汽车焊装工艺
汽车车身零部件焊装夹具的特点和装配工艺
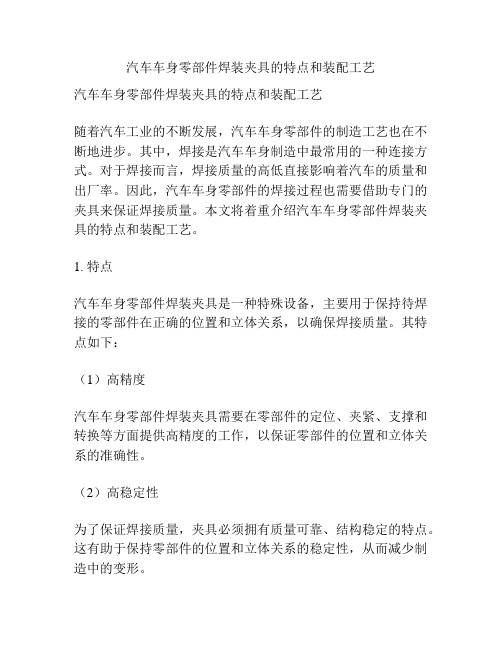
汽车车身零部件焊装夹具的特点和装配工艺汽车车身零部件焊装夹具的特点和装配工艺随着汽车工业的不断发展,汽车车身零部件的制造工艺也在不断地进步。
其中,焊接是汽车车身制造中最常用的一种连接方式。
对于焊接而言,焊接质量的高低直接影响着汽车的质量和出厂率。
因此,汽车车身零部件的焊接过程也需要借助专门的夹具来保证焊接质量。
本文将着重介绍汽车车身零部件焊装夹具的特点和装配工艺。
1. 特点汽车车身零部件焊装夹具是一种特殊设备,主要用于保持待焊接的零部件在正确的位置和立体关系,以确保焊接质量。
其特点如下:(1)高精度汽车车身零部件焊装夹具需要在零部件的定位、夹紧、支撑和转换等方面提供高精度的工作,以保证零部件的位置和立体关系的准确性。
(2)高稳定性为了保证焊接质量,夹具必须拥有质量可靠、结构稳定的特点。
这有助于保持零部件的位置和立体关系的稳定性,从而减少制造中的变形。
(3)高度自动化随着汽车工业的不断发展,车身零部件焊装需求不断增长,因此高度自动化的夹具设计越来越受到关注。
目前,自动化夹具已经成为焊接工艺中不可或缺的一部分。
(4)环保性传统的焊接工艺中会使用大量的化学电解污染物,对环境造成不必要的危害。
换句话说,汽车车身零部件焊装夹具应具有节能环保的特点。
2. 装配工艺汽车车身零部件焊装夹具的装配工艺在汽车制造中起着至关重要的作用。
其主要过程包括夹具设计、夹具制造和夹具试验三个阶段,下面一一介绍。
(1)夹具设计夹具设计是汽车车身零部件焊装夹具装配工艺的第一步。
在设计过程中,应考虑零件的特点,包括工件尺寸、形状、位置和不同焊接加工的要求。
(2)夹具制造夹具制造过程中需要注意各夹具部件的精度要求、夹具的材质和加工精度、接口尺寸以及各零部件之间的匹配精度。
此外,夹具还需要开展优化设计,以提供更加完美的闭环控制,从而充分实现自动化的生产流程。
(3)夹具试验夹具试验是确保汽车车身零部件焊装夹具在实际运用中能够完美执行其功能的最后一个步骤。
汽车焊接工艺知识

Page *
焊接——是通过加热或者加压,或者两者并用;加或不加填充材料;使两分离的金属表面达到原子间的结合,形成永久性连接的一种工艺方法。
焊接设备-保证焊接强度
焊接夹具-保证焊接尺寸
2.1 焊接的定义
Page *
焊接方法分类
钎焊
点焊 凸焊
熔化焊
ห้องสมุดไป่ตู้
火焰铜钎焊 激光钎焊
CO2焊 螺柱焊 TIG/MIG焊(非熔化极/溶化极惰性气体保护焊)
常用焊接方法
2.2 焊接方法简介
Page *
CO2气体保护焊是采用CO2气体作为保护介质,焊接时,CO2气体通过焊枪的喷嘴,沿焊丝的周围喷射出来,在电弧周围形成气体保护层,机械地将焊接电弧与空气隔离开来,从而避免了有害气体的侵入,保证焊接过程的稳定以获得优质的焊缝。
CO2气体保护焊方法的原理
2.2 焊接方法简介
第二部分 装焊工艺
2.4 装焊生产设备及工艺装备
焊接设备
螺柱焊设备
Page *
2.4 装焊生产设备及工艺装备
焊接夹具
车身的定位主要依靠焊接夹具和焊接辅具,而焊接夹具和辅具作用是夹紧和定位
夹具的组成
夹具是有各种不同作用的元件组成的,所谓夹具元件,是指夹具上用来完成一定作用的一个零件或一个简单部件,分为:
2.4 装焊生产设备及工艺装备
焊接夹具
夹具的组成
谢 谢!
顶盖
侧围
弧焊
弧焊
弧焊
弧焊
Page *
第二部分 装焊工艺
2.3 装焊生产工艺流程
左/右侧围总成工艺流程
侧围总成爆炸图
Page *
左/右车门工艺流程
车门总成爆炸图
汽车车身焊装工艺技术(DOCX 51页)
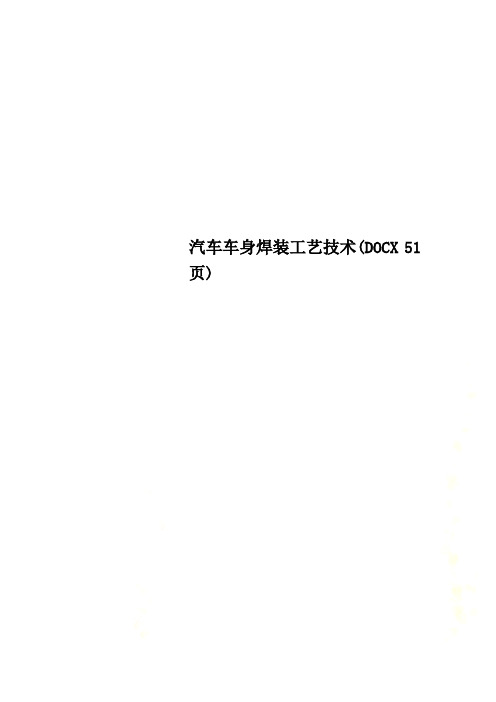
汽车车身焊装工艺技术(DOCX 51页)汽车车身焊装工艺汽车车身装配主要采用焊接方式,在汽车车身结构设计时就必须考虑零部件的装配工艺性。
焊装工艺设计与车身产品设计及冲压工艺设计是互相联系、互相制约的,必须进行综合考虑,它是影响车身制造质量的重要因素。
第一节焊装工艺分析工艺性好坏的客观评价标准就是在一定的生产条件和规模下,能否保证以最少的原材料和加工劳动量,最经济地获得高质量的产品。
影响车身焊装工艺性的主要因素有生产批量、车身产品分块、焊接结构、焊点布置等。
一.生产批量车身的焊装工艺主要由生产批量的大小确定的。
一般来说,批量越小,夹具的数量越少,自动化程度越低,每台夹具上所焊的车身产品件数量越多;反之,批量越大,焊装工位越多,夹具数量越多,自动化程度越高,每台夹具上所焊的车身产品件数量越少。
1.生产节拍的计算生产节拍是指设备正常运行过程中,单位产品生产所需要的时间。
假设某车年生产纲领是30000辆份 / 年工作制:双班,250个工作日,每个工作日时间为8小时设备开工率:85%则生产节拍的计算为:2.时序图设计时序图(TIME CHART)是指一个工位从零部件上料到焊好后合件取料的整个过程中所有动作顺序、时间分配以及相互间互锁关系,这些动作包括上下料(手动或自动),夹具夹紧松开,自动焊枪到位、焊接、退回以及传送装置的运动等。
生产线上每个工位的时序图设计总时间以满足生产节拍为依据,同时时序图也是焊装线电气控制设计的技术文件和依据,是机电的交互接口。
如图4-1所示为一张时序图,它的内容包括:(1)设备名称,它是以完成动作的单元来划分。
例如移动装置,夹具单元1,焊接,车身零部件名称等。
其中车身零件名称表示上料动作,组件名称表示取料动作。
2)相应设备的动作名称,它是以动力源的动作来划分的。
例如移动装置是由气缸驱动上下运动和电机驱动工位间前后运动组成,它的动作名称分别为上升,下降,前进,后退;再例如夹具是由夹紧气缸驱动夹紧,它的动作名称分为夹紧,打开等。
汽车焊装工艺流程

汽车焊装工艺流程
《汽车焊装工艺流程》
汽车焊装工艺流程是汽车制造过程中的重要环节。
焊装是指将各个零部件通过焊接工艺连接成整车的过程。
在汽车制造过程中,焊接工艺是非常关键的环节,它直接影响着汽车的质量和性能。
汽车焊装工艺流程通常包括以下几个步骤:
1. 材料准备:在焊装工艺开始之前,首先需要准备好各种焊接材料,包括焊丝、焊剂、焊接工具等。
2. 零部件安装:在焊接之前,需要将各个零部件先进行安装,确保它们的位置和角度都是正确的。
3. 焊接工艺选择:根据不同的零部件和焊接要求,选择合适的焊接工艺,包括气体保护焊、电弧焊、激光焊等。
4. 焊接操作:根据焊接工艺的要求,进行具体的焊接操作,确保焊接的质量和牢固度。
5. 检测和修复:完成焊接后,需要进行质量检测,确保焊接的质量达标。
如有不合格的地方,需要及时修复。
6. 表面处理:最后还需要对焊接部位进行表面处理,确保其外观和防腐性能。
总的来说,汽车焊装工艺流程是一个非常复杂和精细的过程,需要工匠们的精湛技艺和严谨态度。
只有通过严格的流程控制和质量管理,才能保证汽车焊装工艺的质量和可靠性。
汽车厂焊装车间工艺流程

汽车厂焊装车间工艺流程英文回答:The process flow in the welding workshop of an automobile factory involves several steps. Let's take a look at the general process:1. Preparation: The first step is to prepare the materials and equipment needed for the welding process. This includes ensuring that the welding machines are in good working condition and that all necessary materials, such as metal sheets and welding rods, are available.2. Assembly: The next step is to assemble the parts that need to be welded. This can involve joining different metal sheets together or attaching various components to the main structure of the car. The parts are carefully positioned and clamped in place to ensure proper alignment during the welding process.3. Welding: Once the parts are assembled, the actual welding process begins. This typically involves using electric arc welding, which melts the metal at the joint and fuses it together. The welder carefully controls the welding machine to ensure proper heat and penetration, resulting in a strong and durable weld.4. Inspection: After the welding is complete, the welded joints are inspected for quality. This can involve visual inspection to check for any visible defects, such as cracks or incomplete fusion. Non-destructive testing methods, such as ultrasonic or X-ray inspection, may also be used to detect any internal defects that are not visible to the naked eye.5. Finishing: Once the welding and inspection are done, the welded parts may undergo further finishing processes. This can include grinding down any excess weld material to achieve a smooth surface, as well as painting or coating the welded joints to protect them from corrosion.6. Final inspection: Before the welded parts are sentto the next stage of the production process, a final inspection is conducted to ensure that all quality standards have been met. This can involve checking the dimensions and alignment of the welded parts, as well as conducting additional tests to verify the strength and integrity of the welds.中文回答:汽车厂焊装车间的工艺流程包括以下几个步骤。
汽车焊装工艺整体流程
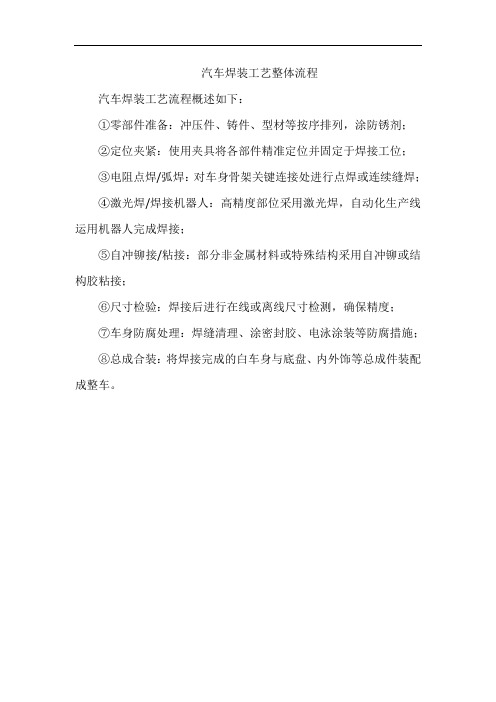
汽车焊装工艺整体流程
汽车焊装工艺流程概述如下:
①零部件准备:冲压件、铸件、型材等按序排列,涂防锈剂;
②定位夹紧:使用夹具将各部件精准定位并固定于焊接工位;
③电阻点焊/弧焊:对车身骨架关键连接处进行点焊或连续缝焊;
④激光焊/焊接机器人:高精度部位采用激光焊,自动化生产线运用机器人完成焊接;
⑤自冲铆接/粘接:部分非金属材料或特殊结构采用自冲铆或结构胶粘接;
⑥尺寸检验:焊接后进行在线或离线尺寸检测,确保精度;
⑦车身防腐处理:焊缝清理、涂密封胶、电泳涂装等防腐措施;
⑧总成合装:将焊接完成的白车身与底盘、内外饰等总成件装配成整车。
客车车身焊接工艺及焊装质量的控制措施

客车车身焊接工艺及焊装质量的控制措施一、客车车身焊接工艺:客车车身焊接工艺是指在焊接过程中所采用的具体方法和步骤。
正确的焊接工艺可以确保焊接质量,提高车身的强度和耐久性。
常见的客车车身焊接工艺包括下列几种:1. 电弧焊接:电弧焊接是一种常用的焊接方法,通过电弧的热量将焊条和工件熔化并连接起来。
在客车车身的焊接过程中,常使用电弧焊接法进行连接和固定。
2. 气体保护焊接:气体保护焊接是一种在焊接过程中使用保护气体的焊接方法,常使用惰性气体如氩气来保护熔化的金属,防止氧化和污染。
3. 焊接变形控制技术:在客车车身焊接过程中,经常会出现焊接变形的问题,主要是由于热应力引起的。
通过采用适当的焊接变形控制技术,可以有效降低焊接变形的程度。
二、焊装质量的控制措施:1. 选用合适的焊接设备:选择适合的焊接设备是确保焊装质量的首要步骤。
合适的焊接设备可以提供稳定的焊接工艺参数和高质量的焊接效果。
2. 控制焊接材料的质量:焊接材料的质量对焊装质量有很大影响。
在选择焊接材料时,应根据客车车身的材料特性和焊接要求进行选择,并确保焊接材料符合相应的标准和规范。
3. 控制焊接工艺参数:焊接工艺参数是影响焊接质量的重要因素。
通过合理调整焊接电流、电压、焊接速度等参数,可以控制焊接过程中的热量输入和焊接强度,提高焊接质量。
4. 焊接过程监控:焊接过程监控是对焊装质量进行有效控制的重要手段。
通过采用焊接过程监控技术,可以对焊接过程中的温度、应力、变形等进行实时监测和控制,及时发现并修正焊接缺陷。
5. 焊接质量检测:焊接质量的检测是确保焊装质量的重要环节。
采用合适的检测方法和设备,对焊接接头的外观、尺寸、成分和性能等进行全面检测,及时发现焊接缺陷并采取相应的措施进行修正。
6. 定期维护和保养:为保证焊装质量的稳定性和可靠性,需要定期维护和保养焊接设备和工具。
定期对焊接设备进行检修、维护和校准,确保焊接设备的性能和稳定性。
通过正确的焊接工艺和焊装质量的控制措施,可以提高客车车身的焊接质量,确保车身的强度和耐久性,提高客车的安全性和舒适性。
白车身焊装焊接工艺

白车身焊装焊接工艺The saying "the more diligent, the more luckier you are" really should be my charm in2006.车身焊接工艺一、车身装焊工艺的特点汽车车身壳体是一个复杂的结构件,它是由百余种、甚至数百种薄板冲压件经焊接、铆接、机械联结及粘接等方法联结而成的;由于车身冲压件的材料大都是具有良好焊接性能的低碳钢,所以焊接是现代车身制造中应用最广泛的联结方式;表1列举了车身制造中常用的焊接方法:表1 车身制造中常用的焊接方法及典型应用实例焊接方法典型应用实例电阻焊点焊单点焊悬挂式点焊机车身总成、车身侧围等分总成固定式点焊机小型板类零件多点焊压床式多点焊机车身底板总成C形多点焊接车门、发动机盖总成缝焊悬挂式缝焊机车身顶盖流水槽固定式缝焊机油箱总成凸焊螺母、小支架电弧焊CO2气体保护焊车身总成亚弧焊车身顶盖后两侧接缝手工电弧焊厚料零部件气焊氧—乙炔焊车身总成补焊钎焊锡钎焊水箱特种焊微弧等离子焊车身顶盖后角板激光焊车身底板车身制造中应用最多的是电阻焊,一般占整个焊接工作量的60%以上,有的车身几乎全部采用电阻焊;除此之外就是二氧化碳碳气体保护焊,它主要用于车身骨架和车身总成的焊接中;由于车身零件大都是薄壁板件或薄壁杆件,其刚性很差,所以在装焊过程中必须使用多点定位夹紧的专用装焊夹具,以保证各零件或合件在焊接处的贴合和相互位置,特别是门窗等孔洞的尺寸等;这也是车身装焊工艺的特点之一;为便于制造,车身设计时,通常将车身划分为若干个分总成,各分总成又划分为若干个合件,合件由若干个零件组成;车身装焊的顺序则是上述过程的逆过程,即先将若干个零件装焊成合件,再将若干个合件和零件装焊成分总成,最后将分总成和合件、零件装焊成车身总成;轿车白车身装焊大致的程序图为如图1所示:电阻焊1.电阻焊及其特点将置于两电极之间的工件加压,并在焊接处通以电流,利用电流通过工件本身产的的热量来加热而形成局部熔化,断电冷却时,在压力继续作用下而形成牢固接头;这种工艺过程称为电阻焊;电阻焊的种类很多,按接头形式可分为搭接电阻焊和对接电阻焊两种;结合工艺方法,搭接电阻焊又可分为点焊、缝焊和凸焊三种,对接电阻焊一般有电阻对焊和闪光对焊两种;特点:(1)利用电流通过工件焊接处的电阻而产生的热量对工件加热;即热量不是来源于工件之外,而是内部热源;(2)整个焊接过程都是在压力作用校完成的,即必须施加压力;(3)在焊接处不需加任何填充材料,也不需任何保护剂;形成电阻焊接头的基本条件只有电极压力和焊接电流;2.点焊点焊是利用在焊件间形成的一个个焊点来联接焊件的;两焊件被压紧于两柱形电极之间并通以强大的电流,利用电阻热将工件焊接区加热到形成应有尺寸的熔化核心为止;然后切断电流,熔核在压力作用下冷却结晶形成焊点;点焊在车身制造中应用最广;点焊的形式很多,但按供电方向来分只有单面点焊和双面点焊两种;在这两种点焊中按同时完成的焊点数又可分为单点、双点和多点焊;点焊是车身制造中应用最广的焊接方法,一辆轿车的车身上有3500~5000个焊点,可以说,汽车车身是一个典型的点焊结构件;(1)点焊的机械性质A.与铆接和螺栓紧固相比,点焊无松动且刚性高,但滑动系数小,在设计时必须注意可能会出现的应力集中;B.点焊没有像铆接和螺栓紧固那样的铆钉头和螺帽,所以剥离方向的抗拉强度不如铆接和螺栓紧固,但剪切强度可以选取较大的焊点直径的以保证,因为可以说点焊优于铆接和螺栓紧固;C.点焊的疲劳强度,对于单纯的剪切载荷而言语铆接等差别不大,但在板有变形时及承受剥离方向重复的载荷时,其疲劳强度软弱;D.由于点焊焊点部分的金属组织不均匀,所以机械强度也不相同,一般周边强度大,中心部强度小;(2)点焊工艺要求A.焊点质量的一般要求点焊结构靠单个或若干个合格的焊点实现接头的连接,接头质量的好坏完全取决于焊点质量及点距;焊点质量除了取决于焊点尺寸外,还与焊点表面与内部质量有关;焊点外观上要求表面压坑浅、平滑呈均匀过渡,无明显凸肩或局部挤压的表面鼓起;外表面没有环状或颈项裂纹,也无熔化、烧伤或粘附的铜合金;从内部看,焊点形状应规则、均匀,无超标的裂纹和缩孔等内部缺陷及热影响区金属的组织与力学性能有无发生明显的变化等;不同厚度板和多层板的焊接,点焊和板厚的关系两层点焊时:图2所示;图2三层焊点时:图3所示;图3点焊的使用范围由板厚方面来看:点焊用于薄板重叠搭接,虽然损失了重叠部分的材料,但使总成装配加工变得容易;如果板厚较大的话,重叠部分的材料也随之增大,如果用对接接缝,熔焊焊接也不困难;与之相反,随着点焊板厚的增加,由于焊机电气设备等机械电气容量成倍增大,点焊变得十分不利;根据上述理由,一般点焊的板厚为1.6mm以下,板厚在~3.2mm之间,很难判定是采用熔焊还是采用点焊,但在板厚为3.2mm以上,多数结构不采用点焊;汽车车身覆盖件大都是低碳钢的薄板;表2为低碳钢板点焊的最小间距,最小搭接及强度,可供选取焊接规范时参考;表2注:a.本表所示的被焊件材料的抗拉强度为30~32kgf/mm2b.强度为剪切强度c.强度是按焊接手册的数值,并按焊点直径成比例计算出来的,不是实验数据;d.最小焊点间距表示了实质上能忽略相邻点点焊分流效应的极限值;e.最小搭接是如图4所示尺寸表示的长度;f.不等厚板焊接时,按薄板考虑;图4B.点焊所需的最小空间:图5所示;图5(3)点焊设备焊件的点焊是在点焊机上完成的;点焊机的种类很多,按用途可分为通用的和专用的两大类;专用的点焊机主要是多点点焊机;通用式点焊机按安装方法又可分为固定式、移动式或悬挂式点焊机;按电源性质分为Ⅰ频、脉冲及变频点焊机;按加压机构的传动装置分为脚踏式、电动凸轮式、气压传动式及液压传动式点焊机等;但不论哪一类点焊机,一般均由供电系统、控制系统、加压机构和冷却系统等几部分组成;固定式点焊机在车身焊接中主要用来点焊合件、分总成和一些较小的总成;焊机不动,每焊完一个焊点后,焊件移动一个点距,以进行下一个焊点的焊接;移动式点焊机可以用在不便用固定式点焊机焊接的外形尺寸大的车身零部件;悬挂式点焊机是将焊接变压器和焊接工具悬挂在空中,移动方便灵活,适合于装焊大型薄板件;按变压器与焊具连接方式,分为有缆式和无缆式两种;有缆悬挂式点焊机的焊钳与变压器之间用一种特殊的电缆连接,其优点是移动方便,适合于大总成的点焊,劳动强度低;缺点是二次回路长,功率损耗大;无缆悬挂式点焊机,它的焊接工具部分与变压器直接连接,其优点是由于没有二次回路中电缆损耗,功率利用充分,在焊接同样厚度的材料时,变压器的功率和体积均可减小;缺点是移动起来不方便;3.缝焊缝焊类似于连续点焊,是以旋转的滚盘状电极代替点焊的柱状电极;所以缝焊的焊缝实质上是由许多彼此互相重叠的焊点组成;缝焊按滚盘转动与馈电方式可分为连续缝焊,断续缝焊和步进式缝焊等;缝焊主要用于要求气密性的焊缝.缝焊也是电阻焊,焊接原理跟点焊一样,只不过是缝焊用滚盘代替了点焊的电极,焊件置于两滚盘之间,靠滚盘转动带动焊件向前移动;同时通以焊接电流,形成类似连续点焊的焊缝;缝焊按滚盘转动与馈电方式分为:连续缝焊、断续缝焊和步进式缝焊;按供电方向或一次成缝条数也可分为单面缝焊、双面缝焊、单缝缝焊和双缝缝焊等;断续缝焊时,滚盘连续转动,焊件在两滚盘间连续移动,而焊接电流断续接通;由于焊接电流间断地接通,滚盘和焊件有冷却的机会,滚盘损耗小,焊缝也不易过热,因此应用最广泛;由于缝焊的分流较大,故焊接电流一般比点焊增加20~60%,具体数值视材料厚度和点距而定;要求气密性的缝焊接头,各焊点之间必须有一定的重叠,通常焊点间距应比焊点直径小30~50%,焊点间距可按下列经验公式选取;对于低碳钢 C=~t对于铝合金 C=~t式中 C——缝焊焊点间距mm; t——两焊件中较薄焊件的厚度mm;对于非气密性接头,焊点间距可在很宽的范围内变化,甚至可以使各相邻焊点相互分离,成为缝点焊;缝焊工艺参数主要是根据被焊金属的性能、厚度、质量要求和设备条件来选择,通常可参考已有的推荐数据初步确定表3,再通过工艺试验加以修正;表3 低碳钢的缝焊规范凸焊是点焊的一种变型,它是利用零件原有的能使电流集中的型面、倒角或预控制的凸点来作为焊接部位的;凸焊时,一次可在接头处形成一个或多个熔核;在汽车车身制造中,凸焊主要用于将较小的零件如螺母、垫圈等焊到较大的零件上;凸焊与点焊相比,其不同点是在焊件上预先加工出凸点,或利用焊件上原有的能使电流集中的型面、倒角等作为焊接时的局部接触部位;因为是凸点接触,提高了单位面积上的压力与电流,有利于板件表面氧化膜的破裂与热量的集中,减小了分流电流,一次可进行多点凸焊,提高了生产率,并减小了接头的变形;凸焊的特征:(1)即使热容量明显不同的组合也很容易得到良好的热平衡焊接厚板和薄板时,厚板上加上突点,厚板的热容量就等于薄板的热容量;(2)可得到与板厚无关的低强度焊接点焊时根据板厚决定焊点的大小;(3)电极寿命长,操作效率高;(4)能进行焊点间距小的点焊;凸焊的标准凸起形状如表4和图6所示;表4注:凸起的大小取决于薄板的板厚,凸起在厚板上加工;图6凸焊由于需要预先冲制出凸起部分,所以比点焊多一些焊前准备的工序和设备;因而,在选用凸焊时,必须全面考虑; 为了使各个凸点熔化能均匀一致,凸焊时电极压力和焊接电流应均匀地分布在同时焊的各个凸点上;为此,凸点冲制必须精确,尺寸稳定,且焊件必须仔细清理;5.二氧化碳气体保护焊二氧化碳气体保护焊是一种熔化极气体保护电弧焊接法,它利用焊丝与工件间产生的电弧来熔化金属,由CO2气体作为保护气体,并采用光焊丝作为填充金属; 1CO2气体保护焊与其他电弧焊相比,具有以下优点:生产率高;操作性能好;焊接质量高;对铁锈的敏感性小;成本低;易于实现机械化和自动化;气体保护焊的适应性强,应用范围广; 2二氧化碳气体保护焊的规范参数,主要有电源极性、焊丝直径、电弧电压、焊接电流、气体流量、焊接速度、焊丝伸出长度、直流回路电感等;选择这些参数的原则是:要在保证焊接质量的前提下,尽可能提高劳动生产率,并要注意焊接规范参数对飞溅,气孔、焊缝形成及焊接过程稳定性的影响,在汽车车身焊接中,常用的CO2气体保护焊焊接规范列于表5中;表5 CO2气体保护焊焊接规范气体保护焊自动焊机是由焊接电源、送丝机构、行走机构、焊矩、气路系统和控CO2制系统等部件组成;气路系统包括减压阀、预热器、干燥器和流量计等;CO气体保护焊2半自动焊机中设有行走机构,其余部分与自动焊机相同;CO焊电源有如下几种:抽头式硅整流电源、高漏抗式硅整流电源、自调电感式硅2整流电源、自饱和和电抗器式硅整流电源、可控硅式整流电源和晶体管式整流电源等;为了获得较高的焊接质量,现在大都采用可控硅整流电源;送丝机构的作用是将焊丝按要求的速度送至焊接电弧区,以保证焊接的正常进行,一气体保护焊半自动焊机根据其送丝方式的不同,有推丝式、般都采用等速送丝方式;CO2拉丝式和推拉丝式三种送丝机构,推丝式送丝机构用于直径较粗的焊丝;拉丝式送丝机构稳定可靠,焊工操作范围也不受限制,推拉丝式结构复杂,制作技术要求高,国内很少应用;国内焊机常采用双主动式送丝辊轮,辊轮直径一般为30~40mm;焊枪是直接施焊的工具,起到导电、导丝、导气的作用;常用的半自动焊枪有拉丝焊枪、推丝式手枪形焊枪和推丝式鹅颈形焊枪;二、激光焊接激光焊接是本世纪汽车工业上应用的新技术;它的原理是利用原子受辐射,使工作物质受激而产生的一种单色性高、方向性强、亮度高的光束,经聚焦后把光束聚焦到焦点上可获得极高的能量密度,利用它与被焊工件相互作用,使金属发生蒸发、融化、熔合、结晶、凝固而形成焊缝;1.激光焊接特点A.由于激光束的频谱宽度窄,经汇聚后后的光斑直径可小到0.01mm,功率密度可达109W/cm2,它和电子束焊同属于高能焊;可焊~50mm厚的工件;B.脉冲激光焊加热过程短、焊点小、热影响区小;C.与电子束焊相比,激光焊不需要真空,也不存在X射线防护问题;D.能对难以接近的部位进行焊接,能透过玻璃或其他透明物体进行焊接;E.激光不受电磁场的影响;F.激光的电光转换效率低;工件的加工和组装精度要求高,夹具要求精密,因此焊接成本高;激光焊接的特点是被焊接工件变形极小,几乎没有连接间隙,焊接深度/宽度比高,例如焊缝宽1毫米,深为5毫米,因此焊接极为牢固,表面焊缝宽度很小,连接间隙实际为零,焊接质量比传统方法高;所以在一些用激光焊接的汽车顶壳是不用装饰条遮蔽焊接线的;在汽车制造中,激光焊接主要用于车身框架结构的焊接,例如顶盖与侧面车身的焊接,传统焊接方法的电阻点焊已经逐渐被激光焊接所取替;用激光焊接技术,既提高了工件表面的美观,又降低了板材使用量,由于零件焊接部位几乎没有变形,不需要焊后热处理,还提高了车身的刚度;2.激光焊接设备激光焊接设备的关键是功率激光器,主要有两大类,一是固体激光器,又称Nd:YAG激光器;Nd钕是一种稀土族元素,YAG代表钇铝柘榴石,晶体结构与红宝石相似;Nd:YAG激光器波长为μm,优点是产生的光束可以通过光纤传送,因此可以省去复杂的光束传送系统,适用于柔性制造系统,通常用于焊接精度要求比较高的工件;汽车工业常用输出功率为3-4千瓦的Nd:YAG激光器;另一类是气体激光器,又称CO2激光器,分子气体作工作介质,产生平均为μm的红外激光,可以连续工作并输出很高的功率,激光功率在2-5千瓦之间,目前已有2 0千瓦在实验运用;。
车身焊装工艺全面介绍

电弧焊 电弧焊
追求不断创新
二、焊装车间工艺流程
侧围总成 地板总成
左右后侧面 车门总成
左右前侧面 车门总成
车身总拼
车身调整
品质检验
发动机 舱总成
顶盖
前围上部总成
后挡板门总成
发动机罩总成 及翼子板
涂装车间
追求不断创新
三、焊装车间的管理特征
面品控制
关
焊接强度
焊点直径和焊接强度都随焊接电流的增加而增大。但电流过大且压力较 小时,也会造成板间的飞溅;反之则可能将飞溅减至最小程度。 3)、通电时间
通电时间长,则热量生成多、焊点直径大、熔深也深。但通电时间过长 也未必有利,如果电流一定,则通电时间过于延长也不会使焊点增大,反 而还会出现电极压痕和热变形现象。
追求不断创新
三 焊装车间的管理特征
四 焊装车间质量特征 五 焊接工艺编制说明
追求不断创新
一、焊接基础知识
(一).焊接的定义
两种或两种以上同种或异种材料通过原子或分 子之间的结合和扩散连接成一体的工艺过程。 促使原子或分子之间产生结合和扩散的方法是加 热或加压,或同时加热又加压。
追求不断创新
一、焊接基础知识
(二).焊接的分类
控制指的是,在进行电阻点焊的过程中,应用相应的技术进行在线监 测,保证不合格焊点被及时发现。
检验指的是,对已经完成的焊点进行破坏性和非破坏性检查,达到 排除不合格焊点的目的。破坏性检查是对整个车身的焊点进行逐一检 查,比较全面,可以发现所有不合格的焊点。但是,检查后的车身只 能报废,且抽样频率较低,不利于问题的及时发现。非破坏性检查是 对车身焊点进行的日常检查,传统的方法是目视检查和凿检,一般选 取部分典型焊点,且有一定的局限性。
汽车厂焊装车间工艺流程
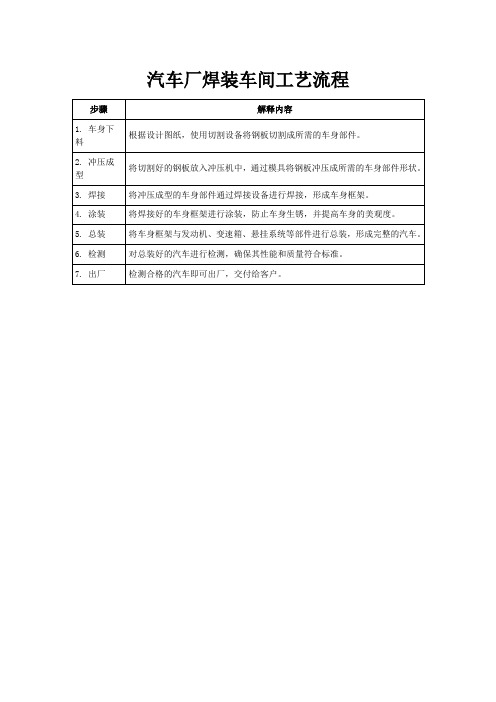
步骤
解释内容
1. 车身下料
根据设计图纸,使用切割设备将钢板切割成所需的车身部件。
2. 冲压成型
将切割好的钢板放入冲压机中,通过模具将钢板冲压成所需的车身部件形状。
3. 焊接
将冲压成型的车身部件通过焊接设备进行焊接,形成车身框架。
4. 涂装
将焊接好的车身框架进行涂装,防止车身生锈,并提高车身的美观度。
5. 总装
将车身框架与发动机、变速箱、悬挂系统等部件进行总装,形成完整的汽车其性能和质量符合标准。
7. 出厂
检测合格的汽车即可出厂,交付给客户。
焊装滚边工艺
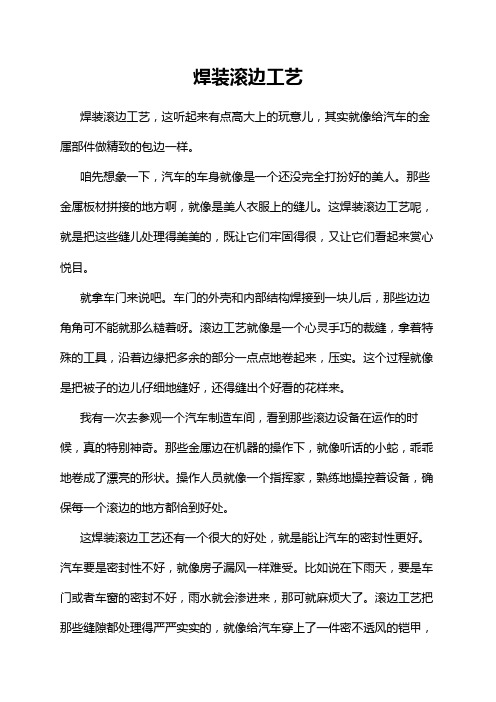
焊装滚边工艺焊装滚边工艺,这听起来有点高大上的玩意儿,其实就像给汽车的金属部件做精致的包边一样。
咱先想象一下,汽车的车身就像是一个还没完全打扮好的美人。
那些金属板材拼接的地方啊,就像是美人衣服上的缝儿。
这焊装滚边工艺呢,就是把这些缝儿处理得美美的,既让它们牢固得很,又让它们看起来赏心悦目。
就拿车门来说吧。
车门的外壳和内部结构焊接到一块儿后,那些边边角角可不能就那么糙着呀。
滚边工艺就像是一个心灵手巧的裁缝,拿着特殊的工具,沿着边缘把多余的部分一点点地卷起来,压实。
这个过程就像是把被子的边儿仔细地缝好,还得缝出个好看的花样来。
我有一次去参观一个汽车制造车间,看到那些滚边设备在运作的时候,真的特别神奇。
那些金属边在机器的操作下,就像听话的小蛇,乖乖地卷成了漂亮的形状。
操作人员就像一个指挥家,熟练地操控着设备,确保每一个滚边的地方都恰到好处。
这焊装滚边工艺还有一个很大的好处,就是能让汽车的密封性更好。
汽车要是密封性不好,就像房子漏风一样难受。
比如说在下雨天,要是车门或者车窗的密封不好,雨水就会渗进来,那可就麻烦大了。
滚边工艺把那些缝隙都处理得严严实实的,就像给汽车穿上了一件密不透风的铠甲,不管外面是狂风还是暴雨,车里都能保持干爽舒适。
再说说安全方面。
牢固的滚边就像是给汽车的关键部位上了一道保险。
在发生碰撞或者震动的时候,那些经过滚边处理的部件就不容易散架或者变形。
这就好比我们用绳子捆绑东西,如果只是简单地绕一圈,很容易就松开了,但是如果把绳子的接头处好好地处理一下,像滚边这样把它弄牢固,那东西就不容易散开了。
而且,从美观的角度看,滚边后的汽车部件看起来更加精致。
这就像我们给一幅画装裱边框一样,一个漂亮的边框能让画增色不少。
汽车的滚边就像是那精美的边框,让汽车整体的外观更加高档大气。
在实际操作这个焊装滚边工艺的时候,可不像我们想象的那么简单。
这需要操作人员有丰富的经验和高超的技巧。
就像做饭一样,同样的食材,不同的厨师做出来的味道就是不一样。
汽车生产的总装工艺简介
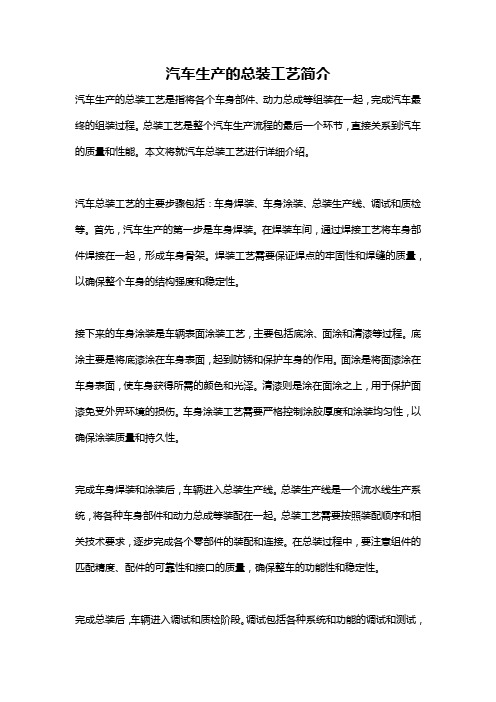
汽车生产的总装工艺简介汽车生产的总装工艺是指将各个车身部件、动力总成等组装在一起,完成汽车最终的组装过程。
总装工艺是整个汽车生产流程的最后一个环节,直接关系到汽车的质量和性能。
本文将就汽车总装工艺进行详细介绍。
汽车总装工艺的主要步骤包括:车身焊装、车身涂装、总装生产线、调试和质检等。
首先,汽车生产的第一步是车身焊装。
在焊装车间,通过焊接工艺将车身部件焊接在一起,形成车身骨架。
焊装工艺需要保证焊点的牢固性和焊缝的质量,以确保整个车身的结构强度和稳定性。
接下来的车身涂装是车辆表面涂装工艺,主要包括底涂、面涂和清漆等过程。
底涂主要是将底漆涂在车身表面,起到防锈和保护车身的作用。
面涂是将面漆涂在车身表面,使车身获得所需的颜色和光泽。
清漆则是涂在面涂之上,用于保护面漆免受外界环境的损伤。
车身涂装工艺需要严格控制涂胶厚度和涂装均匀性,以确保涂装质量和持久性。
完成车身焊装和涂装后,车辆进入总装生产线。
总装生产线是一个流水线生产系统,将各种车身部件和动力总成等装配在一起。
总装工艺需要按照装配顺序和相关技术要求,逐步完成各个零部件的装配和连接。
在总装过程中,要注意组件的匹配精度、配件的可靠性和接口的质量,确保整车的功能性和稳定性。
完成总装后,车辆进入调试和质检阶段。
调试包括各种系统和功能的调试和测试,如发动机、制动系统、悬挂系统等。
调试的目的是验证车辆各个零部件和系统的正常工作,确保车辆具备良好的性能和安全性。
质检阶段是对整车进行全面的质量检查,包括外观检查、功能检测、油漆质量检验等,以确保整车符合相应的技术规范和质量要求。
总体来说,汽车生产的总装工艺是一个复杂而精细的过程。
各个工艺步骤之间存在密切的关联和依赖关系,需要严格控制各个环节的质量和工艺参数。
同时,总装工艺也需要合理的生产组织和管理,以提高生产效率和降低生产成本。
随着科技的不断进步,汽车总装工艺也在不断创新和发展。
例如,现代汽车生产中已经引入了自动化生产设备和机器人技术,以提高生产效率和降低生产成本。
汽车四大工艺流程

汽车四大工艺流程
《汽车四大工艺流程》
汽车制造过程中有四大工艺流程,分别是冲压、焊装、涂装和总装。
冲压工艺是汽车零部件加工的第一道工序,通过冲压设备将板材加工成所需形状的零部件,比如车门、引擎盖等。
冲压工艺流程需要精密的模具和设备,能够高效地生产出各种形状的零部件。
焊装工艺是将冲压好的零部件进行焊接组装,形成汽车的车身结构。
焊装工艺需要高精度的焊接设备和工艺技术,能够确保汽车的结构强度和安全性。
涂装工艺是对焊装好的车身进行表面处理和喷漆,使汽车具有良好的外观和防腐蚀性能。
涂装工艺流程需要严格的环境控制和精密的喷涂设备,确保汽车表面质量和涂层均匀性。
总装工艺是将经过冲压、焊装和涂装的零部件进行装配,形成完整的汽车产品。
总装工艺需要高效的生产线和工艺流程,能够将各种零部件快速、准确地组装到汽车上,确保汽车质量和生产效率。
四大工艺流程共同构成了汽车制造的关键环节,是确保汽车质量和生产效率的重要过程。
随着科技的进步和工艺水平的提高,
汽车制造工艺流程不断优化和改进,将为汽车制造业的发展和进步带来新的机遇和挑战。
汽车车身焊装工艺

8
(3)凸焊
利用使电流集中的凸点来作为焊接部位的。 在接头处形成一个或多个熔核。
上电极 螺母
工件
定位销
绝缘套
电极
10章车身焊装工艺
9
气体保护焊接机KRII200
10章车身焊装工艺
10
10章车身焊装工艺
11
缝焊机
10章车身焊装工艺
12
(4)对焊 电阻对焊是用夹具桨两焊件夹紧,并使之 端面相互挤紧,然后通电加热。
10章车身焊装工艺
10.3点 焊
41
(2)零件装配
装配缺陷是间隙过大和位置错移。均造成制件 焊后变形或应力过大。
间隙↑→电极压力将消耗于压紧间隙,焊接压力↓ 飞溅倾向↑→焊核尺寸和接头强度波动↑焊接变形↑
一般装配间隙<(0.5-0.8)mm,焊接尺寸较小而刚度 较大的冲压件时,应减小到(0.1-0.2)mm.
规范3
焊接电 流变压 器级数 (千安/ 级数) 焊接 时间( 秒/周 波) 电 极 压 力 /N
规范4
焊接 电流 变压 器级 数 (千 安/ 级数 ) 9.5 /5 10. 5/6 11. 5/7 13. 5/8 ----焊接 时间 (秒/ 周波 )
0.8 1.0 1.2 1.5 1.8 2.0
180 0 225 0 300 0 380 0 -----
车身焊装工艺流程,正确焊接顺序为
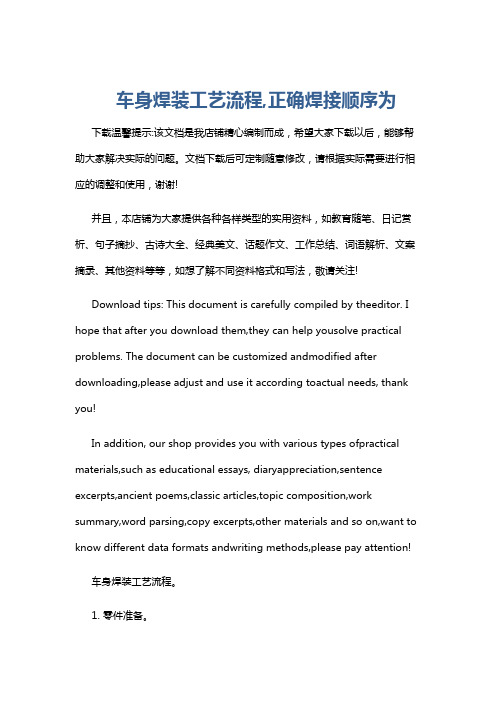
车身焊装工艺流程,正确焊接顺序为下载温馨提示:该文档是我店铺精心编制而成,希望大家下载以后,能够帮助大家解决实际的问题。
文档下载后可定制随意修改,请根据实际需要进行相应的调整和使用,谢谢!并且,本店铺为大家提供各种各样类型的实用资料,如教育随笔、日记赏析、句子摘抄、古诗大全、经典美文、话题作文、工作总结、词语解析、文案摘录、其他资料等等,如想了解不同资料格式和写法,敬请关注!Download tips: This document is carefully compiled by theeditor. I hope that after you download them,they can help yousolve practical problems. The document can be customized andmodified after downloading,please adjust and use it according toactual needs, thank you!In addition, our shop provides you with various types ofpractical materials,such as educational essays, diaryappreciation,sentence excerpts,ancient poems,classic articles,topic composition,work summary,word parsing,copy excerpts,other materials and so on,want to know different data formats andwriting methods,please pay attention!车身焊装工艺流程。
1. 零件准备。
对冲压件、铸件、锻件等组成零件的清洗、除锈、表面处理。
项目七 汽车车身焊装基础知识
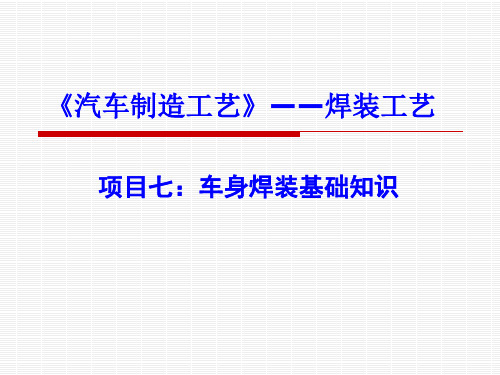
4.白车身总成调整线
每一个车身都要经过一系列精心 的调试,保证各项工艺间隙的精 确度,任何一个不平整的小瑕疵 在车身经过检测光廊时都无所遁 形。
4.车身焊接工艺性 1)易实现焊接 通过选择合适的焊钳,对焊接位置进行 模拟,保证实现焊接。在进行焊钳选择时,尽量选择常 见型号的焊钳,减少焊钳种类和备品备件种类,便于焊 钳通用和车间管理。合理选择点焊钳型号可以实现焊接 设备和作业人员数量合理、作业方便、减低劳动强度等 效果。 2)保证焊接质量 匹配过程中,焊接区域尽量保持平面, 减少曲面焊接,减少焊点扭曲。
5. 焊装夹具
焊装夹具用于焊接工件的定位夹紧,保证所属焊装零件之 间的相对位置和焊接件的尺寸精度,减少焊装过程中焊接 件的变形,提高焊装生产率,是保证车身焊装精度的最重 要的因素。
焊装夹具的主要作用有以下几个方面:
①准确、可靠的定位和夹紧,可以减轻甚至取消下料和划线工作。 减小制品的尺寸偏差,提高了零件的精度和可换性。
学习内容
车身焊装 工艺流程
车身 焊装设备
焊接的 概念
任务一:了解汽车车身焊装过程
1.轿车白车身的总成
车身前端总成工艺流程图
车身地板总成工艺流程图
车身后端总成工艺流程图
右侧围总成工艺流程图
白车身焊装工艺流程图
白车身装配工艺流程
2.车身焊装工艺
从车身制件到车身焊接总成的每一个过程,既相互 独立,又承前启后,因此组件的焊接精度决定着部件分总 成的焊接精度,最后影响和决定着车身总成的焊接精度与 质量。
汽车焊装工艺FMEA分析方法

2024年2月8日星期四
•教学目标及课程大纲:理解Q公司焊装工艺文件,并且能正确、熟练维护、编制焊装工艺文件!
1、学员了解焊装工艺文件种类,每一种文件是质量体系的那一阶段的活动 的输出,及每一种工艺文件作用。
2、学员熟悉焊装工艺流程图、PFMEA、控制计划表格文件中每一项目的意 义及在各种工艺中如何填写这些项目,如流程图中的变差来源、产品特 性、过程特性,FMEA中的预防、探测、风险,控制计划中的控制方法、 反应计划等。
填入FMEA文件的编号,以便查询(Q7200-04-BS-00/001 )。
FMEA 注明正在进行过程分析的系统、子系统或部件的名称和编号。 填入整车、部门和小组。如已知,还包括供方的名称。
关填键入日初期次是F指ME项A应目完计划成中的过时程间设,计该冻日结期日不期应,超此过日计期划不的能投超入过生SO产P批日准期日 编填制入日编期制为FMFEMAE原A编始制稿生的效日日期期及,最比新关期修键日订期的早日,期此。日(期Q公不司能更只改填原始
2、PFMEA应在开始生产之前、产品质量策划过程中进行,它是对新的/修改 的过程的一种规范化的评审与分析;是为新的/修改的产品项目指导其预防、解 决或监视潜在的过程问题。
3、PFMEA是一种动态文件,当发现新的失效模式时需要对它进行评审和更 新。FMEA 维护的另一个要素包括周期性的评审。特定的焦点应该放在发生率和 探测率的排序上。在有产品或过程更改或过程控制改善时,这尤其重要。此外 ,万一无论是市场问题或生产问题发生时,如中断,排序应由此而修改。
• 4、是一种事前行为,体现预防为主的思想
• 5、分析方法:从局部入手,分析对总成的影响
FMEA分类
• CFMEA——概念FMEA • DFMEA——设计FMEA • PFMEA——过程FMEA • MFMEA——机器FMEA
焊装工艺规划及布置

对于大型或复杂的重型机械零件,可以采用焊接机器人或自动化焊接设备,以提高 焊接质量和效率。
案例三:航空航天产品的焊装工艺特殊性
航空航天产品的焊装工艺需要满足高精 度、高强度、高可靠性的要求,因此需
和缺陷。
数据记录与分析
02
记录焊接过程的各种数据,如电流、电压、焊接速度等,分析
数据以评估工艺稳定性和产品质量。
持续改进
03
根据监控结果和数据分析,对工艺进行持续改进,提高焊接质
量和效率。
05
焊装工艺案例分析
案例一:汽车车身焊装线规划与布置
在布置汽车车身焊装线时,应 遵循工艺流程的顺序,合理安 排设备和工位的布局,以提高 生产效率。
要采用特殊的焊接工艺和材料。
航空航天产品的焊装工艺需要考虑到产 在航空航天产品的焊装工艺中,应注重
品的结构和性能特点,采用合适的焊接 焊接质量控制和检测,以确保焊接质量
方法和设备,以避免对产品造成损伤或 和可靠性。同时,还需要加强焊接安全
变形。
防护措施,保障操作人员的安全和健康。
06
总结与展望
当前焊装工艺的挑战与机遇
焊装工艺规划及布置
目
CONTENCT
录
• 引言 • 焊装工艺规划 • 焊装生产线布置 • 焊装工艺实施与管理 • 焊装工艺案例分析 • 总结与展望
01
引言
目的和背景
焊装工艺是汽车制造过程中的重要环节,其目的是将各个零件按 照设计要求进行精确的焊接,形成完整的白车身。
随着汽车工业的发展,对焊装工艺的要求越来越高,需要不断优 化和改进,以提高生产效率和产品质量。
- 1、下载文档前请自行甄别文档内容的完整性,平台不提供额外的编辑、内容补充、找答案等附加服务。
- 2、"仅部分预览"的文档,不可在线预览部分如存在完整性等问题,可反馈申请退款(可完整预览的文档不适用该条件!)。
- 3、如文档侵犯您的权益,请联系客服反馈,我们会尽快为您处理(人工客服工作时间:9:00-18:30)。
表3-2
焊接电流 A 6000~8000
1.2
1.3 2.0 3.0 4.0 5.0 6.0
6
6 8 8 10 11 13
1000~2500
1500~3500 2500~5000 5000~8000 6000~9000 8000~10000 10000~14000
0.25~0.50
0.25~0.50 0.35~0.60 0.60~1.00 0.80~1.20 0.90~1.50 1.20~2.00
三、车身焊装工艺方法
车身焊装工艺是一个广义的概念,是指将冲压成型的车身各组件组装
成一个完整白车身的全部工艺过程,其内容主要有焊接、滚/折边、涂胶、 合装、返修等。由于焊接工艺的比重超过90%以上,因此将其统称为焊装。 焊接:通过加热或者加压或者两者并用,添加或不加填充材料,使两 分离的工件在其接合表面达到原子间的结合,形成永久性连接的一种工艺 方法。常用的焊接工艺有五大类近20种不同的焊接工艺方法。
者减少通电时间。
3)带镀层钢板的点焊
点焊镀锌或镀铝钢板时,应比不带镀层的钢板提高电流 20~30%,并同时提高电极压力20%。
7、点焊质量检验
电焊质量的检验 最常用、最简单且最 有效的方法是撕开法, 如图3-7所示。优质焊 点的标志是:在撕开 试样的一片上有圆孔, 而另一片上有圆凸台。 厚板或经淬火处理的 材料有时不能撕出圆 孔和凸台,但可通过 剪切的断口判断熔核 的直径。
过小会引起严重飞溅。
2)焊接时间
对于给定的工件材料和厚度,焊接时间由焊接电流和凸点 刚度决定。在凸焊低碳钢和低合金钢时,影响焊接质量的因素 主要是电极压力和焊接电流。在电极压力和焊接电流确定后, 通过调节焊接时间,以获得满意的焊接质量。若希望缩短焊接 时间,就要相应增大焊接电流,但过份增大焊接电流可能引起 金属过热和飞溅。通常情况下,凸焊的焊接时间比点焊长,而 电流比点焊小。多点凸焊的焊接时间稍长于单点凸焊,以减少 因凸点高度不一致而引起各点加热的差异。采用预热电流或电 流斜率控制(通过调幅使电流逐渐增大到需要值),可以提高 焊点强度的均匀性并减少飞溅。
二、车身焊接工艺布局
轿车车身的所有组成部件都由薄板冲压而成,汽车制造业将其统称为 冲压件,其中90%以上的冲压件的板厚只有0.6~0.8mm,承力最大的冲 压结构件其板厚亦小于3mm。 车身冲压件的面厚比很大,刚 度非常小,极易变形,要想将 多片极易变形的冲压件组焊成 高精度的车身分总成,在组焊 的全过程必须保持每一个冲压 件的形状不变,且各冲压件的 相对位置精度高。欲做到这一 点,车身焊装车间采用了大量 与之相适应的焊装夹具。
6、点焊工艺参数的选用
选择点焊工 艺参数时可以采 序 用计算法或查表 号 1 法(见表3-2), 2 无论采用哪种方 3 法,所选择出来 4 的工艺参数都不 5 可能是十分精确 6 和合适的,需针 7 对具体的工件的 8 特点由实验确定。
点焊工艺参数表
板厚 mm 1.0 电极直径 mm 6 焊接压力 N 1000~2000 通电时间 S 0.20~0.40
车身焊装工艺流程
车身焊接工艺布局
车身焊装工艺方法
一、车身焊装工艺流程
为了便于焊接成形、且获得准确的车身外形尺寸和优良 的外观质量,常将由薄板冲压成形的片状冲压件焊装成具有 一定强度或功能的分总成,再将分总成焊装成大总成,将大 总成焊装在一起组成车身的六大片(车身底板总成、顶盖总 成、左/右侧围总成、前围总成、后隔板总成),然后将六大 片合焊在一起构成车身焊接总成,装上车门、发动机罩、翼 子板、行李箱盖便构成了整体焊接白车身,如图3-1至图3-2 所示。
第三章 汽车焊装工艺
车身是汽车的基体,它不仅要承受来自汽车内、外部的所 有力和力矩,为乘客和货物提供保护,而且还要满足用户对汽 车外观质量日益苛刻的高要求,即车身应具有“承力、保护、 美学”三大最基本的功能。此三大功能是否能得到最大限度地 实现,在很大程度上取决于车身焊装质量。这正是业内常说
“车身焊装工艺水平直接关系着汽车产品的外观质量和使用性
图3-7 点焊质量的撕裂检验
二、凸焊
前面述及,凸焊的焊接原理和设备与点焊很接近,
只是焊接接头有所不同,因此人们常将凸焊称为是点
焊的一种特殊形式。
1、凸焊的工艺特点
1)在一个焊接循环内可焊接一个焊点又可焊接多个焊点,生产率高, 没有分流影响,因此可在窄小的部位上布置焊点而不受点距的限制。 2)由于电流密集于凸点上,电流密度大,故可用较小的电流进行焊 接,并能可靠地形成较小的熔核。 3)凸点的位置准确、尺寸一致,各点的强度比较均匀。因此对于给 定的强度、凸焊焊点的尺寸可以小于点焊。 4)由于采用大平面电极,且凸点设置在一个工件上,所以可最大限 度地减轻另一工件外露表面上的压痕。大平面电极的电流密度小、散热好, 电极的磨损要比点焊小得多,因而大大降低了电极的保养和维修费用。 5)与点焊相比,工件表面的油、锈、氧化皮、镀层和其它涂层对凸 焊的影响较小。当然,工件表面越洁净,其焊接质量就越好越稳定。 6)凸焊的不足之处是需要冲制凸点的附加工序;电极比较复杂;若 一次要焊多个焊点,则需要使用更高的电极压力和高精度的大功率焊机。 由凸焊的上述特点不难看出,凸焊特别适合于车身上的螺帽焊接。
常用的车身焊接工艺方法
电 阻 焊 焊 接 方 法 及 设 备 悬点焊机+手工焊钳/一体式焊钳 点焊机器人 单点焊 固定点焊机、凸焊机 龙门式多点焊机 多点焊 C型(鳄鱼式)多点焊机 组合式多点焊机 悬挂缝焊机 缝焊 固定缝焊机 自动/半自动二氧化碳气体保焊机 气体保焊 自 动 / 半 自 动 混 合 气 体 保 焊 机 (MAG焊机) 氩弧焊(MIG焊) 手工电弧焊 螺柱焊 气体焊 锡钎焊 等离子弧焊 电子束焊 激光焊 激光复合焊 摩擦焊 典型应用 白车身及各大总成、分总成 同上 螺钉、螺母、小件 白车身、地板总成等 地板、侧围、车门、发动机罩、行 李箱盖总成等 白车身顶盖流水槽等 油箱等 白车身总成 车门铰链、摇篮、消音器等 车身顶盖后部两侧接缝等 厚料零部件 各种焊接螺柱 白车身总成补焊 水箱等 白车身顶盖后角板 齿轮 车身地板、顶盖总成等 车身地板、顶盖、侧围、前后骨架 等总成 后桥壳管和法兰转向杆
2、凸焊电极
常用的凸焊电极有圆形平头电极、大平头棒状电极、螺帽 专用电极等三种基本类型。 1)圆形平头电极:圆形平头电极又称为标准点焊电极, 若进行凸焊作业时采用标准点焊电极,则电极接触面直径应不 小于凸点直径的两倍,以减小工件表面的压痕。 2)大平头棒状电极:大平头棒状电极常用于局部位置 的多点凸焊,如加强垫圈的凸焊,一次可焊4~6点。大平头 棒状电极的接触面必须足够大,应超过全部凸点的边界,超出 量一般应相当于一个凸点的直径。 3)螺帽专用电极:螺帽专用电极主要用于螺帽的焊接。 汽车车身上需要焊接的螺帽非常多,因此螺帽专用电极在汽车 车身焊接工艺中应用的非常广泛。
熔 化 焊
钎焊 特 种 焊
第二节 电阻焊
将被焊工件置于两电极之间加压,并在焊接处通以电流,利用电流流 经工件接触面及其邻近区域产生的电阻热将其加热到熔化或塑性状态,使 之达到金属结合而形成牢固接头的工艺过程,由于焊接所需要的热来自于 电流通过工件焊接处的电阻产生的热量,因此将其称为电阻焊。电阻焊有 点焊、凸焊、缝焊、对焊等多种不同的焊接方式,如图3-6所示。点焊是电 阻焊最典型的代表。点焊有单点焊、多点焊、单面点焊和双面点焊等多种, 其特点是生产率高、质量好、成本低、工作条件好、易于实现自动化,因 此在车身焊接中是一种应用最广泛焊接方式。
3、凸焊质量的影响因素
Biblioteka 电极压力焊接时间焊接电流
电极材料
1)电极压力
凸焊的电极压力取决于被焊金属的性能,凸点的
尺寸和一次焊成的凸点数量等。电极压力应足以在凸
点达到焊接温度时将其完全压溃,并使两工件紧密贴
合。电极压力过大会过早地压溃凸点,失去凸焊的作
用,同时因电流密度减小而降低接头强度;电极压力
7000~10000
8000~12000 9000~14000 14000~18000 15000~20000 17000~24000 20000~26000
1)两种不同厚度钢板的点焊
当两工件的厚度比小于3:1时,焊接并无困难。此时工艺
参数可按薄件的厚度选择,并稍增大一些焊接电流或通电时 间即可。 当两工件的厚度比大于3:1时,此时除按上上述方法处理 外,还应采取下列措施,以保证焊接质量。
3、通电时间的影响
通电时间又称焊接时间,焊接时间与焊接电流在一定范围
内可以相互补充。为了获得一定强度的焊点,可以采用大电流、 短时间焊接模式(简称强条件或硬规范),也可采用小电流、 长时间(简称弱条件或软规范)。选用硬规范还是软规范,取 决于金属的性能、厚度和所用焊机的功率。对于不同性能和厚
度的金属所需的电流和时间,都有一个上下限,选用时应特别
一、点焊
点焊的焊接过程由预压、通电、维持、休止四
部分组成。其焊接质量的好坏与预压力、通电时间、
通电电流、工件性能、电极的形状与材料等因素有
直接关系,其中通电电流和通电时间对焊接质量的
影响最大。
1、预压力的影响
点焊的预压力是由电极施加的,因此预压力又称为电极
压力。适当的电极压力对于保证焊接质量十分有利,其原因 是:适当的电极压力可以破坏焊接接头表面氧化污物层,使 焊接接头表面保持良好的接触,促进焊接接头的熔合,热熔 时在电极压力作用下形成的塑性环防止周围气体侵入和液态
能”的原因。轿车车身是各类汽车车身中结构最复杂、焊点和 采用的焊接方式最多、对焊接质量要求最高的一种,是汽车焊
装工艺中的典型代表,因此,本章以轿车车身为例介绍车身焊
装工艺。
第一节 焊装工艺流程与布局
轿车车身是由数以千计薄板冲压成型的板壳构件通过焊
接工艺方法组合在一起的形体复杂、高强度空间板壳结构, 其焊装工艺过程十分复杂。为此需对车身焊装工艺进行全面、 科学、合理的规划。