八钢管线钢深脱硫技术的探讨.doc
钢铁冶炼过程中烟气脱硫技术研究

钢铁冶炼过程中烟气脱硫技术研究随着工业化的发展,钢铁冶炼工业已经成为了经济发展的重要支柱。
然而,传统的钢铁冶炼工艺中存在许多问题,其中一个重要的问题就是烟气中的二氧化硫(SO2)排放对环境造成的负面影响。
因此,寻求一种高效、环保的烟气脱硫技术变得尤为重要。
烟气脱硫技术一般分为干法脱硫和湿法脱硫两大类。
干法脱硫技术主要是利用吸附材料吸附烟气中的SO2,这种方法优点是能够处理高温、高湿度的废气,适用于需要高效处理大量烟气的钢铁冶炼工艺。
然而,干法脱硫技术的劣势也很明显,吸附材料的制备成本较高,同时在吸附过程中会产生大量的灰尘等附加物质,需要进一步的处理。
相比之下,湿法脱硫技术在钢铁冶炼过程中得到了广泛的应用。
这种技术通过将烟气吹入含有吸收剂的脱硫装置中,将SO2转化为硫酸盐或硫酸,从而实现脱硫。
湿法脱硫技术具有高效、稳定且灵活的特点,能够适应不同的工艺要求,并且处理出的废水可以再生利用,降低了废水排放的问题。
在湿法脱硫技术中,常用的吸收剂包括石灰石、石膏等。
这些吸收剂可以将SO2转化为CaSO3和CaSO4等无毒、无害的酸性物质,减少了对环境的污染。
同时,湿法脱硫系统中采用的反应器也是关键组成部分,反应器的设计应该能够保持适当的产物浓度,满足处理出的水质量要求。
然而,目前湿法脱硫技术还存在一些问题。
其中一个关键问题是吸收剂的使用量过大或者循环利用不彻底,导致成本过高或者环境污染比较严重。
除此之外,由于反应器中的反应过程比较复杂,很容易引起沉淀、冲刷等问题,这也给系统的运行带来了一定困难。
针对上述问题,近年来科学家和工程师们在湿法脱硫技术上进行了许多的研究和改进。
例如,一些研究人员提出了基于活性碳的脱硫方法,该方法可以更好地控制SO2的转化反应,同时减少吸收剂的使用量。
其他一些研究还关注于反应器设计和反应参数的优化,通过改进反应器内部的流动状态,减少沉淀和冲刷的问题,并提高系统的运行效率。
总体来说,钢铁冶炼过程中的烟气脱硫技术是当前环保、节能的重点研究之一。
深脱硫钢在LF炉中的脱硫处理工艺分析
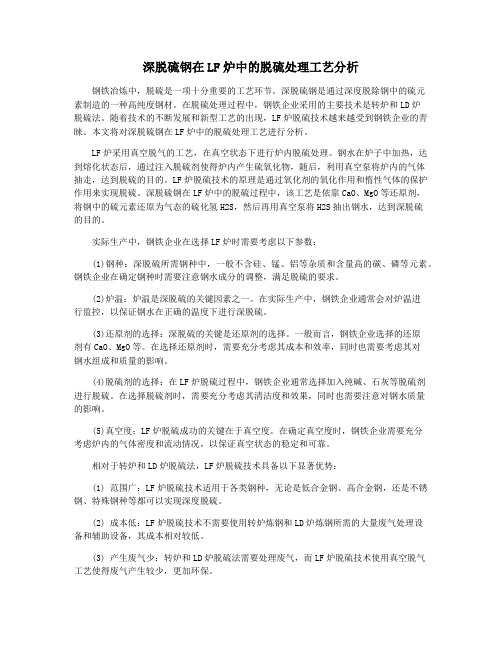
深脱硫钢在LF炉中的脱硫处理工艺分析钢铁冶炼中,脱硫是一项十分重要的工艺环节。
深脱硫钢是通过深度脱除钢中的硫元素制造的一种高纯度钢材。
在脱硫处理过程中,钢铁企业采用的主要技术是转炉和LD炉脱硫法。
随着技术的不断发展和新型工艺的出现,LF炉脱硫技术越来越受到钢铁企业的青睐。
本文将对深脱硫钢在LF炉中的脱硫处理工艺进行分析。
LF炉采用真空脱气的工艺,在真空状态下进行炉内脱硫处理。
钢水在炉子中加热,达到熔化状态后,通过注入脱硫剂使得炉内产生硫氧化物,随后,利用真空泵将炉内的气体抽走,达到脱硫的目的。
LF炉脱硫技术的原理是通过氧化剂的氧化作用和惰性气体的保护作用来实现脱硫。
深脱硫钢在LF炉中的脱硫过程中,该工艺是依靠CaO、MgO等还原剂,将钢中的硫元素还原为气态的硫化氢H2S,然后再用真空泵将H2S抽出钢水,达到深脱硫的目的。
实际生产中,钢铁企业在选择LF炉时需要考虑以下参数:(1)钢种:深脱硫所需钢种中,一般不含硅、锰、铝等杂质和含量高的碳、磷等元素。
钢铁企业在确定钢种时需要注意钢水成分的调整,满足脱硫的要求。
(2)炉温:炉温是深脱硫的关键因素之一。
在实际生产中,钢铁企业通常会对炉温进行监控,以保证钢水在正确的温度下进行深脱硫。
(3)还原剂的选择:深脱硫的关键是还原剂的选择。
一般而言,钢铁企业选择的还原剂有CaO、MgO等。
在选择还原剂时,需要充分考虑其成本和效率,同时也需要考虑其对钢水组成和质量的影响。
(4)脱硫剂的选择:在LF炉脱硫过程中,钢铁企业通常选择加入纯碱、石灰等脱硫剂进行脱硫。
在选择脱硫剂时,需要充分考虑其清洁度和效果,同时也需要注意对钢水质量的影响。
(5)真空度:LF炉脱硫成功的关键在于真空度。
在确定真空度时,钢铁企业需要充分考虑炉内的气体密度和流动情况,以保证真空状态的稳定和可靠。
相对于转炉和LD炉脱硫法,LF炉脱硫技术具备以下显著优势:(1) 范围广:LF炉脱硫技术适用于各类钢种,无论是低合金钢、高合金钢,还是不锈钢、特殊钢种等都可以实现深度脱硫。
钢铁冶炼中脱硫技术的研究进展

钢铁冶炼中脱硫技术的研究进展关键信息项:1、钢铁冶炼中脱硫技术的分类及特点名称:____________________________特点:____________________________适用范围:____________________________2、现有脱硫技术的应用情况应用领域:____________________________应用比例:____________________________效果评估:____________________________3、新型脱硫技术的研发方向重点研究领域:____________________________预期成果:____________________________4、脱硫技术对钢铁质量的影响具体影响方面:____________________________质量提升程度:____________________________5、脱硫技术的成本分析设备投资:____________________________运营成本:____________________________成本效益比较:____________________________11 引言钢铁冶炼中的脱硫技术是提高钢铁质量、减少环境污染的重要环节。
随着钢铁工业的不断发展,对脱硫技术的要求也日益提高。
本协议旨在对钢铁冶炼中脱硫技术的研究进展进行全面梳理和分析。
111 钢铁冶炼中脱硫的重要性钢铁中的硫含量过高会严重影响其质量和性能,如降低韧性、延展性和焊接性能等。
同时,在钢铁生产过程中排放的含硫废气也会对环境造成严重污染。
因此,有效的脱硫技术对于钢铁工业的可持续发展具有重要意义。
112 脱硫技术的分类1121 燃烧前脱硫主要包括煤炭洗选和气化等方法。
煤炭洗选通过物理或化学方法去除原煤中的部分硫分,但其脱硫效果有限。
气化技术则将煤炭转化为气体,在气化过程中实现脱硫,但该技术成本较高。
深脱硫钢在LF炉中的脱硫处理工艺分析

深脱硫钢在LF炉中的脱硫处理工艺分析随着环保要求越来越高,炼钢行业也在不断寻求更加环保、高效的生产工艺,深脱硫钢在LF炉中的脱硫处理工艺正是其中之一。
LF炉是炼钢过程中的重要设备之一,对于钢水的净化和精炼起着至关重要的作用。
在LF炉中使用深脱硫钢进行脱硫处理,可以有效降低炼钢过程中的硫含量,提高钢水的质量,并且符合环保要求。
本文将对深脱硫钢在LF炉中的脱硫处理工艺进行分析,为炼钢行业提供参考。
一、深脱硫钢的特点深脱硫钢是一种在钢水中添加深脱硫剂进行处理的工艺。
深脱硫钢在LF炉中的脱硫处理工艺主要适用于高硫含量的钢水,能够有效降低钢水中的硫含量,提高钢水的质量。
深脱硫钢的特点主要包括以下几点:1. 高效脱硫:深脱硫钢可以在较短的时间内有效降低钢水中的硫含量,达到脱硫的效果。
2. 环保:相比传统的脱硫方法,深脱硫钢对环境的影响更小,更符合现代环保要求。
3. 适用范围广:深脱硫钢适用于多种钢水,能够应对不同硫含量的钢水,具有很好的通用性。
深脱硫钢的特点使其在LF炉中的脱硫处理工艺中具有重要的应用价值,能够帮助炼钢企业提高钢水的质量,降低生产成本,同时达到环保要求。
深脱硫钢在LF炉中的脱硫处理工艺主要包括以下几个步骤:1. 添加深脱硫剂:在LF炉中钢水进行脱氧处理后,需要加入深脱硫剂。
深脱硫剂主要由氧化钙、氧化铁和其他助剂组成,能够有效吸附和还原钢水中的硫,达到脱硫的效果。
2. 搅拌混合:在添加深脱硫剂后,需要进行搅拌混合,使深脱硫剂充分与钢水接触,促进脱硫反应的进行。
搅拌混合过程需要控制时间和速度,确保深脱硫剂能够均匀地分布在钢水中。
3. 保温处理:添加深脱硫剂后,需要对钢水进行保温处理,促进脱硫反应的进行。
保温处理的时间和温度需要根据深脱硫钢的具体配方和钢水的硫含量来确定,以达到最佳的脱硫效果。
4. 处理残渣:脱硫反应结束后,会产生一定量的残渣,需要对残渣进行处理,以便后续的钢水处理。
处理残渣的方法包括打包、输送和回收等,确保残渣对环境不产生污染。
钢铁行业烧结烟气脱硫技术范文

钢铁行业烧结烟气脱硫技术范文钢铁行业是我国重要的基础产业之一,但其生产过程中所产生的烟气排放,尤其是含硫烟气的排放对环境造成了严重的污染。
针对这一问题,烧结烟气脱硫技术被广泛应用于钢铁行业,以减少和控制烟气中的硫排放,达到环境保护的要求。
本文将对钢铁行业烧结烟气脱硫技术进行详细介绍。
钢铁行业烧结烟气脱硫技术是通过将烟气中的硫物质与添加了脱硫剂的喷雾剂接触反应,使其发生反应生成能够溶解于水中的硫酸钙,并通过各种设备进行固液分离从而达到脱硫的目的。
常见的脱硫剂包括石灰石和石膏等。
烧结过程中产生的烟气中含有大量的硫氧化物,主要是SO2,这些气体对环境的影响非常大。
因此,在烧结过程中采用烟气脱硫技术进行治理是十分必要的。
烟气脱硫技术主要包括湿法脱硫和干法脱硫两种方式。
湿法脱硫技术是目前应用较为广泛的一种脱硫方式。
其主要原理是将烟气通过喷雾器,与添加了脱硫剂的喷雾剂进行充分接触和反应,使硫氧化物与脱硫剂发生化学反应,生成可溶解于水中的硫酸钙,并采用各种设备进行固液分离。
湿法脱硫技术具有脱硫效率高、适应性强、操作稳定等优点,但其缺点是设备复杂,投资和运营成本较高。
干法脱硫技术主要是将含硫烟气在特定条件下通过吸附、催化等方式进行脱硫。
常见的干法脱硫技术包括活性炭吸附法、催化剂催化法、干式湿法法等。
干法脱硫技术适用于烟气中硫含量较低的情况下,其优点是设备简单、投资和运营成本相对较低,但脱硫效率相对较低。
钢铁行业烧结烟气脱硫技术的关键是选用合适的脱硫剂,并合理设计设备和工艺。
常用的脱硫剂有石灰石和石膏等,其选择要考虑成本、生产工艺等因素。
此外,脱硫系统的设计要合理,包括反应器、喷雾器、吸收器、分离器等各个部分的布置设计和选型。
总结而言,钢铁行业烧结烟气脱硫技术是解决烟气中硫排放问题的有效手段。
湿法脱硫技术是目前应用较为广泛而成熟的一种技术,其脱硫效率高、适应性强,但设备复杂、投资和运营成本较高。
干法脱硫技术适用于硫含量较低的情况下,其优点是设备简单、投资和运营成本相对较低,但脱硫效率相对较低。
深脱硫钢在LF炉中的脱硫处理工艺分析

深脱硫钢在LF炉中的脱硫处理工艺分析深脱硫钢是指含硫量小于等于10ppm的钢种,对钢材的性能和质量有着极大的提高作用。
LF炉是钢铁炼制中广泛采用的炉子之一,其主要功能是对炼钢工艺中的高温钢液进行精炼处理,其中包括脱碳、脱硫、脱磷等工艺。
本文将以深脱硫钢的生产工艺为主线,结合LF炉中的脱硫处理流程,对深脱硫钢在LF炉中的脱硫工艺进行分析。
1. 深脱硫钢制备深脱硫钢的制备是深脱硫工艺中的第一步。
其主要原理是利用Ca、Mg、Al等元素与钢液中的硫元素结合,形成稳定的硫化物,达到脱硫的效果。
制备深脱硫钢的过程中,需要将所需的合金元素和除铁渣、氧化物、硫化物等杂质外,控制各种元素含量以形成合适的化学成分。
深脱硫钢中的硫含量较低,要求对钢液中的硫原子进行有效控制,并使钢液的温度和氧化还原条件得到优化。
2. LF炉脱硫处理LF炉是精炼炉中最常用的一种,可有效实现钢液中硫、碳等元素的控制。
LF炉的脱硫处理主要分为两种方式:化学脱硫和加氢脱硫。
其中,加氢脱硫是目前应用较为广泛的一种方法。
(1) 化学脱硫化学脱硫是利用钙、铝、镁等元素与钢液中的硫结合,形成硫化物,从而实现脱硫的过程。
脱硫反应中,反应温度会升高,因此在处理过程中需要严格控制温度,以使反应率得到最优化。
加氢脱硫也是一种常用的脱硫方法。
加氢脱硫的原理是将H2气体注入钢液中,异硫氢酸(HS-)和氢气(H2)直接反应生成H2S气体,从而实现脱硫。
在该脱硫方法中,需要控制钢水的常温pH值,以确保HS-的生成速度,还需要控制加氢速率和通氢量等参数。
3. 脱硫剂的选择在深脱硫钢的制备和LF炉中的脱硫处理中,脱硫剂的选择是关键因素之一。
常用的脱硫剂主要包括CaO/CaF2/纯Ca等。
其中,CaO是最常用的脱硫剂之一,其优点是价格便宜且易于购买。
另外,也可以使用氢氧化钙作为脱硫剂,在加入后溶解生成的氢氧化物可以与钢液中的硫化物反应形成硫化钙。
4. 化学计量比的控制化学计量比是指加入到钢液中的脱硫剂量与钢液中的硫含量之间的比例。
炼钢的脱硫方法

炼钢的脱硫方法
炼钢的脱硫方法是炼钢工艺中的一个重要环节。
在炼钢过程中,铁水中的硫含量会对钢的性能产生不良影响,因此需要进行脱硫处理。
目前常用的炼钢脱硫方法有物理法、化学法和生物法。
物理法主要包括气体脱硫法和渣液脱硫法。
气体脱硫法是将含硫的铁水通过喷吹氧气的方式,使其与氧化剂反应,生成气体二氧化硫,达到脱硫的目的。
渣液脱硫法是将含硫铁水注入含有氧化剂的炉渣中,使其与氧化剂反应,生成气体二氧化硫和固体硫酸钙,达到脱硫的目的。
化学法主要包括碱性脱硫法和氧化剂脱硫法。
碱性脱硫法是将含硫铁水加入碱性溶液中,使其与氢氧化钙反应,生成气体二氧化硫和固体硫酸钙。
氧化剂脱硫法是将含硫铁水加入含有氧化剂的溶液中,使其与氧化剂反应,生成气体二氧化硫和固体硫酸钙。
生物法主要是利用微生物进行脱硫。
这种方法不仅能够有效脱除铁水中的硫,而且还能够将脱除的硫转化为硫酸盐,具有环保、经济的优点。
但是生物法的脱硫速度较慢,需要较长时间的处理。
综上所述,不同的脱硫方法各有优缺点,炼钢厂可以根据自身的生产需要和环保要求选择合适的脱硫方法。
- 1 -。
深脱硫钢在LF炉中的脱硫处理工艺分析

深脱硫钢在LF炉中的脱硫处理工艺分析近年来,随着环保要求的不断提高,钢铁行业对钢的质量要求越来越高。
以深脱硫钢为例,它需要通过一些专门的处理工艺来脱除钢中的硫元素,提高产品的质量。
下面,我们将详细介绍深脱硫钢在LF炉中的脱硫处理工艺。
1. 深脱硫钢的特点及脱硫处理工艺需求深脱硫钢是指钢中硫含量较低的钢种,在一般情况下,硫含量应该在0.005%以下,如果无法达到这个标准,其腐蚀性和机械强度将下降,从而影响产品的质量。
为了达到这样的硫含量,需要使用特定的脱硫剂和设备,并在LF炉中进行脱硫处理。
深脱硫钢需要的脱硫剂一般为2-3mm的石灰石块,它可以在LF炉中迅速分解生成CO2,同时硫元素与钙的化学反应将硫转化为CaS,在渣中形成CaS类物质。
(1)脱硫剂的加入在LF炉的转炉内,需要先加入一定数量的石灰石块(脱硫剂)以达到脱硫的效果。
其加石量一般为顶砖重的0.5%-1.0%。
加入的时间一般为钢水处理的中期,也就是钢水进入LF炉后5-10分钟之后,这样可以让脱硫剂充分产生反应。
(2)温度控制温度控制是LF炉脱硫过程中的关键一步。
石灰石的分解生成CO2的反应速度与温度有关,温度越高,反应速度越快。
因此,在加入脱硫剂后,需要增加炉温,一般控制在1600℃以上,这样可以使脱硫剂充分分解产生反应,为脱除钢水中的硫元素提供充足的时间和工艺条件。
(3)搅拌处理在搅拌过程中,需要将钢水流动起来,以便让脱硫剂能够充分分散和载运。
LF炉的搅拌一般采用氧气喷吹,通过向钢水中注气的方式来搅动钢水,这样可以使石灰石与钢水的接触更加充分。
(4)渣的剔除在脱硫完成后,需要将反应生成的渣进行剔除,这个过程需要控制好剔渣速度和剔渣时间,以避免过剩的渣物质对钢水的影响。
3. 成效评估处理好的钢水,其硫含量应该控制在0.002%-0.005%之间,其机械性能、物理性能和腐蚀性能等指标也需要符合相关的行业标准。
通过合理的工艺处理和评估,可以达到满足深脱硫钢质量要求的目标。
金属冶炼中的脱硫和脱氧技术

能化控制,提高生产效率和产品质量。
环保要求和可持续发展
1 2
绿色冶金的推广
在金属冶炼过程中,加强环保意识,推广绿色冶 金技术,降低对环境的污染和破坏。
资源循环利用
通过金属冶炼过程中的副产物回收和再利用,实 现资源的循环利用,降低能耗和资源消耗。
3
低碳排放和节能减排
通过技术改进和创新,降低金属冶炼过程中的碳 排放和能耗,实现低碳排放和节能减排的目标。
常见的生物脱硫技术包括生物滤池法、生物滴滤塔法等 。
生物脱硫技术的优点是处理效率高、能耗低、操作简单 ,且不产生二次污染。
生物脱硫技术的缺点是处理时间较长,需要适宜的微生 物生长条件,且对硫化物浓度的适应性有限。
化学脱硫技术
化学脱硫技术是指利用化学反 应去除气体中的硫化物,通常
在高温或催化条件下进行。
02
湿法脱硫技术的优点是处理效率高、能耗低、操作简单,适用于处理 低浓度的硫化物。
03
常见的湿法脱硫技术包括碱液吸收法、酸液吸收法、氧化吸收法等。
04
湿法脱硫技术的缺点是会产生大量废水,需要处理后才能排放,对 硫化物浓度的适应性有限。
生物脱硫技术
生物脱硫技术是指利用微生物的代谢作用去除气体中的 硫化物,通常在常温或低温条件下进行。
总结词
钢铁工业中,脱硫和脱氧技术主要用于 提高钢材的质量和性能,减少环境污染 。
VS
详细描述
在钢铁冶炼过程中,硫和氧是常见的杂质 元素,它们会导致钢材的脆性增加、耐腐 蚀性下降等问题。通过采用脱硫和脱氧技 术,可以有效去除钢材中的硫和氧,提高 其机械性能和耐腐蚀性。同时,这些技术 的应用还能减少环境污染,降低生产成本 。
有色金属冶炼中的应用
深脱硫钢在LF炉中的脱硫处理工艺分析

深脱硫钢在LF炉中的脱硫处理工艺分析一、引言随着环境保护意识的加强,钢铁工业对废气排放的要求越来越高。
脱硫处理是钢铁生产过程中非常重要的环保措施,能够有效减少废气中的硫化物排放,降低污染物对环境的影响。
深脱硫钢是一种含硫量较低的高品质钢材,其在LF炉中的脱硫处理工艺分析对于提高钢铁生产质量和环境保护具有重要意义。
二、LF炉中的脱硫原理LF炉是钢铁冶炼中的关键设备,主要用于对钢水进行再脱硫和脱氧。
在LF炉中进行脱硫处理时,主要采用CaO、FeO等还原剂与钢水中的硫反应,生成CaS、FeS等硫化合物,并随废渣一同排出炉外。
还有一部分硫化合物通过气相排出。
LF炉脱硫主要依靠物理、化学相互作用来实现钢水中硫的有效脱除。
三、深脱硫钢的特点深脱硫钢是指钢水中硫含量极低的钢种,通常硫含量小于0.005%。
深脱硫钢的制备需要经过严格的工艺控制和脱硫处理,以确保钢水中硫含量达到要求。
深脱硫钢具有强度高、韧性好、耐腐蚀性强等优点,被广泛应用于汽车制造、船舶制造、航空航天等领域。
四、LF炉中深脱硫钢的脱硫处理工艺1. 硫含量监测:在LF炉中对原料钢水进行硫含量监测,确保原料钢水硫含量符合深脱硫钢的要求。
2. 还原剂添加:LF炉中添加合适的还原剂,如CaO、FeO等,与钢水中的硫发生反应,生成硫化合物。
3. 温度控制:控制LF炉的温度,使脱硫反应能够有效进行,提高硫化合物的析出速度。
4. 气相脱硫:通过气体排放系统对废气进行脱硫处理,减少硫化物的排放。
五、影响LF炉脱硫效果的因素1. 温度:温度是影响LF炉脱硫效果的重要因素,适当的温度有利于脱硫反应的进行。
2. 还原剂的选择:不同的还原剂对脱硫效果有不同的影响,选择合适的还原剂可以提高脱硫效率。
3. 炉型结构:LF炉的结构对脱硫效果也有一定的影响,合理的炉型结构能够提高脱硫效率。
4. 搅拌方式:LF炉中的搅拌方式也会影响脱硫效果,适当的搅拌能够促进硫化合物的析出和排出。
X70快速深脱硫工艺实践探讨

X 7 0 s t e e l i f n i s h e d p r o d u c t 【 S 】 ≤0 . 0 0 2 0 %o f t h e d e e p d e s u l f u r i z a t i o n t a r g e t .
Ke y wor ds : LF f u r na c e; de e p de s ul f ur i z a t i o n; s l a g s y s t e m
Di s c u s s i o n o n X7 0 S t e e l Pr a c t i c e o f Ra p i d a n d De e p De s u l p h u r i z a t i 0 n
Pr o c e s s
XU Ho n g - f e i
E-mai l : x u h f @b y g t . e o m. c n
3 3
2 0 1 3年 第 2期
新疆钢铁
总 1 2 6期
T艺 流程 :高 炉 一铁 水预 处理 一 1 2 0 t 转 炉 吹炼
一
影 响造 白渣 的过程 , 从而 恶 化脱硫 条 件 , 降 低脱 硫效 率 。因此 , 转炉 挡 渣成 功 率 和精炼 初 始温 度 , 往 往也
送管径的加大 , 要求 X 7 0高级别管线钢更具有高强
度、 高韧 性 、 低 韧 脆 变温 度 和 良好 的焊 接 性 能 , 硫 含 量 及 硫 化 物 洁 净 度作 为 钢 的 洁 净 度 的 重 要 标 志 之
一
八钢炼钢管线钢生产要求 ‘ 1 ) ( S S≤4 ) 0 X 1 0 , 与 国外
2 0 I 3 年第 2 期
深脱硫钢在LF炉中的脱硫处理工艺分析

深脱硫钢在LF炉中的脱硫处理工艺分析深脱硫钢是一种具有低硫含量的钢种,其脱硫处理工艺在LF炉中进行。
LF炉是一种用于钢水净化和调温的设备,在钢铁生产中起着重要的作用。
下面将对深脱硫钢在LF炉中的脱硫处理工艺进行分析。
深脱硫钢的主要目标是将钢水中的硫含量降低到较低水平。
脱硫处理的基本原理是将钢水中的硫与氧化剂进行反应,生成易挥发的气态SO2,从而实现脱硫的目的。
LF炉中的脱硫处理主要分为两个阶段:初始脱硫和主要脱硫。
在初始脱硫阶段,通过加入氮气、氧气、喷吹剂等,在钢水中形成一层气泡层。
气泡层能够增加气液接触面积,促进氧化还原反应的进行。
通过调节气泡层的氧化还原环境,控制脱硫反应的进行。
在主要脱硫阶段,根据硫含量的不同,选择适当的脱硫剂,如CaO、MgO等,加入到钢水中。
脱硫剂与钢水中的硫反应生成易挥发的气态SO2。
通过增加脱硫剂的摩擦作用,促进硫在钢水中的扩散,加快脱硫反应速度。
在整个脱硫过程中,需要保持合适的温度和气泡层的稳定性。
温度过低会降低脱硫反应的速度,而温度过高又会导致SO2的挥发速度过快,影响脱硫效果。
气泡层的稳定性也对脱硫效果有重要影响。
稳定的气泡层能够增加气液接触面积,提高脱硫效率。
除了上述基本步骤,还可以采取一些辅助措施来提高脱硫效果。
可以通过调整炉内气氛中的氧气和氮气含量来控制氧化还原环境。
对于较高硫含量的钢水,还可以采取多次脱硫的方法,以进一步降低硫含量。
深脱硫钢在LF炉中的脱硫处理工艺是一个复杂的过程,需要综合考虑温度、气泡层的稳定性、脱硫剂的选择等多个因素。
通过优化这些参数,可以提高深脱硫钢的脱硫效率,得到低硫含量的高质量钢材。
钢结构中的脱硫与污水处理技术

钢结构中的脱硫与污水处理技术引言钢结构是一种重要的建筑结构形式,由于其高强度、轻质和可重复使用的特点,在工业和民用建筑领域得到广泛应用。
然而,钢结构在生产和使用过程中也会产生大量的废水和废气,包括含有高浓度酸性物质的脱硫废水。
因此,研究和应用脱硫与污水处理技术对于保护环境、减少污染排放具有重要意义。
1. 钢结构脱硫技术脱硫是指从废气或废水中去除硫化物的过程。
在钢结构中,脱硫技术主要应用于脱除炉渣中的硫化物,以降低废水的污染程度。
1.1 物理吸附法物理吸附法是利用吸附剂对硫化物进行吸附和分离的一种方法。
常用的吸附剂包括活性炭、分子筛等,它们能够通过表面吸附作用将硫化物分离出来。
这种方法操作简单、成本较低,但处理效果一般。
1.2 化学沉淀法化学沉淀法是利用化学反应使硫化物与其他物质结合形成不溶性沉淀物,从而达到脱硫的目的。
常用的沉淀剂有氢氧化钙、氢氧化钠等。
该方法的优点是处理效果好,但产生的废渣需要进行后续处理。
1.3 生物降解法生物降解法是利用生物体中的微生物对硫化物进行降解的方法。
通过培养合适的微生物群落,将硫化物转化为无毒的物质。
生物降解法具有很好的处理效果,但需要较长的处理时间,且对操作条件要求较高。
2. 钢结构污水处理技术钢结构污水处理技术主要用于处理生产过程中产生的污水,将其中的有害物质去除或降解,以达到排放标准。
2.1 机械过滤法机械过滤法是利用过滤设备将污水中的悬浮颗粒物、沉淀物等固体物质去除的一种方法。
常见的过滤设备有格栅、旋转筛等。
机械过滤法适用于处理大颗粒物质,但对于微小颗粒物质的去除效果较差。
2.2 化学处理法化学处理法主要包括共沉淀法、氧化法等。
共沉淀法是利用化学反应使污水中的有害物质与沉淀剂结合形成沉淀物,从而去除污水中的有害物质。
而氧化法则是通过氧化剂氧化污水中的有机物质,使其变为易于分离的化合物。
2.3 生物处理法生物处理法是利用生物体中的微生物对污水中的有机物质进行降解的方法。
钢铁行业烧结烟气脱硫技术

钢铁行业烧结烟气脱硫技术钢铁行业是我国的重点行业之一,但其生产过程中会产生大量的烟气排放,其中主要有二氧化硫等有害气体。
烟气脱硫技术是钢铁行业对烟气进行治理的关键环节之一。
本文将从烟气脱硫技术的背景、工艺原理、技术方案等多个方面进行探讨,以期提供参考和借鉴。
一、烟气脱硫技术的背景钢铁行业是我国的支柱产业之一,然而,钢铁生产中产生的烟气排放会对环境造成严重的影响,其中二氧化硫的排放量尤为突出。
二氧化硫是一种有害气体,其大量排放会导致酸雨的生成,对生态环境和人体健康造成严重危害。
因此,对钢铁行业的烟气进行脱硫处理变得尤为重要。
二、烟气脱硫技术的工艺原理烟气脱硫技术的工艺原理主要是利用化学反应将烟气中的二氧化硫转化为硫酸盐,从而达到脱除二氧化硫的目的。
常用的烟气脱硫技术包括湿法石灰石法、湿法石膏法、干法石灰-活性炭法等。
下面将具体介绍几种典型的烟气脱硫技术。
1. 湿法石灰石法湿法石灰石法是一种常用的烟气脱硫技术,其工艺流程主要包括石灰石破碎、石灰浆制备、喷射吸收器和石膏浆处理等。
在脱硫过程中,烟气经过喷射吸收器,与喷射进入吸收器的石灰浆进行接触,反应生成硫酸钙,然后硫酸钙与水反应生成石膏,最后通过过滤、浓缩等工序处理石膏浆。
2. 湿法石膏法湿法石膏法是另一种常用的烟气脱硫技术,其工艺流程主要包括石膏浆制备、喷射吸收器、脱水系统和石膏浆处理等。
在脱硫过程中,烟气通过喷射吸收器,并与进入吸收器的石膏浆进行接触,其中的二氧化硫与石膏浆中的氢氧化钙发生反应生成硫酸钙,最后通过脱水系统将石膏浆中的水分去除。
3. 干法石灰-活性炭法干法石灰-活性炭法是一种较新的烟气脱硫技术,其工艺流程主要包括石灰粉和活性炭的混合制备、喷射吸收器和颗粒收集器等。
在脱硫过程中,石灰粉和活性炭经过混合后,喷射进入吸收器与烟气进行接触,石灰粉中的氧化钙和活性炭中的活性成分可以吸附和催化气体中的二氧化硫,从而达到脱硫的效果。
三、烟气脱硫技术的技术方案钢铁行业烟气脱硫技术的选择应根据钢铁生产工艺的特点、地理环境的条件和经济效益等因素综合考虑,以下是几种常用的技术方案。
钢铁制造流程脱硫工艺

钢铁制造流程脱硫工艺引言随着工业的发展,钢铁制造产生了大量的废气和废水,其中含有大量的二氧化硫(SO2)。
二氧化硫是一种有害气体,对环境和人类健康造成了巨大的危害。
为了减少二氧化硫的排放,钢铁制造过程中引入了脱硫工艺。
本文将介绍钢铁制造流程中主要的脱硫工艺及其原理。
1. 石灰石脱硫工艺石灰石脱硫是一种常见的钢铁制造过程脱硫工艺,它主要通过反应碱性氧化物与二氧化硫进行化学反应,使硫化物转化为较稳定的硫酸盐。
具体工艺步骤如下:1.加入石灰石石粉:将石灰石石粉加入脱硫设备的喷射器中。
2.喷射器喷射:利用喷射器将石灰石石粉喷入反应器,与废气中的二氧化硫发生反应。
3.反应:石灰石石粉中的碱性氧化物与二氧化硫发生反应,生成硫化物。
4.氧化:通过加入适量的氧气或空气,将硫化物氧化为硫酸盐。
5.除尘:将除尘器中产生的硫酸盐进行集中处理。
6.脱水:对硫酸盐进行脱水处理,形成固体硫酸盐产品。
7.再生:通过加热脱水后的硫酸盐,使其分解为二氧化硫和石灰石。
石灰石脱硫工艺具有工艺简单、成本低廉的特点,是钢铁制造中常用的脱硫工艺。
2. 氨法脱硫工艺氨法脱硫是另一种常见的钢铁制造过程脱硫工艺,它主要通过二氧化硫与氨气的反应,生成较稳定的硫酸铵。
具体工艺步骤如下:1.加入氨气:将氨气加入脱硫设备的喷射器中。
2.喷射器喷射:利用喷射器将氨气喷入反应器,与废气中的二氧化硫发生反应。
3.反应:二氧化硫与氨气在反应器中进行反应,生成硫酸铵。
4.除尘:将除尘器中产生的硫酸铵进行集中处理。
5.干燥:对硫酸铵进行干燥处理,形成固体硫酸铵产品。
6.再生:通过加热干燥后的硫酸铵,使其分解为二氧化硫和氨气。
氨法脱硫工艺具有高效、脱硫效果好的特点,但成本较高,需要处理产生的废液。
3. 湿法脱硫工艺湿法脱硫是采用吸收剂将二氧化硫吸收至溶液中,通过化学反应转化为硫酸盐或硫酸铵。
湿法脱硫工艺主要包括氧化吸收和还原吸收两个过程:3.1 氧化吸收1.加入吸收剂:将吸收剂加入脱硫设备中的吸收塔。
18X80管线钢深脱硫技术研究
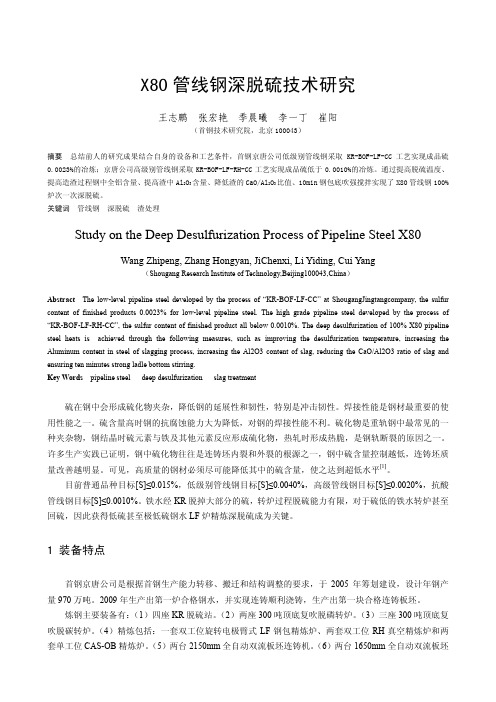
X80管线钢深脱硫技术研究王志鹏张宏艳季晨曦李一丁崔阳(首钢技术研究院,北京100043)摘要总结前人的研究成果结合自身的设备和工艺条件,首钢京唐公司低级别管线钢采取KR-BOF-LF-CC工艺实现成品硫0.0023%的冶炼;京唐公司高级别管线钢采取KR-BOF-LF-RH-CC工艺实现成品硫低于0.0010%的冶炼。
通过提高脱硫温度、提高造渣过程钢中全铝含量、提高渣中Al2O3含量、降低渣的CaO/Al2O3比值、10min钢包底吹强搅拌实现了X80管线钢100%炉次一次深脱硫。
关键词管线钢深脱硫渣处理Study on the Deep Desulfurization Process of Pipeline Steel X80Wang Zhipeng, Zhang Hongyan, JiChenxi, Li Yiding, Cui Yang(Shougang Research Institute of Technology,Beijing100043,China)Abstract The low-level pipeline steel developed by the process of “KR-BOF-LF-CC”at ShougangJingtangcompany, the sulfur content of finished products 0.0023% for low-level pipeline steel. The high grade pipeline steel developed by the process of “KR-BOF-LF-RH-CC”, the sulfur content of finished product all below 0.0010%. The deep desulfurization of 100% X80 pipeline steel heats is achieved through the following measures, such as improving the desulfurization temperature, increasing the Aluminum content in steel of slagging process, increasing the Al2O3 content of slag, reducing the CaO/Al2O3 ratio of slag and ensuring ten minutes strong ladle bottom stirring.Key Words pipeline steel deep desulfurization slag treatment硫在钢中会形成硫化物夹杂,降低钢的延展性和韧性,特别是冲击韧性。
八钢烧结脱硫在高硫原料条件下运行实践

八钢烧结脱硫在高硫原料条件下运行实践摘要:新疆八钢炼铁厂烧结分厂在原料二氧化硫含量不断上升、烧结脱硫系统承载超负荷运行情况下,通过优化配矿结构、完善脱硫系统工艺和烧结脱硫操作等,提高脱硫能力,经过一年多的运行实践,脱硫设施和烧结运转率达到98%以上,脱硫效率达到98%,粉尘排放浓度控制在10mg/m3。
关键词:优化配矿结构;改进脱硫工艺和操作;提高脱硫能力1.前言目前,钢铁行业的SO2等大气污染排放量已占全国工艺排放量的11%左右,仅次于电力行业,居第2位。
其中烧结工序是钢铁工业中排放空气污染物的主要污染源之一,据统计烧结工序产生的SO2约占钢铁生产系统空气污染物中SO2的40%~60%。
随着我国环保标准的日益趋严和防治大气污染的环保立法不断完善,减少烧结工序SO2的排放是钢铁工业实现绿色、可持续发展的必然要求,也是提高钢铁同行业的竞争力的主要途径。
八钢烧结分厂两台265m2烧结机和一台430m2烧结机,脱硫系统于2012年12月投入运行,设计脱硫入口烟气SO2最大浓度是2200mg/Nm3。
近几年随着钢企的发展和铁矿资源的紧缺,八钢烧结铁料SO2含硫不断升高,脱硫入口烟气SO2最大浓度时有超过最大量程3000mg/Nm3,脱硫系统的生产压力陡增,环保风险大,限制了烧结产能。
对此,炼铁厂分厂优化烧结配矿结构、降低混匀料S含量波动幅度、改进脱硫系统工艺控制,提高脱硫能力,将烧结出口排放SO2浓度均值控制在60mg/Nm3以内。
2.烧结烟气特点分析烧结烟气是在将置于烧结机台车上的各种粉状含铁原料、燃料和熔剂点火熔化,高温烧结成型过程中所产生的含有多种污染成分的气体。
烧结烟气主要特点是:(1)烟气量大且波动大。
由于烧结漏风率高(50%以上)和固体物料循环率高,有相当一部分空气没有通过烧结料层,使烧结烟气量大大增加,每产生一吨烧结矿大约产生4000~6000m3烟气,变化幅度可高达40%以上。
(2)烟气温度变化范围大在90~200℃。
毕业设计-深脱硫工艺应用与研究

毕业设计-深脱硫工艺应用与研究
(2)根据硫在渣钢之间的平衡反应(3)和气相与钢水之间的硫氧平衡,可以计算出硫在渣钢之间的分配比。
(3) (4)对于不同的炼钢炉渣,提高碱度和降低炉渣中FeO含量有利于提高炉渣的脱硫能力。
脱硫反应速度由铁水侧和炉渣侧硫的传质速度决定,[10]。
它可以由下式表示:(5)其中是反应面积、铁水重量和渣-钢界面上硫的平衡浓度,并且是传质系数:。
随着炉渣碱度的增加,金属侧流动的传质速度增加,而炉渣侧的传质速度降低。
增加搅拌强度有利于提高脱硫速度。
综上所述,脱硫的最佳热力学、动力学条件是:
(1)提高炉渣碱度,降低炉渣含量;(2)降低钢种的氧活度,提高硫的活度系数;(3)提高处理温度;(4)提高熔池的搅拌强度。
3.2钢水脱硫
钢水脱硫主要取决于脱氧方法和钢水脱氧程度。
钢的平衡如下:
(6) (7)将等式(7)代入等式(4),可以获得钢水脱硫的热力学条件。
(8)从方程(8)可以看出,影响钢水脱硫的主要因素是:(1)钢水和炉渣的氧化。
白渣处理(FeO+MnO。
浅析八钢烧结烟气脱硫方案的选择
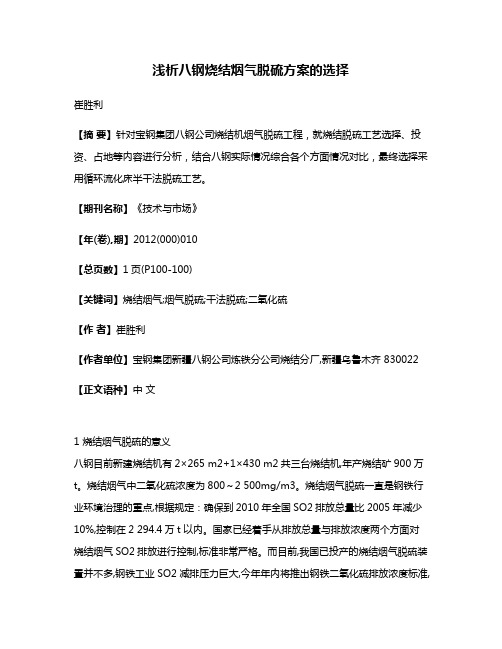
浅析八钢烧结烟气脱硫方案的选择崔胜利【摘要】针对宝钢集团八钢公司烧结机烟气脱硫工程,就烧结脱硫工艺选择、投资、占地等内容进行分析,结合八钢实际情况综合各个方面情况对比,最终选择采用循环流化床半干法脱硫工艺。
【期刊名称】《技术与市场》【年(卷),期】2012(000)010【总页数】1页(P100-100)【关键词】烧结烟气;烟气脱硫;干法脱硫;二氧化硫【作者】崔胜利【作者单位】宝钢集团新疆八钢公司炼铁分公司烧结分厂,新疆乌鲁木齐 830022【正文语种】中文1 烧结烟气脱硫的意义八钢目前新建烧结机有2×265 m2+1×430 m2共三台烧结机,年产烧结矿900万t。
烧结烟气中二氧化硫浓度为800~2 500mg/m3。
烧结烟气脱硫一直是钢铁行业环境治理的重点,根据规定:确保到2010年全国SO2排放总量比2005年减少10%,控制在2 294.4万t以内。
国家已经着手从排放总量与排放浓度两个方面对烧结烟气SO2排放进行控制,标准非常严格。
而目前,我国已投产的烧结烟气脱硫装置并不多,钢铁工业SO2减排压力巨大,今年年内将推出钢铁二氧化硫排放浓度标准,钢铁企业在选择烧结脱硫技术上将有法可依。
因此,烧结烟气脱硫势在必行。
2 八钢烧结烟气主要特点①八钢烧结作业率较高,大约93%以上,产生的烟气量大。
2×265 m2+1×430m2三台烧结机烟气量为2×160万m3/h+1×240万m3/h(工况)。
②烟气温度较高。
随烧结工况变化大,大烟道中的烟气温度一般在80℃~160℃。
③烟气粉尘浓度高。
粉尘主要以铁及其化合物为主,由于使用不同的原料还可能含有微量重金属元素及碱金属元素。
④烟气中含湿量大。
为了提高烧结料层的透气性,混合料在烧结前加水混合、制粒,按重量比计算,水分含量一般在7%~8%左右。
⑤含有害气体。
烟气中含有一定量的SOx、NOx、HCl和HF等,它们遇水后将形成酸雨,腐蚀金属构件。
- 1、下载文档前请自行甄别文档内容的完整性,平台不提供额外的编辑、内容补充、找答案等附加服务。
- 2、"仅部分预览"的文档,不可在线预览部分如存在完整性等问题,可反馈申请退款(可完整预览的文档不适用该条件!)。
- 3、如文档侵犯您的权益,请联系客服反馈,我们会尽快为您处理(人工客服工作时间:9:00-18:30)。
八钢管线钢深脱硫技术的探讨作者:徐鸿飞来源:《大陆桥视野·下》2013年第08期摘要为了快速有效地实现高级别管线钢的深脱硫技术,本文通过生产实践对管线钢脱硫各影响因素的分析,通过对转炉出钢“渣洗”工艺的实施,精炼初炼温度、渣量、强搅拌工艺等热力学和动力学条件的改善,实现高级别管线钢成品[S]≤0.002 0%的深脱硫目标。
关键词 LF炉深脱硫渣系一、前言随着输送石油、天然气效率的提高,输送管径的加大,高级别管线钢更趋向高强度、高韧性、低韧脆变温度和良好的焊接性能的方向发展,而硫含量及硫化物洁净度作为钢的洁净度的重要标志之一,对钢材性能有重要影响,直接影响到钢的抗腐蚀性能,以及形成的塑性夹杂物恶化钢的各向异性。
近年来,用户对低硫钢和超低硫钢(ω(S)≤40×10-6)的需求量日益增加,一些特殊用途的高级钢,对ω(S)的要求往往低于20×10-6,国外有的厂家甚至低于10×10-6。
因此,降低硫含量和改变夹杂物形态的钙处理工艺,提高板卷的横向冲击韧性和减少性能的方向性,是优质生产管线钢的关键工艺。
目前八钢股份炼钢厂管线钢生产要求ω(S)≤40×10-6,与国外相比还有很大差距,而八钢二炼钢厂采用“三机对四炉”的作业体系,对实现快速深脱硫、提高单机作业率提出了更高的要求。
因此,研发管线钢精炼深脱硫技术及应用具有重要的实用价值。
二、工艺流程高炉-铁水预处理-120 t转炉吹炼-出钢合金化-LF+RH二次精炼-板坯连铸-轧制。
三、工艺现状及影响因素分析1.LF精炼深脱硫机理。
LF深脱硫必须满足良好的热力学和动力学条件,而大渣量、高碱度、适当高的钢水温度、较低的炉渣氧化性、良好的吹氩搅拌以及钢水钙处理是钢水深脱硫的有利条件。
脱硫反应的基本离子方程可表示为:[S]+(O2-)=[O]+(S2-)上式是一个吸热反应,高温有利于脱硫反应进行。
温度的重要影响主要体现在高温能促进石灰溶解和提高炉渣流动性。
影响钢水脱硫效果的热力学因素主要包括:渣的硫容量(CS)和硫在钢-渣间的分配系数(LS);钢水温度及炉渣黏度。
2.炉渣对脱硫的影响。
通常脱硫反应需要提高炉渣的碱度,碱度高,游离的CaO多,或(O2-)增大,有利于脱硫。
但过高的碱度,常出现炉渣黏度增加,反而降低脱硫效果。
而从热力学角度可以看出,脱硫反应是在还原性气氛中进行,渣中的(FeO)高不利于脱硫。
当炉渣碱度高时、流动性差时,炉渣中有一定量的(FeO),可助熔化渣。
在实际生产中,当渣中ω( FeO+ MnO)< 1%时,脱硫反应速率会得到显著的提高。
当(FeO)图1 渣中FeO含量与硫分配系数的关系3.渣量及初炼温度对脱硫的影响。
在实际生产现场,转炉出钢下渣过多和备包时间过长,会使钢中氧含量增加、精炼初始温度降低,影响造白渣的过程,从而恶化脱硫条件,降低脱硫效率。
因此,转炉挡渣成功率和精炼初始温度,往往也制约到精炼的脱硫效率。
钢液最终[S]量与初始钢液及钢包顶渣含硫量ΣS和渣量b有关系如下:[S]=ΣS-(S)×b÷100 (1)可见,增大渣量有利于脱硫。
要取得理想的深脱硫效果,应严格控制初始钢中[S]含量及转炉出钢下渣量,并适当增加LF造渣材料的加入量,渣量与脱硫速率的关系如图2所示。
脱硫反应的平衡常数KS与温度的关系式为:lgKS=-5743/T+1.621 (2)在平衡条件下,KS与温度成正比,提高温度有利于脱硫。
虽然KS随温度的变化值不大,但提高钢、渣温度可以改善其流动性,增大钢渣界面反应面积,提高脱硫速度,从而加速脱硫过程,钢水温度与脱硫率的关系如图3所示。
4.钢包底吹Ar搅拌对脱硫的影响。
钢包底吹氩搅拌具有两种功能:一是均匀钢水的成分与温度,促进夹杂的上浮;二是加快渣-钢的反应。
两种功能在气体流量的临界点上下表现是不一样的。
当气体流量高于临界点时,对渣-钢反应有利。
搅拌气体量增加时,脱硫反应速率急剧增大,原因是渣粒卷入金属熔池增大了渣-钢接触界面,促进了脱硫反应的快速进行,前提条件是[ S]比较高。
对于底吹 Ar 搅拌方式,通过顶渣脱硫,脱硫反应速率在不同[ S] 浓度下,限制环节是不同的。
[ S] ≥0. 005%以上时, Ar 气的搅拌能力是限制环节;当[ S] ≤0. 005%时, S 的传质是限制环节。
5.渣系对脱硫的影响。
根据精炼渣系的选择原则,脱硫渣系主要有CaO-CaF2、CaO-CaF2-Al2O3、CaO-SiO2-Al2O3等,其中CaO- CaF2的渣系硫容量最高,其脱硫能力也最强因此,在不具备喷粉的条件下,采用CaO- CaF2脱硫单从脱硫角度讲,CaF2的含量最好为30%左右,此时计算硫容比可达到140以上,但考虑到钢包的侵蚀,实际上一般将CaF2含量约控制在15%。
但此类渣系需要在温度较高的冶炼环境下,方可发挥良好的脱硫效果。
在实际生产中,往往需要选择熔点更低、易渣化、吸附夹杂更强的渣系,同时具有经济高效、能实现快速脱硫,那么,通过CaO-SiO2-Al2O3三元相图,结合八钢现有工艺条件,试验适用于管线类钢的脱硫工艺,其意义非常深远。
四、LF精炼深脱硫实践及操作1.转炉出钢环节的控制。
提高转炉终点一次命中率,降低再次次数,适当提高出钢温度,出钢温度控制在1 630 ℃以上,充分利用出钢过程中高温钢流的搅拌“渣洗”脱硫,具体措施是在出钢至20%时左右时,开始短时间内向钢包内快速地加入合金、脱氧渣等,改善包内顶渣环境,增加钢水与加料的接触时间和面积,达到快速形渣、提高脱硫率的目的。
除此之外,出钢过程脱硫率还受到加入量和钢渣氧化性等动力学条件的影响,采用下渣检测技术,提高挡渣率,控制包内渣厚低于100 mm,降低转炉终渣中的TFe含量,提高渣料加入量,可增加相对硫容量,通过降低顶渣熔点来促进钢-渣以及渣-渣间的界面反应,既具有提高出钢过程脱硫率和降低顶渣氧化性的双重作用。
采用此方法后,降低了LF精炼脱硫的处理时间,缩短了精炼时间,降低精炼电耗,降低精炼劳动强度,快速完成钢水成分控制,降低了精炼成本,且脱硫率较高,采用转炉出钢渣洗脱硫的经验,平均脱硫率控制为20%~30%,基本实现精炼初始硫小于8×10-6的目标。
2.生产调度环节的控制。
采用品种钢调度系统组织生产,提高钢包的热周转率,降低钢水的过程温降,将出钢至LF精炼环节的闲置时间控制在25 min内,确保精炼初炼温度在1540 ℃以上,缩短LF精炼脱硫时间。
3.LF精炼环节的控制。
在确保LF精炼有良好初始温度的前提下,LF精炼冶炼初期采取早化渣、化好渣的控制策略,合理控制炉渣碱度和熔渣的流动性,并根据渣面状况,适当适时地配加一定量的石灰、高铝渣球、合成渣等精炼脱氧渣料,也可在渣面撒入少量铝粒,降低炉渣中TFe含量,根据八钢工艺现状,前期渣量宜控制在13 kg/t,中后期根据渣况控制目标渣系;通过LF精炼前期的造渣、化渣、调渣等环节,将钢水温度快速提升至1 560 ℃以上,停电蘸取炉渣判断氧化性,当渣中w( FeO)≤1.0%~1.5%时,炉渣呈白色,即通常所说的白渣,是快速脱硫的最佳时机,此时采取吹Ar强搅拌模式进行快速脱氧、脱硫,搅拌时间根据渣样颜色和脱氧程度约控制在2 min~5 min,搅拌过程中注意炉内气氛的微正压操作,并适当加入少量的埋弧剂,避免脱氧钢水的二次吸氮,此环节脱硫率可达到50%以上,甚至一次将钢中的[S]直接脱至2×10-6以下;LF精炼中后期,注重渣系的调节和控制,由于此时钢水已经处于强还原气氛状态,脱硫水平已经减缓,钢液中的[S]已经接近或者达到控制目标,吹氩气流宜控制不裸露钢液面为标准,适当调整活性石灰的加入量,控制目标精炼顶渣指标为:CaO≈50%~60%,SiO2≤6%,Al2O3≈20%~30%,为控制钢液吸所及脱除夹杂物创造条件。
为确保脱硫效果和夹杂物的变性处理,冶炼末期需要进行钙处理作业,同时注意控制钢中的酸溶铝[Als]=0.025%~35%之间,钙处理时,合理控制喂线速度和节奏,避免钢液面发生强烈钙蒸气反应,确保夹杂物的变性和实现脱硫的双赢效果。
五、工艺效果八钢通过开展对管线钢快速深脱硫技术的工艺实践,结合原有工艺环境,有针对性地采取了一系列的工艺优化,图4是对工艺实施前后X70管线钢脱硫水平的控制效果图(各随机取12炉次的样本)。
图4 工艺实施前后X70管线钢脱硫水平控制效果图上述控制曲线显示,工艺改进前成品[S]控制波动较大,且靠近成分上限值炉次较多,工艺优化后,成品[S]控制线较为平稳,说明工艺得到稳定化和可控化,最好值达到了[S]=0.001 1%的水平,最高值也只有0.002 0%,平均值达到了0.001 59%,实现了控制目标。
六、结论通过对脱硫一系列热力学和动力学条件的分析和实践,结合八钢现有炼钢环境和工艺特点,在开展管线钢深脱硫的实践中,LF精炼生产X70系列管线钢可以实现40 min内快速将[S]从0.008%深脱硫降至0.002%以下。
而要实现此冶炼周期,需要满足以下条件:(1)控制好转炉出钢环节的“渣洗”脱硫,杜绝出钢过程的下渣,确保包内形成良好的顶渣和预脱氧条件,确保出钢过程中的脱硫率,降低精炼环节初始硫和化渣时间;(2)提高钢水出钢温度,减少钢水的闲置时间,确保LF精炼初炼温度在1 540 ℃以上,缩短LF精炼脱硫时间,争取早化渣、化好渣,降低炉渣中TFe含量,当渣中w( FeO)≤1.0%~1.5%时,抓住快速脱硫的最佳时机,采取吹Ar强搅拌模式进行快速脱氧、脱硫,搅拌时间根据渣样颜色和脱氧程度约控制在2 min~5 min;(3)控制目标精炼顶渣指标为:CaO≈50%~60%,SiO2≤6%,Al2O3≈20%~30%,为控制钢液吸所及脱除夹杂物创造条件。
参考文献[1]张占省,胡志刚,赵彦华,等.转炉出钢过程中渣洗脱硫的试验研究.河北冶金,2008,6:9-11.[2]黄希钴.钢铁冶金原理[M].北京:冶金工业出版社,2007.[3]成国光,宋波,陆钢,等. 钢液深脱硫精炼工艺的研究[ J] . 钢铁, 2001, 36( 3): 21 -23.[4]姜周华,张贺艳,战东平,等. LF 炉冶炼超低硫钢的工艺条件[ J] . 东北大学学报:自然科学版, 2002,23 ( 10): 952 -955.[5]张鉴.炉外精炼的理论与实践[M].北京:冶金工业出版社, 1991:517.[6]张彩军,朱立光,蔡开科等[J]. LF 精炼渣脱硫的理论与工业实验研究.河南冶金,2006,14( 4): 9.。