纸面石膏板生产工艺技术.-熟石膏处理和冷却
纸面石膏板生产工艺
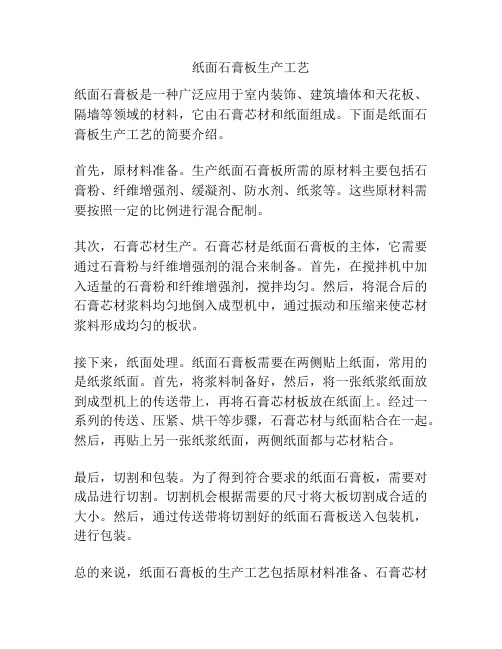
纸面石膏板生产工艺
纸面石膏板是一种广泛应用于室内装饰、建筑墙体和天花板、隔墙等领域的材料,它由石膏芯材和纸面组成。
下面是纸面石膏板生产工艺的简要介绍。
首先,原材料准备。
生产纸面石膏板所需的原材料主要包括石膏粉、纤维增强剂、缓凝剂、防水剂、纸浆等。
这些原材料需要按照一定的比例进行混合配制。
其次,石膏芯材生产。
石膏芯材是纸面石膏板的主体,它需要通过石膏粉与纤维增强剂的混合来制备。
首先,在搅拌机中加入适量的石膏粉和纤维增强剂,搅拌均匀。
然后,将混合后的石膏芯材浆料均匀地倒入成型机中,通过振动和压缩来使芯材浆料形成均匀的板状。
接下来,纸面处理。
纸面石膏板需要在两侧贴上纸面,常用的是纸浆纸面。
首先,将浆料制备好,然后,将一张纸浆纸面放到成型机上的传送带上,再将石膏芯材板放在纸面上。
经过一系列的传送、压紧、烘干等步骤,石膏芯材与纸面粘合在一起。
然后,再贴上另一张纸浆纸面,两侧纸面都与芯材粘合。
最后,切割和包装。
为了得到符合要求的纸面石膏板,需要对成品进行切割。
切割机会根据需要的尺寸将大板切割成合适的大小。
然后,通过传送带将切割好的纸面石膏板送入包装机,进行包装。
总的来说,纸面石膏板的生产工艺包括原材料准备、石膏芯材
生产、纸面处理、切割和包装等过程。
通过这些工艺步骤,能够得到优质、符合要求的纸面石膏板产品。
纸面石膏板生产.ppt

六、制板车间—生产线干端
纸面石膏板生产线最后,干燥机出板进入敞开冷却、缓冲辊道区,有序 等待通过出板机出板。通过收集辊道、二号横向进入合片机。合片为了保护 石膏板象牙面。合片后按尺寸切边,包边,堆垛、打包。 1、干端,本质就是是一个冷却、输送处理过程。 2、所有的生产成本已经付出,防止二横积板损失是重中之重。现代化大型石膏
行业可以考虑设计具有复合效果的成型装备,对减少停机、降低运行成 本应该有意义。
纸面石膏板工艺控制
5、成型的工艺本质:石膏粉遇水反应凝固硬化,并实现护面纸与湿石膏板芯材的湿 粘结。纸芯界面析出的二水石膏针状晶体与护面纸松散的最内层交错连生。 变性淀粉的添加与否与添加量多少与湿粘结没有任何关联。
6、AIII对搅拌机运行有影响,会造成浆体凝固异常。 搅拌机,内部结块失去动态平衡、浆体性能异常,是停机的经常性因素。
5、干燥机速度与成型速度有比例关系:根据层数、列数。 6、干燥机供热:热风-热风置换、天然气直燃、热风-蒸汽换热、导热油-空
气。换热次数决定热效率。要做好干燥机保温、减少热桥。 7、现在干燥机最高进口热风温度可以达到280℃以上。 8、板材干燥过程要密切监控:板的温度、含水率变化,循环风温度、湿度,
10、制粉线工艺设计要求: 工艺先进、产品稳定-高质量、高效节能、运行稳定、运行成本低; 余热利用; 自动化程度高、少用人; 符合本安-规范-环保要求等。
二、制板车间—配料
配料工艺水平基本决定石膏板的内在品质,反映了每条石膏板生产线工艺水 平、产品质量。
1、纸面石膏板配料可以分为:干料、湿料;主料、辅料、添加剂等 石膏粉、护面纸、水、淀粉,粘边胶是必须最基本的原材料; 其他辅料与添加剂都是功能性的:降低成本、改善性能、提高运行质量等等: 促凝剂、缓凝剂、发泡剂、减水剂、防水剂、纸浆、玻璃纤维等等。
纸面石膏板生产工艺技术-石膏板天花板质量控制方法

天花板是一般是安装在一座室内顶部表面的地方。
在室内设计中,天花板可以写画、油漆
美化室内环境及安装、光管、、开天窗、装空调,改变室内照明及空气流通的效用。
是对装
饰室内屋顶材料的总称。
天花板经特殊工艺处理,抗静电,不落尘,不沾尘,能彻底满足高精度电子厂房、医院手
术室、等高无尘、高洁净场所的要求。
天花板有不同规则尺寸:595*595mm,600*600mm,603*603mm,603*1209mm 。
石膏板天花板是以熟石膏为主要案原料掺入添加剂与纤维制成,具有质轻、绝热、吸声、
阻燃和可锯等性能但石膏板,容易裂和变形。
多用与商业空间科学,一般采用600*600规格,有明骨和暗骨之分,龙骨常用铝或铁。
天花板质量的控制,我们一般需要测试天花板的长度、宽度、厚度、外观质量主要看包装
是否完好,无碰撞问题。
内在质量需要测试重量,含水率、干粘结、强度等质量指标。
现在的石膏天花板的生产设备已经很先进,产量高,质量稳定。
但是天花板的质量很大一
部分石来自纸面石膏板的质量。
因此纸面石膏板的质量如尺寸,表面平整度,粘结好,强度
稳定等。
纸面石膏板生产工艺技术-石膏板成型和凝固
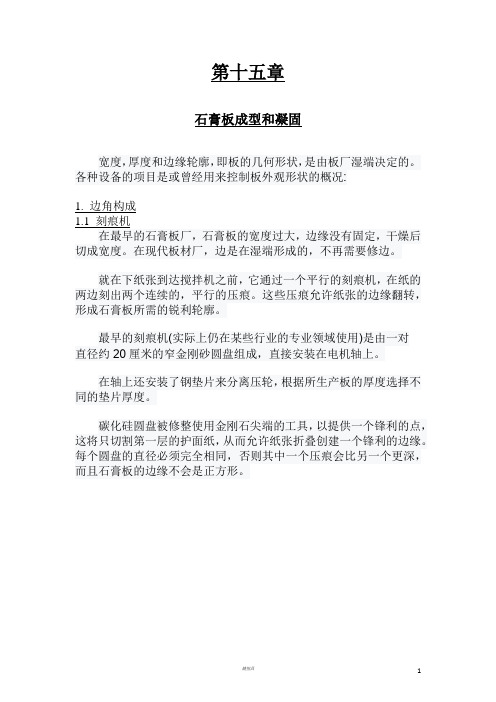
第十五章石膏板成型和凝固宽度,厚度和边缘轮廓,即板的几何形状,是由板厂湿端决定的。
各种设备的项目是或曾经用来控制板外观形状的概况:1. 边角构成1.1 刻痕机在最早的石膏板厂,石膏板的宽度过大,边缘没有固定,干燥后切成宽度。
在现代板材厂,边是在湿端形成的,不再需要修边。
就在下纸张到达搅拌机之前,它通过一个平行的刻痕机,在纸的两边刻出两个连续的,平行的压痕。
这些压痕允许纸张的边缘翻转,形成石膏板所需的锐利轮廓。
最早的刻痕机(实际上仍在某些行业的专业领域使用)是由一对直径约20厘米的窄金刚砂圆盘组成,直接安装在电机轴上。
在轴上还安装了钢垫片来分离压轮,根据所生产板的厚度选择不同的垫片厚度。
碳化硅圆盘被修整使用金刚石尖端的工具,以提供一个锋利的点,这将只切割第一层的护面纸,从而允许纸张折叠创建一个锋利的边缘。
每个圆盘的直径必须完全相同,否则其中一个压痕会比另一个更深,而且石膏板的边缘不会是正方形。
现代刻痕机使用更小的(75毫米直径),锯齿状的双金属刀片代替了碳化硅盘,独立可调压轮下方的纸张,以控制每根压痕的深度。
INDEPENDENTLYADJUS TABLE ANVILSTWIN CUTTER BLADESS CORERMOTORBOTTOM PAPER各种其他压痕系统已被使用,包括倾斜,高度可调电机,不同的锯齿配置,锯齿盘和压痕盘,而不是刀具。
正如两个压痕机叶片之间的距离控制板的厚度一样,两组压痕机之间的距离(在护面纸的每边各设置一组)控制板的宽度。
1.2 震动器石膏/水的石膏浆从搅拌机通过一个喷嘴或多个喷嘴分配到底部的纸。
然后,在浆料进入挤出机之前,要求浆料完全分散在纸张的宽度上。
在现代工厂的速度下,实现这种传播的时间通常不到两秒钟。
浆体本身的流动特性在实现这种扩散过程中发挥了很大的作用(这就是为什么我们在浆体中使用的水要比半水合物再水化所需的水多得多),但也使用了其他机械手段。
在搅拌机和挤出机之间的湿端部装有各种设计的振动器,以促进浆液的扩散,并有助于去除一些较大的气泡,这些气泡如果留在板芯中,可能会对板的质量造成问题。
纸面石膏板生产工艺技术-石膏板供料系统
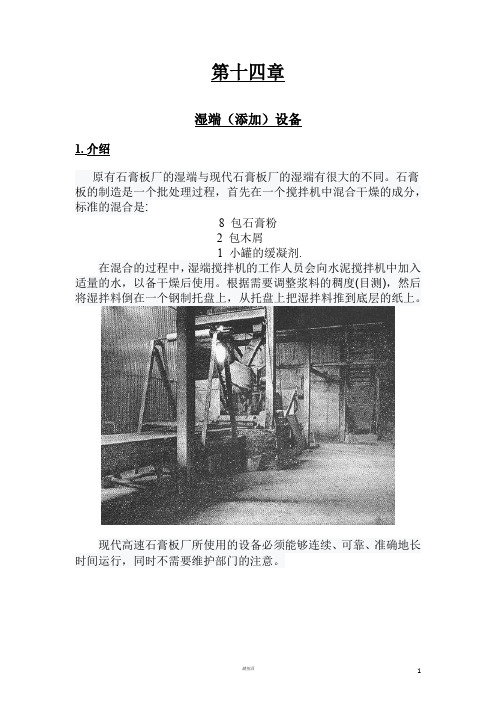
第十四章湿端(添加)设备1. 介绍原有石膏板厂的湿端与现代石膏板厂的湿端有很大的不同。
石膏板的制造是一个批处理过程,首先在一个搅拌机中混合干燥的成分,标准的混合是:8 包石膏粉2 包木屑1 小罐的缓凝剂.在混合的过程中,湿端搅拌机的工作人员会向水泥搅拌机中加入适量的水,以备干燥后使用。
根据需要调整浆料的稠度(目测),然后将湿拌料倒在一个钢制托盘上,从托盘上把湿拌料推到底层的纸上。
现代高速石膏板厂所使用的设备必须能够连续、可靠、准确地长时间运行,同时不需要维护部门的注意。
2. 喂料器2.1 固体喂料器2.1.1 石膏供料器石膏的流动特性随石膏的存放时间、温度和来源的不同而变化很大。
刚从煅烧炉中取出的石膏通常会像水一样流动,而在筒仓中放置数小时的石膏会顽固地拒绝移动,尽管有机械筒仓排放系统的最大努力和/或用大锤“敲击”。
尽管如此,我们的操作要求将石膏精确、准确和一致地送入搅拌器里。
固体处理系统最简单的形式之一是螺旋输送机:对于大多数运输系统,螺旋输送机是由安装在传动轴上的金属片或塑料螺杆组成。
装配好的螺杆在槽或圆柱体中旋转,旋转时将固体材料沿槽推进。
运动的方向取决于螺杆的形状和轴的旋转方向。
螺旋输送机操作简单,最初用于水平运输,但现在也用于将材料向上倾斜。
螺旋输送机的特殊形式的计量螺杆,螺杆之间的间隙和周围的管的紧,有容积的材料在运输这交付率成正比的速度旋转的螺旋。
计量螺杆是石膏给料器的标准形式。
它们有时水平安装,有时倾斜安装。
有时进料系统由一个计量螺杆组成,而在其他地方则采用双螺杆串联,第一个螺杆比第二个螺杆输送稍多一点:在诸如上述的系统中,通过使用热石膏或冷石膏,松散盒被用来平衡石膏体积密度的变化。
第一个计量螺杆的输送量将略高于工厂的要求,溢流将返回到主石膏系统。
石膏冲过螺杆或卡死螺杆的任何倾向都是有限的,因此第二个计量螺杆的供应是相当均匀的。
因此,第二螺杆可以实现对搅拌器石膏的合理稳定送料。
在20世纪60年代和70年代,研究了几种不同的石膏给料系统,包括称重皮带给料机。
纸面石膏板的制作工艺流程

纸面石膏板的制作工艺流程英文回答:The manufacturing process of paper-faced gypsum board involves several steps. First, gypsum rock is mined from quarries and crushed into a fine powder. This powder is then mixed with water to form a slurry. Next, the slurry is poured onto a layer of paper and covered with another layer of paper. The paper acts as a facing material, providing strength and stability to the board.After the slurry is sandwiched between the layers of paper, it is passed through a set of rollers to remove excess water and flatten the board. This step is crucial in ensuring the board's dimensional stability and uniform thickness. The board is then cut into desired lengths and transferred to a drying chamber.In the drying chamber, the boards are subjected to high temperatures to remove any remaining moisture. This processis known as calcination, and it causes the gypsum to undergo a chemical reaction, transforming it into a hard, solid material. The drying time can vary depending on the board thickness and environmental conditions.Once the boards are fully dried, they are inspected for quality control. Any defective boards are discarded, and only the ones that meet the required standards are packaged and prepared for distribution. The finished boards are typically bundled together and wrapped in plastic or paper to protect them during transportation.中文回答:纸面石膏板的制作工艺流程包括几个步骤。
石膏板生产工艺流程

石膏板生产工艺流程简介、工艺原理纸面石膏板是以建筑石膏为主要原料,掺入适量添加剂与纤维做板芯, 以特制的板纸为护面,经加工制成的板材。
纸面石膏板具有重量轻、隔声、 隔热、加工性能强、施工方法简便的特点。
纸面石膏板的生产技术是基于建筑石膏水化机理。
建筑石膏的主要成分为B 型半水石膏,与水结合形成二水石膏,方程式表示为:CaSO T/2H 2O +3/2H 2O、工艺流程简介纸面石膏板生产工艺流程图 1、熟料的制备:我们公司产品采用的主要原料是电厂产出的脱硫石膏,其主要成分为CaSO • 2H2O,其经过回转窑煅烧后可得到 B 型半水石膏为主建筑石膏,该过程 用方程式表示为:加热CaSO 4 • 2H 2O 一 CaSQ • I/2H 2O +3/2H 2O煅烧后的建筑石膏经冷却后,储存于大料仓,以备用。
2、配料部分:备料:CaSO 4 • 2H 2O 放热图1 纸面石膏板生产工艺流程图①、改性淀粉、缓凝剂、纸浆、减水剂、水等原料经定量计量后放入水力碎浆机搅拌成原料浆,然后泵入料浆储备罐备用;②、发泡剂和水按比例投入发泡剂制备罐搅拌均匀,泵入发泡剂储备罐备用;③、促凝剂和熟石膏粉原料经提升输送设备进入料仓备用;配料:料浆储备罐中的浆料使用计量泵泵入到搅拌机,发泡剂使用动态发泡装置发泡后进入搅拌机,促凝剂和石膏粉使用全自动计量皮带称计量后进入搅拌机,然后所有主辅料在搅拌机混合成合格的石膏浆。
所有主辅料的添加都含括在自动控制系统中,随生产线速度的不同自动调节,以适应大规模、高速度的要求。
图2 纸面石膏板生产线立体形象示意图3、成型输送部分上纸开卷后经自动纠偏机进入成型机,下纸开卷后经自动纠偏机、刻痕机、震动平台进入成型机,搅拌机的料浆落到震动平台的下纸上进入成型机,在成型机上挤压出要求规格的石膏板,然后在凝固皮带上完成初凝、在输送辊道上完成终凝,经过定长切断机切成需要的长度(2400mm、3000mm或其它),经横向机转向,转向后两张石膏板同时离开横向机,然后使用靠拢辊道使两张板材的间距达到要求后,经分配机分配进入干燥机干燥。
纸面石膏板生产工艺及应用
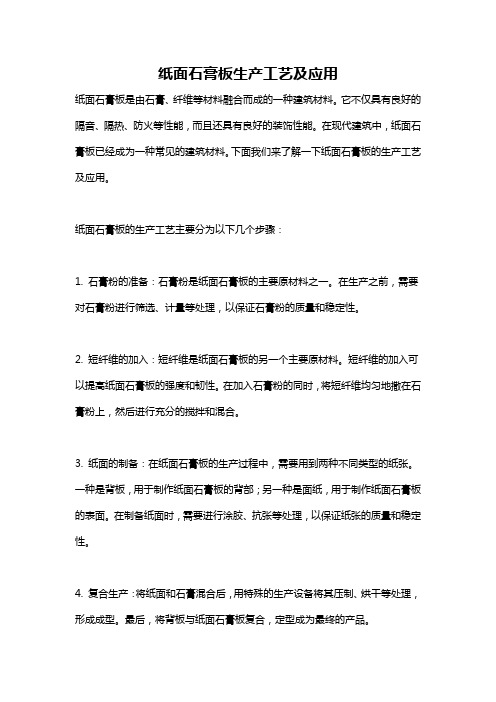
纸面石膏板生产工艺及应用纸面石膏板是由石膏、纤维等材料融合而成的一种建筑材料。
它不仅具有良好的隔音、隔热、防火等性能,而且还具有良好的装饰性能。
在现代建筑中,纸面石膏板已经成为一种常见的建筑材料。
下面我们来了解一下纸面石膏板的生产工艺及应用。
纸面石膏板的生产工艺主要分为以下几个步骤:1. 石膏粉的准备:石膏粉是纸面石膏板的主要原材料之一。
在生产之前,需要对石膏粉进行筛选、计量等处理,以保证石膏粉的质量和稳定性。
2. 短纤维的加入:短纤维是纸面石膏板的另一个主要原材料。
短纤维的加入可以提高纸面石膏板的强度和韧性。
在加入石膏粉的同时,将短纤维均匀地撒在石膏粉上,然后进行充分的搅拌和混合。
3. 纸面的制备:在纸面石膏板的生产过程中,需要用到两种不同类型的纸张。
一种是背板,用于制作纸面石膏板的背部;另一种是面纸,用于制作纸面石膏板的表面。
在制备纸面时,需要进行涂胶、抗张等处理,以保证纸张的质量和稳定性。
4. 复合生产:将纸面和石膏混合后,用特殊的生产设备将其压制、烘干等处理,形成成型。
最后,将背板与纸面石膏板复合,定型成为最终的产品。
纸面石膏板的应用非常广泛。
它主要用于室内隔断、天花板、墙面等装饰和隔音隔热等方面。
具体应用领域包括:1. 室内隔断:纸面石膏板具有良好的防火、隔音和隔热性能,非常适合用于室内隔断。
它可以有效地隔离不同的房间,创造舒适的居住和工作环境。
2. 天花板:纸面石膏板的质地轻盈,安装方便,可以使用各种造型设计,呈现出美观的视觉效果。
它还可以通过加入吸声材料等处理,增强其隔音隔热性能。
3. 墙面装饰:纸面石膏板的表面可以进行各种不同的装饰处理,如喷涂、贴壁纸等。
它不仅可以在视觉上提升房间的美观度,还具有保温和噪声隔绝等功能。
4. 其他装饰:除了以上应用领域外,纸面石膏板还可以用于其他的装饰方面,如柜子、石膏线条、壁板等。
这些产品可以温和而有效地点缀和丰富空间装饰。
总之,纸面石膏板是一种具有多种功能的优质建筑材料。
纸面石膏板生产工艺技术-石膏芯凝固和强度提高
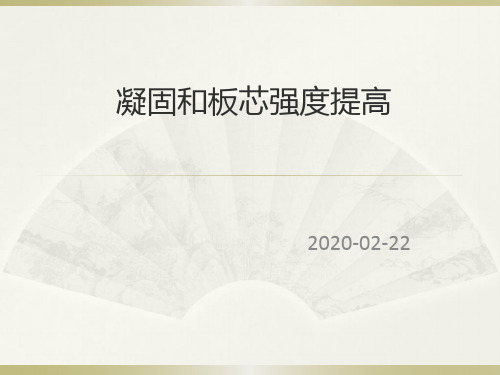
凝固和水合测试
凝固测试
薄刀片法 拇指法 – 参考一定距离用拇指感觉板的硬度 维卡仪 –初凝和终凝 撕纸光洁度
水合测试
石膏浆温度上升曲线 – 在线和离线测试 在最短烘干机入口时间下取石膏浆或湿板放入异
丙醇中,取石膏用于石膏相分析,判断水合效果。 板芯分析-进入干燥机的前缘和后缘 石膏芯强度测试
聚合物工艺可能在将来会是稳定的添加剂
影响强度的杂质
天然石膏Natural Gypsum
大多数的天然杂质不影响石膏芯强度 可溶性盐会消弱石膏芯和护面纸之间的
粘结力 白云石碳酸盐在煅烧炉中分解生成碱性
石膏浆,降低会强度 过烧产生的有机污染物会延缓并导致强
度损失 湿废料分解产生的污染物会导致强度损
过多使用促凝剂会产生过多的小晶体,从 而导致石膏板偏软。提高促凝剂的质量 (增加表面积等)以降低促凝剂的用量。
其它促凝剂
大量的无机酸 氯化物 硝酸盐 大多数硫酸盐和双硫酸盐 硫酸钾“钾”(K2SO4)是最常见
的可溶性化学促凝剂
缓凝剂
由于缓凝剂对晶体形状的影响,使用 缓凝剂通常会导致石膏芯强度的降低
失
影响强度的杂质
合成或副产品石膏中的杂质即使在非 常低的水平下也会导致强度损失
通常脱硫石膏比较正常,但过量氯离 子会降低强度。副产品石膏含有一系 列影响强度的杂质
磷石膏含有磷酸盐和磷酸 柠檬石膏中含有柠檬酸(强力缓凝剂和减
强剂)
大多数杂质通过改变晶体形状和降低 晶体之间的粘结力而导致强度损失
监测石膏芯密度与石膏芯抗压强度 的关系及与工艺效率的关系
板芯强度测试
石膏芯强度提高
强度取决于石膏晶体之间的链接互锁和结合 力
纸面石膏板生产工艺技术-生产过程简介
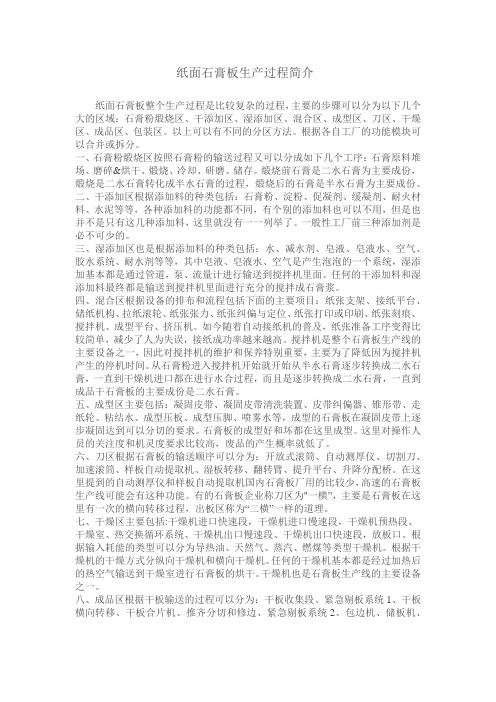
纸面石膏板生产过程简介纸面石膏板整个生产过程是比较复杂的过程,主要的步骤可以分为以下几个大的区域:石膏粉煅烧区、干添加区、湿添加区、混合区、成型区、刀区、干燥区、成品区、包装区。
以上可以有不同的分区方法。
根据各自工厂的功能模块可以合并或拆分。
一、石膏粉煅烧区按照石膏粉的输送过程又可以分成如下几个工序:石膏原料堆场、磨碎&烘干、煅烧、冷却、研磨、储存。
煅烧前石膏是二水石膏为主要成份,煅烧是二水石膏转化成半水石膏的过程,煅烧后的石膏是半水石膏为主要成份。
二、干添加区根据添加料的种类包括:石膏粉、淀粉、促凝剂、缓凝剂、耐火材料、水泥等等,各种添加料的功能都不同,有个别的添加料也可以不用,但是也并不是只有这几种添加料,这里就没有一一列举了。
一般性工厂前三种添加剂是必不可少的。
三、湿添加区也是根据添加料的种类包括:水、减水剂、皂液、皂液水、空气、胶水系统、耐水剂等等,其中皂液、皂液水、空气是产生泡泡的一个系统,湿添加基本都是通过管道,泵、流量计进行输送到搅拌机里面。
任何的干添加料和湿添加料最终都是输送到搅拌机里面进行充分的搅拌成石膏浆。
四、混合区根据设备的排布和流程包括下面的主要项目:纸张支架、接纸平台、储纸机构、拉纸滚轮、纸张张力、纸张纠偏与定位、纸张打印或印刷、纸张刻痕、搅拌机、成型平台、挤压机。
如今随着自动接纸机的普及,纸张准备工序变得比较简单,减少了人为失误,接纸成功率越来越高。
搅拌机是整个石膏板生产线的主要设备之一,因此对搅拌机的维护和保养特别重要,主要为了降低因为搅拌机产生的停机时间。
从石膏粉进入搅拌机开始就开始从半水石膏逐步转换成二水石膏,一直到干燥机进口都在进行水合过程,而且是逐步转换成二水石膏,一直到成品干石膏板的主要成份是二水石膏。
五、成型区主要包括:凝固皮带、凝固皮带清洗装置、皮带纠偏器、锥形带、走纸轮、粘结水、成型压板、成型压脚、喷雾水等,成型的石膏板在凝固皮带上逐步凝固达到可以分切的要求。
纸面石膏板生产工艺技术-石膏板厂热能消耗分析
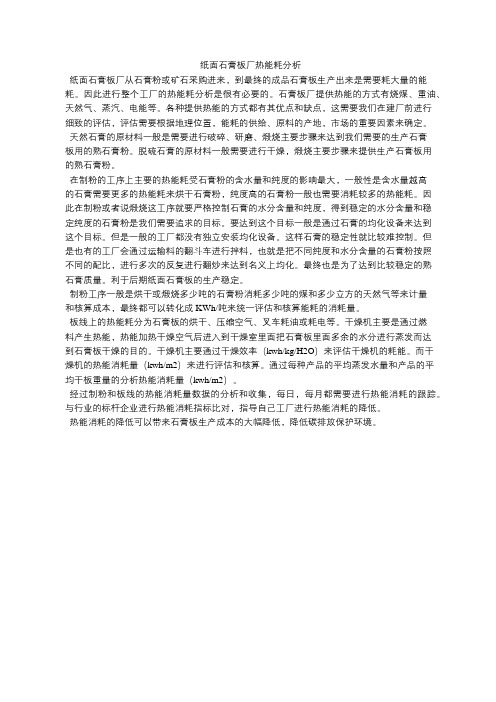
纸面石膏板厂热能耗分析纸面石膏板厂从石膏粉或矿石采购进来,到最终的成品石膏板生产出来是需要耗大量的能耗。
因此进行整个工厂的热能耗分析是很有必要的。
石膏板厂提供热能的方式有烧煤、重油、天然气、蒸汽、电能等。
各种提供热能的方式都有其优点和缺点,这需要我们在建厂前进行细致的评估,评估需要根据地理位置,能耗的供给、原料的产地,市场的重要因素来确定。
天然石膏的原材料一般是需要进行破碎、研磨、煅烧主要步骤来达到我们需要的生产石膏板用的熟石膏粉。
脱硫石膏的原材料一般需要进行干燥,煅烧主要步骤来提供生产石膏板用的熟石膏粉。
在制粉的工序上主要的热能耗受石膏粉的含水量和纯度的影响最大,一般性是含水量越高的石膏需要更多的热能耗来烘干石膏粉,纯度高的石膏粉一般也需要消耗较多的热能耗。
因此在制粉或者说煅烧这工序就要严格控制石膏的水分含量和纯度,得到稳定的水分含量和稳定纯度的石膏粉是我们需要追求的目标。
要达到这个目标一般是通过石膏的均化设备来达到这个目标。
但是一般的工厂都没有独立安装均化设备。
这样石膏的稳定性就比较难控制。
但是也有的工厂会通过运输料的翻斗车进行拌料,也就是把不同纯度和水分含量的石膏粉按照不同的配比,进行多次的反复进行翻炒来达到名义上均化。
最终也是为了达到比较稳定的熟石膏质量。
利于后期纸面石膏板的生产稳定。
制粉工序一般是烘干或煅烧多少吨的石膏粉消耗多少吨的煤和多少立方的天然气等来计量和核算成本,最终都可以转化成KWh/吨来统一评估和核算能耗的消耗量。
板线上的热能耗分为石膏板的烘干、压缩空气、叉车耗油或耗电等。
干燥机主要是通过燃料产生热能,热能加热干燥空气后进入到干燥室里面把石膏板里面多余的水分进行蒸发而达到石膏板干燥的目的。
干燥机主要通过干燥效率(kwh/kg/H2O)来评估干燥机的耗能。
而干燥机的热能消耗量(kwh/m2)来进行评估和核算。
通过每种产品的平均蒸发水量和产品的平均干板重量的分析热能消耗量(kwh/m2)。
纸面石膏板生产工艺
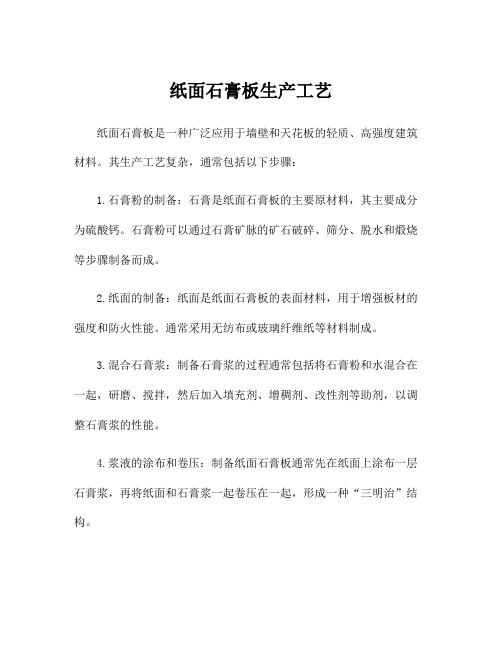
纸面石膏板生产工艺
纸面石膏板是一种广泛应用于墙壁和天花板的轻质、高强度建筑材料。
其生产工艺复杂,通常包括以下步骤:
1.石膏粉的制备:石膏是纸面石膏板的主要原材料,其主要成分为硫酸钙。
石膏粉可以通过石膏矿脉的矿石破碎、筛分、脱水和煅烧等步骤制备而成。
2.纸面的制备:纸面是纸面石膏板的表面材料,用于增强板材的强度和防火性能。
通常采用无纺布或玻璃纤维纸等材料制成。
3.混合石膏浆:制备石膏浆的过程通常包括将石膏粉和水混合在一起,研磨、搅拌,然后加入填充剂、增稠剂、改性剂等助剂,以调整石膏浆的性能。
4.浆液的涂布和卷压:制备纸面石膏板通常先在纸面上涂布一层石膏浆,再将纸面和石膏浆一起卷压在一起,形成一种“三明治”结构。
5.切割和硬化:将卷好的纸面石膏板切割成所需长度,并将其置于加热室中,在高温下进行脱水和硬化,以确保板材具有足够的强度和防火性能。
6.包装和存储:将制成的纸面石膏板进行包装和存储,以便将其运往各个建筑工地。
通常将板材分别打包成适当的大小和形状,以防止板材在运输过程中受到损坏。
总之,纸面石膏板的生产工艺需要经过多个步骤的加工和处理,在质量和性能上经过精心的调整和控制。
这使得纸面石膏板成为了一种优良的轻质建筑材料,为建筑工程的发展提供了重要的支持。
石膏板生产工艺流程

石膏板生产工艺流程简介一、工艺原理纸面石膏板是以建筑石膏为主要原料,掺入适量添加剂与纤维做板芯,以特制的板纸为护面,经加工制成的板材。
纸面石膏板具有重量轻、隔声、隔热、加工性能强、施工方法简便的特点。
纸面石膏板的生产技术是基于建筑石膏水化机理。
建筑石膏的主要成分为β型半水石膏,与水结合形成二水石膏,方程式表示为:CaSO 4·1/2H 2O +3/2H 2O CaSO 4·2H 2O 放热二、工艺流程简介待处理锯边封边堆垛图1 纸面石膏板生产工艺流程图1、熟料的制备:我们公司产品采用的主要原料是电厂产出的脱硫石膏,其主要成分为CaSO4·2H2O,其经过回转窑煅烧后可得到β型半水石膏为主建筑石膏,该过程用方程式表示为:加热CaSO4·2H2O CaSO4·1/2H2O +3/2H2O煅烧后的建筑石膏经冷却后,储存于大料仓,以备用。
2、配料部分:备料:①、改性淀粉、缓凝剂、纸浆、减水剂、水等原料经定量计量后放入水力碎浆机搅拌成原料浆,然后泵入料浆储备罐备用;②、发泡剂和水按比例投入发泡剂制备罐搅拌均匀,泵入发泡剂储备罐备用;③、促凝剂和熟石膏粉原料经提升输送设备进入料仓备用;配料:料浆储备罐中的浆料使用计量泵泵入到搅拌机,发泡剂使用动态发泡装置发泡后进入搅拌机,促凝剂和石膏粉使用全自动计量皮带称计量后进入搅拌机,然后所有主辅料在搅拌机混合成合格的石膏浆。
所有主辅料的添加都含括在自动控制系统中,随生产线速度的不同自动调节,以适应大规模、高速度的要求。
图2 纸面石膏板生产线立体形象示意图3、成型输送部分上纸开卷后经自动纠偏机进入成型机,下纸开卷后经自动纠偏机、刻痕机、震动平台进入成型机,搅拌机的料浆落到震动平台的下纸上进入成型机,在成型机上挤压出要求规格的石膏板,然后在凝固皮带上完成初凝、在输送辊道上完成终凝,经过定长切断机切成需要的长度(2400mm、3000mm或其它),经横向机转向,转向后两张石膏板同时离开横向机,然后使用靠拢辊道使两张板材的间距达到要求后,经分配机分配进入干燥机干燥。
纸面石膏板生产工艺技术-石膏的煅烧

第八章煅烧和煅烧炉1. 介绍煅烧是在高温下长时间保持一种物质直至其分解的过程,通常伴随着气体(通常是水或二氧化碳)的析出。
石膏经过煅烧,其煅烧产物在建筑工业中使用了几千年。
石膏被用来粉刷一些埃及金字塔的内墙,也被用来铺满周围的人行道。
煅烧过程的基本原料为硫酸钙二水合物(石膏):CaSO4.2H2O当石膏煅烧后石膏生产用于建筑行业,通常煅烧所得的是失去1½分子的水:CaSO4.2H2O heat CaSO4. ½H2O + 1½H2O 石膏技术课程的这个模块考察了煅烧过程中所涉及的工艺,过去煅烧石膏所用的设备和现代煅烧设备。
2.煅烧原理煅烧是在高温下长时间加热一种材料的过程。
这个过程导致物质随着气体(通常是水、二氧化碳等)的演化而分解。
煅烧的一个经典例子是从石灰石(碳酸钙的自然形式)中生成石灰(CaO),并伴随着二氧化碳(CO2)的过程。
CaCO3heat CaO + CO2在我们自己的工业中,我们关心的是石膏的热分解与水的演变:CaSO4.2H20 heat CaSO4.½H2OGypsum HemihydrateCaSO4Soluble or InsolubleAnhydriteCaSO4.2H2OResidual gypsum杂质杂质2.1 硫酸钙的相硫酸钙可以以以下几种形式存在:2.1.1 二水石膏石膏是硫酸钙(CaSO4)与两分子水(H2O)结合,化学上称为硫酸钙二水合物:CaSO4.2H2O除了被称为“石膏”,它还有许多其他的名称,其中一些与它所形成的特定晶体形状有关。
这些其他的名字包括:矿物石膏石石膏粉雪花石膏透明石膏纤维石膏化学石膏石膏副产品脱硫石膏烟气石膏2.1.2. 半水石膏半水石膏是硫酸钙结合½水分子和化学描述硫酸钙半水化合物:CaSO4.½H2O半水石膏在工业上也有许多名称,包括:石膏熟石膏煅烧石膏石膏粉烧石膏业界公认的半水合物有两种不同的物理形式:α-半水石膏和β-半水石膏而这将是更详细地描述, 值得注意的是在这一点上, α-半水石膏准备通过湿法煅烧石膏(如:高压釜, 煮盐溶液) 而β-半水石膏通常从干燥过程获得(如:煅烧炉, 回转窑等.)2.1.3. 无水石膏无水石膏是以无水形式存在的硫酸钙,即不含水。
纸面石膏板生产工艺技术-脱硫石膏

第四章脱硫石膏1. 介绍脱硫法(DSG)是电厂烟气脱硫(FGD) 工艺的产物。
在20 世纪的下半叶, “酸雨”已成为公认的问题,1988 年欧共体指令发布,要求从现有燃煤电厂二氧化硫的排放在应该减少20%,到21 世纪降低40% 以上。
当这些发电厂使用的煤中的硫被燃烧形成二氧化硫(SO2) ,二氧化硫与大气中的水结合形成硫酸(H2SO3) 时,就会产生酸雨。
SO2 + H2O = H2SO3为了除去二氧化硫,烟气用石灰石浆进行洗涤,然后氧化生成石膏:吸收SO2 + H2O = H2SO3中和H2SO3 + CaCO3 = CaSO3 + CO2 + H2O氧化CaSO3 + ?O2 + 2H20 = CaSO4.2H2O (gypsum)FGD 工厂的设计能力是每年减少28 万吨SO2 ,满负荷运行时每年将使用54 万吨石灰石生产80 万吨石膏。
每年可从该脱硫池中提取100 万吨石膏。
2.脱硫工厂以下详细介绍了FGD 工厂和工艺流程。
电厂烟气脱硫在过去十年中,人们越来越认识到有必要减少和控制燃烧矿物燃料的发电厂的二氧化硫(SO2) 排放量,从而减少酸雨的一种成分。
为此,发电厂为了改造足够的燃煤电厂的烟气脱硫(FGD), 以确保一个稳定的二氧化硫排放量下降通过剩余的世纪,因此建立一个提供FGD 设备的发电站。
.姚恒昌1大型燃烧车间成立欧洲经济共同体1988 年6月通过的《大型燃烧工厂指令》要求,到1993 年将现有工厂的二氧化硫排放量减少20% ,到1998 年减少40% ,到2003 年减少60%。
在烟气脱硫装置,由于其体积大,最有可能从烟气排放中脱除二氧化硫。
科学证据表明,排放的二氧化硫对土壤和地表水的酸度有一定影响; 它具有较长的剩余运行寿命,并且可以在现有的工厂配置中安装FGD。
此外,它与FGD 原料(石灰石)和副产品(石膏)市场的潜在来源有良好的地理位置,有足够的运输连接和任何必要改进的潜力。
- 1、下载文档前请自行甄别文档内容的完整性,平台不提供额外的编辑、内容补充、找答案等附加服务。
- 2、"仅部分预览"的文档,不可在线预览部分如存在完整性等问题,可反馈申请退款(可完整预览的文档不适用该条件!)。
- 3、如文档侵犯您的权益,请联系客服反馈,我们会尽快为您处理(人工客服工作时间:9:00-18:30)。
第九章熟石膏煅烧后的处理1. 介绍抹灰石膏是在建筑石膏的制造过程中研磨,以改变半水合物灰泥的和易性,并提供现场抹灰工人所需的性能。
在石膏板的制造过程中,有证据表明,煅烧后的研磨可以带来更大的分散性和提高成品板的硬度。
在许多地方,人们发现在使用前冷却石膏是有益的,既可以减少与热石膏储存有关的问题,也可以最大限度地提高板芯强度。
2. 建筑石膏在煅烧后的研磨在我国倾向于在建筑的砌体上使用底层抹灰,并在顶部使用面层抹灰。
类似地,石膏板有使用面层抹灰的趋势。
纵观世界上的其他国家,湿抹灰是一个单一的抹灰工艺要求,所需的特征是通过使用一系列的添加剂在配制的产品,和石膏板进行直接的面层抹灰后而会粘牢。
在欧洲大陆,许多建筑石膏是在旋转窑中生产的,而旋转窑是用直径约50毫米的石膏石提供的。
一旦煅烧,使用锤磨或类似设备将其磨成所需的粒度分布(PSD)。
可以使用管磨机研磨煅烧后熟石膏,因为这些磨机可以产生所需的粒度分布和颗粒形状,使我们的建筑石膏具有最佳的性能特点。
2.1管磨机粉碎过程中使用了许多不同类型的机器(通过粉碎和磨削来减小尺寸),管磨机属于“滚磨机”的范畴。
滚筒式磨机的显著特点是使用可占容器或壳体体积一半的松散棒或球。
当壳体旋转时,壳体的摩擦力使松动的杆或球(研磨介质)在壳体的上升侧被提起。
当杆状体或球状体达到一定的临界高度时,它们呈瀑布状,沿被提升的其它介质的自由表面向下滑落。
粉碎发生在杆或球之间的推挤在提升过程,在滚动的行动和冲击过程中下降。
滚筒式磨机是一种带棒的磨机,被称为“棒状磨机”,特别适用于将颗粒尺寸从25毫米减少到0.5毫米以下。
棒磨机包括一个外壳,通常圆柱形、旋转与轴水平和1½之间的长度和直径的2倍。
杆的长度比壳体的内部长度略短,这防止了杆在宽度上的定位。
在整个设备和里面的杆件成一定的角度,因此在壳体的进料端分离杆件的距离为进料颗粒的尺寸,在出料端分离杆件的距离为产品的尺寸。
因此,棒就形成了一个大圆锥体,它的作用就像一个筛子,允许更小的颗粒通过棒,直到它们在受到棒的作用时,到达小于其特定尺寸的空间。
滚筒式磨机是一种带球的磨机,称为“球磨机”或“管式磨机”。
球磨机的长径比不超过1.5,管磨的长径比超过这个数字。
球可以有多种尺寸,也可以是单一尺寸,它们可以由不同的材料制成。
在一定的速度和载荷条件下,球在壳体一侧向上运动时出现联锁现象,且相对静止。
球在升到顶部后,球从最上自由落下,或以自由落体的形式滑下,落在坡脚上。
球的碰撞、滑动和冲击,主要是在球的向下运动过程中,使球的中间物质发生粉碎,形成最终的颗粒形状。
球磨机(管式磨机)比其他滚磨机的主要优点是它能(在足够的时间内)生产几乎任何细度的材料。
但是需要注意的是,在研磨过程中产生的能量往往会产生热量,从而使我们的产品煅烧并释放水分。
球磨机对水分特别敏感,通常在处理含水量超过1%的材料时不会结块。
球磨机或管机的实际粉碎机理可分为两个阶段。
在第一个阶段,大的粒子被碰撞打破,在第二个阶段,小的粒子进一步减少了压缩所带来的两个球旋转接触的挤压作用。
它可以计算出击碎的活动,如果粒度大于0.035倍球直径,30毫米直径球用于我们的大多数管磨机,会击碎粒子直径小于1毫米的物料(我们的熟石膏是要这更好的)。
最大的磨削速率是在磨管机中实现的,其中装球量约为磨管机内部体积的50%。
将装球量降低到40%可使研磨率降低25%。
最佳的旋转速度是,当球在磨中最高的材料上运行时,球被抛到材料的顶端,在那里最大的颗粒往往会聚集。
这个最佳速度被发现在临界速度的50%到75%之间(临界速度是离心力作用于壳体上的最小速度,即离心力刚好与介质重量平衡的速度)。
为了获得最大的新表面积量,球磨机的最佳填充似乎比完全填充球与球之间的空隙要多一些所以等软材料的石膏和石膏产品,最优的灌装机是在1½倍球之间的必要填补这些间隙。
在许多应用中,磨管机被分为不同的部分,第一部分是大的球,中间部分是逐渐小的,直到最后一部分使用最小的球产生最好的研磨2.2 影响管式磨工艺的因素除了上述的理论的注意事项,一些实际的因素影响我们的管磨机的使用2.2.1 管磨机薄片所有的管状石膏都含有一定比例的片状物质,称为管磨机薄片。
这些薄片要么是直径约3毫米的压实薄片,其特征是中心较暗,在显微镜下观察时,可以看到中心凹处,颗粒被钢球击中而压实并变平。
这些薄片是在研磨过程中压实而成的。
第二种不同类型的薄片要大得多,形状不规则可达7毫米,它认为这些薄片是由堆积在表面的颗粒层形成的,要么是管状内衬,要么是钢球。
人们发现,这些薄片是由非常细小的颗粒组成的,这些颗粒通常在水中迅速分散,所以一般来说,它们在成品中不会产生任何质量问题。
唯一的例外是,如果薄片是由硬石膏岩或硬石膏颗粒压实的,因为这些颗粒在水中不会分解,并会引起工作性能的投诉。
2.2.2 磨机速度研磨机的转速对研磨效率有相当大的影响,所以我们将考虑在不同的研磨速度下会发生什么。
研磨速度和负载系数,即相对于研磨机的装载体积,决定了装载的研磨方式。
在低速或高负载情况下,小球会相互滚动。
它们以同心圆的路径上升循环,然后像级联一样下降,因此这种行为称为级联。
装料的球通常是一层一层地移动,每一层都有不同的速度,磨里的材料被压力和摩擦分解。
随着磨机转速的增加,钢球上升到一个更高的极限点,在这个极限点上,钢球从壳体表面被抛出,沿着抛物线轨迹自由下落,落在坡脚处的冲击上。
在这种情况下,研磨是通过冲击破碎完成的,这种类型的作用被称为奔流。
只要管磨机的速度低于临界转速,钢球将继续沿抛物线轨迹下落。
经计算,任意管磨机的临界转速(Nc)与管磨机的内半径(r cm)有关,通过:N c = 300 / r完全离心是在110%到115%的临界速度下完成的。
在实践中我们的管磨机速度变化在50%和75%之间的临界转速和一组结论可能会引起有关石膏的性能,增加管磨机速度约75%至80%的临界速度,之后负载将奔流,磨机变得不那么有效。
有如下结论:∙对于给定的球径和球磨时间,比表面积会随着球磨速度的增加而增加。
∙对于给定的球径和球磨时间,随着球磨速度的增加,对水的需求也会增加。
∙对于给定的球径和球磨时间,随着球磨速度的增加,管状薄片的数量会增加。
在球径、球装载和石膏装载的设定条件下,每一个管磨机都有一个最佳速度,在最短的时间内达到相关要求的性能。
水需求的增加是因为在球磨的原始材料中粒子比较小,虽然原始粒子及其合成的重量较小的粒子将是相同的,粒子的表面积会比原来的更大的粒子。
每个颗粒都必须被一层水包围才能产生浆液,所以比表面积大的石膏需要更多的水。
2.2.3球的大小和装载量在磨机恒定条件和恒速的情况下,可通过改变球的尺寸和载荷系数来影响球磨过程。
实验表明,在使用BG通常使用的尺寸的钢球时,保持球荷载体积恒定:∙对于给定的球磨速度和球磨时间,比表面随着球径的减小而增大。
∙对于给定的球磨速度和生产一个固定的比表面积,用水量随着球径的减小而减少。
在这种情况下,需水量的减少可能是粒径分布的函数,粒径分布又决定了石膏颗粒之间的空隙。
众所周知,孔隙空间越小,对水的需求量就越小,通过减小球的尺寸得到的磨粒越细,孔隙空间就越小,对水的需求量就越低。
∙对于给定的磨速和生产一个固定的比表面,管状薄片的数量随着球的尺寸减小而减少。
因此,球的尺寸越小,研磨就越细,顺便提一下,在其他因素保持不变的情况下,磨机内衬的磨损就会减少。
球的尺寸可以减小多少是有限制的,这取决于管壁内穿孔端板上孔的大小。
这些孔的作用是防止球漏入管柱输送系统,同时允许管状石膏快速通过穿孔,防止在管磨机上堆积。
载荷系数的定义是球装载量相对于磨机的体积,可以简单地通过将球移出或加入磨机来改变。
据计算,球磨的最大效果将在负载系数约为55%的情况下得到,但由于我们是为了产品质量而不是效率进行磨削,因此负载系数大大低于这个数字。
上述考虑和结论是指具有光滑衬里的磨机,它们被认为具有高的磨机产能。
还有其他几种类型的衬里型材可供选择,它们的使用会影响磨粉机的性能,可能还会影响磨粉石膏的性能。
2.2.4管磨机对老化石膏的影响实验表明,新煅烧的石膏比几天前的石膏需要更长的时间到达特定的比表面积。
这被认为是由于新煅烧的石膏通常含有可溶性硬石膏,而老石膏中含有少量的游离水作为研磨剂。
管状磨机研磨老化的石膏的一个次要影响是,由于存在少量的游离水分,在磨机或球装料上没有材料堆积。
2.2.5热/冷球磨一般情况下,在工厂运行条件下,由于磨机操作温度的原因,管磨机磨好的石膏的凝固时间将等于或长于原料的凝固时间。
由于我们的大多数生产工厂都是连续运转的,因此由于磨机内部摩擦产生的热量以及热石膏通过磨机的通道,在管壁中遇到的温度会升高。
这就产生了煅烧好的石膏中部分残留生石膏的效果,由于生石膏起到了促进剂的作用,生石膏水平的降低就产生了延长凝结时间的效果。
当管壁间歇运行并能在两次运行之间冷却时,管磨机研磨石膏的凝结时间比进料时间短。
这是因为管磨机在研磨过程中会暴露石膏的新鲜表面,而且由于磨机是冷的,石膏不会被煅烧,因此会起到促凝作用。
在我们的一些球磨作业中,冷却系统是绝对必要的,其中之一就是制造石膏板工厂促凝剂。
在这些操作中,我们将磨碎的石膏和另一种物质(通常是nansa南砂)研磨在一起,在石膏颗粒上形成表面涂层。
为了防止石膏煅烧,重要的是在两次生产之间允许管磨机进行冷却。
发现惰性体和钢球的混合物是生产这种促凝剂的最佳研磨介质。
对这种混合研磨介质进行球磨后的检验表明,球团体与磨内钢球几乎完全分离,在磨的进给端和出给端均有球团存在。
这似乎是一种机理,研磨石膏颗粒与(nansa南莎)混合体会产生有效的表面涂层。
2.2.6供料速度控制磨机是根据溢流原理工作的,也就是说,在一端进料会导致另一端的物料溢出。
因此,通过改变石膏的进给速度,我们可以控制成品的细度。
为了确保产品的一致性,我们必须准确地控制给磨机的进给,这是通过使用各种类型的控制设备来实现的。
这些包括:∙电子检测控制∙计量螺杆∙变速旋转阀必须特别注意进料控制设备,以确保进料的一致性和产品的一致性。
3. 石膏板厂煅烧后的石膏处理在石膏板厂里,目前在很多地方都在普遍使用。
所使用的研磨机的类型因地而异,通常取决于现有设备的可用性。
在有的工厂,使用球磨机和锤磨,也有使用精磨机的。
先进的在测试使用克里斯蒂和诺里斯锤磨机。
这些试验表明,在这些工厂中煅烧后研磨有以下几个优点:-∙提高强度(约10%)∙减少用水量,从而减少膏比(约0.8%)∙提高干燥机入口水化(2.3%)∙减少蒸发负荷(减少5kg/100m2)这些好处可以转化为生产率的提高或石膏板重量的减少使用锤磨机并不是用于这些目的的理想设备,其他带有内置分类器的磨机(例如精磨机)可能能够更好地控制粒度分布,这似乎是该系统最大限度地获益的关键4. 熟石膏的冷却在这一过程中,石膏的冷却有两个原因,一是为了使其能够储存在筒仓中而不遭受二次煅烧;二是为了降低石膏板生产时浆体的温度。