烧结剂和喷吹剂
硬质合金的烧结气氛及其控制

硬质合金的烧结气氛及其控制The Sintering Atmosphere of Hard Alloy and Its Control目前,硬质合金的烧结已在金属切削、航空航天、机械制造、医疗器械等诸多行业中得到广泛应用,它能替代传统钢制件,具有较高的热韧性和耐磨性。
为了保证硬质合金烧结工艺在精度、性能、耐久性等方面都满足要求,烧结气氛控制显得尤为重要。
At present, the sintering of hard alloy has been widely used in many industries such as metal cutting, aerospace, mechanical manufacturing and medical instrument industry. It can replace traditional steel parts and has high thermal toughness and wear resistance. In order to ensure that the sintering process of hard alloy meets the requirements in precision, performance and durability, the control of sintering atmosphere is particularly important.硬质合金的烧结气氛控制一般分为4类:真空烧结、气氛烧结、助烧剂烧结和半气体烧结。
真空烧结指的是在真空状态下进行烧结,气氛烧结指的是空气、氮气或氩气等常压气体为主要气氛烧结,助烧剂烧结指的是添加助烧剂,以改善烧结气氛烧结,而半气体烧结则指的是混合真空和气体烧结。
The control of sintering atmosphere of hard alloy is generally divided into four categories: vacuum sintering, atmosphere sintering, sintering aid sintering and semi-gas sintering. Vacuum sintering refers to sintering in vacuum state,atmosphere sintering refers to sintering under atmosphere of air, nitrogen or argon and other atmospheric pressure gases as the main atmosphere, sintering aid sintering refers to the additionof sintering aids to improve the sintering atmosphere, and semi-gas sintering refers to the mixed vacuum and gas sintering.根据成型原理的不同,硬质合金的烧结气氛可以分为固溶处理型、凝固型和渗透型。
高炉冶炼技术操作规程
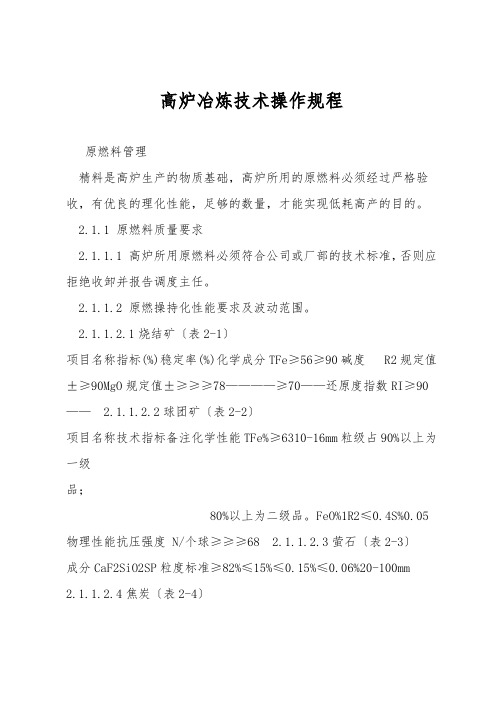
高炉冶炼技术操作规程原燃料管理精料是高炉生产的物质基础,高炉所用的原燃料必须经过严格验收,有优良的理化性能,足够的数量,才能实现低耗高产的目的。
2.1.1 原燃料质量要求2.1.1.1 高炉所用原燃料必须符合公司或厂部的技术标准,否则应拒绝收卸并报告调度主任。
2.1.1.2 原燃操持化性能要求及波动范围。
2.1.1.2.1烧结矿〔表2-1〕项目名称指标(%)稳定率(%)化学成分TFe≥56≥90碱度 R2规定值±≥90MgO规定值±≥≥≥78————≥70——还原度指数RI≥90—— 2.1.1.2.2球团矿〔表2-2〕项目名称技术指标备注化学性能TFe%≥6310-16mm粒级占90%以上为一级品;80%以上为二级品。
FeO%1R2≤0.4S%0.05物理性能抗压强度 N/个球≥≥≥68 2.1.1.2.3萤石〔表2-3〕成分CaF2SiO2SP粒度标准≥82%≤15%≤0.15%≤0.06%20-100mm 2.1.1.2.4焦炭〔表2-4〕指标种类指标C固≥85%Ag≤12.5%Vg≤1.9%S≤0.7%H2O≤8%反应性CRI≤25%反应后强度CSR≥65%M10≤8%M25≥92%M40≥80%粒度40—80mm指标种类炼铁球磨用白煤炼铁球磨用烟煤Ag≤12%≤10%Vg≤12%25-35%S≤0.6%〔阳泉≤0.8%〕≤0.6%H2O≤9%≤9%可磨性≥70%≥70%粒度0-10㎜0-25㎜2.1.1.2.5煤〔表2-5〕原燃料料仓管理2.1.2.1 高炉用各种原燃料必须按品种卸入规定的料仓,严禁混料,料仓的配用计划由高炉车间提出经生产调度室同意后执行。
2.1.2.2 同一种原料应均衡地卸入所占料仓,上料时必须循环取料,避免局部烧结仓存时间过长,存放时间过长粉末增多的烧结矿应按比例搭配间断入炉。
2.1.2.3 成分无大变化可以清仓,取样时间、卸料时间、数量、仓号,必须通知高炉工长。
氧化铝陶瓷低温烧结助剂研究概述

氧化铝陶瓷低温烧结助剂研究概述氧化铝陶瓷是一种重要的结构陶瓷材料,具有优异的耐磨性、耐腐蚀性、抗高温性等特点,在工业生产和科研领域有着广泛的应用。
然而,氧化铝陶瓷的低温烧结难度较大,需要添加一定的助剂才能够实现良好的烧结效果。
本文将对氧化铝陶瓷低温烧结助剂的研究进展进行概述。
1. 氧化铝陶瓷低温烧结助剂的分类氧化铝陶瓷低温烧结助剂主要分为有机助剂和无机助剂两类。
有机助剂包括聚乙烯醇(PVA)、聚丙烯酸(PAA)、聚乙烯酮(PVP)等;无机助剂包括碳酸钙、硼酸、氧化钙、氢氧化钠等。
2. 有机助剂在氧化铝陶瓷低温烧结中的应用有机助剂可以在氧化铝陶瓷低温烧结过程中起到增强材料粘结力、促进颗粒成核、调节材料微观结构等作用。
其中,PVA 是一种常用的有机助剂,可以有效地提高氧化铝陶瓷的烧结密度和力学性能。
PAA则可以在低温下促进氧化铝颗粒的成核和晶粒生长,提高材料的致密性和硬度。
PVP则可以增加氧化铝陶瓷的塑性变形能力,降低其断裂韧性。
3. 无机助剂在氧化铝陶瓷低温烧结中的应用无机助剂可以在氧化铝陶瓷低温烧结过程中起到促进颗粒成核、调节晶体生长速率、防止晶体生长过快等作用。
其中,碳酸钙可以促进氧化铝陶瓷颗粒的成核和晶粒生长,提高材料的致密性和硬度;硼酸则可以防止氧化铝陶瓷晶体生长过快而导致材料开裂;氢氧化钠则可以调节氧化铝陶瓷晶体生长速率,提高材料的致密性和强度。
4. 氧化铝陶瓷低温烧结助剂的优化为了进一步提高氧化铝陶瓷低温烧结助剂的效果,需要对其进行优化。
目前,主要采用的方法包括改变助剂添加量、改变助剂种类、采用复合助剂等。
其中,复合助剂是一种较为有效的优化方法,可以充分发挥不同助剂的作用,提高氧化铝陶瓷的致密性和力学性能。
综上所述,氧化铝陶瓷低温烧结助剂是实现氧化铝陶瓷低温烧结的关键因素之一,其种类和添加量对于材料的致密性和力学性能具有重要影响。
未来,我们还需要进一步深入研究不同助剂的作用机制,以及如何优化氧化铝陶瓷低温烧结助剂的配方,为其在工业生产和科学研究中的应用提供更为可靠的技术支持。
SYP冶金助剂助钢铁业节能减排

SYP冶金助剂助钢铁业节能减排一个严峻的现实钢铁,是国民经济建设的重要原材料。
钢铁行业又是能源消耗和污染物排放的“大户”。
中国已成为世界第一产钢大国。
但是,我国钢铁行业能耗占全国总能耗的14.71%,工业粉尘排放量占工业排放总量的15.18%。
总体来看,我国钢铁工业能耗与国际先进水平的差距为10%-15%。
对于工艺装备落后的中小企业,300立方米以下小高炉工序能耗比国内先进水平高200公斤标煤/吨左右,20吨以下小转炉工序能耗比国内先进水平高90公斤标煤/吨左右,总能耗与国际先进水平差距在50%左右,污染物排放更为严重。
能源消耗和对环境的污染,严重制约着钢铁工业的发展。
国家宏观调控正在逐步加强,以经济、法律、行政手段把节能减排、保护生态环境作为刚性的硬任务和约束性指标。
严峻的现实使人们认识到,节能减排是促进经济社会科学、和谐发展的大事。
钢铁行业节能减排成为重中之重。
为此,中国钢铁工业协会提出,钢铁行业节能减排工作的重点是推广节能减排先进工艺和技术,促进企业重视和强化节能减排工作。
要是能有一项新技术或新产品,既能降低能耗,又能提高产量,还能净化环境,也就是人们所说的,既让马儿跑得快,又让马儿少吃草,那该多好啊。
这正是钢铁企业追寻的目标。
一串闪光的数据正当钢铁业人士苦苦寻找节能减排的先进工艺技术的时候,一种既能使钢铁生产工序节能减排,又能提高产量,改善品质的助剂已经在许多钢铁企业悄然应用。
这就是廊坊腾达助剂有限公司研制生产的“SYP冶金助剂”。
廊坊腾达助剂有限公司是国家科技部研发与生产“SYP冶金助剂”的依托单位,是国家高新技术企业。
几年来,他们先后研发出“SYP 烧结增效剂”、“SYP喷煤增效剂”、“SYP球团粘结剂”、“SYP 焦炭钝化剂”等系列产品,被评为国家高新技术产品,河北省优质产品,获国家创新基金支持,获第十七届全国发明展览会金奖和最佳节能技术奖。
“SYP冶金助剂”有着怎样的效果呢?SYP烧结增效剂:唐钢在烧结混合料中配加0.03%的SYP烧结增效剂后,烧结矿增产5.84%,固体燃耗降低2.94千克/吨,转鼓指数提高 ,铁酸钙含量平均提高10%,年创经济效益9800多万元,SO2排放量每年减少309.6吨,氮氧化合物的排放浓度也由原来的480ppm 降低到434ppm 。
烧结剂对耐火材料的影响

水玻璃结合剂(water glass binder)一种无机材料的胶结剂。
又称泡花碱。
在工业上呗广泛用作无机材料胶结剂,在耐火材料工业作为结合剂用相当广泛,也广泛用于造纸及纺织等工业。
添加剂对耐火材料烧结的影响在固相烧结时,少量的添加剂(烧结助剂)可与主晶相形成固溶体促进缺陷增加;在液相烧结时,添加剂能够改变液相的性质(如粘度、组成等),因而能起促进烧结的作用。
添加剂的作用可能在于以下几个方面。
形成固溶体。
当添加物与烧结物形成固溶体时,可以增加晶格缺陷,活化晶格,从而促进烧结。
一般来说,他们之间形成有限置换固溶体更有助于促进烧结。
添加剂离子的电价、半径与主晶格离子的电价、半径相差越大,晶格畸变程序也越大,促进烧结的作用也越明显。
如Al2O3烧结时,加入3%的Cr2O3形成连续固溶体可在1860℃烧结,而加入1%~2%只需在1600℃左右就能致密化。
阻止晶型转变。
有些氧化物在烧结时发生晶型转变并伴有较大的体积效应,这就难以实现烧结致密化,并容易引起坯体开裂。
这时若能选用适宜的添加剂加以抑制,即可促进烧结。
ZrO2烧结时添加一定量的CaO、MgO就属这一机理。
约在1200℃,m- ZrO2转变为t- ZrO2,并伴有约10%的体积收缩,使制品稳定性变坏。
引入电价比Zr4+低的Ca2+(或Mg2+),可形成稳定的立方萤石结构的固溶体。
这样,既防止了制品的开裂,又增加了晶体中缺陷浓度,使烧结加快。
抑制晶粒长大。
烧结后期晶粒长大,对促进烧结致密化有重要作用。
但若二次再结晶或间断性晶粒长大过快,会使晶粒变粗、晶界变宽而出现反致密化现象并影响制品的显微结构。
这时,可通过加入能抑制晶粒异常长大的添加剂来促进烧结。
在烧结透明Al2O3制品时,为抑制二次再结晶,消除晶界上的气孔,一般加入MgO或MgF2,高温下形成镁铝尖晶石包裹在Al2O3晶粒表面,抑制了晶界迁移的速度,并促使气孔的排出,对促进坯体的烧结具有显著的作用。
喷吹煤

目录索引喷吹燃料简介:1、喷吹燃料历史2、中国高炉喷吹燃料特点3、喷吹煤粉种类4、喷吹无烟煤与喷吹烟煤区别喷吹煤特点喷吹煤评价指标无烟煤价格喷吹煤价格参考资料高炉喷吹燃料简介高炉喷吹燃料:气体、液体或固体燃料通过专门的设备从风口喷入高炉,以取代高炉炉料中部分焦炭的一种高炉强化冶炼技术。
它可改善高炉操作,提高生铁产量,降低生铁成本。
高炉炼铁是以冶金焦作为燃料和还原剂的,喷吹燃料在风口区的高温下转化为CO和H2,可以代替风口燃烧的部分焦炭,一般可取代20%~30%,高的可达50。
喷吹燃料已成为当代高炉降低焦比的主要措施。
喷吹燃料还可以促进高炉采用高风温和富氧鼓风,这几项技术相结合,已成为强化高炉冶炼的重要途径。
高炉喷吹燃料历史:早在19世纪,欧洲、美国就有人提出了高炉喷吹燃料的设想,有的还申报了专利。
但是直到20世纪中叶才在工业上逐步实现。
1947年法国纳维一梅松(Na,yes.Maisons)工厂试验向高炉喷吹燃料油,1948年前苏联捷尔仁斯基工厂向高炉喷吹煤粉,1957年前苏联彼得洛夫斯基工厂在高炉上喷吹天然气。
自此以后,世界各国根据自己的资源条件和世界市场上燃料的价格喷吹不同的燃料。
例如前苏联,俄罗斯及美国天然气资源丰富则大量喷吹天然气,60年代世界市场油价便宜,世界各国在高炉上大量喷吹重油。
70年代末,因油价高涨,大部分高炉停止喷油,并逐步转为喷吹煤粉。
1990年日本、德国有2/3的高炉在喷吹煤粉,喷吹量一般为50~80kg/t铁,到1998年有的已超过200kg/t铁。
中国从50年代末开始在高炉上喷油,60年代初大部分高炉已实现喷油。
1964年首都钢铁公司和鞍山钢铁公司在高炉上喷吹无烟煤成功,1966年首钢座高炉全年平均喷煤量达159kg/t。
重庆钢铁厂在60年代喷吹过天然气,有的厂还喷吹过焦油、沥青。
60年代末,逐步转为喷煤粉。
中国高炉喷吹燃料的特点是:采用喷吹燃料的高炉多,重点企业中90%以上的高炉已喷吹煤粉,喷吹煤种有无烟煤、烟煤和二者的混合煤,喷吹量一般在80~100kg/t,宝山钢铁公司等的大型高炉的喷吹量已达到200kg/t以上。
烧结助剂

几种常用的低温烧结复合助剂在实际生产中,单一助剂往往不能同时满足其烧结和机电性能的要求,一般情况下单一助剂在降低烧结温度的同时会导致陶瓷性能的降低,因此,采用多种不同助剂组成的复合添加剂要比单独使用其中一种助剂更为常见。
在选配复合助剂时一般要遵循以下原则:(1) 不同助剂之间应具有协同促进烧结的作用,多种助剂复合添加与单一助剂相比可以更好的降低烧成温度;(2) 不同助剂之间最好不发生反应,否则会减弱或抵消其促烧作用;(3) 不同助剂之间可以起到相互补充的作用,一种助烧剂在促进烧结的同时对材料性能产生的不利影响可以由另一种助剂进行弥补,故一般根据烧结助剂的作用往往选择将可以降低烧结温度的助剂与可以改善烧结体显微组织结构和烧结性能的其他助剂搭配使用。
在具体选用不同助剂组成复合助剂的时候,一般形成低共熔体系的添加剂主要以玻璃形成体如SiO2为主,辅以玻璃中间体Al2O3、BeO、ZnO 等和玻璃调整体MgO、Li2O、BaO、CaO、Sr2O 等形成MgO-Al2O3-SiO2( MAS) ,CaO-Al2O3-SiO2( CAS) ,Li2O-Al2O3-SiO2( LAS) 等系统。
对于高纯氧化铝陶瓷,通常都选用MgO 作为基本的烧结助剂进行添加,但是MgO 的高温挥发性会使陶瓷表面产生大的晶粒。
由于稀土元素添加剂可以在添加量极低的情况下很大程度地减小氧化铝的晶界长大速率,现在多采用MgO 和La2O3或Y2O3等复合的形式加入到氧化铝陶瓷中。
目前,比较常用的复合助剂主要有CaO-MgO-SiO2体系、MnO2-TiO2-MgO 体系以及CuO-SiO2体系。
1 CaO-MgO-SiO2体系采用这一体系的烧结助剂,可在1500 ~ 1550 ℃左右合成氧化铝基陶瓷。
薄占满等的研究表明体系中MgO 对氧化铝陶瓷的细晶显微结构起了重要作用,MgO 在烧结中能维持CaO/SiO2比,即维持烧结系统中的液相量,并有尖晶石、镁铝硅酸盐、铝硅酸盐、铝酸盐等多种第二相晶体生成,对晶界移动具有钉扎作用,它们有效地抑制了晶粒的生长; 同时引入了少量的La2O3、Sm2O3等稀土氧化物,使Al2O3陶瓷的烧结温度下降大约30 ℃,其表面显微结构也有所改善,这主要是由于La2O3和Sm2O3为网络变性离子,能够分解熔体网络而促进烧结。
烧结料面喷吹蒸汽技术的应用效果

HUANG Jianping
( Fujian Tsing Tuo Group Co.ꎬ Ltd.ꎬ ferronickel factoryꎬ Ningde 355006ꎬ China)
Abstract In order to improve sinter qualityꎬ reduce sintering consumption and alleviate environmental pressureꎬ the
了提高烧结矿产质量、降低成本及污染物排放的良好效果ꎬ满足了高炉冶炼需求ꎮ
关键词 水蒸汽 喷吹 烧结料面 热交换
中图分类号 TF6243 文献标识码 B
文章编号 1001 ̄1943(2019)06 ̄0022 ̄04
APPLICATION EFFECT OF STEAM SPRAYING
取得了改善烧结矿质量和还原性的效果
理红土镍矿ꎬ这样原料含水高ꎬ烧损大ꎬ
或环冷机废气进行返回料面的
足高炉冶炼需求ꎮ 镍烧结矿作为生产镍铁的主要
热风烧结本质上也属于喷吹技术ꎬ有显著的节能和
原料ꎬ提高其产品质量对镍铁生产起到重要作用ꎮ
减排效果ꎻ日本 JFE 通过喷吹液化气技术取得了改
into the sinter bed. Production practice shows that that the sinter yield increases by 2% ꎬ the drum index increases by
1. 39%~2. 19% ꎬ solid fuel consumption decreases by 4. 58~5. 05 kg / tꎬ and the NO x content of sintering waste gas de ̄
烧结料面喷吹蒸汽在烧结机的研究与应用

烧结料面喷吹蒸汽在烧结机的研究与应用摘要:本文研究了喷吹位置、喷吹量和喷吹强度三个工艺参数对烧结矿质量和燃料消耗的影响,分析了蒸汽喷吹对烧结机节能减排的影响。
试验表明,喷吹位置设置在距离点火位置8~20m、喷吹量为4~6.5t/h、控制蒸汽喷吹强度在0.2~0.6kg/(m2·min)时,可节约焦粉量0.9~1.8kg/t、提高产量20~80t/h、CO排放量降低20%~25%、二噁英排放量降低35%~40%。
关键词:烧结;蒸汽喷吹;节能;减排前言烧结工序是钢铁工业污染物排放和能源消耗大户,烧结SO、NOx、和二噁英2排放分别占钢铁工业污染物的65%、50%和70%以上,能耗约占10%。
此外,烧结过程中CO排放量远高于其他几种污染物排放,传统烟气处理工艺难以脱除CO。
从2018年1月1日开始,我国开始对排放CO污染物进行征税,烧结烟气中CO的治理将越来越受重视。
通过采用烧结机料面喷吹蒸汽技术,可显著减低CO[1,2]和二噁英的排放量。
1蒸汽喷吹主要工艺参数(1)喷吹位置在蒸汽喷吹烧结生产时,其喷吹位置对于强化效果有直接影响。
适宜蒸汽喷吹的范围为点火后一段时间到废气升温点前。
这是因为喷吹位置过于靠前,此时料层刚被点火,形成高温带较薄,喷吹蒸汽容易使水蒸气反应的吸热量占高温带热量的权重过大,导致有“灭火”的可能。
喷吹位置过于靠后,烧结料层大多已烧结完毕转化成烧结矿,蒸汽不再参与高温反应,难以起到原设计强化烧结的作用。
考虑到前10%位置为烧结点火位置,点火后5min也占据烧结机10%~15%的位置。
因此,确定较佳喷吹位置为烧结机长度方向30%,到废气升温点前,烧结机料面喷吹蒸汽位置选取的是距点火位置8~20m。
(2)喷吹量在确定好合适喷吹位置参数的基础上,进一步摸索较优的蒸汽喷吹量参数范围,对于强化该技术效果极其重要。
蒸汽喷吹量过少,无法达到技术强化的效果;蒸汽喷吹量过多,则多余的水汽容易在料层内吸热并加重过湿层,反而对生产能耗和污染物排放量等指标造成负面影响。
炼铁烧结常用数据【自己总结】

炼铁烧结常用数据【自己总结】钢铁冶炼常用数据烧结1、烧结料层中固定碳含量低,按重量计算只占总量的3%~5%,而且分布的很分散。
2、一般烧结过程中可除去90%以上的S,加入少量的氯化物CaCl2,可生成易挥发性的A S Cl3、Pb Cl2、Zn Cl2,易除去60%的As,90%的Pb和60%的Zn。
K2O,Na2O、和P2 O5在烧结过程中较难去掉。
3、烧结点火温度取决于烧结物的融化温度,常控制在1250±50℃,球团在1200~1300℃培烧成。
4、我国优质烧结矿要求:转鼓指数T≥70.00%、抗磨指数A≤5%,筛分指数C≤6.0%,球团筛分指数C≤5.0%,表明烧结矿的粉末含量多少,C 越小越好。
转鼓指数T = m1/m o×100%抗磨指数A = m o-(m1- m2)/ m o×100%筛分指数C = 100-A/100×100% (在高炉槽下取矿) m o—入鼓试样质量kg, m1—转鼓后〉6.3mm粒级部分的质量kg, m2—转鼓后6.3—0.5mm粒级部分的质量kg, C —筛分指数,A〉5mm粒的量kg落下强度F是另一种评价烧结矿常温强度的方法,用来衡量烧结矿的抗冲击能力。
优质的烧结矿落下强度F=86%~87%,合格的烧结矿落下强度F=80%~83%落下强度F = m1/ m o×100%m o—试样总质量kg,m1—落下四次后〉10mm粒级部分的质量kg,烧结矿石灰配比误差1%,影响烧结矿的碱度0.04,燃料波动1%,,影响烧结矿FeO 变化2%~3%,使烧结矿的还原性及强度受到影响。
炼铁1、通常入炉矿石料度5~35mm之间,小于5mm粉末是不能直接入炉的。
2、高炉冶炼成份波动TFe<±0.5%~1.0%,w(SiO2)≤±0.2%~0.3%,烧结矿碱度+0.03%~0.1% 。
3、冶炼1吨生铁含尘量30~80kg之间,是矿粉和焦粉的混合物,含Fe40%左右,C 10%左右,还有一定量的SiO2,作烧结原料,取代部分熔剂、燃料、矿粉降成本,配料中不应该超过10%。
烧结助剂的制备

烧结助剂的制备烧结助剂是一种能够提高烧结物料质量的化学添加剂,适用于各种不同类型的烧结工艺。
对于矿石、冶金、水泥等行业来说,烧结助剂的制备是非常重要的。
下面将详细介绍烧结助剂的制备方法与流程。
1.烧结助剂的制备原理烧结助剂主要是为了改善物料的结晶过程,提高烧结的速率和进行无损烧结。
烧结助剂一般可以分为硅酸盐、氟化物、碳酸盐、氧化物和铁系等种类。
硅酸盐是一种常用的烧结助剂,它可以提高烧结物料的成分均匀性,缩短烧结时间,提高细粒料的强度和固化温度。
2.烧结助剂的制备流程(1)原料筛选:首先选取适宜的原料,进行筛选分级。
(2)物料配比:按照一定比例将不同类型的原料进行混合,确定烧结助剂的成分和配比。
(3)混合制浆:将混合好的原料加入适量的水中,搅拌均匀,形成稠密的糊状物质。
这个过程需要使用混合机或制浆机。
(4)过筛挤压:制成的烧结助剂需要过筛,去掉颗粒较大的杂质。
接着将烧结助剂的粘稠物挤出,并按照所需要的形状进行造型。
(5)干燥烧结:将形成的烧结助剂送入烘箱中进行干燥。
干燥后的烧结助剂需要送入窑中进行烧结,时间一般需要约3小时,温度在1200℃左右。
烧结后的烧结助剂需要冷却后才能包装出售。
3.烧结助剂的制备注意事项(1)先对原料进行筛选和清洁,确保原材料的质量,减少杂质。
(2)烧结助剂制备的过程中需要注意,不同原料的重量比例不能过大过小,否则会影响烧结助剂的质量。
(3)烧结助剂需要按照一定规格进行造型,否则不易使用。
总之,烧结助剂的制备是一个比较复杂的工艺,需要我们对原材料、配比、混合制浆、造型、烧结等多个环节都进行精心处理。
只有注意细节,才能生产出优质的烧结助剂,提升烧结物料的质量。
石英砂烧结用助熔剂

石英砂烧结用助熔剂
本文介绍了石英砂烧结用助熔剂的种类及烧结工艺,可以明确石英砂烧结用助熔剂的作用,以及它们的烧结要求。
1 石英砂烧结用助熔剂
石英砂烧结用助熔剂是一种特殊的助熔剂,用于结合石英砂颗粒,使其形成烧结的模型,以达到烧结要求。
助熔剂有多种形式,可分为硅酸盐类、碳酸盐类、离子交换剂类及其他类。
其中,丙烯酸钠和氧化铝是最常用的石英砂烧结用助熔剂,它们能形成具有高粘度的熔融液,从而提供较高的烧结强度。
2 烧结工艺
烧结工艺的要求有:首先,需要选择合适的石英砂颗粒,并研磨成指定的粒度;其次,采取合适的助熔剂,使之熔融成稠浆,并加以保温一定时间。
最后,利用压力将稠浆压实,生成模型,并进行熔融。
烧结完成后,石英砂颗粒将原有的分散模式变为聚集模式,形成一个完整的烧结模型,具有更好的烧结强度和热稳定性。
3 助熔剂作用
助熔剂的作用是调节烧结过程中的熔融度,使熔融度达到所需水平以达到烧结要求。
具体而言,助熔剂能够影响熔融混合物的粘度、压缩强度及抗热变性能,从而达到良好的烧结效果。
助熔剂的选择要根据助熔剂的特性,石英砂的组成,以及烧结要求来确定,以获得更好的性能。
摘要:本文介绍了石英砂烧结用助熔剂的种类及烧结工艺,可
以明确石英砂烧结用助熔剂的作用,以及它们的烧结要求。
助熔剂的选择要根据其特性、石英砂的组成以及烧结要求来确定,以获得更好的性能。
高炉喷吹和烧结用煤对煤质的要求

高炉喷吹和烧结用煤对煤质的要求1、高炉喷煤对煤质的要求高炉喷吹技术是将粉状煤和高炉热风一起从高炉风口喷入高炉,在风口前燃烧,产生热量和一氧化碳,作为高炉的热量和还原剂,代替部分焦炭进行高炉冶炼,从而节省焦炭。
目前,我国高炉平均喷吹量达到120千克/吨铁,宝钢高炉喷吹量达到260千克/吨铁,处于世界领先水平。
高炉喷吹用煤应能满足高炉冶炼工艺要求和对提高喷吹量和置换比有利,以便替代更多的焦炭。
高炉喷吹对煤质性能的要求及相关的指标有:工业分析指标、发热量、粒度及均匀性、可磨性、燃烧性、爆炸性、反应性、灰熔性、着火点、煤岩结构、灰成分分析、比表面积和密度等。
归结起来主要有以下几方面。
(1)煤的灰分越低越好。
灰分含量应相同或低于使用的焦炭灰分,一般要求Ad<12.5%.我国目前喷吹的煤粉一般灰分含量与焦炭灰分含量相当,或煤的灰分含量略大于焦炭灰分含量。
在这两种情况下,喷吹煤粉形成的渣量要比全焦冶炼时大些,因为在两者灰分含量相同时,只有置换比1。
0时,两者灰分形成的渣量相等,而在置换比小于1。
0时,喷吹煤粉灰分形成的渣量将大于置换焦炭形成的渣量。
但这种差异也只占灰分形成渣量的一小部分,例如吨铁渣量在490KG/T 左右,喷煤比为150KG/T铁,置换比0。
8KG/KG,两者灰分均为13%,则增加的渣量为3。
9KG/T左右,占灰分形成渣量的10%,占吨铁总渣量的0。
8%左右。
如果喷吹煤粉灰分高于焦炭灰分,则增加的渣量将多些,例如煤粉灰分为15%,则增加的渣量为10。
5KG/T左右,增加的渣量占吨铁总渣量的2。
15%,所以要求喷吹煤粉的灰分越低越好。
(2)硫含量越低越好。
煤的含硫量应与使用焦炭的含硫量相同(或低于),一般要求St<0.61%。
若煤的含硫量高于使用的焦炭含硫量,为保证生铁质量,必须增加溶剂和燃料消耗,相应增加排渣量。
(3)胶质层越薄越好。
Y<10mm,这样可避免在喷吹过程中结焦,堵塞喷枪和风口影响喷吹和高炉正常生产。
烧结料面富氢气体喷吹技术

烧结料面富氢气体喷吹技术
烧结料面富氢气体喷吹技术是一种在烧结过程中向料面喷射富氢气体的技术。
它的目的是通过富氢气体的喷吹,提高烧结料的燃烧效率,加快烧结速率,降低能耗和烟气排放。
富氢气体喷吹技术主要包括以下步骤:
1. 准备富氢气体:将氢气通过制氮机进行净化和富集,得到富氢气体。
2. 喷吹富氢气体:将富氢气体通过喷嘴喷射到烧结料的表面,形成氢气氛围。
3. 燃烧反应:烧结料与富氢气体发生反应,产生高温,加速烧结过程。
4. 控制参数:通过控制喷吹氢气的流量、压力和喷嘴位置等参数来控制烧结过程。
烧结料面富氢气体喷吹技术的优点包括:
1. 提高烧结效率:富氢气体可以促进燃烧反应,提高烧结料的燃烧效率。
2. 加快烧结速率:烧结料面富氢气体的喷吹可以加快烧结速率,提高生产效率。
3. 降低能耗:富氢气体喷吹技术可以使燃料更加充分利用,减少能耗。
4. 环保减排:烧结料面富氢气体喷吹可以降低烟气排放,减少对环境的影响。
然而,烧结料面富氢气体喷吹技术也存在一些挑战和限制,如氢气的安全性问题、设备的成本和维护等方面的考虑。
因此,
在实际应用中需要综合考虑各种因素,选择适合的喷吹技术和参数,以实现最佳的烧结效果。
氧化锆烧结助剂

氧化锆烧结助剂随着工业的不断发展,材料科学技术也日渐完善,人们对于新材料研究的需求也越来越高。
而氧化锆烧结助剂就是一种新型的材料在材料科学技术领域的一个重要研究方向。
本文主要从氧化锆烧结助剂的定义、作用、应用等方面进行探讨,以期对于该领域的深入了解。
氧化锆烧结助剂是一种在氧化锆材料烧结过程中添加的辅助材料。
它可以改变氧化锆粉末的物理性质和化学性质,进而影响氧化锆烧结所需的烧结温度、时间、压力等条件,从而实现提高氧化锆材料烧结致密度、硬度、抗弯强度、耐磨性等性能的目的。
氧化锆烧结助剂的作用主要分为以下三个方面:1、制备氧化锆陶瓷时的流动性控制在氧化锆制备过程中,粉体原料的流动性是影响陶瓷成型的关键因素之一。
普通的氧化锆粉体在进行热压烧结时,很难完全烧结成致密的陶瓷,而氧化锆烧结助剂的加入可以改善氧化锆粉体的流动性,使其更容易填充成型模具中,从而为制备高质量的陶瓷奠定了基础。
2、增强氧化锆陶瓷的力学性能氧化锆烧结助剂在氧化锆材料烧结过程中可以使氧化锆颗粒发生特殊的扭曲结构,因此能够增强烧结后的氧化锆陶瓷的硬度、韧性和耐磨性等力学性能。
这些性质对于氧化锆陶瓷在工业制造中的应用至关重要。
氧化锆烧结助剂的加入也可以改善氧化锆陶瓷的化学稳定性,从而提高其抗腐蚀性能。
氧化锆陶瓷本身是一种优良的高温稳定材料,但在某些特殊化学环境下仍然会发生变化,而氧化锆烧结助剂的加入可以协同氧化锆陶瓷本身的材料化学特性,从而提高其化学稳定性。
除了在氧化锆陶瓷制备过程中的应用外,氧化锆烧结助剂在其他领域也具有广泛的应用前景:1、作为太阳能电池锗、铌酸锂等材料的添加剂2、利用氧化锆烧结助剂发展具有高压、高强度、高质量的氧化锆电极,在微波熔炼、X光荧光分析等领域中具有广泛的应用。
3、在核能领域中,氧化锆烧结助剂也被广泛应用于核燃料棒材料的制备过程中,以提高材料的密度、力学性能和化学稳定性。
总之,氧化锆烧结助剂是一种非常重要的新型材料,其广泛的应用领域和作用机制,对推动材料科学技术的发展和提高材料性能的研究具有重要的作用。
烧结焊剂组成、作用及制备工艺总结

烧结焊剂的组成、作用及制备工艺总结1.烧结焊剂组成及其作用CaF2:在焊剂中以萤石或者冰晶石的形式添加,是低氢型烧结焊剂中的一种重要组分,在碱性渣里,可以促进CaO熔化,降低熔渣的黏度,对熔渣起稀释作用,并与自由的SiO2在高温作用下反应生成SiF4气体,气体能排除电弧区的氢气,防止氢溶解于金属中及液态金属表面的H2O发生化学反应形成不溶于钢液的稳定氢化物HF,减少氢在金属中的溶解度。
含量过高会造成焊接电弧的不稳定,主要是CaF2的电离电位较高,且电离所得的F-离子极易夺取电弧中的电子,使焊接电弧的稳定性降低,从而导致焊缝金属成形变差,因此,萤石的加入量为15~30%;10%~25%;15%-20%。
CaF2的含量和熔化温度区间之间的关系较为复杂。
当CaF2的含量在6%~14%之间增加时,焊剂的熔化温度区间减小;当含量从14%增加到18%时,焊剂的熔化温度区间增大;而含量从18%增加到22%时,熔化温度区间减小;但是当萤石的含量再增加时,焊剂的熔化温度区间基本不变。
偏碱性盐类,熔点较低(1360℃)表面张力小,膨胀系数大,是焊剂中不可缺少的组分,加入一定量时,能有效降低焊剂的熔点表面张力和粘度,改善焊道的摊开性、熔合性和脱渣性。
Al2O3:是一种高温下很稳定的氧化物,属于高熔点物质(2050℃),表面张力大,氧化性小,对堆焊金属成分影响小。
焊剂中含量增加愈多,焊道鱼鳞波纹愈细小,当含量超过40%时,焊道较光亮平滑,但会使熔渣粘度增大,流动性变差,使焊道两侧边缘与母材熔合处较陡,容易造成焊缝金属夹渣和咬边等缺陷。
主要通过氧化铝、铝矾土和焦宝石等的形式加入焊剂,其在焊剂中主要作为造渣剂,在焊接过程中随着其含量增加起着提高熔渣的熔点及黏度的作用。
另外,Al2O3在高温下有利于提高电弧的集中程度,对于保证焊接过程中焊丝电弧的稳定性有较好的效果,但由于其在高温下不易分解,熔点较高,会影响焊道外观形貌,所以在焊剂中含量不宜过高。
3工业用煤质量要求简

3 工业用煤质量要求简介一、煤焦用煤对煤质的要求1 、单种炼焦煤的结焦特性及其在配煤中的作用( 1 )气煤.气煤在加热时能产生较多的胶质体.但这种胶质体的热稳定性差,容易分解。
气煤由半焦转变为焦炭时,产生大量挥发物:因此收缩度大,形成焦炭纵裂纹多,块度小,机械强度名日氏。
但在配煤中配入气煤,可以音化工产品的回收率.降低煤的膨胀压力。
( 2 )肥煤.肥煤在加热时能产生大量胶质体.热稳定性较好.成焦时熔融性较好,但是由于肥煤成焦时,其内部应力未及时松驰。
会产生较多的横裂纹。
肥煤在配煤中的作用很重要。
被认为是基础煤,因此它具有很强的粘结力,可以粘结一部分弱粘煤炼成强度较好的冶金焦炭。
( 3 )焦煤(通常称主焦煤)。
炼焦煤具有中等挥发分与中等胶质层,单独炼焦时形成热稳定性很好的胶质体。
能炼制成块大、裂纹少、耐磨性好的焦炭,在工业不发达时常用它单独炼焦。
但在现代室式焦炉中用焦煤单独炼焦时,由于收缩小,膨胀压力大,造成推焦困难.甚至损坏焦炉。
在配煤中它可以起到提高焦炭强度的作用。
( 4 )痰煤。
瘦煤在加热时产生的胶质体t 少,形成的焦炭块度大,裂纹少,但不耐磨。
在配煤中配入瘦煤可以增加焦炭的块度。
2 、焦炭在高炉炼铁中的作用高炉炼铁使用的炉料包括铁矿石〔天然矿石、烧结矿或球团矿)、溶剂(石灰石或白云石)和焦炭,炉料从炉顶依次分批装入炉内.焦炭在高炉炼铁中的作用可以概括为:( l )提供热量.焦炭在焦炉风口前的回旋区内激烈燃烧,燃烧产生的热能是主炉冶炼过程中的主要热源。
( 2 )还原作用。
焦炭是回旋区内姗烧生成的高温煤气。
在上升过程中将热能供给炉料,使之与焦炭发生吸热反应,生成CO 和H2 ,随后CO 与铁矿石中的铁氧化物发生还原反应转化为金属铁.( 3 )骨架作用。
高炉冶炼过程都发生在煤气上升和炉料下降的相向运动和相互作用之中,整个料柱的透气性是高炉运行的关键。
在料柱上部,焦炭起煤气流分配层的作用;在料柱中部.焦炭起骨架作用,支撑着已经熔融的铁矿石,使煤气正常上升:在料柱下部,高温下仍以固态块状存在的焦炭与已经成为液态的铁水和熔渣混在一起,成为煤气上升与铁水、炉渣下降的疏松骨架.3 、焦炭质量标准( l )抗碎机械强度(M40 ) ,指焦炭在转鼓中转动一定时间后,大于40mm的重量所点试样总质量的百分数。
- 1、下载文档前请自行甄别文档内容的完整性,平台不提供额外的编辑、内容补充、找答案等附加服务。
- 2、"仅部分预览"的文档,不可在线预览部分如存在完整性等问题,可反馈申请退款(可完整预览的文档不适用该条件!)。
- 3、如文档侵犯您的权益,请联系客服反馈,我们会尽快为您处理(人工客服工作时间:9:00-18:30)。
铁精矿强化烧结剂唐山炼铁厂关于铁精矿强化烧结剂使用情况报告为解决环绕机烧结矿FeO高,燃料消耗高,粒度碎、强度差等问题,我厂在两台环式烧结机上使用了铁精矿强化烧结助燃剂,达到了预期效果。
1、烧结试用原料化学成份及烧结生产原料配比:(1)、原料化学成份(%)(2)烧结生产原料配比2、生产试验工艺流程:选取上述各种原料按湿料比通过人工跑盘、调整、控制下料量,在燃料(焦粉)配料园盘后方配料皮带上方安装下料装置。
HL-01配加量为烧结湿混合料的0.3‰,按比例配料的原料经皮带运输机送到一次混合机加水湿润混匀,然后再经二次混合机造球制粒后均匀布在烧结机炉床上,经点火烧结形成烧结矿,经破碎、筛分、冷却、成品矿送往高炉。
3、本次试验分为两个阶段:4月1日—4月6日主要是摸索试验提高转鼓指数,降低返矿率;4月7日—4月8日主要是降燃料配比实验。
试验结果:烧结配加HL-01前后几个指标对比试验期HL-01的统计配比为0.316‰,固体燃料(焦粉)消耗在试验期(二),下降了6.4Kg/t,降低比例为9.5%;两个试验期平均转鼓指数为74.15% ,比基期71.6%提高了2.55%,烧结矿FeO平均为11.72%比基期降低了0.475%。
高炉槽下返矿率两个试验期平均为9.01%,比基期的11.10%下降了2.09%。
冷筛自循环返矿率比过去比较下降1%左右。
4、经济效益浅析:〈1〉直接效益A、配加HL-01吨矿焦粉降低6.4Kg,每吨焦粉价格按内部价220元/ T,年可节约焦粉60万吨×6.4÷1000=3840吨×220=84.48万元,B、结块率提高,返矿率下降,冷筛约1%,高炉槽下2.09%,两项合计返矿减少3.09%,年降低成本:0.0309×60万吨×(292-150)=263.27万元〈2〉间接效益高炉产量试验期比基期提高1.2%。
两座179m3高炉年产44万吨,可增产:44万吨×1.2%=5280吨,计52万元。
〈3〉配加HL-01烧结助燃剂增加的成本为A、吨烧结矿增加的成本:吨矿耗HL-04量×单价=0.45Kg/t×7600/1000=3.42元/吨B、节约焦粉吨矿降低成本:6.4×0.22=1.41元/吨因配加HL-04增加的总成本=(3.42-1.41)×60万吨=120.6万元〈4〉、年经济效益合计:节焦效益+降低返矿增产效益+高炉增产效益—配加HL-01=84.48+263.27+52.0-120.6=279.15万元。
铁精矿强化烧结开发节能、环保产品的意义在能源日渐紧张的今天,节能降耗已经成为世界性的大课题,据1996年10月讨论世界地质资源开发问题伦敦国际会议估计:石油按已探明的储量还可开采28年左右;天然气还可开采50年;铁精矿还可开采60年;原煤可开采近200年。
我国虽是能源大国,但人均占有量仅为世界人均占有量的五分之一,而能源利用率仅为发达国家的0%。
面对资源,能源的匮乏,我国指定了“开发与节约”的能源方针,倡导开发新能源技术和节能环保产品。
因此,开发节能环抱产品具有划时代意义。
铁精矿强化烧结剂开发节能、环保产品的状况世界上发达国家早在十多年前就对铁精矿烧结的节能降耗进行了大量的研究,花费了巨额资金和人力、物力,并生产出铁矿烧结添加剂。
它提高烧结机利用系数3%-4%。
提高烧结矿转鼓指数4%-5%以上,降低亚铁含量1%-1.5%左右,这些节能产品在世界许多国家得到了广泛应用。
我公司在对市场调研后与中科院合作,联合开发了HL-01铁精矿烧结助燃剂,其性能已达到并超过国际水平(这种添加剂可节煤15%-30%,使烧结机利用系数提高4%-6%,烧结矿转鼓指数提高4%-7%,亚铁含量降低1.5%-2.5%),为我国的钢铁工业发展做出了巨大贡献。
铁精矿强化烧结形状特征及意义HL-01铁精矿强化烧结助燃剂,其特征为浅粉红色沫末状结晶体,有滑腻手感,无臭味。
它是以低温烧结和燃气化助燃理论为基础,在钢铁烧结中可以缩短时间,提高结块率。
该产品不仅解决了铁精矿烧结工艺的传统强化措施(低温烧结、小球烧结、燃料分加等)存在的弊端,同时也攻克了传统添加剂应用方面生产综合负值的问题。
HL-01铁矿烧结剂是根据配方按比例加以助燃剂、增强剂、增氧剂、燃气化剂、阻凝剂等经混合、烘干后制成,在烧结混合料中添加少量的强化剂后,对燃料的气化燃烧反应起到一定的催化作用,可降低燃料消耗,加快烧结燃烧速度,提高烧结机的利用系数,增加烧结矿产量和强度,提高结块率,降低返矿率。
强化烧结剂的主要功能1、助燃:可对固体燃料的气化燃烧起催化助燃作用,特别是对固体燃料中非碳物质的催化作用更强,增加固体燃料的反应活性,使烧结过程燃烧带温度提高,有利于矿化反应的进行,能生产极多的液相。
2、提高效率:可改善烧结过程气一固一液相间的传热质条件,使烧结速度加快,烧结时间缩短,提高生产效率。
3、提高成品效率:可使混合料的熔融温度降低,点火条件得以改善,降低返矿量,提高成品率。
4、抑制粉化:本烧结助燃剂中的卤化物和稀土元素可使烧结矿的自然粉花现象得以抑制,有利于烧结强度的提高。
5、环保:由于反应的放热节能作用,在烧结生产中降低了固体燃料的加入,减少烧结废气中SO2的含量,降低环境污染。
6、节能:在助燃剂的强化、催化作用下,大部分液相反应可在低于1300℃以下完成,致使烧结终点的提前,烧结机利用系数提高,固体燃耗可降低15%以上,生产过程的其它固定费用亦同步下降。
7、综合利用:HL-01铁精矿强化烧结助燃剂可提高烧结机利用系数5%以上,提高烧结矿转鼓指数6%以上,降低亚铁含量2%左右,提高成品率,降低返矿率,经济和社会效益显著。
铁精矿强化烧结剂的物理特征铁精矿强化烧结剂的工作机理HL-01强化烧结助燃剂。
是由多种非能源性无机化工原料按比例复配而成的一种化学添加剂,其主要作用是在烧结生产不变的情况下,提高烧结速度和烧结矿强度,降低粉花率,改善和提高成矿质量,达到增产、降耗、环保等个方面的经济效益和社会效益。
化学添加剂作为一种化学工业品,已广泛地应用于各行各业,成为工业生产中不可缺少的一种化工产品,近年来,由于国家对环保及,同时可降低烧结尾汽中SO2含量,为企业创造良好的经济效益和社会效益。
节能方面的要求和标准逐步提高、创新,用于燃料方面的化学添加剂不断的被研制和开发出来,并且从技术水平、性能特点、效果也逐步提高,特别是在铁精矿烧结中使用化学添加剂,居国内首创,是烧结冶炼方面的前端技术,对于改善烧结矿质量提高,产量提高,节能效果。
环保改善等各个方面均有较高的实用价值。
强化烧结剂对煤燃烧过程的影响1、在对煤的工业分析中,常把煤的组成分为七大部分几。
即:碳、氢、氧、硫、灰、水在工业使用中,对煤的组成分为:固定碳、挥发份、灰份及水,以上说法是从煤的化学成分组成去划分定义的,而从煤的结构组成方面讨论则是以上元素,以多芳香环为结构单元组成的,在在芳香环周围有侧链、管能团等。
这些官能团中有羚基(含酚羚基、醇羚基)甲氧基、醛基、羰基,还有少量含氮、硫的官能团。
因此形成不同的煤,也就是说燃料中的化学元素是由有机结构单元和无机结构单元交错复合存在着。
所以煤的燃烧也就是不能单纯地看成是一种简单的单个化学元素的氧化反应。
2、煤的燃烧就是由煤中各种有机单元和无机单元结构在加温过程中裂解后与氧发生强烈的氧化反应,形成CO2、H2O、SO2等过程,从宏观角度看,煤的燃烧是碳、氢、硫与氧在高温下的氧化反应。
煤与非燃烧物混合燃烧,如炉窑、烧结、炼制等在不同的燃烧方式下,煤在燃烧过程中的结构裂解及氧化均有不同的变化。
不同的燃烧方式加入不同的烧结剂,就可以控制和改善在燃烧中的结构裂解构成,从而达到提高燃烧效率。
控制燃烧气氛,改善燃烧环境,适应生产需要。
3、在煤燃烧过程中,如果加入各种不同的烧结剂,煤的燃烧就会发生不同的变化,烧结剂对燃烧的影响分为以下几种:a:降低煤的燃点b:提高燃烧温度c:改变燃烧时间d:改变燃烧后产生的气氛和燃烧性质,调整烧结的成分,这种方法只是挖掘了煤燃烧过程中可发挥而没有正常发挥的能量,不是创造能量。
强化烧结剂对烧结固体燃料的影响铁精矿烧结过程中,为使烧结过程能达到所需要的温度,在烧结料中加入一定量的煤,煤和烧结料均匀的混合在一起,因此烧结料层中的层状燃烧即不同于一般锅炉、炉灶中层状燃烧,也不同于单颗粒碳的燃烧。
因此烧结料层中煤的数量相对较少(约3%-5%)且被周围的其它不可燃的矿物包围着。
其燃烧规律介于二者之间,有以下特点:1、需要较大的空气过剩系数(约1.4-1.5)以保证煤能够与空气有较大的接触机会,促使煤较完全燃烧。
2、燃烧生成CO2、CO,在燃烧温度下CO2占优势,虽然CO2可参加二级反应形成CO,但由于燃烧层很薄,高温停留时间很短,反应受到很大限制,不可能有明显的改观。
在燃烧层和预热层的氧化物还参加了还原和氧化反应,燃烧的空气过剩系数较大,在高碳粒较远处存在着自由氧。
这些特定条件都决定了气相中的CO2、自由氧也不能被消耗完。
3、在燃烧料层中,既存在有氧化区,也存在有还原区,二区域呈离散型分布。
在一般情况下,总的气氛性质为氧化性。
4、烧结料层中,煤的燃烧基本处于扩散速度范围内,但在燃烧前的预热干燥层中,煤中可燃挥发物由于浓度不够而不易燃烧。
因此降低了煤的整体可燃性,影响扩散速度,从而影响烧结带的移动速度。
在这种特点下,添加适量的化学烧结剂,有效控制燃烧整体的氧化气氛,裂解煤中低温不可燃结构单元,降低燃点,增加可燃单元,这样就可以充分利用烧结料移动速度和燃烧层厚度、降低返矿率,提高烧结机利用系数。
使用强化烧结剂对烧结生产的影响1、在一定条件下,提高垂直烧结速度,烧结产量提高。
而垂直烧结速度的快慢取决于两个因素,即料层中燃料的燃烧速度和传热速度。
在正常配碳量的情况下,使用烧结剂改变燃烧特性,提高燃烧效率,加快燃烧反应速度,由于燃烧效率的提高,燃烧尾气中可燃气体减少,CO2>和H2O的含量增高,因此气体热容量增大,气体传热速度加快,所以垂直烧结速度提高。
2、从提高烧结矿强度和成品率出发,要求高温区温度较高,厚度较大,以保证各种高温反应能充分进行,产生较多的液相。
温度过高,厚度过大,易产生过熔,也会产生负影响。
在正常取碳量的烧结料中,加入化学烧结剂可使煤在正常燃烧时一些可燃烧而又不具备燃烧条件没有燃烧的部分充分燃烧,使高温区内部热源增加,提高了高温区温度;燃料煤中的低温挥发物在化学烧结剂的作用下,提高挥发温度,参加燃烧,使燃烧厚度增大。
强化烧结剂对烧结矿强度和粉花率的影响烧结料中配碳量决定着烧结的温度,气氛性质的烧结速度,因而对烧结矿的矿物组成和结构都有影响。