精益生产系统培训教材
精益生产培训教材

21/52
四、多技能工训练,提升员工技能
22/52
五、通过防呆技术,降低员工劳动复杂性
1、常见的防呆构造
不需要注意力,即使有人 因为疏忽也不会发生错误 的构造。
不需要经验与直觉, 即使是外行人来做也 不会做错的构造。 • 例如: 电脑的接线插头。
不需要专门知识与高度的技 能,不管是谁或在任何时候 工作都不会出现差错的构造。 • 例如: 模具自动夹紧装置,一 个按键就能完成模具的 自动夹紧。
6/52
五、精益的基本思想:人性尊重
创造出以产品制造为核心的附加值
挑战
长期志向
沉思熟虑和决断
智慧与改善
改善
建立起简朴而紧凑的系统
有组织地进行彻底的学习 实践主义、完成任务的志向
现地实物
改善 尊重人性 现地实物
尊重利益享有者 公司与职员的相互信任的相互负责 尊重个人人性的发辉团队的缩合力量
12/52
八、组织工作时间
维护与改进
改进:活动对提高现行标准
在“精益”组织工作
事情 如何 变得 更好: 宏和大型流程改进 工艺改进
• 高管理
• 高管理
• 中层管理
• 中层管理
•监事
•监事
•运营商
•运营商
0
25
50
75
100
0
25
50
75
100
%的总工作时间
13/52
%的总工作时间
第二部分:工具篇
当重要责任。
11/52
七、精益倡导模式
自我实现需求
1
人是公司最重要的资源,培养善于观察和思考的员工
2
把从事改善的积极性,作为选拔人才的一项重要考核指标
精益生产培训教材((000002)

16
业绩对比
项目
地区
生产率(辆/人/年)
质量(缺陷/100辆车)
场地(平方英尺/车/年
库存(8个样件,天)
团队(占劳动力%)
工种轮换(0-无 4-高 )
建议数/年/雇员
缺勤率
自动化(组装)
日本
55 60 5.7 0.2 69 3.0
61.6 5.0 1.7
北美
6 82 7.8 2.9 17 0.9
• Ongoing efforts to improve Quality, Productivity, and Responsiveness
• Recognition of employee abilities
• 消除浪费 • 不断改进 • 员工参与
• Builds on synchronous manufacturing
Starting with Toyota in the late 50’s and
catching on in the mid – 80’s in the reminder of the industrial world, Lean Manufacturing has become a key strategy for manufacturers
交货期的保障
2020/1/11
21
生产管理的任务
Quality 质量
Cost 成本
ivery 交货
2020/1/11
22
生产管理者的职责
• 组长:质量及不合格品的注意;生产线 停线的责任
• 领班:生产力改进;成本降低 • 主管:生产控制,作业标准,质量控制,
福特首创的装配线是大规模低品种生产方式的代表, 工人被当成工作的机器
精益生产培训系列教材

出料
入料
12
LB生产线平衡
生产线平衡的意义:
➢ 缩短产品装配时间,增加单位时间的产量,降低生产成本; ➢ 减少工序间的在制品,减少场地的占用; ➢ 减少工序之间的准备时间,缩短生产周期; ➢ 消除员工等待现象,提升员工士气; ➢ 改变传统小批量作业模式,使其达到一个流生产; ➢ 可以稳定和提升产品质量; ➢ 提升工厂整体生产效率和降低现场的各种浪 费现象。
的指标。
平衡率=
∑(各工序的作业时间) 瓶颈工序时间*人数 * 100%
30 25 20 15 10 5 0
产线平衡图
10 15 18 30
20 15 12
A B CD
平衡率 =【(20+15+30+12)/30*4】*100% = 64%
平衡损失 = 1 - 平衡率 = 36%
对生产线来说,平衡损失越小越好,一般控制 5%-13%之间,至少要控制在15%以内。
答:节拍时间=有效出勤时间/[生产计划量X(1+不良率)] =480X2X20/[19200X(1+0%)] =60秒/个
14
LB生产线平衡
常用术语介绍:传送带速度(CV)
传送带速度,是指流水线的皮带传递速度,一般情况下,采用一定的距离作好标 记,然后测定其时间,进而得出流水线传送带的实际速度,
计算公式:CV = 间隔标记距离 / 所耗时间 采用流水线作业的企业,传送带的速度关系着作业效率、疲劳程度以及产量。 理想的传送带速度,是恰好能完成预定产量的同时又能减少员工的身心疲劳。
34
LB生产线平衡
基本原则和方法:平衡手法
工时测量流程: 选定测量工序
选定工序,阅读SOP和观察作业人员操作,了解该工序 的全部操作内容,并询问作业人员加以确认;
精益生产培训教材(PPT 70页)
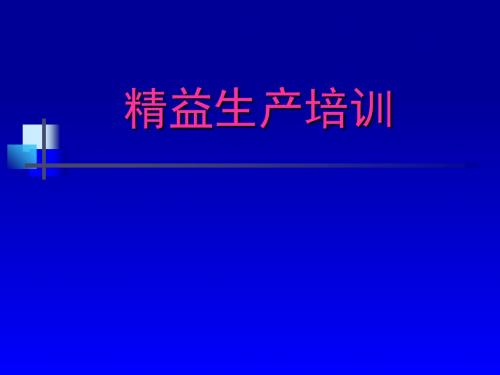
第三部分:精益生产之方式要求 3.2 单件流
第三部分:精益生产之方式要求 3.3 拉动式
何谓“拉动式生产”? 生产活动是由“客户”需求决定的,在进行生产
时,每一个生产过程都是由下一个生产过程的需求决 定,从而不生产额外的产品,这样就可以消除因生产 过剩产生的多余库存了。 为何需要“拉动式生产”? —没有需求的生产是没有意义的; —拉动使生产有了方向性; —通过一级一级的拉动可以使流程有序平稳地进行, 避免了浪费。
以顾客为导向的效率:
提高产量的做法:
改善
400pcs/4人·8hr
600pcs/5人·8hr
做客户需求的产量:
改善
400pcs/4人·8hr
360pcs/3人·8hr
以最少的人员,做出市场实际需求量的产品才是以顾 客为导向的真正的效率提升。
一、精益管理的诞生
课程内容
精益与其说是一种生产方式,更确切
Time ”,简称“JIT”。
“JIT”的概念
JIT是英文“Just In Time”的缩写,翻译成中 文为准时(及时)生产,即通常所讲的使生产做到 “在需要的时候,按需要数量生产所需要的产品”。
其主要目的是使生产过程不要处于盲目状态,而 是建立一种均匀、稳定的、有节奏的生产线。
丰田公司通过多年不断改善,建立了JIT的生产模 式:
一项很细小专一的工作 大批量:每分钟一辆,每天7000辆 价格低:像自来水一样便宜
1.3 精益生产方式
追求零浪费!!
只在适当的时
间里生产市场需 精 要的必要数量的 益
产品
所有的经营活动 都要有效益和 最大的经济性
精益生产的特点:
消除一切浪费,追求精益求精和不断改善。精 简并消除一切不增值的岗位。精简产品开发设 计,生产,管理中一切不产生附加值的工作, 以最优品质,最低成本和最高效率对市场需求 作出最迅速的响应。
精益生产(TPS)培训教材

丰田生产管理方式第一次授课§1—1.企业经营与成本:利润=售价—成本为了提高利润:(1)提高售价 (售价由市場規律决定,提高售价就会卖不出去)「售价=成本+利润」⇒成本主义是行不通的(2)降低成本(成本的三要素:经费、劳务费、材料费)利润=售价—成本(3) 企业不断降低成本的方法彻底的消除浪費,从而降低成本,提高利润。
§1-2.物品製造和成本:* 成本的3要素:材料费、劳务费、管理费*分析成本才能发现哪些是不必要的成本:1.生产出的不良品2.过多的库存3.设备在等待4.不必要的物流5.不必要的作业6.员工在等待等等……*降低成本的方法:①排除浪费②降低原材料采购的价格③降低费用的开支④提高效率⑤缩短生产周期⑥排除人的浪费§ 1-3.什么是丰田生产方式:何谓丰田生产方式:丰田生产方式就是以彻底排除浪费为目标,致力于降低成本,如何做的便宜等一切车间的实践活动的统称。
它是从大批量的生产方式转变为JUST IN TIME(将必要的东西,仅仅是必要的量,在必要的时候进行生产)的生产方式.在最短的生产期间内,挑战由于自动化而实现省人化,到设备的最适化所采用的手法的总称。
§ 1-4.什么是丰田生产方式:丰田生产方式的两大支柱:(1)丰田佐吉翁的带“イ”旁的自动化即:问题显在化的看得見管理+自动化,不是单纯的把人的工作交给机器去做,而是能自动检测不良,发现不良时能自动停止,不向下工程提供不良品.(2)丰田喜一郎的“Just in time”即:“必要的物品、在必要的時候、按必要的量生産”。
* 由大野耐一汇集成“丰田生产方式”§ 1—5.丰田生产方式的目的:1、丰田生产方式的目的:彻底消除浪费为目标,致力于降低成本。
具体地説是追求以下四項為零:①Lead time為0 ―→缩短加工周期(加工时间+停滞时间=工場内的加工周期)②工数的浪费為0―→进行动作和作业的改善③设备的浪费為0―→设备减少+小型化+最适合化④品质的浪费為0―→加工时进行检查,发现不良立即停止例: <加工周期〉加工时间:停滞时间丰田 1 : 300优良企业 1 : 5000亏损企业 1 : 100002、培养发现浪费的眼睛:*发现浪费的第一步就是到现场!!!§ 2-1.车间改善的必要性:§ 2-2.车间的浪费:1、浪费的定义:不能产生利润的行为.首先最重要的是要认识浪费:增加成本的各个要素“一旦认为是浪费,就立刻废除"这种姿态对于在职场里工作的我们来说非常重要*怎样排除动作的浪费:1.明确取放顺序2.明确是左手还是右手拿取方便3.物品不要放得过远4.工具不要迟延§ 2-3.时效分析*标准与改进由于有称为“标准"的比较基准,问题就明确了,由于问题明确了,就有了改进和提高效率·评价1.评价将作业者进行的作业速度与标准速度进行比较,用百分比表示的数值2.评价的目的a、用于标准时间根据时效研究,修正所得的时间值并作成作业标准时间值找到指导作业\改进作业的着眼点具备了效率评价能务,则明白了标准作业速度;明确了指导作业的要点产生向目标靠拢的愿望b、评价训练:观看训练用电影\录像,培养评价工作能力考虑作业的困难程度,是仅用手来进行的作业,还是使用整个身体来进行的作业以100%作业标准速度若感到比标准速度快,则有105,110,120等大数值若感到比标准速度慢,则有95,90,85等小值反复训练\修正自己的基准,争取在一定时间内,对一定的作业能正确评价的工作能力。
精益生产培训教材

.36666666666666666666第1讲企业组织生产的价值(VSM)分析(一)【本讲重点】1.JIT诞生背景2.价值流程图(VSM)分析两个流程3.流程分析案例JIT生产方式的产生生产经营方式是指生产者对所投入的资源要素、生产过程以及产出物的有机有效组合和运营方式的一种通盘概括,是对生产运作经管中的战略决策、系统设计和系统运行经管问题的全面综合。
到目前为止,制造业的生产方式经历了一个从手工生产、批量生产到精益生产的演变过程。
传统生产方式的优缺点1.传统生产方式的优点20世纪初,美国福特汽车创始人亨利•福特创立了以零部件互换原理、作业单纯化原理以及移动装配法为代表的批量生产方式,由此揭开了现代化大生产的序幕。
几十年来,随着制造业产品越来越复杂,自动化技术以及各种加工技术的发展,这种生产方式在形式和内容上都不断增添新的内容,成为目前最为传统的生产方式。
图1-1 传统生产方式的特征如图1-1所示,在消费需求旺盛、商品相对供应不足的时代,企业生产的产品品种单一,通过大批量生产就可达到降低成本的目的。
一旦成本得到降低,企业就可以进一步扩大生产规模,形成“大批量—低成本”的循环模式。
因此,传统生产方式实际上是一种“以量取胜”的生产方式。
2.传统生产方式的缺点在商品紧缺的年代,传统的生产方式获得了巨大的成功。
但是,随着商品经济的发展,顾客不再满足于使用单一的商品,开始追求与众不同的多样化产品。
由于少品种、大批量的传统生产方式忽视了顾客的个性化需求,因而越来越不能适应市场的需求。
此外,当前的工业产品具有一个显著特征:价格越来越便宜。
在这种情况下,传统生产方式本来具备的优点变成了缺陷:在传统生产方式下,企业制造出的产品形成大量的库存。
由于产品价格不断降低,这些库存处于持续贬值的过程中。
这给企业带来了巨大的损失。
因此,商品经济的发展呼唤小批量、多品种的生产方式。
JIT生产方式的产生20世纪后半期,兼备手工生产及大量生产两者的优点,又能克服两者缺点的一种高质量、低成本并富有柔性的新的生产方式在战后崛起的日本丰田公司应运而生,即JIT(just in time)生产方式,也被称为“丰田生产方式”,在国内被译为“精益生产方式”。
精益生产培训教材(PPT 41页)
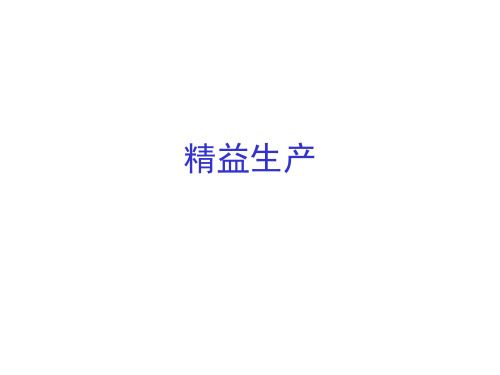
The Job
工 作
Time Fluctuation 时间波动
Job Element Sheet 工作要素单
Element 1 要素 1
Job Element Sheet 工作要素单
Element 2 要素 2
Job Element Sheet 工作要素单
Element 3 要素 3
Job Element Sheet 工作要素单
TIME FLUCTUATION WORKSHEET 时间波开工作单 JOB ELEMENT SHEET 工作要素单 TIME MEASUREMENT SHEET 时间测量单
STANDARDISED OPERATIC THEET 标准作业单
Quality Process Sheet
Department/ Welding 05
精益生产
课程内容
• 定义 • 产生与开展 • 特点与优越性 • 核心内容与生产要素 • 标准化介绍 • 最终目的
什么是精益生产?
• 精益生产是 通过系统结构、人员组织、运行方式和市 场供求等方面的变革,使生产系统能很快适应用户需 求不断变化,并能使生产过程中一切无用、多余的东 西被精简,最终到达包括市场供销在内的生产的各方 面最好的结果。
Worksheet
#
5-140
Opr
WGL
Page__1__ of__1__
Sup
Maint
Eng
3302246
QC QUICK
CHANGE OVER
VISUAL FACTORY
FORD Total Prod.T
F
M
Maint.
P
ERROR PROOFING D
精益生产培训教材(PPT 124页)

- 生产过程在不连 续和材料流动中 断时截断
收集及输入数据
设定供给商数据
参加物料流
参加信息流
计算现况的状态 SSTTAAMMPPIINNGG
S. WELD #1
冲压厂共有六个工序 1. 冲压 2. 点焊1工位 3. 点焊2工位 4. 装配1工位 5. 装配2工位 6. 发运
S. WELD #2
20
尽善尽美 (Perfection)
• 精益思想定义企业的根本目标是:通过尽善尽美的价值创造过 程〔包括设计、制造和对产品或效劳整个生命周期的支持〕为 用户提供尽善尽美的价值
• 精益生产的“尽善尽美〞有3个含义:用户满意、无过失生产和 企业自身的持续改进
• 尽善尽美〞是永远追求的目标,持续地对尽善尽美的追求,将 造就一个永远充满活力、不断进步的企业
ü 投入过多人力或设备 ü 错估需求
生产过剩
人力过剩
错估需求
无法应付订单的恐慌 心理
原因
订单应接不暇 的话怎么办?
库存量会不会 不够啊?
30
常见的七大浪费 – 动作的浪费
动作的浪费:作业员没有效率的不合理的动作产生的浪费
动作与工作
31
常见的七大浪费 – 制造不良的浪费
制造不良的浪费:原材料、半成品和成品的异常造成的浪费
价值流是指从原材料到成品赋予价值的全部活动。识别价 值流是实行精益思想的起步点,并按照最终用户的立场寻 求全过程的整体最正确
價值流
流程
流程
流程 客人
業 務 /採 購
生 産 /品 檢
…
倉 管 /運 輸
原料
成品
18
流动 (Flow)
• 精益思想要求创造价值的各个活动〔步骤〕流动起来,强 调的是“动〞,所有的停滞均为企业的浪费
精益生产培训教材(共 38张PPT)
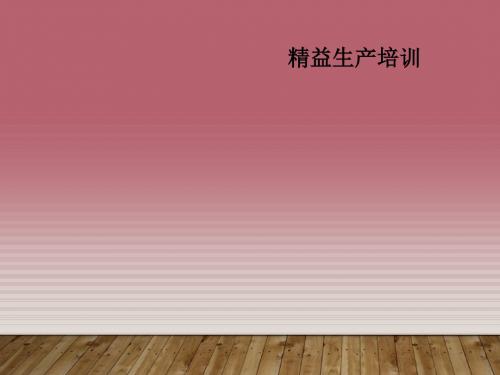
柏拉图
柏拉图
28
• 改善效果之确认
(元)
25000
改善前
(%)
100 75
(元)
25000
改善後 效果
支 出 金 額
20000 15000 10000 5000 0
累 計 比 率
支 出 金 額
20000 15000 10000 5000 0
50 25 0
伙 零 水 教 交 其 食 用 電 育 際 他 費 錢 瓦 費 費 斯 費
经过取消、合并、重排后的必要工序,应 采用最简单的方法或设备替代,以节省人
作业改善压缩
分割转移
作 业 时 间
作 業 改 善
作 业 时 间
工序
1
2
3
4
5
工序
2
3
并行作业,增加人员
拆解去除
1人 作业 作 业 时 间 作 业 时 间
2人 作业
工序
1
2
3
4
5
工序
1
2
3
作业改善后合并
重排
作 业 时 间
作 业 时 间
伙 零 水 教 交 食 用 電 育 際 費 錢 瓦 費 費 斯 費
29 柏拉图
• 效果确认的柏拉图制作要决
1. 2. 3. 4. 必须两个柏拉图并排,分为改善前与改善后。 收集数据的期间和对象必须一致。 季节性的变化应列入考虑。 对於改善项目以外的要因也要加以注意。
3.多能工培养
多能工是指掌握多个岗位作业技
21
QC手法——鱼骨图
开车人数增加
交通事故多
道路施工
收入提高 生活品质提高 虛榮心作祟休闲增加 休息日多 活动地点多 货车任意卸貨 购物商圈 停车位少 等候停车对伍长 收費速度慢
精益生产培训教材(PPT 155页)

Electronic & Electrical
Industrial Equipment
Handtools and Hardware
稍有应用/不应用
Controls & Measuring
Benchmark Results 定标结果
5.00% 4.50% 4.00% 3.50% 3.00% 2.50% 2.00% 1.50% 1.00% 0.50% 0.00%
• Emphasize on lead time reduction
• Improve asset utilization
• Built to customer demand
• 在同步生产的基 础上,强调缩短 生产周期
• 提高资源利用率 • 需求驱动
• Remove constraints to respond to customer demand through the entire supply pipeline (supplier-customer)
➢ Pull materials through the process
➢ Balanced operations based on customer demand
➢ Minimal build unless tied to customer order
➢ Extend to Supplier Base
➢ Toyota Production System丰田制造系统
➢ _____ Production System______ 制造系统
➢ etc?..
等等…...
Lean Manufacturing - Key Characteristics 精益制造 - 关键特性
精益生产培训教材

3 Shifts TAKT Time CT = C/O Time = DT = Scrap / Rework = # Operators WIP =
# Material Handlers Max Size 2 Shifts 0 Overtime
分析当前状态 设计将来状态
C/O Time = DT = Scrap = WIP =
课程一: 课程一:
精益生产概论
精益生产的发展历史
福特生产系统 •生产线大量生产 •大批量标准化产品 •工人掌握单一技术 丰田生产系统(TPS) 丰田生产系统(TPS) (TPS •JIT生产(按客户需求品种和数量准时生产) •拉动生产 •强调生产数量和库存数量与市场匹配 •按照客户需求定制产品
精益生产的发展历史
消除浪费的四步骤
第一步: 第一步: 了解什么是浪费 了解什么是浪费
第二步: 第二步: 识别工序中哪里存在浪费 识别工序中哪里存在浪费
第四步: 第四步: 实施持续改进措施 实施持续改进措施, 持续改进措施, 重复实施上述步骤
第三步: 第三步: 使用合适的工具来消除 使用合适的工具来消除 已识别的特定浪费
精益生产既是一种以最大限度地减少企业生产所占用的资 源和降低企业管理和运营成本为主要目标的生产方式,同 源和降低企业管理和运营成本为主要目标的生产方式, 时它又是一种理念,一种文化。实施精益生产就是决心追 时它又是一种理念,一种文化。 求完美的历程,也是追求卓越的过程。 求完美的历程,也是追求卓越的过程。
1985年美国麻省理工学院组织了世界上14个国家的专家、 学者,花费了5年时间,耗资500万美元,对日本等国汽车 工业的生产管理方式进行调查研究后总结出来的生产方式, 在日本称为丰田生产方式。
精益生产体系教材
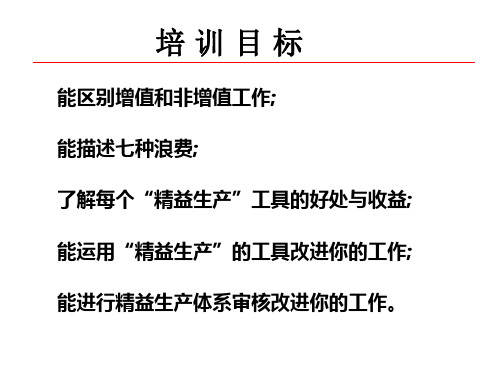
物品很容易找到并很容易拿到
我们可以知道物品放得太多或太少
第二步:Straighten 整顿
现场组织管理- 5S
现场组织管理 - 5S
Step 3: Shine 清洁
ASSIGNMENTS 分配职责
METHODS 确定方法
TOOLS 准备工具
IMPLEMENT 付渚行动
TARGETS 建立目标
合格品或安全状态
待审查区
固定位置的物品
废品区或容器
有害物品或 防撞标识
Red
Blue
White
Yellow
Grey
一般区域
现场组织管理- 可视管理
TOOLS
每件物品有指定的位置, 每件物品在它的位置上!P54
A
2
3
4
5
7
8
9
100
6
90
80
70
20
30
40
50
60
成功实施看板的6项条件
平稳的生产环境 快速换线QCO 稳定的设备(TPM) 5S 供应商保质保量的供货 标准化工作
看板的益处
加强了工位之间的交流 给先道工位基于实际情况而不是计划的指示 防止过量生产 设定补充的优先级 帮助显示瓶颈工位,然后通过Kaizen来解决瓶颈 使物料控制目视化 显示存储和发送地点 显示标准数量和容器类型 显示运输方式和频次 看板计划板显示生产状况 使人们致力于标准化工作
培 训 目 标
能区别增值和非增值工作; 能描述七种浪费; 了解每个“精益生产”工具的好处与收益; 能运用“精益生产”的工具改进你的工作; 能进行精益生产体系审核改进你的工作。
精益生产背景介绍
批量生产 Mass Production
精益生产培训教材
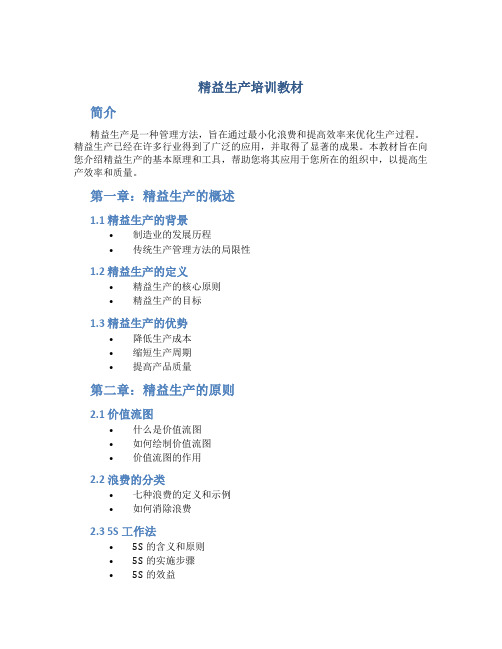
精益生产培训教材简介精益生产是一种管理方法,旨在通过最小化浪费和提高效率来优化生产过程。
精益生产已经在许多行业得到了广泛的应用,并取得了显著的成果。
本教材旨在向您介绍精益生产的基本原理和工具,帮助您将其应用于您所在的组织中,以提高生产效率和质量。
第一章:精益生产的概述1.1 精益生产的背景•制造业的发展历程•传统生产管理方法的局限性1.2 精益生产的定义•精益生产的核心原则•精益生产的目标1.3 精益生产的优势•降低生产成本•缩短生产周期•提高产品质量第二章:精益生产的原则2.1 价值流图•什么是价值流图•如何绘制价值流图•价值流图的作用2.2 浪费的分类•七种浪费的定义和示例•如何消除浪费2.3 5S工作法•5S的含义和原则•5S的实施步骤•5S的效益2.4 拉动生产•拉动生产的概念•拉动生产的优势•如何实现拉动生产第三章:精益生产的工具和技术3.1 价值流分析•什么是价值流分析•如何进行价值流分析•价值流分析的结果和应用3.2 现场管理•现场管理的原则•现场管理的实施步骤•现场管理的效果评估3.3 连续流水线•连续流水线的概念和优势•连续流水线的设计原则•连续流水线的布局和优化3.4 Jidoka•Jidoka的含义和原则•Jidoka的实施步骤•Jidoka在质量管理中的应用第四章:精益生产的实践案例4.1 案例一:汽车制造业•汽车制造业中的挑战•如何应用精益生产解决挑战•汽车制造业的成功案例4.2 案例二:电子产品制造业•电子产品制造业中的挑战•如何应用精益生产解决挑战•电子产品制造业的成功案例4.3 案例三:医药制造业•医药制造业中的挑战•如何应用精益生产解决挑战•医药制造业的成功案例结语精益生产是一种强大的管理方法,它可以帮助组织提高生产效率、降低成本,并提高产品质量。
通过学习和应用本教材中所介绍的原理、工具和案例,您将能够在自己的组织中实施精益生产,并取得显著的成果。
祝您在精益生产的道路上取得成功!。
精益生产培训教材81张幻灯片课件

2024/8/3
43
3-S:清扫
清扫:
清除各场所内的脏污,并防止污染的发生。
目的:清除污染源,保持各场所干净整洁,是品质管理的
基础。
清扫厉行“三扫”原则:
扫漏:针对溢出物;
扫黑:针对角落之物;(即看不到的地方)
扫怪:针对怪异之处。
44 44
5S---STANDARDIZE 标准化
No carrying 不需负重
No crawling 不需俯地
2024/8/3
No accumulating 不需累积
No stacking 不需堆积
No walking 不需走动
No stopping 没有停顿
49
发现浪费方法之 4
VSM 价值流 Gemba 去现场 5S 整理整顿 Visual Control 可视化管理 Layout 布局 Standard Work 标准作业
等料 等人 等机器 等指令 等检验 等……
2024/8/3
11
Waiting 等待
3#
2#
1#
2024/8/3
12
七大浪费之 5:过量生产 OVER
PRODUCTION
生产过多,(局部超产,超额) 生产过早,(局部提早) 超计划生产,(总量超出) 超出客户的需求
2024/8/3
13
Over Production 超额生产
我们所做的就是: 从顾客下定单直到我们收到钱为止。 哪些活动不增加价值。
Order 下定单
Cash 收到钱
2024/8/3
Simple, very clear focus简单,清楚
28
VSM 当前状态
- 1、下载文档前请自行甄别文档内容的完整性,平台不提供额外的编辑、内容补充、找答案等附加服务。
- 2、"仅部分预览"的文档,不可在线预览部分如存在完整性等问题,可反馈申请退款(可完整预览的文档不适用该条件!)。
- 3、如文档侵犯您的权益,请联系客服反馈,我们会尽快为您处理(人工客服工作时间:9:00-18:30)。
⊙Shorter lead time and on time delivery 快速并准时交货
⊙Grow the mix , special configurations 需求品种增加,特殊定制
⊙Maintain/improve quality and reduce price 不断改进质量及降低销售价格
长青树 (2-2) 市场竞争及全球化
产品生命周期
life cycle change/产品生命周期 年 30
20
10
0 化妆品 玩具 机床 食品 药品
50年前 现在
product styles in supermarket/商品种类
60000 50000 40000 30000 20000 10000
需求拉动
按需求生产
象开发的河流 一样通畅流动
Flow 流动
降低成本,改善质量,缩短生产周期
The Competition Advantage Of A Lean Enterprise
长青树 (4-2) 精益企业竞争优势
在三到五年的时间里:
◎生产时间减少90% ◎库存减少90% ◎生产效率提高60% ◎到达客户手中的缺陷减少50% ◎废品率降低50% ◎与工作有关的伤害降低50%
◎生产多于下游客户所需 Making More Than Needed
◎生产快于下游客户所求 Making Faster Than Needed
部品
工位1
工位2
工位1快于工位2
······
部品
工位1
···出荷(15pcs)
工位2
工位2多于客户需求(多生产8pcs)
Waste of Inventory
起源于20世纪50年代丰田汽车公司,而在80年代中 期被欧美企业纷纷采用.随着微利时代的来临,精益 生产模式成为企业竞争的有力武器.
Manufacturing Evolution
长青树 (1-2) 制造系统演化史
Henry Ford ⊙Assembly line mass production ⊙Produce in high volume with low variety ⊙Single skill 福特首创的装配线是大规模低品种生产 方的代表,工人被当成工作的机器 Toyota Production System (TPS)
⊙Total life cycle of product becoming shorter and shorter 产品的生命周期越来越短
⊙No boundary , business globalize village 无国界,业务“地球村”
Marketing Competition and Globalization
⊙Just-in-Time Production (produce only what is needed)
⊙Pull System ⊙High variety to meet customers wants 丰田系统是建立在准时化观念上的拉动式生 产模式,以应付小订单多品种的挑战
Marketing Competition and Globalization
LEAN MANUFACTURING SYSTEM
精益生产系统
What Shall We Talk….?
长青树 内容安排
第一单元
精益生产及精益企业
What Shall We Talk….?
长青树 内容安排
①生产系统的发展简介 ②市场竞争及全球化 ③精益思想和精益企业 ④精益生产系统的五个要素 ⑤标准 精益企业的实践
0
种类
1997
1980
1990
2000
产品 种类
时间
产品种类
长青树 (3) Lean-”精益” 释义
(lean)精益-形容词:无肉或少肉,少脂肪或无脂肪,文
体或措词简练
(fat) 反义词:肥胖的,多肉的,过重的,不结实的,过
分肥胖的,丰满的,粗短的,肥大的,软的
精益生产: 通过消除企业所有环节上的不增值活动,实现连续的信息 流,物流及现金流,从而达到降低成本,缩短生产周期和 改善质量的目的
(1) 识别和消除七种浪费
●Overproduction 过量生产 ●Inventory 库存 ●Conveyance 搬运 ●Correction 返工 ●Processing 过程不当 ●Motion 多余动作 ●Waiting 等待
Waste of Overproduction
长青树 (1-1) 过量生产
长青树 (1-2) 库存浪费
……否则,要检查一下你有哪里做错了!
长青树 (5) 构筑精益企业之屋
全面质量管理 自动化及防错 全面生产维护 设备总有效性
精益企业
消除浪费降低成本
库存降低
准时化生产
看板拉动
均衡混流生产
缩短生产周期
小批量生产
流动生产
作业快速转换 设备布局 多技能员工
观念转变,消除浪费,价值流管理,团队精神及5S,持续改进
Lean Thinking and Lean Manufacturing System
长青树 (1-1) 精益思维和精益生产系统
Starting with Toyota in the late 50’s and catching on in the mid-80’s in the reminder of the industrial world, Lean Manufacturing has become a key strategy for manufacturers
长青树
What is Lean Manufacturing
(4-1) 什么是精益生产-五个原则
Perfect 完美
没有任何事物是 完美的不断改进
Value 价值
站在客户 的立场上
Value stream 价值流
Lean manufacturing
精益生产
从接单到发货 过程的一切活动
Demand pull
What Shall We Talk….?
长青树 内容安排
第二单元长青树 内容安排
①识别和消除七种浪费 ②过程质量及差错预防 ③从增值比看改善空间 ④制造周期和交付周期 ⑤5S及目视工厂 ⑥打造高绩效团队
长青树
Identify and Eliminate 7 Wastes