数控车床加工过程中尺寸精度的控制
确保数控车床精度的日常调整方法
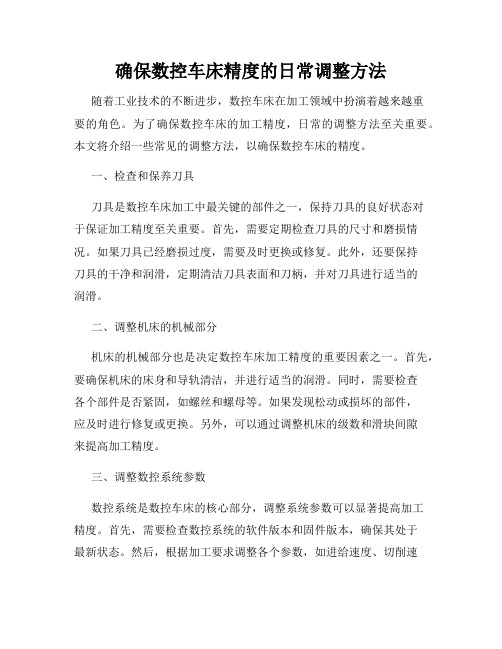
确保数控车床精度的日常调整方法随着工业技术的不断进步,数控车床在加工领域中扮演着越来越重要的角色。
为了确保数控车床的加工精度,日常的调整方法至关重要。
本文将介绍一些常见的调整方法,以确保数控车床的精度。
一、检查和保养刀具刀具是数控车床加工中最关键的部件之一,保持刀具的良好状态对于保证加工精度至关重要。
首先,需要定期检查刀具的尺寸和磨损情况。
如果刀具已经磨损过度,需要及时更换或修复。
此外,还要保持刀具的干净和润滑,定期清洁刀具表面和刀柄,并对刀具进行适当的润滑。
二、调整机床的机械部分机床的机械部分也是决定数控车床加工精度的重要因素之一。
首先,要确保机床的床身和导轨清洁,并进行适当的润滑。
同时,需要检查各个部件是否紧固,如螺丝和螺母等。
如果发现松动或损坏的部件,应及时进行修复或更换。
另外,可以通过调整机床的级数和滑块间隙来提高加工精度。
三、调整数控系统参数数控系统是数控车床的核心部分,调整系统参数可以显著提高加工精度。
首先,需要检查数控系统的软件版本和固件版本,确保其处于最新状态。
然后,根据加工要求调整各个参数,如进给速度、切削速度和回转精度等。
调整参数时,要谨慎操作,避免过于激进的调整导致加工精度下降。
四、定期校准设备定期校准数控车床是确保加工精度的重要手段之一。
校准可以包括对机床几何误差的测量和调整,对数控系统的测试和调整,以及对刀具的测量和校准等。
定期校准可以帮助发现和修复潜在的问题,提高机床的稳定性和精度。
五、培训操作人员最后,为了确保数控车床的精度,培训操作人员是必不可少的。
操作人员应接受专业的培训,了解数控车床的工作原理、操作方法和常见故障处理方法。
他们还应具备良好的操作习惯,如正确安装刀具、合理设置加工参数和保持机床的清洁。
结论确保数控车床的精度是一项复杂而重要的任务。
通过检查和保养刀具,调整机床的机械部分,调整数控系统参数,定期校准设备以及培训操作人员等方法,可以有效地提高数控车床的加工精度。
数控车床的对刀方法及修改刀补控制尺寸精度
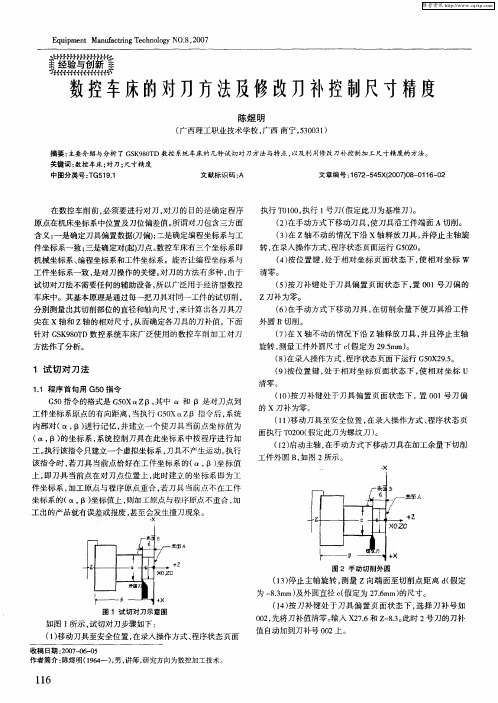
工出的产 品就有误差或报废 , 至会发生撞刀现象 。 甚
-
×
n
- n
厂 B 掌
} 1 丁 4 1 ×: 0
.
图 2 手 动 切 削 外 圆
1
外●~ 盥一 7 _
(3停止主轴旋 转 , 量 z向端 面至切削 点距离 d 假定 1) 测 (
《 装备制造技术)07 ) 0 年第 8 2 期
重复步骤(0 至(3 , 1 ) 1 )即可完成所有刀的对刀。 (5 如果 程序 首句为 G 0 0 Z 0 在 录人操作 方式 、 1) 5 X10 10, 程 序状态页面下执行 G O 0 Z 0 , OX1O 1 0使刀具 回到起刀点。
清零 。 (0 按 刀 补 键 处 于 刀 具 偏 置 页 面 状 态 下 , 0 1号 刀 偏 1) 置 0 的 X刀 补 为 零 。
1试 切 对 刀法
11 程 序 首 句 用 G 0指 令 . 5
G 0指令 的格式是 G 0 Zp, 中 和 p 是对 刀点 到 5 5X 其 工件坐标 系原点 的有 向距离 , 当执行 G 0 Z 指令后 , 5X p 系统
() 6 在手动方式下移动刀具 , 在切削余量 下使 刀具沿工件
外 圆 B切 削 。
( ) x轴不动 的情况下沿 z轴释放刀具 , 且停止主轴 7在 并 旋转 , 测量工件外 圆尺寸 c假定为 2 . m o ( 95 a r () 8 在录入操作方式 、 程序状态页面下运行 G 0 2 .。 5X 9 5 () 9 按位 置键 , 于相对坐标 页面状 态下 , 处 使相 对 坐标 u
在数控车 削前 , 必须要进行对 刀 , 对刀 的 目的是确定 程序 原点在 机床坐标系中位置及刀位偏差值。 所谓对刀包含三方面
数控机床加工误差原因及对策分析

数控机床加工误差原因及对策分析数控车床为零件加工的主要方式,对于零件加工具有较高的自动化水平,但是就实际情况来看,零件加工经常会因为设备自身或者操作不当等因素限制,而造成工件精度达不到专业要求,存在一定误差。
零件加工精度最终由机床刀具与零件间相对位移误差决定,因此需要确定加工误差存在的原因,以降低误差为面对,采取措施进行优化。
本文选择经济性数控机床为对象,就其加工误差与优化对策进行了简要分析。
标签:数控机床;加工误差;补偿0 引言数控机床零件加工经常会因为各项因素的影响而出现误差,即加工后零件实际几何参数与设计几何参数间存在一定偏差,导致零件精确度不能满足设计要求,最终只能作为不合格或者废品处理。
以提高数控机床加工精确度为的目的,需要对各类加工误差原因进行分析,有针对性的采取措施进行处理,对存在的误差进行有效补偿。
1 数控机床加工误差分析经济性数控车床对零件的加工,应用为步进电机开环伺服系统或者半闭环伺服系统来驱动刀具,在这个过程中就会因为受各项因素的影响而存在加工误差。
一方面,数控机床自身因素。
主要是因为数控机床所用构件精确度较低,以及机床装配过程中存在误差,导致零件加工后精确度达不到设计要求。
针对此种误差原因,一般可以就高精度零部件进行更换,以及在装配环节做好控制,争取提高机床自身精确度。
另外,对于部分技术能力可以达到要求的企业,还可以选择对步进电机构成的开环伺服系统进行适当的改造,使其成为闭环伺服系统,来提高零件加工精度[1]。
另一方面,工艺操作因素。
部分零件在加工过程中,会因为机床以及零件本身的热变形,造成切削、振动、装夹、磨损等细节存在误差。
想要对此类误差进行补偿,需要建立补偿模型在CNC系统内补偿,实施难度比较大,对提高数控机床零件加工精确度需要重点研究。
2 数控机床加工误差原因与对策分析2.1 数控机床自身原因2.1.1 控制系统误差(1)开环控制系统。
开环控制系统并未设置反馈装置,数控信号为单向流程,并不能对移动部件实际位移量进行测量与反馈,进而会影响对加工过程中所存误差的调整。
数控车床的几种精确对刀方法
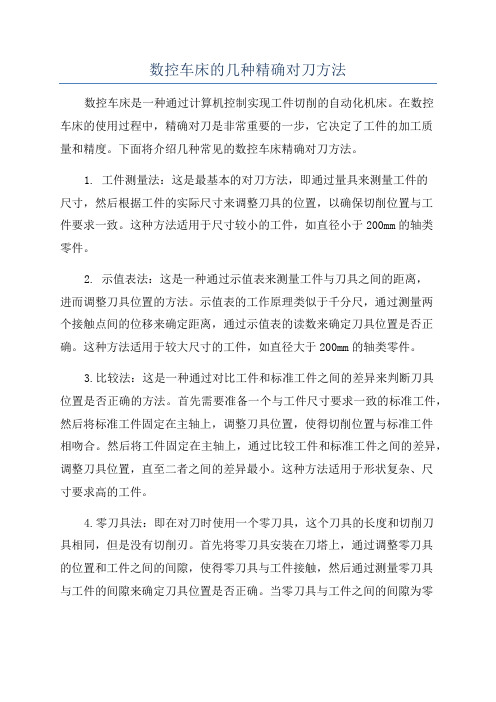
数控车床的几种精确对刀方法数控车床是一种通过计算机控制实现工件切削的自动化机床。
在数控车床的使用过程中,精确对刀是非常重要的一步,它决定了工件的加工质量和精度。
下面将介绍几种常见的数控车床精确对刀方法。
1. 工件测量法:这是最基本的对刀方法,即通过量具来测量工件的尺寸,然后根据工件的实际尺寸来调整刀具的位置,以确保切削位置与工件要求一致。
这种方法适用于尺寸较小的工件,如直径小于200mm的轴类零件。
2. 示值表法:这是一种通过示值表来测量工件与刀具之间的距离,进而调整刀具位置的方法。
示值表的工作原理类似于千分尺,通过测量两个接触点间的位移来确定距离,通过示值表的读数来确定刀具位置是否正确。
这种方法适用于较大尺寸的工件,如直径大于200mm的轴类零件。
3.比较法:这是一种通过对比工件和标准工件之间的差异来判断刀具位置是否正确的方法。
首先需要准备一个与工件尺寸要求一致的标准工件,然后将标准工件固定在主轴上,调整刀具位置,使得切削位置与标准工件相吻合。
然后将工件固定在主轴上,通过比较工件和标准工件之间的差异,调整刀具位置,直至二者之间的差异最小。
这种方法适用于形状复杂、尺寸要求高的工件。
4.零刀具法:即在对刀时使用一个零刀具,这个刀具的长度和切削刀具相同,但是没有切削刃。
首先将零刀具安装在刀塔上,通过调整零刀具的位置和工件之间的间隙,使得零刀具与工件接触,然后通过测量零刀具与工件的间隙来确定刀具位置是否正确。
当零刀具与工件之间的间隙为零时,即可确定刀具位置正确。
这种方法适用于切削刀具无法直接测量的情况下,如刀具形状复杂或刀具长度超过测量仪器范围的情况。
需要注意的是,对于数控车床的精确对刀方法,不同的机床可能会有不同的要求和适用范围,具体的对刀方法应根据机床的实际情况和工件要求来选择。
在对刀过程中,还需要注意对刀时机床的静止状态、对刀速度和对刀力度的控制,以确保对刀的准确性和稳定性。
此外,对于精度要求较高的工件,还可以采用自动对刀装置、光学对刀仪等专用设备来实现更精确的对刀。
数控车床加工精度控制的方法

数控车床加工精度控制的方法摘要:操作数控车床加工时,采用何种方法控制加工精度,是技术人员需要掌握的关键技能,本文以2022年全国职业院校技能大赛,数控综合应用技术赛项样题,自行小车中的关键零件车轮的加工为例,介绍了在数控车床上加工车轮零件时精度控制的方法。
同时对该方法的基本原理、具体操作和注意事项都进行了详细阐述。
关键词:数控车床;加工精度;方法引言本文以2022年全国职业院校技能大赛,数控综合应用技术赛项样题,自行小车中的关键零件车轮(如图1所示)的加工为例,介绍了在数控车床上加工车轮零件时精度控制的方法。
在样题中车轮零件为批量件,车轮零件加工精度控制的好坏将直接影响自行小车能否完成功能测试,行驶3m并通过2mm和4mm高的障碍,而加工车轮零件最难的是端面槽小径、同轴度的精度控制和防止车轮零件变形,所以控制好精度和防止车轮零件变形就已经成功了一大半。
竞赛任务书要求:①根据图纸要求完成4个批量赛件的加工;②根据评分标准完成评分内容的检测;③安全文明生产。
毛坯:φ60×240mm的45钢棒料。
刀具:外圆车刀、外圆切槽刀、φ14麻花钻、φ12整体硬质合金镗刀、加工范围φ20~φ45的断面切槽刀。
量具:游标卡尺、25~50千分尺、50~75千分尺、25~50公法线千分尺、深度游标卡尺、16~20内径三点千分尺、40~50内径三点千分尺、杠杆百分表及磁力表座×2。
机床及夹具:机床型号CK6150;三爪卡盘硬爪、软爪各一副。
通过对车轮零件图纸的分析可知,主要的目的是考察学生的工艺分析、机床操作、工量刀具的选择及使用、精度控制等综合能力。
图1 车轮图样一、车轮加工工艺及优化1.用硬爪夹持毛坯,伸出长度不少于50mm,钻孔孔深不少于90mm,平右端面,对刀(含外圆车刀、切槽刀、端面切槽刀、镗刀);2.粗加工外轮廓至Z-45mm处,粗加工右端内轮廓至Z-35mm处,如下所示;内孔的尺寸不便于测量,从而不利于精度控制。
数控车床加工过程中尺寸精度的控制

刀面与工件、 切屑产生强烈摩擦 , 使刀具磨损 。 当刀具 磨损达到一定值时 , 工件 的表面粗糙度值增大 , 切屑 颜色和形状发生变化 , 并伴有振动。刀具磨损将直接
影 响切 削 生产率 、 加 工质 量和 成本 。
3 刀具的制造误差及弹性变形
我们很多人都有这样的经历 , 就是在前一刀车削
会 影 响几 何 精 度 ( 如 零 件 变 形 时容 易 产 生 锥度 , 因为 远 离 卡盘 的位 置形 变 幅度 越 大 ) , 刀具 的强 度不 足 , 我
差 其中, 后两种误差是与工件和刀具 的定位 、 安装有 关, 和加 工本 身无 关 。要提 高加 工精 度减 小加 工误 差 ,
尺 寸精 度 是 指 加 工 后 的工 件 尺 寸 和 图纸 尺 寸 要
形 变 的最 终 原 因是 这些 对 象 的强 度 不 足 和切 削 力 太
大。
求相符合的程度 。 两者不相符合的程度通常是用误差
大小 来 衡量 。误 差 包括 加 工误 差 、 安 装误 差 和定 位 误
弹性形变会直接影响零件加工尺寸精度 , 有 时还
T O1 0 1 G O 0 X1 0 0 Z1 o o
X52 Z2
么在理上如果不考虑各种误差的话在第一次精加
工后工件的尺寸 比图纸尺寸大 l m m , 然后把 x磨损值
由l m m改为 0 m m, 进行第二次精加工 , 就得到了工件
的最后 尺寸 。
当然 第 一 次 精 加 工 后工 件 的实 际 尺 寸 不 一定 恰
技 经 济市 场
数控 车床加 工过程 中尺寸精度 的控 制
寇录峰 ,袁彦辉
( 驻 马店农 业 学校 , 河 南 驻马 店 4 6 3 0 0 0 )
数控车加工中外圆尺寸的控制方法
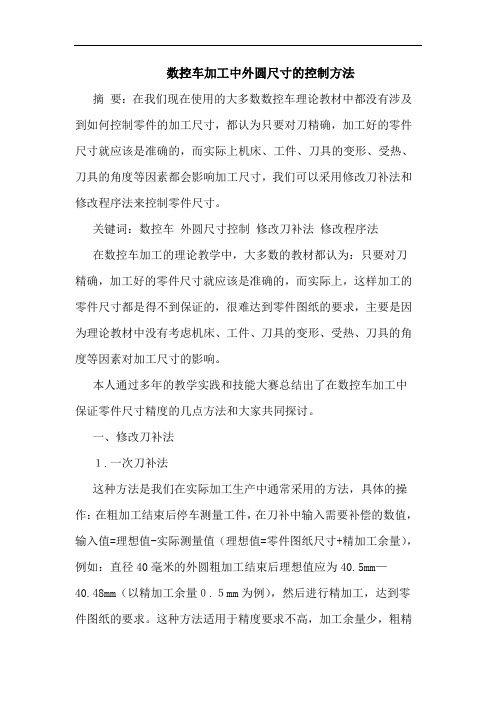
数控车加工中外圆尺寸的控制方法摘要:在我们现在使用的大多数数控车理论教材中都没有涉及到如何控制零件的加工尺寸,都认为只要对刀精确,加工好的零件尺寸就应该是准确的,而实际上机床、工件、刀具的变形、受热、刀具的角度等因素都会影响加工尺寸,我们可以采用修改刀补法和修改程序法来控制零件尺寸。
关键词:数控车外圆尺寸控制修改刀补法修改程序法在数控车加工的理论教学中,大多数的教材都认为:只要对刀精确,加工好的零件尺寸就应该是准确的,而实际上,这样加工的零件尺寸都是得不到保证的,很难达到零件图纸的要求,主要是因为理论教材中没有考虑机床、工件、刀具的变形、受热、刀具的角度等因素对加工尺寸的影响。
本人通过多年的教学实践和技能大赛总结出了在数控车加工中保证零件尺寸精度的几点方法和大家共同探讨。
一、修改刀补法1.一次刀补法这种方法是我们在实际加工生产中通常采用的方法,具体的操作:在粗加工结束后停车测量工件,在刀补中输入需要补偿的数值,输入值=理想值-实际测量值(理想值=零件图纸尺寸+精加工余量),例如:直径40毫米的外圆粗加工结束后理想值应为40.5mm—40.48mm(以精加工余量0.5mm为例),然后进行精加工,达到零件图纸的要求。
这种方法适用于精度要求不高,加工余量少,粗精加工的切削深度相差不大,冷却充分,机床、刀具工件刚性较好的场合。
2.两次刀补法对于加工精度要求较高,切削余量较大,机床、刀具和工件的刚性不好,粗精车产生的切削力相差较大的情况下,采用一次刀补法往往还不能保证零件的加工要求,这时我们通常采用两次修改刀补的方法。
通过第一次修改刀补,消除了由于粗加工切深较大而引起的变形,从而保证第二次精加工的尺寸。
具体操作如下:在粗加工结束后停车,直接在刀补中输入0.3(以精加工余量0.5mm为例,要求对刀误差不大于0.1mm),进行精加工,精加工结束后停车测量工件,在刀补中输入需要补偿的数值,输入值=零件图纸尺寸-实际测量值(以外圆直径为40mm为例,第一次精加工结束后直径40mm处的理想值应为40.3mm),此时如测量值为40.2mm,说明此时误差0.1mm,需输入40-40.2=0.2mm,然后再进行精加工,达到零件图纸的要求。
外圆尺寸精度的控制(数控车)
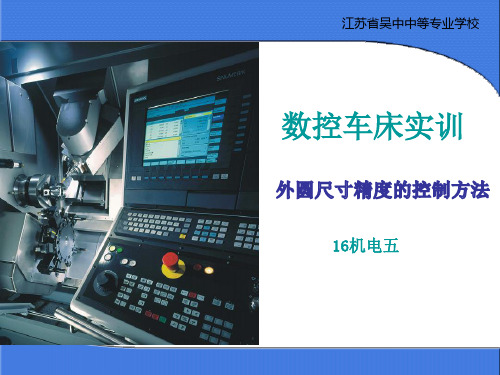
对于加工精度要求较高,切削余量较大,机床、刀具和 工件的刚性不好,通过一次精加工控制不了尺寸的,我们通 过两次精加工控制尺寸。
江苏省吴中中等专业学校
G71 G71
U 3 P Q
R
X方向 的精加 工余量
U 0.5mm W F
粗加工之前在 磨耗X方向留 余量0.5mm 粗加工完的尺寸比 实际尺寸大1mm
Φ 48.02
检 测 结 果
Φ 47.97 Φ 47.85 Φ 47.99
Φ 48.015
江苏省吴中中等专业学校
用数控车床加工外圆,加工误差是可以控制的,只要我 们加工前把应该出现的问题考虑周全并解决,加上合理的尺
寸控制方法就能把尺寸精度控制在合理的范围之内。
江苏省吴中中等专业学校
二、外圆尺寸精度控制的控制方法
江苏省吴中中等专业学校
三、知识拓展
根据图纸 要求计算 出+输入 磨耗值和 程序修改 值是多少?
江苏省吴中中等专业学校
课堂小结 :
修改磨耗法控制外圆尺寸精度的步骤是什么?
1.对好外圆刀在对应的磨测量并计算+输入磨耗值 4.精加工并测量
测量计算 并修改程 序
江苏省吴中中等专业学校
请多指教!
江苏省吴中中等专业学校
我们以Φ 40的外圆为基准, 用修改磨耗的方法获得理 想尺寸,+输入磨耗值 =40-40.48=-0.48
Φ 43的+输入磨耗值 =43.52-43=-0.52 磨耗里已经减去0.48还 差0.05就在程序里减
江苏省吴中中等专业学校
O1002; T0101; M05; M03S1200; M00; G0X52; T0101 Z2; M03S1600 G71U2R0.2; G00X52; G71P1Q2U0.5W0.02F0.2; Z2; N1G01X40; G70P1Q2F0.1; Z-15; G00X52; X43; Z100; Z-25; M30 把Φ 43的基本尺 X50 寸改写成X42.95 N2G00X52; Z2;
经济型数控车床尺寸精度控制方法

尺 寸 精 度 误差 产生 的原 因和 控制 方法做 以下 阐述 , 以供 参
考。
2 . 4 切 削参 数选 用 经 济 型数 控 车没 有 恒 线速 度 进 给 功 能 ,加 工不 同 直径 的 台阶表 面 时切 削速 度 是 不 同的 ; 而
各 台阶表 面 的精 加 工 余量 也 不相 同。 这样 , 在 精加 工 不 同 2 . 1 数 控 系 统 经 济 型数 控 系统 采 用 开 环 控 制 系统 , 台阶表 面 时 , 刀尖 承 受 的切 削力 不 同 , 刀 尖 对 已加 工 表 面 其 机床 定 位 精度 不 高 , 无检 测 、 反 馈和 适 应控 制装 置 , 存在 的挤压 程度 也 不 同 , 导 致精 加工 不 同 台阶表 面 时膨 胀 变形 加 工 精 度不 高 的 问题 。特 别是 在加 工 批 量 产品 时 , 若 产 品 量 不 同。 所以, 不 同 台阶表 面尺 寸精 度会 有误 差。 这 少量 的 尺 寸精 度 要 求小 于 0 . O 1 mm、 圆度 要 求小 于 0 . 0 0 5 mm 时 , 误 差也 足 以对尺 寸精度 造 成影 响 , 特 别 是 当精 车余 量很 少 用 经济 型 数控 车将 无 法保 证加 工精 度。 时( 约 <0 . 1 mm ) , 这种 影 响会 更突 出。 2 . 2 数 控 机床 方面 机 床 本身 的 制造 和 安 装精 度 对加 3 数 控 车加 工 中控 制 尺寸 的方 法 工精 度 也 会造 成 影 响 : 机 床 主轴 精 度造 成 工件 圆 度和 直线
3 . 1 首 件 试切 法 在 加 工批 量 产 品时 ,首 件 产 品 由于
2 影 响数控 车 加工 尺寸 精度 的 因素
度超 差 : 刀 架 回转精 度造 成 刀具 重 复定 位 误差 。 滚珠 丝杠 对 刀误 差 等原 因 , 造 成工 件 误 差超 出工 件 工精度 。 加工要求 , 通 过 测 量 出工 件 的尺 寸误 差 值 , 然 后 将 刀 补 值 修 改一 个误 差量 , 使 其余 的工件 达到 图纸要 求。 保 证径 向 2 . 3 . 1 刀具 几何 形 状 对尺 寸精度 的影 响。刀 具在 切削 尺寸 方法 如下 : 过程中, 因切 削力 的作 用 , 对 已加工 表 面造 成挤 压 , 产 生膨 ①绝对坐标输入法。 根据“ 大减小 , 4 d J o 大” 的原则 , 在 胀 变 形 。 因此 , 精 车 刀 会选 择 较 大 的几 何 角 度 , 使 刀 刃锋 如 图 1所 示刀 补表 中修 0 0 1 —0 0 4处修 改 X 刀补 值 。如 :
解析数控车床加工精度的影响因素及提高措施
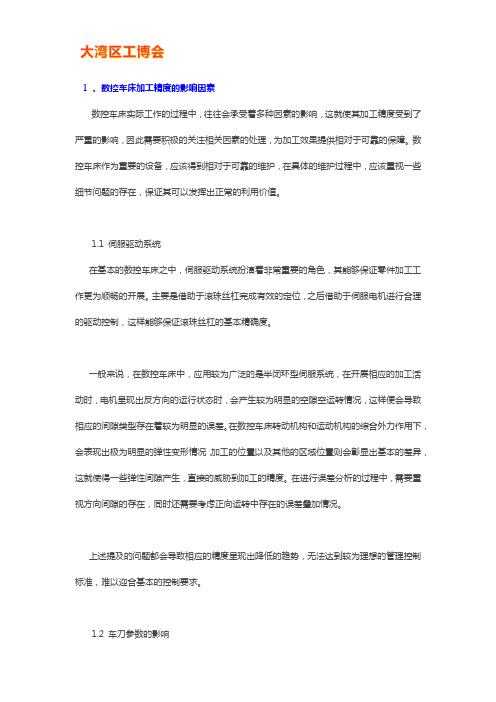
1 、数控车床加工精度的影响因素数控车床实际工作的过程中,往往会承受着多种因素的影响,这就使其加工精度受到了严重的影响,因此需要积极的关注相关因素的处理,为加工效果提供相对于可靠的保障。
数控车床作为重要的设备,应该得到相对于可靠的维护,在具体的维护过程中,应该重视一些细节问题的存在,保证其可以发挥出正常的利用价值。
1.1 伺服驱动系统在基本的数控车床之中,伺服驱动系统扮演着非常重要的角色,其能够保证零件加工工作更为顺畅的开展。
主要是借助于滚珠丝杠完成有效的定位,之后借助于伺服电机进行合理的驱动控制,这样能够保证滚珠丝杠的基本精确度。
一般来说,在数控车床中,应用较为广泛的是半闭环型伺服系统,在开展相应的加工活动时,电机呈现出反方向的运行状态时,会产生较为明显的空隙空运转情况,这样便会导致相应的间隙类型存在着较为明显的误差。
在数控车床转动机构和运动机构的综合外力作用下,会表现出极为明显的弹性变形情况,加工的位置以及其他的区域位置则会彰显出基本的差异,这就使得一些弹性间隙产生,直接的威胁到加工的精度。
在进行误差分析的过程中,需要重视方向间隙的存在,同时还需要考虑正向运转中存在的误差叠加情况。
上述提及的问题都会导致相应的精度呈现出降低的趋势,无法达到较为理想的管理控制标准,难以迎合基本的控制要求。
1.2 车刀参数的影响通常来讲,在数控车床的加工实践中,往往是借助于编程控制的基本手段落实车刀的调整,保证可以更加顺畅的开展零部件的切削工作,由此让其基本的形状符合相应的要求。
在车削加工的基本环节之中,车刀一般会反映出主偏角以及刀尖圆弧半径的基本数值,在对棒料进行适当的加工时,轴向的尺寸还是很容易产生一些误差问题,面对这样的情况应该做出合理的分析,判断这类误差和主偏角往往是呈现出一种反比的关系,当不断地增加相应的主偏角之后,相应的误差可以适当的降低,但是对比于刀尖圆弧半径来看,两者之间还是存在着正比的关联。
如果在具体加工的过程中车刀的参数发生了较为显著的变化,会使得相应的精度受到较为直接的影响。
数控车床轴类零件加工的精确度控制

数控车床轴类零件加工的精确度控制数控车床是一种高效的机械加工设备,可用于高精度的零件加工。
在数控车床上加工轴类零件时,精确度控制是非常重要的。
该文档将探讨数控车床轴类零件加工的精确度控制。
本文将从以下方面进行介绍:1. 数控车床轴类零件加工的基本要求2. 数控车床中影响精确度的因素3. 如何控制数控车床轴类零件的精度1. 数控车床轴类零件加工的基本要求在数控车床上加工轴类零件需要符合一些基本的要求。
首先,加工出的轴应该具有高精度和高质量。
其次,加工出的轴应该符合所需的尺寸和形状。
最后,加工过程应该具有高效性和节省时间。
2. 数控车床中影响精确度的因素在数控车床上加工轴类零件时,有许多因素会影响精度。
其中包括以下几个重要方面:1. 材料:轴材料必须具有一定的强度和稳定性,这样才能保证加工时的精度。
另外,当材料硬度较高时,可能会影响加工的精度。
2. 刀具:刀具是数控车床上非常重要的一个因素。
刀具类型、使用寿命等属性会影响加工的精度。
3. 机床参数:机床参数对加工精度也有很大影响。
例如,床身的刚性、主轴的精度、导轨的质量等等都会对整个加工精度产生影响。
4. 程序编程:数控车床需要通过程序实现精确的加工过程,因此程序编程的合理性对精度控制至关重要。
如果程序有错误,则可能导致加工不准确。
5. 环境因素:数控车床加工的环境因素,如温度和湿度,也会影响加工精度。
3. 如何控制数控车床轴类零件的精度为了控制数控车床轴类零件的精度,我们需要采取以下措施:1. 优化切削条件:切削参数包括刀具的选择、加工速度、进给率、切削深度等。
为了使加工达到最佳效果,应尽可能优化切削条件。
2. 优化加工技术:在加工过程中,应使用最先进的加工技术。
例如,应该尽可能使用工艺小切削,避免轴类零件受到过多的削除力。
3. 优化程序设计:程序设计应该尽可能合理化,尽可能减少加工中学习模式的重复。
4. 优化材料选择:在选择轴材料时,应尽量选择稳定性高的材料,以确保加工效果的一致性。
数控车床加工四大要求

飞舵五金
数控车床加工四大要求
在使用数据车床进行加工前,不仅要考虑车床还要考虑加工件等各方面因素,按要求加工才能发挥数控车床的最大作用。
下面给大家介绍飞舵数控车床加工四大要求。
一、材料与热处理要求:零件图样上给定的材料与热处理要求,是选择刀具、数控车床型号、确定切削用量的依据。
二、表面粗糙度要求:表面粗糙度是保证零件表面微观精度的重要要求,也是合理选择数控车床、刀具及确定切削用量的依据。
三、形状和位置精度的要求:零件图样上给定的形状和位置公差是保证零件精度的重要依据。
四、尺寸精度要求:分析零件图样尺寸精度的要求,以判断能否利用车削工艺达到,并确定控制尺寸精度的工艺方法。
不以规矩,不能成方圆。
在数控加工前后都要按要求操作,保证生产效率和工件精度,否则不仅影响生产,还会对车床造成损坏,得不偿失。
GSK988T数控车床刀尖半径及加工尺寸精度研究

GSK988T数控车床刀尖半径及加工尺寸精度研究作者:张志红来源:《山东工业技术》2018年第18期摘要:本文介绍了GSK988T系统数控车床加工零件时刀尖半径补偿及零件尺寸精度的保证方法。
分析了为什么要使用刀尖半径补偿,介绍了GSK988T系统数控车床后置刀架的刀沿位置,并说明刀尖半径补偿和零件尺寸精度的保证方法在数控车削加工中的应用情况。
关键词:GSK988T;刀尖半径补偿;尺寸精度DOI:10.16640/ki.37-1222/t.2018.18.0400 引言使用数控车床车削加工锥面时,必须将假设的刀尖点的路径作适当的修正,使之车削加工出来的工件能获得正确的尺寸,这种修正方法称为刀尖半径补偿。
此外,合理利用刀具补偿功能还可以简化编程,有效减轻操作者的劳动强度,提高加工效率。
本文以GSK988T数控系统为例,说明刀尖半径补偿与零件尺寸精度的保证方法的应用。
[1]1 刀尖半径补偿功能车削台阶面或端面时,对加工表面的尺寸和形状影响不大,但在端面的中心位置和台阶的清角位置会产生残留误差,如图1所示。
车削锥面时,不会影响锥度,但对圆锥大端直径和小端直径尺寸有影响,产生过切或少切现象,见图1。
车削圆弧面时,对圆弧半径和圆度有影响。
[2]车削凹圆弧,会使加工后的圆弧半径变大,其值=理论轮廓半径R+刀尖圆弧半径r;车削外凸圆弧时,会使加工后的圆弧半径变小,其值=理论轮廓半径R–刀尖圆弧半径r。
1.1 刀尖方位号在GSK988T系统数控车床中,对应每个刀具补偿号,都有一组偏置量X、Z,刀尖圆弧半径补偿量R和刀尖方位号TIP。
假想刀尖方位号共有10个(0-9),后置刀架数控车床车刀刀尖对应的方位编号如图2所示。
1.2 刀尖半径补偿的方法在GSK980TDc数控系统的系统面板上按下“刀补”键,即进入了刀具偏置磨损界面,如图5所示。
刀尖半径R值和刀尖方位号在刀具偏置磨损界面中设置。
在程序中使用G41/G42/G40指令进行刀尖半径补偿。
数控车床加工精度的影响因素及提高措施
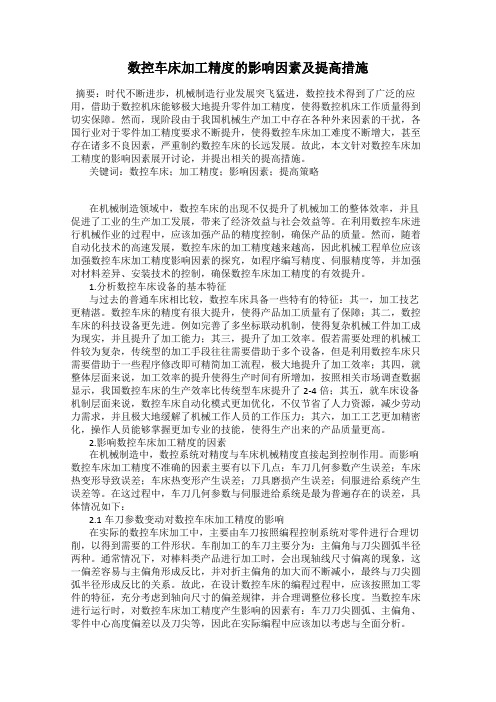
数控车床加工精度的影响因素及提高措施摘要:时代不断进步,机械制造行业发展突飞猛进,数控技术得到了广泛的应用,借助于数控机床能够极大地提升零件加工精度,使得数控机床工作质量得到切实保障。
然而,现阶段由于我国机械生产加工中存在各种外来因素的干扰,各国行业对于零件加工精度要求不断提升,使得数控车床加工难度不断增大,甚至存在诸多不良因素,严重制约数控车床的长远发展。
故此,本文针对数控车床加工精度的影响因素展开讨论,并提出相关的提高措施。
关键词:数控车床;加工精度;影响因素;提高策略在机械制造领域中,数控车床的出现不仅提升了机械加工的整体效率,并且促进了工业的生产加工发展,带来了经济效益与社会效益等。
在利用数控车床进行机械作业的过程中,应该加强产品的精度控制,确保产品的质量。
然而,随着自动化技术的高速发展,数控车床的加工精度越来越高,因此机械工程单位应该加强数控车床加工精度影响因素的探究,如程序编写精度、伺服精度等,并加强对材料差异、安装技术的控制,确保数控车床加工精度的有效提升。
1.分析数控车床设备的基本特征与过去的普通车床相比较,数控车床具备一些特有的特征:其一,加工技艺更精湛。
数控车床的精度有很大提升,使得产品加工质量有了保障;其二,数控车床的科技设备更先进。
例如完善了多坐标联动机制,使得复杂机械工件加工成为现实,并且提升了加工能力;其三,提升了加工效率。
假若需要处理的机械工件较为复杂,传统型的加工手段往往需要借助于多个设备,但是利用数控车床只需要借助于一些程序修改即可精简加工流程,极大地提升了加工效率;其四,就整体层面来说,加工效率的提升使得生产时间有所增加,按照相关市场调查数据显示,我国数控车床的生产效率比传统型车床提升了2-4倍;其五,就车床设备机制层面来说,数控车床自动化模式更加优化,不仅节省了人力资源,减少劳动力需求,并且极大地缓解了机械工作人员的工作压力;其六,加工工艺更加精密化,操作人员能够掌握更加专业的技能,使得生产出来的产品质量更高。
数控车床加工零件尺寸误差原因及调整办法

– 189 –《装备维修技术》2019年第4期(总第172期)doi:10.16648/ki.1005-2917.2019.04.163数控车床加工零件尺寸误差原因及调整办法倪磊(江苏省东海中等专业学校,江苏 连云港 222300)摘要: 数控车床是机械加工中常用设备,其加工出的产品尺寸准确性如何进行保证?尺寸误差产生后如何进行调整?本文指出了使用刀具长度补偿和程序补偿两种方法调整尺寸,并强调了操作人员素养的重要性。
关键词: 数控车床;加工零件;尺寸精度;调整办法在现代化制造业中数控机床占据着重要地位,它的先进程度及加工的产品尺寸精度直接决定着机械设备的使用性能,拥有高性能机械设备的制造业,可以大幅度提升国家总体经济实力。
数控车床是支撑起现代化制造业支撑柱中的一根,它担负着大量设备零件的加工制造,零件尺寸精度的控制是我们技术人员要着重掌握的。
我们从零件产生加工误差的原因进行分析,研究如何解决并避免再次发生。
数控车床主要加工回转类零件,大部分零件主要构成要素有孔、外圆、槽、螺纹。
下面我将从数控车床加工原理、数控车床加工误差产生原因、误差调整办法这三个方面进行研究。
1. 数控车床加工原理数控车床是利用CNC 装置控制刀架的移动和主轴旋转将工件加工出来。
在数控车床加工零件前,工艺人员需要分析图纸编制加工工艺及程序,调试人员将程序输入到数控车床控制系统中,经过操作人员调试,将工件加工出来。
零件加工过程中,主轴带动工件旋转,伺服系统在数控装置发出的指令控制下带动刀具加工工件,操作人员进行零件尺寸检测并利用补偿功能修正尺寸。
2. 零件加工产生误差的原因数控机床在加工零件时,零件尺寸精度会受到机床刚性、工件变形、刀具磨损等因素的影响,在加工过程中我们要分析原因并予以解决。
2.1 加工刀具磨损影响加工精度数控车床在加工零件时,刀具会有磨损过程。
在加工外圆时,刀具磨损后外圆尺寸会增大,进而造成尺寸超差。
在加工内孔过程中,刀具磨损后内孔尺寸会变小,造成尺寸超差。
浅析数控车床的加工精度

浅析数控车床的加工精度摘要:数控车床作为一种重要的加工设备,其加工精度直接影响到工件的质量和精度要求。
本文通过对数控车床的加工精度进行浅析,探讨了影响加工精度的因素,并提出了提高加工精度的方法与措施。
旨在为数控车床的加工精度提升提供一定的理论支持和实践指导。
关键词:数控车床;加工精度随着制造业的发展,数控车床作为一种高效、精确的加工设备,被广泛应用于各个领域。
而加工精度作为衡量数控车床性能的重要指标,对于满足工件的精度要求具有关键意义。
一、数控车床的加工精度概述数控车床加工精度是指在数控车床上进行加工过程中,工件达到的尺寸、形状和位置的精确程度。
它是衡量数控车床加工质量的重要指标之一。
随着工业技术的不断发展,数控车床在各个领域得到了广泛应用,而加工精度的提高也成为了人们关注的焦点。
首先,尺寸精度是数控车床加工中的一个重要方面。
在工件加工过程中,尺寸精度的高低直接影响着工件能否符合设计要求。
要提高尺寸精度,可以通过控制切削量、刀具和刀具夹持方式、工件夹紧方式等来实现。
只有确保这些因素的合理选择和控制,才能保证工件加工后的尺寸与设计要求之间的偏差尽可能小。
其次,形状精度也是数控车床加工中不可忽视的一点。
在实际应用中,工件的形状往往要求具备一定的几何精度,例如平面度、圆度、圆柱度等。
为了提高形状精度,可以采取优化工艺参数、选择合适的刀具和夹具、控制加工温度等措施。
通过这些方式,能够有效减小工件加工后形状与设计要求之间的偏差,确保工件的几何形状达到精确的要求。
此外,位置精度也是影响数控车床加工精度的重要因素之一。
位置精度主要指工件上各个特定点之间的相对位置精度,例如平行度、垂直度、同轴度等。
要提高位置精度,可以通过优化工艺参数、提高机床刚性、加强夹紧与定位等来实现。
只有确保工件在加工过程中的稳定性和精度,才能保证位置精度的提升。
最后,表面粗糙度也是数控车床加工精度的重要方面之一。
工件表面的光洁程度对于某些特定工件的功能和装配要求有着重要影响。
基于数控车床加工精度的影响因素及提高对策探析

基于数控车床加工精度的影响因素及提高对策探析摘要:数控机床加工零部件方便快捷,节省人力并且更为高效。
影响零部件的质量因素有很多,除了工艺因素、操作技巧之外更主要的是数控机床的加工精度。
想要提高数控机床加工的精度就要对影响精度的因素给予控制,本文对影响数控车床精度的因素进行了分析,并提出了一些方法和措施为提高数控车床的加工精度起到了一定的指导作用。
关键词:数控车床加工精度因素分析0.前言在机械制造的发展过程中,数控车床的出现无疑是最让人欣喜的事情。
数控车床一出现就得到了制造业的广泛关注同时也被广泛的使用。
作为先进的制作加工仪器,数控车床不仅是为机械制造业提供了便利,节约了大量的人力劳动;还同时创造出了更为丰富的社会、经济价值。
数控车床在加工制作零件的过程中,对加工精度的要求和控制直接关系到生产出的产品质量。
制造业的不断前进和发展推动着产品制作的自动化进程,也不断提升着对制作产品的品质新要求,要想保证产品质量就必须相应提高数控车床制造加工的精度。
数控车床在制造加工零部件时的加工精度主要是由车床的精度、编程精度、伺服精度以及插补精度等因素共同来决定。
除了这些主要的影响因素以外,数控车床制作加工的精度还要受到很多外界环境因素的影响,比如说材料质地、制造过程、安装水平、检测技术、控制手段、环境等。
不管是内部因素还是外部环境影响,每一个小小因素差异或是控制不到位都会是造成数控车床制造加工出现误差的原因。
因此,要想保证生产的零件加工质量就必须对数控车床加工过程给予合理控制,对能够影响车床加工精度的影响因素进行综合分析,找出能够影响车床精度的主要影响因素。
除了要加强对影响因素的分析控制之外还要掌握一些数控车床加工操作中的技巧和方法有效的避免精度误差的出现。
1.影响数控车床加工精度的因素分析影响数控车床制作加工的因素有很多,不仅仅只有机床的内部因素还包括了一些外部影响因素。
数控车床出现精度偏差主要影响制作零部件本身的尺寸和形状。
数控车如何确定加工精度
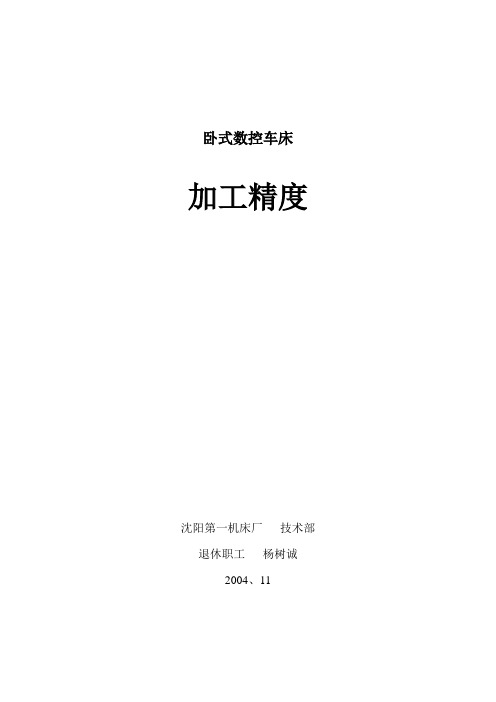
卧式数控车床加工精度沈阳第一机床厂技术部退休职工杨树诚2004、11在制定工艺方案、审核用户提供的零件时,能不能加工以及如何加工,要由两方面确定:一是加工件的尺寸,形状和材质;二是待加工零件各部位的尺寸精度;成批加工稳定性要求;形位公差和粗糙度要求、本文探讨后一个问题。
一、尺寸精度:JB/T 9871-1999《金属切削机床精度等级》3、4节中有这样的叙述:“相对精度等级为P级的圆柱面加工机床,如能达到IT6至IT7的公差,圆度、圆柱度达8级的加工精度,则一般应放在绝对精度等级Ⅴ级的位置上(例如卧式车床)。
”即标准中明确了卧式车床为相对精度P级(即普通精度等级)机床,绝对精度等级为Ⅴ级,加工精度为IT6~IT7。
数控车床CAK系列是在卧式车床的基础上发展起来的,它执行的JB/T8324、1-96《简式数控卧式车床精度》的主要项目与卧式车床相同,因此CAK系列加工精度应为IT6~IT7。
普及型数控车床CKS系列在主要部件制造精度、成品精度上较经济型数控车床有所提高,执行的GB/T16462-1996《数控卧式车床精度检验》也比《简式数控卧式车床精度》有所提高。
CKS系列加工精度应确定为IT6。
CKG6132数控高精度车床、CHH6125卧式车削中心应属于相对精度M级(精密级)或G 级(高精密级)机床,绝对精度为Ⅳ或Ⅲ级,其加工精度为IT5~IT6。
上述精度要求是标准或参照标准规定,也是写在样本、说明书中对用户的承诺,是必须达到的。
从发展趋势看用户对数控卧式车床加工精度有提高的要求:如汽车的主要部件制造精度在提高;有些用户要求以车代磨等。
我们应力争加工精度达到更高些。
前述加工精度为精车精度,半精车可达IT8~IT10,IT11~IT12粗车就可达到。
见表1。
数控卧式车床轴向加工精度能满足用户要求。
加工对象难以遇到轴向尺寸公差小于0.1mm的零件。
即使切槽宽度有公差要求、又不能用同一刀刃加工,达到精度要求也不困难。
数控车床控制尺寸精度的技巧

数控车床控制尺寸精度的技巧数控车床控制尺寸精度的技巧数控车削加工技术已广泛应用于机械制造行业,如何高效、合理、按质按量完成工件的加工,每个从事该行业的工程技术人员或多或少都有自己的经验。
下面yjbys店铺为介绍几例数控车削加工技巧。
希望对大家的工作有所帮助!1)修改刀补值保证尺寸精度由于第一次对刀误差或者其他原因造成工件误差超出工件公差,不能满足加工要求时,可通过修改刀补使工件达到要求尺寸,保证径向尺寸方法如下:a. 绝对坐标输入法根据“大减小,小加大”的原则,在刀补001~004处修改。
如用2号切断刀切槽时工件尺寸大了0.1mm,而002处刀补显示是X3.8,则可输入X3.7,减少2号刀补。
b. 相对坐标法如上例,002刀补处输入U-0.1,亦可收到同样的效果。
同理,对于轴向尺寸的控制亦如此类推。
如用1号外圆刀加工某处轴段,尺寸长了0.1mm,可在001刀补处输入W0.1。
2)半精加工消除丝杆间隙影响保证尺寸精度对于大部分数控车床来说,使用较长时间后,由于丝杆间隙的影响,加工出的工件尺寸经常出现不稳定的现象。
这时,我们可在粗加工之后,进行一次半精加工消除丝杆间隙的影响。
如用1号刀G71粗加工外圆之后,可在001刀补处输入U0.3,调用G70精车一次,停车测量后,再在001刀补处输入U-0.3,再次调用G70精车一次。
经过此番半精车,消除了丝杆间隙的影响,保证了尺寸精度的稳定数控,机床,模具设计,数控车床,数控技术3)程序编制保证尺寸精度a. 绝对编程保证尺寸精度编程有绝对编程和相对编程。
相对编程是指在加工轮廓曲线上,各线段的终点位置以该线段起点为坐标原点而确定的坐标系。
也就是说,相对编程的坐标原点经常在变换,连续位移时必然产生累积误差,绝对编程是在加工的全过程中,均有相对统一的基准点,即坐标原点,故累积误差较相对编程小。
数控车削工件时,工件径向尺寸的精度一般比轴向尺寸精度高,故在编写程序时,径向尺寸最好采用绝对编程,考虑到加工及编写程序的'方便,轴向尺寸常采用相对编程,但对于重要的轴向尺寸,最好采用绝对编程。
- 1、下载文档前请自行甄别文档内容的完整性,平台不提供额外的编辑、内容补充、找答案等附加服务。
- 2、"仅部分预览"的文档,不可在线预览部分如存在完整性等问题,可反馈申请退款(可完整预览的文档不适用该条件!)。
- 3、如文档侵犯您的权益,请联系客服反馈,我们会尽快为您处理(人工客服工作时间:9:00-18:30)。
数控车床加工过程中尺寸精度的控制
作者:孙许涛
来源:《魅力中国》2018年第22期
摘要:随着中国制造的崛起,数控机床在机械加工中使用频率也是越来越高,工件的精度将直接影响装备的精度及使用。
数控机床在加工过程中,会存在着一些不确定因素对加工精度的影响,例如机床精度的高低、工件安装的高低、刀具刃磨几何参数是否合理、切削用量的选用是否合理、切削力与切削热作用的大小、量具精度的高低与测量方法是否正确等等。
这些都会影响到工件加工的精度。
本文以GSK980T数控车床零件加工为例,研究了如何通过简单的方法来控制数控车床的加工精度,以达到加工成合格品的目的。
关键词:数控车床;加工精度;控制
一、精確对刀,直接控制尺寸
(1)可以利用对刀仪进行对刀,但是对刀仪价格昂贵,容易损坏;
(2)利用自动循环指令程序G94,可以切削工件后往外退刀,不刮伤工件而造成尺寸减小,对刀精度相对较高。
但操作相对来说比较烦琐。
(3)手轮摇动,使刀具慢慢在靠近工件,但要有一定的距离时,比如大约距离工件X、Z 方向3mm左右时,调到最小倍率档,轻摇进给,直至看到细微铁削飞出,退出道具,停主轴,锁机床进行测量。
(测量时候尽量不要用数显卡尺)
这样对刀后,在刀具没有磨损,机床控制精度可以的情况下可以直接加工零件,尺寸精度可以控制在±002mm范围内。
手动试切工件,Z向车进Z向退刀,X向车进X向退刀,至后建立坐标时直接修输入测量值,方便快捷的完成对刀。
但由于直进直退的切削,刀对工件会产生测量误差或者其他原因造成工件误差超出工件公差。
造成对刀的坐标不是准确的刀具位置,不能满足加工要求时,可通过修改刀具偏置即刀补值使工件达到尺寸要求。
二、修改刀补值保证尺寸精度
由于第一次对刀误差或者其他原因造成工件误差超出工件公差,不能满足加工要求时,可通过修改刀补使工件达到要求尺寸,保证径向尺寸方法如下:修改刀补值保证尺寸精度前,必须先在刀补页面001―004处使刀补值X、Z清零,刀没有偏置下再去设偏置。
(一)保证径向尺寸方法。
对于径向尺寸的控制,根据“先放大再减小”的原则,在刀补001-OO4处(也包括基准刀)修改。
譬如用 1号刀切削时工件径向尺寸放大+1mm,而 001处刀补原显示是 X0,则可输人
U1,加工一次后测量。
如直径测得Φ30.82(要求Φ30.00),这时减少1号刀补值,如U-0.82后再加工一次。
也可以在001刀补处输人X直径值,亦可收到同样的效果。
为避免机床或对刀精度问题,最好不要一次加工成型至要求值,即放在尺寸后测量所得的余量,也应该分两次以上来试切削来检验机床的精度。
(二)保证轴向尺寸方法。
对于轴向尺寸的控制,根据“长加大,短减小”原则,在刀补 001-004处修改。
如用2号刀加工某处轴段,加工后尺寸差-0.1mm(要求轴长10.45mm,测得10.35mm),而002处刀补显示是Z-420,可在 002刀补处输入W-0.1,使其刀补变为Z-430。
一般车前轴向可以不留余量,直接加工。
此方法来控制尺寸较简便,广泛适用于工厂中的加工。
三、绝对编程保证尺寸精度
编程有绝对编程和相对编程。
相对编程是指在加工轮廓曲线上,各线段的终点位置以该线段起点为坐标原点而确定的坐标系。
也就是说,相对编程的坐标原点经常在变换,连续位移时必然产生累积误差,绝对编程是在加工的全过程中,均有相对统一的基准点,即坐标原点,故累积误差较相对编程小。
数控车削工件时,工件径向尺寸的精度一般比轴向尺寸精度高,故在编写程序时,径向尺寸最好采用绝对编程,考虑到加工及编写程序的方便,轴向尺寸常采用相对编程,但对于重要的轴向尺寸,最好采用绝对编程。
四、修改程序和刀补并用控制尺寸
数控加工中,我们经常碰到这样一种现象:程序自动运行后,停车测量,发现工件尺寸达不到要求,尺寸变化无规律。
譬如用1号外圆刀加工一个三阶台阶轴工件,经粗加工和半精加工后停车测量,各轴段径向尺寸如下:φ30.06mm、φ23.03mm及φ16.02mm。
对此,笔者采用修改程序和刀补的方法进行补救,方法如下:
(一)修改程序
原程序中的X30不变,X23改为X23.03,X16改为X16.04,这样一来,各轴段均有超出名义尺寸的统一公差0.06mm;
(二)改刀补
在1号刀刀补001处输入U-0.06。
经过上述程序和刀补双管齐下的修改后,再调用精车程序,工件尺寸一般都能得到有效的保证。
上述五种控制尺寸方法分析
从理论上说,方法一的通过试切、测量,得到的对刀数据应是准确的,但实际上由于机床的定位精度、重复精度、操作方式、刀具的磨损等多种因素的影响,使得试切的精度是有限的,因此还须通过上述的另一些方法保证加工尺寸精确。
方法二方便快捷,也是多人采用的方法之一。
程序中加工首段必须有T0101指令,而对刀前一般要先清除刀补,除按刀补键中001-004中清零外,还须得程序段值介面下执行
G00U1W1运行一次来清刀补。
要不机床会带有前者操作留下的刀补值造成后者对刀时出现
G50 X385而位置显示的不是X38.50的值。
方法三的绝对值编程保证尺寸精度,刀补值偏置,放大零件尺寸在加工外圆时为正值
U+1,内孔时则为负值U-1,内外圆是相反刀补值加工的。
方法四修改程序和修改刀补并用,如在加工前改变X、Z值,会带来一定的计算量,加工后修改程序中值从而达到加工尺寸。
但是如操作者想再次使用此程序加工下同样零件时,必须再次修改正确的程序X、Z值才能加工。
除非加工中是变化无常的,各轴的尺寸值是不一致时才用此方法来进行控制。
方法是多样的,方法不是一成不变的。
所以我们可以多种方法一起采用,如方法一可以和方法二一起使用,方法三和方法四一起用的。
只要操作者思路清晰,不混乱的情况下而造成零件加工尺寸小就行了。
建议方法二是较方便快捷的控制方法。
总结,数控加工时的零件尺寸精度的控制的操作是数控加工的关键,明白刀具的走刀位置,坐标系建立与变更。
才能精确的加工出想要的尺寸精度。
在程序编制和实践加工中灵活运用各种尺寸控制方法,尽可能减少对刀误差,运用刀具补偿值及时调整或上述的方法加工中所出现的加工误差,有效地提高零件加工精度。