PLC系统在轧钢加热炉自动控制中的应用
SMATIC S7-300 PLC在加热炉控制系统中的应用

科技资讯科技资讯S I N &T NOLOGY I NFORM TI ON 2008N O .10SCI ENC E &TECH NOLOG Y I N FOR M A TI ON 学术论坛1系统概述通钢集团吉林钢铁热轧厂的加热炉采用推钢式蓄热加热炉,采用的燃料为高炉煤气。
由一次仪表采集的各种过程变量送入PL C ,再由PL C 根据设定控制方式和控制目标值分别驱动相应的执行机构,调节过程变量,实施对各点的温度、压力、流量的调节控制。
所有的检测和控制均由计算机系统完成,非常情况下可在仪控室电柜上根据两只温度表的测量值,手动操作相应的操作器来控制生产过程。
2系统的选型及特点我们选用的是西门子公司的S M A T I C S7-300的可编程控制器和台湾研华工控机组成先进、实用、可靠的自动调节控制系统,再配以先进的W I NCC 监控软件,实现了加热炉监控系统的各项功能。
SM ATI C S7-300PLC,作为西门子公司的一代普通型产品,具有以下特点:①功能强:极强的计算性能,完善的指令集,M PI 接口和通过SI M AT I C NET 联网的网络能力,功能更强;②快速:指令处理及其快速,功能强大的CPU 只需0.3m s 就可以处理1024个二进制语句,在面向字处理方面也同样表现出色;③通用:高性能模板和六种CPU 使用任一应用场合,模块可扩至3个扩展机架,集成立M M I (人机界面)接口电路,用户友好的W I N-DOW S STEP7编程;④全集成:全部模块化,运行可靠,性能价格比高。
上位监控软件W I NCC 。
W I NC C 是西门子公司推出的组态软件平台,它使用方便,可以构造灵活的界面和强大的功能,用W I NCC 组态软件能开发出较强的组合画面。
①灵活的画面切换。
②灵活有效的报警方式。
③强大的功能和简单直观的操作方式。
④灵活实用的设置功能。
⑤实用的管理功3硬件配置(1)CPU 3146E S7314-1A G13-0AB 0(2)接口模块I M 3606E S7360-3C A01-0AA0(3)接口模块I M 3616E S7361-0B A01-0AA0(4)模拟量输入模块6ES7331-7KF02-0AB0(5)模拟量输出模块6ES7332-5HF00-0AB0(6)开关量输入模块6ES7321-1BL 00/1BH02-0AA0()电源模块S36S 3(8)通讯卡CP56116GK1561-1AA00(9)存储卡64K E PROM 6ES7953-8LF 11-0AA0(10)导轨6ES7390-1AF30-0AA 04控制过程整个生产过程中将流量、压力、温度等参数送工控机处理,并在CR T 上显示,同时可随时调阅各种历史档案或根据用户要求打印各种生产报表,声光报警系统可及时对故障、误操作等进行报警,并向操作者提示处理方法。
PLC的加热炉自动上料控制系统
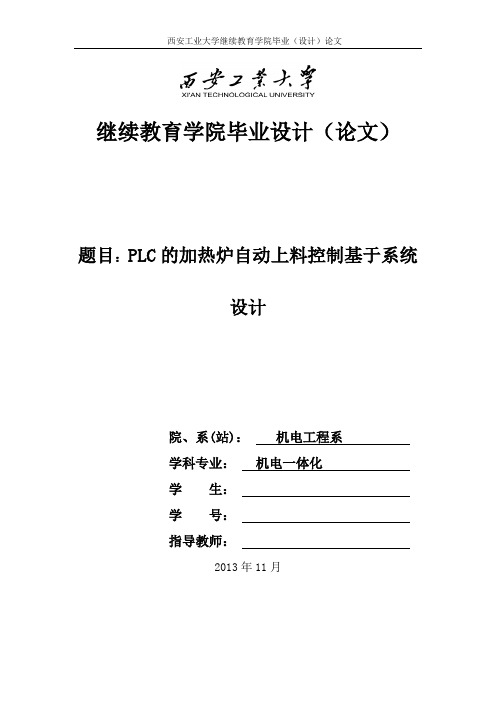
继续教育学院毕业设计(论文)题目:PLC的加热炉自动上料控制基于系统设计院、系(站):机电工程系学科专业:机电一体化学生:学号:指导教师:2013年11月PLC的加热炉自动上料控制基于系统设计摘要可编程逻辑控制器是集微处理器,存储器,输入输出接口与中断系统于一体的器件,已经被广泛应用于机械制造,冶金,化工,能源,交通等各个行业。
PLC 具有较强的逻辑运算能力,可以实现各种开关量从简单到复杂的逻辑控制,在现代工业生产过程中,有许多连续变化的模拟量,如温度,压力,流量,液位等,可编程逻辑控制器可实现对模拟量的控制。
本次设计针对加热炉自动上料控制系统,考虑到生产实际工程,以工业生产中常见的加热炉为主体,分析并设计它的自动上料控制系统。
控制运料小车在生产轨道上的动作,生产轨道上设有行程开关,可以让小车自动发出信号,控制炉门的开闭,同时小车前进后退与卸料过程都可以自动实现。
这次设计完成了主电路,辅助电路的设计。
另外设计出了控制系统对应的梯形图,通过PLC编程程序,用STEP-7软件和S7-200联机调试,成功地仿真了整个生产工程,运行良好,达到了设计的目标。
模拟加热炉自动上料控制系统的生产现场,也取得了很好的效果。
关键词:S7-200PLC,PLC,加热炉,自动上料,STEP-7目录1 可编程控制器概述 (1)1.1 可编程控制器的产生背景 (1)1.2 继电器控制系统与PLC控制系统的比较 (1)1.3 可编程控制器的综述与发展趋势 (2)1.3.1 可编程控制器的特点 (2)1.3.2 可编程控制器的分类 (4)1.3.3 可编程控制器的应用范围 (4)1.3.4 可编程控制器的发展趋势 (4)2 可编程控制器的硬件结构和工作原理 (8)2.1 PLC的硬件结构 (8)2.2 PLC的扫描工作原理 (8)2.3 S7-200系列PLC (13)2.3.1 S7-200系列PLC的主要功能 (14)2.3.2 S7-200系列的组网 (14)2.4 PLC 的基本编程元件 (14)3 可编程控制器的设计技巧 (16)3.1 可编程控制器的编程 (16)3.1.1 可编程控制器的编程原则和技巧 (16)3.1.2 可编程控制器控制系统的设计步骤 (16)3.2 可编程控制器应用中常见的问题 (16)4 加热炉自动上料控制系统的设计 (18)4.1 设计的具体过程 (18)4.1.1 设计任务 (18)4.1.2 设计意义 (18)4.1.3 设计方案的选择 (19)4.1.4 设计流程图 (19)4.2 加热炉自动上料控制系统的方案实施 (21)4.2.1 分析生产过程并确定I/O点数 (21)4.2.2 合理分配I/O端口并制表 (21)4.3 绘制电路图与梯形图 (22)4.3.1 绘制主电路图 (22)4.3.2 绘制辅助电路接线图 (23)4.3.3 画出梯形图 (24)4.4 用STEP-7软件与S7-200联机调试 (27)5 结论 (28)致谢 (29)参考文献 (30)1可编程控制器概述1.1 可编程控制器的产生背景在20世纪60年代以前,工厂里实现生产过程自动控制的设备主要是以继电器为主要元件的控制装置,复杂的控制系统可能要使用成百上千个各式各样的继电器,用成千上万根导线连接起来。
基于GE PLC的梅钢热轧加热炉系统改造

3.3 用编码器实现步进梁的行程计算 由于本 次改 造加 热炉机 械设 备不 作改 动,液 压
缸上 没有位 移传 感器 ,为 了实现 自动 推钢 、抽钢 , 在推 钢前必 须知 道上 一块 板坯在 炉内 的位 置才能 预 设推 钢行程 ;在 抽钢 前必 须知道 板坯 在出 炉侧的 溢
2. Baosteel Meishan Hot Strip Mill, Nanjing 210039)
Abstr act During the innovation of the furnace1 about Meishan Hot Strip Mill, a set of GE9070PLC was used to instead of WDPF system and SLC500 serials PLC of pump control system about walking beam. Net configuration and software abilities are simply introduced here. The results of the application indicate that the system is reliable for use, achieve objective.
本次改造选用 GE 公司的 90-70PLC 作为 1 号 加热炉新的 L1 控制系统,以实现自动推钢、自动 抽钢 、步进 梁的 自动 周期 运行、 液压 站泵 控、以 及 与 L2 的数据交换等功能。
2 新系统的自动化系统图
PLC 系统信号是通过SWITCH 与主轧线 EGD 主 干网相连,采用UDP/IP 协议,以EGD(Ethernet Global Da ta )的 报文格 式与上位 机交换 信号( Excha nge ); PLC 与远程 I/O 之间采用 Genius BUS 现场总线实现 数据通讯;PLC 系统与 ABB 传动之间使用 Profibus DP 实现数据通信,PLC 与 HMI Server 构成 100Mbps、
加热炉炉温PLC模糊控制系统的设计
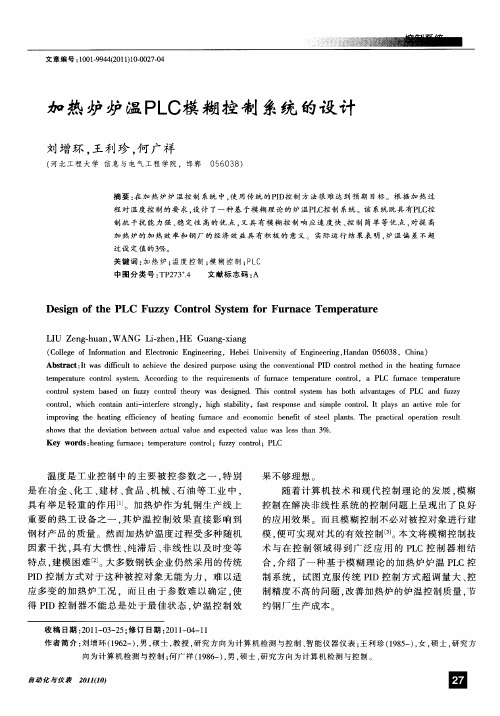
De i n o he PLC sg ft Fuz y Co t o se f r Fur c m pe a ur z n r lSy t m o na e Te rt e
Absr t:twa fiul t c e e t e e ie p r s u i g t o v n ina PI c nr lm eh d i he h tng f r a e t ac I s di c t o a hiv h d sr d u po e sn he c n e to l D o to t o n t eai u n c f tmpe au e o to s se e r tr c n r l y tm. Ac o dng o he e ie e t o u a e e c r i t t r qur m ns f f r c tmpe au e o to , a n rt r c n rl PLC ur a e e f n c tmpea u e r t r c n rl y t o to s sem ba e o fz y o to t e r wa d sg e . Ths o to s se s d n u z c nr l h oy s ein d i c n r l y tm h s a boh d a t g s f PLC a d u z t a v n a e o n f z y c n rl whih c n an nt— ne fr to g y, hg sa lt o to , c o t i a i i tree sr n l ih tbii y,f s r s o e a d i p e o r 1 t ly a ci o e o a t e p ns n sm l c nto.I p a s n a t ve r l fr i p o i t e e tn efce c o e tn f na e n m r vng h h ai g f in y f h ai g ur c a d e o mi b ne t f te p a t.The r c ia o e ai r s l i c no c e f o se l l n s i p a tc l p r t on e ut s ws t tt e i t n bewe n a t lv l e a d e p c e aue wa e st a % . ho ha he d v ai t e cua au n x e td v l s ls h n 3 o K e wo ds: e tn u a e;t mp r t e c n rl u z o r l y r h a ig fr c n e e aur o to ;f z y c nto ;PLC
基于PLC控制的加热炉温度控制系统设计

基于PLC控制的加热炉温度控制系统设计概述加热炉是工业生产中常见的设备之一,其主要作用是提供高温环境用于加热物体。
为了确保加热炉的稳定性和安全性,需要设计一个可靠的温度控制系统。
本文将介绍一个基于PLC(可编程逻辑控制器)控制的加热炉温度控制系统设计方案。
系统设计原理在加热炉温度控制系统中,PLC作为核心控制器,通过监测温度传感器的输出信号,根据预设的温度设定值和控制策略,控制加热炉的加热功率,从而实现对加热炉温度的稳定控制。
以下是系统设计的主要步骤:1.硬件设备选择:选择适合的温度传感器和控制元件,如热电偶、温度控制继电器等。
2.PLC选型:根据实际需求,选择合适的PLC型号。
PLC需要具备足够的输入输出点数和计算能力。
3.传感器连接:将温度传感器接入PLC的输入端口,读取实时温度数据。
4.温度控制策略设计:根据加热炉的特性和工艺需求,设计合适的温度控制策略。
常见的控制策略包括比例控制、积分控制和微分控制。
5.控制算法实现:根据温度控制策略,编写PLC程序,在每个采样周期内计算控制算法的输出值。
6.加热功率控制:使用控制继电器或可调功率装置,控制加热炉的加热功率。
7.温度反馈控制:通过监测实际加热炉温度和设定值之间的差异,不断修正加热功率控制,使加热炉温度稳定在设定值附近。
系统硬件设计基于PLC控制的加热炉温度控制系统的硬件设计主要包括以下几个方面:1.温度传感器:常用的温度传感器有热电偶和热敏电阻。
根据加热炉的工艺需求和温度范围,选择适合的温度传感器。
2.PLC:选择适合的PLC型号,根据实际需求确定PLC的输入输出点数和计算能力。
3.控制继电器或可调功率装置:用于控制加热炉的加热功率。
根据加热炉的功率需求和控制方式,选择合适的继电器或可调功率装置。
4.运行指示灯和报警器:用于显示系统的运行状态和报警信息。
PLC程序设计PLC程序是基于PLC的加热炉温度控制系统的关键部分,其主要功能是实现温度控制算法。
浅谈轧钢加热炉自动控制系统的应用

加热 炉控 制采 用PC 制系 统与检 测仪 表相 结合, L控 通过检 测烧 钢过程 的各 项工 艺参数 , 实现 优化 数学 模型控 制 及煤气 和 空气双 交叉 限辐最 佳燃 烧控 制, 对加热 炉 的炉温 、 压 、 温及 相关 保护 措施 等项 目进 行 自动 控制 , 由计 算 炉 烟 并 机系 统控 制 的操作 站 监视 全部 生产 过程 , 该系统 使 加热 炉更 节能 、高 效、安 全 、稳 定运 行 。 采 用 P C 制系 统 与检 测仪表 结 合, 加热 炉 的炉温 、炉 压、烟 温及 相 L 控 对 关 的保 护措 施等 项 目进行 自动控 制 。由计 算机 系统 的操作 站监视 全 部生产 过 程 ,保证 加 热 炉节 能 、高效 、安 全 、稳 定运 行 。加 热 炉 控 制系 统 采 用 一套 8 e e sP C im n L 控制 , 1 个主 机架 , 采用 ¥ 20 系 列 :4个 E 2 O 远 பைடு நூலகம்机 架, 7 40 T OM 均采用 ¥ 20 7 30系列模 块 。加热 炉 出料操 作室 采用一 台工 控机 , 于燃 烧系 统 用 的监视 和操 作 。 烧控 制 P C 燃 L 完成 仪表 各个 检测 项 目的回路 控制 、参数 采集 、 数 据处 理, 操作 站完 成炉 子生产 所 需的全 部操 作 、参 数显 示和监 控 , 括总 体 包 和 分组 流程 画面 、回路 调整 和显 示画 面 、故障报 警 画面 、瞬时和 历史 趋势 画 面等功 能 。 加热 炉过程 控制 计算 机 系统 的主要 目的 是完成 加热 炉各 段炉温 手 、 自动控 制 操 作 和 监 视 。 2燃烧 控制 系 统 2 1怎 样控 制温 度 . 加热 炉 分 五段 进行 温 度控 制, 括均 热 段 、均热 段 下层 、加 热 二段 上 、 包 加 热 二 段下 层 和 加 热一 段 。五 段均 采 用 相 同 的温 度 控 制方 案 。 () 1 改进 型双交 叉 限幅控 制方法 相对 于 串级 比值 方法, 为了对 空燃 比控制 更加精 细, 出现 了带有 双交 叉限 幅的 串级 比值控 制方 法, 简称 双 交叉控 制 方法 。优 点 是有效 控 制 了动态 空燃 比, 同时缺 点是 限幅 牺牲 了系 统跟踪 负荷 变化 的速 度, 但 降低 了系统 的 响应速 度, 为进一 步提 高响应 速度 , 改进 型双交 叉方法 还 将 限幅系数 设为 可 以根据温 度 偏差 自动修 正, 以便 在温 度偏 差较 大时减 弱或 取消 限幅 功能, 即限幅 系数是 动 态 的, 这样 将 大大 提 高控 制 系统 的 响应 速 度 。 () 气过 剩系 数 u 自动修 正策 略 2空 随着 生产负 荷的 变化, 理论 空气 过剩 系数也 应该 随之 变化, 这一 点在 实施 温 度控制 时应 该考 虑到 。 种变化 的 空气过 剩 系数修 正策 略对提 高燃 烧效 率, 这 降低氧化 烧损 有好 处 。另 外, 在常 规控 制 的低负 荷状态 时 , 为了保 证在 小流量 情况 下, 使空气和 煤气 能够很 好的混 合燃烧 , 必须 在相应 的煤气 流量 的情况下 , 适 当加 大空 气 的流 量, 能保 证 在小 流 量情 况下 的合理 燃 烧 。 才 ( ) 路基 本报 警 、连锁 等 功能 超温 报 警功 能 3回 当相 应炉 段 的温 度超 过 允许 值 , 系统 发 出报 警信 号 。热 电偶 断 偶保 护 、 报警 功能 : 当任何一 只热 电偶被烧 坏, 本回路 立 即切 换到 手动模式 , 同时系统发 出报 警信 号 。 温度 调节器 输 出限幅 功 能 : 据最 大加 热速 率对 温度调 节器 输 出 根 限幅, 防止 钢 坯 过热 。最 大加 热 速率 由炉 内负荷 及 要求 的在炉 内时 间而 定 。 () 4 温度 控制 器工 作模 式 为方便 操作 , 温度 控 制器设 计 手动 、本 地 自动 和数 模 3 控制模 式 。 种 手 动模 式 : 手动 模 式下 , 气 流量 和煤 气 流量 的调节 阀 工作 在手 动 方 在 空 式 。由操作 员 直接 改变 阀 门的开 度 。 本地 自动 模式 : 地 自动就 是 并联 串级 、交 叉 限幅工 作模 式 。也是 在坯 本 料加热 时, 控制 系统 经常 使用 的方 式 。在本 模式 下, 统 的所有 在线 自动检 测 系 正常 。流量 调节 回路 、温度 调节 回路 都工 作在 闭环状 态 。操作 员只 需要输 入 相应供 热段 的炉膛 目标 温度 值给 控制系 统, 则系 统就 会 自动 、 比例 的调节相 成 应 供热段 的 空煤气 流量 , 而保证 炉 温 的控制 精度 。 从
基于智能控制技术的轧钢控制技术研究
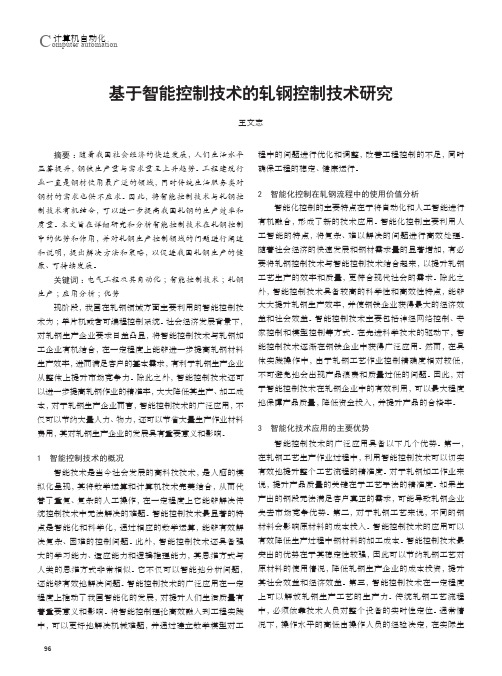
C omputer automation计算机自动化基于智能控制技术的轧钢控制技术研究王文志摘要:随着我国社会经济的快速发展,人们生活水平显著提升,钢铁生产量与需求量呈上升趋势。
工程建筑行业一直是钢材使用最广泛的领域,同时传统生活服务类对钢材的需求也供不应求。
因此,将智能控制技术与轧钢控制技术有机结合,可以进一步提高我国轧钢的生产效率和质量。
本文旨在详细研究和分析智能控制技术在轧钢控制中的优势和作用,并对轧钢生产控制领域的问题进行阐述和说明,提出解决方法和策略,以促进我国轧钢生产的健康、可持续发展。
关键词:电气工程及其自动化;智能控制技术;轧钢生产;应用分析;优势现阶段,我国在轧钢领域方面主要利用的智能控制技术为;单片机或者可编程控制系统。
社会经济发展背景下,对轧钢生产企业要求日益凸显,将智能控制技术与轧钢加工企业有机结合,在一定程度上能够进一步提高轧钢材料生产效率,进而满足客户的基本需求,有利于轧钢生产企业从整体上提升市场竞争力。
除此之外,智能控制技术还可以进一步提高轧钢作业的精准率,大大降低其生产、加工成本,对于轧钢生产企业而言,智能控制技术的广泛应用,不仅可以节约大量人力、物力,还可以节省大量生产作业材料费用,其对轧钢生产企业的发展具有重要意义和影响。
1 智能控制技术的概况智能技术是当今社会发展的高科技技术,是人脑的模拟化呈现,其将数学运算和计算机技术完美结合,从而代替了重复、复杂的人工操作,在一定程度上它能够解决传统控制技术中无法解决的难题。
智能控制技术最显著的特点是智能化和科学化,通过相应的数学运算,能够有效解决复杂、困难的控制问题。
此外,智能控制技术还具备强大的学习能力、适应能力和逻辑推理能力,其思维方式与人类的思维方式非常相似。
它不仅可以智能地分析问题,还能够有效地解决问题。
智能控制技术的广泛应用在一定程度上推动了我国智能化的发展,对提升人们生活质量有着重要意义和影响。
将智能控制理论高效融入到工程实践中,可以更好地解决机械难题,并通过建立数学模型对工程中的问题进行优化和调整,改善工程控制的不足,同时确保工程的稳定、健康运行。
PLC在钢铁冶金企业电气自动化控制中的应用阐述

PLC在钢铁冶金企业电气自动化控制中的应用阐述摘要:为了更好的促进我国钢铁冶金行业的发展,需要对控制技术进行不断更新。
PLC的应用有效提高了生产工作的安全性和效率,同时降低了运维成本,全面提高钢铁行业电气自动化控制的整体质量。
因此本文主要对PLC在钢铁冶金企业自动化控制中的应用进行相应的分析,在此基础上提出下文内容。
关键词:PLC;钢铁冶金;企业;电气自动化;控制应用引言钢铁冶金工业生产水平在很大程度上决定了我国整体工业生产水平。
提高钢铁冶金企业电气自动化控制水平,是现阶段钢铁冶金工业生产的必然要求。
PLC 技术在目前工业生产领域中的应用非常广泛,为提高我国钢铁冶金企业电气自动化控制的技术水平,有效节约人力物力。
1.PLC的概念及作用1.1PLC的概念PLC 是可编程逻辑控制器的英文缩写,是一种工控计算机,也是现在电气自动化控制的核心组件。
PLC 通过以太网、Profibus、Tc-net 等总线技术与上位机相连,通过执行存储器中的程序来实现逻辑运算、控制、模数转换等多种功能。
PLC 常用的图形编程语言如梯形图、时序图等。
PLC 与传动设备、I/O 设备、电磁阀、继电器和各类仪器仪表等相连,通过数字或模拟量输入方式采集设备信号并将指令输出给现场设备实现控制目的。
PLC 具有抗干扰强、可扩展、指令丰富、编程语言易掌握、维护简便、成本低等优势而被广泛应用于各行业的自动化控制中。
1.2PLC在钢铁冶金企业电气自动化控制中的作用目前在钢铁行业常见的3级工厂自动化控制体系中,基础自动化就是以PLC 及其上位机为核心搭建的。
基础自动化的主要功能是能够直接控制工艺设备的传动、液压、流体、执行机构等,工艺闭环控制、定位、时序和设备保护功能通常都包含在该级控制中。
基础自动化的信息可以传输给过程自动化用于更复杂的运算和控制,比如在轧线物料跟踪功能中基础自动化的PLC可以采集和处理物料跟踪信息,向下直接控制设备动作,向上给过程自动化的宏观物料跟踪提供追踪数据。
GE 9070 PLC在热轧板厂2号加热炉中的应用

L 与L 1 2之 间通 过 以太 网连 接 , G 用 E公 司
开发 的 P C进行 通 讯 , 套 9 7 L L 两 0 0P C之 间 也通
过以太网连接采用 E D通信 。该 方式允许一 台 G 设备 作 为 “ 出 方 ( R UC R) 通 过 “ 换 产 P OD E ” 交 ( X HA G ) 共享其部分 内存 给一个 或多个 E C N E”
定 , 成 自动抽 钢 过程 , 完 将板 坯 抽 出 放炉 前 辊 道 上, 由炉前辊 道把 板坯送 往轧 线进行 轧制 。
S 应用 实例
板 坯 在 2号 炉 炉前 辊 道 Z 、 5上 自动 定 位 4Z
过程 , 辊道 示意见 图 3 。
来实现两台设备 间的通讯。如需实现和原有设备
“ 求 方 ( ONS 需 C UME ” R) 。系 统 通 过 配 置 “ 出 产 方号 ( R DUC RI ) “ 换号 ( X HAN P O E ”,交 D E C GE I ) ,需求方 号 ( ONS D ”“ C UME D)和 执行 周期 RI
算板坯移出量, 2 L 下发抽钢设定 , 1 L 根据抽钢设
的数据共 享 , 再 配置 “ 号 ( OUPI ” 完 需 组 GR D) 来ቤተ መጻሕፍቲ ባይዱ
成 。该 方式 中 “ 出方 ( ROD E ” 产 P UC R) 发送 数 据
以短坯定位在 Z 上为例 , 5 板坯从 Z 上被运 1
l 号推钢机 2 号推钢机
和“ 求方 ( O S ME ” 需 C N U R) 接受数 据是不 同步 的。故该方式适 用于有规律 的周期性的数据传 送。系 统 支 持 最 多 25 个 “ 换 ( X 5 交 E— CHANGE ” 每 个 “ 换 ( X ), 交 E CHANGE) 最 长 ”
基于PLC控制器的炼钢加热炉压力系统设计

l 生 訇 化
基于P L C 控制器的炼钢加热炉压 力系统设计
Pr es sur e s ys t em des i gn s t eel m aki ng f ur nace based on t he PLC con t r ol l er
刘
洁 ,虞慧群
第4 期 2 0 1 3 - 0 4 ( 上)
务1
控 ,以保 证炼 钢加 热炉 正 常运 行 。 对 压 力 值 的 采 样 是 整 个 控 制 系 统 最 基 础 的 部
分 ,采 样 正 确 与否 直 接关 系 到 整个 控 制 系 统 的 质 量 ,对 采样 值 的处 理 则 显 得 格 外 重 要 。本 设 计 采
备 ;过 低 , 炉 内 可能 会 吸 进 冷 空 气 , 进 而对 炼 钢
加 热 炉 的 燃 烧 质量 和 效 果 造 成 一 定 的 影 响 ,并 增
行 实 时 控 制 。上 位 机 运 行 用组 态软 件 设 计 的 监 控 画 面 ,对炼 钢 加 热 炉 生 产 过 程 及 控制 系统 进 行 监
收稿日期:2 0 1 3 - 0 1 -1 5 基金项目:国家 自然科学 基金 资助项 目 ( 6 1 1 7 3 0 4 8 ) 作者简介:刘洁 ( 1 9 7 8一),女 ,安徽蚌埠人,工程师,工学硕士 ,研究方 向为虚拟仿真、计算机应用技 术与控制 系统 实现 。
[ 1 4 0 ] 第3 5 卷
接 控 制 炉 膛 压 力 以及 煤 气 压 力 的 大 小 ,这 样 炉 膛
压 力的控 制就 得到 了解 决 。
我 国大 部分 的大 中小钢 厂 , 因为随 着P L C 技 术 的不 断发展和 完善 ,其 应用范围也已变得越来越广泛口 】 , 利 用 计 算 机 系统 实现 对 炼 钢 加 热 炉 实 时 精 确 的控
SIMATIC S7—300PLC在蓄热式加热炉自动控制系统中的应用

1 工 作 原 理
SMA I 7— 0 L I TC s 3 0P C硬件 采用 模块 化设 计结
到出炉 方 向将 加 热 炉 分 为 预 热 段 、 热 段 、 热 加 均 段 , 一段 都有 独立 的空 、 气 管道 及 相 应 的调 节 每 煤 阀和流量 计 等 设 备 , 且 每 一 段 都设 置 了相 同数 并 量 的温 度 检 测 点 。P C采 集 并 整 理 这 些 温 度 数 L
维普资讯
黑
龙
江
冶
金
度不 均 匀 。各 层 圈 梁 不 贯 通 , 墙 布 置 零 乱 等 。 砖 这 些都减 小 了建 筑物 整 体抵 抗 水 平 和垂 直 方 向地 震力 的能 力 。为 了保 证 地 震 力 的 可 靠 传 递 , 墙 在 体错 层 的部 位 应 采 取 有 效 措 施 , 强 楼 ( ) 板 加 屋 盖
的整体性与楼( 盖板 的联结。具体要求在设计 屋)
一
台人机 界 面 工 控 机 进 行 通 讯 , 字 量 输 入 模 块 2 数
块 、 出模 块 1 , 拟 量 输 入模 块 1 输 块 模 0块 、 拟 量 模
收稿 日期 :0 8— 2—2 20 0 1
定 的空燃 比的情 况 下 , 空 气 流 量 和煤气 流量 用
( 转5 ) 下 5页
间的最 大距 离为 1 。 1 C 3 3模块 用 来 与 两 0米 块 P4
据, 再根据具体情况发 出指令 调整调节 阀的开度
以达 到 预期要 求 。炉温 的变 化 是通 过 改 变煤 气 和 空气 的流 量值 实 现 的。参 与 炉 温调 节 的设备 是 每 段炉 顶左 侧 的热 电偶 、 气 调节 阀和 煤 气调 节 阀。 空 炉膛 温度 、 气流 量 和煤 气 流 量 是 用 SE 件 空 T P7软 中 自带 的连 续 式 PD调 节 器 F 4 计 算 出来 后 , I B1 在
西门子PLC在加热炉燃烧控制系统中的应用

21 年第2 期 02 0
科技 I向导
◇ 科技论坛◇
西门子 P C在加热炉燃烧控制系统中的应用 L
吴10 ) 7 4 1 要】  ̄i要介 绍 了西 门子 s—0 本- - 7 40系列 P C在加热炉燃烧控制 中的应用 , 用了炉压前馈控制 、 态响应 的双 交叉限幅控 制等 L 采 带动
( h u o t n d p rme t fL i u io n te S a Do g L i u 2 1 0 ) T ea t ma o e a t n aW n a d se l h n n aw 7 1 4 i o r
【 bt c]h rc ot tdc t plao f IM N 7 40si L o t han — raecm utncn o N W A sr t i aiem syir ue h ap ctno S E Ss —0 ee P Cf er etg f nc o bso ot1 e a T s tl l no e i i E rs rh e i u i r.
新的控制 方式, 高了系统的调节响应速度 , 提 加热炉温升快 , 温度控制稳定 , 少了氧化烧损 , 减 降低 了燃料 消耗 . 提高 了加热炉的燃烧控制水平
【 关键词 】 前馈控制 ; 双交叉限幅控 制; 程序升温
Th pp i a i n o I e a l to f S EM ENS c PLC n c m b s o o t o o e e tng f r a e i o u t n c n r lf r r h a i i u n c W U M a - he o s ng
基于PLC加热炉温度模糊控制系统的研究_宋乐鹏

中 文 核 心 期 刊《 微 计 算 机 信 息 》( 测 控 自 动 化 )2008 年 第 24 卷 第 8-1 期 表 1 模糊控制查询表
图 2 模糊控制原理框图
图 3 隶属函数
技
4 模糊控制算法
术
本加热炉控制系统的主要目的是控制加热炉的温度恒定,加
热 炉 的 温 度 与 煤 气,空 气 的 供 给 量,工 件 温 度,环 境 温 度 等 因 素 有
2 PLC 的温度控制系统
图 1 是 PLC 加 热 炉 温 度 模 糊 控 制 系 统 , 本 系 统 采 用 FX2NPLC,配 FX- 4AD、FX- 2DA 两块模拟量输入、输出功能模块。 该 PLC 扫描速度快,抗干扰能力强,利用输入点将按等级划分的偏 差转化为开关量信号引入 PLC, 然后根 据偏 差 的 大小 决 定 输出 值的大小。在炉温上升到给定值的 90%以前,采取全开度控制,节 省升温时间,待炉温上升到给定值的 90%时,采用模糊控制,提高 控 制 精 度,当 炉 温 上 升 到 给 定 值 的 105%时,采 取 失 度 控 制,使 炉
控制是一种理想的加热炉控制器。
关键词: 模糊控制; PLC; 加热炉; 温度控制
中图分类号: TP273
文献标识码: B
Abstr act: Combine a heavy temperature control of the chongqing squeeze steel factory heater- furnace system, with improvemen the
4,+5,+6}。各模糊子集的隶属函数取三角型函数,如图 3 所示。
由 于 在 不 同 的 温 度 下,系 统 要 求 的 工 作 状 态 是 不 同 的,对 误
GE90-30 PLC在炼轧厂加热炉系统中的应用

总第 12 5 期 20 0 6年 1 0月
南
方
金
属
S m.1 2 u 5
S OUT HER ME L N TA S
O tb r 2 o co e 0 6
文章编号 :10 09—90 {06 0 0 5 0 7 0 2 0 )5— 0 2— 3
系统控制功能.淘汰了原有加热炉 C R S上位操 OO 作站 , 新增电控和仪控 ( 双机 ) 人机接 口系统.淘汰
了日 本横河公 司 I L型 D S系统 , x X C 应用 G 9 3 E 0— 0 P C实现加热炉仪表控制功能 , L 确保系统具有全油 燃烧、 油气混烧 、 全煤气燃烧的功能. 新组成 的加热 炉系统配备两级 自动化系统 , 采用 G 9 E 0系列可编
的满足工 艺要求 , 为提高产品质量 、 产量提供 了保证 .
关键词 : 热炉 ; E 03 P C 加 G 9 -0 L ;控制 系统
中图分类 号 : G3 7 T 5 1 T 0 ;M 7 文献标识码 : B
Ap l a i n ft e GE 0-3 p i t so h 9 c o 0 PLC n t e h a i g f r a e s se i h e t u n c y tm n
Ab t a t h ewok tp l gc s c u e a s c ae i h 9 -0 P C u e n t e h a n u n c y t m s e sr c .T e n t r o o o i  ̄ t r s o it d w t t e GE 0 3 L s d i h e t g f r a e s se Wa d - h i
f rc n iu u a t g a d r ln n t o o tn o sc si n ol g u i n i
PLC 系统在轧钢生产线自动控制中的应用

虑 R e m t o e I / 0网络 的连 接距 离和 系统对 实 时性 的要求 .采 用 1 1 5 . 2 k b i t / s 的通信速率 。 R e mo t e I / O网工作在扫描器方式下 . P L C处理器通过 R e mo t e U O接 口模块和远程 F l e x I / O适配器建立 串行通信链 变频器的通 信接 口 为 R e m o t e I / 0网中的 网络设备提供直接、 数字的通信链路 , 系统通过组态 P L C的 I , 0标签 . 利用通信接 口建立输入 、 输 出数 据链 。对 P L C而言 , 每 台变频 器被看作是一个安装有 I / 0模块 的远程框架 . 只需要对这些 模块进 行读写 . 就可 以向与其相连 的变频器发送命令 , 控制设备 的运 行: 又可从变频器读取各项数据 . 监视设备 的运行状态 , 并将数据 实时 传送 到 P L C中 通过 画面就 可以在 主控室 的操作站显示器上 , 为操作 1 . 轧钢生产工艺流程 详细的信息 , 并可以直接操作设备 , 甚至在变频器发 出 热轧带钢作为原料 . 进入酸洗流水线 由于热轧带 钢经过轧制和 人员提供实时 、 可 以及时复位变频器来避免 因处理不及时而导致事 冷却后在表面形成一层氧化铁皮 . 必须在冷轧之前进行 酸洗以清除掉 报警 出现故 障时. 使 这层氧化铁膜 . 露 出新鲜干净 的带钢基体金属表 面。带钢经过酸洗线 故发生 连铸机 的电气系统实现 了传动设备的远程 网络实时控制 , L C对变频器 的驱动实现了网络化数字式控制 . 以一条通信 电缆取代 之后 . 就被传送至冷轧设备 , 被加工至客户所要 的厚 度。然后 , 经过退 P 与传统 的模拟量 、 开关量控制方法相 比, 不仅大大 提高 火工序 . 令钢 带内部 晶体结 构重组 , 使钢带 的韧性得到增强 。 最后经过 大量 的硬接线 。 精确 性和可靠性 . 而且安装 、 调试 、 维护的成本也 相 平 整流水线 . 消除带钢表 面的凹凸不平现象后 . 得到成 品。 整个生产过 了系统的实时性 、 。 程 中, 冷轧流水线 的工艺最 为复杂 、 安全性要求最高 。 在轧制过程 中工 应 降低目 由来 自 操 作台或者 P L C的信 号对 变频器 的频率 进行控制 .通过 作人员或调试人员需要在现场进行检测 、 设定 、 调试 、 润滑 、 清洗 、 手动 装载和故 障排 除等操作 。在这些操作过程 中。 带钢 的开卷 、 再卷 、 乳酸 变频器 的频率变化来控制 电动机 的转速或者液压提升机液压缸 流量 . 小车 的走行速度和液压提升速度大小 。通过变频调速装 液 喷射 、 换辊 、 钢卷小 车移 动 、 x射线 测厚 , 以及 轧制过程等都 会对工 进而控制大 、 . 5 ~ 作人员或调试人 员造成碾压 、 碰撞 、 冲击 、 切割 、 缠绕 、 拖拽 、 灼伤 、 辐射 置对 电动机进行速度 控制 .可使 大 、小车水平速度 可调范围为 1 1 5 m m/ s 变频调速 自动控 制系统控制交流异步 电动机 . 采用有位 置 等伤害 所 以 . 必 须采用安 全保护 和控制设备 , 来 减少机器的风险 , 保 3 闭环控制功能的配 置 . 保证 出钢机 L 形 钩一次 准确定位 。基 于可靠 性 护人 和 机 器 的 安 全 正常工作时使用 一台变频器控 制一 台电动机 . 每台电动机轴 上 通 常粗轧机每轧制一块板坯最 快需要 3 0 ~ 6 0 s . 因此 , 出钢机的工 考虑 . 也称 光码盘) , 利 用其进行位置 反馈 形成位置闭环 控 作节奏应 与此相适应 为了提 高速度 和定位 准确性 , 需要采用 自动控 装有 脉冲编码器f 制方式 . 同时也减 轻了操作 工的劳动强度 根据 以上分析 , 在大车 自 动 制系统。 3 . 结 论 对 准出钢位置之后 . 小车和提升机 每次 的执行动作是相 同的。 因此 , 小 炼钢是一个 复杂的生产流程 . 连铸坯 的质量 受到浇铸条件 、 过程 车和提升机的动作完全可以由 1 9动控制来 完成 , 以便操作工集 中注 意 力监视生产线其他 工作 . 避免枯 燥的重复 劳动 , 进而减少 由于人工操 状态的直接影响 . 即使采用 了先进 的工艺 、 设备 和技术 , 但 由于连铸生 作 失误所 引起 的事故 当然 . 为了应付特殊情况 的出现 , 小车和提升机 产工艺特点影 响. 炉次交接 、 设备 故障及操作不稳定 等都会不可避 免 产生异常 . 从而使铸坯 质量 受到不 同程度 的 也应具备 手动控 制的功能 因此 . 在小车的控制方式选择上 . 采用手动 地使 生产过程 出现波 动 、 损害 . 对后道轧钢 工序和最终产 品质量的影 响不 容忽视 . 给企业造 成 和 自动 两 种控 制 方 式 经济和产品信誉 的损失 。通 过采取 P L C系统对 轧钢生产线 自 动控 制 2 . P L C 系 统在 轧 钢 生产 线 自动 控 制 中的 应 用 电气设备 的检测和控制主要包括大包 回转台的旋转 、 包臂升降、 大 包水 I : 1 开闭, 中间包车行走 、 对 中、 升降 , 结晶器振动 、 振频调节 , 拉矫机 传动. 拉矫 辊压下 , 引锭杆上行 、 回收跟踪 、 脱坯 、 存放 , 铸坯定尺切割 , 以及切割前后辊道 . 输送辊 道 , 翻钢机 , 铸 坯分 离机 , 步进冷床 的控制 。 液压系统 、 油气润滑系统 、 干油润滑系统 的检测 、 控制也由 P L C完成日 。 所有主生产线传动设备全部采用了变频 器驱动 , 连铸机从钢包 回 转台直至横向移钢车等机械设备的传动中共使用了一百多 台变频器 , 功率 范 围为 0 . 7 5 4 5 k W 所 有变频 器通 过其 内置 的通信 接 口连 接 R e m o t e I / 0通信适配器 . 直接挂在 由 9个 R e m te o I / O接 口模块组建 的 9 个R e m o t e I / O网络上 . 构成 了基于 R e m o t e I / O网络的传动系统 综合考
轧钢棒材生产线的PLC控制系统

轧钢棒材生产线的PLC控制系统在自动化操纵领域,PLC是一种重要的操纵设备。
目前,世界上有200多厂家生产300多品种PLC产品,应用在汽车(23%),粮食加工(16.4%)、化学/制药(14.6%)、金属/矿山(11.5%)、纸浆/造纸(11.3%)等行业。
上世纪80年代至90年代中期,是PLC进展最快的时期,年增长率一直保持为30%—40%。
在那个时期,PLC在处理模拟量能力、数字运算能力、人机接口能力和网络能力得到大幅度提高,PLC逐步进入过程操纵领域,而且在某些应用上取代了在过程操纵领域处于统治地位的DCS系统。
现今,PLC差不多具有通用性强、使用方便、适应面广、可靠性高、抗干扰能力强,编程简单等特点。
在可预见的今后,PLC 在工业自动化操纵专门是顺序操纵中的主导地位,是其他操纵技术无法取代的。
本文介绍了S7-200 PLC操纵系统在轧钢棒材生产中系统中的应用,着重描述了系统配置及冷床操纵功能。
最后通过,通过测试和实验的成功说明本文研究成果的可行性和可靠性。
关键词:PLC操纵系统;轧钢;棒材生产;冷床顺序操纵;ABSTRACTIn the area of Automation Control,Programmable Logic Controller is an important control equipment.Currently,there are over 200 manufacturers that produce more than 300 varieties of PLC products,which are now applied in auto industry(23%),grain processing(16.4%),chemical&pharmacy(14.6%),metals&mine(11.5%),paper pulp and paper making(11.3%) and many other industries.The PLC develop fastest during the 1980s and the mid-1990s,the value of gross output of PLC increase at the speed of 30%-40% per year.In this period,the PLC technology has developed rapidly in the field of analogy processing,digital quantity operation,man-machine interface,network service,gradually the PLC entered the field of process control because of these,and in some fields the PLC has token the place of Distributed Control System-the once king in the field of process control.And now,the PLC has been equipped with good commonality,ease of use,wide applicability,high reliability,good anti-interference,easy programmability and some other advantages.In the foreseeable future,the PLC will dominate the industrial automation and control,especially Sequence Control,and it can't be replaced by other control technologies.This article will introduce how s7-200 PLC system works in rolling steel bar production,and it focus on describing System Configuration and cooling bed stly,tests and experiments show that the research results this article describes are practical and reliable.Key words:PLC control system; steel rolling; bar production;sequence control of the cooling bed;目录第一章绪论 01.1 课题研究背景和意义 01.2 国内外进展状况与进展趋势 (2)第二章可编程操纵器简介 (9)2.1 可编程操纵器的进展历史 (9)2.2 PLC的特点 (10)2.3 PLC的工作原理 (11)2.4 PLC的体系结构 (12)2.5 PLC操纵程序设计 (15)第三章轧钢棒材生产线冷床操纵系统的硬件设计部分 (17)3.1 硬件组成及操纵要求 (17)3.2 PLC输入、输出的安排 (19)第四章系统软件设计部分 (25)4.1 系统流程设计图 (25)4.2 顺序功能图 (25)4.3 PLC程序 (26)第五章结论 (32)致谢 (33)参考文献 (34)第一章绪论钢棒材是经济建设中必不可少的一种材料,钢棒材品种繁多,广泛应用于汽车制造、电气机械、船舶制造工业、大跨度桥梁、高层建筑等社会生活各个方面。
东芝V3000PLC在炉卷轧机系统中的应用

据 数 学 模 型被 自动控 制 , 学 模 型 决 定 冷 却速 率 和 冷 数 却方式, 后送往 热矫直机进行矫直 。 之
河南省重点工程, 具有 当今 世界先进水平的炼钢轧钢
生 产 线 。 生 产 的钢 种 有 普 通 碳 素 结 构 钢 , 力容 器 、 可 压 造船 、 炉 、 锅 汽车 大 梁和 管 线 用钢 , 及 低 合 金 高 强度 以 钢 和桥 梁 板 , 计 年 产 1 0 中厚 钢 板 。 制 系统 的好 设 万t 1 控 坏直接影响钢板的板形 、 差 、 公 质量 和 成材 率 , 代化 现 的 轧 机 生 产 线 对 控 制 系 统 的 要 求 日趋 严 格 , 基 础 自 而 动 化 系 统 直 接面 向 生 产 过 程 , 水 平 至 关 重 要 。 其 图 1 炉 卷轧机 区工艺流 程 图
--—
厂 — ] 交换 I 机
、 、
L_ T
j] rI — _—
S 3M I LL
一
轨机 础自 化 动 系统
_=] _ _ rIj— ] __
作 者简 介 : 继 东(9 1)主要 从 事 电气工程 及 其 自动化 维 李 18 一,
护工作。
f V30 L 0 0P C } f v OoP C f f 3 0 L V3 0 L { f V 00P C O 0P C 3 0 L
1 炉卷轧机 区工艺流程
轧 机 区 工艺 流程 框 图如 图 1 示 。 所 加热 炉 可 以热装 ( 接从连铸机来的板坯 ) 冷装( 板坯库 ) 作 。 直 和 从 操 板 坯 首 先被 送 入 加热 炉 内, 热到 轧 制温 度 , 热好 的钢 加 加 坯 先 经 过 除鳞 机 除鳞 , 后进 入 立辊 轧 机 和 水 平 轧 机 之 进行轧制 。 根据 轧 制表 可进 行 常 规 轧 制和 炉 卷 卷 曲轧
PLC及特殊功能模块在加热炉自控中的应用

现 仪 控 系 统 1 套 自动 调 节 回路 中 , 6 均采 用 P D 节 , I调 操 作 方 式 分 为 自动 、 动 方 式 . 行 机 构 有 1 套 电动 方 手 执 4 式 、套 液 动 方 式 。 操 作 站 能 实现 对 炉 子 的状 态 监 控 、 2 意 外 事 件 报警 等 功 能 。
一
子 的 炉 温 ( 型 ) 换 热 器 处 温 度 ( 型 ) 热 电偶 检 测 进 S 、 K 由 PC L 。所 有 信 号 经 P C 别 计 算 转 换 后 , 与 控 制 , 可 L分 参 并
在操作站显示 。
2加 热 炉 压 力 控 制 .
、
系统构 成
本 系 统 选 用 1 上 位 机 MAS E I W 、 台 监 控 站 台 T RV E 1 O eaeSain 2 i 以A B A A U L p rt tt 5 0 o  ̄ B DV NTB I D软 件 包 . L PC 部 分选 用 A B MAS E I C 2 01 B T R P E E 0 / .它 具 有 成 本 低 、 运 行 可靠 、 能 较 强 的 特 点 。本 系统 大 致 可 以分 为 三 个 部 功 分 : 1 仪 控 系统 以及P D调 节部 分 ; 2 双 交 叉 限 幅 燃 烧 () I () 系统 ;3 P C和变 频 器 的通 讯 部 分 。 ( )L 系统 构 成框 图如 图 1 示 所
二 、 控 系统 组 成及 控 制 功 能 仪
为 确 保 助燃 空 气 与煤 气 压 力 保 持 稳 定 、 内燃 烧 顺 炉 利 进 行 , 气 和 空 气 的 压 力 必 须 进 行 控 制 。加 热 炉 炉 内 煤
- 1、下载文档前请自行甄别文档内容的完整性,平台不提供额外的编辑、内容补充、找答案等附加服务。
- 2、"仅部分预览"的文档,不可在线预览部分如存在完整性等问题,可反馈申请退款(可完整预览的文档不适用该条件!)。
- 3、如文档侵犯您的权益,请联系客服反馈,我们会尽快为您处理(人工客服工作时间:9:00-18:30)。
PLC系统在轧钢加热炉自动控制中的应用作者:刘克军
来源:《科学与财富》2010年第02期
[摘要] 加热炉是轧钢生产线的重要设备,其控制系统的好坏对热轧产品的产量、质量有很大的影响。
应用PLC技术的加热炉是集数据采集、安全联锁保护、程序控制、过程调节、上位通讯及人机对话于一体的综合控制系统,PLC可为轧钢生产设备的故障诊断提供强有力的技术支持。
在进行故障诊断系统的设计时,根据诊断系统的功能要求,选用适当的PLC,可丰富和完善诊断系统的功能,这是PLC应用中最具代表性的系统之一。
[关键词] PLC 加热炉自动控制应用
1、PLC自动控制系统
可编程控制器(Programmable Controller)是计算机家族中的一员,是为工业控制应用而设计制造的。
早期的可编程控制器称作可编程逻辑控制器(Programmable Logic Controller),简称PLC,它主要用来代替继电器实现逻辑控制。
随着技术的发展,这种装置的功能已经大大超过了逻辑控制的范围,在世界各地得到了广泛应用。
同时,PLC的功能也不断完善。
随着计算机技术、信号处理技术、控制技术、网络技术的不断发展和用户需求的不断提高,PLC在开关量处理的基础上增加了模拟量处理和运动控制等功能。
今天的PLC不再局限于逻辑控制,在运动控制、过程控制等领域也发挥着十分重要的作用。
近10年来,随着PLC价格的不断降低和用户需求的不断扩大,越来越多的中小设备开始采用PLC进行控制,PLC在我国的应用增长十分迅速。
随着中国经济的高速发展和基础自动化水平的不断提高,今后一段时期内PLC在我国仍将保持高速增长势头。
2、轧钢加热炉与PLC控制系统
2、1轧钢加热炉
轧钢加热炉燃烧介质各参数的稳定运行非常重要,它直接影响到钢坯的质量,并涉及安全生产等重大问题。
在生产过程中对加热炉炉压、炉温、煤气流量、空气流量的稳定有严格的要求。
要想实现这些参数的稳定,并且达到较好地配比有不同的方法可以实现。
加热炉的热工检测控制量共128点,其中模拟量输入56点,模拟量输出24点,开关量输入24点,开关量输出24点。
调节回路16套,分别对加热炉的煤气、空气的流量、压力,炉内温度,换热器的保护等进行控制。
2、2系统组成
硬件采用西门子S7-300系列PLC,燃烧热工调节系统。
上位操作站(兼容工程师站)采用高可靠性的研华工业控制计算机,上位机与PLC的通讯采用SIMENS MPI 现场总线。
并配置编程软件STEP7 5.0及西门子专用监控组态软件WINCC 7.0,采用冗余备份主从控制型控制器,具有良好的人机界面,操作人员可以进行参数的设定、修改、温度压力等曲线的调用和设备操作。
人机接口能显示全景画面、区域画面、报警画面、操作者指导信息画面、图表画面、趋势记录、系统维护等各种画面。
PLC系统结构如图1。
该系统将动态采集的温度、流量、压力等参数以动态趋势图的形式显示,并根据要求进行存储和打印。
2、3加热炉压力控制的应用
为保证助燃空气与煤气压力保持稳定、使炉内燃烧顺利进行,煤气和空气的压力必须进行控制。
加热炉炉内压力过高,过低都不恰当,过高会使炉门喷火并损伤炉子设备,过低会使加热炉吸入冷空气,影响加热炉燃烧质量及效果,炉内压力的控制也很重要。
1、助燃空气压力控制
助燃空气压力的大小,是保证喷嘴正常工作的重要条件。
助燃空气压力调节是PID调节。
如果设定值与反馈值存在偏差,PID调节开始进行,尽可能在短时间内使偏差最小。
当反馈值大于设定值,经PID运算后向阀门输出控制信号,使阀门关小,于是压力下降,当反馈值小于设定值,经PID运算向阀门输出信号,使阀门开大,压力升高。
2、煤气压力控制
煤气压力控制阀主要起安全保护作用,煤气和空气若是出现低压,将会出现事故。
所以在煤气和空气主管道上,分别装有两个低压开关,在换热器前后也各装有一个。
任意一个低压开关动作,将会使煤气主关断阀都会自动关闭,停炉,保护加热炉。
3、炉膛压力控制
炉膛压力主要通过调节煤气侧引风机入口和空气侧引风机入口总管控制阀开度,进行调节,保持适度的微正压以防止外部冷空气侵入和炉内气体外溢,并有辅助烟道配合控制炉压。
为了避免炉膛内压力波动,换向时,调节阀动作禁止。
由于炉压滞后大,时间常数小,因此采用前馈—负反馈调节。
2、4加热炉温度控制系统的应用
加热炉温度控制实现过程是:首先通过一次测温元件热电偶将加热炉的温度转化为电压信号,PLC主控系统内部的A/D转换器将送进来的电压信号转化为PLC可识别的数字量,然后PLC
将系统给定的温度值与反馈回来的温度值进行比较,采用连续PID控制,发现有偏移则控制相应的煤气阀门、空气阀门来调节煤气、空气流量,通过控制加热炉燃烧来达到控制炉温的目的。
为保证炉温的均匀性、燃烧的合理性,我厂实施多段燃烧及相应的控制控制策略,以消除各供热段之间的互相干扰。
为保证各供热区温度的可控性,首先须对各区设置独立的,以温度为主环,空气、煤气流量调节为副环的炉温控制回路。
根据工艺的供热情况,共分为3个供热调节回路:加热段、预热段和均热段的3个燃烧控制区段,三段分别换向燃烧。
各个燃烧控制段采用2维交叉控制方式,以保证热负荷变化时的合理空燃配比,同时保证温度控制的快速响应。
根据最大加热速率对温度调节器输出限幅,防止钢坯过热。
最大加热速率与炉内负荷及坯料在炉时间有关。
2、5安全防护和环保
重点煤气区域设置了4点CO浓度监测、报警装置,以防煤气外泄造成的安全事故。
2、6 PLC在故障诊断系统中的应用
故障诊断系统是典型的人机系统,根据系统中的信息流向和功能划分的结果,基于操作站智能化的故障诊断系统。
PLC对数字量信号的识别是通过其数字量输入模块完成的。
PLC控制轧钢生产设备时,设备中的压力、温度、液位、行程数字及操作按钮等数字量传感器与PLC的输入端子相连,每个输入端子在PLC的数据区中分配有一个“位”,每个“位”在内存中为一个地址。
读取PLC输入位的状态值可作为识别数字量故障信号的根据。
诊断数字量故障的过程,实质就是将PLC正常的输入位状态值与相应的输入位的实际状态值相比较的过程。
如果二者比较的结果是一致的,则表明设备处于正常工况,不一致则表明对应输入位的设备部位处于故障工况。
这就是PLC诊断基于数字量信号故障的基本原理。
这种诊断方法,故障定位准确,可进行实时在线诊断。
通过PLC的图形功能块编程,还可将故障诊断融入过程控制,达到保护轧钢设备的目的。
系统的输入模块要完成轧钢生产设备故障检测信号、控制指令和专家知识的接收工作。
处理模块要求能自动实现特征参数提取、控制指令代码转换的功能。
专家知识的整理和表达由领域专家和系统专家协作完成。
控制模块是故障诊断系统的核心,它根据控制指令,利用专家知识,完成从故障特征到故障原因的识别工作。
控制模块的功能越完善,故障诊断系统的智能化程度越高。
输出模块通过声光报警装置和人机界面,给出故障定位、预报和解释的结果。
其中,人机界面还能提供排除故障的技术路线。
实现信息源从输入模块到输出模块的全自动流向,减少人在其中的干预作用,是轧钢生产设备对其故障诊断系统的要求。
采用PLC的故障诊断系统,有助于实现故障诊断过程的自动化。
参考文献
1、应桃,李文,钟春华。
GE90-30 PLC在炼轧厂加热炉系统中的应用,《南方金属》,2006年05期
2、赵守庭。
PLC在加热炉控制系统中的应用,《电气传动自动化》,1997年01期
3、李文霞,崔朝贤,王利民。
中型轧钢厂加热炉自动控制系统,《冶金自动化》,1998年06期
4、邱公伟主编。
可编程控制器网络通信及应用。
北京:清华大学出版社,2000
5、邹益仁等编著。
现场总线控制系统的设计和开发。
北京:国防工业出版社,2003
6、廖常初主编.可编程序控制器的编程方法与工程应用,重庆:重庆大学出版社,2001
7、陈在平等主编。
可编程序控制器技术与应用系统设计。
北京:机械工业出版社,2002
8、宫淑贞等编著。
可编程控制器原理及应用。
北京:人民邮电出版社,2002■。