详解丰田精益生产管理模式共35页PPT资料
合集下载
精益生产(丰田管理模式TPS)培训资料
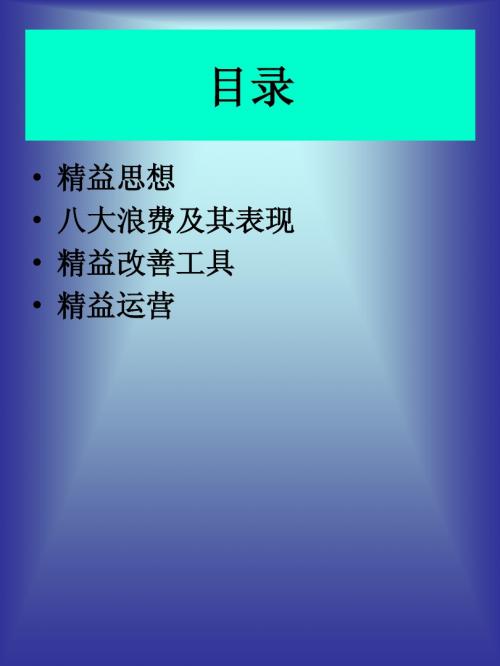
丰田生产方式的演进
全世界学习丰生 产方式
全世界学习丰生 产方式源自精益思想什么是“精益”?
• Lean Production • ——“Lean”是由瘦肉组成的肌肉(没有肥 肉)。
精益思想 --可以好似目标朝着剔除浪费(肥 肉)以承载整个系统的良性运营
精益思想
奉献顾客物美价廉产品 --价格、品质、交货期,符合变化的需求
■ 创造价值的过程 √设计满足市场 √按订单生产 √优质服务 ■没有浪费的过程
目录
• • • • 精益思想 八大浪费及其表现 精益改善工具 精益运营
精益思想
• • • • • • • • • • • • 1什么是“精益” 2精益思想 3精益思想的来源——IMVP 4精益着眼点 5精益思想的五大原则 6基于制造现场的浪费 7精益运营的八大浪费 8八大浪费的原因 9精益模式的核心(L/T) 10识别价值流及其目的 11精益生产的目标 12精益流
丰田管理模式ppt课件

2
不降低成本就无法提高利润
成本中心型
• 以计算或实际的成本为中心,加
上预先设定好的利润而得出售价,
• 其公式为: 售价 = 成本+利润 • 在供应< 销量时,在垄断产品时
可以如此定价
2019
-
3
售价中心型
• 在供应>销量时,以售价为中心,
当市场售价降低时利润随之减少,
其公式为: 本
利润 = 售价- 成
3.标准在制品,是指各工序规定数量、放置地点 和位置与器具
2019
-
20
标准作业的制定方法
工序号
1 2 3 4 5 6 7 8 9 10 11 12
工序内容
车平面 车内孔 镗6~Φ12孔 铣槽3 铣槽5 精镗3~Φ16孔 精镗6~Φ12孔 去毛剌
清洗 检验 包装
标准作业组合表
时间 手动 机动 2 4 6 8 10 12 14 16 18
11
典型的工序看板
前工序 部件1-3线 出口位置
POS.12-2
部件号A232-605C 箱号:003
箱内数量:100 看板编号:2/5
使用工序 总装1-3 入口位置
POS.12-8
2019
-
12
均衡化同步同节拍生产
• 同步化节拍生产是按照生产工艺规定和
物流顺序确定生产提前期条件下和产品
总装配线保持同步地进行生产
快调工装
质量保证和 过程控制
标准作业
多工序操作
目视管理 设备TPM管理
自动化 省人化
自主、无止境改善
2019
-
9
实现精益生产重要手段
-拉动式看板管理
后道工序向前道工序领取工件,前道只生 产被领取那部分工件,实现适时、适量、 适产品的生产
详解丰田精益生产管理模式

单击此处输入你的正文,请阐述观点
供应链管理:需要与供应商建立紧密的合作关系,确保原材料的供应和质量
单击此处输入你的正文,请阐述观点
面临的挑战与应对策略
挑战:市场竞争激烈,需要不断提高产品质量和降低成本
应对策略:采用精益生产管理模式,通过消除浪费、提高生产效率和产品质量来降低成本
挑战:员工素质参差不齐,需要提高员工的技能和素质
持续改进:不断改进生产过程,提高产品质量和生产效率
拉动原则:通过客户需求拉动生产,实现准时化生产
消除浪费:通过消除生产过程中的浪费,提高生产效率和降低成本
减少浪费
减少动作浪费:通过改进工作流程和操作方法,减少不必要的动作和浪费时间
减少等待浪费:通过合理安排生产计划和流程,减少等待时间和空闲时间
减少不良浪费:通过提高产品质量和减少缺陷,降低不良率,减少浪费
04
价值流分析
识别产品或服务流程中的浪费
确定价值流中的关键过程和活动
制定改进计划并实施
持续改进并优化价值流
制定生产计划与目标
确定生产计划:根据市场需求和产能规划,制定合理的生产计划
设定生产目标:明确生产目标,包括产量、质量、成本等方面的要求
制定生产计划表:将生产计划细化为具体的生产计划表,包括生产时间、生产数量、生产批次等方面的信息
丰田生产方式(TPS)的诞生
精益生产管理模式的形成与发展
发展历程
起源:二战后日本汽车工业的崛起
1950年代:丰田生产方式的初步形成
1960年代:精益生产概念的提出
1970年代至今:精益生产管理模式的不断完善与创新
精益生产管理模式的核心理念
消除浪费:通过消除生产过程中的浪费,提高生产效率和产品质量
供应链管理:需要与供应商建立紧密的合作关系,确保原材料的供应和质量
单击此处输入你的正文,请阐述观点
面临的挑战与应对策略
挑战:市场竞争激烈,需要不断提高产品质量和降低成本
应对策略:采用精益生产管理模式,通过消除浪费、提高生产效率和产品质量来降低成本
挑战:员工素质参差不齐,需要提高员工的技能和素质
持续改进:不断改进生产过程,提高产品质量和生产效率
拉动原则:通过客户需求拉动生产,实现准时化生产
消除浪费:通过消除生产过程中的浪费,提高生产效率和降低成本
减少浪费
减少动作浪费:通过改进工作流程和操作方法,减少不必要的动作和浪费时间
减少等待浪费:通过合理安排生产计划和流程,减少等待时间和空闲时间
减少不良浪费:通过提高产品质量和减少缺陷,降低不良率,减少浪费
04
价值流分析
识别产品或服务流程中的浪费
确定价值流中的关键过程和活动
制定改进计划并实施
持续改进并优化价值流
制定生产计划与目标
确定生产计划:根据市场需求和产能规划,制定合理的生产计划
设定生产目标:明确生产目标,包括产量、质量、成本等方面的要求
制定生产计划表:将生产计划细化为具体的生产计划表,包括生产时间、生产数量、生产批次等方面的信息
丰田生产方式(TPS)的诞生
精益生产管理模式的形成与发展
发展历程
起源:二战后日本汽车工业的崛起
1950年代:丰田生产方式的初步形成
1960年代:精益生产概念的提出
1970年代至今:精益生产管理模式的不断完善与创新
精益生产管理模式的核心理念
消除浪费:通过消除生产过程中的浪费,提高生产效率和产品质量
详细讲解丰田精益生产管理模式

(条件)
平准化生产
节拍时间
后工程引取
TTMC
单击此处添加大标题内容
单击此处添加正文,文字是您思想的提炼,为了演示发布的良好效果,请言简意赅地阐述您的观点。您的内容已经简明扼要,字字珠玑,但信息却千丝万缕、错综复杂,需要用更多的文字来表述;但请您尽可能提炼思想的精髓,否则容易造成观者的阅读压力,适得其反。正如我们都希望改变世界,希望给别人带去光明,但更多时候我们只需要播下一颗种子,自然有微风吹拂,雨露滋养。恰如其分地表达观点,往往事半功倍。当您的内容到达这个限度时,或许已经不纯粹作用于演示,极大可能运用于阅读领域;无论是传播观点、知识分享还是汇报工作,内容的详尽固然重要,但请一定注意信息框架的清晰,这样才能使内容层次分明,页面简洁易读。如果您的内容确实非常重要又难以精简,也请使用分段处理,对内容进行简单的梳理和提炼,这样会使逻辑框架相对清晰。为了能让您有更直观的字数感受,并进一步方便使用,我们设置了文本的最大限度,当您输入的文字到这里时,已濒临页面容纳内容的上限,若还有更多内容,请酌情缩小字号,但我们不建议您的文本字号小于14磅,请您务必注意。单击此处添加正文,文字是您思想的提炼,为了演示发布的良好效果,请言简意赅地阐述您的观点。您的内容已经简明扼要,字字珠玑,但信息却千丝万缕、错综复杂,需要用更多的文字来表述;但请您尽可能提炼思想的精髓,否则容易造成观者的阅读压力,适得其反。正如我们都希望改变世界,希望给别人带去光明,但更多时候我们只需要播下一颗种子,自然有微风吹拂,雨露滋养。恰如其分地表达观点,往往事半功倍。当您的内容到达这个限度时,或许已经不纯粹作用于演示,极大可能运用于阅读领域;无论是传播观点、知识分享还是汇报工作,内容的详尽固然重要,但请一定注意信息框架的清晰,这样才能使内容层次分明,页面简洁易读。如果您的内容确实非常重要又难以精简,也请使用分段处理,对内容进行简单的梳理和提炼,这样会使逻辑框架相对清晰。为了能让您有更直观的字数感受,并进一步方便使用,我们设置了文本的最大限度,当您输入的文字到这里时,已濒临页面容纳内容的上限,若还有更多内容,请酌情缩小字号,但我们不建议您的文本字号小于14磅,请您务必注意。单击此处添加正文,
丰田精益管理模式PPT课件

發展員工與事業伙 伴為組織創造價值
6.使工作標準化,以達到持續改進 7.運用視覺管理使問題無處隱藏 8.只使用可靠的﹑經過充分測試的技術以協助員工及生產流程 9.把徹底瞭解且拥護公司理念的員工培養成為領導者,使他們能教導其他員工 10.培養與發展信奉公司理念的傑出人才與團隊
11.重視事業伙伴與供應商網絡,激勵並助其改進
馬自達 33.4% 股分
FORD
7.現金RMB2000億元(2008年
五十鈴.
財務虧損RMB254億元(金融風 暴)
富士重 工.鈴
GM
8.每年執行一百萬個提案改善
木
9.增值比20%(一般企業0.005%)
資金占用及成本1:5(中國)
三菱
克萊斯勒
10.工廠分布26個國家,52家工廠
2(2000034年年1)8萬員工提案改善237萬
日本汽車工業超過美國﹐年產量1300萬輛﹐在美國市場占有率一路提 升至30% 丹尼爾魯斯出版(改變世界的機器)豐田生產方式定名為精益生產備受製 造業的關注與推廣
萊克著作(豐田模式)4P14項管理原則
优质 2019/11/8
15
4P 長期理念
正確的流程方能產 生優異成果
管理原則 1.管理決策以長期理念為基礎,既使因此犧牲短期財務目標也在所不惜 2.建立無間斷的操作流程以使問題浮現 3.實施拉式生產制度以避免生產過剩 4.使各製造流程工作負荷水準穩定(生產均衡化) 5.一出現品質問題,就停止生產(自働化)
標
產 業 領 導 目
標
員工滿意﹑股東滿 意﹑董事會滿意
財力.資金
四.正確的策略規劃
指 引
選 擇
差 異 化
競 爭 利
基
丰田精益生产PPT

分销渠道
✓现场决不是狭义意义上的“车间”! ✓现场管理的内涵:制造型企业全部门、全过程管理 ✓现场管理常常被忽略,而过度注重研发、营销、财务 ✓分清企业中的2种人:赚钱的人、花钱的人
客户
管理哲学: “执行”→→“实现”的学问
生产运作管理的误区:功利主义
✓ 体系论:ISO体系、精益生产JIT体系、、、 ✓ 工具论:TQM、TPM、6sigma、SPC、、、、
生命进化的法则——适者生存
龙
世
❖庞大的身躯—能量负担
界
❖低下的神经系统—信息反馈迟钝
的 悲
❖不适应多变的自然环境
哀
:
灭亡
当代海洋霸主、陆地霸主的 生存之道?
企 企业的生命同样遵循这个法则———
业
适应市场环境者生存
的
生
要求:完善的管理体制、快速的市场反 应机制、供应链的协同作战
命
三种经营策略
企业使命及其实践
与
X O 机修工
全员预防保全
理解持续改进对理解日本人和西方人在管 理方法上的差异是非常重要的。
日本的持续改进是过程导向思维方式,而 西方人是创新和结果导向思维方式,创新和持 续改进都是一个企业生存和发展所必需的。
✓不一味追求“突破性”创新(科技突破、管理突破、 最新生产技术)
✓注重“渐变式”“细节性”改进,达到从量变到质 变的飞跃
ムラ:不平衡、不均匀
2023/5/10
等待浪费
搬运浪费
工 8 不良浪费
厂 大 动作浪费
浪 常
见
加工浪费
的 费 库存浪费
地下工厂
企业每生产一件产品就在制 造一份浪费。伴随企业运营中各 业务环节不被察觉或不被重视的 浪费,日本企业管理界将之形象 地比喻为“地下工厂”。
丰田方式精益生产 ppt课件
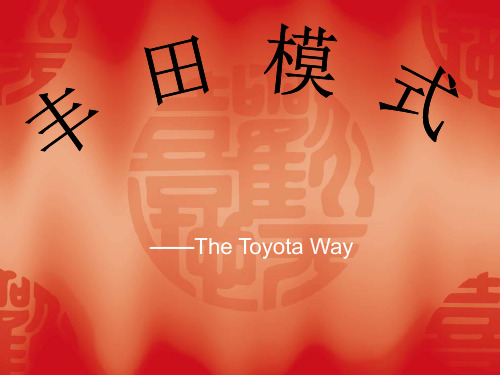
全向沟通
LT(Learning Team)活动流程图
现状调查
确定目标
分析原因
分头调研 集中汇总
总结反思
互查互纠 集中通报
各抒己见 多方论证
沟通交流 辩论趋同
安排对策
各施己长 各负其责
固化巩固
监测评估
实施对策
5W
大野耐一问:“5个为什么”的事情:
问:“机器为什么停了?” 答:“机器超负荷,保险丝断了。” 问:“为什么会超负荷?” 答:“因为轴承润滑不充分。” 问:“为什么没充分地润滑呢?” 答:“因为润滑泵供油不足。” 问:“为什么会供油不足?” 答:“因为泵轴磨损已经摇晃了。” 问:“为什么会磨损了呢?” 答:“因为没加过滤器进去了粉屑。”
丰田的企业文化
丰 田 宪 法
追求创新
丰田企业文化
愈战愈勇
关 注 人 性
一、追求创新
改进福特的
福特的“大
生产体制
规模生产模式”
不适用于日本 设计制度,
鼓励员工创新
JIT生产模 式
如今,备受瞩目的“流程再造”,本质上就是本着“精益生产模式”重塑企业组 织结构,可以说“JIT生产方式”相对于“大规模生产模式”是原创性和革命性的 创新。
了解情况
真正的问题
3.找出问题所在区 域/找出原因点
调查原因
为什么?
为什么? 为什么?
为什么? 为什么?
找出原 因点 (POC) 直接原因 原因 原因 原因 原因
根本原因
基本因果调查
4 .5个为什么? 调查根本原因
5.对 策
6.评估对策成效
7.把新流程方法标准化
四、活用“看板”
看板,是一种传递信号的载体,指各现场的 负责人将各自的作业内容写在现成的纸张等 上面,挂在工作场地,使每一个作业者都能 一目了然。
丰田公司精益生产管理

提高质量 环境保护
产品开发流程
市场 策划
开发周期 L/T ↓
直材成本↓
开发
生产周期 L/T ↓
设计 准备
制造成本↓ 生产效率↑
客户 订单执行流程
销售
计划
采购
生产 审查
物流
客户
市场
5、生产运作管理的目标
J I T ust n ime
适品 ·适量 ·适时
流线化生产
逐步消除库存 逐步根绝浪费
利润最大化
PPT模板下载:.1ppt/moban/ 行业PPT模板:.1ppt/hangye/
节日PPT模板:.1ppt/jieri/
PPT素材下载:.1ppt/sucai/
PPT背景图片:.1ppt/beijing/ PPT图表下载:.1ppt/tubiao/
优秀PPT下载:.1ppt/xiazai/
PPT教程: .1ppt/powerpoint/
○ 均衡化生产(平稳、有序) ○ 准时化
· 拉动式生产 Pull · 单件流 one piece flow · 节拍时间 Taket time
○ 自动化
· 自动防错(愚巧化,防呆法)Pokayoke · 自动化 Jidoka
准时化
流线化生产过程中,所需要的零件在需要 的时刻、以所需要的数量不多不少地送到生 产线,从根本上解决库存在物资和财务上给经 营管理造成的负担.
市场 品牌 市场 需求 效应 竞争
经营 特质
模式 构建
精英 团队
企业文化
从10个亿到1000个亿,通过兼并收购和新建扩 建可以做到,关键是:
· 有好的模式可以快速复制 · 有精英团队支撑快速扩张
9、好的模式必须构建三大竞争优势
精益生产学习资料丰田公司PPT课件
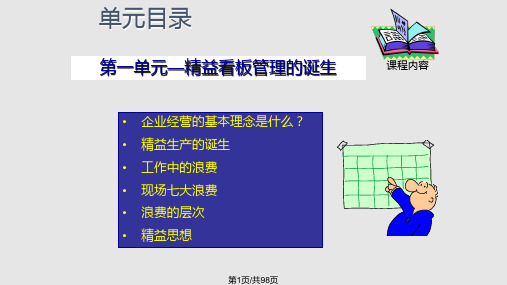
不符合精 益生产的 一切物料 搬运活动
第14页/共98页
4、现场的七大浪费
4、作业本身
对最终产品或服务 不增加价值的过程
第15页/共98页
4、现场的七大浪费
5、动作的浪费
任何不增加产品或服务价值的 人员 和 设备的动作
第16页/共98页
4、现场的七大浪费
6、等待的浪费
当两个关联要素间 未能完全同步时 所产生的空闲时间
现场七大浪费
浪费
• 过量生产 • 库存 • 搬运 • 作业本身 • 等待 • 多余动作 • 不良
第9页/共98页
4、现场的七大浪费
1、过量生 产
•生产多于下游客户所需 Making More Than Needed •生产快于下游客户所求 Making Faster Than Needed
第10页/共98页
按照当天品种的 循环时间生产
通过看板方式进行对前工序每天 的生产指示
决定个品种的月生产计划
决定混流装配线的产品顺序计划
月份需求预测
来自销售商的日订货
第38页/共98页
6、以均衡化适应市场的多样化 生产计划
第39页/共98页
6、以均衡化适应市场的多样化
星期一的生产 星期二的生产 星期三的生产 星期四的生产
• 限制作业不良影响他人的限制位置 • 防止不合格加工的动作防止 • 防止装配漏件的监控装置 • 快速处理问题的系统
第34页/共98页
5、自働化
快速处理问题
目标 生产线安定 解决问题防止再发 管理者的行动 警示灯显示停线情况 发掘问题
第35页/共98页
5、自働化
应用5-WHY快速寻找原因
当场采取应急措施 追查原因时应连续问5个为什么, 直到找到最直接的根本原因。
第14页/共98页
4、现场的七大浪费
4、作业本身
对最终产品或服务 不增加价值的过程
第15页/共98页
4、现场的七大浪费
5、动作的浪费
任何不增加产品或服务价值的 人员 和 设备的动作
第16页/共98页
4、现场的七大浪费
6、等待的浪费
当两个关联要素间 未能完全同步时 所产生的空闲时间
现场七大浪费
浪费
• 过量生产 • 库存 • 搬运 • 作业本身 • 等待 • 多余动作 • 不良
第9页/共98页
4、现场的七大浪费
1、过量生 产
•生产多于下游客户所需 Making More Than Needed •生产快于下游客户所求 Making Faster Than Needed
第10页/共98页
按照当天品种的 循环时间生产
通过看板方式进行对前工序每天 的生产指示
决定个品种的月生产计划
决定混流装配线的产品顺序计划
月份需求预测
来自销售商的日订货
第38页/共98页
6、以均衡化适应市场的多样化 生产计划
第39页/共98页
6、以均衡化适应市场的多样化
星期一的生产 星期二的生产 星期三的生产 星期四的生产
• 限制作业不良影响他人的限制位置 • 防止不合格加工的动作防止 • 防止装配漏件的监控装置 • 快速处理问题的系统
第34页/共98页
5、自働化
快速处理问题
目标 生产线安定 解决问题防止再发 管理者的行动 警示灯显示停线情况 发掘问题
第35页/共98页
5、自働化
应用5-WHY快速寻找原因
当场采取应急措施 追查原因时应连续问5个为什么, 直到找到最直接的根本原因。
相关主题
- 1、下载文档前请自行甄别文档内容的完整性,平台不提供额外的编辑、内容补充、找答案等附加服务。
- 2、"仅部分预览"的文档,不可在线预览部分如存在完整性等问题,可反馈申请退款(可完整预览的文档不适用该条件!)。
- 3、如文档侵犯您的权益,请联系客服反馈,我们会尽快为您处理(人工客服工作时间:9:00-18:30)。
5. 标准作业
TTMC
5-1 标准作业
以人的活动为中心,把各阶段的 最有效的做法(安全、品质、生产 性)作为全员必须遵守的规则予以 确定、表现的方式。
5-2 标准作业的目标
TTMC
1. 通过排除了无效动作的有效率 的劳动实现较高的生产率。
2. 实现与适时生产有关的各工序 间的同步化(生产线的平衡)。
利息费
磨损
利息费
TTMC
第4层浪费
※扩大库容 ※增加搬运工 ※增加设备 ※增加库管人员
··· ·····
购置费、折旧 费、间接劳务
费、管理费
产品成本的增加
3. 准时化生产的重要性
TTMC
3-1 准时化
在必要的时候
(条件)
生产必要数量的 必要的产品
①平准化生产 ②节拍时间
③后工程引取
3-2 平准化生产
没有附加价值的作业
※在现有的作业条件下,没有附加 价值,却必须要作的动作。
(步行、取部品等)
有附加价值的作业
※根据不同的作业内容给产品带来 附加价值的动作。
2-2 浪费的种类
·生产过剩的浪费
·等待的浪费 ·搬运的浪费 ·加工过程本身的浪费 ·库存的浪费 ·动作的浪费 ·制造不良的浪费
TTMC
浪费
TTMC
2-3 生产过剩的浪费是最大的浪费
多了、 快了反 而不好
包含2层含义:
· 在规定的时间内多生 产 · 提前生产出来
2-4 生产过剩浪费的危害
第1层浪费
生产能力过剩
※多余的人 ※多余的设备 ※多余的库存
第2层浪费
生产过剩
※工作进展 过度
第3层浪费
库存过剩
※在生产线后 面和中间堆积
库存
劳务费、折旧费、 机时、工时、
将生产的物品的种类与数量进行平均化
TTMC
量的平均化
数
偏差大
量
最大値
最小値
种类的平均化
CCB B A A
偏差小 CB A CB A
没有进行平准化生产的问题点
TTMC
70 70 70 70
归纳每个部品进行流动
60 60 60 60
秒
50 50 50 50
CC CC A A A A B B B B
问题点
目
录
1. 什么是TPS
2. 必须根除浪费
3. JUST IN TIME 的重要性
4. 4. 自働化
5. 标准作业
6. 看板的使用
7. 改善
TTMC
1.什么是TPS
1-1TPS的起源
丰田佐吉 丰田喜一郎 大野耐一
TTMC
1-2 丰田生产方式(TPS)是指
oyota
TTMC
roduction
ystem
①只作A工序,只是A的部品成为必要,在此期间,BC的部品搁置。
②因制作产品的不同与作业时间的不同会产生人员的增减。
70
70
70
70 平准化流程
60
60
60
60
秒
50
50
50
50
C AB C AB C AB C AB
3-3 节拍时间
TTMC
一日的负荷时间 节拍时间=
1日的生产必要数(个or台)
将1个部品或1台的量在多长的时间内进行生产的时间值 (负荷时间:定时(没有加班) 可动率:按100%计算)
生产线
TR-12
TTMC
③工程间引取看板
工程间的部品引取
TTMC
(かんばん例)
前工程
成形 511
工程间引取 品番 90153-11020 品名 502N前门保险缸 色 3P1 収容数 1
后工程
总装 221
④外注部品引取看板
目的:外注部品的引取
TTMC
(かんばん例)
所番地
703 0-1
K-2-1-7
3. 3. 把在制品的“标准持有量” 限定在必要的最小数量。
5-3 标准作业3要素 节拍时间 标准作业顺序
TTMC
标准手持
用最小限度的作业人员和在制品进行的所 有工序之间的同步生产
标准作业
节拍时间
标准作业顺序
标准手持
6. かんばん 看板
6-1 かんばん(看板)的起源
TTMC
6-2 看板 的作用
1-3 TPS的目的
TTMC
追求物品制造的合理性, 彻底排除浪费,达到降低成 本的目的。
1-4 TPS的两大支柱思想
TTMC
◇准时化生产 (JUST IN TIME)
◇自働化
2.必须根除浪费
2-1 什么是浪费
有附加价值 的作业
浪费
作业者的 动作
无附加价不必要的动作。 (等待、手修等)
前工程
成形 511
工程内かんばん 品番 90153-11020 品名 502N 前门保险缸 色 3P1 収容数 1
后工程
总装 221
②信号かんばん看板
目的:工程内的制造途中
(象冲压等的有计划变更的批量生产工程)
(かんばん例)
53311-12570
基准数
5
仓库 加工数
22-A-66
材料 500
BL-8
引取看板信箱
②
FED
① 组装生产线
ABC ④
工程间看板
③
信箱
⑤
A
B
ABC加工生产线
原 料
C
完成品
D
E
DEF加工生产线
原 料
F
TTMC
③取下部品的工程内看板,防入工程内看板信箱内,将取回的引 取看板插在部品箱旁边。
引取看板信箱
②
FED
① 组装生产线
ABC ④
工程间看板
③
信箱
⑤
A
B
ABC加工生产线
原 料
①生产搬运的指示和作业的信息。 ②“目视管理”的工具 过分制造的抑制
工序快慢进度的检知 ③工序改善的工具
6-3 看板的种类
(1)仕掛看板 ①工程内看板 ②信号看板
(2)引取看板 ③工程間引取看板 ④外注部品引取看板
TTMC
①工程内看板
目的:工程内的制造途中
(生产线作业的工序)
TTMC
(かんばん例)
トヨタ自動車株式会社
アイシン高岡
90153-11020
S5 収容数
326
6-4.看板的流程和规则
TTMC
①在拿取部品的第一个部品或达到规定的部品量时取下看板
引取看板信箱 ②
FED
① 组装生产线
ABC ④
工程间看板
③
信箱
⑤
A
B
ABC加工生产线
原 料
C
完成品
D
E DEF加工生产线
原 料
F
TTMC
②一定量(一定时间)将看板取下,搬运担当者拿取下的看板去 前一个工序取部品
C
完成品
D
E
DEF加工生产线
原 料
F
领回かんばん
部品箱
工程内かんばん㌃
TTMC
④搬运到组装生产线的部品箱,要带着看板一同放在组装部品的放 置场所(绝对不许搬运没有看板的部品)
引取看板信箱
②
FED
① 组装生产线
ABC ④
例题
※ 1日的生产必要台数为200台,负荷时间为8小时 (460分钟),此时的节拍时间是多少?
4. 自働化
TTMC
自动化
·目的是对手工作业进行转换 ·即使发生异常,机械也在运转并且生产出不良品
自働化
· 加工品及机械发生异常时自动停止、
不制造不良品=代替了人
(自働化所追求的)
①用很快的速度生产出优良品 ②防止设备故障 ③省人化(不需要看着设备)