_1300立式磨底座的铸造工艺改进_米国发
移动轮座铸造工艺改进

部件 , 生产批量 大 , 件 结构 复杂 , 铸 质量 104k , 2 g材 质 为 Z 30 50 技 术 要 G 1 —7 . 求 表 面 光 洁 无 粘砂 、 夹 渣 、 孔 、 孔 和 裂 纹 等 缩 气 铸造 缺 陷 。 零件 结构 形状 如图 1 所示 。 件未 注尺 铸
Ab t c :h s atce r s l e h r b e ffr rp o e s t r u h i rv n r c s , u ig c r mi r n oe s a t i r l e ov s te p o l ms o me r c s h g mp o i g p e s r T i o o o sn h o c i r , o
1 由于整体模 型都在下箱 , ) 这样下箱较高 , 起
模 较 困难 , 起模 吸力 大 , 型粘砂 严重 , 模 不好修 型 。
2芯子多 , ) 操作麻烦 , 铸件精度低。 3 由于 芯 子 较 大 , 型 时 必 须 用 15 0 m ) 造 0 m ̄
150mm砂 箱 , 砂量 较大 , 0 用 生产效 率较低 。
2 1年第 5 00 期
2 1年 1 月 00 O
・
铸 造
设
备
与 工
艺
O t 0 0 N5 c2 1 o .
F U D Y E U P N N E H O O Y O N R Q IME TA D T C N L G
铸 造工 艺 ・
移动轮座铸造 工艺改进
刘 波 方 素娥 , 200 ; 5 11 (. 集 团重工机 械有 限公 司生产部 , 1济钢 山东 济 南
案, 解决 了原工艺存在的问题 。
关键 词 : 动轮 座 ; 真模 拟 ; 艺改 进 移 仿 工
低压铸造升液管的研究与应用_米国发
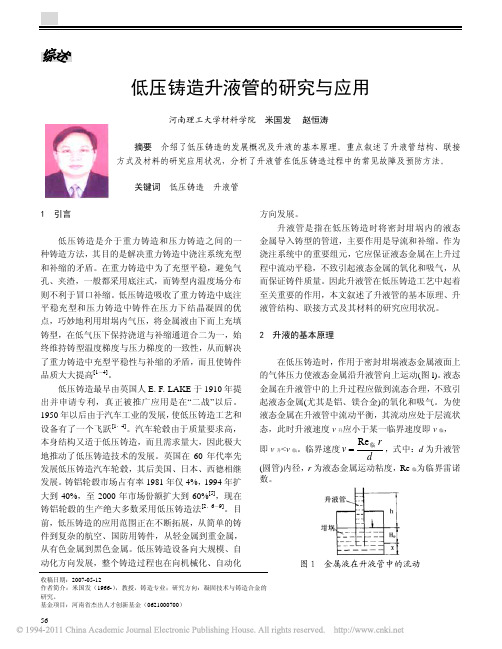
钛酸铝陶瓷不仅具有较高的熔点(1860℃)、较低
的热膨胀系数( α ≤ 2.0×10-6/℃)和优良的抗热震性 (ΔTc ≥ 1200℃)[21~23],且具有与铝等许多有色金属熔
体不润湿的特性,因此是制备铸铝用升液管的优良材 料。目前国内对钛酸铝陶瓷升液管进行了广泛的研 究:浙江大学的徐刚等利用 XRD 对试验采用不同稳 定剂制备的钛酸铝陶瓷在 85O℃铝熔体中的稳定性进 行了研究;发现稳定剂 MgO+Y2O3 的固溶可有效抑制 钛酸铝的分解,利用钛酸铝所制备的陶瓷升液管可连 续运行 60d 不破坏[23];还对材料的抗热震性能进行了 研究,经过 12 个周期的进入和热震,强度变化很小, 抗热震性能优良,可以适应铝合金低压铸造的间歇应 用[24]。湖南陶瓷研究所的李忠权等采用一步法进行钛 酸铝陶瓷升液管的研究,讨论了添加剂和烧成温度对
合理的升液管不仅可以满足快速平稳充型的要求,也
可满足合金液传热、除气、滤渣等要求[12,13]。
3.1 升液管的设计原则
a. 为避免对坩埚的严重冲刷和将杂质吸入铸型,
对不同合金应分开使用,升液管下口距坩埚底部距离
应有 50~100mm;
b. 考虑清理和喷涂料的方便,最小内径不应小于
35mm;
c. 为保证升液平稳、并实现顺序补缩,要求升液
HRM3700立式生料磨的改进
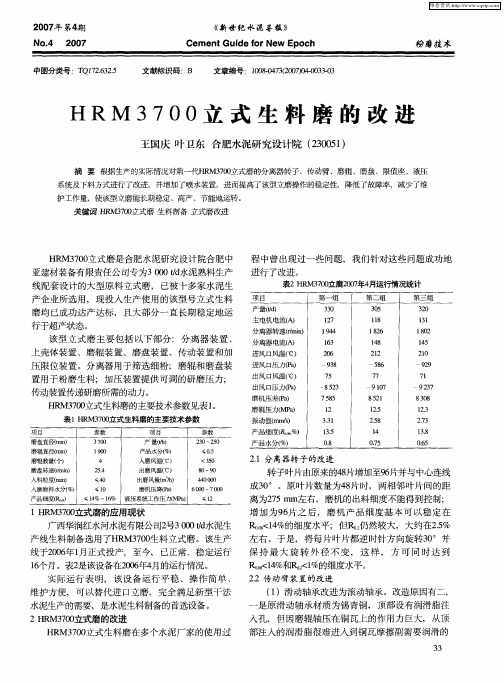
1 0 2 8 15 4
20 1 —99 2 7 1 9 3 7 2
该 型 立 式磨 主 要 包括 以下 部 分 :分 离 器 装 置 、
上壳体装置、磨辊装置、磨盘装置 、传动装置和加 压 限位装 置 。分离 器用于 筛选 细粉 ;磨 辊和 磨盘 装 置用 于粉磨 生料 ;加 压装 置提供 可调 的研 磨压 力 ; 传动装置传递研磨所需的动力 。 Ⅷ 30立式生料磨 的主要 技术参数见表 1 7O 。
HR 70 M30 立式磨 是合 肥水泥 研究设 计 院合肥 中 亚建材装备有限责任公司专为3 0 水泥熟料生产 0t 0 / d 线配套设计的大型原料立式磨,已被十多家水泥生 产 企业 所选 用, 现投入 生产 使用 的该 型号 立式 生料
磨 均 已成 功达 产达 标 ,且大 部分 一直 长期 稳定地 运 行于超产状态 。
7 8 5 5 1 2 31 . 3 1. 35 O8 .
8 2 1 5 1. 25 25 .8 1 4 05 . 7
8 0 8 3 1- 23 23 . 7 1. 3 8 O5 . 6
磨辊数量( 爪J
磨盘转速( i r n / ) a r 入料粒度( m m ) 入磨物料水
左右。于是,将每片叶片都逆时针方向旋转3 。并 0
保 持 最 大 旋 转 外 径 不 变 , 这 样 , 方 可 同 时 达 到
Ro 1%和R。1 。 4 < o %的细度水平 。 <
.
2 传 动 臂 装 置 的 改进 . 2
( )滑动轴 承改进 为滚动轴 承 。改造 原 因有二 , 1
是原滑动轴承材质为锡青铜,顶部设有润滑脂注 入 孔 ,但 因磨辊 轴压 在铜 瓦上 的作 的润 滑脂 很难进 入到铜 瓦摩擦 副需 要润滑 的
后从板座铸造工艺的改进

后从板座铸造工艺的改进
李新茹
【期刊名称】《铁道机车车辆工人》
【年(卷),期】1997(000)009
【总页数】2页(P11-12)
【作者】李新茹
【作者单位】济南机车车辆厂
【正文语种】中文
【中图分类】U272.06
【相关文献】
1.罐车一体式后从板座及上心盘座铸造缺陷的分析及改进措施 [J], 孙建伟
2.QT400—15指形板座的消失模与砂型的铸造工艺及效果对比 [J], 先克;袁芳蓉
3.接点座的覆膜砂壳型铸造工艺改进 [J], 王文生
4.圆弧“U”形结构安装座铸造工艺改进 [J], 俞树吉; 朱学梅; 王峰; 任国波; 李春
5.QT600-3后板簧座的垂直线铸造工艺改进 [J], 杜可珍;周应好
因版权原因,仅展示原文概要,查看原文内容请购买。
M1350磨床大修方案

M1350磨床大修方案.docxM1350磨床大修方案及报价一、大修方案机床整体运回我公司,拆卸、分解、检测、清洗各零部件一工作台床身导轨副局部1、对床身和工作台导轨面精刨加工处理。
确保各导轨面的直线度和平行度。
然后采取合研工艺方法,以工作台下导轨面、床身两端导轨面三面合研,间距200mm递进,确保工作台下导轨面死点接触60%以上,具备工作台导轨初基准要求。
2、以工作台下导轨面为基准对床身导轨进行整体合研,两面铲刮,去除床身凸点和工作台虚点同时保证工作台实点接触达80%以上,这时以工作台为基准全程拖研,修刮床身导轨面,保证导轨面的直线度、平行度、外表精度以及纵横向导轨面的垂直度。
确保以下精度至要求:13/全长082/全长接合点685mm23、以床身导轨为基准,采用平板拖研配刮研工作台下体导轨面,保证配合精度,以及与上下结合面的平行度。
4、用专用检具刮研工作台上体上部导轨,保证导轨的直线度以及与下体下部导轨的平行度。
二磨头进给导轨副1、修刮磨头底座安装面至接合点355mm2,有效提高接触刚性,降低振动影响。
2、以床身导轨为基准,配刮研磨头进给滑座导轨面,保证接触精度以及磨头主轴中心线与床身纵向导轨的平行度。
3、配研磨头进给导轨滑动面,确保以下精度至要求:直线度1mm/全长床身垂直2mm/全长接合点8105mm2三头架、尾座移动导轨副1、制作专用桥板,配刮工作台上导轨面,确保和下导轨面平行度。
2、配研尾座调整面,确保移动面接合点8105mm2,相对尾座移动导轨轴向平行度1/300mm。
3、采用镶补工艺,修刮头架和尾座移动面,确保头尾架中心等高以及轴线平行度等技术标准至精度要求4、配刮各夹紧压板紧固面60%接触。
四磨头总成局部:拆解磨头,检查各部件,如果主轴、轴瓦损坏,由用户确认后,对砂轮主轴进行数控磨床精磨处理至要求,刮研轴瓦保证与主轴的接触精度和主轴间隙。
调整轴瓦位置,保证主轴中心线与轴承孔的同轴度以及前后轴瓦的同轴度。
HRM1300M立式煤磨安装说明
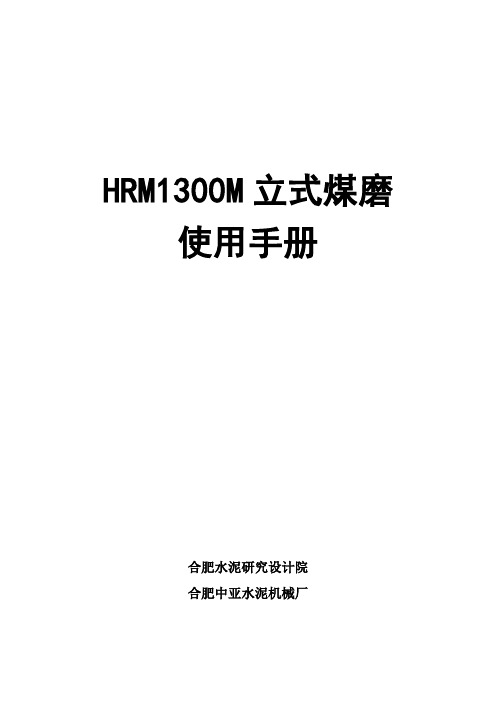
HRM1300M立式煤磨使用手册合肥水泥研究设计院合肥中亚水泥机械厂目录第一部分 HRM1300M立式磨安装一、前言二、技术参数及性能三、结构及工作原理四、设备安装五、液压及润滑系统的酸洗安装第二部分 HRM1300M立式磨调试及使用一、前言二、磨机分部件试运行三、立式磨整机空负荷试运行四、立式磨带负荷试运行五、人员培训六、磨机操作七、可能出现的问题及解决办法第三部分 HRM1300M立式磨维护及检修一、前言二、磨机的维护保养及检修三、润滑表四、易损件表第四部分图纸一、 HRM1300M立式磨总图二、 HRM1300M立式磨基础图三、 HRM1300M立式磨下壳体磨盘安装图四、 HRM1300M立式磨减速机电机安装图五、 HRM1300M立式磨磨加压、检修油缸安装图六、 HRM1300M立式磨分离器检修图七、 HRM1300M立式磨磨辊装置检修图八、 HRM1300M立式磨液压系统原理图第一部分HRM1300M立式磨安装一、前言HRM1300M立式磨是合肥水泥研究设计院下属合肥中亚水泥机械厂荣誉产品。
该型立式磨经多年生产实践考验,产品性能不断提高,逐步跨入国际同类产品先进行列,深得广大国内外用户青睐。
HRM1300M立式磨是一种技术性能优异的烘干兼粉磨设备,主要用于煤的粉磨,可广泛应用于建材、轻工、化工、火力发电等行业。
该型立式磨具有粉磨效率高、电耗低、入料粒度大、产品细度易于调节、设备工艺流程简单、占地面积小、噪音低、扬尘小、使用维护简单、运行费用低、耐磨材料消耗少等优点。
除此之外,该型立式磨还具有如下独特性能:1、磨辊可用液压装置翻出机外,更换辊套衬板及磨机检修空间大,检修作业十分方便。
2、磨辊辊套能翻面使用,延长了耐磨材料的使用寿命。
3、开机前无需在磨盘上布料,并且磨机可空载启动,免除开机难的烦恼。
4、采用磨辊限位装置,避免磨机工作时间因断料而产生的剧烈震动。
5、采用新型磨辊密封装置,密封更加可靠,并且无需密封风机,进一步降低磨内氧含量,抑爆性能更加优异。
立式磨床全长控制改造
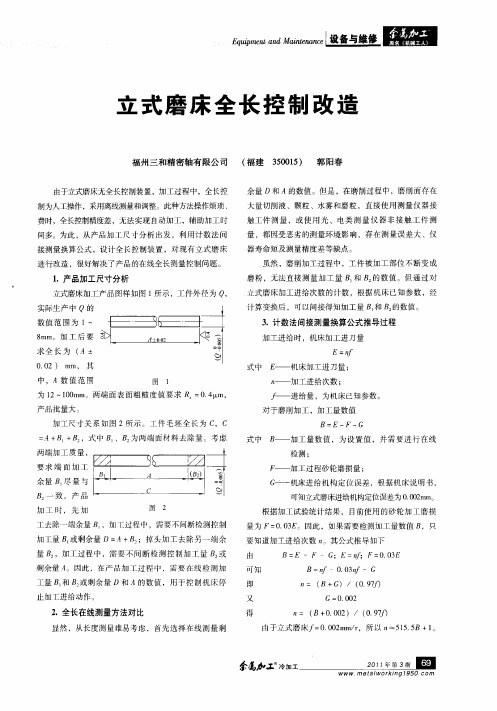
定加工量 曰的具体数值 B和 B ;然后, 。 分别将 B 和 口
代入公式换算出加工进给次数 r的具体数值 n和 / ;最 t 7 , , 后 ,使用 n和 n的具体数值去控制机床停止加工进给。
例如 :某产 品毛坯全 长 C= 04 m,要求加工后全 5.m 长 A=5 r 0 m。按产品加工尺寸分析可知加工量 a
数 范 为1 乇 三 值 围 ~ 三
8 m。加 工 后 要 m
。
三二口 三三
2 ,
3 计数法间接测量换算公式推导过程 .
加工进给时 ,机床加工进刀量
E=n 厂
f
l
求全长为 ( ± I 4
00 .2) m m, 其 中 ,A数 值 范 围 图 1
式中 E —— 机床加 工进 刀量 ;
B】 =B 2:0 2 m .r a
的接线端⑥ 和⑧
为计数器计数 溢 出时 ,输 出控制
将加工 量数值 B 、B 代 人公式 ,求得 。
H = 2 1. B+1= 0 . ( ) l n —55 5 14 1 次
取 n= 0 15次,即加工量 B的数 值取 02 m 时,只 .m 要控制机床加工进给 15次。 0 计数法间接测量原理误差包括计数误差和换算公 式
脚 眦 口
m
l量 丝 塑量堡
立 式 磨 床 全 长 控 制 改 造
福州三和精密轴有 限公 司 ( 福建 30 1 ) 郭 阳春 5 0 5
由于立式磨床无全长控制装置,加工过程 中,全长控 制为人工操作 ,采用离线测量和调整。此种方法操作烦琐 、
费时,全长控制精度差 ,无法实现 自动加工 ,辅助加工时 间多。为此 ,从产品加工 尺寸分析 出发 ,利用计 数法 间 接测量换算公式 ,设计全长控 制装 置 ,对现有立 式磨床 进行改造 ,很好解决 了产 品的在线全长测量控制问题。
一种新型下抽芯浇铸活塞用模具[实用新型专利]
![一种新型下抽芯浇铸活塞用模具[实用新型专利]](https://img.taocdn.com/s3/m/6f9c70f8cc7931b764ce15cb.png)
专利名称:一种新型下抽芯浇铸活塞用模具专利类型:实用新型专利
发明人:谢成明,米国发,李世清
申请号:CN201520777485.5
申请日:20151009
公开号:CN205096490U
公开日:
20160323
专利内容由知识产权出版社提供
摘要:本实用新型公开了一种新型下抽芯浇铸活塞用模具,包括顶模、外模、定位套、内模及侧冒口,所述顶模一端镶嵌在外模上部,另外一端高于外模上平面,所述侧冒口竖直连接外模的侧面,所述定位套一端镶嵌在外模底平面内部,另外一端高于底平面,所述内模套装在定位套内部并且端面高于定位套端面。
通过上述方式,本实用新型一种新型下抽芯浇铸活塞用模具,将原有手工生产方式更改为半自动机械化生产,采用半自动浇铸机生产头部铸造燃烧室活塞,工艺过程由时间继电器控制,工作循环稳定、可控,能有效保证产品铸造质量,提高燃烧室活塞铸造的生产效率,降低了铸造材料的浪费,减小了产品后道加工量,提高了产品的经济价值。
申请人:江苏兄弟活塞有限公司
地址:223600 江苏省宿迁市沭阳县台州北路105号
国籍:CN
代理机构:苏州广正知识产权代理有限公司
代理人:孙德荣
更多信息请下载全文后查看。
铸钢车轮铸造工艺模拟与优化_米国发
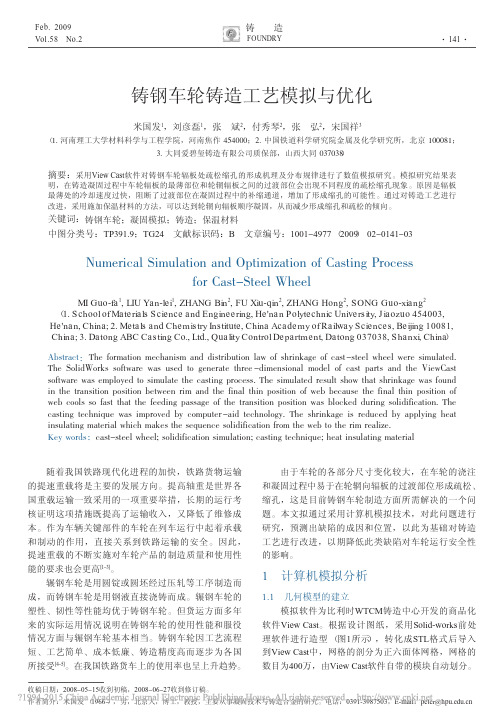
摘要:采用View Cast软件对铸钢车轮辐板处疏松缩孔的形成机理及分布规律进行了数值模拟研究。模拟研究结果表
明,在铸造凝固过程中车轮辐板的最薄部位和轮辋辐板之间的过渡部位会出现不同程度的疏松缩孔现象。原因是辐板 最薄处的冷却速度过快,阻断了过渡部位在凝固过程中的补缩通道,增加了形成缩孔的可能性。通过对铸造工艺进行 改进,采用施加保温材料的方法,可以达到轮辋向辐板顺序凝固,从而减少形成缩孔和疏松的倾向。
随着我国铁路现代化进程的加快,铁路货物运输 的提速重载将是主要的发展方向。提高轴重是世界各 国重载运输一致采用的一项重要举措,长期的运行考 核证明这项措施既提高了运输收入,又降低了维修成 本。作为车辆关键部件的车轮在列车运行中起着承载 和制动的作用,直接关系到铁路运输的安全。因此, 提速重载的不断实施对车轮产品的制造质量和使用性 能的要求也会更高[1-3]。
图8 铸钢车轮实物 Fig. 8 Product of cast-steel wheel
图9 车轮断面低倍组织 Fig. 9 Macrostructure of wheel cross section
4 结语
(1) 方案Ⅰ模拟结果说明在辐板与轮辋过渡部位 出现了缩孔和疏松,这主要是由于凝固顺序不理想造 成的。
根据实际经验而定。浇注系统采用雨淋式浇注系统, 具体装配图如图2所示。
2 浇注工艺设计
方案Ⅰ:车轮采用石墨型,砂衬为水玻璃砂,砂
图1 铸钢车轮三维图 Fig. 1 Geometry the casting
衬厚度一般小于80 mm (具体厚度根据石墨型在使用 中的磨损程度而定),中芯为酚醛树脂砂。方案Ⅱ:在
铸钢件进料口的铸造工艺模拟及改进_米国发
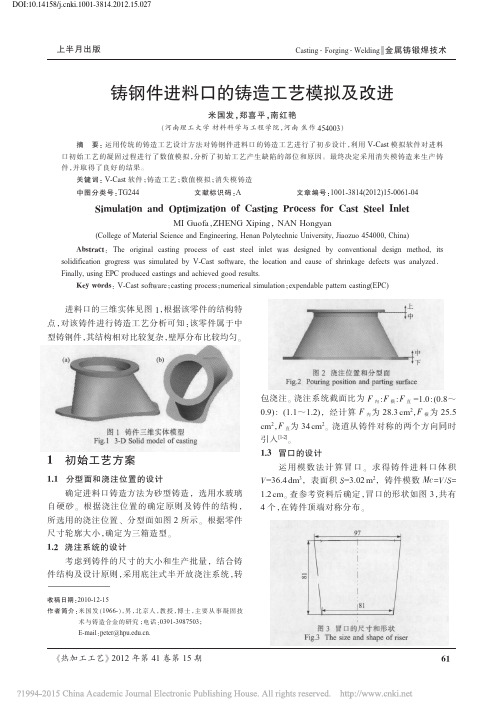
Simulation and Optimization of Casting Process for Cast Steel Inlet
MI Guofa,ZHENG Xiping, NAN Hongyan
(College of Material Science and Engineering, Henan Polytechnic University, Jiaozuo 454000, China)
凝固过程各时间阶段凝固情况如图 6 所示,透 明表示已经完全凝固。 当凝固时间 t=120 s 时,在型 腔内的边缘部分有一部分厚度的钢液已经凝固; t=200 s 时, 壁厚相对较小的部分已经开始凝固,加 冷铁的部分凝固的较快;t=250 s 时, 内浇道已经凝 固,两侧加了冷铁的筋已完全凝固;t=280 s 时,铸件 大部分已经凝固,加了冷铁的底面已完全凝固,4 个 冒口的温度最高,可以补缩铸件;t=300 s 时,在热节
Key words: V-Cast software;casting process;numerical simulation;expendable pattern casting(EPC)
进料口的三维实体见图 1,根据该零件的结构特 点,对该铸件进行铸造工艺分析可知:该零件属于中 型铸钢件,其结构相对比较复杂,壁厚分布比较均匀。
L1
Ⅳ
570 Ⅳ 210
740 380
ⅤⅠ Ⅲ
Ⅱ
Ⅱ
ⅤⅠ Ⅲ
L1
210
Ⅴ
Ⅴ
(a) 底面
(b) 顶面
图 10 内芯的区域划分 Fig.10 The regional division of inner core
40~50 ℃下烘干,形成铸型内壳。 将带有抽气室的砂箱放在振动台上,底部放入 100
- 1、下载文档前请自行甄别文档内容的完整性,平台不提供额外的编辑、内容补充、找答案等附加服务。
- 2、"仅部分预览"的文档,不可在线预览部分如存在完整性等问题,可反馈申请退款(可完整预览的文档不适用该条件!)。
- 3、如文档侵犯您的权益,请联系客服反馈,我们会尽快为您处理(人工客服工作时间:9:00-18:30)。
图 2 初始工艺下铸件凝固过程 Fig.2 Progress of casting solidification under original process
(f) t=1200 s
间 t=200 s 时,内浇道横浇道和型腔内金属液的边缘 部分已经凝固;t=400 s 时, 浇注系统和壁厚相对较 小的部分已经完全凝固; t=600 s 时, 铸件进一步凝 固,形成了孤立液相区;t=800 s 时,整个铸件没有形 成正向的温度梯度,也没有按照顺序凝固,造成铸件 的心部最后凝固;t=1000 s 时,没有凝固的液相部分 进一步缩小,因得不到有效的补缩,因此必然产生凝 固 缺 陷 ;t=1200 s 时 ,铸 件 中 心 会 最 后 凝 固 ,产 生 缩 孔和缩松。
改进方案一模拟结果如图 5 所示。 增加暗冒口 之后,铸件凝固时间延长了,可以看出铸件的下端首 先凝固,温度最高部分就在冒口和铸件的结合处; t =1200 s 时, 孤立液相区就存在与冒口和铸件的结 合部分,如果最后凝固,必然会产生缺陷,从图 6 的模 拟结果中可以证实,因此工艺需要进一步改进。
4 改进方案二的模拟
optimized process 1
54
Hot Working Technology 2011 , Vol.40 , No. 21
上半月出版
Casting·Forging·Welding 金属铸锻焊技术
图 7。 可以看出,增加保温套之后,凝固时间再次延 长,保温冒口起到了保温作用,t=600 s 时,其凝固状 态和原来类似,此时,整个铸件形成一个从下到上的 正向温度梯度, 可以很好的保证铸件的顺序凝固, t=1200 s 时,可以看出保温冒口内的温度是最高的, 补缩通道畅通,可以对铸件进行有效的补缩,实现了 从铸件到冒口的顺序凝固,缩孔、缩松完全出现在冒
作、 分型负数及芯头间隙等方面作出优化设计和优 选的情况下, 实样模造型工艺方案的造型工艺更简 化、造型效率更高、造型工序成本低,更受造型生产 操作者的欢迎。
参考文献:
[1] 中 国 机 械 工 程 学 会 铸 造 学 会. 铸 造 手 册. 第 5 卷·铸 造 工 艺 [M].北 京 机 械 工 业 出 版 社 ,2003.
[4] 智 平 , 王 延 露 . 底 杯 铸 件 铸 造 工 艺 模 拟 [J]. 铸 造 ,2006,55 (2):149-151.
[5] 米国发,赵大为,刘翔宇.大型磨台铸钢件的数值模拟与工艺 优 化[J].热 加 工 工 艺 ,2008,37(11):31-33.
[6] 李魁盛,王文清.铸造工艺学[J]. 北京:机械工业出版社,2002.
MI Guofa,ZHENG Xiping, NAN Hongyan
(College of Material Science and Engineering, Henan Polytechnic University, Jiaozuo 454003, China)
Abstract: he solidification of initial scheme of 准1300 vertical grinder base was simulated by V-Cast software, and the causes of the shrinkage defects were analyzed.Based on the simulation resul,the riser and insolating materials were increased to optimize process.The appropriate casting process is gained and the casting quality is ensured at last
因。根据模拟结果,添加了冒口和保温材料,以优化工艺;最终获得了合适的工艺,消除了缩孔、缩松缺陷,保证了铸件质
量。
关键词: V-Cast 软件;铸造工艺;数值模拟
中 图 分 类 号 :TG244
文 献 标 识14(2011)21-0050-03
Casting Process Optimization of Φ1300 Vertical Grinder Base
6 结论
(1) 运 用 V-Cast 模 拟 软 件 , 通 过 对 铸 钢 件 准1300 立式磨底座原始工艺进行凝固过程模拟,准 确预测了产生的缩孔、缩松缺陷,为设计合理的铸 造工艺提供了参考。
(2)借 助 V-Cast 软 件 ,通 过 增 加 冒 口 ,增 加 保 温套等措施,实现了铸件的顺序凝固,消除了缩孔、 缩松,确定了最佳工艺,有效解决了 Φ1300 立式磨 底座在生产中的铸造缺陷。
Key words: V-Cast software;casting;numerical simulation
传统铸件的生产是根据经验确定铸造工艺,先 试浇铸,检验试样是否存在浇铸缺陷,如有则修改工 艺方案,然后重复上述过程,直至获得合格铸件。 本 文运用 V-Cast 模拟 软件对轴承 内盖的凝固 过 程 进 行了模拟计算分析,预测了缺陷产生的位置及原因, 并根据模拟结果进行工艺优化,消除了缺陷,得到了 质 量 合 格 的 铸 件 [1-6]。
口中(图 8),该方案能够有效解决 Φ1300 立式磨底座 在现实生产中的铸造缺陷。
5 生产验证
按照最后确定的铸造工艺方案进行了试生产, 经无损检测铸件内部没有缩松、缩孔缺陷,符合技术 要求。
固 相 率 (%) 100 75 50 25
固 相 率 (%) 100 75 50 25
0
0
图 6 改进方案一的缩孔、缩松位置 Fig.6 The positions of shrinkage defects under optimized process 1
2.2 凝固过程模拟结果及分析 凝固过程各时间阶段凝固情况如图 2 所示。 其
中深色显示的部位表示钢液仍处于液态或半液态, 没有完全凝固,透明表示已经完全凝固。
由图 2 铸件凝固温度场图可以看出, 当凝固时
(a) t=200 s
(b) t=400 s
(c) t=600 s
(d) t=800 s
(e) t=1000 s
由图 3 凝固缺陷图可以看出, 靠近铸件顶部大 平面和下部厚壁相接处出现缩孔缩松等缺陷, 针对 上述出现的结果, 采用在铸件顶部加冒口的设计方 法来消除。
3 改进方案一的模拟
3.1 增加暗冒口 根据初始工艺方案模拟结果, 铸件顶部出现缺
陷,可以考虑在顶部增加一个暗冒口来解决。 根据模
数方法来计算冒口,查铸造工艺手册,并根据生产情 况,可选标准圆柱形暗冒口,其尺寸是直径 120 mm, 高度 240 mm,如图 4 所示。 3.2 凝固过程模拟结果及分析
1.2 浇注位置的确定 浇注位置在很大程度上着眼于控制铸件的凝
固,实现顺序凝固的铸件,可消除缩孔、缩松,保证获 得致密铸件。浇注系统的引入位置为:开设两个內浇 道,开设在分型面处,呈对称分布。 1.3 浇注系统的确定
铸钢的特点是熔点高,流动性差,收缩大,易氧 化, 故其浇注系统要求结构简单, 横截面尺寸应较 大,要求快速、平稳地充型,并有利于铸件的顺序凝 固。考虑到铸件的尺寸的大小和生产批量,结合铸件 结构及设计原则,采用中注式半开放浇注系统,并用 转包浇注。
浇 注 系 统 截 面 比 为 F 內 ∶F 橫 ∶F 直 =1.0∶(0.8-0.9)∶ (1.1-1.2),经计算,F 內=9.67 cm2,F 橫=8.7 cm2,F 直= 11.6 cm2。
2 初始方案的模拟
2.1 相关参数的设定
《热加工工艺》 2011 年第 40 卷第 21 期
53
金属铸锻焊技术 Casting·Forging·Welding
4.1 设计保温冒口 通过查铸造工艺手册, 并根据该铸件的结构特
点, 在方案一的基础上设计保温冒口。 经计算可得 到保温冒口套直径 D =135 mm,高度 H =160 mm。 4.2 凝固过程模拟分析
经过改进后,对方案二进行模拟,其凝固结果如
固 相 率 (%) 100 75 50 25 0
图 3 初始工艺下缺陷分布
(上接第 52 页)成功的分型负数是:下箱与中箱的分 型负数和中箱与上箱的分型负数均为 2.5 mm(在实 践中 也可以简化 为中箱模样 、3 个腿脚模 块不 放 缩 尺);1# 砂芯的芯头配合间隙为 3 mm,2# 砂芯的芯头 配合间隙为 1.5 mm。
3 结束语
对于大型球铁件风电行星架类铸件, 实样模造 型工艺方案与大砂芯造型工艺方案相比, 在模型的 分型、模块的定位、砂芯的设计、芯盒的结构及其制
2011 年 11 月
用 Pro/E 软 件 绘 出 铸 件 的 实 体 模 型 , 转 化 为 STL 格式文件,导入 V-Cast 模拟软件进行实体网格 划 分 ,网 格 数 1 000 000,材 料 牌 号 为 ZG45,水 玻 璃 砂造型, 浇注温度 1580 ℃, 液相临界温度:1512.0 ℃,相临界温度:1469.9 ℃,铸型初始温度 25 ℃。
参考文献:
[1] 陈立林,米国发,王有超.门框底衬铸钢件的铸造工艺设计及 数 值 模 拟 [J].热 加 工 工 艺 ,2010,39(3):53-55.
[2] 李弘英, 赵成 志. 铸 造 工 艺 设 计[M].北 京 :机 械 工 业 出 版 社 , 2005.
[3] 熊守美,许庆彦,康进武.铸造过程模拟仿真技术[M].北京: 机 械 工 业 出 版 社 ,2004.
DOI:10.14158/ki.1001-3814.2011.21.024 上半月出版
Casting·Forging·Welding 金属铸锻焊技术
准1300 立式磨底座的铸造工艺改进
米国发,郑喜平,南红艳 (河南理工大学 材料科学与工程学院,河南 焦作 454003)