微小型薄底零件的轴向车铣实验研究
微细铣削工艺基础与实验研究

微细铣削工艺基础与实验研究一、本文概述《微细铣削工艺基础与实验研究》一文旨在深入探讨微细铣削工艺的基础理论与实验研究。
微细铣削作为一种高精度的制造技术,在微电子、光学、生物医学等领域具有广泛的应用前景。
本文首先概述了微细铣削技术的发展背景和研究意义,然后从工艺原理、加工设备、切削力分析、表面质量评价等方面对微细铣削工艺进行了系统的阐述。
在实验研究方面,本文设计了多组实验,研究了不同工艺参数对微细铣削加工效果的影响,并分析了实验结果,为微细铣削工艺的优化提供了理论支持和实践指导。
本文的研究成果对于提高微细铣削的加工精度和效率,推动相关领域的科技进步具有重要的参考价值。
二、微细铣削工艺基础微细铣削工艺是一种高精度、高效率的制造技术,广泛应用于微纳制造、光学元件加工、微电子机械系统(MEMS)等领域。
了解微细铣削工艺的基础知识对于优化加工过程、提高产品质量具有重要意义。
微细铣削是利用高速旋转的微小铣刀,在工件表面进行切削加工的过程。
铣刀在切削过程中,通过去除工件材料来实现对工件的形状和尺寸控制。
微细铣削的切削深度通常较小,一般在微米级甚至纳米级,因此要求铣刀具有极高的精度和稳定性。
微细铣削刀具是微细铣削工艺中的关键元件,其性能直接影响加工质量和效率。
微细铣刀通常采用硬质合金、陶瓷或金刚石等材料制成,具有较小的直径和较高的硬度。
为了减小切削力、降低切削温度和提高加工精度,微细铣刀的设计也需考虑刃口形状、刃口角度等因素。
微细铣削设备是实现微细铣削工艺的重要装备,需要具备高精度、高刚性和高稳定性等特点。
常用的微细铣削设备包括超精密机床、光学投影铣床等。
这些设备通常配备有高精度测量系统、控制系统和冷却系统,以实现对加工过程的精确控制和优化。
微细铣削工艺参数的选择对加工质量具有重要影响。
常见的工艺参数包括切削速度、进给速度、切削深度、背吃刀量等。
通过优化这些参数,可以实现加工精度、表面质量和生产效率的平衡。
微细铣削加工质量评价是对加工结果进行评估和优化的过程。
《微型精密铣床的研究和设计》范文
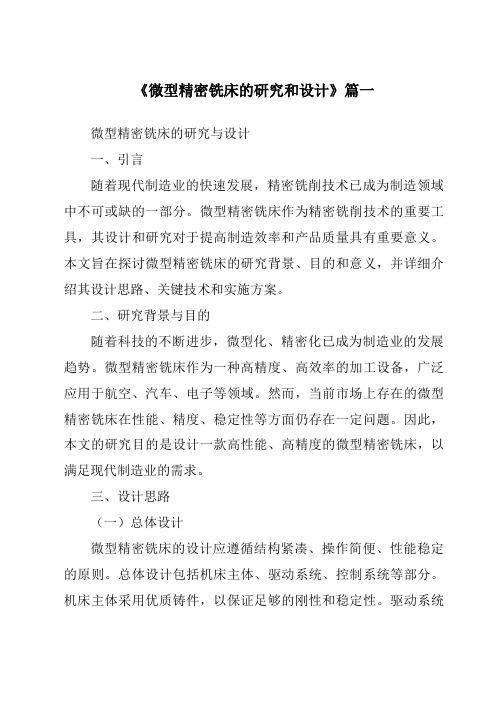
《微型精密铣床的研究和设计》篇一微型精密铣床的研究与设计一、引言随着现代制造业的快速发展,精密铣削技术已成为制造领域中不可或缺的一部分。
微型精密铣床作为精密铣削技术的重要工具,其设计和研究对于提高制造效率和产品质量具有重要意义。
本文旨在探讨微型精密铣床的研究背景、目的和意义,并详细介绍其设计思路、关键技术和实施方案。
二、研究背景与目的随着科技的不断进步,微型化、精密化已成为制造业的发展趋势。
微型精密铣床作为一种高精度、高效率的加工设备,广泛应用于航空、汽车、电子等领域。
然而,当前市场上存在的微型精密铣床在性能、精度、稳定性等方面仍存在一定问题。
因此,本文的研究目的是设计一款高性能、高精度的微型精密铣床,以满足现代制造业的需求。
三、设计思路(一)总体设计微型精密铣床的设计应遵循结构紧凑、操作简便、性能稳定的原则。
总体设计包括机床主体、驱动系统、控制系统等部分。
机床主体采用优质铸件,以保证足够的刚性和稳定性。
驱动系统采用高性能伺服电机和精密丝杠,以确保加工过程中的精度和稳定性。
控制系统采用先进的数控系统,实现自动化加工。
(二)关键技术1. 精密传动技术:采用高精度齿轮和轴承,保证传动精度和稳定性。
2. 数控技术:采用先进的数控系统,实现自动化加工和精确控制。
3. 切削参数优化:通过优化切削参数,提高加工效率和表面质量。
四、关键技术设计与实施方案(一)精密传动系统设计精密传动系统是微型精密铣床的核心部分,其设计直接影响机床的加工精度和稳定性。
设计过程中,应选择高精度齿轮和轴承,以保证传动精度。
同时,采用先进的润滑系统,降低传动系统的摩擦和磨损,延长使用寿命。
(二)数控系统设计数控系统是微型精密铣床的“大脑”,负责自动化加工和精确控制。
设计过程中,应选择性能稳定、功能强大的数控系统,实现加工过程的自动化和智能化。
同时,应具备友好的人机界面,方便操作人员进行参数设置和操作。
(三)切削参数优化设计切削参数的优化对于提高加工效率和表面质量具有重要意义。
微细铣削机床研制及硬脆性材料切削实验研究

关键词:微细加工;桌面铣床;开放式数控;硬脆性材料
I
万方数据
山东理工大学硕士学位论文
ABSTRACT
ABSTRACT
Micromilling is an ultra-precision machining technique which is capable of realizing the fabrication of three-dimensional and complicated geometrical features. The CNC micromilling machine tool with excellent motion performances is the prerequisite for micromilling techniques. In order to conduct micromilling studies, the design and development of a CNC micromilling machine tool is introduced in the study firstly. Experimental evaluations are conducted for the developed desktop micromilling machine tool. Furthermore, the micromilling process has been conducted for the typical hard and brittle material. Considering the fact that features to be created in micromilling are usually small-sized, the CNC micromilling machine tool is designed as a desktop one. The miniaturized desktop machine tool not only saves space and energy, but also has the ability to improve the accuracy theoretically. Open architecture CNC system is applied to the developed machine tool. The controller uses the UMAC motion card from Delta Tau which has integrated I/O and power supply. It also has high-speed USB, Ethernet, Macro communication system to communicate with IPC to satisfy the performance expansions. Direct drive linear motors are used to avoid the transmission errors brought by conventional ball screws. Linear encoders with the graduation of 5nm are used for feedback to construct the closed-loop control. After the construction of the desktop micromilling machine tool, PID debugging, calibration and compensation by laser interferometer are conducted to realize the sub-micron positioning accuracy. Based on the minimum chip thickness theory in micromachining, experimental studies are conducted on the typical ductile material copper. The effect of the feed and axial depth of cut on surface roughness has been studied. The developed machine tool also has been verified by the experiments. The physical properties of single-crystalline silicon have been analyzed to select the micromilling cutter and cutting fluid. Experimental studies have been conducted on the developed machine tool. The federate and the cutting fluid supply method have been selected as the experimental factors. Based on the federate identified in previous studies, the two-factor and whole-level experiments have been conducted. The surface roughness has been analyzed by white-light interferometer. Variance analysis has been used to study the effects of the experimental factors on the surface roughness and the sequence of importance has been identified. It shows that the larger the federate, the worse the surface roughness is. The cutting fluid is very important in micromilling of single-crystalline silicon. The cutting fluid has more effects on the surface roughness than that of the federate. Brittle-ductile transmissions (ductile-mode micromachining) can be realized in a certain micromilling conditions. The experimental study found the basis for further studies on micromilling of hard and brittle materials. Keywords: Microcutting; Desktop milling machine tools; Open CNC; Hard and brittle materials
微径铣刀及微细铣削技术的研究

微径铣刀及微细铣削技术的研究1引言近年来,民用和国防等领域对各种微小型化产品的需求不断增加,对微小装置的功能、结构复杂程度、可靠性等要求也越来越高。
因此,研究开发经济上可行、能够加工三维几何形状和多样化材料、特征尺寸在微米级到毫米级的精密三维微小零件的微细加工技术具有重要意义。
目前,微细切削已成为克服MEMS技术局限性的重要技术,而微细铣削技术因具有高效率、高柔性、能加工复杂三维形状和多种材料的特点,已成为一个非常活跃的研究热点。
2微径铣刀及其制造技术(1)制造工艺及刀具性能磨削是一种传统的铣刀制造工艺,但对于直径仅为零点几毫米的微径铣刀,要在磨削力作用下,在不均质的刀具材料上磨削加工出锋利的切削刃口,是一件十分困难的事情,这也成为微径铣刀发展的一个技术瓶颈。
为此,从理论和实验的角度出发,可以选择一种不产生切削力的加工方法(如激光加工、聚焦离子束加工等)。
聚焦离子束加工方法从原理上比较适合用于制造微径铣刀。
Friedrich和Vasile等人采用聚焦离子束加工技术制作了微径铣刀,最小直径达到22mm。
利用微径铣刀和定制的高精度铣床,在聚甲基丙烯酸甲酯(PMMA)上加工出了89.5°直壁微槽结构,深度为62mm,槽间肋厚为8mm。
Adams等人采用聚焦离子束加工技术制作了一些直径约为25μm的微径铣刀,其轮廓形状有两面体、四面体和六面体,切削刃分为2刃、4刃和6刃,刀具材料为高速钢和硬质合金。
用这些刀具分别对铝、黄铜、4340钢和PMMA四种工件材料进行了微细铣削加工。
但是,由于使用微径铣刀进行切削加工必须采用小进给量,且刀具磨损剧烈,加工毛刺较大,加工效果至今不能令人满意。
立铣刀的刀刃几何形状主要有直体、锥体三角形(D-type)、半圆形(D-type)和已商品化的螺旋刃立铣刀四种。
Fang等人通过实验和有限元分析,从刀具刚度和加工性能出发,对上述四种立铣刀进行了研究对比。
结果表明,锥体D-type立铣刀更适合微细切削加工,并用直径0.1mm的锥体立铣刀成功制作了特征尺寸小于50μm的生物医学零件和特征尺寸小于80μm的微型压花模具。
基于车铣复合加工的微小型结构件工艺研究
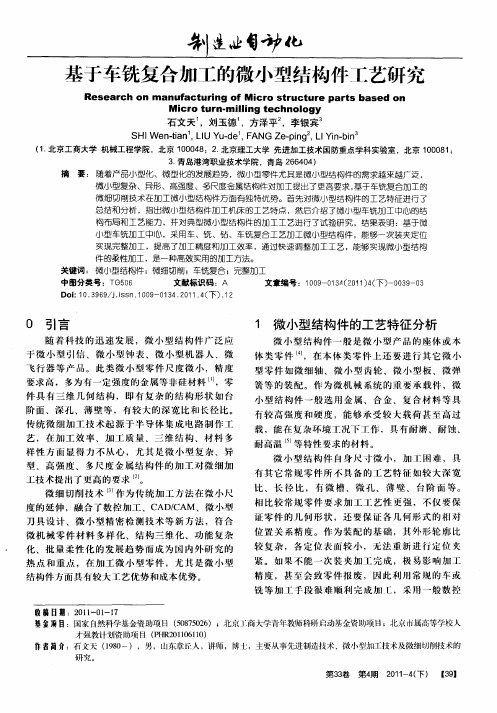
SHl e —in。 LU — e , ANG Ze p n L n bn W nt a , I Yu d F — ig , I Yi. i。
(. 1 北京工商大学 机械工程学院 ,北京 1 0 4 ;2 北京理工大学 先进加工技术 国防重点学科 实验 室 ,北京 1 0 8 008 . 001
紧 。 如 果不 能 一次 装夹 加 工 完成 ,极 易 影 响 加 工
刀具 设 计 、微 小 型 精 密 检 测 技 术 等 新 方 法 ,符合 微 机 械 零 件 材 料 多样 化 、结 构 三 维 化 、 功 能 复 杂
化 、批 量 柔 性 化 的 发 展趋 势 而 成 为 国 内 外研 究 的
小型车铣 加工中心 ,采用车 、铣 、钻 、车铣 复合工 艺加 工微小型结 构件 ,能够 一次装夹定位 实现完整加 工 ,提 高了加工精度和 加工效率 ,通过快 速调整加工 工艺 ,能够实现微 小型结构 件的柔性加工 ,是一种高效实用的加工方法。 关键词 : 微小型结构件 ; 细切削 ;车铣复合 ;完整加工 微 中图分类号 :T 0 G5 6 文献标识码 :A 文章编号 :1 0 —0 3 ( 0 14 下 ) 0 9 3 9 1 A 2 1 ) ( 一03 —0 0
度 的延 伸 ,融 合 了数 控 加工 、C / AM、微 小 型 AD C
有 较 高 强 度 和 硬 度 ,能 够 承 受 较 大 载 荷 甚 至 高过
载 ,能 在 复 杂环 境工 况 下 工作 ,具 有 耐 磨 、耐 蚀 、 耐高 温 。 等特 性要 求的 材料 。
微 小 型 结 构 件 自身 尺 寸 微 小 ,加 工 困 难 ,具 有其 它 常 规 零 件所 具 备 的 工艺 特 征 如 较 大 深 宽 比 、 长 径 比 ,有 微 槽 、微 孔 、薄 壁 、 台 阶 面 等。 相 比较 常 规 零 件 要 求加 工 工 艺性 更强 ,不 仅 要保 证 零 件 的 几何 形状 ,还 要 保 证 各 几 何 形 式 的 卡 对 H 位 置 关 系 精 度 。作 为 装 配 的基 础 ,其 外 形 轮 廓 比 较 复 杂 ,各 定 位 表 面 较 小 ,无 法 重 新 进 行 定位 灾
《微型精密铣床的研究和设计》范文
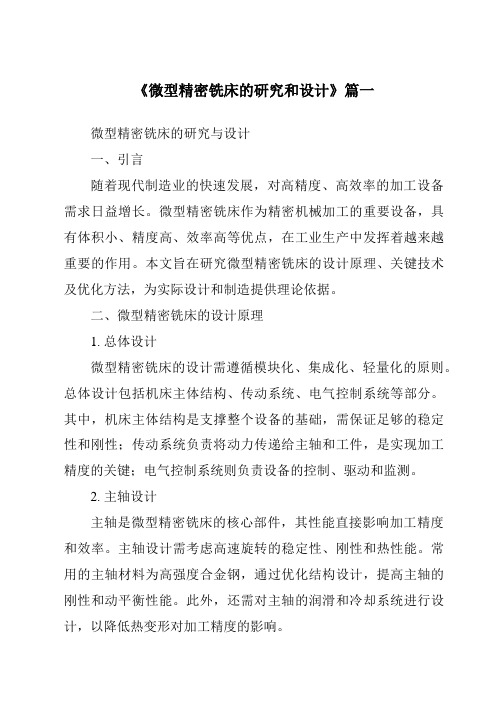
《微型精密铣床的研究和设计》篇一微型精密铣床的研究与设计一、引言随着现代制造业的快速发展,对高精度、高效率的加工设备需求日益增长。
微型精密铣床作为精密机械加工的重要设备,具有体积小、精度高、效率高等优点,在工业生产中发挥着越来越重要的作用。
本文旨在研究微型精密铣床的设计原理、关键技术及优化方法,为实际设计和制造提供理论依据。
二、微型精密铣床的设计原理1. 总体设计微型精密铣床的设计需遵循模块化、集成化、轻量化的原则。
总体设计包括机床主体结构、传动系统、电气控制系统等部分。
其中,机床主体结构是支撑整个设备的基础,需保证足够的稳定性和刚性;传动系统负责将动力传递给主轴和工件,是实现加工精度的关键;电气控制系统则负责设备的控制、驱动和监测。
2. 主轴设计主轴是微型精密铣床的核心部件,其性能直接影响加工精度和效率。
主轴设计需考虑高速旋转的稳定性、刚性和热性能。
常用的主轴材料为高强度合金钢,通过优化结构设计,提高主轴的刚性和动平衡性能。
此外,还需对主轴的润滑和冷却系统进行设计,以降低热变形对加工精度的影响。
三、关键技术研究1. 动力学分析动力学分析是微型精密铣床设计的重要环节。
通过对机床的动态特性进行分析,可以了解机床在加工过程中的振动、变形等情况,为优化设计提供依据。
常用的动力学分析方法包括有限元法、模态分析法等。
2. 精度控制技术精度控制技术是保证微型精密铣床加工精度的关键。
包括误差补偿技术、热误差控制技术等。
误差补偿技术通过对机床误差进行检测和修正,提高加工精度;热误差控制技术则通过优化机床结构、改进润滑和冷却系统等方法,降低热变形对加工精度的影响。
四、优化方法与实施步骤1. 优化方法针对微型精密铣床的设计和制造过程,可采用多种优化方法,如结构优化、材料选择、工艺优化等。
其中,结构优化可通过改变机床的结构布局、减轻重量、提高刚性和稳定性等手段,提高机床的性能;材料选择则需根据实际需求,选择合适的材料以保证机床的耐用性和可靠性;工艺优化则包括对加工工艺的改进和优化,以提高加工效率和精度。
微小型超精密微细铣削机床的研制
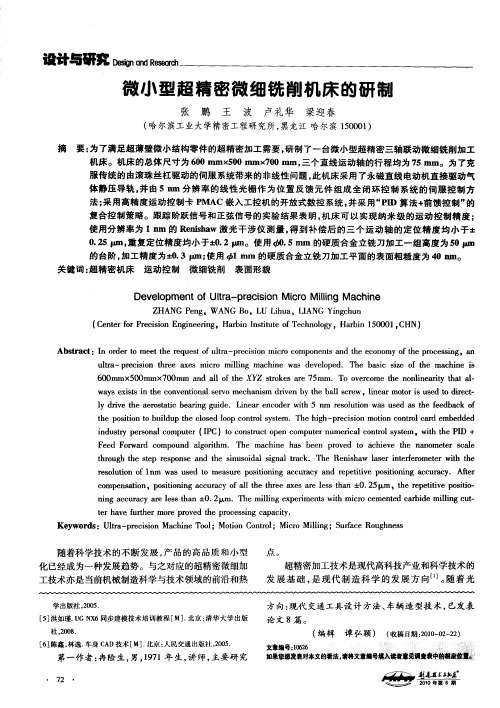
02 n 重 复定位 精度 均小 于± . n .5t , e O2t 。使用 . l的硬质 合金 立铣 刀加工 一组高度 为 5 ^ e 5mi l 0. m
的 台阶 , 工精 度为 ± . 加 O3 关键词 : 超精 密机床 运 动控 制 ; 使用 mi 的硬质 合金 立铣 刀加工 平面 的表面粗 糙度为 4 m。 l l 0n 微 细铣 削 表 面形 貌
h o g h t p r s o s n h i s i a i a ta k t r u h t e se e p n e a d t e s u o d l s n r c . T e Re ih w l s r i tr r mee t h n gl h n s a a e n ef o t rwi 1t e e l
( e t rPeio nier g H ri s tt o T c nl y Ha i 5 0 1 C N) C ne f rcs nE g ei , abnI tue f eh oo , r n1 0 0 , H ro i n n ni g b
Absr c t a t:I r e o me tt e r q e to l a p e iin mir o o e t n h c n my o h r c s ig,al n o d rt e h e u s fut — r c so co c mp n n sa d t e e o o ft e p o e sn r l u ta lr —prc so h e a e mir mi i g e iin t r e x s co l n ma h n wa d v l p d. T e a i sz o h ma h n i l c ie s e eo e h b sc ie f t e c ie S 6 0mm x O 0 5 Omm x Omm n l o h Z to s a e 7 am. T v r o h o ln aiy t a — 7O a d al ft e XY sr ke r 5r o o e c me t e n n i e rt ta h l wa se it n t ec n e i n ls r o me h n s d v n b h l s r w,l a tri s d t r c- y xssi o v nt a e v c a im r e y te bal c e h o i i rmo o su e o die t ne l rv h e sai e rn u d . Lie n o e t m e o ui n wa s d a h e d c f y d e t e a r ttc b a ig g i e i o n a e c d rwi 5 a r s l t s u e s t e fe ba k o r h o t e p st n t ul u hec o e o p c n rls se h o ii o b i p t ls d lo o to y tm.T e h g o d h ih-p e iin moi n c n rlc d e e e r cso to o to a mb dd d r
《2024年微型精密铣床的研究和设计》范文

《微型精密铣床的研究和设计》篇一微型精密铣床的研究与设计一、引言随着现代制造业的快速发展,精密铣削技术在各种零部件的加工制造中得到了广泛应用。
然而,传统的大型铣床由于其庞大的体积和较高的成本,往往无法满足某些特殊或小批量生产的需求。
因此,微型精密铣床的研发与优化成为了现代机械工程领域的研究热点。
本文旨在研究并设计一款具有高精度、高效率、高稳定性的微型精密铣床,以适应日益增长的微型零件加工需求。
二、需求分析1. 性能需求:考虑到铣削过程的复杂性,微型精密铣床需要具备高精度、高效率和高稳定性的特点。
此外,还需要具备较好的可操作性和可维护性。
2. 工艺需求:设备应能适应多种不同材质的铣削需求,如金属、合金等,以满足市场对多种零件的加工需求。
3. 市场需求:随着科技的发展,对微型零件的需求日益增长,因此,微型精密铣床应具有较高的市场竞争力。
三、设计与研究1. 机械结构设计:采用模块化设计思路,将铣床分为底座、立柱、工作台、驱动系统等模块。
其中,底座和立柱采用高强度材料,以确保设备的稳定性;工作台采用滚珠导轨以提高加工精度;驱动系统采用高性能电机和先进的传动技术。
2. 控制系统设计:采用数字化控制技术,如伺服控制技术和实时监控技术,实现对铣削过程的精确控制。
同时,采用友好的人机交互界面,方便操作人员使用。
3. 精度优化:通过优化机械结构设计和控制系统设计,提高设备的加工精度。
此外,还可以采用误差补偿技术,如热误差补偿和机械误差补偿等,进一步提高设备的稳定性。
4. 工艺优化:针对不同材质的铣削需求,设计不同的工艺流程和参数设置。
同时,通过仿真软件对铣削过程进行模拟和优化,以提高设备的加工效率和产品质量。
四、实验与验证在完成微型精密铣床的设计后,需要进行实验验证其性能和精度。
首先,对设备进行装配和调试,确保各部件的正常运行。
然后,进行一系列的铣削实验,包括不同材质、不同工艺参数下的铣削实验。
通过实验数据的分析和处理,验证设备的性能和精度是否达到预期目标。
微小型座体零件车铣加工技术研究
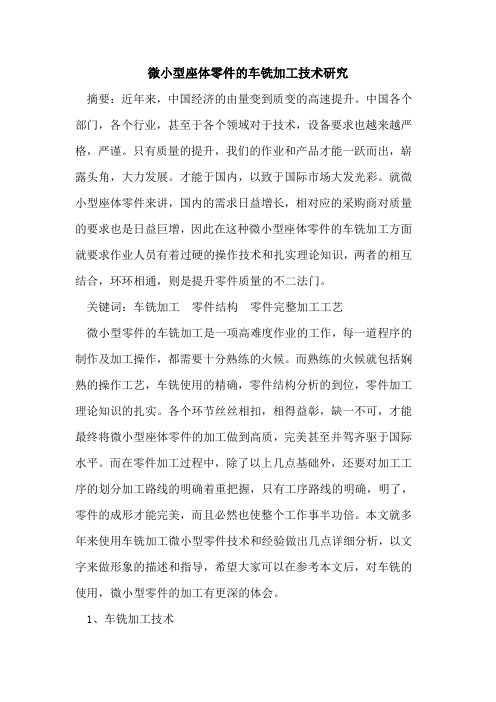
微小型座体零件的车铣加工技术研究摘要:近年来,中国经济的由量变到质变的高速提升。
中国各个部门,各个行业,甚至于各个领域对于技术,设备要求也越来越严格,严谨。
只有质量的提升,我们的作业和产品才能一跃而出,崭露头角,大力发展。
才能于国内,以致于国际市场大发光彩。
就微小型座体零件来讲,国内的需求日益增长,相对应的采购商对质量的要求也是日益巨增,因此在这种微小型座体零件的车铣加工方面就要求作业人员有着过硬的操作技术和扎实理论知识,两者的相互结合,环环相通,则是提升零件质量的不二法门。
关键词:车铣加工零件结构零件完整加工工艺微小型零件的车铣加工是一项高难度作业的工作,每一道程序的制作及加工操作,都需要十分熟练的火候。
而熟练的火候就包括娴熟的操作工艺,车铣使用的精确,零件结构分析的到位,零件加工理论知识的扎实。
各个环节丝丝相扣,相得益彰,缺一不可,才能最终将微小型座体零件的加工做到高质,完美甚至并驾齐驱于国际水平。
而在零件加工过程中,除了以上几点基础外,还要对加工工序的划分加工路线的明确着重把握,只有工序路线的明确,明了,零件的成形才能完美,而且必然也使整个工作事半功倍。
本文就多年来使用车铣加工微小型零件技术和经验做出几点详细分析,以文字来做形象的描述和指导,希望大家可以在参考本文后,对车铣的使用,微小型零件的加工有更深的体会。
1、车铣加工技术车铣加工技术不是普通意义上的车削与铣削功能的简单组合,是完全摒弃了传统的车削加工机理和部分车削功能部件(如车刀和车刀架等)。
它能实现车削功能-回转体表面加工,但不是采用车削,是以铣代车。
它还能独立完成铣、镗、钻、磨削等工种,具有加工平面、孔和回转体表面的能力,因此对于以回转体为基体的零件,本铣加工一般均能实现完整加工。
完整加工是指在一台机床上能加工完一个零件的所有工序。
有时也可能需要两台机床。
实现零件完整加工的优点是明显的。
相对传统工序分散的生产方法而言,被加工零件越复杂,完整加工的优势就越明显。
微细加工中的微型铣床_微刀具磨损及切削力的实验研究
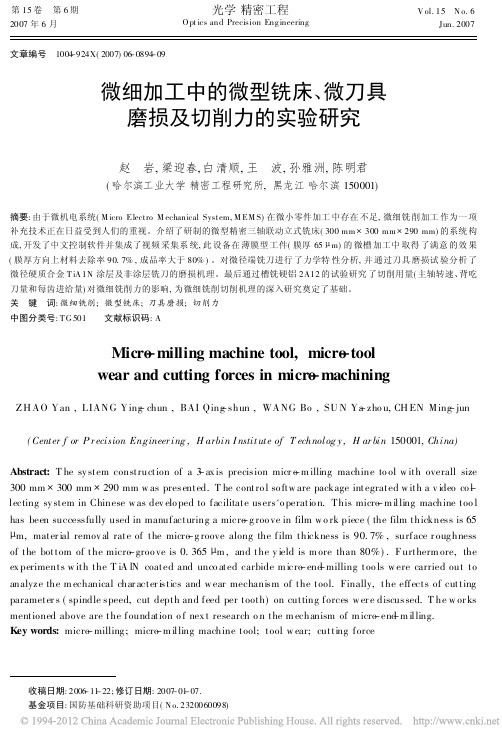
第15卷 第6期2007年6月光学精密工程O pt ics and Precision Eng ineeringV ol.15 N o.6Jun.2007收稿日期:2006-11-22;修订日期:2007-01-07. 基金项目:国防基础科研资助项目(N o.2320060098)文章编号 1004-924X(2007)06-0894-09微细加工中的微型铣床、微刀具磨损及切削力的实验研究赵 岩,梁迎春,白清顺,王 波,孙雅洲,陈明君(哈尔滨工业大学精密工程研究所,黑龙江哈尔滨150001)摘要:由于微机电系统(M icro Electro M echanical System,M EM S)在微小零件加工中存在不足,微细铣削加工作为一项补充技术正在日益受到人们的重视。
介绍了研制的微型精密三轴联动立式铣床(300mm @300mm @290mm)的系统构成,开发了中文控制软件并集成了视频采集系统,此设备在薄膜型工件(膜厚65L m)的微槽加工中取得了满意的效果(膜厚方向上材料去除率90.7%,成品率大于80%)。
对微径端铣刀进行了力学特性分析,并通过刀具磨损试验分析了微径硬质合金T iA 1N 涂层及非涂层铣刀的磨损机理。
最后通过槽铣硬铝2A12的试验研究了切削用量(主轴转速、背吃刀量和每齿进给量)对微细铣削力的影响,为微细铣削切削机理的深入研究奠定了基础。
关 键 词:微细铣削;微型铣床;刀具磨损;切削力中图分类号:T G 501 文献标识码:AMicro -milling machine tool,micro -toolwear and cutting forces in micro -machiningZH AO Yan ,LIANG Ying -chun ,BAI Qing -shun ,WANG Bo ,SU N Ya -zho u,CH EN Ming -jun (Center f or P r ecision Engineer ing ,H arbin I nstitute of T echnolog y ,H ar bin 150001,China)Abstract:T he sy stem construction of a 3-ax is precision micr o -m illing machine to ol w ith overall size 300mm @300mm @290mm w as presented.T he contro l so ftw are package integrated w ith a v ideo co -llecting sy stem in Chinese w as dev elo ped to facilitate users'o peratio n.This micro -m illing machine too l has been successfully used in manufacturing a micro -g roo ve in film w o rk piece (the film thickness is 65L m,mater ial remov al rate of the micro -g roove along the film thickness is 90.7%,surface r oug hness of the bottom of the micro -groo ve is 0.365L m ,and the y ield is m ore than 80%).Furtherm ore,the ex periments w ith the T iA lN coated and unco ated carbide m icro -end -milling too ls w ere carried out to analyze the m echanical char acter istics and w ear mechanism of the tool.Finally,the effects of cutting parameter s (spindle speed,cut depth and feed per tooth)on cutting forces w er e discussed.T he w or ks mentioned above are the foundation o f nex t research o n the m echanism of m icro -end -m illing.Key words:micro -milling ;micro -m illing machine tool;tool w ear;cutting force1引言随着科学技术的发展,近年来在IT、医疗器械以及通讯领域,人们对微小型零件(如:微型传感器、微型加速度计、微透镜阵列等)的需求日益增加。
微小型零件的微细切削加工工艺研究

作 者 简 介 : 文 天 (9 0 ) 男 , 石 1 8 一 , 山东 章 丘人 , 京 工 商 大 学 机 械 学 院 讲 师 , 士 , 究 方 向 为 先 进 制 造 技 术 、 小 型 加 工 技 术 及 微 细 切 削 技 北 博 研 微
pa r A c o dig t h haa trsis f m ir oc s i e h l y ,M r rs a e dvi d n o pe . c r n o t e c r ce itc o c o pr e sng t c noog i o pa t c n b i de it c m ir ha ,t r e di e so ls r c u e he tm e a nd g a r s ti n r d c d t e pr c s i h r c c o s f h e - m n ina tu t r ,s e t la e rpa t ,I si to u e h o e sngc a a - t t rs isa d m eho s ofm ir rs eitc n t d co pa t .The ee to icpl f t e m i a u e m a hi nd t o s i o s lc in prn i e o h nit r c ne a o l s pr - po e n w o s lc h a eila d s r t r fm ir u tn o s i pon e u . r rsm u t s d a d ho t ee tt e m t ra n tucu e o c o c ti g t ol s it d o t M i o pat s c
室 , 京 1 0 7 北 0 0 2)
《微型精密铣床的研究和设计》

《微型精密铣床的研究和设计》篇一一、引言微型精密铣床作为现代制造工业中的重要设备,其在航空、汽车、模具等领域的广泛应用,为高精度、高效率的加工提供了重要保障。
本文旨在研究并设计一款具有高精度、高效率、高稳定性的微型精密铣床,以适应现代化制造业的需求。
二、微型精密铣床的研发背景及意义随着科技的进步和制造业的不断发展,对于设备的精度、效率和稳定性要求越来越高。
微型精密铣床作为实现高精度加工的重要设备,其研发和设计显得尤为重要。
本设计的研究与开发,不仅可以提高我国制造业的加工水平,还可以促进相关产业的发展,提高国家整体竞争力。
三、微型精密铣床的设计要求1. 精度:保证加工的精度,满足各种复杂零件的加工需求。
2. 效率:提高加工效率,减少加工时间,降低生产成本。
3. 稳定性:保证设备在长时间运行中的稳定性,减少故障率。
4. 安全性:确保操作安全,降低操作人员的劳动强度。
5. 便捷性:操作简便,维护方便。
四、微型精密铣床的总体设计1. 机械结构:采用模块化设计,方便维护和升级。
主要部件包括床身、主轴、进给系统等。
床身采用铸件结构,保证设备的稳定性和精度。
主轴采用高精度轴承,保证加工的精度和效率。
进给系统采用伺服电机驱动,实现精确控制。
2. 控制系统:采用先进的数控系统,实现设备的自动化控制。
通过编程,可以实现各种复杂的加工操作。
同时,控制系统具有友好的人机界面,方便操作人员操作。
3. 动力系统:采用高性能的电机和传动系统,保证设备的动力性能和运行稳定性。
五、微型精密铣床的关键技术及创新点1. 高精度加工技术:采用先进的加工工艺和检测手段,保证设备的加工精度。
2. 高效率加工技术:通过优化设备结构和工艺流程,提高设备的加工效率。
3. 稳定性控制技术:采用先进的控制系统和算法,保证设备在长时间运行中的稳定性。
4. 创新点:模块化设计、数控系统的人机交互界面优化、高精度轴承的应用等。
六、实验与测试在完成微型精密铣床的设计后,需要进行实验与测试,以验证设备的性能和稳定性。
微细铣削技术研究

题目:微细铣削技术研究
报告人:李光俊 任课老师:张弘弢 导师:贾振元 2011年04月23日
目录
一、研究背景及意义 二、微细制造技术简介 三、微细铣削加工机理 四、微细铣削刀具 五、微细铣削加工设备 六、微细铣削研究发展趋势
2
一、研究背景及意义
随着科学技术的不断发展,在航空航天、国防工业、汽车工 业、微电子工业、医疗器械、光学仪器等各个领域,对精密微 小零件的需求日益迫切。
从工艺方面对尺寸效应的研究
从模型方面对尺寸效应的研究
8
三、微细铣削加工机理
从力学方面对尺寸效应的研究
从力学方面对尺寸效应的研究涉及切削力、切削比能、 切削温度、刀具磨损、切屑形成、弹塑性变形等众多领域, 焦点集中在两个方面: 最小切削厚度的研究 由于最小切削厚度是探索切屑形成的最基本条件,从以金 刚石刀具为代表的超精密切削研究到当前的微铣削研究, 关于最小切削厚度的研究一直没有停止。 切削力的研究 由于微观尺度铣削加工的许多现象和变化难以观察和测量, 切削力作为一个受许多加工因素影响的函数,越来越受到 微切削研究领域的重视。
3
一、研究背景及意义
微小型化零件的尺寸范围为0.1~10mm,几何特征尺寸范围为 0.01~1mm,结构复杂且精度要求比较高。 如何实现适用于多种材料、结构复杂的小型化零件的高精度、 低成本加工成为微小型化制造技术的关键。
4
二、微细制造技术简介
微细制造技术是二十世纪七十年代开始才逐步发展起来 的前沿、交叉性新兴学科领域,是当前机械制造科学与技 术领域的前沿和热点,从美国的斯坦福大学开始,后续的 日本和欧洲各国均投入大量的人力进行探究。 微细机械加工技术以微小机械零件为加工对象,利用系 统化、集成化理论和技术,根据加工工件机构及要求实现 机床各部件的有机结合,在较小的空间内完成微小零件的 制造,实现在小空间内加工小零件的目的。 微细加工技术减小了整个制造系统以及零件的尺寸规模, 既可以节省能源又可以节省制造空间和资源,符合节能、 环保的生产模式,是绿色制造的发展方向之一,是衡量一 个国家制造技术水平的重要标志。
微小零件加工机床设计研究

零件加工作为生产制造中的重要环节,零件加工精度与效率对于生产效率与质量都有较大的影响。
随着现代制造业不断发展,产品体积不断缩小,功能日趋增多。
为了让微小零件达到装配要求,需要使用精密加工技术。
但是我国目前微小零件加工技术仍存在许多问题,需要不断改进才能够达到微小零件的加工要求。
1 微小零件加工关键技术分析针对微小零件的精加工,首先需要确定微小零件位姿信息,之后需要对微小零件进行拾取和对准,从而进行后续加工。
1.1 微小零件位姿测量在机床进行加工作业时,首先需要对微小零件进行测量,传统人工定位无法满足微小零件定位精度要求。
目前,主要是采取机器视觉技术进行定位,该技术自1980年出现后得到了快速发展,主要是利用光学装置和非接触传感器获取真实世界的图像,并以此为依据对控制机器人下一步动作进行调整,具有较好的三维视觉定位效果,能够实现微小零件测量目标。
机器视觉对微小零件位姿信息采集主要步骤如下:通过对微小零件图像采集、分析与处理,确定图像中定位的特征信息,从而完成对微小零件的定位。
该技术与其他测量方法相比,具有以下优势:第一,非接触性测量,这种测量方式不会对微小零件表面造成损伤,同时也不会由于接触而对微小零件位姿信息造成影响;第二,光谱采集范围广,人眼只能在自然光环境中观察物体,而该技术能够通过光学传感器从不同波段的光谱中采集图像,从而拓展图像采集范围;第三,长时间作业,人眼在长时间作业后会感到疲劳,工作时间有限,而该技术能够对微小零件进行连续采集,且观察效果不受影响;第四,适用范围广,可代替人工在工作环境恶劣的地方进行作业;第五,测量效率高,计算机技术的进步提高了图像储存与处理速度,能够进行大数据处理。
1.2 微小零件的拾取与对准微小零件加工机床通常都是利用末端执行器对微小零件进行操作,但是与其他类型零件加工相比,其操作存在持部位对微小零件的遮挡,以便机器视觉观测。
微夹持器根据夹持方式,分为材料耦合式、形状耦合式和力耦合式,材料耦合将主要是利用微夹持器与微小零件的吸附效应;形状耦合主要是利用微小零件的形状设计微夹持器,从而实现微小零件的夹持;力耦合主要是通过力来夹持微小零件,包括磁力、真空吸附力等。
薄壁零件端铣建模与试验研究

80 圆园19袁57渊8冤
机械制造 总第 660 期
针对大型薄壁零件的端铣加工与精度保障袁 学者 开展了相应研究遥 武凯等咱1暂建立了薄壁腹板铣削加工 受力模型袁通过对立铣刀铣削模型进行分析袁推导了刀 具相对零件任意切削位置处的切削轴向分力表达式袁 并通过有限元仿真给出了腹板的加工变形规律遥 陈婷
收稿日期院圆园员9 年 2 月
婷咱2暂针对 TC4 钛合金薄壁板加工袁采用正交试验法建 立了薄壁腹板立铣切削力峰值预测模型遥 廖玉松等咱3暂 针对铝合金腹板铣削加工袁通过开展变参数试验袁分析 了切削深度尧 刀具及走刀方式对加工变形的影响遥 李 钦生等咱4暂对大型薄壁零件在加工中的装夹支撑方式及 加工工艺路线进行了研究袁 实现了对加工中变形量的 控制遥 丁杰等咱5暂针对薄壁端铣提出了刀位优化方法袁实 现了对加工振动的有效抑制遥 毛毅明等咱6暂针对筋板加 工变形问题袁使用经验公式对切削力进行了计算袁优化 了刀路袁实现了变形补偿遥
type parts are used. Such parts are difficult to be processed and clamped袁 and there tend to be weak rigid
support areas袁 which makes it difficult for traditional cutting force model to make an accurate description on
介观尺度薄壁件微铣削加工变形预测及抑制

摘要微小型产品在航空航天、通讯设备、医疗器械等领域应用日益广泛,其中某些微小零部件具有介观尺度薄壁特征。
而介观尺度薄壁件的高精度加工是一大难题。
微铣削技术是加工介观尺度薄壁件的有效方法,具有效率高、精度高、成本低等优势。
但是,薄壁件具有刚性弱、加工工艺性差等特点,微铣削加工中容易产生变形,直接影响薄壁件加工精度。
因此,薄壁件微铣削加工变形预测和抑制是实现薄壁件高精度加工的前提和关键。
本文针对介观尺度薄壁件微铣削加工过程中变形预测和抑制进行深入研究。
首先,基于Abaqus有限元仿真软件建立了薄壁微铣削加工过程仿真模型,采用Johnson-Cook 材料模型和损伤模型描述难加工材料Inconel718的材料属性和损伤准则,实现了Inconel718薄壁微铣削加工过程的铣削力预测,并通过实验验证了模型准确性;其次,基于生死单元方法建立了薄壁微铣削加工变形预测模型,实现了加工变形量的预测,实验验证了预测结果的可靠性,并分析了薄壁微铣削加工变形规律;最后,基于回归分析法建立了刀具磨损预测模型,提出了考虑刀具磨损的刀具轨迹补偿方案。
根据影响薄壁加工变形的因素详细分析了薄壁微铣削加工变形原因,并提出了相应的改进措施。
最终实现了薄壁的高精度加工。
本文研究成果可为薄壁件微铣加工变形抑制奠定基础,为实现薄壁件高精度加工提供参考。
关键词:微铣削;薄壁件;ABAQUS;过程仿真;变形预测Prediction and Suppression of Micro-milling Mesoscale Thin-walledDeformationAbstractMicrominiature products are increasingly used in aerospace, medical equipment, communication equipment and other fields, some of which have thin-walled features of meso-scale. The high-precision processing of meso-scopic thin-walled parts has become a barrier. Micro-milling technology is an effective method for processing meso-scale thin-walled parts, which has the advantages of high efficiency, high precision and low cost. However, thin-walled parts have the characteristics of weak rigidity and poor processability, and are easily deformed during micro-milling, which directly affects the precision of thin-walled parts. Therefore, the prediction and suppression of micro-milling thin-walled parts deformation are the premise and key to achieve high-precision machining of thin-walled parts.In this paper, the deformation prediction and suppression in the process of micro-milling of meso-scale thin-walled parts are studied in depth. First, based on the ABAQUS finite element simulation software, a simulation model of the thin-walled micro-milling process is established. The Johnson-Cook material model and damage model are used to describe the material properties and damage criteria of Inconel718, a difficult-to-machine material. The accuracy of the model is verified through experiments. Secondly, based on the birth-death element method, a deformation prediction model of micro-milling thin-walled parts is established to realize the prediction of the machining deformation. The experiment verifies the reliability of the prediction results, and this paper analyzes the thin-wall micro-milling machining deformation rules through experiments. Finally, based on the regression analysis method, a tool wear prediction model is established, and a tool path compensation scheme considering tool wear is proposed. According to the factors that affect the deformation of thin-walled machining, the causes of deformation of thin-wall micro-milling are analyzed, the corresponding improvement measures are proposed, and high-precision machining of thin-wall is finally realized. The research results of this paper can lay a foundation for the deformation suppression of thin-walled parts micro-milling, and can provide a reference for achieving high-precision machining of thin-walled parts.Key Words:Micro-milling; Thin-walled parts; ABAQUS; Process simulation; Deformation prediction- II -目录摘要 (I)Abstract (II)1 绪论 (1)1.1 课题来源、背景及研究意义 (1)1.1.1 课题来源 (1)1.1.2 研究背景与意义 (1)1.2 国内外研究现状 (3)1.2.1 薄壁铣削加工变形预测与抑制 (3)1.2.2 薄壁铣削力模型研究 (4)1.3 存在的问题 (7)1.4 研究目标和主要内容 (7)2 薄壁微铣削加工过程有限元仿真 (9)2.1 微铣薄壁件过程有限元仿真模型 (9)2.1.1 模型建立与网格划分 (9)2.1.2 材料参数与失效准则 (11)2.1.3 相互作用与载荷 (13)2.1.4 铣削过程仿真输出 (14)2.2 薄壁微铣削过程仿真实验验证 (15)2.3 本章小结 (19)3 薄壁微铣削加工变形预测 (20)3.1 薄壁微铣削变形预测模型 (20)3.1.1 几何模型与网格划分 (20)3.1.2 单元编码与载荷施加 (21)3.1.3 单元删除 (24)3.1.4 变形预测 (24)3.2 实验验证变形模型 (25)3.3 本章小结 (31)4 介观尺度薄壁微铣加工变形抑制 (32)4.1 考虑刀具磨损的变形抑制方案 (32)4.1.1 微铣刀磨损预测 (33)4.1.2 变形抑制方案 (39)4.2 变形因素分析与抑制 (41)4.3 本章小结 (44)结论 (45)展望 (46)参考文献 (47)攻读硕士学位期间发表学术论文情况 (52)致谢 (53)大连理工大学学位论文版权使用授权书 (54)- IV -1 绪论1.1 课题来源、背景及研究意义1.1.1 课题来源本课题来源于国家自然科学基金“介观尺度薄壁特征微铣加工理论与技术研究(项目编号:51875080)”及辽宁省自然基金资助计划“微流控芯片热压模具微铣加工理论与技术研究”(项目编号:2019-MS-038)。
车铣复合加工下的微小型结构件工艺

车铣复合加工下的微小型结构件工艺随着加工制造技术快速发展,微小型结构件已广泛应用于机器人、钟表和飞行器等方面。
此类零件多为加工精度高、尺寸较小、性能强度较高的金属等非硅材料。
且此类微小型结构件多为形状复杂的三维几何结构,其长径比与深宽比较大。
而车铣复合加工技术作为一种融合了CAD/CAM技术、数控加工工艺、微小型精密检测技术及微小型刀具设计技术的复合加工工艺,其具有功能复杂、结构三维化、材料多样化和批量柔性化等技术优势。
一、车铣复合加工下的微小型结构件工艺特征微小型结构件一般是微弹簧、微小型板及微小型齿轮、微细轴等微小型产品的本体或座体类零件。
其作为此类微小型机械系统的重要装配和结构承载件,一般均具有较大的荷载承受能力和较强的硬度、强度,且具有耐腐蚀及耐磨和耐高温等性能优势,能够在极其恶劣、复杂工况下工作。
由于此类微小型结构件加工困难,技术精度和质量要求较高。
因此,其它常规零部件不具有较大的长径比及深宽比等。
在复合加工过程中,为了确保一次加工成形,且满足加工精度要求,通常需采用精密的数控机床进行加工。
总体而言,车铣复合加工下的微小型结构件工艺具有加工尺度小、精度高、加工能力强及柔性好等技术优势。
基于以上技术优势,可实现对微小型结构件进行多轴复合联动加工。
二、车铣复合加工下的微小型结构件工艺路线如下图1所示为车铣复合加工下的微小型结构件加工中心。
该车铣复合加工中心集成了车削和铣削的加工功能,配备12工位转塔式刀架,在复合加工时,车铣主轴转速可达*****r/min,不仅具备C轴精确分度功能,且能够精确定位主轴锁定技术装置,甚至还可用于对一般微小型零件的车削要求。
车削中心是以车床为基本体,增加动力铣、钻、镗,以及副主轴的功能,使零件需要二次,三次加工的工序在车削中心上一次完成。
复杂的轴类复合零件可以由一台机床完成所有加工步骤,大大降低上下料、换机台加工的时间,以及减少人为公差的机会,零件的形位精度大大提高,达到一次装夹完成加工的概念,如图2所示。
- 1、下载文档前请自行甄别文档内容的完整性,平台不提供额外的编辑、内容补充、找答案等附加服务。
- 2、"仅部分预览"的文档,不可在线预览部分如存在完整性等问题,可反馈申请退款(可完整预览的文档不适用该条件!)。
- 3、如文档侵犯您的权益,请联系客服反馈,我们会尽快为您处理(人工客服工作时间:9:00-18:30)。
Ab s t r a c t :Th e i n lu f e n c e o f c u t t i n g p a r a me t e r s o n s u r f a c e r o u g h n e s s a nd c u t t i ng v i b r a t i o n i s r e s e a r c h e d i n a x i a l t u r n
me n t i s c o mp l e t e d,t h e n c u t t i n g v i b r a t i o n a n d s u r f a c e r o u g h n e s s a r e me a s u r e d . E x p e ime r n t r e s u l t s s h o w
的加 工 , 采用 匹配 的切 削参 数可 以获得 较好 的 表面粗 糙 度。
关键 词 : 微 小型 ; 轴 向车铣 ; 切 削参 数 ; 切 削振 动 ; 表 面粗 糙度
中 图分类 号 : T G 5 0 1 . 1 文献标 识码 : B
E x p e r i me n t a l r e s e a r c h o n mi c r o t h i n p a r t s b y a x i a l t u r n— — mi l l i n g
工 技术 具有 加 工精度 高 、 切削 平稳 、 刀具 磨损 小 和间 断 切 削易 于排 屑及 散热 等 优 点 , 而 更 适 用 于微 小 型 零 件 的加 工 l l I 4 J 。特 别是 对 于具有 宏尺 度外 形 尺寸 及 中 间
本研究 以航空仪 表传 感器 中的某高 精度 薄底 回转
微 小 型零 件在航 空航 天 、 兵 器装 备 、 仪器 仪表 等领
域 的广 泛应 用 , 对微 细 结 构加 工 技 术 也 提 出 了更 高 的
削、 铣削相 比 , 铣刀 的跳 动量 更 显 著 , 对 加 工过 程 的影
响也 更突 出 。
要 求 。相 比传统 的车削 、 铣削 加工 , 微小 型 车铣复 合加
微 小 型 薄 底 零 件 的轴 向车 铣 实 验 研究 术
邓勇军 张之敬 金 鑫 许 志尧 张朝枭
( 北 京理 工大 学 , 北京 1 0 0 0 8 1 ) 摘 要: 研 究跨 尺度微 小 型薄底 零 件的轴 向车铣 加 工过 程 中 。 切 削参 数 对 表面 粗 糙 度和 切 削 振动 的 影 响规 律 。在选 择 的切 削用量 范 围 内, 采用正 交 实验法 对切 削参 数进 行 了优 选 实验 , 对切 削振 动和 表 面粗 糙 度进行 了检 测 。实验 结 果表 明 。 在精 密 微小 型车 铣 复合 加 工 机床 上 进 行 跨尺 度 微 小型 薄 底 零件
—
mi l l i n g o f c r o s s—s c a l e mi c r o p a ns .W i t h i n t h e s e l e c t e d r a n g e o f c u t t i n g p a r a me t e r s,o nh o g o n a l e x p e i— f
加工 过程 中力 变形 、 热 变 形 比较 严 重 , 废 品率 高 , 生 产
1 零 件 加 工 工 艺 分 析
如 图 1所示 微 小 型 薄 底 回转体 零 件 图 , 6 1 0孑 L 特
征 属 于宏尺 寸 , 底面 厚度关 键 特征 尺寸 为 0 . 0 8 mE, 属 于 中间尺度 , 孔底 内表 面粗 糙 度要 求 为 R ≤0 . 8 m m,
D E N G Y o n g j u n , Z H A N G Z h i j i n g , J I N X i n , X U Z h i y a o , Z H A N G C h a o x i a o ( B e i j i n g I n s t i t u t e o f T e c h n o l o g y , B e i j i n g 1 0 0, 通 过正 交实 验 , 研 究切 削用 量对 跨 尺 度微小 型零 件加 工 的表 面粗糙 度和 切削振 动 的影
响程 度 , 探 讨切 削参 数 的优化 选择 问题 , 达到 提高 加工 表面 质量 的 目的 。
尺 度特 征尺 寸 的跨 尺度 微 小 型 零 件 , 采 用 传统 的加 工 方法 , 工 件 的尺 寸精度 和形 位精 度难 以达 到加 工要 求 ,