FLUX-KEG325落料冲孔复合模结构分析
冲孔落料复合模具工作原理
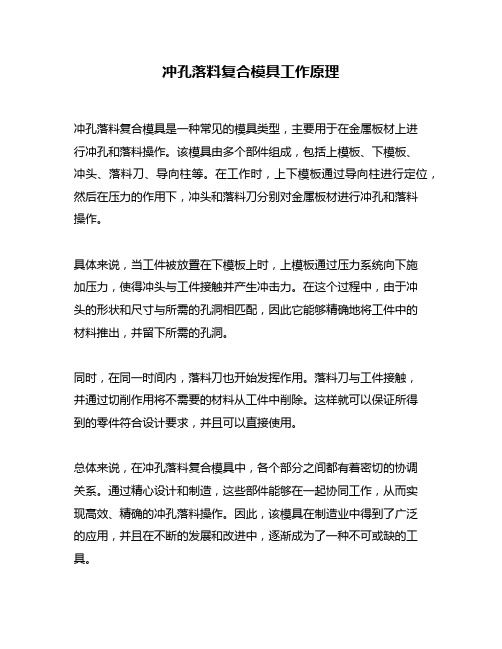
冲孔落料复合模具工作原理
冲孔落料复合模具是一种常见的模具类型,主要用于在金属板材上进
行冲孔和落料操作。
该模具由多个部件组成,包括上模板、下模板、
冲头、落料刀、导向柱等。
在工作时,上下模板通过导向柱进行定位,然后在压力的作用下,冲头和落料刀分别对金属板材进行冲孔和落料
操作。
具体来说,当工件被放置在下模板上时,上模板通过压力系统向下施
加压力,使得冲头与工件接触并产生冲击力。
在这个过程中,由于冲
头的形状和尺寸与所需的孔洞相匹配,因此它能够精确地将工件中的
材料推出,并留下所需的孔洞。
同时,在同一时间内,落料刀也开始发挥作用。
落料刀与工件接触,
并通过切削作用将不需要的材料从工件中削除。
这样就可以保证所得
到的零件符合设计要求,并且可以直接使用。
总体来说,在冲孔落料复合模具中,各个部分之间都有着密切的协调
关系。
通过精心设计和制造,这些部件能够在一起协同工作,从而实
现高效、精确的冲孔落料操作。
因此,该模具在制造业中得到了广泛
的应用,并且在不断的发展和改进中,逐渐成为了一种不可或缺的工具。
落料冲孔复合模设计实例

落料冲孔复合模设计实例在此实例中,我们需要设计一个落料冲孔复合模,用于冲压一块厚度为2mm的方形薄板。
薄板的尺寸为100mm × 100mm。
冲孔部分需要在薄板的四个角上冲孔,冲孔直径为10mm。
同时,需要在薄板的一边进行切割,切割长度为80mm。
首先,我们需要确定冲孔的位置和数量。
考虑到薄板的尺寸和形状,我们决定在薄板的四个角上进行冲孔。
冲孔直径为10mm。
为了保证冲孔的准确性和稳定性,我们需要设计一个冲孔模具,包括冲孔钢模和冲孔衬套。
冲孔钢模的尺寸为20mm × 20mm × 10mm。
冲孔衬套的尺寸与冲孔钢模相匹配。
冲孔钢模通过安装在冲床上,固定在冲床的上模座上。
冲孔衬套则通过螺纹固定在冲孔钢模上。
薄板在冲孔时会被钢模和衬套夹住,冲孔钢模通过冲击力将薄板冲孔。
接下来,我们需要设计切割部分的模具。
根据需求,切割长度为80mm。
我们选择使用切割刀具来完成切割操作。
切割刀具的尺寸为80mm × 10mm,其材料为高速钢。
切割刀具通过安装在切割模架上,固定在冲床的下模座上。
切割模架通过滑动导轨与下模座连接,可以准确地控制切割位置和长度。
为了提高生产效率,我们可以选择一次冲孔和切割多个薄板。
这就需要在冲床上设计合适的夹持装置,以固定多个薄板。
夹持装置可以同时夹持多个薄板,使冲孔和切割的连续进行,提高生产效率。
在设计完成后,我们需要进行模具制造和组装。
首先,我们制造冲孔钢模和冲孔衬套,确保其尺寸和形状的准确性。
接着,制造切割刀具和切割模架,保证其切割性能和精度。
最后,将冲孔钢模、冲孔衬套、切割刀具和切割模架组装在冲床上。
当我们需要进行冲孔和切割时,将薄板放入夹持装置中,通过冲床的运动,冲孔钢模将薄板冲孔,切割刀具将薄板切割。
这样,我们就完成了落料冲孔复合模的设计和制造。
总结起来,落料冲孔复合模的设计需要考虑冲孔和切割的几何形状、材料厚度和生产效率等因素。
在此设计实例中,我们根据需求设计了冲孔模具和切割模具,并制造和组装了这些模具。
落料冲孔复合模设计方案实例

落料冲孔复合模设计方案实例一、引言随着工业制造技术的不断发展,冲压工艺在各个领域得到广泛应用。
而在冲压过程中,落料冲孔操作是一个非常重要的环节。
为了提高生产效率和产品质量,设计和制造一套高效可靠的落料冲孔复合模非常关键。
本文将以某企业生产的金属工件为例,介绍一种落料冲孔复合模设计方案。
二、设计目标在设计落料冲孔复合模时,需实现以下目标:1. 提高生产效率:减少生产过程中的冲孔次数和时间。
2. 保证产品质量:减少冲压产生的变形和裂纹,提高工件尺寸和形状的一致性。
3. 提高模具使用寿命:减少因冲压而导致的模具磨损和损坏。
三、设计要素1. 材料选择:选用高硬度和高耐磨性的冷作工具钢作为模具材料,以确保模具的使用寿命和稳定性。
2. 设计结构:根据金属工件的形状和尺寸要求,合理设计落料冲孔复合模的结构和布局。
模具的结构应有利于材料的流动和排气,并能够减小冲压时的变形和应力集中。
3. 润滑系统:在模具设计中,考虑设置润滑系统来减少摩擦和热量的产生,以延长模具寿命。
4. 加工工艺:考虑使用先进的数控加工设备和软件,进行精确的模具制造和调试,以确保模具的准确度和稳定性。
四、具体方案基于以上设计要素,我们提出以下具体方案:1. 模具结构设计:采用分层式复合模设计,将落料和冲孔的功能集成在同一个模具内。
同时,在模具底部设计合适的排气孔和排渣槽,以确保材料的流动性和排气性。
2. 润滑系统设计:在模具的摩擦面和冲孔孔径处设置润滑油槽和喷油装置,以减少热量的产生和模具磨损。
同时,结合自动化控制系统,实现润滑油的定量供给和循环利用,提高润滑效果。
3. 加工工艺设计:采用数控加工设备进行模具的制造和加工,结合CAD和CAM软件进行模具的设计和调试。
优化加工工艺参数,确保模具的精度和稳定性。
五、验证和改进在设计完成后,进行模具的试制和测试。
通过实际生产的验证,对设计方案进行评估和改进。
调整模具的结构和加工工艺参数,优化模具的性能和稳定性,以实现更好的生产效果和质量要求。
落料冲孔翻遍复合模设计讲解

模具设计课程设计说明书班级: 05010903姓名:常剑学号: 2009301233指导老师:蒋建军康永刚时间: 2012年10月1目录第一章概论 (3)第二章工件工艺性分析及方案确定 (8)第三章排样计算等 (11)第四章冲裁力及压力中心计算 (14)第五章主要工作部分尺寸计算 (16)第六章凸模、凹模及凸凹模的结构设计及校核 (19)第七章主要零部件设计 (24)2第一章概论1.1引言日常生产、生活中所使用到的各种工具和产品,大到机床的底座、机身外壳,小到一个胚头螺丝、纽扣以及各种家用电器的外壳,无不与模具有着密切的关系。
模具的形状决定着这些产品的外形,模具的加工质量与精度也就决定着这些产品的质量。
因为各种产品的材质、外观、规格及用途的不同,模具分为了铸造模、锻造模、压铸模、冲压模等非塑胶模具,以及塑胶模具。
随着科学技术的进步和工业生产的迅速发展,冲压加工技术的应用愈来愈广泛,模具成形已成为当代工业生产的重要手段。
1.2冲压模地位及我国冲压技术1.2.1冲压模相关介绍冷冲压:是在常温下利用冲模在压力机上对材料施加压力,使其产生分离或变形,从而获得一定形状、尺寸和性能的零件的加工方法。
冲压可分为五个基本工序:冲裁、弯曲、拉深、成形和立体压制。
冲压模具:在冷冲压加工中,将材料(金属或非金属)加工成零件(或半成品)的一种特殊工艺装备,称为冷冲压模具(俗称冷冲模)。
冲压模按照工序组合分为三类:单工序模、复合模和级进模。
复合模与单工序模相比减少了冲压工艺,其结构紧凑,面积较小;冲出的制件精度高,工件表面较平直,特别是孔与制件的外形同步精度容易保证;适于冲薄料,可充分利用短料和边角余料;适合大批量生产,生产率高,所以得到广泛应用,但模具结构复杂,制造困难。
冲压模具是冲压生产必不可少的工艺装备,是技术密集型产品。
冲压件的质量、生产效率以及生产成本等,与模具设计和制造有直接关系。
模具设计与制造技术水平的高低,是衡量一个国家产品制造水平高低的重要标志之一,在很大程度上决定着产品的质量、效益和新产品的开发能力。
落料冲孔复合模研发设计实例
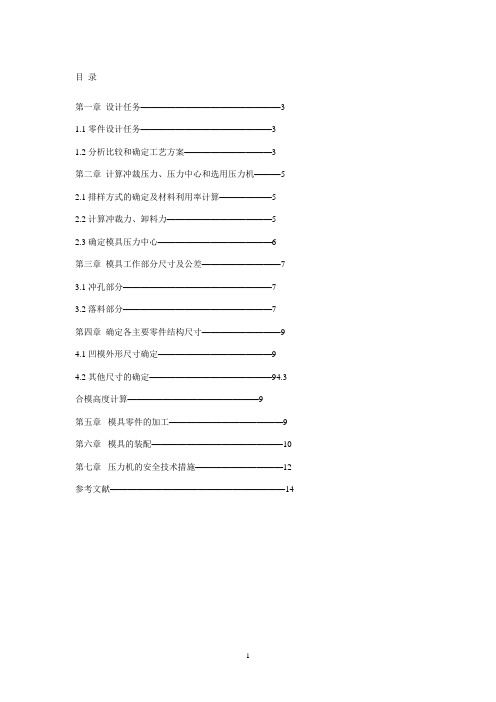
目录第一章设计任务————————————————3 1.1零件设计任务———————————————31.2分析比较和确定工艺方案——————————3第二章计算冲裁压力、压力中心和选用压力机———5 2.1排样方式的确定及材料利用率计算——————52.2计算冲裁力、卸料力————————————52.3确定模具压力中心—————————————6第三章模具工作部分尺寸及公差—————————7 3.1冲孔部分—————————————————73.2落料部分—————————————————7第四章确定各主要零件结构尺寸—————————9 4.1凹模外形尺寸确定—————————————94.2其他尺寸的确定——————————————94.3 合模高度计算———————————————9第五章模具零件的加工—————————————9 第六章模具的装配———————————————10 第七章压力机的安全技术措施——————————12 参考文献————————————————————14落料冲孔复合模设计实例(一)零件工艺性分析工件为图1所示的落料冲孔件,材料为Q235钢,材料厚度2mm ,生产批量为大批量。
工艺性分析内容如下:1.材料分析Q235为普通碳素结构钢,具有较好的冲裁成形性能。
2. 结构分析零件结构简单对称,无尖角,对冲裁加工较为有利。
零件中部有一异形孔,孔的最小尺寸为6mm ,满足冲裁最小孔径min d ≥mm 20.1=t 的要求。
另外,经计算异形孔距零件外形之间的最小孔边距为5.5mm ,满足冲裁件最小孔边距min l ≥mm 35.1=t 的要求。
所以,该零件的结构满足冲裁的要求。
3. 精度分析:零件上有4个尺寸标注了公差要求,由公差表查得其公差要求都属IT13,所以普通冲裁可以达到零件的精度要求。
对于未注公差尺寸按IT14精度等级查补。
由以上分析可知,该零件可以用普通冲裁的加工方法制得。
落料冲孔复合模具设计

"""""""""""""""""""""""""""""""""""""""""""""""" 作者: 甄瑞麟, 男, ( 上接第 !) 页) $"(’ 年生, 高工、 副教授, 主要
"
结语
该复合模经生产实践证明, 其结构合理, 动作正确
#
结语此Βιβλιοθήκη 具结构设计合理, 加工简单, 操作方便, 一次
成形, 效率成倍提高, 生产应用取得了显著的经济效 益。 参
$ &
考
文
献
王孝培6 冲压手册6 北京: 机械工业出版社, &%%&6 许发樾等6 冲模设计应用实例6 北京: 机械工业出版社, &%%&6
作者: 王绪芳, 女, $",& 年生, 实验师, 从事实验、 实训教学工作。 ( 编辑 李 静) # ( 收稿日期: &%%( 7 $& 7 $, ) #
/
工艺分析及模具设计
由于零件壁厚较薄, 属窄缘类零件。一般情况下,
・# !" ・
很好的效果, 使生产效率成倍提高。
位销定位。该模具采用后侧导柱模架。工作时, 将裁 好的条料放在下模上, 并依靠定位销定好位。上模下 行,上卸料板 ! 在橡胶 $$ 作用下压住坯料; 当凸凹模 " 进入凹模 ( 时, 先落料再继续下行时完成冲孔工序; 压力机此时恰好到达下死点。中间废料由打杆 ) 打 出。当上模返回时, 上卸料板 ! 在橡胶 $$ 弹力作用 下, 把边缘废料从凸凹模 " 上卸下, 同时下卸料板把工 件从下模中顶出。
落料冲孔复合模设计
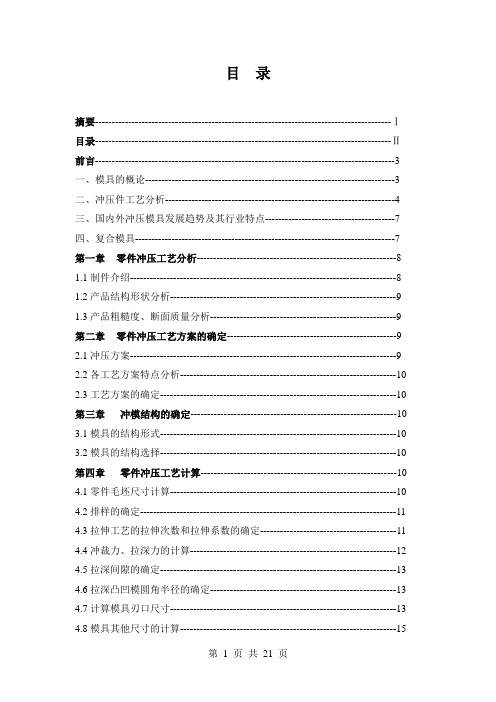
目录摘要-----------------------------------------------------------------------------------------Ⅰ目录-----------------------------------------------------------------------------------------Ⅱ前言------------------------------------------------------------------------------------------3一、模具的概论---------------------------------------------------------------------------3二、冲压件工艺分析---------------------------------------------------------------------4三、国内外冲压模具发展趋势及其行业特点---------------------------------------7四、复合模具------------------------------------------------------------------------------7 第一章零件冲压工艺分析------------------------------------------------------------8 1.1制件介绍--------------------------------------------------------------------------------8 1.2产品结构形状分析--------------------------------------------------------------------9 1.3产品粗糙度、断面质量分析--------------------------------------------------------9 第二章零件冲压工艺方案的确定---------------------------------------------------9 2.1冲压方案--------------------------------------------------------------------------------9 2.2各工艺方案特点分析-----------------------------------------------------------------10 2.3工艺方案的确定-----------------------------------------------------------------------10 第三章冲模结构的确定--------------------------------------------------------------10 3.1模具的结构形式-----------------------------------------------------------------------10 3.2模具的结构选择-----------------------------------------------------------------------10 第四章零件冲压工艺计算-----------------------------------------------------------10 4.1零件毛坯尺寸计算--------------------------------------------------------------------10 4.2排样的确定-----------------------------------------------------------------------------11 4.3拉伸工艺的拉伸次数和拉伸系数的确定-----------------------------------------11 4.4冲裁力、拉深力的计算--------------------------------------------------------------12 4.5拉深间隙的确定-----------------------------------------------------------------------13 4.6拉深凸凹模圆角半径的确定--------------------------------------------------------13 4.7计算模具刃口尺寸--------------------------------------------------------------------13 4.8模具其他尺寸的计算-----------------------------------------------------------------15第五章模架的选用--------------------------------------------------------------------15 5.1模架的类型-----------------------------------------------------------------------------15 5.2模架的类型尺寸-----------------------------------------------------------------------15 5.3压力中心的确定-----------------------------------------------------------------------16 第六章零件冲压工艺计算-----------------------------------------------------------17 6.1导向零件的选用-----------------------------------------------------------------------17 6.2模柄的选用-----------------------------------------------------------------------------17 6.3卸料装置的确定-----------------------------------------------------------------------17 6.4推件、顶件装置-----------------------------------------------------------------------17 6.5定位装置--------------------------------------------------------------------------------18 第七章零件冲压工艺卡的编制-----------------------------------------------------18 7.1落料凹模的选材、加工及热处理工艺过程--------------------------------------18 7.2凸模的选材、加工及热处理工艺过程--------------------------------------------19 第八章制件冲压工艺卡的编制-----------------------------------------------------19致谢-------------------------------------------------------------------------------------------20结束语----------------------------------------------------------------------------------------20参考文献-------------------------------------------------------------------------------------21前言板料冲压是金属加工的一种基本方法,他用以生产各种板料零件,具有生产效率高、尺寸精度好、重量轻、成本低并易于实现机械化和自动化等特点。
落料冲孔复合模说明书
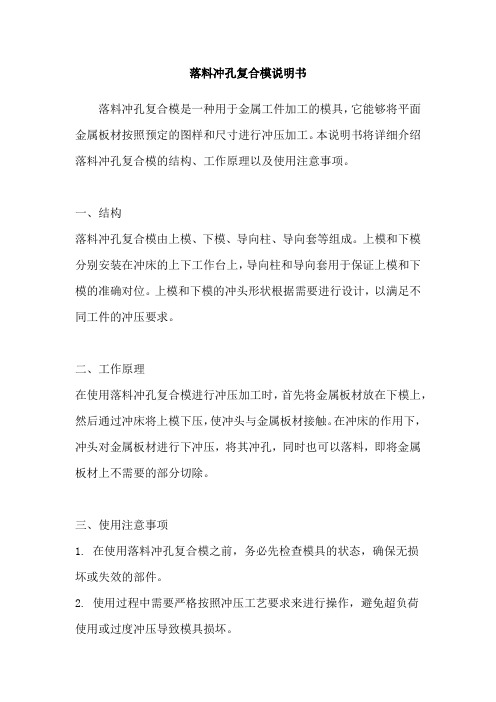
落料冲孔复合模说明书
落料冲孔复合模是一种用于金属工件加工的模具,它能够将平面金属板材按照预定的图样和尺寸进行冲压加工。
本说明书将详细介绍落料冲孔复合模的结构、工作原理以及使用注意事项。
一、结构
落料冲孔复合模由上模、下模、导向柱、导向套等组成。
上模和下模分别安装在冲床的上下工作台上,导向柱和导向套用于保证上模和下模的准确对位。
上模和下模的冲头形状根据需要进行设计,以满足不同工件的冲压要求。
二、工作原理
在使用落料冲孔复合模进行冲压加工时,首先将金属板材放在下模上,然后通过冲床将上模下压,使冲头与金属板材接触。
在冲床的作用下,冲头对金属板材进行下冲压,将其冲孔,同时也可以落料,即将金属板材上不需要的部分切除。
三、使用注意事项
1. 在使用落料冲孔复合模之前,务必先检查模具的状态,确保无损
坏或失效的部件。
2. 使用过程中需要严格按照冲压工艺要求来进行操作,避免超负荷
使用或过度冲压导致模具损坏。
3. 定期对落料冲孔复合模进行维护保养,包括清洁、润滑等,以延长模具的使用寿命。
4. 在更换冲头时,应选择合适的冲头大小和形状,以确保冲压出的工件符合要求。
5. 使用过程中要注意安全,避免手部接触冲头及其他机械部件,以免发生意外。
总之,落料冲孔复合模是一种广泛应用于金属加工行业的模具,它能够高效地完成冲压加工工艺,提高生产效率和产品质量。
只有正确使用并进行维护保养,才能确保其正常运行和延长使用寿命。
图解落料冲孔模具结构
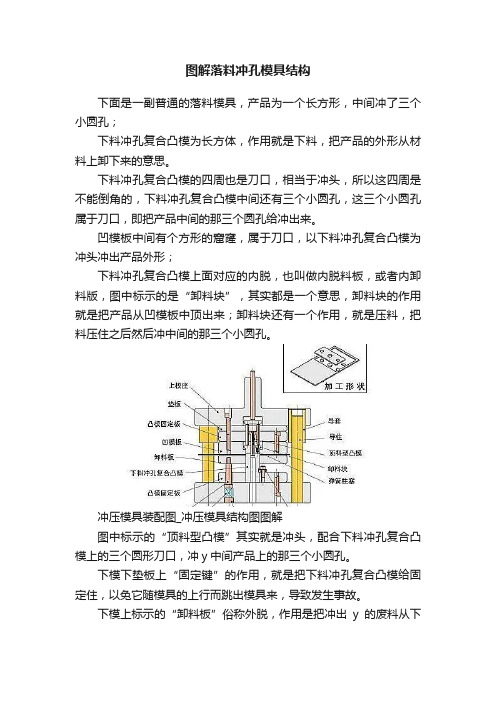
图解落料冲孔模具结构
下面是一副普通的落料模具,产品为一个长方形,中间冲了三个小圆孔;
下料冲孔复合凸模为长方体,作用就是下料,把产品的外形从材料上卸下来的意思。
下料冲孔复合凸模的四周也是刀口,相当于冲头,所以这四周是不能倒角的,下料冲孔复合凸模中间还有三个小圆孔,这三个小圆孔属于刀口,即把产品中间的那三个圆孔给冲出来。
凹模板中间有个方形的窟窿,属于刀口,以下料冲孔复合凸模为冲头冲出产品外形;
下料冲孔复合凸模上面对应的内脱,也叫做内脱料板,或者内卸料版,图中标示的是“卸料块”,其实都是一个意思,卸料块的作用就是把产品从凹模板中顶出来;卸料块还有一个作用,就是压料,把料压住之后然后冲中间的那三个小圆孔。
冲压模具装配图_冲压模具结构图图解
图中标示的“顶料型凸模”其实就是冲头,配合下料冲孔复合凸模上的三个圆形刀口,冲y中间产品上的那三个小圆孔。
下模下垫板上“固定键”的作用,就是把下料冲孔复合凸模给固定住,以免它随模具的上行而跳出模具来,导致发生事故。
下模上标示的“卸料板”俗称外脱,作用是把冲出y的废料从下
料冲孔复合凸模脱出来,以免废料卡在下料冲孔复合凸模上。
像这种冲压模具设计的时候要注意,模具下行的时候,内脱(卸料块)和外脱(卸料板)要同时压住料,也就是说产品放在模具里面(加料厚)合模的时候,模具上下模打死的情况下,外脱(卸料板)要贴死下垫板,内脱(卸料块)要贴死上垫板,这样才能保证打出来产品平面度良好,不会发生翘曲、以免光亮带不整齐的情况出现。
在架模的时候也没必要打得太死,只要能把产品完整冲出来,外脱没必要必要与下垫板贴死,留一点缝隙比较适宜。
落料冲孔复合模设计实例
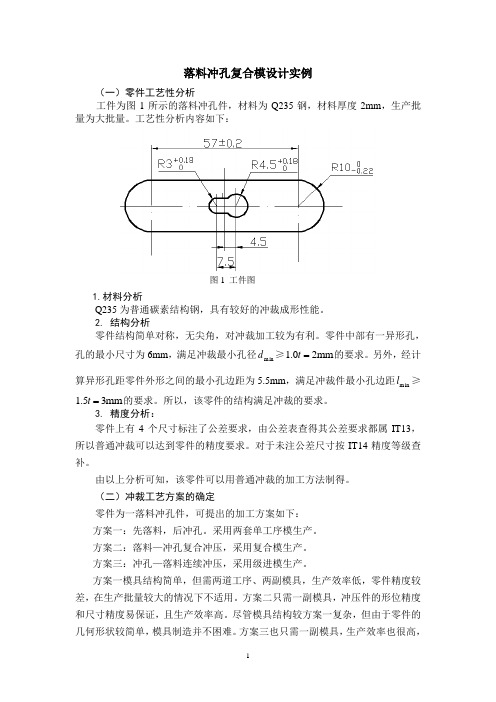
落料冲孔复合模设计实例(一)零件工艺性分析工件为图1所示的落料冲孔件,材料为Q235钢,材料厚度2mm ,生产批量为大批量。
工艺性分析内容如下:1.材料分析Q235为普通碳素结构钢,具有较好的冲裁成形性能。
2. 结构分析零件结构简单对称,无尖角,对冲裁加工较为有利。
零件中部有一异形孔,孔的最小尺寸为6mm ,满足冲裁最小孔径min d ≥mm 20.1=t 的要求。
另外,经计算异形孔距零件外形之间的最小孔边距为5.5mm ,满足冲裁件最小孔边距min l ≥mm 35.1=t 的要求。
所以,该零件的结构满足冲裁的要求。
3. 精度分析:零件上有4个尺寸标注了公差要求,由公差表查得其公差要求都属IT13,所以普通冲裁可以达到零件的精度要求。
对于未注公差尺寸按IT14精度等级查补。
由以上分析可知,该零件可以用普通冲裁的加工方法制得。
(二)冲裁工艺方案的确定零件为一落料冲孔件,可提出的加工方案如下: 方案一:先落料,后冲孔。
采用两套单工序模生产。
方案二:落料—冲孔复合冲压,采用复合模生产。
方案三:冲孔—落料连续冲压,采用级进模生产。
方案一模具结构简单,但需两道工序、两副模具,生产效率低,零件精度较差,在生产批量较大的情况下不适用。
方案二只需一副模具,冲压件的形位精度和尺寸精度易保证,且生产效率高。
尽管模具结构较方案一复杂,但由于零件的几何形状较简单,模具制造并不困难。
方案三也只需一副模具,生产效率也很高,图1 工件图但与方案二比生产的零件精度稍差。
欲保证冲压件的形位精度,需在模具上设置导正销导正,模具制造、装配较复合模略复杂。
所以,比较三个方案欲采用方案二生产。
现对复合模中凸凹模壁厚进行校核,当材料厚度为2mm 时,可查得凸凹模最小壁厚为4.9mm ,现零件上的最小孔边距为5.5mm ,所以可以采用复合模生产,即采用方案二。
(三)零件工艺计算 1.刃口尺寸计算根据零件形状特点,刃口尺寸计算采用分开制造法。
冲孔落料复合模毕业设计论文
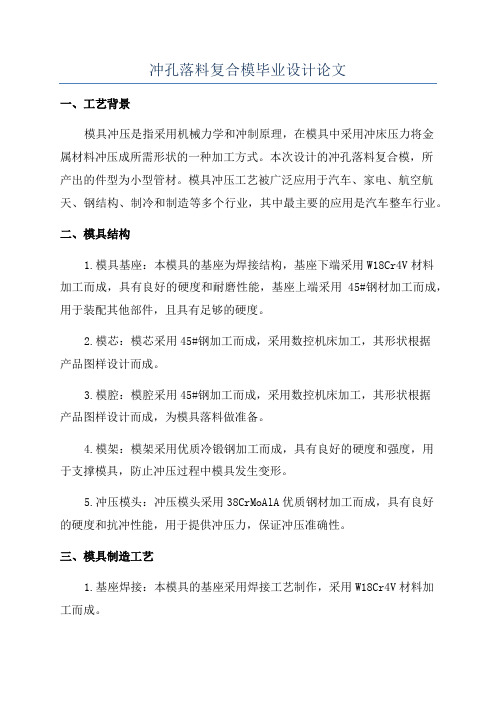
冲孔落料复合模毕业设计论文
一、工艺背景
模具冲压是指采用机械力学和冲制原理,在模具中采用冲床压力将金
属材料冲压成所需形状的一种加工方式。
本次设计的冲孔落料复合模,所
产出的件型为小型管材。
模具冲压工艺被广泛应用于汽车、家电、航空航天、钢结构、制冷和制造等多个行业,其中最主要的应用是汽车整车行业。
二、模具结构
1.模具基座:本模具的基座为焊接结构,基座下端采用W18Cr4V材料
加工而成,具有良好的硬度和耐磨性能,基座上端采用45#钢材加工而成,用于装配其他部件,且具有足够的硬度。
2.模芯:模芯采用45#钢加工而成,采用数控机床加工,其形状根据
产品图样设计而成。
3.模腔:模腔采用45#钢加工而成,采用数控机床加工,其形状根据
产品图样设计而成,为模具落料做准备。
4.模架:模架采用优质冷锻钢加工而成,具有良好的硬度和强度,用
于支撑模具,防止冲压过程中模具发生变形。
5.冲压模头:冲压模头采用38CrMoAlA优质钢材加工而成,具有良好
的硬度和抗冲性能,用于提供冲压力,保证冲压准确性。
三、模具制造工艺
1.基座焊接:本模具的基座采用焊接工艺制作,采用W18Cr4V材料加
工而成。
落料冲孔复合模的设计

落料冲孔复合模的设计
落料冲孔复合模是一种常用的模具,常用于金属成形加工中。
下面介绍落料冲孔复合模的设计步骤。
1. 确定产品设计要求:包括产品尺寸、形状、质量要求等。
2. 确定材料选择:考虑到产品的使用环境及性能要求,选择适
合的材料。
3. 制定加工工艺:根据产品的尺寸、形状进行材料切割、折弯、冲孔等加工工艺的制定。
4. 设计模具结构:根据产品的工艺要求,选择合适的模具结构,包括打孔模、落料模、定位模等。
5. 设计模具的排列和定位:根据产品尺寸和工艺要求,确定模
具的排列和定位。
6. 设计模具的冷却系统:在模具设计中,合理的冷却系统可以
提高加工效率和降低成本。
7. 完成模具设计:根据以上步骤制定的要求,完成模具设计,
注意要对设计进行合理的校核和评估。
8. 制作模具:根据设计图纸和工艺流程制作模具。
9. 检验模具:对制作好的模具进行严格的检验和试模,确保模
具符合要求。
以上是落料冲孔复合模的设计步骤。
冲孔落料复合模具设计

冲孔落料复合模具设计
一、概述
冲孔落料复合模具是一种常见的复杂成型模具。
它通过模具做成空心
的产品,通常用于金属制品和塑料制品的制作,可以实现冲孔、落坯和成
型功能。
本文的主要内容是设计一种新型的冲孔落料复合模具,它具有较
高的体积效率、较高的加工精度,能够有效减少成型周期,并有效提高生
产率和工作效率。
二、复合模具结构
1.冲孔落料复合模具由上模、开口上模、开口下模和下模4部分组成,它们分别由定子构件组成,定子构件上设有冲孔板、落料板和成型板三种
板材。
2.上模包括定子座、凸模、凹模、垫块和支架等组成部分,它们相互
配合,形成复合模具的上表面。
3.定子构件支撑着开口上模和下模,开口上模上设有冲孔孔洞,而开
口下模上设有成型孔洞,它们两者之间隔有一定的距离,能够实现冲孔落
料功能。
4.下模由定子座、支架和支撑构件等组成,它们之间由螺栓和垫圈固定,形成复合模具的下表面。
三、冲孔落料复合模具优点
1.高体积效率:冲孔落料复合模具能够实现冲孔落料一体化,不需要
多种模具,能够有效减少模具组合,提高机械组合效率,节省生产空间,
提高生产效率。
2.高加工精度:冲孔落料复合模。
冲孔落料复合模具设计

冲孔落料复合模具设计一、引言冲孔落料是一种常见的金属板材加工方式,可以通过冲孔和落料来实现对材料上的孔洞和缺口的加工。
为了提高生产效率和产品质量,设计一种冲孔落料复合模具是十分关键的。
二、模具结构设计1.上模上模采用较硬的材料,如合金钢等,以提高其耐磨性和耐腐蚀性。
上模一般设计为多个冲孔模块的集合,可以根据产品的设计要求进行选择。
冲孔孔径的大小和形状需要根据产品的要求进行设计,一般可以通过拉伸槽的装置来调整冲孔的位置和角度。
2.下模下模采用较软的材料,如塑料或橡胶等,以减少对下方的金属板材的损伤。
下模的形状需要与上模的冲孔模块相匹配,以保证冲孔的准确性和质量。
下模可以通过气动或液动装置来实现冲孔和落料的动作,可以根据产品的要求进行调整。
三、模具工作原理当上模和下模合并时,上模的冲孔模块和下模的落料形状之间会形成一个工作腔。
通过施加压力,上模以一定的速度向下冲击,使上模冲孔模块与金属板材接触,将孔洞冲出。
同时,下模的形状会顶住冲孔孔洞,使其成为落料形状。
当冲孔和落料动作完成后,上模和下模分开,取出已经冲孔和落料的金属板材。
四、模具优化设计在冲孔落料复合模具设计过程中,要考虑以下几个方面的优化设计。
1.优化上模的冲孔模块排列方式,使得冲孔过程更加均匀、稳定,并减少模具的使用次数和更换时间。
2.优化下模的形状和结构,通过减小落料形状的尺寸和加工槽口的数量,以提高产品的加工精度和成品率。
3.采用先进的材料和工艺,如表面处理和涂层等,以提高模具的耐用性和寿命。
4.考虑模具的维修和维护问题,设计合理的拆卸和安装装置,以便进行模具的更换和维修。
五、结论冲孔落料复合模具的设计是一项复杂而重要的工作。
通过优化设计模具的结构和工作原理,可以提高产品的加工效率和质量,并减少对模具的使用和更换次数。
因此,在实际设计中,需要综合考虑材料性能、工艺要求和经济效益,以达到最佳的设计效果。
筒形件落料、拉深、冲孔、复合模模具课程设计剖析

目录序言 (2)第一部分冲压成形工艺设计 (5)Ⅰ明确设计任务,收集相关资料 (5)Ⅱ冲压工艺性分析 (6)Ⅲ制定冲压工艺方案 (6)Ⅳ确定毛坯形状,尺寸和主要参数计算 (10)第二部分冲压模具设计 (15)rⅡ计算工序压力,选择压力机 (16)Ⅲ计算模具压力中心 (19)Ⅴ、弹性元件的设计 (25)Ⅵ模具零件的选用 (27)Ⅶ冲压设备的校核 (29)Ⅷ其他需要说明的问题 (30)Ⅸ模具装配 (32)设计总结 (35)参考文献 (36)序言目前我国模具工业与发达国家相比还相当落后。
主要原因是我国在模具标准化,模具制造工艺及设备等方面与工业发达国家相比差距很大。
随着工业产品质量的不断提高,模具产品生成呈现的品种、少批量、复杂、大型精密更新换代速度快。
模具设计与技术由于手工设备,依靠人工经验和常规机加工,技术向以计算机辅助设计,数控编程切屑加工,数控电加工核心的计算机辅助设计(CAD/CAM)技术转变。
模具生产制件所表现出来的高精度,高复杂程度,高生产率,高一致性和抵消耗是其它制造加工方面所不能充分展示出来,从而有好的经济效益,因此在批量生产中得到广泛应用,在现代工业生产中有十分重要的地位,是我国国防工业及民用生产中必不可少的加工方法。
随着科学技术的不断进步和工业生产的迅速发展,冲压零件日趋复杂化,冲压模具正向高效、精密、长寿命、大型化方向发展,冲模制造难度日益增大。
模具制造正由过去的劳动密集、依靠人工的手工技巧及采用传统机械加工设备的行业转变为技术密集型行业,更多的依靠各种高效、高精度的NC机床、CNC机床、电加工机床,从过去的单一的机械加工时代转变成机械加工、电加工以及其他特种加工相结合的时代。
模具制造技术,已经发展成为技术密集型的综合加工技术。
本专业以培养学生从事模具设计与制造工作能力的核心,将模具成型加工原理、设备、工艺、模具设计与制造有机结合在一起,实现理论与实际相结合,突出实用性,综合性,先进性。
落料冲孔复合模具设计.

落料冲孔复合模具设计绪论模具主要类型有:冲模,锻模,塑料模,压铸模,粉末冶金模,玻璃模,橡胶模,陶瓷模等。
除部分冲模以外的的上述各种模具都属于腔型模,因为他们一般都是依靠三维的模具形腔是材料成型。
(1)冲模:冲模是对金属板材进行冲压加工获得合格产品的工具。
冲模占模具总数的50%以上。
按工艺性质的不同,冲模可分为落料模,冲孔模,切口模,切边模,弯曲模,卷边模,拉深模,校平模,翻孔模,翻边模,缩口模,压印模,胀形模。
按组合工序不同,冲模分为单工序模,复合模,连续模。
(2)锻模:锻模是金属在热态或冷态下进行体积成型是所用模具的总称。
按锻压设备不同,锻模分为锤用锻模,螺旋压力机锻模,热模锻压力锻模,平锻机用锻模,水压机用锻模,高速锤用锻模,摆动碾压机用锻模,辊锻机用锻模,楔横轧机用锻模等。
按工艺用途不同,锻模可分为预锻模具,挤压模具,精锻模具,等温模具,超塑性模具等。
(3)塑料模:塑料模是塑料成型的工艺装备。
塑料模约占模具总数的35%,而且有继续上升的趋势。
塑料模主要包括压塑模,挤塑模,注射模,此外还有挤出成型模,泡沫塑料的发泡成型模,低发泡注射成型模,吹塑模等。
(4)压铸模:压铸模是压力铸造工艺装备,压力铸造是使液态金属在高温和高速下充填铸型,在高压下成型和结晶的一种特殊制造方法。
压铸模约占模具总数的6%。
(5)粉末冶金模:粉末冶金模用于粉末成型,按成型工艺分类粉末冶金模有:压模,精整模,复压模,热压模,粉浆浇注模,松装烧结模等。
目前,我国17000多个模具生产厂点,从业人数五十多万。
除了国有的专业模具厂外,其他所有制形式的模具厂家,包括集体企业,合资企业,独资企业和私营企业等,都得到了快速发展。
研究和发展模具技术,对于促进国民经济的发展具有特别重要的意义,模具技术已成为衡量一个国家产品制造技术的重要标志之一,随着工业生产的迅速发展,模具工业在国民经济中的地位日益提高,并在国民经济发展过程中发挥越来越大的作用。
带浮动凸模的拉伸、落料及冲孔复合模
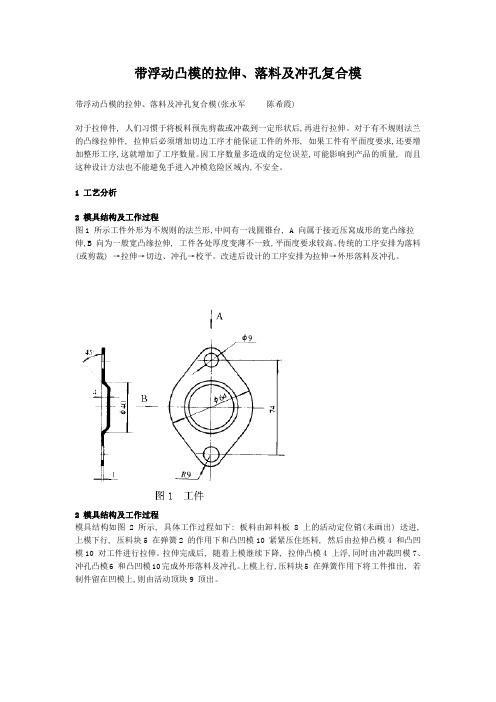
带浮动凸模的拉伸、落料及冲孔复合模带浮动凸模的拉伸、落料及冲孔复合模(张永军陈希霞)对于拉伸件, 人们习惯于将板料预先剪裁或冲裁到一定形状后,再进行拉伸。
对于有不规则法兰的凸缘拉伸件, 拉伸后必须增加切边工序才能保证工件的外形, 如果工件有平面度要求,还要增加整形工序,这就增加了工序数量。
因工序数量多造成的定位误差,可能影响到产品的质量, 而且这种设计方法也不能避免手进入冲模危险区域内,不安全。
1 工艺分析2 模具结构及工作过程图1 所示工件外形为不规则的法兰形,中间有一浅圆锥台, A 向属于接近压窝成形的宽凸缘拉伸,B 向为一般宽凸缘拉伸, 工件各处厚度变薄不一致,平面度要求较高。
传统的工序安排为落料(或剪裁) →拉伸→切边、冲孔→校平。
改进后设计的工序安排为拉伸→外形落料及冲孔。
2 模具结构及工作过程模具结构如图 2 所示, 具体工作过程如下: 板料由卸料板8 上的活动定位销(未画出) 送进, 上模下行, 压料块5 在弹簧2 的作用下和凸凹模10 紧紧压住坯料, 然后由拉伸凸模4 和凸凹模10 对工件进行拉伸。
拉伸完成后, 随着上模继续下降, 拉伸凸模4 上浮,同时由冲裁凹模7、冲孔凸模6 和凸凹模10完成外形落料及冲孔。
上模上行,压料块5 在弹簧作用下将工件推出, 若制件留在凹模上,则由活动顶块9 顶出。
3 聚氨酯橡胶块的设计在设计聚氨酯橡胶块外形尺寸时, 先初选预压缩量ε 1 = 5 % , 终压缩量ε 2 = 20 % , 然后计算橡胶高度, 再根据橡胶厂提供的有关图表和数据,计算橡胶的压缩力,最后与工件的成形力比较,如果两者不是很接近,再重选ε 1 和ε 2 ,直到两者相近为止。
严格来讲, 工件成形力和橡胶压缩力的计算都不是太精确,实际应用时,还需在计算基础上通过调整橡胶高度来调整橡胶的压缩力。
同时,聚氨酯橡胶组织细密,内部没有气泡和空隙, 可以认为其体积不可压缩, 因此,聚氨酯橡胶块的安放空间要根据体积不变的原则来计算。
- 1、下载文档前请自行甄别文档内容的完整性,平台不提供额外的编辑、内容补充、找答案等附加服务。
- 2、"仅部分预览"的文档,不可在线预览部分如存在完整性等问题,可反馈申请退款(可完整预览的文档不适用该条件!)。
- 3、如文档侵犯您的权益,请联系客服反馈,我们会尽快为您处理(人工客服工作时间:9:00-18:30)。
FLUX-KEG325落料冲孔复合模結構分析
2005/8/28作成CRD 舒爱国
P1/5
一、前言
复合模是一种多工序的冲模。
是在压力机的一次工作行程中,在模具同一部位同时完成数道分离工序的模具。
它在结构上的主要特征是有一个既是落料凸模又是冲孔凹模的凸凹模。
按照复合模工作零件的安装位置不同,分为正装式复合模和倒装式复合模两种。
在此介绍的是胜美达使用的倒装式落料冲孔复合模具(模具编号:PPEC002136)。
正装式复合模:主要是产品留在下模。
倒装式复合模:主要是产品留在上模。
二、部品图FLUX-KEG325
用于此处
图一: FLUX-KEG325图二: 形名:KEG325
图三
2005.9.17 13:44:35
CRD
'05.9.17
張国平
P2/5上冲孔凸模
推料套
图五:上凸模、推料套装配图
图六:上凹模
上冲孔凸模
推料套
上凹模
P3/5凸凹模
图八:下模写真
废料刀
气管
图九:上模写真
废料刀:为了生产安全防止带料无限延长下去,方便废料回收,按照一定的步距将废料切断。
气管:当模具上行时空气进入气管将制品吹出。
六、模具结构分析图
图十:模具结构
说明:下凸凹模 1 装在下模,上凹模(又称落料凹模) 2 和上凸模 4 装在上模。
推件装置由打杆 5 、推料板 6 和上推料套 3 组成。
冲孔废料 8 直接由冲孔凸模从下凸凹模内孔推下,无顶件装置,结构简单,操作方便。
废料由此漏下
特点:复合模具生产效率高,冲裁件的内孔与外缘的相对位置精度高,板料的定位精度要求比级进模低,冲模的轮廓尺寸较小。
但复合模具结构复杂,制造精度要求高,成本高。
复合模主要用于生产批量大、精度要求高的冲裁件。
以上。