柔性化总拼技术在轿车焊装线上的应用
焊装智能柔性生产线规划

生产能力
年生产纲领(辆)
全年工作日 * 每日有效工作时间(
备注:节拍 CT= T*D*60*60/A 秒(节拍非整
数,舍去小数
点后面的数据,
取整)
D年工作有效 时间(多少
天),一般选
取295天(单 休+国家法定 节假日)
180000
辆 / h 29 .8辆 / h
h )* K 295 * 1 * 21 .5 * 0 .95
年生产纲领(辆)
180000
第10页,共22页
奇瑞商用车(安徽)有限公司
02 焊装智能柔性生产线规划
2.3 自动化生产线平面布局
建设二三级白车身分总成焊接岛(发舱总成、侧围总成等),实施多车型柔性化
生产,采用高速滚床实施主下线车身骨架的高效输送,同时采用空中大循环滑翘机构
AI《汽车制造业》未经允许严禁转载
总成
加强梁外板
(定位 焊)
顶盖总 成
STN
MB40 (涂胶)
MB50 MB60 (定位焊) (补焊)
MB70 (补焊)
MB80 (补焊)
MB90 MB100 MB110 MB1200
(机器人 (人工 (预留 弧焊) 弧焊) 在线检 验
(人工 检验)
工作描述:
1)机舱从分装直接调入UB10工位,前底板采用机器人抓手从置放台上去下,空中将搭接位置胶涂完,
每天有效工作
时间T:三班: (24-1.5(吃 饭)-(10/60) *2*3)*0.95 (设备可动率)
=20.425小时
生产线年产量
A;工位节拍 取整为120s。
AI《汽车制造业》未经允许严禁转载 工位节拍 全年工作日 * 每日有效工作时间( h)* 3600( s)* K 295 *1 * 21 .5 * 3600 * K s/ 辆 120 .8s/ 辆
发动机智能装配线的柔性化设计及应用探究

发动机智能装配线的柔性化设计及应用探究摘要:发动机是汽车的心脏,属于汽车不可缺少的构成部分,其质量会对汽车寿命、行驶安全产生直接影响。
发动机会应用到装配线进行装配生产,随着汽车需求量不断增加,发动机装配线生产压力逐渐提升,如何提升发动机装配线生产质量与效率,是需要重点关注的话题。
基于此,本文重点对发动机智能装配线的柔性化设计及应用进行分析,从发动机装配线生产特点入手,进行了发动机智能装配线的柔性化设计,提出发动机装配生产线的智能化应用,希望为相关人员提供参考借鉴。
关键词:发动机;智能装配线;柔性化设计引言我国社会经济不断发展下,为制造业发展带来了良好契机,智能制造已经成为制造业未来发展的主要趋势。
汽车发动机直接决定着汽车的性能,因此,汽车发动机生产线应不断优化改进,通过先进技术的不断应用,形成智能装配线,基于智能化技术下,提升发动机装配线生产效率,进一步提升发动机生产质量。
本文就发动机智能装配线的柔性化设计及应用相关内容进行分析,具体如下。
一、发动机装配线生产特点发动机制造过程中会涉及到较为复杂的制造工艺,装配环节尤为重要,若想保证发动机装配工作的良好开展,提升装配生产效率,应通过发动机装配线加以实现。
对于发动机总装环节而言,是一种离散型流水线制造模式,实际生产装配环节,缸体会从第一道工序按照一定顺序进行加工,经历过全部工序后,最终形成发动机产品。
装配环节较为复杂,经历工序较多,并且生产环节还应对所有数据信息进行详细记录。
发动机装配线生产特点主要体现在以下几方面:第一,对质量及标准要求高[1]。
若想保证发动机质量,装配线需要有高质量的控制能力,并且,当存在不合格发动机时,还能对其进行返修,这种情况下,会使整线控制程序更加负责。
第二,多机型混线以及柔性化生产。
发动机装配线应具备机型识别功能,可以获取不同机型的工作参数,针对性的进行设备控制,并且,对操作工做出指导,更好的开展装配工作。
此外,柔性化的好坏,会对装配线后续拓展、改造产生直接影响,可通过科学配置软件实现柔性化生产。
211246006_一种白车身总拼焊装柔性化拼台的设计与应用
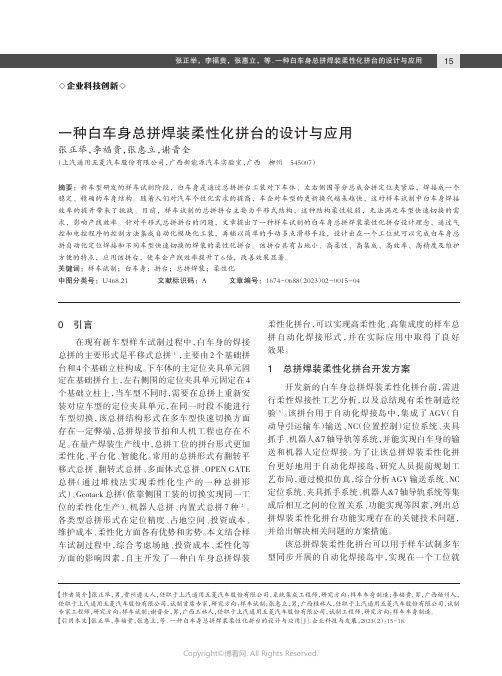
0引言在现有新车型样车试制过程中,白车身的焊接总拼的主要形式是平移式总拼[1],主要由2个基础拼台和4个基础立柱构成。
下车体的主定位夹具单元固定在基础拼台上,左右侧围的定位夹具单元固定在4个基础立柱上,当车型不同时,需要在总拼上重新安装对应车型的定位夹具单元,在同一时段不能进行车型切换,该总拼结构形式在多车型快速切换方面存在一定弊端,总拼焊接节拍和人机工程也存在不足。
在量产焊装生产线中,总拼工位的拼台形式更加柔性化、平台化、智能化。
常用的总拼形式有翻转平移式总拼、翻转式总拼、多面体式总拼、OPEN GATE 总拼(通过堆栈法实现柔性化生产的一种总拼形式)、Geotack总拼(依靠侧围工装的切换实现同一工位的柔性化生产)、机器人总拼、内置式总拼7种[2]。
各类型总拼形式在定位精度、占地空间、投资成本、维护成本、柔性化方面各有优势和劣势。
本文结合样车试制过程中,综合考虑场地、投资成本、柔性化等方面的影响因素,自主开发了一种白车身总拼焊装柔性化拼台,可以实现高柔性化、高集成度的样车总拼自动化焊接形式,并在实际应用中取得了良好效果。
1总拼焊装柔性化拼台开发方案开发新的白车身总拼焊装柔性化拼台前,需进行柔性焊接性工艺分析,以及总结现有柔性制造经验[3]。
该拼台用于自动化焊接岛中,集成了AGV(自动导引运输车)输送、NC(位置控制)定位系统、夹具抓手、机器人&7轴导轨等系统,并能实现白车身的输送和机器人定位焊接。
为了让该总拼焊装柔性化拼台更好地用于自动化焊接岛,研究人员提前规划工艺布局,通过模拟仿真,综合分析AGV输送系统、NC 定位系统、夹具抓手系统、机器人&7轴导轨系统等集成后相互之间的位置关系、功能实现等因素,列出总拼焊装柔性化拼台功能实现存在的关键技术问题,并给出解决相关问题的方案措施。
该总拼焊装柔性化拼台可以用于样车试制多车型同步开展的自动化焊接岛中,实现在一个工位就一种白车身总拼焊装柔性化拼台的设计与应用张正举,李福贵,张惠立,谢晋全(上汽通用五菱汽车股份有限公司,广西新能源汽车实验室,广西柳州545007)摘要:新车型研发的样车试制阶段,白车身是通过总拼拼台工装对下车体、左右侧围等分总成合拼定位夹紧后,焊接成一个稳定、精确的车身结构。
汽车焊装生产线多车型混合生产

一、前言随着我国经济的蓬勃发展,人民生活水平的提高,汽车越来越多地进入了家庭。
人们购买力的提高,也刺激了汽车消费的迅猛增长。
汽车生产企业面对瞬息万变的市场,对产品的市场销售难以准确预测,因此汽车企业的生产能力能否弹性地适应市场波动进行快速调整,显得至关重要。
汽车市场的竞争点越来越集中在产品的更新换代上,面对如此快速的产品更新,汽车行业过去采用的那种大批量单车种专用线的生产模式已不太适应当前发展的要求。
因此多品种的柔性化共用线生产方式也就越来越多地应用在汽车生产中,尤其对于汽车焊装生产这一复杂的专业化制造过程来说,如何实现“柔性化”又是汽车柔性化生产关键。
二、焊装生产线的作用及分类装焊生产的主要任务就是完成车身(也称为白车身,Body in white)的制造,对于轿车来说,车身焊装线一般是由地板总成线、左右侧围总成线、CRP(仪表台横梁+顶盖+后行李仓托架)线和门盖总成线、车身装配调整线等组成。
而各分总成又由很多合件、组件及零件(大多为冲压件)组成,当今由于汽车主机厂考虑到起初的开发投资、日后的生产物流、品质管理等因素,这些分总成线一般都建在主机厂附近的配套厂,采用即时直供方式为主机厂焊装线服务。
所谓专有化焊装线,也称之为单一化焊装生产线,就是该焊装线只能为单一车型提供生产,若再开发新车种生产时,就必须异地或迁移现有焊装线后重新建设焊装线,因此,厂房、设备及公用动力设施重复投资造成浪费,人员流动生产效率低。
而柔性化焊装线,是指在相同的地方同一条生产线上可以同时满足多个车种的生产,其通用设备和公用动力设施一次性投入永久性享用,每次开发新车型时,只需增加部分专用设备;改造事先预置的通用设备;调试各种共用化程序。
因此,避免了重复投资造成的浪费,而且缩短了技改时间,但起初的一次性投资相对会较大。
三、柔性化焊装线然而,这种柔性焊装线它究竟是如何实现多车种混线生产的呢?下面就以东风悦达起亚2工厂焊装线为例来说明柔性制造技术在焊装生产线上的应用,东风悦达起亚 2工厂焊装线,是依据30万台,年纲领设计的,厂房面积33600平方米,分二个阶段投入实施,目前第一阶段15万台,年的能力已经建成并投产,可以同时生产3个车型的车身。
车身焊装生产线焊装主线设计分析

车身焊装生产线焊装主线设计分析摘要:焊装主线是汽车生产流程的关键一环,对整车性能具有直接影响。
车身焊接生产线的合理布局不仅能够有效提高车间空间利用率,还能够提高焊接生产线的工作效率。
本文以某车身焊装生产线ft装主线设计项目为例,介绍了车身焊接工艺,论述了焊装主线平面布置设计原则,重点阐述了焊装主线传输系统与合装台、自动人行过道切换结构等方面的设计要点,希望为今后相似项目的开展提供帮助。
关键词:车身焊装;焊装主线;传输系统;合装台;自动人行过道切换结构引言在汽车的生产工艺中,汽车车身作为汽车中的关键部件,其焊接质量直接影响着产品的整体质量与效果。
汽车焊装主线不仅是汽车焊装工艺的直接体现,也是汽车焊接生产线的核心部分。
焊装主线的合理设计能够有效提高生产线的生产效率。
因此,针对目前车身焊装生产线进行优化设计,对于优化管理提高产品市场竞争力意义重大。
1项目概况该车型具有多重变体,根据轴距的不同可以分为L1-L4,车身高度可分为3个档次,分别该项目为某汽车公司上海工厂项目,该项目乘用车生产线的生产节拍为15JPH 204s, 为高中低顶,移门分为左右移门和无移门,盲窗也分为有无车型。
该生产线包含了 21个工位的主线以及补焊,3个工位顶盖设备。
2车身焊接工艺在汽车制造工艺中,车身焊接是将汽车冲压或者相关零部件通过焊接的工艺将这些部件组合起来从而形成白车身。
汽车焊装总成线主要包括了前围总成焊接线、后围总成焊接线、左右侧围总成焊接线以及地板总成焊接线组成。
汽车车身作为壳体钣金件是经过薄钢板焊接的复牵结构,一个车身是由数百个钣金冲压件经点焊、钎焊、气体保护焊等焊装工艺组成。
对于车身焊接土艺具有明显的焊接顺序,所以在进行焊接前一定要明确焊接的顺序。
对于车身在焊接过程中需要通过相关夹具来确定各个钣金件的位置从而能够更好的进行夹紧,保证产品在焊接过程中能够处于正确位置提高产品焊接精度。
位于工位与工位或分总成线间的传输装置,能够灵活传递产品,确保焊接节拍有序进行。
浅谈汽车车身焊接生产线规划设计
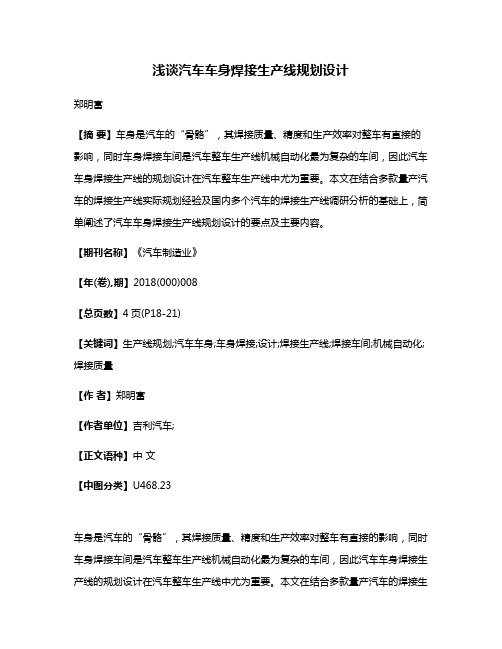
浅谈汽车车身焊接生产线规划设计郑明富【摘要】车身是汽车的“骨骼”,其焊接质量、精度和生产效率对整车有直接的影响,同时车身焊接车间是汽车整车生产线机械自动化最为复杂的车间,因此汽车车身焊接生产线的规划设计在汽车整车生产线中尤为重要。
本文在结合多款量产汽车的焊接生产线实际规划经验及国内多个汽车的焊接生产线调研分析的基础上,简单阐述了汽车车身焊接生产线规划设计的要点及主要内容。
【期刊名称】《汽车制造业》【年(卷),期】2018(000)008【总页数】4页(P18-21)【关键词】生产线规划;汽车车身;车身焊接;设计;焊接生产线;焊接车间;机械自动化;焊接质量【作者】郑明富【作者单位】吉利汽车;【正文语种】中文【中图分类】U468.23车身是汽车的“骨骼”,其焊接质量、精度和生产效率对整车有直接的影响,同时车身焊接车间是汽车整车生产线机械自动化最为复杂的车间,因此汽车车身焊接生产线的规划设计在汽车整车生产线中尤为重要。
本文在结合多款量产汽车的焊接生产线实际规划经验及国内多个汽车的焊接生产线调研分析的基础上,简单阐述了汽车车身焊接生产线规划设计的要点及主要内容。
焊接生产线的规划设计基础是汽车的既定产能目标,根据该目标计算出生产节拍、确定生产协作方式(加工深度)和规划设备投资等。
汽车车身焊接生产线规划涉及工艺设计、平面布局(Lay-out)、信息化(生产管理系统)设计、土建及公用系统设计、节能环保设计和人员规划六大方面。
由于消费者对产品多样化的需求、市场变化、生产成本压缩和遵守顾客交货期等因素的驱动下,在进行焊接生产线规划时,应考虑多款车型混线生产,做到“柔性化”生产,本文以规划设计一条可实现单班6万台、双班12万台产能的两款车型(一款4门轿车、一款4门SUV)车身焊接生产线为例,简单论述主要方面。
设计前提1.工作制度和年时基数拟采用两班工作制,每班工作8 h,全年工作天数250天。
2.生产节拍整体规划一条单班6万台、双班12万台产能的汽车车身焊接生产线,按照工作制度和年时基数,则理论生产节拍为:60 000台÷250天÷8 h=30台/h,即30 JPH(JPH:Jet per Hour,每小时产出量)。
焊接技术在汽车车身焊接中的应用

焊接技术在汽车车身焊接中的应用摘要:汽车车身焊接技术作为汽车制造核心技术之一,一直备受重视。
汽车车身焊接技术伴随着汽车工业技术的发展而发展,目前如激光焊接技术,焊接机器人技术等被大量应用。
汽车焊接技术领域凸显出自动数字化,柔性化,虚拟化等一些发展趋势。
本文从汽车车身焊接技术特点入手,到分析技术应用现状再到对未来汽车焊接技术发展趋势展望,仅供参考。
关键词:车身焊接技术激光焊接机器人焊接1、当前汽车制造业中焊接技术的应用现状1.1 电阻点焊应用现状分析在车身焊接过程中,常用的焊接方法之一就是电阻点焊技术,电阻点焊的质量与焊接的静臂电极、动臂电极、电流之间的总电阻、焊接时间有着不可分割的直接联系。
因此,在运用电阻点焊技术来焊接汽车车身各个零部件时,要对影响电阻点焊质量的相关因素进行更好的分析与掌握,这样才能更好的提升电阻点焊效率,促进汽车车身焊接效果与品质的更好提升。
1.2 弧焊技术应用现状分析在常用的焊接技术中,弧焊技术是其中一种较为重要的焊接技术,且在汽车车身焊接过程中应用比较频繁。
在应用弧焊技术时,其最重要的焊接工艺就是熔化极惰性气体保护焊,其能够对焊接点进行更好地拿捏。
但是弧焊技术应用的问题也是比较明显的,其要求所有种类的焊接零件焊接方法必须是自动化。
但是将自动化焊接运用到汽车车身零件的焊接工作中,其焊口的精准性不易被把握,容易产生焊接轨迹偏移的问题,使得焊接质量大大的降低。
由此可见,焊接误差的存在会大大的降低焊接的质量与汽车制造水平。
1.3 激光焊的应用现状分析激光焊是一种以聚焦的激光束作为能源轰击焊件所产生的热量进行焊接的方法。
激光焊接是激光材料加工技术应用的重要方面之一。
在1970年,激光焊主要用于焊接薄壁材料与低速焊接,焊接过程是一种热传导。
换句话说,激光焊主要是运用激光辐射来对零部件的表面进行加热,表面热量通过热传导向内部扩散,通过对激光脉冲的能量、宽度、峰值功率和重复频率等参数进行合理控制,使工件熔化来形成特定的熔池。
汽车整车柔性化制造技术

汽车整车柔性化制造技术什么是柔性化制造技术?柔性化制造技术,意味着生产线上的工艺装备具有很大程度的通用性,在进行新的产品生产时,不需要或较少对原有生产线进行改造。
为什么需要柔性化制造技术?当前,汽车市场的个性化需求越来越高,为了更好的占领市场,必须适应这个趋势,改变以往大批量、单一化的生产模式,转变为小批量、多品种的生产模式。
大批量、单一化的生产模式,大部分是采用专用的工艺装备进行专用件及车型的生产,如果还是采用以往的工艺装备方案进行小批量、多品种的生产,则必然会造成大量的工艺装备投资,使制造成本增加。
而且,会造成产能的大幅度浪费。
正是在这种矛盾下,产生了新的柔性化制造技术。
这种制造技术,可以最大程度的降低工艺装备的投资成本,而且可以最大程度的利用产能。
除此之外,还可以最大程度的缩短开发时间,实现新车型的迅速投产。
在目前不确定的市场环境下,汽车制造商比以往任何时候都需要具有灵活多变的生产工厂。
除了可以针对市场做出快速灵敏的反应外,还可以使产能最大化。
一个成本较低的工厂,一个可以满负荷生产不同车型的工厂,一个可以对多变的市场迅速做出反应而迅速调整的工厂在今天看来无论对主机厂还是供应商来说都是一个理想化的工厂。
怎样才能实现柔性化制造技术?要实现柔性化制造技术,需要从产品设计、设备开发、管理技术几方面入手。
1、产品设计:柔性化制造技术要从产品的设计开始。
因为柔性是相对的柔性,不存在万能的生产设备。
所以,柔性化制造技术对产品设计的平台化、模块化、标准化要求十分重要,产品设计要重点考虑工厂的局限性和硬点,这些,是柔性化制造技术的开端和基础。
例如:假设我们的车身输送系统定位销的间距是3200mm×960mm。
如果新车型将这个间距改成3210mm×950mm,那我们就要对输送系统进行大幅度的调整。
同样,如果通过调整,新车型的车身输送系统定位销间距保持在3200mm×960mm,我们就没有必要对我们的车身输送设备做出任何改变。
汽车车身焊装夹具的设计对策
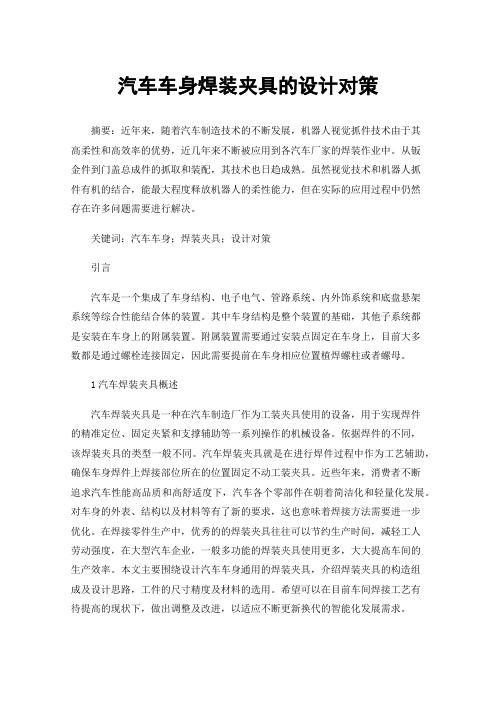
汽车车身焊装夹具的设计对策摘要:近年来,随着汽车制造技术的不断发展,机器人视觉抓件技术由于其高柔性和高效率的优势,近几年来不断被应用到各汽车厂家的焊装作业中。
从钣金件到门盖总成件的抓取和装配,其技术也日趋成熟。
虽然视觉技术和机器人抓件有机的结合,能最大程度释放机器人的柔性能力,但在实际的应用过程中仍然存在许多问题需要进行解决。
关键词:汽车车身;焊装夹具;设计对策引言汽车是一个集成了车身结构、电子电气、管路系统、内外饰系统和底盘悬架系统等综合性能结合体的装置。
其中车身结构是整个装置的基础,其他子系统都是安装在车身上的附属装置。
附属装置需要通过安装点固定在车身上,目前大多数都是通过螺栓连接固定,因此需要提前在车身相应位置植焊螺柱或者螺母。
1汽车焊装夹具概述汽车焊装夹具是一种在汽车制造厂作为工装夹具使用的设备,用于实现焊件的精准定位、固定夹紧和支撑辅助等一系列操作的机械设备。
依据焊件的不同,该焊装夹具的类型一般不同。
汽车焊装夹具就是在进行焊件过程中作为工艺辅助,确保车身焊件上焊接部位所在的位置固定不动工装夹具。
近些年来,消费者不断追求汽车性能高品质和高舒适度下,汽车各个零部件在朝着简洁化和轻量化发展。
对车身的外表、结构以及材料等有了新的要求,这也意味着焊接方法需要进一步优化。
在焊接零件生产中,优秀的的焊装夹具往往可以节约生产时间,减轻工人劳动强度,在大型汽车企业,一般多功能的焊装夹具使用更多,大大提高车间的生产效率。
本文主要围绕设计汽车车身通用的焊装夹具,介绍焊装夹具的构造组成及设计思路,工件的尺寸精度及材料的选用。
希望可以在目前车间焊接工艺有待提高的现状下,做出调整及改进,以适应不断更新换代的智能化发展需求。
2汽车车身焊装夹具的设计对策2.1侧围内外板高节拍柔性预装方案侧围预装工位是主焊线生产的第一序,是总拼工位的前提。
在侧围内板的预装工位中,需要在侧围内板上完成和地板搭接位置的涂胶工艺以及和地板连接的搭扣工艺。
柔性制造技术在汽车生产中的应用
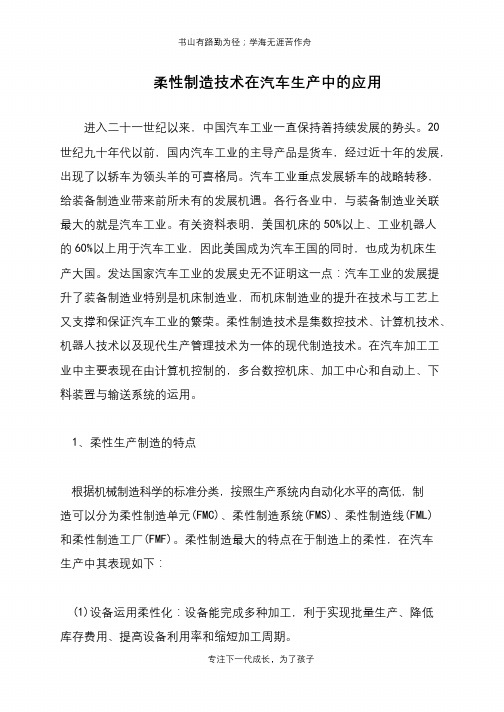
书山有路勤为径;学海无涯苦作舟
柔性制造技术在汽车生产中的应用
进入二十一世纪以来,中国汽车工业一直保持着持续发展的势头。
20 世纪九十年代以前,国内汽车工业的主导产品是货车,经过近十年的发展,出现了以轿车为领头羊的可喜格局。
汽车工业重点发展轿车的战略转移,给装备制造业带来前所未有的发展机遇。
各行各业中,与装备制造业关联最大的就是汽车工业。
有关资料表明,美国机床的50%以上、工业机器人的60%以上用于汽车工业,因此美国成为汽车王国的同时,也成为机床生产大国。
发达国家汽车工业的发展史无不证明这一点:汽车工业的发展提升了装备制造业特别是机床制造业,而机床制造业的提升在技术与工艺上又支撑和保证汽车工业的繁荣。
柔性制造技术是集数控技术、计算机技术、机器人技术以及现代生产管理技术为一体的现代制造技术。
在汽车加工工业中主要表现在由计算机控制的,多台数控机床、加工中心和自动上、下料装置与输送系统的运用。
1、柔性生产制造的特点
根据机械制造科学的标准分类,按照生产系统内自动化水平的高低,制
造可以分为柔性制造单元(FMC)、柔性制造系统(FMS)、柔性制造线(FML) 和柔性制造工厂(FMF)。
柔性制造最大的特点在于制造上的柔性,在汽车
生产中其表现如下:
(1)设备运用柔性化:设备能完成多种加工,利于实现批量生产、降低
库存费用、提高设备利用率和缩短加工周期。
专注下一代成长,为了孩子。
汽车自动化柔性焊装线技术探讨

《装备维修技术》2019年第3期(总第171期)doi:10.16648/ki.1005-2917.2019.03.075汽车自动化柔性焊装线技术探讨彭裕磊(比亚迪汽车工业有限公司,广东深圳518000)摘要:随着汽车市场竞争激烈化及客户个性化需求的提升,同时企业也面临着用地资源紧张、车型种类增多、更新周期加快等,自动化柔性焊装线生产已成为当前汽车车身焊接的主流趋势。
它最显著的优势就是能适应多品种车型、灵活程度高、占地面积集中,大大提高焊装线生产效率,降低人力成本的投入,可更好适应当今汽车市场车型不断更新换代快速化的客观需求。
高自动化、高柔性、高标准化、高模块化、高产能的焊装线解决方案,可大幅降低投资及后期维护成本,提高主机厂的技术实力及竞争优势。
本文将以车身焊接自动化柔性焊装生产线为研究对象,分析自动化柔性生产线的工艺需求和特点,从生产线的规划方式、自动化柔性、标准化等,为后期多车型共线建设模块化、标准化柔性焊装线的实践运用提供理论参考。
关键词:汽车焊接;自动化;柔性;应用;规划一、汽车自动化柔性焊装线技术必要性和优势目前,汽车厂生产现状大趋势:多品种车型并行、小批量生产增多、产品生命周期缩短、生产线建设周期缩短、机器人逐渐替代人工、智能化信息化订单式生产增多等。
亟待解决的需求与矛盾:工业用地资源紧张,用于焊装生产的厂房已建设并固化,现有厂房无法满足不断新增的车型。
如某热销车型焊装线产能满足不了订单需求,人工焊接工位过多,同时又存在其它订单少的单一自动线大量机器人、焊接设备等资源闲置浪费;后续又会继续增加车型投入生产,对应工装和焊接设备在不断的投入,单一车型产量小,设备及产线利用率极低。
故需分期建设能多车型混线生产的高自动化、高柔性、高产能的车身焊装生产线,以满足当前及后续多车型生产需求。
其优势如下:(一)设备及产线利用率高降低后续重复性投入汽车行业竞争的加剧与客户需求的提升,车型需不断的推陈出新和更新换代,焊装线已由单一品种大量生产方式向多品种批量柔性生产方式转变。
车身焊装生产线机器人布局设计
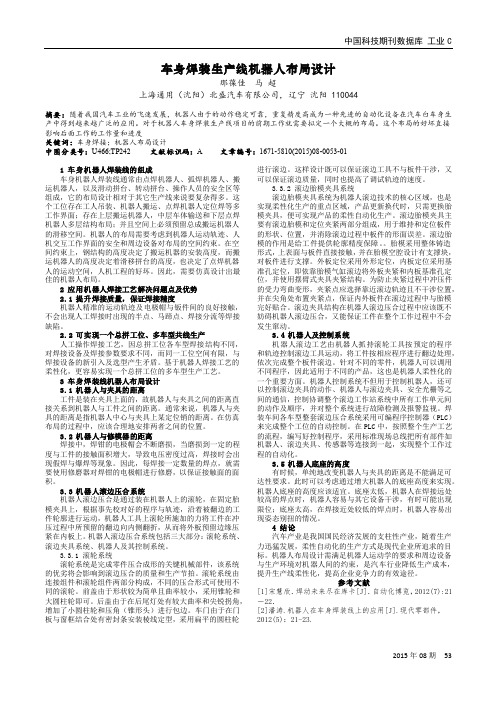
中国科技期刊数据库 工业C2015年08期 53车身焊装生产线机器人布局设计那葆佳 马 超上海通用(沈阳)北盛汽车有限公司,辽宁 沈阳 110044摘要:随着我国汽车工业的飞速发展,机器人由于的动作稳定可靠,重复精度高成为一种先进的自动化设备在汽车白车身生产中得到越来越广泛的应用。
对于机器人车身焊装生产线项目的前期工作就需要拟定一个大概的布局。
这个布局的好坏直接影响后面工作的工作量和进度关键词:车身焊接;机器人布局设计 中图分类号:U466;TP242 文献标识码:A 文章编号:1671-5810(2015)08-0053-011 车身机器人焊装线的组成车身机器人焊装线通常由点焊机器人、弧焊机器人、搬运机器人,以及滑动拼台、转动拼台、操作人员的安全区等组成,它的布局设计相对于其它生产线来说要复杂得多。
这个工位存在工人吊装、机器人搬运、点焊机器人定位焊等多工作界面;存在上层搬运机器人,中层车体输送和下层点焊机器人多层结构布局;并且空间上必须预留总成搬运机器人的滑移空间。
机器人的布局需要考虑到机器人运动轨迹、人机交互工作界面的安全和周边设备对布局的空间约束。
在空间约束上,钢结构的高度决定了搬运机器的安装高度,而搬运机器人的高度决定着滑移拼台的高度,也决定了点焊机器人的运动空间,人机工程的好坏。
因此,需要仿真设计出最佳的机器人布局。
2 应用机器人焊接工艺解决问题点及优势 2.1 提升焊接质量,保证焊接精度机器人精准的运动轨迹及电极帽与钣件间的良好接触,不会出现人工焊接时出现的半点、马蹄点、焊接分流等焊接缺陷。
2.2 可实现一个总拼工位、多车型共线生产人工操作焊接工艺,因总拼工位各车型焊接结构不同,对焊接设备及焊接参数要求不同,而同一工位空间有限,与焊接设备的新引入及选型产生矛盾。
基于机器人焊接工艺的柔性化,更容易实现一个总拼工位的多车型生产工艺。
3 车身焊装线机器人布局设计 3.1 机器人与夹具的距离工件是装在夹具上面的,故机器人与夹具之间的距离直接关系到机器人与工件之间的距离。
汽车车身焊装线

各个工位的base板通过连接板连在一起构成了整个汽车焊装线的支撑装置,它既要支撑整个传输装置又要支撑焊装夹具。此外,为了保证夹具与车身零件的基准一致,在base板上按照设计基准画出基准刻度线。图中的调平装置主要起到对整个传输装置调平作用。
base板结构
1 base板2调平装置3 base板连接板
汽车车身焊装线
一、汽车车身焊装线的组成
汽车车身焊装生产线是轿车、微型客车等车型生产过程中的重要生产线之一,从汽车工业的发展历史来看,车身焊装线经历了20世纪50~60年代手工焊接线→20世纪70年代的自动化刚性焊装线→20世纪80年代以后的机器人柔性焊装线阶段。
就每条焊装线而言,它由焊接夹具、传输装置、焊接设备(焊枪、焊接机器人)构成;就整个汽车车身焊装线而言,它大体包括车身侧围总成线、车身门盖总成线、底板总成线、车身焊装主线等(目前尚无绝对的概括)。其中每部分又有相应的主线、子线、左右对称线和独立岛。根据生产节拍、自动化程度及生产方式等的不同,每条线又分为若干个工位;各工位间通过传输装置连为一体,每工位负责完成一部分工作。具体如图1:
以上所介绍的是传输装置的主要结构,通过除此以外还有一些辅助装置:
6,缓冲锁紧装置(如下图)
缓冲锁紧装置
1汽缸支撑架2限位块3汽缸4缓冲器5缓冲器支架6行程开关
焊装线传输装置共设置了4个缓冲锁紧装置分别分布于顶升框架的两端,主要是对“移动滑板”的水平运动起到缓冲和锁紧作用。具体过程是:当“移动滑板”快要运动到传输装置的末端时,便与缓冲器接触从而减缓运动速度;当“移动滑板”运动到传输装置的末端后,行程开关命令汽缸夹紧固定在移动滑板上的限位块从而起到锁紧作用。该装置实现了汽车焊装线传输装置慢启、慢停的进退动作要求,保证了传输装置运行安全、可靠。
轿车白车身焊装生产线的工艺规划与布局设计
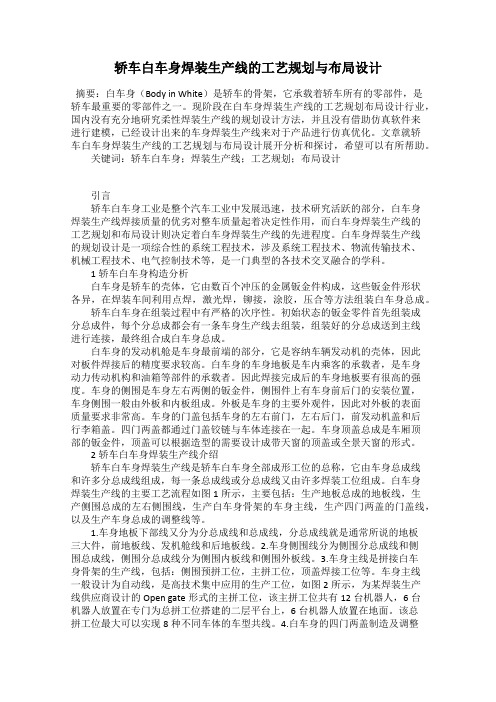
轿车白车身焊装生产线的工艺规划与布局设计摘要:白车身(Body in White)是轿车的骨架,它承载着轿车所有的零部件,是轿车最重要的零部件之一。
现阶段在白车身焊装生产线的工艺规划布局设计行业,国内没有充分地研究柔性焊装生产线的规划设计方法,并且没有借助仿真软件来进行建模,已经设计出来的车身焊装生产线来对于产品进行仿真优化。
文章就轿车白车身焊装生产线的工艺规划与布局设计展开分析和探讨,希望可以有所帮助。
关键词:轿车白车身;焊装生产线;工艺规划;布局设计引言轿车白车身工业是整个汽车工业中发展迅速,技术研究活跃的部分,白车身焊装生产线焊接质量的优劣对整车质量起着决定性作用,而白车身焊装生产线的工艺规划和布局设计则决定着白车身焊装生产线的先进程度。
白车身焊装生产线的规划设计是一项综合性的系统工程技术,涉及系统工程技术、物流传输技术、机械工程技术、电气控制技术等,是一门典型的各技术交叉融合的学科。
1轿车白车身构造分析白车身是轿车的壳体,它由数百个冲压的金属钣金件构成,这些钣金件形状各异,在焊装车间利用点焊,激光焊,铆接,涂胶,压合等方法组装白车身总成。
轿车白车身在组装过程中有严格的次序性。
初始状态的钣金零件首先组装成分总成件,每个分总成都会有一条车身生产线去组装,组装好的分总成送到主线进行连接,最终组合成白车身总成。
白车身的发动机舱是车身最前端的部分,它是容纳车辆发动机的壳体,因此对板件焊接后的精度要求较高。
白车身的车身地板是车内乘客的承载者,是车身动力传动机构和油箱等部件的承载者。
因此焊接完成后的车身地板要有很高的强度。
车身的侧围是车身左右两侧的钣金件,侧围件上有车身前后门的安装位置,车身侧围一般由外板和内板组成。
外板是车身的主要外观件,因此对外板的表面质量要求非常高。
车身的门盖包括车身的左右前门,左右后门,前发动机盖和后行李箱盖。
四门两盖都通过门盖铰链与车体连接在一起。
车身顶盖总成是车厢顶部的钣金件,顶盖可以根据造型的需要设计成带天窗的顶盖或全景天窗的形式。
浅析智能化焊装工厂生产线设计规划

图3 智能化制造管理集控中心
4.生产辅助设计 生产辅助包括培训、库房、质量、生活以及班组 园地等。其中,培训功能主要有新员工培训室、实操 培训区、机器人示教培训区等;库房主要有劳保、生 辅材料、备件及维修间等;质量功能如三坐标、蓝 光、匹配、AUDIT及车身拆检室等;生活功能主要有 卫生间、水房、清洁间及吸烟室等;班组园地具备人 员休息、班级管理目视化、现场查询资料等功能。
专项模块设计
1.物流模块设计 焊装物流,依托自动化物流设备、大数据网联等技 术,优化人员、场地、设备利用率、物料出入库以及配 送通过手持/移动终端下达任务;采用叉车、AGV、牵引 车设备、道口分配调度系统及RF无线扫码,通过LES系 统传递零件需求信息,定时指导物流配送。 外协件由3PL配送至卸货区,验收合格后入物料缓 存区。需整合的零件送至物料分拣区分拣,无需分拣 的零件(专用器具)直接进缓存;将整合料车和专用 器具配送至对应装配工位。
现代化汽车工厂设计是一项复杂的系统工程。作 为整车四大工艺中较为典型的焊装工厂,既涉及工 艺、设备、工程及物流等专业,又要满足产品多样 化、个性化趋势下的柔性化、高节拍、节能环保等需 求。2015年中国发布了《智能制造2025》规划,促进 了装备智能化、数字化的高速发展,也深刻影响着汽 车工厂设计规划方式。3 Nhomakorabea扩展性设计
扩展性设计主要体现在产能和产品扩展途径,根 据产能目标制定产能扩张策略。例如一次性规划分步 实施或一次性实施。如图2所示,产品的扩展性,主要 通过产品设计平台化、产线设备高柔性化,逐步扩展 到多车型共线生产。
(1)一级总成生产线 包括下部线、主焊线。下 部线主要功能是实现前机舱及前、后地板合拼。涉及 三大块定位,定位机构较复杂,下部总成合拼柔性化 方式可以采用NC柔性化系统、台车系统、多夹具切换 系统等。主焊线将下部总成、左右侧围、顶盖合拼成 完整的白车身。主焊柔性化方式可以采用柔性化G AT E
汽车侧围分拼柔性焊接线布局浅析

汽车侧围分拼柔性焊接线布局浅析摘要:侧围是汽车覆盖件中较为复杂的成形零件,其高品质的外观质量和产品精度要求,集成了冲压工艺、CAE分析、结构设计、加工调试等各技术领域的最高水平。
文章重点就汽车侧围分拼柔性焊接线布局展开相关论述。
关键词:汽车侧围分拼;柔性焊接线;布局焊装作为汽车四大工艺之一,其工艺和设备水平对车身质量有着十分重要的影响。
车身焊装车间最重要最复杂的是总拼线的总拼工位,总拼工位一般分为预拼工位和焊装工位,分为两个工位后,使得总拼工位更具条理,每个分工位的工作量减少,在车型较多时避免了一个工位内设备种类、数量过多和控制过程复杂的现象发生。
随着国内汽车市场越来越大,各个汽车厂商的生产线线速在不断的提高,40-60JPH已经成为新常态的工艺规划要求,同时也有一些厂家在挑战65JPH甚至更高,在此情况下,除了总拼焊焊装工位,预拼工位也成为了关键和瓶颈工位,其工艺设计布置是否能够满足高节拍需求,车型柔性是否能够满足多车型共线生产,设备投资和人员数量需求是否能够符合各个公司精益指标要求都非常重要。
一、侧围分拼焊接过程侧围分总成是由多个合件、组件及冲压单件组成。
在侧围分拼焊接线上,将若干散件按照一定的零件搭接顺序进行拼合,其中个别零件在拼合前还需要在规定的位置完成涂胶;拼合后由输送系统将所有散件送入后道定位工装对各零件精确定位,控制所有零件间的相对尺寸,并使用焊枪进行定位焊接,使各散件连接为一个整体;之后再由输送系统送入后道补焊工装进行补焊,直至完成侧围分总成的所有焊接工艺。
二、预拼工位工艺分析对于预拼工位,一般的工艺流程为,空中EMS机运小车运输侧围总成零件到预拼工位正上方,再通过升降机或者机器人把侧围总成零件传送到地面,由人工或者机器人来搬运侧围总成到车身上,通过预搭扣,把侧围总成挂在车身上,以实现侧围预拼合。
(一)人工工艺方案传统主线侧围拼合工位的工艺为人工上料。
人工上料:侧围从 EMS 小车到工位的方法有三种:EMS小车下降到工位上空;升降机移动侧围到工位旁;机器人抓料到工位旁。
●●柔性总拼技术应用介绍●●

适用于节拍要求不高、批量生产、车型数量规划一定,
且后续更换车型较少的情况
视频
柔性总拼技术应用介绍
特点:
3.多面体总拼–现代、起亚、三菱、吉利、
长丰、北汽、哈飞等使用四面体,一汽轿车使
用三面体。
车型切换通过旋转实现,整个切换只占一个工位,占地
少,车型切换可以在15s内完成,最多四款车型,可达
7.4Flexible-turntable–KUKA、TKDN
特点:
切换容易;模块化设计,新车型改造较容易;最多6款车型
共线。
适用于批量生产。占地面积较大。
视频一
柔性总拼技术应用介绍
柔性总拼技术应用介绍
7.5GEOTACK-FFT
特点:
切换容易;模块化设计,新车型改造较容易;整体制作难
度Hale Waihona Puke 大。适用于多车型柔性化生产。点地面积较大。
Fixture
LowerRobots
柔性总拼技术应用介绍
柔性总拼技术应用介绍
7.7MFS-MINO
特点:
占地小22m×12m;效率高满足60JPH,可布14-16台机器
人;可8款车型柔性共线生产;需要预装;模块化设计、全
伺服驱动;可分阶段建设(1→2→4→8车型)。顶部浮动连
接机构,延长夹具精度维护周期。
驱动对车身稳定性更好。
柔性总拼技术应用介绍
1.3单一车型平稳+翻转总拼
特点:
单一车型,节拍较低,一般总拼工位不使用机器人
焊接,机器人布置在补焊工位。
因有翻转,可用AFM直接上料、不需要预装。
柔性总拼技术应用介绍
2.1多工位人工焊接-东风日产
特点:
滑橇浅谈汽车智能化焊装生产线的安装与调试
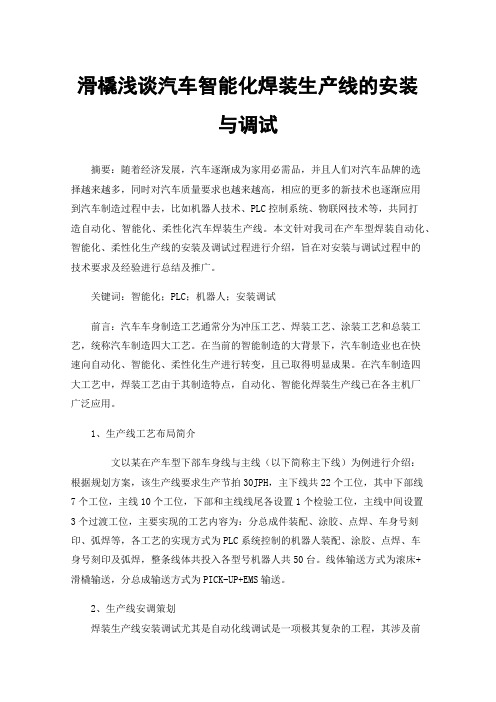
滑橇浅谈汽车智能化焊装生产线的安装与调试摘要:随着经济发展,汽车逐渐成为家用必需品,并且人们对汽车品牌的选择越来越多,同时对汽车质量要求也越来越高,相应的更多的新技术也逐渐应用到汽车制造过程中去,比如机器人技术、PLC控制系统、物联网技术等,共同打造自动化、智能化、柔性化汽车焊装生产线。
本文针对我司在产车型焊装自动化、智能化、柔性化生产线的安装及调试过程进行介绍,旨在对安装与调试过程中的技术要求及经验进行总结及推广。
关键词:智能化;PLC;机器人;安装调试前言:汽车车身制造工艺通常分为冲压工艺、焊装工艺、涂装工艺和总装工艺,统称汽车制造四大工艺。
在当前的智能制造的大背景下,汽车制造业也在快速向自动化、智能化、柔性化生产进行转变,且已取得明显成果。
在汽车制造四大工艺中,焊装工艺由于其制造特点,自动化、智能化焊装生产线已在各主机厂广泛应用。
1、生产线工艺布局简介文以某在产车型下部车身线与主线(以下简称主下线)为例进行介绍:根据规划方案,该生产线要求生产节拍30JPH,主下线共22个工位,其中下部线7个工位,主线10个工位,下部和主线线尾各设置1个检验工位,主线中间设置3个过渡工位,主要实现的工艺内容为:分总成件装配、涂胶、点焊、车身号刻印、弧焊等,各工艺的实现方式为PLC系统控制的机器人装配、涂胶、点焊、车身号刻印及弧焊,整条线体共投入各型号机器人共50台。
线体输送方式为滚床+滑橇输送,分总成输送方式为PICK-UP+EMS输送。
2、生产线安调策划焊装生产线安装调试尤其是自动化线调试是一项极其复杂的工程,其涉及前期划线、机械设备安装、夹具安装标定、钢结构搭建、水气管路安装、电气设备安装、电气线路接线、电气程序输入与调试、机器人及其附属设备安装调试、线体联动、机器人焊接程序输入等一系列复杂工作,且涉及到不同的设备供应商及主机厂各部门协调工作,因此为保施工进度及质量前期安调策划显得十分必要。
生产线安装调试涉及单位较多,过程中由规划单位进行组织、协调,包括各供应商厂家、焊装车间、设备主管单位、安保单位及现场工艺等,各单位协调生产,及时跟踪安调过程,对于过程异常状况进行重点分析,制定切实可行的补救措施及追赶计划,最终保证项目保质保量推进。
标准化柔性生产线大擂台:丰田、大众、通用、日产、现代各有千秋!
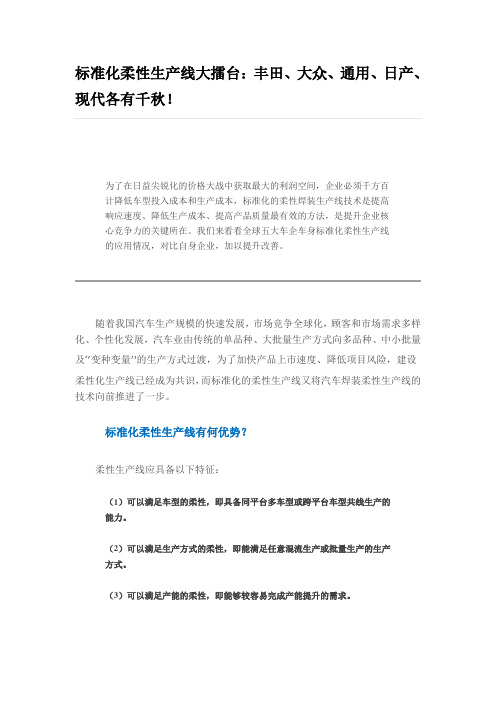
标准化柔性生产线大擂台:丰田、大众、通用、日产、现代各有千秋!为了在日益尖锐化的价格大战中获取最大的利润空间,企业必须千方百计降低车型投入成本和生产成本,标准化的柔性焊装生产线技术是提高响应速度、降低生产成本、提高产品质量最有效的方法,是提升企业核心竞争力的关键所在。
我们来看看全球五大车企车身标准化柔性生产线的应用情况,对比自身企业,加以提升改善。
随着我国汽车生产规模的快速发展,市场竞争全球化,顾客和市场需求多样化、个性化发展,汽车业由传统的单品种、大批量生产方式向多品种、中小批量及“变种变量”的生产方式过渡,为了加快产品上市速度、降低项目风险,建设柔性化生产线已经成为共识,而标准化的柔性生产线又将汽车焊装柔性生产线的技术向前推进了一步。
标准化柔性生产线有何优势?柔性生产线应具备以下特征:(1)可以满足车型的柔性,即具备同平台多车型或跨平台车型共线生产的能力。
(2)可以满足生产方式的柔性,即能满足任意混流生产或批量生产的生产方式。
(3)可以满足产能的柔性,即能够较容易完成产能提升的需求。
标准化柔性生产线则是指不同的生产线使用了相同的解决方案,配备了相同或相似的设备,使用了相同的生产工艺。
因此,标准化柔性生产线具备以下优势:(1)由于配备相同的设备,使用相同的生产工艺,所以在生产设备、生产工艺流程和质量管理方面实现了三个标准的统一,将产品的不合格率降低到了最低限度,提高了产品质量,是提升竞争力的源泉。
(2)标准化的柔性生产系统能帮助汽车生产企业迅速应对市场变化,跟上消费者的需求,这是汽车企业提高竞争力的关键。
(3)由于使用了标准化的配置,生产线的开发和建设周期都大大缩短,使用周期大大延长,降低了投资,提高了效益。
(4)标准化的配置使生产线的故障率降低,维修保养变得更加简单。
支撑标准化柔性生产线的要素是什么?要建设或开发一套标准化的柔性生产线需要众多的要素支撑,其中车身结构和工艺是基础,夹具的柔性技术是关键:车身的结构和生产工艺决定了生产流程,具有相似车身结构和定位要求的车型,其生产线较容易实现柔性共线,反之车身结构差距较大或生产工艺区别太大的产品,其共线生产的难度较大,即使勉强共线经济性也不好;焊接生产线中刚性最强的设备是定位夹具,是制约柔性化生产的关键,定位夹具特别是关键定位设备结构的标准化和模块化,带动了标准化柔性生产线技术的发展。