a-半水高强度石膏生产新工艺
α型半水石膏的研制

α型半水石膏的研制摘要以简化生产工艺流程,降低生产成本为原则,研究开发了无转晶剂的两种生产α型半水石膏工艺。
其产品质量可达到:标准稠度低于40%,抗折强度高于10MPa,抗压强度大于30MPa。
关键词α型半水型石膏转晶剂成本1β型半半水α型半水α型半水但由于α进行了中试生产,现做些总结,供读者参考。
2无转晶剂生产方法没有添加转晶剂,也可以生产出水膏比低于40%的α型半水石膏,并可降低生产成本,但其工艺技术控制都要求比较高。
2.1生成α型半水石膏的工艺原理二水石膏脱去1.5个结晶水形成半水石膏,其反应式为CaSO4·2H2O=CaSO4·H2O+1.5H2O 在不同压力下二水石膏脱水形成半水石膏石膏的温度也不同。
图1中曲线1为二水石膏——半水石膏的“压力——温度”平衡曲线。
从图上可以看出,曲线1非常接近液相水—气相水的“压力—温度”平衡曲线2,并相交于C点,在没有添加转晶剂条件下,要制成α型半水石膏,二水石膏的结)就容易制成α2上,致2.2,层间隔图2中22中3力。
进口C的蒸气是用于初始液态水升温加热和配合加热器3控制蒸压釜内液态水温度。
为了使生产的α型半水石膏不搬动,在同一蒸压釜内进行干燥。
在图2中,设计了干燥热空气鼓入口D 和抽出口B。
干燥时,在B抽汽的同时,由D鼓入干热空气,对已生成的α型半水石膏直接干燥。
为了降低能耗,蒸压釜、加热器和管道都要外加保温层。
2.3该生产α型半水石膏工艺特点该生产α型半水石膏工艺和其它蒸压法工艺相比,有如下特点:1.蒸压釜2.热水泵3.电加热器A.蒸汽进口B.干燥余气抽出口C.蒸气进口D.干燥热空气鼓入口E.排水口a.二水石膏全部浸泡在液态水中,通过调整加热器供热量和蒸汽进口A的蒸汽压力,使二水石膏保持在图1ABC区间“温度—压力”内,进行加热,结晶水全部以液态排出,确保二水石膏全部生成αb.αc.2.4区间内,脱水生成无水石膏。
干燥温度过低干燥时间延长,甚至使α型半水石膏转回到二水石膏,经实验,干燥温度控制在130~1400C较好。
α半水磷石膏的制备 蒸压法
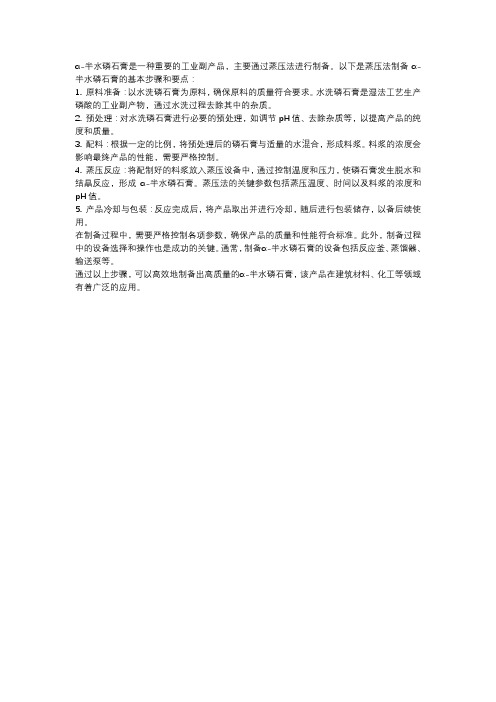
α-半水磷石膏是一种重要的工业副产品,主要通过蒸压法进行制备。
以下是蒸压法制备α-半水磷石膏的基本步骤和要点:
1. 原料准备:以水洗磷石膏为原料,确保原料的质量符合要求。
水洗磷石膏是湿法工艺生产磷酸的工业副产物,通过水洗过程去除其中的杂质。
2. 预处理:对水洗磷石膏进行必要的预处理,如调节pH值、去除杂质等,以提高产品的纯度和质量。
3. 配料:根据一定的比例,将预处理后的磷石膏与适量的水混合,形成料浆。
料浆的浓度会影响最终产品的性能,需要严格控制。
4. 蒸压反应:将配制好的料浆放入蒸压设备中,通过控制温度和压力,使磷石膏发生脱水和结晶反应,形成α-半水磷石膏。
蒸压法的关键参数包括蒸压温度、时间以及料浆的浓度和pH值。
5. 产品冷却与包装:反应完成后,将产品取出并进行冷却,随后进行包装储存,以备后续使用。
在制备过程中,需要严格控制各项参数,确保产品的质量和性能符合标准。
此外,制备过程中的设备选择和操作也是成功的关键。
通常,制备α-半水磷石膏的设备包括反应釜、蒸馏器、输送泵等。
通过以上步骤,可以高效地制备出高质量的α-半水磷石膏,该产品在建筑材料、化工等领域有着广泛的应用。
半水石膏生产工艺

半水石膏生产工艺
半水石膏生产工艺
半水石膏是利用熟石膏石膏煅烧石膏造成石膏半水化反应得到。
下面是半水石膏生产工艺的步骤。
首先,准备原料。
半水石膏生产的主要原料是石膏石膏,也称为天然石膏,是一种无机非金属矿产,主要由硫酸钙组成。
石膏粉末是由熟石膏经过破碎、磨碎、研磨等工艺处理得到的。
其次,石膏粉末与适量的水进行混合。
根据需要,可以添加一些辅助材料,如防火材料、增塑剂等。
混合后的石膏浆料应具有一定的流动性,方便施工。
然后,将混合好的石膏浆料灌注到特制的模具中。
模具的形状可以根据产品的需求进行定制,常见的有板状、条状、角状等。
在灌注过程中,需要注意控制灌注速度和压力,确保石膏充分填充模具的每个细节。
接下来,待石膏浆料凝固。
石膏浆料中的水分和石膏粉末通过水合反应生成半水化石膏,同时释放出一定的热量。
因此,在凝固过程中,需要控制温度和湿度,以确保石膏能够均匀凝固,而不会出现裂纹或不均匀收缩。
最后,将凝固后的石膏制品从模具中取出,经过一定的干燥和固化时间后,即可得到成品。
成品可以进行表面处理和装饰,如抛光、刷漆等。
半水石膏具有良好的耐火性、隔热性和吸湿性,广泛应用于建筑装饰、内墙隔音、防火隔离等领域。
通过控制石膏粉末与水的比例、混合和硬化过程中的温湿度等参数,可以获得不同性能的半水石膏制品。
- 1、下载文档前请自行甄别文档内容的完整性,平台不提供额外的编辑、内容补充、找答案等附加服务。
- 2、"仅部分预览"的文档,不可在线预览部分如存在完整性等问题,可反馈申请退款(可完整预览的文档不适用该条件!)。
- 3、如文档侵犯您的权益,请联系客服反馈,我们会尽快为您处理(人工客服工作时间:9:00-18:30)。
岩石。用于 A-半水石膏制造的天然二水石膏以 Ca-
SO4·2H 2O 质量含量为 85% 以上的雪花石膏矿石为
好。
二水石膏的脱水化学反应过程如下:
与大气压相通
CaSO 4·2H2O
140~170℃
B-CaSO4·1/ 2H2O + 3/ 2H2O
饱和蒸汽压或盐类溶液
Ca SO 4·2H2O
( 1997 年 11 月收修改稿)
《现代化工》邮发代号 82-67, 1998 年定价仍是 72 元。
·24·
ห้องสมุดไป่ตู้
1998 年第 2 期 现代化工
二水天然石膏在控制加热的条件下, 可以转化 成许多不同形态的中间产物, 其中最具应用价值的 是 A-半水石膏、B-半水石膏及可溶性硬石膏。A-半水 石膏又称为高强度建筑石膏, 其用途广泛, 制作方法 一般有蒸汽加压法和水溶液法两种。
蒸汽加压法是将一定块度的天然石膏矿石, 在 密闭的蒸压釜中, 维持一定的温度和压力, 以使二水 石膏脱水再结晶为规定晶型的半水石膏, 为了使结 晶过程易于进行, 通常在装料前于料块上浇洒媒晶 剂( cry st al mo dif ier) 。工业上常用的是蒸汽加压法, 蒸压釜一般设计为圆筒状, 卧式安装, 釜内安排有特 制的料车轨道, 进料小推车在装料后, 沿轨道推入釜 内, 尔后密闭通入蒸汽加热。这种方法的缺陷是蒸压 釜的有效容积利用率很低, 媒晶剂用量大且效果不 明显, 加之冷料进釜使得蒸汽消耗量很大。
A-半水高强度石膏生产新工艺
李天文 ( 中国科学院化工冶金研究所, 北京 100080)
姜四清 ( 山西省曲沃县高强度石膏厂, 043400)
摘要 本工艺将 A-半水石膏生产 中的“水溶液法 ”和“蒸汽加压 法”的优点巧妙 地结合起来, 用 于二水石 膏块矿的 加工生 产, 形成了具有特色的“汽液结合法”工艺。工艺中利用“闪蒸原理”进行负压干燥, 媒晶剂溶液循环使用, 媒晶剂溶液的余热预热 生料, 使得生产能力及产品质量大为提高, 能耗大幅度降低。 关键词 A-半水石膏, 汽液结合法, 二水石膏
的数目沿轴向由疏到密。在釜的外壁均布直径 <50 mm 的 6 个管口以使热风均匀一致地流进内胆与釜 壁的夹层内。
4 生产应用
生产中使用的石膏矿为天然雪花石膏, CaSO 4 ·2H2O 质量分数为 85% ~95% , 其余杂质以石灰石 为主。媒晶剂溶液为: 琥珀酸 3. 2% , 硫酸钾0. 5% , 渗透剂 0. 1% 。每釜的装料量约为 6 t , 块度为 30~ 50 mm , 堆密度为 1. 2~1. 5 t / m3。石膏矿用量都为 1. 2 t 时, 与蒸汽加压法的消耗定额对比见附表, 汽 液结合法的产品质量完全可以跟上述两法相比, 但 是它的燃煤消耗量比蒸汽加压法减少近一半, 这主 要是得益于烘干时间的大幅度的缩短, 以及媒晶剂 溶液对原料的预热作用。
水溶液法一般多采用磨细的石膏粉作原料与无
·22·
机盐水溶液混合, 放置在密闭的反应釜中, 同时加入 媒晶剂, 在一定的温度和压力下, 使二水石膏溶解再 结晶成 A-型半水石膏[ 1] 。这种方法多用于烟道气脱 硫石膏及湿法磷酸副产磷石膏的处理, 由于半水石 膏在低于脱水温度( ~97℃) 下的逆变性, 脱离反应 釜后的 A-半水石膏料浆必须尽快在 120~140℃下 烘干。料浆的粒度细含水量大, 烘干设备复杂, 后继 烘干工序负荷大, 是此种方法的不足之处。
A-半 水石膏的 形成实 际上是 石膏“溶解-再结
晶”过程。通常情形下, 二水石膏在无其它物质的干
扰下, 易生成晶粒细碎的针状结晶, 实验表明, 针状
结晶水膏比最大, 制品的强度最低, 而六角形或短柱
状结晶水膏比最小, 制品的强度也最高。所以, 工业
生产中在二水石膏脱水过程中加入一定量的对 A-
半水石膏结晶有诱导作用的媒晶剂, 可以改变 A-半
A new technology of A-calcium sulphate hemihydrate
L i T ianw en
( T he Inst itute o f Chemical M et allurg y o f the Chinese A cadem y of Sciences, Beijing 100080)
附表 汽液结合法与蒸汽加压法消耗定额的比较
项 目
蒸 汽( 0. 3M Pa) / t 外加剂/ kg 工业自来水/ m3 标准煤/ t
蒸汽加压法
0. 5 2. 5 1. 5 0. 3
汽液结合法
0. 3 1. 0 1. 2 0. 17
5 结论
¹ 本工艺主要设备蒸压釜集蒸压和烘干于一 体, 与蒸汽加压法相比减少了轨道、矿石小车等附属 运输设施, 设备结构紧凑, 生产流程缩短, 节省投资。
水物的晶系, 使结晶过程朝所要求的晶型进行。所
以, 正确选择和使用媒晶剂, 对于提高产品的强度是 至关重要的。
在蒸汽加压法中媒晶剂的使用, 一般是进料前, 将一定浓度的媒晶剂水溶液淋洒于料车中的石膏料 块上, 因而媒晶剂只能少量地粘在石料的表面上及 缝隙中, 晶型转换的效果非常有限。与此相对照, 在 水溶液法中由于石膏物料完全浸泡于含有媒晶剂的 溶液中, 转晶效果十分理想。本工艺在实施中将水溶 液法媒晶剂使用方法与蒸汽加压法块料加工的特点 结合使用取得了良好效果。
现代化工 1998 年第 2 期
压釜底部阀门 D1 和 D2, 利用蒸压釜( 1) 内的蒸汽 余压将釜内残留的媒晶剂溶液压入蒸压釜( 2) , 此时 蒸压釜( 2) 中应装满待蒸压的石膏生料。媒晶剂溶液 从蒸压釜( 1) 中压出后, 立即关闭阀门 D1、D2, 打开 排污阀 P1 迅速排污卸压。完成后, 半闭所有与蒸压 釜( 1) 相联通的阀门, 打开顶部阀门 S1, 并起动水环 式真空泵。利用釜中物料本身的潜热及闪蒸原理, 使
总之, 能耗大、产量低是上述两种方法的严重缺 陷, 同时也是 制约 A-半水石膏 拓宽用 途的主 要因 素。针对上述方法的不足之处, 我们摸索出能够显著 降低能耗提高产品质量和产量的“汽液结合法”, 并 在实际生产中得以顺利实施。
1 基本原理
天然二水石膏是由 CaSO 4·2H2O 所组成的层积
1998 年第 2 期 现代化工
J iang S iqing
( Sha nx i Q uw o Hig h-Str eng th G ypsum P lant , 043400)
Abstract A new technolog y char acterized as “Steaming -Boiling O peration”w as developed for conv erting dihy dr ate g ypsum lumps into A-hemihy dr ate by combining the virtues of “Aqueous-Solutio n Pr ocess” and “Steam Pr essur ized P ro cess”. Seeing it s desiccatio n by neg ativ e pr essur e, recycle of cr ysta l mo difier s and pr eheating of r aw gy psum, this techno lo gy has been rendered m ost efficient in pro ducing calcium sulphate hemihy drat e, w ith hig her quality and lo wer energ y co nsumptio n. Key words A-hemihy dr ate, st eaming -boiling operat ion, dihy dr ate g ypsum
º 在烘干中利用“闪蒸原理”进行负压干燥, 极 大地提高了烘干效率, 既降低了能耗, 又缩短了生产 周期。这是本工艺的独创之处。
» 生产过程中原料石膏浸泡于媒晶剂溶液中参 加反应, 转晶效果大为增强, 同时媒晶剂的循环使 用, 不但降低了媒晶剂的消耗, 而且也无污水排放。
参考文献
1 特公昭 53-52294 2 特公昭 53-23020
3 蒸压釜基本结构
蒸压釜的结构示意于图 2。
图 2 蒸压釜示意图
1- 内胆; 2- 中心管; 3- 加料口; 4- 中心管接口; 5- 热风管接口; 6- 出料口
蒸压釜为双层结构, 釜的内胆厚 8 m m, 周围分布有 直径 <20 mm 小孔。釜的中心管( 1) 上分布有直径 <20 mm 小孔, 为了使气流在物料中分布均匀, 开孔
120~140℃
A-CaSO 4·1/ 2H2O + 3/ 2H2O
所以根据不同的加热温度和条件, 半水石膏又有 A
和 B 两种形态, 这取决于对二水石膏采用的生产加
工方法。A-半水石膏是在饱和水蒸气的气氛中加热,
由二水石膏缓慢脱水形成( 如蒸汽加压法) 或者是在
某些盐类溶液中结晶形成( 如水溶液法) [ 2] 。
2 工艺流程
工艺流程如图 1 所示。 石膏矿经锷式破碎机破碎成 30~50 m m 的块 度, 用提升机装入蒸压釜内, 由给液泵将媒晶剂溶液 打入蒸压釜中。蒸压釜的设计集蒸压与烘干为一体, 改变了以往蒸汽加压法中蒸压与烘干分别于蒸压釜 与烘干窑中进行而另设轨道、料车等弊病, 使得设备 紧凑, 操作方便, 节省人力。生产采用双釜轮替操作, 在一个釜蒸压时另一个釜烘干。同时, 带有 A-半水 石膏晶种媒晶剂溶液可以循环使用, 这对于诱导和
·23·
存在于物料表面及内部的水分迅速汽化, 抽出釜外 达到部分真空干燥的目的。抽真空的管路联接有空 气 冷凝 器以 保障 水环 式 真空 泵的 工 作温 度 低于 40℃。在釜中温度降至 80℃时, 立即将热风阀 R1 开 启, 向釜中通入 120~140℃的间接热风, 继续干燥 至物料含水量小于 0. 3% 。干燥完结后关闭阀门 S1、 R1。打开釜的底盖出料, 出釜的物料应尽快地磨完, 贮藏陈化。卸压后的蒸压釜( 1) 再装入生料蒸压。此 时蒸压釜( 2) 应刚完成蒸压, 准备进入烘干阶段。依 照 对蒸压釜( 1) 操作, 两釜始终处于“蒸压-烘干”的 循环使用中。生产表明利用蒸压后物料本身的潜热 进行部分负压干燥, 可以使干燥过程由原来的 10 h 缩短为 5 h, 这 样就大大 降低了能 耗, 提高 生产效 率。另外, 媒晶剂溶液在循环使用时本身始终带有温 度, 这对于预热进釜的生料大有好处。尤其是在冬 季, 可以避免大量冷凝水的产生, 节约蒸汽用量。