注塑模具里都有什么
注塑模具结构及设计-8(斜顶_强脱)
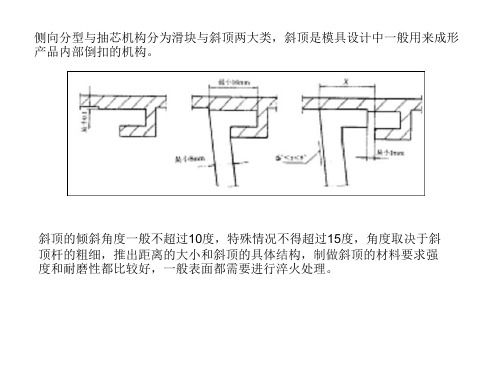
在设计斜顶结构时,要注意产品的侧定位,防止 产品随斜顶走,产生侧抽不良。
当在斜顶的 后面有顶杆 时,如果两 者靠的太近, 在顶出时斜 顶与顶杆可 能会产生干 涉。
斜斜顶是通 过改变导滑 块里滑槽的 方向,使斜 顶相对于产 品的移动方 向改变,来 避免斜顶对 产品铲胶。
产品的倒 扣处需要 斜顶抽芯 才能出模
斜顶设计 方案一: 倒扣的大 部分成型 在斜顶里 面。
缺点:斜 顶侧向抽 芯时产品 的倒扣根 部处容易 产生撅白 或折断。
斜顶设计方案二:倒扣的一部分成型在模芯里 面,而斜顶仅仅只侧抽芯防碍出模的部分。
分体式的斜顶头和斜顶杆之间可以采用 键槽,燕尾槽,定位销,螺纹等多种形 式来定位连接。
分体式的斜顶头和 斜顶杆,可以 做成
头部和杆部粗细大 小不一样的情况, 把斜顶头和斜顶杆 分开加工。
3°
3°
分体式的斜顶头和斜Байду номын сангаас杆,可以
由一个斜顶头和两个斜顶杆组成。 对于这类斜顶很难保证斜顶杆的 角度和斜顶头的角度精度一致, 为了防止角度不一致时防碍斜顶 顶出和出毛刺,通常将斜顶头的 三面加上角度,使斜顶头的背面 15°的角度比斜顶杆的角度大一点。
动,定模分开。
顶出初始阶段,外侧型腔和产品一起 向上走,内侧的型芯相对产品向下走, 为强制脱模让出空间。
强制顶出时,制品为脱出倒扣向内变形。
脱出倒扣后,制品又弹性恢 复到原来的形状,可以完整 顺利的取出制品。
侧向分型与抽芯机构分为滑块与斜顶两大类,斜顶是模具设计中一般用来成形 产品内部倒扣的机构。
注塑模具常用材料
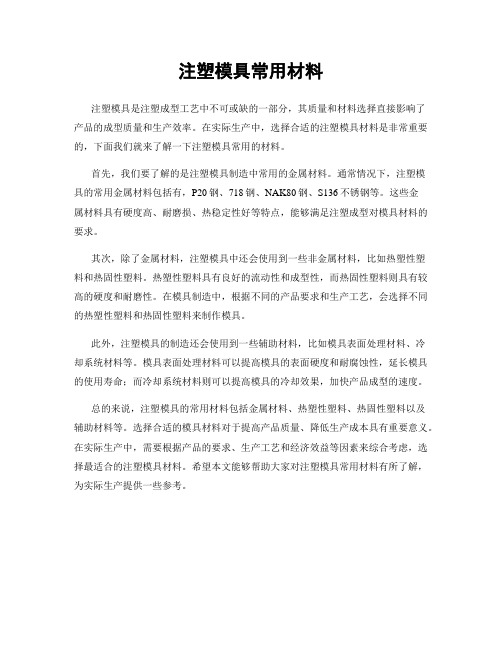
注塑模具常用材料
注塑模具是注塑成型工艺中不可或缺的一部分,其质量和材料选择直接影响了
产品的成型质量和生产效率。
在实际生产中,选择合适的注塑模具材料是非常重要的,下面我们就来了解一下注塑模具常用的材料。
首先,我们要了解的是注塑模具制造中常用的金属材料。
通常情况下,注塑模
具的常用金属材料包括有,P20钢、718钢、NAK80钢、S136不锈钢等。
这些金
属材料具有硬度高、耐磨损、热稳定性好等特点,能够满足注塑成型对模具材料的要求。
其次,除了金属材料,注塑模具中还会使用到一些非金属材料,比如热塑性塑
料和热固性塑料。
热塑性塑料具有良好的流动性和成型性,而热固性塑料则具有较高的硬度和耐磨性。
在模具制造中,根据不同的产品要求和生产工艺,会选择不同的热塑性塑料和热固性塑料来制作模具。
此外,注塑模具的制造还会使用到一些辅助材料,比如模具表面处理材料、冷
却系统材料等。
模具表面处理材料可以提高模具的表面硬度和耐腐蚀性,延长模具的使用寿命;而冷却系统材料则可以提高模具的冷却效果,加快产品成型的速度。
总的来说,注塑模具的常用材料包括金属材料、热塑性塑料、热固性塑料以及
辅助材料等。
选择合适的模具材料对于提高产品质量、降低生产成本具有重要意义。
在实际生产中,需要根据产品的要求、生产工艺和经济效益等因素来综合考虑,选择最适合的注塑模具材料。
希望本文能够帮助大家对注塑模具常用材料有所了解,为实际生产提供一些参考。
注塑模具基础小知识

三、模具的基本加工过程
●模具常用加工设备:CNC数控加工,线切割(快走丝,慢走丝), 模具常用加工设备: 数控加工, 数控加工 线切割(快走丝,慢走丝),
火花机,铣床,车床,磨床,钻床; 火花机,铣床,车床,磨床,钻床; ●模具从设计到第一次试模过程:分析产品→定出模芯尺寸 模具从设计到第一次试模过程:分析产品 定出模芯尺寸 定出模芯尺寸→ 模具从设计到第一次试模过程 由模芯尺寸及抽芯机构定出模架规格→至此,先发模芯数据及 由模芯尺寸及抽芯机构定出模架规格 至此, 至此 模架规格给专业模架厂定材料→模具局部细化设计 模具局部细化设计→模具细化设 模架规格给专业模架厂定材料 模具局部细化设计 模具细化设 计完成(包括分模及拆铜公),模架,模芯材料到位→根据分模 ),模架 根据分模, 计完成(包括分模及拆铜公),模架,模芯材料到位 根据分模, 模芯,行位,斜顶,镶块等发CNC加工 同步模架传统加工→ 加工→同步模架传统加工 模芯,行位,斜顶,镶块等发CNC加工→同步模架传统加工→ 模芯CNC加工完成 模芯电火花加工 模芯手工抛光 前后模配模 加工完成→模芯电火花加工 模芯手工抛光→前后模配模 模芯 加工完成 模芯电火花加工→模芯手工抛光 →模具整体组装 第一次试模 模具整体组装→第一次试模 模具整体组装
二板模浇注系统
三板模浇注系统
四、排气系统
注塑机熔融的液态胶从喷嘴到主流道,分流道,次分流道, 注塑机熔融的液态胶从喷嘴到主流道,分流道,次分流道, 到浇口,再进入型腔,当填充到整个型腔的末端, 到浇口,再进入型腔,当填充到整个型腔的末端,通常容易 产生末端困气的问题,会使产品产生表面气纹或缺胶; 产生末端困气的问题,会使产品产生表面气纹或缺胶; 根据产品的特点,大产品, 根据产品的特点,大产品,料流时间长的一般都需要开排 气槽,排气槽的数据大小通常在5个丝以下 个丝以下, 气槽,排气槽的数据大小通常在 个丝以下,具体需要根据不 同塑料的流动特性决定,流动性好的通常2-3个丝就够了 个丝就够了。 同塑料的流动特性决定,流动性好的通常 个丝就够了。 因分型面的配合度是靠模具师傅通过红丹手工打磨配合的, 因分型面的配合度是靠模具师傅通过红丹手工打磨配合的, 是不存在整个分型面都能达到0对 的配合的 的配合的, 是不存在整个分型面都能达到 对0的配合的,故通常第一次 试模通常都不开排气槽,试模首件如有困气问题, 试模通常都不开排气槽,试模首件如有困气问题,再确定开 排气槽的位置。 排气槽的位置。
注塑模具基础知识

注塑模具介绍—排气系统
排气系统:各个零件之间的配合间隙就是模具的排气系统, 当这些间隙不能满足要求时,就需要额外加排气槽排气,如 上图所示排气槽。有时,需要在模具的特殊位置用烧结金属 (蜂窝煤式金属合金)制作排气入子。
模具加工工艺
热处理:模具中常用的热处理方式有: 调质、淬火、回火、表面渗碳、表面渗 氮等。
表面处理:主要是对应与产品表面的咬 花处理。活動零部件的表面塗層處理。
抛光:模具上的抛光主要应用与产品表 面要求的抛光位置;深肋位,产品脫模 不顺的地方等。
磨床:主要有圆磨床和平面磨床。一般加工精度在 0.005mm。
圆磨床加工导柱、销钉、顶针、圆型芯等圓形零件。
平面磨床主要進形零件的平面加工,也可利用治具加工零 件外圓。
模具加工工艺—钻床
钻床:钻床加工精度一般都只要求在0.1mm。主要 加工水路、顶针过孔、螺丝过孔等。
模具加工工艺—CNC
热流道的优点: 1、热流道集合了两板模和三板模
的优点,并拥有很多不可比拟的 优点。 2、热流道模具可以做到没有流道, 节省流道消耗物料,不需要冷却 流道,不需要等待塑料计量,大 大节省成型周期。 热流道的缺点:热流道结构复杂, 维修困难;需要成型机外接设备 (如温控箱、外接气管);成品 高;只适用于大批量生产。
模具加工工艺
塑胶模具常用加工及处理方法: 车、镗、铣、磨、钻、CNC、电火花、 线切割、热处理、表面处理、抛光等。
模具加工工艺—车床
车床:加工精度一般0.02mm。加工圓 形零件及零件上的圓形結構。
注塑模具加工工艺及流程

注塑模具加工流程开料:前模料、后模模料、镶件料、行位料、注塑工斜顶料;开框:前模模框、后模模框;注塑模具加工厂;开粗:前模模腔开粗、后模模腔开粗、分模线开粗;铜公:前模铜注塑模具材料公、后模铜公、分模线清角铜公;线切割:镶件分模线、铜公、斜顶枕位;电脑锣:注塑模具精锣分模线、精锣后模模芯;电火花:前模粗、铜公、公模线清角、后模骨位、枕位注塑人才网;钻孔、针孔、顶针;行位、行位压极;斜顶复顶针、注塑模具加工厂配顶针;其它:①唧咀、码模坑、垃圾钉(限位钉);②飞模;③水口、撑头、弹簧、注塑模具成本分析运水;省模、抛光、前模、后模骨位;细水结构、拉杆螺丝拉钩、弹簧注塑xx淬火、行位表面氮化;修模刻字。
模具设计知识一、设计依据尺寸赫斯基注塑ehs精度与其相关尺寸地正确性。
根据塑胶制品地整个产品上地具体要和功能来确定其外面质量和具体注塑工艺流程尺寸属于哪一种:外观质量要求较高,尺寸精度要求较低地塑胶制品,如玩具;功能性塑胶制品,尺寸要求严格;外观与尺寸都要求很严地塑胶制品,如照相机。
xx注塑脱模斜度是否合理。
脱模斜度直接关系到塑胶制品地脱模和质量,即关系到注射过程中,注射是否能顺利进行:脱模斜度有足够;斜度要与塑胶制品在成型地分模或低温注塑材料分模面相适应;是否会影响外观和壁厚尺寸地精度;是否会影响塑胶制品某部位地强度注塑产品伤痕修复机。
二、设计程序对塑料制品图及实体(实样)地分析和消化:A、制品注塑技术地几何形状;&中国注塑nbsp;&n注塑工bsp;B、尺寸、公差及设计基准;&中国注塑网nbsp;&n苏州注塑公司bsp;C、技术要求;&注塑模具成本分析nbsp;D、塑料名称、牌号&nbs参观注塑车间p;注塑上下料机器人E、表面要求型腔数量和型腔排列:A、制品重量与注射机地注射量;B、制品地投影面积与注射机地锁模力;C、模具外形尺寸与注射机安装模具地有效面积,注塑成型机(或注射机拉杆内间距)D、制品精度、颜色;增强pa9t注塑温度;宝源注塑机械E、制品有无侧轴芯及其处理方法;F、制品地生产批量;&nb什么是注塑sp;&nbs中国注塑人才网p;G、经济效益(每模地生产值)型腔数量确定之后,便进行型腔地排列,即型注塑工艺腔位置地布置,型腔地排列涉及模具尺寸,浇注系统地设计、浇注系统地平衡、抽芯(滑赫斯基注塑ehs 块)机构地设计、镶件及型芯地设计、热交换系统地设计,以上这些问题又与分型面及浇口位置地选双色注塑择有关,所以具体设计过程中,要进行必要地调整,以达到比较完美地设计。
注塑模具实用教程第8章注塑模结构件设计ppt课件
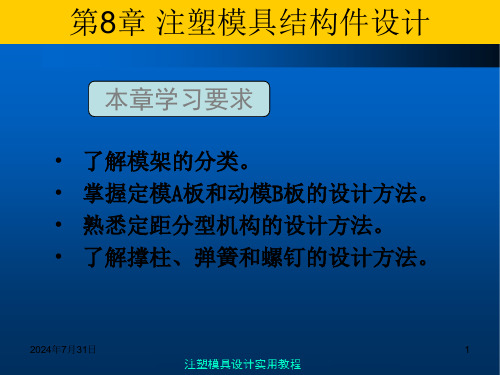
定模A板和动模B板的尺寸取决于内模镶件的外形尺寸,而内模 镶件的外形尺寸又取决于塑件的尺寸、结构特点和数量,内模镶 件设计详见第7章《注塑模具成型零件设计》。
从经济学的角度来看,在满足刚度和强度要求的前提下,模具 的结构尺寸越小越好。
确定定模A板和动模B板的尺寸常用计算法和经验法二种,在实 际工作过程中常用经验法。
2024年7月31日
20
第8章 注塑模具结构件设计
1.计算方法(相关公式见书) 2.经验确定法
模架长宽尺寸E和取决于内模镶件的长宽尺寸A和B,即A、B 板的开框尺寸。
2024年7月31日
21
第8章 注塑模具结构件设计
(1)A、B板的宽度尺寸确定。 一般来说在没有侧向抽芯
的模具中,模板开框尺寸A应大致等于模架推件固定板宽度尺寸C, 在标准模架中,尺寸C和E是一一对应的,所以知道尺寸A就可以 在标准模架手册中找到模架宽度尺寸E。
2024年7月31日
2
第8章 注塑模具结构件设计
8.1 概述
8.1.1 本章主要内容
• ① 模架的规格型号; • ② 动模板和定模板的设计; • ④ 方铁什么情况下要加高; • ⑤ 定距分型结构的设计; • ⑥ 撑柱的设计; • ⑦ 复位弹簧设计; • ⑧ 定位圈的设计; • ⑨ 紧固螺钉的设计。
2024年7月31日
29
第8章 注塑模具结构件设计
注意:① 表中的“A×B”和“框深a”均指动模板开框的长、 宽和深; ② 动模B板高度B等于开框深度a加钢厚Ha,向上取标准值 (公制一般为10的倍数); ③ 如果动模有侧抽芯,有滑块槽,或因推杆太多而无法加撑 柱时,须在表中数据的基础上再加5~10mm; ④动模板高度尽量取大些,以增加模具的强度和刚度。 动、定模板的长、宽和高度尺寸都已标准化,设计时尽量取 标准值,避免采用非标模架。
注塑模的结构

斜导柱侧向分型与抽芯塑模工作示意图6
合模,复位杆首先撞上定模 板复位,同时斜导柱进入斜 导孔,侧滑块复位
完全合模, 准备充模
8、模架
注塑模具的分类
1、按模具总体结构特征分类
1)单分型面注塑模 开模时,动、定模分开,从单一的分型面取出塑件和浇注 系统冷凝料,又称双(两)板式注射模具。
2)双分型面注塑模 有两个不同的分型面,用于分别取出塑件和冷凝料。它是 在动模板和定模板之间增加一块可往复移动的型腔板(又 称中间板或流道板),双分型面又称三板式注射模具。
2.按模具型腔的容量分类
一般把模具型腔容积达3000cm3以上的注射模称为大型注 射模。大型注射模设计与制造的难度高、造价昂贵,必须 慎重考虑塑料熔体的流动性、模具的力学特性和温度调节 系统。习惯上把模具型腔容积在100cm3及以内的注射模称 为小型注射模。介于两者之间为中型注射模。
二、注射模具的典型结构
提箱手把需人工后处理(生产效率低)
1.工作原理
A-A为第一分型面,
分型后浇注系统凝料由
此脱出;B-B为第二分
型面,分型后塑件由此
脱出。
1-支架;2-支承板;3-型芯 固定板;4-推件板;5-导柱; 6-限位销;7-弹簧;8-定距 拉板;9-型芯;10-浇口套; 11-定模座板;12-中间板(定 模板);13-导柱;14-推杆; 15-推杆固定板;16-推板
根据模具上各个部分 功能和所起作用
动模 定模
成型零部件 结构零部件
浇注系统 温度调节系统
排气系统
一、注塑模具的分类
注塑模具的组成
两大部分: 动模(安装在注射机的动模板上 ) 定模(安装在注射机的定模板上 ) 注射前动、定模在注射机驱动下闭合,形成型腔和浇注 系统,注射机将已塑化的塑料熔体通过浇注系统注入型 腔,经冷却凝固后,动定模打开,脱模机构推出塑件。
多腔注塑模具设计说明
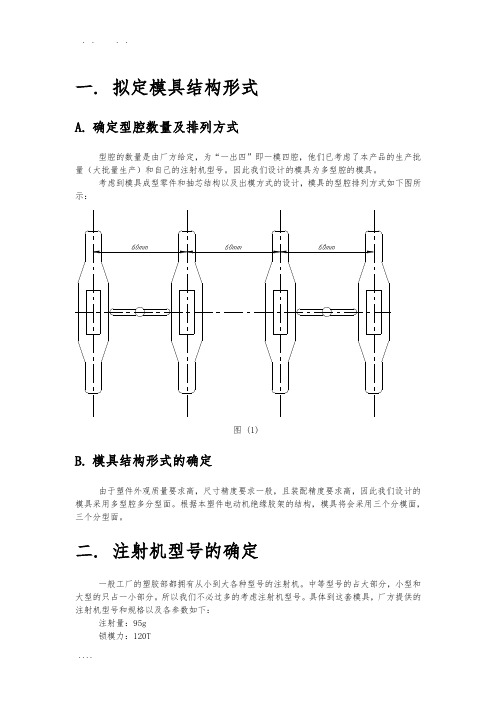
一.拟定模具结构形式A.确定型腔数量及排列方式型腔的数量是由厂方给定,为“一出四”即一模四腔,他们已考虑了本产品的生产批量(大批量生产)和自己的注射机型号。
因此我们设计的模具为多型腔的模具。
考虑到模具成型零件和抽芯结构以及出模方式的设计,模具的型腔排列方式如下图所示:图 (1)B.模具结构形式的确定由于塑件外观质量要求高,尺寸精度要求一般,且装配精度要求高,因此我们设计的模具采用多型腔多分型面。
根据本塑件电动机绝缘胶架的结构,模具将会采用三个分模面,三个分型面。
二.注射机型号的确定一般工厂的塑胶部都拥有从小到大各种型号的注射机。
中等型号的占大部分,小型和大型的只占一小部分。
所以我们不必过多的考虑注射机型号。
具体到这套模具,厂方提供的注射机型号和规格以及各参数如下:注射量:95g锁模力:120T模板大小:400×550开模距离:推出形式:推出位置:推出行程:三.分型面位置的确定如何确定分型面,需要考虑的因素比较复杂。
由于分型面受到塑件在模具中的成型位置、浇注系统设计、塑件的结构工艺性及精度、嵌件位置形状以及推出方法、模具的制造、排气、操作工艺等多种因素的影响,因此在选择分型面时应综合分析比较,从几种方案中优选出较为合理的方案。
选择分型面时一般应遵循以下几项原则:1)分型面应选在塑件外形最大轮廓处。
2)便于塑件顺利脱模,尽量使塑件开模时留在动模一边。
3)保证塑件的精度要求。
4)满足塑件的外观质量要求。
5)便于模具加工制造。
6)对成型面积的影响。
7)对排气效果的影响。
8)对侧向抽芯的影响。
其中最重要的是第5)和第2)、第8)点。
为了便于模具加工制造,应尽是选择平直分型面工易于加工的分型面。
如下图所示,采用A-A这样一个平直的分型面,前模(即定模)做成平的就行了,胶位全部做在后模(即动模),大简化了前模的加工。
A-A分型面也是整个模具的主分模面。
下图中虚线所示的B-B和C-C分型面是行位(即滑块)的分型面。
注塑模具知识大全

注塑模具的基本组成部分及分类一、注塑模具组成模具的结构虽然由于塑料品种和性能、塑料制品的形状和结构以及注射机的类型等不同而可能千变万化,但是基本结构是一致的。
模具主要由浇注系统、调温系统、成型零件和结构零件组成。
其中浇注系统和成型零件是与塑料直接接触部分,并随塑料和制品而变化,是塑模中最复杂,变化最大,要求加工光洁度和精度最高的部分。
注塑模具由动模和定模两部分组成,动模安装在注射成型机的移动模板上,定模安装在注射成型机的固定模板上。
在注射成型时动模与定模闭合构成浇注系统和型腔,开模时动模和定模分离以便取出塑料制品。
为了减少繁重的模具设计和制造工作量,注塑模大多采用了标准模架。
1.浇注系统浇注系统是指塑料从射嘴进入型腔前的流道部分,包括主流道、冷料穴、分流道和浇口等。
浇注系统又称流道系统,它是将塑料熔体由注射机喷嘴引向型腔的一组进料通道,通常由主流道、分流道、浇口和冷料穴组成。
它直接关系到塑料制品的成型质量和生产效率。
2.主流道它是模具中连接注塑机射嘴至分流道或型腔的一段通道。
主流道顶部呈凹形以便与喷嘴衔接。
主流道进口直径应略大于喷嘴直径(0.8mm)以避免溢料,并防止两者因衔接不准而发生的堵截。
进口直径根据制品大小而定,一般为4-8mm。
主流道直径应向内扩大呈3°到5°的角度,以便流道赘物的脱模。
3.冷料穴它是设在主流道末端的一个空穴,用以捕集射嘴端部两次注射之间所产生的冷料,从而防止分流道或浇口的堵塞。
如果冷料一旦混入型腔,则所制制品中就容易产生内应力。
冷料穴的直径约8-10mm,深度为6mm。
为了便于脱模,其底部常由脱模杆承担。
脱模杆的顶部宜设计成曲折钩形或设下陷沟槽,以便脱模时能顺利拉出主流道赘物。
4.分流道它是多槽模中连接主流道和各个型腔的通道。
为使熔料以等速度充满各型腔,分流道在塑模上的排列应成对称和等距离分布。
分流道截面的形状和尺寸对塑料熔体的流动、制品脱模和模具制造的难易都有影响。
塑料注塑时模具产生的模垢

塑料注塑时模具产生的模垢2011-08-25 21:17:41 发布人:一.什么是模垢,先看外观.模垢是指在模具表面上有附着物析出的一种现象.成型品表面上出现的白线便是模垢.其成分是树脂里析出的稳定剂和低分子量的聚合物.从熔融了的塑胶树脂中一点点析出并经过长时间的积累后就会形成可以看到的模垢.二.模垢的生成原因1.塑胶树脂分解首先,就附着成分而言,塑胶树脂分解后产生单体(或*低聚物).塑胶树脂分解得越多则附着物也就越多,因此提高机筒的温度设定或延长滞留时间会产生更多的模垢.2.添加物(稳定剂等)很多的塑料中一般都使用了稳定剂和润滑剂等添加剂.这些添加剂也有可能堆积成模垢.就滑动性等级等来说,向油性表面析出也是产品的特点,因此,在成型时很容易变成模垢附着在上面.3.模具温度塑胶树脂的分解物、稳定剂等都是低分子量物质,注射熔融时会发生液化或是气化.这些物质接触模具后被冷却并附着在模具上,因此模具温度对模垢有很大影响.模具温度越低,模垢就附着得越多.4.排气口模垢的起因物质在接触模具前大部分已经气化.如果能把气体高效地从模具排出,模垢也会减少.相反,如果在流动末端等处没有设置排气口,或者有排气口但是很薄,效率很低,或者排气口因模垢附着而被堵塞,模垢就会更加厉害.5.注射速度在排气口效果不大,排气不畅的情况下,模垢有时也会受到注射速度的影响.其原因是注射速度过快,气体和挥发物无法完全排出到模具外.6.预干燥就材料而言,干燥条件对模垢的影响很大.无论哪种塑料都含有单体和*低聚物(初期带入成分).即使成型时在机筒内产生的成分很少,但如果不对初期带入成分多的材料进行充分干燥,模垢就会恶化.7.回收塑料使用回收塑料也会带来很大影响.这是因为回收塑料经历了多次受热,因此比初期使用的产品含有更多的单体(或低聚物).此外,本公司推荐的混合比最高为25%.8.着色剂一般来说,为使颜料能够分散到塑料上,着色剂中含有相当数量的润滑剂.这样一来,析出到模具表面上的量也会增多,模垢也就趋向恶化.模垢的状态还会因颜色和着色方法而发生变化.9.特殊等级市面上出售的塑料材料有各种等级.为增加某些功能而添加了特殊添加剂的代价是使模垢明显增多,因此更应注意加强对此类等级的模垢管理.三.模垢的对策1.试着降低塑胶树脂温度各种塑胶树脂都有推荐的使用温度(产品目录或产品包装袋等上面均已注明).检查成型机的设定温度是否超出范围,如果超出,则请降低温度.另外,成型机上所显示的温度是传感器所处位置的温度,与实际树脂温度多少会有一些差异.如果可能,建议测量实际温度.2.缩短滞留时间即使成型机的设定温度处在各种塑胶树脂的推荐温度范围内,长时间滞留在机筒内也会使塑胶树脂渐渐分解,从而容易产生模垢.如果成型机在计量方面有延迟时间的设置功能,请灵活应用该功能.此外,使用适合成型品大小的成型机可以缩短滞留时间.3.确认干燥条件每种塑胶树脂都有相应的推荐干燥条件.请确认目前的情况是否满足这些条件.4.强化干燥条件塑胶树脂里残留有很少的模垢起因物质——单体.完全去除这些单体是很困难的.如果想严格控制模垢的产生,则可通过强化干燥条件并去除这些单体来改善模垢状况.特别是在使用回收材料时必须这样做.另外在干燥温度方面,机器温度和实际温度有时存在一定的差异.尤其要注意料斗式烘箱.5.提高模具温度模具温度偏低时模垢会增多.成形周期和尺寸管理会发生变化,温度调节器所需要的能源费用也会增多.如果要长期进行批量生产,则提高模具温度将会有效降低模垢.6.检查排气口排气口堵塞后,气体无法排出,模垢便会增多.如果排气口变脏,请清理干净.此外还应确认排气口的位置、数量以及大小是否足够.强化排气口对模垢很有效.7.回收材料的使用方法回收材料的混合比越高,模垢就产生得越多.本公司推荐25%以下的混合比.此外还必须充分进行干燥.8. 特殊等级的使用方法部分特殊等级会产生大量模垢.为了减少模垢,必须同时使用各种方法,如进行充分干燥、尽量不用回收材料、在指定的推荐温度范围内使用、加强排气口等.此外,定期进行模具维护也很重要.9.模具维护与其说模垢的附着量是按一定比例增加的,倒不如说一旦附着就会迅速增加.一般来说,刚刚附着的模垢容易去除,而随着附着量的增加,去除的难度也会增大.请定期清理模具,在模垢还没有堆积之前去除掉.在不损伤模具的情况下去除模垢是一项很困难的作业.请最好选用适合所用树脂的溶剂来进行超音波洗净.使用洗洁剂(Clipika Ace等)时请尽量用棉布和牙签擦洗.为保养起见,预先只把模腔“分解打包”也是一种好办法.<<补充说明>>*1 低聚物(oligomer)树脂材料(聚合物)是指特定的基本化学结构聚合而成的物质.市场上出售的产品的聚合次数一般在数百到数万之间.这种重复聚合的次数称为聚合度.聚合度小的聚合物称之为低聚物.由于聚合物是单体连续结合而成的,因此其聚合度的分布范围很广―― 从很低的聚合物到很大的聚合物.聚合度小的低聚物的比例虽然很小,但由于分子量小,比较容易变动和分解,这也是模垢的起因之一.。
什么是注塑模具
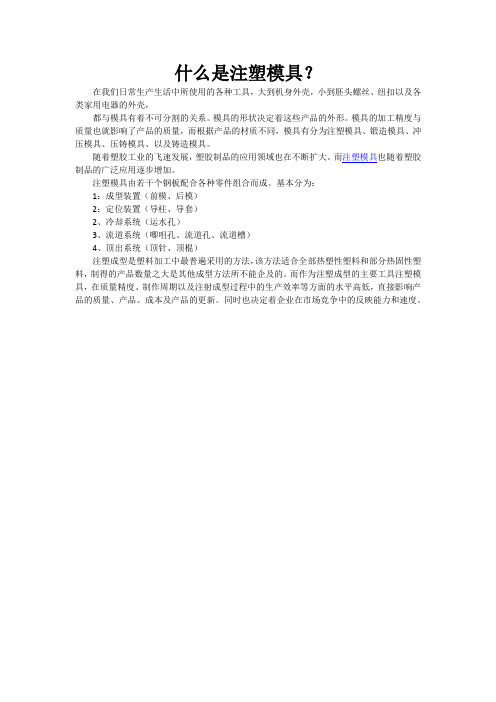
什么是注塑模具?
在我们日常生产生活中所使用的各种工具,大到机身外壳,小到胚头螺丝、纽扣以及各类家用电器的外壳,
都与模具有着不可分割的关系。
模具的形状决定着这些产品的外形。
模具的加工精度与质量也就影响了产品的质量,而根据产品的材质不同,模具有分为注塑模具、锻造模具、冲压模具、压铸模具、以及铸造模具。
随着塑胶工业的飞速发展,塑胶制品的应用领域也在不断扩大。
而注塑模具也随着塑胶制品的广泛应用逐步增加。
注塑模具由若干个钢板配合各种零件组合而成。
基本分为:
1:成型装置(前模、后模)
2:定位装置(导柱、导套)
2、冷却系统(运水孔)
3、流道系统(唧咀孔、流道孔、流道槽)
4、顶出系统(顶针、顶棍)
注塑成型是塑料加工中最普遍采用的方法,该方法适合全部热塑性塑料和部分热固性塑料,制得的产品数量之大是其他成型方法所不能企及的。
而作为注塑成型的主要工具注塑模具,在质量精度、制作周期以及注射成型过程中的生产效率等方面的水平高低,直接影响产品的质量、产品、成本及产品的更新。
同时也决定着企业在市场竞争中的反映能力和速度。
注塑模具标准件.

拉 料 杆
无头螺丝
D
L L1 L2
3
4
5
0.4左右 2.5~5
6
……
根据实际板厚确定
R
0.3~0.5
拉料杆
拉料杆
说明:拉料杆常用于三板模中,利用L距离的倒扣勾住流道料, 开模后使流道料脱离产品。如图
点 浇 口
点浇口流道 拉料杆
点浇口
点浇口
D=0.5~2 a=3~10 b=20~60 L=0.5~2
耐磨块(油板)
限位螺丝
滑 块 座
W=3~5 h=5~8 D =斜撑斜直径+1~2
a<=24 b=a+2~3 D1=弹簧直径+1
铲机、压块
h1=5~15 h=螺丝杯头高+1 D=螺丝直接+1 D1=螺丝杯头直径+1~2
耐 磨 块
说明:耐磨块的大小根据滑块座底下大小确定。
斜 撑 销
d
10
D
L
13
100 70
120 90
…… ……
D d
100 35
120 35
…… ……
说明:定位环又叫定位圈,与注塑机连接,给注塑机喷嘴定位作用。
唧 嘴
D d h:型号不 同尺寸不同, 可查看相关标 准件书,L可 根据实际需要 长度任意调整。
说明:注塑成型时唧嘴和注塑机喷嘴相接触,常见形式有销钉 和螺丝固定二种形式,如上图。
延伸唧嘴
其它形式
说明:延伸唧嘴是把定位环和唧嘴二部分做成一个整体的模具零件 其规格尺寸可参照定位环和唧嘴自行设计出所需要的规格。
说明:边锁/零度束块,是一种 模具标准零件,常用于 精密定位,成对使用。
注塑模具结构介绍
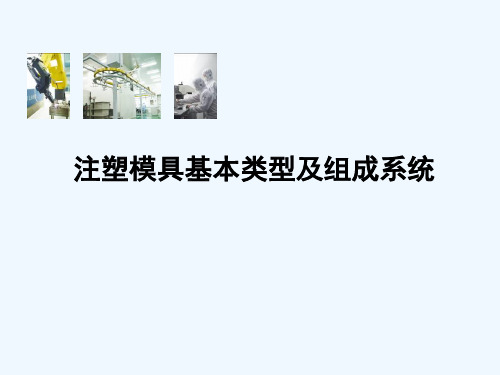
Content
一、注塑模基本类型
FAMILY MOLD实例:有3个产品型腔
Content
一、注塑模基本类型
3、按注塑材料
A、单色模
单色模是指产品只有一种注塑材料成型的模具,最常见的模具。
B、双色模
双色模是指有两种不同特性注塑材料共同成型产品的模具。
C、多色模
B、双分型面(三板模)
三板模是以不同分型面分别取出流道和塑件,与两板模相比, 三板模是在上顶板和定模A板之间增加一块脱料板,流道设计 在定模A板与脱料板之间; 三板模结构复杂、制造成本较高,需要较大的开模行程,但 浇口可以用点浇口开在塑件上方的任意位置。
Content
一、注塑模基本类型
三板模开合模:开模顺序2-3-1;合模顺序3-2-1
孔水平摆放,熔接痕在 一条线上,影响产品强度
孔垂直摆放,熔接痕分开
二、注塑模组成系统
F.常用浇口
Content
二、注塑模组成系统
Content
二、注塑模组成系统
Content
二、注塑模组成系统
Content
二、注塑模组成系统
Content
二、注塑模组成系统
Content
G. 影响流道因素: 产品材料、产品壁厚、流道排布长度、流道截面积大小;
➢对于流动性好的材料,流道尺寸可取小,反之取大; ➢流道直径大小一般取产品壁厚的 2.5~3倍; ➢为平衡注射压力损失,流道截面半径每层级相差0.5mm;
➢流道排布尽量使产品充填平衡,尽量减短流道长度,从而节约材料,提高充填效果; ➢流道设计要经过模流分析验证;
分流道
主流道
平衡排布
注塑模具冷流道系统设计手册(1)
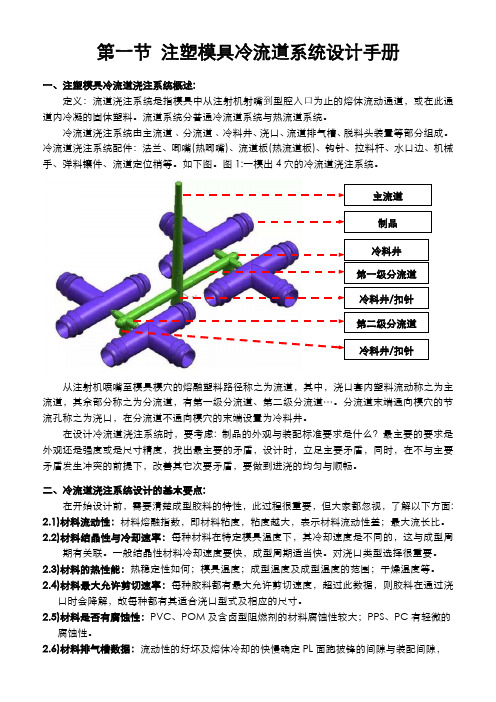
第一节 注塑模具冷流道系统设计手册一、注塑模具冷流道浇注系统概述:定义:流道浇注系统是指模具中从注射机射嘴到型腔入口为止的熔体流动通道,或在此通道内冷凝的固体塑料。
流道系统分普通冷流道系统与热流道系统。
冷流道浇注系统由主流道﹑分流道﹑冷料井、浇口、流道排气槽、脱料头装置等部分组成。
冷流道浇注系统配件:法兰、唧嘴(热唧嘴)、流道板(热流道板)、钩针、拉料杆、水口边、机械手、弹料镶件、流道定位梢等。
如下图。
图1:一模出4穴的冷流道浇注系统。
从注射机喷嘴至模具模穴的熔融塑料路径称之为流道,其中,浇口套内塑料流动称之为主流道,其余部分称之为分流道,有第一级分流道、第二级分流道…。
分流道末端通向模穴的节流孔称之为浇口,在分流道不通向模穴的末端设置为冷料井。
在设计冷流道浇注系统时,要考虑: 制品的外观与装配标准要求是什么?最主要的要求是外观还是强度或是尺寸精度,找出最主要的矛盾,设计时,立足主要矛盾,同时,在不与主要矛盾发生冲突的前提下,改善其它次要矛盾,要做到进浇的均匀与顺畅。
二、冷流道浇注系统设计的基本要点:在开始设计前,需要清楚成型胶料的特性,此过程很重要,但大家都忽视,了解以下方面: 2.1)材料流动性:材料熔融指数,即材料粘度,粘度越大,表示材料流动性差;最大流长比。
2.2)材料结晶性与冷却速率:每种材料在特定模具温度下,其冷却速度是不同的,这与成型周期有关联。
一般结晶性材料冷却速度要快,成型周期适当快。
对浇口类型选择很重要。
2.3)材料的热性能:热稳定性如何;模具温度;成型温度及成型温度的范围;干燥温度等。
2.4)材料最大允许剪切速率:每种胶料都有最大允许剪切速度,超过此数据,则胶料在通过浇口时会降解,故每种都有其适合浇口型式及相应的尺寸。
2.5)材料是否有腐蚀性:PVC 、POM 及含卤型阻燃剂的材料腐蚀性较大;PPS 、PC 有轻微的 腐蚀性。
决定加工精度及加工工艺与加工成本;每种胶料有其特定排气槽的设计数据。
注塑基础知识考题

注塑基础知识考题
1. 什么是注塑?
- 注塑是一种通过将熔化的塑料注入模具中,经凝固后形成所需产品的加工过程。
2. 注塑的主要步骤有哪些?
- 模具闭合,塑料熔化,注射,冷却,模具开启,脱模。
3. 注塑的主要原料是什么?
- 注塑的主要原料是熔融状态的塑料颗粒(塑料树脂)。
4. 注塑模具的主要部分有哪些?
- 注塑模具的主要部分包括模具基板、模腔和模芯。
5. 注塑的主要加工设备是什么?
- 注塑的主要加工设备是注塑机,主要包括注射装置、保压装置、模具闭合装置和控制系统。
6. 注塑产品的质量问题有哪些?
- 注塑产品的质量问题包括短射、气泡、热缩、脱模难、尺寸不合格等。
7. 如何提高注塑产品的质量?
- 可以通过优化产品设计、提高模具精度、优化注塑工艺参数等方式来提高注塑产品的质量。
8. 注塑加工的优点是什么?
- 注塑加工具有生产效率高、生产周期短、成本低、产品表面光洁等优点。
9. 注塑加工的缺点是什么?
- 注塑加工的缺点包括模具制作周期长、模具制作成本高、注塑机设备投资较大等。
10. 注塑技术有哪些应用领域?
- 注塑技术广泛应用于汽车、电子电器、家居用品、玩具等各个领域。
注塑模具基础知识介绍

• 三板模的缺点:
– 三板模流道比较长,需要更长的冷却时间,也 就是需要更长的成型周期。
– 三板模消耗物料多。 – 三板模相对来说结构复杂
热流道模基本结构
热流道模基本结构
热流道模基本结构
• 热流道模具,不看流道系统和两板模基本 一样,但是从流道系统来说,热流道算是 另一类注塑模具。
修改模方式
增加骨位
如果骨位较深,会影响出模和走胶就需要做镶件,加顶针;
如果骨位较浅,不影响出模和走胶,就直接打火花加工和加顶 针(根据需要)。
骨位较深改模内容
骨位较浅改模内容
评估,改图,出图
评估,改图,出图
订购镶件料,顶针
订购顶针
CNC编程订料,回来加工铜公 CNC编程订料,回来加工铜公
拆后模胚模仁
订购司筒
拆后模胚模仁
模仁打孔线割 有加强筋还需CNC编程订铜公 加工铜公打火花 B板/顶针面板/顶针底板/底板 加工 司筒回来后产品有倒角的要打 火花,没有则需做到数 装模、配模、试模
做镶针改模内容
评估,改图,出图
订购镶针、顶针
拆后模胚模仁
模仁打孔线割,做挂 台 有加强筋还需CNC编程 订铜公加工铜公打火 花B板/顶针面板加工 镶针回来后产品有倒 角的要打火花,没有 则需做到数 装模、配模、试模
• 两板模的缺点:
– 两板模除潜伏式和牛角式浇口外都需要后续加 工去除浇口。
两板模的进胶形式
牛角浇口
标准三板模基本结构
标准三板模基本结构
*三板模可用于所有类型产品; *三板模大拉杆,停止螺丝和流道长度的关系如下:
A=B+10=流道长度(C)+30左右
15:塑胶模具部件名称及材质与表面处理
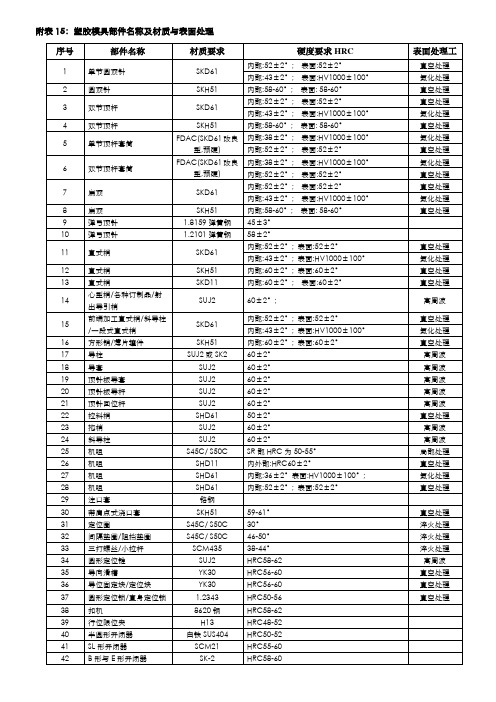
附表15:塑胶模具部件名称及材质与表面处理序号部件名称材质要求硬度要求HRC 表面处理工1 单节圆顶针SKD61 内部:52±2°; 表面:52±2° 真空处理内部:43±2°; 表面:HV1000±100° 氮化处理2 圆顶针SKH51 内部:58-60°; 表面: 58-60° 真空处理3 双节顶杆SKD61 内部:52±2°; 表面:52±2° 真空处理内部:43±2°; 表面:HV1000±100° 氮化处理4 双节顶杆SKH51 内部:58-60°; 表面: 58-60° 真空处理5 单节顶杆套筒FDAC(SKD61改良型,预硬)内部:38±2°; 表面:HV1000±100° 氮化处理内部:52±2°; 表面:52±2° 真空处理6 双节顶杆套筒FDAC(SKD61改良型,预硬)内部:38±2°; 表面:HV1000±100° 氮化处理内部:52±2°; 表面:52±2° 真空处理7 扁顶SKD61 内部:52±2°; 表面:52±2° 真空处理内部:43±2°; 表面:HV1000±100° 氮化处理8 扁顶SKH51 内部:58-60°; 表面: 58-60° 真空处理9 弹弓顶针 1.8159弹簧钢45±3°10 弹弓顶针 1.2101弹簧钢58±2°11 直式梢SKD61 内部:52±2°; 表面:52±2° 真空处理内部:43±2°; 表面:HV1000±100° 氮化处理12 直式梢SKH51 内部:60±2°; 表面:60±2° 真空处理13 直式梢SKD11 内部:60±2°; 表面:60±2° 真空处理14 心型梢/各种订制品/射出导引梢SUJ2 60±2°; 高周波15 前端加工直式梢/斜导柱/一段式直式梢SKD61内部:52±2°; 表面:52±2° 真空处理内部:43±2°; 表面:HV1000±100° 氮化处理16 方形销/薄片镶件SKH51 内部:60±2°; 表面:60±2° 真空处理17 导柱SUJ2或SK2 60±2° 高周波18 导套SUJ2 60±2° 高周波19 顶针板导套SUJ2 60±2° 高周波20 顶针板导杆SUJ2 60±2° 高周波21 顶针回位杆SUJ2 60±2° 高周波22 拉料梢SHD61 50±2° 真空处理23 拖梢SUJ2 60±2° 高周波24 斜导柱SUJ2 60±2° 高周波25 机咀S45C/ S50C SR部HRC为50-55° 局部处理26 机咀SHD11 内外部:HRC60±2° 真空处理27 机咀SHD61 内部:36±2°表面:HV1000±100°; 氮化处理28 机咀SHD61 内部:52±2°; 表面:52±2° 真空处理29 注口套铬钢30 带肩点式浇口套SKH51 59-61° 真空处理31 定位圈S45C/ S50C 30° 淬火处理32 间隔垫圈/阻挡垫圈S45C/ S50C 46-50° 淬火处理33 三打螺丝/小拉杆SCM435 38-44° 淬火处理34 圆形定位锥SUJ2 HRC58-62 高周波35 导向滑槽YK30 HRC56-60 真空处理36 导位固定块/定位块YK30 HRC56-60 真空处理37 圆形定位锁/直身定位锁 1.2343 HRC50-56 真空处理38 扣机8620钢HRC58-6239 行位限位夹H13 HRC48-5240 半圆形开闭器白铁SUS404 HRC50-5241 SL形开闭器SCM21 HRC55-6042 B形与E形开闭器SK-2 HRC58-60。
注塑模具的结构与分类

注塑模具的结构与分类注塑模的基本结构都是由定模和动模两大部分组成的。
定模部分安装在注塑机的固定板上,动模部分安装在注塑机的移动板上。
注塑成型时,定模部分和随液压驱动的动模部分经导柱导向而闭合,塑料熔体从注塑机喷嘴经模具浇注系统进入形腔;注塑成型冷却后开模,即定模和动模分开,一般情况下塑件留在动模上,模具顶出机构将塑件推出模外。
根据模具上各部件的作用不同,一般注塑模可由以下几个部分组成。
成型零部件指定模、动模部分中组成型腔的零件。
通常由型芯、凹模、镶件等组成,合模时构成型腔,由于填充塑料熔体,它决定塑件的形状和尺寸。
浇注系统浇注系统是熔融塑料从注塑机喷嘴进入模具型腔所流经的通道,它由主流道、分流道浇口和冷料井组成。
导向机构导向机构分为动模与定模之间的导向机构和顶出机构的导向机构两类。
首者是保证动模和定模在合模时准确对合,以保证塑件形状和尺寸的精确度;后者是避免顶出过程中推出板歪斜而设置的。
脱模机构用于开模时将塑件从模具中脱出的装置,又称顶出机构。
其结构形式很多,常见的有顶杆脱模机构、推板脱模机构和推管脱模机构等。
侧向分型与抽芯机构当塑件上的侧向有凹凸形状的孔或凸台时,就需要有侧向的凸模或型芯来成型。
在开模推出塑件之前,必须先将侧向凸模或侧向型芯从塑件上脱出或抽出,塑件才能顺利脱模。
使侧向凸模或侧向型芯移动的机构称为侧向抽芯机构。
加热放冷却系统为了满足注塑工艺对模具的温度要求,必须对模具温度进行控制,所以模个常常设有冷却系统并在模具内部或四周安装加热元件。
冷却系统一般在模具上开设冷却水道。
排气系统在注塑成型过程中,为了将型腔内的空气排出,常常需要开设排气系统,通常是在分型面上有目的的开设若干条沟槽,或利用模具的推杆或型芯与模板之间的配合间隙进行排气。
小型塑件的排气量不大,因此可直接利用分型而排气,而不必另设排气槽。
其他零部件如用来固定、支承成型零部件或起定位和限位作用的零部件等。
看了看注塑模具的结构下面我们来谈一谈他的分类,这边根据注塑模的结构特征对其进行分类如下单分型面注塑模开模时,动模和定模分开,从而取出塑件,称单分型面模具,又称双板式模。
- 1、下载文档前请自行甄别文档内容的完整性,平台不提供额外的编辑、内容补充、找答案等附加服务。
- 2、"仅部分预览"的文档,不可在线预览部分如存在完整性等问题,可反馈申请退款(可完整预览的文档不适用该条件!)。
- 3、如文档侵犯您的权益,请联系客服反馈,我们会尽快为您处理(人工客服工作时间:9:00-18:30)。
注塑模具里都有什么
模具的结构虽然由于塑料品种和性能、塑料制品的形状和结构以及注射机的类型等不同而可能千变万化,但是基本结构是一致的。
模具主要由浇注系统、调温系统、成型零件和结构零件组成。
其中浇注系统和成型零件是与塑料直接接触部分,并随塑料和制品而变化,是塑模中最复杂,变化最大,要求加工光洁度和精度最高的部分。
注塑模具由动模和定模两部分组成,动模安装在注射成型机的移动模板上,定模安装在注射成型机的固定模板上。
在注射成型时动模与定模闭合构成浇注系统和型腔,开模时动模和定模分离以便取出塑料制品。
为了减少繁重的模具设计和制造工作量,注塑模大多采用了标准模架。
浇注系统
浇注系统是指塑料从射嘴进入型腔前的流道部分,包括主流道、冷料穴、分流道和浇口等。
浇注系统又称流道系统,它是将塑料熔体由注射机喷嘴引向型腔的一组进料通道,通常由主流道、分流道、浇口和冷料穴组成。
它直接关系到塑料制品的成型质量和生产效率。
主流道
它是模具中连接注塑机射嘴至分流道或型腔的一段通道。
主流道顶部呈凹形以便与喷嘴衔接。
主流道进口直径应略大于喷嘴直径(0.8mm)以避免溢料,并防止两者因衔接不准而发生的堵截。
进口直径根据制品大小而定,一般为4-8mm。
主流道直径应向内扩大呈3°到5°的角度,以便流道赘物的脱模。
冷料穴
它是设在主流道末端的一个空穴,用以捕集射嘴端部两次注射之间所产生的冷料,从而防止分流道或浇口的堵塞。
如果冷料一旦混入型腔,则所制制品中就容易产生内应力。
冷料穴的直径约8-10mm,深度为6mm。
为了便于脱模,其底部常由脱模杆承担。
脱模杆的顶部宜设计成曲折钩形或设下陷沟槽,以便脱模时能顺利拉出主流道赘物。
分流道
它是多槽模中连接主流道和各个型腔的通道。
为使熔料以等速度充满各型腔,分流道在塑模上的排列应成对称和等距离分布。
分流道截面的形状和尺寸对塑料熔体的流动、制品脱
模和模具制造的难易都有影响。
如果按相等料量的流动来说,则以圆形截面的流道阻力最小。
但因圆柱形流道的比表面小,对分流道赘物的冷却不利,而且这种分流道必须开设在两半模上,既费工又不易对准。
因此,经常采用的是梯形或半圆形截面的分流道,且开设在带有脱模杆的一半模具上。
流道表面必须抛光以减少流动阻力提供较快的充模速度。
流道的尺寸决定于塑料品种,制品的尺寸和厚度。
对大多数热塑性塑料来说,分流道截面宽度均不超过8m,特大的可达
10-12m,特小的2-3m。
在满足需要的前提下应尽量减小截面积,以增加分流道赘物和延长冷却时间。
浇口
它是接通主流道(或分流道)与型腔的通道。
通道的截面积可以与主流道(或分流道)相等,但通常都是缩小的。
所以它是整个流道系统中截面积最小的部分。
浇口的形状和尺寸对制品质量影响很大。
浇口的作用是:
A、控制料流速度:
B、在注射中可因存于这部分的熔料早凝而防止倒流:
C、使通过的熔料受到较强的剪切而升高温度,从而降低表观粘度以提高流动性:
D、便于制品与流道系统分离。
浇口形状、尺寸和位置的设计取决于塑料的性质、制品的大小和结构。
一般浇口的截面形状为矩形或圆形,截面积宜小而长度宜短,这不仅基于上述作用,还因为小浇口变大较容易,而大浇口缩小则很困难。
浇口位置一般应选在制品最
厚而又不影响外观的地方。
浇口尺寸的设计应考虑到塑料熔体的性质。
型腔它是模具中成型塑料制品的空间。
用作构成型腔的组件统称为成型零件。
各个成型零件常有专用名称。
构成制品外形的成型零件称为凹模(又称阴模),构成制品内部形状(如孔、槽等)的称为型芯或凸模(又称阳模)。
设计成型零件时首先要根据塑料的性能、制品的几何形状、尺寸公差和使用要求来确定型腔的总体结构。
其次是根据确定的结构选择分型面、浇口和排气孔的位置以及脱模方式。
最后则按控制品尺寸进行各零件的设计及确定各零件之间的组合方式。
塑料熔体进入型腔时具有很高的压力,故成型零件要进行合理地选材及强度和刚度的校核。
为保证塑料制品表面的光洁美观和容易脱模,凡与塑料接触的表面,其粗糙度
Ra>0.32um,而且要耐腐蚀。
成型零件一般都通过热处理来提高硬度,并选用耐腐蚀的钢材制造。
调温系统
为了满足注射工艺对模具温度的要求,需要有调温系统对模具的温度进行调节。
对于热塑性塑料用注塑模,主要是设计冷却系统使模具冷却。
模具冷却的常用办法是在模具内开设冷却水通道,利用循环流动的冷却水带走模具的热量;模具的加热除可利用冷却水通道热水
或蒸汽外,还可在模具内部和周围安装电加热元件。
成型零件
是指构成制品形状的各种零件,包括动模、定模和型腔、型芯、成型杆以及排气口等。
成型部件由型芯和凹模组成。
型芯形成制品的内表面,凹模形成制品的外表面形状。
合模后型芯和型腔便构成了模具的型腔。
按工艺和制造要求,有时型芯和凹模由若干拼块组合而成,有时做成整体,仅在易损坏、难加工的部位采用镶件。
排气口
它是在模具中开设的一种槽形出气口,用以排出原有的及熔料带入的气体。
熔料注入型腔时,原存于型腔内的空气以及由熔体带入的气体必须在料流的尽头通过排气口向模外排出,否则将会使制品带有气孔、接不良、充模不满,甚至积存空气因受压缩产生高温而将制品烧伤。
一般情况下,排气孔既可设在型腔内熔料流动的尽头,也可设在塑模的分型面上。
后者是在凹模一侧开设深0.03-0.2mm,宽1.5-6mm的浅槽。
注射中,排气孔不会有很
多熔料渗出,因为熔料会在该处冷却固化将通道堵死。
排气口的开设位置切勿对着操作人员,以防熔料意外喷出伤人。
此外,亦可利用顶出杆与顶出孔的配合间隙,顶块和脱模板与型芯的配合间隙等来排气。
结构零件
它是指构成模具结构的各种零件,包括:导向、脱模、抽芯以及分型的各种零件。
如前
后夹板、前后扣模板、承压板、承压柱、导向柱、脱模板、脱模杆及回程杆等。
1.导向部件
为了确保动模和定模在合模时能准确对中,在模具中必须设置导向部件。
在注塑模中通常采用四组导柱与导套来组成导向部件,有时还需在动模和定模上分别设置互相吻合的内、外锥面来辅助定位。
2.推出机构
在开模过程中,需要有推出机构将塑料制品及其在流道内的凝料推出或拉出。
推出固定板和推板用以夹持推杆。
在推杆中一般还固定有复位杆,复位杆在动、定模合模时使推板复位。
3.侧抽芯机构
有些带有侧凹或侧孔地塑料制品,在被推出以前必须先进行侧向分型,抽出侧向型芯后方能顺利脱模,此时需要在模具中设置侧抽芯机构。
台州市黄岩诺航模塑有限公司坐落于“中国模具之乡”—浙江省台州黄岩模具城,台州市黄岩诺航模塑有限公司是一家专业从事设计和制造大中型塑料模具,注塑模具,塑料吹塑模具及塑料制品的厂家,用品质积累客户,致力于以做台州市黄岩模塑厂最好的厂家。
想要了解更多关于注塑模具的信息,欢迎来官网咨询留言。
出师表
两汉:诸葛亮
先帝创业未半而中道崩殂,今天下三分,益州疲弊,此诚危急存亡之秋也。
然侍卫之臣不懈于内,忠志之士忘身于外者,盖追先帝之殊遇,欲报之于陛下也。
诚宜开张圣听,以光先帝遗德,恢弘志士之气,不宜妄自菲薄,引喻失义,以塞忠谏之路也。
宫中府中,俱为一体;陟罚臧否,不宜异同。
若有作奸犯科及为忠善者,宜付有司论其刑赏,以昭陛下平明之理;不宜偏私,使内外异法也。
侍中、侍郎郭攸之、费祎、董允等,此皆良实,志虑忠纯,是以先帝简拔以遗陛下:愚以为宫中之事,事无大小,悉以咨之,然后施行,必能裨补阙漏,有所广益。
将军向宠,性行淑均,晓畅军事,试用于昔日,先帝称之曰“能”,是以众议举宠为督:愚以为营中之事,悉以咨之,必能使行阵和睦,优劣得所。
亲贤臣,远小人,此先汉所以兴隆也;亲小人,远贤臣,此后汉所以倾颓也。
先帝在时,每与臣论此事,未尝不叹息痛恨于桓、灵也。
侍中、尚书、长史、参军,此悉贞良死节之臣,愿陛下亲之、信之,则汉室之隆,可计日而待也。
臣本布衣,躬耕于南阳,苟全性命于乱世,不求闻达于诸侯。
先帝不以臣卑鄙,猥自枉屈,三顾臣于草庐之中,咨臣以当世之事,由是感激,遂许先帝以驱驰。
后值倾覆,受任于败军之际,奉命于危难之间,尔来二十有一年矣。
先帝知臣谨慎,故临崩寄臣以大事也。
受命以来,夙夜忧叹,恐托付不效,以伤先帝之明;故五月渡泸,深入不毛。
今南方已定,兵甲已足,当奖率三军,北定中原,庶竭驽钝,攘除奸凶,兴复汉室,还于旧都。
此臣所以报先帝而忠陛下之职分也。
至于斟酌损益,进尽忠言,则攸之、祎、允之任也。
愿陛下托臣以讨贼兴复之效,不效,则治臣之罪,以告先帝之灵。
若无兴德之言,则责攸之、祎、允等之慢,以彰其咎;陛下亦宜自谋,以咨诹善道,察纳雅言,深追先帝遗诏。
臣不胜受恩感激。
今当远离,临表涕零,不知所言。