4-2 工件在夹具中的定位
浅谈工件在夹具中定位的基本原理

在 夹 具 设 计 的定 位 分 析 中 , 用 x、 Y、 z分 别 表 示 沿 x
轴、 Y轴 和 z轴 的移 动 自由度 ;用 x、Y、z 分别表示沿 x 轴、 Y轴 和 z轴 的转 动 自由度 。由此 可 见 , 要 使 工 件 在 夹 具 中 占有 确 定 的位 置 ,等 于要 在 空 间 直 角 坐标 系 中确 定 刚 体 的 六个 坐标 参 数 ,即要 对 这 六 个 自由 度加 以必 要 的 约 束 条 件 。 为便 于分 析 定 位 问题 ,引 出 定 位支 承 点 的概 念 ,将 具 体 的定 位 元 件 抽 象化 ,转 化 为 相 应 的定 位 支 承
求, 讨论工件定位时 , 只需 要 用 五 个 定 位 支 承 点 , 限 制 工
件 相应 的五 个 运 动 自由度 ,便 可确 定 工 件 正确 的加 工 位 置。 那 么 定位 支 承点 是 如何 限 制工 件 自由度 的?下 面 给予
分析。
Y
图 1 刚体 在 空 f - B I 具 有 的六 个 自 由度
要 保 证槽 底 面与 A 面 的尺 寸 h± Ah且 平 行 , A面 必 须 放 在 与 铣床 工 作 台 平面 相 平行 的水 平 面上 ,要 确 定 A面 的
位置 , 必 须 用 三个 定 位 支 承点 , 因为 只要 三 个点 便 可 确 定 空 间一个 平 面 的 位置 ; 另外 , 要 保证 槽 的 侧 面 与 B面 的 尺 寸 a±△a且 平行 ,即要 求 槽侧 面 和 B面都 与 铣床 工 作 台 的直 线进 给 运 动方 向平 行 , B面 必须 位 于 与工 作 台进 给 运 动方 向相 平行 的 直线 上 , 要 确 定 B面 这样 一 个 位 置 , 需 要 用 两个 定 位支 承 点 , 因为 空 间 的一 条 直线 的位 置 , 只要 两 点便 可 以确定 。 因此 , 在 铣槽 工 序 中 , 为 满 足 加工 技 术 要
机械制造技术基础课后答案(1)
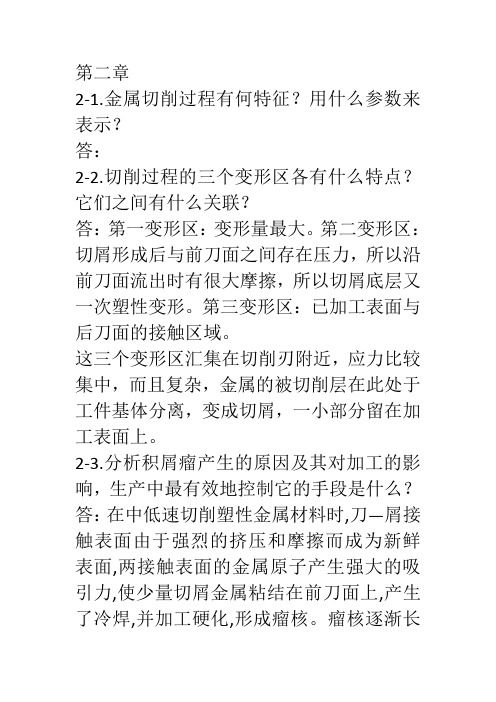
第二章2-1.金属切削过程有何特征?用什么参数来表示?答:2-2.切削过程的三个变形区各有什么特点?它们之间有什么关联?答:第一变形区:变形量最大。
第二变形区:切屑形成后与前刀面之间存在压力,所以沿前刀面流出时有很大摩擦,所以切屑底层又一次塑性变形。
第三变形区:已加工表面与后刀面的接触区域。
这三个变形区汇集在切削刃附近,应力比较集中,而且复杂,金属的被切削层在此处于工件基体分离,变成切屑,一小部分留在加工表面上。
2-3.分析积屑瘤产生的原因及其对加工的影响,生产中最有效地控制它的手段是什么?答:在中低速切削塑性金属材料时,刀—屑接触表面由于强烈的挤压和摩擦而成为新鲜表面,两接触表面的金属原子产生强大的吸引力,使少量切屑金属粘结在前刀面上,产生了冷焊,并加工硬化,形成瘤核。
瘤核逐渐长大成为积屑瘤,且周期性地成长与脱落。
积屑瘤粘结在前刀面上,减少了刀具的磨损;积屑瘤使刀具的实际工作前角大,有利于减小切削力;积屑瘤伸出刀刃之外,使切削厚度增加,降低了工件的加工精度;积屑瘤使工件已加工表面变得较为粗糙。
由此可见:积屑瘤对粗加工有利,生产中应加以利用;而对精加工不利,应以避免。
消除措施:采用高速切削或低速切削,避免中低速切削;增大刀具前角,降低切削力;采用切削液。
2-4切屑与前刀面之间的摩擦与一般刚体之间的滑动摩擦有无区别?若有区别,而这何处不同?答:切屑形成后与前刀面之间存在压力,所以流出时有很大的摩擦,因为使切屑底层又一次产生塑性变形,而且切屑与前刀面之间接触的是新鲜表面,化学性质很活跃。
而刚体之间的滑动摩擦只是接触表面之间的摩擦,并没有塑性变形和化学反应2-5车刀的角度是如何定义的?标注角度与工作角度有何不同?答:分别是前角、后角、主偏角、副偏角、刃倾角(P17)。
工作角度是以切削过程中实际的切削平面、基面和正交平面为参考平面确定的刀具角度。
2-6金属切削过程为什么会产生切削力?答:因为刀具切入工具爱你,是被加工材料发生变形并成为切屑,所以(1)要克服被加工材料弹性变形的抗力,(2)要克服被加工材料塑性变形的抗力,(3)要克服切屑与前刀面的摩擦力和后刀面与过度表面和以加工表面之间的摩擦力。
夹具的定位夹紧与夹具设计
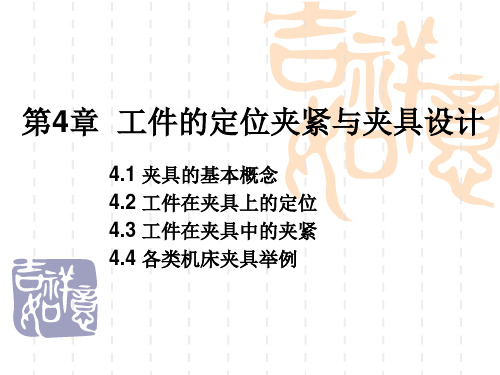
▪ 2.误差值的估算
▪ 一般夹县的制造精度,其误差值取该零 件尺寸公差值的1/3~1/5。
▪ 上述误差中,安装误差和对定误差都是 和夹具有关的误差,一般约占整个加工误 差的三分之一。
4.2工件在夹具上的定位
4.2.1 工件的安装
这里安装有两个含义即定位和夹紧。 定位:工件在机床上加工时,首先要把工件安放在机
定位基准面的变化而自动调整井与之相适应。如图 4-17所示。自位支承常用于毛坯表面、断续表面、 阶梯表面的定位以及有角度误差的平面定位。
(4)辅助支承 辅助支承是在工件定位后才参与支承的元件,
其高度是由工件确定的,因此它不起定位作用,但 辅助支承锁紧后就成为固定支承,能承受切削力。 辅助支承的结构形式很多,图4-18是其中的3种。
而常按下面的步骤设计菱形销。
1)确定两销中心距尺寸及其公差 取工件上两孔中
心距的基本尺寸为两定位销中心距的基本尺寸,其公
差取工件孔中心距公差的1/5~1/3,即令:
Tlx=(1/5~1/3)Tlk。
2)确定圆柱销直径及其公差 取相应孔的最小直径 作为圆柱销直径的基本尺寸,其公差一般取g6或f7。
3)确定菱形销宽度、直径及其公差 首先按有关标 准(参考表4-3)选取菱形销的宽度b;然后按式(4-2)计算 出菱形销与其配合孔的最小间隙△2min;再计算菱形 销直径的基本尺寸;d2=D2-△2min;最后按h6或h7选 取菱形销直径的公差。
表4-2 典型定位元件的定位分析(续)
表4-2 典型定位元件的定位分析(续)
表4-2 典型定位元件的定位分析(续)
3.完全定位和不完全定位
3.完全定位和不完全定位
3.完全定位和不完全定位
4.欠定位和过定位 (1)欠定位 根据工件加工面位置尺寸要求必须
第4章定位原理和机床夹具设计2
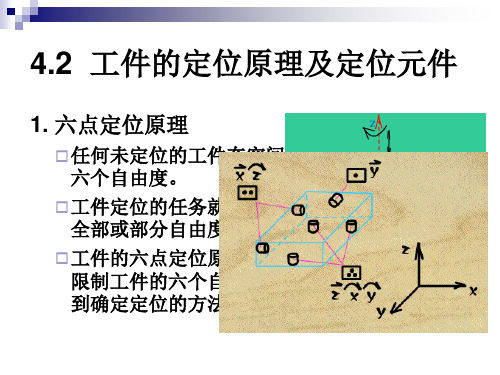
H7 g 6( f 7)
Z
△Z≠ 0 △Y≠ 0
Y
圆柱心轴
X
y
4.2 工件的定位原理及定位元件
3.工件以外圆柱面定位
V形块 定位套 半圆套 支承定位
3.工件以外圆柱面定位
V形块
固定V形块 活动V形块 长V形块 短V形块
3.工件以外圆柱表面定位
3.工件以外圆柱表面定位
定位套
工件以外圆定位的定位套
yz
销2
x y
销1
y 0
x
支承平面
z x y
(3) 过定位
案例4 一面两销定位方案
B 削边销
(3) 过定位
z
案例4 一面两销定位方案
z x y
销1 削边销
y 0
x
支承平面
z x y
(3) 过定位
案例5
滚齿加工的定位方案
x y x y
待加工 的齿轮
z x y
(3) 过定位
案例5
滚齿加工的定位方案
(1)正确的定位 工件定位面与夹具定位元件的定位工 作面相接触或配合来限制工件的自由度, 二者一旦脱离接触或配合,则定位元件就 丧失了工件自由度的作用。
2.应用六点定位原理应注意的问题
(2)一个定位支撑点仅限制一个自由度:原 则上不超过六个。 (3)分析定位支撑点的定位作用时,不考虑 力的影响
2.应用六点定位原理应注意的问题
常用的定位元件
1.工件以平面定位
主要支承
固定支承 可调支承 自位支承
支承钉 支承板
辅助支承
1.工件以平面定位
固定支承
支承钉和支承板
钻套
支承板
支承板
工装夹具设计中的定位分析
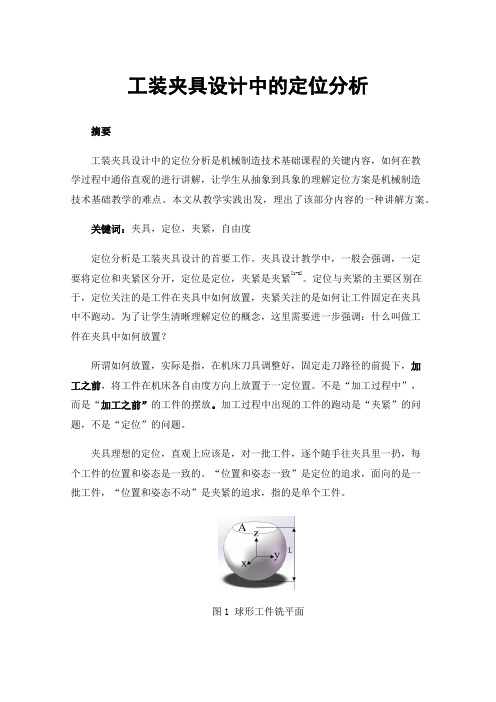
工装夹具设计中的定位分析摘要工装夹具设计中的定位分析是机械制造技术基础课程的关键内容,如何在教学过程中通俗直观的进行讲解,让学生从抽象到具象的理解定位方案是机械制造技术基础教学的难点。
本文从教学实践出发,理出了该部分内容的一种讲解方案。
关键词:夹具,定位,夹紧,自由度定位分析是工装夹具设计的首要工作。
夹具设计教学中,一般会强调,一定要将定位和夹紧区分开,定位是定位,夹紧是夹紧[1-3]。
定位与夹紧的主要区别在于,定位关注的是工件在夹具中如何放置,夹紧关注的是如何让工件固定在夹具中不跑动。
为了让学生清晰理解定位的概念,这里需要进一步强调:什么叫做工件在夹具中如何放置?所谓如何放置,实际是指,在机床刀具调整好,固定走刀路径的前提下,加工之前,将工件在机床各自由度方向上放置于一定位置。
不是“加工过程中”,而是“加工之前”的工件的摆放。
加工过程中出现的工件的跑动是“夹紧”的问题,不是“定位”的问题。
夹具理想的定位,直观上应该是,对一批工件,逐个随手往夹具里一扔,每个工件的位置和姿态是一致的。
“位置和姿态一致”是定位的追求,面向的是一批工件,“位置和姿态不动”是夹紧的追求,指的是单个工件。
图1 球形工件铣平面如图1所示,用立式普通铣床在一批球形工件上加工图示平面,最少需要限制几个自由度?首先需要明确,要加工的是一批工件,不是一个工件,要关注的是:一批工件,逐个放置到已经调好刀的机床上,工件所放位置对待加工尺寸的影响。
待加工尺寸是什么?如图1所示,该案例所指的待加工尺寸是L,需要保证尺寸L,即平面A相对于最低点的距离。
以球心为原点建立工件坐标系,在机床工作台面上建立机床坐标系,工件在机床上的位置和姿态,即转化为工件坐标系相对于机床坐标系的位置和姿态。
列出工件的六个自由度,如图1所示,即 , , , , ,,对六个自由度逐个分析。
对于,考虑当第个球形毛坯放置在机床坐标系的,第(n+1)个球形毛坯放置在的位置时,加工出的平面的定位尺寸会发生变化吗?很明显不会,但是可能会由于放置的位置超出设定的行程,出现“加工不到”的问题,“加工不到”对于定位尺寸的精度没有影响,所以可以不限制。
工件在夹具中的定位与夹紧

(3)精基准的选择
主要应保证加工精度和装夹方便
选择精基准一般应遵循以下原则:
1)基准重合原则
设计(工序)与定位
2)基准统一原则
各工序的基准相同
3)互为基准原则
两表面位置精度高
4)自为基准原则
加工余量小而均匀
考虑定位方案时,先分析必须消除哪些自由度, 再以相应定位点去限制。
(3)欠定位与过定位
工件应限制的自由度未被限制的定位,为欠定位, 在实际生产中是绝对不允许的。
工件一个自由度被两个或以上支承点重复限制的 定位称为过定位或重复定位。一般来说也是不合 理的。
过定位造成的后果: (1)使工件或夹具元件变形,引起加工误差; (2)使部分工件不能安装,产生定位干涉(如一面两销)
六点定位原理。
实际中一个定位元件可体现一个或多个支承点, 视具体工作方式及其与工件接触范围大小而定
定位与夹紧的区别: 定位是使工件占有一个正 确的位置,夹紧是使工件保持这个正确位置。
(2)完全定位与不完全定位 工件的六个自由度被完全限制的定位称完全定位, 允许少于六点的定位称为不完全定位。 都是合理的定位方式。
(2)夹紧力作用点的确定 1)夹紧力应作用在刚度较好部位
2)夹紧力作用点应正对支承元件或位于支承元件
形成的支承面内
3)夹紧力作用点应尽可能靠近加工表面
(3)夹紧力大小的估算
夹紧力的大小根据切削力、工件重力的 大小、方向和相互位置关系具体计算,并 乘以安全系数K ,一般精加工K =1.5~2, 粗加工K = 2.5~3。
向上的变动量。由工件定位面和夹具定位元件的制造误差 以及两者之间的间隙所引起。
机械制造工艺学——工件的定位
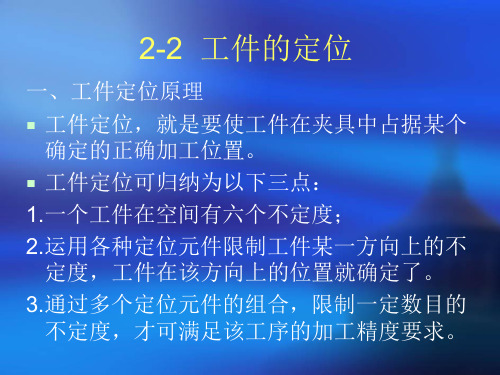
基准不重合误差:
(四)提高工件在夹具中定位精度的措施
即如何减少或消除基准位置误差和基准 不重合误差。
1、减少或消除基准位置误差的措施 (1)选用基准位置误差小的定位元件 A、以毛坯平面作为定位基准时,可以多点自
位支承取代球头支承钉。
B、以内孔和端面定位时,可应用浮动球面支 承,以减小轴向定位误差。
的定位元件,称为固定支承。
(2)可调支承:定位支承点的位置可以调节的 定位元件,称为可调支承。
主要用于以制造精度不高的毛坯面定位的场合。
(3)自位支承:定位支承点的位置随工件定 位基准位置变化而自动与之适应的定位元件, 称为自位支承。
自位支承一般只起一个定位支承点的作用。
2、辅助支承:只起提高工件支承刚性或辅助 定位作用的定位元件,称为辅助支承。
削边定位销的直径为
当以两个或两个以上的组合表面定位时,重 复定位可能造成不良后果。
为减少重复定位造成的加工误差,可采取如 下措施:
(1)改变定位元件结构
(2)撤消重复定位的定位元件:
(3)提高工件定位基准之间、定位元件定位 面之间的位置精度
二、定位元件的选择 定位表面不同,应选择不同的定位元件 (一)平面定位元件 1.主要支承:工件定位时起主要定位支承作用 (1)固定支承:定位支承点的位置固定不变
*为提高定位稳定性和刚度,以加工过的表面 定位时,可以出现重复定位。
三、定位误差的分析与计算
(一)定位误差及其计算方法
1、定位误差的概念及产生原因: *定位误差:指由于工件定位不准确,而造成
工序尺寸或位置要求方面的加工误差。
*上存在着公差范围内的差异。
2-2 工件的定位
一、工件定位原理
工件定位,就是要使工件在夹具中占据某个 确定的正确加工位置。
工件在夹具中的定位

第二节 工件在夹具中的定位
确定基准的注意:⑴作为基准的点、线、面在工件上不一定存在,如孔的中心线、外圆的轴线以及对称面等,而是常常由某些具体的表面来体现,这些面称为基准面。⑵作为基准,可以是没有面积的点或线,但是基准面总是有一定面积的。⑶基准的定义不仅是对尺寸之间的联系,对位置精度(平行度、垂直度等)也是同样的。
第14页/共41页
第二节 工件在夹具中的定位
欠定位与过定位1)欠定位:按工序的加工要求,工件应该限制的自由度而未予限制的定位。欠定位是绝对不允许的。
第15页/共41页
第二节 工件在夹具中的定位
2)过定位:工件的同一自由度被二个或二个以上的支承点重复限制的定位。可能造成工件的定位误差,或者造成部分工件装不进夹具的情况。过定位不是绝对不允许,要由具体情况决定。
第20页/:包括固定支承钉、固定支承板。
第21页/共41页
第二节 工件在夹具中的定位
第22页/共41页
第二节 工件在夹具中的定位
(2)可调支承 可调支承是顶端位置可在一定高度范围内调整的支承。多用于未加工平面的定位,以调节和补偿各批毛坯尺寸的误差,一般每批毛坯调整一次。
弹簧夹头的速度是有弹性的,如果工件尺寸是一致的,弹簧夹头的速度会更快。如果工件尺寸的变化大,可能需要采用卡爪卡盘以适应尺寸范围宽的加工工件。
第35页/共41页
第二节 工件在夹具中的定位
4.工件以组合表面定位实际加工过程中,工件往往是以几个表面同时定位的,称为“组合表面定位”。
(1)一个平面和二个与其垂直的孔的组合在箱体、连杆、盖板等类零件加工中,常采用这种组合定位,俗称“一面二孔”定位。(会出现定位干涉问题)
(4)辅助支承 在生产中,有时为了提高工件的刚度和定位稳定性,常采用辅助支承。如图所示阶梯零件,当用平面1定位铣平面2时,于工件右部底面增设辅助支承3,可避免加工过程中工件的变形。
机械制造技术基础-卢秉恒 答案 第四章

4-15分别简述车、铣、钻床夹具的设计特点
3)钻床夹具——钻套高度要适中,过低导引性能差,过高 会增加磨损。钻套装在钻模板上后,与工件表面应有适当间 隙,以利于排屑,一般可取所钻孔径的0.3-1.5倍。钻套材 料一般为T10A或20钢,渗碳淬火后硬度为58-64HRC。 必要时可采取合金钢
欠定位——按工序的加工要求,工件应该限制自由度而未予限 制的定位。
过定位——工件的一个自由度被两个或两个以上的支撑点重 复限制的位。
第七页,共26页。
4-6组合定位分析的要点是什么? (1)
答:(1)几个定位元件组合起来定位一个工件相应的 几个定位面,该组合定位元件能限制工件的自由度总数等于 各个定位元件单独定位各自相应定位面时所能限制的自由度 数目之和,不会因组合后而发生数量上 的变化。
第八页,共26页。
4-6组合定位分析的要点是什么? (2)
(2)组合定位中定位元件在单独定位某定位面时原来起 限制工件移动自由度的作用可能会转化成限制工件转动自 由度的作用,但一旦转化后,该定位元件就不能再起原来限 制工件移动自由度的作用了。
(3)单个表面的定位是组合定位分析的基本单元。
第九页,共26页。
4-7根据六点定位原理,分析题图4-72所示定位方案 中,各定位元件所限制的自由度 (1)
答:a.左顶点 x z 右顶点
yxy
b.左圆锥销
x
y
右圆锥销
z
xz
c.下两支撑板
侧支撑板
z xy
削边销
x
y
第十页,共26页。
4-7根据六点定位原理,分析题图4-72所示定位方案 中,各定位元件所限制的自由度 (2)
答:(1)定位元件——使工件在夹具中有准确的位置,起 到定位作用。
工件的装夹与定位
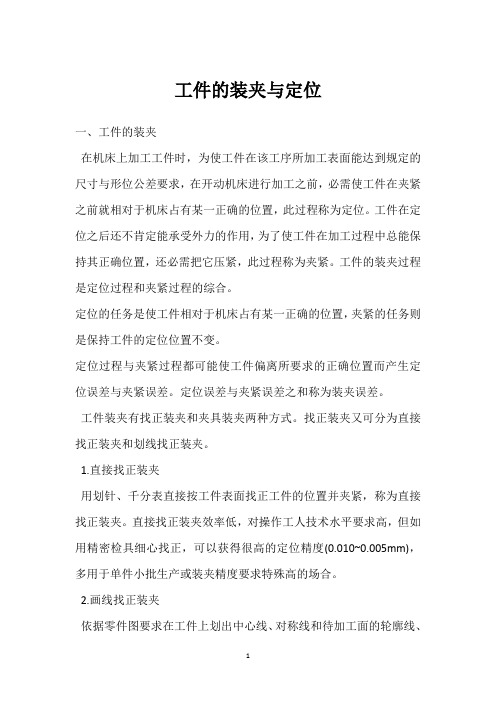
工件的装夹与定位一、工件的装夹在机床上加工工件时,为使工件在该工序所加工表面能达到规定的尺寸与形位公差要求,在开动机床进行加工之前,必需使工件在夹紧之前就相对于机床占有某一正确的位置,此过程称为定位。
工件在定位之后还不肯定能承受外力的作用,为了使工件在加工过程中总能保持其正确位置,还必需把它压紧,此过程称为夹紧。
工件的装夹过程是定位过程和夹紧过程的综合。
定位的任务是使工件相对于机床占有某一正确的位置,夹紧的任务则是保持工件的定位位置不变。
定位过程与夹紧过程都可能使工件偏离所要求的正确位置而产生定位误差与夹紧误差。
定位误差与夹紧误差之和称为装夹误差。
工件装夹有找正装夹和夹具装夹两种方式。
找正装夹又可分为直接找正装夹和划线找正装夹。
1.直接找正装夹用划针、千分表直接按工件表面找正工件的位置并夹紧,称为直接找正装夹。
直接找正装夹效率低,对操作工人技术水平要求高,但如用精密检具细心找正,可以获得很高的定位精度(0.010~0.005mm),多用于单件小批生产或装夹精度要求特殊高的场合。
2.画线找正装夹依据零件图要求在工件上划出中心线、对称线和待加工面的轮廓线、找正线,然后按找正线找正工件在机床上的位置并夹紧,这种装夹方法称为划线找正装夹。
与直接找正装夹方法相比,划线找正方法增加了一道技术水平要求高且费工费事的划线工序,生产效率低;此外,由于所划线条自身就有肯定宽度,故其找正误差大(0.2~0.5mm)。
划线找正装夹方法多用于单件小批生产中难以用直接找正方法装夹的外形较为简单的铸件或锻件。
3. 夹具装夹产量较大时,无论是划线找正装夹,还是直接找正装夹,均不能滿足生产率要求。
这时,一般均须用夹具来装夹工件。
夹具事先按肯定要求安装在机床上,工件按要求装夹在夹具上,不需找正就可进行加工。
使用夹具装夹工件,不仅可以保证装夹精度,而且可以显著提高装夹效率,还可减轻工人的劳动强度,对工人技术水平要求也不高。
成批生产和大量生产中广泛采纳夹具装夹工件。
工件在夹具中的定位概要

定位销一般可分为固定式和可换式两种。 图4-5-26所示,为固定式定位销的几种典型结构。 图4-5-27所示,为可换式定位销,以便定期维修更换。
注意: 工件以圆孔定位时,与上述心轴或定位销等元件的 接触,可以看成是圆柱面与圆柱面的接触。这时,接触 面 的长短不一样,所限制自由度的数目也不一样. (1)接触面较长 如图4-5-28中(a),H≈Ha 这时算作 长销,相当于四个定位支承点,限制四个自由度X.Y
幻灯片 9
2.定位分析小结 (1)工件在夹具中定位正确与否,可先将各式各样的 定位元件转化成支承点,然后按定位基本原理来分析。 (2)工件应该消除的自由度数目,由工件在该工序的加 工要求所决定。但是,有时为了安全可靠或减少夹紧力 等,定位元件实际限制工件自由度数目可多于按工序要 求必需消除的自由度数目,如图4-5-17但不包括重复定位 情况。 (3)根据加工要求,采用“完全定 位”、“准定位”都是合理的,“欠定 位”是不允许的。 当支承点数目虽然等于或多于需要 消除的自由度数目,但并未完全限 制应消除的自由度时,仍属于“欠 定位”,甚至即是“欠定位”又是 “过定位”。
例,图4-5-14齿轮坯上作为定位基准的 内孔和端面,往往是在一次装夹中一同加 工出来的,内孔和端面具有很高的垂直度。 虽然X.Y被重复限制,但因为定位基准之 间保证了较高的位置精度,并不会引起相干
幻灯片 10
实质上,这时所限制的自由度,仍然只有五个X.Y.Z.X.Y 并非七个。由此可见,象这种只不过是形式上的过定位,实际上 是完全可用的。 b根据定位基本定律的分析已属过定位,而且重复限制相同自 由度的定位支承点之间,又存在严重的干涉和冲突,以致造成工 件或夹具的变形,从而明显影响定位精度,则对这种类型的过定 位,严禁采用。 例图4-5-15所示,图4-5-16所示
工件在夹具中的精度分析

工件在夹具中的精度分析
在夹具设计中,当结构方案拟定之后,就应对夹具的方案进行精度分析和估算;在夹具总图设计完成之后,有必要根据夹具有关元件和总图上的配合性质及技术要求等,再进行一次复算。
在夹具中造成工件工序误差的因素,来自夹具方面的有定位误差ΔD、夹具在机床上的安装误差ΔZ、导向或对刀误差ΔT,来自加工方法方面的误差ΔG有机床方面的误差、刀具方面的误差、工艺系统变形方面的误差、调整测量方面的误差等。
上述各项误差在工序尺寸方向上的分量之和就是对工序尺寸造成的加工总误差∑Δ,即
∑Δ=ΔD+Δz+ΔT+ΔG
式中各项按极大值计算。
其和应不超过该工序尺寸的公差δk,即
∑Δ=ΔD+Δz+ΔT+ΔG≤δk
上式即为误差计算不等式。
只有满足此式,才能保证加工精度。
当夹具要保证的工序尺寸怀止一个时,每个工序尺寸都要满足它自己的误差不等式。
另外,因为式中各项误差不可能同时出现最大值,故对这些随机性变量,可按概率法合成,即
∑Δ=ΔD+Δz+ΔT+ΔG≤δk2。
§4.2 工件在夹具中的定位
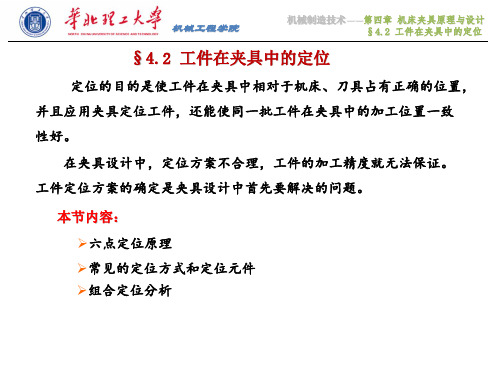
标准化,斜面夹角
有60°90°120°。 长V形块定位限制工
件四个自由度:短V
形块定位限制工件 二个自由度。
机械工程学院
机械制造技术——第四章 机床夹具原理与设计 §4.2 工件在夹具中的定位
定位套筒
结构简单,但定心精度不高,当工件外圆与定位孔配合较松时,
还易使工件偏斜,因而常采用套筒内孔与端面一起定位,以减少偏斜。若工 件端面较大,为避免过定位,定位套应做短些。长定位套限制工件四个自由 度;短定位套限制工件四个自由度。
如图所示,用六个定位支承点与工件接触,并保证定位支承点合理分布,
每个定位支承点限制工件的一个自由度,便可将工件六个自由度完全限制, 工件在夹具中的位置就被唯一确定,即要使工件完全定位,就必须限制工件
在空间的六个自由度——“六点定位原理”。
机械工程学院
机械制造技术——第四章 机床夹具原理与设计 §4.2 工件在夹具中的定位
4.2.3 组合定位分析
工件的形状千变万化各不相同,不能用单一定位元件定位单个表面就可解决定位 问题,而是要用几个定位元件组合起来同时定位工件的几个定位面。因此一个工件在 夹具中的定位,实质上就是把前面介绍的各种定位元件作不同组合来定位工件相应的 几个表面,以达到工件在夹具中的定位要求,对这种定位的分析就是组合定位分析。 组合定位分析要点 a)几个定位元件组合起来定位一个工件相应的几个定位面,该组合定位元件能 限制工件的自由度总数等于各个定位元件单独定位各自相应定位面时所能限制的 自由度的数目之和,不会因组合后而发生数目上的变化,但它们限制了哪些方向 的自由度却会随不同组合情况而改变。 b)组合定位中,定位元件在单独定位某定位面时原起限制工件移动自由度的作 用可能会转化成起限制工件转动自由度的作用。但一旦转化后,该定位元件就不
第二章 工件在夹具中的定位与工件的夹紧

第二章工件在夹具中的定位§2.1 概述1.定位的概念本门课研究的是专用夹具,定位就专门研究工件在专用夹具中的定位,而专用夹具加工的是一批工件,所以定位就专门研究一批工件在专用夹具中的定位。
由工艺课中所讲定位的概念来分析:定位:工件加工前,在机床或夹具中占据某一正确加工位置的过程。
↓工件加工前,在夹具中占据某一正确加工位置的过程。
↓指一批工件先后装到夹具中,都能占据一致正确加工位置的过程。
↓一致在坐标系中就是确定定位:工件加工前,在夹具中占据“确定”、“正确”加工位置的过程。
怎样才算“确定”、“正确”,是本章要讲的主要内容。
2.基准的概念⑴基准:零件上用以确定其它点、线、面位置所依据的要素(点、线、面)。
⑵设计基准:在零件图上用以确定点、线、面位置的基准。
由产品设计人员确定。
⑶工序基准:工序图上用以确定被加工表面位置的基准。
查找:首先找到加工面,确定加工面位置的尺寸就是工序尺寸,其一端指向加工面,另一端指向工序基准。
见图2.1所示键槽为加工面,h、L 、为三个方向的工序尺寸,三个方向上的中心线为工序基准。
工序基准由工艺人员确定。
⑷定位基准:确定工件在夹具中位置的基准,即与夹具定位元件接触的工件上的点、线、面。
当接触的工件上的点、线、面为回转面、对称面时,称回转面、对称面为定位基面,其回转面、对称面的中心线称定位基准。
定位基准由工艺人员确定,是工序图上标“”所示的基准(定位基准的标注形式见附表1)。
(5) 对刀基准:确定刀具相对夹具(工件)位置的夹具上的基准,一般选与工件定位基准重合的夹具定位元件上的要素为对刀基准。
3.工件尺寸精度获得的方法⑴试切法:试切→测量→调刀,反复进行,达到要求,工件单件加工时用。
⑵定尺寸刀具法:由刀具尺寸确定加工要素尺寸。
⑶调整法:事先调整好刀具与工件(夹具)的相对位置,在加工一批工件过程中,刀具位置不变。
本门课中涉及尺寸精度获得的方法一般视为调整法。
⑷自动控制法:通过自动控制机床、刀具的运动,达到尺寸精度的方法。
工件加工过程中的定位原理是什么

在进行机械生产加工的过程中,为了保证工件的位置精度和调整法获得尺寸精度时,工件相对于机床与刀具需要存在一个正确位置,这个位置就是我们提到的生产中的定位。
生产中我们经常用到的定位方式有:直接找正、划线找正以及用夹具装夹。
本文就来为大家介绍一下工件定位中的原理。
1、六点定则工件在夹具中的定位的目的,是要让同一工序中的所有工件,加工时按照加工要求在夹具中占有正确的位置。
怎样才能让工件按照加工要求在夹具中保持正确的位置呢?任意工件在夹具中未定位前,可以看成空间直角坐标系中的自由物体,它可以沿着三个坐标轴平行方向放在任意位置,这三个坐标轴移动的自由度为X、Y、Z;工件沿三个坐标轴转角方向的位置也是可以任意放置的,即具有绕三个坐标轴转动的自由度X,Y,Z。
所以,要使工件在夹具中占有一致的正确位置,必须限制工件的六个自由度。
为了限制工件的自由度,在夹具中通常会用一个支承点限制工件的一个自由度,这样用合理布置的六个支承点来限制工件的六个自由度,使工件的位置完全确定。
2、对定位的错误理解很多人认为工件在夹具中被夹紧了,没有自由度,工件也就定位了。
在生产中的定位,就是在夹紧前在夹具中按照加工要求占有一致的正确位置,而夹紧是在任何位置,不能保证各个工件在夹具中处于同一位置。
另一种错误的理解是,工件定位后,仍具有沿定位支承相反的方向移动的自由度。
因为工件的定位是以工件的定位基准面与定位元件相接触为前提条件,如果工件离开了定位元件也就不成为定位,也就谈不上限制其自由度了。
3、工件定位时应限制的自由度与加工要求的关系工件不需要限制自由度而没有限制的定位,称为不完全定位。
不完全定位在加工中是被允许的。
在考虑定位方案时,为了简化就夹具结构,对不需要限制的自由度,一般不设置定位支承点。
工件在夹具中的加工误差及夹具误差估算

在下图(a)所示工件上铣缺口,加工尺寸为 A和B。下图(b)所示为加工示意图,加工尺寸A 的工序基准是F面,定位基准是E面,两者不重合。 刀具相对于夹具的对刀尺寸C,在加工过程中是 不变的。由于一批工件中尺寸S的公差δS 使F面(工序基 准)的位置在一定 范围内变动,从而 使加工尺寸A产生 误差,这个误差就 是基准不重合误差。
基准不重合误差为:
B Amax Amin Smax Smin S
S是定位基准和工序基准间的距离尺寸,称为定 位尺寸。当工序基准的变动方向与加工尺寸的方向相 同时,基准不重合误差等于定位尺寸的公差,即
B S
当工序基准的变动方向与加工尺寸方向不同,其 夹角为α时,基准不重合误差为:
B S cos
② 基准位移误差 当工序基准与定位基准相同时,由于定位副
的制造误差和最小间隙配合引起定位基准位置变 动,从而造成的加工误差,称为基准位移误差, 用ΔY表示。
如下图所示,工件以圆柱孔在芯轴上定位,在圆 柱面上铣键槽,加工尺寸为A和B。
加工尺寸A的定位基准和工序基准都是内孔
轴线,两者重合,基准不重合误差ΔB=0。但由 于工件内孔和芯轴有制造误差和最小配合间隙,
一般来说,用试切法加工工件时,不会引起 定位误差,但是用调整法加工工件时,则会引起 定位误差。
(1)定位误差的产生原因
工件在夹具中定位时,造成定位误差的原因 有两个:基准不重合误差和基准位移误差。
① 基准不重合误差 基准不重合误差是指由于工件的工序基准和定位
基准不重合而造成的加工误差,用ΔB表示。
2.夹紧误差ΔJ
夹紧误差ΔJ是指工件在夹紧变形时产生的误差, 其大小是工件基准面至刀具调整面之间距离的最大 与最小尺寸之差。
它包括工件在夹紧力作用下的弹性变形、夹紧 时工件发生的位移量或偏转量、工件定位面与夹具 支承面之间的接触部分的变形等。当夹紧力方向、 作用点和大小合理时,夹紧误差近似为零。
- 1、下载文档前请自行甄别文档内容的完整性,平台不提供额外的编辑、内容补充、找答案等附加服务。
- 2、"仅部分预览"的文档,不可在线预览部分如存在完整性等问题,可反馈申请退款(可完整预览的文档不适用该条件!)。
- 3、如文档侵犯您的权益,请联系客服反馈,我们会尽快为您处理(人工客服工作时间:9:00-18:30)。
第二节 工件在夹具中的定位 4. 过定位:工件的同一自
由度被二个或二个以上的 支承点重复限制的定位。 可能造成工件的定位误差, 或者造成部分工件装不进 夹具的情况。过定位不是 绝对不允许,要由具体情 况决定。
举例:
第二节 工件在夹具中的定位
第二节 工件在夹具中的定位
第二节 工件在夹具中的定位
根据定位误差产生的原因,定 位误差是基准不重合误差与基准位 移误差向量合成。可表示为:
D C W
在具体计算时,先分别求出 εC 和 εW 的大小并确定方向, 然后按公式将两项合成即得定位误差 εD 。一般情况下定位误 差的大小为:
ε D C W
第二节 工件在夹Байду номын сангаас中的定位
三、定位误差分析与计算
前面几部分内容中,我们讨论了根据工件的加
工要求,确定工件应被限制的自由度、正确定位以 及典型表面的定位方法及元件等问题。 但还没讨论工件安装在夹具中加工是否能满足 工件加工精度的要求,要解决这一问题,需要进行 工件定位误差的分析和计算来判断。
第二节 工件在夹具中的定位 (一) 定位误差分析 何为 定位误差?
W O1O 2 OO 1 OO 2 Dmax d min Dmin d max
2 2
第二节 工件在夹具中的定位
对刀尺寸
基准位移 误差εW
W O1O 2 OO 1 OO 2 Dmax Dmin d max d min
2 2
第二节 工件在夹具中的定位
在实现定心的同时,能将工件夹紧的机构,称为定心 夹紧机构,如三爪自定心卡盘、弹簧夹头等。
第二节 工件在夹具中的定位
第二节 工件在夹具中的定位
第二节 工件在夹具中的定位 (三) 常见的定位分析 1. 完全定位:加工中工件的6个自由度须完全约束
第二节 工件在夹具中的定位 2. 不完全定位:按加工要求,允许有一个或几个自由度不
第二节 工件在夹具中的定位
第二节 工件在夹具中的定位
V形块工作面间的夹角常取60°、90°、120°三种,其中 90°V形块应用的最多。90°V形块的典型结构和尺寸已标准化, 使用时可根据定位圆柱面的长度和直径进行选择。 V形块结构有多种形式,图a)用于较短的经过加工的外圆面 定位;图b)用于较长的未经加工的圆柱面定位;图 c)用于较长 的加工过的圆柱面定位。
被限制的定位。不完全定位是合理的定位方式,在实际生产 中,工件被限制的自由度数一般不少于三个。
第二节 工件在夹具中的定位
短圆柱销
侧挡销
完全定位
平面支承
不完全定位
连杆加工定位方案
第二节 工件在夹具中的定位 3. 欠定位:按工序的加工要求,工件应该限制的自由度而未
予限制的定位。欠定位是绝对不允许的!
第二节 工件在夹具中的定位 (二) 常见的定位方法与定位元件
典型表面的定位方法
工件的定位表面有各种形式,如平面、外圆、内孔等,对于这
些表面,总是采用一定结构的定位元件。常见的定位方法有:平 面定位、圆孔定位、外圆柱面定位、组合表面定位等。
定位元件的设计应满足下列要求:
⑴ 要有与工件相适应的精度; ⑵ 要有足够的刚度,不允许受力后发生变形; ⑶ 要有耐磨性,以便在使用中保持精度。一般多采用低碳钢渗 碳淬火或中碳钢淬火,硬度为58∼62HRC。
第二节 工件在夹具中的定位
第二节 工件在夹具中的定位
第二节 工件在夹具中的定位
圆锥销的结构如图所示,图a)的结构用于未经加工的孔定位; 图 b)的结构用于已加工孔的定位;图 c)所示形式为浮动圆锥 销,用于工件需平面和圆孔同时定位的情况。
第二节 工件在夹具中的定位
第二节 工件在夹具中的定位
第二节 工件在夹具中的定位
定位误差的来源主要有两个方面:定位基准和设计基 准不重合误差和定位基准位移误差组成,分别简称为基准 不重合误差εC和基准位移误差(基准位置误差)εW 。 一般认为如果工件的定位误差不大于工件加工尺寸公差
值的1/3,该定位方案就能满足本工序加工精度的要求。即:
1 定位误差的设计准则是: D T 3
对刀尺寸
基准位移 误差εW
W
TD Td O1O 2 OO 1 OO 2 2 2
从式中可以看出基准 位移误差是由定位副 的制造误差造成的。
第二节 工件在夹具中的定位 由上面的分析,可以得到如下结论: ① 定位误差只产生在按调整法加工一批工件的 情况下,用试切法加工时,不存在定位误差; ② 定位误差(包括基准不重合误差和基准位移 调整法是一种加工前按规定的尺寸调整好刀 误差)都与工件的定位方式有关。 试切法就是通过对工件试切、测量、调整刀
具与工件相对位置及进给行程,从而保证在加工 具再试切的反复过程,使工件的实际尺寸达到合 时自动获得所需距离尺寸精度的加工方法。这种
格的机加工方法。在普通机床上进行单件或小批 加工方法在加工时不再试切。生产率高,用于大 量生产时广泛采用这种方法获得尺寸精度。 批量生产。
第二节 工件在夹具中的定位 (二) 典型定位形式定位误差的计算
工件以平面定位时,可不考虑基准位移误差
εW
第二节 工件在夹具中的定位
例1:按图所示的定位方案铣工件上的台阶面 C,试分析和计 算工序尺寸(20±0.15)mm的定位误差,并判断这一方案是 否可行。
D
1 T? 3
第二节 工件在夹具中的定位
解: B 面为定位基准,而 C 面的设计 基准为 A面,两者不重合,所以存 在基准不重合误差。设计基准和 定位基准之间的联系尺寸是 40±0.14mm ,因此基准不重合误
第二节 工件在夹具中的定位
第二节 工件在夹具中的定位
支承板:支承板用于面积较大、经过加工的平面定位,有不带
斜槽和带斜槽两种。其中带斜槽的支承板,便于清除切屑,采 用较多;不带斜槽的支承板则主要用于侧面定位。
第二节 工件在夹具中的定位
第二节 工件在夹具中的定位
第二节 工件在夹具中的定位 圆柱定位销的结构:
第二节 工件在夹具中的定位
第二节 工件在夹具中的定位
用于面积较小、 且经过加工的平 面定位。
用于未经过加 工的平面定位。
用于侧 面定位 或未经 过加工 的平面 定位。
第二节 工件在夹具中的定位
可调支承是顶端位置可在一定高度范围内调整的支承。多用于未加 工平面的定位,以调节和补偿各批毛坯尺寸的误差,一般每批毛坯 调整一次。
第二节 工件在夹具中的定位
第二节 工件在夹具中的定位
销1、销2其中一个 使用菱形销!!
第二节 工件在夹具中的定位 消除过定位及其干涉的两种途径:
a) b) 改变定位元件的结构,以消除被重复限制的自由度。 提高工件定位基面之间及定位元件工作表面之间的位
置精度,以减小或消除过定位引起的干涉。
第二节 工件在夹具中的定位
εD C W
若基准不重合和基准位移引起的加工尺寸变化方向相同时,取 “+”号,反之取“-”号。(这种情况只出现在以曲面定位的情况)
第二节 工件在夹具中的定位 1.工件以平面定位时定位误差εD的计算
工件以平面定位时,由于定位副容易制造得准
确,可视εW =0;若工件以粗基准定位,则工序尺寸 的公差值很大(远>εW ),也可视εW =0。故只计算 εC即可。 因此:
定位误差是由于工件在夹具上(或
机床上)的定位不准确而引起的加工误 差。
第二节 工件在夹具中的定位
例如: 在轴上铣键槽,要保证尺寸H。若采用V形块定位,键槽铣刀按 尺寸H调整好位置,由于工件外圆直径有公差,使工件中心位置发生 变化,造成加工尺寸H发生变化(若不考虑加工过程中产生的其它加 工误差)。此变化量(即加工误差)是由于工件的定位而引起的,故 称为定位误差,用εD表示。
第二节 工件在夹具中的定位
定位的目的是使工件在夹具中相对于机
床、刀具占有确定的正确位置,并且应用夹
具定位工件,还能使同一批工件在夹具中的
加工位置一致性好。
在夹具设计中,定位方案不合理,工件
的加工精度就无法保证。工件定位方案的确
定是夹具设计中首先要解决的问题。
第二节 工件在夹具中的定位
一、基准的概念
差εC =0.28mm。
工件以平面定位尺寸不考虑基准 位移误差,所以:
第二节 工件在夹具中的定位 1.基准不重合误差εC
例如:工件以底面定位铣 台阶面,要求保证尺寸 a 。 刀具的位置按定位面到刀 具端面间的距离 c (调整 尺寸)调整,由于一批工 件中尺寸 b 的公差使工件 顶面(设计基准)位置在 一范围内变动,从而使加 工尺寸a产生误差。
设计基准
c
定位基准
基准不重合误差 εC为定位基准和设 计基准之间联系尺寸的公差,如图 中尺寸b的公差
又可分为: ① 定位基准:在加工中使工件在机床夹具上占有正确位 置所采用的基准; ② 度量基准:在检验时所使用的基准; ③ 装配基准:装配时用来确定零件或部件在机器中位置 所采用的基准。
第二节 工件在夹具中的定位
如图所示铣削加工 C 面,保证尺 寸 20±0.15mm,则:A面为设
计基准;B面为定位基准。
第二节 工件在夹具中的定位 2.基准位移误差εW
零件上定位 基准(面) 不准确
基准位移误差(εW)
夹具上定位 元件不准确
第二节 工件在夹具中的定位
对刀尺寸
基准位移 误差εW
心 轴 :d
m ( m Td )
工 件 内 孔 :D
n TD n
第二节 工件在夹具中的定位
对刀尺寸
基准位移 误差εW
如图所示心轴定位时,定位基准 为锥面中心线,定位基准面为锥
面。
第二节 工件在夹具中的定位
二. 定位原理
任何未定位的工件在空间直角坐标系中都具有六个 自由度,即沿三个坐标轴的移动和绕三个坐标轴的转 动。因此,要使工件在夹具中占有一致的正确位置, 就必须对工件的自由度加以限制。