毛坯热处理节能技术
热处理节能技术现状和展望
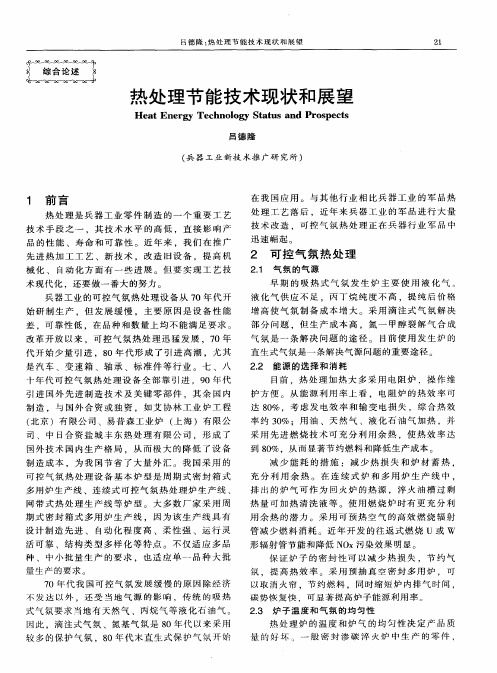
在 我 国应 用 。与 其 他 行 业 相 比 兵器 工 业 的军 品 热
处 理 工艺 落 后 ,近年 来兵 器 工 业 的 军 品进 行 大 量
技 术 改 造 .可 控 气 氛 热 处 理 正 在 兵 器 行 业 军 品 中
迅 速 崛起 。
先 进 热 加 工 工 艺 、新 技 术 ,改 造 旧设 备 ,提 高 机
式 气 氛要 求 当地 有 天然 气 、丙 烷 气 等 液 化石 油 气 。 因此 ,滴 注 式气 氛 、氮基 气 氛 是 8 0年代 以来 采 用 较 多 的保 护 气 氛 ,8 0年代 末 直 生 式 保 护 气 氛 开 始
改革 开 放 以来 ,可 控 气 氛 热 处 理 迅 猛 发 展 ,7 0年 代 开 始 少量 引进 ,8 0年 代 形成 了 引进 高潮 ,尤 其
气 氛 是 一 条 解 决 问题 的途 径 。 目前 使 用 发 生 炉 的
直 生式 气氛 是一 条解 决气 源 问题 的重要 途径 。
是 汽 车 、变 速 箱 、轴 承 、标 准 件 等 行 业 。 七 、八
吕德 隆 : 热处 理 节 能技 术 现 状 和 展望
—
2 1
x — — K — — ∞ —
综 合 论 述
q— — f — — f ’ —f —
热 处 理 节 能 技 术 现 状 和 展 望
H e tEne g c o o y S a usa d o pe t a r y Te hn l g t t n Pr s c s
可 控 气 氛 热 处 理 设 备 基 本 炉 型是 周 期 式 密 封 箱 式
多 用 炉 生 产 线 、连 续 式 可 控 气 氛 热 处 理 炉 生 产 线 、
纺织工业中的化学纤维节能技术

2.智能化:智能化技术的应用将对化学纤维生产过程进行精确控制,实现生产过程的自动化、信息化,提高生产效率,降低能耗。
3.高性能化:通过研发新型高性能化学纤维,提高纤维的附加值,满足不同领域的高性能需求,从而实现节能。
3.持续改进:根据监测和评估结果,不断优化生产工艺和设备,推动节能技术的持续改进。
十六、化学纤维节能技术的未来展望
随着科技进步和社会发展,化学纤维节能技术将呈现出以下发展趋势:
1.新材料的应用:新型高性能纤维材料和生物基纤维的发展,将为化学纤维行业带来更低能耗和更环保的生产方式。
2.智能化生产:智能化、自动化生产线的广泛应用,将实现化学纤维生产过程的精确控制,提高生产效率和能源利用率。
在化学纤维行业不断追求节能降耗的今天,通过技术创新、政策引导和市场驱动,我国纺织工业的节能技术正逐步迈向世界先进水平。未来,化学纤维节能技术的进步将为行业带来更加绿色、高效、可持续的发展前景。
十四、化学纤维节能技术的培训与人才培养
在化学纤维节能技术的推广与应用中,人才培养是关键环节。为了满足行业需求,以下措施至关重要:
2.无溶剂或低溶剂改性:采用无溶剂或低溶剂改性技术,减少溶剂的使用和回收过程中的能耗。
3.超临界流体技术:利用超临界流体的特殊性质,如低粘度、高扩散性等,实现高效、低能耗的纤维改性。
三、化学纤维加工过程中的节能技术
化学纤维加工过程中的节能技术主要包括:
1.高效节能设备:选用高效节能的纺纱、织造、染整等设备,降低能耗。
4.多功能化:开发具有多种功能的化学纤维,如保暖、导电、抗菌等,减少其他辅助材料的使用,实现节能。
热处理生产的节能与环保技术研究
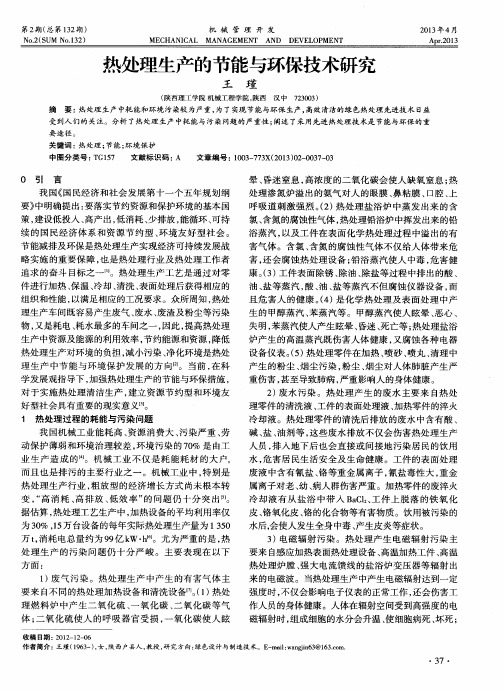
物, 又是耗 电、 耗水最多的车间之一 , 因此 , 提高热处理 生产 中资源及能源 的利用效率 , 节约能源和资源 , 降低 热 处 理生 产对 环境 的负担 , 减小 污染 、 净 化环 境是 热处
理 生 产 中节 能 与 环 境 保 护 发 展 的方 向 。当 前 , 在科 学 发 展观 指导 下 , 加强 热处 理生 产 的节 能与 环保 措施 , 对 于实 施 热处 理 清 洁 生产 , 建立 资 源 节 约 型 和环 境 友 好 型 社会 具有 重要 的现实 意义 。
氯、 含氮的腐蚀性气体 , 热处理铅浴炉中挥发出来 的铅 浴蒸汽 , 以及 工 件 在 表 面化 学 热处 理 过 程 中溢 出 的有 害气体 。含氯 、 含氮的腐蚀性气体不仅给人体带来危 害, 还会腐蚀热处理设备 ; 铅浴蒸汽使人 中毒 , 危害健 康。 ( 3 ) 工件 表 面除 锈 、 除油 、 除盐 等过 程 中排 出的 酸 、 油、 盐等蒸汽 , 酸、 油、 盐等蒸汽不但腐蚀仪器设备 , 而 且 危 害 人 的健 康 。 ( 4 ) 是 化 学 热处 理 及 表 面 处 理 中产 生 的 甲醇 蒸 汽 、 苯 蒸 汽等 。 甲醇蒸 汽 使 人 眩晕 、 恶心 、 失明 , 苯蒸汽使人产生 眩晕 、 昏迷 、 死亡等 ; 热处理盐浴 炉产生的高温蒸汽既伤害人体健康 , 又腐蚀各种 电器 设备仪表。 ( 5 ) 热处理零件在加热 、 喷砂 、 喷丸 、 清理 中 产 生 的粉 尘 、 烟 尘 污染 , 粉尘 、 烟尘 对 人 体 肺脏 产 生 严 重 伤害 , 甚至 导致 肺病 , 严 重影 响人 的身体健 康 。
冷却液。热处理零件 的清洗后排放的废水 中含有酸 、 碱、 盐、 油剂 等 , 这 些 废水 排 放 不仅 会 伤 害 热处 理 生 产
通过调整热处理工艺降低能耗的几种方法

通过调整热处理工艺降低能耗的几种方法随着节能减排的持续推广和实施,降低工业生产中的能耗已经成为了各企业必须关注和解决的问题。
其中,热处理作为一个重要的工业生产环节,其能耗问题尤为突出。
为此,在热处理生产过程中,采用多种方法调整热处理工艺,从而减少热处理的能耗。
1. 调整热处理工艺参数热处理过程的能耗直接与工艺参数相关,采取正确的工艺参数可以使热处理设备的能效显著提高。
首先,应通过合理的热处理温度和时间配比,减少热处理能量的消耗。
其次,减小热处理时间,可以使处理部件的温度梯度减小,从而避免能量的浪费。
此外,在工业生产中,往往能够采取适当的热处理介质,如空气、氮气、惰性气体等,对材料进行热处理,降低热处理温度和时间的多项措施。
2. 优化热处理设备的结构和设计为降低热处理的能耗,需要对热处理设备的结构和设计进行优化。
首先,应选择高效、节能的热处理设备,如采用能源利用率高的气氛炉,可以节省大量的热能。
其次,在设备设计上,可以考虑优化热处理炉子内部的空气流动方式和热量传递方式,充分利用炉子内空气的流动和热传递,避免产生局部高温区域,减少不必要的能耗。
此外,对于高耗能的某些热处理方法,如淬火、回火等方法,应采用先进的加热和传热方法,同时充分利用余热,克服对环境的不良影响。
3. 优化热处理工艺流程热处理工艺流程的优化也是降低能耗的重要措施。
首先,应考虑合理的时间、温度和工艺模式配合,从而使得工艺过程的能量损失达到最小。
其次,加入适量的浸渍剂可以减少热处理的能耗,提高产品表面的质量。
此外,在生产过程中,还应充分考虑相关的环境因素和能源利用率,从而优化热处理工艺流程,减少能耗。
4. 整体优化热处理系统为使热处理生产达到高效节能的目标,必须对整个热处理系统进行全面优化。
首先,应对热处理的能量运用与节能的问题进行全面考虑。
其次,要注重热处理现场管理,从生产计划、物品流转、作业流程等方面入手,精益求精实现优化。
在评价热处理系统能耗指标时,应注意研究整体优化的策略,不仅注重单个产品的能耗指标,还要注重提高整体热处理系统的能效。
热处理发展趋势

热处理发展趋势热处理是一种非常重要的金属加工工艺,它通过加热和冷却的方式改变金属材料的组织结构和性能,从而提高材料的硬度、强度和耐磨性等。
随着科技的进步和工业的发展,热处理技术也在不断发展,以下是一些热处理发展趋势:1. 智能化和自动化:随着人工智能和自动化技术的不断发展,热处理设备和工艺控制系统越来越智能化。
自动控制系统可以实时监测和调节热处理过程中的温度、压力和时间等参数,从而提高热处理的稳定性和一致性。
2. 环保和节能:环保和节能是现代工业发展的重要方向,热处理行业也不例外。
新型热处理设备采用高效的能源利用和废气处理技术,减少了能源的浪费和环境污染的排放。
通过优化热处理工艺和参数,可以减少处理时间和能耗,提高能源利用效率。
3. 先进的工艺和材料:随着辅助技术的不断推进,热处理工艺也在不断创新。
采用先进的淬火介质和控制方法,可以提高金属材料的淬透性和耐磨性。
新型金属合金材料的开发和应用也在推动热处理技术的发展,例如高强度、高耐腐蚀性和高温合金等。
4. 数据化和信息化:随着数据采集和处理技术的快速发展,热处理行业也逐渐实现数据化和信息化。
通过采集和分析热处理过程中的各种数据,可以深入了解材料和工艺之间的关系,优化热处理工艺参数,提高产品的质量和一致性。
5. 个性化定制和灵活生产:随着市场需求的不断变化,热处理行业越来越注重个性化定制和灵活生产。
热处理设备具备较大的调节能力和适应性,可以根据不同的工件和要求进行定制化的热处理工艺。
灵活生产模式可以提高生产效率和客户满意度,满足个性化和小批量生产的需求。
热处理技术在智能化、环保节能、先进工艺和材料、数据化信息化和个性化定制等方面都有着较为明显的发展趋势。
这些趋势的出现和应用,将进一步推动热处理行业的发展和进步。
机械工艺中的节能与环保技术

机械工艺中的节能与环保技术在当今社会,随着工业化进程的加速和资源环境压力的不断增大,节能与环保已经成为机械工艺领域中至关重要的课题。
机械工艺作为制造业的重要组成部分,其在生产过程中的能源消耗和环境污染问题不容忽视。
因此,积极探索和应用节能与环保技术,对于提高机械工艺的可持续发展能力、降低生产成本、保护环境具有重要的现实意义。
一、机械工艺中的能源消耗与环境影响机械工艺涵盖了从原材料加工到成品制造的一系列生产流程,包括铸造、锻造、焊接、切削加工、热处理等。
在这些工艺过程中,能源的消耗主要体现在以下几个方面:首先,机械设备的运行需要消耗大量的电能。
例如,机床、起重机、压缩机等设备在工作时都需要持续供电,以驱动电机、液压系统等部件。
其次,加工过程中的热能消耗也不容忽视。
在热处理、铸造等工艺中,需要对材料进行加热,这往往需要消耗大量的燃料或电能。
此外,原材料的运输和存储也会产生一定的能源消耗。
机械工艺对环境的影响主要表现为废水、废气、废渣的排放以及噪声污染等。
例如,在切削加工过程中会产生大量的切屑和切削液废水;铸造和焊接过程中会产生废气和粉尘;热处理过程中可能会排放有害气体;而机械设备的运行则会产生噪声。
二、节能技术在机械工艺中的应用1、优化工艺设计通过对机械加工工艺的优化设计,可以减少不必要的工序和加工余量,从而降低能源消耗。
例如,采用先进的计算机辅助设计(CAD)和计算机辅助制造(CAM)技术,对零件的结构和加工工艺进行精确模拟和优化,提高材料利用率,减少加工时间和能源消耗。
2、选用高效节能设备在机械工艺中,选用高效节能的设备是实现节能的重要途径。
例如,选用节能型的机床、电机、压缩机等设备,这些设备通常具有更高的能源利用效率和更低的能耗。
同时,对于一些老旧设备,可以进行节能改造,如安装变频器、节能电机等,提高设备的运行效率。
3、余热回收利用在许多机械工艺过程中,会产生大量的余热。
对这些余热进行回收利用,可以有效地降低能源消耗。
热处理节能新工艺

热处理节能新工艺01采用高效节能的热处理工艺1)如果把渗碳温度从930℃提高到1050℃,可以减少40%的工艺周期,例如在真空炉中低压渗碳工艺,在1050℃进行渗碳。
2)用氮碳共渗等代替渗氮和碳氮共渗,可把工艺温度从850~930℃降到550~580℃;代替一般气体渗氮,可把渗氮时间从30~70h减少到2~3h。
3)以碳氮共渗代替薄层渗碳。
处理温度可以由930℃降至850℃;当渗层深度在1mm以下时,碳氮共渗比渗碳时间能缩短30%;并由于加热温度低、时间短,因此工件淬火后变形小。
4)乙炔低压渗碳技术,渗碳速度快,节能;原料气消耗低,排放小,可实现高温渗碳,达到缩短工艺周期,节能的目的。
02缩短加热时间工艺1)零保温淬火按传统热处理工艺,保温时间≥总加热时间的1/2或1/3。
对于达到薄件尺寸的碳素钢和低合金结构钢,加热温度在Ac1或Ac3以上时可采用零保温淬火工艺。
实践证明,35Cr、45Cr和42CrMo等调质钢采用零保温淬火工艺,均能达到装机服役条件。
与传统的保温淬火工艺相比,省去了工件透烧和奥氏体均匀化所需要的时间,可降低20%~30%能耗。
例如,某传动轴材料45钢,传统热处理工艺为:840℃×60min淬火,600℃×120min回火,硬度215~245HBW。
在试验的基础上,确定该传动轴采用(870±10)℃×0min淬火及(680±10)℃×0min回火的“零保温”调质工艺。
经检验,淬火后得到细小的板条状马氏体组织,回火后显微组织为细的回火索氏体,硬度215~235HBW,完全满足其技术要求,使用效果良好。
2)不均匀奥氏体加热淬火。
钢件加热到奥氏体状态,使碳化物充分溶解奥氏体达到均匀化需要较长时间,但奥氏体未达到均匀化即实行淬火并不影响其淬火、回火后的性能。
03采用表面、局部加热替代整体加热方法表面加热淬火方法是以感应、火焰、激光等加热工件表面,然后靠喷液、浸液、自冷方式使钢件淬硬。
热处理能耗及设备的节能降耗
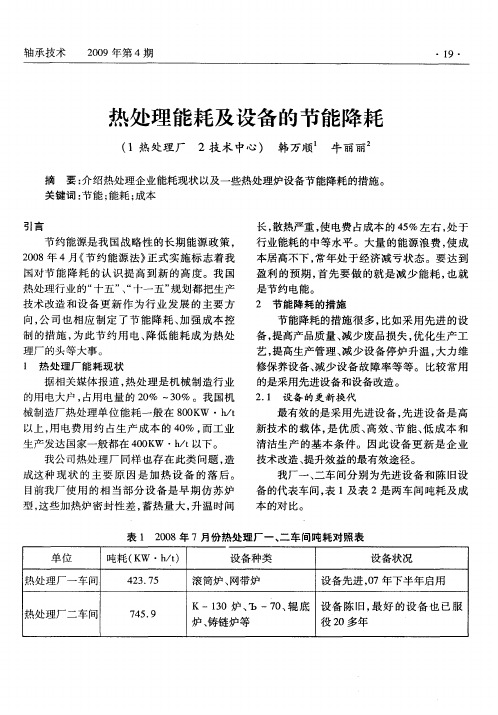
目前 我厂 使 用 的 相 当部 分 设 备 是 早 期 仿 苏 炉 型 , 些 加热 炉密 封 性 差 , 这 蓄热 量 大 , 温 时 间 升
表 1 20 0 8年 7月份 热处 理厂 一 、 车 间吨耗 对照 表 二 单 位 热 处理 厂一 车 间 吨耗 ( W ・ / ) K ht 4 3 7 2 .5 设 备种类 滚筒 炉 、 网带炉 设 备状况 设备 先进 ,7年 下半 年启 用 0
沉重 的成本 负担 ( 7月份 二 车 间 电 费 占生 产成
建造 一台大 型 的 回火 炉 , 台淬 火 炉 的轴 三 承零 件淬 火 后 , 过 清 洗 直 接装 入 标 准 箱 内 , 通 由传送 带 送 入 大 型 回火 炉 进 行 回火 。经 过 基
2 1 设备 的更新换 代 .
制的措施 , 为此节约用 电、 降低 能耗成 为热 处 理 厂 的头等 大事 。
1 热 处 理 厂 能 耗 现 状
据相 关 媒体 报 道 , 处 理是 机 械 制 造 行 业 热 的用 电大 户 , 占用 电 量 的 2 % ~ 0 。我 国机 0 3% 械制 造厂 热 处理单 位 能耗 一 般 在 8 0 W ・ / 0K ht 以上 , 电 费 用 约 占生 产 成 本 的 4 % , 用 0 而工 业 生产 发达 国家一般 都 在 4 0 W ・ / 以下 。 0K ht 我公 司热处 理 厂 同样 也存 在 此 类 问题 , 造 成这 种 现 状 的 主 要 原 因 是 加 热 设 备 的 落 后 。
20 0 9年第 4期
成本 ( 万元 )
18 1 9 .
电费 占成本
4 .l 2 8 %
热处理厂 一车 间
热处理生产管理中的节能降耗措施
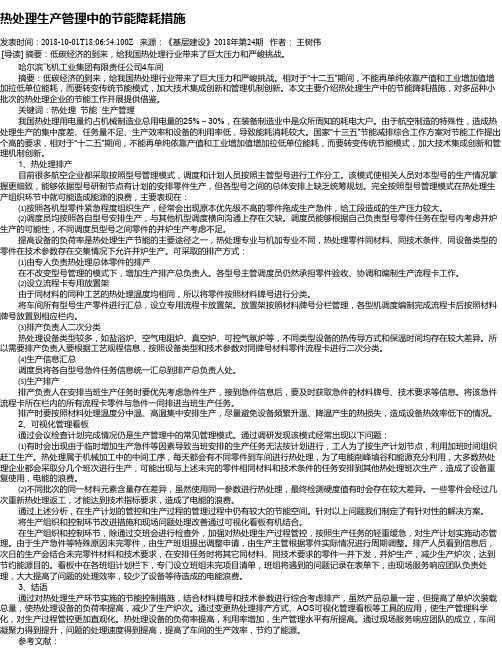
热处理生产管理中的节能降耗措施发表时间:2018-10-01T18:06:54.100Z 来源:《基层建设》2018年第24期作者:王树伟[导读] 摘要:低碳经济的到来,给我国热处理行业带来了巨大压力和严峻挑战。
哈尔滨飞机工业集团有限责任公司4车间摘要:低碳经济的到来,给我国热处理行业带来了巨大压力和严峻挑战。
相对于“十二五”期间,不能再单纯依靠产值和工业增加值增加拉低单位能耗,而要转变传统节能模式,加大技术集成创新和管理机制创新。
本文主要介绍热处理生产中的节能降耗措施,对多品种小批次的热处理企业的节能工作开展提供借鉴。
关键词:热处理节能生产管理我国热处理用电量约占机械制造业总用电量的25%~30%,在装备制造业中是众所周知的耗电大户。
由于航空制造的特殊性,造成热处理生产的集中度差、任务量不足、生产效率和设备的利用率低,导致能耗消耗较大。
国家“十三五”节能减排综合工作方案对节能工作提出个高的要求,相对于“十二五”期间,不能再单纯依靠产值和工业增加值增加拉低单位能耗,而要转变传统节能模式,加大技术集成创新和管理机制创新。
1、热处理排产目前很多航空企业都采取按照型号管理模式,调度和计划人员按照主管型号进行工作分工。
该模式使相关人员对本型号的生产情况掌握更细致,能够依据型号研制节点有计划的安排零件生产,但各型号之间的总体安排上缺乏统筹规划。
完全按照型号管理模式在热处理生产组织环节中就可能造成能源的浪费,主要表现在:⑴按照各机型零件紧急程度组织生产,经常会出现原本优先级不高的零件拖成生产急件,给工段造成的生产压力较大。
⑵调度员均按照各自型号安排生产,与其他机型调度横向沟通上存在欠缺。
调度员能够根据自己负责型号零件任务在型号内考虑并炉生产的可能性,不同调度员型号之间零件的并炉生产考虑不足。
提高设备的负荷率是热处理生产节能的主要途径之一,热处理专业与机加专业不同,热处理零件同材料、同技术条件、同设备类型的零件在技术参数存在交集情况下允许并炉生产。
现代热处理节能技术和装备(下)
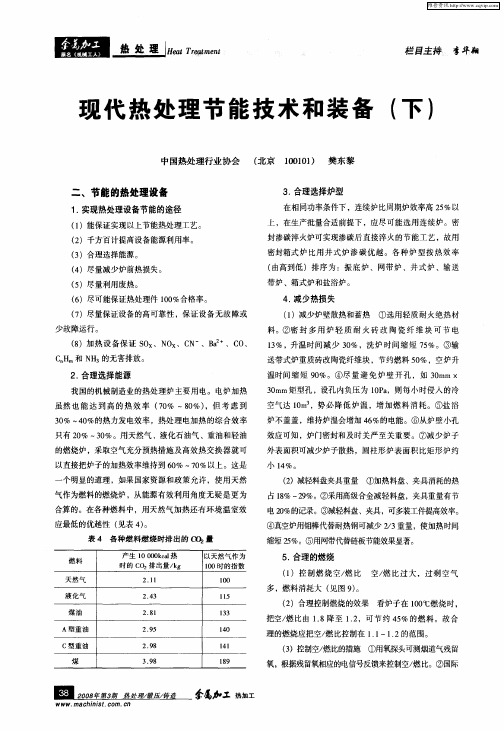
栏 且主持
李华翔
现 代 热 处理 节 能技 术 和装 备 ( ) 下
中国热处理行业协会 ( 北京 10 0 ) 樊东黎 0 1 1
二、节能的热处理设备
1 实现热处理设备节能的途径 .
( )能保证 实现 以上节能热处理工艺。 1 ()千方百计提高设备能源利用率。 2
煤
看炉子在 10C 0  ̄燃烧时 ,
2 8 .l
2 9 .5 2 9 .8
3 9 .8
l3 3
l0 4 1l 4
l9 8
把空/ 燃比由 18降至 12 . .,可 节约 4% 的燃料 。故 合 5
理的燃烧应把空/ 比控制在 1 1 . 燃 . ~12的范围。
()控制空/ 比的 3 燃 措施 ①用氧探头可测烟道气残留 氧, 根据残留氧相应的电信号反馈来控制空/ 比。②国际 燃
物中 N x 0 过高 ,会污染大气的限制 ( 见图 1) 5。
《
1 1 1
f30 0 ̄ (
囊 蒌
/ 1 0 2 0 7/O 。 / O r 8 [
/
.
璺
担
/
宴 紫
’
— ,
/
过剩 空气率 ( %)
2O 37 5 1 68 . . . .
只有 2 % ~3 %。用天然气 、液化石油气 、重油和轻油 0 0
的燃烧 炉 , 采取空气充分预热措施 及高效热交换 器就可 以直接把炉子 的加热效率维持 到 6% ~ 0 0 7 %以上 。这是
一
个明显 的道理 ,如果国家资源和政策允许 ,使 用天然
()减轻料盘夹具重量 ①加热料盘、夹具消耗的热 2 占 1 ~ 9 ②采用高级合金减轻料盘,夹具重量有节 8 2%。 % 电 2%的 0 记录。③减轻料盘 、 夹具 ,可多装工件提高效率。 ④真空炉用钼棒代替耐热钢可减少 23 / 重量 ,使加热时间 缩短 2%。⑤用网带代替链板节能效果显著。 5
节能、高效、优质的热处理工艺(四)

要减少淬火 内应力 , 防止淬火开裂 。在 马氏体转变 区应慢冷 , 在珠光体转变区应快冷。如 P 0 2 钢在 40 0 60℃之 间需 要快速冷却 ,1 可 以慢一些冷 0 78钢 却 。淬火介 质 可 以采 用水 、 空气 、 。 油 为 了淬火 各 阶段 具 有 理 想 冷 却 速 度 , 型锻 坯 大 不采 用单 一 的淬火介 质 , 而是综 合 采 用几 种 介质 , 分 阶段冷 却 。 大型锻 坯 采用 “ 水 一 ” “ 空一 一 ” 空一 油 和 炉一 水 油 双液 淬火 , 以便 使 锻 坯 组 织 淬 火 为 马 氏体 。对 于 7 8钢 1 来说 , 氏体很 稳定 , 奥 可在 炉 内降 温后 再 空 冷 。即在 加热 炉 内从奥 氏体化 温度 降 温到 70~ 0 保 持 5 80o C,
第3 2卷第 4期 21 0 1年 8月
热处理技术与装备
RE CHUL IHU YU Z ANGB I I S HU J E
Vo .3 No 4 1 2, .
Au , 0 1 g 2 1
・
工艺 研究 ・
节能 、 高效 、 质 的热处 理 工 艺 ( ) 优 四
刘 宗 昌 , 长 军 , 云 萍 袁 计
—
可按炉子最大功率 升温 ( 也可随炉升温 ) 当指示仪 , 表达 到奥 氏体 化 温 度 时 , 始 计 算 均 温 时 间 。均 温 开 时 问决 定 于锻 坯 的尺寸 和装 炉 量 。 当从 炉子 火 孔 目 视锻坯 的颜色 与炉膛 火色 一 致 时 , 温 结 束 , 始计 均 开 算保温 时 间 。均 温 +保 温 时 间 可 以 按 经 验 法 确 定 , 即按锻 坯有 效厚 度 每 2 m 加热 1h进 行 计算 。热 5m 透时 间也 可用 计算 机计算 。锻 坯 在 台 车退 火 炉 中的 加热 时 间见表 3 。锻坯 热 透 后 的保 温 时 间一 律 2h 。
热处理降本增效改善提案

热处理降本增效改善提案
热处理是一种材料加工过程,可以通过加热和冷却的组合来改变材料的性能。
它被广泛应用于金属制造业,特别是在航空航天和汽车制造领域。
然而,热处理成本较高,为了提高效率并降低成本,有必要改善热处理降本增效的方案。
以下是一些建议。
1.优化加热方式和时间:通过优化加热方式和时间,可以减少加热时间,提高加工效率,降低能源消耗和成本。
同时,多温区控制可以更好地控制结果。
2. 探究新的工艺:对于特殊的材料,可以探索新的工艺和技术。
例如,采用高速加热和冷却来提高效率和质量。
3. 加强设备和工具的维护:为了确保热处理设备和工具的正常运行,需要加强设备和工具的维护,以提高寿命和效率。
4. 采用先进的数据管理:采用先进的数据管理系统,可以帮助企业更好地掌握加工过程,实现实时监测,准确追踪每一个产品的质量数据,从而提高效率并降低成本。
5. 通过培训提高员工技能:为了提高生产效率和质量,需要通过培训和技能提升来提高员工技能和专业知识,使他们更好地掌握热处理的技术和方法。
总之,热处理降本增效是一个系统性的问题,需要企业从加工技术、设备维护、数据管理以及员工培训等各个方面综合考虑。
只有通
过不断的改进和优化,才能实现降低成本、提高生产效率和提高产品质量的目标。
汽车制造企业能耗分析及节能新技术
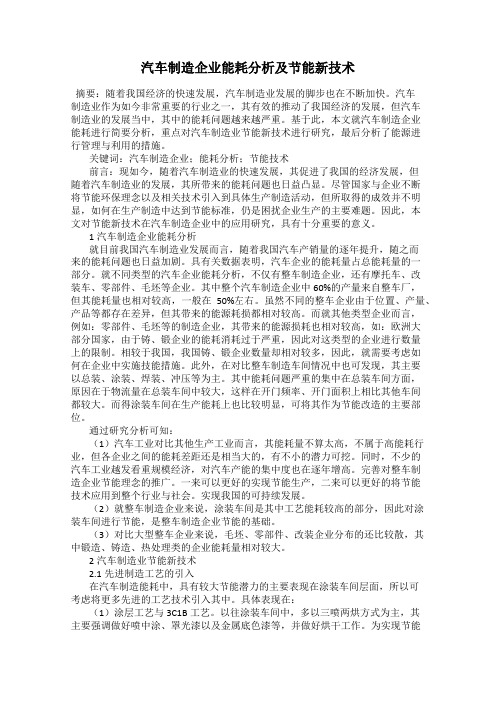
汽车制造企业能耗分析及节能新技术摘要:随着我国经济的快速发展,汽车制造业发展的脚步也在不断加快。
汽车制造业作为如今非常重要的行业之一,其有效的推动了我国经济的发展,但汽车制造业的发展当中,其中的能耗问题越来越严重。
基于此,本文就汽车制造企业能耗进行简要分析,重点对汽车制造业节能新技术进行研究,最后分析了能源进行管理与利用的措施。
关键词:汽车制造企业;能耗分析;节能技术前言:现如今,随着汽车制造业的快速发展,其促进了我国的经济发展,但随着汽车制造业的发展,其所带来的能耗问题也日益凸显。
尽管国家与企业不断将节能环保理念以及相关技术引入到具体生产制造活动,但所取得的成效并不明显,如何在生产制造中达到节能标准,仍是困扰企业生产的主要难题。
因此,本文对节能新技术在汽车制造企业中的应用研究,具有十分重要的意义。
1汽车制造企业能耗分析就目前我国汽车制造业发展而言,随着我国汽车产销量的逐年提升,随之而来的能耗问题也日益加剧。
具有关数据表明,汽车企业的能耗量占总能耗量的一部分。
就不同类型的汽车企业能耗分析,不仅有整车制造企业,还有摩托车、改装车、零部件、毛坯等企业。
其中整个汽车制造企业中60%的产量来自整车厂,但其能耗量也相对较高,一般在50%左右。
虽然不同的整车企业由于位置、产量、产品等都存在差异,但其带来的能源耗损都相对较高。
而就其他类型企业而言,例如:零部件、毛坯等的制造企业,其带来的能源损耗也相对较高,如:欧洲大部分国家,由于铸、锻企业的能耗消耗过于严重,因此对这类型的企业进行数量上的限制。
相较于我国,我国铸、锻企业数量却相对较多,因此,就需要考虑如何在企业中实施技能措施。
此外,在对比整车制造车间情况中也可发现,其主要以总装、涂装、焊装、冲压等为主。
其中能耗问题严重的集中在总装车间方面,原因在于物流量在总装车间中较大,这样在开门频率、开门面积上相比其他车间都较大。
而得涂装车间在生产能耗上也比较明显,可将其作为节能改造的主要部位。
热处理的节能
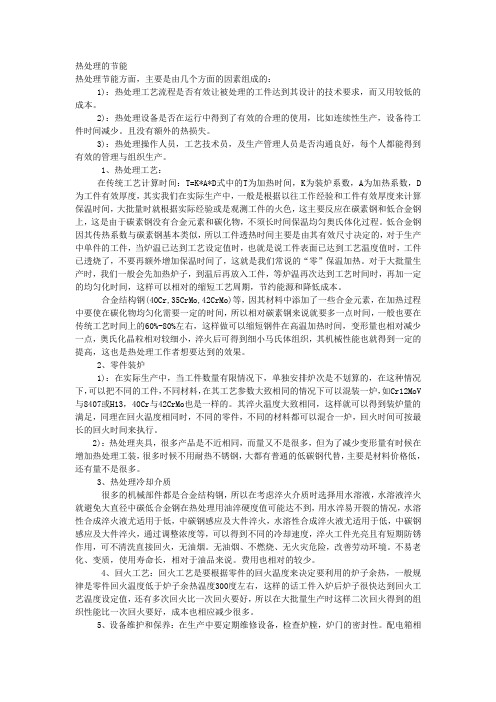
热处理的节能热处理节能方面,主要是由几个方面的因素组成的:1):热处理工艺流程是否有效让被处理的工件达到其设计的技术要求,而又用较低的成本。
2):热处理设备是否在运行中得到了有效的合理的使用,比如连续性生产,设备待工件时间减少。
且没有额外的热损失。
3):热处理操作人员,工艺技术员,及生产管理人员是否沟通良好,每个人都能得到有效的管理与组织生产。
1、热处理工艺:在传统工艺计算时间:T=K*A*D式中的T为加热时间,K为装炉系数,A为加热系数,D 为工件有效厚度,其实我们在实际生产中,一般是根据以往工作经验和工件有效厚度来计算保温时间,大批量时就根据实际经验或是观测工件的火色,这主要反应在碳素钢和低合金钢上,这是由于碳素钢没有合金元素和碳化物,不须长时间保温均匀奥氏体化过程。
低合金钢因其传热系数与碳素钢基本类似,所以工件透热时间主要是由其有效尺寸决定的,对于生产中单件的工件,当炉温已达到工艺设定值时,也就是说工件表面已达到工艺温度值时,工件已透烧了,不要再额外增加保温时间了,这就是我们常说的“零”保温加热。
对于大批量生产时,我们一般会先加热炉子,到温后再放入工件,等炉温再次达到工艺时间时,再加一定的均匀化时间,这样可以相对的缩短工艺周期,节约能源和降低成本。
合金结构钢(40Cr,35CrMo,42CrMo)等,因其材料中添加了一些合金元素,在加热过程中要使在碳化物均匀化需要一定的时间,所以相对碳素钢来说就要多一点时间,一般也要在传统工艺时间上的60%-80%左右,这样做可以缩短钢件在高温加热时间,变形量也相对减少一点,奥氏化晶粒相对较细小,淬火后可得到细小马氏体组织,其机械性能也就得到一定的提高,这也是热处理工作者想要达到的效果。
2、零件装炉1):在实际生产中,当工件数量有限情况下,单独安排炉次是不划算的,在这种情况下,可以把不同的工件,不同材料,在其工艺参数大致相同的情况下可以混装一炉,如Cr12MoV 与8407或H13,40Cr与42CrMo也是一样的。
节能热处理新工艺技术的分析
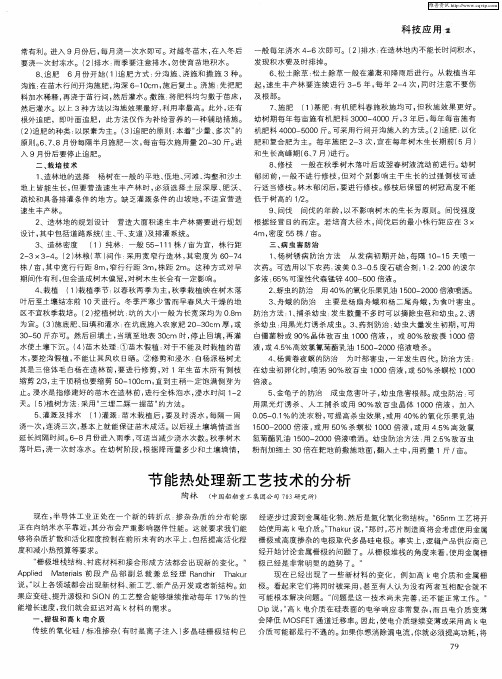
4 栽植 、
() 1 栽植季节 : 以春秋 两季为主 , 季栽植映在树木 落 秋
2 蚜虫的防治 、 3 舟蛾 的防治 、
用 4 %的氧化乐果乳油 1 0 — 0 0倍液喷洒。 0 020 5
叶后至土壤结冻前 1 O天进行。冬季严寒 少雪而早春风大干燥 的地
主要 是杨扇舟蛾 和杨 二尾舟蛾 , 为食 叶害虫。 区不 宜 秋 季 栽 培 。 ( 挖 植 树 坑 : 的 大 小 一 般 为长 宽 深均 为 O8 2) 坑 m 防 治 方 法 :、 杀 幼 虫 : 生 数 量 不 多 时 可 以摘 除 虫苞 和 幼 虫。 、 1捕 发 2 诱 为宜 。 ( 施底 肥 、 3) 回填 和 灌 水 : 坑 底 施 入 农 家 肥 2 — 0 m 厚 , 在 0 3c 或 杀幼 虫 : 黑 光 灯 诱 杀 成 虫 。 3 药 剂 防 治 : 虫 大 量 发 生 初 期 , 用 用 、 幼 可
3 一 O斤 亦可 。 然 后 回填 土 , O5 当填 至 地 表 3 c 时 , 止 回 填 , 灌 白僵 菌 粉 或 9 % 晶 体 敌 百 虫 1 0 0m 停 再 0 0 0倍 液 , ,或 8 %敌 敌 畏 1 0 0 0 0倍
水使土壤 下沉 。( 苗木 处理 一 4) ①苗木假植 : 对于不能及 时栽植 的苗 液 , 45 或 .%高效氯氰菊酯乳油 1 0 — 0 0倍液 喷杀。 0 20 5 木, 要挖沟假植 , 不能让 其风吹 日晒。②修剪和 浸水 白杨 派杨树尤 4 杨黄卷夜螟 的防治 为叶部害虫 , 、 一年发生四代。 防治方法 : 其是三倍体毛 白杨在造林前 , 要进行修 剪 , 1年生苗 木所有 侧枝 在幼虫初卵化时 , 对 喷洒 9 %敌百 虫 1 0 0 0 0倍 液 , 5 %杀螟松 10 或 0 00 缩剪 23 主干顶稍也要缩剪 5 一10 m, 到主稍一定饱满侧 芽为 倍 液 。 /, O c 直 0 止。 浸水是指修建好的苗木在造林前 , 进行全株泡水 , 浸水 时间 1 2 —
热处理技术的现状与发展方向

新热处理技术的出现也给热处理行业带来了新的发展机遇。例如,真空热处理 技术可以避免氧化和脱碳等缺陷,提高工件的质量和寿命;离子注入技术可以 提高工件的耐磨性和抗腐蚀性;激光热处理技术可以获得高强度、高硬度的表 面层,提高工件的整体性能。
热处理行业发展趋势
未来,热处理行业将朝着高质量、高效益、环保可持续的方向发展。具体表现 在以下几个方面:
二、热处理技术的术也在不断创新和发展。例如,真空热处理、 激光热处理、高频热处理等新型热处理技术正在逐步推广应用,这些技术能够 更好地满足高精度、高效率、环保等方面的要求。
2、新的应用领域
热处理技术正不断拓展其应用领域。例如,在新能源领域,太阳能电池板的边 框和支架、风力发电的轴承等都需要进行热处理;在航空航天领域,飞机起落 架、航空发动机等关键部件也需要进行精密的热处理。
2、热处理技术的应用范围
热处理技术广泛应用于各种金属材料和非金属材料的加工和生产过程中,如钢 铁、有色金属、玻璃、陶瓷、塑料等。
3、当前热处理技术的优缺点
(1)优点:通过热处理技术,可以显著提高材料的硬度、耐磨性、抗疲劳性 等性能,同时也能优化材料的内部结构,提高产品的稳定性和可靠性。
(2)缺点:热处理过程容易产生环境污染,能源消耗较大,且部分工艺参数 难以精确控制,可能会导致产品质量不稳定。
我国热处理行业的现状及市场前 景
我国热处理行业经历了快速的发展,目前已经形成了较为完善的产业链和产业 聚集地。在市场需求方面,随着我国制造业的转型升级和高端装备制造产业的 快速发展,热处理市场需求持续增长。此外,汽车、航空航天、能源等领域对 高性能材料的需求也不断增加,进一步推动了热处理行业的发展。
因此,我们需要加强热处理技术的研究与开发,提高产品质量和生产效率,以 满足制造业不断发展的需求,同时也要注重环保和节能减排,推动热处理行业 的可持续发展。
制造模具节能措施方案

制造模具节能措施方案
节能是现代工业生产的重要方向,对于模具制造行业也是不可或缺的,以下是一些制造模具节能的措施方案:
1. 设计优化:在模具的设计阶段,可以通过优化结构、减少材料用量等方式来降低能耗。
例如,采用较小的模具尺寸能够减少材料和能源的消耗,同时还可以提高生产效率。
2. 材料选择:选择具有较高强度和耐磨性的材料,能够减少模具在使用过程中的能源损耗。
此外,还可以采用再生材料,如再生塑料等,以减少对原料的消耗。
3. 热处理控制:对于需要进行热处理的模具部件,合理控制加热温度和保温时间,避免过度加热和能源浪费。
4. 物料利用:在模具制造过程中,尽量减少废料的产生和损耗。
废料可以进行再利用或者回收利用,减少对新材料的需求。
5. 设备维护:定期对模具制造所用的设备进行维护,保持设备的正常运转,减少能源的消耗。
同时,还可以定期清洗设备,避免堵塞和能源浪费。
6. 人员培训:加强对模具制造人员的培训,使其具备节能意识和技能。
通过培训,能够提高工人的技术水平,降低能源的浪费和损耗。
7. 环保意识:在模具制造过程中,注重环保意识的培养,减少
污染的排放。
采用环保材料和环保工艺,对环境造成的影响最小化。
通过以上的措施,可以有效降低模具制造过程中的能源消耗,减少资源的浪费,实现模具制造行业的可持续发展。
国内外加热炉和热处理炉的现状和节能技术
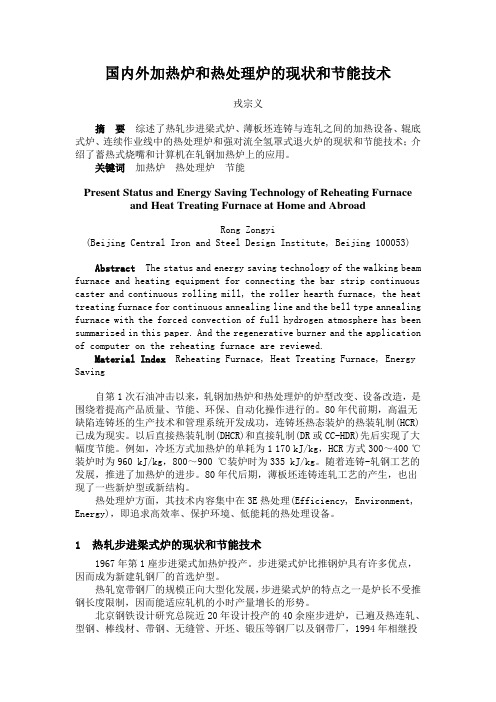
国内外加热炉和热处理炉的现状和节能技术戎宗义摘要综述了热轧步进梁式炉、薄板坯连铸与连轧之间的加热设备、辊底式炉、连续作业线中的热处理炉和强对流全氢罩式退火炉的现状和节能技术;介绍了蓄热式烧嘴和计算机在轧钢加热炉上的应用。
关键词加热炉热处理炉节能Present Status and Energy Saving Technology of Reheating Furnace and Heat Treating Furnace at Home and AbroadRong Zongyi(Beijing Central Iron and Steel Design Institute, Beijing 100053)Abstract The status and energy saving technology of the walking beam furnace and heating equipment for connecting the bar strip continuous caster and continuous rolling mill, the roller hearth furnace, the heat treating furnace for continuous annealing line and the bell type annealing furnace with the forced convection of full hydrogen atmosphere has been summarized in this paper. And the regenerative burner and the application of computer on the reheating furnace are reviewed.Material Index Reheating Furnace, Heat Treating Furnace, Energy Saving自第1次石油冲击以来,轧钢加热炉和热处理炉的炉型改变、设备改造,是围绕着提高产品质量、节能、环保、自动化操作进行的。
- 1、下载文档前请自行甄别文档内容的完整性,平台不提供额外的编辑、内容补充、找答案等附加服务。
- 2、"仅部分预览"的文档,不可在线预览部分如存在完整性等问题,可反馈申请退款(可完整预览的文档不适用该条件!)。
- 3、如文档侵犯您的权益,请联系客服反馈,我们会尽快为您处理(人工客服工作时间:9:00-18:30)。
毛坯热处理节能技术
资料来源:一览钢铁英才网
汽车结构件大多采用锻造成型工艺。
汽车锻件分热锻、温锻和冷锻,涉及零件品种多,批量大,毛坯的热处理能耗巨大。
为了大幅降低锻件毛坯的热处理能耗,目前以及未来采取的主要措施有以下几种。
非调质钢的应用
与调质钢比较,非调质钢的主要优点:①锻件无须调质处理,是典型的资源节约型结构材料。
②不存在因淬火产生的变形、开裂等工序质量问题,省去了后续校直、探伤等工序。
③在零件的横截面上可得到均匀一致的组织和性能,而调质钢由于受材料淬透性的影响,零件的表面和心部往往存在较大的组织和硬度差异。
国内非调质钢主要用于发动机曲轴、连杆、前轴、转向节等零件。
非调质钢的应用,可以使生产此类零件的热处理能耗降低70%~80%。
从节能、环保的角度讲,微合金化非调质钢的应用将是汽车用结构钢的发展方向之一。
目前制约非调质钢进一步推广应用的主要障碍是材料价格。
国内许多特钢厂将非调质钢作为高端产品,使非调质钢的直接用户享受不到节能带来的经济效益。
随着更高强韧性非调质钢的开发以及非调质钢的不断推广普及,汽车动力传动系统的大部分零件可以用非调质生产制造,节能效果将更加显著。
免退火冷镦钢的应用
汽车标准件采用冷镦成型。
免退火冷镦钢通过化学成分的调整,控轧、控冷,细化晶粒并使珠光体变态,降低轧制态的硬度,提高其塑性变形能力,减小变形抗力。
免退火冷镦钢的应用,省略了冷拔前的退火工艺,降低了生产成本。
目前,免退火冷镦钢可用于生产818级汽车紧固件类零件。
随着冶金技术的发展,免退火冷镦钢有可能应用于更高强度的紧固件生产中。
锻造余热热处理的应用
锻造余热热处理有余热等温退火和余热淬火。
对大批量生产的汽车零件,锻压机后接余热热处理生产线,可以方便地实施在线余热等温退火或余热淬火。
为了保证锻造余热热处理质量,需要严格控制锻件的始锻和终锻温度及终冷过程控制。
对重要零件也有采用终冷到临界温度以下发生中间相组织转变,然后再加热到奥氏体进行淬火的工艺方法,以此细化组织得到强韧性更好的毛坯件。
在生产中采用锻造余热热处理能够使毛坯热处理能耗降低50%~70%。