装点 气泡/油污 A 面 点条状≤2m ㎡ 且≤3pcs B 面 点条状≤2m ㎡ 且≤3pcsC 面 点条状≤3m ㎡ 且≤5pcs或距油污表面45cm 处观察不可见目视 ▲线 皱折 A 面 10m ㎡ ≤1条 B 面 10m ㎡ ≤1条 C 面 30m ㎡ ≤2条或距皱折表面45cm 处观察不可见 目视 ▲切割偏斜 切割或因破损组合后皆应≤2mm目视 ▲ 面印刷不良印刷位置偏移≤2mm或距印刷表面45cm 处观察无异样 目视 ▲。
首件检验管理规定

首件检验管理规定文件管理序列号:[K8UY-K9IO69-O6M243-OL889-F88688]首件检验管理制度一、目地:为规范首件作业流程,避免因未做首件出现盲目生产造成批量性质量问题,特制订本管理规定二、范围:本公司各车间制造过程,均应进行首件检验。
三、定义:首件检验:是指产品在批量生产之前,或因生产过程中设备、人员等影响产品生产的因素有较大变化时,应对产品所用原材料和所生产出的产品重新进行全方位的检查确认;首件品指的是量产前面第一或前几件产品。
四、检验时机:1. 产品连续批量生产前;2. 设备模具更换或设备模具损坏维修好以及优化改进后;3. 工程变更产品首次生产时;4. 批量生产后中途转做其它产品,重新开始生产时;五、检验流程:1. 操作工按照生产计划单依据工艺技术标准要求进行自检;2. 操作工判定生产制作的产品首件符合要求时,填写自检数据并签名,并将首件交互检人员进行确认,互检人员确认合格后签名。
3. 由班组长对首件进行确认;3. 操作工将该首件提交QC(过程检验员)进行确认.4. QC(过程检验员)依据依据工艺卡片、图纸等技术标准进行全面检查确认,并对检验的结果作出判定。
如判定不合格,应向相应的操作工提出,并要求改善,重新制作首件,直至判定为合格为止,方可以进行量产。
5. 检验人员对首件判定不合格但属于设计问题或生产加工单位暂时无法改善的问题时.由生产车间通知部门主管、品质主管、技术中心进行裁决,必要时通知其他有关部门人员一起进行判定评审,判定合格或临时放行才能进行大批量生产。
六、 首件合格品处理方式:首件合格样品均由过程检验员放置在过程检验遏制区,并由过程检验员进行钢印标识,待本工序完工后与剩余相同规格的半成品一起流入下道。
七、 责任划分:1. 对于所有检验项目以检验指导书、工艺卡片及图纸等技术标准为准,检验必须认真对照技术标准确认,不能漏检项目或在不确认是否合格的情况下盲目签字确认。
班组零部件加工首、末件检验管理规定

1目的为了强化班组的质量管理,规范首件、末件检验,降低质量风险。
2适用范围本管理规定适用于生产线的首件检验和末件检验。
3职责3.1 技术质量室负责本规定的归口管理,对执行情况进行检查并按《班组产品质量评审考核办法》实施考核。
3.2 各相关部门应严格执行本规定。
4机加工工序首件检验要求4.1 首件检验指令的分类首件检验指令包括:首件自检、首件边做边检和首件停机送检等。
首件自检:即首件生产后仅要求操作工进行自检,合格后开始生产。
首件边做边检:即首件生产后送精测间或平台边生产边等待检测结果。
首件停机送检:即首件生产后送精测间或平台停机检测,检测合格后生产。
4.2 自检检测要求4.2.1普通加工工序:要求所有加工项目都要检测。
4.2.1.1同一把刀具钻、攻、粗镗具有相同检测内容的孔允许使用规定的检测手段检测该刀具加工的最后一个孔,其它孔目测。
4.2.1.2其它同一把刀具加工的具有相同检测内容的加工部位,首、尾加工部位必须检测,中间加工部位目测。
4.2.1.3具有不相同检测内容的加工部位,必须按4.3.1.1和4.3.1.2规定进行检测。
4.2.2精加工工序:同一把刀具钻、攻具有相同检测内容的孔允许按4.3.1.1和4.3.1.3要求检测,其它同一把刀具加工的所有内容都必须检测。
4.2.3有专用量具检测的项目必须使用相应的专用量具检测。
无专用量具检测的项目,通用量具可以检测的项目必须使用通用量具检测(高精度通用量具可以代用低精度通用量具,量程在测量范围内的游标卡尺、深度卡尺允许代用)。
无专用量具检测的项目,通用量具不可以检测的项目必须目测。
4.2.4首检工件在填写自检记录表时在“追溯号”旁标注“首”记号(自检记录表中有特殊规定的按自检记录表中的要求填写)。
末检件工件在填写自检记录表时在“追溯号”旁标注“末”记号。
4.2.5首件自检必须完成所有频次检内容。
4.3 送精测间检测要求4.3.1送检前工件必须进行自检并清理,送检时按照精测间要求进行登记,并注明“首件”、“专检”等能清楚表明检测目的的字样(允许简写)。
9首件检验管理办法

首件检验管理办法
1主题内容与适用范围
1.1本办法规定了首件检查管理办法。
1.2本办法适合于加工首件检验。
2首件检查
在加工生产过程中,具有下列情况之一,必须进首件检查。
2.1每台每班机床工作者,加工完第一个产品零件一道工序时,必须停车送检。
2.2变更工序或变换加工零件时。
2.3变换机床设备或操作工人时。
2.4改变工艺方法或更换工装时,都必须进行首件检查。
3首件检查要求
3.1首件检查必须按图纸工艺和有关技术文件,要认真进行质量检查。
在确认首件合格后,检查人员注(或打上)标记,方可进行成批生产。
3.2在加工过程中一旦发现首件检查出现问题“不合格”,出现质量问题时,检查人员必须填写首件检查质量问题报告单,可借用《工料废品通知单》但必须注明“首件”字样说明原因。
3.3不打“首件”检查,不能进行生产加工、所加工件不予检查、不予记录计件工资。
4检查与考核
4.1本办法由技术质量计量检验办归口管理与考核检查。
26。
首件检验管理规定

南缔(厦门)展示器材有限公司版 本 号:A0页 号:第 2 页/共2 页 6.1.2在首件制作过程中,生产线负责按生产现行有效的工艺标准完成首件制作。
如果需要后工序一同验证时应必须完成后道工序加工。
6.2以下情况均需作首件检查a.每日开始生产时;d.首次批量生产的新品;c.由于设备、工艺等原因停机调整,再开机时要进行首件确认;e.由于材料的规格变更后,投入生产时要进行首检确认f.换产品型号生产时;g.异常处理后,重新生产时。
6.3首件检查6.3.1操作员在每批产品批量生产前自行进行首件检验,数据并记录于“自主作业标准/检查表”。
检验合后,将首件样品交品管人员进行首件确认。
6.3.2若操作人员无能力完成首件自检的,生产部应安排技术人员或班组长代为进行首件自检。
6.3.3若操作员检验不合格须通知班长或工装管理专门人员调整机台,直至首件检验合格为止。
6.3.4检验员按照要求依有效检验规范、工艺文件、产品要求、图纸等,使用正确的检测工具,检测手段对首件进行确认。
6.2.5首件检验合格后,品检员依《标识与可追溯管理程序》进行产品标识。
6.2.6首检检测结果记录 “制程检验规范/记录表”的首件栏。
6.4首检不合格的时立即返回,重新制作首件,并按以上步骤重新确认6.5首件检查相应的责任6.5.1任何不做首件,或首件不合格即开始量产,由直接责任人承担不良损失。
6.5.2首件误检或漏检导致产品批量不良,由生产作业员及品管检验人员共同承担不良损失。
6.5.3没经检查或未检查完毕但检验员出具好合报告或合格标识的,由检验员承担不良损失。
6.6首件的使用6.6.1视生产需要,品检员可同时签发多个首件样品。
6.6.2首件样品应放置于生产作业员容易获取的位置,便以自检时使用。
6.6.3首件应自始至终保留致当班、当天、本工序或本工位生产加工完后的全过程。
6.7首件的处置6.7.1视其需要,如本批量未生产完成,可保留到第二天,以便第二天的首件比对,原则上只保留一天。
首件检验管理规定

前言为了规范车间首件检验管理,保障产品质量,实行首件检验制度,对于一些违规违章行为进行制止,使大家养成良好的工作习惯,根据公司实际状况和工作管理需求,现编制《首件检验管理规定》供内部工作与协调管理。
本流程由生产部提出并归口。
本流程由生产部负责起草。
本流程起草人:都强、郑英玉、王拯、明廷家、张建勇、吴军1、目的为了加强首/末件确认工作,杜绝因首件失误或者未进行首件检验确认后进行量产而造成质量问题的产生,特制定此规范。
2、范围适用于本公司干荷装配车间、免维护车间产品生产过程首件检验。
3、定义首件产品---每班开始生产的第一件产品;---更换操作者的第一件产品;---更换、调整设备、工装后生产的第一件产品;---采用新标准生产第一件产品;---采用新材料或待用材料生产的第一件产品。
4、职责4.1生产车间负责生产过程各工序检验,并记录;4.2质量管理部负责首检加工件监督、确认签。
5、内容5.1车间现场管理人员(班组长)负责首件检验前,根据生产任务及相关要求填写《总装车间首件记录表》的“要求”栏,并负责指导、监督操作工实施,首件完成后签字确认;5.2各岗位操作工负责确认本岗位首件是否符合相关要求,并在确认后负责填写《记录表》的“判定”栏;5.3质检员负责各工序完工后首检加工件质量确认签字,首件必须经质检员最终判定合格后方可批量生产;5.4最终判定:正常情况下首件检验必须整线确认完毕后方可生产,若热封工序后出现生产异常情况,经线长及质检员确认后热封之前的工序也可生产,在“备注”说明。
现场应适当控制生产节奏,产品不得积压过多;5.5穿壁焊工序操作工必须进行试焊,并经检验员确认合格后方可进行首件生产;5.6首样制造完成要放置在首样台上,并做好标识,《首件记录表》放置在首样台上,以供随时查阅;5.7车间每日需收集《首件记录表》上交生产部保存,保存期一年;5.9填写《首样检验单》,要字迹清晰;修改处不得划掉错误项,错误项以双横杠划掉,在边上写上正确项,并签名。
首件检验制度(质量管理)

首件检验规程
1.总则
1.1制定目的
为确保生产品质,避免出现批量生产出现的返工、报废性问题,特制定本规章。
1.2适用范围
本公司各制造单位的生产加工过程,均应进行首件检验,并依本规章执行。
1.3权责单位
(1)质检部负责本规章制定、修改、废止之起草工作。
(2)总经理负责本规章制定、修改、废止之核准。
2.首件检验规定
2.1定义
本规章所称的首件是指制造单位各工程加工生产的产品,经自我检验确认,判定符合要求后,拟进行批量生产前的第一个件产品(半成品、成品)。
2.2首件检验时机
(1)新产品第一次量产时的首件产品。
(2)每班次加工批量在10件以上(下料在30件以上)开始生产加工时。
(3)当班中途更换操作者或更换生产设备,开始生产加工时。
3.首检控制方法与程序
3.1首检由操作者当班开始生产,在调整好设备、工装、生产条件具备并处于正常生产状态时,加工的第一件自检合格品。
3.2由操作者负责通知质检人员进行首件检测,由质检人员按以下要求检验:
a) 图号与生产工序是否相符;
b) 检测首件质量是否符合产品图样和技术要求并记录。
3.3经质检人员检测判定首检合格,操作者方可成批生产加工。
3.4首检不合格,质检人员及时协助操作者查明不合格原因,调整设备或工装,并重新提交首检,直至首检合格。
3.5质检员随时巡检深入生产工序,了解情况,检查生产工人的操作方法及设备情况,随机抽查批量生产的产品是否与首件检验记录相符。
4.记录
《首件检验确认单》
5.附件
《不合格品控制程序》
编制:
审核:
批准:
日期:。
首件检验管理规定

上海年凯机电设备有限公司首件检验管理规定1目的规范首件质量管理,明确首件送检和检验职责,杜绝产品批量质量事故的发生。
2适用范围本规定适用于公司车间各道工序的首件管理,包括车床、铣床、磨床、钻床、线切割、等离子切割机、下料、焊接、以及钳工修整、打磨等。
3名词解释首件:指成批零件每道工序中的第一个零件,或在重新调整设备、校正工具、材料或操作者变更后,加工出来的第一个零件。
4首件检验管理规定4.1“首件必检”:操作者完成本工序首件、并自检合格后,必须持《日生产调度计划单》、技术图样到检查站报检。
只有检验员确认首件合格,方可继续加工其余零件。
4.2检验员应依据图纸、技术要求、标准规范等对首件零件进行检验。
4.3如果首件检验不合格,操作者应分析原因,进行返工返修,或者重新加工一个首件,直至合格。
4.4对首件检验,检验员应在《日生产调度计划单》做好首件检验记录,并对首件零件进行特殊标识:首件合格标“○”,首件不合格标“●”。
操作者应注意保护好零件上的首件标识。
4.5如果因操作者没有履行首件送检,导致批量零件不合格,操作者承担全部责任;如果检验员对首件检验出现误判,导致批量零件不合格,操作者和检验员共同承担责任。
4.6检验员在巡检过程中,如果发现操作者没有对首件进行送检,第一次予以口头警告,再次发现将处以一定的经济处罚。
4.7检验员应统筹安排检验工作,优先对首件零件进行检验。
5附则5.1质量责任界定和划分参照《质量工作奖惩条例》规定。
5.2本办法由综合管理部、质量部负责制订、解释、修订并监督实施。
5.3本办法自2016年4月6日起试行。
5.4附录《产品检验记录》附录:产品检验记录(检验员用记录表单)。
首末件检验管理规定

首末件检验管理规定首末件检验管理规定1.检验流程2.首末件检验是指对生产过程中的首件和末件产品进行严格的检验和测试,以确保产品质量符合相关标准和规范。
以下是首末件检验的流程和步骤:3. a. 制定检验计划:根据生产计划和产品要求,制定首末件检验的计划和方案。
4. b. 确定检验项目:明确需要检验的部位、尺寸、质量、外观等项目,并准备好相应的检验工具。
5. c. 进行抽样检查:按照规定的抽样方案,从生产批次中抽取首件和末件产品进行检查。
6. d. 执行检验:根据检验计划和项目,对首件和末件产品进行严格的质量检验和测试。
7. e. 记录检验结果:将检验过程中发现的问题和数据记录下来,并填写相应的检验报告。
8. f. 分析检验结果:对检验结果进行分析,评估产品质量状况,提出改进措施。
9.g. 储存检验记录:将检验报告和相关数据资料进行存档,以备后续查阅和处理。
10.责任与职责11.在首末件检验过程中,各个岗位和人员需要明确自己的责任和职责,以确保检验工作的顺利进行和质量问题的及时处理。
以下是相关岗位和人员的职责:12. a. 生产人员:负责按照生产计划进行生产,关注生产过程中的异常情况,并及时处理或上报。
13. b. 质检人员:负责制定首末件检验计划和方案,执行检验操作,分析检验结果,提出改进措施。
14. c. 技术人员:负责协助质检人员制定检验方案,提供技术支持和指导,解决检验过程中出现的技术问题。
15. d. 仓库管理人员:负责配合质检人员进行产品入库前的质量检查,确保产品数量和质量符合要求。
16. e. 上级管理人员:负责对首末件检验工作进行监督和考核,确保检验质量和效率得到保障。
17.首件检验标准18.首件检验是对生产过程中的首件产品进行严格的检查和测试,以确保后续产品的质量稳定和符合相关标准。
以下是首件检验的标准和要求:19. a. 外观完好:产品外观应无破损、划痕、变形等质量问题。
20. b. 尺寸符合:产品的尺寸应符合图纸和工艺要求,误差在允许范围内。
工程首件制度规定
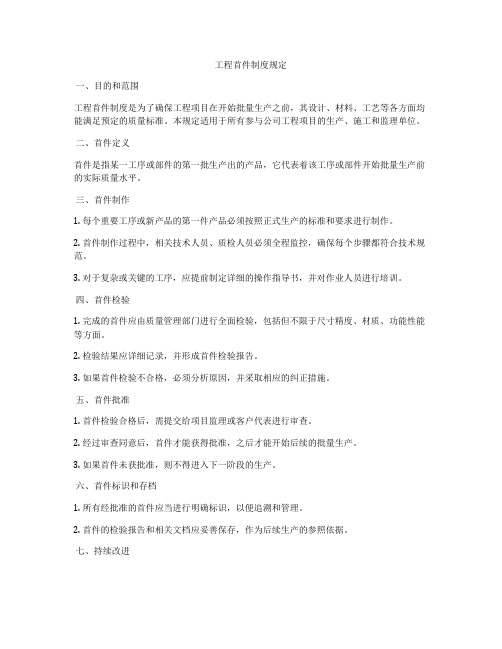
工程首件制度规定一、目的和范围工程首件制度是为了确保工程项目在开始批量生产之前,其设计、材料、工艺等各方面均能满足预定的质量标准。
本规定适用于所有参与公司工程项目的生产、施工和监理单位。
二、首件定义首件是指某一工序或部件的第一批生产出的产品,它代表着该工序或部件开始批量生产前的实际质量水平。
三、首件制作1. 每个重要工序或新产品的第一件产品必须按照正式生产的标准和要求进行制作。
2. 首件制作过程中,相关技术人员、质检人员必须全程监控,确保每个步骤都符合技术规范。
3. 对于复杂或关键的工序,应提前制定详细的操作指导书,并对作业人员进行培训。
四、首件检验1. 完成的首件应由质量管理部门进行全面检验,包括但不限于尺寸精度、材质、功能性能等方面。
2. 检验结果应详细记录,并形成首件检验报告。
3. 如果首件检验不合格,必须分析原因,并采取相应的纠正措施。
五、首件批准1. 首件检验合格后,需提交给项目监理或客户代表进行审查。
2. 经过审查同意后,首件才能获得批准,之后才能开始后续的批量生产。
3. 如果首件未获批准,则不得进入下一阶段的生产。
六、首件标识和存档1. 所有经批准的首件应当进行明确标识,以便追溯和管理。
2. 首件的检验报告和相关文档应妥善保存,作为后续生产的参照依据。
七、持续改进1. 通过首件制度的实施,可以不断收集生产过程中的问题和不足,为持续改进提供数据支持。
2. 定期回顾首件制度的执行情况,根据实际情况进行调整和完善。
八、责任分配1. 项目经理负责组织实施首件制度,并对最终的产品质量负责。
2. 质量管理部门负责首件的检验工作,并出具检验报告。
3. 生产部门负责按照规定流程和标准进行首件的制作。
4. 技术部门负责提供技术支持,确保首件的制作符合设计要求。
九、违规处理违反首件制度规定的行为,将根据情节轻重进行相应处理,严重者可暂停项目进度,直至问题得到解决。
质量首件制管理制度

质量首件制管理制度一、总则本制度旨在规范和管理质量首件制度,确保产品质量符合标准和要求,提高质量管理水平和效率。
二、适用范围本制度适用于公司所有生产制造环节,包括原材料采购、加工生产、产品检验等。
三、定义1. 质量首件:指批量生产之前,首次取样加工并检验符合要求的产品。
2. 首件制度:指在批量生产之前,必须完成质量首件的检验和批准。
四、质量首件制度流程1. 原材料采购- 采购部门负责按照质量要求选择合格的原材料供应商。
- 采购部门与供应商签订合同,并要求供应商提供质量保证书。
- 采购部门对原材料进行抽样检验,确保其质量符合要求。
2. 生产准备- 生产部门按照工艺流程准备加工设备和工序。
- 首件样品由生产部门根据工艺要求加工完成。
3. 质量检验- 质检部门对首件样品进行全面检验,包括尺寸、外观、性能等。
- 若首件样品符合产品标准和要求,进行下一步批准。
- 若首件样品不符合产品标准和要求,需及时调整工艺或材料,并重新进行首件检验。
4. 批准发布- 质检部门根据首件样品检验结果,决定是否批准该产品进行批量生产。
- 批准后,将相关信息记录并通知生产部门开始批量生产。
5. 监测追踪- 生产部门需对批量生产过程进行质量监测和追踪。
- 如发现质量问题,及时采取纠正措施,避免批量生产出现不良品。
五、责任与义务1. 采购部门负责选择合格供应商并进行抽样检验。
2. 生产部门负责按照工艺要求加工首件样品。
3. 质检部门负责对首件样品进行全面检验和批准发布。
4. 各部门需积极配合和沟通,确保首件制度顺利进行。
六、风险控制1. 严格按照质量标准和要求进行首件样品检验,确保产品质量。
2. 加强监测和追踪,及时纠正生产过程中的质量问题。
3. 开展定期内部审核,及时发现和解决质量管理中存在的问题。
七、附则本制度自发布之日起生效,如需修改或补充,应经相关部门批准并按规定程序操作。
印刷厂首检制度文件范本

印刷厂首检制度文件范本一、目的为确保产品质量,提高生产效率,防止不合格品流入下道工序,减少损失,特制定本首检制度。
本制度规定了印刷厂在生产过程中进行首检的要求、程序和责任分工。
二、适用范围本制度适用于印刷厂的所有生产工序,包括但不限于印刷、烫金、覆膜、装订等。
三、首检定义首检是指在生产过程中,对每一批(或一定数量)产品进行的第一件(批)产品的检查。
首检的目的是确保产品符合图纸、工艺文件和质量要求,防止不合格品流入下道工序。
四、首检要求1. 生产前的准备:生产前应确保生产设备、工具、材料等符合要求,操作人员经过培训且熟悉生产工艺。
2. 首件检验:生产出的第一件产品应进行全面的检查,包括外观、尺寸、印刷质量、烫金效果、覆膜质量等。
3. 首检记录:首检记录应详细记录首件的检验结果,包括检查项目、检查人员、检查时间等。
4. 首检不合格处理:首检不合格的产品应立即隔离,不得流入下道工序。
分析原因,采取纠正措施,重新首检。
5. 生产过程中变化:生产过程中,如发生设备、材料、工艺方法等变更,应重新进行首检。
五、首检程序1. 生产前准备:生产前由班组长组织,对生产设备、工具、材料等进行检查,确保符合要求。
2. 首件检验:由操作人员完成首件生产后,自行进行自检。
自检合格后,将首件送至检验员处。
3. 检验员首检:检验员对首件进行全面检查,确保产品符合质量要求。
如检验不合格,将不合格品隔离,并通知班组长及操作人员分析原因,采取纠正措施。
4. 生产过程监控:生产过程中,班组长、检验员应随时监控生产质量,发现异常立即采取措施。
六、责任分工1. 班组长:负责组织生产前的设备、工具、材料检查;督促操作人员进行自检;负责生产过程的监控。
2. 操作人员:负责按照工艺要求进行生产,完成首件自检;发现异常立即报告班组长。
3. 检验员:负责对首件进行全面检查,确保产品符合质量要求;对生产过程中的产品质量进行监控。
4. 质量管理部门:负责对首检记录进行管理,对不合格品进行处理;定期对生产过程进行稽查。
4首件检验管理规定

河北因朵科技有限公司
首件鉴定管理办法
第一条目的
为规范首件鉴定管理,保证优质、稳定的生产出满足设计要求或顾客要求和产品,和防止造成批量不合格产品,参照GJB 908A-2008《首件鉴定》,制定本办法。
第二条范围
适用于公司所有的新产品试制及批量生产的首件鉴定管理。
第三条职责
1 研发部负责组织新产品试制的首件鉴定。
2 生产部负责组织批量生产的首件鉴定,并参与新产品试制的首件鉴定。
3 质检部参加首件鉴定工作,并负责提供首件鉴定过程中所需的检验及《试验报告》。
第四条工作程序
1 首件鉴定是对试生产的第一件零组部件进行全面的过程和成品检查,以确定生产条件能否保证生产出符合设计要求的产品,并做好记录。
2 检验内容:组装情况,功能实现情况,工具满足情况;
河北因朵科技有限公司首件鉴定报告
第五条相关记录
1.《首件鉴定报告》
2.《产品性能检验报告》
——————。
- 1、下载文档前请自行甄别文档内容的完整性,平台不提供额外的编辑、内容补充、找答案等附加服务。
- 2、"仅部分预览"的文档,不可在线预览部分如存在完整性等问题,可反馈申请退款(可完整预览的文档不适用该条件!)。
- 3、如文档侵犯您的权益,请联系客服反馈,我们会尽快为您处理(人工客服工作时间:9:00-18:30)。
4.1首件检验:凡生产活动中符合首件八大时机的检查,称之为首件检验。
4.2首件检验八大时机:
4.2.1每日开机生产之首件;
4.2.2换模生产之首件;
.2.4更换作业员生产之首件;
4.2.5设备故障修复后生产之首件;
4.2.6模治具故障修复后重新生产之首件;
5.3开机后,作业人员依据生产计划进度管理看板上的派工次序及数量展开作业,在进行
开机生产3件后,依照首件检验项目展开首件检验,并将检验结果记录在【首件检验
记录表】上。
5.4依项目核对检验完成合格后,作业员须在首件产品上贴上【首件合格标签】,并填写
【首件检验记录表】,填写内容包括:生产工序、日期、产品名称、规格、检验结果
7、本办法经总经理签核生效后发行。
COPY分发部门:
董事长总经理总经办设备部生管部品管部各车间
工程技术部
3.2生产车间组长:负责首件检验的确认并在【首检合格标签】和【首件检验记录表】上签字审核。
3.3生产车间主任对本车间的生产质量负最终承担负责,并负责首检规定未落实者之教
导、纠正、提报。
3.4品管部:负责对首检管理规定的规划与稽核,并协助进行品质改善。
3.5生产副总、稽核组:负责对首检管理规定的执行状况进行监督。
检/巡检异常记录表】中,要求车间主管签字确认。
5.10稽核人员、生产副总、品管部经理不定时对首件检验管理规定执行状况进行查核,
对异常状况(含自己发现和品管部报备的)要求相关责任部门人员进行改善,并视
情况要求责任单位主管对责任人员进行提报处罚。
6、附件:
6.1【首检合格标签】
6.2【首件检验记录表】
6.3【首检/巡检异常记录表】
4.2.7质量问题对策后生产之首件;
4.2.8更换工作环境后生产之首件。
5、作业内容:
5.1每日下班前各车间组长、主管应依据生管之生产排程进行生产派工,将当日的生产完
成数量和次日的派工计划填写在【生产计划进度管理看板】上。每日上班前,准备好
当日生产的技术资料和生产所需物料。
5.2组长、主管在每天班前早会上要说明、强调当日的生产重点及品质控制重点。
5.6每日开始生产一小时内,组长/主管应坚守岗位,不得托辞不在现场指挥生产,并且
应在1小时内对所负责之区域完成各生产工序的首件质量确认,确保首件检查的合格
状况。确认完成后,在【首件合格标签】上签字确认,并将首件检查确认的数据填写
在【首件检验记录表】上(含检查的项目数据和检查时间)。
5.7生产车间组长、主管及品管部门相应人员应定时(2H/次)对所管辖区域内的生产进行
与检验时间,完成后方可进行批量生产。首件产品在当班生产最后,揭掉【首件合格标签】后随当日产品一起转入下工序。
5.5当首件检验不合格时,作业员应立即停止生产,同时报告组长/主管请求协助,并将
不合格样品置于不良品存放区,同时在【首件检验记录表】上注明检验结果,待异常
排除后重新进行首件检查,并记录检查结果。
青岛市首胜实业有限公司
制订部门
编制
文件名称
首件检验管理规定
审查
文件编号
核准
文件版次
A/0
页数
总2页
生效日期
1、目的:为提升制程生产质量,防止批量不良产生,减少重工返修等失败成本,满足客
户质量要求特制定本管理规定。
2、范围:公司内所有与产品直接产出之生产活动均属之。
3、权责:
3.1生产作业人员:负责首件的制作及检查,并填写【首检合格标签】和【首件检验记录表】。
巡回检查,及时发现制程过程中的质量问题并落实改善处理。
5.8各车间主管应对本车间的生产质量负最终责任,每日应保持2次查核首件检验的执行
状况,并落实巡回检查,发现异常状况应及时予以纠正与提报,督导部属及时改善。
5.9品管部人员在巡检过程中有权监督车间组长、主管对首件检验的落实情况,发现异
常时应及时予以沟通,对不听劝告者,可报备生产副总予以纠正要求,同时记录在【首