塑胶(料)件设计与注塑
塑胶加工工艺

塑胶加工工艺
塑胶加工工艺指的是将塑胶原料通过加热熔化后注射、吹塑、挤塑等方式加工成所需的形状和产品的过程。
常见的塑胶加工工艺包括:
1. 注塑成型:将熔融的塑胶注入模具中,通过冷却固化后得到成型的产品。
注塑成型广泛应用于电子、家电、汽车等行业。
2. 吹塑成型:将加热融化的塑胶通过气压吹塑成型。
此工艺适用于生产中空容器,如塑料瓶、塑料桶等。
3. 挤塑成型:将塑胶颗粒或熔融的塑胶料挤出成型。
这种工艺适用于生产长条状或异形的产品,如塑料管道、塑料板材等。
4. 压制成型:将熔融的塑胶料注入压制机中,经过热压成型得到所需产品,常用于生产硬质塑料制品。
5. 旋转成型:塑胶原料在模具内通过旋转方式均匀覆盖在模具内壁,经过加热固化后得到中空球体产品,如塑料球、婴儿座椅等。
6. 真空成型:将加热塑胶片条材吸附在模具表面,通过真空吸气将塑胶件变形成型。
以上仅列举了常见的塑胶加工工艺,不同工艺的选择取决于产品的形状、尺寸和要求等因素。
塑胶模具加工及注塑工艺介绍

塑胶模具加工及注塑工艺介绍
1、 塑胶模的基本组成有哪几部分? 塑胶模的基本组成为:模架(整个模芯的支承部分)、模腔(塑胶材料的流通通道)、模 芯(决定产品成型的结构)、压板(固定模芯用)、定位导柱、水冷系统组成部分。 1、 模架常用的材料是什么? 2,模架常用的材料有:S55、S45、S50、日本产的富得巴。 3、 什么叫镶件?镶件的常用材料是什么?作用是什么? 镶件是组成模芯的一系列的拼接件。镶件的常用材料为日本大同的SAD61、AK80,镶件的 作用主要是组成复杂的模芯,在注胶时形成复杂的产品。 4、 模具一般需经过哪些热处理过程?热处理的作用是什么? 模具一般需经过淬火、调质、渗氮等热处理过程。 热处理的作用是增加模具的硬度,强度,去除内应力,以增加模具的寿命。 5、 什么叫蚀纹?蚀纹分哪些种类?有什么区别? 蚀纹是在模具表面用化学或电加工的办法制作出不同纹路的底纹,以增加塑胶件的表面效 果,提高产品的成品率。蚀纹根据加工方法不同,分为化学蚀纹和电火花蚀纹,根据蚀纹 效果的不同分为细纹和粗纹。化学蚀纹一般加工效率低,易形成均匀的细纹,电火花蚀纹 加工效率高,易于形成不同的粗纹,但均匀性不佳。 6、 什么叫脱模剂?常用的脱模剂有哪些?作用是什么? 脱模剂是涂覆在模具表面的油剂,在注胶后能够使工件易于拔模脱落。 常用的脱模剂有干性、中性、油性之分,油性越高,对工件的表面效果影响越大。 7、 模具的精度由哪些因素决定? 模具的精度由加工精度、装配精度、定位精度等因素决定。 8、 选择模具分型面要考虑哪些因素? 选择模具的分型面主要考虑拔模和抽芯的方便程度。 9、 什么叫拔模斜度?拔模斜度的范围是多少? 拔模斜度是指塑胶的模芯为了从已成型的塑胶件中方便抽出,同时不伤塑胶件,模芯通常 有一个斜度,这个斜度叫拔模斜度。拔模斜度的范围一般在0.5°-1° 。 10、什么是行位?什么是型芯?抽芯的长度受哪些因素限制?
注塑成型介绍及工艺介绍

b.射速、射出、保压、背压、螺杆转速分段控制。
c.搅拌性、寿命长的螺杆装置。
d.料管互换性,自动清洗。
e.油泵之平衡、稳定性。
2.锁模系统
a.高速度、高钢性。
b.自动调模、换模装置。
c.自动润滑系统。
d.平衡、稳定性。
基本结构: 1.公模(下模) 公模固定板、公模辅助板、顶针板、公模板。 2.母模(上模) 母模板、母模固定板、进胶圈、定位圈。 3.衡温系统 冷却.稳(衡)定模具温度。
四、 注塑机
主要由塑化、注射装置,合模装置和传动机构组成; 电气带动电机,电机带动油泵,油泵产生油压, 油压带动活塞,活塞带动机械,机械产生动作;
公司产品主要用于油汀,如:部分油汀的面板.烘衣架.电子油汀透明罩等等;
100度 2.干燥条件:100度至120度4小时以上。 3.料管温度:250度至300度 4.热变形温度:130度左右; 5.模具收缩率:0.5%-0.7%
PC材料之流动性随温度升高则越高,因温度调节在成型上占比重较大。
目前大部分使用的塑料有:PP ABS PBT PC PA PPS POM 等。
1、 PP料:(聚丙烯polypropylene) 目前大部分使用的厂牌有:
中国石化 台湾化纤 镇海炼化 韩国现代 新加坡mytex 印度SEETEC
特性: 比重较轻,流动性好,无色.无味.无臭.无毒,光泽度.拉伸强度.耐热性能好,二次加工性能好,有良好的绝缘性.化学稳定性;加上价格低廉,主要适用于编织袋.玩具.周转箱.家电.管材.板材等。
增高密度,这时螺杆对塑料施加的压力叫保压;
3.锁模力: (吨位)
锁模机构对模具所能施加的最大夹紧力;
塑胶件设计规范范文
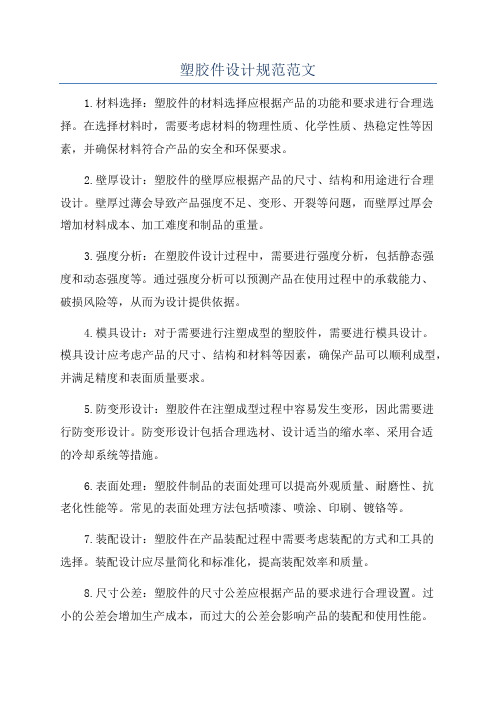
塑胶件设计规范范文1.材料选择:塑胶件的材料选择应根据产品的功能和要求进行合理选择。
在选择材料时,需要考虑材料的物理性质、化学性质、热稳定性等因素,并确保材料符合产品的安全和环保要求。
2.壁厚设计:塑胶件的壁厚应根据产品的尺寸、结构和用途进行合理设计。
壁厚过薄会导致产品强度不足、变形、开裂等问题,而壁厚过厚会增加材料成本、加工难度和制品的重量。
3.强度分析:在塑胶件设计过程中,需要进行强度分析,包括静态强度和动态强度等。
通过强度分析可以预测产品在使用过程中的承载能力、破损风险等,从而为设计提供依据。
4.模具设计:对于需要进行注塑成型的塑胶件,需要进行模具设计。
模具设计应考虑产品的尺寸、结构和材料等因素,确保产品可以顺利成型,并满足精度和表面质量要求。
5.防变形设计:塑胶件在注塑成型过程中容易发生变形,因此需要进行防变形设计。
防变形设计包括合理选材、设计适当的缩水率、采用合适的冷却系统等措施。
6.表面处理:塑胶件制品的表面处理可以提高外观质量、耐磨性、抗老化性能等。
常见的表面处理方法包括喷漆、喷涂、印刷、镀铬等。
7.装配设计:塑胶件在产品装配过程中需要考虑装配的方式和工具的选择。
装配设计应尽量简化和标准化,提高装配效率和质量。
8.尺寸公差:塑胶件的尺寸公差应根据产品的要求进行合理设置。
过小的公差会增加生产成本,而过大的公差会影响产品的装配和使用性能。
9.耐用性设计:塑胶件在使用过程中需要具有一定的耐用性。
耐用性设计包括选择合适的材料、优化结构、进行耐久性测试等。
10.产品标识:塑胶件在制造过程中需要进行产品标识,包括产品型号、批次号、生产厂家等信息。
产品标识有助于产品追溯和质量控制。
请注意,以上只是一些常见的塑胶件设计规范,具体的设计规范还需根据具体产品和行业的要求来确定。
在进行塑胶件设计时,还需充分考虑产品的使用环境、工艺要求和成本等因素,确保产品的质量和可生产性。
塑胶件的成本计算公式

塑胶件的成本计算公式塑胶产品成本计算公式塑胶产品成本计算公式单价(VAT/17%)=材料费+加工费+包装费+管理费+税一、材料费:1、塑胶原料:A、透明产品:(产品净重+50%水口+5%损耗)X原料价格(VAT/17%)。
B、不透明产品:(产品净重+2%损耗)X原料价格(VAT/17%)。
2、油漆费:(喷油后产品重量-注塑产品重量+15%损耗)X色漆价格(VAT/17%)。
3、铜花母:价格按0.10元/个计算。
二、注塑及其加工费:1、成型费标准:注塑机型/吨位(T) 成型费(元/分钟)海天/80T ¥0.48海天/110T ¥0.57海天/150T ¥0.62海天/200T ¥0.75海天/250T ¥0.892、喷油费:A、大件产品(如外壳):价格按0.05元/个(含人工费)计算。
B、小件产品(如按键、封帽等):价格按0.05元/排(含人工费)计算。
3、丝印费A、普通丝印(1~3行字或符号):价格按0.03元/次/颜色(含材料和人工费)计算B、大丝印(4行字或符号以上):价格按0.04元/次/颜色(含材料和人工费)计算。
C、镜片丝印:加5%成品损耗。
注塑件费用=材料费+加工费+包装费+运输费说明:1. 材料费=【(1+材料损耗)*产品重量*批量+调机损耗材料重量+正常报废率*产品重量*批量】*材料单价/批量其中材料损耗一般为3%-5%;调机损耗材料重量和正常报废产品重量一般产品为5000g---15000g2.加工费=(调机时间/批量+成型时间/模具穴数)*注塑机工缴费其中据我了解目前上海地区注塑机工缴费按注塑机吨位区分为(国产设备)设备吨位(T ) 工缴费( 元/小时) 设备吨位(T ) 工缴费( 元/小时)80 35-45 200 110-160100 45- 60 250 150-200120 65-85 300 180-220150 80-110 350 200-250180 95-140 400 250-350另一种注塑价格核算方法是按材料区分,规定材料价格*产品重量。
塑胶成型的几种方法

塑胶成型的几种方法1.引言1.1 概述塑胶成型是一种常见的制造工艺,用于生产各种塑胶制品。
它是将熔化的塑胶材料通过一系列工艺流程加工成所需的形状和尺寸。
塑胶成型方法多种多样,每种方法都有其适用的领域和特点。
一般而言,塑胶成型方法可分为热流道成型、注塑成型、吹塑成型和挤出成型等几种常见的方法。
热流道成型是利用热流道系统将熔化的塑胶材料注入模具中,通过模具的开合运动形成所需的产品形状。
热流道成型具有生产效率高、产品质量稳定等优点,适用于生产高精度和高质量要求的塑胶制品。
注塑成型是将熔化的塑胶材料注入到模具中,并经过冷却固化成型的工艺过程。
注塑成型具有成本低、生产效率高、产品尺寸精度高等特点,广泛应用于各个行业,如汽车零部件、电子产品外壳等。
吹塑成型是将加热融化的塑胶材料注入到吹塑机中,通过气压将塑胶膨胀成型,最后冷却固化而成。
吹塑成型适用于生产空心的塑胶制品,如瓶子、容器等,具有生产效率高、产品质量稳定等优点。
挤出成型是将塑胶颗粒或熔化的塑胶材料经过挤出机的螺杆加热、挤压,使其通过模具的开合形成所需形状。
挤出成型适用于生产连续型的制品,如塑胶管材、板材等,具有生产效率高、生产成本低等特点。
综上所述,塑胶成型方法多样,每种方法都有其适用的领域和特点。
在选择合适的塑胶成型方法时,需要考虑产品设计要求、生产效率、质量稳定性等因素,以确保生产出符合需求的优质塑胶制品。
1.2 文章结构文章结构部分的内容如下:文章结构:本文将对塑胶成型的几种方法进行详细介绍和分析。
首先,将在引言部分概述本文的主要内容,包括对塑胶成型方法的概述和文章的目的。
接下来,在正文部分,将分别介绍两种常见的塑胶成型方法,包括方法1和方法2,并对它们的原理、特点以及在实际应用中的优缺点进行详细阐述。
最后,在结论部分,将对本文进行总结,并对未来的研究方向和进一步的改进提出展望。
通过对不同的塑胶成型方法的介绍和分析,本文旨在帮助读者更全面地了解塑胶成型的原理和方法,从而为相关领域的研究和实践提供参考和指导。
塑胶件注塑工艺关键技术

塑胶件注塑工艺关键技术
塑胶件注塑工艺的关键技术包括以下几个方面:
1.模具设计:模具是注塑工艺的基础,其设计是否合理直接影响到产品的质量和生产效率。
模具设计应根据塑胶件的结构、尺寸、精度要求等因素进行,确保模具的强度、刚度和耐久性。
2.注塑机选择:注塑机是实现注塑工艺的重要设备,其选择应根据生产规模、塑胶类型、制品精度和生产环境等因素进行。
3.原料选择:塑胶原料的种类和品质直接影响到制品的性能和品质,应根据产品要求选择合适的原料,确保生产出的塑胶件符合设计要求。
4.注塑工艺参数控制:注塑工艺参数如注射压力、注射速度、模具温度等对制品的质量和生产效率有很大的影响。
在实际生产中,应根据原料的性能和塑胶件的特点,设置合理的工艺参数。
5.质量控制:在注塑过程中,应对制品进行严格的质量检查,确保其符合设计要求。
常见的质量控制方法包括尺寸测量、外观检查、性能测试等。
6.环境保护:注塑工艺会产生一定的废气、废水和固废等污染物,应采取有效的治理措施,保护环境。
7.人员培训和管理:操作人员的技能和素质对注塑工艺的质量和效率有很大的影响,应对其进行专业的培训和管理,确保其按照规定的要求进行操作和维护设备。
以上是塑胶件注塑工艺的关键技术,在实际生产中,应根据具体情况进行合理的选择和应用,以确保生产出的塑胶件符合设计要求,提高生产效率和质量。
塑胶件设计规范

1. 目的:制订塑胶件设计规范,以利所有RD及PE人员在作塑胶件设计时能有所依循。
2.范围:本公司所有塑胶件的设计。
3.权责:.:RD或PE:图面的绘制。
.:模具课或供应商:塑胶模具的制作。
.:成型课:产品射出成型.4.定义:无。
5.作业内容:.产品材质的选用.根据不同的产品选用不同的材质.我司一般所用的塑胶料材质分为以下几类:5.1.1PC料其组成成为聚碳酸酯.材料特性为耐高温、耐腐蚀、耐磨性.尺寸稳定性高.且具有一定的刚性及韧性.其熔融状态下流动性较差.根据防火等级不一样又可分为PC94-V0(公司所用P4 478塑胶扣具旋转把手就选用此料)、PC94-V2(一般COVER与RM均选用此料).PC94-V0的防火等级要高於PC94-V2.另PC料可以用玻璃纤维来增强其刚性和力学强度.以达到受一定的压力而不变形.根据加玻纤的百分比不一样可以分PC+10%GF、PC+20%GF(P4塑胶扣具把手与主体选用料).PC料在设计时的肉厚最佳范围在~之间.PA66(俗称尼龙)其组成成分为聚胺.材料特性为具有良好的电气性能、热性能及力学综合性能,其力学强度随温度而异.在熔融状态下有很高的流动性.吸水性大.(与RM相配的黑白小豆豆选用料) .结构的设计.COVER结构设计所依规范.a.与风扇配合的螺丝孔中心距离.五公分的为40mm,六公分为50mm,七公分为,八公分为,且孔距公差要控制在±以内.b.Cover中间方孔要做到至少与风扇内框即出风口一样大,使cover不能挡住风扇风量.模具的设计模具设计首先根据产品的大小、材质、注塑机的规格决定模具的模穴数及模架的规格.(一般的模架的规格不能超过480*450MM)根据图纸的要求进行模具的设计(包括重点尺寸的控制、流道的设计、浇口的设计、顶针位置的设计以及脱模角度的控制等.设计时尽量要求好成型、好脱模、注塑时间短.根据所设计的模具在电脑上用Pro-E进行模流分析,看是否有注不满,有气泡等不良现象.模具设计的注意事项A.要考虑料流畅通填充型腔,尽量避免尖角、缺口.B.在不影响产口尺寸及功能的情况下尽量将脱模斜角取大.一般为~2度.C.设计浇口应考虑孔止填充不足,异向性变形,易产生熔接痕等因素.D.模具型芯、型腔应有足够刚性、强度及耐腐蚀性.E.顶出机构应均有力,便於换修.F.模具应设有排气斜槽,并宜设於易发生熔接痕部位.模具的制作.模具的制作需要严格按照模具图纸制作.模芯模腔加工要保证平面度、粗糙度.特别要注意重点尺寸的把握.模具试模.塑胶料的准备.根据产品的要求选用塑胶料.(我司通常所用的塑胶料有PC 料、PC加玻纤、尼龙NA66)PC料要试模前要经过洪干处理.120度连续四小进烘干使水份降在%以下.NA66料需要在成型前经过烘干处理.90度连续烘干五小时使水份降在%以下.注塑成型.A.试模前模具检查.a.外观检查.b.空运转检查.B.模具试模一般PC料的成型温度要控制在270~320度.NA66料的温度控制在260~275度之间.产品尺寸及功能检验.根据产品图检验注塑成型後的产品各尺寸是否合格.另实际组装是否有干涉.。
塑胶模具的科学注塑方法研究及应用

塑胶模具的科学注塑方法研究及应用摘要:传统的注塑试模过程,往往只是获取注塑机床及辅助设备上显示的表面上的成型参数,这些参数不能够反应注塑过程的真实情况,导致所得参数的可复制性差,不能有效指导批量生产。
本文从塑胶材料的角度出发,基于材料本身的流动行为,研究制定了一套科学的注塑方法,获取塑胶材料在干燥、熔胶、注塑填充、补缩、保压、冷却等过程中实际的温度、压力、速度、时间、位置等参数数据;这些参数不受试模机床差异、辅助设备差异以及它们本身精度的影响,能有效指导批量生产。
本文为注塑试模调试人员及生产调机人员提供了一套标准的、科学的试模流程和方法,并附以案例说明。
关键词:科学注塑、试模、塑胶、模具、成型参数Research and Application of Scientific Injection Molding Method for Plastic MouldZhengZichengGree Electric Appliances,Inc.ofZhuhaiZhuhai,Guangdong519000Abstract: In the traditional injection molding trial process, the molding parameters on the surface displayed on the injection molding machine and auxiliary equipment are often obtained, but these parameters cannot reflect the real situation of the injection molding process. As a result, the reproducibility of the obtained parameters is poor and the batch production can not be effectively guided. Based on the flow behavior of plastic materials, a set of scientific injection molding methods is developed in this paper. Obtain actual temperature, pressure, speed, time, position and other parameter data of plastic materials during drying, glue melting, injection filling, feeding, pressure maintaining, cooling and other processes; theseparameters are not affected by the difference of testing machine tool, auxiliary equipment and their own accuracy, and can effectively guide batch production. This paper provides a set of standard and scientific test process and method for injection mould commissioning personneland batch production adjustment personnel, and a case is attached.Key words: scientific injection molding, trial molding, plastic, mold, molding parameters1、前言:塑胶模具的试模是指在模具零部件完成加工制作、模具组装完毕后,在批量生产之前通过注塑机进行注塑试生产并得到注塑件样品,然后通过对样品的检测、装配、实验测试情况,以及试生产过程中对模具各方面的符合性排查评估,来确定该模具是否符合设计要求、满足批量生产要求的过程。
塑胶产品注塑成型工艺

塑胶产品注塑成型工艺塑胶类零件制造过程,根据需要先要进行塑胶成型、加工成各类塑胶半成品或部件,注塑成型是塑胶零件主要的成型方法之一。
注塑成型必须借助注塑机等成型设备和注塑模具才能完成,对于注塑原理与工艺流程以及注塑模具结构和原理等理论内容在其他有关资料中都有详尽的描述,在此不必重复。
本章主要介绍在塑胶产品制造过程中常涉及的实际内容和问题。
2.1概述塑胶产品制造过程中,塑胶件成型是其中十分重要内容之一。
塑胶件成型是将各种形态(粉料、粒料、熔料和分散体)的塑料制成所需形状的制品或坯件的过程。
塑胶件成型是以注塑、挤塑和压延三大成型工艺为主,塑胶产品制造又以注塑成型工艺最为常见。
所谓注塑成型(injectionmolding)是指将已加热熔融的材料喷射注入模具内,经冷却与固化后,得到成型品德方法。
其具体过程是,将粒状或粉状塑料从注塑机的料斗送入加热的料筒中,经加热塑化成熔融状态,由螺杆施压而通过料筒端部的喷嘴注入低温的、闭合的模具型腔中经冷却硬化而保持模腔所赋予的形状,开模取出胶体后就完成了一个工作周期。
注塑成型是塑胶成型加工中普通采用的方法,它适用于全部热塑性塑料(热塑性塑料:在特定的温度范围内能反复加热熔融和冷却硬化的一类塑料,如ABS、PP、PE、PC、PA、POM)和部分热固性塑料,塑胶塑胶产品的大部分零部件都是通过注塑成型制造的。
注塑成型的成型周期短(几秒到几分钟),成型制品质量可由几克到几十千克,能一次成型外形复杂、尺寸精确、带有金属或非金属嵌件的模塑品。
因此,该方法适应性强,生产效率高。
注塑成型又称注射模塑成型,它是一种注射兼模塑的成型方法。
注塑成型方法的优点是生产速度快、效率高,操作可实现自动化,花色品种多,形状可以由简到繁,尺寸可以由大到小,而且制品尺寸精确,产品易更新换代,能成形状复杂的制件,注塑成型适用于大量生产与形状复杂产品等成型加工领域。
不利的一面是模具成本高,且清理困难,所以小批量制品就不宜采用此法成型。
塑胶制品的设计和制造流程优化

塑胶制品的设计和制造流程优化随着现代工业的快速发展和技术的不断进步,塑料制品已经成为我们生活中必不可少的一种原材料。
从小到大,我们几乎每天都会接触到各种形状、各种用途的塑料制品。
由于其成本低、成型难度小、制作速度快以及使用的方便性,许多公司在产品的制造中都大量采用了塑胶制品。
然而,即便是如此受欢迎的塑胶制品,其设计和制造流程却面临着一些问题。
在这篇文章中,我们将探讨如何优化塑胶制品的设计和制造流程。
一、塑胶制品的设计流程在塑胶制品的设计过程中,最重要的一步是将原型转化为模具,这样才能批量生产塑胶制品。
通常,塑胶模具制造是一项非常昂贵、技术难度大的工艺,需要专业的技术人员和生产线来完成。
由于塑料成型的特殊性质,不同形状、大小、厚度的塑物制品所需要的模架和模具也各不相同。
因此,一个完美的设计流程和高效的模具制造工艺是非常重要的。
1、使用CAD技术进行设计在当今的工业界,许多公司都改用计算机辅助设计软件(CAD)来制作设计图纸。
使用CAD后,我们就可以更轻松地创造和修改设计,降低制造成本和缩短制造时间。
CAD技术可以让人们在三维环境下设计模型,使得人们能够更好地理解产品设计,节约时间和成本,提高设计的准确性。
2、适当运用机械工程原理另外,在设计过程中,我们应运用机械原理,使塑胶制品的结构更加合理,提高其强度和使用寿命。
考虑到制品的使用环境和使用状态,设计师需要确保产品模型在正常使用状态下不会被损坏,同时要考虑到材料(如重量、厚度、钢性和韧性)的选择。
如果我们能在初始设计阶段中遵循这些原则,生产过程中将减少许多未知因素,为后续制造工作提供了可靠的保障。
二、塑胶制品的制造流程优化的制造流程将大幅提高企业的效率和效益。
在塑胶制品的制造过程中,主要包括以下几个环节:原料配料、热成型加工、后处理工具和品检。
1、使用符合质量标准的原材料塑料材料的质量对制造过程及制成的产品的质量有着至关重要的影响。
因此,选用符合相关质量标准要求的原材料是非常重要的。
塑胶制品设计原则

(3)便于模具加工和维修。如图3.2.6 图3.2.7所示,转轴位 模具上制作镶件。
2.3 行位、斜顶
胶件侧壁有凹凸形状、侧孔和扣位时,模具开模顶出胶件 前则须将侧向型芯抽出,此机构称行位。如图 3.2.8 所 示,胶件外侧孔,需后模行位抽芯。 如图 3.2.9 所示,胶件内侧凹槽,若用斜顶出模,顶部开 距不够,须采用内行位。
1 二板模(大水口模) 二板模是指那些能从分模面分开成前、后两半模的模具。
2 三板模(细水口模) 三板模主要由三个部分或模板组成,开模后,各模板之 间相隔一段距离,胶件从形成分模面的两块模板之空间 距离落下,浇道则从另一空间距离落下(这是对冷流道 模具来讲),这种把胶件与浇道分隔开的模具称三板模。 三板模如图4.1.7所示,其开模要求为: D为模具中最长入浇道值,A=D+E+(10~15mm),并且, A110mm(手横向取浇道
2.2 擦、碰面
模具擦、碰面如图3.2.2所示。模具的 擦面应有斜度,擦面斜度有两个功用:
(1)防止溢胶,因为竖直贴合面不能加
预载;
模具上碰面
(2)减少磨损。
模具上擦面
图3.2.2
分析擦、碰面可从如下几方面考虑; (1)保证结构强度。如图3.2.3为避免模具凸出部位变形或 折断,设计上B/H之值大于等于1/3较合理。
3.2 装配间隙
各胶件之间的装配间隙应均匀,一般胶件间隙(单边)如下: 固定件之间间隙图3.3.1止口间隙图3.3.2 (1)固定件之间配合间隙 0~0.1mm,如图3.3.1所示; (2)面、底壳止口间隙0.05~0.1mm,如图3.3.2所示;
(3)规则按钮(直径Ø15 )的活动间隙(单边)0.1~0.2mm;规 则按钮(直径Ø >15 ) 的活动间隙(单边)0.15~0.25mm;异形按钮的活动间隙 0.3~0.35mm,如图3.3.3所示。
第三章:塑胶件设计指南
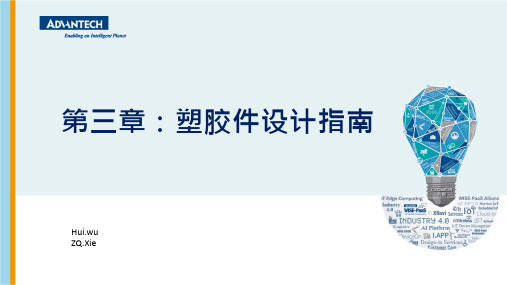
比重 1.25 1.39 1.58
比重 1.65 1.43 1.63 1.54
吸水率
标准:ASTM D570 ISO62
样品规格:1.圆片:直径50mm,厚度4mm
2.方片:60mm× 60mm× 1mm 3.条形:76.2mm× 25.4mm× 3.2mm
方法:
1. 把样品放到干燥箱干燥(条件50度/24小时), 移至干燥器中冷却 到室温,取出后测试每个样品的重量M1;
压缩模塑 压缩模塑又称模压,是模塑料在闭合模腔内借助加压的成型方法。通常,压缩模塑适用于热固性塑料,压缩模塑用的主 要设备是压机和塑模。压缩模塑的主要优点是可模压较大平面的制品和能大量生产。
溢出式
半溢出式
不溢出式
吹塑成型 借气体压力使闭合在模具中的热型坯吹胀成为中空制品,或管型坯无模吹胀成管膜的一种方法。该方法主要用于各种包 装容器和管式膜的制造。凡是熔流率为0.04 ~ 1.12的都是比较优良的中空吹塑材料,如聚乙烯、聚氯乙烯、聚丙烯、聚 苯乙烯、热塑性聚酯、聚碳酸酯、聚酰胺、醋酸纤维素和聚缩醛树脂等,其中以聚乙烯应用得最多。
常见塑料的比重
树脂 PA66 PA6 PC
PP PBT POM ABS PA46 LCP
比重 1.14 1.14 1.20
0.91 1.3 1.40 1.03 1.18 1.37
尼龙增强类 PA66+15%GF PA66+33%GF PA66+50%GF
卤素与无卤产品 FR285 NY NP216 BF509G6 NP516
注射成型(最常用) 注射成型(注塑)是使热塑性或热固性模塑料先在加热料筒中均匀塑化,而后由柱塞或移动螺杆推挤到闭合模具的模腔中 成型的一种方法。注射成型几乎适用于所有的热塑性塑料。近年来,注射成型也成功地用于成型某些热固性塑料。注射 成型的成型周期短(几秒到几分钟),成型制品质量可由几克到几十千克,能一次成型外形复杂、尺寸精确、带有金属或 非金属嵌件的模塑品。
塑胶零件设计常识!
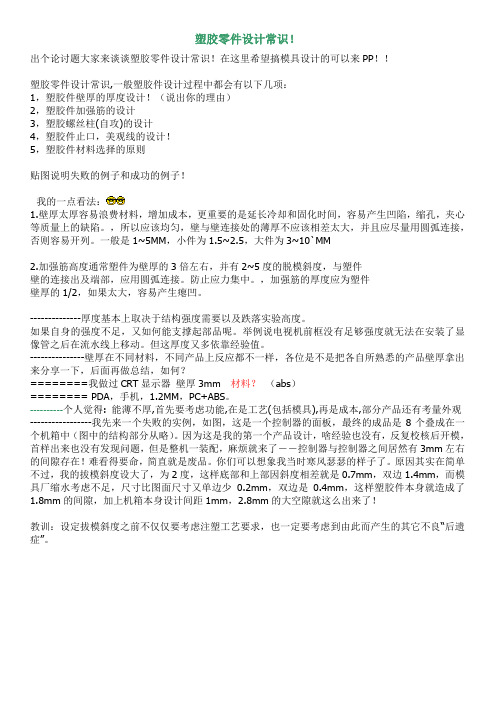
塑胶零件设计常识!出个论讨题大家来谈谈塑胶零件设计常识!在这里希望搞模具设计的可以来PP!!塑胶零件设计常识,一般塑胶件设计过程中都会有以下几项:1,塑胶件壁厚的厚度设计!(说出你的理由)2,塑胶件加强筋的设计3,塑胶螺丝柱(自攻)的设计4,塑胶件止口,美观线的设计!5,塑胶件材料选择的原则贴图说明失败的例子和成功的例子!我的一点看法:1.壁厚太厚容易浪费材料,增加成本,更重要的是延长冷却和固化时间,容易产生凹陷,缩孔,夹心等质量上的缺陷。
,所以应该均匀,壁与壁连接处的薄厚不应该相差太大,并且应尽量用圆弧连接,否则容易开列。
一般是1~5MM,小件为1.5~2.5,大件为3~10`MM2.加强筋高度通常塑件为壁厚的3倍左右,并有2~5度的脱模斜度,与塑件壁的连接出及端部,应用圆弧连接。
防止应力集中。
,加强筋的厚度应为塑件壁厚的1/2,如果太大,容易产生瘪凹。
--------------厚度基本上取决于结构强度需要以及跌落实验高度。
如果自身的强度不足,又如何能支撑起部品呢。
举例说电视机前框没有足够强度就无法在安装了显像管之后在流水线上移动。
但这厚度又多依靠经验值。
---------------壁厚在不同材料,不同产品上反应都不一样,各位是不是把各自所熟悉的产品壁厚拿出来分享一下,后面再做总结,如何?========我做过CRT显示器壁厚3mm 材料?(abs)======== PDA,手机,1.2MM,PC+ABS。
----------个人觉得: 能薄不厚,首先要考虑功能,在是工艺(包括模具),再是成本,部分产品还有考量外观-----------------我先来一个失败的实例,如图,这是一个控制器的面板,最终的成品是8个叠成在一个机箱中(图中的结构部分从略)。
因为这是我的第一个产品设计,啥经验也没有,反复校核后开模,首样出来也没有发现问题,但是整机一装配,麻烦就来了--控制器与控制器之间居然有3mm左右的间隙存在!难看得要命,简直就是废品。
面向制造和装配的产品设计-第二部分-塑胶件的设计
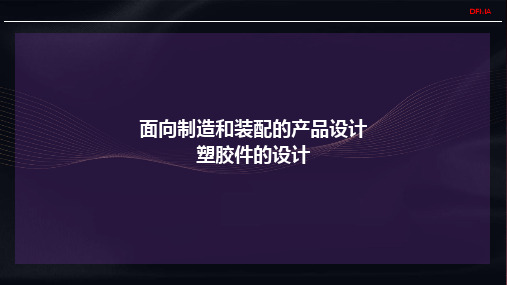
圆角的设计 零件应力集中系数
五、塑胶件设计--脱模斜度
决定脱模斜度的因素:脱模斜度一般取1~2°;收缩率较大的塑胶件脱模斜度较大;尺寸精度要求较高的特征处取较小脱模斜度:公模侧脱模斜度小于母模侧以利于脱模;壁厚较厚时,成型收缩大,取较大脱模斜度;咬花面与复杂面取较大脱模斜度;玻纤增强塑料取较大脱模斜度;零件某些平面因为功能需要可以不设置脱模斜度,但模具则需设计侧抽芯结构,模具结构复杂,成本高:在零件功能和外观等允许情况下,零件脱模斜度尽可能取大;脱模斜度的大小与方向不能影响零件的功能实现。脱模斜度的大小和方向不能影响零件的功能实现:
在允许的情况下,可以通过U形槽、零件表面断差的设计以及表面咬花等方式来掩盖塑胶件表面缩水
支柱壁厚处或加强筋壁厚处局部去除材料(我国台湾地区称之为“火山口”),可以大幅降低零件外观缩水的可能性,“火山口”设计会在一定程度上降低支柱或加强筋的强度。
离浇口越远处,越容易产生表面缩水。对于零件重要外观表面对表面缩水要求高的区域,可以合理设计浇口的位置使其靠近该区域,减小缩水。同时,浇口的位置应使得塑胶熔料从壁厚处流向壁薄处。若熔料从壁薄处流向壁厚处,壁薄处首先冷却凝固,壁厚处表面很容易产生缩水,内部则容易产生气泡。
面向制造和装配的产品设计塑胶件的设计
目录
一、定义与特性二、分类三、材料四、塑胶件设计零件壁厚避免尖角脱模斜度加强筋的设计支柱的设计孔的设计提高塑胶件强度的设计提高塑胶件外观的设计降低塑胶件成本低设计注塑模具可行性设计塑胶件的装配卡扣装配卡扣的设计机械固定,自攻螺钉超声波焊接塑胶件DFMA检查表
五、塑胶件设计--定义与特性
五、塑胶件设计--提高塑胶件强度的设计
精密塑胶件注塑模具顶出结构及加工成型工艺研发

精密塑胶件注塑模具顶出结构及加工成型工艺研发一、导言随着工业技术的发展,精密塑胶件在各个行业中得到了广泛的应用。
注塑模具是生产精密塑胶件的重要成型工具,包括模具结构设计、加工成型工艺研发等方面,都对精密塑胶件的质量和生产效率有着重要的影响。
本文将重点探讨精密塑胶件注塑模具顶出结构及加工成型工艺的研发。
二、模具顶出结构设计模具的顶出结构是指在注塑过程中,塑料熔料在充模过程中,通过顶出装置使塑料零件从模具中弹出的一种结构。
对于精密塑胶件的顶出结构设计,应综合考虑以下几个方面的因素:1.模具材料的选择。
模具材料的选择应根据精密塑胶件的材料性质和生产工艺要求进行选择,一般常用的模具材料有P20、45#、718等。
同时,模具材料的硬度和耐磨性也是影响顶出结构设计的重要因素。
2.顶出方式的选择。
常见的顶出方式有机械顶出、气动顶出和液压顶出等。
对于精密塑胶件而言,要考虑到产品的表面光洁度和尺寸精度等因素,通常采用气动顶出或液压顶出方式较为合适。
3.顶出装置的设计。
顶出装置通常包括顶出销和顶出板两部分。
其中,顶出销的材料应与模具材料相匹配,以保证顶出销的刚性和耐磨性,同时辅助顶出板的设计要合理,以保证塑料零件能够完整且顺利地脱模。
1.模具加工工艺研发。
模具加工工艺主要包括模具加工序列的确定、工艺参数的选择和加工精度控制等。
通过合理的模具加工工艺研发,可以提高模具的加工效率和加工精度。
2.塑料熔融流道设计。
塑料熔融流道设计的好坏直接影响着塑胶件的质量和生产效率。
对于精密塑胶件而言,流道应尽可能短而粗,以保证塑料熔料的快速流动和顺畅充模。
3.注塑工艺参数的优化。
注塑工艺参数的优化包括注射速度、保压时间、保压压力和注射温度等方面的考虑。
通过调整这些参数,可以获得更好的塑胶件成型品质和缩短生产周期。
4.模具温度控制。
模具温度对于塑胶件的收缩率和表面光洁度有着重要的影响。
通过合理的模具温度控制,可以避免塑胶件的变形和表面瑕疵。
常用塑胶注塑加工工艺

常用塑胶注塑加工工艺一、PS(聚苯乙烯)1 .PS的性能:PS为无定形聚合物,流动性好,吸水率低(小于00.2%),是一种易于成型加工的透明塑料。
其制品透光率达88-92%,着色力强,硬度高。
但PS制品脆性大,易产生内应力开裂,耐热性较差(60-80℃),无毒,比重1.04g\cm3左右(稍大于水)。
成型收缩率(其值一般为0.004—0.007in/in),透明PS--这个名称仅表示树脂的透明度,而不是结晶度。
(化学和物理特性:大多数商业用的PS都是透明的、非晶体材料。
PS具有非常好的几何稳定性、热稳定性、光学透过特性、电绝缘特性以及很微小的吸湿倾向。
它能够抵抗水、稀释的无机酸,但能够被强氧化酸如浓硫酸所腐蚀,并且能够在一些有机溶剂中膨胀变形。
)2 .PS的工艺特点:PS熔点为166℃,加工温度一般在185-215℃为宜,熔化温度180~280℃,对于阻燃型材料其上限为250℃,分解温度约为290℃,故其加工温度范围较宽。
模具温度40~50℃,注射压力:200~600bar,注射速度建议使用快速的注射速度,流道和浇口可以使用所有常规类型的浇口。
PS料在加工前,除非储存不当,通常不需要干燥处理。
如果需要干燥,建议干燥条件为80C、2~3小时。
因PS比热低,其制作一些模具散热即能很快冷凝固化,其冷却速度比一般原料要快,开模时间可早一些。
其塑化时间和冷却时间都较短,成型周期时间会减少一些;PS制品的光泽随模温增加而越好。
3.典型应用范围:包装制品(容器、罩盖、瓶类)、一次性医药用品、玩具、杯、刀具、磁带轴、防风窗以及许多发泡制品——鸡蛋箱。
肉类和家禽包装盘、瓶子标签以及发泡PS缓冲材料,产品包装,家庭用品(餐具、托盘等),电气(透明容器、光源散射器、绝缘薄膜等)。
二、HIPS(改性聚苯乙烯)1. HIPS的性能:HIPS为PS的改性材料,分子中含有5-15%橡胶成份,其韧性比PS提高了四倍左右,冲击强度大大提高(高抗冲击聚苯乙烯),已有阻燃级、抗应力开裂级、高光泽度级、极高冲击强度级、玻璃纤维增强级以及低残留挥发分级等。
塑胶件设计规范

塑胶件设计规范:(限于目前常用的热塑性塑料件设计)1.壁厚设计根据零件功能及形状大小而定。
注塑成型壁厚一般不大于4mm。
常用材料壁厚如下,特殊要求的壁厚另行考虑。
热塑性塑料名称厚度范围典型厚度备注ABS 1.5~4.5 2.5 拐角内圆角最小半径25%壁厚PC 0.75~9.5 2.4 一般设计壁厚不超过3.1mmPP 0.6~7.6 2.0 一般设计壁厚不超过2.5mmPS 0.8~6.4 2.2 50%壁厚PA 0.4~3.2 1.6 0.5mmPOM 0.4~3.2 1.6PMMA 0.6~6.4 2.4PPO 0.8~9.5 2.0SAN 0.8~6.4 1.6PU 0.6~38 12.7LDPE 0.5~6.4 1.6HDPE 0.9~6.4 1.6LCP 0.4~1.5 1.5平面准则:尽量壁厚均匀一致。
因故不能做到,需做渐变过度,过度的部分长高比例大于等于3:1转角准则:壁厚均匀原则在拐角处同样适用。
2.BOSS柱设计:(常用塑料)设计原则,首先考虑连接强度。
下表是对于一般结构件连接情况;对于重要外观件,BOSS 柱外径,在连接强度不高情况下,可以适当做小。
当连接有强度要求,又有外观要求时,需按下面参数设计,同时设计出火山口。
BOSS柱要求使用司筒顶出,斜度不大于0.25度。
说明:PC柱比ABS更容易打爆,若出现此现象,外径可适当加大材料螺钉内孔直径外径连接有效深度PP ST2.2 1.8±0.05 4 4.5ST 2.6 2.1±0.05 4.8 5ST2.9 2.3±0.05 5.5 6ST 3.3 2.6±0.05 6.0 6.5ST 3.5 2.8±0.05 6.5 7ST 3.9 3.2±0.05 7.2 8ST 4.2 3.4±0.05 7.8 8.5ST 4.8 3.8±0.05 9 9.5ST 5.5 4.4±0.05 10 11ST 6.3 5.1±0.05 11.5 12.5ST 8 6.4±0.05 14.8 16材料螺钉内孔直径外径连接有效深度PA6,PA66,SAN /POM ST2.2 1.8±0.05 4 4.5ST 2.6 2.2±0.05 4.8 5ST2.9 2.4±0.05 5.5 6ST 3.3 2.8±0.05 6.0 6.5ST 3.5 3±0.05 6.5 7ST 3.9 3.3±0.05 7.2 8ST 4.2 3.5±0.05 7.8 8.5ST 4.8 4±0.05 9 9.5ST 5.5 4.6±0.05 10 11 ST 6.3 5.3±0.05 11.5 12.5ST 8 6.8±0.05 14.8 16火山口设计:壁厚<2mm,A尺寸做0.75mm2mm≤壁厚,A尺寸做60~70%壁厚3.加强筋设计3.1加强筋厚度一般设计,加强筋厚度不超过壁厚0.6倍。
塑胶结构设计规范

3-24W,USB输出: 直伸式(分模线在R角处)结构,方形R角 外形(推荐选用)
3-24W ,DC线输出: 直伸式(分模线在R角处)结构,方形R角外 形(推荐选用)
电源胶壳常规结构设计11
3.14 立式(弹片结构)胶壳PCB固定结构设计:
X(PCB 高度)
A
面壳
PCB B
01(此筋条通常2根即可,应 根据胶壳实际大小增加数量)
面壳
02
M(胶壳分型面 到底部筋条) G1(装配间隙)
PCB
B
元件面筋条
4.0-6.0 10.0MAX
引脚面筋条
A
0.15(单边间隙)
Detail 02 立式胶壳面壳&底 Scale 3:1 壳PCB卡槽尺寸
4.0-6.0
电源胶壳常规结构设计15 常规A型USB插头与胶壳(超声波封焊)配合结构尺寸设计:单位:mm
电源胶壳常规结构设计16
电源胶壳常规结构设计17 常规AC座与胶壳配合尺寸设计:
电源胶壳常规结构设计18 3.22 车充设计标准: 3.22.1 外形尺寸设计标准(除特殊要求外,常规车充外形尺寸标准参考如下图):
3.1.7 产品装配结构设计: 按功率定义两种结构
1) 24W以下功率(含):采用弹片和引线两种标准结构(主推弹片结构)
3.1.7 产品装配结构设计:
2) 30-90W功率:采用引线标准结构。因PCB LAYOUT尺寸长宽比例问题,此功 率段产品外观定义为正方型结构;
3.1.8 产品外观定义
- 1、下载文档前请自行甄别文档内容的完整性,平台不提供额外的编辑、内容补充、找答案等附加服务。
- 2、"仅部分预览"的文档,不可在线预览部分如存在完整性等问题,可反馈申请退款(可完整预览的文档不适用该条件!)。
- 3、如文档侵犯您的权益,请联系客服反馈,我们会尽快为您处理(人工客服工作时间:9:00-18:30)。
塑胶(料)件设计与注塑
简介:该课程根据产品设计的实际情况对塑料件的相关知识进行系统的整理。
从塑料的高分子结构入手,对塑料原材料性能,塑料件的通用设计,结构设计,装配设计,注塑工艺及模具设计的内容进行全面的讲解。
从根本上解决工程师,技术主管,采购,品质等需要了解塑料件知识的人员,不知如何系统学习的问题。
将机械设计的思想及多年的设计经验也揉和在该课程中。
...
广州开课;课程时长:2天;详细会务信息请登陆森涛培训网查看
适合对象:
技术总监、项目经理,结构工程师、机械工程师、质量工程师,工艺和制造工程师,模具设计工程师,注塑工程师,直接负责塑料件的采购人员及想对塑料件做全面了解的人员。
课程介绍
----材料、设计、装配、注塑、模具全面系统的培训
二天课程:
该课程根据产品设计的实际情况对塑料件的相关知识进行系统的整理。
从塑料的高分子结构入手,对塑料原材料性能,塑料件的通用设计,结构设计,装配设计,注塑工艺及模具设计的内容进行全面的讲解。
从根本上解决工程师,技术主管,采购,品质等需要了解塑料件知识的人员,不知如何系统学习的问题。
将机械设计的思想及多年的设计经验也揉和在该课程中。
培训特色:
根据客户提供及经典案例,介绍塑胶件的相关具体内容和要求,以及在设计,生产中的实际应用,并提供现场的辅导,包括结构设计、传动设计及综合分析等。
课程内容:
第一篇认识塑料Understanding Plastic (3 hours)
一、塑料是什么 * what's plastic
二、塑料的分类* the classification of plastic
三、塑料的机械特性* mechanical properties
四、塑料的热特性* thermal properties
五、塑料的电气特性 * electric properties
六、塑料的环境特性* environment properties
七、塑料的模塑特性* molding properties
八、常用塑料介绍 * introduction of some common plastic
第二篇塑料件通用设计 Plastic Parts General Design (3 hours)
一、壁厚的设计 * wall thickness design
二、筋的设计* ribs design
三、凸台、螺丝柱的设计* bosses design
四、角板的设计* gussets design
五、尖角的设计* sharp corner design
六、拔模设计* draft design
七、孔洞的设计* holes and cores
八、倒扣的设计 * undercut
九、模塑螺纹的设计 Molded-in thread
十、模塑文字*lettering
十一、活动铰链设计* living hinge design
十二、塑料轴承设计*plastic bearing design
十三、塑料件公差的设计 Tolerance design
十四、塑胶件的装配 Assembly design
第三篇塑料件结构件设计Plastic Parts Structure Design (3 hours)
一、结构设计考虑的因素 * structure consideration in plastics
二、短期的机械性能* short-term mechanical properties
三、长期的机械性能* long-term mechanical properties
四、结构设计公式* structure design formulas
五、刚度的设计* designing for stiffness
六、长期负载的设计 * designing for long-term loading
七、冲击负载的设计 * designing for impact
八、热负载的设计 * thermal loading
第四篇塑料件注塑工艺过程Plastic Parts Molding process (3 hours)
一、浇口的考虑 * gating consideration
二、流动取向的影响* mold filling orientation
三、充模的压力损失* mold filling pressure losses
四、导流、限流、滞流* flow leader, flow restrictors, flow hesitation
五、熔接线* welding lines
六、改善熔接线的性能与外观* improving welding lines
七、收缩与扭曲变形* shrinkage and warpage of molding parts
八、顶出 * part ejection
第五篇塑料件装配的设计 Plastic Parts Assembly design (3 hours)
一、压入装配 * press fit assemblies
二、卡扣设计 * snap joint assemblies
三、紧固件的装配* mechanical fasteners
四、镶件装配* insert assemblies
五、焊接装配* welding assemblies
六、粘接装配* adhesive bonding assemblies
第六篇塑料模具知识 Plastic Parts Mold basic (3 hours)
一、模具的类型* mold classification
二、模具的结构* mold structure
三、模具的生产动作过程 mold movements in production
二、倒扣的模具处理* molding undercut
三、零件的顶出* part ejection
四、模具的排气* mold venting
五、唧嘴、流道、浇口* sprues, runner, and gates
六、模具的冷却* mold cooling
七、滑块的知识* mold sliders
老师介绍:
李老师
华南理工大学机械设计及理论硕士;
首席GD&T形位公差与尺寸链培训师;
首席产品结构设计培训师;
机械制造及其自动化专业高级工程师
多家国内外知名企业顾问;
培训机构研发技术类课程指定老师;
【背景经历】
在欧美仪器、设备行业及国内家电,电子行业,从事研发、制造工作13年。
多年的高级工程师,研发经理职业经历。
具有丰富的机械结构与机械传动设计经验,并在海外研发工作多年,熟悉行内的最新动向及技术更新,了解大量的国外产品设计案例。
在培训方面,有丰富的授课经验:多家培训公司定期公开课的指定讲师,获得学员和机构的一致好评;多家大型企业内训指定讲师,定期到企业内部开展培训和辅导,好评96%以上。
可根据客户特定需求来调整课纲,编撰课件。
授课内容更贴近客户需求,更好服务客户。
可就现场问题做分析与咨询,辅导客户,完成项目。
【培训特色】
擅长结合客户的产品和案例讲解,激发学员兴趣,达到真正掌握并灵活运用。
培训以讲解和实际产品练习相结合的方式,注重与学员之间的互动。
通过大量欧美机械设计产品优秀案例、生动的语言,将专业知识讲解得让学员想听、易懂,有收获。
工作语言为英语和汉语普通话。
【主讲课程】
《塑胶(料)件的设计与注塑》 2 - 3 天;
《塑胶产品设计》1-2天;
《GD&T形位公差与尺寸链计算》 1 - 2天;
《机械图纸的尺寸公差的合理标注》1-2天
《产品结构设计》2-3天;
《金属材料》2天;
温馨提示: 本课程可引进到企业内部培训,欢迎预约!
资料来源: 森涛培训网。